丰田 生产计划组织协调共32页
丰田公司生产计划的编制与薪酬分配(pdf 24页)
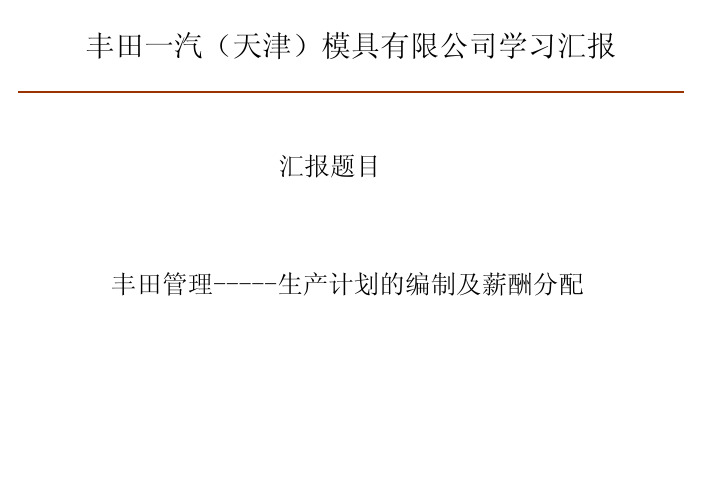
三.各部分计划的制作原则及步骤----顺序计划
d.根据机械加工负荷调整结果及《各部门对应周期表》制作顺序计划
各工序组完日
各部门对应周期表
顺序计划
三.各部分计划的制作原则及步骤
(二).工程计划的制作原则及其步骤:
1.制作原则:遵守顺序计划中的对应的时间节点,准确反映各部品之间的组装关系,作业内容及时间。 2.制作步骤: ① 泡沫工程计划表的制作
组完日期确定原则:
1.模具第1序与第2序之间组
完日相差5天,后序每两序之
间组完日相差6天。
2.对于侧围,翼子板等左右
对称模具的相同工序R,L侧, 组完日相差5天。
系 统 整
理
判定原则
步骤b
08年12月计划组
装完了模具为: 671112-1/3
OK NG
1.负荷比较平均的分配在 各周次。
2.3
671112-2/3
丰田一汽(天津)模具有限公司学习汇报
汇报题目 丰田管理-----生产计划的编制及薪酬分配
丰田一汽(天津)模具有限公司学习汇报
丰田管理-----生产计划的编制及薪酬分配
• 学习背景
生产计划不能有效指导生产
标准定额----不具备支撑计划编制 生产负荷测算----不具备指导营销
薪酬分配不能有效调动员工
工作量统计-----不准确 12-10
各部门对应周期表 (见附录3)
机械对应日期 10-31~11-28 组装对应日期 12-1~12-10
按标准周期推算 负荷确认保证
系统生成
671112-1/3调整负荷用工程计划表
标准工程计划表
7.1
上型
.
.
2.1 压边圈
丰田生产管理方式概述(doc 52页)

丰田生产方式日本丰田汽车工业公司副总经理:大野耐一第一章出自需要为石油冲击所唤醒昭和四十八年(一九七三年)秋天发生石油冲击以后,社会上好像开始强烈地关心起丰田生产方式来了。
无论怎么说,石油冲击对于政府、企业和个人生活全都产生了巨大影响。
第二年,日本经济下降到无增长的状态,整个产业界陷入了恐怖的深渊。
就在各家公司由于萧条而非常苦恼的时候,丰田虽然收益有所减少,确保住了大于其他公司的盈利,因此引起了社会上的注意,人们说,丰田这家企业采用着足以对付冲击的生产方法……。
我在石油冲击以前很早的时候,每遇到人,就打算介绍什么是丰田式的制造技术,什么是丰田的生产方式。
可是,当时人们对此不太感兴趣。
石油冲击以后,经过昭和五十年(一九七五年)、五十一年(一九七六年)、五十二年(一九七七年),丰田的盈利与年俱增,拉大了同其它公司的距离,于是丰田生产方式开始受到重视了。
在昭和四十八年(一九七三年)以前,日本经济一直保持高速度的增长。
在那个时代,企业可以采用美国的生产方式。
但是,高速度增长一停止,增长率一降低,美国式的有计划大量生产方式就行不通了。
日本的工业,譬如设备、工厂设计,全都一直是仿效美国的。
偶然也有过两位数的增长率。
那时候采用有计划大量生产是非常合适的。
但是,到了高速度增长停止并减产的时候,采用历来的大量生产方式不合算,这一点显著的表现出来了。
战后的昭和二十五年(一九五零)、二十六(一九五一)年,我们想也没想过汽车的数量会象现在这样的多起来。
在那以前很久,在美国,汽车种类少,便发明了大量生产的方法来降低成本。
这种方法渐渐地成了美国的一个特点。
可是,日本并非如此。
当时我们的课题是,怎样才能够创造出多品种、少量生产的方法来降低成本。
从昭和三十四年(一九五九)、三十五(一九六零)年起的十五年里,日本在经济方面实现了速度非常快的增长,因此,采用和美国一样的做法,也在各个方面表现出大量生产的相当好的效果。
但是,我们从昭和二十五年(一九五零)、二十六(一九五一)年起就开始认识到,不加取舍地单纯模仿美国式的大量生产方式是危险的。
丰田生产方式标准作业与改善ppt课件

1个螺母 送入机
3个螺母送入机
方向盘
5
P7
(2)动作的方向是否突然变化?(迂回行走、转身掉头)
(3)有没有不自然的姿势或身体重心上下移动的动作?
踮脚站。曲膝。下蹲。前倾。 挺胸。弯腰、扭腰。
零件的位置太低 ,所以弯腰前倾 搬取。
6
P8
发现浪费动作的着眼点
2、观察身边,找出浪 费的动作。
7
P9
2、观察身边,找出浪费的动作。
从远处眺 望
从近处观 看
像大夫那 样仔细察 看、观察
像守护病人 那样仔细 “看护”
・5个为什么 → 真因 → 改善
27
P29
・推进改善的时候,大体上分成2方法。
①作业改善‥确定作业上的规则、重新确定作业的分 配、明示物品的配置、 作业动作的改善 等、将标准作业作为 原点去实施改善。 (不花钱可实施。) ②设备改善‥导入机器装置、将设备自动化等
№ 错解理由 错解记入例
没有具体的表达出浪 费的动作
光是说
5 “○○没
有做”, 这不是表 述浪费动 作
身体(
6 重点是
腰部) 前倾的 角度不 到45°
没有做到用双手去 组装○○
没有做到1次性地 组装○○
拿取
○○的
未到
时候,
45°
身体前
倾才能
拿到。
基准
正解例
要具体的表达出浪费 的动作是什么样的
要表达出来没有 做○○的具体的 动作。
要素祖业
秒
秒
用右手取螺丝刀 1.0
0.9
用左手取螺丝 2.1
1.1
拧螺丝①
3.0
2.1
拧螺丝②
3.0
TPS丰田生产模式PPT课件

B易 于 暴 露 异 常 的 工 具
时间
800-9:00 9:00-10:00 10:00-11:00 11:00-12:00 13:00-14:00 14:00-15:00 15:00-16:00 16:00-17:00 17:00-18:00
合计
生产管理板
计划
60
实际数量
60
未进行原因
第47页/共48页
——经常为100%最理想
第9页/共48页
7
整体的生产效率比个体的生产效率 更为重要
赛艇
第10页/共48页
轴承厂的实例
B
D
d
内轮生产线(节拍快) 外轮生产线(节拍慢)
第11页/共48页
8 提高效率和强化劳动是不同的概念
提高效率
将动作“改善为有效劳动”(工作)
工
浪
动作
作
费
工
浪
作 动作 费
工
浪
作 动作费
缩短生产周期 简化生产流程
第29页/共48页
(3)按售出情况从事生产的概念较薄弱
a)由于生产的速度比售出的速度快,所以导致 生产过剩,出现停滞现象。
生产节拍
每天平均作业时间 每天所需数量
(例如)
每天平均作业时间 8小时 460分钟
每天所需数量
460件
生 产节 446 分 6 件 拍 00 钟 1分/钟 件
利润
售价
成本
利润
售价
成本
利润
售价
成本
利润
售价
成本
增加利润的方法:
1、提高售价
2、降低成本
需求>供应
需求≤供应
售价是顾客决定的
丰田汽车的4P和14项原则(与“生产”相关文档共204张)

七种浪费——搬运
定义:对物料的任何移动
表现:
需要额外的运输工具
需要额外的储存场所
需要额外的搬运人员 大量的盘点工作 产品在搬运中损坏
起因: 生产方案没有均衡化
生产换型时间长
工作场地缺乏组织
场地规划不合理 物料方案不合理
第25页,共204页。
七种浪费——库存的浪费
定义:任何超过客户或者后道作业需求的供给
员工创造力的浪费
第20页,共204页。
丰田生产方式的焦点是在工序中消除 浪费
观看影片----工厂的浪费
第21页,共204页。
Transportation
Processing
七大浪费
Waiting
Excessive Motion
Inventory
第22页,共204页。
Processing
Defect
第四层次的浪费
1)多余的仓库
2)多余的搬运工
3)多余的搬运设备
4)多余的库存管理、质量维护人员
5)使用多余的计算机
第三层次的浪费
过剩库存的浪费
利息支出 〔时机本钱〕
的增加
用能销售的速度制造 〔丰田生产方式的中心课题〕
好途径
第二层次的浪费〔最大的浪费〕
制造过剩的浪费〔工作进展过度〕
坏途径
第一层次的浪费〔过剩的生产能力的存在〕
第11页,共204页。
精益生产追求的目标
一、根本目标 工业企业是以盈利为目的的社会经济组织。因此,最大限度地获取利润就成为
精益生产的根本目标。
二、终极目标 精益求精,尽善尽美,永无止境地追求“七个零 〞 (1)“零〞转产工时浪费(Products•多品种混流生产) (2)“零〞库存(Inventory•消减库存)
采购管理案例:丰田公司的JIT计划模式

采购管理案例:丰田公司的JIT计划模式JIT采购的核心是把供应商纳入自己的供应体系,严格按产出计划,由后工序拉动,实现小批量零库存。
1.长期能力协调丰田公司设有生产规划课,专门从事制订长期生产计划,时间跨度为3年。
此计划不要求精确的车型和数量,只根据市场走势估计3年内可能要生产的车型和数量,越是往后越不准确。
每半年制订一次,滚动制作。
此计划需要通知供应链上合作企业,让他们知道丰田公司3年内的生产规模和采购规模,使供应商做好必要的长期生产能力准备,制订相应的长期能力计划。
2.月度能力协调月度计划是指制订其后3个月的计划,计划的依据是客户订单和适当的预测。
由于丰田公司是按需生产,国外客户的计划主要根据已获得的订单安排,国内客户先按订单安排,不足部分依靠预测方法。
国外订单先由当地销售部门汇总形成采购文件,再把全部汇总文件发送到设在东京的海外规划部,汇总整理后送到生产管理部。
所有文件信息传达都是通过计算机网络,速度很快,达到准时的要求。
由于是按订单排计划,因此车型和数量都确定了。
此类计划是滚动制订,第一个月基本上是确定的计划,可以执行的计划。
第二个月和第三个月作为内定计划,下一次作计划时再进行调整。
这类计划的作用是为各级生产商提供月度的能力、物资与资金准备信息。
由于生产对象大致明确,准备工作可以有的放矢。
3.月生产计划每月中旬制订下月生产计划,到中旬末计划完毕后,再根据最新订单作微调。
到下旬,开始计算该生产计划的全部的物料需求,并决定各种型号的车每天的生产量、生产工序组织、生产节拍计算等。
计算由计算机完成,工作量浩大,需要算20 h。
该计划生产的车都是有明确客户的,下线就可以提走。
该计划的作用有两个:(1)是月度可执行的生产计划;(2)提供给供应商,做好月度内的供应计划。
4.日投产顺序计划准时化生产的准时概念已经以日、小时计量,所以有了月生产计划还不足以实施准时化生产,须进一步制订按日的生产作业计划,而此计划又不同于一般的日计划,其最大特点是除了计划中的品种数量参数外,还有投产顺序,即计算混合装配线上的各种车型的投入顺序。
丰田生产管理得含义及架构
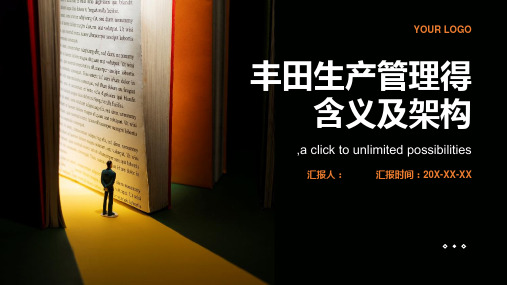
优势:准时化生产可以降低生产成本、提高产品质量、增强企业竞争力。同时,还可以提高员工的工作效率和满意度, 增强企业的凝聚力和向心力。
适用范围:准时化生产适用于各种制造业和服务业企业,特别是那些需要精确控制生产过程和产品质量的企业。
丰田生产管理的架构
准时化生产
定义:准时化生产是一种以减少浪费为目标的生产方式,通过精确地计划和协调生产过程中的各个环节,实现准时、 高效、高质量的生产。
核心思想:准时化生产的核心思想是消除浪费,包括时间、人力、物力等方面的浪费。通过精确地计划和协调生产过 程中的各个环节,实现准时、高效、高质量的生产。
目标:提高产品质量,降低成本,增强客户满意度。
方法:采用统计技术和数据分析方法,对生产过程中的各个环节进行监控和改进。
实施步骤:制定质量标准,建立质量管理体系,开展质量改进活动,持续改进并优化流程。
供应链管理
供应商选择与评估:选择合适的供应商,确保产品质量和交货期
库存管理:通过实时库存监控和预测分析,降低库存成本
丰田生产管理的含义
丰田生产管理的定义
丰田生产管理是 一种以市场需求 为导向,以降低 成本、提高生产 效率为目标的生 产管理方法。
它强调生产过程 中的精益化、准 时化、自动化和 信息化,通过消 除浪费、提高生 产效率和质量来 降低成本。
丰田生产管理不 仅是一种生产管 理方法,更是一 种企业文化和思 维方式,它注重 持续改进和创新, 追求卓越和完美。
丰田生产管理在 汽车制造业中得 到了广泛应用, 并逐渐扩展到其 他领域,成为全 球制造业的重要 参考和借鉴。
丰田_生产计划的组织协调

③
1直
实际
停止
⑦ ⑧ 時間
生产线停止状况
⑨
实/际数 /停止时间 停止状况
//
生产节拍 管理
GL CL 課長
⑪
管理者确认
//
//
//
//
//
//
终了时间
⑩ 終了時間
四 车间生产组织协调
生产计划的实施
生产进度管理 —— 安东
生产线可动率 = 当前实际/当前计划 = 实际下线数×节拍
已开线时间
案例分析
07年11月总装下线计划
250 200 150 100
50 0 1日 4日 7日 10日 13日 16日 19日 22日 25日 28日
总产量
二 生产计划的制定
2.品种数量的均衡 日与日之间每种车型都应生产相同的数量。
07年11月总装下线计划
100
80
60
哈弗汽油
哈弗柴油
40
K2风骏
20
0
1日 3日 5日 7日 9日 11日 13日 15日 17日 19日 21日 23日 25日 27日 29日
一 生产计划概述
●车辆投产(着工)顺序表范例
产 量
车身号
车型
颜色
驱动形 式
天窗
尾翼Ⅰ
ABS支架
车身指示 单代码
底盘指示 单代码
1 00001 2SD2 玫瑰红 两 ○ × ×
05
01
2 00002 2SD2 玫瑰红 两 ○ × ×
05
01
3 00003 2SD2 玫瑰红 两 ○ × ×
05
01
4 00004 2SD2 玫瑰红 两 ○ × ×
(丰田管理)丰田生产方式与标准作业
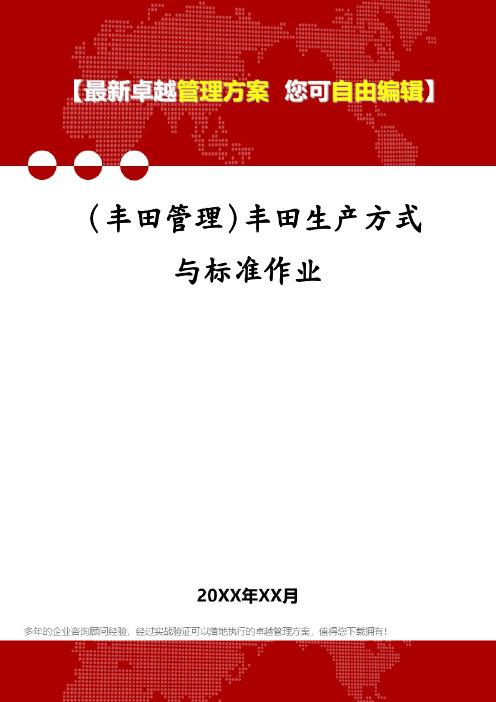
(丰田管理)丰田生产方式与标准作业例如,与1500CC级别的同等轿车相比,本公司的车价同其他公司的车价没有什么太大的差别。
也许可以认为基本上相同吧。
假设本公司的车价提高时,如果其他公司的售价比本公司低,一般顾客可能都会购买便宜的车。
日常生活中还有很多同样的例子。
如果相同级别(质量或形状)的东西一起摆在那里,消费者大概都会选择便宜一些的东西。
因此,完全有理由认为价格是由行情决定的。
在确定汽车销售价格时,只计算成本加上利润部分的成本主义的思维方式是不成立的。
售价=成本+利润如果认为这个公式成立,那么,只能陷入无法控制生产成本的思维模式中。
或者说,无论采用何种制造方法,其成本都是一样的。
这种思维方式会增加消费者的负担,结果导致企业规模缩小、濒临破产。
其次,关于增加销量的问题,虽然销售一线人员正在日夜拼命地扩大销量,但是,当今社会竞争如此激烈,只依靠本公司的力量来增加销售量是非常困难的。
虽然我们也通过汽车或住宅的推介活动等方式积极促销,但作为生产厂家,应把主要精力放在生产质量过硬的、有吸引力的商品上。
最后,有一种观点叫做售价≠成本+利润。
换言之,如果销售价格由市场行情决定,那么,为了提高利润,就必须降低成本。
因此,我们要积极推进降低成本活动,并理解其必要性。
这一活动应该是我们全员参与的全公司性活动。
大差异。
下面列举材料方面的例子来说明。
如果备足今天将使用的材料,那么,今天的工作就不会受到任何影响。
假设,即使考虑到准备材料的生产周期等因素,大概备足十天的货也足够了吧。
但是,有时某个企业准备了1—2个月的库存量,也有的企业竟然准备了半年的库存量。
由于对这些材料也需付钱,所以除了材料外,还浪费利息,而且在保管过程中会生锈、破损、不能使用;有时,某些材料会因设计变更而不再使用。
另外,由于销路问题,不需要那么多材料,造成很大的浪费。
因此,即使本来成本极低的东西,由于制造方法不当而发生的费用不断膨胀,那么从整体上看,它的成本就会变得很高了。
丰田日产的生产计划

由经销商
标准配置・不同版本・混合
7天 确定旬度订单
特别订单
4天
(当天订单)
(1天为单位) (1天为单位)
生产顺序计划 2天 5天
(循环时间为单位)
确定月度计划
・3个月前的内部通知→2个月前的内部通知→1个月前确定
按照大分类规格确定混流的产品,实行平准化生产 以经销商的需求预测为基础,加大生产能力。 调配零部件,向零部件厂发出供货的内部通知
日变更)
大分类:车体、发动机、传动、档次级别 最终规格1:选装件和颜色等选项都加以指定(标准)。 最终规格2:最细的分类(特殊订单)。
N-3月
N-2月
N-1月
N月(当月) 上旬 中旬 下旬
月度计划 旬度订单
确定月度计划 按照车型(车名)·组装线制定的生产计划(主计划)
5~10天
特殊订单 顺序
当 日
订单生产型的同期生产 “上游工序和下游工序同时把握客户的订单信息,构
筑一气贯通不间断的流程,各自的生产顺序有条不紊的生产 状态。”
改善的推进 追查打乱生产顺序和时间的要因,进行切实的改善。
5个活动领域
第一领域(车辆主生产线) 确定顺序计划生产(实际执行生产计划) 多车型混流一贯式生产线
第三领域 客户
第二领域(和自产零件的同期化)
第二领域
和车辆计划的同期生产 原材料(毛坯)整流化生产(单向流动生产)
第一领域
机械加工工序(隧道式生产)
车体 涂装 总装
套件组装生产(迎合出货生产·均衡顺序生产)
第三领域(和外包零部件的同期化) 和整车计划同期的迎合出货生产
(交货指示牌生产) 供应商内的同期化 第四领域(车辆物流的同期化) 车辆计划和配车计划·交货调试的同期化
003丰田精益生产PPT113页(1)

Lean Thinking & Lean Production System
思索:
企业的目标:做大?做强? 狼来了!来自何方? 核心课题(Toyota成功的启示):生产何等品质的产 品?以何等成本生产同等品质的产品?(迎接“同质化”、 “微利时代”的挑战) 路在何方? 制造的固有技术(工艺技术):自主创新、核心技术 制造的链接技术(管理技术):精益体制
管理理念一:简捷、简捷、再简捷 !→→ 准确实现、避免偏 差
管理体系流程化 管理标准显在化 管理方法可视化
管理理念二:以人为本、共同实现!→→集思广益、荣辱以共
全员参与 自主管理
Topdown与Downtop并行
维护部门生产保养
全公司生产保养 1968年Nippon Denso 首次创立日本特色的 全员生产性保全体制 ,80%~90%员工参 与
福特T型车的成功启示:流水线生产方式(Line Production) 流水线生产方式的挑战:多品种、小批量 Toyota的生产方式革命:流线化、批量细分化、单件流(One Piece Flow) 现代开发新产品的“并行工程”
突破库存瓶颈:流线化生产 流线化生产的核心含义:细胞化
工序1 工序4 1
易
缺
难
足
1、标准作业
标准作业
有规律的重复 性作业,如:组装工 序的螺栓紧固。
非标准作业
没有规律的非 重复性作业,如:补 充螺栓。
如果操作者在作业中同时需要进行 标准作业和非标准作业,必然造成生产动 作的停顿,从而使生产不稳定。
标准作业
为达到人员的安定,首先要分离标 准作业和非标准作业。
标准作业
JIT-准时生产制p32(共32张PPT)

Just In Time
③ 不良重修的Muda。
④ 动作的Muda。
⑤ 加工的Muda。
⑥ 等待的Muda。
⑦ 搬运的Muda。
--中国现场改善网--企业管理资料免费分享平台
第二节 JIT的含义
一、 JIT的概念
3、 理想的生产方式
(1)它设置了一个最高标准,一种极限,就是“零库存”。实际生产可以无限地接 近这个极限,但却永远不可能达到零库存。有了这个极限,才使得改进永无 止境。
从供方工作地: 38#油漆
出口存放处号 No.38—6
零件号:A435 油箱座
容器:2型(黄色) 每一容器容量:20件
看板号: 3号(共发出5张)
到需方工作地: 3#装配
入口存放处号 No.3—1
--中国现场改善典网-型-企的业传管送理看资料板免费分享平台
第四节 看板管理系统
三、 看板的类型 2、生产看板:是用于指挥工作地的生产,它规定了所生产的零件及其数量。它只在 工作地和它的出口存放处之间往返。当需方工作地转来的传送看板与供方工作地 出口存放处容器上的生产看板对上号时认识厂看板就被取下,放入生产看板盒内。 该容器(放满零件)连同传送看板一起被送到需方工作地的入口存放处。工人按 顺序从生产看板盒内取走生产看板并按生产看板的规定从该工作地的入口存放处 取出要加工的零件,加工完成规定的数量之后,将生产看板挂到容器上。
2)牵引式系统
WC2
WC3
…
推进式系统
计划部门
WCn-1
输出
WCn 产品
原材料输入
产品输出
WC1
பைடு நூலகம்WC2
WC3
…
WCn-1
WCn
牵引式系统
丰田式生产管理系统讲义.pptx

制造过多的浪费 待工待料的浪费 搬运的浪费 加工本身的浪费 库存的浪费 动作的浪费 制造不良的浪费
致力于上述浪费之根除,以大幅增加工作效率,同时 将过剩的人员清楚的显示出来
前推式及时化
生产方式改善归纳 以产品为导向的工厂设施规划。 单件流程的生产线。 双仓式的物料供应方式。 弹性的人力运用。 同步化的生产规划。 目视管理。
看板制度是一种能调和控制一个工厂的各 项生产程序,以适当的原料或半成品,在 必要的时间,生产出必要数量的必要产品 的信息系统。
另一方面其生产线上每一工作站所需之零 组件,均能适时适量的配合供应,而不像 传统生产线需库存大批零组件,因此也被 称为「零库存管理」。
看板技术
降低成本为基本目标
展开一种能使生产同步化、准时进行的方法
目视管理
目视管理又可称为玻璃式的管理 (Glass Management)与传统式的黑箱管理完全不同,它的 主要特色为:
集体的思想和意识导向。 任何事物都透明化。 与全体同仁共同分享进步的过程。 公司内部的每位员工都能无拘束的提出改善建议。
「目视管理」就是指,用眼睛一眼即可看出现场 是否有异常歐 。
丰田式生产管理的架构
后面的制程把必要的对象,在必要的时候 ,按照必要的数量,到前制程去领取,而 前制程仅生产被领走的数量
全依赖计划的方式同时对整体制程作生产 排程,对于数千种零组件,装配成制品的 汽车整体制程上,要实现及时生产是极为 困难的
丰田式生产管理的架构
通常停止生产线会造成生产的减少,但停 止生产线的目的,是为了建立一条不再停 止的理想生产线,所以在停止时,管理者 必须全力去解决问题的症结。正如大野耐 一先生所说:「不停止的生产线,不是很棒 的生产线,就是很差的生产线」。
丰田公司生产管理-42页精选文档

丰田生产管理模式研究背景在20世纪70年代之前,汽车世纪就是美国世纪,底特律汽车的标准一度代表全球的标准。
其中,福特汽车公司和通用汽车公司更是鼎鼎有名的汽车行业楷模,前者创造了“大规模生产模式”,而后者更是以规模扩张见长的典范。
在那个时候,出生于弹丸之国日本的丰田无论是在技术上还是在规模上根本无法与福特及通用相提并论。
1868年,日本爆发了影响深远的明治维新,仅在1870~1896年短短的26年间,明治政府就颁布了30次重要的教育改革法令,其文部省占用的经费比政府中任何省、部都多。
政府出高薪聘请西方教师到日本讲学,也不断派人到海外留学,并把初等教育普及到偏远乡村。
这一切,预示了跨过世纪门坎后,远东日本的腾飞。
今日的丰田光芒四射,已晋升为世界第二大汽车制造商,并被誉为“全球最成功的汽车制造商”。
汽车业分析师估计,若按现在的趋势持续下去,丰田汽车终将在生产规模、整体盈利额与品牌价值上全面超越通用汽车,成为全世界最大的汽车制造商。
一、丰田起步 TPS萌芽丰田佐吉:要靠自己的技术立“国”!提起丰田,人们都自然会联想到丰田佐吉。
农家子弟丰田佐吉,人们眼中一个能够创造奇迹的人。
因家境贫寒,他连小学都没上过。
母亲夜夜织布的辛苦,激发出他的创造力。
从少年时代起,他就埋头开发各种各样的织布机,被誉为“发明王”,载入日本教科书。
产业革命的风云中,佐吉成为一代企业家,奠定了今天跨国集团丰田汽车公司的基础。
他最重要的堪称是划时代的发明,是1896年完成的“丰田式汽动织机”,它可以由一名挡车工同时照看3-4台机器,极大地提高了生产效率;能给设备赋予类似人的“智能”,使之在出现异常情况时自动停车。
(是丰田方式中“自动化”萌芽)丰田佐吉认为:◆求人不如求己;◆打开那扇窗看看,外面是很辽阔的;◆发明之最终目的,在于其完全实用化;◆若不实行健全的营业性试验,则不可能将其真正价值展现。
他逝世以后,他的遗训被归纳为五条并作为“丰田纲领”而流传下来:◆上下一致,至诚从业,产业报国;◆致心于研究与创造,常于潮流之先驱;◆戒慎华美,质实刚健;◆发挥温情友爱的精神,缔造家庭优良门风;◆尊崇神佛,力行报恩感谢的生活。