点焊焊接质量的评判标准
焊接质量评定标准

焊接质量评定标准
焊接质量评定标准是根据焊接作业的要求制定的一套评定标准,用于评定焊接工艺的合格性和焊缝的质量。
焊接质量评定标准一般包括以下几个方面:
1. 焊接工艺评定标准:用于评定焊接工艺的合格性,包括焊接方法、焊接材料、焊接参数等方面的要求。
2. 焊工资格评定标准:用于评定焊工的技能水平和资格合格性,包括焊工的培训、考核和认证等方面的要求。
3. 焊接检验评定标准:用于评定焊缝的质量,包括焊缝的外观、尺寸、力学性能、化学成分等方面的要求。
4. 焊接缺陷评定标准:用于评定焊缝中可能存在的缺陷,如气孔、夹渣、裂纹等,以及这些缺陷的容许范围和评定方法。
5. 焊接质量评定标准:用于评定焊接作业整体质量,包括焊接过程控制、设备维护、操作规范等方面的要求。
这些标准旨在确保焊接作业的安全可靠,焊缝的质量符合要求,以及提高焊接工艺的一致性和可重复性。
具体标准的制定和适用范围会根据不同的行业和应用领域而有所差异。
焊接质量检验标准

焊接质量检验标准焊接在电子产品装配过程中是一项很重要的技术,也是制造电子产品的重要环节之一。
它在电子产品实验、调试、生产中应用非常广泛,而且工作量相当大,焊接质量的好坏,将直接影响到产品的质量。
电子产品的故障除元器件的原因外,大多数是由于焊接质量不佳而造成的。
因此,掌握熟练的焊接操作技能对产品质量是非常有必要的。
(一)焊点的质量要求:对焊点的质量要求,应该包括电气接触良好、机械接触牢固和外表美观三个方面,保证焊点质量最关键的一点,就是必须避免虚焊。
1.可靠的电气连接焊接是电子线路从物理上实现电气连接的主要手段。
锡焊连接不是靠压力而是靠焊接过程形成牢固连接的合金层达到电气连接的目的。
如果焊锡仅仅是堆在焊件的表面或只有少部分形成合金层,也许在最初的测试和工作中不易发现焊点存在的问题,这种焊点在短期内也能通过电流,但随着条件的改变和时间的推移,接触层氧化,脱离出现了,电路产生时通时断或者干脆不工作,而这时观察焊点外表,依然连接良好,这是电子仪器使用中最头疼的问题,也是产品制造中必须十分重视的问题。
2.足够机械强度焊接不仅起到电气连接的作用,同时也是固定元器件,保证机械连接的手段。
为保证被焊件在受振动或冲击时不至脱落、松动,因此,要求焊点有足够的机械强度。
一般可采用把被焊元器件的引线端子打弯后再焊接的方法。
作为焊锡材料的铅锡合金,本身强度是比较低的,常用铅锡焊料抗拉强度约为3-4.7kg/cm 2,只有普通钢材的10%。
要想增加强度,就要有足够的连接面积。
如果是虚焊点,焊料仅仅堆在焊盘上,那就更谈不上强度了。
3.光洁整齐的外观良好的焊点要求焊料用量恰到好处,外表有金属光泽,无拉尖、桥接等现象,并且不伤及导线的绝缘层及相邻元件良好的外表是焊接质量的反映,注意:表面有金属光泽是焊接温度合适、生成合金层的标志,这不仅仅是外表美观的要求。
典型焊点的外观如图1所示,其共同特点是:① 外形以焊接导线为中心,匀称成裙形拉开。
焊接质量检验标准.

XX 机械制造有限公司
焊接质量检验标准
1.目的
通过正确定义焊接质量的检验标准,保证员工在焊接、检验过程中制造出合格的产品。
2.范围
适用于焊接车间。
3.工作程序
焊接质量标准根据生产制造现场工艺实际情况,可采用边界样本目视化来清楚地分辨出焊接质量是否符合要求。
3.1电阻点焊焊点不合格质量的界定和CO 2气体保护焊焊点、焊缝不合格质量的界定。
3.1.1以下8 种电阻焊点被认为是不可接受的,界定为不合格质量: 3.1.1.1虚焊(无熔核或者熔核的尺寸小于4mm )焊点,代号为L 。
3.1.1.2沿着焊点周围有裂纹的焊点,代号为C 。
3.1.1.3烧穿,代号为B 。
3.1.1.4
3.1.1.5
3.1.1.6钢板变形超过25度的焊点,代号为D
3.1.1.7压痕过深的焊点(材料厚度减少50%),代号为I 。
3.1.1.8漏焊,代号为M 。
3.1.2以下10种CO 2气体保护焊焊点、焊缝被认为是不可接受的,界定为不合格质量: 3.1.2.2焊缝金属裂纹;
3.1.2.2夹杂(焊缝中夹杂着除母材和焊丝外的物质或氧化物); 3.1.2.3气孔(焊逢中产生气孔); 3.1.2.4咬边;
缺陷B :烧穿
3.1.2.5未熔合;
3.1.2.9飞溅。
飞溅,焊缝堆积过高,焊缝不连续
3.1.3
以下4个凸点焊螺母的焊接质量是3个是可接受的,
1个是不可接受的。
焊接评定标准

焊接评定标准焊接评定标准是指用于评定焊接工艺和焊接人员的技能和能力是否符合特定要求的标准体系。
这些评定标准通常由国家或行业组织制定,旨在确保焊接工艺和焊接人员的质量和安全性。
下面是一些与焊接评定标准相关的参考内容:1. 焊接规范和要求:焊接评定标准应基于特定行业或国家的焊接规范和要求。
这些规范和要求包括焊接材料的质量和规格、焊接参数的控制、检测和检验要求等。
参考内容可以包括焊接规范的摘要、焊接参数的范围和限制等。
2. 非破坏性检测(NDT)标准:焊接评定涉及到对焊接接头的质量进行评估,其中非破坏性检测是一种常用方法。
相关参考内容可以包括NDT技术的原理和应用、不同NDT方法的优缺点、NDT参数的控制要求等。
3. 焊接工艺标准:焊接评定还涉及对焊接工艺的评估。
相关参考内容可以包括焊接工艺规范的要求和说明、焊接工艺参数的选取和控制、焊接工艺评价的方法和指标等。
4. 焊接质量标准:焊接评定通常还涉及对焊接质量的评估。
相关参考内容可以包括焊缝质量的要求和标准、焊缝检测方法和评定标准、焊缝缺陷的分类和修复要求等。
5. 检验和认证要求:焊接评定还可能涉及对焊接人员和焊接过程的检验和认证。
相关参考内容可以包括焊接人员的培训和认证要求、焊接设备和材料的检验和认证要求、焊接过程的监督和评估方法等。
6. 安全和环保要求:焊接评定标准还应考虑焊接过程的安全和环保要求。
相关参考内容可以包括焊接过程中的安全措施和防护要求、焊接废气和废水的处理方法和要求、焊接设备和材料的安全性评价等。
总结起来,焊接评定标准的参考内容应包括焊接规范和要求、非破坏性检测标准、焊接工艺标准、焊接质量标准、检验和认证要求,以及安全和环保要求等。
这些参考内容将有助于评定焊接工艺和焊接人员是否符合特定要求,从而确保焊接质量和安全性。
焊接质量检验方法和标准

焊接质量检验方法和标准1目的规定焊接产品的表面质量、焊接质量、确保产品满足客户的要求,适用范围:适用于焊接产品的质量认可.2责任生产部门,品质部门可参照本准则对焊接产品进行检验.一、熔化极焊接表面质量检验方法和标准CO2保护焊的表面质量评价主要是对焊缝外观的评价,看是否焊缝均匀,是否有假焊、飞溅、焊渣、裂纹、烧穿、缩孔、咬边等缺陷,以及焊缝的数量、长度以及位置是否符合工艺要求,具体评价标准详见下表二、焊缝质量标准保证项目1、焊接材料应符合设计要求和有关标准的规定,应检查质量证明书及烘焙记录。
2、焊工必须经考核合格,检查焊工相应施焊条件的合格证及考核日期.3、I 、II级焊缝必须经探伤检验,并应符合设计要求和施工及验收规范的规定,检验焊缝探伤报告焊缝表面I、II级焊缝不得有裂纹、焊瘤、烧穿、弧坑等缺陷.II 级焊缝不得有表面气孔夹渣、弧坑、裂纹、电焊擦伤等缺陷,且I级焊缝不得有咬边,未焊满等缺陷基本项目焊缝外观:焊缝外形均匀,焊道与焊道、焊道与基本金属之间过渡平滑,焊渣和飞溅物清除干净。
表面气孔:I、II级焊缝不允许;III级焊缝每50MM长度焊缝内允许直径≤0。
4t;气孔2个,气孔间距≤6倍孔径咬边:I级焊缝不允许。
II级焊缝:咬边深度≤0.05t,且≤0.5mm,连续长度≤100mm,且两侧咬边总长≤10%焊缝长度。
III级焊缝:咬边深度≤0。
1t,,且≤1mm。
注:,t为连接处较薄的板厚。
三、焊缝外观质量应符合下列规定1一级焊缝不得存在未焊满、根部收缩、咬边和接头不良等缺陷,一级和二级焊缝不得存在表面气孔、夹渣、裂纹、和电弧擦伤等缺陷2二级焊缝的外观质量除应符合本条第一款的要求外,,尚应满足下表的有关规定3 三级焊缝应符合下表有关规定焊缝质量等级检测项目二级三级未焊满≤0.2+0.02t 且≤1mm,每100mm 长度焊缝内未焊满累积长度≤25mm≤0.2+0.04t 且≤2mm,每100mm 长度焊缝内未焊满累积长度≤25mm根部收缩≤0.2+0.02t 且≤1mm,长度不限≤0.2+0.04t 且≤2mm,长度不限咬边≤0.05t 且≤0.5mm,连续长度≤100mm,且焊缝两侧咬边总长≤10%焊缝全长≤0.1t 且≤1mm,长度不限裂纹不允许允许存在长度≤5mm 的弧坑裂纹电弧擦伤不允许允许存在个别电弧擦伤接头不良缺口深度≤0.05t 且≤0.5mm,每1000mm 长度焊缝内不得超过1 处缺口深度≤0.1t 且≤1mm,每1000mm 长度焊缝内不得超过1 处表面气孔不允许每50mm 长度焊缝内允许存在直径≤0.4t 且≤3mm 的气孔2 个;孔距应≥6倍孔径表面夹渣不允许深≤0.2t,长≤0.5t 且≤20mm四、焊接质量检验中常见的缺陷名词1、焊瘤:焊接过程中溶化金属流淌到焊缝之外未溶化的母材上所形成的金属瘤2、咬边:沿焊趾的母材部位产生的沟槽和凹陷。
《焊接检验准则》word版

1 目的规定焊接产品表面质量、配合、焊接质量、扭矩的检验准则,确保产品满足顾客的要求。
2 适用范围适用于焊接产品的质量认可。
3 定义无4 责任生产部门、质量保证部负责按照本准则对焊接产品进行检验。
5 规定5.1 焊接产品检验区域划分。
5.2 焊接产品焊接表面质量的检验方法和标准5.2.1点焊表面质量检验方法和标准5.2.1.1 点焊缺陷数量的评价见下表1(当规定点焊数量是5个或更少时,不允许出现缺陷点焊,然而当焊点数量大于等于6个时,设计中应根据表1允许有一定的焊点缺陷。
)表1最小有效焊点数设计图中规定的焊点数最小的有效焊点数最大应用焊点数1-5n n6-10n-1n+111-20n-2n+221-30n-3n+331-40n-4n+441+n-12%n+12%n为工程设计图中规定的实际焊点数;焊点数为一次点焊工序中必须的数量。
5.2.1.2点焊质量评价见下表缺陷名称缺陷说明评定结论图示漏焊少于工艺要求的焊点数量不允许,必须返工(按原工艺要求补焊)无烧穿焊点表面有穿孔现象不允许,必须返工(在不影响表面质量的情况下按原工艺返工,或选择其他补焊方式,如锡补、CO2补等)位置半点焊不允许,超过要求焊点数的10%时必须返工(按原工艺要求补焊)焊点间距不均匀具体评价见5.2.1.3飞溅焊点边毛刺、凸起等焊接产品可见部分不允许有焊接飞溅;其它不可见部分允许有轻微焊接飞溅,但不能破坏螺纹,不能影响下道工序略凹陷焊点压痕太深具体评价见5.3.2.3倾斜/不平整压痕形状不均匀造成母材倾斜、不平整倾斜角度大于30°不允许,必须返工板材厚度比t v0.5-0.6>0.6-0.8>0.8-1.0>1.0-1.1>1.1-1.2>1.2-1.5最小点距e101215181824最小边缘距离V5 5.5 6.5778板材厚度比t v>1.6-2.0>2.0-2.5>2.5-3.0>3.0-3.5>3.5-3.8>3.8-4.0最小点距e273645546363最小边缘距离V910111213132CO2保护焊的表面质量评价主要是对焊缝外观的评价,看是否焊缝均匀,是否有假焊、飞溅、焊渣、裂纹、焊穿、缩孔、咬边等缺陷,以及焊缝的数量、长度及位置是否符合工艺要求。
焊接质量检验标准.

XX机械制造有限公司焊接质量检验标准1.目的通过正确定义焊接质量的检验标准,保证员工在焊接、检验过程中制造出合格的产品。
2.范围适用于焊接车间。
3.工作程序焊接质量标准根据生产制造现场工艺实际情况,可采用边界样本目视化来清楚地分辨出焊接质量是否符合要求。
3.1电阻点焊焊点不合格质量的界定和CO2气体保护焊焊点、焊缝不合格质量的界定。
3.1.1以下8 种电阻焊点被认为是不可接受的,界定为不合格质量:3.1.1.1虚焊(无熔核或者熔核的尺寸小于4mm)焊点,代号为L。
3.1.1.2沿着焊点周围有裂纹的焊点,代号为C。
3.1.1.3烧穿,代号为B。
缺陷B:烧穿3.1.1.4边缘焊点(不包括钢板所有边缘部分的焊点),代号为E。
缺陷E:焊点E、F为边缘焊点,不3.1.1.5位置偏差的焊点(与标准焊点位置的距离超过10mm),代号P。
3.1.1.6钢板变形超过25度的焊点,代号为D。
3.1.1.7压痕过深的焊点(材料厚度减少50%),代号为I。
3.1.1.8漏焊,代号为M。
3.1.2以下10种CO2气体保护焊焊点、焊缝被认为是不可接受的,界定为不合格质量: 3.1.2.2焊缝金属裂纹;3.1.2.2夹杂(焊缝中夹杂着除母材和焊丝外的物质或氧化物);3.1.2.3气孔(焊逢中产生气孔);3.1.2.4咬边;3.1.2.5未熔合;缺陷D:钢板变形α大于25度的焊缺陷I:压痕过深焊点I,压痕深度≥板材厚咬边:焊逢偏向一母材,与另一母材熔合过少,未能达到要求的3.1.2.6未焊透;3.1.2.7熔透过大;3.1.2.8蛇形焊道;未熔合:填充金属填充极少,导致焊缝与母材间未熔合未焊透:填充金属未能完全填充,导致焊缝与母材间未焊透熔透过大:焊缝高度小于准备要求,严重的导致烧穿蛇形焊道:焊缝弯曲,形状象蛇3.1.2.9飞溅。
3.12.10飞溅,焊缝堆积过高,焊缝不连续3.1.3以下4个凸点焊螺母的焊接质量是3个是可接受的,1个是不可接受的。
焊接质量判定标准

一、以下
8 种焊点被认为是不可接受的:
1. 虚焊(无溶核或者溶核的尺寸小于4mm )焊点,代号为L 2. 沿着焊点周围有裂纹的焊点,代号为C 3. 烧穿,代号为B
4. 边缘焊点(不包括钢板所有边缘部分的焊点),代号为E 5. 位置偏差的焊点(与标准焊点位置的距离超过10mm ),代号P 6. 钢板变形超过25度的焊点,代号为D
7. 压痕过深的焊点(材料厚度减少50%),代号为I 8. 漏焊,代号为M
二、以下焊缝被认为是不可接受的:
1.焊缝偏离焊接位置
2.气泡、夹渣
直径大于1.5mm 的气孔或
渣;每10mm 长的
焊缝内总长大1.5mm 、个数超过3的气孔或夹渣
3.弧坑
弧坑长度L>5mm
4.咬边
深度H>0.5mm ,两侧
咬边总长超过15%设计要求
5.焊肉不足
深度H>δ25% 或1mm
6.余高太大
余高h>3mm
7. 未焊透
深度h>δ15%
8.
焊缝长度超过或短于设计要求长度的10%
9.烧穿 10.漏焊。
电阻点焊质量判定标准
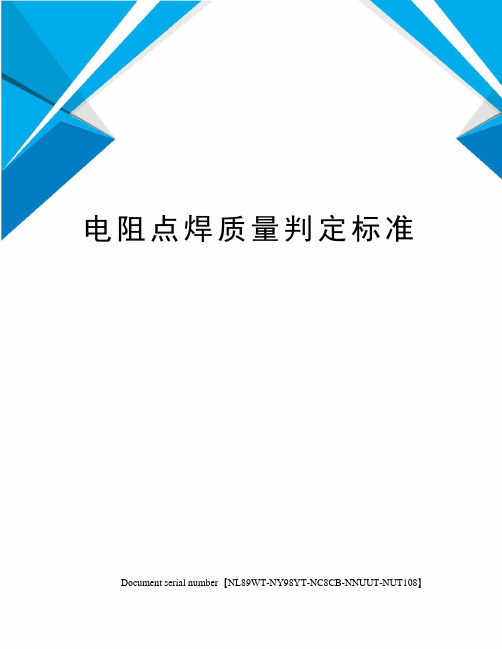
1.2.2撕裂点是指在破坏性实验中被拉出来的部分,包括全部或部分核心,撕裂点的平均直径是取两轴的直径平均值,在结合面处测得的。
1.2.3在某些特定钢板或载荷类型下,不一定会有撕裂点被拉出来。这种情况下,须采用熔化区域冶金实验以确定焊点是否合格。
裂纹:围绕焊点圆周有裂纹是不可接受的。但焊点表面由电极加压产生的有限的表面裂纹是可接受的。
2.3.2如果焊接图纸上没有要求,则采用上表数值。
2.3.3在同一类型内,二个或多个相邻焊点漏焊或破坏将导致不合格。
附件:电阻点焊的八种典型缺陷。
拟订: 校对: 审核: 批准:
扭曲:当钢板变形超过25度时,其上的焊点必须通过焊接工艺调整以降低扭曲,直至小于25度。
压痕过深:由于电极压力造成单层钢板厚度减多焊点:焊点数不得多于焊接图纸上所规定的数量,除非由于修补所要求的焊点增加。应改进焊接工艺以减少焊点数。
2排列焊点质量判定标准
电阻点焊质量判定标准
电阻点焊质量判定标准
1单一焊点质量判定标准
焊点按下列标准评判
1.1.1结构焊点按照、、、、、、、、的要求评判。结构焊点是指那些影响产品性能的焊点。所有焊点都是结构焊点,除非焊接图纸上有工艺焊点的特别说明。所有结构焊点都必须指定其焊点类型。
1.1.2工艺焊点按照、、、的要求评判。工艺焊点是指那些使产品便于在工艺上进行组合的焊点,没有结构性能上的要求。工艺焊点必须得到产品工程部门的批准并在焊接图纸上说明。
焊点类型一致性要求
2.3.1如果在一个焊点类型内合格的焊点数达到或超过下表所示值,或者符合焊接图纸上的要求并且的情况不存在,则该类型是合格的。
排列焊点判定
类 型
可接受焊点数
焊接质量检验标准

XX机械制造有限公司
焊接质量检验标准
1. 目的
通过正确定义焊接质量的检验标准,保证员工在焊接、检验过程中制造出合格的产品。
2. 范围
适用于焊接车间。
3. 工作程序
焊接质量标准根据生产制造现场工艺实际情况,可采用边界样本目视化来清楚地分辨出焊接质量是否
符合要求。
3.1电阻点焊焊点不合格质量的界定和CO气体保护焊焊点、焊缝不合格质量的界定。
3.1.1以下8种电阻焊点被认为是不可接受的,界定为不合格质量:
3.1.1.1虚焊(无熔核或者熔核的尺寸小于4mr)焊点,代号为L。
3.1.1.2 沿着焊点周围有裂纹的焊点,代号为C o
3.1.1.3烧穿,代号为B。
缺陷B :烧穿
3.1.1.4 边缘焊点(不包括钢板所有边缘部分的焊点),代号为巳
4应严缺陷E:焊点E、
F为边缘焊点,不
3.1.1.5 位置偏差的焊点(与标准焊点位置的距离超过10mm,代号P o
3.1.1.8
漏焊,代号为M 3.1.2以下10种CO 气体保护焊焊点、焊缝被认为是不可接受的,界定为不合格质量
3.122 焊缝金属裂纹;
3.122 夹杂(焊缝中夹杂着除母材和焊丝外的物质或氧化物
); I F 电母材熔合过少,未能达到要求的
(A/B) $50%或(C/D) $50%
缺陷I:压痕过深焊点
I ,压痕深度》板材厚
3.1.1.7 压痕过深的焊点(材料厚度减少 50%,代号为I 。
3.1.2.5 未熔合;。
焊接质量评定标准

焊接质量评定标准一、引言焊接作为一种重要的金属连接方式,在工业生产和制造中得到广泛应用。
为确保焊接质量和连接的强度,制定适当的焊接质量评定标准是十分必要的。
本文旨在探讨焊接质量评定的标准和要点,以指导相关行业在焊接过程中提高质量和效率。
二、焊接质量评定标准的概述焊接质量评定标准是判断焊接工艺和焊接接头是否满足要求的依据。
一个合格的焊接工艺应该满足以下几个方面:1. 焊接强度:焊缝应具备足够的强度,能够承受预期的载荷;2. 焊接质量:焊缝应具备良好的密封性和韧性,以防止漏气和显著的变形;3. 焊接外观:焊接表面应平整光滑,无显著的焊接缺陷和瑕疵。
三、焊接质量评定标准的要点为了确定焊接质量评定标准的要点,需要考虑以下几个关键因素:1. 焊接材料:不同种类的焊接材料对焊接质量有着不同的要求。
选择适当的焊接材料非常重要,以确保焊缝的强度和质量。
2. 焊接工艺:不同的焊接工艺,如电弧焊、气体保护焊等,对焊缝的质量和强度有着直接影响。
制定适当的焊接工艺参数和操作规范,能够有效提高焊接质量。
3. 焊接缺陷:焊接过程中常常会出现一些焊接缺陷,如气孔、裂纹、未焊透等。
评定焊接质量的标准应该能够识别和判定这些常见缺陷,并给出相应的处理方法。
4. 检测方法:为了评定焊接质量,需要使用合适的检测方法,如X射线检测、超声波检测等。
这些方法能够有效地检测焊接缺陷和确定焊接质量是否符合标准。
四、焊接质量评定标准的应用案例下面通过一个案例来具体说明焊接质量评定标准的应用。
案例:某汽车零部件的焊接质量评定在汽车制造过程中,焊接质量对零部件的耐久性和安全性有着重要作用。
为了评定某汽车零部件的焊接质量,可以采用以下标准进行评定:1. 外观检查:对焊接表面进行检查,确认焊缝无明显的气孔、裂纹和未焊透等缺陷,并且焊缝平整光滑。
2. 强度测试:对焊接接头进行拉伸测试,以确定焊缝的强度和可靠性。
测试结果应满足设计要求和行业标准。
3. 金相分析:对焊缝进行金相分析,以确认焊接过程是否存在材料的脱落或异常现象。
焊接质量检验标准
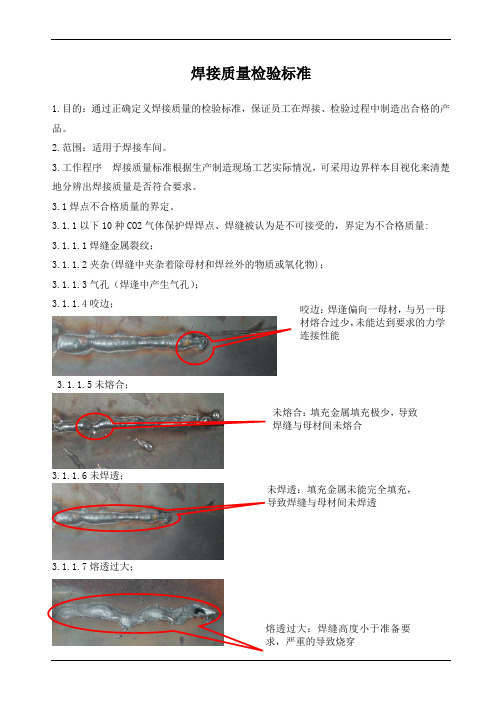
焊接质量检验标准1.目的:通过正确定义焊接质量的检验标准,保证员工在焊接、检验过程中制造出合格的产品。
2.范围:适用于焊接车间。
3.工作程序焊接质量标准根据生产制造现场工艺实际情况,可采用边界样本目视化来清楚地分辨出焊接质量是否符合要求。
3.1焊点不合格质量的界定。
3.1.1以下10种CO2气体保护焊焊点、焊缝被认为是不可接受的,界定为不合格质量: 3.1.1.1焊缝金属裂纹;3.1.1.2夹杂(焊缝中夹杂着除母材和焊丝外的物质或氧化物);3.1.1.3气孔(焊逢中产生气孔);3.1.1.4咬边;3.1.1.5未熔合;3.1.1.6未焊透;3.1.1.7熔透过大;咬边:焊逢偏向一母材,与另一母材熔合过少,未能达到要求的力学连接性能未熔合:填充金属填充极少,导致焊缝与母材间未熔合未焊透:填充金属未能完全填充,导致焊缝与母材间未焊透熔透过大:焊缝高度小于准备要求,严重的导致烧穿3.1.1.8蛇形焊道;3.1.2.9飞溅。
3.12.10飞溅,焊缝堆积过高,焊缝不连续4.钣金焊接4.1 焊接质量 4.1.1焊点、焊缝应尽量置于对外观无影响的位置,且焊点布局应尽量匀称,大小适中,不能出现表面烧穿,擦伤等缺陷。
不能明显出现焊道不平整或弯曲、焊接喉部厚度不均匀、多余部分不均匀、焊角长度不均匀和漏焊等情况。
4.1.2焊接后工件表面应无明显的凹凸变形和影响产品外观又不可纠正的扭曲变形。
4.1.3布于主要外观表面及拼角位的焊缝应满焊,便于打磨处理。
不能打磨处理的次要外观表面及拼角位的焊缝,焊点应尽量平顺均匀。
4.2 精加工状态 必须充分除净焊渣和飞溅物。
不能有划手的感觉。
4.3 母材不能明显出现膨胀、凹扁和拉伸的情况。
4.4焊接应牢固、可靠,适应各构件的力度要求。
不能出现假焊、虚焊和焊点松脱裂纹 5 焊接缺陷 在标准文件中规定焊接缺陷检验标准,如文件无特殊要求,焊接缺陷不得超过下表Ⅲ级。
蛇形焊道:焊缝弯曲,形状象蛇飞溅:焊接过程中焊丝飞到焊缝外粘在母材表面的物质飞溅,焊缝堆积过高,焊缝不连续。
焊接质量检测标准
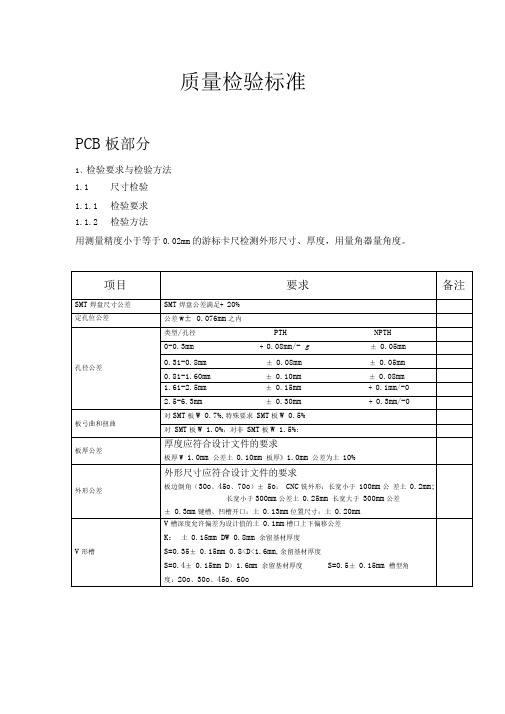
质量检验标准PCB板部分1、检验要求与检验方法1.1尺寸检验1.1.1检验要求1.1.2检验方法用测量精度小于等于0.02mm的游标卡尺检测外形尺寸、厚度,用量角器量角度。
1.2外观检验1.2.1 检验要求2.在填写各工序质量报表时,应选用此文件所注明的缺陷项目表,作为记录相应缺陷的依据,如果出现缺陷项目表中未有注明之缺陷,应在质量报表下面之备注栏填写缺陷名称。
3.对于不合格产品有缺陷处标记(用小红标贴标记),在检验报表上相应的缺陷栏记录好,不合格品应同合格品分开,以免与合格品混淆。
4.所有不合格产品均要退回相应的生产工序返修(或返工) ,对于特殊情况的机板,如起铜皮、PCB录油脱落、绿油起泡、PCB补线、线路上锡、PCB补油、PCB起泡等机板,则根据公司的实际情况进行分类,并单独处理。
5.ESD防护:凡接触PCBA半成品必需配带良好静电防护措施(一般配带防静电手环接上静电接地线或带防静电手套)。
一、焊前检查(1)每天上班前3-5分钟把电烙铁插头插入规定的插座上,检查烙铁是否发热,如发觉不热,先检查插座是否插好,如插好,若还不发热,应立即向管理员汇报,不能自随意拆开烙铁,更不能用手直接接触烙铁头•(2)已经氧化凹凸不平的或带钩的烙铁头应更新的:1、可以保证良好的热传导效果;2、保证被焊接物的品质。
如果换上新的烙铁嘴,受热后应将保养漆擦掉,立即加上锡保养。
烙铁的清洗要在焊锡作业前实施,如果5分钟以上不使用烙铁,需关闭电源。
海绵要清洗干净不干净的海绵中含有金属颗粒,或含硫的海绵都会损坏烙铁头。
(3)检查吸锡海绵是否有水和清洁,若没水,请加入适量的水(适量是指把海绵按到常态的一半厚时有水渗出,具体操作为:湿度要求海绵全部湿润后,握在手掌心,五指自然合拢即可),海绵要清洗干净,不干净的海绵中含有金属颗粒,或含硫的海绵都会损坏烙铁头。
二、操作要求1.0焊接过程中,一些元件的温度控制:(1)无铅SMD元件1)普通元件如0603, 0805, 3216的元件,电烙鉄温度的范围:330C± 20C。
- 1、下载文档前请自行甄别文档内容的完整性,平台不提供额外的编辑、内容补充、找答案等附加服务。
- 2、"仅部分预览"的文档,不可在线预览部分如存在完整性等问题,可反馈申请退款(可完整预览的文档不适用该条件!)。
- 3、如文档侵犯您的权益,请联系客服反馈,我们会尽快为您处理(人工客服工作时间:9:00-18:30)。
1
2
电流线 板表面凸点 加热区
点焊过程示意图
3
4
5
加热区 熔化区 塑性环
点焊过程示意图
二、 点焊焊接质量的评判标准
GM4488M
GM4488M
1 范围 本说明提供了汽车点焊认可标准,用于由 GM 负责的产品设计的建立或认可. 1.1 本说明中各项要求的执行是强制性的,除非在焊接图纸上另有不同的特定的焊点要求说 明.任何不同于 GM4488 要求的例外都必须与可靠的工程实践经验相一致. 1.2 某些特定焊点或一组同类型焊点指定的关键产品特性也许有超出本说明的产品要求. 1.3 当焊接结构在预期的时间内承受了预期的载荷 ,那么它才被认为是合格的 .车身焊件的 承载量由于其形式和大小的不同而不同,无法在本说明内详述;因此,本说明中涉及的承载要求焊 接质量标准是特别建立的,仅用于工艺及产品的检验.任何将此文件用于其它用途,如事故后焊接 质量评估,将导致错误的结论. 1.4 不符合本说明标准的焊点将被判为不合格 .不合格的焊点由于保留了部分工程特性 ,也 许仍能在保持各部分的完整性上起作用. 1.5 焊接部门将负责建立检验措施以保证本说明及 GM9621P 的贯彻实施. 2 参考标准 GM1000M,GM4491M,GM9621P,GM1805QN,GM6122M
用溶化区域冶金实验以确定焊点是否合格. 4.3 裂纹.周围有裂纹的焊点是不合格的.焊点表面由于电极压下而留下的有限裂纹被认为 是合格的. 4.4 气孔.贯穿于焊点的气孔是不合格的. 4.5 漏焊.当焊点数少于要求的数量时,此漏焊是不合格的. 4.6 边缘焊点.由于电极的限制,在点焊区域内,没有包括钢板所有边缘部分的焊点是不合格 的.(图 3) 4.7 位置公差.对于位置确定的焊点,若焊点离该位置大于 10mm,此焊点不合格.对于位置不 确定的焊点,若焊点离该位置大于 20 mm,此焊点不合格. 4.8 变形.当钢板变形达 25 度时,其上的焊点必须通过焊接工艺调整以降低变形直至小于 25 度.(图 4) 4.9 收缩.由于电极压力造成单层钢板厚度减少达 50%时(图 5),须通过焊接工艺调整以减少 钢板收缩> 4.10 增加焊点.焊点数不得多于焊接图纸上所规定的数量,除非如第 10 条中所述的由于修补 所要求的焊点增加.应改进焊接工艺以减少焊点数.
3 要求 3.1 化学品限制及管制(GM1000M).所有用于本说明的化学材料都必须符合 GM1000M 条 款. 3.2 点焊分类.有两种点焊,结构的和工艺的. 3.2.1 结构点焊. 结构点焊是指那些影响产品性能的点焊 .所有点焊都是结构点焊,除非 焊接图纸上有工艺焊点的特别说明.所有结构焊点都必须指定其点焊类型. 3.2.2 工艺点焊. 工艺点焊是指那些使产品便于在工艺上进行组合的点焊 ,但没有结构 性能上的要求.工艺点焊必须得到产品工程部门的批准并在焊接图纸上说明. 4 单个点焊验收标准 4.1 点焊将按下列标准评估: 4.1.1,结构点焊按 4.2,4.3,4.4,4.5,4.6,4.7,4.8,4.9 和 4.10 评估. 4.1.2,工艺点焊按 4.3,4.4,4.7 和 4.10 评估. 4.2 大小.一个撕裂点或熔核的测量尺寸如大于等于表 1 所列值则该焊点是合格的,否则不合 格. 注 1:二层焊时,在参考表 1 时,用薄的钢板确定最小焊点尺寸.三层及三层以上时,用次薄的钢 板确定最小尺寸.由产品工程部在图纸上或授权修改版上确定的最小钢板厚度必须执行. 注 2:由设备设定的焊点尺寸一般大于表 1 数值,不在此说明内提供. 4.2.1 熔核大小按图 1 所示在结合面处测得. 4.2.2 撕裂点是指在破坏性实验中被拉出来的部分,包括全部或部分核心.撕裂点的平均 直径是取两轴的直径平均值(图 2),在结合面处测得. 4.2.3 在某些特定钢板或载荷类型下,不一定会有撕裂点被拉出来.在这种情况下,须采
值。
熔核尺寸过小
虛焊照片
边缘焊点
边缘焊点
虛焊产生原因: 焊接时间短;焊接压力高;焊接电流低 电极头部面积小;电极头部面积大;配 合间隙差;焊点相邻太近;焊枪接触工 件、工装(分流);焊点接近板材边缘; 板材金属特性;焊接角度不垂直。 生产中注意问题:1、防止分流 2、电极帽磨损及时修磨、更换
(2) 烧穿:焊点中含有穿透所有板材
3、点焊接头的形成
点焊接头是在热-机械(力)联合作用下 形成的。电阻热是建立焊接温度场、促进焊 接区塑性变形和获得优质连接的基本条件。
Rew Rw Rc Rw Rew R
焊接区等效电路示意图
总电阻=接触电阻+内部电阻------动态变化 R=2Rew+2Rw+Rc
Q=I2RT--------静态(平均值) Q=∫0t i(t)2r(t)dt---动态(瞬时值) 由于电流、电阻是动态变化的,随焊接(加热) 过程的进行而变化(交流电、板材在不同温度电阻不 同)
8.2 一级焊点打磨.这一级别适用于钢板表面不能有任何标记 ,凹陷或不完美的地方,这样在油漆 后就不会有任何痕迹.这通常用于汽车外表面可视部分.这一级别一般不用于 GM-PCP 焊点类型. 表面打磨一般要达到这一要求. 8.3 二级焊点打磨.这一级别是指那些表面允许有很小痕迹的工件 ,通常用于整车上不经常 被看见的部分,或有些痕迹也是可接受的地方.表面打磨很少要求达到这一标准. 8.3.1 二级打磨.焊接毛刺等是不允许的.产品工程部将指定可允许的痕迹深度并由经批 准的视觉样规进行控制. 8.4 三级焊点打磨.这一级别适用于一般表面,没有特殊要求. 8.4.1 三级打磨.由于安全,外观,配合或其它原因,焊接毛刺是不允许的,必须对每一焊点 在图纸上加以说明.这就要求仅对需要打磨的地方进行打磨. 9 焊点返修要求 9.1 所有不确定类型的已知不合格焊点都必须返修. 9.2 所有已知的由 4.3,4.4 说明不合格焊点都必须返修. 9.3 除 9.1,9.2,其余焊点在有有关产品工程师评估和认可的文件基础上可被认为合格.
电极
板材
导线电流场
单块板电流场
点焊时电流场
电流场示意图
4、电阻焊的基本过程
F/I
Ffo
Fpr
基本点焊过程 1)预压
Fw
I I1
I2
2)通电加热 (焊接阶段)
t7 t8 t9 t10
t1 t2 t3 t4
t5
t6
T
3)冷却结晶 (锻压阶段)
复 杂 点 焊 焊 接 循 环 ( welding cycle) 示 意 图
点焊焊接质量的评判标准
上海江森鹤华汽车金属零部件 有限公司烟台分公司 2007.10
目录
1、电阻焊基本原理及过程 2、点焊焊接质量的评判标准 3、焊接质量控制
一、电阻焊基本原理及过程
1、焊接方法分类
熔化焊 压力焊 钎焊
电 阻 焊
扩 散 焊
摩 擦 焊
旋 弧 焊
磁 力 脉 冲 焊
超 声 波 焊
爆 炸 焊
5 焊点类型 5.1 焊点类型通常在图纸上加以说明,一个焊点类型是指将 2 个零件焊在一起的一行,一列或 一组焊点,如果改变了零件组合(如在同一行,同一列,同一组中有二层和三层组合情况),那么将被 视为不同的类型,除非这种情况将导致一个焊点形成一个类型,也许一个类型仅说明了一个结构 上的分类.如果一行,一列或一组焊点组合被另一类型焊点或无焊接区打断,则应视为二个或更多 的类型.同一类型的焊点必须由同一制造厂完成. 6 点焊分类 6.1 GM-PCP 点焊类型.必须符合 GM-PCP 要求的焊点类型是 GM-PCP 点焊类型.其适用于对 整车功能有很大影响或极易造成整车结构破坏的分总成件. 6.2 非 GM-PCP 点焊类型.不符合 GM-PCP 要求的焊点类型是非 GM-PCP 点焊类型.其适用 于对整车功能没有影响或不会造成整车结构破坏的分总成件 .主要是为了改善用户的乘坐舒适 性. 6.3 使用 GM1805QN 将产生 KPCs.受到影响的焊点和焊点类型将用适当的 KPC 标记表示
10 点焊返修工艺. 10.1 有裂纹和气孔的不合格焊点须按需先打磨,再用 GMAW 补焊.如果是不合格的同类型 焊点,则返修后必须符合第 5 条要求. 10.2 所有不合格的同类型焊点须按产品工程部指定工艺返修,或按以下工艺. 10.2.1 电阻点焊返修.所用点焊枪必须符合被焊钢板类型及厚度的要求 .补焊点必须符 合定位要求(见 4.7).每一须返修的焊点需要一个补焊点.补焊点须符合本说明的要求. 10.2.2 电弧点焊和塞焊.如果不用 10.2.1,可用电弧点焊和塞焊代替. 电弧点焊和塞焊必 须符合 GM4491M 标准.所有用这种方式返修的操作工必须定期考核并通过当地的考核程序. 10.2.3 弧焊返修.如果不用 10.2.1 方式,弧焊可用来返修两块较厚的钢板接头.弧焊必须 位于离被返修点 6mm 以内,长度至少 20 mm..弧焊必须符合 GM6122M 标准.所有用这种方式返修 的操作工必须定期考核并通过当地的考核程序. 10.3 当 10.2 所述方式不能用时,产品工程部必须指定合适的返修方法,并以符合该工厂 工艺的书面形式给出,例如螺柱连接,铆接等. 11 一般信息 本标准初定于 1985 年 4 月,更新版有(略).
影响接触电阻的因素
1、表面状态(油污、锈蚀等) 2、电极压力 3、加热温度
影响内部电阻的因素
1、边缘效应、绕流现象(电流分布不均匀,导电截面变 大,电阻减小) 2、材料的热物理性能(电阻率)、机械性能(压溃强 度)、点焊规范参数及特征(电极压力及硬、软规范)
3、焊件厚度,材质
4、受热状态、温度
电流线
7 点焊类型一致性要求. 7.1 如果在一个焊点类型内合格的焊点数达到或超过表 2 所示值,或者符合焊接图纸 上的要求并且 7.3 的情况不存在,则该类型是合格的. 7.2 如果焊接图纸上没有要求,则采用表 2 数值. 7.3 在同一类型内,二个或多个相邻焊点漏焊或破坏将导致不合格. 注 3:大于 10 点的类型-每增加 10 点, 增加 10 点对应的值,再增加余下点所对应的值. 注 4:仅有 1 点的类型,强制性的焊点类型和端部焊点类型不用. 8 焊点表面修磨 8.1 以下分类是有关焊点在最终装配时所要求达到的外观质量.不是对第四条作修改. 当要求达到一,二级外观要求时,由于打磨对焊点性能造成的影响必须考虑