缩孔异常分析及对策
产生缩孔的条件

产生缩孔的条件
产生缩孔的条件主要有以下几个方面:
1. 材料的特性:当材料的延伸性较差、韧性较差或硬度较高时,容易产生缩孔。
这是因为材料在受到外力作用时,难以形成均匀的变形,容易出现局部的收缩。
2. 受力状态:当材料受到剪切力、挤压力或拉伸力时,容易产生缩孔。
这是因为在受到这些力的作用下,材料会发生局部的变形,造成局部收缩。
3. 加工工艺:在一些加工过程中,如铸造、锻造、冲压等,材料会经历熔化、变形等过程,容易产生缩孔。
这是因为在这些过程中,材料受到高温和高压的作用,容易出现气体的聚集和挤压,从而形成缩孔。
4. 设计参数:当设计参数不合理时,容易产生缩孔。
例如,材料的厚度过大、角度过小、半径过小等会增加材料的变形难度,容易形成缩孔。
需要注意的是,以上条件并非绝对,不同的材料和加工工艺可能会有不同的产生缩孔的条件。
因此,在实际应用中,需要根据具体情况来进行分析和判断。
缩孔的防止措施

缩孔的防止措施1. 背景介绍在工程领域中,缩孔是一种常见的问题,指的是混凝土浇筑过程中未能填满模板或者未完全充实的空洞或空隙。
缩孔可能会导致混凝土结构的强度和稳定性受到影响,从而影响到工程的质量和安全性。
为了防止缩孔问题的发生,在混凝土浇筑过程中需要采取一些防止措施。
2. 防止缩孔的措施以下是防止缩孔问题发生的几种常用措施:2.1 混凝土配合比设计混凝土配合比设计是防止缩孔的关键因素之一。
合理的配合比设计可以确保混凝土的流动性和可塑性,从而减少浇筑过程中的空隙和空洞。
在设计配合比时,需要考虑到使用的材料种类和质量、水胶比、粉料含量以及外加剂的使用等因素。
2.2 浇筑技术控制控制好混凝土的浇筑技术也是防止缩孔的重要措施之一。
以下是几个浇筑技术控制的要点:•振捣方式和时间:使用适当的振捣方式和时间可以帮助混凝土充实模板中的空隙和空洞。
振捣应该均匀地分布在整个浇筑区域,并且持续时间应该足够长,确保混凝土能够流动并充分充实。
•浇注方式:采用合适的浇注方式可以有效地减少缩孔的发生。
例如,在梁柱节点处可以采用低压喷射的方式进行浇注,将混凝土均匀地注入模板中,避免产生空洞。
2.3 加大修补措施如果在施工过程中发现缩孔问题,需要及时采取修补措施,以确保施工质量。
以下是一些常用的修补措施:•补丁修复:针对小面积的缩孔,可以使用混凝土补丁进行修复。
补丁的混凝土需要与原混凝土具有相同的成分和性能。
•重新浇筑:对于大面积的缩孔,需要重新浇筑混凝土。
在重新浇筑之前,需要清理和处理好原混凝土表面,确保新旧混凝土之间能够良好的结合。
重新浇筑时需要遵循之前提到的浇筑技术控制措施。
3. 缩孔的影响如果缩孔问题得不到有效的控制和修复,可能会带来以下几个方面的不良影响:•结构强度丧失:缩孔可能导致混凝土结构的强度丧失,从而影响到整个工程的安全性和稳定性。
•结构变形:缩孔也可能导致混凝土结构的变形增大,使得结构整体的稳定性下降。
•耐久性下降:缩孔会导致混凝土中的空隙增多,从而影响到混凝土的耐久性。
分析铸造缩松缺陷形成原因及对策

分析铸造缩松缺陷形成原因及对策铸造缩孔缺陷是在铸造过程中常见的一种问题,它会给制造业带来很多麻烦和损失。
本文将分析铸造缩孔缺陷的形成原因,并提出相应的对策,以期为相关行业提供帮助和指导。
一、铸造缩孔缺陷的形成原因分析1.1 完全凝固不均匀在铸造过程中,铸件凝固是逐渐进行的,如果凝固速度不均匀,就会导致缩孔缺陷的形成。
常见的原因包括铸件的凝固时间过短、冷却速度不均匀、局部温度过高等。
1.2 金属液收缩过大铸造过程中,金属液在凝固过程中会收缩,如果收缩过大,就容易形成缩孔。
这主要是由于铸件材料的物理性质不合理,或者是铸型的设计不合理所导致的。
1.3 铸造材料含有气体铸造材料中含有气体会在凝固过程中释放出来,如果释放过快,就会形成孔洞。
常见的原因是铸造材料中含有气体的含量过高,或者是在铸造过程中没有采取有效的排气措施。
1.4 基材与液态金属的相容性差如果铸件的基材与液态金属的相容性差,就容易在凝固过程中产生裂纹和缩孔。
一般来说,基材与液态金属的相容性差会导致界面张力增大,从而影响凝固过程。
二、对策提出2.1 优化铸造工艺参数通过优化铸造工艺参数,可以降低缩孔缺陷的发生概率。
具体来说,可以调整金属液的浇注温度和速度,控制铸件的凝固时间,改进冷却系统等措施。
2.2 优化铸造材料选择合适的铸造材料也是减少缩孔缺陷的关键。
应选择具有较低的收缩率和较好的流动性的材料,以确保凝固过程中的收缩程度可控。
2.3 采取有效的排气措施在铸造过程中,采取有效的排气措施可以减少气体对铸件凝固过程的干扰,从而降低缩孔缺陷的风险。
排气措施可以包括加入剂、提高浇注温度、采取适当的连续浇注等。
2.4 提高基材与液态金属的相容性为了减少缩孔缺陷的形成,可以通过提高基材与液态金属的相容性来增加界面的稳定性。
可以通过改变基材化学成分、调整金属液的配方等方式来实现。
三、结语以上是对铸造缩孔缺陷形成原因及对策的分析。
通过优化铸造工艺、材料选择、排气措施以及提高基材与液态金属的相容性等方法,可以有效降低缩孔缺陷的发生概率,提高铸件的质量和产能。
注塑缺陷原因分析与改善技术2

充填不足的原因有:a、成型条件设定不适当; b、模具的设计与制作不合理; c、成型品的肉厚太薄等所致。
成型条件的对策是: 提高熔料温度(熔胶筒温度)、提高模具温度、增大注射压力
/注射速度及提高熔料的流动性;模具方面可增大主流道或分流道尺 寸或者检讨浇口位置、大小、数目等,设法使节熔融材料容易流动 到型腔的各个角落。为了使成型空间内的气体顺利疏散,可在适当 位置开设排气槽/或排气针。
A、注塑缺陷原因分析及改善方法
三、银纹(料花、水花)
银纹的行成,一般是由于注射起动过快,使熔料及模腔中 的空气无法排出,空气夹混在胶料内,使得制品表面产生银丝 即是所谓的银纹。银纹不但影响外观,而且使塑件的机械强度 降低许多;为避免发生这种缺陷,必须找出原因并予以改善 1、塑料本身含有水份或洞剂
由于塑料在制造过程时曝露于空气中,吸入水气/油剂或者在混料时掺
十三、成品表面无光泽
成型品表面失去材料本来的光泽,形成乳白色层膜,或为 模糊状态(哑色)等均称为表面无光泽。
成型品表面光泽不良,大都是由于模具表面状态不良所致。 模具表面抛光不良或有模垢时,成型品表面当然得不到良好的 光泽;使用过多的离型剂或油脂性离型剂亦是表面光泽不良的原 因。材料吸湿或含有挥发物及异质物混入(污染),亦是造成 制品表面光泽不良的原因之一。
塑胶课
讲师:林勤
认识注塑加工
注塑加工是一门知识面广、技术性和经验性强的行 业,它涉及到塑料性能、注塑模具结构、注塑机功能、 注塑工艺调校、着色技术、水口料回收/利用、品质控 制及生产管理等方面的知识。在注塑生产过程中,会 经常出现一些现象(如:喷嘴流延、漏胶、水口拉丝、 粘模、塑化噪音、螺杆打滑、开模困难等)及产品质 量缺陷(如:缩水、缺胶、披峰、夹水纹、水波纹、 气纹、流纹、料花、开裂、粘模、顶白、拖花、漏胶、 内应力、气泡、色差、盲孔、断柱、翘曲变形等), 如何快速有效地改善这些注塑不良现象,仅凭过去的 经验是不够的,需要全面系统地掌握注塑专业技术知 识和积累丰富的实践经验,学会科学分析问题和处理
注塑件缺陷分析与改善(八)缩孔

注塑件缺陷分析与改善(八)缩孔缩孔(真空泡、空穴)是制品内部的缩孔表现为圆形或拉长的气泡形式(如图3-9)。
透明制品可以从外面看出里面的缩孔,不透明的制品无法从外面看见。
注塑件出现缩孔现象会影响产品的强度和力学能力,如果塑件是透明制品,则缩孔还会影响制品的外观。
下面对缩孔的成因及改善作简要分析。
1、缩孔的原因分析缩孔是因熔体在冷却收缩时未能得到充分的熔体补充而引起的。
缩孔现象常常出现在塑件的厚壁区,如加强筋或支撑住与塑件表面的相交处。
塑件厚壁区出现缩孔是熔体转为固体时,壁厚处体积收缩慢,形成拉应力,此时如果制品表面硬度足够,而又无熔体补充则制品内部便形成空洞。
缩孔通常产生在壁厚部位主要与模具冷却快慢有关,熔体在模具内的冷却速度不同,不同位置的熔体的冷却程度就会不一样,如果此时冷却层有足够的刚度抵抗其收缩应力,则在制品中心部分形成真空。
2、缩孔的改善方法(1)模具方面a) 模具温度过低:要提高模具温度(使用模温机)。
b) 成品断面,筋或柱位过厚:改善产品的设计,尽量使用壁厚均匀。
c) 浇口尺寸太小或位置不当:改善浇口或改变浇口位置(壁厚处)。
d) 流道过长或太细(熔料容易冷却):缩短流道长度或加粗流道。
e) 流道冷料穴太小或不足:加大冷料穴或增开冷料穴。
f) 射嘴阻塞或漏胶(发热圈会烧坏):拆除或者清理射嘴或重新对嘴。
(2)注塑工艺方面a) 注射压力太低或注射速度过慢:要提高注射压力或注射速度。
b) 保压压力或保压时间不足:提高保压压力,延长保压时间。
c) 熔料温度偏低或射胶量不足:提高熔料温度或增加熔胶行程。
d) 模内冷却时间太长:减少模内冷却,使用热水浴冷却。
e) 水浴冷却过急(水温过低):提高水温,防止水浴冷却过快。
f) 背压太小(熔料密度低):适当提高背压,增大熔料密度。
(3)设备方面a) 检查螺杆及止逆阀三件套是否磨损。
b) 增大射嘴孔径。
缩孔异常分析及对策(王子炜)_图文

漆雾缩孔
上海天地涂料有限公司
缩孔理论概述
缩孔问题对于常温干燥成膜的溶剂型涂料来说往往不太明显,但 是对于需要高温烘烤的溶剂型涂料来说却是十分突出的问题。
配方中所采用的树脂或其它高分子聚合物的相对分子质量分布范 围太宽,其中可能含有一些低分子化合物,或者含有相对分子质量过 高的化合物,有的甚至是胶凝物。如低分子化合物与颜料混合时,虽 然能混溶,但是在高温烘烤时,溶剂熔融物黏度很大,当低分子物从 颜料外层挥发出来,随着固化的发展,树脂熔融物无法再流平而形成 凹陷的缩孔;如遇高分子胶凝物与颜料混合,那么它们之间就难以达 到真正的混溶,在这种条件下,当涂层在高温烘烤时,由于组分混溶 不佳,其表面张力也达不到平衡,这个过程是十分短促的,它们之间 不可能有充分的流平时间,随着涂膜的形成,最后涂膜表面出现缩孔 或流平状态不佳的情况。
上海天地涂料有限公司
缩孔理论概述
在制造溶剂型涂料的过程中,如果物料混合效果不好,或挤出混炼质量不 高,没有把颜料凝聚团打碎分散,这种凝聚团的出现,表明涂层中必然存 在着气团,这样已润湿的颜料粒子与少量未润湿的颜料干粒子之间在涂层 上的表面张力是不相同的。当固化成膜时,由于气体蒸发和粒子间不均匀 的相聚或迁移,就造成了涂膜表面的缩孔,甚至产生针孔、麻点。
上海天地涂料有限公司
缩孔
上海天地涂料有限公司
缩孔
上海天地涂料有限公司
引起的主要原因
●环境原因 ○喷涂环境的空气洁净度差,有灰尘、纤维等杂质 ○空气流通不良、漆雾过多、 ○喷涂温度过高或稀释剂挥发太快
●设备、机器原因 ○喷涂压力不足、雾化不良; ○喷抢清洗不良; ○输漆循环系统处理不良、过滤网选定不合适
●涂装作业时的原因 ○工作人员服装不洁或材质容易掉纤维; ○车体清扫不良或清扫材质容易掉纤维 ○底材没有除去凸起物
缩孔的原因和处理方法

缩孔的原因和处理方法缩孔是一种常见的材料断裂问题,它通常发生在材料中的孔洞或裂纹处,导致材料的强度和韧性下降。
缩孔的原因很多,包括材料的制造过程、材料的化学成分以及外部环境的影响等。
本文将就缩孔的原因和处理方法展开讨论。
我们来看一下导致缩孔的主要原因。
其一是材料的制造过程中存在的问题。
例如,材料在铸造、锻造或焊接过程中,由于工艺参数的不合理或操作不当,容易产生内部缺陷,如气孔、夹杂物等。
这些内部缺陷会在材料中形成缩孔,降低了材料的强度和韧性。
其二是材料的化学成分对缩孔的影响。
某些元素或化合物的存在会增加材料的脆性,使其更容易形成缩孔。
例如,硫、磷等元素会降低钢材的韧性,增加缩孔的发生几率。
此外,材料中的非金属夹杂物也会促使缩孔的生成。
其三是外部环境对材料的影响。
在一些特殊的工作环境中,例如高温、高压或腐蚀性介质的作用下,材料容易产生缩孔。
这是因为在这些极端条件下,材料的内部结构容易发生变化,从而导致缩孔的形成。
针对缩孔问题,我们可以采取一些有效的处理方法。
首先,要加强材料的质量控制。
在材料的制造过程中,要严格控制工艺参数,确保材料的内部缺陷尽量减少。
同时,要加强对原材料的筛选,避免使用含有大量非金属夹杂物的材料。
可以通过改变材料的化学成分来减少缩孔的发生。
例如,可以降低材料中硫、磷等元素的含量,增加钢材的韧性。
此外,可以采用一些特殊的合金设计,使材料具有更好的抗缩孔能力。
对于在特殊工作环境下容易产生缩孔的材料,可以采取一些防护措施。
例如,在高温环境下使用耐热合金材料,可以减少缩孔的发生。
在腐蚀性介质中工作的材料可以选用耐蚀材料,提高材料的抗蚀性能。
定期对材料进行检测和维护也是减少缩孔的有效手段。
通过无损检测技术,可以及时发现材料中存在的缺陷,并采取相应的修复措施。
另外,对于承受重要载荷的结构材料,要定期进行维护和检修,确保其正常运行。
缩孔是一种常见的材料断裂问题,其产生原因复杂多样。
通过加强材料的质量控制,改变材料的化学成分,选择合适的材料和加强维护等方式,可以有效减少缩孔的发生。
卷钢涂装时异常及对策

一、表面缺陷1、缩孔涂料涂覆后收缩,局部露出底面,呈小圆形或椭圆形漆膜凹陷。
措施:A:确保带钢表面洁净,无油、水、杂质等。
B:确保底漆冷却水洁净无油污。
C:涂料与带钢表面温度应接近。
D:调整涂料粘度。
E:添加表面活性剂。
2、辊印沿带钢运行方向,在固化的漆膜表面上有凹凸不平的线条或痕迹。
措施:A:调整涂漆辊与板面的压力和间隙。
B:保证涂漆辊表面平整无赃物,硬度不能太高。
C:调整涂料粘度。
D:添加表面活性剂,提高涂料流平。
E:调节辊速比。
3、起泡漆膜上有米粒状浮起小泡,内部充满液体或气体。
措施:A:检查炉温曲线是否合理,避免溶剂蒸发过快。
B:检查涂覆前板面是否有水或其它污染残留。
C:检查涂料是否污染或在高湿环境下长期存放。
D:调整涂料粘度。
4、局部漏底在板面上有一部分没有涂上,露出基材或底漆。
措施:A:检查基板形状,有无凹陷部位。
B:检查涂漆辊表面是否有缺陷。
C:提漆辊提料不好或涂料液面太低。
5、颗粒或划痕在板面上有颗粒或划痕措施:A:涂料中混入异物,检查供漆管口过滤网是否破损。
B:检查涂漆辊表面是否有异物。
6、花斑涂料附着量不均匀,在板面形成形状怪异、颜色光泽不一致的斑痕。
措施:A:调整提料辊的转速。
B:提高漆盘中的涂料液面。
C:涂料搅拌要均匀。
D:调整涂覆辊使其表面涂料形成均匀的条纹状。
E:连续使用的涂料保证黏度和温度一致。
7、针孔漆膜表面由于溶剂或水分膨胀形成的小孔。
措施:A:检查涂装前板面是否有水。
B:降低进口炉温,确保溶剂逐步蒸发。
C:降低涂料黏度,确保涂料流平充分。
二、性能缺陷1、T弯性能差在现用基板上T弯检测不合格。
措施:A:检查前处理是否充分,铬化层是否太厚或不均匀,前处理液是否老化。
B:检测板温是否合理,确保漆膜不过烘或固化不良。
C:化验室检测涂料,确认是否为涂料本身有问题。
2、耐MEK性能差彩板耐MEK不合格,或有点状掉漆。
措施:A:检查烘烤温度是否达到要求,是否温度线速不配套导致固化不充分。
塑料件常见缺陷及对策手册

塑料件常见缺陷及对策手册
塑料件常见缺陷及对策手册如下:
1. 熔体流动不畅:主要表现为铸件的形状或尺寸变化,可能会影响产品的外观和使用效果。
解决方案包括提高模具温度、加大喷嘴孔径、增加压力等。
2. 表面气泡:主要是由于熔融状态下的气体逸出不完全导致的,会影响产品的外观和质量。
解决方法包括提高熔体温度、增加注射速度、调整模具结构等。
3. 热裂纹:主要是由于材料热应力引起的,会影响产品的性能和寿命。
解决方案包括减少注射压力、降低模具温度、改进模具结构等。
4. 缩孔:主要是由于熔体内部存在气体或材料中含水过多导致的。
解决方案包括预干燥原材料、增加熔体温度、减少注射速度等。
5. 毛边和毛刺:主要是由于模具设计不合理、注射速度过快等原因导致的。
解决方案包括调整模具结构、降低注射速度等。
6. 非均匀收缩:主要表现为铸件形状或尺寸的变化不一致,会影响产品的精度和性能。
解决方案包括增加模具温度、降低注射压力等。
7. 材料老化:主要是由于材料长时间暴露在高温、紫外线等环境下导致的。
解决方案包括选择耐老化的材料、优化制造工艺等。
以上是塑料件常见缺陷及对策手册的简单介绍,具体情况还需要根据实际生产中遇到的具体问题进行分析和处理。
电泳缺陷分析及对策
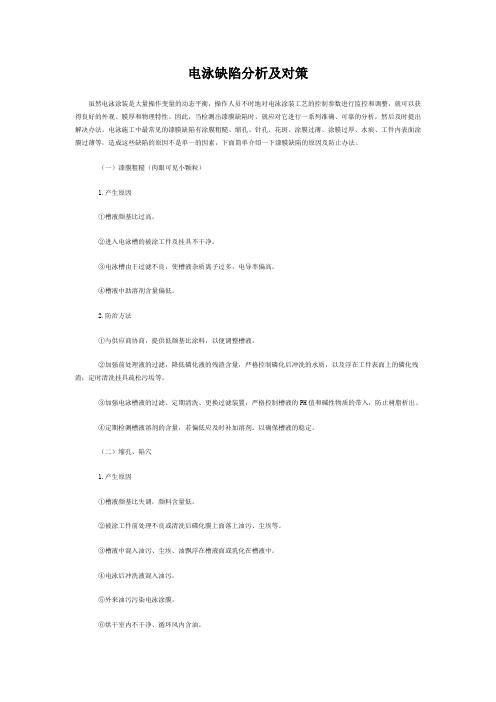
电泳缺陷分析及对策虽然电泳涂装是大量操作变量的动态平衡,操作人员不时地对电泳涂装工艺的控制参数进行监控和调整,就可以获得良好的外观、膜厚和物理特性。
因此,当检测出漆膜缺陷时,就应对它进行一系列准确、可靠的分析,然后及时提出解决办法。
电泳施工中最常见的漆膜缺陷有涂膜粗糙、缩孔、针孔、花斑、涂膜过薄、涂膜过厚、水痕、工件内表面涂膜过薄等,造成这些缺陷的原因不是单一的因素,下面简单介绍一下漆膜缺陷的原因及防止办法。
(一)漆膜粗糙(肉眼可见小颗粒)1.产生原因①槽液颜基比过高。
②进入电泳槽的被涂工件及挂具不干净。
③电泳槽由于过滤不良,使槽液杂质离子过多,电导率偏高。
④槽液中助溶剂含量偏低。
2.防治方法①与供应商协商,提供低颜基比涂料,以便调整槽液。
②加强前处理液的过滤,降低磷化液的残渣含量,严格控制磷化后冲洗的水质,以及浮在工件表面上的磷化残渣;定时清洗挂具疏松污垢等。
③加强电泳槽液的过滤。
定期清洗、更换过滤装置,严格控制槽液的PH值和碱性物质的带入,防止树脂析出。
④定期检测槽液溶剂的含量,若偏低应及时补加溶剂。
以确保槽液的稳定。
(二)缩孔、陷穴1.产生原因①槽液颜基比失调,颜料含量低。
②被涂工件前处理不良或清洗后磷化膜上面落上油污、尘埃等。
③槽液中混入油污、尘埃、油飘浮在槽液面或乳化在槽液中。
④电泳后冲洗液混入油污。
⑤外来油污污染电泳涂膜。
⑥烘干室内不干净、循环风内含油。
2.防止方法①调整槽液的颜基比,补加色浆提高颜料含量。
②加强被涂工件脱脂工序的管理,确保磷化膜不被二次污染。
③在槽液循环系统安装除油过滤装,同时检查油污染来源,以便彻底清除油法。
④加强后冲洗液水质的检测,定期清洗更换过滤袋,以确保后冲洗水过滤质量。
⑤保持涂装环境洁净,清除对涂装有害的物质,尤其是含有机硅物质源(如电缆、拉延油、防锈油、防焊渣粘结剂、密封胶等),涂装车间及相关车间的设备及工艺介质所使用的原材料和辅助材料都不能含有酯酮。
⑥按工艺规定,定期清扫烘干室,保持烘干室和循环热风的清洁。
锂电池制程异常案例分析
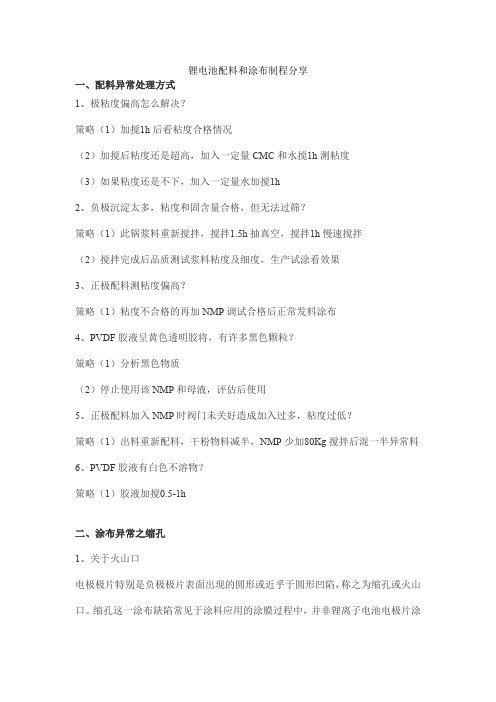
锂电池配料和涂布制程分享一、配料异常处理方式1、极粘度偏高怎么解决?策略(1)加搅1h后看粘度合格情况(2)加搅后粘度还是超高,加入一定量CMC和水搅1h测粘度(3)如果粘度还是不下,加入一定量水加搅1h2、负极沉淀太多,粘度和固含量合格,但无法过筛?策略(1)此锅浆料重新搅拌,搅拌1.5h抽真空,搅拌1h慢速搅拌(2)搅拌完成后品质测试浆料粘度及细度,生产试涂看效果3、正极配料测粘度偏高?策略(1)粘度不合格的再加NMP调试合格后正常发料涂布4、PVDF胶液呈黄色透明胶将,有许多黑色颗粒?策略(1)分析黑色物质(2)停止使用该NMP和母液,评估后使用5、正极配料加入NMP时阀门未关好造成加入过多,粘度过低?策略(1)出料重新配料,干粉物料减半,NMP少加80Kg搅拌后混一半异常料6、PVDF胶液有白色不溶物?策略(1)胶液加搅0.5-1h二、涂布异常之缩孔1、关于火山口电极极片特别是负极极片表面出现的圆形或近乎于圆形凹陷,称之为缩孔或火山口。
缩孔这一涂布缺陷常见于涂料应用的涂膜过程中,并非锂离子电池电极片涂布时特有的现象。
如下图2、缩孔的形成在涂布过程中可能会产生各种各样的缺陷,气泡、肥边、火山口、多边形凹陷、橘皮状等,缩孔是最常见的问题之一。
从根本上意义讲由于成膜时所产生的表面张力梯度造成的,这种现象称之为Maragoni效应。
材料间表面张力不匹配,是产生缩孔的主要诱因。
粘度、流动性以及干燥风速和烘箱温度等都可能改变表面张力及其作用过程,从而诱发缩孔的产生。
固化前可流动膜面中存在低表面张力的微粒(如粉体,油滴等),造成中央表面张力较低,流体以污染物为中心向四周迁移,最终形成边缘高于中心的圆形下陷(缩孔)。
3、缩孔的预防选用相容性好的分散剂或分散介质,减少涂料本体中低表面张力大颗粒(包括大液滴)的存在;添加疏水表面活性分散剂和溶剂等也可以控制缩孔的程度。
4、涂布缩孔解决方案1)材料表面结构的进一步改性通过对石墨材料表面进一步的改性,提高极性基团,提高其亲水性;2)调整粘合剂有效成分的分子结构通过调整粘合剂有效成分的分子结构,降低其极性基团的含量,有效降低LA型水性粘合剂产品的表面张力,提高其对石墨材料的润湿程度。
铸件缩孔和缩松缺陷,十点分析
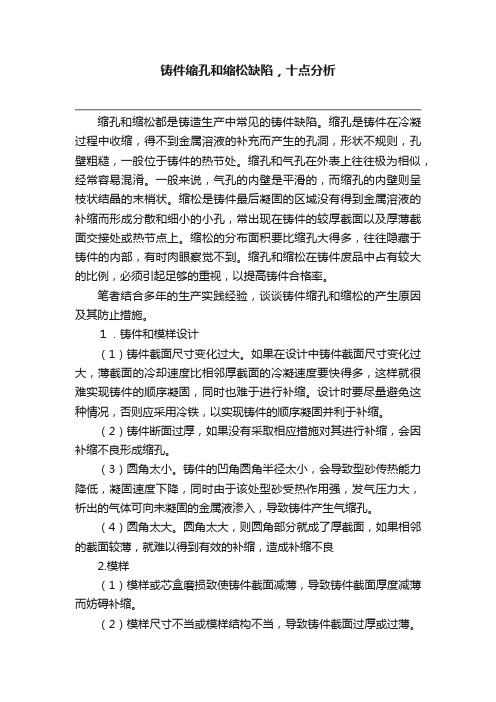
铸件缩孔和缩松缺陷,十点分析缩孔和缩松都是铸造生产中常见的铸件缺陷。
缩孔是铸件在冷凝过程中收缩,得不到金属溶液的补充而产生的孔洞,形状不规则,孔壁粗糙,一般位于铸件的热节处。
缩孔和气孔在外表上往往极为相似,经常容易混淆。
一般来说,气孔的内壁是平滑的,而缩孔的内壁则呈枝状结晶的末梢状。
缩松是铸件最后凝固的区域没有得到金属溶液的补缩而形成分散和细小的小孔,常出现在铸件的较厚截面以及厚薄截面交接处或热节点上。
缩松的分布面积要比缩孔大得多,往往隐藏于铸件的内部,有时肉眼察觉不到。
缩孔和缩松在铸件废品中占有较大的比例,必须引起足够的重视,以提高铸件合格率。
笔者结合多年的生产实践经验,谈谈铸件缩孔和缩松的产生原因及其防止措施。
1.铸件和模样设计(1)铸件截面尺寸变化过大。
如果在设计中铸件截面尺寸变化过大,薄截面的冷却速度比相邻厚截面的冷凝速度要快得多,这样就很难实现铸件的顺序凝固,同时也难于进行补缩。
设计时要尽量避免这种情况,否则应采用冷铁,以实现铸件的顺序凝固并利于补缩。
(2)铸件断面过厚,如果没有采取相应措施对其进行补缩,会因补缩不良形成缩孔。
(3)圆角太小。
铸件的凹角圆角半径太小,会导致型砂传热能力降低,凝固速度下降,同时由于该处型砂受热作用强,发气压力大,析出的气体可向未凝固的金属液渗入,导致铸件产生气缩孔。
(4)圆角太大。
圆角太大,则圆角部分就成了厚截面,如果相邻的截面较薄,就难以得到有效的补缩,造成补缩不良2.模样(1)模样或芯盒磨损致使铸件截面减薄,导致铸件截面厚度减薄而妨碍补缩。
(2)模样尺寸不当或模样结构不当,导致铸件截面过厚或过薄。
设计时应注意控制模样的厚度,尽量使邻近较厚截面的薄截面保持最大的厚度。
3.砂箱(1)上箱太浅。
生产中为了节省型砂用量或为了降低砂箱和造型成本而使用高度不够的上箱,这是造成缩松缺陷的常见原因。
上箱太浅,会降低金属液的静压力,以致难以进行补缩,补缩压力不够,会导致产生缩松或缩孔,或二者兼有之。
汽车涂装面漆缩孔缺陷排查模型及应用

汽车涂装面漆缩孔缺陷排查模型及应用作者:陈磊陈桂林贾亮郑晓旭田刚李映图来源:《汽车与驾驶维修(维修版)》2023年第09期摘要:缩孔为汽车涂装行业常见问题,而且导致缩孔的物质种类繁多,某些物质极少量即可形成缩孔,只能通过批量生产烘干漆膜验证缩孔原因。
根据喷涂膜厚目标及工艺过程,需要通过逐层漆膜、逐个工位以及逐一要素来排查导致漆膜表面张力变化因素,并针对性采取预防措施。
本文通过对干膜缩孔缺陷形态进行详细分析,确定排查优先级。
物料喷涂前采用物料升温老化降低流平效果来模拟缺陷;喷涂后采用车身湿膜极限暴露来验证过程中缩孔影响因素。
在此模型指导下发现,面漆烘干炉入口温差导致冷凝物析出形成缩孔问题,通过对烘干炉风平衡调节实现车身均匀升温溶剂均匀挥发,从而避免在烘干炉入口段形成冷凝物,解决缩孔问题,并完善缩孔缺陷排查模型。
关键词:面漆缩孔;漆膜;表面张力;温差中图分类号:U463.82+1 文献标识码:A0 引言汽车涂装生产过程中,车身漆膜在成膜过程中由于表面张力[1] 差异而形成表面凹陷缺陷,定义为缩孔[2]。
缩孔为汽车涂装行业常见问题,排查难点有:能导致缩孔的物质种类繁多;数量极少即可形成缩孔;验证方法以批量喷车烘干后验证,具有严重滞后性。
因此,总结汽车涂装缩孔缺陷排查模型,用于指导缩孔缺陷排查及预防,减少返修成本,提升过程管理水平,并持续推动工艺、物料革新具有意义。
汽车车身常见漆膜构成如图1 所示,普遍包含电泳、预喷涂层、色漆和清漆层,工艺通用设计为电泳烘干、色漆闪干和清漆烘干方式。
不同的工艺标准决定了各涂层的厚度,从而决定了设备选型、工艺布局和物料选择等。
因此缩孔缺陷排查要根据生产线特点而开展[3],具有很强的现场特殊性。
本文根据喷漆成膜共性梳理出影响缩孔的主要因素,从而针对性预防管理缩孔缺陷。
由于在喷涂过程中,涂层是逐层覆盖的过程,每层涂层在成膜及烘干过程中都会出现漆膜表面张力变化[4],都可能在过程中形成缩孔缺陷。
射出成型之缺陷异常+原因分析与对策

射出成型之缺陷异常原因分析与对策【射出成型之缺陷異常原因分析与对策】概述成型品原则上都是依据规格/标准和客户的要求制造的,但在实际注塑秤过程中它的变化仍是相当广泛而复杂的;有时当生产进行得很顺利时,会突然产生缩水、变形、裂痕、银纹或其它不良缺陷等。
在注塑时我们需从胶件所产生的缺陷,来准确分析/判断问题点所在,找出解决问题的方法,这是一种专业性的技术及经验的累积。
有时只要变更注塑工艺条件、对模具/机器方面稍做调整与改善或更换所使用的原料,就可以解决问题。
注塑成型中对成型品物性的主要影响因素可从以下四个方面来考虑:A、原料B、注塑机C、注塑模具D、成型条件注塑过程中出现的异常问题很多,主要是“产品质量缺陷”和“注塑生产中特有的异常现象”两大类。
注塑产品常见的质量缺陷有:缺胶、缩水、银纹(料花)、披锋(飞边)、烧焦、气泡(缩孔)、水波纹、喷射纹(蛇纹)、流纹(流痕)、夹水纹、裂纹(龟裂)、顶白、表面无光泽、翘曲变形、黑条、混色、拖花、透明度不足、尺寸偏差、剥离(起皮)、冷料斑、黑点、气纹、色差、盲孔、断柱等……注塑生产中特有的异常现象有:喷嘴流涎(流涕)、漏胶、胶件粘模、水口拉丝、嵌件不良、多胶、断针、堵嘴、顶针位穿孔、模印、压模、塑化噪音、下料不畅、螺杆打滑、开模困难等等。
下面分析各种注塑缺陷及异常现象产生的原因并探讨其解决问题的方法。
A、注塑常见缺陷原因分析及改善方法目錄1、走胶不齐的原因分析及改善对策且 (2)2、缩水(缩痕)的原因分析及改善对策 (3)3、银纹(料花、水花)的原因分析对改善对策 (5)4、披锋(飞边)/烧焦(困气)原因分析及改善对策 (8)5、缩孔(真空泡)的原因分析及改善对策 (9)6、水波纹的原因分析及改善对策 (10)7、喷射纹(蛇纹)/流纹(流痕)的原因分析及改善对策 (11)8、夹水纹(熔接线)的原因分析及改善对策 (12)9、裂纹(龟裂)的原因分析及改善对策 (13)10、顶白或顶爆的原因分析及改善对策 (14)11、成品表面无光泽/胶件翘曲变形的原因分析及改善对策 (15)12、黑条(黑纹)的原因分析及改善对策 (17)13、混色的原因分析及改善对策 (18)14、拖花(拉伤)/透明度不足的原因分析及改善对策 (19)15、尺寸偏差/剥离(起皮)的原因分析及改善对策 (20)16、冷料斑/黑点的原因分析及改善对策 (21)17、气纹(阴影)的原因分析及改善对策 (22)18、色差的原因分析及改善对策 (23)19、强度不足的原因分析及改善对策 (24)20、气泡/金属嵌件不良的原因分析及改善对策 (25)21、盲孔的原因分析及改善对策 (26)22、内应力产生的原因及改善对策 (27)23、表面浮纤产生的原因对改善对策 (28)24、白点产生的原因及改善对策 (29)25、注塑生产特有的异常现象(11种现象) (30)26、其它注塑异常现象(10种情况) (36)一、走胶不齐(缺胶未射滿)provides venture platform, makes many youth round has venture dream, for national solution has important of employment problem. Relevant departments units carefully to discover, cultivate talent. From the perspective of Dongping, contradiction of rapid economic development and personnel shortages. Currently facing the industry transformation and upgrading, and transform and upgrade traditional industries, is the development of new industries such as tourism, logistics, e-commerce, we still lack a large number of capital operation and management of talents, the lack of technological innovation, technology transfer, product research and development, tourism services and other high-level professional and technical personnel. Especially with theIndustry further develops, the demand is growing. We must stand in the global and strategic height, with a high degree of political responsibility and historical mission, counties implement talent strategies as a major and pressing task to seize good, practical human resource development as industrial counties of the country. Departments at all levels must firmly establish the "talent is wealth, talent is competitive, talent is creativity" concept, fully aware of the extreme importance of talent, the real talent working on the agenda, the primary task of the primary resources to support the development of talent. 2 the construction of enterprisers ' as the starting point, and promote the transformation and充填不足是溶融的塑料未完全注满模具成型空间的各个角落之现象。
简述铸件中缩孔的产生原因及其防止方法

简述铸件中缩孔的产生原因及其防止方法铸件是金属熔化后在模具中冷却凝固成型的工艺,其制作过程中容易产生各种缺陷,其中缩孔是常见的一个问题。
缩孔是指铸件中含有孔隙,并且表面凹陷或凸起的缺陷,严重影响铸件的力学性能。
下面将从铸件中缩孔的产生原因以及防止方法两个方面进行简述。
一、铸件中缩孔的产生原因1.高熔点和低液态温度:某些合金的熔点较高,浆料在浇注过程中凝固速度快,易产生缩孔。
2.铸型材料不合适:铸型材料的选择不合理也会导致缩孔的产生。
比如铸型材料不耐火或热膨胀系数太大,容易损坏或产生内应力,进而引起缩孔。
3.浇注温度过低:浇注温度过低会导致凝固时间过长,浆料在凝固过程中收缩不完全,形成缩孔。
4.浇注速度过快:如果铸件的浇注速度过快,会导致气体无法有效排出,导致缩孔的产生。
5.气体和杂质的存在:铸料中夹杂有气体和杂质,会在凝固过程中形成缩孔。
二、铸件中缩孔的防止方法1.提高浇注温度:适当提高浇注温度可以减缓凝固时间,增加液态时间,有利于气体的排出,减少缩孔的产生。
2.控制浇注速度:合理控制浇注速度,避免过快过慢,以保证气体和杂质顺利排出,并且减少凝固收缩,减少缩孔的产生。
3.选择合适的铸型材料:铸型材料要具有一定的耐火性和热膨胀系数,并且能够充分耐高温应力,避免产生内应力引起缩孔。
4.使用脱气剂:在铸造过程中添加一定比例的脱气剂,能够有效除去铸料中的气体和杂质,降低铸件中气孔和夹杂物的数量。
5.采用真空冶炼和真空注射技术:通过真空冶炼可以减少金属中含气量,降低铸件中气孔的产生。
同时,真空注射技术可以使浆料在铸造过程中迅速排除气体,避免缩孔的产生。
6.优化浇注系统和浇注工艺:设计和优化浇注系统可以改变浇注方式,减少铸件内的气体和杂质,减少缩孔的产生。
7.特殊处理工艺:对于一些特殊的铸件,如大型铸件、厚壁铸件等,可以通过局部预热、冷却措施等特殊处理工艺,改善凝固过程,减少缩孔的产生。
总之,铸件中缩孔的产生是多种因素综合作用的结果,防止缩孔的产生需要从原材料、铸型材料、浇注工艺等多个方面综合考虑,通过优化工艺、控制温度和速度等方式来减少缩孔的发生,保证铸件质量。
汽车涂装异常分析及对策
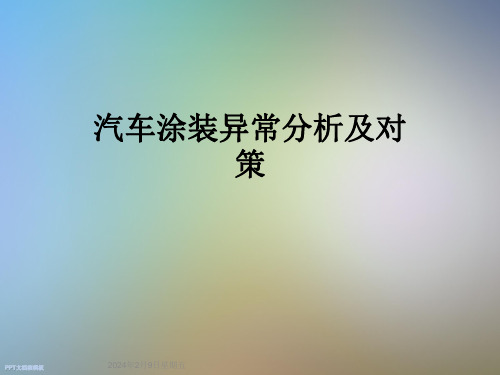
•
白化、发白
现象及原因
○ 涂膜表面好似有霞雾,呈乳 白色,失去光泽
○ 易发生于高温多湿条件下。 涂装后,因溶剂中的溶剂快 速挥发致使空气中的水分凝 结,作用于涂膜面而使其失 去光泽。
•
可能引起的原因
• 环境原因
○ 湿度高
○ 压缩空气带入水份
• 涂装原因
○ 被涂物温度低于室温
• 涂料原因
涂料达到良好的雾化 ●一次喷涂膜厚增加,改善漆膜流动性 ●降低喷涂环境温度、风速,减慢溶剂挥发速度 ●降低被涂物的温度 ●加强操作人员培训、调整合适的喷涂速度、喷涂距离
处置
●轻微桔皮抛光即可(以#500~#800~#1000的砂纸水磨,再以中目→ 细目→极细目研磨修正)
●严重桔皮则需打磨后返工
•
流挂
持小于70%)
•
鲜艳性不良
现象:
○ 漆膜出现反射影像不够鲜明,像有一层雾气遮盖着,这是由于 射向涂膜的反射光向反射方向两侧散射,造成反射影像不够鲜明 ,这种病态称为涂膜的鲜艳性不良。主要表现在其装饰性差,一 般平滑性、光泽不良会导致鲜艳性差 ○ 鲜艳性用PGD表示,一般高级轿车鲜艳性为0.8~1.0;普通型轿 车、轻型车等要求在0.6~0.7左右,如低于此规定数据,则称为鲜 艳性不良
•
对策及处置
• 对策:
○在涂装车间,无论是设备、工具还是生产用辅助材料等,绝对 不能带有对油漆有害的物质,尤其是硅酮。
○确保压缩空气清洁,应无油无水 ○确保涂装环境清洁,空气中应无尘埃、油雾和漆雾等 ○严禁裸手、脏手套和脏擦布接触被涂面,确保被涂面洁净 ○旧涂层应充分打磨彻底、擦净 ○改良涂料性能、提高涂料对缩孔的敏感性
●定期清扫送风系统、整理过滤无纺布、保证喷涂环境的空气 洁净度
圆坯内部缩孔、疏松的优化改进

圆坯内部缩孔、疏松的优化改进江苏某圆坯厂生产中低碳圆坯,主要规格为φ310、φ350、φ400,主要钢种为20钢、45钢等常规中低碳钢种。
在生产过程中,发现圆坯内部有明显的疏松和缩孔,同时偶有发现中间裂纹,由于该厂生产的坯料主要为穿管坯料,此类缺陷为下游客户的生产带来了较高的异常报废率,严重影响了该厂的市场占有率。
为了提高本厂产品质量,特组织对产品质量进行攻关。
一、圆坯现状疏松疏松、缩孔从目前坯料的表现来看,在铸坯内部有明显的缩孔与疏松。
从等级判断来看,疏松约为1级,缩孔约为1.5级。
正是因为此种缺陷,在后续的穿管过程中出现较明显的内裂与掉肉现象,严重影响穿管质量。
二、原因分析2.1 疏松原因分析:疏松主要是钢芯在凝固末期,凝固收缩不均匀,液态钢水不能及时补缩,钢水在凝固过程中,部分杂质富集,晶粒之间出现空隙的现象,就是疏松。
针对此种现象,主要考虑钢水在凝固末期的补缩。
首选末端电磁搅拌进行改善。
其次要注意二冷水的梯度配制,控制二冷后期的均匀稳定,避免快速冷却。
2.2 缩孔原因分析:缩孔主要是凝固末端钢水凝固收缩不能得到钢水补充,出现缩孔。
缩孔里面有较多的夹杂富集和较明显的元素偏析,是后续轧制出现裂纹的主要原因,需要大力改善,严格控制,避免此类异常。
三、优化措施缩孔与疏松均与结晶器冷却与二冷有明显关系,为了合理掌控铸坯冷却,减少疏松与缩孔,主要采取以下措施进行优化:3.1 合理优化结晶器冷却,适当弱化结晶器冷却,减少一冷、二冷之间的冷却梯度,控制激冷层的均匀度;3.2 合理调整二冷各区之间的冷却配比,适当提高一冷、二冷水量,控制三区、四区水量,合理控制柱状晶的长度,合理提升柱状晶的比例。
四、结果验证经过一冷、二冷的优化的合理优化,铸坯内部得到了明显的改善,已经没有疏松现象,缩孔也控制在0.5级以内。
低倍优化结果如下:优化之后的坯料质量逐步趋于稳定,产品合格率由原来的95%提升到99.5%以上。
- 1、下载文档前请自行甄别文档内容的完整性,平台不提供额外的编辑、内容补充、找答案等附加服务。
- 2、"仅部分预览"的文档,不可在线预览部分如存在完整性等问题,可反馈申请退款(可完整预览的文档不适用该条件!)。
- 3、如文档侵犯您的权益,请联系客服反馈,我们会尽快为您处理(人工客服工作时间:9:00-18:30)。
气污染了油漆本身造成缩孔。
上海天地涂料有限公司
有害物质源
缩孔异常分析及对策
引起缩孔的根源
上海天地涂料有限公司
缩孔表现
上海天地涂料有限公司
缩孔的形成
上海天地涂料有限公司
润湿不良表象
上海天地涂料有限公司
A类缩孔:露底缩孔
上海天地涂料有限公司
B类缩孔:鱼眼
上海天地涂料有限公司
C类缩孔:带凹弧针孔
上海天地涂料有限公司
D类缩孔:凹穴
上海天地涂料有限公司
上海天地涂料有限公司
有害物质来源(个案参考)
1、链条油、机油、润滑油 2、输漆管道的输漆胶管或塑料管 3、防焊接飞溅剂 4、电缆电线外皮 5、化妆品(护手霜、摩丝、保湿霜) 6、密封胶(硅酮类) 7、聚氨酯发泡剂、含硅油的泡沫 8、脱模剂(各类) 9、压缩空气中的成分 10、灰尘(打磨灰、建筑灰尘、细小纤维)
在涂装工艺中,遇到不同生产单位的2种溶剂型涂料,由于组分有所区别 ,颜料粒子的性质也有明显的差异,如前期颜料粒子表面张力较小,这些 颜料粒子虽 经清扫,但很难清除彻底,在涂装室周壁、 管道或空气中尚 存在微量的粒子。当喷涂后期有较大表面张力粒子时,其涂层表面由于2 种颜料之间存在着表面张力的较大差异,该微粒对周围粒子产生排斥作用 ,这样涂膜表面必然会产生缩孔之类的弊病,若是前期的颜料粒子表面张 力较大,而后期的颜料粒子表面张力较小,那么极少量表面张力大的颜料 粒子落到大量表面张力小的颜料粒子中去,此情况下,涂膜表面出现缩孔 的机会就比较小。因此,在涂装施工中既要注意2种溶剂型涂料的混溶关 系,又要保持施工周围环境的洁净,主要是防止其它微粒及粉尘的侵入, 防止涂膜上出现缩孔或针孔的弊病。
上海天地涂料有限公司
缩孔
上海天地涂料有限公司
缩孔
上海天地涂料有限公司
引起的主要原因
●环境原因 ○喷涂环境的空气洁净度差,有灰尘、纤维等杂质 ○空气流通不良、漆雾过多、 ○喷涂温度过高或稀释剂挥发太快
●设备、机器原因 ○喷涂压力不足、雾化不良; ○喷抢清洗不良; ○输漆循环系统处理不良、过滤网选定不合适
漆雾缩孔
上海天地涂料有限公司
缩孔理论概述
缩孔问题对于常温干燥成膜的溶剂型涂料来说往往不太明显,但 是对于需要高温烘烤的溶剂型涂料来说却是十分突出的问题。
配方中所采用的树脂或其它高分子聚合物的相对分子质量分布范 围太宽,其中可能含有一些低分子化合物,或者含有相对分子质量过 高的化合物,有的甚至是胶凝物。如低分子化合物与颜料混合时,虽 然能混溶,但是在高温烘烤时,溶剂熔融物黏度很大,当低分子物从 颜料外层挥发出来,随着固化的发展,树脂熔融物无法再流平而形成 凹陷的缩孔;如遇高分子胶凝物与颜料混合,那么它们之间就难以达 到真正的混溶,在这种条件下,当涂层在高温烘烤时,由于组分混溶 不佳,其表面张力也达不到平衡,这个过程是十分短促的,它们之间 不可能有充分的流平时间,随着涂膜的形成,最后涂膜表面出现缩孔 或流平状态不佳的情况。
德国杜尔公司设计涂装流水线时设备图纸上全部注明:所有零部件 必须绝对无有机硅化合物(硅酮聚合物)
上海天地涂料有限公司
容易产生缩孔的涂料(排除异常情况)
1、清漆和含颜料少的色漆 2、烘干型涂料比自干、快干更容易产生 3、漆基、颜料、溶剂、助剂等选择及配比 不当,导致抗缩孔性能差的涂料 4、表面张力大、流平性和释放气泡性差的 涂料(水性涂料、丙烯酸、环氧、氨基醇酸 、聚酯、聚氨酯等树脂为基的涂料)
●涂装作业时的原因 ○工作人员服装不洁或材质容易掉纤维; ○车体清扫不良或清扫材质容易掉纤维 ○底材没有除去凸起物
●材料导致的原因 ○涂料变质,出现析出、反粗、絮凝等异常 ○涂料的颜料或闪光材质分散不良 ○涂料未过滤或过滤效果不好
上海天地涂料有限公司
油漆制造过程中针对缩孔注意事项
涂料配方设计时,抗缩孔性能适应不了客户现场的特殊情况; 粉料研磨不佳; 丙烯酸类添加剂结晶; 铝粉润湿不良 漆料中含有油污等污染物; 压缩空气中含有油污或在不洁净环境中施工或由于压缩空气的输送管道没有定期清
上海天地涂有限公司
缩孔理论概述
在制造溶剂型涂料的过程中,如果物料混合效果不好,或挤出混炼质量不 高,没有把颜料凝聚团打碎分散,这种凝聚团的出现,表明涂层中必然存 在着气团,这样已润湿的颜料粒子与少量未润湿的颜料干粒子之间在涂层 上的表面张力是不相同的。当固化成膜时,由于气体蒸发和粒子间不均匀 的相聚或迁移,就造成了涂膜表面的缩孔,甚至产生针孔、麻点。
上海天地涂料有限公司
人机料法环
上海天地涂料有限公司