钢铁料消耗计算
粗钢生产工序能耗计算

粗钢生产工序能耗计算引言能耗计算是工业生产过程中的一个重要环节,通过对不同工序的能耗进行准确计算,可以帮助企业找出能耗较高的环节,进而采取相应的节能措施,提高生产效率,降低成本。
本文将针对粗钢生产过程中的不同工序进行能耗计算,以帮助企业更好地控制和优化能源消耗。
粗钢生产工序简介粗钢是指通过冶炼过程制得的未经初步加工的钢材,具有较高的含碳量和较低的纯度。
粗钢生产工序一般包括:原料准备、熔炼冶炼、钢水处理、连铸、初轧和粗轧等环节。
原料准备能耗计算原料准备环节主要包括铁矿石的破碎、磨矿、混合和配料等过程。
根据实际产量和生产数据,可以计算出原料准备环节的能耗。
原料准备能耗 = 原料准备消耗能量 / 产量熔炼冶炼能耗计算熔炼冶炼环节是将铁矿石和其他辅助材料经高温熔炼,得到钢水的过程。
熔炼冶炼能耗可以通过以下公式计算:熔炼冶炼能耗 = 燃料消耗能量 + 电能消耗能量 + 冷却水消耗能量 / 产量钢水处理能耗计算钢水处理环节是将熔炼冶炼出来的钢水经过脱硫、脱氧等处理,提高钢水的纯度和质量。
钢水处理能耗可以通过以下公式计算:钢水处理能耗 = 电能消耗能量 + 冷却水消耗能量 / 产量连铸能耗计算连铸是将钢水浇铸成连续铸坯的过程,连铸能耗可以通过以下公式计算:连铸能耗 = 电能消耗能量 + 冷却水消耗能量 + 氧气消耗能量 / 产量初轧能耗计算初轧环节是将连铸坯经过初轧机轧制成规定尺寸的厚板,并进行质量控制。
初轧能耗可以通过以下公式计算:初轧能耗 = 电能消耗能量 + 冷却水消耗能量 / 产量粗轧能耗计算粗轧环节是将初轧后的厚板不断轧制,降低其厚度,最终得到要求尺寸的薄板。
粗轧能耗可以通过以下公式计算:粗轧能耗 = 电能消耗能量 + 冷却水消耗能量 / 产量结论通过对粗钢生产工序的能耗计算,可以帮助企业找出能源消耗较高的环节,并针对性地采取节能措施,提高能源利用效率,降低生产成本。
在实际应用中,还应考虑到设备能效、操作参数等因素对能耗的影响,以实现更精确和全面的能耗计算和优化。
材料消耗计算方法
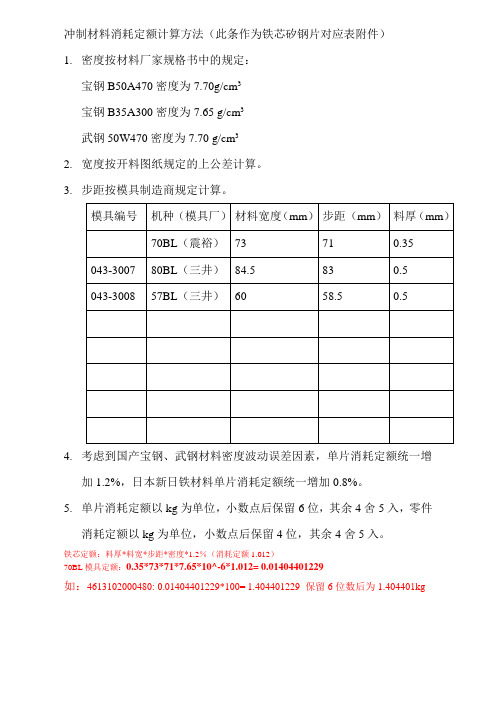
冲制材料消耗定额计算方法(此条作为铁芯矽钢片对应表附件)
1.密度按材料厂家规格书中的规定:
宝钢B50A470密度为7.70g/cm3
宝钢B35A300密度为7.65 g/cm3
武钢50W470密度为7.70 g/cm3
2.宽度按开料图纸规定的上公差计算。
3.步距按模具制造商规定计算。
4.考虑到国产宝钢、武钢材料密度波动误差因素,单片消耗定额统一增
加1.2%,日本新日铁材料单片消耗定额统一增加0.8%。
5.单片消耗定额以kg为单位,小数点后保留6位,其余4舍5入,零件
消耗定额以kg为单位,小数点后保留4位,其余4舍5入。
铁芯定额:料厚*料宽*步距*密度*1.2%(消耗定额1.012)
70BL模具定额:0.35*73*71*7.65*10^-6*1.012=0.01404401229
如:4613102000480: 0.01404401229*100=1.404401229 保留6位数后为1.404401kg。
关于50吨转炉钢铁料消耗测算及影响因素分析

攀成钢50吨转炉钢铁料消耗测算及影响因素分析杨文明刘志军易良刚攀钢集团成都钢钒有限公司攀成钢50吨转炉2008年钢铁料消耗为1133.91kg/t,随后逐年降低,至2010年降低至1114.539kg/t,而在2011年1-8月钢铁料消耗达到1118.819kg/t。
通过对2011年1-8月钢铁料测算与2010年同期比较,掌握钢铁料各工序消耗状况,分析原因,并提出改进措施。
0 前言钢铁料消耗是炼钢厂的重要经济技术指标,其成本约占炼钢成本的80%左右,降低其消耗是炼钢厂降低成本、提高竞争力的主要手段之一,也是操作水平和综合管理水平的体现。
从某种意义上说炼钢企业降低了钢铁消耗量就意味着增加了企业收入,因此,炼钢企业不断优化钢铁料消耗指标,对提高企业经济效益和产品竞争力具有十分重要的意义。
1、钢铁料消耗的定义按照中国钢铁工业协会制定的《中国钢铁工业生产统计指标体系》的规定[1],钢铁料=生铁量+废钢铁量,钢铁料消耗=钢铁料量÷合格钢产量。
废钢铁包括各种废钢、废铁等。
在计算废钢铁消耗指标时, 除轻薄废钢、渣钢、优质钢丝、各类铁、钢屑按规定的折合标准进行折合外, 其它废钢均按实物量计算。
计算钢铁料消耗应按每投一次料就算一次消耗。
1.1 对钢铁料消耗定义的理解《中国钢铁工业生产统计指标体系》的规定,钢铁料=生铁量+废钢铁量,钢铁料消耗=钢铁料量÷合格钢产量。
根据该原则,钢铁料消耗中的几个问题需要做出如下解释。
1)合金吸收量是否应该扣除在生产过程中几乎每炉钢都要加入合金(如硅铁、锰铁等),加入的合金是没有在钢铁料量中扣除的。
而一些钢铁企业(如酒钢)是将合金吸收量进行了扣除,这样钢铁料消耗就降低。
根据“规定”我们认为加入的合金不应该计入钢铁料消耗。
2)中间包余水及切头切尾量在回炉时是否计入“废钢铁料量”。
50吨转炉主要生产高品质的管坯钢,连浇炉数少,中间包余水及切头切尾量大,我们认为这部分废钢属于自产废钢,不应计入消耗。
影响钢铁料消耗的主要因素分析

影响钢铁料消耗的主要因素分析1前言钢铁料消耗指标是炼钢厂重要的经济技术指标,一般占生产成本的80~85%,对炼钢厂的成本有重要的意义。
钢铁料消耗国家规定的统计标准:转炉钢铁料消耗(kg/t钢)=[铁水+生铁+废钢铁量(kg)]/转炉合格产出量(t),其中:生铁包括高炉铁块、还原铁;废钢铁包括各种废钢、废铁等。
(行业惯例目前都以合格铸坯量代替转炉合格产出量)以下对影响钢铁料的主要因素进行梳理,由于涉及的因素较多,以定性分析为主。
2影响钢铁料消耗的主要因素2.1铁水预处理铁水脱硫处理的钢铁料损失主要发生在处理前后的扒渣带铁和处理过程中的喷溅及铁水倒运铁损失等。
扒渣带铁与铁水自带的高炉渣和脱硫渣量成正比,其中脱硫渣量的大小与采用的脱硫剂有关。
如复合喷吹脱硫工艺,脱硫剂消耗为4 kg/t铁,渣量为4.64kg/t铁,扒渣铁损为2.09 kg/t铁。
2.2转炉冶炼转炉的钢铁料损失主要由冶炼的烟尘、钢渣及喷溅等因素引起,占本工序损失量的98%,回炉、钢水出不尽等占一部分。
烟尘损失:通常情况下占转炉工序损失量的55%,其中碳氧化损耗约占44%、金属烧损约占11%,这部分损失量主要取决于钢铁料中碳含量。
钢渣中金属损失量:通常情况下占损失量的37 %,其中硅、锰氧化损失约占7.5%,铁氧化损失约占22.5%,渣中钢粒约占7%。
喷溅损失:通常情况下约占6%。
回炉、钢水出不尽等:通常情况下约占2%。
转炉冶炼是一个氧化过程,减少氧化损失是减少钢铁料损失的关键。
氧化损失中,一类为必要损失,无法避免,如碳、硅、锰等元素氧化,以获得化学热,这部分损失为必要损失。
另一类氧化损失是可以避免或减少的,如转炉后吹。
2.3 连铸连铸的钢铁料损失主要包括氧化铁皮、切割损失、切头切尾、中包注余、大包注余、漏钢、废品、清理损失等。
其中中包注余、切头切尾、切割损失等因素,占连铸工序钢铁料损失量的80%。
中包注余:通常约占连铸工序损失量的40%。
炼钢部分各种计算公式汇总
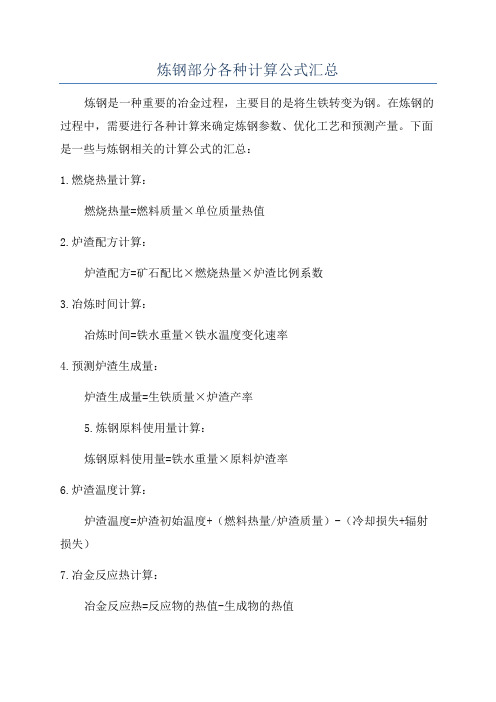
炼钢部分各种计算公式汇总炼钢是一种重要的冶金过程,主要目的是将生铁转变为钢。
在炼钢的过程中,需要进行各种计算来确定炼钢参数、优化工艺和预测产量。
下面是一些与炼钢相关的计算公式的汇总:1.燃烧热量计算:燃烧热量=燃料质量×单位质量热值2.炉渣配方计算:炉渣配方=矿石配比×燃烧热量×炉渣比例系数3.冶炼时间计算:冶炼时间=铁水重量×铁水温度变化速率4.预测炉渣生成量:炉渣生成量=生铁质量×炉渣产率5.炼钢原料使用量计算:炼钢原料使用量=铁水重量×原料炉渣率6.炉渣温度计算:炉渣温度=炉渣初始温度+(燃料热量/炉渣质量)-(冷却损失+辐射损失)7.冶金反应热计算:冶金反应热=反应物的热值-生成物的热值8.炉温控制计算:炉温控制=炉温目标值-炉温测量值9.耗氧量计算:耗氧量=氧气流量×氧浓度×燃烧公式系数10.炉渣替代率计算:炉渣替代率=炉渣替代量/炉渣生成量11.冷却水量计算:冷却水量=冷却热量/剪切热12.制氧气量计算:制氧气量=铁水含氧量×铁水重量×(氧气纯度/100)13.吹氧流量计算:吹氧流量=制氧气量/铁水供氧时间14.坩埚温度计算:坩埚温度=铁水温度+气氛温度15.炉水质量计算:炉水质量=炉水比例×矿石质量以上是一些与炼钢相关的计算公式的汇总。
当然,实际的炼钢过程非常复杂,还需要考虑其他因素如温度、压力、流量等等。
这些公式只是提供了一些基本的计算方法,实际应用中还需要根据具体情况进行适当的调整和修正。
炼铁铁料单耗计算
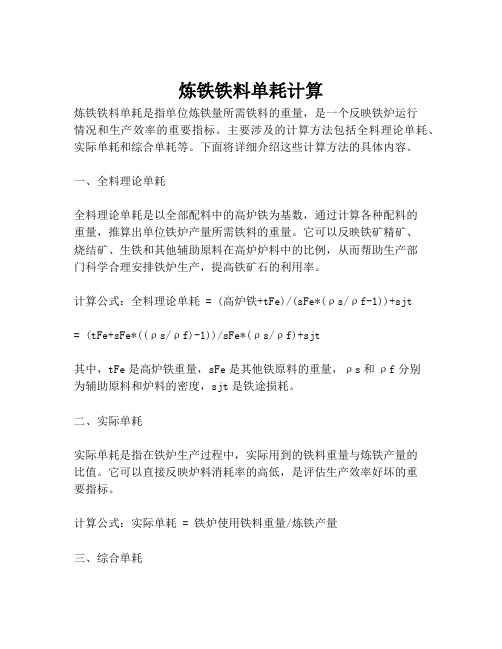
炼铁铁料单耗计算炼铁铁料单耗是指单位炼铁量所需铁料的重量,是一个反映铁炉运行情况和生产效率的重要指标。
主要涉及的计算方法包括全料理论单耗、实际单耗和综合单耗等。
下面将详细介绍这些计算方法的具体内容。
一、全料理论单耗全料理论单耗是以全部配料中的高炉铁为基数,通过计算各种配料的重量,推算出单位铁炉产量所需铁料的重量。
它可以反映铁矿精矿、烧结矿、生铁和其他辅助原料在高炉炉料中的比例,从而帮助生产部门科学合理安排铁炉生产,提高铁矿石的利用率。
计算公式:全料理论单耗 = (高炉铁+tFe)/(sFe*(ρs/ρf-1))+sjt= (tFe+sFe*((ρs/ρf)-1))/sFe*(ρs/ρf)+sjt其中,tFe是高炉铁重量,sFe是其他铁原料的重量,ρs和ρf分别为辅助原料和炉料的密度,sjt是铁途损耗。
二、实际单耗实际单耗是指在铁炉生产过程中,实际用到的铁料重量与炼铁产量的比值。
它可以直接反映炉料消耗率的高低,是评估生产效率好坏的重要指标。
计算公式:实际单耗 = 铁炉使用铁料重量/炼铁产量三、综合单耗综合单耗是全料理论单耗和实际单耗相结合的综合指标。
它要考虑到铁炉运行的各种因素,包括料型、炉温、喷煤、风量等。
只有达到全料单耗,又达到实际单耗的要求,才能说明铁炉生产达到最佳状态。
计算公式:综合单耗 = 铁炉使用铁料重量/炼铁产量 + (实际单耗-全料理论单耗)/全料理论单耗四、注意事项1.计算时应严格按照各种原料的实际重量进行计算;2.不同企业的计算方法可能有所不同,要根据自身的情况选择合适的计算方法;3.计算的过程中需要关注铁途损耗的影响,进行正确的调整和计算;4.每个铁炉的生产情况都不同,要根据实际情况进行相应的计算和分析。
总之,炼铁铁料单耗的准确计算对于评估铁炉生产效率、优化炉料配比、提高铁矿石利用率等方面均具有重要意义。
需要在实际生产中采用合适的计算方法,确保数据的准确性和科学性。
主要生产指标的计算公式
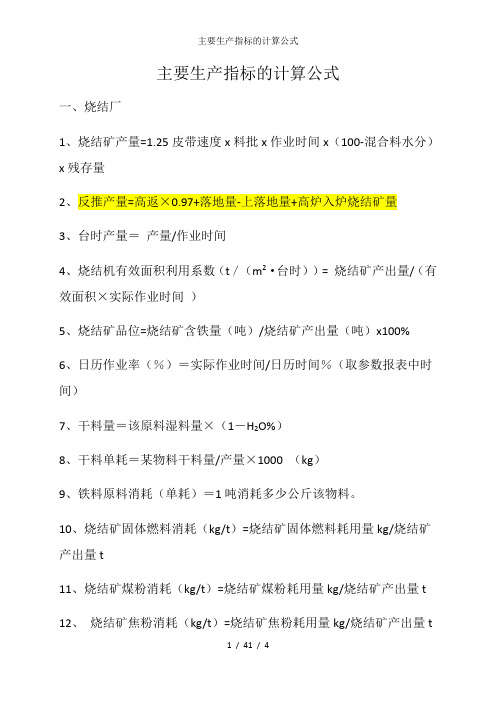
主要生产指标的计算公式一、烧结厂1、烧结矿产量=1.25皮带速度x料批x作业时间x(100-混合料水分)x残存量2、反推产量=高返×0.97+落地量-上落地量+高炉入炉烧结矿量3、台时产量=产量/作业时间4、烧结机有效面积利用系数(t/(m2·台时))= 烧结矿产出量/(有效面积×实际作业时间)5、烧结矿品位=烧结矿含铁量(吨)/烧结矿产出量(吨)x100%6、日历作业率(%)=实际作业时间/日历时间%(取参数报表中时间)7、干料量=该原料湿料量×(1-H2O%)8、干料单耗=某物料干料量/产量×1000 (kg)9、铁料原料消耗(单耗)=1吨消耗多少公斤该物料。
10、烧结矿固体燃料消耗(kg/t)=烧结矿固体燃料耗用量kg/烧结矿产出量t11、烧结矿煤粉消耗(kg/t)=烧结矿煤粉耗用量kg/烧结矿产出量t12、烧结矿焦粉消耗(kg/t)=烧结矿焦粉耗用量kg/烧结矿产出量t13、一次配料:某料下料量=某料的百分比×总下料量∕100 (t)14、一次配料某物料配比=某料总配比表中配比/一次配料物料在总配比表配比之和15、某物料下料量=某物料下料量(吨/小时)×运行时间段16、成品率=产量/(产量+返矿)%(返矿取配料配比变更)17、出矿率=产量/(混合料总量×0.92)%18、返矿率=返矿/(产量+返矿)%二、炼铁厂1、生铁合格率(%)=生铁检验合格量(吨)/生铁检验总量(吨)x100%2、生铁一级品率(%)=一级品生铁总量/合格生铁检验总量x100%3、入炉焦比是反映高炉冶炼每1吨合格生铁所消耗的干焦炭量。
入炉焦比(kg/t)=干焦耗用量kg/合格生铁产量t4、干焦量=湿焦量x(1-湿焦含水%)5、综合焦比是指高炉冶炼每1吨合格生铁所消耗的综合干焦(将各种燃料均折合成干焦计算)量。
综合焦比(kg/t)=综合干焦耗用量kg/合格生铁产量t6、综合干焦量=干焦量+其他各种燃料量x折合干焦系数7、喷煤比是反映高炉冶炼1吨合格生铁所消耗的煤量。
钢材消耗量计算
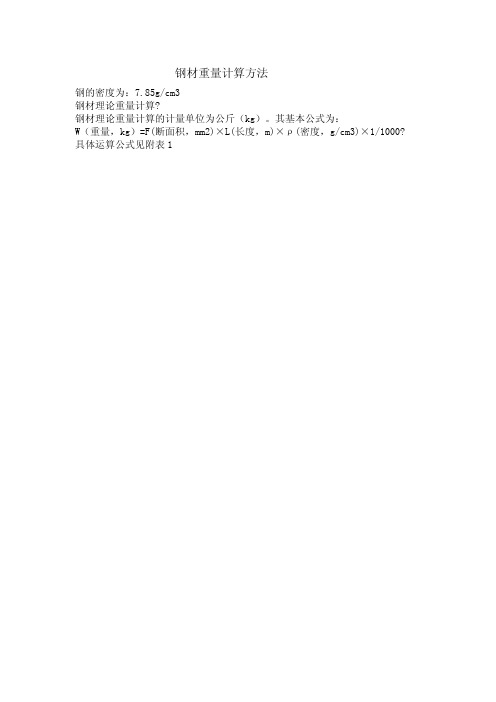
钢材重量计算方法钢的密度为:7.85g/cm3钢材理论重量计算?钢材理论重量计算的计量单位为公斤(kg)。
其基本公式为:W(重量,kg)=F(断面积,mm2)×L(长度,m)×ρ(密度,g/cm3)×1/1000? 具体运算公式见附表1附录1名称(单位)计算公式符号意义计算举例圆钢/盘条 (kg/m)W=0.006165×d×d d=直径mm直径100mm的圆钢,求每m重量。
每m重量W=0.006165×100^2=61.65kg螺纹钢 (kg/m) W=0.00617×d×dd=断面直径mm断面直径为12mm的螺纹钢,求每m重量。
每m重量W=0.00617×12^2=0.89kg方钢 (kg/m)W=0.00785×a×a a=边宽mm边宽20mm的方钢,求每m重量。
每m重量W=0.00785×20^2=3.14kg扁钢 (kg/m)W=0.00785×b×d b=边宽mmd=厚mm边宽40mm,厚5mm的扁钢,求每m重量。
每m重量W=0.00785×40×5=1.57kg六角钢 (kg/m)W=0.006798×s×s s=对边距离mm对边距离50mm的六角钢,求每m重量。
每m重量W=0.006798×50^2=17kg八角钢 (kg/m)W=0.0065×s×s s=对边距离mm对边距离80mm的八角钢,求每m重量。
每m重量W=0.0065×80^2=41.62kg等边角钢 (kg/m)W=0.00785×[d(2b–d)+0.215(R^2–2r^2)]b=边宽d=边厚R=内弧半径r=端弧半径求20mm×4mm等边角钢的每m重量。
从冶金产品目录中查出4mm×20mm等边角钢的R为3.5,r为1.2,则每m重量W=0.00785?×[4×2×20–4)+0.215×(3.5^2–2×1.2^2)]=1.15kg不等边角钢(kg/m)W=0.00785×[d(B+b–d)+0.215(R^2–2r^2)]B=长边宽b=短边宽d=边厚R=内弧半径r=端弧半径求30mm×20mm×4mm不等边角钢的每m重量。
炼钢铁水消耗计算公式
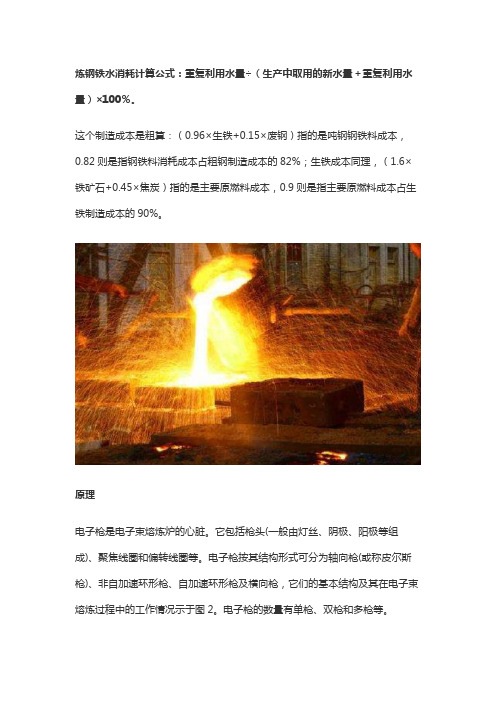
炼钢铁水消耗计算公式:重复利用水量÷(生产中取用的新水量+重复利用水量)×100%。
这个制造成本是粗算:(0.96×生铁+0.15×废钢)指的是吨钢钢铁料成本,0.82则是指钢铁料消耗成本占粗钢制造成本的82%;生铁成本同理,(1.6×铁矿石+0.45×焦炭)指的是主要原燃料成本,0.9则是指主要原燃料成本占生铁制造成本的90%。
原理
电子枪是电子束熔炼炉的心脏。
它包括枪头(一般由灯丝、阴极、阳极等组成)、聚焦线圈和偏转线圈等。
电子枪按其结构形式可分为轴向枪(或称皮尔斯枪)、非自加速环形枪、自加速环形枪及横向枪,它们的基本结构及其在电子束熔炼过程中的工作情况示于图2。
电子枪的数量有单枪、双枪和多枪等。
钢铁料消耗计算
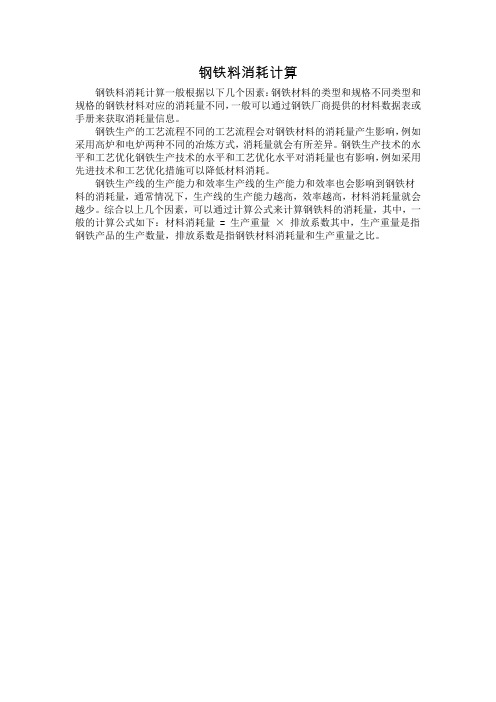
钢铁料消耗计算
钢铁料消耗计算一般根据以下几个因素:钢铁材料的类型和规格不同类型和规格的钢铁材料对应的消耗量不同,一般可以通过钢铁厂商提供的材料数据表或手册来获取消耗量信息。
钢铁生产的工艺流程不同的工艺流程会对钢铁材料的消耗量产生影响,例如采用高炉和电炉两种不同的冶炼方式,消耗量就会有所差异。
钢铁生产技术的水平和工艺优化钢铁生产技术的水平和工艺优化水平对消耗量也有影响,例如采用先进技术和工艺优化措施可以降低材料消耗。
钢铁生产线的生产能力和效率生产线的生产能力和效率也会影响到钢铁材料的消耗量,通常情况下,生产线的生产能力越高,效率越高,材料消耗量就会越少。
综合以上几个因素,可以通过计算公式来计算钢铁料的消耗量,其中,一般的计算公式如下:材料消耗量 = 生产重量×排放系数其中,生产重量是指钢铁产品的生产数量,排放系数是指钢铁材料消耗量和生产重量之比。
120吨转炉铁平衡和电炉钢铁料消耗值
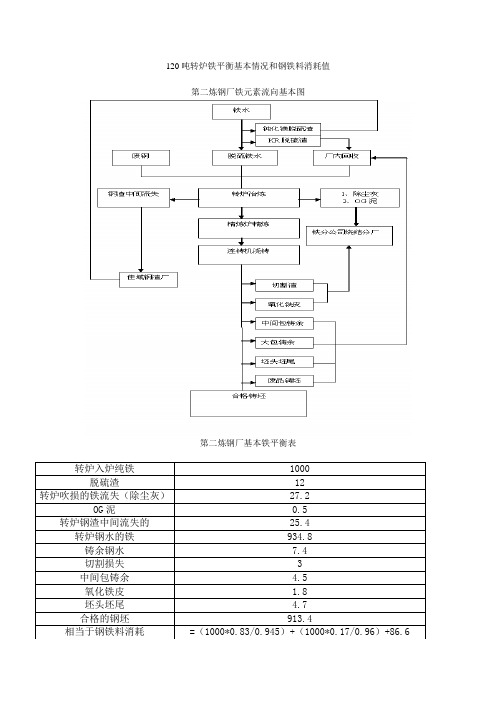
=(1000*0.83/0.945)+(1000*0.17/0.96)+86.6
=1141
回收:11kg(中间包铸余和事故损失)+12坯头坯尾+
20(25*0.85大块铁含量*0.9回收率
kg佳域钢渣厂+2.5(大包铸余,从70吨电炉拨)=1095
电炉的铁平衡
转化图
铁元素平衡计算
电炉入炉纯铁
120吨转炉铁平衡基本情况和钢铁料消耗值
第二炼钢厂铁元素流向基本图
第二炼钢厂基本铁平衡表
转炉入炉纯铁
1000
脱硫渣
12
转炉吹损的铁流失(除尘Байду номын сангаас)
27.2
OG泥
0.5
转炉钢渣中间流失的
25.4
转炉钢水的铁
934.8
铸余钢水
7.4
切割损失
3
中间包铸余
4.5
氧化铁皮
1.8
坯头坯尾
4.7
合格的钢坯
913.4
1000
钢渣带走的铁元素
32
除尘灰带走
31.2
铸余钢水
4
切割损失
4.2
中间包铸余
2.5
氧化铁皮
2.6
坯头坯尾
3.5
合格的钢坯
920
相当于吨钢的钢铁料消耗
=(1000*0.25/0.95)+(1000*0.75/0.98)+80
=1105
消化自产回收5坯头坯尾+3中间包铸余+5大包铸余
实际的钢铁料消耗1092
炼钢部分各种计算公式汇总
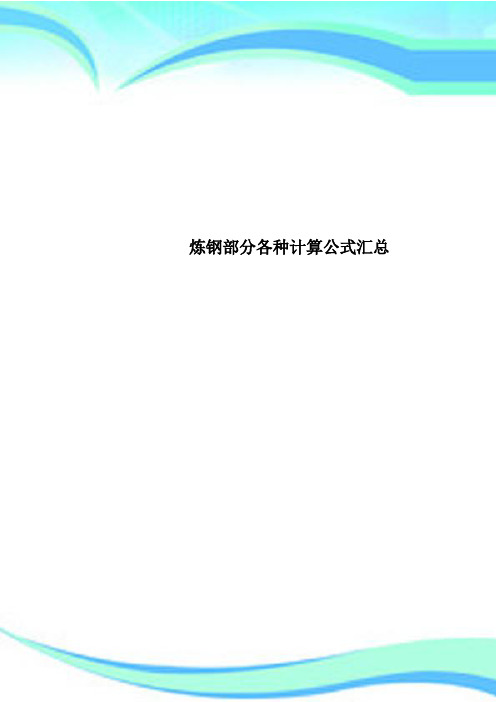
炼钢部分各种计算公式汇总————————————————————————————————作者: ————————————————————————————————日期:炼钢部分各种计算公式汇总1、转炉装入量装入量=错误!未定义书签。
2、氧气流量Q=错误!Q-氧气流量(标态),错误!或 错误!V-1炉钢的氧气耗量(标态),m3; t-1炉钢吹炼时间,min 或h 3、供氧强度 I=错误!I-供氧强度(标态),错误!未定义书签。
; Q -氧气流量(标态),错误!;T-出钢量,t注:氧气理论计算值仅为总耗氧量的75%~85%。
氧枪音速计算 α=(κgR T)1/2m/sα—当地条件下的音速,m/s ;κ—气体的热容比,对于空气和氧气,κ=1.4;g —重力加速度,9.81m/s 2;R —气体常数,26.49m/κ。
马赫数计算 M=ν/αM —马赫数;ν—气体流速,m/s ;α—音速,m/s。
冲击深度计算h冲=K 错误!未定义书签。
h 冲—冲击深度,m ;P0—氧气的滞止压力(绝对),㎏/㎝2;d0—喷管出口直径,m ;H 枪—枪位,m;ρ金—金属的密度,㎏/m 3;d c —候口直径,m ;B —常数,对低粘度液体取作40;K —考虑到转炉实际吹炼特点的系数,等于40。
在淹没吹炼的情况下,H=0,冲击深度达到最大值,即 hma x=P 00.5·d00.6ρ金0.4有效冲击面积计算R=2.41×104(错误!未定义书签。
)2R—有效冲击半径,m ;νmax —液面氧射流中心流速,m/s; νm ax =ν出错误!·错误!未定义书签。
ν出—氧射流在出口处的流速,m/s 。
金属-氧接触面积计算在淹没吹炼时,射流中的金属液滴重是氧气重量的3倍,吹入1m3氧气的液滴总表面积(金属-氧气的接触面积): S Σ=\f (3G 金,r 平均·ρ金)G金—1标米3氧气中的金属液滴重量=3×1.43㎏;r 平均—液滴的平均半径,m ;ρ金—金属液的密度,7×103㎏/m 3。
钢铁料消耗计算

钢铁料耗计算知识钢铁料耗是炼钢厂重要的经济技术指标,一般占转炉生产成本的80~85%,降低钢铁料耗成为一个炼钢厂降成本的主要手段,钢铁料耗指标即体现了炼钢厂技术水平,也体现了管理水平,对炼钢厂的成本有重要的意义。
一、钢铁料耗的统计方式。
1.理论基础任何指标都要统一标准才好对比,钢铁料耗的理论基础是物质不灭定律,推广到具体的钢铁料耗方面为物料平衡,投入量与产出量之间的关系,为了统计方便,国家专门制订了钢铁料耗统计的相关规定。
2.国家规定的统计标准:转炉钢铁料消耗(kg/t钢)=[生铁+废钢铁量(kg)]/转炉(电炉)合格产出量(t)其中:生铁包括冷生铁、高炉铁水、还原铁;废钢铁包括各种废钢、废铁等。
凡分别管理、按类配用下列废钢铁的,在计算废钢铁消耗指标时,可按下列统一的折合标准折合计算:a. 轻薄料废钢,包括锈蚀的薄钢板以及相当于锈蚀薄板的其他轻薄废钢,按实物量×60%计算,其加工压块按实物量×60%计算;关于轻薄废钢,国家标准GB/T4223-1996中有明确规定;b. 渣钢是指从炉渣中回收的带渣子的钢,按实物×70% 计算;经过砸碎加工(基本上去掉杂质)的渣钢,按实物量×90%计算;c. 优质钢丝(即过去所称“钢丝”)、钢丝绳、普通钢钢丝(即过去所称“铁丝”)、铁屑以及钢锭扒皮车屑和机械加工的废钢屑(加工压块在内),按实物量×60%计算;d. 钢坯切头切尾、汤道、中注管钢、桶底钢、冻包钢、重废钢等均按实物计算。
3某些厂家的统计方式国家标准规定钢铁料消耗,是入炉料计算,实际企业计算时,炼钢厂内部回收的废钢都被扣除了.二.钢铁料耗构成1.投入的铁料量由于考虑理论与实际投入的铁量之间的差异,实际生铁、废钢铁量,但是冶炼过程加入的含铁物质如烧结矿、生矿、合金等含铁物质对钢铁料耗的降低是有贡献,贡献的大小是可以计算的;所以在条件允许下,可以多消化烧结矿、生矿等含铁物质,根据资料有关厂家吨钢消化生矿达到60kg,对钢铁料耗贡献大.2. 生产的合格钢坯:依据规定,参与计算的是转炉(电炉)生产合格钢坯量;三.钢铁料耗影响:1. 内部(工艺技术、管理等)影响因素(1)转炉炉前吹损转炉炉前吹损包括生铁和废钢的化学损失,烟尘损失,渣中氧化损失,渣中铁珠损失,喷溅损失,依据理论和首钢、武钢、马钢等公司转炉生产的实践经验转炉炉前吹损约为7.38~11.72%。
钢厂常用的计算公式

钢厂常用的计算公式钢厂是生产钢材的重要工业基地,其中涉及到许多计算公式用于生产和管理过程。
本文将介绍钢厂常用的计算公式,包括原料配比计算、熔炼温度计算、能耗计算等方面。
1. 原料配比计算。
原料配比是钢厂生产中非常重要的一环,它直接影响到钢材的质量和成本。
在原料配比计算中,通常会涉及到焦炭、铁矿石、废钢等原料的配比比例。
其中,焦炭的配比计算公式为:焦炭配比 = (理论焦比现场焦比)/(理论焦比实际焦比)。
其中,理论焦比是根据原料成分计算出来的理论值,现场焦比是实际生产中的焦比,实际焦比是实际生产中的焦比。
通过这个公式,可以调整焦炭的配比比例,以达到最佳的生产效果。
2. 熔炼温度计算。
熔炼温度是指在钢厂生产过程中,将原料加热至熔化状态所需要的温度。
熔炼温度的计算公式为:熔炼温度 = (熔点起始温度)/ 加热速率。
其中,熔点是原料的熔点,起始温度是原料的初始温度,加热速率是加热过程中的温度变化速率。
通过这个公式,可以计算出加热原料所需要的时间和能量,从而合理安排生产计划。
3. 能耗计算。
在钢厂生产中,能耗是一个非常重要的指标,直接关系到生产成本和环保效益。
能耗的计算公式为:能耗 = 电力消耗 + 燃料消耗。
其中,电力消耗是指生产过程中所消耗的电能,燃料消耗是指生产过程中所消耗的燃料。
通过这个公式,可以计算出每吨钢材的能耗,从而评估生产效率和成本。
4. 产量计算。
产量是衡量钢厂生产效率的重要指标,它直接关系到钢厂的经济效益和市场竞争力。
产量的计算公式为:产量 = 原料消耗废料产出。
其中,原料消耗是指生产过程中所消耗的原料,废料产出是指生产过程中所产生的废料。
通过这个公式,可以计算出每天、每月或每年的产量,从而评估生产效率和成本。
5. 质量损失计算。
质量损失是钢厂生产中不可避免的问题,它直接关系到产品质量和客户满意度。
质量损失的计算公式为:质量损失 = (原料消耗合格产品产出)/ 原料消耗。
其中,原料消耗是指生产过程中所消耗的原料,合格产品产出是指生产过程中所产生的合格产品。
钢铁料消耗计算
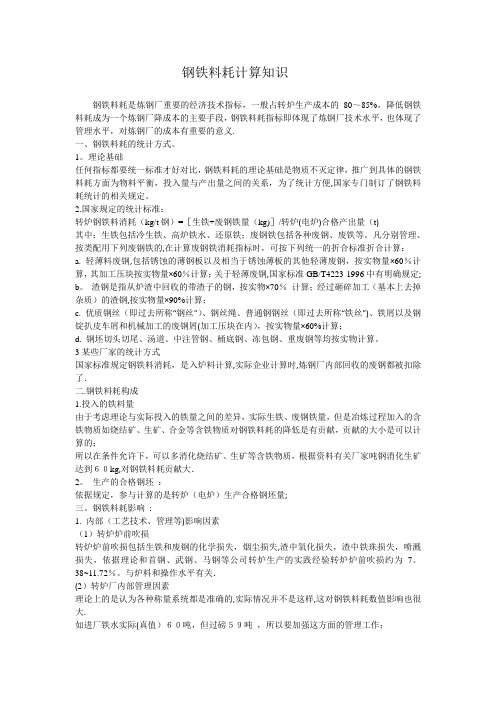
钢铁料耗计算知识钢铁料耗是炼钢厂重要的经济技术指标,一般占转炉生产成本的80~85%,降低钢铁料耗成为一个炼钢厂降成本的主要手段,钢铁料耗指标即体现了炼钢厂技术水平,也体现了管理水平,对炼钢厂的成本有重要的意义.一、钢铁料耗的统计方式。
1。
理论基础任何指标都要统一标准才好对比,钢铁料耗的理论基础是物质不灭定律,推广到具体的钢铁料耗方面为物料平衡,投入量与产出量之间的关系,为了统计方便,国家专门制订了钢铁料耗统计的相关规定。
2.国家规定的统计标准:转炉钢铁料消耗(kg/t钢)=[生铁+废钢铁量(kg)]/转炉(电炉)合格产出量(t)其中:生铁包括冷生铁、高炉铁水、还原铁;废钢铁包括各种废钢、废铁等。
凡分别管理、按类配用下列废钢铁的,在计算废钢铁消耗指标时,可按下列统一的折合标准折合计算:a. 轻薄料废钢,包括锈蚀的薄钢板以及相当于锈蚀薄板的其他轻薄废钢,按实物量×60%计算,其加工压块按实物量×60%计算;关于轻薄废钢,国家标准GB/T4223-1996中有明确规定; b。
渣钢是指从炉渣中回收的带渣子的钢,按实物×70%计算;经过砸碎加工(基本上去掉杂质)的渣钢,按实物量×90%计算;c. 优质钢丝(即过去所称“钢丝")、钢丝绳、普通钢钢丝(即过去所称“铁丝”)、铁屑以及钢锭扒皮车屑和机械加工的废钢屑(加工压块在内),按实物量×60%计算;d. 钢坯切头切尾、汤道、中注管钢、桶底钢、冻包钢、重废钢等均按实物计算。
3某些厂家的统计方式国家标准规定钢铁料消耗,是入炉料计算,实际企业计算时,炼钢厂内部回收的废钢都被扣除了.二.钢铁料耗构成1.投入的铁料量由于考虑理论与实际投入的铁量之间的差异,实际生铁、废钢铁量,但是冶炼过程加入的含铁物质如烧结矿、生矿、合金等含铁物质对钢铁料耗的降低是有贡献,贡献的大小是可以计算的;所以在条件允许下,可以多消化烧结矿、生矿等含铁物质,根据资料有关厂家吨钢消化生矿达到60kg,对钢铁料耗贡献大.2。
炼钢钢铁料消耗梳理
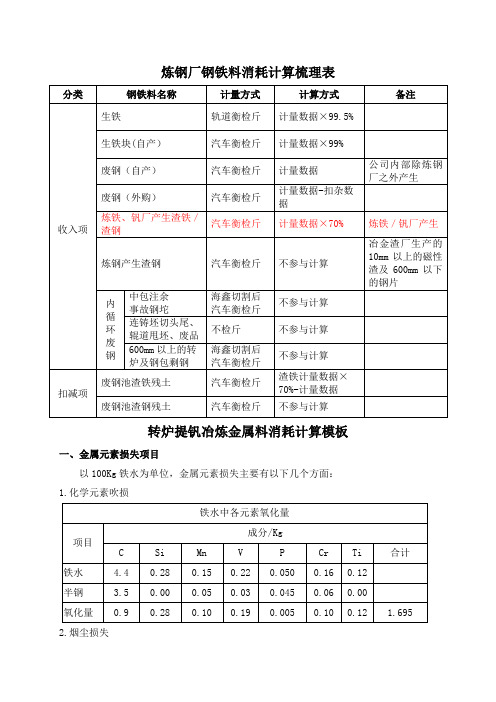
炼钢厂钢铁料消耗计算梳理表
转炉提钒冶炼金属料消耗计算模板一、金属元素损失项目
以100Kg铁水为单位,金属元素损失主要有以下几个方面:1.化学元素吹损
2.烟尘损失
烟尘量为铁水量的0.7%(借鉴承钢和承德建龙的经验数值),其中FeO为70%,Fe2O3为20%,则烟尘中的Fe损失:
100×0.7%×(70%×56/72+20%×112/160)=0.479Kg
3.钒渣中铁损失
钒渣中铁损失包括2部分,一是金属铁(铁珠),二是铁的氧化物。
金属铁占渣量的16%(YB/T008-2006 钒渣标准要求“金属铁≤19%”,同时借鉴承钢和承德建龙的经验数值),则金属铁损失:
100÷31×16%=0.516Kg。
铁的氧化物(FeO、Fe2O3)折合成TFe占渣量的30%(借鉴承钢和承德建龙的经验数值),则铁氧化物损失:
100÷31×30%=0.968Kg。
钒渣中铁损失合计:0.516Kg+0.968Kg=1.484Kg。
二、金属元素收入项目
使用TFe:60%的铁皮球作为冷却剂增加了金属元素的收得量,100Kg铁水使用铁皮球2.6Kg,则增加金属元素:2.6×60%=1.56Kg。
三、金属物料平衡表
计算转炉提钒冶炼金属料消耗:
100÷97.902=1021.4Kg/t
考虑高炉钒钛冶炼后铁水实际带渣量增加,转炉提钒冶炼金属料消耗适当增加2-4Kg/t。
拟定责任人:康建光
联系电话:137********
传达人员:李总、郭殿锋、曹凤胜、崔宝良、焦学义、王敏、黄正权、任凤博。
钢铁料消耗的合理测算与管理

图 2 2001 年全厂钢铁料消耗目标分解图
( 3) 把钢铁料消耗作为形象指标纳入各单位 经济责任制考核, 考核份额占到了各单位经济责 任制的 10% 。 ( 4) 强化钢铁料消耗的过程控制 , 做到按浇次 分析 , 天天分析 , 周周分析, 同时制定有针对性的 措施 , 月底由主管部门作全面详细分析。 ( 5) 定期召开降低钢铁料的专题研讨会和技 术经验交流, 集思广益, 群策群力。 ( 6) 稳定原料、 炼钢、 连铸工序的标准化操作, 大力开展职 工培训, 提高职工操作 水平, 减少漏 钢、 回炉、 断机等生产事故, 广泛开展 无漏钢、 无 回炉、 无断机!的 三无!劳动竞赛活动。 4. 2 技术攻关工作 ( 1) 铁水扒渣时防止带铁, 摇炉时防止泼铁。 ( 2) 铁水喷吹枪位适当 , 防止铁水喷溅。 4. 2. 2 炼钢 ( 1) 采用溅渣护炉技术 , 加强对炉体的维护, 控制好炉型 , 零位控制在 - 200 mm 以下, 前后大 24
Proper Calculation and Management on the Charging Material Consumption
Cheng Rui Li Xiaohu Zhao Zhongfu
( No. 1 Steelmaking Plant of WISCO Wuhan Hubei 430083)
3
钢铁料消耗的现状
2000 年我厂钢铁料消耗为 1 129. 33kg t , 与国
内同行业先进水平相比 , 还存在较大差距 , 因此, 有必要进一步采取切实可行的措施 , 严格管理, 合 理测算, 做到过程受控, 从而达到进一步降低钢铁 料消耗的目的。
武钢技术 2003 年第 41 卷第 4 期
钢铁料消耗计算

钢铁料耗计算知识钢铁料耗是炼钢厂重要的经济技术指标,一般占转炉生产成本的80~85%,降低钢铁料耗成为一个炼钢厂降成本的主要手段,钢铁料耗指标即体现了炼钢厂技术水平,也体现了管理水平,对炼钢厂的成本有重要的意义。
一、钢铁料耗的统计方式。
1. 理论基础任何指标都要统一标准才好对比,钢铁料耗的理论基础是物质不灭定律,推广到具体的钢铁料耗方面为物料平衡,投入量与产出量之间的关系,为了统计方便,国家专门制订了钢铁料耗统计的相关规定。
2. 国家规定的统计标准:转炉钢铁料消耗(kg/t钢)二[生铁+废钢铁量(kg)]/转炉(电炉)合格产出量(t)其中:生铁包括冷生铁、高炉铁水、还原铁;废钢铁包括各种废钢、废铁等。
凡分别管理、按类配用下列废钢铁的,在计算废钢铁消耗指标时,可按下列统一的折合标准折合计算:a.轻薄料废钢,包括锈蚀的薄钢板以及相当于锈蚀薄板的其他轻薄废钢,按实物量X60计算,其加工压块按实物量X60计算;关于轻薄废钢,国家标准GB/T4223-1996中有明确规定;b .渣钢是指从炉渣中回收的带渣子的钢,按实物X 70%计算;经过砸碎加工基本上去掉杂质)的渣钢,按实物量X 90%计算;C.优质钢丝(即过去所称钢丝”、钢丝绳、普通钢钢丝(即过去所称铁丝”)、铁屑以及钢锭扒皮车屑和机械加工的废钢屑(加工压块在内),按实物量X 60计算;d.钢坯切头切尾、汤道、中注管钢、桶底钢、冻包钢、重废钢等均按实物计算。
3 某些厂家的统计方式国家标准规定钢铁料消耗,是入炉料计算,实际企业计算时,炼钢厂内部回收的废钢都被扣除了.二.钢铁料耗构成1.投入的铁料量由于考虑理论与实际投入的铁量之间的差异,实际生铁、废钢铁量,但是冶炼过程加入的含铁物质如烧结矿、生矿、合金等含铁物质对钢铁料耗的降低是有贡献,贡献的大小是可以计算的;所以在条件允许下,可以多消化烧结矿、生矿等含铁物质,根据资料有关厂家吨钢消化生矿达到6 0 kg,对钢铁料耗贡献大.2.生产的合格钢坯:依据规定,参与计算的是转炉(电炉)生产合格钢坯量;三.钢铁料耗影响:1.内部(工艺技术、管理等)影响因素1)转炉炉前吹损转炉炉前吹损包括生铁和废钢的化学损失,烟尘损失,渣中氧化损失,渣中铁珠损失,喷溅损失,依据理论和首钢、武钢、马钢等公司转炉生产的实践经验转炉炉前吹损约为7.38~11."72%。
- 1、下载文档前请自行甄别文档内容的完整性,平台不提供额外的编辑、内容补充、找答案等附加服务。
- 2、"仅部分预览"的文档,不可在线预览部分如存在完整性等问题,可反馈申请退款(可完整预览的文档不适用该条件!)。
- 3、如文档侵犯您的权益,请联系客服反馈,我们会尽快为您处理(人工客服工作时间:9:00-18:30)。
钢铁料耗计算知识
钢铁料耗是炼钢厂重要的经济技术指标,一般占转炉生产成本的80~85%,降低钢铁料耗成为一个炼钢厂降成本的主要手段,钢铁料耗指标即体现了炼钢厂技术水平,也体现了管理水平,对炼钢厂的成本有重要的意义。
一、钢铁料耗的统计方式。
1.理论基础
任何指标都要统一标准才好对比,钢铁料耗的理论基础是物质不灭定律,推广到具体的钢铁料耗方面为物料平衡,投入量与产出量之间的关系,为了统计方便,国家专门制订了钢铁料耗统计的相关规定。
2.国家规定的统计标准:
转炉钢铁料消耗(kg/t钢)=[生铁+废钢铁量(kg)]/转炉(电炉)合格产出量(t)
其中:生铁包括冷生铁、高炉铁水、还原铁;废钢铁包括各种废钢、废铁等。
凡分别管理、按类配用下列废钢铁的,在计算废钢铁消耗指标时,可按下列统一的折合标准折合计算:a. 轻薄料废钢,包括锈蚀的薄钢板以及相当于锈蚀薄板的其他轻薄废钢,按实物量×60%计算,其加工压块按实物量×60%计算;关于轻薄废钢,国家标准GB/T4223-1996中有明确规定;
b. 渣钢是指从炉渣中回收的带渣子的钢,按实物×70% 计算;经过砸碎加工(基本上去掉杂质)的渣钢,按实物量×90%计算;
c. 优质钢丝(即过去所称“钢丝”)、钢丝绳、普通钢钢丝(即过去所称“铁丝”)、铁屑以及钢锭扒皮车屑和机械加工的废钢屑(加工压块在内),按实物量×60%计算;
d. 钢坯切头切尾、汤道、中注管钢、桶底钢、冻包钢、重废钢等均按实物计算。
3某些厂家的统计方式
国家标准规定钢铁料消耗,是入炉料计算,实际企业计算时,炼钢厂内部回收的废钢都被扣除了.
二.钢铁料耗构成
1.投入的铁料量
由于考虑理论与实际投入的铁量之间的差异,实际生铁、废钢铁量,但是冶炼过程加入的含铁物质如烧结矿、生矿、合金等含铁物质对钢铁料耗的降低是有贡献,贡献的大小是可以计算的;
所以在条件允许下,可以多消化烧结矿、生矿等含铁物质,根据资料有关厂家吨钢消化生矿达到60kg,对钢铁料耗贡献大.
2. 生产的合格钢坯:
依据规定,参与计算的是转炉(电炉)生产合格钢坯量;
三.钢铁料耗影响:
1. 内部(工艺技术、管理等)影响因素
(1)转炉炉前吹损
转炉炉前吹损包括生铁和废钢的化学损失,烟尘损失,渣中氧化损失,渣中铁珠损失,喷溅损失,依据理论和首钢、武钢、马钢等公司转炉生产的实践经验转炉炉前吹损约为7.38~11.72%。
与炉料和操作水平有关.
(2)转炉厂内部管理因素
理论上的是认为各种称量系统都是准确的,实际情况并不是这样,这对钢铁料耗数值影响也很大。
如进厂铁水实际(真值)60吨,但过磅59吨,所以要加强这方面的管理工作;
渣钢回收的回收管理工作特别重要,由于转炉冶炼操作的控制波动较大。
渣中含有大块和小块钢以及铁颗粒的回收对降低钢铁料耗指标有重要的影响,影响多大体现了管理水平的高低。
转炉厂钢水的流转工序管理,钢包的剩余钢水量、中包包底钢水量以及连浇炉数,连铸坯的定尺长度及割缝;生产事故和质量事故的金属损失等;
有些是转炉厂可以控制的如钢包的剩余钢水量、中包包底钢水量以及连浇炉数、连铸坯的割缝等,如连铸坯的定尺长度和钢种不能控制的,公司计划是什么就执行什么。
转炉厂钢坯出厂钢坯未计重量、支数的。
特别是出厂钢坯,若出厂时没有记数如10炉钢,有2支没记数,每支1.65吨
这对钢铁料耗的数值影响是很大的!
2.外部因素
(1)统计因素
根据国家规定的统计标准,a类、b类、c类在实践中比较难以区分,所以在选择折算系数时难以确定,对转炉的钢铁料耗也有较大的影响。
如一车60吨的小锣帽废钢,折算系数该怎么计。
(2)外部的称量系统因素
理论上称量系统是准确的,但在实际工作中不完全是这样的;若进入转炉的生铁、废钢铁量和出转炉的合格钢坯的称量系统出现系统误差,对钢铁料耗影响确实较大。
(3)原料因素
受高炉生产影响,铁水质量波动大如含Si 0.5%的铁水与Si 1.6%的铁水对转炉的钢铁料耗的影响是显著的;生铁块与废钢影响也是如此。
若有的钢厂铁水富余,全铁水炼钢,若含Si 0.5%的铁水与Si 1.6%的铁水,那钢铁料耗的数值影响5kg/t和16kg/t,可见钢铁料耗相差11kg/t。
(4)钢种的影响
由于合金在计算钢铁料耗时,投入项不计合金量的
而在计算合格产出量时,合金参与了合格产出量的计算,所以合金对钢铁料耗有影响,有时还特别大!!!
案例分析(为了分析便于的问题)
以某钢厂生产60Si2Mn和20MnSi钢的生产为例,进行钢铁料耗的分析。
炼钢终点控制一致,入炉原料基本相似。
1.基础数据
铁水65t,生铁10t,废钢5t,根据理论和实践经验转炉吹损8~12%,为计算选8.8%;60Si2Mn 的合金FeMnSi加入0.775t,FeSi加入1.580t,铸坯收得率99.75%;20MnSi的合金FeMnSi 加入1.10t,FeSi加入0.12t, 铸坯收得率99.73%;合金全部加入钢水中它重量的回收经理论和生产实践92%计;
2.投入铁料量
铁水65t +生铁10t +废钢5t =80 t
3. 收得铁料量
60Si2Mn钢合格钢坯:[80×(1-8.8%)+(0.775+1.58)×92%]×99.75%=74.75t
20MnSi钢合格钢坯:[80×(1-8.8%)+(1.10+0.12)×92%]×99.73%=73.88t
4. 计算钢铁料耗(按国家规定公式)
60Si2Mn钢铁料耗=80/74.75×1000=1070.23kg/t
20MnSi钢铁料耗=80/73.88×1000=1082.8kg/t
生产60Si2Mn和20MnSi钢的案例对入炉金属料的废钢折算系数没有考虑,实际操作中是有废钢折算系数,考虑分析问题原因未考虑;
从上面可以看出转炉炉前对钢铁料耗影响约90kg/t,所以炉前的操作控制显得特别重要,减少炉前的喷溅等事故。
有的恶性喷溅事故,金属料损失严重。
每喷溅一次损失金属料有的2t多(70t转炉)。
不同的钢种,由于合金加入量的不同,对钢铁料耗的贡献也不同,合金加入量大,对钢铁料耗的贡献也大,因此生产不同的钢种要考虑不同的钢铁料耗指标;铸坯收得率收得率钢包残钢量、连浇炉数、中包残钢量、铸坯定尺长度、铸坯割缝、头坯量和尾坯量等影响,
所以以上每个环节都要在满足质量的条件下严格控制,精细化管理;加大炼钢厂内部废钢的回收,对钢铁料耗有重大贡献。