电火花线切割机运丝机构及控制讲解
数控电火花线切割加工简述及结构组成

数控电火花线切割加工简述及结构组成
导读:电火花线切割加工是电火花加工的一个分支,是一种直接利用电能和热能进行加工的工艺方法,它用一根移动着的导线(电极丝)作为工具电极对工件进行切割,故称线切割加工。
线切割加工中,工件和电极丝的相对运动是由数字控制实现的,故又称为数控电火花线切割加工,简称线切割加工。
数控电火花线切割加工机床可分为机床主机和控制台两大部分。
1.控制台
控制台中装有控制系统和自动编程系统,能在控制台中进行自动编程和对机床坐标工作台的运动进行数字控制。
2.机床主机
机床主机主要包括坐标工作台、运丝机构、丝架、冷却系统和床身五个部分。
(1)坐标工作台它用来装夹被加工的工件,其运动分别由两个步进电机控制。
(2)运丝机构它用来控制电极丝与工件之间产生相对运动。
(3)丝架它与运丝机构一起构成电极丝的运动系统。
它的功能主要是对电极丝起支撑作用,并使电极丝工作部分与工作台平面保持一定的几何角度,以满足各种工件(如带锥工件)加工的需要。
(4)冷却系统它用来提供有一定绝缘性能的工作介质——工作液,同时可对工件和电极丝进行冷却。
电火花线切割机床操作规程及注意事项

电火花线切割机床操作规程及注意事项
一、操作规程
●操作准备
1、将机床丝筒导轨、丝杠、齿轮注入20号机械油,保证机构运转灵活。
2、检查工作液箱内的工作液是否充足,水管和出水嘴应保证通畅。
3、检查电极丝是否装在导轮“V”型槽内,与导电块、断丝保护块接触良好。
4、检查电极丝张力,若张力不足,需要先张紧电极丝。
●操作顺序:
1、开控制柜上总电源开关,启动计算机,输入切割程序。
2、将控制柜上的丝速开关、功率管开关、中精加工规准开关、断丝保护开关、定中心选择开关,拨到适当位置。
3、设定好合理的丝筒速度后,将变频、加工、进给、高频打开,工作液泵启动,调节好工作液流量后,操作计算机按预编切割程序进行加工。
4、加工完成后,首先关断高频电源,再关工作液泵,待轮中残留液排出后,关丝筒电机,最后关断控制柜电源。
●维护保养:
1、每日加工结束后,丝筒导轨、丝杠、齿轮需再注入20#机械油。
2、每日加工结束后,机床必须擦干净。
3、导轮需定期加注高速润滑脂。
(60—80工作小时)。
二、注意事项
●未经许可,不能操作室内任何设备,不能摇动各设备的手轮。
●注意在机床的允许范围内进行加工,不能超重、超行程工作。
●定期检查并更换导电块、导轮、轴承等易损件,定期更换工作液。
●计算机启动后,从开到关间隔时间不小于五分钟。
电火花线切割加工基础知识

第三章 电火花线切割加工基础知识
(4) 电极丝比较细,可以加工微细的异形孔、窄缝和复杂 形状的工件;
(5) 脉冲电源的加工电流比较小,脉冲宽度比较窄,属于 中、精加工范畴,采用正极性加工方式;
(3) 工件在工作台上应合理装夹,避免电极丝切割时割到 工作台或超程,损坏机床。工件装夹时,还应对工件进行找正, 可用百分表或块规进行校正。
(4) 穿丝孔位置须合理选择,一般放在可容易修磨凸尖的 部位上。穿丝孔的大小以3~10 mm为宜。
第三章 电火花线切割加工基础知识
3.合理电规准的选择 大多数的电火花线切割加工采用一个固定的电规准自始 至终进行加工。若工件尺寸精度和表面粗糙度的要求高,则 必须采用小的脉冲能量的电规准进行加工,以提高加工精度 和改善加工表面粗糙度,但是加工速度将会降低。
500(可调)
2.5
2.5
2.5
6.3~3.2
2.5
2.5
0.015
0.012
0.015
0.025
0.01
0.02
80
80
100
120
120
120
3°~60°,依各厂家的型号不同而不同 各种型号均由单板(或单片)机或微机控制
第三章 电火花线切割加工基础知识
3.3 电火花线切割加工工艺
1.线切割加工程序的编制
第三章 电火花线切割加工基础知识
2) 坐标工作台 电火花线切割机床是通过坐标工作台(X轴和Y轴)与电极丝 的相对运动来完成工件加工的。一般都用由X轴方向和Y轴方 向组成的“+”字拖板,由步进电机带动滚动导轨和丝杆将工 作台的旋转运动变为直线运动,通过两个坐标方向各自的进给 运动,可组合成各种平面图形轨迹。
电火花慢走丝线切割机操作步骤的介绍

电火花慢走丝线切割机操作步骤的介绍1开机首先合上慢走丝线切割总电源开关,再按下控制面板上的按钮,启动数控系统及机床2电极丝安装供丝绕线轴上成卷电极丝的丝头依次穿过压紧卷筒、滚筒、导轮、恒张力控制轮、上部电极丝导向器、工件、下部电极丝导向器至拉丝卷筒。
一定范围内调节好伺服电机恒张力控制装置,使电极丝保持一定的张力,稳定地运行。
电极丝安装完毕后,需校正其垂直度。
慢走丝电火花线切割加工时可以采用距离密着加工,即使上部导向器与工件的距离尽量靠近,避免因距离较远而使电极丝振幅过大影响工件加工质量。
3程序运行为了减少慢走丝加工时工件材料变形可以有效提高工件、加工精度及改善表面质量,慢走丝线切割时应采用少量、多次切割方式。
因而在粗加工或半精加工时可留一定余量,以补偿材料因原应力平衡状态被破坏所产生的变形和最后一次精加工时所需的加工余量,当最后精加工时即可获得较为满意的加工效果。
4零件检测加工结束,卸下零件,检测有关加工参数是否达到相应的要求。
5工件安装慢走丝线切割机床上应用的桥式夹具、电极丝垂直度检具、回转工作台、数控转台等机床附件、工具与快走丝线切割机床相同。
近年推出的线切割基准装夹系统采用了通用的装夹夹具和找正工具,只需极简单的操作,就可快速准确地完成工件的找正和装夹,广泛用于慢走丝线切割机床上。
6机床操作面板及其功能应用数控电火花慢走丝线切割机床的操作面板也包括控制面板和手控盒面板,与快走丝线切割机床大同小异。
但因电极丝单向运行,无储丝筒,不再设储丝筒操作面板。
7程序输入按机床操作说明书的要求,通过在不同操作模块间的切换,用键盘输入加工程序或直接调用已有程序并装入内存,完成生成工件切割程序操作。
执行程序前,先将程序模拟运行一遍,检验程序的运行状况。
8关机首先将工作台移至各轴中间位置;随后按下红色急停按钮;最后扳下电源主开关,关闭电源并断开外接线路。
线切割工作原理及操作

线切割工作原理及操作线切割工作原理及操作1. 引言在制造业中,线切割技术被广泛应用于金属加工领域。
它通过使用一根细小且高速振动的金属丝来切割工件,从而实现高精度的切割效果。
本文将深入探讨线切割的工作原理及操作方法,以帮助读者更好地理解该技术的应用。
2. 工作原理线切割技术基于电火花原理,即利用高频电流在工件表面产生的火花进行切割。
具体而言,线切割机通过引导一根直径约0.1至0.3毫米的金属丝,在辅助电解液的作用下与工件形成导电通路。
高频脉冲电流通过金属丝,引发电火花,在工件表面产生剧烈的化学反应。
这个过程持续不断,直到金属丝逐渐切割穿过工件。
3. 设备和操作方法线切割机是实现线切割技术的关键设备。
它通常由控制系统、电源系统和机械部分组成。
在操作过程中,首先需要根据工件的尺寸和形状,设计并生成一套切割程序。
将切割程序输入到线切割机的控制系统中。
在进行线切割之前,需要准备工作件和电解液。
工作件通常是金属材料,可以是钢、铝、铜等。
电解液则是一种具有高离子导电能力和冷却效果的液体,用于维持切割过程中的稳定性和效果。
接下来,将待切割的工件固定在工作台上,并调整切割机的参数,如电流、速度和张力等。
开始线切割操作。
线切割机将根据预设程序,精确控制金属丝的运动轨迹和电流信号,确保切割过程的稳定性和准确性。
4. 优势与应用线切割技术具有以下优势:一是切割精度高,能够实现毫米级的切割精度。
二是能够切割各种形状的工件,包括平面、曲面和立体等。
三是切割过程中无力量作用于工件,避免了热变形和机械变形的问题。
四是切割速度快,提高了生产效率。
线切割技术广泛应用于航空航天、汽车制造、电子设备和模具制造等领域。
5. 个人观点和理解对于我来说,线切割技术是一项非常有价值的制造技术。
它通过精密的电火花原理,实现对各种金属材料的高精度切割,为各种行业的生产提供了重要支持。
线切割技术的发展,不仅推动了制造业的进步,也为产品创新提供了更多可能。
电火花线切割加工技术详解
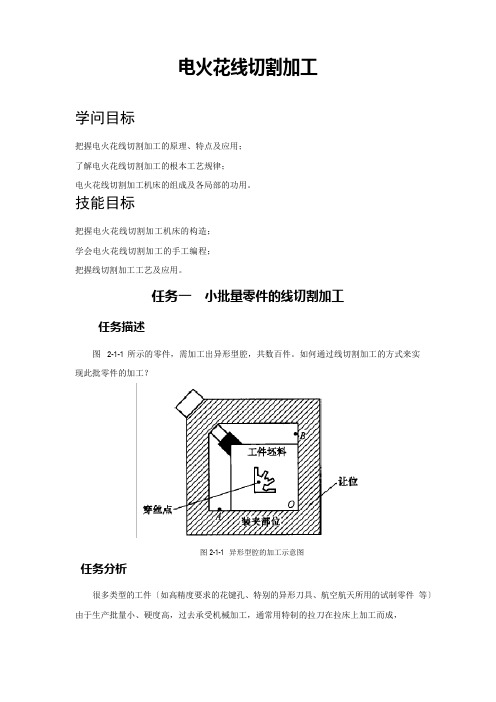
电火花线切割加工学问目标把握电火花线切割加工的原理、特点及应用;了解电火花线切割加工的根本工艺规律;电火花线切割加工机床的组成及各局部的功用。
技能目标把握电火花线切割加工机床的构造;学会电火花线切割加工的手工编程;把握线切割加工工艺及应用。
任务一小批量零件的线切割加工任务描述图2-1-1 所示的零件,需加工出异形型腔,共数百件。
如何通过线切割加工的方式来实现此批零件的加工?图2-1-1 异形型腔的加工示意图任务分析很多类型的工件〔如高精度要求的花键孔、特别的异形刀具、航空航天所用的试制零件等〕由于生产批量小、硬度高,过去承受机械加工,通常用特制的拉刀在拉床上加工而成,而拉刀本钱格外高,因此对于高硬度、带有斜度的工件很难适用。
在这种状况下承受慢速走丝线切割进展加工,可以极为便利地满足加工要求。
学问预备一、电火花线切割加工的原理、特点及应用随着电火花加工技术的进展,在成形加工方面逐步形成两种主要加工方式:电火花成形加工和电火花线切割加工。
电火花线切割加工〔wire cut EDM,简称WEDM〕自20 世纪50 年月末产生以来,获得了极其快速的进展,已逐步成为一种高精度和高自动化的加工方法,在模具制造、成形刀具加工、难加工材料和周密简单零件的加工等方面获得了广泛应用。
目前电火花线切割机床已占电加工机床的60%以上。
1.电火花线切割加工的进展电火花线切割加工历经半个多世纪的进展,已经成为先进制造技术领域的重要组成部分。
电火花线切割加工不需要制作成形电极,能便利地加工外形简单、大厚度的工件,且工件材料的预加工量少,因此在模具制造、产品试制和零件加工中得到了广泛应用。
尤其是进入20 世纪90 年月后,随着信息技术、网络技术、航空和航天技术、材料科学技术等高技术的进展,电火花线切割加工技术也朝着更深层次、更高水平的方向进展。
我国上海仪表工程师于 20 世纪60 年月独创的特种快速走丝电火花加工机床,经过30 多年的进展和完善,现已成为模具加工不行缺少的装备,也是中国模具生产企业装备数量最多的电火花加工机床。
电火花线切割
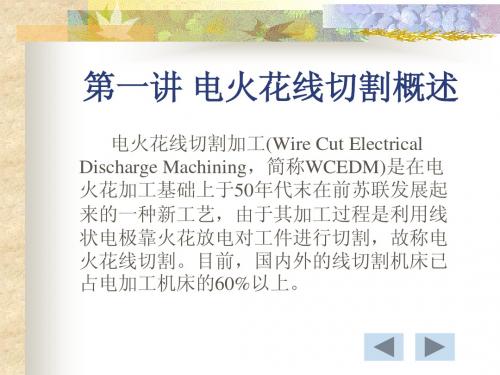
(2)正确选择穿丝孔、进刀线和退刀线 穿丝孔是电极丝相对工件运动的起点, 同时也是程序执行的原点,所以穿丝孔应选 择在容易找正、并在加工过程中便于检查的 位置。为保证加工精度,穿丝孔的位置应设 置在工件上,一般为基准点位置。 而在设置进刀线及退刀线时应注意不与 轮廓第一条边重合、不与第一条边夹角过小 或距离过近,最好是通过工件的中心线。
4.编制加工程序
线切割程序编制可采用手动或电脑自动编程,无论采用那种 方法进行编程均应对以下几个方面进行充分考虑: (1)配合间隙 在对有配合间隙要求的工件(如冲模的凸凹模)进行切割时, 在编程时应把配合间隙值考虑在程序中。 (2)过渡圆 为了提高切割工件的使用寿命,在工件的几何图形交点,特 别是小角度的拐角处应加上过渡圆,其半径一般在0.1-0.5mm范 围内。 (3)起割点和切割路线 起割点一般选择在工件几何图形的拐角处,或容易将凸尖 修去的部位。切割路线的确定以防止或减少工件变形为原则。
(2)电极丝
高速走丝机床的电极丝是快速往复运行 的,在加工过程中要反复使用。这类电极丝主 要有钼丝、钨丝和钨钼丝。低速走丝线切割机 床一般用黄铜作电极丝,电极丝作单向低速运 行,用一次就作为废料回收,不必用高强度和 耐损耗的钼丝。电极丝直径过大或过小对加工 速度的影响较大。电极丝的走丝速度影响切割 速度,这是因为随着走丝速度的提高,使工作 液易被带入放电间隙,改善间隙状态。 但是工艺条件确定后,切割速度的提高 是有限的。
四、数控线切割技术的发展趋势
1.切割速度、加工精度、表面粗糙度、复 杂度的进一步提高;
mm 2 低速目前最高切割速度:300 min
高速最高切割速度可达:260
mm 2
min
2.线切割机床逐步形成产品的系列化、标 准化和通用化,向大型、精密、高效率、多功 能及自动化等方向发展。
数控电火花线切割机床的操作
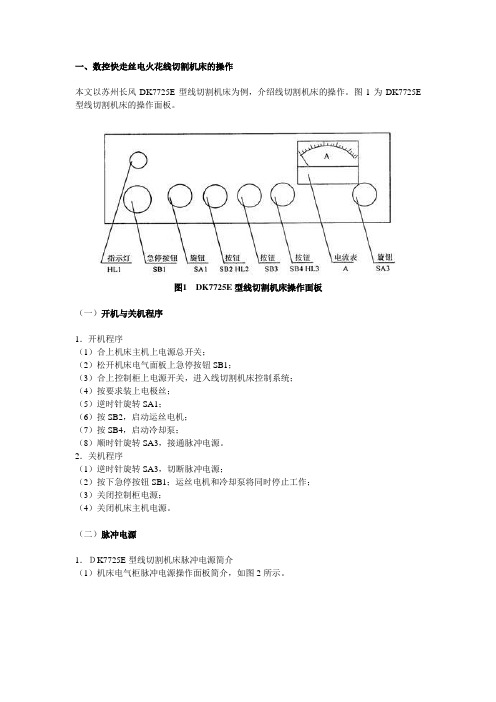
一、数控快走丝电火花线切割机床的操作本文以苏州长风DK7725E型线切割机床为例,介绍线切割机床的操作。
图1为DK7725E 型线切割机床的操作面板。
图1 DK7725E型线切割机床操作面板(一)开机与关机程序1.开机程序(1)合上机床主机上电源总开关;(2)松开机床电气面板上急停按钮SB1;(3)合上控制柜上电源开关,进入线切割机床控制系统;(4)按要求装上电极丝;(5)逆时针旋转SA1;(6)按SB2,启动运丝电机;(7)按SB4,启动冷却泵;(8)顺时针旋转SA3,接通脉冲电源。
2.关机程序(1)逆时针旋转SA3,切断脉冲电源;(2)按下急停按钮SB1;运丝电机和冷却泵将同时停止工作;(3)关闭控制柜电源;(4)关闭机床主机电源。
(二)脉冲电源1.DK7725E型线切割机床脉冲电源简介(1)机床电气柜脉冲电源操作面板简介,如图2所示。
SA1——脉冲宽度选择SA2~SA7——功率管选择SA8——电压幅值选择RP1——脉冲间隔调节PV1——电压幅值指示急停按钮——按下此键,机床运丝、水泵电机全停,脉冲电源输出切断。
图2 DK7725E型线切割机床脉冲电源操作面板(2)电源参数简介①脉冲宽度脉冲宽度ti选择开关SA1共分六档,从左边开始往右边分别为:第一档:5us 第二档:15us 第三档:30us 第四档:50us 第五档:80us 第六档:120us②功率管功率管个数选择开关SA2~SA7可控制参加工作的功率管个数,如六个开关均接通,六个功率管同时工作,这时峰值电流最大。
如五个开关全部关闭,只有一个功率管工作,此时峰值电流最小。
每个开关控制一个功率管。
③幅值电压幅值电压选择开关SA8用于选择空载脉冲电压幅值,开关按至“L”位置,电压为75V左右,按至“H”位置,则电压为100V左右。
④脉冲间隙改变脉冲间隔t0调节电位器RP1阻值,可改变输出矩形脉冲波形的脉冲间隔t0,即能改变加工电流的平均值,电位器旋置最左,脉冲间隔最小,加工电流的平均值最大。
- 1、下载文档前请自行甄别文档内容的完整性,平台不提供额外的编辑、内容补充、找答案等附加服务。
- 2、"仅部分预览"的文档,不可在线预览部分如存在完整性等问题,可反馈申请退款(可完整预览的文档不适用该条件!)。
- 3、如文档侵犯您的权益,请联系客服反馈,我们会尽快为您处理(人工客服工作时间:9:00-18:30)。
1 绪论1.1前言电火花线切割机床是一类在模具制造等行业中广泛应用的典型数控机床。
电火花割加工技术WEDM(Wire Electrieal Diseharse Machining)自问世以来,得到了迅速的发逐步成为机械制造领域中的一个重要组成部分。
高速走丝电火花线切割机床是通过线具电极,对工件进行脉冲性放电加工的。
工作时脉冲电源的正极接工件,负极接电极电极丝由储丝筒带动往复移动,通过控制工件的运动轨迹和速度,从而切割出符合技求的工件。
由于其加工性能与被加工材料无关,而且在加工过程中无切削力,从而容工复杂、精密和高硬度的零件,特别是对薄壁、窄缝零件的加工更具有优势。
工材精密复杂零件、微细零件的加工中占有极其重要的地位。
近年来,在电机模具行业,模具工业的增长,高速冲硬质合金模具的不断推出,模具的大型化和精密化,采用电线切割来加工模具逐渐被广泛认可。
目前国内外的线切割机床约占电加工机床的60%,在低速走丝线切割机床诞生后不久,我国也自行研制出具有首创性的高速走丝线机床。
数十年来,这种机床对我国的制造业发展做出了很大贡献。
由于其价格低廉、比高,因而受到国内许多中小型企业和工厂的青睐,广泛应用于仪器仪表、家用电器车和电机等行业,尤其在加工制造方面发挥了巨大作用。
据统计,目前我国数控高速线切割机床约有10余万台,居世界第一位,2002年国内线切割机床产量1。
5万台,其大部分是高速走丝的线切割机床。
近年来,随着电子技术、计算机技术和控制技术的高速发展,电加工机床的数控也不断地取得了长足的进步。
传统的CNC技术由于通用性差、通讯能力弱以及不便于功能等缺点,已逐渐不适应现代制造业发展的要求。
因此,目前数控技术正在向通用放式实时动态全闭环控制的模式发展,开放式的数控系统已逐渐成为新一代数控系统流。
尽管我国的高速走丝电火花线切割机床与慢速走丝机床相比,在结构、工艺和数术等方面仍有一定差距,但是仍非常适合于加工中等精度和表面粗糙度的零件或模具此提高线切割加工设备的性能(如:实现高速走丝电火花多次切割技术、角度旋转、尖理等功能)对加快我国制造业的发展有着重要意义。
当前发达国家正在紧锣密鼓地进行着开放式数控系统的研究,正为我国数控产业展提供了良好的契机,开发我国自主版权的开放式数控系统平台是赶超发达国家的历遇。
我国控制器硬件由于受制造业水平的影响可靠性差,成为制约我国数控产业发展颈。
借用PC硬件和建立开放式控制系统软件平台就完全可以绕开这个问题。
数控技开放式道路,将我国同世界上发达国家的数控研究摆在了同一起跑线上,我们只有抓个机遇,才能开发出具有中国自主版权的高性能数控系统,独立自主地发展我们自己控产业,打破国外对我国的技术垄断。
此外,现有文献数据采样插补算法存在着许多点和不足之处。
有鉴于此,本课题“电火花线切割加工机运丝机构及数控工作台机电系统设计”针对培养数控系统模块化设计指导思想、提高高速走私线切割加工设备的性能而提出的。
1.2国内外动态1.2.1国外电火花线切割加工技术的发展及现状1943年,原苏联学者拉扎连科夫妇研究电火花放电时开关触点受腐蚀损坏的现象和原因,发现电火花的瞬时高温可使局部的金属熔化、气化而被蚀除掉,从而开创和发明了电火花加工方法。
电火花线切割加工(WEDM)是在电火花加工的基础上于50年代末最早在原苏联发展起来的一种新的工艺形式,是用线状电极靠火花放电对工件进行切割,故称为电火花线切割。
电火花线切割加工以获得广泛的应用。
目前国内外的线切割机床约占电加工机床的60%以上。
与电火花成型加工方法相比,线切割加工方法具有设备成本低、生产效率高以及工具电极的设计和制造大大简化等特点,同时还可节约一部分材料。
因此,线切割加工方法自问世于前苏联以来,得到了迅速的发展。
近20年来,电火花线切割机床的价格下降了六倍多,加工速度提高了十几倍,工件的最大尺寸增加了十四倍,可加工的工件锥度达到80º。
目前慢走丝线切割机床最小驱动单位达0.lum,加工精度已接近或达到精密磨削的精度,最大切削速度超过3O0mm2/min,标志着WEDM总的加工速度有了明显的提高,微精加工脉冲电源的开发,使精加工表面粗糙度可达到Ra0.l~0.2μm(多次切割)。
线切割加工水平的提高使它从“特种加工”进入到常规加工的行列。
线切割加工水平的提高不仅归功于机械结构和工艺方法的改善,更得力于先进技术的应用和计算机软件的发展。
欧美和日本等国研究的数控低速走丝电火花线切割机床,采用闭环数字交(直)流伺服控制系统,动态性能好、定位精度高。
同时机床具有数字自适应控制电源,并具有自动走丝、自动卸除废料、短路自动回退等自动化技术,对电极丝张力和工作液压力也可进行控制。
同时,集以D、以PP、CAM 及仿真于一体的自动编程系统不断发展和成熟,目前基于PC的图形交互式自动编程系统成为线切割自动编程系统的主流。
从2002年美国芝加哥国际机床展展出的线切割机床可以看出当前国外WEDM的技术特点与发展动向:(l)提供不同档次的系列产品,供用户选择(2)改进了走丝系统,使运丝更平稳,张力更稳定(3)自动穿丝与自动重穿丝技术该功能虽然是国外WEDM普遍配备的,但近年来的改进重点在提高可靠性和穿丝速度上。
(4)减少机床的热变形,提高热稳定性(5)高精度的锥度切割(6)直线电机的应用(7)联网这是一个在适应网络时代的到来而开拓的新功能。
虽然与外部计算机的通信并不是新鲜事,按任务的要求可以把外部计算机看成是机床数控系统的外围设备,也可以把机床看成是外部计算机的一个终端。
这一功能尽管目前的实用性还不够明显,但无疑是今后的一个发展方向。
(8)拓展在零件加工中的应用(9)高速度加工高速度化一直是国外厂商追求的目标。
在这方面,日本厂商一直走在世界的前列。
例如,三菱电机公司的标准型DWCH系列机床,由于采用G25电源,最高生产率达250mm2/min,其经济型DWCC2系列机床也是250mm2/min。
著名的Sodick公司的A500—E型电火花线切割机的电源数控柜由于采用32位CPU,使加工速度大幅度提高,同样可以达到300mm2/min。
快走丝电火花线切割技术最初是在我国发展起来的一种电火花加工方法,它与慢走丝电火花线切割技术无论从加工方法还是加工装置上都有很大区别。
因此,我国的电火花线切割技术的发展主要体现在快走丝线切割技术的进步上。
相对而言,我国的慢走丝电火花线切割技术起步较晚,其水平与国外同类产品相比还存在较大的差距。
1.2.2我国电火花线切割技术的发展及现状1、机床品种多样化,年产量稳步增长多年来,我国生产的数控电火花切割机一直是单一的高速走丝线切割机。
随时间推移,为了满足市场需求,又开发生产了自旋式电火花线切割机、走丝速度可调的电火花切割机(含高低双速走丝电火花线切割机)以及低双速走丝电火花线切割机等。
机床品种的多样化可以满足用户的需要,扩大数控电火花线切割机加工的应用范围。
高速走丝电火花线切割机是我国当前发展的主要产品,广大的科技工作者为了进一步提高它的工艺性能及自动化程度做了大量开发工作,并开发生产了2000mm×1200mm×500mm及1000mm×630mm×1000mm等超大型高速走丝电火花线切割机床,扩大了它的应用范围,满足了用户的各种需要,使其年产量稳步增长,至今以达到了12000台/年,并有约300台/年出口到世界各国。
低速走丝电火花线切割机过去曾是“进口机”的代名词,现在已有苏州沙迪克三光机电有限公司、北京阿奇工业电子有限公司、苏州电加工机床研究所,汉川机床厂等多家制造厂商自行开发生产,年产量达300多台。
这些机床性能好,价格不到进口机的一半,深受国内用户的欢迎。
自旋式电火花线切割机和走丝速度可调的电火花线切割机目前虽处在开发和完善阶段,产量也不大,但开发思想都是企图借鉴高速走丝和低速走丝二者的优点创造一种新型的电火花切割方法。
它的成功不仅能为我国的电火花线切割增加一个新品种,并以它的性能价格比好以及加工消耗低的特点找到它自身的应用范围,而且为高速走丝的电火花线切割机的多次切割工艺奠定基础。
2、高速走丝系统日趋完善高速走丝有助于工作液进入窄小的加工区,改善排屑条件,这对于切割大厚度工件以及提高切割速度都是很有作用的。
同时,电极丝的往返运动可使电极丝重复使用,减少电极丝的消耗,降低切割加工的生产成本。
然而,高速走丝也会造成导向器(导轮、导向块等)的磨损和系统的振动,加上电极丝的张力不容易控制,它将给加工稳定性、加工精度及表面质量带来严重影响。
为了解决高速走丝所存在的问题,完善高速系统,广大科技工作者己做了大量的开发研究工作,并获得了明显的效果。
上海大量电子设备有限公司已于1999年开发生产了数字程序控制短程往返走丝系统,根据加工条件设定正向移动和反向移动的时间,以消除高速走丝的换向切割条纹,改善加工表面质量。
北京阿奇工业电子有限公司根据高速走丝正向和反向移动张力不一的缺点,开发了新型的恒张力高速走丝机构。
这种新型的恒张力高速走丝机构。
这种新型机构不仅可以紧丝,而且可以保证正向和反向移动时电极丝的张力基本一致。
因此,走丝系统上、下丝架的导轮是对称设置的,可以保证正、反向移动时产生摩擦阻力相近,使电极丝的张力在整个过程中恒定。
电极丝的张力直接影响电极丝的振动和频率,并影响线切割加工的效果,为了使高速走丝系统的电极丝的张力恒定,华中理工大学开发了一种高速走丝线切割机铝丝恒张力伺服系统。
这种控制系统的实际使用虽然存在不少问题,但他们的开发思路是积极的。
为了提高丝架的刚性,南昌江南电子仪器厂开发了龙门式丝架,非常适合于大中型电火花线切割机,且锥度切割不受偏移量限制。
苏州沙迪克三光机电有限公司开发生产的锥度切割装置可以稳定切割720的锥型零件,而苏州金马机械电子公司的DK7740B机床能在200mm厚的工件做300锥度的切割,表明近几年来我国高速走丝WEDM机床的加工范围有了较大发展。
1.3课题的提出意义与目的通过上文的介绍,我们已经对国内外电火花线切割机床的发展有了一个基的认识。
线切割加工主要用于模具制造,随着市场竞争的日益激烈,模具开发术难度越来越大,加工要求也越来越高,时间和成本估算要求越来越严格,谁快速提供市场和客户可以接受的产品,缩短产品研制、上市的时间,谁就赢得市场竞争的主动权。
深圳福斯特数控机床有限公司生产的数控电火花线切割机床的数控系统是90年代初研制的产品,采用单板机作为主机。
这种基于单板机有存储器容量小,以实现掉电保护、接口电路扩展不方便、抗干扰性能较差等不足之处。
近10年来电子技术有了很大的发展,各种芯片的价格越来越低,功能越来越强。
为可赢得市场,该公司需要开发一套针对中小型用户的经济型电火花线切割机床的数控系统,要求用单片机系统实现32位工控机所具有的大锥度切割功能并且具有较低价位。