压铸模设计如何选择内浇口位置
模具设计浇口位置(入水口)的选择技巧

模具设计浇口位置(入水口)的选择技巧一、浇口位置的要求1.外观要求 (浇口痕迹, 熔接线)2.产品功能要求3.模具加工要求4.产品的翘曲变形5.浇口容不容易去除二、对生产和功能的影响1.流长(Flow Length)决定射出压力,锁模力,以及产品填不填的满流长缩短可降低射出压力及锁模力。
2.浇口位置会影响保压压力,保压压力大小,保压压力是否平衡,将浇口远离产品未来受力位置(如轴承处)以避免残留应力,浇口位置必须考虑排气,以避免积风发生不要将浇口放在产品较弱处或嵌入处,以避免偏位(Core Shaft)。
三、选择浇口位置的技巧1. 将浇口放置于产品最厚处,从最厚处进浇可提供较佳的充填及保压效果。
如果保压不足,较薄的区域会比较厚的区域更快凝固,避免将浇口放在厚度突然变化处,以避免迟滞现象或是短射的发生。
2. 可能的话,从产品中央进浇,将浇口放置于产品中央可提供等长的流长,流长的大小会影响所需的射出压力,中央进浇使得各个方向的保压压力均匀,可避免不均匀的体积收缩。
3. 浇口(Gate) :浇口是一条横切面面积细小的短槽,用以连接流道与模穴.横切面面积所以要小,目的是要获得以下效果:1)模穴注不久, 浇口即冷结.2)除水口简易.3)除水口完毕,仅留下少许痕迹4)使多个模穴的填料较易控制.5)减少填料过多现象.设计浇口的方法并无硬性规定,大都是根据经验而行,但有两个基本要素须加以折衷考虑:1. 浇口的横切面面积愈大愈好,而槽道之长度则愈短愈佳,以减少塑料通过时的压力损失.2. 浇口须细窄,以便容易冷结及防止过量塑料倒流.故此浇口在流道中央,而它的横切面应尽可能成圆形.不过, 浇口的开关通常是由模件的开关来决定的.3. 浇口尺寸:浇口的尺寸可由横切面积和浇口长度定出,下列因素可决定浇口最佳尺寸:1)胶料流动特性2)模件之厚薄3)注入模腔的胶料量4)熔解温度5)工模温度决定浇口位置时,应紧守下列原则:1. 注入模穴各部份的胶料应尽量平均.2. 注入工模的胶料,在注料过程的各阶段,都应保持统一而稳定的流动前线.3. 应考虑可能出现焊痕,气泡,凹穴,虚位,射胶不足及喷胶等情况.4. 应尽量使除水口操作容易进行,最好是自动操作.5. 浇口的位置应与各方面配合。
如何确定内浇道位置

如何确定内浇道位置铸件的凝固补缩方式与内浇道的位置有很大关系,一般要求内浇道的开设位置应符合铸件的凝固补缩方式,通常:1)要求同时凝固的铸件,内浇道应开设在铸件薄壁处,并且要数量多,分散布置,使金属液快速均匀地充满型腔,避免内浇道附近的砂型局部过热。
2)要求定向凝固的铸件,内浇道应开设在铸件厚壁处。
如果设有补缩冒口,最好将冒口设在铸件与内浇道之间,使金属液经冒口引入型腔,以提高冒口的补缩效果,如球墨铸铁曲轴、齿轮以及铸钢齿轮等。
有时为避免铸件因温差过大产生较大的收缩应力,内浇道也可开设在铸件次壁厚处。
3)对于结构复杂的铸件,往往采用定向凝固与同时凝固相结合的所谓“较弱定向凝固”原则安排内浇道位置开设,即对每一个补缩区按定向凝固的要求设置内浇道,而对整个铸件则按同时凝固的要求采用多个内浇道分散冲型,这样设置即可使铸件个厚大部位得到充分补缩而不产生缩孔及缩松,而又可将应力和变形减到最小程度。
4)当铸件壁厚相差悬殊而又必须从薄壁处开始内浇道引入金属液时,则应注意同时使用冷铁加快厚壁处的凝固及加大冒口,浇注时还应该采取点冒口等工艺措施,以保证厚壁处的补缩。
但是,开设内浇道位置时不能只考虑铸件的凝固补缩方式,而且还应考虑和注意以下问题:1、内浇道不要开设在铸件质量要求高的部位,因内浇道附近晶粒粗大,也最好不要开设在非加工面上,以避免影响铸件外观质量。
对有耐压要求的管类铸件,内浇道常开设在法兰处,以防止管壁处产生缩松;2、内浇道不要正冲着砂型和砂芯,或其他薄弱的突出部分,以防冲砂。
对旋转体铸件,内浇道要切向引入,并力求方向一致,使杂质集中并排入冒口或相应的工艺凸台中;3、内浇道不要开设在靠近冷铁或芯撑处,以避免降低冷铁的作用或造成芯撑过早熔化;4、内浇道应使金属液沿型壁注入,不要使金属液长时间降落在型壁表面上使砂型局部过热;5、内浇道开设应有利于冲型平稳、排气和除渣,从各个内浇道进入型腔的金属液流向应力求一致,避免因流向混乱而不利于渣、气的排出;6、对收缩倾向大的合金,如铸钢件,内浇道的设置应不妨碍铸件的收缩,避免铸件产生较大应力或因收缩受阻而开裂;7、内浇道应尽量开设在分型面上,便于造型操作;8、内浇道设置位置应便于开箱和铸件清理以及去除浇注系统,而不影响铸件的使用和外观;9、在满足浇注要求的前提下,应尽量减少浇注系统的金属消耗,并且应使砂箱尺寸尽可能小,以减少型砂和金属液的消耗;10、内浇道与铸件交接处的横截面厚度一般应小于铸件壁厚的二分之一,至多不超过三分之二,用封闭式浇注系统时,内浇道要设置断口槽,以防止清理时造成铸件缺肉。
铸造工艺学课件浇注位置的确定
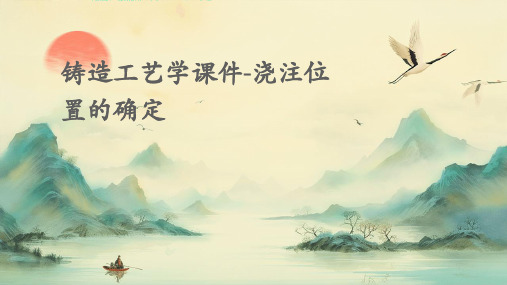
按铸件在铸型中的位置和金属 液的流动方向组合分类:可分 为上后浇注、下前浇注、侧底
浇注等。
02
浇注位置的选择原则
铸件结构的考虑
铸件结构
浇注位置应有利于金属液的流动和填充,同时要 考虑到铸件的结构,如壁厚、肋条、凸台等。
减少缺陷
浇注位置应尽量减少铸件内部和表面的缺陷,如 气孔、夹渣、冷隔等。
简化模具
浇注位置应有利于模具的 设计和制造,降低模具成 本。
冷却效果
浇注位置应有利于提高模 具的冷却效果,缩短铸件 冷却时间。
脱模方便
浇注位置应有利于脱模, 避免卡模或损坏铸件。
铸造工艺的考虑
工艺适应性
浇注位置应有利于铸造工艺的实 施,如砂型铸造、金属型铸造等 。
质量控制
浇注位置应有利于质量控制和检 测,便于发现问题和解决问题。
要点二
人工智能技术的应用
通过训练神经网络模型,实现对浇注位置的自动优化。该 方法可以大幅提高优化效率和准确性,减少人工干预和试 错成本。
THANKS
感谢观看
详细描述
在确定飞机起落架的浇注位置时,需 要考虑以下几点
实例三:飞机起落的浇注位置确定
浇口位置应避开起落架的承力部位和连接部位,以免影响起 落架的强度和稳定性。
浇口位置应与起落架的材料和冷却系统相配合,保证起落架 在铸造过程中能够得到充分的冷却,防止出现铸造缺陷。同 时,考虑到飞机起落架的使用环境和安全性要求,浇注位置 应尽量减小对起落架外观和质量的影响。
基于铸造工艺的确定方法
总结词
根据铸造工艺的特点,选择合适的浇注位置,以确保金属液能够顺利填充型腔并获得完整、清晰的铸件。
详细描述
铸造工艺的特点对浇注位置的选择具有重要影响。对于采用底注式浇注的铸造工艺,应选择将金属液从底部注入 型腔的位置作为浇注口。对于采用顶注式浇注的铸造工艺,应选择将金属液从顶部注入型腔的位置作为浇注口。
铸件浇口的设计规范
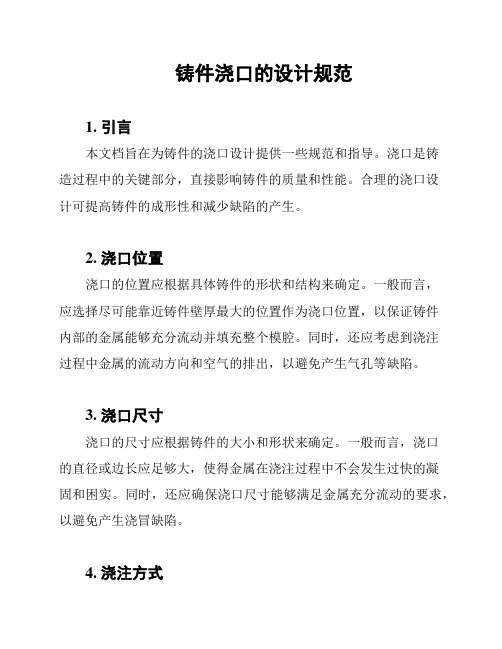
铸件浇口的设计规范1. 引言本文档旨在为铸件的浇口设计提供一些规范和指导。
浇口是铸造过程中的关键部分,直接影响铸件的质量和性能。
合理的浇口设计可提高铸件的成形性和减少缺陷的产生。
2. 浇口位置浇口的位置应根据具体铸件的形状和结构来确定。
一般而言,应选择尽可能靠近铸件壁厚最大的位置作为浇口位置,以保证铸件内部的金属能够充分流动并填充整个模腔。
同时,还应考虑到浇注过程中金属的流动方向和空气的排出,以避免产生气孔等缺陷。
3. 浇口尺寸浇口的尺寸应根据铸件的大小和形状来确定。
一般而言,浇口的直径或边长应足够大,使得金属在浇注过程中不会发生过快的凝固和困实。
同时,还应确保浇口尺寸能够满足金属充分流动的要求,以避免产生浇冒缺陷。
4. 浇注方式浇注方式的选择应根据铸件的形状、尺寸和材料来确定。
常用的浇注方式包括顶浇、底浇、侧浇等。
在选择浇注方式时,应考虑到金属在模腔内的流动路径和方向,以避免产生太多的湍流和气体夹杂。
5. 浇注温度浇注温度的选择应根据铸件的材料和结构来确定。
一般而言,浇注温度应使得金属液流动性好,同时又能保证铸件的凝固过程能够顺利进行。
浇注温度过高可能导致金属液的喷溅和气孔的产生,而浇注温度过低可能导致金属液流动性差和凝固不完全。
6. 浇注速度浇注速度的选择应根据铸件的材料和尺寸来确定。
一般而言,浇注速度应使得金属液在浇注过程中能够充分填充整个模腔并压实,同时又不能过快引起金属液的喷溅和气孔的产生。
浇注速度过慢可能导致金属液的凝固过早和铸件成形性差。
7. 浇注压力浇注压力的选择应根据铸件的材料和尺寸来确定。
一般而言,浇注压力应使得金属液能够顺利流动并填充整个模腔,同时又不能过大引起金属液的喷溅和气孔的产生。
浇注压力过小可能导致金属液无法充分填充模腔。
8. 浇注过程控制在铸造过程中,应对浇注过程进行有效的控制。
包括控制浇注温度、浇注速度和浇注压力等参数,及时发现和处理异常情况,确保铸件的质量和性能。
压铸模流道与浇口设计

压铸模流道与浇口设计压铸模流道设计是压铸模具设计中的重要环节,其质量的好与坏直接影响着铸件的质量和生产效果。
好的流道设计能够使得金属熔液在铸件中充分流动,保证铸件的充填性和凝固性,减少缩孔、破裂等缺陷。
因此,在进行压铸模具设计时,流道设计是需要重点考虑和完善的。
首先,流道设计需要考虑到金属熔液进入模腔的流动路径。
一般情况下,流道设计应遵循从大到小、从圆到方、从长到短的原则。
即,从金属熔液流动的开始到结束,流道的截面积逐渐减小,形状也从圆形转变为方形。
这样可以使得金属熔液在流动过程中更加平稳,避免较大的速度差异引起的涡流和过剩的测射。
其次,流道设计还应考虑到金属熔液的冷却影响。
流道的设计应使其能够迅速将熔液引导到模腔中,并确保流动的速度和温度均匀。
这样可以避免熔液在流动过程中过度冷却而凝固,造成流道堵塞或铸件表面不光滑的问题。
同时,流道设计还需要考虑到金属熔液的流动阻力。
流道的长度和弯曲度越小,流经流道的金属熔液的阻力就越小,流动能力就越好。
因此,在流道设计中应尽量减少流道的弯曲和咽喉,使金属熔液能够顺畅地流动。
另外,在流道设计中,浇口的位置和形状也是需要注意的。
浇口的位置应选择在铸件底部或靠近铸件底部的位置,以充分利用重力来推动金属熔液流动。
浇口的形状应选择为喇叭口状或倒喇叭口状,以便于金属熔液的顺畅流动和避免气泡和杂质的混入。
在进行流道设计时,还需要综合考虑模腔的结构和形状。
流道设计应适应模腔的形状,保证金属熔液能够均匀地流入并充填整个模腔。
同时,流道的尺寸也需要根据铸件的尺寸和结构来进行合理确定,以保证铸件的充填性能和凝固性能。
需要注意的是,流道设计还应结合具体的铸造材料和生产工艺来进行综合考虑和设计。
不同的铸造材料和生产工艺对流道的要求和设计方法也会有所不同。
总结起来,压铸模流道设计的目标是使金属熔液在模腔中充分流动,保证铸件的充填性能和凝固性能。
良好的流道设计能够避免铸件缺陷,提高生产效率和质量。
浇口位置选择原则

浇口位置选择原则浇口位置选择是指在铸件制造过程中进行浇注的位置选择。
由于铸件形状和毛坯布置的差异,浇口位置的选择将直接影响到铸造工艺的质量和效率。
因此,合理选择浇口位置对于保证铸造品质量、提高生产效率和降低生产成本至关重要。
1.保证浇注顺利:浇口位置应选择在铸件上最易流动的地方,以确保铸炉中金属液能够顺利流入模腔内。
通常情况下,浇口位置应尽量选择在铸件高部位或尖角处,避免选择在铸件底面或圆滑曲面上。
此外,还要避免浇口位置选择在铸件内部造成飞溅金属液的地方,以防止金属溅出造成损伤。
2.保证铸件质量:浇口位置对于避免铸件内部缺陷和夹杂物的形成非常重要。
浇口位置应选择在铸件上靠近毛坯布置中心线的位置,以避免金属液在流动过程中产生不必要的湍流和气泡。
此外,还要避免选择在铸件表面容易形成气孔和缺陷的地方,如焊接接头和锐角处。
3.提高铸造效率:浇口位置的选择还应考虑到生产效率的问题。
合理选择浇口位置可以减少金属液的流动阻力和浇注时间,并且降低金属液与空气接触的面积,减少氧化损失。
因此,浇口位置应选择在铸件上流线型最短的位置,以提高浇注速度和铸造效率。
4.减少铸造变形:浇口位置的选择还应考虑到减少铸件变形的问题。
浇口的位置选择应使金属液能够均匀地填充模腔,避免出现局部过热或过冷的现象。
此外,还需要注意避免浇口位置选择在铸件上易变形的地方,如薄壁处和内外角处,以减少铸造变形的发生。
5.方便浇注和排气:浇口位置的选择还应便于浇注和排气。
浇口位置应选择在模腔与金属液进口管相连的地方,以减少金属液的喷溅和溅出。
同时,还需要确保浇口位置不会被气体和砂化物堵塞,以保证金属液可以顺利地流入模腔内。
总之,浇口位置选择原则主要包括保证浇注顺利、保证铸件质量、提高铸造效率、减少铸造变形和方便浇注和排气等方面。
在实际操作中,需要根据具体的铸造工艺和铸件形状进行合理选择,以确保铸造工艺的质量和效率。
压铸件浇口位置
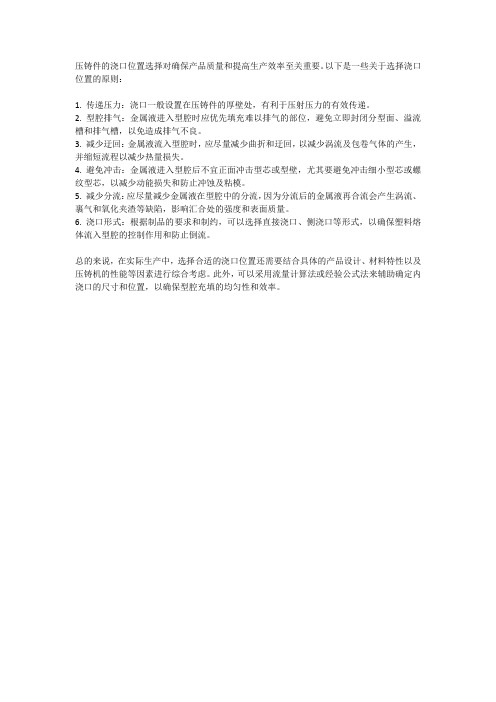
压铸件的浇口位置选择对确保产品质量和提高生产效率至关重要。
以下是一些关于选择浇口位置的原则:
1. 传递压力:浇口一般设置在压铸件的厚壁处,有利于压射压力的有效传递。
2. 型腔排气:金属液进入型腔时应优先填充难以排气的部位,避免立即封闭分型面、溢流槽和排气槽,以免造成排气不良。
3. 减少迂回:金属液流入型腔时,应尽量减少曲折和迂回,以减少涡流及包卷气体的产生,并缩短流程以减少热量损失。
4. 避免冲击:金属液进入型腔后不宜正面冲击型芯或型壁,尤其要避免冲击细小型芯或螺纹型芯,以减少动能损失和防止冲蚀及粘模。
5. 减少分流:应尽量减少金属液在型腔中的分流,因为分流后的金属液再合流会产生涡流、裹气和氧化夹渣等缺陷,影响汇合处的强度和表面质量。
6. 浇口形式:根据制品的要求和制约,可以选择直接浇口、侧浇口等形式,以确保塑料熔体流入型腔的控制作用和防止倒流。
总的来说,在实际生产中,选择合适的浇口位置还需要结合具体的产品设计、材料特性以及压铸机的性能等因素进行综合考虑。
此外,可以采用流量计算法或经验公式法来辅助确定内浇口的尺寸和位置,以确保型腔充填的均匀性和效率。
压铸模具设计浇道流道设计精讲教程

压铸模具设计浇道流道设计精讲教程压铸模具是压铸工艺中的一种重要工具,其设计的好坏直接影响到产品的质量和生产效率。
而浇道流道设计则是压铸模具设计中的关键环节之一,它决定了熔化金属流动的路径和方式,直接影响到铸件的充型性能和凝固过程。
在压铸模具设计中,浇道是指从熔化金属进入模腔的通道,流道是指熔化金属在模具中流动的路径。
浇道流道的设计合理与否直接关系到铸件的充型质量和凝固性能。
因此,设计师在进行浇道流道设计时需要考虑以下几个方面:1. 浇道流道的位置:浇道流道的位置应尽量选择在铸件较厚的部位,以便熔化金属在流动过程中能够充分填充铸件细节,避免铸件出现空隙和缺陷。
2. 浇道流道的长度:浇道流道的长度应尽量短,以减小熔化金属的流动阻力,提高充型速度。
同时,短浇道流道还能减少熔化金属在流动过程中的冷却损失,提高铸件的凝固性能。
3. 浇道流道的截面积:浇道流道的截面积应根据铸件的充型需求和熔化金属的流动特性进行合理选择。
截面积过小会增加金属的流动阻力,导致充型不良;截面积过大则会增加金属的冷却损失,影响铸件的凝固性能。
4. 浇道流道的形状:浇道流道的形状应尽量简洁,避免出现过多的转弯和分支,以减小金属流动的阻力和能量损失。
同时,浇道流道的形状也要考虑到铸件的结构特点和充型需求,以保证熔化金属能够充分填充铸件细节。
在进行浇道流道设计时,还需要考虑到以下几个问题:1. 浇道流道的位置和长度如何确定:浇道流道的位置和长度的确定需要考虑到铸件的结构特点、充型需求和凝固性能。
一般来说,浇道流道的位置应选择在铸件较厚的部位,长度应尽量短,以提高充型速度和凝固性能。
2. 浇道流道的截面积如何确定:浇道流道的截面积的确定需要考虑到铸件的充型需求和熔化金属的流动特性。
一般来说,截面积应根据铸件的充型速度和凝固性能进行合理选择,过小会增加金属的流动阻力,过大则会增加金属的冷却损失。
3. 浇道流道的形状如何确定:浇道流道的形状的确定需要考虑到金属流动的阻力和能量损失。
浇注位置的选择原则

浇注位置的选择原则
合金钢铸件浇注时,需要选择合适的位置。
如果位置不好,会对铸件质量产生不好的影响。
所以,要选择合适的浇注位置。
另外,记住选择浇注位置的原则:
1.合金钢铸件的重要加工面或主要加工面朝下或在侧面:浇注时,金属液中的气体、熔渣和铸型中的砂粒会上浮,可能造成铸件上部出现气孔、夹渣、砂眼等缺陷,而铸件厂家生产的铸件下部组织会比较致密。
机床床身的浇注位置要面朝下导轨,以保证这个重要工作面的质量。
圆周面质量要求高,垂直浇注方案可以使圆周面在侧面,保证质量均匀。
2.大平面向下或倾斜浇注:浇注时热的熔融金属对铸型上部产生强烈的热辐射,使顶面砂型鼓包、拱起甚至开裂,造成大平面出现夹砂、砂眼等缺陷。
采用大平面向下或倾斜浇注的方法,可以避免大平面的铸造缺陷。
3.合金钢铸件的薄壁朝下、侧立或倾斜:为防止铸件薄壁出现冷隔和铸造缺陷,面积较大的薄壁应放在铸件下部或侧壁或倾斜位置。
4.大部分厚度应放在分型面的顶部或侧面。
主要目的是方便粗冒口的加料。
合金钢铸件主要用于重大设备,性能良好,有时会出现缩孔。
那么铸造缩孔的原因是什么呢?
1.模具的工作温度控制不符合定向凝固的要求。
2.涂层选择不当,不同部位涂层厚度控制不好。
3.合金钢铸件在模具中的位置设计不合理。
4.浇注和冒口的设计未能起到足够的补缩作用。
5.合金钢铸件的浇注温度过低或过高。
铸件浇道、排气系统的设计注意事项
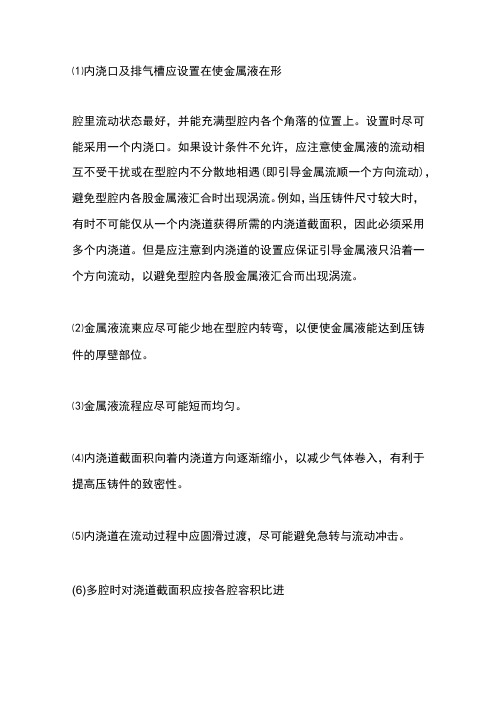
⑴内浇口及排气槽应设置在使金属液在形腔里流动状态最好,并能充满型腔内各个角落的位置上。
设置时尽可能采用一个内浇口。
如果设计条件不允许,应注意使金属液的流动相互不受干扰或在型腔内不分散地相遇(即引导金属流顺一个方向流动),避免型腔内各股金属液汇合时出现涡流。
例如,当压铸件尺寸较大时,有时不可能仅从一个内浇道获得所需的内浇道截面积,因此必须采用多个内浇道。
但是应注意到内浇道的设置应保证引导金属液只沿着一个方向流动,以避免型腔内各股金属液汇合而出现涡流。
⑵金属液流柬应尽可能少地在型腔内转弯,以便使金属液能达到压铸件的厚壁部位。
⑶金属液流程应尽可能短而均匀。
⑷内浇道截面积向着内浇道方向逐渐缩小,以减少气体卷入,有利于提高压铸件的致密性。
⑸内浇道在流动过程中应圆滑过渡,尽可能避免急转与流动冲击。
(6)多腔时对浇道截面积应按各腔容积比进行分段减少。
⑺型腔中的空气和润滑剂挥发的气体,应由流入的金属液推到排气槽处,然后从排气槽处逸出型腔。
特别是金属液的流动不应将气体留在盲孔内或过早地堵塞排气槽。
(8)金属流束不应在散热不良处形成热冲击。
(9)对带有筋的压铸件,应尽可能地让金属流顺筋的方向流动。
(IO)应避免金属液直接冲刷容易损坏的模具部分和型芯。
不可避免时,应在内浇道上设置隔离带,避免热冲击。
(11)通常内浇道愈宽愈厚,非均匀流动的危险也愈大。
应尽量不要采用过厚的内浇口,避免切除内浇道时产生变形。
(12)型腔的排气溢流槽是为了排除铸造时最初喷入的金属液,并且使模具的温度一致。
溢流槽设在铸型容易存气的位置,作为排出气体用,改善金属液的流动状态,将金属液导向型腔的各个角落,以得到良好的铸造表面。
排气槽有连接在溢流槽与集渣包前面的,也有与型腔直接连接的。
设计时应注意:①排气槽的总截面积应大致相当于内浇道截面积。
②分型面上的排气槽的位置是根据型腔内金属液流动状态而确定的。
排气槽最好设计成弯曲状,而不是直通状,以防止金属液外喷伤人。
合理选择浇口位置 改善压铸件质量
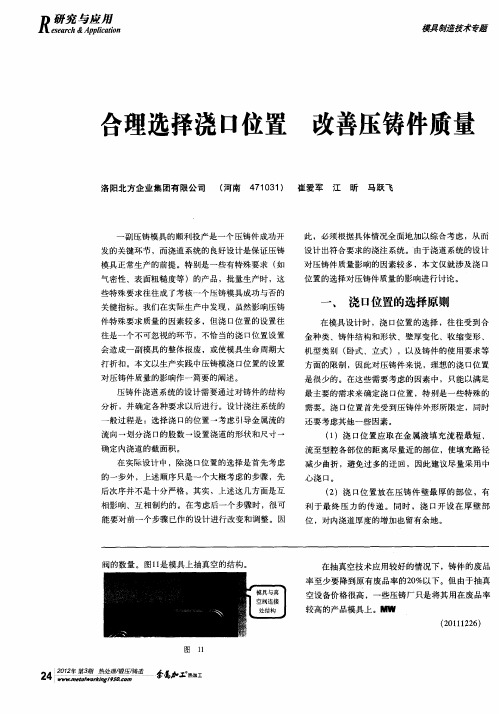
例 起 到 小 幅 改 善 ,不 能 从 根 本 上 解 决 铸 件 漏 气 的 问 题 。 为 此 , 决 定 对 该 模 具 的 浇 口位 置 进 行 更 改 , 如
图4 示 。 所
体 ,该产 品采 用ADC1 2合金 ,在DCC 0 压铸机 40
压铸 件 ,内 浇道 应 设 置 在金 属 液最 终 都能 保 持 压 力
的部 位 。
由上述分析 可知 ,该模具 的浇 口位 置设计 欠 妥 ,导致 了铸件气 密性检测 不合格 ,通过 调整 工
艺 参 数 仅 能 够 对 漏 气 的 比
二,浇 口位置影响压铸件质量实ቤተ መጻሕፍቲ ባይዱ
1 汽车 空调压缩机下壳体 .
是很少 的。在这些需要考虑的因素 中,只能以满足
最主要的需求来确定浇 口位置 ,特别是一些特殊的 需要。浇 1位置首先受到压铸件外形所限定,同时 = I 还要考虑其他一些因素。
般过程是 :选择浇 口的位置一考虑 引导金属流的
流向一划分浇 1的股数 一设置浇道的形状和尺寸一 : 1 确定 内浇道的截面积 。 在实际设计 中,除浇 口位置的选择是首先考虑
的一 步 外 ,上 述 顺序 只 是一 个 大 概考 虑 的步 骤 ,先
( )浇 I位置应取在金 属液填充流程最短 、 1 = I 流至型腔各部位的距离尽量近的部位 ,使填充路径
减少 曲折 ,避免过 多的迂回 ,因此建议尽量采用中
心 浇 口。
后次序并不是十分严格 。其实 ,上述这几方面是互
R
合理选择浇口位置 改善压铸件质量
洛 阳北方企业集 团有 限公司 ( 河南 4 1 3 ) 崔爱军 7 1 0 江 昕 马跃飞
铸件内浇道的基本设计原则
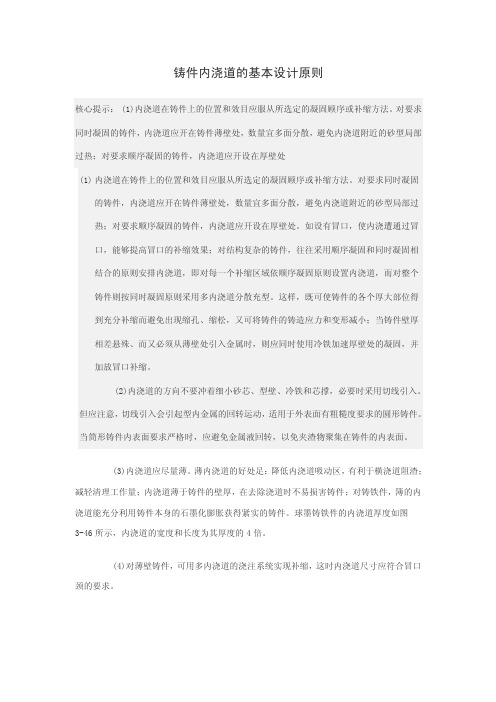
铸件内浇道的基本设计原则核心提示: (1)内浇道在铸件上的位置和效目应服从所选定的凝固顾序或补缩方法。
对要求同时凝固的铸件,内浇道应开在铸件薄壁处,数量宜多面分散,避免内浇道附近的砂型局部过热;对要求顺序凝固的铸件,内浇道应开设在厚壁处(1)内浇道在铸件上的位置和效目应服从所选定的凝固顾序或补缩方法。
对要求同时凝固的铸件,内浇道应开在铸件薄壁处,数量宜多面分散,避免内浇道附近的砂型局部过热;对要求顺序凝固的铸件,内浇道应开设在厚壁处。
如设有冒口,使内浇遭通过冒口,能够提高冒口的补缩效果;对结构复杂的铸件,往往采用顺序凝固和同时凝固相结合的原则安排内浇道,即对每一个补缩区域依顺序凝固原则设置内浇道,而对整个铸件则按同时凝固原则采用多内浇道分散充型。
这样,既可使铸件的各个厚大部位得到充分补缩而避免出现缩孔、缩松,又可将铸件的铸造应力和变形减小;当铸件壁厚相差悬殊、而又必须从薄壁处引入金属时,则应同时使用冷铁加速厚壁处的凝固,并加放冒口补缩。
(2)内浇道的方向不要冲着细小砂芯、型壁、冷铁和芯撑,必要时采用切线引入。
但应注意,切线引入会引起型内金属的回转运动,适用于外表面有粗糙度要求的圆形铸件。
当筒形铸件内表面要求严格时,应避免金属液回转,以免夹渣物聚集在铸件的内表面。
(3)内浇道应尽量薄。
薄内浇道的好处足:降低内浇道吸动区,有利于横浇道阻渣;减轻清理工作量;内浇道薄于铸件的壁厚,在去除浇道时不易损害铸件;对铸铁件,簿的内浇道能充分利用铸件本身的石墨化膨胀获得紧实的铸件。
球墨铸铁件的内浇道厚度如图3-46所示,内浇道的宽度和长度为其厚度的4倍。
(4)对薄壁铸件,可用多内浇道的浇注系统实现补缩,这时内浇道尺寸应符合冒口颈的要求。
(5)内浇道避免开设在铸件品质要求很高的部位,以防止金相组织粗大。
对受求耐压、防渗漏的管类件,内浇道通常开在法兰处,以防止管壁处出现缩松;内浇道开设在加工表面上,则有利于铸件的外观。
压铸模内浇口设计
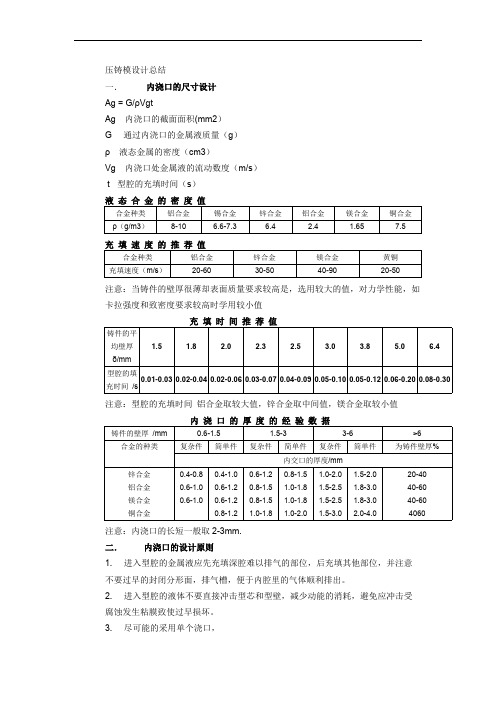
压铸模设计总结一.内浇口的尺寸设计Ag = G/ρVgtAg 内浇口的截面面积(mm2)G 通过内浇口的金属液质量(g)ρ液态金属的密度(cm3)Vg 内浇口处金属液的流动数度(m/s)t 型腔的充填时间(s)液态合金的密度值合金种类铝合金锡合金锌合金铝合金镁合金铜合金ρ(g/m3)8-10 6.6-7.3 6.4 2.4 1.657.5充填速度的推荐值合金种类铝合金锌合金镁合金黄铜充填速度(m/s)20-6030-5040-9020-50注意:当铸件的壁厚很薄却表面质量要求较高是,选用较大的值,对力学性能,如卡拉强度和致密度要求较高时学用较小值充填时间推荐值铸件的平均壁厚δ/mm1.5 1.82.0 2.3 2.53.0 3.8 5.0 6.4型腔的填充时间/s0.01-0.030.02-0.040.02-0.060.03-0.070.04-0.090.05-0.100.05-0.120.06-0.200.08-0.30注意:型腔的充填时间铝合金取较大值,锌合金取中间值,镁合金取较小值内浇口的厚度的经验数据铸件的壁厚/mm0.6-1.5 1.5-33-6>6复杂件简单件复杂件简单件复杂件简单件为铸件壁厚%合金的种类内交口的厚度/mm锌合金铝合金镁合金铜合金0.4-0.80.6-1.00.6-1.00.4-1.00.6-1.20.6-1.20.8-1.20.6-1.20.8-1.50.8-1.51.0-1.80.8-1.51.0-1.81.0-1.81.0-2.01.0-2.01.5-2.51.5-2.51.5-3.01.5-2.01.8-3.01.8-3.02.0-4.020-4040-6040-604060注意:内浇口的长短一般取2-3mm.二.内浇口的设计原则1. 进入型腔的金属液应先充填深腔难以排气的部位,后充填其他部位,并注意不要过早的封闭分形面,排气槽,便于内腔里的气体顺利排出。
铝合金压铸模具浇排设计方案
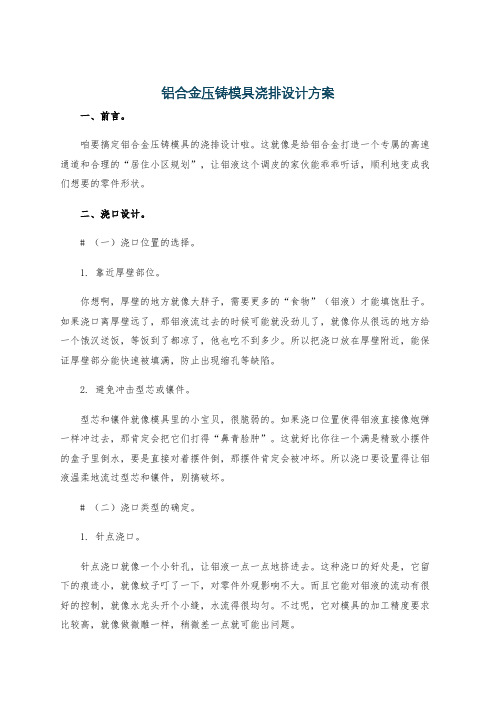
铝合金压铸模具浇排设计方案一、前言。
咱要搞定铝合金压铸模具的浇排设计啦。
这就像是给铝合金打造一个专属的高速通道和合理的“居住小区规划”,让铝液这个调皮的家伙能乖乖听话,顺利地变成我们想要的零件形状。
二、浇口设计。
# (一)浇口位置的选择。
1. 靠近厚壁部位。
你想啊,厚壁的地方就像大胖子,需要更多的“食物”(铝液)才能填饱肚子。
如果浇口离厚壁远了,那铝液流过去的时候可能就没劲儿了,就像你从很远的地方给一个饿汉送饭,等饭到了都凉了,他也吃不到多少。
所以把浇口放在厚壁附近,能保证厚壁部分能快速被填满,防止出现缩孔等缺陷。
2. 避免冲击型芯或镶件。
型芯和镶件就像模具里的小宝贝,很脆弱的。
如果浇口位置使得铝液直接像炮弹一样冲过去,那肯定会把它们打得“鼻青脸肿”。
这就好比你往一个满是精致小摆件的盒子里倒水,要是直接对着摆件倒,那摆件肯定会被冲坏。
所以浇口要设置得让铝液温柔地流过型芯和镶件,别搞破坏。
# (二)浇口类型的确定。
1. 针点浇口。
针点浇口就像一个小针孔,让铝液一点一点地挤进去。
这种浇口的好处是,它留下的痕迹小,就像蚊子叮了一下,对零件外观影响不大。
而且它能对铝液的流动有很好的控制,就像水龙头开个小缝,水流得很均匀。
不过呢,它对模具的加工精度要求比较高,就像做微雕一样,稍微差一点就可能出问题。
2. 侧浇口。
侧浇口就比较实在,像个小侧门。
铝液从侧面流进去,比较简单直接。
它适合一些形状不是特别复杂的零件。
这种浇口加工起来比较容易,就像盖个普通的小房子,不需要太多的技巧。
但是它可能会在零件表面留下比较明显的浇口痕迹,就像脸上有个小疤一样,影响美观。
三、流道设计。
# (一)主流道设计。
1. 尺寸确定。
主流道就像高速公路的主干道,要足够宽敞才能让铝液大军顺利通过。
一般来说,主流道的直径要根据零件的大小和所需铝液的量来确定。
如果零件大,需要的铝液多,主流道就得粗一点,就像大货车要走大路一样。
要是主流道太细了,铝液就会堵在那里,就像一群人挤在小胡同里,谁也走不动。
压铸模流道与浇口设计
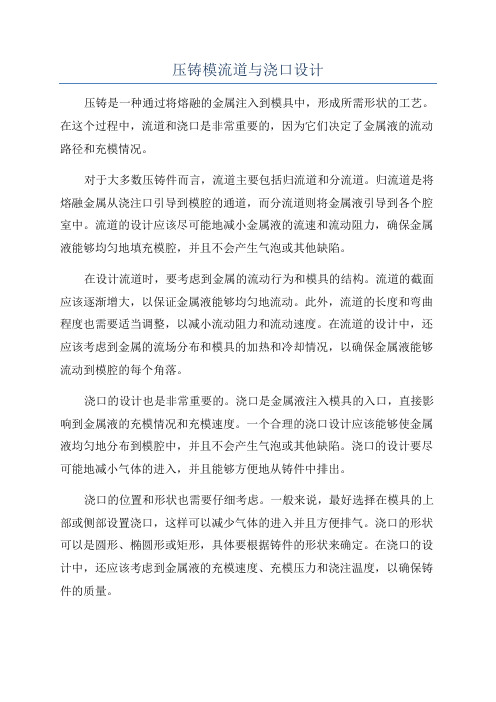
压铸模流道与浇口设计压铸是一种通过将熔融的金属注入到模具中,形成所需形状的工艺。
在这个过程中,流道和浇口是非常重要的,因为它们决定了金属液的流动路径和充模情况。
对于大多数压铸件而言,流道主要包括归流道和分流道。
归流道是将熔融金属从浇注口引导到模腔的通道,而分流道则将金属液引导到各个腔室中。
流道的设计应该尽可能地减小金属液的流速和流动阻力,确保金属液能够均匀地填充模腔,并且不会产生气泡或其他缺陷。
在设计流道时,要考虑到金属的流动行为和模具的结构。
流道的截面应该逐渐增大,以保证金属液能够均匀地流动。
此外,流道的长度和弯曲程度也需要适当调整,以减小流动阻力和流动速度。
在流道的设计中,还应该考虑到金属的流场分布和模具的加热和冷却情况,以确保金属液能够流动到模腔的每个角落。
浇口的设计也是非常重要的。
浇口是金属液注入模具的入口,直接影响到金属液的充模情况和充模速度。
一个合理的浇口设计应该能够使金属液均匀地分布到模腔中,并且不会产生气泡或其他缺陷。
浇口的设计要尽可能地减小气体的进入,并且能够方便地从铸件中排出。
浇口的位置和形状也需要仔细考虑。
一般来说,最好选择在模具的上部或侧部设置浇口,这样可以减少气体的进入并且方便排气。
浇口的形状可以是圆形、椭圆形或矩形,具体要根据铸件的形状来确定。
在浇口的设计中,还应该考虑到金属液的充模速度、充模压力和浇注温度,以确保铸件的质量。
在流道和浇口的设计中,还需要考虑到模具的制造成本和生产效率。
流道和浇口的设计应该尽可能地简单和经济,同时也要能够满足产品的质量要求。
此外,在模具的制造过程中,还需要考虑到流道和浇口的冷却和加热情况,以确保模具的寿命和稳定性。
总之,流道和浇口的设计是压铸工艺中非常重要的环节。
一个合理的流道和浇口设计可以确保金属液能够均匀地填充到模腔中,并且不会产生气泡或其他缺陷。
同时,流道和浇口的设计还需要考虑到模具的制造成本和生产效率。
通过合理的流道和浇口设计,可以提高压铸件的质量和性能。
压铸的浇口计算公式
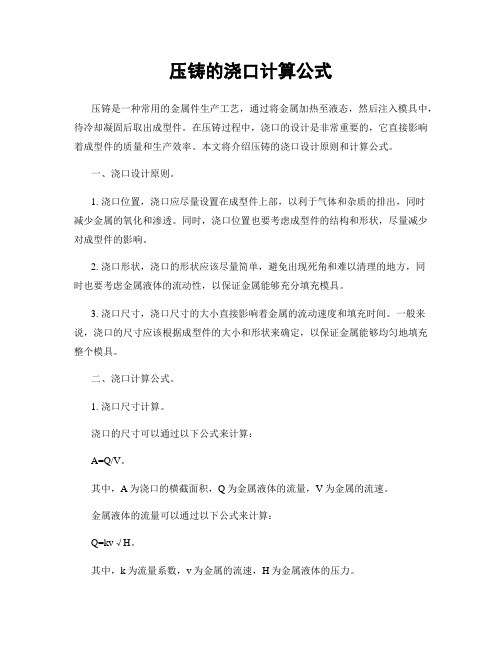
压铸的浇口计算公式压铸是一种常用的金属件生产工艺,通过将金属加热至液态,然后注入模具中,待冷却凝固后取出成型件。
在压铸过程中,浇口的设计是非常重要的,它直接影响着成型件的质量和生产效率。
本文将介绍压铸的浇口设计原则和计算公式。
一、浇口设计原则。
1. 浇口位置,浇口应尽量设置在成型件上部,以利于气体和杂质的排出,同时减少金属的氧化和渗透。
同时,浇口位置也要考虑成型件的结构和形状,尽量减少对成型件的影响。
2. 浇口形状,浇口的形状应该尽量简单,避免出现死角和难以清理的地方,同时也要考虑金属液体的流动性,以保证金属能够充分填充模具。
3. 浇口尺寸,浇口尺寸的大小直接影响着金属的流动速度和填充时间。
一般来说,浇口的尺寸应该根据成型件的大小和形状来确定,以保证金属能够均匀地填充整个模具。
二、浇口计算公式。
1. 浇口尺寸计算。
浇口的尺寸可以通过以下公式来计算:A=Q/V。
其中,A为浇口的横截面积,Q为金属液体的流量,V为金属的流速。
金属液体的流量可以通过以下公式来计算:Q=kv√H。
其中,k为流量系数,v为金属的流速,H为金属液体的压力。
金属的流速可以通过以下公式来计算:v=√(2gH)。
其中,g为重力加速度,H为金属液体的压力。
2. 浇口位置计算。
浇口的位置可以通过以下公式来计算:h=(2/3)√(2gh)。
其中,h为浇口的高度,g为重力加速度,h为金属液体的压力。
三、浇口设计实例。
假设有一个直径为100mm的圆形成型件,需要设计浇口。
首先,我们可以通过以下公式来计算浇口的尺寸:A=Q/V。
假设金属液体的流速v为1m/s,金属液体的压力H为2m,流量系数k为0.9,则可以计算得出金属液体的流量Q为:Q=0.91√2=1.27m²/s。
根据圆形成型件的面积计算得出A=πr²=3.145050=7850mm²。
将流量Q和横截面积A代入浇口尺寸计算公式中,可以得出浇口的尺寸为:V=Q/A=1.27/7850=0.000161m/s。
怎么样来设计压铸模具的进胶口呢
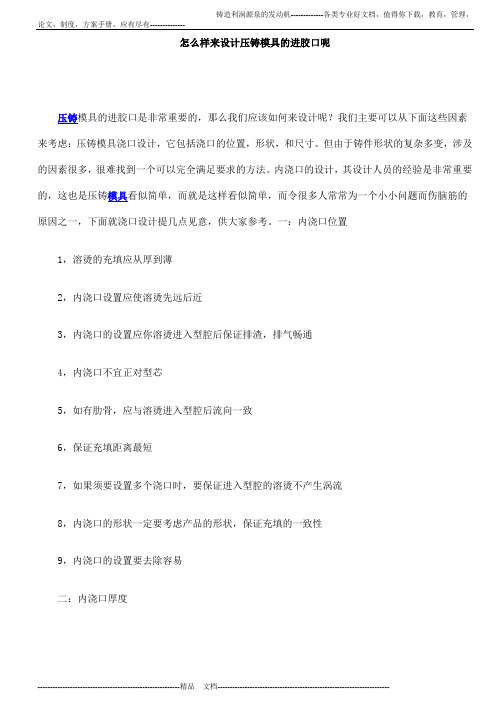
怎么样来设计压铸模具的进胶口呢
压铸模具的进胶口是非常重要的,那么我们应该如何来设计呢?我们主要可以从下面这些因素来考虑:压铸模具浇口设计,它包括浇口的位置,形状,和尺寸。
但由于铸件形状的复杂多变,涉及的因素很多,很难找到一个可以完全满足要求的方法。
内浇口的设计,其设计人员的经验是非常重要的,这也是压铸模具看似简单,而就是这样看似简单,而令很多人常常为一个小小问题而伤脑筋的原因之一,下面就浇口设计提几点见意,供大家参考。
一:内浇口位置
1,溶烫的充填应从厚到薄
2,内浇口设置应使溶烫先远后近
3,内浇口的设置应你溶烫进入型腔后保证排渣,排气畅通
4,内浇口不宜正对型芯
5,如有肋骨,应与溶烫进入型腔后流向一致
6,保证充填距离最短
7,如果须要设置多个浇口时,要保证进入型腔的溶烫不产生涡流
8,内浇口的形状一定要考虑产品的形状,保证充填的一致性
9,内浇口的设置要去除容易
二:内浇口厚度
内浇口厚度是与产品的壁厚有很大的关系,一般是与壁厚成正比,告诉大家一经验公式供参考,t=T/3±0。
5,t为浇口的厚度,T为产品的壁厚,但这不是所有的情况都适用哦,它还要考虑通过浇口的溶烫的体积,分析着用啊,
三:内浇道的形状
内浇道的形状,不管是扇形,漏斗形,锥形,但有点是非常重要的,那就是保证溶烫经过流道不能产生涡流。
几种形状可以单用,可以混用。
压铸模的浇口位置的选择对铸件的影响
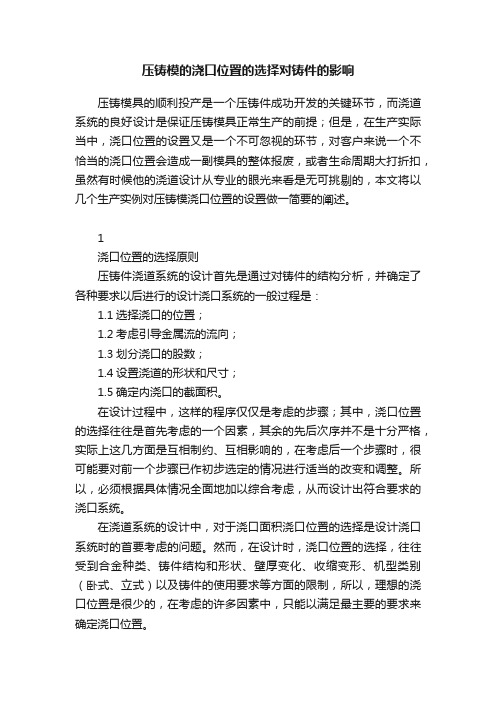
压铸模的浇口位置的选择对铸件的影响压铸模具的顺利投产是一个压铸件成功开发的关键环节,而浇道系统的良好设计是保证压铸模具正常生产的前提;但是,在生产实际当中,浇口位置的设置又是一个不可忽视的环节,对客户来说一个不恰当的浇口位置会造成一副模具的整体报废,或者生命周期大打折扣,虽然有时候他的浇道设计从专业的眼光来看是无可挑剔的,本文将以几个生产实例对压铸模浇口位置的设置做一简要的阐述。
1浇口位置的选择原则压铸件浇道系统的设计首先是通过对铸件的结构分析,并确定了各种要求以后进行的设计浇口系统的一般过程是:1.1选择浇口的位置;1.2考虑引导金属流的流向;1.3划分浇口的股数;1.4设置浇道的形状和尺寸;1.5确定内浇口的截面积。
在设计过程中,这样的程序仅仅是考虑的步骤;其中,浇口位置的选择往往是首先考虑的一个因素,其余的先后次序并不是十分严格,实际上这几方面是互相制约、互相影响的,在考虑后一个步骤时,很可能要对前一个步骤已作初步选定的情况进行适当的改变和调整。
所以,必须根据具体情况全面地加以综合考虑,从而设计出符合要求的浇口系统。
在浇道系统的设计中,对于浇口面积浇口位置的选择是设计浇口系统时的首要考虑的问题。
然而,在设计时,浇口位置的选择,往往受到合金种类、铸件结构和形状、壁厚变化、收缩变形、机型类别(卧式、立式)以及铸件的使用要求等方面的限制,所以,理想的浇口位置是很少的,在考虑的许多因素中,只能以满足最主要的要求来确定浇口位置。
在实际的设计中,浇口位置首先取决于铸件轮廓所给予能够开设的具体条件、同时,还要考虑其它一些有素,浇口位置的选择一般从专业的角度来讲需要注意以下几个方面的问题:(1).取在金属液填充流程最短,浇口位置应使填充路径减少曲折和避免过多的迂回,从而达到包卷气体少、金属流汇集处少和涡流现象少的效果。
(2)浇口位置应使金属流流至型腔各部位的距离尽量同等,从而造成金属流流至各个最远的型腔部位(指将铸件分割成若干部位)的条件相同,以达到各个分割的远离部位同时停止填充和凝固。
[整理]选择内浇口位置1
![[整理]选择内浇口位置1](https://img.taocdn.com/s3/m/75738f413d1ec5da50e2524de518964bcf84d2c0.png)
1压铸过程:清理模具~模具加热~喷刷涂料~安放嵌件~合模~浇料~压射~凝固~开模~推出取件2压力铸造:在高压的作用下将液态或者半液态金属以较高的速度填充压铸模型腔,并在压力状态下凝固结晶.3热压室压铸机:是锌合金及、铝合金等低熔点合金压铸的常用设备。
5填充模具型腔时金属流动状态:喷射及喷射流;压力流;再喷射;补缩金属流。
6金属液流动对压铸件的质量:表面质量:速度大,表面质量高;内部质量:速度小,内部缺陷少。
7压力铸造与砂型铸造特点比较:①金属模具有导热性,凝固速度快,表面层晶粒细化,高强度、耐磨性,冷却速度快,高充填速度。
②无退让性③无透气性8压铸成型与塑料注射成型的特点比较:①熔体流动性质不同:金属熔体不可压缩②熔体温度不同:压》塑③压射压力与压射速度不同:压》塑④脱模斜度和脱模力不同:压》塑⑤浇注系统不同9压铸成型:优点:1生产率高;2压铸件尺寸精度高,表面粗糙度值低;3可压铸复杂薄壁零件;4压铸件的力学性能高;5压铸件中可嵌铸其他材料零件。
缺点:1易产生气孔;2不宜小批量生产;3模具寿命低。
10压铸件的结构要求:壁厚、孔、加强筋、脱模斜度、圆角、螺纹与齿轮、嵌件。
嵌件设计原则:1与压铸件接触牢固;2在模具内有可靠的定位和正确的配合;3周围应有一定金属层厚度。
脱模斜度:1内表面脱模斜度大于外表面;2脱模斜度大~脱模力小;3脱模斜度大小:压铸件的材料、形状及型腔表面粗糙度。
11压铸合金:压铸锌合金:熔点低,密度大,铸造性能好,可压铸复杂零件,压铸时不粘模,压铸件表面易镀Cr,Ni等金属,机械切削性能好,但易老化,抗腐蚀性能不高压铸铝合金:熔点比锌合金高,密度较小,强度较高,耐磨性较好,导热,导电性能好,机械切削性能良好,易粘模压铸镁合金:密度小,机械强度高,重量轻,不易粘模,易氧化压铸铜合金:机械强度高,导热性和导电性好,密度大,熔点高,模具寿命较低12压射力:压射冲头作用于压室中金属液面上的力压射力的变化:1排气阶段:低速前进,封住压室上的入注口,推动金属液在压室中向前流动。
- 1、下载文档前请自行甄别文档内容的完整性,平台不提供额外的编辑、内容补充、找答案等附加服务。
- 2、"仅部分预览"的文档,不可在线预览部分如存在完整性等问题,可反馈申请退款(可完整预览的文档不适用该条件!)。
- 3、如文档侵犯您的权益,请联系客服反馈,我们会尽快为您处理(人工客服工作时间:9:00-18:30)。
壓鑄模設計如何選擇内澆口位置?[/
答:(1)内澆口布置應考慮鑄件的外觀取在金屬液填充流程最短鑄件壁厚最厚的部位。
(2)内澆口布置應考慮取在金屬液流進型腔不起旋渦排氣順暢部位。
(3)内澆口布置應考慮盡可能取在金屬液流不正面沖擊型芯的部位。
(4)内澆口布置應考慮取在鑄件不易變形的部位。
(5)内澆口布置應考慮設置在鑄件成形後易去除澆口或沖切澆口部位。
(6)對于不允許有氣孔存在鑄件,内澆口應設置在金屬液始終都能保持壓力部位。