环氧树脂浇注工艺
环氧树脂注胶施工工艺流程

环氧树脂注胶施工工艺流程
环氧树脂注胶是目前民用建筑中应用频率最高的新型结构胶之一,不仅因其优良的抗压、抗拉性能,还因其化学性质稳定,不易老化。
环氧树脂注胶的制作和使用需要符合一定的技术要求,下面就环氧树脂注胶施工的工艺流程做一介绍。
1. 准备施工现场和材料
首先,需要为环氧树脂注胶的施工现场做好准备工作,包括清理现场,确保地面平整,无油污和灰尘等;同时检查施工材料,确保无潮气、结块、变色以及其它表面缺陷。
2. 处理胶嘴
将环氧树脂的注胶装置固定好,然后处理胶嘴。
首先在胶嘴开口处塞上铜丝网,然后压入一定长度的塑料管,保证胶嘴通畅。
3. 混合树脂与固化剂
混合环氧树脂和固化剂的比例需要根据实际施工情况而定,一般来说选择A、B两桶组份的比例为2:1,混合时间为2~3分钟左右,同时需要注意搅拌器的转速和时间。
4. 泼洒注胶
将混合好的环氧树脂放入环氧树脂注胶桶中,通过注胶桶内压力从长条胶嘴中泼洒至需要补强加固的建筑结构处。
注胶时需要对要补强的建筑结构进行分类分区,根据需要注胶的位置进行具体的操作。
根据需求可以采用单组份或双组份注胶工艺。
5. 整体固化
环氧注胶结束后需要给予固化时间,每种胶水所需的时间不同,在固化过程中需要保持施工现场的干燥,温度不宜太高也不宜太低。
6. 检查效果
固化时间到后,对已经注胶的区域进行检查和测试,如检查其粘接强度是否符合要求,有无空鼓现象,不合格的要及时处理,保证注胶的质量。
以上便是环氧树脂注胶施工的主要工艺流程,该工艺适合于民用建筑中需要局部加固的实际操作,施工过程中需要注意选材和比例的准确性,同时也需要具备丰富的施工经验和较强的技术实力。
环氧浇注工艺存的问题和不足

环氧浇注工艺存在的问题与不足环氧浇注工艺作为一种广泛应用于电气绝缘领域的成型技术,具有许多优点,如优良的电气性能、较高的机械强度以及良好的耐化学腐蚀性等。
然而,在实际应用过程中,该工艺仍存在一些问题和不足,这些问题和不足在一定程度上限制了环氧浇注工艺的发展和应用范围。
一、工艺控制难度较高环氧浇注工艺涉及多个环节,包括原材料的选择、配方的设计、混合均匀性的控制、浇注操作以及后续的固化处理等。
这些环节都需要精确控制,否则很容易导致产品质量的不稳定。
例如,原材料的选择不当可能导致产品性能下降,配方设计不合理可能导致浇注过程中出现缺陷,而浇注操作的不规范则可能导致内部空洞或裂纹等问题。
二、固化收缩问题环氧树脂在固化过程中会产生一定的收缩,这种收缩可能导致产品尺寸不稳定,甚至产生应力集中和开裂等问题。
尤其是在大型复杂构件的浇注过程中,固化收缩问题尤为突出。
为了解决这个问题,通常需要采取一系列措施,如优化配方、控制固化条件、采用补偿收缩等,但这些措施往往会增加工艺复杂性和成本。
三、环保问题环氧树脂在固化过程中可能产生挥发性有机化合物(VOCs),这些化合物对环境和人体健康具有一定的危害。
随着环保意识的提高,如何降低环氧浇注工艺中的VOCs排放已成为一个亟待解决的问题。
目前,一些环保型环氧树脂和固化剂的开发和应用在一定程度上缓解了这个问题,但仍需进一步研究和改进。
四、成本问题虽然环氧浇注工艺在电气绝缘领域具有广泛的应用前景,但其较高的成本在一定程度上限制了其市场推广和应用。
原材料的价格、工艺设备的投资以及生产过程中的能耗等因素都可能导致环氧浇注产品的成本较高。
因此,如何在保证产品质量的前提下降低成本,是环氧浇注工艺面临的一个重要问题。
综上所述,环氧浇注工艺在实际应用过程中仍存在一些问题和不足,这些问题和不足在一定程度上限制了其发展和应用范围。
未来,随着科技的不断进步和环保要求的不断提高,环氧浇注工艺将面临更多的挑战和机遇。
环氧树脂灌缝施工工艺
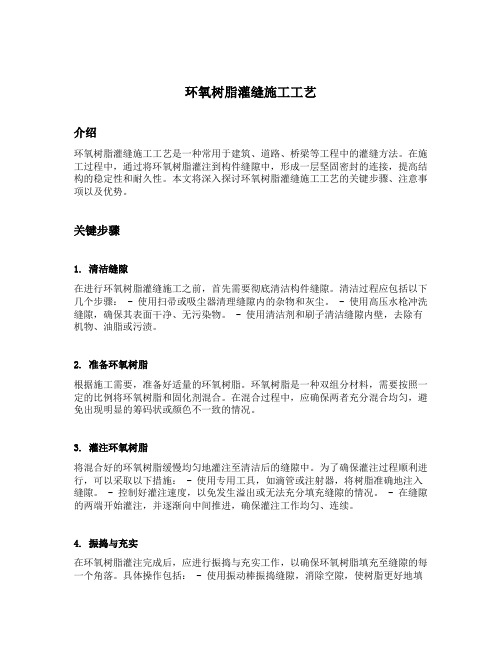
环氧树脂灌缝施工工艺介绍环氧树脂灌缝施工工艺是一种常用于建筑、道路、桥梁等工程中的灌缝方法。
在施工过程中,通过将环氧树脂灌注到构件缝隙中,形成一层坚固密封的连接,提高结构的稳定性和耐久性。
本文将深入探讨环氧树脂灌缝施工工艺的关键步骤、注意事项以及优势。
关键步骤1. 清洁缝隙在进行环氧树脂灌缝施工之前,首先需要彻底清洁构件缝隙。
清洁过程应包括以下几个步骤: - 使用扫帚或吸尘器清理缝隙内的杂物和灰尘。
- 使用高压水枪冲洗缝隙,确保其表面干净、无污染物。
- 使用清洁剂和刷子清洁缝隙内壁,去除有机物、油脂或污渍。
2. 准备环氧树脂根据施工需要,准备好适量的环氧树脂。
环氧树脂是一种双组分材料,需要按照一定的比例将环氧树脂和固化剂混合。
在混合过程中,应确保两者充分混合均匀,避免出现明显的筹码状或颜色不一致的情况。
3. 灌注环氧树脂将混合好的环氧树脂缓慢均匀地灌注至清洁后的缝隙中。
为了确保灌注过程顺利进行,可以采取以下措施: - 使用专用工具,如滴管或注射器,将树脂准确地注入缝隙。
- 控制好灌注速度,以免发生溢出或无法充分填充缝隙的情况。
- 在缝隙的两端开始灌注,并逐渐向中间推进,确保灌注工作均匀、连续。
4. 振捣与充实在环氧树脂灌注完成后,应进行振捣与充实工作,以确保环氧树脂填充至缝隙的每一个角落。
具体操作包括: - 使用振动棒振捣缝隙,消除空隙,使树脂更好地填充缝隙。
- 在振捣的同时,可以使用钢板或钢棒充实缝隙,推动环氧树脂的进一步渗透、填充。
5. 后续处理环氧树脂灌缝完成后,还需进行一些后续处理工作: - 去除多余的环氧树脂,确保施工表面的整洁和美观。
- 根据需要,对施工表面进行必要的抛光和修整。
注意事项在进行环氧树脂灌缝施工时,需要注意以下几点: 1. 施工环境:施工现场应保持干燥、无尘、无风,并确保温度适宜,避免低温或高温对环氧树脂固化的影响。
2. 比例配比:在混合环氧树脂和固化剂时,应按照规定的比例进行配比,确保施工质量。
环氧树脂浇注成型
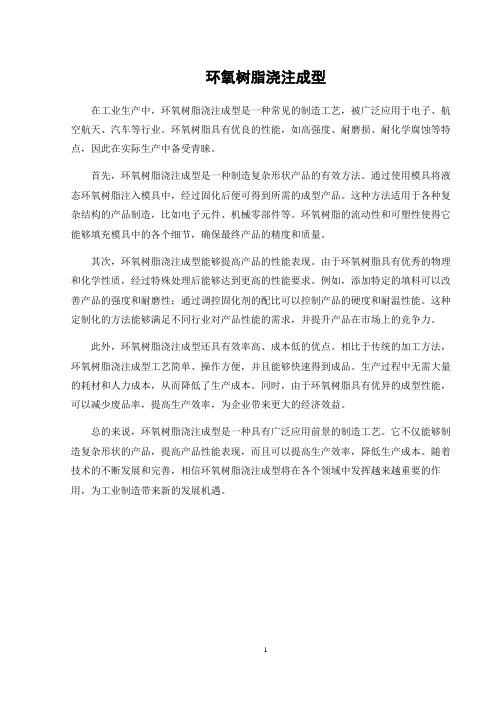
环氧树脂浇注成型
在工业生产中,环氧树脂浇注成型是一种常见的制造工艺,被广泛应用于电子、航空航天、汽车等行业。
环氧树脂具有优良的性能,如高强度、耐磨损、耐化学腐蚀等特点,因此在实际生产中备受青睐。
首先,环氧树脂浇注成型是一种制造复杂形状产品的有效方法。
通过使用模具将液态环氧树脂注入模具中,经过固化后便可得到所需的成型产品。
这种方法适用于各种复杂结构的产品制造,比如电子元件、机械零部件等。
环氧树脂的流动性和可塑性使得它能够填充模具中的各个细节,确保最终产品的精度和质量。
其次,环氧树脂浇注成型能够提高产品的性能表现。
由于环氧树脂具有优秀的物理和化学性质,经过特殊处理后能够达到更高的性能要求。
例如,添加特定的填料可以改善产品的强度和耐磨性;通过调控固化剂的配比可以控制产品的硬度和耐温性能。
这种定制化的方法能够满足不同行业对产品性能的需求,并提升产品在市场上的竞争力。
此外,环氧树脂浇注成型还具有效率高、成本低的优点。
相比于传统的加工方法,环氧树脂浇注成型工艺简单、操作方便,并且能够快速得到成品。
生产过程中无需大量的耗材和人力成本,从而降低了生产成本。
同时,由于环氧树脂具有优异的成型性能,可以减少废品率,提高生产效率,为企业带来更大的经济效益。
总的来说,环氧树脂浇注成型是一种具有广泛应用前景的制造工艺。
它不仅能够制造复杂形状的产品,提高产品性能表现,而且可以提高生产效率,降低生产成本。
随着技术的不断发展和完善,相信环氧树脂浇注成型将在各个领域中发挥越来越重要的作用,为工业制造带来新的发展机遇。
1。
HEXION环氧树脂浇注工艺
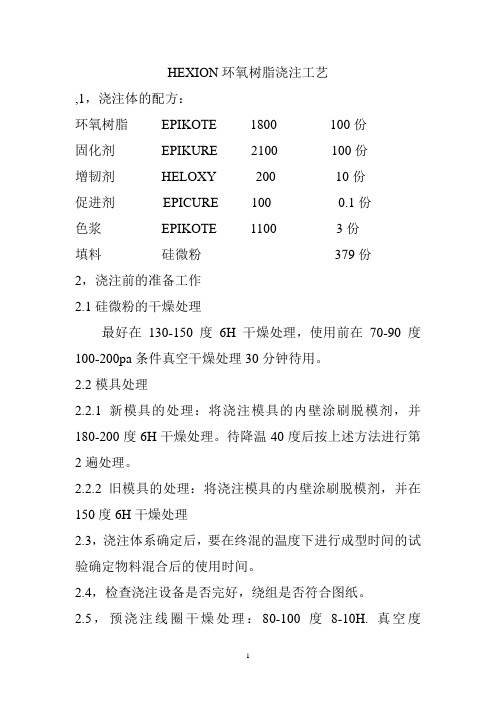
HEXION环氧树脂浇注工艺,1,浇注体的配方:环氧树脂EPIKOTE 1800 100份固化剂EPIKURE 2100 100份增韧剂HELOXY 200 10份促进剂EPICURE 100 0.1份色浆EPIKOTE 1100 3份填料硅微粉379份2,浇注前的准备工作2.1硅微粉的干燥处理最好在130-150度6H干燥处理,使用前在70-90度100-200pa条件真空干燥处理30分钟待用。
2.2模具处理2.2.1新模具的处理:将浇注模具的内壁涂刷脱模剂,并180-200度6H干燥处理。
待降温40度后按上述方法进行第2遍处理。
2.2.2旧模具的处理:将浇注模具的内壁涂刷脱模剂,并在150度6H干燥处理2.3,浇注体系确定后,要在终混的温度下进行成型时间的试验确定物料混合后的使用时间。
2.4,检查浇注设备是否完好,绕组是否符合图纸。
2.5,预浇注线圈干燥处理:80-100度8-10H. 真空度100-200pa2.6,浇注罐的预热处理:75度1-2H,真空度200-300pa2.7,在浇注前2H将变压器线圈送入真空浇注罐中,预热1-2H。
3,浇注工艺3.1将环氧树脂、增韧剂和色浆按比例的量加到甲罐中进行脱水脱气处理,温度75度,真空度100pa(推荐工艺200-300pa)时间1H,然后加入188.5份的硅微粉继续抽空1-2H直至表面无气泡为止。
3.2将固化剂、促进剂加到乙罐中,同样进行脱水脱气处理,温度65度,真空度100pa时间1H,然后加入188.5份的硅微粉继续抽空1-2H,直至表面无气泡为止。
3.3将甲乙两罐的树脂和固化剂注入混料罐中(静态或动态混料罐),温度70度,真空度100pa,时间约40分钟,3.4浇注,浇注罐的温度在75度左右,真空度比混料罐高800-1000pa,由阀门的大小来控制浇注的速度,一般在30-40分钟浇注完(浇注的速度一般控制在1-5升/分)浇注完成后,抽真空100-500pa,30min。
环氧树脂浇注成型工艺
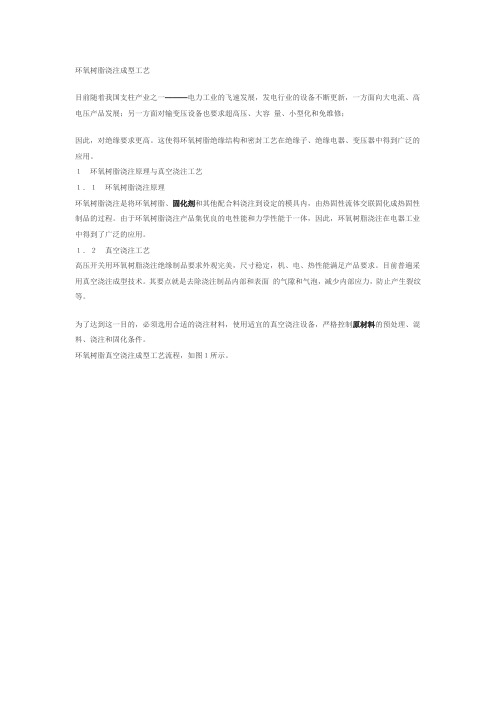
环氧树脂浇注成型工艺目前随着我国支柱产业之一———电力工业的飞速发展,发电行业的设备不断更新,一方面向大电流、高电压产品发展;另一方面对输变压设备也要求超高压、大容量、小型化和免维修;因此,对绝缘要求更高。
这使得环氧树脂绝缘结构和密封工艺在绝缘子、绝缘电器、变压器中得到广泛的应用。
1环氧树脂浇注原理与真空浇注工艺1.1环氧树脂浇注原理环氧树脂浇注是将环氧树脂、固化剂和其他配合料浇注到设定的模具内,由热固性流体交联固化成热固性制品的过程。
由于环氧树脂浇注产品集优良的电性能和力学性能于一体,因此,环氧树脂浇注在电器工业中得到了广泛的应用。
1.2真空浇注工艺高压开关用环氧树脂浇注绝缘制品要求外观完美,尺寸稳定,机、电、热性能满足产品要求。
目前普遍采用真空浇注成型技术。
其要点就是去除浇注制品内部和表面的气隙和气泡,减少内部应力,防止产生裂纹等。
为了达到这一目的,必须选用合适的浇注材料,使用适宜的真空浇注设备,严格控制原材料的预处理、混料、浇注和固化条件。
环氧树脂真空浇注成型工艺流程,如图1所示。
2真空浇注成型工艺关键技术(1)原材料的预处理原材料预处理是在一定温度下加热至一定时间,并经过真空处理以脱除原材料中吸附的水分、气体及低分子挥发物,达到脱气脱水的效果。
(2)混料混料的目的是使环氧树脂、填料、固化剂等混合均匀,便于进行化学反应。
混料分一次和二次混料。
树脂和填料混合称一次混料,在一次混料中加入固化剂成为二次混料。
一次混料是使填料被树脂充分浸润。
因为环氧树脂与酸酐固化剂的反应是放热反应,填料是导热性好的材料,它能将反应释放的热量向外传导而不积集,使浇注物内应力均匀分布而不产生缩痕。
二次混料时间要确保固化剂混合均匀,其温度、真空度的参数也很重要。
温度过高,将使混合料黏度迅速增加,影响脱气浇注工序;真空度用以保证混合料的脱气、脱水,但不能导致固化剂的气化,所以真空度要恰当。
(3)浇注浇注是将组装好并预热到一定温度的模具放入真空浇注罐中或在真空浇注罐内预热,模具温度略高于混合料的温度,浇注罐抽真空度到1330Pa以下,维持一定温度[1],最后将混合均匀的物料浇入模具内;浇注完成后要继续抽真空一段时间,以去除浇注件内所形成的气泡,即可关闭真空,打开浇注罐,将模具送入固化炉进行固化。
环氧树脂浇铸成型工艺流程

环氧树脂浇铸成型工艺流程
环氧树脂浇铸成型工艺是一种常见的制造工艺,用于生产具有高强度、耐磨性和耐腐蚀性的产品。
本文将介绍环氧树脂浇铸成型的工艺流程和关键步骤,帮助读者了解这一制造过程。
首先,环氧树脂浇铸成型工艺的第一步是准备工作。
在开始实际浇铸之前,需要准备好所需的原材料,包括环氧树脂、固化剂、填料等。
确保所有材料的质量符合要求,并按照配方比例准备好。
接下来是模具制备阶段。
选择合适的模具对于最终产品的质量至关重要。
根据产品的形状和尺寸,选择适合的模具,并进行表面处理以确保产品的顺利脱模。
在将模具放置在合适的位置后,可以进行下一步操作。
然后是混合环氧树脂和固化剂。
将事先准备好的环氧树脂和固化剂按照一定的比例混合均匀,通常在一定的时间内搅拌以确保两者充分混合。
在混合过程中可以添加适量的填料以调整产品的性能特性。
随后是浇注和固化环节。
将混合好的环氧树脂倒入准备好的模具中,确保浇注过程中没有气泡产生。
根据产品的大小和复杂程度,选择合适的固化时间和温度,等待环氧树脂完全固化。
最后是脱模和后处理。
在环氧树脂完全固化后,小心地将产品从模具中取出。
根据产品的要求,进行必要的修整和表面处理工作。
最终得到的产品将具有高强度、耐磨性和耐腐蚀性的特点,可以用于各种工业领域。
总的来说,环氧树脂浇铸成型工艺流程包括准备工作、模具制备、混合环氧树脂和固化剂、浇注和固化、脱模和后处理等关键步骤。
通过掌握这些步骤,可以生产出高质量的环氧树脂制品,满足不同领域的需求。
1。
环氧浇注工艺

环氧浇注工艺一、概述本船主机、舵机及尾轴管的安装均采用环氧树脂浇注,本船选用高尔登公司提供的PR610-7CF环氧树脂。
根据主机安装工艺要求,在主机轴系校中结束、主机位置确定、舵杆安装完毕、尾轴管定位后,再浇注主机、舵机环氧垫块、固定尾轴管,按图纸要求主机环氧垫块理论厚度为42mm,舵机垫片的理论厚度为30mm,尾轴管与尾轴毂及前铸钢件间隙内应注满环氧树脂。
二、主机、环氧垫块浇注的准备工作A:1、主机进舱前或在主机定位前在主机基座内测点焊5mm厚钢质内档板,挡板高度比环氧垫块高度要低10-15mm。
2、根据主机安装及校中工艺要求,同时考虑环氧垫块初始压缩量0.001x垫块厚度,调整好主机位置。
3、根据主机安装图SC4255-420-01,安装主机侧面及端部支撑垫块,为了减小侧面支撑因焊接应力而发生的变形,应将其先点焊在底座面板上,当焊缝冷却后,侧面支撑上所有焊于面板上的焊缝,应以适当的间隔分步进行焊接,每次间隔时间应保证挡板充分冷却。
4、主机底座下平面及船体基座上平面应仔细清除水、油等其他杂物。
5、点焊环氧树脂浇注外档板〔75×5扁钢〕,侧面支撑处应保证侧向支撑锁紧块的安装要求,同时涂油脂及密封胶泥保证不泄漏。
6、基座螺栓孔用孔塞塞好,并用密封胶堵好。
7、所有与环氧树脂垫块接触的外表都应喷上脱膜剂。
8、按船检及船东要求安装测量销〔检查环氧树脂垫片压缩量〕。
9、所有准备工作结束在浇注前最后检查主机的安装位置应满足主机轴系校中安装工艺的要求。
B、舵机环氧垫块浇注前准备工作1、根据舵机安装图SC4255-232-03要求,同时考虑环氧垫块初始压缩量0.001X垫块厚度,调整好舵机高度位置。
2、清除基座面板及设备座底面板上的油污等污物。
3、按舵机安装图中所要求尺寸制作垫块模框,可用泡沫条插入机座底面与基座面板之间围成三面,外侧用金属挡板〔δ=5mm〕,点焊于基座面板上,挡板的位置距舵机座外端面25-30mm,高度应比浇注垫块高25-30mm〔先在基座面板外侧延伸30mm的金属板,再在此板点焊上外挡板〕见详图,组成后的模框四周缝隙用密封胶堵,以确保浇注时不泄漏。
环氧树脂浇注工艺

1、目的线圈的环氧树脂浇注是一项工艺性强、技术难度较高的生产工序。
为确保变压器质量,每个操作人员必须严格按本作业指导书的规定进行操作。
未经技术部门同意,任何人不得擅自更改.2、适用范围指导书适用于10~35kV级树脂绝缘干式电力变压器.3、工艺装备:3。
1真空浇注设备:真空浇注罐:可调温度在0~150℃,有恒温控制装置,温度控制精度±3℃,真空度小于50Pa.电动混料罐:可调温度在0~150℃,有恒温控制装置,温度控制精度±3℃。
抽真空设备:应具备油水滤清器、冷凝器、真空泵及增压泵等。
3。
2专用固化箱:可调温度在0~250℃,并有恒温控制装置,温度控制精度±2℃.3。
3称量工具:50kg电子称3。
4通风、起重等常用设备4、工作场所的安全防护4.1工作场所环境要保持整洁与通风,配备。
4.2工作场所溅出物的处理,用锯末或回丝吸干,弃于废物箱内。
4.3参与该项工作的作业人员应穿防护服,戴护目镜、手套,在加料、混料时使用呼吸罩。
4.4皮肤保护:开始工作前先清洗后对暴露皮肤涂防护霜,若皮肤被浇注原料粘污,用吸纸擦掉,然后用温水和无碱皂清洗.眼睛沾染了树脂、固化剂或混合料时,应立即用清水进行冲洗10~15分钟,然后请医生诊治。
4。
5如作业人员呼吸道吸入原料蒸汽出现不适异兆,应立即将人员转移至通风处并请医生处理。
5、材料及配方5.1树脂配方(按重量比)5。
1.1采用菏泽或嘉兴东方化工厂固化剂和增韧剂树脂: 硅微粉:固化剂:增韧剂: 色浆:促进剂百分比20% :60% :15% :5%:0。
2% :0。
03%(范围0。
03~0.04%)重量比100 :300 :75 :25 : 1 :0。
15 (范围0。
15~0。
2)5。
1.2采用嘉兴清洋化学有限公司固化剂和增韧剂树脂:硅微粉:固化剂: 增韧剂: 色浆: 促进剂百分比20。
7% :62。
1%:13。
9%: 3.3%: 0.207% :0.03% (范围0。
环氧树脂真空浇注工艺技术
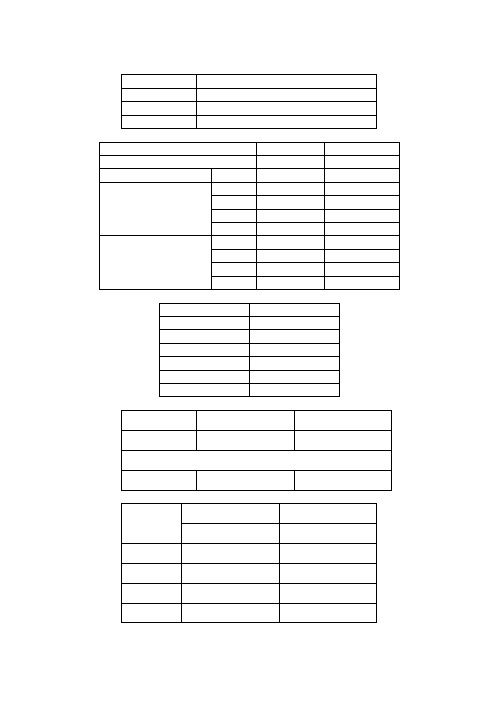
(Static Mixers)一种的高效混合设备通过固定在管内的混合单元内件,使进入二股混合料产生流体的切割、剪切、旋转和重新混合;达到混合料之间良好分散和充分混合的目的,得到均质浇注料。
环氧树脂混合料静态混合的主要技术特点:静态混合罐混料过程精确可控,混料时间短、混合料新鲜,流动性能优越,提高了环氧树脂浇注料对线圈和嵌件的浸润性,能最大程度保证混合材料的低粘度和活性,解决了动态机械搅拌混料因长时间搅拌、抽真空而导致的凝胶时间缩短、粘度增高的问题。
同时,可根据生产量随时混料,缩短周期,提高效率,杜绝动态搅拌混料方式每次浇注都会产生余料的痼疾,节约材料。
对于二组份粘度较大或混合比例差距过大的混合料,上述二种混合器很难在短时间内达到混合的目的,为此,可选择动态混合器进行强制、快速的混合,以增强混合效果。
见图二十一环氧树脂-酸酐配方体系的固化过程——温度-密度变化曲线图二十一图二十一图二十一图二十一六,电工浇注用环氧树脂真空浇注技术工艺链中应加以重视的几个要点环氧树脂浇注料固化成型后,浇注绝缘部件外观光洁无裂缝、无气泡,但是,浇注的绝缘部件(如:电流电压互感器、干式变压器等)却产生了“局部放电”超标现象。
高压电器产生“局部放电”超标现象是与产品结构设计、绝缘材料互配、环氧树脂浇注料和浇注工艺技术有关;在此,我们只对与环氧树脂浇注料和浇注工艺有关的五大要素进行分析探讨:1,微量杂质:主要由配方组分材料(环氧树脂、固化剂、增韧剂、硅微粉)内存在的低分子挥发物,水份和微量金属氧化物等;混料设备及输料管道内有污染物;生产现场粉尘环境污染;操作人为因素和被封装部件表面有油污等;2,微裂纹:这类裂纹发生在浇注件的深层,特别是环氧树脂与部件之间界面上存在的微裂纹;线状”裂纹,是环氧树脂固化物内应力泄放而造成的开裂。
这种类型的开裂条纹,容易发生的几个部位:①环氧树脂浇注层厚薄不均匀处,没有过渡区域;②环氧树脂浇注层有尖锐角或直角处(与浇注模具设计有关);③与金属嵌件接触处,特别是金属嵌件有尖锐角或直角而没有倒园角处;④与金属接触处的环氧树脂层较薄等。
环氧树脂施工工艺流程
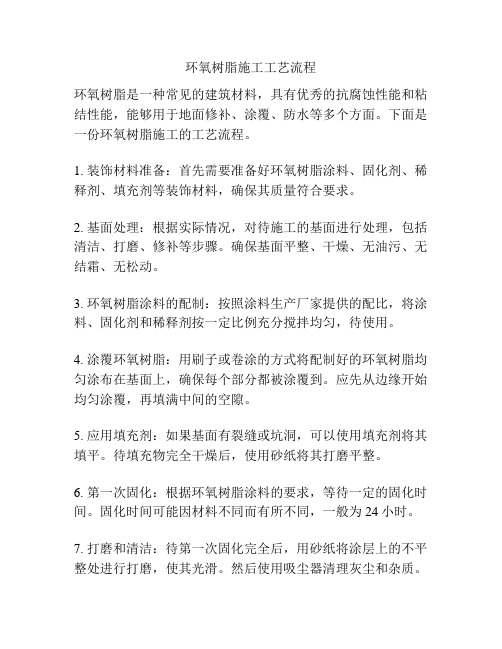
环氧树脂施工工艺流程环氧树脂是一种常见的建筑材料,具有优秀的抗腐蚀性能和粘结性能,能够用于地面修补、涂覆、防水等多个方面。
下面是一份环氧树脂施工的工艺流程。
1. 装饰材料准备:首先需要准备好环氧树脂涂料、固化剂、稀释剂、填充剂等装饰材料,确保其质量符合要求。
2. 基面处理:根据实际情况,对待施工的基面进行处理,包括清洁、打磨、修补等步骤。
确保基面平整、干燥、无油污、无结霜、无松动。
3. 环氧树脂涂料的配制:按照涂料生产厂家提供的配比,将涂料、固化剂和稀释剂按一定比例充分搅拌均匀,待使用。
4. 涂覆环氧树脂:用刷子或卷涂的方式将配制好的环氧树脂均匀涂布在基面上,确保每个部分都被涂覆到。
应先从边缘开始均匀涂覆,再填满中间的空隙。
5. 应用填充剂:如果基面有裂缝或坑洞,可以使用填充剂将其填平。
待填充物完全干燥后,使用砂纸将其打磨平整。
6. 第一次固化:根据环氧树脂涂料的要求,等待一定的固化时间。
固化时间可能因材料不同而有所不同,一般为24小时。
7. 打磨和清洁:待第一次固化完全后,用砂纸将涂层上的不平整处进行打磨,使其光滑。
然后使用吸尘器清理灰尘和杂质。
8. 第二次涂覆:使用同样的方法和涂料,进行第二次涂覆。
确保涂层的厚度和均匀性。
9. 第二次固化:同样等待一定的固化时间,一般为24小时。
待固化完全后,用手碰触涂层表面,确保其干燥。
10. 房间通风:对于室内施工,完成后需要打开窗户、通风机等设备进行通风,排出涂覆过程中产生的有害气体。
11. 完工验收:等待涂层充分干燥后,进行完工验收。
检查涂层是否平整、无裂缝、无气泡、无色差等。
以上就是环氧树脂施工的简要工艺流程。
在实际施工过程中,需要根据具体情况进行调整和完善,以确保施工效果和质量。
同时,施工人员需要具备一定的专业知识和技能,以确保施工安全和质量。
环氧树脂填充工艺流程
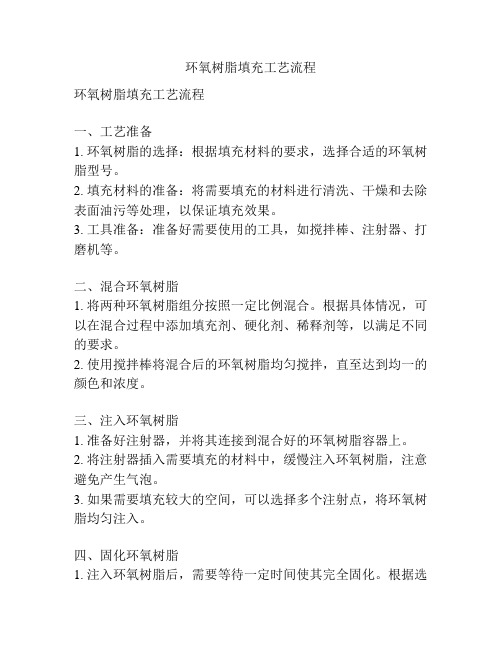
环氧树脂填充工艺流程环氧树脂填充工艺流程一、工艺准备1. 环氧树脂的选择:根据填充材料的要求,选择合适的环氧树脂型号。
2. 填充材料的准备:将需要填充的材料进行清洗、干燥和去除表面油污等处理,以保证填充效果。
3. 工具准备:准备好需要使用的工具,如搅拌棒、注射器、打磨机等。
二、混合环氧树脂1. 将两种环氧树脂组分按照一定比例混合。
根据具体情况,可以在混合过程中添加填充剂、硬化剂、稀释剂等,以满足不同的要求。
2. 使用搅拌棒将混合后的环氧树脂均匀搅拌,直至达到均一的颜色和浓度。
三、注入环氧树脂1. 准备好注射器,并将其连接到混合好的环氧树脂容器上。
2. 将注射器插入需要填充的材料中,缓慢注入环氧树脂,注意避免产生气泡。
3. 如果需要填充较大的空间,可以选择多个注射点,将环氧树脂均匀注入。
四、固化环氧树脂1. 注入环氧树脂后,需要等待一定时间使其完全固化。
根据选用的环氧树脂型号和环境温度,固化时间可能会有所不同。
2. 在固化过程中,可以进行一些辅助措施,比如加热或施加压力,以加快固化过程。
五、修整表面1. 当环氧树脂完全固化后,可以进行表面修整。
使用打磨机或砂纸对填充部位进行打磨,使其与周围材料的表面光滑一致。
2. 清洁表面,去除打磨产生的粉尘和杂质。
六、检验填充效果1. 对填充部位进行检验,确认填充效果是否符合要求。
可以通过目测或者其他检测手段,比如材料的硬度、尺寸、密封性等来评估填充质量。
2. 如果填充效果不理想,可以进行必要的修补或调整。
七、记录和总结在整个填充过程中,要注意记录关键参数,比如环氧树脂的配比、固化时间等,并进行总结。
根据填充效果和总结,可以进行工艺改进,提高填充质量和效率。
以上就是环氧树脂填充工艺流程的一般步骤。
具体操作过程中,需要根据具体材料和要求进行调整和改进。
环氧树脂灌缝施工工艺

环氧树脂灌缝施工工艺环氧树脂灌缝施工工艺环氧树脂灌缝施工工艺是一种常用的建筑施工工艺,主要用于填充建筑物中的缝隙,以提高建筑物的密封性和防水性。
环氧树脂灌缝施工工艺具有施工简单、效果显著、耐久性强等优点,因此在建筑行业中得到了广泛的应用。
环氧树脂灌缝施工工艺的步骤如下:1.准备工作在进行环氧树脂灌缝施工之前,需要对施工区域进行清理和处理。
首先,需要清除施工区域的灰尘、油污等杂物,以确保施工区域的干净和整洁。
其次,需要对施工区域进行处理,例如打磨、切割等,以便于后续的施工操作。
2.混合环氧树脂将环氧树脂和固化剂按照一定比例混合,搅拌均匀,直到形成均一的混合物。
需要注意的是,混合过程中要避免产生气泡,以免影响后续的施工效果。
3.灌缝施工将混合好的环氧树脂倒入灌缝器中,然后将灌缝器插入需要灌缝的缝隙中。
在灌缝的过程中,需要逐渐将灌缝器向后移动,以确保灌缝物质充满整个缝隙。
灌缝完成后,需要等待一定时间,让环氧树脂充分固化。
4.修整和打磨在环氧树脂灌缝施工完成后,需要对施工区域进行修整和打磨。
首先,需要将多余的环氧树脂切割掉,以便于后续的打磨操作。
然后,需要使用打磨机对施工区域进行打磨,以使其表面平整光滑。
总之,环氧树脂灌缝施工工艺是一种简单有效的建筑施工工艺,可以提高建筑物的密封性和防水性。
在进行环氧树脂灌缝施工之前,需要对施工区域进行清理和处理,然后将环氧树脂和固化剂按照一定比例混合,搅拌均匀,然后进行灌缝施工。
最后,需要对施工区域进行修整和打磨,以使其表面平整光滑。
环氧树脂浇注成型工艺
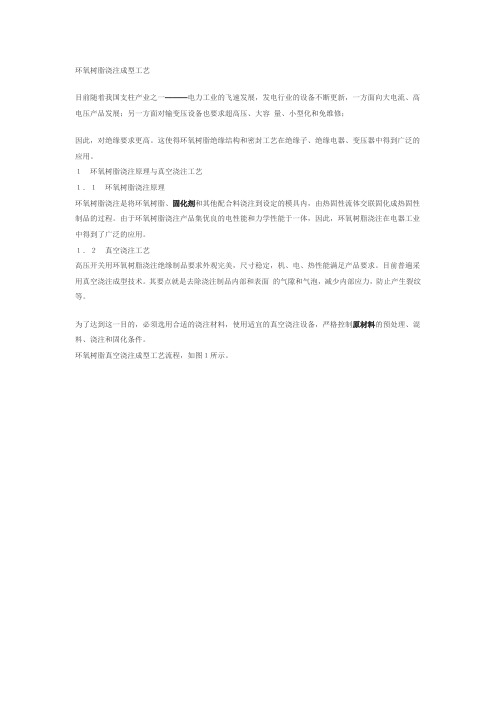
环氧树脂浇注成型工艺目前随着我国支柱产业之一———电力工业的飞速发展,发电行业的设备不断更新,一方面向大电流、高电压产品发展;另一方面对输变压设备也要求超高压、大容量、小型化和免维修;因此,对绝缘要求更高。
这使得环氧树脂绝缘结构和密封工艺在绝缘子、绝缘电器、变压器中得到广泛的应用。
1环氧树脂浇注原理与真空浇注工艺1.1环氧树脂浇注原理环氧树脂浇注是将环氧树脂、固化剂和其他配合料浇注到设定的模具内,由热固性流体交联固化成热固性制品的过程。
由于环氧树脂浇注产品集优良的电性能和力学性能于一体,因此,环氧树脂浇注在电器工业中得到了广泛的应用。
1.2真空浇注工艺高压开关用环氧树脂浇注绝缘制品要求外观完美,尺寸稳定,机、电、热性能满足产品要求。
目前普遍采用真空浇注成型技术。
其要点就是去除浇注制品内部和表面的气隙和气泡,减少内部应力,防止产生裂纹等。
为了达到这一目的,必须选用合适的浇注材料,使用适宜的真空浇注设备,严格控制原材料的预处理、混料、浇注和固化条件。
环氧树脂真空浇注成型工艺流程,如图1所示。
2真空浇注成型工艺关键技术(1)原材料的预处理原材料预处理是在一定温度下加热至一定时间,并经过真空处理以脱除原材料中吸附的水分、气体及低分子挥发物,达到脱气脱水的效果。
(2)混料混料的目的是使环氧树脂、填料、固化剂等混合均匀,便于进行化学反应。
混料分一次和二次混料。
树脂和填料混合称一次混料,在一次混料中加入固化剂成为二次混料。
一次混料是使填料被树脂充分浸润。
因为环氧树脂与酸酐固化剂的反应是放热反应,填料是导热性好的材料,它能将反应释放的热量向外传导而不积集,使浇注物内应力均匀分布而不产生缩痕。
二次混料时间要确保固化剂混合均匀,其温度、真空度的参数也很重要。
温度过高,将使混合料黏度迅速增加,影响脱气浇注工序;真空度用以保证混合料的脱气、脱水,但不能导致固化剂的气化,所以真空度要恰当。
(3)浇注浇注是将组装好并预热到一定温度的模具放入真空浇注罐中或在真空浇注罐内预热,模具温度略高于混合料的温度,浇注罐抽真空度到1330Pa以下,维持一定温度[1],最后将混合均匀的物料浇入模具内;浇注完成后要继续抽真空一段时间,以去除浇注件内所形成的气泡,即可关闭真空,打开浇注罐,将模具送入固化炉进行固化。
环氧树脂施工工艺流程

环氧树脂施工工艺流程环氧树脂是一种常用的建筑材料,其施工工艺流程对于工程质量和效果有着重要的影响。
下面将介绍环氧树脂施工的工艺流程。
首先,进行基面处理。
在进行环氧树脂施工之前,必须对基面进行处理,确保其平整、无灰尘、无油污等。
对于新浇筑的混凝土基面,需要等到其养护期结束后再进行施工;而对于旧基面,则需要清理、打磨、修补等处理,以确保环氧树脂与基面的粘接牢固。
接下来是环氧树脂底涂。
在基面处理完成后,需要进行环氧树脂底涂。
首先是搅拌环氧底涂材料,然后使用滚筒或刮刀均匀涂抹在基面上,形成一层均匀的涂层。
底涂的目的是提高基面的附着力,增加环氧树脂地坪的耐磨性和耐腐蚀性。
然后进行环氧树脂中涂。
环氧树脂中涂是为了填平基面的不平整和气孔,提高环氧地坪的平整度和美观度。
在底涂干燥后,使用滚筒或镘刀将环氧中涂材料均匀涂抹在地面上,形成一层平整的涂层。
接着是环氧树脂面涂。
环氧树脂面涂是环氧地坪的最后一道工艺,其质量直接影响到地坪的美观度和耐久性。
在中涂干燥后,使用滚筒或镘刀将环氧面涂材料均匀涂抹在地面上,形成一层光滑、坚固的面涂层。
最后是环氧树脂封固。
环氧树脂封固是为了提高地坪的耐磨性和耐化学腐蚀性。
在面涂干燥后,使用专用的环氧封固剂进行封固处理,形成一层坚固的保护膜,增加地坪的使用寿命。
总的来说,环氧树脂施工工艺流程主要包括基面处理、底涂、中涂、面涂和封固等环节。
只有严格按照工艺流程进行施工,才能确保环氧地坪的质量和使用效果。
希望以上内容能对环氧树脂施工工艺流程有所帮助。
细说环氧树脂浇注工艺方法
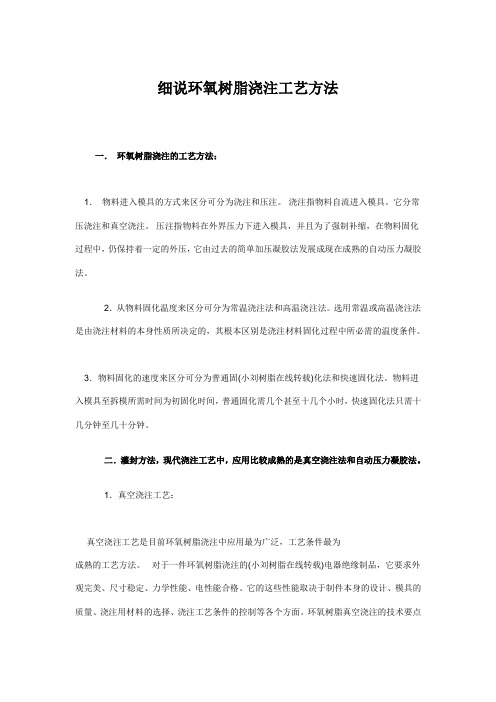
细说环氧树脂浇注工艺方法一.环氧树脂浇注的工艺方法:1.物料进入模具的方式来区分可分为浇注和压注。
浇注指物料自流进入模具。
它分常压浇注和真空浇注。
压注指物料在外界压力下进入模具,并且为了强制补缩,在物料固化过程中,仍保持着一定的外压,它由过去的简单加压凝胶法发展成现在成熟的自动压力凝胶法。
2.从物料固化温度来区分可分为常温浇注法和高温浇注法。
选用常温或高温浇注法是由浇注材料的本身性质所决定的,其根本区别是浇注材料固化过程中所必需的温度条件。
3.物料固化的速度来区分可分为普通固(小刘树脂在线转载)化法和快速固化法。
物料进入模具至拆模所需时间为初固化时间,普通固化需几个甚至十几个小时,快速固化法只需十几分钟至几十分钟。
二.灌封方法,现代浇注工艺中,应用比较成熟的是真空浇注法和自动压力凝胶法。
1.真空浇注工艺:真空浇注工艺是目前环氧树脂浇注中应用最为广泛,工艺条件最为成熟的工艺方法。
对于一件环氧树脂浇注的(小刘树脂在线转载)电器绝缘制品,它要求外观完美、尺寸稳定、力学性能、电性能合格。
它的这些性能取决于制件本身的设计、模具的质量、浇注用材料的选择、浇注工艺条件的控制等各个方面。
环氧树脂真空浇注的技术要点就是尽可能减少浇注制品中的气隙和气泡。
为了达到这一目的,在原料的预处理、混料、浇注等各个工序都需要控制好真空度、温度及工序时间。
2.自动压力凝胶工艺自动压力凝胶工艺是20世纪70年代初由瑞士CIBA-Geigy公司开发的技术。
因为这种工艺类似于热塑性塑料注射成型的(小刘树脂在线转载)工艺方法,因此也称其为压力注射工艺。
它的最为显著的优点是大大提高了浇注工效。
可以说自动压力凝胶技术的开发成功及在工业上的大量应用,是真空浇注由间歇、手工操作向自动化生产发展的一场革命,它和真空浇注的主要区别在于:⑴浇注材料是在外界压力下通过管道由注入口注入模具。
⑵物料的混料处理温度低,模具温度高。
⑶物料进入模具后,固化速度快,通常为十几分钟至几十分钟。
环氧树脂注浆液施工工艺流程

环氧树脂注浆液施工工艺流程英文回答:The construction process of epoxy resin grouting slurry typically involves the following steps:1. Surface Preparation: The surface to be grouted should be clean, free from dust, grease, and loose particles. Any cracks or voids should be repaired and sealed properly.2. Mixing the Epoxy Resin: The epoxy resin is typically supplied as a two-component system, consisting of a resin and a hardener. These two components are mixed together in the correct ratio according to the manufacturer's instructions. It is important to ensure thorough mixing to achieve a uniform consistency.3. Injection: The mixed epoxy resin is injected into the prepared cavities or cracks using a suitable injectionmethod. This can be done either manually or with the helpof injection pumps. The injection should start from the lowest point and progress upwards to ensure completefilling of the voids.4. Curing: After injection, the epoxy resin requires sufficient time to cure and harden. The curing time canvary depending on the specific product used and the ambient conditions. It is important to follow the manufacturer's recommendations for curing time and temperature.5. Finishing: Once the epoxy resin has cured, anyexcess material can be removed by grinding or sanding. The surface can then be finished as required, such as bypainting or applying a protective coating.环氧树脂注浆液施工工艺流程通常包括以下步骤:1. 表面处理,待注浆的表面应清洁,无尘、无油脂和松散颗粒。
微电机环氧树脂真空浇注工艺过程及注意事项

微电机环氧树脂真空浇注工艺过程及注意事项微电机环氧树脂真空浇注工艺是一种常用的封装方式,具有优异的性能和可靠性,但在操作过程中需要注意一些细节问题。
首先,准备工作要做好。
包括环氧树脂、硬化剂、填充材料、真空设备等。
环氧树脂选择要考虑其耐高温、耐腐蚀、粘度等因素;硬化剂的配比要准确,否则会影响固化速度和性能;填充材料要选择与环氧树脂相容性良好的材料。
其次,要注意真空设备的选择和使用。
真空泵的性能对于环氧树脂浇注的质量和效率有很大影响,应选择性能稳定、抽真空速度快的设备,并且进行适当维护和保养。
在使用过程中,要注意操作规程,保持设备清洁干燥,避免污染环氧树脂。
最后,环氧树脂浇注过程中也需要注意一些技巧。
如要控制浇注速度和浇注量,避免气泡和缺陷的产生;要注意环氧树脂在浇注过程中的温度控制,避免过热或过冷导致固化不良;在浇注后的固化过程中,要注意温度、湿度等条件的控制,以保证环氧树脂的性能和可靠性。
总之,微电机环氧树脂真空浇注工艺需要严格控制各个环节,注意细节问题,才能保证浇注质量和产品性能。
- 1 -。
- 1、下载文档前请自行甄别文档内容的完整性,平台不提供额外的编辑、内容补充、找答案等附加服务。
- 2、"仅部分预览"的文档,不可在线预览部分如存在完整性等问题,可反馈申请退款(可完整预览的文档不适用该条件!)。
- 3、如文档侵犯您的权益,请联系客服反馈,我们会尽快为您处理(人工客服工作时间:9:00-18:30)。
环氧树脂浇注工艺
环氧树脂浇注工艺 1 线圈干燥。
1.1将装配好浇注模具的线圈均匀放置在专用小车上推入烘炉。
1.2烘炉加热:温度105℃保温时间6小时。
1.3 将预加热过的线圈用小车推入真空浇注
罐。
1.4 将各浇注分接管的软管适当分布放在线圈的上端(局放要求高时不适合此法)高压线圈要求放在面板处绑紧固定。
1.5 浇注罐加热设置为80℃模具70℃。
值(3000Pa)再启动罗茨泵继续抽真空至100~300 Pa在该真空下保持1~2小时。
2 单组分备料。
将A/B组分别放入烘箱中预热设置温度在70℃时间以浇注料实际温度达到设定的温度为准一般2小时以上以利于浇注料抽取。
3 混合料备料。
3.1 混合料罐加热温度设置60℃。
3.2 按生产需要用量将环氧树脂和固化剂按重量比例抽入到混合料罐次序为先抽A料再抽B料。
3.3 启动混合料罐搅拌电机。
3.
4 开启备料真空系统真空控制在100~200 Pa。
混合料重量少于200 kg抽真空搅拌时间控制在1~1.5小
时。
混合料重量大于200 kg抽真空搅拌时间控制在1.5~2小时。
4 线圈浇注。
4.1 确保线圈干燥及混合料脱气完成后才可对线圈进行浇注。
4.2打开气动下料阀再分别打开相应手动浇注阀对各线圈进行浇注树脂浇注高度以略高于模具溢流口为宜。
4.3 浇注时间视线圈大小而定从开始进料到线圈注满时间控制在1小时。
小容量线圈导线之间间隙小树脂难渗透浇注时可分段下料。
大容量线圈可连续下料但要控制下料速度。
4.4 浇注过程注意观察各线圈模具的密封情况。
如出现模具泄漏该线圈要暂停浇
注。
4.5 全部线圈注满后继续抽真空静置20分钟再破去浇注罐真空。
然后充气加压到2公斤观察各线圈树脂面下降情况。
对树脂下降到低于模具溢流口的线圈进行补注树脂(视情况看是否再抽真空)。
打开浇注罐门将小车拉出罐
外。
5 管道清洗。
5.1 将混合料罐和下料管道中的剩料放干净。
5.2 用专用清洗剂清洗混合料罐和下料管道。
清洗时要先清洗混合料罐的搅拌装置。
清洗管道时要反复二至三次开、闭各阀门以达到更好的清洗效
果。
6 线圈固化。
6.1把小车转移到固化烘炉内观察模具摆放情况要求确保模具放置水平固化后的浇注体上、下端面才能平整。
6.2 凿__住模具溢流口的玻璃胶
并用杯子接住多余流出的树脂。
树脂高度低于模具溢流口的线圈要补加树脂。
6.3固化的温度、时间按如下固化曲线进
行:①80℃6小时(其中3小时后观测补
料)②100℃4小时③130℃,6小时④降温至100℃保温1小时后拆模线圈完全冷却后打磨。