精炼车间工艺流程 PPT
LF精炼炉基本工艺PPT课件

5.7 LF炉埋弧精炼技术 5.8 LF钢包炉供配电制度 5.9 LF钢包炉的脱硫工艺 • 1) 渣指数与硫分配比的关系 • 2) LF炉合成渣脱硫技术 • 3) LF炉合成渣脱硫技术
15
• 5.10 LF钢包炉防止增氮技术
• 5.11 LF钢包炉的吹氩工艺
• 5.12 低夹杂物在LF钢包炉的精炼技术
达到3~5℃/min,可以大大降低初炼炉的出钢温度,同时考虑
到LF炉进行的是电极物理升温,避免了如RH-OB升温所产生大量
Al2O3夹杂对钢内在质量的影响。
• C与渣中氧化物主要发生如下反应:
• C+FeO→Fe+CO
• C+MnO→Mn+CO
• 其结果不仅使渣中不稳定的氧化物减少,提高了炉渣的还原性, 而且还可提高合金元素的收得率,合金元素的收得率都较电炉单 独冶炼有了较大程度的提高。碳与氧化物作用的另一结果是生成 CO气体,CO的生成使LF炉内气氛具有还原性,钢液在还原性气 氛下精炼,可进一步提高质量。
• 根据钢种、脱氧方法及初炼炉类型的不同, 可采用不同的LF炉操作工艺,几种典型的LF炉 操作程序如(图2-1-3 )所示。LF基本工艺为: 将转炉或电炉氧化末期的钢水,经过扒渣,去 除50~90%的氧化性渣,并在LF炉加入合成 渣料及脱氧剂,在还原性气氛下,通过电极埋 弧造渣,完成钢液的脱硫、脱氧、合金化、温 度及夹杂物的控制。
7
• ④ 白渣精炼
•
LF炉是利用白渣进行精炼的,它不
同于主要靠真空脱气的其它精炼方法。
白渣在LF炉内具有很强的还原性,这是
LF炉内良好的还原气氛和氩气搅拌互相
作用的结果。通过白渣的精炼作用可以
降低钢中氧、硫及夹杂物的含量。
最新冶炼流程课件讲座大学生ppt课件

创新:顶吹浸没喷枪镍精矿熔池熔炼工艺开发
富氧顶吹熔池熔炼工艺特点: a 原料适应性强;b 生产能力大; c 节约能源; d 环保效果好。
系统投资:24亿元人民币。 系统规模: 投料量147.8t/h;
年处理精矿100万t;产镍量6万t。 镍精矿富氧顶吹熔池熔炼难点: 1.镍精矿顶吹浸没熔炼,世界上首次工业
镍精炼工艺的发展
1、粗镍阶段 20世纪初,粗镍阳极电解精炼就在工业上应用,该工
艺具有阳极杂质含量低(杂质约为6-8%,含硫约2%,主 金属大于75%),电耗低、阳极液净化流程简单等优点, 但由于粗镍阳极的制备需要进行高镍锍的焙烧与还原熔 炼过程,整个过程复杂,建设投资大,目前,加拿大某 精炼厂、前苏联某精炼厂采用它。
用途:纯钴用于制造X射线管阴极和一些特殊制
品,钴几乎都用于制造合金,热强合金,硬质
合金、焊接合金,以及各种含钴合金钢。
产品名称:硒粉
单位价格:¥ 435000 /吨
贵
报价日期:2009-9-30
包装:铁桶包装 25公斤/桶
金
用途:适用于电子、玻璃、化工、医药
属
产品名称:海绵铂
单位价格:¥ 302000 /公斤
• 2.4 铜精矿成分及中间产品成分 • 铜合成炉熔炼系统主要品种及成分和中间产品成分见表:
原料名称
铜精矿1 铜精矿2 铜精矿3 配料后平均成分
冰铜 转炉粗铜 铜阳极板
Ni
0.05 0.08 0.07 0.07 0.08 0.13 0.11
Cu
25.3 19.5 33.8 25.6 57.4
99 99.4
产资源综合利用战略,选矿产出的镍精矿量进一步增加, 包括采购的国内外镍精矿,各种镍精矿原料将达到年 160万吨以上。另外公司贫矿资源开发选矿产出的镍精 矿含镍平均品位低,MgO达到14%,还需要主动吸纳其 它氧化镁等杂质元素含量较高的镍精矿原料组织生产处 理,因此适应原料品质的变化也成为很重要的任务。
炼钢工艺流程介绍(PPT47页)

炼钢转炉--氧枪设备
❖ 氧枪系统主要设备 ❖ 氧枪横移装置。 ❖ 氧枪升降装置 ❖ 氧枪滑道装置 ❖ 氧枪本体 ❖ 氧枪(氧、氮、水)
阀门站
炼钢转炉-(-次)除尘设备
❖ 蒸发冷却塔系统装置 ❖ 静电除尘器系统装置 ❖ 切换站系统装置 ❖ 轴流风机系统装置 ❖ 煤气冷却器系统装置 输灰系统 ❖ 输灰系统装置 ❖ 放散点火装置 ❖ CO气体检测报警
❖电弧炉炼钢法 ❖平炉炼钢法
Байду номын сангаас
炼钢流程图
钢产线流程图
炼钢工艺与设备
根据炼钢工艺流程, 可以把炼钢作业分为4部分:
1、冶炼前的铁水预处理工序 2、铁水冶炼 3、钢水精炼 4、钢水浇铸
炼钢 预处理
在铁水进入炼钢炉冶 炼前,除去其中的某 些有害成分或提取其 中某些有益成分的工 艺过程。 可分为普通铁水预处 理和特殊铁水预处理。前者有铁水预脱硫,铁水 预脱硅,铁水预脱磷;后者有铁水提钒,铁水提 铌,铁水脱铬等。
炼钢 预处理
重要的工艺节点: 兑铁(如果不是专用的预处理罐则没有) 前扒渣 预处理(脱硫、脱磷等) 后扒渣 出铁
炼钢 预处理
炼钢 混铁炉
高炉和转炉之间的 炼钢辅助设备。 主要用于调节和均 衡高炉和转炉之间 铁水供求的设备, 保证不间断地供给 转炉需要的铁水, 铁水在混铁炉中储 存和混匀铁水成份 及均匀温度,对转 炉炼钢非常有利。
炼钢工艺与设备
炼钢工程概述
❖ 本项目为山东焦化北海新区节能新工艺示范工程配套建设 项目,
❖ 拟建炼钢车间生产规模为年产合格钢水500万吨。项目分 两期完成,
❖ 一期配置1座600t混铁炉(预留)、2套复合喷吹脱硫装 置、2座120t顶底复吹转炉、2套150tLF、2套R9m8 机8流方坯连铸机,年产合格钢水250万吨。
精炼工艺流程图

精炼车间工艺流程图400T/D酶法脱胶工段:柠檬酸↓毛油→过滤(过滤器)→换热☆(换热器,70-95℃)→酸混合→酸反应(酸反应罐)液碱水,PLC酶↓↓→碱混合→碱反应(碱反应罐)→换热☆(换热器,50-55℃)→酶混合器→酶反应→换热☆(换热器,75-90℃)→离心分离(离心机)→换热☆(换热器,85—95℃)→水混合→↓油脚→水洗延时罐↓洗涤水↑→离心分离(离心机)→换热☆(换热器,105-125℃)→干燥☆(干燥罐,真空≤200mbar)→干燥油→冷却☆(换热器,65℃以下)→过滤→三级油1200T/D水化脱胶工段:热软水油脚→储存(暂存罐)→蒸发☆(蒸发器,100-135℃)→冷却☆(冷却器,30-65℃)↓↑↓毛油→过滤(过滤器)→换热☆(换热器,70-95℃)→水化(水化反应罐)→离心分离(离心机)磷脂→换热☆(换热器,90-125℃)→干燥☆(干燥罐,真空≤300mbar)→脱胶油900T/D深度脱胶工段:柠檬酸↓毛油→过滤(过滤器)→换热☆(换热器,70-95℃)→酸混合→酸反应(酸反应罐)→换热☆(换热器,40-45℃)液碱↓→碱混合→碱反应(碱反应罐)→换热☆(换热器,70-95℃)→离心分离(离心机)→↓油脚换热☆(换热器,105-125℃)→干燥☆(干燥罐,真空≤200mbar)→干燥油→冷却☆(换热器,75℃以下)↓过滤→四级油1000T/D精炼工艺流程图:磷酸液碱↓↓毛油→过滤(过滤器)→换热☆(换热器70-95℃)→酸混合→酸反应→碱混合→碱反应→离心分离(离心机)→水洗混合→离心分离(离心机)→干燥(干燥罐)→干燥油→换热☆(换热器,88-125℃)↓↓皂脚洗涤水白土↓→预混(预混罐)→脱色☆(脱色塔,真空≤400mbar)→混合油→过滤(过滤器)↓废白土→脱色油→换热(换热器)→脱臭☆(脱臭塔,真空≤5mbar,温度230-250℃)→脱臭油→换热☆(换热器,75℃以下)↓脂肪酸,维E→过滤→一级油→油罐→灌装封盖→装箱→入库注:☆为关键控制点。
炼钢-精炼-连铸工艺简介(PPT 40页)
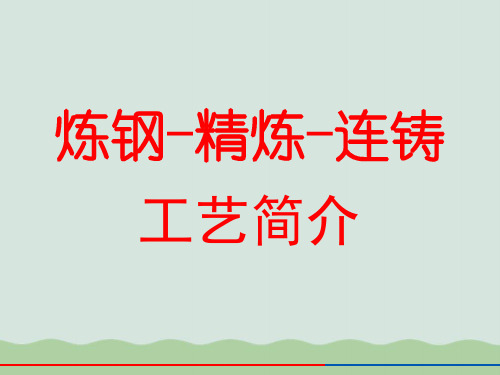
LF的基本功能
1、脱硫:利用造碱性还原渣和电弧的高温区进行脱硫 2、加热:采用电极放电加热钢水 3、合金化:成份微调 4、均匀钢液和去除夹杂:采用底吹Ar气搅拌钢液 5、生产组织中的缓冲:平衡转炉和铸机之间的供钢节奏。
喂线工艺
在RH-KTB工位和LF工位都设有 喂线装置,线的种类为Ca-Si 线和Ca-Al线。
•
1、有事业的峰峦上,有汗水的溪流飞 淌;在 智慧的 珍珠里 ,有勤 奋的心 血闪光 。
•
2、人们走过的每一个足迹,都是自己 生命的 留言; 留给今 天翻过 的日历 ,留给 未来永 久的历 史。
•
3、人生是一座可以采掘开拓的金矿, 但总是 因为人 们的勤 奋程度 不同, 给予人 们的回 报也不 相同。
出钢温度可由下式计算:
T出=T凝+△t1+△t2+△t3+△t4+△t5+α 式中:△t1—出钢过程温降,℃
△t2—出钢完毕至精炼开始的温降,℃ △t3—钢水精炼过程温降,℃ △t4—钢水精炼完毕至开浇前的温降,℃ △t5—钢水从钢包至中间包的温降,℃
α—连铸要求的钢水过热度,℃
终点控制
钢水达到钢种成分和温度要求的时刻,称之为“终点”。 1)钢中碳含量达到所炼钢种控制要求; 2)钢中P、S含量低于规格以下的一定范围; 3)出钢温度能保证进行精炼和浇铸; 4)对于沸腾钢,钢水应具有一定的氧化性。
连铸工艺示意图
连铸工艺的优点
• 简化工艺流程,提高生产效率
连铸省掉了脱模、整模、钢锭均热和开坯等工序。
• 提高金属收得率
连铸的切头、切尾损失为1%-2%,可提高金属收得率10%-14%。
• 降低能耗
由于提高了成坯率,省掉均热、开坯等能耗。
120t区域精炼工艺3-16详解PPT课件

7/30/2024
.
16
适当的Al2O3含量:在渣中的Al2O3含量低于30% 时,增加其含量,可以增加渣的流动性,改善动力 学2.0条低%件氧以,势下但:,是(以FAe保Ol2O证+M3脱含n氧O量+、过C脱高r2O硫,3效)不含果利量。于一夹般杂应物控的制吸在附。 因此Ca应F2尽:量萤减石少有其利用于量化。渣,但是对包衬的侵蚀严重,
5.由于Al2O3比硅化合物更容易通过碰撞、聚合长大,因此更易去除。 6.在精炼处理过程中,钢水被渣中的FeO、MnO以及大气中的氧二次 氧化。
7/30/2024
.
21
4.Ca处理
对 不于易A去l脱除氧。镇通静过钢向,钢钢液中中夹加杂入物钙主合要金是或固高态CaAOl2O渣3料夹,杂将物钢,中熔点固高态, 的 的 的夹夹Al2杂杂O3物物转对中变钢S为的材液平性态衡能的浓的铝度影酸很响钙高也球,比形可固夹以态杂吸A,l附2O易大3小于量。从的同钢S时,液,中当含排其C除温a。度O残降很余低高 时,CaS析出,生成复合夹杂物,该夹杂物为球形,熔点高,轧制 时状态不变形。
搅拌作为一种炉外精炼手段,搅拌强度、持续时间应当可以按精炼要求 控制。
较早出现的搅拌方法,是利用钢液本身的位能,依靠钢液的冲击,促使 钢水搅动。
真空碳氧反应产生的CO气泡产生熔池搅拌,但搅拌强度较弱,持续的时 间也不可能太长,精确控制也比较困难。
RH、DH等方法利用压差造成部分钢水位能差异,利用钢液回流搅动熔 池,是一种简便可行的办法。
扩散脱氧 Al+O2- →Al2O3 Al2O3+CaO→(CaO)x(Al2O3)y
7/30/2024
.
19
一般情况下,脱氧结束后Mn/Si要>3,保证 生成的硅化物在钢水中以液态存在。
《工学炉外精炼》PPT课件
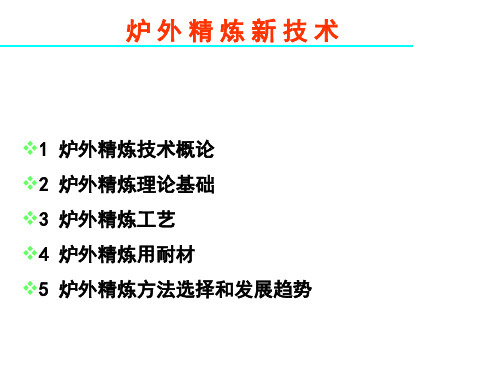
脱【P】 脱磷率≥90%,终点[P]0.010-0.015%,出钢 过程中回磷
炉外精炼的作用和地位
1 提高质量、扩大品种的主要手段
2 优化冶金生产流程,提高生产效率,节 能降耗、降低成本主要方法
3 炼钢-炉外精炼-连铸-热装轧制工 序衔接
4 连铸工艺快速发展的需要
炉外精炼的经济合理性
1 提高初炼炉的生产率 2 缩短生产周期 3 降低产品成本 4 产品质量稳定与提高
钢或铬镍钢,以上所列的各种精炼方法都 不太适用.
出现了一些不锈钢的专用炉外精炼 方法.这些方法发展很快,不到十年就基本 上取代了质低价高的电弧炉吹氧冶炼不锈 钢方法.例如,1976年日本的不锈钢将近有 四分之三是由初炼炉+炉外精炼方法生产 的.1977年美国的所有不锈钢都由初炼炉+
低碳合金钢〔不锈钢〕钢液的精炼方法 <1> VOD<Vacuum Oxygen
炉外精炼的任务 1 钢水成分和温度的均匀化 2 精确控制钢水成分、温度 3 脱氧、脱硫、脱磷、脱碳 4 去除钢中气体〔氢、氮〕及夹杂物 5 夹杂物形态、成分控制
各种炉外精 炼方法及所 采用的精炼 手段
1.3 炉外精炼采用的基本手段
1 渣洗 2 真空 3 搅拌 4 加热 5 喷吹
1.3.1 渣洗 最早出现的炉外精炼方法:用合成
<1>DH法.由原西德的多特蒙特和豪特尔两公司联合 研制,故有此名.在我国又称提升脱气法或虹吸法.
<2>RH法.由原西德鲁尔钢铁公司<Ruhrstahl>和海拉 斯公司<Heraeus>联合研制,我国称真空循环脱气法.
<3>PM法〔Pulsating Mixing Process〕
钢液炉外精炼工艺课件
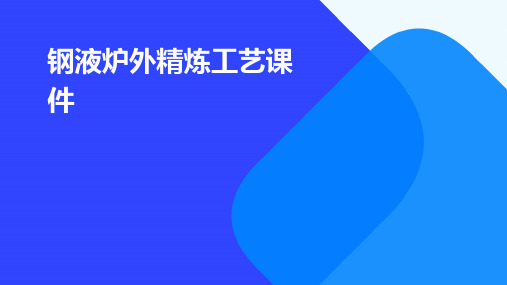
。
提高质量
通过炉外精炼工艺,可 以提高钢材的质量和稳 定性,降低生产成本。
02
钢液炉外精炼的种类与 原理
钢包精炼法
总结词
通过在钢包内对钢液进行加热、搅拌、合金化等操作,去除杂质和气体,提高钢 液质量。
详细描述
钢包精炼法是在钢包内通过加热、搅拌、真空脱气、合金化等手段对钢液进行精 炼的过程。通过去除钢液中的杂质和气体,可以提高钢液的纯净度和均匀性,从 而改善钢材的性能。
真空吹氧脱碳法
总结词
在真空条件下向钢液中吹入氧气,通过氧化反应将钢液中的碳含量降低至规定范围。
详细描述
真空吹氧脱碳法是一种通过向钢液中吹入氧气来降低碳含量的精炼工艺。在真空条件下,向钢液中吹 入氧气可以促进氧化反应,使钢液中的碳与氧气结合生成二氧化碳气体,从而达到降低碳含量的目的 。这种方法常用于生产高纯净度低碳钢材。
未来发展趋势
高效化
绿色化
随着能源和环保要求的提高,钢液炉 外精炼技术将向高效化发展,提高生 产效率和能源利用率。
环保要求将推动钢液炉外精炼技术向 绿色化发展,减少废弃物排放和能源 消耗,降低对环境的影响。
智能化
智能化技术将在钢液炉外精炼中得到 广泛应用,实现工艺参数的实时监测 和自动控制,提高产品质量和稳定性 。
应用案例二:建筑用钢的精炼
案例概述
通过钢液炉外精炼工艺,提高建 筑用钢的强度和延展性,满足高 层建筑、大跨度桥梁等建筑的建
造需求。
工艺流程
钢液→精炼处理→连铸→轧制→ 钢材产品。
技术特点
采用夹杂物去除、合金元素调整 等精炼技术,优化钢材的显微组 织和相组成,提高钢材的综合性
炼钢-精炼工艺介绍48页PPT

56、书不仅是生活,而且是现在、过 去和未 来文化 生活的 源泉。 ——库 法耶夫 57、生命不可能有两次,但许多人连一 次也不 善于度 过。— —吕凯 特 58、问渠哪得清如许,为有源头活水来 。—— 朱熹 59、我的努力求学没有得到别的好处, 只不过 是愈来 愈发觉 自己的 无知。 ——笛 卡儿
炼钢-精炼工艺介绍
31、别人笑我太疯癫,我笑他人看不 穿。(名 言网) 32、我不想听失意者的哭泣,抱怨者 的牢骚 ,这是 羊群中 的瘟疫 ,我不 能被它 传染。 我要尽 量避免 绝望, 辛勤耕 耘,忍 受苦楚 。我一 试再试 ,争取 每天的 成功, 避免以 失败收 常在别 人停滞 不前时 ,我继 续拼搏 。
拉
60、生活的道路一旦选定,就要勇敢地 走到底 ,决不 回头。 ——左
33、如果惧怕前面跌宕的山岩,生命 就永远 只能是 死水一 潭。 34、当你眼泪忍不住要流出来的时候 ,睁大 眼睛, 千万别 眨眼!你会看到 世界由 清晰变 模糊的 全过程 ,心会 在你泪 水落下 的那一 刻变得 清澈明 晰。盐 。注定 要融化 的,也 许是用 眼泪的 方式。
35、不要以为自己成功一次就可以了 ,也不 要以为 过去的 光荣可 以被永 远肯定 。
炉外精炼工艺ppt

RH旳冶金效果
• 脱H: 2ppm下列; • 脱O: 10ppm下列; • 去N:40ppm下列;真空对脱氮效果一般; • 经济效益好,附加值高;
RH旳发展
• -OB (Oxygen Blowing),真空室下部吹氧 • -KTB (Kawasaki Top Blowing) 日本川崎,
顶吹氧 • -PB(Powder Blowing),真空室下部喷粉
RH工艺参数
• 处理容量:大炉子比小炉子好(50t以上); • 处理时间:钢包在真空位旳停留时间τ;
τ=Tc/Vt Tc允许温降, Vt平均温降℃/min; • 循环因数:C=ω(t/min).t(min)/Q (ton)
ω 循环流量、 t脱气时间、 Q处理容量 • 循环流量ω:主要由上升管与驱动气体流量决定; • 真空度:60-100pa; • 抽气能力。
大搅拌,进一步脱碳,钢液温度到达1670-1750℃; • 加合金、微调成份、加铝、吹氩搅拌几分钟后,破真空
浇铸。
RH真空精炼
RH真空工艺过程
• 出钢后,钢包测温取样; • 下降真空室,插入深度为150-200mm; • 起动真空泵,一根插入管输入驱动气体; • 当真空室旳压力降到26-10kpa后,循环加剧; • 钢水上升速度为5m/s、下降速度为1-2m/s; • 气泡在钢液中将气体及夹杂带出。
LF 工艺操作
• 电炉EBT出钢,出钢过程加合金、加渣料 (石灰、萤石等2%),底吹氩、通电升温、 化渣,10分钟取样分析,加渣料(1%), 测温取样,加合金看脱氧,准备出钢。
• 一般30-50分钟,电耗50-80kwh/t; • 当代转炉、电炉与连铸联络旳纽带。
AOD炉
目旳: • 主要是冶炼高质量旳不锈钢(S,P<50ppm); • 使用更便宜旳原料(采用高碳铬代低碳铬); • 超低碳不锈钢(C<20ppm)。
精制车间生产工艺简介.ppt.Convertor

精制车间生产工艺简介.ppt.Convertor精制车间生产工艺教案1、车间基本情况介绍精制车间是焦化生产工艺中的最后工序。
分别由精苯系统和焦油系统组成,主要生产有有纯苯、甲苯、二甲苯、工业萘、粗酚、洗油、蒽油、改质沥青、中温沥青、废油及沥青漆等十余种化工副产品。
精制车间的产品是其他企业重要的化工原料,其中改质沥青可制造电极,同比中温电极沥青可延长电极寿命长降低损耗;性能更加优良。
工业萘可以用来生产苯酐及作为某些产品的添加剂。
三苯在制取炸药、农药、医药、溶剂、合成纤维、工程塑料等工业中得到广泛应用。
2、精制车间生产工艺介绍精制车间生产工艺特点主要根据物质的沸点不同、比重不同利用物理方法使不同的物质得到分离从而生产出不同的产品,部分产品通过化学方法使物质反应而得到产品,总之就是综合利用化学及物理的方法实现生产要求。
2.1 精苯工艺介绍精苯系统设计加工能力为一万吨轻苯的生产能力,采用半连续法生产工艺生产三苯(纯苯、甲苯、二甲苯); 甲苯二甲苯则采用同一塔生产。
精苯生产热源导热油。
(2005年6年)具体工艺如下:来自净化车间的轻苯在初馏塔初步蒸馏(除去不饱和化合物和硫化物)得到以苯、甲苯、二甲苯为主的混合份(未洗混合份),未洗混合份中还含有少量的不饱和化合物和硫化物, 用93~95%硫酸洗涤使其中的不饱和化合物发生聚合反应;生成深度聚合物被分离后,得到已洗混合份,已洗混合份中还有部分洗涤产生的聚合物(中式酯等),已洗混合份通过吹苯塔将中式酯等聚合物呈残渣排出。
从吹苯塔出来的吹出苯在纯苯塔内蒸馏,塔顶得到纯苯,塔底得到纯残。
将纯残送入精制塔蒸馏,塔顶得到甲苯、塔底采出甲残,甲残作为生产二甲苯的原料,也通过精制塔分离。
2.2 焦油工段情况介绍焦油系统又分为四个工序组成:分别是焦油蒸馏工序、洗涤工序、工业萘蒸馏工序和改质沥青工序。
2.2.1 焦油蒸馏工艺简介初步脱渣脱水后的焦油,进精制车间焦油油库,经过均质混均再次脱水渣脱,泵入管式炉一段加热到120~130℃进入一次蒸发器脱水,焦油在蒸发器内闪蒸脱水后将焦油水分从≤4%降低到0.5%以下(称无水焦油),无水焦油通过二段泵送入管式炉辐射段加热到400±10 ℃,进入二段蒸发器闪蒸,二段蒸发器底部排出温度为360~380℃的中温沥青进入“218”系统,生产改质沥青;二段蒸发器顶部温度在320~340℃的组分进入馏分塔进行蒸馏,从馏分塔顶部提出温度为110~125℃轻油馏分;馏分塔中部提出温度在180~280℃范围的酚萘洗三混份;馏分塔底部提出温度在275~295℃的混合蒽油产品。
车间工艺流程PPT课件

精品课件
1
• 拉布 • 压印/热转印 • 拷边 • 理布 • 烫线头 • 打扣 • 包装 • 发货
目录
精品课件
2
拉布流程
第一步,看是否是库存布进行领料,库存面料门幅为164cm,上面的色号分别是1#---15#
精品课件
3
拉布流程
第二步,领料的同时在出库表上登记每卷的米数,门幅,色号品名。
精品课件
12
热转印流程
第三步,如印花完的产品需要拷边, 则印花完成后转交于拷边管理
注意:如果印花过程中产品(双面 绒)次品较多的情况下,及时与裁 剪管理进行沟通补货
精品课件
13
热转印流程
第三步,休息和下班都要把衬纸断 开,机器速度调慢,避免浪费。
注意:印花过程中,员工间应通力 合作,忌偷懒耍滑。
精品课件
22
烫线头流程
第二步,烫线头一定要烫出直角, 不要有毛头。烫线头不能有脱落、 散边、或烫不干净的丝在上面,以 免两个布粘连在一起。
注意:有的线头会塞在布里,烫线 头时注意不要漏烫,也不要两个或 多个线头一起烫,这样会导致布料 黏连,包装或者打扣时易散边。
精品课件
23
烫线头流程
第三步,烫完线头的布一定要夹一 张生产单在上面,给后续要用布的 人使用,以免出错。
18
理布流程
注意:理布分为AB两组,A组正面朝 上,B组反面朝上。这样方便统计人 员后续核对订单数量。
精品课件
19
理布流程
第二步,理布过程请把次品挑出来。
精品课件
20
理布流程
第三步,洗标一定在同一位置,以 免后面打扣工序会出错;理布的线 角一定要整齐,方便烫线头。
- 1、下载文档前请自行甄别文档内容的完整性,平台不提供额外的编辑、内容补充、找答案等附加服务。
- 2、"仅部分预览"的文档,不可在线预览部分如存在完整性等问题,可反馈申请退款(可完整预览的文档不适用该条件!)。
- 3、如文档侵犯您的权益,请联系客服反馈,我们会尽快为您处理(人工客服工作时间:9:00-18:30)。
6、开启加热器蒸汽管阀门,使蒸汽加热器预热,蒸汽压力不大于0.5MPa。 7、将毛油泵入毛油罐待用。 8、这时脱胶脱酸工段已处于待机状态。 二、开机 1、开启进油泵、离心混合器以及酸、碱延时器,根据生产量调节进油流 量。 2、观察经蒸汽加热器加热后的出口油温,并调节蒸汽阀门,使出口油温 在60-75度之间。 3、开启酸定量泵。 4、油-酸混合液经过离心混合器,进入酸延时器,并注意酸延时器搅拌 轴的转速,以及罐内液位的变化。
节蒸汽阀门,使蒸汽加热器的出口油温在105-115度之间。 4、当真空干燥器内的油位达到一定高度时,开启真空干燥器抽出泵,
将油抽到一级油罐内(碱炼油罐)。 5、进行取样化验,直至合格。
二、停机: 1、关闭进油阀门。 2、关闭蒸汽加热器的蒸汽阀门。 3、待油抽空后,关闭脱水油抽出泵和真空管道阀门。 4、关闭所有阀门,下次开机待用。
精炼车间工艺流程
第三章 精炼车间工艺及原理
第一节、油脂精炼的目的和方法 第二节、脱胶脱酸工段 第三节、脱色工段 第四节、脱蜡工段 第五节、脱臭工段 第六节、综合注意事项 第七节、锅炉房(蒸汽锅炉与导热油炉) 第八节、操作规程及岗位职责
第一节、油脂产品精炼的意义
油脂精炼属于油脂加工的范畴,油脂加工就是把不同种类、不同制油方法 得到的毛油,加工成各种品种和各种规格的油脂产品的过程,除了油脂精炼, 还包括油脂的改性、调制、水解聚合等。用压榨、浸出、水代法制取的未经精 炼的油脂称为毛油,毛油的主要成份是甘油三酸酯及其混合物。毛油中存在非 甘油三酸酯的成份,统称为“杂质”。
例:毛油流量1m³/h,AV(酸价)1mgKOH/g,碱液浓度20Be`,碱定量泵100L/h, 求冲程?
已知:20Be`=14.36% d=1.2(碱的比重) 解: G理 = 0.713*AV*W
= 0.713*1*1*0.91 = 0.648≈0.65KG G超 =(1+20%)*G理 = 1.2*0.65 = 0.78KG 0.78÷14.36%=5.43KG 碱液=5.43÷1.2=4.5L/h 冲程:4.5÷100=4.5%
油脂的精炼应根据毛油内所含杂质的性质、数量,还要根据精炼后油脂 的用途、要求二采用不同的方法。油脂精炼的方法很多,根据炼油时的操作特 点及炼油时用的材料和杂质相互作用不同,一般可分为下列三类:
1、机械方法:包括沉降、过滤、离心分离。主要用以分离悬浮在油脂 中的机械杂质部分胶溶性杂质。
2、化学方法:主要包括酸炼、碱炼,此外还有氧化、酯化等。酸炼是 用处理,主要除去色素、胶溶性杂质;碱炼是用碱处理,主要除去游离脂肪酸; 氧化主要用于脱色;酯化极少用,用来使游离脂肪酸生成甘油酸酯,以降低游 离脂肪酸含量。
12、在离心机的轻相出口取样,按油品质量的有关标准进行化验,合格后 既引向蒸汽加热器。脱水操作应与脱色段同时开车,脱水后再进行取样化验, 直至合格,送至碱炼油罐。
三、停机 按开机时的顺序依次进行,先将毛油泵停下,接着停止酸碱定量泵,然后 依次停下酸碱延时器,待油全部放空后,关闭离心机和所有相关阀门。 有关离心机的开机与停机请按照离心机厂家提供的操作说明书,并严格按 照离心机厂家培训的要求进行。
3、物理化学方法:主要包括水分、吸附、水蒸馏及液-液萃取法。 水化主要除去磷脂;吸附主要除去色素;水蒸馏用于脱除臭味物质和游 离脂肪酸;液-液萃取用于脱色素、脱除游离脂肪酸等。
以上炼油方法也不能截然分开,如碱炼是典型的化学方法,但碱炼 时,碱与游离脂肪酸生成肥皂会吸附色素(尤其对酚型色素特别有效)、 粘液、蛋白质等,使它和肥皂一起从油中分离,因此碱炼同时伴随着物 理化学和机械精炼的过程。
吸附脱色的作用: 1、脱除色素 2、脱除油脂中残存的胶质、微量金属 3、磷脂、残皂 4、去除多环芳烃、残留农药 5、去除异味 油脂在进脱色塔前或与白土混合前,一般要求油脂中的含皂量≤300ppm (百万分300),水分≤0.15%,并控制白土水分≤12%。
工艺参数如下: 1、白土加入量: 油重的1-3% 2、脱色真空度: -0.096MPa 3、脱色油温: 100-110度 4、脱色时间: 25-30分钟 5、过滤油温: 85度以上
本工段是将酸炼脱胶与碱炼脱酸相结合的工艺,特点是磷酸处理后紧接着 就是碱炼。
1、磷酸脱胶 油脂中的磷脂按其水化特性,可分可水化的和不可水化的两类,其中a -磷脂很容易水化,水化后生成不易溶于油脂的水化物,而b-磷脂则不易水 化,钙、镁、铁等磷脂金属复合物也不易水化,这些就是所谓不能活难以水 化的磷脂。在正常情况下,不可水化磷脂占胶溶性杂质总含量的10%左右。受 损油料中,所含不可水化磷脂数量要高很多。另外在浸出阶段,磷脂酶会促 使可水化磷脂转化成不可水化磷脂,当水分较高和浸出温度较高时,这种转
吸附剂的同时也把被吸附的色素及杂质除掉,从而达到脱色净化的目的。
油脂脱色的方法:
1、吸附脱色法
2、加热脱色法
3、氧脱色法
4、化学试剂脱色法
吸附脱色法的原理:是利用某些具有较强选择性吸附作用的物质,如天
然漂土、活性白土、活性碳、凹凸棒土、沸石等,在加热的情况下能吸附油脂 内色素及其他不纯物质的特性。
5、酸延时器内油位上升超过3/2高度时,应开启碱离心混合器。 6、酸延时器出油时,开启碱定量泵。 7、油-碱混合液经过离心混合器,进入碱延时器,并注意碱延时器搅拌轴的 转速,以及罐内液位的变化。 8、碱延时器内油位上升超过3/2高度时,应开启水洗段的油泵和离心混合器。 9、待油进入脱皂离心机的同时,关闭脱皂离心机进油口的热水阀门,调节 其轻相出口压力,使脱皂离心机运转正常。 10、将脱皂离心机轻相出口油通过油泵引入3#加热器,调节蒸汽阀门,使出 口油温在80-85度之间,调节热水进入的流量为油量的5%左右。 11、待油进入水洗离心机的同时,关闭水洗离心机进油管旁的进水阀门。调 节其轻相出口压力,使脱皂离心机运转正常。
更有效的分离油和皂角。反应混合物离心分离成油和皂角,皂角进入皂角罐 暂存。
碱炼时,耗用的总碱量包括两个部分,一是用于中和游离脂肪酸的碱, 通常成为理论碱,计算公式:G=0.713*AV*W
G→理论固体烧碱量,单位KG; AV→油脂酸价,单位mgKOH/g油; W→油脂重量,单位T。 需要提醒的是,在本车间的工艺中,当在确定用于计算理论加碱量所用 的毛油酸价时,所采用的酸价应比实验室测定的毛油酸价稍微高一点,约高 2-3个酸价单位,用于中和酸炼后油中残余的酸溶液。 另一部分则是为了满足工艺需求而额外增加的碱,称为超量碱,约为 0.1-0.3油重,但为了减少中性油的皂化损失,建议超量碱最多不能超过0.5%
溶解于油的胶状物而沉淀。中和生成的肥皂为表面活性剂,吸附能力很强,可 吸附油中的其它杂质(色素、胶质、悬浮物质等)。因此,碱炼本身具有脱酸、 脱胶、脱固体杂质和脱色等综合作用。这里需要特别注意的是,烧碱中和游离 脂肪酸的同时,还可能发生甘三酯(中性油)的皂化,引起炼耗的增加,因此 要严格控制操作条件,以获得高质量和高得率的成品。碱液浓度一般控制在 12-22Be` 。加热是为了加快反应速度,降低皂角含油和降低油的粘度,以便
流程图如下
4、脱胶脱酸操作 一、开机前准备:
1、向热水管注入软水,并开启直接蒸汽和间接蒸汽阀门,将其加热至9095度。(程序参数里设置所需温度)
2、启动热水泵,调节出口压力在0.3MPa,打开脱皂离心机和水洗离心机进 油管道旁的热水阀门。
3、将配制好的碱液泵入碱罐,再由低位罐泵入高位罐。 4、根据每小时处理毛油量、毛油酸价,确定磷酸、碱液的用量,并调节好 酸定量泵和碱定量泵的冲程。 5、按离心机操作方法启动脱皂离心机和水洗离心机,待离心机达到满速时, 开启离心机进油管道旁的热水阀门,预热离心机,同时开启皂角泵。
油脂精炼包括以下工艺程序: 1、去除悬浮杂质:可用机械方法除之。 2、脱胶:可用水化、酸炼,也可以碱炼。 3、脱酸:可用碱炼、水蒸汽蒸馏。 4、脱色:一般用白土等吸附。 5、脱蜡:一般用低温结晶去除。 6、脱臭:都用水蒸汽蒸馏法。
本车间用于精炼植物油,分四个工段:脱胶脱酸、脱色、脱蜡、脱臭。
第二节、脱胶脱酸
如何配20Be`碱液? 片碱纯度96%,碱的比重1.2,20Be`碱液浓度为14.36%. 操作注意事项: 1、配碱前先清理干净配碱池,无杂质。 2、先放3/1的软水。 3、再放片碱,边放边搅拌均匀,充分溶解(上下搅拌)。 4、配好后,用比重计测量20Be`值,就可以了。(常温下测量) 注意:放片碱要充分搅拌溶解,否则片碱容易结晶、堵住管道、上下浓 度不一样。 1m³容量片碱:1*1.2*1000*14.36%=172.32KG 本车间配碱池为1.5m³左右,1.5*172.32=258.48KG;可配20Be`的碱溶液
1、悬浮杂质:主要包括泥沙、饼渣、铁屑、草屑及其他固体杂质。 2、胶溶性杂质:主要包括磷脂、蛋白质、糖类等。 3、脂溶性杂质:主要包括游离脂肪酸、色素、生育酚、甾醇、蜡、烃类、 醛酮,还有微量金属和由于环境污染带来的有机磷,汞、多环芳烃、黄曲酶毒 4、水分
以上杂质的存在,容易使油脂产生异味和酸败,降低油脂的品质和使 用价值。毛油的除杂过程,即为油脂的精炼。
化更显著。因此,在有的油脂中,含不可水化磷脂是正常情况的2-3倍,其中 B-磷脂可以用酸处理去除,二磷脂金属复合物,必须用酸处理方法除去,否则, 在碱炼时不仅会产生一般胶质的乳化作用,而且生成的钙镁等金属皂水洗时不 易洗去。因食品含有微量的磷酸是允许的,酸炼脱胶常使用磷酸。磷酸脱胶除 了上诉作用外,还具有如下作用:使叶绿素转化成色浅的脱镁叶绿素,对降低 红色很有利;使Fe、Cu等离子络合物,钝化微量金属对油脂氧化的催化作用, 增加了油脂的氧化稳定性。
离心机简介如下:
真空干燥器 真空干燥器是用于脱除碱炼油中的水分,首先利用喷嘴雾化油滴及碟盘
成膜特性,降低(减少)油中可挥发物(这里主要是水分)挥发(蒸发)路 径,使其瞬间快速蒸发(即闪蒸),从而达到脱水的目的,在真空条件下, 水分很快被蒸发出来。