alinco dr620 维修手册 英文版
InRow RC维修手册

设置常规配置 . . . . . . . . . . . . . . . . . . . . . . . . . . . . . . . . . . . . . . . . . . . . 11
制冷单元配置 . . . . . . . . . . . . . . . . . . . . . . . . . . . . . . . . . . . . . . . 11
运行和维护
InRow®RC
ACRC100 ACRC103
This manual is available in English on the enclosed CD. Dieses Handbuch ist in Deutsch auf der beiliegenden CD-ROM verfügbar. Deze handleiding staat in het Nederlands op de bijgevoegde cd. Este manual está disponible en español en el CD-ROM adjunto. Ce manuel est disponible en français sur le CD-ROM ci-inclus. Questo manuale è disponibile in italiano nel CD-ROM allegato. 本マニュアルの日本語版は同梱の CD-ROM からご覧になれます。 Instrukcja Obsługi w jezyku polskim jest dostepna na CD. O manual em Português está disponível no CD-ROM em anexo. Данное руководство на русском языке имеется на прилагаемом компакт-диске. 您可以从包含的 CD 上获得本手册的中文版本。 您可以从附属的CD上获得本手册的中文版本。
力帆620汽车原厂维修手册

目录一、概述 (1)1.1 RDC15-FA剖面结构及调整垫片位置 (1)1.2 RDC15-FA传动原理简图 (2)1.3 RDC15-FA的动力传动路线 (3)1.4 RDC15-FA功能概述 (4)1.5 RDC15-FA各机构概述 (5)1.5.1 1.5.2 1.5.3 1.5.4 液力变矩器 (5)油泵 (6)无级变速机构 (7)推力钢带 (8)1.5.5 P档锁止机构 (8)1.5.6 1.5.7 中间减速单元 (9)换向机构(前进/倒档机构) (9)1.6液压系统 (11)1.6.1 1.6.2 1.6.3 液压控制线路 (11)档位控制实现 (11)锁止离合器 (12)1.7电控系统 (13)1.7.1 简介 (13)1.7.2 TCU输入/输出信号参考值 (14)1.7.3 RDC15-FA布线图 (16)注意事项 (18)二、故障诊断 (19)2.1“安全-失效”模式功能介绍 (19)2.2故障诊断说明 (20)2.3故障诊断前的检查与测试 (25)2.3.1 2.3.2 2.3.3 油液检查与更换 (25)失速测试 (26)管路压力测试 (26)2.4路试 (27)2.4.1 2.4.2 2.4.3 发动机启动前的检查 (30)怠速检查 (30)巡航测试 (32)2.5症状的故障诊断 (34)2.5.1 2.5.2 2.5.3 2.5.4 仪表盘档位显示灯不亮或显示不正确 (34)操纵杆面板指示灯不亮 (36)发动机在P或N档不能起动 (37)换档杆在P档时,能推动车辆前后移动 (37)2.5.5换档杆在N 档时车辆能够移动......................................... 38 巨大冲击N →R ,N →D 档.............................................. 38 换档杆在R 档时,车辆不能倒车....................................... 39 换档杆在D 、L 档时,车辆不能向前行驶................................ 40 车速在L 档不发生变化............................................... 41 车速在动力模式下不发生变化........................................ 42 车速在D 档不发生变化.............................................. 43 发动机制动无法让车辆减速.......................................... 44 车速在手动模式加速挡不发生变化.................................... 46 车速在手动模式减速挡不发生变化.................................... 47 挡位在P 、R 挡时不能换挡. (48)挡位在R 挡时倒车灯不亮 (49)2.5.62.5.72.5.82.5.92.5.102.5.112.5.122.5.132.5.142.5.152.5.16 2.6故障代码 (51)2.6.1 诊断仪参考值 (51)故障代码列表 (52)2.6.2 三、RDC15-FA 总成拆解 (53)四、RDC15-FA 组件检修与装配 (59)4.1前壳体 (59)检修 (60)装配 (62)4.2中间轴 (64)检修 (65)装配 (66)4.3输入轴 (67)检修 (68)装配 (71)4.4中壳体 (74)检修 (75)4.5主动轴 (81)检修 (82)装配 (84)4.6被动轴 (85)检修 (86)装配 (86)4.7后壳体 (88)检修 (89)装配 (91)五、RDC15-FA 总成装配 (93)附录 (102)专用维修工具 (102)通用维修工具 (105)概述一、概述1.1 RDC15-FA剖面结构及调整垫片位置28 9131011 C546 12A 71.2 RDC15-FA传动原理简图RDC15-FA各部件的相互作关系1、液力变矩器2、油泵5、太阳轮6、行星轮7、齿圈9、主动带轮轴10、从动带轮轴11、金属带3、输入轴4、前进档离合器8、倒档离合器12、驻车制动抓各部件主要功能:部件功能液力变矩器连接发动机与油泵,传递发动机动力;实现汽车的平稳起步;当车辆低速行驶或行驶阻力增大时,实现增扭降速;当车辆高速行驶或行驶阻力减少时,实现“闭锁”,整个液力变矩器形成一个同轴转动刚体油泵为液压系统提供液压油源输入轴将液力变矩器输入动力传递给行星架前进档离合器太阳轮结合/分离行星架与太阳轮的联结,实现正向行驶功能将输入动力传递给主动带轮轴倒档制动器金属带制动/脱开齿圈与壳体的联结,实现倒档功能将输入动力传递给从动带轮轴,实现速比连续变化汽车挂入P档时,阻止从动带轮转动P档制动抓1.3 RDC15-FA的动力传动路线导轮涡轮泵轮闭锁离合器液力变矩器总成主减速器RDC15-FA的动力传动路线RDC15-FA的传动路线如图所示。
索拉尔顿系列汽车维修指南说明书

AccessoriesInstallation.................................... 99ACCESSORY (Ignition KeyPosition)........................................ 45AddingAutomatic TransmissionFluid........................................ 145Brake Fluid................................. 147Clutch Fluid................................ 148Engine Coolant........................... 139Engine Oil................................... 134Manual Transmission Fluid ..... 146Power Steering Fluid................. 148Windshield Washer Fluid......... 144Additional Safety Information........ 16Door Locks................................... 17Driving with Pets......................... 17Head Restraint Position.............. 16Seat-back Position........................ 16Storing Cargo Safely................... 17Additives, Engine Oil..................... 136AdjustmentsHeadlights.................................. 165Head Restraints (51)Mirrors.......................................... 55Seats.............................................. 49Steering Wheel............................ 40Airbag (SRS).................................... 10Air Cleaner Element...................... 149Air Conditioning............................... 64Maintenance............................... 157Usage............................................. 64Air Outlets (Vents).......................... 66Air Pressure, Tires........................ 159Alcohol and Drugs........................... 24Alcohol in Gasoline.......................... 92Aluminum Wheels, Cleaning........ 177Antenna, Cleaning......................... 176Antifreeze....................................... 139Anti-lock Brakes (ABS)Indicator Light.................... 31, 114Operation.................................... 112Anti-theft Steering Column Lock .. 45Appearance Care........................... 175Ashtrays............................................ 60Audio System................................... 72Automatic Speed Control................ 41Automatic Transmission............... 106Capacity, Fluid........................... 209Checking Fluid Level. (145)Shifting........................................ 106Shift Lever Positions................. 106Shift Lock Release (109)BatteryCharging SystemIndicator........................... 30, 196Jump Starting............................. 191Maintenance............................... 152Specifications............................. 209Before Driving................................. 91Belts, Seat........................................... 5Beverage Holder.............................. 58Body Repair (181)CONTINUEDBrakesAnti-lock System (ABS) (112)Break-in, New Linings (92)Fluid (146)Light, Burned-out (170)Parking (56)System Indicator (30)Wear Indicators (111)Brakes, ABSOperation (112)System Indicator................. 31, 114Braking System (111)Break-in, New Car (92)Brightness Control, Instruments (37)Brights, Headlights (36)Bulb ReplacementBack-up Lights (170)Brake Lights (170)Cargo Area Light (172)Ceiling Light (172)Front Parking Lights (168)Front Side Marker Lights (168)Headlights (167)High-mount Brake Light (169)License Plate Lights (172)Rear Side Marker Lights (170)Specifications (209)Spotlights (172)Turn Signal Lights (168)Bulbs, Halogen (167)Cables, Jump Starting With (191)Capacities Chart (208)Carbon Monoxide Hazard (25)Cargo Area Cover (52)Cargo, Loading (100)Cassette PlayerCare (88)Operation (85)CAUTION, Explanation of (ii)CD Changer (81)Certification Label (206)Chains (164)Change OilHow to (137)When to (128)Changing a Flat Tire (185)Changing Engine Coolant (141)Charging System Indicator ... 30, 196CheckingAutomatic TransmissionFluid (145)Battery Condition (152)Brake Fluid (146)Clutch Fluid (148)Drive Belts (158)Engine Coolant (139)Engine Oil (96)Fuses (200)Manual Transmission Fluid (146)Power Steering Fluid (148)Checklist, Before Driving (102)Child Safety (18)Cigarette Lighter (59)Cleaner, Air (149)CleaningAluminum Wheels (177)Antenna (176)Carpeting (178)Exterior (176)Fabric (178)Interior (178)Leather (178)Seat Belts (178)Vinyl............................................178CleaningWindows..................................... 179Clock, Setting the ............................ 57Clutch Fluid.................................... 148Code, Audio System........................ 89CO in the Exhaust......................... 213Cold Weather, Starting in............. 103Compact Spare............................... 184Console Compartment.................... 59Consumer Information*................ 218Controls, Instruments and.............. 27CoolantAdding.........................................139Checking..................................... 139Proper Solution.......................... 139Temperature Gauge.................... 33Corrosion Protection..................... 180Crankcase Emission ControlSystem......................................... 213Cruise Control Operation ............... 41Customer Relations Office.. (218)DANGER, Explanation of................. ii Dashboard. (28)Daytime Running Lights................. 36Dead Battery, What to Do............ 191Defects, Reporting Safety............. 219Defogger, Rear Window................. 39Defrosting the Windows................. 70DEXRON ® III AutomaticTransmission Fluid.................... 145Dimensions..................................... 208Dimming the Headlights................ 36DipstickAutomatic Transmission........... 145Engine Oil..................................... 96Directional Signals........................... 37Disabled, Towing Your Car If...... 204Disc Brake Wear Indicators......... 111Disposal of Used Oil...................... 138DoorsLocking and Unlocking............... 46Power Door Locks....................... 46DOT Tire Quality Grading........... 211Downshifting, 5-speed ManualTransmission.............................. 104Drive Belts...................................... 158Driving............................................ 101Economy....................................... 98In Bad Weather.. (115)In Foreign Countries (93)Economy, Fuel................................. 98Emergencies on the Road............. 183Battery, Jump Starting.............. 191Changing a Flat Tire................. 185Charging System Indicator...... 196Checking the Fuses................... 200Low Oil Pressure Indicator...... 195Malfunction Indicator Lamp .... 197Manually Closing Moonroof .... 198Overheated Engine................... 193Emergency Brake............................ 56Emergency Flashers....................... 39Emission Controls......................... 213EngineCoolant Temperature Gauge ..... 33Drive Belts.................................. 158Malfunction IndicatorLamp................................ 31, 197Oil Pressure Indicator........ 30, 195Oil, What Kind to Use (134)CONTINUEDEngineOverheating (194)Specifications (208)Ethanol in Gasoline (93)Evaporative Emission Controls (213)Exhaust Fumes (25)Expectant Mothers, Use ofSeat Belts by (9)Exterior, Cleaning the (176)Fabric, Cleaning (178)Fan, Interior (64)Features, Comfort andConvenience (63)Filling the Fuel Tank (94)Filters Air (149)Oil (137)First Gear, Shifting (108)5-speed Manual TransmissionChecking Fluid Level (146)Shifting the (104)Flashers, Hazard Warning (39)Flat Tire, Changing a (185)FluidsAutomatic Transmission (145)Brake (147)Clutch (148)Manual Transmission (146)Power Steering (148)Windshield Washer (144)FM Stereo RadioReception (72)Folding Rear Seat (52)Foreign Countries, Driving in (93)Four-way Flashers (39)Front End, Towing byEmergency Wrecker (204)Fuel (92)Fill Door and Cap (94)Gauge (33)Octane Requirement (92)Oxygenated (92)Reserve Indicator (31)Tank, Filling the (94)Fuses, Checking the (200)Gas Mileage, Improving (98)Gasohol (93)Gasoline (92)Fuel Reserve Indicator (31)Gauge (33)Octane Requirement (92)Tank, Filling the (94)Gas Station Procedures (94)GaugesEngine Coolant Temperature (33)Fuel (33)Gearshift Lever PositionsAutomatic Transmission (106)5-speed ManualTransmission (104)Glass Cleaning (179)Glove Box (48)Halogen Headlight Bulbs (167)Hatch (47)Opening the (47)Open Monitor Light....................31Hazard Warning Flashers (39)HeadlightsAiming (165)Daytime Running Lights (36)High Beam Indicator (31)High Beams, Turning on (36)Low Beams, Turning on (36)Reminder Chime (36)Replacing Halogen Bulbs (167)Turning on (36)Head Restraints (51)Heating and Cooling (64)High Altitude, Starting at (103)High-Low Beam Switch (36)Hood, Opening the (95)Horn (35)Hot Coolant, Warning about (139)Hydraulic Clutch (148)Hydroplaning (116)Identification Number, Vehicle (206)If Your Car Has to be Towed (204)IgnitionKeys (44)Switch (44)Timing Control System (214)Indicator Lights, InstrumentPanel (29)Infant Restraint (18)Inflation, Proper Tire (159)Inside Mirror (55)Inspection, Tire (160)Instrument Panel (28)Instrument Panel Brightness (37)Interior Cleaning (178)Interior Lights (61)Introduction (i)Jacking up the Car (187)Jack, Tire (186)Jump Starting (191)Keys (44)Label, Certification (206)Lane Change, Signaling (37)Lap/Shoulder Belts (6)Leaking of Exhaust into Car (25)Leather, Cleaning (178)Lighter, Cigarette (59)LightsBulb Replacement (167)Indicator (29)Parking (36)Turn Signal (37)Loading Cargo (100)LOCK (Ignition Key Position) (45)LocksAnti-theft Steering Column (45)Fuel Fill Door (94)Glove Box (48)Hatch (47)Power Door (46)Low Coolant Level (139)Lower Gear, Downshiftingto a (104)CONTINUED。
打印机维修手册:StylusPhotoRX600_RX610_RX620_RX630_C

PRECAUTIONS
SERVICE MANUAL
Scanner • Printer • Copier
EPSON Stylus PHOTO RX600/610 , RX620/630
SEOT03006
Notice:
All rights reserved. No part of this manual may be reproduced, stored in a retrieval system, or transmitted in any form or by any means, electronic, mechanical, photocopying, recording, or otherwise, without the prior written permission of SEIKO EPSON CORPORATIONEPSON PRODUCT SHOULD BE PERFORMED ONLY BY AN EPSON CERTIFIED REPAIR TECHNICIAN. 2. MAKE CERTAIN THAT THE SOURCE VOLTAGES IS THE SAME AS THE RATED VOLTAGE, LISTED ON THE SERIAL NUMBER/RATING
Precautionary notations throughout the text are categorized relative to 1)Personal injury and 2) damage to equipment.
中性620K新说明书英文

ShenzhouShante Uninterruptible Power System-UPSON LINE6K(S)/(S)/10K(S)10KS(3P)/15KS(3P)/20KS(3P)USER MANUALPlease comply with all warnings and operating Instructions in this manual and on the unit strictly. Save this manual properly. Do not operate this unit without reading thoroughly all safety information and operating instructions carefully.SEE INSTALLATION INSTRUCTIONSBEFORECONNECTING TO THE SUPPLYTable of contents1. Brief introductionSystem and model description (3)Description of commonly used symbols (4)Appearance (5)Product specification and performance………………………………………………….6-8●General specification●Electric performance●Operating environment2. InstallationUnpacking & Inspection (9)Input and output power chords and protective earth installation…………………….9-11 Operating procedure for connecting long backup time modelUPS with the external battery (12)Parallel operation (13)3. Operation and operating mode (14)mode……………………………………………………………………………15-184. Battery maintenance (18)5. Notes for battery disposal and battery replacement (19)6. Trouble shooting…………………………………………………………………………….20-21 Appendix 1 Display panel……………………………………………………………………22Appendix 2 The corresponding form of the LED display…………………………………23-24System and model descriptionThis Online Series is an uninterruptible power supply incorporating double-conversion technology. It provides perfect protection specifically for computer equipment communication Systems to computerized instruments.Its true online double-conversion design eliminates all mains power disturbances. A rectifier converts the alternating current from the utility power to direct current. This direct current charges the batteries and powers the inverter. On the basis of this DC voltage, the inverter generates a pure sinusoidal AC voltage, which is constantly powering the loads.Computers and Peripherals are thus powered entirely by the UPS. In the event of power failure, the maintenance-free batteries power the inverter.This manual is applicable to the following models:1) The CR6K is a standard model with inbuilt battery, hereinafter called 6K;2) The CR6KS is a long backup time model, which is able to connect with the externalbattery bank, hereinafter-called 6KS;3) The 3CR6K is a standard model with inbuilt battery, hereinafter called three-phase6K.4) The 3CR6KS is a three-phase input and single-phase output long backup time model,which is able to connect with the external battery bank. Hereinafter called three-phase 6KS.5) The is a standard model with inbuilt battery, hereinafter-called ;6) The is a long backup time model, which is able to connect with the external batterybank, hereinafter-called ;7) The is a standard model with inbuilt battery, hereinafter-called three-phase .8) The is a three-phase input and single-phase output long backup time model, whichis able to connect with the external battery bank. Hereinafter called three-phase .9) The CR10K is a standard model with inbuilt battery, hereinafter-called 10K;10) The CR10KS is a long backup time model, which is able to connect with the externalbattery bank, hereinafter-called10 KS;11) The 3CR10K is a standard model with inbuilt battery, hereinafter-called three-phase10K;12) The 3CR10KS is a three-phase input and single-phase output long backup timemodel, which is able to connect with the external battery bank. Hereinafter called three-phase 10KS.13) The 3CR15KS is a three-phase input and single-phase output long backup timemodel, which is able to connect with the external battery bank. Hereinafter called three-phase 15KS.14) The 3CR20KS is a three-phase input and single-phase output long backup timemodel, which is able to connect with the external battery bank. Hereinafter called three-phase 20KS.Description of commonly used symbolsThe following symbols will be used in this manual and may appear during the course of your practical applications. Therefore, all users should be familiar with them and understand their meanings.Notation and ExplanationNotation ExplanationAlert you to pay special attentionCaution of high voltageTurn on the UPSTurn off the UPSIdle or shut down the UPSAlternating current source (AC)Direct current source (DC)Protective groundAlarm silenceOverload indicationBattery checkRecyclableDo not dispose with ordinary trash1. AppearanceBACK VIEW of 6K(S)/ Three Phase 6K(S) BACK VIEW of (S)/10k(S)/Three Phase (S)/10K(S)BACK VIEW of Three Phase 15K/Three Phase 20KProduct specification and performance General specification (Standard Models)Note: if the UPS is installed or used in a place where the altitude is above than 1000m, the output power must be derated in use, please refer to the following:Unpacking and inspection1) Unpack the packaging and check the package contents. The shipping packagecontains:● A UPS● A user manual● A communication cable● A battery cable (for 6KS/10KS only)2) Inspect the appearance of the UPS to see if there is any damage duringtransportation. Do not turn on the unit and notify the carrier and dealer immediately if there is any damage or lacking of some parts.Input and output power chords and protective earth ground installation1、Notes for installation1) The UPS must be installed in a location with good ventilation, far away from water,inflammable gas and corrosive agents.2) Ensure the air vents on the front and rear of the UPS are not blocked. Allow at least0.5m of space on each side.3) Condensation to water drops may occur if the UPS is unpacked in a very lowtemperature environment. In this case it is necessary to wait until the UPS is fully dried inside out before proceeding installation and use. Otherwise there are hazards of electric shock.2、InstallationInstallation and wiring must be performed in accordance with the local electric code and the following instructions by professional personnel.For safety, please cut off the mains power switch before installation. The battery breaker also needs to be cut off if it is a long backup time model (“S” model).1) Open the terminal block cover located on the rear panel of the UPS, please referto the appearance diagram.2) For 6K(S) UPS, it is recommended to select the UL 1015 10AWG(6mm2)wire orother insulated wire which complies with AWG Standard for the UPS input and output wirings.The protective earth ground wire refers to the wire connection between toe equipment which consumes electric equipment and the ground wire. The wire diameter of protective earth ground wire should be at least as above mentioned for each model and green wire of green wire with yellow ribbon wire is used.1) After having completed the installation, make sure the wiring is correct.2) Please install the leak current protective breaker at the output power distribution panelof the UPS if necessary.3) To connect the load with the UPS, please turn off all the loads first, then perform theconnection and finally turn on the loads one by one.4) No matter the UPS is connected to the utility power or not, the output of the UPS mayhave electricity, The parts inside the unit may still have hazardous voltage after turning off the UPS. To make the UPS have no output, power off the UPS, and then disconnect the utility power supply.5) Suggest charging the batteries for 8 hours before use. After connection, turn the inputbreaker in the “ON” position, the UPS will charge the batteries automatically. You can also use the UPS immediately without charging the batteries first, but the backup time may be less than the standard value.6) If it is necessary to connect the inductance load such as a monitor or a laser printer tothe UPS. the start-up power should be used for calculating the capacity of the UPS, as its start-up power consumption is too big when it is started.Input and output Terminal Block wiring diagram of 6K(S)/(S)/10K(S) Important notes: If the UPS is used in single mode, JP1 and JP2 must be connected by 10AWG (6mm2). If the UPS is used in parallel mode, the Jumper between JP1 and JP2must be removed.2.InstallationInput and output Terminal Block wiring diagram of three-phase 10KS Important notes: If the UPS is used in single mode, JP1 and JP2 must be connected by 10AWG (6mm2). If the UPS is used in parallel mode, the Jumper between JP1 and JP2 must be removed.Input and output Terminal Block wiring diagram of three-phase 15KS/20KSImportant notes: If the UPS is used in single mode, JP1 and JP2 must be connected by 6AWG (25mm2). If the UPS is used in parallel mode, the Jumper between JP1 and JP2 must be removed.2.InstallationOperating procedure for connecting the long backup time model UPS with the external battery1、The nominal DC voltage of external battery pack is 240VDC. Each battery packconsists of 20 pieces of 12V maintenance free batteries in series. To achieve longer backup time, it is possible to connect multi-battery packs, but the principle of “same Voltage, same type” should be strictly followed.2、The connector of the external battery cable is used to plug into the external batterysocket of the UPS. the other end of the external battery cable is made of three open wires with ring terminals to connect with the external battery pack(s). The procedure of installing battery bank should be complied with strictly. Otherwise you may encounter the hazardous of electric shock.1) A DC breaker must be connected between the battery pack and the UPS. Thecapacity of breaker must be not less than the data specified in the general specification.2) Set the battery pack breaker in “OFF”position and connect the 20 pieces ofbatteries in series.3) You must connect the external battery cable to the battery first, if you connect thecable to the UPS first, you may encounter the hazardous of electric shock. The positive pole of the battery is connected to the 10KS/3 phase 10KS in parallel with blue and brown wires; the negative pole of the battery is connected to the 10KS/3 phase 10KS in parallel with black and white wires; the green and yellow ribbon wire is connected to the ground of the battery cabinet. For three-phase 15KS/20KS, the connection of battery wire is the same as that of input and output wire, and a green or green and yellow ribbon wire UL1015 6AWG (25mm2) must be connected between the input protective earth terminal and the battery cabinet.3、To complete the connection by plugging the connector of the external battery cableinto the external battery socket of the UPS. Do not attempt to connect any loads to the UPS now. You should connect the input power wire to the right position first, And then set the breaker of the battery pack in the ON position. After that set the input breaker in the ON position, The UPS begins to charge the battery packs at the time.the external battery cable diagram for 6KS/10KS(The cable may vary from different “S”models)2.InstallationParallel operation1、Brief introduction of the redundancyN+X is currently the most reliable power supply structure. N represents the minimum UPS number that the total load needs; X represents the redundant UPS number .l. e.the fault UPS number that the system can handle simultaneously. The bigger the X is, the higher reliability of the power system is. For occasions where reliability is highly depended on, N+X is the optimal mode.As long as the UPS is equipped with parallel cables, up to 3 UPSs can be connected in parallel to realize output power sharing and power redundancy.1、Parallel installation1) Users need to a standard 25-pin communication cable, which should have 25 cores,corresponding stitches and shield, as the UPS parallel cable. The length of the parallel cable is appropriate to less than 3 m.2) Strictly follow the stand-alone wiring requirement to perform the Input wiring of eachUPS.3) Connect the output wires of each UPS to an output breaker panel.4) Disconnect the Jumper on JP1 and JP2 of the terminal block first, and connecteach output breaker to a main output breaker and then to the loads.※The requirement of the output wiring is as follows:●When the distance between the UPSs in parallel and the breaker panel is lessthan 20 meters, the difference between the wires of input & output of theUPSs is required to be less than 20%:●When the distance between the UPSs in parallel and the breaker panel isgreater than 20 meters, the difference between the wires of input & output ofthe UPSs is required to be less than 10%2、Operation and maintenance1) To perform the general operation, follow the stand-alone operating requirement;2) Startup: The units transfer to INV mode simultaneously as they start up sequentially in utility power mode:Shutdown: the units shut down sequentiallyin INV mode. When the last one completesthe shutdown action, each unit will shut downthe inverter simultaneously and transfer tobypass mode.Parallel InstallationdiagramIt is easy to operate the equipment, with no previous training. You just need to read through this manual and operate according to the instructions in it. The meaning of the LED indicators. Please refer to the appendix 1 “Display panel”3.Operation and Operating modeOperationon the UPS with utility power supplied(in Line mode/AC mode)※Your first use of Internal Battery models.1) When you operate first time, Please open the battery breaker cover plate and turn onthe Battery Breaker. Then close the battery breaker cover plate.2) After you make sure that the power supply connection is correct, set the input breakerin the “ON” position first. At this time the fan rotates and the UPS supplies power to the load via the bypass. The UPS operates in Bypass mode.3) To power on the UPS by simply pressing the “ON” button continuously for more than 1second.4) When being powered on, the UPS will perform self-diagnosis, with the load/battery level LEDs turned on and then off one after another in ascending order. A few seconds later, the INV LED is turned on, the UPS is already running in Utility Power mode. If the utility power is abnormal, the UPS will operate in battery mode without output interruption of the UPS.2. Turn on the UPS with on utility power supplied (in battery mode)1) Press the “ON” button continuously for more than 1 second to power on the UPS For long back up time model (“S” model), please make sure that the battery breaker is in “ON” position.2) During the course of starting up, the UPS has the same action as if it is connected to utility power except that the utility power LED is not turned on and the battery LED is turned on instead.3. Turn off the UPS with utility power supplied (in Line mode/AC mode)1) Press the “OFF” button continuously for more than 1 second to turn off the inverter ofthe UPS immediately.2) When being powered off, the UPS will perform self-diagnosis, the Load/Battery levelLEDs will be turned on and then off one after another in ascending order, then the INV LED will be turned off and Bypass LED will be turned on. The UPS is working in Bypass mode.3) Upon completion of the above to turn it off, output of electric current of the UPS is stillpresent. In order to cut off the output from the UPS, simply cut off the utility power supply and the UPS will perform self-diagnosis, finally not any display is shown on the display panel and no voltage output is available from the UPS output.4. Turn off the UPS with on utility power supplied (in Battery mode)1) Press the “OFF” button continuously for more than 1 second to power off the UPS.2) When being powered off, the UPS will perform self-diagnosis, the Load/Batterylevel LEDs will be turned on and then off one after another in ascending order.Finally not any display is shown on the display panel and on voltage is available form the UPS output.Suggestions:Please turn off the connected loads before turning on the UPS and turn on the loads one by one after the UPS is working in INV mode. Turn off all of the connected loads before turning off the UPS.ISOLATE UNINTERRUPTIBLE POWER SUPPLY(UPS)BEFORE WORKING ON THIS CIRCUIT3.Operation and Operating modeOperating mode(LED display mode)1. Utility power modeThe display panel in utility power mode is shown in the following diagram, The utility power LED and the INV LED are turned on, The load level LEDs will be turned on in accordance with the load capacity connected.1) If the battery LED is turned on and the utility power LED flashes, it indicates thevoltage or frequency of the utility power has exceeded the normal range, theUPS operates in battery mode.Fig-3-1 The utility power mode2) If output overloaded, the load level LEDs will be turned on and alarm will keeptwice every second. You should get rid of some unnecessary loads one by oneto decrease the loads connected to the UPS less than 90% of its nominal powercapacity.Note: Please follow the following steps to connect the generator:●Activate the generator and wait until the operation is stable before supplying power ofthe generator to the UPS (be sure that the UPS is in idle mode). Then turn on the UPS according to thestart-up procedure. After the UPS is turned on, then the loads can be connected to the UPS one by one.●The power capacity of the AC generator should be at least twice of the UPS capacity.2. Battery modeThe display panel in battery mode is shown in the following diagram . The battery LED and the INV LED are turned on. The displayed number of the battery level LEDs will be turned on in accordance with the battery capacity. Note that the load level LEDs in utility power mode will indicate the level of the battery capacity in battery mode instead.1) When the UPS is running in battery mode, the buzzer beeps once every 4 again,The buzzer will stop beeping (in silence mode). Press the “ON” button onceagain for more than 1 second to resume the alarm function.Fig 3-2 Battery mode diagram3.Operation and Operating mode2) When the battery capacity decreases, the number of the battery capacity LEDs turnedon will be reduced. If the battery voltage descends to the alarm level, the buzzer will beep once every second to remind the users of in sufficient battery capacity and the UPS is soon going to shut down automatically. Then the load operations should be carried out promptly and the loads should be eliminated one by one.3. Bypass modeThe display panel in bypass mode is shown in the following diagram . The utility power LED and the bypass LED are lit. The displayed number of the load LEDs will be turned on in accordance with the load capacity connected. The UPS will beep once every 2 minutes in bypass mode.●The utility power LED flashes. it shows that the voltage or frequency of the utilitypower has exceeded the normal range of the UPS.Fig 3-3 UPS bypass mode diagram●Other indications on the display panel are the same in utility mode.●The UPS does not have the backup function when it is in bypass mode. Thepower used by the load is supplied from the utility power via internal filter.4. Abnormality modeIn case the fault LED is turned on when the UPS is in use, it shows that the UPS is operating in abnormal mode. Please refer to the troubleshooting in section 6 for derail.5. Backup time for the standard modelThe backup time of the long backup time model is dependent on the external battery pack capacity and the load level as well as other factors.The backup time of standard model may vary from different models and load level, Please refer to the following:3.Operation and Operating modeLoad Capacity Load Capacity 6KVA BACKUP TIME CURVE 10KVA BACKUP TIME CURVE6. Communication portIntelligent slotThis series is equipped with an intelligent slot for Web power (optional accessory) orother optional card to achieve remote management of the UPS through internet /intranet. Please contact your local distributor for further information,RS232 Interface1) The following are the descriptions and pin assignment of RS232 DB-9 port:Baud rate: 2400bpsData bit: 8 bitEnding bit:1 bitParity bit: NonePin numberFunction description I/O 3Rx Input 2Tx Output 5 Ground GND 3.Operation and Operating modeOptional AS400 interfaceThis optional AS400 card provides dry contact closure signal “OPEN ” or “CLOSE ”.Following are the pin assignment and the descriptions of As400 card:PIN1:UPS failure (normally open, active close)PIN2:summaryPIN3:groundPIN4:Remote shutdownPIN5:CommonPIN6:Bypass active(relay close)PIN7:Battery lowPIN8:UPS On (relay close)PIN9:Utility Power failure(normally open, active close)4. Battery maintenance This series UPS only requires minimal maintenance. The battery used for standardmodels are value regulated sealed lead-acid maintenance free battery. Thesemodels require minimal repairs. The only requirement is to charge the UPS regularlyin order to maximize the expected life of the battery. When being connected to theutility power, whether the UPS is turned on or not, the UPS keeps charging theRS232 InterfaceAS400 Interfacebatteries and also offers the protective function of overcharging and over discharging.●The UPS should be charged once every 4 to 6 months if it has not been used for along tine.●In the regions of hot climates, the battery should be charged and discharged every 2months. The standard charging time should be at least 12 hours.●Under normal conditions, the battery life lasts 3 to 5 years. In case if the battery isfound not in good condition, earlier replacement should be made. Battery replacement should be performed by qualified personnel.●Replace batteries with the same number and same type of batteries.●Do not replace the battery individually. All the batteries should be replaced at thesame time following toe instructions of the battery supplier.Normally, the batteries should be charged and discharged once every 4 to 6 months.Charging should begin after the UPS shuts down automatically in the course of discharging, the standard charging time for the standard UPS should be at least 12 hours.5. Notes for battery disposal and battery replacement1) Before disposing of batteries, remove conductive jewelry such as necklace, wrist watches and rings.2) If it is necessary to replace any connection cables, please purchase the original materials from the authorized distributors or service centers, so as to avoid overheat or spark resulting in fire due to insufficient capacity.3) Do not dispose of batteries or battery packs in a fire, they may explode.4) Do not open or mutilate batteries, released electrolyte is highly poisonous and harmful to the skin and eyes.5) Do not short the positive and negative of the battery electrode, otherwise, it may result in electric shock or fire.6) Make sure that there is no voltage before touching the batteries, The battery circuit is not isolated from the input potential circuit. There may be hazardous voltage between the battery terminals and ground.7) Even though the input breaker is disconnected, the components inside the UPS are still connected with the batteries, and there are potential hazardous voltages. Therefore, before any maintenance and repairs work is carried out, switch off the breaker of the battery pack or disconnect the jumper wire of connecting between the batteries.8) Batteries contain hazardous voltage and current. Battery maintenance such as the battery replacement must be carried out by qualified personnel who are knowledgeable about batteries. No other persons should handle the batteries.6. Troubleshooting6. TroubleshootingWhen you contact the service center, please provide the following information:●Model No. and the serial No. of the UPS;●The date when the problem arose;●Complete description of the problem, including the LED display, alarm warning,and power condition and load capacity. If your UPS is a long backup time model, you may also provide the battery information.Appendix 1 Display Panel●Power ON/OFF: T o turn on the UPS simply by pressing the “ON” button on thefront panel continuousl y for 1 second. Press the “OFF” button on the front panel continuously for 1 second to turn off the UPS.●Bypass LED (orange LED): Whenever the bypass LED is turned on, it shows thatthe loading current is supplied directly from the utility power.●Utility power LED (green LED): Whenever the utility power LED is turned on, itshows that the utility power is normal.●Inv LED (green LED): Whenever the INV LED is turned on, it shows that theloading current is supplied from utility power or battery via the inverter.●Battery LED (orange LED): Whenever the battery LED is turned on, it shows thatthe loading current is supplied from battery via the inverter.●Fault LED (red LED): Whenever the fault LED is turned on, it shows that the UPSis in abnormal condition.●#2-#6 LEDs (the #2 LED is orange and the #3-#6 LEDs are green): These LEDsindicate the percentage of the load capacity in utility power mode or battery capacity level in battery mode.Appendix 2 The corresponding form of the LED DisplayAppendix 2 The corresponding form of the LED Display☆:Solid ON ★: Flash ↑: LED display and alarm warning are dependent on other conditions.。
美国汽车品牌的车辆维修手册说明书
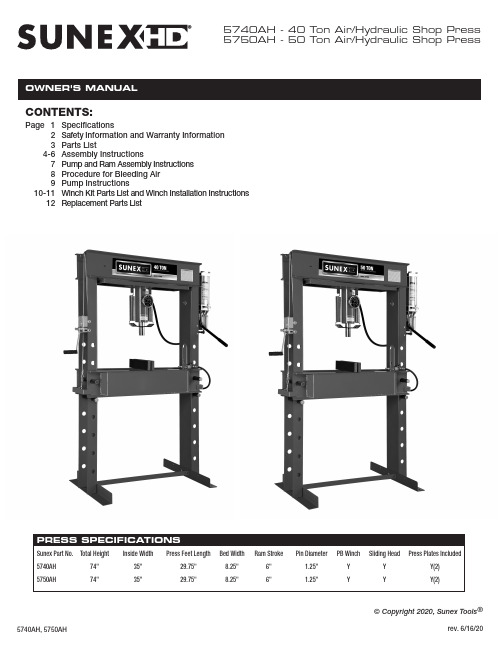
5740AH - 40 Ton Air/Hydraulic Shop Press 5750AH - 50 Ton Air/Hydraulic Shop PressCONTENTS:Page 1Specifications2Safety Information and Warranty Information 3Parts List4-6Assembly Instructions789Pump and Ram Assembly Instructions Procedure for Bleeding Air Pump Instructions10-11Winch Kit Parts List and Winch Installation Instructions 12Replacement Parts List© Copyright 2020, Sunex Tools ®SAFETY INFORMATIONThis symbol alerts you to the possibility of serious injury or death if instructions are not followed.This symbol alerts you to the possibility of damage to or destruction of equipment if instructions are not followed.Failure to heed these warnings may result in lossof load, damage to the press and/or failure resulting in property damage, personal or fatal injury. Thisoperating manual contains important details concern-ing the safe operation of this tool. The user must read and understand these details before any use of the tool. This manual must be retained for future reference.• Read, study, understand and follow all instructions before operating this press.• Always wear safety goggles, (users and bystanders).•Parts being pressed may splinter, shatter, or be ejected from the press at a dangerous rate of speed. Because there are a variety of press applications, it is the responsibility of the press owner to provide adequate guards, eye protection and protective clothing to the press operator.• Visual inspection of the press should be made before use, checking for signs of cracked welds, bent bed pins, loose or missing bolts, leaks, or any other structural damage. Corrections must be made before using the press.•Do not go near leaks. High pressure hydraulic uid can puncture skin and cause serious injury,gangrene, or death. If injured, seek emergency medical help as immediate surgery is required to remove the uid.• Prior to use make sure the press is securely anchored to a concrete oor.•Keep hands, arms, feet, and legs out of work area. Accidental slippage can result in personal injury.• Always use an accurate force gauge to measure pressing force.• Do not exceed the rated capacity or tamper with the pressure/force settings. When attachments and adapters are used the rated capacity of the system shall be no greater than the rated capacity of the lowest rated component or combination of components that make up the system. • Avoid off-center loads. Offset loads can damage ram and may cause load to eject at a dangerous rate of speed. Do not use any spacer or extender between the press ram plunger and the item being pressed. If there is not enough ram stroke, adjust the height of the movable bolster.•Remove all loads from movable bolster before attempting to adjust bolster height. Beware of possible falling bolster.•Press only on loads supported by movable bolster and press plates included. Do not support loads on oor or press frame legs.• When using any accessories such as press plates or arbor plates, be certain they are centered on the movable bolster and in full contact with both sides of the bolster.• Before applying load, be certain all movable bolster supporting pins are fully engaged. Verify lift cables (if equipped) are slack before pressing on the bolster.• Always use a bearing shield when pressing bearings.•Use caution when positioning work to be pressed to ensure the item to be pressed cannot be ejected at a dangerous rate of speed.• Release hydraulic pressure before loosening any ttings.• Maintain proper hydraulic uid levels.• Do not make any alterations or modi cations to the press.•This product may contain one or more chemicals known to the State of California to cause cancer and birth defects or other reproductive harm. Wash hands thoroughly after handling.•Failure to heed and understand these markings may result in serious or fatal personal injury and/or property damage.OWNER/USER RESPONSIBILITYThe owner and/or user must have an understanding of the manufacturer'soperating instructions and warnings before using this press. Personnel involvedin the use and operation of equipment shall be careful, competent, trained,and quali ed in the safe operation of the equipment and its proper use whenservicing motor vehicles and their components. Warning information shouldbe emphasized and understood.If the operator is not uent in English, the manufacturer's instructions andwarnings shall be read to and discussed with the operator in the operator'snative language by the purchaser/owner, making sure that the operatorcomprehends its contents.Owner and/or user must study and maintain for future reference the manufactur-er’s instructions. Owner and/or user is responsible for keeping all warning labels and instruction manuals legible and intact. Replacement labels and literature are available from the manufacturers.INSPECTIONVisual inspection of the shop press should be made before each use of the press, checking for damaged, loose or missing parts. Each press must be inspected by a manufacturer’s repair facility immediately, if subjected to an abnormal load or shock. Any press which appears to be damaged in any way, is found to be badly worn, or operates abnormally must be removed fromservice until necessary repairs are made by a manufacturers's authorized repair facility. It is recommended that an annual inspection of the press be made by a manufacturer’s authorized repair facility and that any defective parts, decals or warning labels be replaced with manufacturer’s speci ed parts. A list of authorized repair facilities is available from the manufacturer.SAFETY INSTRUCTIONS•CHECK YOUR LOCAL, STATE AND FEDERAL REGULATIONSREGARDING THE SAFE USE OF THIS EQUIPMENT.•Your safety is top priority. Please handle equipment with care.•Fully retract unit and remove all items from the press bed frame.•Support the press bed, and remove the pins.•Raise or lower bed to desired height and reinstall press pins. Be certainpins are fully engaged in the parallel anges of the upright columns.•Position press on a at, level, hard surface, preferably concrete.Make sure all nuts and bolts are tight.•Clear the area of bystanders, especially small children, before using.•Set the press bed to the required height. The press is most effectivewhen the work piece is located 1 inch below the ram’s retracted position.The compression stroke can include the entire 5 inch working range.•The press is designed to exert a force on anything which is positionedbeneath its ram. The work piece can pop out from under the ram at a high rate of speed and injure someone.•Pressing Bearings: It is essential that you use the bearing shield whenpressing bearings on or off.LIMITED WARRANTY:SUNEX INTERNATIONAL, INC. WARRANTS TO ITS CUSTOMERS THAT THE COMPANY’S SUNEX TOOLS ® BRANDED PRODUCTS ARE FREE FROM DEFECTS IN WORKMANSHIP AND MATERIALS.Sunex International, Inc. will repair or replace its Sunex T ools ® branded products which fail to give satisfactory service due to defective workmanship or materials, based upon the terms and conditions of the following described warranty plans attributed to that speci c product. This product carries a ONE-YEAR warranty. During this warranty period, Sunex T ools ® will repair or replace at our option any part or unit which proves to be defective in material or workmanship. Other important warranty information....This warranty does not cover damage to equipment or tools arising fromalteration, abuse, misuse, damage and does not cover any repairs or replace-ment made by anyone other than Sunex Tools ® or its authorized warranty service centers. The foregoing obligation is Sunex Tools ®’ sole liability under this or any implied warranty and under no circumstances shall we be liable for any incidental or consequential damages. Note: Some states do not allow the exclusion or limitation of incidental or consequential damages, so the abovelimitation or exclusion may not apply to you. Return equipment or parts to Sunex Tools ®, transportation prepaid. Be certain to include your name and address, evidence of the purchase date, and description of the suspected defect.If you have any questions about warranty service, please write to Sunex Tools ®.This warranty gives you speci c legal rights and you may also have other rightswhich vary from state to state. Repair kits and replacement parts are available for many of Sunex Tools ® products regardless of whether or not the product is still covered by a warranty plan.SHIPPING ADDRESS: MAILING ADDRESS:Sunex Tools Sunex Tools 315 Hawkins Rd. P .O. Box 4215Travelers Rest, South Carolina 29690 Greenville, South Carolina 29608THIS OPERATING MANUAL CONTAINS IMPORTANT SAFETY INFORMATION. READ CAREFULLY AND UNDERSTAND ALL INFORMATION BEFORE OPERATING THIS TOOL. SAVE THIS MANUAL FOR FUTURE USE.WARNING: This product can expose you to chemicals including nickel, which is known to the State of California to cause cancer and birth defects or other reproductive harm.For more information go to .Press Frame - 1Press Bed - 1Press Feet - 2Z Bar - 11/2"-13 x 1-1/2" Hex Head Bolts - 101/2" Nuts - 10Air MotorPump and Ram - 1Pump Extension Handle - 11" x 3" x 14"Press Plates - 2Accessory only -Not needed for assemblyPushing Adapter - 1Accessory only -Not needed for assemblyBearing Shield - 1Accessory only -Not needed for assemblyESTIMATED ASSEMBLY TIME: 30 MINUTESACCESSORIESASSEMBL CONTINUEDPUMP AND RAM ASSEMBL Y INSTRUCTIONSPROCEDURE FOR BLEEDING AIRPUMP INSTRUCTIONSWINCH INSTALLATION INSTRUCTIONS CONTINUED。
Carlin 60200FR 自燃保护系统说明书
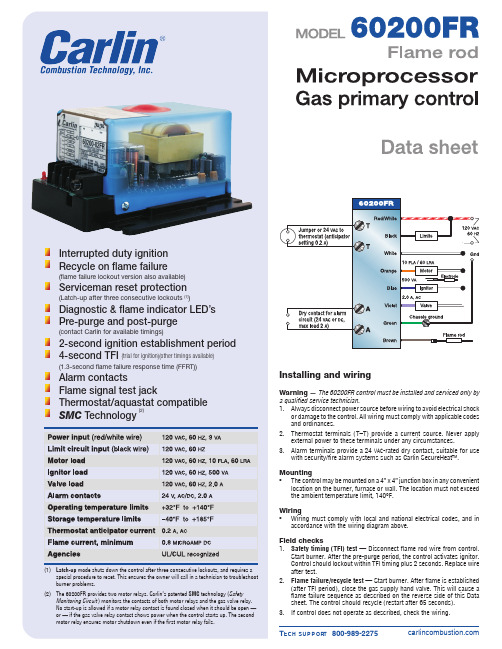
Interrupted duty ignitionRecycle on flame failure(flame failure lockout version also available) Serviceman reset protection(Latch-up after three consecutive lockouts (1)) Diagnostic & flame indicator LED’s Pre-purge and post-purge(contact Carlin for available timings)2-second ignition establishment period 4-second TFI (trial for ignition)(other timings available)(1.3-second flame failure response time (FFRT))Alarm contactsFlame signal test jack Thermostat/aquastat compatible SMC Technology(2)Warning — The 60200FR control must be installed and serviced only bya qualified service technician.1. Always disconnect power source before wiring to avoid electrical shockor damage to the control. All wiring must comply with applicable codes and ordinances.2. Thermostat terminals (T–T) provide a current source. Never applyexternal power to these terminals under any circumstances.3. Alarm terminals provide a 24 vac-rated dry contact, suitable for usewith security/fire alarm systems such as Carlin SecureHeat™.Mounting• The control may be mounted on a 4” x 4” junction box in any convenient location on the burner, furnace or wall. The location must not exceed the ambient temperature limit, 140°F.Wiring• Wiring must comply with local and national electrical codes, and in accordance with the wiring diagram above.Field checks1. Safety timing (TFI) test — Disconnect flame rod wire from control.Start burner. After the pre-purge period, the control activates ignitor.Control should lockout within TFI timing plus 2 seconds. Replace wire after test.2. Flame failure/recycle test — Start burner. After flame is established(after TFI period), close the gas supply hand valve. This will cause a flame failure sequence as described on the reverse side of this Data sheet. The control should recycle (restart after 65 seconds).3. If control does not operate as described, check the wiring.T e ch s u p p or t Start-up & operationDo not start the burner if the combustion chamber contains residual gas. Allow gas to disperse.Per UL requirements, the control will not turn on if the flame rod senses flame during the self-test. If the flame rod senses flame, the green LED turns on. The control will remain in self-test mode until the flame rodCheck 60200FR control label for trial for ignition (TFI), pre-purge and post-purge timings.Model 60200 diagnostic LED’sOFFOFFOFF ONONONFLASHING– RedFLASHINGBLINKING (blinks off momentarily every 3 to 4 seconds)Model 60200FR Microprocessor flame rod gas primary control — Data sheet — Operation/TroubleshootingService & TroubleshootingNo power to control• Check line voltage to the control (at least 95 vac).• Check all electrical connections.Control is in lockout• Red LED will be on. Press the reset button for 1 second.• If the control returns immediately to lockout: Use a voltmeter to check power to the gas valve. (Also check the power to the valve after resetting control and attempting another start.) The control may have detected power on the valve relay contact. If the gas valve wire shows 120 vac, check wiring to make sure wiring is correct and there is no external power feed to the valve. Correct wiring if needed. If the voltmeter shows no power to the valve, the circuit may have an internalcontrol problem. Replace the control.Flame rod sensing flame• Amber LED blinks off each 3 to 4 seconds; green LED on. Remove flame rod lead from rod.If the amber LEDcontrol is defective.If amber and green LED’s To troubleshoot:• Check flame rod by using an ohmmeter to check resistance from flame rod to ground — should be at least 1 megohm .• Connect a flame simulator to the control flame rod lead. If green LED turns on, flame rod assembly is defective. Replace assembly.Repeated flame failuresflashing red LED )Check for:• Defective flame rod assembly• Excessive airflow or draft causing flame to leave burnerhead — Check for proper air band setting and draft.• Excessive back pressure causing flame to be erratic — Checkappliance and flue for sooting/plugging.Control locks out after TFI red LED on )Check for:• No gas to burner — Check gas supply and lines. Verify gas pressure is no higher than allowed for gas valve (usually ½ psig maximum).• Shorted electrode — Inspect for cracked porcelain and replace as needed.• Poor spark — Check electrode spacing and condition per burner manual. Replace or realign if necessary. • Airflow too high — Check air band setting.• Ignitor module defective — Replace if no spark. • Flame rod defective or shorted to burner chassis.•Gas valve stuck in closed position. Check wiring connections. Replace as necessary.• Reversed 120 vac polarity — Make sure the hot and neutral lines are not reversed at power entrance.Carlin part number MN60200FRC Rev. 10/03/11©Copyright 2011 — Carlin Combustion Technology, Inc.Power ONSelf-test 1The control performs a “boot-up” test to verify internal operation each time power is applied to the red/white wire. About 4 seconds after powerapplication, the amber LED turns on. The test continues for about 6 more seconds. If the test fails, the control turns the amber LED off and repeats this test sequence until successful.Stand-by(No call for heat) If Self-test 1 is successful, amber LeD turns off and control waits for heat call.Call for heat Set thermostat (or limit) to call for heat. Thermostat circuit must be closed and power coming to black wire from limit circuit.Self-test 2The amber LED turns on. For the first 3 to 4 seconds, the control per -forms a self-test. If the flame rod senses flame, the green LED turns on.The control repeats the self-test until flame is no longer detected (greenBurner onAfter the self-test, the amber LED turns off. The motor starts.Pre-purge The ignitor starts after the pre-purge period. Two seconds later, the gasvalve opens. The 2-second delay (ignition establishment period) helpsensure a stable spark is in place when the gas valve opens (to compen-sate for sluggish response of some AC ignition transformers).TFIthe TFI if the flame rod senses flame.Run The burner continues firing during call for heat if the flame rod sensesflame. Amber and red LED’s are off during normal running.If flame rod does not sense flame within the TFI time limit after gas valve activation (TFI), lockout occurs. The control turns the red LED on constant, and closes the alarm contact. Green LED is off.To ResetPush in and hold reset button for 1 second, then release.If the control locks out 3 times during a single call for heat, latch-up oc-curs. The control turns on both the amber and red LED’s constant. You must use the special procedure below to reset the control after latch-up.Reset after latch-up — Only a qualified service technician should attempt to reset the control after latch-up. The problem that caused the repeated burner problems must be corrected before returning the burner to normal operation.Push in and hold the reset button for about 10 seconds. The amber and red LED’s will begin to flash alternately.After the LED’s begin flashing, continue to hold the reset button for about another 20 seconds. The LED’s will turn off. Release the reset but -ton and the control will restart. (Releasing the button before the LED’s turn off will cause the control to remain in latch-up.)The 60200FR control will not reset from lockout or latch-up if power isinterrupted.Flame failure If the flame rod loses flame signal during operation (after the TFI), thered LED flashes. The gas valve closes within 2 seconds. The motorremains on for the motor delay off period, then shuts off. Recycle : at Self-test 2(NOTE :. Model 60200FRN only.)Post-purgeSet thermostat (or aquastat) to stop call for heat. The gas valve will turn off within 2 seconds. The motorremains on for the post-purge period, then turns off.Stand-byControl remains in stand-by mode until limit circuit sends power to the black wire and thermostat circuit closes (call for heat).。
Cascade 20D Razorback Clamp 的维修手册说明书
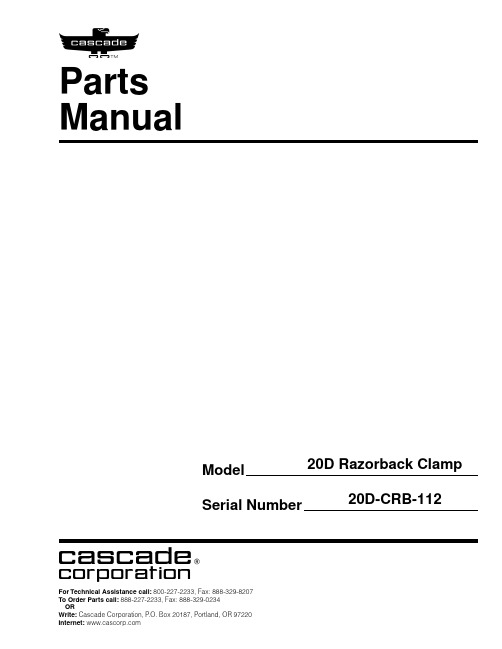
Parts Manual cFor Technical Assistance call: 800-227-2233, Fax: 888-329-8207 To Order Parts call: 888-227-2233, Fax: 888-329-023420D R azorback Clamp20D-CRB-112ModelSerial Number cascadeாcorporationPART NO.DESCRIPTION669224Service Manual 672944Operators Guide668987Installation Instructions680664Servicing Cascade Cylinders-VHS 679929Tool Catalog673964Literature Index Order FormPublicationsREF QTY PART NO.DESCRIPTION 11679150No Step Decal22665595No Hand Hold Decal31679059Quick Change Hook Decal123Base Unit GroupREF QTY PART NO.DESCRIPTION353771Base Unit Group 12207425Hose, 24.00 in.22675055Hose, 17.50 in.31601377Fitting, 8-842601377Fitting, 8-856601377Fitting, 8-863671222Capscrew, 3/8 NC x .75724071Capscrew82671570Cylinder v927861Roll Pin - Inner1027962Roll Pin - Outer 111671549Frame - Upperv See Cylinder page for parts breakdown.q Not included in Base Unit Group.See Restrictor Cartridge page for parts breakdown. Reference: SK-5299.REF QTY PART NO.DESCRIPTION 128667910Washer138667909Capscrew141682098Bumper152665707Nut, 1/2 in. ID1623659Capscrew174668910Bearing184667663Bearing194668911Bearing201680620Mounting Plate - RH211680619Mounting Plate - LH221674168Frame - Lower232667609Restrictor Cartridge q20D25DREF QTY PART NO.DESCRIPTION671570Cylinder Assembly 126510Cotter Pin s 22667624Nut Retainer s 32667625Nut s41671572Shell 51602580Fitting 61558200Piston 712716O-Ring v 81662452Seal v 912785O-Ring v101615128Back-Up Ring v 111563906Retainer 121662448Seal v131638243Nylon Ring v 141636853Wiper v 151667623Nut 161667623Rod 171667626Washer 181—Spacer191671047Seal Loader, Piston v 201671051Seal Loader, Retainer v 668021Service Kitv Included in Service Kit 668021.s Included in Nut Service Kit 668926.Reference: S-7605, S-7658CylinderRestrictor CartridgeREF QTY PART NO.DESCRIPTION667609Restrictor Cartridge 112701O-Ring21667611Plunger312841O-Ring41667610Plug – Special515716Jam NutREF QTY PART NO.DESCRIPTION344388Valve Group 343684Valve Group v 11667490Special Fitting 212841O-Ring q 31667471Spool 42609453Fitting, 1052667487Spring 67604510Fitting, 671678270Check Valve – VPO 82659058Check Valve – PO 92667516Service Kit q101679846Low Flow Spool Kit 112667494Fittingq Included in Service Kit 667513.v Items 1–22 only.Valve GroupREF QTY PART NO.DESCRIPTION1222840O-Ring q 132673098Spring 142667492Poppet151673089Spool Assembly 162667491Sleeve 171343685Valve Body 181661347Service Kit q 191334615Relief Valve 201684625Service Kit 211343687Relief Valve 221667510Service Kit 231334808Valve Bracket 667513Service KitArm Groupq Includes items 1 thru 7 only.Quick-Change Mounting GroupClass IIREF QTY PART NO.DESCRIPTION678833Lower Hook Group12675514Hook24678942Capscrew, 5/8 NC x 1.2532675515Guide42678832PinReference: S-3197.Mounting Plates with Bolt-On Upper HooksREF QTY PART NO.DESCRIPTION1 1 680619 Mounting Plate Assembly–LH q2 1 680620 Mounting Plate Assembly–RH s 316002330Upper Hook–LH 41210491Upper Hook–RH 54768577Capscrew, M20 x 35q Includes items3 and 5.sIncludes items 4 and 5.Do you have questions you need answered right now? Call your nearest Cascade Parts Department.Cascade (UK) Ltd.15, Orgreave Crescent Dore House Industrial Estate HandsworthSheffield S13 9NQ EnglandTel: 742-697524FAX: 742-695121Cascade Scandinavia AB Box 124Hammarvägen 10567 23 Vaggeryd SwedenTel: 42-0-393-36950 FAX: 46-0-393-36959Cascade N.V. European Headquarters P.O. Box 30091300 El Almere Damsluisweg 561332 ED AlmereThe NetherlandsTel: 31-36-5492911 FAX: 31-36-5492964Cascade Norway Østerliveien 37A 1153 Oslo NorwayTel: 47-22-743160 FAX: 47-22-743157Cascade France S.A.R.L.1D Rue De CharaintruBP 18, 91360 Epinay-Sur-OrgeMorangis Cedex, FranceTel: 33-1- 64547500FAX: 33-1-64547501Cascade Hispania S.A.Carrer 5 Sector CZona Franca DuaneraPoligono de la Zon Franca08040 Barcelona, SpainOffice No. 256Tel: 93-264-07-30FAX: 93-264-07-31Cascade Canada Inc.5570 Timberlea Blvd.Mississauga, OntarioCanada L4W-4M6Tel: 905-629-7777FAX: 905-629-7785Cascade GmbHD-41199 MonchengladbachKlosterhofweg 52GermanyTel: 49-216-668230FAX: 49-216-6682323Cascade N.V.Benelux Sales and ServiceP.O. Box 30091300 El AlmereDamsluisweg 561332 ED AlmereThe NetherlandsTel: 31-36-5492950FAX: 31-36-5492974Cascade FinlandAlbert Petreliuksenkatu 301370 VantaaFinlandTel: 358-9-836-1925FAX: 358-9-836-1935Cascade Corporation2501 Sheridan AvenueSpringfield, OH 45505Tel:888-CASCADE (227-2233)FAX: 888-329-0234Cascade Japan Ltd.5-5-41,Torikai KamiSettsu, OsakaJapan, 566Tel: 81-726-53-3490FAX: 81-726-53-3497Cascade Korea108B, Namdong Ind Complex 658-3 Gojan-Dong Namdong-GuInchon, 405-310 KoreaTel: 82-32-821-2051FAX: 82-32-821-2055Cascade Australia1445 Ipswich RoadRocklea, QLD 4106AustraliaTel: 1-800227-223FAX: (07) 3373-7333Cascade New Zealand15 Ra Ora DriveEast Tamaki, AucklandNew ZealandTel: 9-273-9136FAX: 9-273-9137Cascade (Africa) Pty. Ltd.P.O. Box 625, Isando 160060A Steel RoadSparton, Kempton ParkSouth AfricaTel: 27-11-975-9240FAX: 27-11-394-1147Cascade-Xiamen No. 668 Yangguant Rd. Xinyang Industry Zone Haicant, Xiamen City Fujian ProvinceP.R. China 361026 Tel: 86-592-651-2500 FAX: 86-592-651-2571Cascade (Singapore) Trading Co.Four Seasons Park Autumn Block - Apt. 1802 12 Cuscaden Walk SingaporeTel: 65-834-1935FAX: 65-834-1936c。
620使用说明书1-32页

1 4
2 3 7
5 T R I T E C 1 . 6L 8
620
仪器和控制器的操作
620
仪器和控制器的操 作
仪表板 仪表 板 … …… … … … … … …… … … … …… …… … … … …… … … …1 1 手动 空 调 控制 器 ( 选 装 ) …… … … … …… …… … … … …… … … …1 2 自动 空 调 控制 器 ( 选 装 ) …… … … … …… …… … … … …… … … …1 3 组合 仪 表 …… … … … … … …… … … … …… …… … … … …… … … …1 4 组合 仪 表 上的 指 示 灯 … … …… … … … …… …… … … … …… … … …1 5
620
车辆识别代号(VIN)
2 1 1
发动机编号
直列四缸 16 气门 单顶置凸轮轴 多点顺序燃油喷射 1596 85(6000r/min) 149(4500r/min) 800±50 7.8 1587 78(6000r/min) 137(4500r/min)
LF481Q3
车辆的识别代号(VIN)位于上图所示 发动机舱内1的位置和仪表板的左上侧1 的位置,用于车主登记。制造厂铭牌位于 发动机舱内2的位置,铭牌上也标有车辆 识别代号(VIN)。
TR I T E C 1 . 6 L 发动机编号位于上图所示的发动 机 缸体上
5
6
620
各类指示牌、警示牌
1 4 1、助力转向油警示牌。 2、加注机油和冷却液警示牌 。 3、空调冷媒警示牌。 4、玻璃清洗液警示牌。 5、发动机冷却液指示牌。
620
2
John Deere Gator Utility Vehicle XUV 620i 技术手册说明书

JOHN DEERE WORLDWIDE COMMERCIAL & CONSUMER EQUIPMENT DIVISIONNorth American VersionLitho In U.s.a.Manual DescriptionNote: Depending on the particular section or system being covered, not all of the above groups may be used.INTRODUCTIONSpecifications Engine - Gas Steering Safety Drive Train Electrical Brakes MiscellaneousSafetyRecognize Safety InformationUnderstand Signal WordsReplace Safety SignsHandle Fluids Safely - Avoid FiresBe Prepared For EmergenciesUse Care In Handling And Servicing BatteriesPrevent Battery ExplosionsPrevent Acid BurnsAvoid acid burns by:If you spill acid on yourself:If acid is swallowed:Wear Protective ClothingUse Care Around High-pressure Fluid Lines Avoid High-Pressure FluidsAvoid Heating Near Pressurized Fluid LinesService Machines SafelySupport Machine Properly and Use Proper Lifting EquipmentWork In Clean AreaBefore starting a job:Using High Pressure WashersIlluminate Work Area SafelyWork In Ventilated AreaService Tires SafelyAvoid Injury From Rotating Blades, Augers And PTO ShaftsService Cooling System SafelyHandle Chemical Products SafelyDispose of Waste ProperlyPark Machine SafelyBefore working on the machine:Live With SafetySPECIFICATIONS TABLE OF CONTENTS Table of ContentsSpecifications (7)O-Ring Seal Service Recommendations (9)General Information (12)Coolant (15)Serial Number Locations (16)Specifications Metric Fastener Torque Values“Lubricated” means coated with a lubricant such as engine oil, or fasteners with phosphate and oil coatings. “Dry” means plain or zinc plated (yellow dichromate - Specification JDS117) without any lubrication“Lubricated” means coated with a lubricant such as engine oil, or fasteners with phosphate and oil coatings. “Dry” means plain or zinc plated (yellow dichromate - Specification JDS117) without any lubrication“Grade 2” applies for hex cap screws (Not Hex Bolts) up to 152 mm (6 in.) long. “Grade 1” applies for hex cap screws over 152 mm (6 in.) long, and for all other types of bolts and screws of any length.SPECIFICATIONS O-RING SEAL SERVICE RECOMMENDATIONSO-Ring Seal Service RecommendationsFace Seal Fittings With Inch Stud Ends TorqueNote: Torque tolerance is +15%, -20%Stud EndTube NutSwivel Nut Locknut Tube NutStud EndNominal Tube OD/Hose ID Face Seal Tube/Hose End O-Ring Stud EndsMetric Tube OD Inch Tube OD Thread Size Tube Nut/Swivel Nut Torque Bulkhead Lock Nut Torque Thread Size Straight Fitting orLock Nut Torque mm Dash Size in.mm in.N•mlb-ftN•m lb-ftin.N•m lb-ftFace Seal Fittings With Metric Stud Ends TorqueNote: Torque tolerance is +15%, -20%Nominal Tube OD/Hose ID Face Seal Tube/Hose End O-Ring Stud Ends, Straight Fitting or Lock NutMetric Tube OD Inch Tube OD Thread SizeHex SizeTube Nut/Swivel Nut TorqueBulkhead Lock Nut TorqueThread Size Hex Size Steel or Gray Iron Torque Aluminum Torquemm Dash Size in.mm in.mm N•m lb-ft N•m lb-ft mm mmN•m lb-ft N•m lb-ftO-Ring Face Seal FittingsO-Ring Boss FittingsStraight Fitting or Special Nut TorquesImportant: Avoid Damage! DO NOT allow hoses to twist when tightening fittings. Use twowrenches to tighten hose connections; one to hold the hose, and the other to tighten the swivel fitting.ABAABThread SizeTorque a Number of Flats bN•mlb-ftDCEMetric Fastener Torque Value - Grade 7General Information Gasoline4 - Cycle EnginesTo avoid engine damage:ONLY use clean, fresh unleaded gasoline with an octane rating (anti-knock index) of 87 or higherSizeSteel or Gray Iron Torque Aluminum TorqueThread SizeTorque a Number of Flats bN•mlb-ft Caution: Avoid Injury! Gasoline is HIGHLYFLAMMABLE, handle it with care. DO NOTrefuel machine while: indoors, always fill gas tank outdoors; machine is near an open flame or sparks; engine is running, STOP engine; engine is hot, allow it to cool sufficiently first; smoking.Help prevent fires: fill gas tank to bottom of filler neck only; be sure fill cap is tight after fueling; clean up any gas spillsIMMEDIATELY; keep machine clean and in good repair - free of excess grease, oil, debris, and faulty or damaged parts; any storage of machines with gas left in tank should be in an area that is well ventilated to prevent possible igniting of fumes by an open flame or spark, this includes any appliance with a pilot light. To prevent fire or explosion caused by STATIC ELECTRIC DISCHARGE during fueling:•ONLY use a clean, approved POLYETHYLENE PLASTIC fuel container and funnel WITHOUT any metal screen or filter.Gasoline StorageJohn Deere Gasoline Conditioner and Stabilizer (TY15977)4 - Cycle Gasoline Engine OilPLUS - 4TMTURF - GARD TMBreak-In Engine Oil - 4-Cycle GasolineBREAK - IN ENGINE OILalso recommendedTORQ - GARD SUPREME® - SAE 5W-30.5 hours (maximum)Important: Avoid Damage! California Proposition 65 Warning: Gasoline engine exhaust from this product contains chemicals known to the State of California to cause cancer, birth defects, or other reproductive harm.Important: Avoid Damage! Keep all dirt, scale, water or other foreign material out of gasoline.Important: Avoid Damage! ONLY use a quality break-in oil in rebuilt or remanufactured engines for the first 5 hours (maximum) of operation. DO NOT use oils with heavier viscosity weights than SAE 5W-30 or oils meeting specifications API SG or SH, these oils will not allow rebuilt or remanufactured engines to break-in properly. Important: Avoid Damage! After the break-in period, use the John Deere oil that is recommended for this engine.Transaxle OilEMFWD Differential OilAlternative LubricantsSynthetic LubricantsLubricant StorageMixing of LubricantsOil FiltersImportant: Avoid Damage! Mixing of LOWVISCOSITY HY - GARD™ and HY - GARD™ oils is permitted. DO NOT mix any other oils in thistransmission. DO NOT use engine oil or “Type F” (Red) Automatic Transmission Fluid in this transmission.Important: Avoid Damage! Mixing of LOWVISCOSITY HY - GARD™ and HY - GARD™ oils is permitted. DO NOT mix any other oils in thistransmission. DO NOT use engine oil or “Type F” (Red) Automatic Transmission Fluid in this transmission.Important: Avoid Damage! Filtration of oils is critical to proper lubrication performance. Always change filters regularly.SPECIFICATIONS COOLANTBrake FluidThe following John Deere heavy duty brake fluid is PREFERRED for all drum and disc brakes:Chassis GreaseMoly High-Temperature EP GreaseCoolantRecommended Engine CoolantThe following coolants are preferred:Additional recommended coolants:If the recommended coolants are unavailable, use an ethylene glycol or propylene glycol base coolant that meets the following specification:Water QualityImportant: Avoid Damage! Using incorrect coolant mixture can cause overheating and damage to the radiator and engine:•Do not operate engine with plain water.•Do not exceed a 50% mixture of coolant and water.•Aluminum engine blocks and radiators require approved ethylene-glycol based coolant.SPECIFICATIONS SERIAL NUMBER LOCATIONSEngine Coolant Drain IntervalSerial Number LocationsProduct Serial NumberGasoline Engine Serial Number LocationAASuggest:If the above button click is invalid. Please download this document first, and then click the above link to download the complete manual. Thank you so much for readingMORE MANUALS: https:///ENGINE - GAS TABLE OF CONTENTSTable of Contents Specifications (19)Component Location (23)Theory of Operation (30)Diagnostics (36)Tests and Adjustments (42)Repair (52)。
西克(SICK)LECTOR620操作手册_中文版
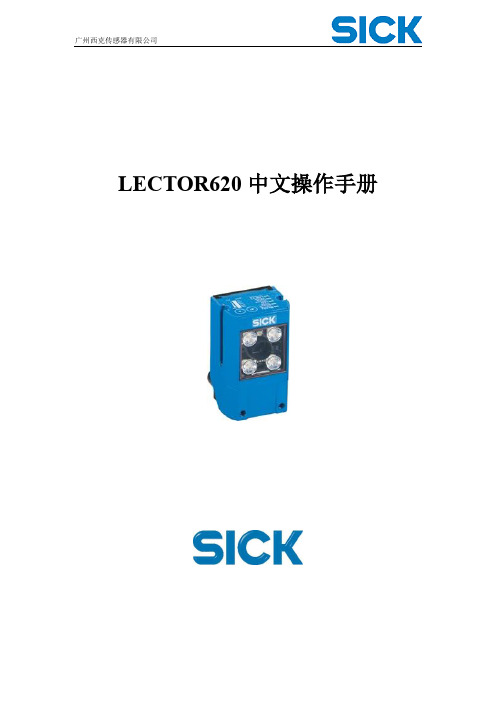
LECTOR620中文操作手册安装距离和角度扫描器的安装距离是指从扫描器的窗口到条码表面的距离。
每种条码的阅读距离都不同,因此安装过程中阅读距离的确定需要查阅相关型号的技术参数。
例如,对于0.5mm分辨率的条码,其最大的视野范围是175mm×112mm(如右图),对应最大视野范围的安装高度为260mm为了避免条码表面对红光直接的反射,条码阅读器一般不采取垂直于条码表面的安装方式,应倾斜20°安装软件操作步骤(1)首先打开SOPAS 软件,一般安装SOPAS后会出现两个软件图标,一个是SOPAS,一个是SOPAS Single Device,两个是同一个软件,不同的是界面排版不同,推荐使用SOPAS Single Device界面版本(2)进入以下画面,会自动搜寻出两个设备,两个所不同是端口号,一个是以太网主口2112,一个是以太网辅口2111,推荐选择2112(3)若搜寻设备的结果如下图则说明扫描枪IP地址与电脑IP地址不一致,可修改电脑IP或扫描枪IP,注意修改时要保证扫描枪和电脑IP地址前三段一致,最后一段不同,同时保证子网掩码相同(4)修改扫描枪IP地址时,可选自动获取或者使用固定IP,推荐使用固定IP地址用于调试和通讯(5)出现选择画面,勾选尾缀为2112的扫描枪,点击继续,即可进入软件主界面。
(6)进入主界面,现处于运行模式Operation ,界面如下图:(7)调试时切换到编辑模式,点击Edit ,此时读码器连续拍照,光源一致闪烁,显示实时图像,右侧有8电脑IP 地址扫描枪IP 地址个参数栏,常用的参数栏如下:(8)第一项参数Camera & Illumination 相机和光源设定:调试要点:图像一定要清晰,根据实际情况调节曝光时间,增益和对比度获取稳定的阅读效果(9)第二项参数Codes 条码设定:本产品可同时阅读一维条码,二维PDF417码,二维码,根据所要读取的条码种类勾选相应的码制1. 相机和光源设定2. 条码种类设定3. 触发设定4. 通讯接口和信号输出设定5. 输出格式设定(10)以上图像和条码设定也可通过自学习方式完成,点击Auto Setup自动设定,如下:(11)点击后显示如下画面,首先调整Reading Distance阅读距离使图像聚焦清晰,调整Shutter time曝光时间使图像变亮,在条码的位置拖动鼠标画一个区域覆盖条码,点击继续进入自学习过程(12)学习成功后如下画面,点击继续;若自学习不成功则会显示Fail,此时可进入软件手动调整参数(13)显示如下实时阅读画面,点击结束完成自学习(14)第三项Trigger & Digital Input触发和输入信号设定,本产品触发读码器方式有很多种,常用是Sensor/Input 1,由外部接入开关量信号触发读码器开始阅读,结束阅读也有多种方式并且可以组合使用,满足任意条件均可结束阅读(15)第四项Interface & Digital Output 通讯接口和信号输出设定,常用通讯方式是串口RS232和以太网(16)串口通讯设置:点开Serial Host ,通常情况下无需修改参数,默认参数即可,但要注意波特率Baud rate 要和上位机一样触发开始串口 输出信号(17)以太网通讯设置:点开Ethernet Host,a.当需要设扫描枪为服务器端时则选择Server模式,上位机需要输入扫描枪的IP地址和端口号,其中端口号可根据需要修改,默认为2112;b.当需要设定扫描枪为客户端时则选择Client模式,此时需要输入上位机的IP地址和端口号,其中端口号可根据需要修改,默认为2112(18)扫描枪支持两路输出,以设定Output/Result 1输出信号为例,可设定成功读取Good Read或者读不到No Read时输出信号,输出电压默认为24V PNP型,也可通过反转功能变成0V有效,NPN型(19)第五项Data Processing 数据处理设定,扫描枪输出的数据格式可根据需要灵活编辑,点击Data Processing 中的Output Format1选项,默认输出格式如下图即“如果成功读取则输出条码内容,否则输出NoRead ”,可以在此处编辑,例如在条码后加入回车换行(20)数据输出格式也可通过设置向导Wizard 完成,点击Wizard 选择好所要的格式后点击继续(21)设定所需要读的码的最多和最少数量,点击继续码可在条码之间加分隔符Code Separator,如空格,斜杠等,设置完成后点击结束(23)设定完成后切换为运行模式Operation ,点击Operation 即可(24)点击参数下载和永久保存,将参数保存在扫描器中:(25)本软件自带数据接收终端,显示所读取到的数据,可用于调试串口和以太网通讯是否正常,点击数据终端Terminal ,以以太网通讯为例操作如下:若是串口则选择用户自定义连接。
莱驰研磨仪维修手册_rm200_英文版

Repair Manual for Mortar GrinderType RM 2001 Notes on the Repair Manual1.1 General PointsThis repair manual for the type RM 200 mortargrinder contains all the information necessary forthe areas named in the table of contents.For your own safety, we recommend that you havethe necessary repairs done only by Retsch GmbH oran authorised agency (service technicians).If repairs that are not described in this manual arenecessary, please consult your supplier or contactRetsch GmbH directly.Retsch GmbHRheinischestr.3642781 Haan / RheinlandGermany1.2 Necessary Documents• Repair Manual• Operating Instructions• Inspection Instructions Doc. No. 98.001.01931.3 Necessary General Inspections• Insulation test as in EN 60204-1 (VDE 0113)• Protective conductor test EN 60204-1 (VDE 0113)• Voltage testing as in EN 60204-1 (VDE 0113)Please refer to Inspection Instruction Doc. No.98.001.0193 for the permissible measurements.1.4 ToolsThe following tools should be ready to hand:Phillips screwdriver 2x100Screwdriver 5x1002A/FHexkey3A/FHexkeyOpen-jaw wrench A/F 5.5Open-jaw wrench A/F 7Open-jaw wrench A/F 81Notes on the Repair Manual (2)1.1General Points (2)1.2Necessary Documents (2)1.3Necessary General Inspections (2)1.4Tools (2)1.5Description of the Device (4)1.6View of the Milling Chamber (6)2Instructions for Repairs and Dismantling (7)2.1Taking off the Hood (7)2.2Setting the Lock Pretensioning (8)2.3Dismantling the Housing (8)2.4Dismantling the Housing Flange (9)2.5Dismantling the Bearing Sleeve (10)2.6Dismantling the Bearing Flange (11)2.7Replacing the Needle Bearing in the Bearing Flange(Pestle Bearing) (11)2.8Replacing the Motor Flange (12)2.9Replacing the Motor (12)2.10Replacing the Motor Pin (14)2.11Setting the Magnetic Switch on the Lid (15)2.12Replacing the Control (16)2.13Replacing and Setting the Scraper (19)2.14Adjusting the Scraper to the Mortar (20)2.15Checking the Scraper Setting (21)2.16Trial Milling Operation (21)2.17Replacing the Rubber Buffer on the Scraper (22)2.18Mounting and Setting the Rotary Knobs (23)2.19Replacing the Window Panes (23)2.20Replacing the Bearing Plate for the Pestle (24)2.21Replacing the Motor Flange Bearing (25)2.22Replacing the Scraper Bearing (26)2.23Replacing the ON/OFF Switch (26)2.24Replacing the Device Fuse (27)3Technical Data (28)3.1Analyses of the Materials (29)4Parts Lists (30)4.1Part 1 Individual Components (30)4.2Part 3 Variant Assignment (32)4.3Spare Parts List for 2-Year Operation (33)4.4Part 5 Recommended Spare Parts (33)5Part 4 Drawings (34)5.1RM200 Views and Sections (34)5.2Dimensional Data Sheet (41)5.3Circuit Diagram (43)1.5 Description of the DeviceDiagram of the Parts of the Device:Front ViewRear ViewGKLMFIJ EHElement Description FunctionA Device socket Connection for the device’s power cableB Fuse tray Holds two glass fusesC Type plate Information on the device and connectedloadsD ON / OFF switch For turning the RM200 on and offE Display and operating unit:see below for explanations Setting the time and starting / stopping the machineF Lock handle For opening and locking the milling chamberG Rotary grip - pestle pressureadjustmentTurning alters the pestle contact pressureH Scale Guide for setting the pestle pressureI Filling aperture Sample material is filled in here.J Viewing window Allows the milling process to be monitored,especially for adjusting the scraperK Setting knob for scraper Sets the contact pressure or gap for thescraperL Pestle setting knob For adjusting the pestle in relation to themortar wallM Hood Closes the milling chamber1.6 View of the Milling ChamberElement DescriptionFunctionV Pestle Crushes and mills the material W Mortar Holds the material to be milledX ScraperMixes the milled material thoroughly and scrapes off any material adhering to the mortar Y Fixing screw for scraper Holds the scraper in place with the screwed-on fixing clamp ZFixing clamp for scraperClamps the scraperYXZ2 Instructions for Repairs and Dismantling2.1 Taking off the HoodTools requiredTorx 25; Hex key 2mm; Open-end wrench 8mmSpare Parts RequiredFig. 2.1-1 1. Disconnect the C mains plug. 2. Remove pestle V and mortar W 3. Unscrew (2x Fs screws) and remove the F lock handle.4. Unscrew the G rotary grip that is on the pestle pressureadjustment mechanism5. Unscrew the threaded pins at both rotary knobs K /L6. Unscrew both rotary knobs K /L.7. Take the adjusting washers and Belleville washers off theaxles.8. Screw in the left axle for the scraper setting mechanism K byturning it in a clockwise direction as far downwards as possible 9. Screw in the right axle for the pestle adjustment L byturning it in an anticlockwise direction as far downwards aspossible10. Unscrew and take out the 4 housing screws (Torx).11. Align the Lf bearing flange pestle until the axle falls down inthe lid of the housing12. Pull the hood upwards and offFig. 2.1-2Fs FK L LfGs2.2 Setting the Lock PretensioningTools requiredHex key 2mmSpare parts requiredDescription of the procedure Fig. 2.2-1 The lock pretensioning on the lock handle F can be influenced by the adjustment of the rubber buffer Gp .1. Open the hood H and unscrew the threaded pin Gw .2. Increase the lock tension: (unscrew)Turn the Gp rubber buffer in an anticlockwise direction.3. Reduce lock tension: (tighten)Turn the Gp rubber buffer in a clockwise direction.4. Check the lock pretensioning by closing the hood H andby tightening the lock handle F2.3 Dismantling the HousingTools requiredPhillips screwdriver size 2Spare parts requiredDescription of the procedure Fig. 2.3-1 1. Remove the 5 Gs housing screws Fig. 2.3-12. Tilt the RM200 on its side and twist off the 4 feet Sf . Fig.2.3-23. Once the RM200 has been set up on the bottom part ofthe housing, you can carefully take off the top part of the housing. Pay attention to the cabling in the housing. Fig. 2.3-3 Fig. 2.3-4Fig. 2.3-4GsGsGsSfGwHGpF2.4 Dismantling the Housing Flange Tools requiredHex key 5mmScrewdriver 5x100Spare parts requiredDescription of the procedureFig. 2.4-1 1. See Chapter 2.1 Taking off the Hood and 2.8 Replacingthe Motor Flange2. Loosen the three Sg screws.3. Tilt the housing flange on its side carefully withoutdamaging the cables.Note: the K1 cable runs from the Hall sensor to thecontrol and the K2 cable runs from the hood switch to the control also.4. There are two ways of loosening the K1 cable ordismantling the Hall sensor:a. Loosen the counternut at the Hall sensor andthen unscrew and remove the Hall sensor.b. If the housing has been dismantled already, theK1 cable can be taken off the control.5. There are also two ways of loosening the K2 cable orremoving the Hs hood switch:a. Loosen the four Sa screws on the rear coverplate Al. Now loosen the counter nut at the hoodswitch and twist it out.b. If the housing has been dismantled already, theK2 cable can also be disconnected from thecontrol and taken out of the housing.K2Al HsSg2.5 Dismantling the Bearing Sleeve Tools requiredScrewdriver 5 mm x 100Water pump pliersSpare parts requiredDescription of the procedureFig. 2.5-1Fig. 2.5-2 Fig. 2.5-3Fig. 2.5-4GKl2.6 Dismantling the Bearing Flange Tools requiredHex key 4mmSpare parts requiredDescription of the procedure1. For the preliminary work, see Chapter2.1Taking off theHood2. For further preliminary work, see Chapter 2.5Dismantling the Bearing Sleeve3. Remove the rubber ring covering the three screws, S1,S2 and S3.4. Fold down the head plate.5. Loosen and remove the S1, S2 and S3 screws. Fig. 2.6-16. When inserting the S1, S2 and S3 screws, secure themwith Loctite.2.7 Replacing the Needle Bearing in the Bearing Flange(Pestle Bearing)Tools requiredDrift punchSpare parts required1 x sealing ring 05.111.00792 x needle bearings 05.484.0009Description of the procedure1. For the preliminary work, see Chapter2.6 Dismantlingthe Bearing Flange2. Remove the Sm sealing ring Fig. 2.7-13. The two bearings are then tapped out from both sideswith a drift punch.4. Now, use a pressing implement to press the new needlebearings and the spacer into the bearing flange.5. Insert the new Sm sealing ring.6. The new needle bearings are secured with Loctite 241and then greased on the inside.S1S32.8 Replacing the Motor FlangeTools required2 screws M5x50 Rubber hammer 2x hex key 4 mmSpare parts requiredDescription of the procedure 1. Openthe M hood. 2. Then, remove the pestle.3. Place two metal sheets underneath as protection forthe motor flange. Insert two screws with M5 threading and a minimum depth of 50 mm into the two Ab forcing bores. Fig. 2.8-1 4. Tighten the screws at the same time in order topress the Mf motor flange off the motor axle in parallel alignment. 5. Insert the motor flange in such a way that the sloton the underside engages with the pin.6. Use a rubber hammer to tap in the new motorflange and in doing so take care that it enters the bearing in a straight line.2.9 Replacing the MotorTools requiredOpen-jaw wrench 8/8 Rapidly acting adhesiveSpare parts requiredThe 03.713.0065 divider RM200 Foam Cellofoam 460UL might be needed. Motor to suit the voltage variantDescription of the procedure 1. For the preliminary work, see 2.3 Dismantling the Housing / 2.12 Replacing the Control2. Remove the K1 K2 K3 K4 cables as stated in Chapter2.12 Replacing the Control3. Loosen the cables at the six-fold distribution in the Evearthing terminal block Fig. 2.9-24. Remove the connection cable to the operating capacitorBk Fig. 2.9-15. Now carefully take the Sc foam divider out of the greyCellofoam. The foam divider is fixed in position with a few small adhesive dots. Fig. 2.9-4When assembling, take care that the foam divider is in the correct position so that the air can circulate appropriately! Fig. 2.9-3 Use rapidly acting adhesive on 4 different adhesive dots to fix the foam divider in position on the motor ventilator hood6. Remove the four motor mounting screwsFig. 2.9-5 Fig. 2.9-6AbFig. 2.9-3Fig. 2.9-4Fig. 2.9-5Fig. 2.9-62.10 Replacing the Motor PinTools requiredDrift punch AdhesiveSpare parts requiredDescription of the procedureFig. 2.10-11. To remove the motor pin, first clamp the motor axle in avice.The motor axle will otherwise be damaged when it is being tapped out! Fig. 2.10-1 / Fig. 2.10-22. Use soft jaws made of aluminium or copper in order notto damage the shaft. The motor shaft must be clamped so that the motor pin points upwards and can be tapped out with a drift punch. Fig. 2.10-2 3. Using the hammer and drift, tap the pin out carefully. 4. Then, apply Loctite 270 adhesive to the new pin and tapit in carefully and centre it precisely.5. The pin may not jut out on either side more than 8.7mm from the axle.Fig. 2.10-22.11 Setting the Magnetic Switch on the LidTools requiredOpen-jaw wrench 13 mmPhillips screwdriver 2 mmSpare parts requiredDescription of the procedure1. Loosen the four screws Rs.2. Remove the rear panel Rb.Rs3. Loosen the counter nut at the magnetic switchon the lid Md.4. While the machine is running, adjust theswitching point on the Md magnetic switch onthe lid by tightening or loosening the screws.5. The switch must trip before the hand can reachinto the milling chamber. The opening width ofthe hood may not exceed a maximum 80 mm.6. The magnetic switch on the lid may not comein contact with the opened lid!7. Then, carefully tighten the counter nut again.Plastic!Check for correct functioning1. Open the lid, the magnet must switch off the RM200 at a gap width not exceeding 80mm. The F4 fault alarm appears.2. Take out the pestle.3. Close the cover.4. Press STOP to cancel the F4 fault alarm.5. If necessary, turn the Md magnetic switch upwards and check it again. (Steps 1-4)6. Tighten the Rb cover again7. Insert the pestle again8. The RM 200 is now ready for operation again.Inspections: general inspection in accordance with 1.3 Necessary General Inspections2.12 Replacing the ControlTools required7- mm keyPhillips screwdriver Size 1Spare parts required03.748.0116Description of the procedure1. Disconnect the mains plug.2. For the preliminary work, see Chapter 2.3Dismantling theHousing3. Loosen the four Sb screws in the bottom panel Fig. 2.12-14. Remove the three cables: K1 cable to the Hall sensor, K2cable to the hood switch, K3 current supply to the motorSee also Diagram Fig. 2.12-8/ Fig. 2.12-85. Remove the D power switch and remove the cables to theK4 mains input.6. Disconnect the plug to the St keypad membraneSbFig. 2.12-6Loosen the three screws on the Ss control board7. Fig. 2.12-78. Then, set the control to the correct mains voltage.9. Press the – + START buttons at the same time and turnon the machine at the D power switch.10. Press the START button again.11. Press the – or + buttons to choose the right program forthe voltage or frequency.See Fig. 2.12-2 and Table12. Then save the setting by pressing the Stop buttonFig. 2.12-2Fig. 2.12-7SsSs DSt K2SsFig. 2.12-8Item Designation Article numberA1 Device plug 05.230.0008 A2 ON/OFF switch 05.703.0168A3 Operating capacitor 05.379.001 /..04/..05 A4 Hall sensor 05.569.0020A5 Motor 05.441.0283/..284/..286/..287/..288/..374/..387 A6 Control board 03.748.0116 A7 Switch on lid 05.703.0249A8 Keyboard membrane03.799.0039Gehäuseunterteil = lower section of the housingK1K2K3K4DSt2.13 Replacing and Setting the ScraperTools requiredSupplied Torx screwdriver T20Spare parts requiredDescription of the procedureFig. 2.13-11. Open the hood and fold it backwards and down.2. Use the enclosed screwdriver to loosen and take outmounting screw Y.3. Swing out the fastening clip4. Remove and replace the scraper.5. Hook in the fastening clip Z again and insert screw Yloosely. The scraper can be moved forwards or backwards in its slot. Before tightening the screw, push the scraper backwards. 6. Close the hood and check visually or with the material tobe milled if the scraper is in proper contact with the mortar. See also: “Checking the Scraper Setting ”.7. If the scraper doesn’t completely touch the bottom of themortar and the inside wall of the mortar (dotted line inFig. 2.13-2), reset it.8. To do this, loosen mounting screw Y again and move thescraper. Tighten the screw again and check if the scraper is now in contact.Fig. 2.13-2YZX2.14 Adjusting the Scraper to the MortarTools requiredSupplied Torx screwdriver T20Spare parts requiredDescription of the procedure When the machine is delivered or when a scraper is re-ordered, it may be necessary to regrind the scraper X . ThisFig. 2.14-1Condition on Delivery groundX2.15 Checking the Scraper SettingDescription of the procedure Fig. 2.15-1 Optimum settings in contact pressure and contact with the bottom of the mortar are necessary for the scraper to work properly.The best way to assess this is to carry out a neutral milling operation.2.16 Trial Milling OperationFig. 2.16-1We recommend the following mixture as neutral millingmaterial for this trial :e.g. 4 – 5 teaspoons of powder sugar5 – 10 ml water1. With the mortar empty, close the lid and press thelock handle until it shuts.2. Turn the G rotary grip to the “0” setting on the Hscale.3. Switch on the device and start operation by pressingthe Q start button.4. Add the powder sugar through the I window openingon the right and then pour the water in.If the scraper has been adjusted correctly, a pasty mixturewill form that does not stick to the inside wall or to thebottom of the mortar behind the scraper.See Fig. 2.15-1 / Fig. 2.16-1To check the milling visually, look through the J window onthe left.wrongcorrect2.17 Replacing the Rubber Buffer on the Scraper Tools requiredHex key 3 mmHex key 4 mmSpare parts requiredDescription of the procedureFig. 2.17-1 1. For the preliminary work, see Chapter 2.1 Taking off2. Remove the Gb screw that keeps the Ga scraper’srubber buffer in place on the spindle axle of the scraper adjustment mechanism.Fig. 2.17-23. Remove the Gc screw on the scraper linking bar(hexagonal recess) Fig. 2.17-24. The Ga rubber buffer can be replaced now.5. The Gb screw must be secured with Loctite 241.Fig. 2.17-3Ga GaGbGc2.18 Mounting and Setting the Rotary Knobs Tools requiredHex key 1.5 mmSpare parts requiredDescription of the procedureFig. 2.18-1 1. Put the adjusting washer on the spindle and push theBelleville washer with the smaller diameter against the adjusting washer.2. Screw the rotary knob onto the spindle until it is firmlypositioned without play.3. Secure the rotary knob with the threaded pin. See alsoFig. 5.1-92.19 Replacing the Window Panes Tools requiredSpare parts requiredDescription of the procedureFig. 2.19-1 The hinge axles for the Fs window panes are offset and for that reason it is important not to mix up the window panes when changing them. The axle is offset upwards and must be on top when installed. If in doubt, refer to Fig. 2.19-2 to see which pane fits into which side.1. Open the pane as far as it can go and press further untilthe hinges disengage.2. Install by pressing the hinge axle into the hinges.3. Test: if installed correctly, the panes can be opened a lotwider than 90°, as shown in Fig. 2.19-1. If not, switchthe two window panes.FsFig. 2.19-22.20 Replacing the Bearing Plate for the Pestle Tools requiredMS13 / MS 10Screwdriver 10 mmSpare parts requiredDescription of the procedureFig. 2.20-1 Fig. 2.20-2 Flat head screw NoteLEFT-HAND THREAD!2.21 Replacing the Motor Flange Bearing Tools requiredSpare parts requiredDescription of the procedureFig. 2.21-1 1. For the preliminary work, see 2.4 Dismantling theHousing Flange2. After the preliminary work the Mfl motor flange bearingcan be pressed out, as shown in Fig. 2.21-2 .Fig. 2.21-2Mfl2.22 Replacing the Scraper Bearing Tools requiredHex key 4 mmHex key 3 mmSpare parts requiredDescription of the procedureFig. 2.22-1 1. Twist out the Gb screw.2. Twist the Sa screw out of the scraper bearing.3. Take off the Sch disc.4. Pull off the Al scraper linking bar.5. Take off the Bb bronze bushing.6. When it is being fitted, the collar of the bushing pointsdownwards!7. If the scraper linking bar can only be turned withdifficulty, insert an adjusting washer 0.5 mm under the bronze bushing Bb.8. Secure the Sa screw with Loctite.2.23 Replacing the ON/OFF Switch Tools requiredSpare parts requiredDescription of the procedureFig. 2.23-1 1. For the preliminary work, see 2.12 Replacing the Control2. Make sure when inserting the new power switch that theOn/Off position is correct in relation to the housingcover.3. Reconnect the cables in conformance to the circuitdiagram.4. Assemble in reverse order.5. Inspections : general inspections as specified on Page 2SaSchAlBp2.24 Replacing the Device FuseTools requirednot applicableSpare parts requiredfor 230-240V 2 fuses MT3,15A Order No. 05.699.0016for 100-110V 2 fuses MT6, 30A Order No. 05.699.0053Description of the procedure1. Disconnect the mains plug C2. Press in the hook on the B fuse holder3. Take out the B fuse holder4. Replace the fuses5. insert the B fuse holder3 Technical DataDriveSingle-phase worm gear motorSee type plateRated power130 wattsIP53Noise characteristic values Noise measurement according to DIN 45635-031-01-KL3Intensity of sound l WA = 85 dB(A)Workplace-related emission level L pAeq = 72 dB(A)Operating conditions:Material to be milled = quartz sand, grain size < 1 mm100 rpm at rated loadOverload protectionElectronic protection by means of the control:The power is monitored and switched off in cases ofcontinuous overloadingDevice fuses2x glass fuses at the rearMT 3.15A at 230-240VMT 6.00A at 100-110VHeight 585 mm when the lid is openWidth 400mmDepth 510 mm when the lid is openApprox. 24 kg without mortar and pestleWidth 400 mm x depth 500 mmIt is not necessary to observe any safety distancemortar * Tungsten carbide* Special steel 2* Stainless steel* Agate* Sintered corundum* Zirconium oxide* Hard porcelain3.1 Analyses of the MaterialsTungsten carbide Hardness approx. 73 HRC94.000%Analysis: WC06.000%CoSpecial steel 2 / 1.2080 H ardness approx. 60 HRC00.400%Si00.450%Mn00.030%P00.030%S12.000%Cr85.340%FeStainless steel 1.4034 Hardness approx. 53 HRC13.000%Analysis: Cr00.030%SP00.050%01.000%Mn01.000%Si00.420%C84.500%FeAgate Hardness approx. 7.0 n. MohsAnalysis: SiO2 99.910%Al2O3 00.020%Na2O 00.020%Fe2O3 00.010%K2O 00.010%00.010%MnOMgO00.010%00.010%CaOSintered corundum 1 Hardness approx. 9.0 n. Mohs2 3SiO2 00.075%00.075%MgO00.070%CaONa2O 0.0100%Fe2O3 00.010%Zirconium oxide Hardness approx. 8.5 n. Mohs2SiO2 00.170%MgO01.400%01.400%CaOFe2O3 00.030%Hard porcelain Hardness approx. 8.0 n. MohsAl2O3 34.000%K2O 03.000%01.000%MgOCaO01.000%The above percentages for the analysed parts are average values.4 Parts Lists4.1 Part 1 Individual ComponentsItem Qty. Article no. Designation02.222.03771 1Lower housing section03.222.03952 1Upper housing section03.049.00033 1Panel bottom03.049.00014 1Panel top03.222.03835 1Hood03.222.03826 1Housing flange (cast aluminium, painted)03.398.00057 1Head plate (cast aluminium, painted)03.748.01168 1Control board03.799.00399 1Keypad membrane10 4 03.244.0016Rubber foot11 4 03.089.0002Spacer bolt (in the metal housing)12 1 03.399.0102Cable harness RM200 (incl. Hall sensor + magnetic switch on the lid) 13 2 03.706.0261Window14 4 03.709.0046Hinge for window15 4 03.709.0047Hinge axle for window16 1 03.183.0048Mortar plate (flange)17 1 03.241.0032Sealing foam rubber grey (mortar plate)18 1 03.007.0093Lid axle19 1 03.861.0022Sealing washer Ø172x140x4 (Sealing ring mortar lid )20 1 03.409.0176Scraper linking bar RM200 complete (welded, incl. bushing)21 1 03.409.0177Scraper clamp22 1 03.403.0052Bearing bushing scraper (bronze)24 1 03.862.0011Scraper Vulkollan®25 1 03.642.0015Spindle scraper adjustment26 2 03.070.0057Setting knob (scraper + pestle )27 1 03.406.0010Bearing plate pestle28 1 03.403.0049Bearing flange pestle29 1 03.403.0055Bearing sleeve pestle30 1 03.261.0040Retainer pestle snapper (for O ring)31 1 03.658.0004Clamping sleeve pestle (handle)32 1 03.706.0254Support ring pestle bearing top33 1 03.112.0073Spacer sleeve spring pestle clamping device34 1 03.390.0004Clamping plate for pestle spring (VA spring steel)35 2 03.089.0020Spacer sleeve bearing plate P36 1 03.403.0054Bearing bushing bearing plate P (bronze)37 1 03.403.0053Bearing block pestle plate38 1 03.642.0014Spindle pestle adjustment39 1 03.243.0054Rubber bump stop (head plate + housing flange rear) dia. 12x340 1 03.009.0074Cover plate (rear)41 1 03.731.0479Sign Retsch Logo sticker42 1 03.243.0058Rubber sealing top hood - bearing flange P.43 1 03.731.0453Type plate44 1 03.731.0441Caution sign45 1 03.731.0495Plate with device name RM20046 1 03.731.0473Plate with Retsch Internet Logo47 2 03.243.0056Rubber bump stop for window RM20048 3 03.042.0319Bolt lock RM20049 1 03.867.0068Lock handle RM20050 1 03.867.0069Lock hook RM20051 1 03.867.0070Lock pusher RM20052 1 03.867.0071Lock holder RM20053 2 03.181.0102Leg spring lock RM20054 2 03.706.0268Washer retainer bottom 10.5x24x1 for pestle plate55 2 03.706.0267Washer retainer top 6.5 x 24 x 1.5 pestle plate56 1 03.706.0266Washer pivot bearing top 8.5 x 24 x 1.5 pestle plate57 1 03.706.0265Washer pivot bearing bottom 12.5 x 28 x 1 pestle plate58 1 03.243.0059Sealing washer bottom pestle head plate cellular polyurethane elastomer59 1 03.713.0065RM200 divider foam Cellofoam 460UL100 2 05.043.0164Collar bushing lid bearing GFM 12-14-15102 1 05.111.0019Sealing ring plate bearing Nilos 3206 av103 1 05.111.0186Sealing foam rubber bottom panel 0.6 m104 1 05.111.0079Sealing ring G 28-37-4105 1 05.114.0091O-Ring pestle arresting device dia. 24 x 4 FPM106 1 05.181.0070Pressure spring pestle clamping device107 1 05.230.0008Device plug (socket + fuse tray)108 4 05.231.0008Plain bearings bearing bushings IGUS GFM 081014-06109 4 05.727.0051Clamp to fix cables in place110 6 05.481.0008Blind rivet for cable clamp dia. 3111 2 05.484.0009Needle bearing pestle NK28-20112 1 05.617.0022Ball bearings 6201 2RS (pestle clamping device)113 1 05.641.0010Scale pestle114 1 08.647.0009Lock washer DIN 6799-10 mm for fixing the small ball bearings in place115 1 05.703.0168Switch (ON-OFF)116 0 05.703.0249Magnetic switch on the lid 29G2326117 3 05.368.0034Ball pestle arresting device (milling balls VA) dia. 5 mm118 1 05.737.0003Angular ball bearing plate119 8 05.710.0053Screw WN 1747 –K50 x 14 for panel top/bottom120 1 08.182.0026Flat head screw DIN 923 M6 x 8 for bearing block pestle pl.121 0 05.569.0020Hall sensor cykn8-02clo (contained in the cable harness)122 1 08.933.0190Cylinder head screw DIN 7984 M6x25 (for scraper) A2124 4 05.710.0072Screw Remform® 5x20for hood Torx Arnold forming technology WN156-3125 1 05.005.0020Rubber shock absorber scraper M5 dia.15 x 15 60° Shore A126 6 05.231.0021Sliding discs bearing plate P IGUS GTM 12-24-015127 1 08.221.0065Threaded pin M8x35 for pestle bearing plate128 2 08.221.0072Threaded pin M6x35 for pestle bearing plate129 3 08.933.0050Cylinder head screw M5x12 DIN 912 for pestle flange130 2 08.523.0021Adjusting washer 10x16x1 for pestle plate131 2 08.221.0071Set screw M4x4 45H DIN 916 with cup point for rotary knobs132 3 08.933.0068Cylinder head screw M6x35 DIN 933 for housing flange133 2 08.221.0060Set screw M5x5 A2 DIN 914 with cone point for lid axle and rubber buffer lock134 1 08.701.0018Washer A6.4 DIN 125 A2 for screw scraper bearing135 1 08.781.0008Belleville washer C25 A2 DIN 2093 (0.7 mm) for pestle plate pivot bearing136 2 08.781.0009Belleville washer C20 A2 DIN 2093 (0.5 mm) for pestle plate retainers on the right137 1 03.731.0451ISO 9001 sticker138 4 08.642.0006Hexagonal nut M5 A2K for fixing the motor in place139 4 08.701.0005Washer DIN 125 for fixing the motor in place A2K140 5 08.401.0006Pan head screw with cross recess M4x8 DIN 7985 for panel box rear and cover plate rear 141 13 05.453.0006 Round magnet for Hall sensor speed measuring and lid switch143 5 05.710.0052Ejot screw for control146 2 08.643.0020Countersunk head screw M5x16 A2 for lock hook150 2 05.710.0073Countersunk head screw 3x10 for hinge window on the right151 1 05.710.0074Countersunk head screw M4x10 Torx A2 for scraper152 1 08.643.0038Countersunk head screw M5x8 DIN 7991 A2 for rubber buffer scraper153 2 03.710.0075Countersunk head screw 3x15 for hinge window on the left。
2017-2018 Honda Clarity 车身维修信息手册说明书
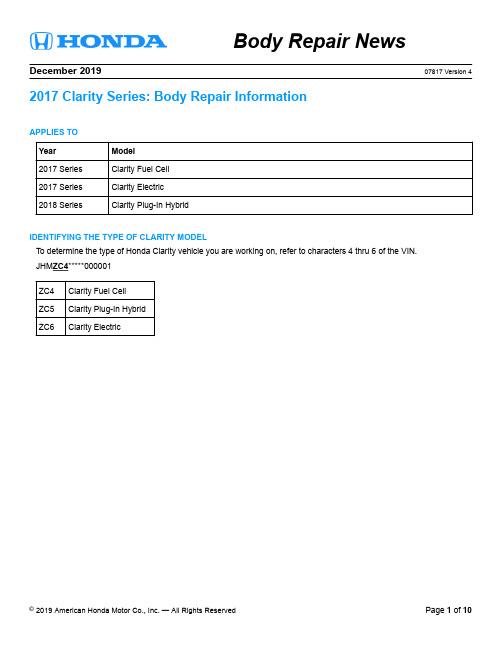
Body Repair NewsDecember 201907817 Version 4 2017 Clarity Series: Body Repair InformationAPPLIES TOYear Model2017 Series Clarity Fuel Cell2017 Series Clarity Electric2018 Series Clarity Plug-In HybridIDENTIFYING THE TYPE OF CLARITY MODELTo determine the type of Honda Clarity vehicle you are working on, refer to characters 4 thru 6 of the VIN.JHM ZC4*****000001ZC4Clarity Fuel CellZC5Clarity Plug-In HybridZC6Clarity ElectricOVERVIEW OF BODY FEATURES•Advanced Compatibility Engineering™ (ACE™) body structure•The same basic body platform supports three electric-powered model variations•Body construction using 52% lightweight materials, including aluminum and ultra-high-strength steel (UHSS - 980 MPa and higher)•World’s first Glass Fiber Reinforced Polymer/Plastic (GFRP) rear bumper beam•Bolt-on resin composite front bulkhead assemblyBODY TECHNOLOGYBODY CONSTRUCTION AND HIGH-STRENGTH STEEL CONTENT•Steel parts are color coded based on their tensile strength in megapascals (MPa).•High-strength steel (HSS) is defined as any steel with a tensile strength of 340 MPa or higher.•Ultra-high-strength steel (UHSS) is defined as any steel with a tensile strength of 980 MPa or higher.•Steel repair and welding procedures vary depending on the tensile strength of the parts involved.These illustrations are for general reference only. Some body parts are constructed from multiple layers of different tensile strength steels. Always refer to the body repair manual body construction section for specific steel tensile strength information.ALUMINUM PARTS & REPAIRABILITYThe following parts are made from aluminum alloy:•Front Bumper Beam•Hood Panel•Front Fenders•Front and Rear Doors•Rear Shelf Panels•Trunk Lid•Front and Rear Subframe (Not Shown)1,500 MPa (HOT STAMP) STEEL LOCATIONS1,500 MPa steel is stronger than ordinary steel, so it can help protect vehicle occupants while reducing overall vehicle weight to improve fuel efficiency.The following numbered parts are constructed of 1,500 MPa steel:1.Front Inner Upper Panel2.Front Pillar Upper Stiffener3.Front Side Frame Extension4.Front Pillar Lower Stiffener5.Side Sill Reinforcement6.Center Pillar Upper Stiffener7.Rood Side Stiffener8.Floor Crossmember Stiffener1,500 MPa stiffeners are located inside the front floor frame, front floor crossmember, and front floor rear crossmember.RESIN COMPOSITE (PLASTIC) FRONT BULKHEADThis vehicle has a lower bulkhead assembly constructed of resin composite material.•The bulkhead design improves engine compartment access during factory assembly and service.•The front bulkhead is attached with multiple bolts and is sold and replaced only as a complete assembly.•The cooling fans, radiator, A/C condenser, hood lock, outside air temperature sensor, and related piping/ components are attached to the front bulkhead.•Over-torquing or using power tools may break these inserts loose, requiring front bulkhead replacement.• A damaged bulkhead must be replaced, not repaired.•For more information, refer to the Front Bulkhead Replacement section in the service information.LASER-BRAZED ROOF ATTACHMENTThe factory roof panel is attached using a laser-brazed joint to the outer side panels.•Laser-brazed joints cannot be duplicated during roof panel replacement.•The original roof panel must be cut off near the lazer-brazed joint, and the remaining flange must be removed separately.•The service roof panel is attached using service replacement bolted clamp-type brackets (5 each side) and panel bonding adhesive.•The roof panel, service brackets, and bolts must be ordered separately. Refer to the online parts catalog.•Refer to the Roof Panel Replacement section in the body repair manual.BEFORE STARTING COLLISION REPAIRSWith any collision repairs, always refer to and follow the information outlined in the Generation Information section of the body repair manual. The following information outlines special consideration when repairing a Honda Clarity vehicle. IPU (Intelligent Power Unit) Leak Test After Airbag DeploymentThis unit applies to the following vehicles:•Clarity Electric•Clarity Plug-In HybridAn IPU leak test must be done on any Clarity Electric or Clarity Plug-In Hybrid involved in a collision severe enough to deploy the airbags. This test consists of pressurizing the IPU with shop air to check for any leaks. If the IPU fails the leak test, it must be replaced.The Clarity Electric has a front and rear IPU. Both of these units must be tested. If you have a vehicle with deployed airbags, take it to an authorized Honda dealer to have this test done before starting any repairs.High-Voltage System ComponentsThese components apply to the following vehicles:•Clarity Electric•Clarity Plug-In Hybrid•Clarity Fuel CellIf you are doing any repairs that require the removal of high-voltage system components, the vehicle must be taken to an authorized Honda dealer. Authorized Honda dealers have the training and equipment needed to remove and install high-voltage components.Refer to the Electrical Powertrain Component Location Index in the service information for a complete list of high-voltage system components.Hydrogen System/Fuel Cell System ComponentsThese components apply to the Clarity Fuel CellAccording to the California Fire Code, the hydrogen level in the hydrogen tanks must be less than 0.5 kg before the vehicle is brought inside the shop for repairs related to the hydrogen system. These rules do not apply to service/repair of non-hydrogen system components and collision repairs as long as no repairs involving welding or open flame are done and the hydrogen system components are not involved.If you are doing any repairs that involve any hydrogen system or fuel cell system-related components or involve welding or open flame, the vehicle must be taken to an authorized Honda Clarity Fuel Cell dealer. For a list of authorized Honda Clarity Fuel Cell dealers, refer to page 10.Refer to the Fuel Cell System Component Location Index in the service information for a complete list of hydrogen/fuel cell system components.DURING COLLISION REPAIRSWith any collision repairs, always refer to and follow the information outlined in the General Information section of the body repair manual. The following information outlines special precautions when repairing a Honda Clarity. Precautions When Using a Heated Paint BoothSystem PrecautionsSRS•Do not apply heat greater than 212°F (100°C) when drying painted surfacesanywhere around the SRS components.Fuel Cell•When drying paint in a heated paint booth, cover the air intake duct, exhaust pipe,and ventilation ducts with tape. Refer to the Fuel Cell System Component LocationIndex in the service information for the location of these components.•High temperature may damage the fuel cell (FC) stack and the compressedhydrogen gas (CHG) tank. When drying paint in a heated paint booth, make sure thetemperature does not exceed 149°F (65°C).Electric Powertrain•High temperature may damage the battery module. When drying paint in a heatedpaint booth, make sure the temperature does not exceed 149°F (65°C).AFTER COLLISION REPAIRSCollision Shut-off History Clear CommandWhen the battery condition monitor module receives a collision detection signal (CDS) from the SRS unit or the H2 (hydrogen) shut-off unit (Clarity Fuel Cell only), it updates the collision shut-off history and stores it in the module’s nonvolatile memory. The battery condition monitor module stops supplying power to the high-voltage circuits, disrupting the control signal to be sent to the high-voltage contactor inside the battery module the next time the system is being turned on.The battery condition monitor module also stops supplying hydrogen to the fuel cell (FC) stack by turning the FC cut relay at the same time. To resume power supply to the high-voltage circuits and hydrogen supply to the FC stack, the collision shut-off history must be cleared.AUTHORIZED HONDA CLARITY DEALERSThe Clarity Electric and Clarity Plug-In Hybrid can be taken to any Honda dealer for service and repairs. To locate an authorized Honda dealer, contact Honda Customer Service at (800) 999-1009.Clarity Fuel Cell repairs should be done only by Authorized Clarity Fuel Cell dealers. For a list of authorized Clarity Fuel Cell dealers, see below.Southern CaliforniaCity Dealer Name Telephone NumberCerritos Norm Reeves Honda Superstore(888) 849-4466Culver City Culver City Honda(424) 298-4875Irvine Norm Reeves Honda Superstore Irvine(888) 721-4053Pasadena Honda of Pasadena(866) 788-5832Torrance Scott Robinson Honda(855) 725-2211Woodland Hills Woodland Hills Honda(800) 494-1164Northern CaliforniaCity Dealer Name Telephone NumberColma Honda of Serramonte(888) 892-5396Dublin Dublin Honda(877) 412-7199Oakland Honda of Oakland(800) 352-1859Palo Alto Anderson Honda(650) 843-6041Roseville AutoNation Honda Roseville(916) 467-8056San Jose Honda of Stevens Creek(855) 357-6146。
莫瑞德独立悬挂系统维修手册说明书
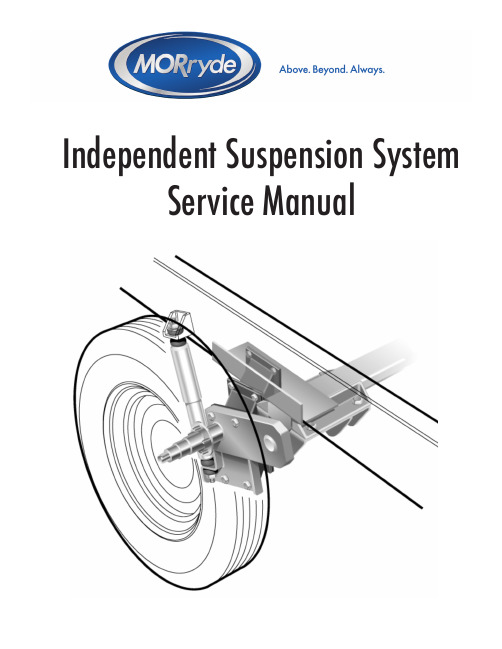
Independent Suspension SystemService ManualIndependent Suspension SystemCONTENTSINTRODUCTION (2)MAINTENANCE (3)SERVICE..............................................................................................................................3-5SUSPENSION ALIGNMENT (5)TROUBLE SHOOTING AND TORQUE CHART..........................................................6-7INTRODUCTIONDESCRIPTIONThe MORryde “IS” Independent Rubber Suspension System uses 100% Natural Rubber Springs to support the trailer weight and absorb road shock. By absorbing the shock, the rubber provides a much smoother towing experience than steel leaf springs. With the new MORryde “IS” Independent Rubber Suspension System, there are no more broken leaf springs! The towing is virtually hassle-free with the smoothest towing available for fifth wheels and travel trailers.The Primary benefits that you can expect from the MORryde ”IS” suspension are:SMOOTHER TOWING - the MORryde suspension has up to 2 1/2 times the suspension travel of leaf springs or rubber axles, allowing the MORryde suspension to absorb road shock much better.IMPROVED TOWABILITY - the MORryde suspension is designed to “block” body roll, improving the cornering and stability of the tow vehicle and trailer combination.AUTOMOTIVE STYLE ALIGNMENT - a MORryde first! You can manage your tire wear through toe and camber adjustments, a feature no other towable suspension offers!HEIGHT ADJUSTABILITY - the MORryde suspension can be adjusted easily to accommodate different tow heights and to compensate for side-to-side load variations.PROVEN DURABILITY - the MORryde suspension has undergone strenuous testing to prove it’s durability. The result? No more broken leaf springs!U.S. PAT. NO. 5,899,470MAINTENANCEMaintenance to the MORryde “IS” suspension system is minimal. For service information regarding bearing options or braking systems on your trailer, please consult the appropriate brake/axle manufacturer.LUBRICATIONAfter November of 2001, the “IS” journal shaft will have a grease zerk on the under side of the “IS” torque bracket. It should be greased every 12 months or 6000 miles.SHOCK ABSORBER MAINTENANCEThe shock absorbers used on the MORryde “IS” rubber suspension are sealed, hydraulic type and require no periodic maintenance. Shock absorbers of this type should be checked every 10,000 miles to make sure they are functioning satisfactorily, bushings are not worn, and the dust cover has not been damaged by flying stones or debris from the road. If a shock absorber is leaking, fails to operate, or develops an unusual noise, the shock absorber should be replaced.SERVICENOTE: ALL SERVICE PROCEDURES MUST BE PERFORMED WITH THE VEHICLE SUPPORTED AT THE FRAME WITH APPROPRIATELY RATED SAFETY STANDS AND JACKS.PROCEDURES FOR JACKING UP UNITIt is permissible to jack up a unit equipped with a MORryde Independent Rubber Suspension System only on the Beam Assembly under the Rubber Springs or the frame of the trailer. The most efficient location to raise a trailer is at the frame. Jacks and safety stands should be positioned towards the front and rear portion of the trailer frame. To perform suspension work tires should be approximately 4” above the ground.INSPECTION/REPLACEMENT OF RUBBER SPRINGSMORryde rubber springs are made of a special formulation of natural rubber. The rubber springs are vulcanized (bonded) to steel plates. There are two unlikely problems that may occur with MORryde rubber springs:1. The first type is bond failure. This condition is apparent when the rubber separates from the metalplate.2. The second type is a rubber failure. This condition is apparent when the rubber tears ordelaminates and generally occurs in the middle of the rubber spring between the metal plates. Either of the conditions described above would not always necessitate replacement of the rubber spring. If there is a question about the integrity of a marginal rubber spring, a 3” wide object (such as a 3” putty knife) can be used to probe the rubber spring in the affected area. (If the probe penetrates the crack or separation .75” or more, the spring should be replaced). Rubber Springs should be inspected when supporting the trailer.REPLACEMENT OF A RUBBER SPRING ASSEMBLY1. Raise the unit until the tires are approximately 4” off the ground, the frame is supported with safety stands and the suspension is hanging unsupported.2. Remove both tires on the side of the unit the Rubber Springs are to be replaced.3. Loosen or cut loose brake wires to obtain slack.4. Remove 3/8” bolts securing Rubber Springs to Hanger Assembly and Beam Assembly.5. Pry rubber springs out from between the Beam Assembly and the Hanger Assembly.6. Align and bolt the rubber spring assembly to the Hanger Assembly. Drift pins can be used to align the bolt holes on the Beam Assembly with the Rubber Spring bolt holes (a bottle or floor jack may be needed to raise the Beam Assembly and the bolt holes of the Rubber Spring).7. Reinstall the shocks.8. Use heat-shrink connectors to reconnect brake wires. Use tie straps to secure brake wires out of harms way of Beam Assembly, Rubber Springs and Shock Absorbers.9. Reinstall tires, torque all bolts and remove jack standREPLACEMENT OF SHOCK ABSORBERThere are two (2) shock absorbers utilized on the MORryde Independent Rubber Suspension System, per axle. These shock absorbers are made by Monroe. They have special valving and stroke length specifically designed for the MORryde suspension. They are rarely available through Monroe after market dealers. Consult with MORryde directly for replacements. Refer to figure below.1. Fastener Nut2. Washer3. Rubber Bushing To replace a shock absorber:1. Remove fasteners.2. Remove shock absorber.3. Install new bushings on new shock absorber per exploded illustration above.4. Install new shock absorber.5. Torque fasteners per Torque Chart in Specification section.4. Clip welded to trailer frame5. Shock Absorber6. Clip welded to Beam AssemblyREPLACEMENT OF BEAM ASSEMBLYThe Beam Assembly attaches the wheel and rubber suspension to the Hanger Assembly, which is welded to the frame of the coach. Should a beam and or spindle become damaged and need to be replaced follow the steps below.1. Jack up the unit (see procedure for jacking up unit).2. Remove tires.3. Remove wheel drum and backing plate, which contains the brakes.4. Remove Rubber Shear Springs from the Beam Assembly.5. Remove shock at the lower end.6. Remove nuts and washer at the end of the journal bar (toward inside of frame).7. Pull out the Beam Assembly.8. Slide in new Beam Assembly. Bearings should be replaced if damaged or worn.9. Reinstall nuts in the journal bar, then the shock, spring, backing plate and wheel drum.10. Appropriately torque all nuts and bolts (see torque chart)11. Reinstall the tires and wheels.SUSPENSION ALIGNMENTThe MORryde independent suspension system allows for automotive style toe and camber wheel alignment. This allows you to manage your RV’s tire wear as effectively as you manage yourtow vehicle. There are four bolts per wheel, which allow for these adjustments. Always adjust the CAMBER first, followed by the TOE.ADJUSTING THE CAMBER1. Connect the alignment machine and level the unit on the alignment turntables.2. If camber is negative, add a shim to the outside of the Torque Bracket.3. If camber is positive, add a shim to the inside of the Torque Bracket.4. Shims are available in three sizes - 1/4”, 1/8”, and 1/16”.25”5. A 1⁄4” shim will change the camber approximately 1 degree.6. To decrease camber, loosen the four Torque Bracket bolts and remove the 3⁄4” bolts one at a timeto install shims.7. Unit will need to be raised to add camber.8. Appropriately torque all bolts.ADJUSTING THE TOE1. Connect the alignment machine and level the unit on the alignment turn tables.2. Loosen the four bolts holding the Torque Bracket to the Hanger Assembly.3. Move the Torque Bracket Assembly to obtain the correct toe readings on the alignment machine.4. Tighten the Torque Bracket bolts.5. Raising the coach is not required to adjust the toe.6. Toe adjustment can be accomplished with a “port-a-power” or large alignment bar.7. Appropriately torque all bolts.The following list covers the most frequent cause for concern, which may arise with the MORryde Independent Suspension System. If a problem occurs that is not addressed here, please contact MORryde International direct for further service information at 574- 293-1581.Problem / Symptom CorrectionCause• Excessive tire wear• Shock absorbers are worn • Tires not aligned• Worn torque bracket bearing• Worn shock absorbers• Improper tire pressure• Improper rubber springdeflection• Worn shock absorbers• Tires rubber on wheel wellor the suspension bottomingout• Improper tire pressure• Torn rubber shear spring• Improper hitch weight• Call MORryde for differentdensity of rubber spring• Replace shock absorber• If spring deflection is correctand height adjustment isnot sufficient, a spacertube needs to be weldedbetween the frame and the“IS” system.• Adjust air pressure• Replace rubber shear spring• Travel trailers should have10%-12% height weight. Fifthwheel trailers should have20%-25% height weight.• Have tires re-aligned• Have the bearings replaced• Replace shock absorber• Adjust air pressure• Rough ride• Excessive swayTROUBLE SHOOTINGTORQUE CHARTBolt Size Grade 8Grade 51/4-20 5/16-18 3/8-16 7/16-14 1/2-13 5/8-11 5/8-18 3/4-107142540601151251901020355590170185280Torque values must be verified with a torque wrench. A calibrated pneumatic impact wrench is not acceptable substitute.AXLE BRAKE INFORMATIONThe MORryde “IS” can utilize several different sizes of brakes. Systems that are factory installed may have different brake components than those systems that are installed after market. In an aftermarket installation, it is possible to upgrade braking systems to use a larger brake such as 12-1⁄/4” x 2-1⁄/2”or 12-1⁄/4” x 3-3/8” brakes or to disc brakes. If after market customers are not upgrading their braking system at the time of installation, the existing braking system on the trailer or fifth wheel will be used. For more brake information, consult your owner’s manual of your trailer or contact MORryde for a more detailed discussion on brake options.PLEASE DIRECT ALL CORRESPONDENCE TO:MORryde International1966 Sterling Ave.Elkhart, IN 46516Phone: (574) 293-1581Fax: (574) 294-4936Email:*******************。
ALINCO DR-620 中文使用说明

ALINCO DR-620 中文使用说明ALINCO DR-620 。
特别提醒禁止将主机或控制面板安装在可能影响驾驶或造成身体伤害的位置禁止将主机或控制面板安装在可能影响放撞气囊工作的位置不要将主机或控制面板安装在可能被冷气热风直吹的地方避免阳光直射ALINCO DR-620 。
面板按键名称及功能PWR 键电源开关键V/M/MW 在VFO 和信道模式之间切换DIAL 改变频率存储信道和不同的功能设定BAND/VVUU 切换主频段为VHF 或UHFCALL/RX BAND 切换到呼叫信道MHZ/SHIFT 在VFO 模式以1MHZ 的频率改变11 TSDCS/LOCK 设定音频静噪和DCS 设定12 HL/PACKET 切换HI/MID/LOW 三档发射功率13 SQL/DIGITAL 设定静噪电平14 FUNC/SET 设定功能15 MIC.CONNECTOR 手咪连接口按FUNC 键后屏幕出现F 字样时的功能第二功能V/M/MW 写入存储信道BAND/VVUU 切换到VV/UU 模式CALL/RXBAND 切换接收波段MHZ/SHIFT 设定偏频方向和差频频率11 TSDCS/LOCK 设定键盘锁功能12 HL/PACKET 包装通讯模式13 SQL/DIGITAL 存取数字通讯模式ALINCO DR-620 。
No. Key 功能1 当FUNC 键被按下时显示2 AM 在AM 模式接收时显示3 Mi 发射功率设定为中档时显示4 Lo 发射功率设定为低档时显示5 Nar 处于窄带接收模式时显示6 +/-设定频偏时显示7 T.SQ 设定音频静噪时显示8 DCS 设定DCS 时显示9 SUB 备用波段在主波段位置时显示*10 键盘锁定时显示11 * 设定失窃告警时显示12 TNC 处于包封通讯模式时显示需要EJ-50U 选件13 备用波段处于存储模式或呼叫模式时显示14 R 倒频使用时显示15 处于数字语音通讯模式时显示16 设定寻呼呼叫音功能时显示17 在备用波段指示频率或存储信道名18 S METER 在备用波段指示接收信号强度或发射功率19 在备用波段收到信号时显示20 主波段指示频率或存储信道名21 S METER 在主波段指示接收信号强度或发射功率22 小数点当改变DCS 代码设定时显示/当处于信道扫描时指示23 指示一个信号在主波段被接收24 SQL 当设定静噪电平时显示25 在存储信道模式时指示信道名。
重庆力帆LF620售后服务(汽车维修)培训手册 03.第一章 电喷系统
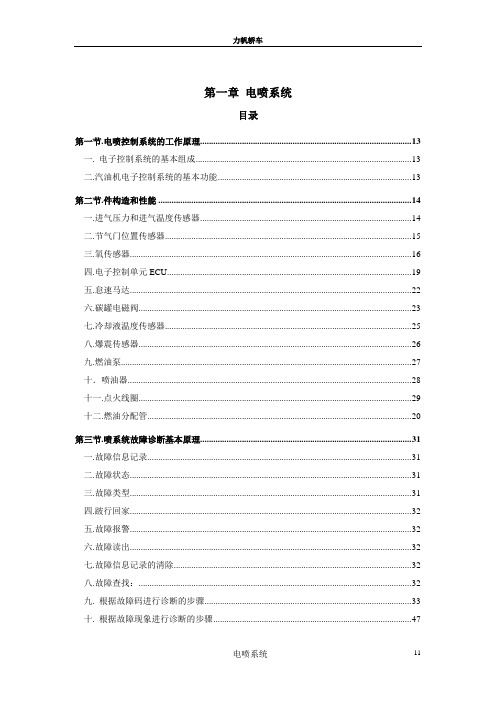
第一章电喷系统目录第一节.电喷控制系统的工作原理 (13)一. 电子控制系统的基本组成 (13)二.汽油机电子控制系统的基本功能 (13)第二节.件构造和性能 (14)一.进气压力和进气温度传感器 (14)二.节气门位置传感器 (15)三.氧传感器 (16)四.电子控制单元ECU (19)五.怠速马达 (22)六.碳罐电磁阀 (23)七.冷却液温度传感器 (25)八.爆震传感器 (26)九.燃油泵 (27)十.喷油器 (28)十一.点火线圈 (29)十二.燃油分配管 (20)第三节.喷系统故障诊断基本原理 (31)一.故障信息记录 (31)二.故障状态 (31)三.故障类型 (31)四.跛行回家 (32)五.故障报警 (32)六.故障读出 (32)七.故障信息记录的清除 (32)八.故障查找: (32)九. 根据故障码进行诊断的步骤 (33)十. 根据故障现象进行诊断的步骤 (47)第四节.统维修安全事项 (62)一.汽油喷射电子控制系统诊断维修注意安全事项 (62)二.安全措施 (62)第一节、电喷控制系统概述一. 电子控制系统的基本组成任何电子控制系统,都是由以下三部份组成的:1.传感器——将发动机的各种非电学物理量转变成电学量,借此将各种信息提供给子控制单元。
·用于力帆1.6(TRITEC)系统电子控制系统的传感器有:·进气压力温度传感器;·节气门位置传感器;·冷却液温度传感器;·氧传感器;·爆震传感器;·曲轴位置传感器;2 电子控制单元——是整个电子控制系统的大脑,英文缩写成ECU。
它对传感器提供的各种信息进行分析和处理,将得出的结论以指令的形式发送给执行器,从而使发动机在优化的状态下运行。
3 执行器——执行电子控制单元的指令。
执行器是电子控制系统的手脚。
用于电子控制系统的执行器有:·燃油泵·喷油器·点火线圈·带步进电机的怠速执行器·炭罐控制阀二.汽油机电子控制系统的基本功能这是汽油机电子控制系统最重要的功能,对汽油机的动力性、经济性和排放以及整车的行驶性和舒适性有举足轻重的作用,涉及λ闭环控制、起动控制、起动后控制、暖机控制、怠速控制(即怠速转速控制)、部分负荷控制、全负荷控制、加速减速控制、超速断油控制、倒拖断油控制和蒸发排放物控制(炭罐控制)等。
美国机器与工具公司4英寸垃圾泵维修部件手册说明书

Please read and save this Repair Parts Manual. Read this manual and the General Operating Instructions carefully before attempting to assemble, install, operate or maintain the product described. Protect yourself and others by observing all safety information. The Safety Instructions are contained in the General Operating Instructions. Failure to comply with the safety instructions accompanying this product could result in personal injury and/or property damage! Retain instructions for future reference. AMT reserves the right to discontinue any model or change specifications at any time without incurring any obligation.©2010 American Machine & Tool Co., Inc. of PA, A Subsidiary of The Gorman-Rupp Company, All Rights Reserved.Periodic m aintenance and inspection is required on all pum ps to insure proper operation. Unit m ust be clear of debris and sedim ent. Inspect for leaks andloose bolts. Failure to do so voids warranty.4-INCH TRASH PUMPRefer to pump manual 1808-633-00 for General Operating and Safety Instructions.DescriptionThis trash pump is a heavy duty, centrifugal, engine-driven, self-priming (to 20 ft. lift after initially filling casing with liquid), portable unit. Pump is equipped with precision lapped mechanical seal to reduce the likelihood of leakage, and a clog-resistant impeller capable of handling solids up to 2" diameter. Units are used to handle water containing stones, sticks, mud and other solids (up to 25% by volume). O-ring sealed flange connections facilitate easy removal of suction and discharge lines. Handles liquids from 40º to 180º F (4ºto 82º C). For use with nonflammable fluids compatible with pump component materials.All models come standard with manual recoil starter, E-start models 3993-96, 3993-D6 and 3994-96 feature in addition a 12V electric starter switch and cables. 5" W x 7¾" L x 5" H battery holder included. (Battery not included; obtain 12V, 32 amp hour battery from local lawn and garden shop).Pump and engine are mounted on rugged transport dolly with fully pneumatic 16" ball bearing wheels. Proper weight distribution ensures easy portability, yet pump is stable when operating. Four position discharge manifold provides a choice in placing hose.SpecificationsSuction inlet...........4" MNPT Discharge outlet........4" MNPT Engine4210-96....1 CY B&S Vanguard 3993-96*...2 CY B&S Vanguard 3994-96*........Honda GX390 3993-D6*...Yanmar Diesel L100 *E-Start ModelsBasic construction.Aluminum with cast iron volute, impeller, wear-plates and discharge manifold;silicon carbide seal. Battery.....12 Volt, type No. 9A1, 32 amp hour (not supplied) Battery tray*..5" W x 7¾" L x 5" H (*E-Start Models)UnpackingRefer to Repair Parts Illustration and Repair Parts List to aid in identifying parts. Unpack and separate all pump components from container, making sure all parts are accounted for. Packages should contain:1.Pump and engine completelyassembled on wheel kit.2.Battery tray (Ref. No. 37) andbattery tray hardware (E-startmodels only).3.4" NPT Nipple Pack and Strainer.ASSEMBLY (Refer to Figure 2)1.Remove pump from packaging.2.Stand pump carefully on pump end.Reposition handle (Ref. No. 32) (asshown in Figure 2) facing outwardsby removing and replacing existinghandle fasteners.3.Electric Start Models Only: Attachbattery tray (Ref. No. 37) to leftengine rail using fasteners used withhandle. Install a 12 volt type no. 9A1garden tractor battery 32 amp hourrating, approx. size 7¾" L x 5" W x6" H (not included) onto battery tray.Using hardware included with pump,insert hook bolts through battery trayholes, thread facing up. Attachbattery box holddown bar acrossbattery and thread wing nuts ontohook bolts. Refer to engine manualfor proper wiring instructions.MaintenanceMECHANICAL SEAL REPLACEMENTRefer to Figures 1 and 2NOTE: Always replace the seal seat(Ref. No. 8), seal head (Ref. No. 9) andshaft sleeve (Ref. No. 10) to ensureproper mating of mechanical sealcomponents!Figure 11.Unthread cap screws (Ref. No. 30)and remove casing (Ref. No. 18)and casing seal (Ref. No. 7) fromadapter (Ref. No. 6).2.Unthread screws (Ref. No. 14) andremove volute (Ref. No. 13) fromadapter.3.Unscrew impeller (Ref. No. 12)from the engine shaft. Remove theimpeller shim (Ref. No. 11), shaftsleeve and seal head from engineshaft. Use a rubber mallet or softblock of wood to loosen impeller.Turn it counterclockwise.Disconnectspark plug wireand battery toprevent accidental starting.3993-251-00 03/20114.Unthread cap screws (Ref. No. 4)and remove the adapter from theengine mounting face.5.Push seal seat from the adapterrecess with a screwdriver.6.Clean the adapter recess beforeinserting a new seal seat.7.Carefully wipe the polishedsurface of the new seal seat witha clean cloth.8.Wet the rubber portion of the sealseat with a light coating of soapywater.9.Press the new seal seat squarelyinto the cavity in the adapter. Ifthe seal seat does not presssquarely into the cavity, it can beadjusted in place by pushing on itwith a piece of pipe. Always use apiece of cardboard between thepipe and the seal seat to avoidscratching the seal seat. (This is alapped surface and must behandled very carefully).10.After the seal seat is in place,ensure that it is clean and has notbeen marred.ing a clean cloth, wipe the shaftand make certain that it isperfectly clean.12.Secure the adapter on the enginemounting face.NOTE: Tighten cap screws EVENLY to avoid cocking rabbet on engine mounting face.13.Apply a light coating of soapywater to the inside rubber portionof seal head and slide onto theshaft sleeve. Slip the shaft sleevewith seal head onto the engineshaft.IMPORTANT: Before installing new shaft sleeve, apply a bead of non-hardening, pliable sealant (such as Permatex® Form-A-Gasket® No. 2) to motor shaft shoulder.Do not touch orwipe the face of the polished part of the seal head.14.Replace any impeller shimsremoved in disassembly.15.Screw the impeller back in placetightening until it is seated againstshims and shaft sleeve.NOTE: Check to ensure that the shaft flange (Ref. No. 2) is in place against engine shaft shoulder.16.Remount volute with fasteners.17.Refer to section titled ShimAdjustment at this time if shaftsleeve or any other parts listedtherein have been replaced.18.Inspect position of flapper valveassembly (Ref. No. 16) to ensureproper movement and sealing.19.Replace O-ring seal on voluterabbet.NOTE: Always inspect O-ring seals.Replace when cracked or worn. WetO-ring with soapy water for ease ofassembly.20.Remount casing.21.Remount any other parts andreconnect spark plug wire andbattery (if so equipped). Pumpshould now run with renewedoriginal performance.SHIM ADJUSTMENT1.When installing a replacementimpeller, engine, shaft sleeve,adapter, or volute, it may benecessary to vary the number ofimpeller shims (Ref. No. 11) that willbe required. This is easily done byadding one shim more than wasremoved and reassembling thepump as described in MechanicalSeal Replacement section.2.Ensure that volute (Ref. No. 13) andadapter (Ref. No. 6) are fitted firmly(check fastener Ref. No. 4 and 14).Remove spark plug wire from engineand turn engine over by pulling therecoil starter. If engine does not turnfreely, disassemble pump andremove one shim.NOTE: When adding or removing shims,it is best to proceed with a 0.010"increment each time. If engine does turnfreely, add shims until it does strike, thenremove a 0.010" shim. This should allowproper clearance.3.Proper running clearance is 0.010".4.Follow the above procedure untilproper clearance is obtained. Thiswill ensure maximum performance.IMPELLER AND WEARPLATEREPLACEMENTImpeller (Ref. No. 13) and volute/wearplate (Ref. No. 14) are subject towear only by abrasive sand or sedimentladen liquids. If badly worn, all theseparts can be replaced easily and thepump thus restored to full efficiency.NOTE: When the clearance between theimpeller and the volute/wearplateexceeds 1/16" at the face of the impelleror 1/8" on the outside diameter of theimpeller, it may be necessary to takecorrective action. The increasedclearance can cause lengthenedpriming times and reduced pumpingcapacity. If both the priming andcapacity of your unit are satisfactory foryour application, it is recommended thatno corrective maintenance beperformed regardless of whatclearances on your unit may havedeveloped, since the increasedclearances in themselves are notgenerally harmful to your pump.Normally, new pump clearances can berestored by simply shimming behind theimpeller. (Add shim washers, Ref. No.11). If the impeller is badly worn it isrecommended that the impeller bereplaced. This is usually all that isrequired since only on unusuallyabrasive services does the cast ironwearplate show deterioration.Occasionally a stone or hard objectmight get caught in the impeller andcause damage to the volute/cutwater. Inthese cases, follow the instructionsbelow for replacement and refer toFigure 2.1.Disassemble pump for access asdescribed in MECHANICAL SEALREPLACEMENT, steps 1 and 2.2.Replace parts as necessary.NOTE: When replacing volute, attachflapper valve assembly (Ref. No. 16) tonew volute with fasteners (Ref. No. 17).NOTE: Before installing new parts,clean all mating surfaces thoroughly.For information pertaining to the engineand engine parts, consult the EngineManual or contact the nearestauthorized service representative or themanufacturer.CLEANINGThese units are designed so that formost cleanout or clogging problems itshould not be necessary to removehoses or piping. The suction area andimpeller chambers can be reached byremoving (2) threaded handles (Ref. No.25) and removing suction cleanoutcover plate (Ref. No. 27) and gasket(Ref. No. 28).NOTE: When replacing cleanout coverplate, carefully wipe clean all surfaceson which the gasket has contact. Also,make sure the gasket is in position. Thescreen in the spark arrester should bechecked.Specifications Information and Repair Parts Manual3993-96, 3993-D6, 3994-96 and 4120-964。