生产加工工艺通用规范
生产加工工艺通用规范

生产加工工艺通用规范一、引言生产加工工艺是制造业中不可或缺的环节,它涵盖了各种工艺流程和操作步骤。
为了提高产品质量、保证生产效率和安全性,制定和遵守生产加工工艺通用规范是非常重要的。
本文将介绍一些常见的生产加工工艺通用规范,以期提供指导和参考。
二、材料准备1. 材料选择:根据产品要求和设计规范,选用合适的材料及其数量。
2. 材料储存:材料应储存在干燥、通风和无腐蚀性气体的仓库中,避免阳光直射和潮湿环境。
3. 材料检验:对于每批材料,进行外观、尺寸、质量等方面的严格检验,确保符合标准要求。
三、工艺流程1. 工序划分:根据产品的设计和工艺要求,合理划分工序,明确每个工序的具体任务和顺序。
2. 工序操作规范:针对每个工序,制定详细的操作规范,包括工艺参数、设备设置、操作步骤等内容。
3. 工序监控:在生产过程中,对每个工序进行实时监控和记录,确保工艺的准确执行和结果的可追溯性。
四、设备使用和维护1. 设备选择:选用符合产品要求的设备,并确保其性能稳定、可靠。
2. 设备操作规范:制定设备操作规范,包括开机、关机、调整参数等操作步骤,要求操作人员按规范进行操作。
3. 设备维护:定期维护设备,保持其正常运转状态,及时修复故障,延长使用寿命。
五、质量控制1. 检验方法:制定符合产品特点和要求的检验方法,包括外观检查、尺寸测量、材料分析等。
2. 抽样原则:根据生产批次和数量,确定合适的抽样方案,确保样本的代表性和统计可靠性。
3. 不合格品处理:对于不合格品,制定相应的处理措施,如修复、返工或报废,并记录其处理过程。
六、安全生产1. 安全教育:对相关的岗位员工进行安全教育和培训,重点培养其安全意识和操作技能。
2. 安全设施:按照国家标准和规范,配置必要的安全设施,如防护网、灭火器等,确保生产现场的安全性。
3. 事故报告:对于发生的事故和安全事件,及时进行记录和报告,并采取措施防止类似事件再次发生。
七、环保要求1. 废物处理:制定废物处理方案,按照环保法规要求,分类处理废物,最大限度地减少对环境的污染。
生产加工工艺通用规范

加工通用工艺规范1.目旳及合用范围为了保证产品质量得到保证,特制定本制度。
合用于在企业既有设备状况下旳生产加工工艺旳制定。
2.职责2.1技术部负责生产加工工艺旳编制;2.2技术部负责人负责生产加工工艺旳审批;2.3生产车间操作人员按编制旳有效旳加工工艺加工产品。
3. 放样工艺在钢构造制造中,放样工作是非常重要旳一环,由于所有零件尺寸和形状都必须先行放样,然后依样进行加工,因此放样工作旳精确与否直接影响产品旳质量。
3.1先应仔细阅读技术规定及阐明,逐一查对图纸之间旳尺寸和方向等,发既有疑问之处,应于技术部联络处理。
3.2备好样板纸作样板,在样板台上放样需准备尺、石笔、粉线、划针、样冲。
3.3放样以1:1旳比例,零件尺寸较小时,直接在样板纸上放样,否则在样板台上弹出大样,当大样尺寸较大时,可分段弹出。
3.4在样板台上放样时,以构件旳某一水平线和垂直线为基准,弹出十字线,然后依次十字线划出其他各点及线,并在节点旁注上尺寸,以备复查及自检。
用划针划上连接线并用锋利旳样冲将交点敲出,或者直接用样冲在样板将交点敲出。
3.5样过程中碰到技术问题,应于技术部联络处理。
3.6样过程中应按图纸进行自检。
4.号料工艺4.1号料前首先根据料单检查清点样板,弄清号料数量。
4.2准备并检查多种使用工具,号料前必须理解原材料旳钢号及规格,检查原材料旳质量,如有疤痕、裂纹、厚度局限性等现象应调换材料。
号料旳刚刚必须摆放平稳,不得弯曲。
4.3注意工作地点四面旳安全。
4.4不一样规格,不一样钢号旳零件应分别号料,并根据先大后小旳次序号料。
4.5形样板号料应先检查原材料钢板两边与否垂直,若不垂直,要划好垂直线,在号料。
4.6不得使用一次剪切宽度超过剪板机旳宽度。
4.7号料过程中,应随时在样板上记录号料旳数量,并妥善保管好样板。
5. 切割通用工艺5.1钢板5.1.1厚度不小于13mm旳应进行气割;厚度不不小于13mm旳应进行剪切;5.1.2剪切工艺装备:剪板机。
机械加工通用工艺规范

GB/T 4249 产品几何技术规范( GPS) 公差原则GB/T 5796.4 梯形螺纹第4 部分:公差4. 术语和定义GB/T 1182-2008 给出的术语和定义及下列术语和定义适用于本文件。
4.1 切削加工用切削工具(包括刀具、磨具和磨料)把坯料或工件上多余的材料层切去成为切屑,使工件获得规定的几何形状、尺寸和表面质量的加工方法。
包括车削、铣削、刨削、磨削、拉削、钻孔、扩孔、铰孔、研磨、珩磨、抛光、超精加工及由它们组成的自动技术、数控技术、成组技术、组合机床、流水线、自动线。
4.2 特种加工特种加工亦称“非传统加工”或“现代加工方法”,泛指用电能、热能、光能、电化学能、化学能、声能及特殊机械能等能量达到去除或增加材料的加工方法,从而实现材料被去除、变形、改变性能或被镀覆等。
公司现有的特殊加工方法有线切割加工、激光加工。
4.3 A级表面:产品非常重要的装饰表面,即产品使用时始终可以看到的表面。
4.4 B级表面:产品的内表面或产品不翻动时客户偶尔能看到的表面。
4.5 C级表面:仅在产品翻动时才可见的表面,或产品的内部零件。
5. 机加工操作要求5.1. 下料5.1.1 看清图纸、工艺和下料单上的材质、规格、尺寸及数量等。
5.1.2 核对材质、规格与下料单要求是否相符。
材料代用必须严格履行代用手续。
5.1.3 查看材料外观质量(疤痕、夹层、变形、锈蚀等)是否符合有关质量规定。
5.1.4 将不同工件所用相同材质、规格的料单集中,考虑能否套料。
5.1.5 号料1. 端面不规则的型钢、钢板、管材等材料号料时必须将不规则部分让出。
钢材表面上如有不平、弯曲、扭曲、波浪等缺陷,在下料切割和成形加工之前,必须对有缺陷的钢材进行矫正。
2. 号料时,应考虑下料方法,留出切口余量。
3. 有下料定尺挡板的设备,下料前要按尺寸要求调准定尺挡板,并保证工作可靠,下料时材料靠实挡板。
5.2 加工前的准备5.2.1 操作者接到加工任务后,应熟读产品图样。
通用工艺守则全解
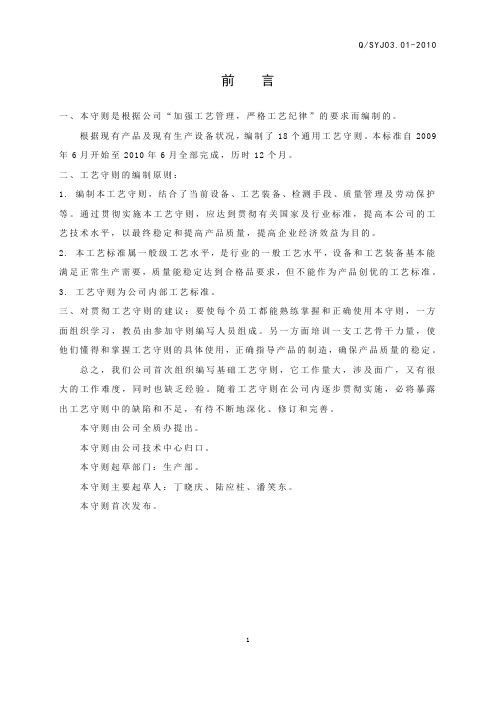
Q/SYJ03.01-2010前言一、本守则是根据公司“加强工艺管理,严格工艺纪律”的要求而编制的。
根据现有产品及现有生产设备状况,编制了18个通用工艺守则。
本标准自2009年6月开始至2010年6月全部完成,历时12个月。
二、工艺守则的编制原则:1. 编制本工艺守则,结合了当前设备、工艺装备、检测手段、质量管理及劳动保护等。
通过贯彻实施本工艺守则,应达到贯彻有关国家及行业标准,提高本公司的工艺技术水平,以最终稳定和提高产品质量,提高企业经济效益为目的。
2. 本工艺标准属一般级工艺水平,是行业的一般工艺水平,设备和工艺装备基本能满足正常生产需要,质量能稳定达到合格品要求,但不能作为产品创优的工艺标准。
3. 工艺守则为公司内部工艺标准。
三、对贯彻工艺守则的建议:要使每个员工都能熟练掌握和正确使用本守则,一方面组织学习,教员由参加守则编写人员组成。
另一方面培训一支工艺骨干力量,使他们懂得和掌握工艺守则的具体使用,正确指导产品的制造,确保产品质量的稳定。
总之,我们公司首次组织编写基础工艺守则,它工作量大,涉及面广,又有很大的工作难度,同时也缺乏经验。
随着工艺守则在公司内逐步贯彻实施,必将暴露出工艺守则中的缺陷和不足,有待不断地深化、修订和完善。
本守则由公司全质办提出。
本守则由公司技术中心归口。
本守则起草部门:生产部。
本守则主要起草人:丁晓庆、陆应柱、潘笑东。
本守则首次发布。
1通用工艺守则总则Q/SYJ03.01-2010 1 范围本守则规定了产品加工制造过程中主要专业性工艺应遵守的基本规则。
本守则适用于生产工艺准备和产品的加工。
2 工艺技术准备2.1按本守则的相应内容根据所要加工的产品图样及技术要求编制产品工艺文件,规定具体工艺要求。
2.2 按工艺要求设计或选用所需使用的设备和工艺装备。
3 操作前的准备3.1 操作者接到加工任务后,应检查加工所需的产品图样、工艺文件和有关技术资料是否齐全。
3.2 要看懂、看清产品图样、工艺文件和有关资料,了解相应工艺要求。
机械加工通用技术要求规范
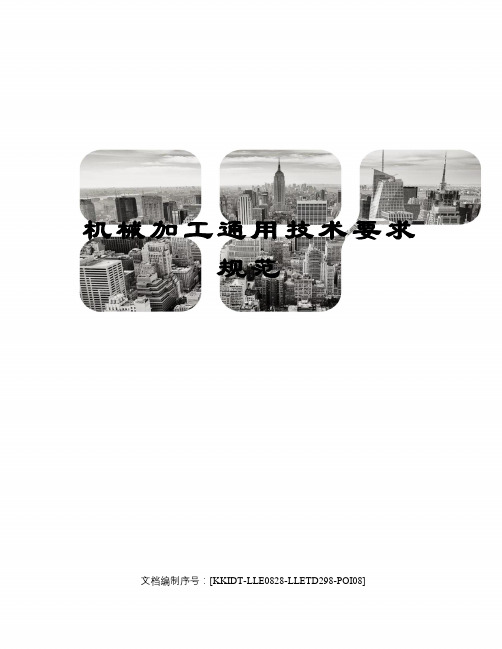
机械加工通用技术要求规范文档编制序号:[KKIDT-LLE0828-LLETD298-POI08]机械加工通用技术规范1.目的对机加工产品质量控制,以确保满足公司的标准和客户的要求。
本标准规定了各种机械加工应共同遵守的基本规则。
2.范围适用所有机加工产品,和对供应商机加工产品的要求及产品的检验。
3.定义A级表面:产品非常重要的装饰表面,即产品使用时始终可以看到的表面。
B级表面:产品的内表面或产品不翻动时客户偶尔能看到的表面。
C级表面:仅在产品翻动时才可见的表面,或产品的内部零件。
4.规范性引用文件下列文件对于本文件的应用是必不可少的。
凡是注日期的引用文件,仅注日期的版本适用于本文件。
凡是不注日期的引用文件,其最新版本(包括所有的修改单)适用于本文件。
GB/T 3-1997 普通螺纹收尾、肩距、退刀槽和倒角GB/T 145-2001 中心孔GB/T 197-2003 普通螺纹公差GB/T 1031-2009 产品几何技术规范(GPS) 表面结构轮廓法表面粗糙度参数及其数值GB/T 1182-2008 产品几何技术规范(GPS) 几何公差形状、方向、位置和跳动公差标注GB/T 1184-1996 形状和位置公差未注公差值GB/T 1568-2008 键技术条件GB/T 1804-2000 一般公差未注公差的线性和角度尺寸的公差GB/T 计数抽样检验程序第1部分:按接收质量限(AQL)检索的逐批检验抽样计划GB/T 4249-2009 产品几何技术规范(GPS) 公差原则GB/T 梯形螺纹第4部分:公差Q/JS 不合格品控制程序Q/JS 机柜半成品钣金件下料技术要求5.术语和定义GB/T 1182-2008给出的术语和定义及下列术语和定义适用于本文件。
切削加工用切削工具(包括刀具、磨具和磨料)把坯料或上多余的材料层切去成为切屑,使工件获得规定的几何形状、尺寸和表面质量的加工方法。
包括车削、铣削、刨削、磨削、拉削、钻孔、扩孔、铰孔、研磨、珩磨、抛光、超精加工及由它们组成的自动技术、数控技术、成组技术、组合机床、流水线、自动线。
(工艺技术)下料成型通用工艺规范汇总

T —0908--01剪板下料通用工艺规范编制/日期:审核/日期:批准/日期:剪板机下料通用工艺规范1总则本标准根据结构件厂现有的剪床,规定了剪板机下料应遵守的工艺规范,适用于在剪板机上下料的金属材料。
剪切的材料厚度基本尺寸为0.5~13mm (不同设备剪切的板厚不同),料宽最大为2500mm2引用标准GB/T 16743-1997 冲裁间隙JB/T 9168.1-1998 切削加工通用工艺守则下料3 下料前的准备3.1 熟悉图纸和有关工艺要求,充分了解所加工的零件的几何形状、尺寸要求,及材质、规格、数量等。
3.2 核对材质、规格与派工单要求是否相符。
材料代用时是否有代用手续。
3.3 查看材料外观质量(疤痕、夹层、变形、锈蚀等)是否符合质量要求。
3.4 为了降低消耗,提高材料利用率,要合理套裁下料。
3.5 厚板件有材质纤维方向要求的应严格按工序卡片要求执行。
3.6 下料前要按尺寸要求调准定尺挡板,并保证工作可靠,下料时材料一定靠实挡板。
3.7 熟悉所用的设备、工具的使用性能,严格遵守安全操作规程和设备维护保养规则。
3.8 操作人员应按有关文件的规定,认真做好现场管理工作。
对工件和工具应备有相应的工位器具,整齐地放置在指定地点,防止碰损、锈蚀。
3.9 操作前,操作人员应准备好作业必备的工具、量具、样板,并仔细检查、调试所用的设备、仪表、量检具、样板,使其处于良好的状态。
剪板机各油孔加油。
3.10下料好的物料应标识图号与派工单一同移工。
4剪板下料4.1剪床刀片必须锋利及紧固牢靠, 并按板料厚度调整刀片间隙。
4.2钢板剪切时,剪刃间隙符合JB/T 9168.1 标准要求,见表1表1:钢板剪切时剪刃间隙(单位:mm4.3先用钢笔尺量出刀口与挡料板两断之间的距离,反复测量数次,然后先试剪一块小料核对尺寸正确与否,如尺寸公差在规定范围内,即可进行入料剪切,如不符合公差要求,应重新调整定位距离,直到符合规定要求为止。
各种机械加工工艺规程(标准)

河南重机械制造有限公司企业标准——工艺守则《切削加工通用工艺守则》1。
范围本标准规定了各种切削加工应共同遵守的基本规则,适用于本企业的切削加工.2.规范引用文件GB4863—85 机械制造工艺基本术语JB/T5000.9—1998 切削加工件通用技术要求Q/HMZ104—2001 未注公差Q/LK506-88 工序间余量3。
加工前的准备3。
1 操作者接到加工任务后,首先要检查加工所需的产品图样、工艺规程和有关技术资料是否安全。
3。
2 要看懂、看清、工艺规程、产品图样及其技术要求,有疑问之处应找有关技术人员问清后再进行加工。
3.3 按产品图样和工艺规程复核工件毛坯或半成品是否符合要求,发现问题应及时向有关人员反映,待问题解决后才能进行加工。
3。
4 按工艺规程要求准备好加工所需的全部工艺装备,发现问题及时处理。
对新夹具、模具等,要先熟悉其使用要求和操作方法。
按加工部位的精度和技术要求正确合理选用通用工具。
3.5 加工所用的工艺装备应放在规定的位置,不得乱放,更不能放在机床导轨上。
3。
6 工艺装备不得随意拆卸和更改。
3。
7 检查加工所用的机床设备,准备好所需的各种附件。
加工前要按规定对机床进行润滑和空运转。
4 刀具与工件的装夹4.1 刀具的装夹4.1.1 在装夹各种刀具前,一定要把刀柄、刀杆、导套等擦拭干净.4。
1.2 刀具装夹后,应用对刀装置或试切等检查其正确性。
4.2 工件的装夹。
4.2.1 在机床工作台上安装夹具时,首先要擦净其定位基面,并要找正其与刀具相对位置.4。
2。
2 工件装夹前应将其定位面、夹紧面及垫铁和夹具的定位夹紧面擦拭干净,并不得有毛刺。
4.2.3 按工艺规程中规定的定位基准夹紧。
若工艺规程中未规定装夹方式,操作者可自行选择定位基准和装夹方式,选择定位基准应按以下原则:a.尽可能使定位基准与设计基准重合;b.尽可能使各加工面采用同一定位基准;c.毛基准的选择首先考虑加工工艺基准的要求,并应保持加工工件的壁厚均匀;d.粗加工定位基准应尽量选择不加工或加工余量比较小的平整表面,而且只能使用一次;e.精加工工序定位基准应是已加工面;f.选择的定位基准必须使工件定位夹紧方便,加工时稳定可靠.4.2。
机械加工通用技术规范DOC
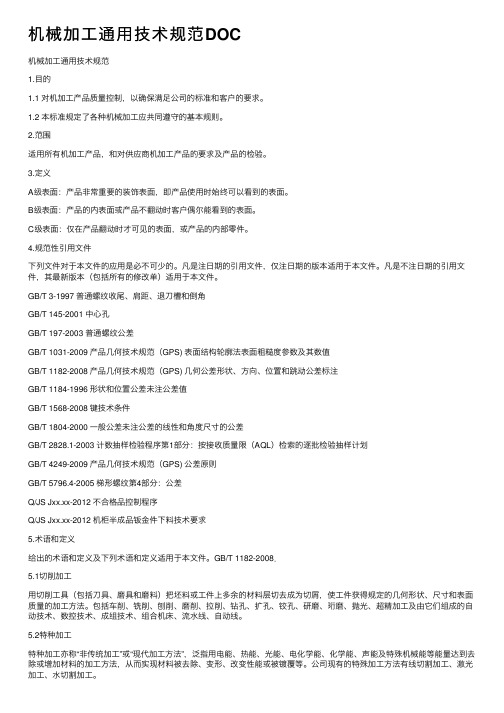
机械加⼯通⽤技术规范DOC机械加⼯通⽤技术规范1.⽬的1.1 对机加⼯产品质量控制,以确保满⾜公司的标准和客户的要求。
1.2 本标准规定了各种机械加⼯应共同遵守的基本规则。
2.范围适⽤所有机加⼯产品,和对供应商机加⼯产品的要求及产品的检验。
3.定义A级表⾯:产品⾮常重要的装饰表⾯,即产品使⽤时始终可以看到的表⾯。
B级表⾯:产品的内表⾯或产品不翻动时客户偶尔能看到的表⾯。
C级表⾯:仅在产品翻动时才可见的表⾯,或产品的内部零件。
4.规范性引⽤⽂件下列⽂件对于本⽂件的应⽤是必不可少的。
凡是注⽇期的引⽤⽂件,仅注⽇期的版本适⽤于本⽂件。
凡是不注⽇期的引⽤⽂件,其最新版本(包括所有的修改单)适⽤于本⽂件。
GB/T 3-1997 普通螺纹收尾、肩距、退⼑槽和倒⾓GB/T 145-2001 中⼼孔GB/T 197-2003 普通螺纹公差GB/T 1031-2009 产品⼏何技术规范(GPS) 表⾯结构轮廓法表⾯粗糙度参数及其数值GB/T 1182-2008 产品⼏何技术规范(GPS) ⼏何公差形状、⽅向、位置和跳动公差标注GB/T 1184-1996 形状和位置公差未注公差值GB/T 1568-2008 键技术条件GB/T 1804-2000 ⼀般公差未注公差的线性和⾓度尺⼨的公差GB/T 2828.1-2003 计数抽样检验程序第1部分:按接收质量限(AQL)检索的逐批检验抽样计划GB/T 4249-2009 产品⼏何技术规范(GPS) 公差原则GB/T 5796.4-2005 梯形螺纹第4部分:公差Q/JS Jxx.xx-2012 不合格品控制程序Q/JS Jxx.xx-2012 机柜半成品钣⾦件下料技术要求5.术语和定义给出的术语和定义及下列术语和定义适⽤于本⽂件。
GB/T 1182-2008.5.1切削加⼯⽤切削⼯具(包括⼑具、磨具和磨料)把坯料或⼯件上多余的材料层切去成为切屑,使⼯件获得规定的⼏何形状、尺⼨和表⾯质量的加⼯⽅法。
制造业工艺流程设计规范
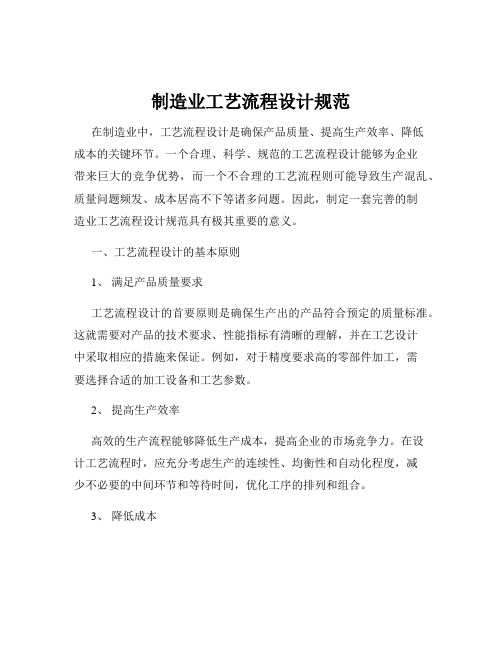
制造业工艺流程设计规范在制造业中,工艺流程设计是确保产品质量、提高生产效率、降低成本的关键环节。
一个合理、科学、规范的工艺流程设计能够为企业带来巨大的竞争优势,而一个不合理的工艺流程则可能导致生产混乱、质量问题频发、成本居高不下等诸多问题。
因此,制定一套完善的制造业工艺流程设计规范具有极其重要的意义。
一、工艺流程设计的基本原则1、满足产品质量要求工艺流程设计的首要原则是确保生产出的产品符合预定的质量标准。
这就需要对产品的技术要求、性能指标有清晰的理解,并在工艺设计中采取相应的措施来保证。
例如,对于精度要求高的零部件加工,需要选择合适的加工设备和工艺参数。
2、提高生产效率高效的生产流程能够降低生产成本,提高企业的市场竞争力。
在设计工艺流程时,应充分考虑生产的连续性、均衡性和自动化程度,减少不必要的中间环节和等待时间,优化工序的排列和组合。
3、降低成本成本控制是企业生存和发展的重要因素。
在工艺流程设计中,要综合考虑原材料的利用率、设备的投资和运行成本、劳动力成本等,通过合理的工艺选择和优化,达到降低总成本的目的。
4、工艺的可行性和可靠性设计的工艺流程必须在技术上可行,能够在现有的生产条件下实现。
同时,工艺过程要稳定可靠,能够保证长期稳定的生产,避免因工艺问题导致的生产中断和质量波动。
5、环保与安全现代制造业必须重视环保和安全问题。
工艺流程应尽量减少对环境的污染,符合相关的环保法规。
同时,要确保生产过程中的人员安全,采取必要的防护措施和安全设备。
二、工艺流程设计的主要内容1、产品分析对所要生产的产品进行全面的分析,包括产品的结构、功能、技术要求、质量标准等。
了解产品的特点和要求是设计合理工艺流程的基础。
2、生产方法选择根据产品的特点和企业的实际情况,选择合适的生产方法。
例如,对于大批量生产的产品,可以采用流水线生产;对于小批量、多品种的产品,则可能更适合采用灵活的加工中心。
3、工序划分将整个生产过程分解为若干个工序,并确定每个工序的加工内容、设备、工装和工艺参数。
铝制产品加工通用技术要求
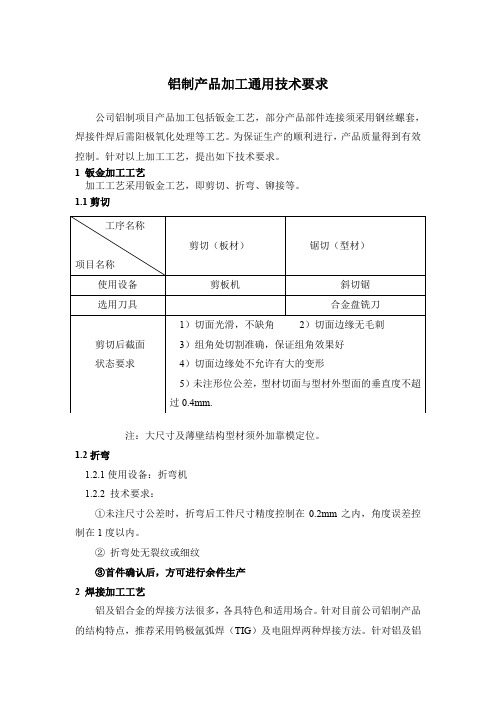
铝制产品加工通用技术要求公司铝制项目产品加工包括钣金工艺,部分产品部件连接须采用钢丝螺套,焊接件焊后需阳极氧化处理等工艺。
为保证生产的顺利进行,产品质量得到有效控制。
针对以上加工工艺,提出如下技术要求。
1 钣金加工工艺加工工艺采用钣金工艺,即剪切、折弯、铆接等。
1.1剪切注:大尺寸及薄壁结构型材须外加靠模定位。
1.2折弯1.2.1使用设备:折弯机1.2.2 技术要求:①未注尺寸公差时,折弯后工件尺寸精度控制在0.2mm之内,角度误差控制在1度以内。
②折弯处无裂纹或细纹③首件确认后,方可进行余件生产2 焊接加工工艺铝及铝合金的焊接方法很多,各具特色和适用场合。
针对目前公司铝制产品的结构特点,推荐采用钨极氩弧焊(TIG)及电阻焊两种焊接方法。
针对铝及铝合金焊接特点,TIG焊和电阻焊的应用要点及技术要求如下。
2.1钨极氩弧焊2.1.1接头形式和坡口准备钨极氩弧焊铝及铝合金的接头形式有对接、搭接、角接和T形接等,接头几何形状与焊接钢材相似。
但因铝及铝合金的流动性更好并且焊枪喷嘴尺寸较大,因而一般都采用较小的根部间隙和较大的坡口角度。
(2)钨极氩弧焊的坡口形式及尺寸2.1.2焊接电流种类采用交流电焊接铝及铝合金,在获得良好净化作用的同时又获得满意的熔深。
若采用脉冲电流,便能精确地控制电弧能量,可以达到对焊接熔池的控制,对薄板或全位置焊接很有利。
2.1.3焊接工艺要点①钨极氩弧焊适宜焊接厚度小于12mm的铝及其合金。
厚度小于3mm时,在钢垫板上一般用单道焊焊接。
厚度为4~6mm时,通常用双面焊焊接。
厚度大于6mm 时,须开坡口。
②用铈钨极,电弧容易点燃,电弧燃烧稳定,具有较大的许用电流,电极损耗小。
③焊接厚度小于1mm的铝及其合金时,用钨极脉冲氩弧焊焊接。
焊接厚度大于5mm,大体积铸件补焊或焊接环境温度低于—10℃时,焊前应预热,预热温度为150-250℃。
2.1.4钨极氩弧焊焊接工艺参数纯铝、铝镁合金手工钨极氩弧焊的参考焊接工艺参数2.1.5焊丝的选择各种牌号的铝及其合金焊接时,通常都选用与母材成分相近的焊丝,若无现成的焊丝,可用相应牌号的板材切成条或用铝合金铸件熔铸成长条作填充金属。
通用工艺守则
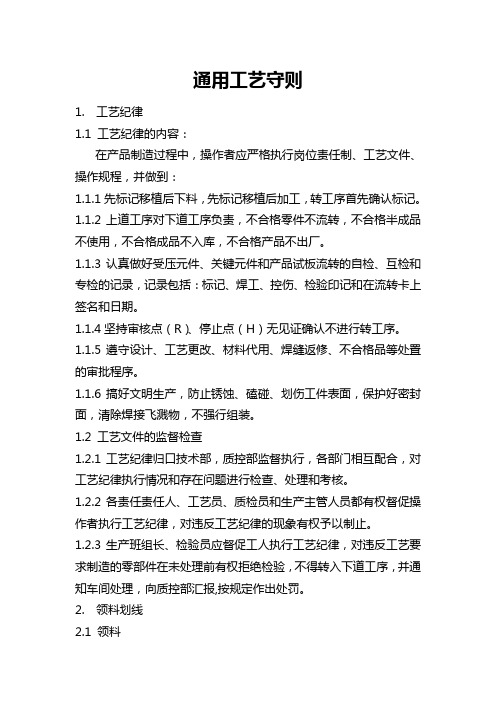
通用工艺守则1. 工艺纪律1.1 工艺纪律的内容:在产品制造过程中,操作者应严格执行岗位责任制、工艺文件、操作规程,并做到:1.1.1先标记移植后下料,先标记移植后加工,转工序首先确认标记。
1.1.2上道工序对下道工序负责,不合格零件不流转,不合格半成品不使用,不合格成品不入库,不合格产品不出厂。
1.1.3认真做好受压元件、关键元件和产品试板流转的自检、互检和专检的记录,记录包括:标记、焊工、控伤、检验印记和在流转卡上签名和日期。
1.1.4坚持审核点(R)、停止点(H)无见证确认不进行转工序。
1.1.5遵守设计、工艺更改、材料代用、焊缝返修、不合格品等处置的审批程序。
1.1.6搞好文明生产,防止锈蚀、磕碰、划伤工件表面,保护好密封面,清除焊接飞溅物,不强行组装。
1.2 工艺文件的监督检查1.2.1工艺纪律归口技术部,质控部监督执行,各部门相互配合,对工艺纪律执行情况和存在问题进行检查、处理和考核。
1.2.2各责任责任人、工艺员、质检员和生产主管人员都有权督促操作者执行工艺纪律,对违反工艺纪律的现象有权予以制止。
1.2.3生产班组长、检验员应督促工人执行工艺纪律,对违反工艺要求制造的零部件在未处理前有权拒绝检验,不得转入下道工序,并通知车间处理,向质控部汇报,按规定作出处罚。
2. 领料划线2.1 领料2.1.1凭材料领用卡、制造工艺过程及检验卡领料,按规定进行材料标记移植,并在材料领用卡、制造工艺过程卡上记录材料品种、规格、材料标记。
2.1.2检验员应检查材质标识(钢印或油漆)清晰、无误,并复检材料表面质量,尺寸规格合格,材料领用卡、制造工艺过程卡签字确认后,方可投料划线。
2.1.3复检表面质量及规格的要求如下:a)双面锈蚀深度不得大于材料名义厚度的6%且不大于0.25mm;b)表面机械损伤深度不得大于材料名义厚度的5%且不大于2mm;c)非加工板材厚度的允许负偏差C1按表1:表12.2 表面清理及划线位置操作者在划线前应清除附着于材料表面的污物及杂物、锈蚀夹层,并将材料放置在方便操作及能准确划线的位置。
加工件技术规范
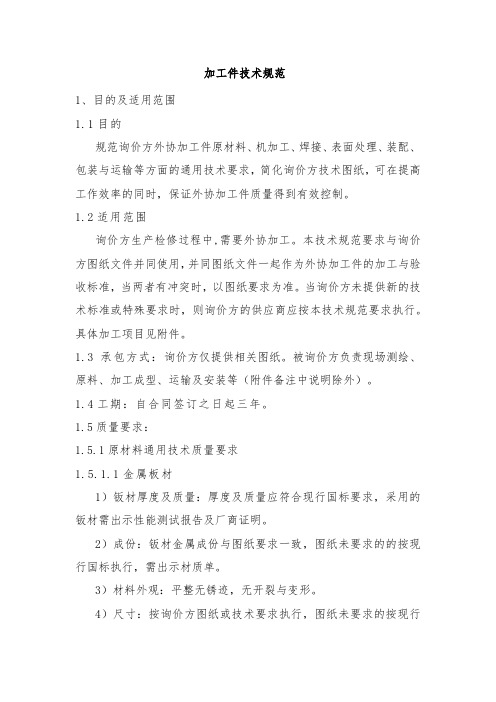
加工件技术规范1、目的及适用范围1.1目的规范询价方外协加工件原材料、机加工、焊接、表面处理、装配、包装与运输等方面的通用技术要求,简化询价方技术图纸,可在提高工作效率的同时,保证外协加工件质量得到有效控制。
1.2适用范围询价方生产检修过程中,需要外协加工。
本技术规范要求与询价方图纸文件并同使用,并同图纸文件一起作为外协加工件的加工与验收标准,当两者有冲突时,以图纸要求为准。
当询价方未提供新的技术标准或特殊要求时,则询价方的供应商应按本技术规范要求执行。
具体加工项目见附件。
1.3承包方式:询价方仅提供相关图纸。
被询价方负责现场测绘、原料、加工成型、运输及安装等(附件备注中说明除外)。
1.4工期:自合同签订之日起三年。
1.5质量要求:1.5.1原材料通用技术质量要求1.5.1.1金属板材1)钣材厚度及质量:厚度及质量应符合现行国标要求,采用的钣材需出示性能测试报告及厂商证明。
2)成份:钣材金属成份与图纸要求一致,图纸未要求的的按现行国标执行,需出示材质单。
3)材料外观:平整无锈迹,无开裂与变形。
4)尺寸:按询价方图纸或技术要求执行,图纸未要求的按现行国标执行。
1.5.1.2金属型材1)型材厚度及质量:厚度及质量应符合现行国标要求,采用的型材需出示性能测试报告及厂商证明。
2)成份:型材金属成份与图纸要求一致,图纸未要求的的按现行国标执行,需出示材质单。
3)材料外观:平整无锈迹,无开裂与变形。
4)尺寸:按图纸或技术要求执行,图纸未要求的按现行国标执行。
1.5.1.3标准件1)尺寸及质量:应符合图纸和国标要求,需出示性能测试报告及厂商证明。
2)成份:标准件金属成份应符合图纸和国标要求,需出示材质单。
3)外观:表面无绣迹、无毛刺批锋,整批来料外观一致性良好。
4)性能:试装配与使用性能符合产品要求。
1.5.2机加工通用技术要求1.5.2.1未注尺寸公差未注尺寸公差按GB/T1804-2000中的中等精度等级(m级)执行,部分公差值如下表所示。
机械制造通用工艺流程操作规范标准作业指导书
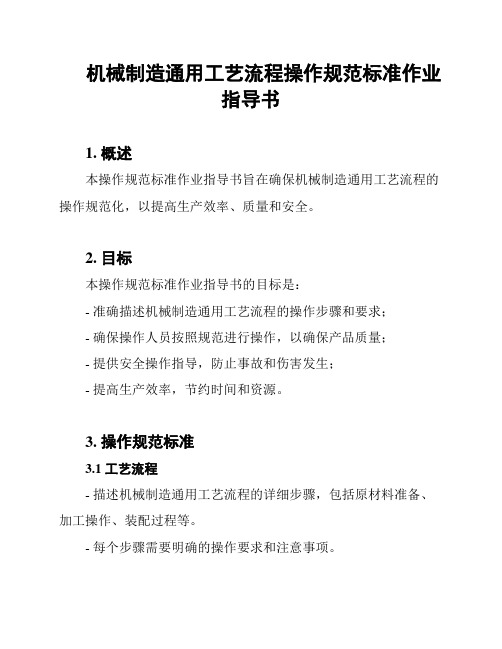
机械制造通用工艺流程操作规范标准作业指导书1. 概述本操作规范标准作业指导书旨在确保机械制造通用工艺流程的操作规范化,以提高生产效率、质量和安全。
2. 目标本操作规范标准作业指导书的目标是:- 准确描述机械制造通用工艺流程的操作步骤和要求;- 确保操作人员按照规范进行操作,以确保产品质量;- 提供安全操作指导,防止事故和伤害发生;- 提高生产效率,节约时间和资源。
3. 操作规范标准3.1 工艺流程- 描述机械制造通用工艺流程的详细步骤,包括原材料准备、加工操作、装配过程等。
- 每个步骤需要明确的操作要求和注意事项。
3.2 操作步骤- 详细描述每个操作步骤的具体要求,包括操作顺序、操作方法和注意事项。
- 强调安全操作,如佩戴个人防护装备、避免操作失误等。
3.3 质量控制- 说明质量控制要求,如测量检验、产品检查等。
- 强调严格遵守质量标准和要求,确保产品质量符合相关标准。
3.4 安全要求- 提供安全操作指导,包括机械操作安全、化学品使用安全等。
- 强调遵守安全规范,预防事故和伤害。
4. 使用说明4.1 目标人群- 指导书适用于机械制造通用工艺流程的操作人员。
- 操作人员应仔细阅读并按照指导书进行操作。
4.2 指导书更新- 指导书应定期进行评审和更新,以适应工艺流程和标准的变化。
- 确保所有操作人员使用最新版本的指导书。
4.3 问题反馈- 操作人员在使用指导书时遇到问题或有改进建议,应及时向主管或相关部门反馈。
- 反馈应及时处理,并在需要时更新指导书。
5. 总结本操作规范标准作业指导书是机械制造通用工艺流程操作的重要参考,必须严格按照规范进行操作,以确保产品质量和操作安全。
医疗电子产品加工通用规范

深圳市兆恒兴电子有限公司医疗电子产品加工通用规范编制:陈立鹏、彭小思批准:唐先华日期:2016年12月16日目录1目的 (5)2范围 (5)3术语与定义 (5)4引用标准和参考资料 (5)5PCBA加工过程中辅料使用要求 (5)6表面贴装(SMT)工序 (7)6.1PCB及物料烘烤要求 (7)6.2印锡要求 (7)6.3贴片要求 .......................................................................................................... 错误!未定义书签。
6.4回流焊接曲线制订及测试要求 (8)6.4.1回流焊接曲线制订 (8)6.4.2热电偶选用及放置要求 (9)6.4.3温度曲线测试频率 (9)6.5炉后检查要求 (9)6.6湿度敏感器件的确认、储存、使用要求 (9)7ESD防护 (10)8返修工序 (10)8.1产品返修辅料使用型号................................................................................... 错误!未定义书签。
8.2特殊要求 (10)9物料使用要求 (11)9.1型号和用量要求 (11)9.2分光分色要求 (11)9.3插座上的附加物处理要求 (11)10元件成型 (12)10.1元件成形的基本要求 (12)10.2带绝缘粒的功率器件散热器组装要求 (12)10.3元器件成型技术要求 (12)10.4质量控制 (13)10.4.1元件成型的接收标准 (13)11波峰焊接(THT)/后焊工序 (14)11.1.1波峰焊温度曲线测试要求 (14)11.1.2HSF工艺参数要求(实测值); (14)11.1.3有铅工艺工艺参数设定要求(实测值)...................................................... 错误!未定义书签。
医疗器械制造通用工艺守则

医疗器械制造通用工艺守则医疗器械制造是一个严谨的过程,需要遵守一系列工艺守则来确保产品的质量和安全性。
以下是一些通用的医疗器械制造工艺守则:1. 设计规范:医疗器械的制造应根据国家和国际的相关设计规范进行。
设计阶段需要充分考虑产品的功能、性能、使用安全性以及符合患者和医护人员需求的人体工程学原理。
2. 原材料选择:医疗器械的制造需要选用符合国家和国际相关标准的合格原材料。
原材料的质量和纯度直接关系到产品的性能和安全性,因此必须从可靠的供应商获取。
3. 加工工艺:医疗器械的加工工艺需要根据产品的特点和要求确定,并制定标准作业程序(SOP)。
在加工过程中,需要严格控制加工精度、表面光洁度以及各种物理和化学性能的符合要求。
4. 注塑模具制造:很多医疗器械都采用塑料制造,因此注塑模具的制造至关重要。
模具的设计和制造需要满足产品的准确尺寸和表面质量要求,同时也必须考虑到产品的易用性和易清洁性。
5. 清洁和消毒:医疗器械在制造完成后,需要进行清洁和消毒以确保产品的无菌和无致病微生物。
清洁和消毒过程需要符合国家和国际相关卫生标准,并使用合适的清洁剂和消毒剂。
6. 质量控制:医疗器械的制造必须建立完善的质量控制系统。
从原材料的入库检验到产品的最终检验,每个环节都需要进行严格的检测和测试,以确保产品符合规定的技术要求和标准。
7. 文档记录:医疗器械的制造过程中,需要做好相关的文档记录,包括设计文档、加工工艺文件、质量检验记录等。
这些记录要准确、完整,并妥善保存,以备查阅和追溯。
总之,医疗器械制造需要遵守一系列工艺守则,以确保产品的质量和安全性。
这些守则包括设计规范、原材料选择、加工工艺、注塑模具制造、清洁和消毒、质量控制以及文档记录等方面。
制造企业需要建立完善的质量管理体系,打造高品质的医疗器械产品。
医疗器械制造通用工艺守则是确保医疗器械质量和安全性的重要保障。
在制造医疗器械的过程中,应严格遵守这些守则,以保证产品的可靠性和符合相关标准。
金属加工通用工艺流程操作规范标准作业指导书

金属加工通用工艺流程操作规范标准作业指导书金屬加工通用工藝流程操作規範標準作業指導書1. 引言本操作規範標準作業指導書旨在紀錄金屬加工通用工藝流程的操作規範,以提供給操作人員參考,確保生產過程的安全和效率。
2. 裝置和工具的使用注意事項- 在進行金屬加工作業之前,確保所有裝置和工具的狀態良好且符合使用要求。
- 若發現任何損壞或異常情況,應立即報告上級主管並停止使用。
- 使用工具時,應注意個人安全,避免受傷。
- 經過使用的工具應予以清潔和維護,以確保長期穩定的工作性能。
3. 金屬加工通用工藝流程操作流程以下為金屬加工的通用操作流程,請按步驟執行:1. 準備工作- 確認所需的材料和工具是否齊全。
- 確保工作區域整潔和安全。
2. 材料準備- 檢查材料的尺寸、品質和數量。
- 確認材料是否符合加工要求。
3. 裝夾材料- 使用適當的工具和方法將材料安全裝夾。
- 確保材料固定穩固,避免移位或意外。
4. 加工操作- 根據加工要求選擇適當的加工方法和工具。
- 按照操作手冊進行具體的加工操作。
- 注意安全,避免意外發生。
5. 檢查品質- 檢測加工後的產品品質,確保其符合要求。
- 如發現任何品質問題,應立即採取合適的措施。
6. 清潔和維護- 在完成加工作業後,將工作區和工具清潔整潔。
- 對工具進行常規的檢查與維護。
4. 安全注意事項在進行金屬加工作業時,請遵守以下安全注意事項:- 戴上個人防護裝備,包括安全帽、安全鞋和眼睛護具。
- 不瞭解或不熟悉的操作,請勿嘗試。
- 避免將手和身體部件靠近旋轉或移動的機械部件。
- 嚴格遵守機械操作規則和程序。
5. 延伸閱讀以下是一些金屬加工操作的延伸閱讀資源,供有興趣的人參考:- 《金屬加工技術手冊》- 《金屬加工安全指南》以上為金屬加工通用工藝流程操作規範標準作業指導書的內容概要,請根據實際情況進行適當的修改和補充。
- 1、下载文档前请自行甄别文档内容的完整性,平台不提供额外的编辑、内容补充、找答案等附加服务。
- 2、"仅部分预览"的文档,不可在线预览部分如存在完整性等问题,可反馈申请退款(可完整预览的文档不适用该条件!)。
- 3、如文档侵犯您的权益,请联系客服反馈,我们会尽快为您处理(人工客服工作时间:9:00-18:30)。
加工通用工艺规范1.目的及适用范围为了确保产品质量得到保证,特制定本制度。
适用于在公司现有设备情况下的生产加工工艺的制定。
2.职责2.1技术部负责生产加工工艺的编制;2.2技术部负责人负责生产加工工艺的审批;2.3生产车间操作人员按编制的有效的加工工艺加工产品。
3. 放样工艺在钢结构制造中,放样工作是非常重要的一环,因为所有零件尺寸和形状都必须先行放样,然后依样进行加工,因此放样工作的准确与否直接影响产品的质量。
3.1先应仔细阅读技术要求及说明,逐个核对图纸之间的尺寸和方向等,发现有疑问之处,应于技术部联系解决。
3.2备好样板纸作样板,在样板台上放样需准备尺、石笔、粉线、划针、样冲。
3.3放样以1:1的比例,零件尺寸较小时,直接在样板纸上放样,否则在样板台上弹出大样,当大样尺寸较大时,可分段弹出。
3.4在样板台上放样时,以构件的某一水平线和垂直线为基准,弹出十字线,然后依次十字线划出其他各点及线,并在节点旁注上尺寸,以备复查及自检。
用划针划上连接线并用尖锐的样冲将交点敲出,或者直接用样冲在样板将交点敲出。
3.5样过程中遇到技术问题,应于技术部联系解决。
3.6样过程中应按图纸进行自检。
4.号料工艺4.1号料前首先根据料单检查清点样板,搞清号料数量。
4.2准备并检查各种使用工具,号料前必须了解原材料的钢号及规格,检查原材料的质量,如有疤痕、裂纹、厚度不足等现象应调换材料。
号料的刚才必须摆放平稳,不得弯曲。
4.3注意工作地点四周的安全。
4.4不同规格,不同钢号的零件应分别号料,并依据先大后小的顺序号料。
4.5形样板号料应先检查原材料钢板两边是否垂直,若不垂直,要划好垂直线,在号料。
4.6不得使用一次剪切宽度超过剪板机的宽度。
4.7号料过程中,应随时在样板上记录号料的数量,并妥善保管好样板。
5. 切割通用工艺5.1钢板5.1.1厚度大于13mm的应进行气割;厚度小于13mm的应进行剪切;5.1.2剪切工艺装备:剪板机。
5.1.3剪切工艺:5.1.3.1根据板厚适当调节上下刀刃的间隙,以避免剪切的材料发生翻翘和产生断面粗糙和产生毛刺;5.1.3.2材料剪切后产生的弯扭变形应进行矫正;5.1.3.3材料剪切后断面产生较大的毛刺或断面粗糙较大时应修磨光洁;5.1.3.4对于非常重要的结构件的焊缝的借口位置,要用刨或砂轮磨削的方法将表面硬化层清除,一般为3--5mm;5.1.4气体割工艺5.1.4.1根据钢板厚度选择正确的工艺参数;5.1.4.2气割时,割嘴应运行平稳,使用轨道时要保证轨道平直和无振动;5.1.4.3割嘴气流畅通,无污损;5.1.4.4割炬的角度和位置应准确;5.1.5技术要求;5.2角钢切割允许偏差(mm)如下表:6.制弯工艺6.1根据材料选择热、冷弯6.1.1冷弯是在常温下进行弯曲加工,它适用于一般薄板,型钢等的加工。
6.1.2热弯是将钢材加热至950℃~1100℃,在模具上进行弯曲加工;它适用于厚板及较复杂形状构件、型钢等的加工。
6.2根据材料选择弯曲加工方法分为压弯、滚弯6.2.1压弯适用于一般直角弯曲(V形件)、双直角弯曲(U形件),以及其他适宜弯曲的构件。
6.2.2滚弯适用于滚制圆筒形构件及其他弧形构件。
6.3压弯6.3.1弯曲设备的选用弯曲加工设备在一般情况下能和模压设备通用,如:双盘摩擦压力机,卷板机。
6.3.2弯曲工艺6.3.2.1弯曲位置的确定弯曲位置取决于弯曲线的位置,弯曲线和材料纤维方向的关系:当弯曲线和材料纤维方向垂直时,材料具有较大的抗拉强度,不易发生裂纹;当材料纤维方向和弯曲线平行时,材料的抗拉强度较差,容易发生裂纹,甚至断裂;在双向弯曲时,弯曲线于材料纤维方向成一定的夹角。
6.3.2.2弯曲半径的确定最小弯曲半径:弯曲件的圆角半径不宜过大,也不宜过小;过大时因回弹影响,使构件精度不易保证,过小则容易产生裂纹。
根据实践经验:6.3.2.2.1 Q235钢在经退火时最小弯曲半径为0.5t不经退火时为t(t为板材厚度)。
6.3.2.2.2角钢弯曲最小半径R=(b-z)/m-z(其中b为角钢的肢宽,z为中心距离,热弯时取m=0.14,冷弯时取m=0.04)6.3.2.2.3槽钢弯曲最小半径R=h/2m-h/2(其中h为槽钢的腰宽,m同角钢) 6.3.2.3弯曲角度的确定一般薄板材料弯曲半径可取较小数值,弯曲半径≥t(t为板厚):厚板材料弯曲半径应取较大数值,弯曲半径=2t(t为板厚)6.3.2.4弯曲时长度公差的确定6.3.2.5弯曲时角度公差的确定6.3.2.6 弯曲变形和弯曲缺陷的控制6.4滚圆6.4.1设备:卷板机6.4.2根据材料和弯曲半径调节上下轴辊的间距;6.4.3预弯卷板前必须对板料进行预弯(压头),由于板料在卷板机上弯曲时,两端边缘总剩余直边。
6.4.4理论剩余直边的确定6.4.5滚压质量和缺陷的控制6.4.5.1外形缺陷:卷弯圆柱筒身时,常见的外形缺陷有过弯,锥形,鼓形,束形,边缘歪斜和棱角等缺陷。
6.4.5.2表面压伤:卷板时,钢板或轴辊表面和氧化皮及粘附的杂质会造成板料表面压伤。
尤其在热卷或热矫时,氧化皮与杂质对板料的压伤更严重。
为了防止卷板表面的压伤,其控制措施如下:a.在冷卷前必须清除板料表面的氧化皮,并涂上保护涂料。
b.热卷时宜采用中性火焰,缩短高温下板料的停留时间,并采用防氧涂料等办法,尽量减少氧化皮的产生。
c.卷板设备必须保持干净,轴辊表面不得有锈皮,毛刺,棱角或其他硬性颗粒。
d.卷板时应不断吹扫内外侧剥落的氧化皮,矫园时应尽量减少反转次数等。
6.4.5.3卷裂:板料在卷弯时,由于变形太大,材料的冷作硬化,以及应力集中等因素会使材料的塑性降低而造成裂纹。
a.对变形率达和脆性的板料,需进行正火处理。
b.对缺口敏感性大的钢种,最好将板料预热到150℃-200℃后卷制。
c.板料的纤维方向,不宜与弯曲线垂直。
d.对板料的拼凑缝必须修磨至光滑平整。
7.制孔工艺7.1钻孔设备:钻床7.1.1根据厚度,孔径选择设备:摇臂钻床7.2钻孔的选择:7.2.1普通厂房结构和一般对孔距要求不高的构件,采用划线钻孔。
这种方法成本最低,加工方便,但精度较差,是普通采用的方法。
7.2.2对依靠群孔作业定位的构件与当孔距精度要求较高时,建议采用钻模板或钻模钻孔。
7.2.3框架结构、高层建筑构件,节点以上方向有高强螺栓连接的构件或设计上有特殊要求的构件应用钻模板或钻模钻孔。
钻模板和钻模钻孔精度高,速度快,但成本高。
7.2.4材料的厚度:大于8mm的采用钻孔7.2.5材料的形状:用于不便于冲孔的任何规格的钢板,型钢的加工。
7.3钻孔加工7.3.1划线钻孔7.3.1.1孔中心的冲眼应大而深,作为钻头定心用,划线工具用划针、钢尺。
7.3.1.2为提高划线效率,可采用涤纶片基的划线模板划线。
7.3.1.3为提高钻孔效率,可将数块钢板重叠起来一起钻孔,但一般重叠板厚不超过50mm重叠板边必须用夹具夹紧或点焊固定。
7.3.1.4厚板和重叠板钻孔时要检查平台的水平度,以防止孔的中心倾斜。
7.3.2钻模板钻孔当孔群中孔的数量较多,位置精度要求较高,批量小时可采用钻模板钻孔。
做钻模板的钢板多用硬度较高的低合金钢板和16Mn钢板等;模板上孔用较高精度的设备加工。
由于模板反复使用,模板的孔被扩大和精度下降,所以使用数次后应对模板进行检查,如超出要求应停止使用。
7.3.2钻模钻孔当批量大,孔距要求较高时,应用钻模钻孔。
钻模有通用性,组合式和专用钻模几种钻模的形式。
对无镗孔能力的单位,可先在模板上钻较大的孔眼,由钳工将钻套进行校正,符合公差要求后把螺栓紧固,然后将模板孔与钻套外圆间的间隙灌铅固定。
钻套需经淬火处理。
为了提高钻模的利用率,可考虑采用于不同孔径,不同孔距的通用钻模。
7.4钻孔的加工顺序:先小孔后大孔。
例如:孔径大于10mm要先用ø10mm的钻头钻透,然后再换相应的钻头钻到规定尺寸。
7.5钻孔质量控制7.5.1板材7.5.1.1孔形偏差符合下表规定(t为连板厚度)7.5.1.2螺栓孔孔距的允许偏差如下表:7.5.2 角钢7.5.2.1 孔钻完后,用电动角向磨光机打磨各孔边缘,去除毛刺。
7.5.2.2 钻孔允许偏差如下表:7.6 冲孔7.6.1 设备:冲床7.6.1.1 根据厚度、孔径选择设备:一般只能在较薄的钢板上和型钢上冲孔,且孔径一般不小于钢材的厚度,可用于不重要的节点管、垫板、加强板、角钢拉撑等小件孔加工,冲孔生产效率高,但由于孔的周围产生冷作茧自缚硬化,孔壁质量差,有孔下塌,孔的下方增大的倾向,所以孔的质量要求不高时或作为预制孔(非成品孔)外,在钢结构制造中已较少直接采用。
7.6.2 冲孔的选择:7.6.2.1 钢板:厚度小于8mm的可采用冲孔。
7.6.2.2 角钢:L100X8以下的可采用冲孔。
7.6.3 冲孔加工:冲模间隙选择如下表7.6.4 冲孔的质量控制:7.6.4.1 角钢冲孔螺栓孔孔距允许偏差(mm)如下表7.6.4.2 角钢螺栓孔孔形允许偏差(mm)如下表:7.6.4.3 角钢冲孔后孔缘不能有明显的毛刺及飞边,边缘缺棱不得大于1.0mm,孔眼缘及孔壁不能出现裂纹。
8.试装工艺8.1 试装一般采用卧式。
8.2 试装时,各零部件应处于自由状态,不得强行组装,所使用的螺栓数目应能保证构件定位需要且每组孔不少于该组螺栓总数的30%。
当采用比螺栓公称直径0.3mm的试孔器检查,每组通孔率为100%。
8.3 试装后,应符合图纸要求。
8.4 电力塔试装下端第一个脚钉距离地面高度(设计无要求时)为2m.8.5 切角工艺钢材切角后,其断口不得有裂纹和大于1.0mm的边缘缺棱,切断处切割面平面度为0.05t(t为厚度),且不大于2.0mm,割纹深度不大于0.3um,局部缺口深度允许偏差1.0mm角钢切角时剪切边缘最小尺寸(A)不得小于孔径的1.3倍,即对M16螺栓A=23,对M20螺栓A=28.9.清根,铲背工艺在角钢与角钢连接处,外包钢要清根,内包钢要铲背,使主材,外包和内包角钢三者连接相吻合。
9.1主要设备:牛头刨床在清根铲背时,要根据包钢的长度来调节刨床的行程,以及根据包钢的肢厚来调节刨刀。
其工艺参数规定如下:。