甲烷化催化剂还原方案模板
甲烷转化催化剂升温还原技术要求

转化催化剂升温还原技术要求(换热转化)四川天一科技股份有限公司2012年2月转化催化剂升温还原技术要求“技术要求”是根据转化催化剂的实际要求编写的,不涉及工厂具体的操作步骤及操作细节如阀门的动作等。
操作应以工程设计文本为准。
“技术要求”所叙述的是工厂在转化工段进行催化剂装填、烘炉、用惰性气体置换系统后所进行的转化催化剂的升温、还原、放硫等化工单元操作要点。
“技术要求”中所列的升温速度是根据装置在原始开车时耐火材料及设备的要求而制定的。
转化催化剂对升温速度无特殊要求。
重复开车时,可采用快速升温还原方案。
一、一、转化催化剂的升温1.1. 空气升温一、二段转化催化剂升温可采用氮气和空气作为介质。
当采用空气作为加热介质时,应注意控制升温速度及终点温度。
在转化系统通入空气后、缓慢地将催化剂床层由常温提高到200℃。
不得超过200℃。
转化催化剂是以金属镍为活性组分的。
因为镍再氧化时放出的热量会使催化剂的温度升高到足以使催化剂熔融或使容器损坏的程度。
因为镍催化剂不得在200℃以上温度与空气接触。
原始开车时已处于氧化状态的转化催化剂采用空气升温,终点可为200℃。
2. 蒸汽升温(1)(1)目的以蒸汽为介质,将一、二段转化催化剂床层温度升高到650℃~700℃左右,同时将一、二段炉顶部和上部温度升高,为二段炉导入空气创造条件。
(2)(2)升温速度催化剂床层从200℃—500℃ 30℃/小时500℃—700℃ 50℃/小时(3)(3)蒸汽升温注意事项①需待转化炉出口温度高于当时压力下蒸汽露点30℃,才能将空气升温切换为蒸汽升温,防止因蒸汽冷凝而损坏催化剂。
②蒸汽已作为加热介质后,需注意系统低点导淋及时排除冷凝水。
③在切换过程中,要减少温度和压力波动,以保持蒸汽不冷凝。
④在蒸汽升温过程中,如原料气供应不具备或因任何原因引起的工程不能进入转化催化剂还原阶段,则升温速度要减慢、控制转化出口温度不超过500℃。
避免因在高温、水蒸汽条件下停留时间过长引起催化剂床层局部超温而使催化剂部分失活。
煤制气甲烷化催化剂两段式升温还原方法

煤制气甲烷化催化剂两段式升温还原方法宋鹏飞;姚辉超;侯建国;王秀林;高振;张瑜;穆翔宇【摘要】煤制天然气甲烷化工艺复杂,一般工艺通常需要6个或更多的反应器,开车前对系统升温和催化剂还原耗时较长,存在前几塔已经还原完成但后几塔还原还不充分的情况,且过程中需要高纯氮做载体,还原过程中的连续放空造成高纯氮大量浪费.提出了采用分段升温、分段还原、再整体升温的方法,充分利用原料气中的还原性气体(H2、CO)作为催化剂的还原气,有效降低高纯氮的放空量,提高还原效率,缩短催化剂升温、还原耗时.【期刊名称】《天然气化工》【年(卷),期】2015(040)006【总页数】3页(P69-71)【关键词】甲烷化;催化剂;还原升温;煤制天然气【作者】宋鹏飞;姚辉超;侯建国;王秀林;高振;张瑜;穆翔宇【作者单位】中海石油气电集团技术研发中心,北京100007;中海石油气电集团技术研发中心,北京100007;中海石油气电集团技术研发中心,北京100007;中海石油气电集团技术研发中心,北京100007;中海石油气电集团技术研发中心,北京100007;中海石油气电集团技术研发中心,北京100007;中海石油气电集团技术研发中心,北京100007【正文语种】中文【中图分类】TQ426;TQ221.11我国为全球头号能源消费国,一次能源消费结构中煤炭的比重接近70%[1]。
而同时我国天然气产量严重不足,对外依存度不断增加,预计2020年将达到37%[2]。
发展煤制天然气符合我国自身资源禀赋的特定条件,与进口气相比具有经济性,作为天然气需求的重要补充在我国能源战略中有重要地位[3-4]。
高温甲烷化是煤制天然气过程中最为关键的技术之一[5]。
目前国外有丹麦的托普索(Topsoe)公司、德国的鲁奇公司、英国的Davy公司、美国的巨点能源公司,国内有西南化工研究设计院有限公司和中海石油气电集团有限责任公司、中科院大连化物所等单位能提供高温甲烷化的成套技术[6-7]。
甲烷化催化剂升温还原方案

鸿基焦化合成车间甲烷化催化剂升温还原方案编写:审核:审定调度部:生产部:设备部:审批技术总监:设备总监生产总监:批准:批准时间:年月日实施时间:年月日一编写依据:合成车间脱碳、甲烷化岗位最终设计方案。
二编制目的及预期目标:甲烷化催化剂厂家是以氧化态形式提供的,氧化态的甲烷化催化剂不具有还原性,只有用H2或CO,对氧化态的甲烷化催化剂进行还原,才具有活性。
为了还原完全、并获得较大的活性镍面积,就必须很好的控制还原过程的温度。
因此必须严格按要求进行还原,以达到最好的还原效果。
三主要内容:(一)升温还原前的准备工作1、确认转化工段开工氮气系统已正常运行。
2、确认R-0801催化剂装填工作已全部结束,处于充氮保护状态。
3、温度计、压力计、联锁等各种仪表均校验合格待用。
4、脱碳系统运行正常。
(二)利用开工氮气循环回路进行升温1、抽去开工氮气管线上两盲板,法兰复位。
2、确认甲烷化系统入口切断阀XV-0702及其旁路阀关闭。
3、确认最终分离器液位调节阀LV-0801及其旁路阀、导淋关闭。
4、确认甲烷化系统出口切断阀HV-0801及其旁路阀关闭。
5、确认PV-0801及其及其旁路阀、导淋关闭。
6、联系调度、转化工段,送开工氮气,氮气循环流量18000m3/h,压力0.7Pa;调整开工氮气温度使甲烷化炉入口温度TI-0805升温速率小于50℃/h;按甲烷化催化剂升温曲线升温至(小于250)℃。
(三)甲烷化催化剂还原1、打开最终冷却器E0801循环冷却水进出口阀,投用最终冷却器。
2、缓慢全开PV-0801,升温还原气改在此处放空;关闭开工氮气出口阀,盲板、法兰复位。
3、现场打开甲烷化入口切断阀XV-0702前导淋,无积水后关闭导淋;稍开XV-0702旁路阀,配入适量的脱碳净化气(CO<2%和CO2<0.3%)。
4、用TIC-0805调节甲烷化炉入口净化气的温度,按甲烷化催化剂升温还原曲线进行还原操作。
5、甲烷化系统升温至300℃时,系统中开始有CO2放出最高可达4%左右,此时加大氮气循环量,待化验分析CO2≤1%时,减少氮气循环量至正常升温时的量。
甲烷化操作实操

1、甲烷合成反应器的反应机理?在甲烷化反应器中主要进行的是甲烷的合成反应,即一氧化碳、二氧化碳与氢在催化剂的作用下转化成甲烷。
甲烷合成反应是个强放热反应,伴随甲烷合成反应同时还发生了一氧化碳的氧化还原。
总反应方程式如下:CO + 3H2 = CH4 + H2OCO2 + 4H2 = CH4 + 2H2OCO + H2O = CO2 + H22.在氨厂典型的甲烷化炉操作条件下,毎1%CO转化的绝热温升为72℃,每1%CO2转化的绝热温升60℃,反应炉的总温升可由下式计算:ΔT=72╳[CO]入+60╳[CO2]入式中:ΔT----分别为进口气中CO、CO2的含量,%(体积分数)3甲烷化设备主要有哪些?甲烷化设备主要有硫吸收器、甲烷化反应器、高压废热锅炉、低压废热锅炉、甲烷化换热器、高压蒸汽过热器、开车加热器、循环压缩机、水冷器、水分离器等设备。
4、甲烷化催化剂的组成及主要组分的作用是什么?甲烷化催化剂是以镍为活性组分在载体上,为获得催化剂的活性和热稳定性有添加了一些促进剂。
主要组分有Ni、Al2O3、MgO、Re2O3等Al2O3是一种普遍使用的载体。
Al2O3具有多种结构形态,用于甲烷化的是具有大孔的Al2O3。
MgO是一种良好的的结构稳定剂。
Re2O3为稀土氧化物,具有良好的活性与稳定性。
5、为什么要对甲烷化催化剂进行还原?还原过过程中有哪些化学反应?①甲烷化催化剂使用前,是以镍(Ni)的氧化物形式纯在,所以使用时,必须还原活化。
在还原剂(H2、CO)被氧化的同时,多组分催化剂中的NiO被还原具有活性的金属镍(Ni),并在还原过程中形成了催化剂的孔道。
而Al2O3不会被还原,起着间接支持催化剂结构的助构作用,使镍处于均匀分散的微晶状态,使催化剂具有较大的比表面、较高的活性和稳定性。
②甲烷化催化剂还原时发生如下反应:NiO + H2 = Ni + H2O - 2.55KJ/molNiO + CO = Ni + CO2 - 30.25 KJ/mol这些都不是强放热反应,还原过程本身不会引起催化剂床层大的温升。
甲烷化技术及催化剂

甲烷化技术及催化剂甲烷化就是利用催化剂使一氧化碳和二氧化碳加氢转化为甲烷的方法,此法可以将碳氧化物降低到10ppm以下,但需要消耗氢气。
一、加氢反应CO+3H2=CH4+H2O+206.16KJCO2+4H2=CH4+2H2O+165.08KJ此反应为强放热反应,有氧气存在时,氧气和氢气反应会生成水,在温度低于200℃,甲烷化催化剂中的镍会和CO反应生成羰基镍:Ni+4CO=Ni(CO)4因此要避免低温下,CO和镍催化剂的接触,以免影响催化剂的活性。
甲烷化的反应平衡常数随温度增加而下降,作为净化脱除CO和CO2作用的甲烷化技术,反应温度一般在280~420℃之间,平衡常数值都很大,在400℃、2.53Mpa压力下,计算CO和CO2的平衡含量都在10-4ppm级。
湖南安淳公司开发的甲烷化催化剂起活温度210℃,使用温度为220~430℃之间。
进口温度增加,催化剂用量减少,压降和功耗有较大的降低。
这部分技术在国内已经非常成熟,而且应用多年。
目前,甲烷化技术已经用在大规模的合成气制天然气上,因此最大的问题是催化剂的耐温及强放热反应器的设计制作上。
二、甲烷化催化剂甲烷化是甲烷蒸汽转化的逆反应,因此甲烷化反应的催化剂和蒸汽转化催化剂一样,都是以镍作为活性组分,但是甲烷化反应在温度更低的情况下进行,催化剂需要更高的活性。
为满足上述需要,甲烷化催化剂的镍含量更高,通常为15~35%(镍),有时还需要加入稀土元素作为促进剂,为了使催化剂能承受更高的温升,镍通常使用耐火材料作为载体,且都是以氧化镍的形态存在,催化剂可压片或做成球形,粒度在4~6mm之间。
催化剂的载体一般选用AI2O3、MgO、TiO、SiO2等,一般通过浸渍或共沉淀等方法负载在氧化物表面,再经焙烧、还原制得。
其活性顺序为:Ni/MgO<Ni/AI2O3<Ni/SiO2<Ni/TiO2<Ni/ZrO2稀土在甲烷化催化剂中的作用主要表现在:提高催化剂活性和稳定性、抗积炭性能好、提高了催化剂耐硫性能。
DTC合成气甲烷化催化剂工业预还原条件研究

当代化工研究[()Modern Chemical Research丄,2020•22基础研究DTC合成气甲烷化催化剂工业预还原条件研究*于博文(大唐国际化工技术研究院有限公司北京100064)摘耍:大唐国际化工技术研究院有限公司自主研发丝DTC系列合成气甲烷化催化剂首次实现国产催化剂在大型煤制气甲烷化装置工业应用.本文总结了DTC系列合成气甲烷化催化剂预还原条件的放大优化过程,并对工业预还原催化剂产話主要指标进行检测评价,结果表明优化后的预还原操作可以满足稳定的工业化生产需要.关键词:合成气甲烷化;工业预还原;优化;检测评价中阖分类号:TQ文献标识码:AResearch on Industrial Pre-reduction Conditions of DTC Syngas Methanation CatalystYu Bowen(Datang International Chemical Technology Research Institute Co.,Ltd.,Beijing,100064) Abstracts DTC series synthesis gas,methanation catalyst,independently developed by Datang International Chemical Technology Research Institute Co.,Ltd.has realized the industrial application of d omestic catalyst in large-scale coal-to-gas methanation plant f or the f irst time.In this paper,the enlargement optimization p rocess of p re-reduction conditions ofDTC series synthesis gas methanation catalysts is summarized,and the main indexes of i ndustrial p re-reduction catalysts are tested and evaluated.The results show that the optimized p re-reduction operation can meet the needs of s table industrial p roduction.Key words:methanation of s yngas\industrial p re-reduction;optimization^detection and evaluation我国资源禀赋为“富煤、贫油、少气”,随着社会经济发展,环保理念深入人心,“煤改气”“蓝天保卫战”持续推进,我国天然气需求量不断增加,对外依存度持续上升。
甲烷化预还原方案
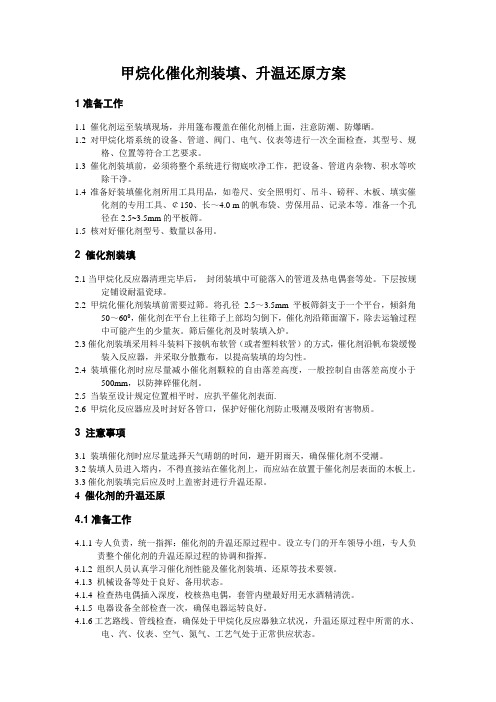
甲烷化催化剂装填、升温还原方案1准备工作1.1 催化剂运至装填现场,并用篷布覆盖在催化剂桶上面,注意防潮、防爆晒。
1.2 对甲烷化塔系统的设备、管道、阀门、电气、仪表等进行一次全面检查,其型号、规格、位置等符合工艺要求。
1.3 催化剂装填前,必须将整个系统进行彻底吹净工作,把设备、管道内杂物、积水等吹除干净。
1.4 准备好装填催化剂所用工具用品,如卷尺、安全照明灯、吊斗、磅秤、木板、填实催化剂的专用工具、¢150、长~4.0 m的帆布袋、劳保用品、记录本等。
准备一个孔径在2.5~3.5mm的平板筛。
1.5 核对好催化剂型号、数量以备用。
2 催化剂装填2.1当甲烷化反应器清理完毕后,封闭装填中可能落入的管道及热电偶套等处。
下层按规定铺设耐温瓷球。
2.2 甲烷化催化剂装填前需要过筛。
将孔径2.5~3.5mm平板筛斜支于一个平台,倾斜角50~600,催化剂在平台上往筛子上部均匀倒下,催化剂沿筛面溜下,除去运输过程中可能产生的少量灰。
筛后催化剂及时装填入炉。
2.3催化剂装填采用料斗装料下接帆布软管(或者塑料软管)的方式,催化剂沿帆布袋缓慢装入反应器,并采取分散撒布,以提高装填的均匀性。
2.4 装填催化剂时应尽量减小催化剂颗粒的自由落差高度,一般控制自由落差高度小于500mm,以防摔碎催化剂。
2.5 当装至设计规定位置相平时,应扒平催化剂表面.2.6 甲烷化反应器应及时封好各管口,保护好催化剂防止吸潮及吸附有害物质。
3 注意事项3.1 装填催化剂时应尽量选择天气晴朗的时间,避开阴雨天,确保催化剂不受潮。
3.2装填人员进入塔内,不得直接站在催化剂上,而应站在放置于催化剂层表面的木板上。
3.3催化剂装填完后应及时上盖密封进行升温还原。
4 催化剂的升温还原4.1准备工作4.1.1专人负责,统一指挥:催化剂的升温还原过程中。
设立专门的开车领导小组,专人负责整个催化剂的升温还原过程的协调和指挥。
4.1.2 组织人员认真学习催化剂性能及催化剂装填、还原等技术要领。
- 1、下载文档前请自行甄别文档内容的完整性,平台不提供额外的编辑、内容补充、找答案等附加服务。
- 2、"仅部分预览"的文档,不可在线预览部分如存在完整性等问题,可反馈申请退款(可完整预览的文档不适用该条件!)。
- 3、如文档侵犯您的权益,请联系客服反馈,我们会尽快为您处理(人工客服工作时间:9:00-18:30)。
J108-2Q型高压甲烷化催化剂装填和升温还原方案
编制: 严会成
复核: 王灵翼
审批: 杨典明
四川亚连凯特化工有限公司
二O一三年四月
J108-2Q中高压甲烷化催化剂装填、还原方案
一、装填前的准备工作:
1、对中高压甲烷化系统的管道、设备、阀门、仪表、电炉等设备作一次全面检查, 还原气体的组分含量、各个参数都必须符合还原条件。
2、催化剂没有装填前要注意防雨、防水。
3、准备充分的Φ10~15能够耐高温的氧化铝球或钢球。
4、准备好吊斗、筛子( 掉到地上的催化剂必须经过筛选后再装填) 、磅秤、帆布袋( 或消防软管) 、记录工具、卷尺、搗棍等。
5、吹净设备以及管道内的积水、灰尘、油污等杂质, 特别是铁屑, 是生成高级烃类的物质。
二、催化剂装填
装填原则: 如果是轴径向塔形在装填之前最好将每一层的分气盒吊出塔外( 具体咨询内件厂家相关技术人员) , 并保证每一层装填密实, 以免造成床层下沉过大和气流分布不均。
1.在进行催化剂装填之前, 应仔细检查甲烷化塔, 保证无一切杂物。
2.一般甲烷化催化剂在装填之前应过筛, 因在运输过程中难免会出现粉尘和碎片, 因而在装填前须用8~10目的筛网进行过筛, 本催化剂由于采用了静态生产工艺, 粉尘和碎片少, 从带孔的
溜槽溜过即可。
3.催化剂床层上下部分均须装耐火球( Φ10~15) , 耐火球装填高度应以我公司现场人员和内件厂家现场服务人员共同确定, 一般100mm左右。
耐火球和催化剂层之间用不锈钢丝网隔开。
装填时催化剂自由下落高度不应大于0.5米, 同时不应将催化剂从某一位置倒进塔内堆成一堆后再扒平, 防止小粒度和粉尘留在堆中心, 而较大颗粒滚向边缘, 导致气体分布不均匀。
可用帆布袋或消防软管作引流管。
4.操作人员进入甲烷化炉内时, 应带上防尘口罩, 踏在铺好的木板上, 切勿直接踩踏催化剂。
5.记录好装填的催化剂重量、体积、装填高度以及热电偶相应位置等。
6.热电偶在装进去前要用棉布擦干里面的水, 以免还原过程温度升到100度左右时, 水气升凝而导致热点偶温度显示不准确。
三、还原前的准备工作:
1、装填结束后, 对系统进行吹扫。
一般厂家新的催化剂能够用高压甲醇的醇后气或精炼气吹扫、置换及升温还原。
2、检查循环机、水泠器、温度计、热电偶、电炉等设备和仪表是否正常。
3、系统充压5.0MPa后启用循环机, 循环机在启用后, 对循
环机排水、排油后甲烷化炉才开始进还原气, 检查电炉绝缘及调压器正常。
4、在升温还原过程中, 当床层温度达到150℃后, 现场操作人员做到每半个小时排水一次, 水不计量。
四、催化剂的升温、还原
J108-2Q甲烷化催化剂的还原介质: 高压甲醇醇后气或者精炼气升温还原。
气质要求: O2≤0.2%、S≤0.1ppm、Cl≤0.03ppm、CO+CO2≤0.7%、H2≥70%, 在电炉功率足够大的情况下, 还原空速最好控制: ≥ h-1。
J108-2Q甲烷化催化剂还原开始温度可控制在200~250℃, 按升温还原方案中的升温速度逐渐提温至正常还原温度450℃。
还原过程本身不会引起催化剂床层大幅度温升, 如采用工艺气进行还原, 当生成一些金属镍后便开始甲烷化反应, 因此还原所用的气体中要求一氧化碳和二氧化碳的总含量应尽可能低, 控制在CO+CO2≤0.7%, 在特殊条件下, 如受热源限制, 甲烷化炉进口温度只能达到300~320℃, 则能够适当提高进口CO+CO2的含量, 利用CO和CO2的甲烷化反应热来提高催化剂床层温度, 但这一操作必须严格控制, 以防催化剂床层温度暴升, 如电炉功率小不能提温到450℃, 也可在后期适当减小空速, 直到温度达到450℃以上。