轧钢机系统的模拟控制
轧钢机PLC控制系统设计

轧钢机PLC控制系统设计1 问题分析及解决方案1.1 问题描述在冶金企业中轧钢机是重要的组成部分,运用PLC实现对轧钢机的模拟,如右图。
当起始位置检测到有工件时,电机M1、M2开始转动M3正转,同时轧钢机的档位至A档,将钢板轧成A档厚度,当钢板运行到左检测位,电磁阀得电动作将左面滚轴升高,M2停止转动,电机M3反转将轧钢板送回起始侧。
此时起始侧再检测到有钢板,轧钢机跳到B档,把钢板轧成B档厚度,电磁阀得电,将滚轴下降,M3正转,M2转动,当左侧检测到钢板时M2停止转动,电磁阀得电将滚轴抬高M3反转,将钢板运到起始侧。
如此循环直到ABC三档全部轧完,钢板达到指定的厚度,轧钢完成。
1.2 分析过程该工作过程分为三个时序,当起始位置第一次检测到信号时,A档轧钢;起始位置第二次检测到信号时,B档轧钢;起始位置第三次检测到信号时,C档轧钢。
由于每个档位都要工作一段时间才能切换,可以用两个定时器来实现。
2 PLC选型及硬件配置PLC选型及硬件配置如图1。
图13 分配I/O地址表I/O地址表如图2。
图2 4 主电路图及PLC外部接线图4.1 主电路图主电路图如图3。
图34.2 PLC外部接线图PLC外部接线图如图4。
图45 控制流程图及梯形图程序5.1 控制流程图控制流程图如图5。
图5开始起始位置检测起始位置检测起始位置检测左侧位置检测左侧位置检测左侧位置检测A档轧钢B档轧钢C档轧钢回起始位回起始位结束YNYYYYYN NNNN5.2 T型图程序6 程序调试6.1 问题调试为了解决A、B、C三个档位的时序问题,我选择用三条T型图程序来实现,但输出有重复,导致T型图程序运行正确但仿真出现错误。
于是我改变方案,采用了M存储器来代替输出,仿真成功。
6.2 仿真图A档运行:传送回初始位:B档运行:C档运行:7 心得体会通过这次设计实践。
我学会了PLC的基本编程方法,对PLC的工作原理和使用方法也有了更深刻的理解。
在对理论的运用中,提高了我们的工程素质,在没有做实践设计以前,我们对知道的掌握都是思想上的,对一些细节不加重视,当我们把自己想出来的程序与到PLC中的时候,问题出现了,不是不能运行,就是运行的结果和要求的结果不相符合。
(完整word版)PLC轧钢机控制系统模拟

PLC实验报告实验二轧钢机控制系统模拟一、实验目的1、掌握可编程控制器的工作原理。
2、通过动手接线,提高学生的实际动手能力以及加强对PLC基本结构的了解。
3、通过实验,,加强学生对PLC逻辑顺序编程的理解。
二、实验内容三.实验设计1.硬件接线图2.I/O端口分配表(1).输入端口A B C DX0X1X2X3启动停止检查钢板到达检查有无钢板(2).输出端口E F G H I J K L Y0Y1Y2Y3Y4Y5Y6Y7正转反转厚钢板中钢板薄钢板主轴电机传送带电磁阀3. 软件梯形图四.工作原理整个控制过程分为7个阶段,用M0,M1,M2,M3,M4,M5,M6来表示这7个阶段。
“按下启动按钮,传送带运行”为阶段M0;“检查有无D,若有,调高阀L动一次,G亮,电机J运行,传送电机正转”为阶段M1;“检查是否到达C,,若到,J.K停止,电机反转”为阶段M2;“检查有无D,若有,传送带运行,调高阀L动一次,H亮,电机J运行,传送电机正转”为阶段M3;“检查是否到达C,,若到,J.K停止,电机反转”为阶段M4;“检查有无D,若有,传送带运行,调高阀L动一次,I亮,电机J运行,传送电机正转”为阶段M5;“检查是否到达C,,若到,正转,钢板送出去,停止”为阶段M6。
整个控制过程中,有且仅有一个M 为1,其余M均为0。
按下A后,M0得电自锁;随后搬动开关检查有钢板传感器D,M1得电自锁,且M0断开;随后搬动开关检查有钢板传感器C,M2得电自锁,且M1断开;随后搬动开关检查有钢板传感器D,M3得电自锁,且M2断开;随后搬动开关检查有钢板传感器C,M4得电自锁,且M3断开;随后搬动开关检查有钢板传感器D,M5得电自锁,且M4断开;随后搬动开关检查有钢板传感器C,M6得电自锁,且M5断开。
M0,M1,M3,M5得电时,传送带K运行;M1,M3,M5得电时,调高阀L动作一次;M1,M2得电时,指示灯G亮;M1,M3,M5,M6得电时,传送电机正转;M1,M3,M5得电时,电机J运行;M3,M4得电时,指示灯H亮;M5,M6得电时,指示灯I亮;M2,M4得电时,传送电机反转。
过程控制级模拟轧钢系统的研制及在热轧试车中的运用

智能制造数码世界 P.266过程控制级模拟轧钢系统的研制及在热轧试车中的运用段俊涛 首钢长治钢铁有线公司轧钢厂摘要 :本文主要以过程控制级模拟轧钢系统的研制及在热轧试车中的运用为重点进行阐述,结合当下过程控制级模拟轧钢系统组成结构为依据,首先分析过程控制级模拟轧钢系统的研制,其次从过程控制级模拟轧钢系统模拟器的研制、综合模拟试验两个方面深入说明并探讨过程控制级模拟轧钢系统的研制在热轧试车中的巧妙运用,进一步强化过程控制级模拟轧钢系统在热轧试车中的运用效率,旨意在为相关研究提供参考资料。
关键词:过程控制级 模拟轧钢系统 研制 热轧试车 有效运用轧钢行业发展的特征具备一定的持续性和实时性,现阶段在轧钢行业的自动化控制研制呈现日新月异的发展趋势,以往大量的作业操作都可以借助体系的控制加以实现。
模拟轧钢针对现场的调试工作和热负荷生产试验产生积极影响,不仅能够在轧钢生产涉及的模拟轧钢作业中设置生产参数,便于生产工艺的顺利实施,包括每一个机架的轧制功以及轧制力,减小试轧的损失;还能够在任一种情况下检验现场设备的运行效果,保证轧钢条件足够充分。
如今过程控制级模拟轧钢系统的研制受到诸多人士的关注,怎样将过程控制级模拟轧钢系统运用在热轧试车中是新时期下轧钢行业发展的主题。
1.过程控制级模拟轧钢系统的研制所谓的模拟轧钢系统,也就是依据模拟信号替换外界的真实信号,促使应用性能依据现场生产涉及的工艺和生产逻辑加以实现,体现检测作业的准确性和统一性。
模拟轧钢系统并没有确切的概念,可以站在模拟轧钢存有的模拟功能以及工艺两个视角下加以分析。
其一,功能区分。
模拟轧钢系统呈现局部性能模拟、单层面性能模拟以及多层面性能模拟等形式,其中局部性能模拟是基于某个信号的模拟以及报文加以形成的模拟系统。
针对轧钢工厂的控制技术[1],抽钢模拟以及加热炉装钢模拟也是局部性能模拟的范畴;单层面性能模拟便是在较为全面的系统视角下,依据多种地区局部模拟理念,综合模拟模拟轧钢系统的一种方式,体现出现代化轧钢系统的完整性;多层面性能模拟便是把两个以及两个以上单层面性能模拟进行结合,之后组建成大规模的控制体系[2]。
PLC的轧钢机控制系统设计

封面作者:PanHongliang仅供个人学习江西理工大学本科毕业设计(论文)任务书电气工程与自动化学院电气专业级(届)班学号学生题目:基于PLC的轧钢机控制系统设计专题题目(若无专题则不填):PLC软件设计原始依据(包括设计(论文)的工作基础、研究条件、应用环境、工作目的等):工作基础:目前,我国基于PLC轧钢机系统已经不同程度得到了推广应用。
PLC轧钢机控制技术的发展主要经历了三个阶段:继电器控制阶段,微机控制阶段,现场总线控制阶段。
现阶段轧钢机控制系统设计使用可编程控制器(PLC),其功能特点是变化灵活,编程简单,故障少,噪音低,维修保养方便,节能省工,抗干扰能力强。
除此之外PLC还有其他强大功能,它可以进行逻辑控制、运动控制、通信等操作;并具有稳定性高、可移植性强等优点,因此受到广大电气工程控制技术人员的青睐。
研究条件及应用环境:本课题是基于PLC的控制系统的研究课题。
工业自动化是国家经济发展的基础,用于实现自动化控制设备主要集中为单片机和PLC。
单片机由于控制能力有限、编程复杂等缺点,现在正逐步退出控制舞台。
PLC则因为其功能强大、编程简单等优点,得到迅速发展及运用。
PLC的功能强大,可以进行逻辑控制、运动控制、通信等操作;并具有稳定性高、可移植性强等优点,因此,PLC是工业控制领域中不可或缺的一部分。
工作目的:轧钢机如控制和使用得当,不仅能提高效率,节约成本,还可大大延长使用寿命。
对轧钢机控制系统的性能和要求进行分析研究设计了一套低成本高性能的控制方案,可最大限度发挥轧钢机加工潜力,提高可靠性,降低运行成本,对提高机械设备的自动化程度,缩短与国际同类产品的差距,都有着重要的意义。
主要内容和要求:(包括设计(研究)内容、主要指标与技术参数,并根据课题性质对学生提出具体要求):1)当整个机器系统的电源打开时,电机M1和M2旋转,以待传送工件。
2)工件通过轨道从右边输送进入轧制系统。
3)感应器S1感应到有工件输送来时,输出高电位,驱动上轧辊按预定下压一定的距离,实现轧制厚度的调节,同时电机M3开始逆时针旋转,并带动复位挡板也逆时针转动,感应器S1复位。
梅钢过程控制级系统模拟轧钢功能的实现

图! 主控画面模拟轧钢控制块 G 3 6 ! % . 4 0 ; . 2 < 2 . H I. J . / 0 ; . 2 2 3 4 3 4F = 3 4 / H ; : : 4 5 5 5
轧 ! " # 模拟轧钢功能和 $!的通讯 由于 ! 为了保证模轧数 "层面没有模拟功能, 据能够上传 ! , " ! # 轧件管理器将内存模轧数据按 照成品卷实绩数据格式进行组织, 使用 $ % & ’ ( ) * ’ 的 / 通过 * % + , . / 0 1 2和$ ( 3 % 3 通讯协议, 4 5 6 4 7 和! 按照约定的通讯电 "的 8 ( +& 建立数据通路, 文, 在模 轧 结 束 后, 发送通讯电文给 ! 。! " "上线 前, 模轧功能在系统调试、 测试过程中发挥了很大的 作用。! #也可以选择屏蔽禁止模拟电文的发送。
轧
钢
・$ Q P・
梅钢过程控制级系统模拟轧钢功能的实现
董 刚 余亚林
南京 ! ) " # # $ %
(上海宝钢集团梅山钢铁公司设备部
摘 要
本文从计算机功能开发角度阐述了梅钢模拟轧钢功能的原理, 模拟轧钢方案的制订, & ! 过程控制级 模拟轧钢 过程控制级 应用系统 程序 事件驱动
系统模拟轧钢功能的程序实现, 以及模拟轧钢对于热轧生产的重要性。 关键词
钢
・" D @・
和动作的调度中心。为了实现模拟轧钢, 采用了以 下的设计思路。 ( )使用 ’ 及时响应操作, 打开 J * G 直控信号, 或关闭控制程序模轧功能块, 模轧抽钢后, 程序锁定 运行在模轧功能, 模轧标志下发 ! , 整个系统实施 J 模拟轧制, 直至结束。 ( )接收模板数据, 按照数据表格式拷贝到内 # 存数据区, 创建整套动态模轧数据。 )模轧功能块指挥模型进行品种规格模拟轧 ( " 件的计算、 设定和数据下装, 完成内存数据区记录数 据的更新、 保存。模型计算点和计算功能见表" 。
轧钢机的模拟控制

轧钢机的模拟控制
1.控制要求
当起动按扭按下,电动机M1、M2运行,按S1表示检测到物件,电动机M3正转,即
M3F 亮。
再按S2,电动机M3反转,即M3R 亮,同时电磁阀Y1动作。
再按S1 ,电动机M3正转,重复经过三次循环,再按S2停机一段时间(3s ),不需要按起动。
当按下停止按钮时,后方可运行。
必须注意不先按S1,而按S2会有动作。
2.I/O 分配输入 输出
起动按钮:I0.0 M1:Q0.0 M3F :停止按钮:I0.3 M2:Q0.1 M3R :S1按钮: I0.1 Y 1:Q0.4 S2按钮: I0.2
3.按图所示的梯形图输入程序。
4.调试并运行程序。
图7-1 轧钢机控制示意图
二、轧钢机控制语句表
三、轧钢机控制梯形图
图7-2 轧钢机控制梯形图。
自动轧钢机的plc控制

PLC的编程语言和编程工具
PLC的编程语言通常采用类似于计算机高级语言的指令集,如Ladder Logic、Function Block Diagram(FBD)、Structured Text(ST)、Instruction List(IL)等。
常用的PLC编程工具包括PLC厂商提供的专用软件包和第三方软件,如Rockwell的RSLogix 5000、Siemens的STEP 7等。这 些软件提供了图形化编程界面,使得用户可以方便地编写、调试和监控PLC程序。
PLC控制技术基础
PLC的定义与特点
PLC(可编程逻辑控制器)是一种专为工业环境设计的数字电子设备,用于执行顺 序控制、逻辑运算、算术运算等操作,并通过数字或模拟输入/输出模块控制各种类 型的机器和设备。
PLC具有高可靠性、高灵活性、易于编程和易于扩展等特点,因此在工业自动化 领域得到了广泛应用。
程序优化与改进
优化算法
根据实际运行情况和性能要求,优化控制算 法,提高控制精度和响应速度。
改进功能
根据生产需求和设备升级,逐步增加或改进 控制功能,提高自动轧钢机的生产效率和产 品质量。
05
系统测试与运行
系统测试方案与实施
测试目的
确保PLC控制系统在自动轧钢机中的稳定性 和可靠性,提高生产效率。
PLC的基本组成和工作原理
PLC主要由中央处理单元(CPU)、存储器、 输入/输出模块、电源和编程设备等部分组成。
PLC的工作原理可以概括为输入采样、程序 执行和输出刷新三个阶段。在输入采样阶段 ,PLC读取输入信号的状态并将其存储在输 入映像寄存器中;在程序执行阶段,PLC按 照用户程序的顺序执行指令,并更新内部存 储器的值;在输出刷新阶段,PLC将输出映 像寄存器的值输出到输出模块,驱动外部设
板带轧机系统自动控制
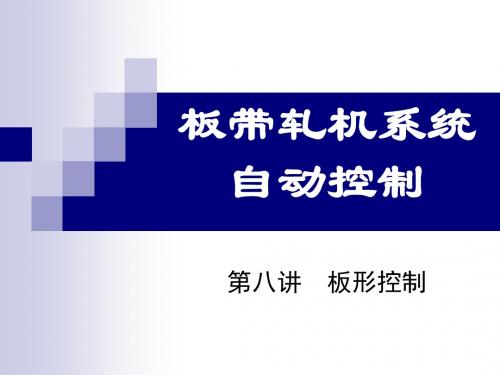
第八讲 板形控制
一、板形与横向厚差>>> 二、影响负载辊缝形状的因素 >>> 三、板形控制的工艺理论 >>>
第八讲 板形控制
板带轧机系统自动控制
2
一、板形与横向厚差
1. 横向厚差和板形概念
板带的几何尺寸精度三大质量指标: 纵向厚差、横向厚差(板凸度)和板形(平直度)
纵 向 厚 差 控制:理论简单,技术容易实现。 板形和板凸度控制:理论复杂,技术难以实现。
28
(5)轧辊磨损的机理模型; (6)轧件变形、辊系变形、轧辊轧件温度和轧辊磨损迭代求解 的稳定性; (7)平直度判别系数的准确确定; (8)平直度标准曲线的确定方法和完备简便实用的平直度标准 曲线数据库; (9)倾辊、弯辊、横移轧辊和分段冷却等控制手段的综合优化
使用策略。
(10)冷连轧机高速冷轧过程中乳化液的浓度、流量、温度及品 质对摩擦系数的影响。
件变形模型和板形判别模型,确定各道次的板形标准曲线模型参数。
3)根据摩擦磨损原理,提出数学模型的结构,结合工业生产实测数据,应 用自适应和自学习方法,确定轧辊磨损的具体数学模型。
4)在控制策略方面,通过数字仿真和工业生产测试两方面,详细分析各控
制手段对各板形模式的调节作用,寻求各控制手段的最佳配合使用策略。
第八讲 板形控制 板带轧机系统自动控制 27
重点解决的关键问题
1.关于板形离线设定控制的机理模型和数字仿真
(1)各种边界条件热交换系数的确定; (2)变形区变形抗力分布的准确计算; (3)变形区热力耦合迭代求解的稳定性; (4)轧辊之间及轧辊与轧件之间的弹性压扁变形的精确计算;
第八讲 板形控制
自动轧钢机的PLC控制系统设计

自动轧钢机的PLC控制系统设计自动轧钢机是一种用于将铁水或钢块进行加工、压制和轧制的关键设备。
它主要由温控系统、液压系统、轮辊线系统和PLC控制系统等组成。
PLC控制系统是整个轧钢机运行和控制的核心部分。
本文将详细介绍自动轧钢机的PLC控制系统设计。
一、系统框架设计自动轧钢机的PLC控制系统主要由中央控制器(CPU)、输入模块、输出模块、通信模块和用户界面组成。
其中,中央控制器用于处理和控制信号,输入模块用于接收传感器信号,输出模块用于控制执行器的操作,通信模块用于与外部设备进行数据交互,用户界面用于人机交互。
二、硬件设计1.中央控制器:选择可编程逻辑控制器(PLC)作为中央控制器,可根据实际需求选择合适的型号和规格。
PLC需要具备足够的输入和输出接口,以满足轧钢机的控制需求。
2.输入模块:根据实际需要选择合适的输入模块,用于接收传感器信号。
例如,温度传感器、压力传感器、位移传感器等。
输入模块需要具备稳定、可靠的信号传输性能。
3.输出模块:根据实际需要选择合适的输出模块,用于控制执行器的操作。
例如,液压阀、电磁阀、电动机等。
输出模块需要具备高效、可靠的控制性能。
4.通信模块:根据实际需求选择合适的通信模块,用于与外部设备进行数据交互。
例如,以太网通信模块、串口通信模块等。
通信模块需要具备稳定、可靠的数据传输性能。
5.用户界面:根据实际需要选择合适的用户界面,用于人机交互。
例如,触摸屏、按钮、指示灯等。
用户界面需要具备直观、易用的操作性能。
三、软件设计1.程序设计:根据轧钢机的工作流程和控制要求编写PLC程序。
程序包括输入信号的检测和处理、输出信号的生成和控制、故障检测和报警等功能模块。
2.控制算法设计:根据轧钢机的特点和要求设计合适的控制算法,包括温度控制、压力控制、轮辊线速度控制等。
控制算法需要满足精度要求,提高轧钢机的生产效率和产品质量。
3.系统调试和优化:在系统安装和调试过程中,根据实际情况对软件进行优化,提高系统的稳定性和可靠性。
PLC轧钢机的模拟控制梯形图

实验六轧钢机的模拟控制
一、实验目的
用PLC构成轧钢机控制系统
二、实验内容
1.控制要求
当起动按扭按下,电动机M1、M2运行,按S1表示检测到物件,电动机M3正转,即M3F亮。
再按S2,电动机M3反转,即M3R亮,同时电磁阀Y1动作。
再按S1 ,电动机M3正转,重复经过三次循环,再按S2时,则停机一段时间(3s),取出成品后,继续运行,不需要按起动。
当按下停止按钮时,必须按起动后方可运行。
必须注意不先按S1,而按S2将不会有动作。
2.I/O分配
输入输出
起动按钮:X0 M1:Y0 M3F:Y2
停止按钮:X3 M2:Y1 M3R:Y3
S1按钮:X1 Y1:Y4
S2按钮:X2
3.梯形图程序。
轧钢机控制示意图
4、轧钢机控制语句表
5.调试并运行程序。
轧钢机控制系统模拟课程设计

轧钢机控制系统模拟课程设计一、设计背景与意义轧钢机是现代钢铁工业中不可或缺的关键设备,其控制系统对于保证轧钢过程的稳定、提高产品质量和降低能耗具有重要意义。
通过模拟轧钢机控制系统的设计和实现,可以帮助学生深入理解控制系统的基本原理,掌握相关的软硬件技术,为今后从事相关领域的工作打下坚实的基础。
二、设计目标1.掌握轧钢机的基本原理和工艺流程;2.设计并实现一个模拟的轧钢机控制系统,具备基本的控制功能;3.测试并分析模拟控制系统的性能和效果。
三、设计方案1.系统硬件选型与搭建:选择合适的微控制器、传感器、执行器等硬件设备,搭建模拟轧钢机的硬件平台;2.控制算法设计与实现:根据轧钢工艺要求,设计合适的控制算法,如PID控制、模糊控制等,并进行编程实现;3.人机界面设计:设计一个友好的人机界面,用于实时监控轧钢过程的状态、参数和操作控制;4.系统集成与调试:将硬件、软件和控制算法集成在一起,进行系统调试和优化。
四、具体任务与分工1.系统硬件选型与搭建:由硬件小组负责,选择合适的硬件设备,搭建模拟轧钢机的硬件平台;2.控制算法设计与实现:由软件小组负责,根据工艺要求设计控制算法,并进行编程实现;3.人机界面设计:由界面小组负责,设计友好的人机界面,实现实时监控和操作控制;4.系统集成与调试:由综合小组负责,将硬件、软件和控制算法集成在一起,进行系统调试和优化。
五、时间计划与进度安排1.第1周:系统调研与方案制定;2.第2-3周:硬件选型与搭建;3.第4-5周:控制算法设计与编程实现;4.第6-7周:人机界面设计与编程实现;5.第8-9周:系统集成与调试;6.第10周:项目总结与验收。
plc课程设计 轧钢机控制系统模拟

plc课程设计-- 轧钢机控制系统模拟题目:轧钢机控制系统模拟课程名称:工厂电气控制及PLC课程设计院部名称:机电工程专业:电气工程及其自动化班级:学生姓名:学号:课程设计学时:指导教师:金陵科技学院教务处制目录摘要.................................................................................. 第一章绪论................................... 错误!未定义书签。
1.1相关背景知识 ............................. 错误!未定义书签。
1.2课程设计的目的......................... 错误!未定义书签。
1.3课程设计的要求......................... 错误!未定义书签。
1.4课程设计的任务......................... 错误!未定义书签。
第二章轧钢机控制系统PLC硬件设计 . 错误!未定义书签。
2.1PLC输入/输出信号及地址分配 ..... 错误!未定义书签。
2.2电气连接图.................................. 错误!未定义书签。
2.3安全保护 (6)第三章轧钢机控制系统PLC软件设计错误!未定义书签。
3.1梯形图设计.................................. 错误!未定义书签。
3.2基本PLC语句对应指令 .......... 错误!未定义书签。
3.3系统调试........................................................................................ 错误!未定义书签。
第四章课程设计总结 ................... 错误!未定义书签。
第五章课程设计图象 ................... 错误!未定义书签。
探究轧钢电气自动化控制系统改造技术及其应用

探究轧钢电气自动化控制系统改造技术及其应用随着工业化进程的不断发展,轧钢企业在生产过程中面临着诸多挑战,如提高生产效率、降低生产成本、确保产品质量等。
传统的轧钢生产方式已经难以满足企业发展的需求,因此轧钢电气自动化控制系统的改造成为了不可或缺的一环。
本文将从轧钢电气自动化控制系统的改造技术以及其应用方面来进行探究。
1. 全数字化控制技术全数字化控制技术是将传统的模拟控制系统升级为数字化控制系统,通过数字化处理技术和网络通信技术来实现对轧钢过程的精准控制。
全数字化控制系统具有控制精度高、系统稳定性好、故障诊断能力强等优点,可以有效提高轧钢生产的效率和产品质量。
2. PLC控制技术PLC(Programmable Logic Controller)是一种用于工业控制的可编程逻辑控制器,通过对数控系统的整体规划和设计,可以实现对轧钢生产过程的自动控制和监测。
PLC控制技术具有可编程性强、稳定性好、可靠性高的特点,可以有效地提高轧钢生产的自动化水平。
3. 远程监控技术远程监控技术是将轧钢生产过程中的各个环节通过网络连接起来,并通过远程监控平台实现对轧钢生产过程的实时监测和控制。
远程监控技术可以实现对生产过程的全方位监控,及时发现和处理问题,提高生产效率和产品质量。
4. 自动化检测技术自动化检测技术是通过各种检测设备和传感器实时监测轧钢生产过程中的各项参数,如温度、压力、速度等,并将数据反馈到控制系统中,实现对轧钢过程的自动化控制。
自动化检测技术可以提高生产过程的可靠性和稳定性,确保产品质量。
二、轧钢电气自动化控制系统的应用1. 提高生产效率2. 降低生产成本通过对轧钢电气自动化控制系统的改造,可以降低生产成本。
利用PLC控制技术可以优化轧钢机的控制逻辑,降低能耗和损耗;利用自动化检测技术可以提高生产过程的可靠性和稳定性,减少废品率和维护成本。
3. 确保产品质量。
基于MCGS的轧钢机模拟控制系统设计说明书

摘要本设计阐述了基于MCGS和PLC的远程轧钢机监控系统的硬件和软件设计.此系统采用主从式结构,上位机采用MCGS组态软件实现监控功能,对轧钢机信息进行实时监控;下位机则以西门子S7-200PLC为核心,进行轧钢机信息的采集和转换,并与上位机进行信息交互,上位机和下位机通过串口方式进行通信,最后实现以MCGS为监控界面并且以PLC为编程控制的轧钢机控制系统。
关键词:轧钢机;远程监控;西门子S7—200PLC;MCGSABSTRACTThis design have introduced the hardware and software design of the long—range Rolling mill monitoring system which are based on MCGS and PLC。
This system adopts the principal and subordinate structure, the superior machine adopts the MCGS configuration software to realize the monitoring function and carry on the real—time monitoring to the ingredient information。
The Lower position machine regards Siemens S7-200PLC as the core to carry on the gathering and the transformation of ingredient information and they also exchange the information with the superior machine。
The superior machine and the lower position machine carry on the correspondence through the serial mode。
轧钢生产仿真实训系统使用说明

轧钢生产仿真实训系统使用说明(粗轧)软件说明书V2.1版目录第1章前言 (5)1.1 系统开发背景与目的 (5)1.1.1研发背景 (5)1.1.2 研发目的 (6)1.1.3 重要意义 (7)1.2系统功能及特性简介 (8)1.2.1 结合轧钢工艺模型 (9)第2章系统的安装及启动 (10)2.1 系统的运行环境 (10)第3章系统操作说明 (11)3.1虚拟界面操作与设备介绍 (11)3.1.1虚拟设备操作按键介绍 (16)3.2操纵界面操作介绍 (16)3.2.1选择批次 (16)3.2.2粗轧监控主界面 (18)3.2.2.1画面切换 (19)3.2.2.2原料与成品规格显示 (20)3.2.2.3退出 (20)3.2.2.4 辊缝值显示 (21)3.2.2.5 传动侧辊缝值显示 (21)3.2.2.6 操作侧辊缝值显示 (21)3.2.2.7 实际辊缝值显示 (22)3.2.2.8 设定辊缝值显示 (22)3.2.2.9 主轧辊转动速度显示 (22)3.2.2.10 选择批次 (23)3.2.2.11 压下正常状态显示 (24)3.2.2.12辊缝的变化方式 (24)3.2.2.13当前规程号显示 (25)3.2.2.14 钢块当前实际长宽厚显示 (25)3.2.2.15 轧制力显示 (26)3.2.2.16 温度显示 (26)3.2.2.17 微调设定辊缝 (26)3.2.2.17.1 道次修正 (26)3.2.2.18设定修正道次号 (28)3.2.2.19设定修正设定辊缝的改变量 (29)3.2.2.20按钮改变要修正的道次号 (29)3.2.2.21 规程信息 (30)3.2.2.22轧制批次情况显示 (31)3.2.2.23除磷箱操作 (31)3.2.2.23.1喷嘴组号选择 (32)3.2.2.23.2 除磷箱打开关闭 (32)3.2.2.23.3 除磷箱水压设定 (32)3.2.2.23.4 除磷箱状态显示 (32)3.2.2.24 系统检查 (33)3.2.3 规程输入界面 (33)3.2.3.1 画面切换 (34)3.2.3.2原料与成品规格显示 (34)3.2.3.3 退出按钮 (34)3.2.3.4 辊缝值显示 (34)3.2.3.5压下正常状态显示 (34)3.2.3.6辊缝的变化方式状态显示 (35)3.2.3.7规程选择 (35)3.2.3.8微调设定辊缝 (36)3.2.3.9直接弹出对话框输入数据修改设定辊缝 (36)3.2.3.10弹出对话框输入数据修改规程总道次 (38)3.2.3.11 下载到 (40)3.2.3.12 切换到 (40)3.2.4 状态显示界面 (40)3.2.4.1 画面切换 (40)3.2.4.2原料与成品规格显示 (41)3.2.4.3 退出按钮 (41)3.2.4.4 辊缝值显示 (41)3.2.4.5压下正常状态显示 (41)3.2.4.6辊缝的变化方式状态显示 (41)3.2.4.7当前规程号显示 (41)3.2.4.8轧辊转速 (42)3.2.4.9 转滚速度 (43)3.2.4.10 轧制力 (43)3.2.4.11 钢块规格 (43)3.2.4.12 钢块温度 (44)3.2.4.13 当前道次号 (45)3.2.4.14 批次信息 (45)3.2.4.15 钢坯角度 (45)3.2.5 曲线回放 (46)3.2.5.1 输入查看条件 (46)3.2.5.2 实时曲线暂停按钮 (46)3.2.5.3 实时曲线实时显示按钮 (46)3.2.5.4回放曲线前移按钮 (47)3.2.5.5回放曲线后移按钮 (47)第4章键盘模拟手柄使用方法 (48)附录:49第1章前言1.1 系统开发背景与目的1.1.1研发背景虚拟现实是综合利用计算机图形学、光电成像技术、传感技术、计算机仿真、人工智能等多种技术,创建一个逼确实、具有视、听、触、嗅、味等多种感知的计算机系统。
轧钢生产仿真实训系统使用说明

轧钢生产仿真实训系统使用说明1. 系统概述轧钢生产仿真实训系统是一款针对轧钢生产流程进行仿真的教学辅助系统。
该系统通过模拟真实轧钢厂的生产环境和流程,为学生提供了一个实际操作的训练平台。
2. 功能特点2.1 模拟真实环境轧钢生产仿真实训系统模拟了真实的钢铁生产厂的环境,包括从原料进料到成品出炉的整个生产流程,让学生能够身临其境地感受到真实的生产场景。
2.2 操作简便该系统设计了简洁直观的操作界面,以便学生能够迅速上手。
用户只需通过鼠标点击和拖拽操作,即可完成各种操作,如调整轧机参数、控制设备运转等。
2.3 实时数据展示系统实时显示轧机的生产数据,包括温度、压力、速度等参数,帮助学生了解生产过程中的关键数据指标,并学会分析和判断生产状况。
2.4 故障模拟为了让学生能够更好地应对生产中的故障情况,系统内置了各种故障模拟场景,学生需要根据故障提示信息进行快速判断和处理,提高应变能力。
3. 系统使用3.1 登录与注册用户需要在系统登录界面输入正确的用户名和密码进行登录。
如果是首次使用,需要先进行注册,并提供必要的个人信息。
3.2 选择实训场景登录成功后,系统会显示可供选择的实训场景,学生可以根据教学实验要求进行选择。
每个实训场景都有特定的目标和任务,学生需要按照要求完成任务。
3.3 操作轧钢设备学生通过操作界面中的按钮和滑动条,可以调整轧钢设备的参数,如温度、压力、速度等。
根据实训场景的要求,学生需要合理调整参数,以达到预期的生产效果。
3.4 监控参数实时变化系统会实时显示轧机的各项参数的变化情况,包括温度、压力、速度等。
学生需要密切关注这些参数的变化,判断生产是否正常,并根据需要进行调整。
3.5 处理故障情况在实际生产中,经常会发生各种故障情况。
系统会随机模拟一些故障场景,例如温度过高、设备故障等。
学生需要根据故障提示信息,快速判断故障原因,并采取相应的措施进行处理。
3.6 查看实训报告学生完成实训后,系统会生成实训报告,包括学生的操作记录、生产数据、故障处理过程等。
基于MCGS的轧钢机模拟控制系统设计说明书毕业论文

摘要本设计阐述了基于MCGS和PLC的远程轧钢机监控系统的硬件和软件设计。
此系统采用主从式结构,上位机采用MCGS组态软件实现监控功能,对轧钢机信息进行实时监控;下位机则以西门子S7-200PLC为核心,进行轧钢机信息的采集和转换,并与上位机进行信息交互,上位机和下位机通过串口方式进行通信,最后实现以MCGS为监控界面并且以PLC为编程控制的轧钢机控制系统。
关键词:轧钢机;远程监控;西门子S7-200PLC;MCGSABSTRACTThis design have introduced the hardware and software design of the long-range Rolling mill monitoring system which are based on MCGS and PLC. This system adopts the principal and subordinate structure, the superior machine adopts the MCGS configuration software to realize the monitoring function and carry on the real-time monitoring to the ingredient information. The Lower position machine regards Siemens S7-200PLC as the core to carry on the gathering and the transformation of ingredient information and they also exchange the information with the superior machine.The superior machine and the lower position machine carry on the correspondence through the serial mode. Finally, they realize the Rolling mill control system with MCGS for monitoring interface and PLC for programming.Key words:Rolling mill;Long-distance monitoring;Siemens S7-200PLC;MCGS毕业设计(论文)原创性声明和使用授权说明原创性声明本人郑重承诺:所呈交的毕业设计(论文),是我个人在指导教师的指导下进行的研究工作及取得的成果。
- 1、下载文档前请自行甄别文档内容的完整性,平台不提供额外的编辑、内容补充、找答案等附加服务。
- 2、"仅部分预览"的文档,不可在线预览部分如存在完整性等问题,可反馈申请退款(可完整预览的文档不适用该条件!)。
- 3、如文档侵犯您的权益,请联系客服反馈,我们会尽快为您处理(人工客服工作时间:9:00-18:30)。
目录1.绪论 (2)2.课题介绍 (7)3.课程设计内容及要求 (9)3.1 控制要求 (9)3.2 设计要求 (11)3.3 控制原理 (11)3.4 控制方案 (11)4.硬件设计 (12)4.1硬件设计要求轧钢机系统结构 (12)4.2元器件选择 (13)4.3元器件清单 (14)4.4硬件控制原理图 (14)5.软件设计 (16)5.1 I/O 地址表 (17)5.2 程序设计及说明 (18)6.运行调试 (20)7.小结 (22)附录 (23)参考文献 (23)1.主电路 (24)2.控制电路 (25)3.总梯形 (26)1.绪论可编程序控制器,英文称Programmable Logical Controller,简称PLC。
它是一个以微处理器为核心的数字运算操作的电子系统装置,专为在工业现场应用而设计,它采用可编程序的存储器,用以在其内部存储执行逻辑运算、顺序控制、定时/计数和算术运算等操作指令,并通过数字式或模拟式的输入、输出接口,控制各种类型的机械或生产过程。
PLC是微机技术与传统的继电接触控制技术相结合的产物,它克服了继电接触控制系统中的机械触点的复杂接线、可靠性低、功耗高、通用性和灵活性差的缺点,充分利用了微处理器的优点,又照顾到现场电气操作维修人员的技能与习惯,特别是PLC的程序编制,不需要专门的计算机编程语言知识,而是采用了一套以继电器梯形图为基础的简单指令形式,使用户程序编制形象、直观、方便易学;调试与查错也都很方便。
用户在购到所需的PLC后,只需按说明书的提示,做少量的接线和简易的用户程序的编制工作,就可灵活方便地将PLC应用于生产实践。
随着科学技术的不断发展,人们的日常生活和生产活动大量的使用自动化控制,不仅节约了人力资源,而且很大程度的提高了生产效率,又进一步的促进了生产力快速发展,并不断的丰富着人们的生活。
早期的自动控制系统是依靠继电-接触器来实现的,其特点是:结构简单、价格低廉、抗干扰能力强,可以实现集中控制和远距离控制,但是其采用固定接线,通用性和灵活性差;又采用触点的开关动作,工作频率低,触点易损坏,可靠性差。
可编程控制器综合了计算机技术、半导体集成技术、自动控制技术、数字技术和通信网络技术发展起来的一种通用工业自动控制装置。
它面向控制过程、面向用户、适应工业环境、操作方便、可靠性高,成为现代工业控制的三大支柱之一。
PLC控制技术代表着当前程序控制的先进水平,PLC装置已成为自动化系统的基本装置。
可编程逻辑控制器PLC具备逻辑控制、定时、计数等功能,编程语言采用直观的梯形图语言,软件更改方便,通用性和灵活性好。
目前,可编程控制器PLC主要是朝着小型化、廉价化、标准化、高速化、智能化、大容量化、网络化的方向发展,与计算机技术相结合,形成工业控制机系统、分布式控制系统,现场总线控制系统,这将使PLC 的功能更强,可靠性更高,使用更方便,适用范围更广。
本设计是基于PLC 的轧钢机控制系统,利用传感器S1来检测传送带上有无钢板,若S1有信号(即开关为ON ),表示有钢板,电机M3正转,信号指示灯MZ 亮。
S1的信号消失(即为OFF ),检测传送带上钢板到位的传感器S2有信号(为ON ),表示钢板到位,电磁阀动作,指示信号灯YU1亮,电机M3反转,指示信号灯MF 亮。
此时,Y 给一向下压下量,S2信号消失,S1有信号,电机M3正转……如此重复上述过程。
A .可编程控制器的基本结构可编程控制器主要由CPU 模块、输入模块、输出模块和编程器组成(如下图所示)。
1、CPU 模块CPU 模块又叫中央处理单元或控制器,它主要由微处理器(CPU )和存储器组成。
它用以运行用户程序、监控输入/输出接口状态、作出逻辑判断和进行数据处理,即读取输入变量、完成用户指令规定的各种操作,将结果送到输出端,并响应外部设备(如编程器、电脑、打印机等)的请求以及进行各种内部判断等。
PLC 的内部存储器有两类,一类是系统程序存储器,主要存放系统管理和监控程序及对用户程序作编译处理的程序,系统程序已由厂家固定,用户不能更改;另一类是用户程序及数据存储器,主要存放用户编制的应用程序及各种暂存数据和中间结果。
2、I/O 模块接触器电磁阀指示灯电源 电源 限位开关选择开关按钮I/O模块是系统的眼、耳、手、脚,是联系外部现场和CPU模块的桥梁。
输入模块用来接收和采集输入信号。
输入信号有两类:一类是从按钮、选择开关、数字拨码开关、限位开关、接近开关、光电开关、压力继电器等来的开关量输入信号;另一类是由电位器、热电偶、测速发电机、各种变送器提供的连续变化的模拟输入信号。
可编程序控制器通过输出模块控制接触器、电磁阀、电磁铁、调节阀、调速装置等执行器,可编程序控制器控制的另一类外部负载是指示灯、数字显示装置和报警装置等。
3、电源可编程序控制器一般使用220V交流电源。
可编程序控制器内部的直流稳压电源为各模块内的元件提供直流电压。
4、编程器编程器是PLC的外部编程设备,用户可通过编程器输入、检查、修改、调试程序或监示PLC的工作情况。
也可以通过专用的编程电缆线将PLC与电脑联接起来,并利用编程软件进行电脑编程和监控。
5、输入/输出扩展单元I/O扩展接口用于将扩充外部输入/输出端子数的扩展单元与基本单元(即主机)连接在一起。
6、外部设备接口此接口可将编程器、打印机、条码扫描仪,变频器等外部设备与主机相联,以完成相应的操作。
B.可编程控制器的工作原理可编程控制器有两种基本的工作状态,即运行(RUN)状态与停止(STOP)状态。
在运行状态,可编程序控制器通过执行反映控制要求的用户程序来实现控制功能。
为了使可编程序控制器的输出及时地响应随时可能变化的输入信号,用户程序不是只执行一次,而是反复不断地重复执行,直至可编程序控制器停机或切换到STOP工作状态。
除了执行用户程序之外,在每次循环过程中,可编程序控制器还要完成内部处理、通信处理等工作,一次循环可分为5个阶段。
在内部处理阶段,可编程序控制器检查CPU,模块内部的硬件是否正常,将监控定时器复位,以及完成一些别的内部工作。
在通信服务阶段,可编程序控制器与别的带微处理器的智能装置通信,响应编程器键入的命令,更新编程器的显示内容。
在输入处理阶段,可编程序控制器把所有外部输入电路的接通/断开(ON/OFF)状态读入输入映像寄存器。
在程序执行阶段,即使外部输入信号的状态发生了变化,输入映像寄存器的状态也不会随之而变,输入信号变化了的状态只能在下一个扫描周期的输入处理阶段被读入。
在输出处理阶段,CPU将输出映像寄存器的通/断状态传送到输出锁存器。
C.可编程控制器的编程语言概述现代的可编程控制器一般备有多种编程语言,供用户使用。
IEC1131-3—可编程序控制器编程语言的国际标准详细的说明了下述可编程控制器编程语言:1)顺序功能图2)梯形图3)功能块图4)指令表5)结构文本其中梯形图是使用得最多的可编程控制器图形编程语言。
梯形图与继电器控制系统的电路图很相似,具有直观易懂的优点,很容易被工厂熟悉继电器控制的电气人员掌握,特别适用于开关量逻辑控制,主要特点如下:1)可编程控制器梯形图中的某些编程元件沿用了继电器这一名称,如输入继电器、输出继电器、内部辅助继电器等,但是它们不是真实的物理继电器(即硬件继电器),而是在软件中使用的编程元件。
每一编程元件与可编程序控制器存储器中元件映像寄存器的一个存储单元相对应。
2)梯形图两侧的垂直公共线称为公共母线(BUS bar)。
在分析梯形图的逻辑关系时,为了借用继电器电路的分析方法,可以想象左右两侧母线之间有一个左正右负的直流电源电压,当图中的触点接通时,有一个假想的“概念电流”或“能流(Power flow)从左到右流动,这一方向与执行用户程序时的逻辑运算的顺序是一致的。
3)根据梯形图中各触点的状态和逻辑关系,求出与图中各线圈对应的编程元件的状态,称为梯形图的逻辑解算。
逻辑解算是按梯形图中从上到下、从左到右的顺序进行的。
4)梯形图中的线圈和其他输出指令应放在最右边。
5)梯形图中各编程元件的常开触点和常闭触点均可以无限多次地使用。
D.可编程控制器的编程步骤(1)确定被控系统必须完成的动作及完成这些动作的顺序。
(2)分配输入输出设备,即确定哪些外围设备是送信号到PLC,哪些是外围设备是接收来自PLC信号的。
并将PLC的输入、输出口与之对应进行分配。
(3)设计PLC程序画出梯形图。
梯形图体现了按照正确的顺序所要求的全部功能及其相互关系。
(4)实现用计算机对PLC的梯形图直接编程。
(5)对程序进行调试(模拟和现场)。
(6)保存已完成的程序。
显然,在建立一个PLC控制系统时,必须首先把系统的需要的输入、输出数量确定下来,然后按需要确定各种控制动作的顺序和各个控制装置彼此之间的相互关系。
确定控制上的相互关系之后,就可进行编程的第二步──分配输入输出设备,在分配了PLC的输入输出点、内部辅助继电器、定时器、计数器之后,就可以设计PLC程序画出梯形图。
在画梯形图时要注意每个从左边母线开始的逻辑行必须终止于一个继电器线圈或定时器、计数器,与实际的电路图不一样。
梯形图画好后,使用编程软件直接把梯形图输入计算机并下载到PLC进行模拟调试,修改→下载直至符合控制要求。
这便是程序设计的整个过程。
2.课题介绍钢铁的用途十分广阔,在国民经济中起着极为重要的作用。
可以说,钢铁生产水平是衡量一个国家工业、农业、国防和科学技术水平的重要标志。
由于科技的进步和人们生活水平的提高,生产设备和产品的更新,人们对钢材的产量和质量提出了更高的要求,为了提高生产率,降低原材料和能源的消耗及产品的成本。
需要进一步完善轧钢设备制造水平,在这种形势下设计新型的轧钢机对其原有的钢铁生产线进行技术更新是非常必要的。
随着计算机控制技术的不断完善和发展,在冶金生产中,通过采用新的控制思想和新的行算机控制手段,以提高产品质量带来更大的经济效益,这是冶金生产的技术进步的必的计算机控制手段,以提高产品质量带来更大的经济效益,这是冶金生产的技术进步的必由之路。
轧钢技术发展前景世界轧钢工业的技术进步主要集中在生产工艺流程的缩短和简化上, 最终形成轧材性能高品质化、品种规格多样化、控制管理计算机化等。
展望未来, 轧钢工艺和技术的发展主要体现在以下几方面:1.铸轧一体化利用轧辊进行钢材生产, 因其过程连续、高效、可控且便于计算机等高新技术的应用, 在今后相当一段时间内, 以辊轧为特征的连续轧钢技术仍将是钢铁工业钢材成型的主流技术, 但轧钢前后工序的衔接技术必将有长足的进步。
在 2O 世纪, 由于连铸的发展, 已经逐步淘汰初轧工序。
而连铸技术生产的薄带钢直接进行冷轧, 又使连铸与热轧工序合二为一。