情境一任务32
工作单1 组建点到点的光传输网-答案
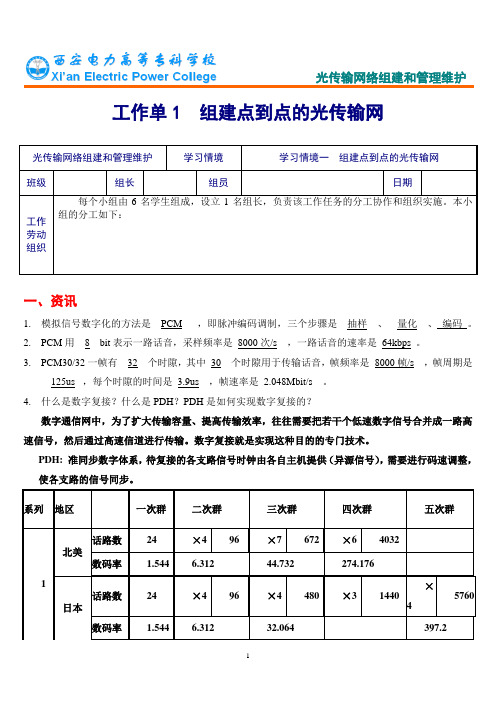
工作单1 组建点到点的光传输网一、资讯1. 模拟信号数字化的方法是__PCM___,即脉冲编码调制,三个步骤是__抽样__、__量化__、_编码 。
2. PCM 用__8__bit 表示一路话音,采样频率是_8000次/s__,一路话音的速率是_64kbps_。
3. PCM30/32一帧有__32__个时隙,其中_30__个时隙用于传输话音,帧频率是_8000帧/s__,帧周期是__125us _,每个时隙的时间是_3.9us__,帧速率是_2.048Mbit/s__。
4. 什么是数字复接?什么是PDH ?PDH 是如何实现数字复接的?数字通信网中,为了扩大传输容量、提高传输效率,往往需要把若干个低速数字信号合并成一路高速信号,然后通过高速信道进行传输。
数字复接就是实现这种目的的专门技术。
PDH: 准同步数字体系,待复接的各支路信号时钟由各自主机提供(异源信号),需要进行码速调整,使各支路的信号同步。
光传输网络组建和管理维护5.PDH有何缺点?(1)接口方面----与设备互联有关电接口方面:PDH具有多种电接口规范,有欧洲系列、北美系列和日本系列标准,我国采用的是欧洲系列标准。
由于不存在世界性标准,因此无法实现多厂家互连互通。
光接口方面:和电接口一样,PDH在光接口方面也没有世界性标准的光接口规范。
各厂家在进行线路编码时,为完成不同的线路监控功能,在信息码后加上不同的冗余码,导致不同厂家同一速率等级的光接口码型和速率也不一样,无法实现多厂家互连互通。
这样在同一传输路线两端必须采用同一厂家的设备,给组网、管理及网络互联带来困难。
(2)复用方式PDH采用异步复用方式通过码速调整(塞入bit)匹配和容纳信号时钟的偏差低速信号在高速信号中的位置无规律性从高速信号插/分低速信号要一级一级进行复用/解复用增加了信号的损伤,不利于大容量传输(3)运行维护方面(OAM)——决定设备维护成本PDH信号的帧结构中用于运行维护工作OAM的开销字节不多,要通过增加冗余码来完成线路性能监控功能。
工程项目管理学习情境一任务一

02
03
团队建设与培训
采取适当的团队建设措施和培训方法, 提高项目团队的协作能力和技能水平。
项目沟通管理
制定沟通计划
根据项目需求和时间计 划,制定详细的沟通计 划,包括沟通目标、沟 通方式、沟通频率和沟 通障碍处理等。
沟通方式选择
根据项目特点和团队成 员的沟通习惯,选择适 当的沟通方式,如会议、 报告、邮件和电话等。
02 工程项目管理基本概念
工程项目的定义与特点
定义
工程项目是指按照一定的建设程 序,在一定的约束条件下,以形 成固定资产为明确目标的一次性 建设事业。
特点
工程项目的特点包括目标明确性 、约束条件性、一次性、整体性 和不可逆性等。
工程项目管理的定义与职能
定义
工程项目管理是指项目管理者在有限 的资源约束下,运用系统的观点、方 法和理论,对项目涉及的全部工作进 行有效地管理,以实现项目的目标。
一款功能强大的项目管理软件,支持项目计划制定、进度 跟踪、资源管理等功能,广泛应用于各类工程项目管理领 域。
Asana
一款团队协作和任务管理软件,支持多项目并行管理、任 务分配、进度跟踪等功能,适用于中小型项目管理。
Trello
一款灵活的项目管理工具,采用看板管理方式,支持任务 清单、进度可视化等功能,适用于敏捷项目管理。
沟通监控与调整
对项目沟通过程进行实 时监控,及时发现和解 决沟通问题,确保项目 信息的有效传递和理解。
项目风险管理
制定风险管理计划
根据项目特点和历史数据,制定详细的风险 管理计划,包括风险识别、风险分析、风险 应对和风险监控等。
风险识别与分析
采用适当的风险识别和分析方法,如头脑风暴、 SWOT分析和概率影响矩阵等,对项目潜在风险进 行识别和分析。
企业经营管理沙盘模拟实训教程训练情境一 实训第一年经营

训练篇 基本方法、经营策略 和分析工具
训练篇 基本方法、经营策略和分析工具
情境一、实训第一年经营 情境二 、实训第二年经营
训练情境一 实训第一年经营
1 分析市场环境 2 投放广告策略 3 订单选择策略 4 竞争对手分析
训练情境一 实训第一年经营
在企业经营沙盘模拟训练中,往往是很多团队在商讨年 初经营战略规划的时候讨论非常热烈,最后也只制定了 广告计划方案,或者只有每个角色孤立的计划,当正式 经营的时候发现销售部门与生产部门、生产部门与采购 部门、财务部门和其他部门的计划不能配合,计划难于 实施。所以需要通过制定企业的总体经营战略规划,并 按照一定的流程进行规划,才能真正做好战略规划,用 于指导企业经营。
市场 本地 本地 本地 区域 区域
数量 2 2 3 2 3
单价 7.5 5.5 6 7.5 6
销售额 账期
15
3
11
2
18
3
15
1
18
2
条件 加急
加急
任务:请为B公司选择出合适的P2产品订单。
任务3 订单选择策略
【任务分析】
订单的选择是企业经营沙盘中的重要环节,这个环 节直接决定了企业产品的销量,进而决定了企业的利 润。在选择订单时,一般应该综合考虑企业可供销售 产品的数量、订单中产品的数量、单价以及账期和交 货期等因素后,做出选择。
训练情境一 实训第一年经营
分析市场
分析竞争对手产能分析
分析企业产能
企业总体 经营思路
(开拓市场、 产品开发、 生产购买等)
制定广告计划,选单 制定生产排程计划 制定采购计划 财务预算和可行性判断
融资 后再 计划
情境教学和任务型教学在一节课中的尝试-主题情境与任务设计

从句、非谓语动词等,然后利用黄金时间紧扣本节课的重点——非谓语动 词, 进行主要学问的分类和概括,新旧学问连接自然。同时还利用多媒体 课件不断地进行新旧学问的比较和质疑,让学生边看图边回答,既学习了 新学问,又稳固了旧学问。
3.多媒体技术与实际生活相结合,整合教学资源。充分运用电脑及网 络资源,开发英语教学资源,拓宽学生学习渠道,改良学生学习方式,提 高教学效果。本模块的任务是主持校内广播,要求学生留心校内内外最近 发生的事,例如植树节的植树活动、硬笔书法大赛、李娜法网赢得了大满 贯、英国威廉王子大婚,等等。既锻炼了学生写作的能力,又使学生充分 利用了网络资源,将网络提供的丰富教学资源融入到了英语教学中。课前 学生把他们收集到的材料,包括照片、文字记录等,经过选择后交给我, 我再做成多媒体课件。这样的内容出如今课堂上,学生感到很傲慢,对教 学内容也很熟识,因为这节课的材料是他们通过自己努力获得的。这是师
3.课堂教学活动多样化,关注全体学生。活动要能够促使学生猎取、
们分成若干组,使每一位学生都有机会主动参加,真正将所学语言学问运 处理和利用信息,用英语与他人沟通,进展用英语解决实际问题的能力;
用到生活中。最终设计实行了任务型教学模式,给学生以自由,让他们自 要有利于学生学习英语学问,进展语言技能,从而提高实际语言运用能力。
二、教学的几点思索
学困生,我设计了简洁的新闻播报和揭皇榜活动。同时,我又设计了小组
1.注重新旧学问连接的同时要注重语言的有用性。这节课我在课前组 商量、小组竞赛活动,让学生在合作中完成学问的积存。
织学生收集素材,并和学生一起处理材料。在课堂上,我真正做到了放手,
4.重点内容的教学方法突出以学生为主体。教师应当擅长发挥主导作
一、教学特色 1.创设情境,激励参加。既然学生是广播节目的主持人,那么就让来 做一下自我介绍,把每个学生自我介绍的场景拍个小短片,并把这个小短 片作为本次课的导入环节。生动的自我介绍的短片很快抓住了学生的兴趣 点,并把他们的心理活动引入到一个新的学问情境,促使学生主动主动地 进入学习状态,让学生迫不及待地想参加,对所要学习的学问产生认识上
2024版高考语文一轮总复习第9章写作第4节情境任务类作文写作pptx课件

二、扣着“任务”写 命题的变化,既带来了审题的变化,更带来了写作要求上的变化。 过去,为了保证审题准确,要求行文过程中扣“题”见“料”;现在, 写作过程中不只要扣“题”见“料”,更要在行文过程中完成多项写作 任务。“任务”落实了吗?是否做到了全面落实?这成为审题是否准确 的实践标准。那么,如何在行文中一一去落实这些“任务”呢?
请从下列任务中任选一个,以青年学生当事人的身份完成写作。 (1)1919年5月4日,在学生集会上的演讲稿。 (2)1949年10月1日,参加开国大典庆祝游行后写给家人的信。 (3)1979年9月15日,参加新生开学典礼后写给同学的信。 (4)2019年4月30日,收看“纪念五四运动100周年大会”后的观后感。 (5)2049年9月30日,写给某位“百年中国功勋人物”的国庆节慰问信。 要求:结合材料,自选角度,确定立意;切合身份,贴合背景;符合文 体特征;不要套作,不得抄袭;不得泄露个人信息;不少于8课时演练
近几年,任务驱动型作文成为新宠,“写作任务”成为它的鲜明 特征。这一作文命题形式改变了高考传统的写作观和写作实践,更具体 地说,它带来了从审题到写作的一系列变化。随着进一步研究和探索, 任务驱动型作文又呈现出新的命题趋势和特点:情境化任务写作,更多 的要求是在真实情境下的任务写作。因此,必须积极应对,从容备考, 尤其是在审题上,要围绕“任务”审;在具体写作过程中,要紧扣“任 务”写。
特别说明的是,任务驱动型作文所提供的材料不少是复合型材料 (如上面材料),理解时要关注两方面:
①将复合型材料从时间、空间、属性等多角度进行分类处理,找 到碎片化材料的内在关联;②仔细研读“引导语”(即“内容指令”), 即对前文材料起概括和总结的句子。
(2)审准“任务”:明确五项任务指令。 ①围绕什么内容写的内容指令。这是审题的关键。有时考生难以 把握命题者试图引导考生围绕一个什么问题展开议论,因而造成作文立 意不明或立意不准的后果。因此,要把材料引导语阅读准,思考清。 ②给了什么样的写作情境。
学习情境一任务一(出版社)

学习情境一:认识典型机械零部件
观看机械零件陈列室
学习情境一:认识典型机械零部件
观看各类模型与实物
学习情境一:认识典型机械零部件
一、机器的组成
两个机器实例:
进气阀3
1.内燃机
功用:内燃机是将燃气燃烧 时的热能转化为机械 能的机器。
活塞2 顶杆8 连杆5
组成:见右图。
曲轴6
齿轮9
排气阀4 气缸体1
内燃机连杆
学习情境一:认识典型机械零部件
三、机器的相关概念
零件装配
学习情境一:认识典型机械零部件
小结
• 1、机器的概念,机器与机构的区别; • 2、零件、构件、部件三者的区别。
完成有用的机械功或转换机械能。
学习情境一:认识典型机械零部件
一、机器的组成
• (二)机器的功能组成
• (1)动力部分:是机器完成预定功能的动力源,应用较多的是电动 机和内燃机。
• (2)执行部分:是直接完成工作任务的部分。 • (3)传动部分:介于动力部分与执行部分之间,用以完成运动和动
力的传递与转换。 • (4)控制部分:是控制机器各部分工作的装置。可采用机械、电子、
•
1、通过参观机械零部件陈列室和机器模型、实物以及动画、视频、
录像等多媒体课件,初步建立对机器及其组成,并完成学习情境(一)工
作任务单中的问题:
(1)什么是机器?机器有哪些特征?机器与机构的区别。
(2)什么是零件?什么是构件?什么是部件?三者的区别。
学习情境一:认识典型机械零部件
工作任务
任务一 认识机器
学习情境一:认识典型机械零部件
学习目标
• 1、本任务要求结合实际,正确认识机器,区分实 际生产和生活中哪些是机器,哪些不是机器;
情境任务驱动:单元整体教学设计的实践研究——以统编语文教材六年级下册第一单元为例

[摘要]单篇教学是小学语文课堂教学的普遍方法,但教师这种“就课论课”的知识学习和技能训练,忽视了单元文本之间的内在联系,很难建立起关联的内容体系,缺乏单元统整的意识。
教学统编语文教材六年级下册第一单元时,教师可以从情境任务驱动入手,从“解读单元内容,重构教学目标”“设计情境任务,承载主要目标”“落实分项任务,聚焦任务解决”“细化综合评价,评估实施效度”等方面,搭建单元整体教学支架,促使学生举一反三、迁移运用,提高学生的语文核心素养。
[关键词]小学语文;单元整体教学;情境任务;教学设计[中图分类号]G623.2[文献标识码]A[文章编号]1007-9068(2024)07-0083-03一、研究背景单篇教学是小学语文课堂教学的普遍方法,但学生从这种零打碎敲、蜻蜓点水式的知识学习和技能训练中,只能习得碎片化的浅层知识,很难建立关联的内容体系。
观察当前小学语文课堂教学后,我发现存在以下四个问题。
其一,知识建构散。
统编语文教材采用“双线”的形式组织单元,但一线教师习惯让学生围绕问题去教材中寻找一个个零星的“点”,使得学生很难在一个连续的整体中建构知识体系。
其二,情境创设浅。
创设情境是教师常用的课堂教学手段,旨在拉近学生与文本的距离,激发学生的学习兴趣。
创设的情境更注重串联教学的环节,而忽视了问题的解决,实为“皮肉分离”。
其三,学习动力低。
单篇教学的情境创设连续性不足、任务驱动性不强、问题解决度不高,无法激发学生的学习兴趣。
而单元整体教学的情境创设能形成情境“串联体”,将学生在单元中经历的学习经验组合成有意义、有情节的学习事件,能使学生产生强烈的“在场感”。
其四,评价任务缺。
评价一直为传统教学所忽视。
而根据“教—学—评”一致性的要求,只有使教师的教、学生的学和对学习的评价这三者保持一致,才能实现教与学的相辅相成。
评价缺位,语文教学就无法达到教了等于学了、学了等于会了的境界。
基于此,我以统编语文教材六年级下册第一单元为例,探讨情境任务驱动下的语文单元整体教学设计。
基于“情境·任务·问题”模式下高三一轮复习——以《影响世界的

基于“情境·任务·问题”模式下高三一轮复习——以《影响世界的工业革命》为例作者:何冠彬来源:《中学历史教学》 2019年第4期2017 年版高中历史新课标要求“教师在设计教学过程中,要注意创设历史情境、以问题为引领和基于史料研习展开教学活动”[1]。
本文将基于新课标的这种精神,创设“情境?任务?问题”模式,由学生主导,以高三一轮复习课《影响世界的工业革命》为例,进行高中一轮历史复习课的教学实践。
一、何谓“情境?任务?问题”模式所谓“情境?任务?问题”模式,是指创设历史新情景,以新情景为依托设置任务,以任务为目标分解问题,以问题为手段提升核心素养。
(一)历史情境的内涵及组成要素“所谓情境,就是事物发生的环境。
情境包含两个要素:一个要素是人,没有了人就不可能有事情发生,也就没有所谓的情境;另一个要素是与人发生关系,这即包括外部的物质环境,也包括当事人的心理环境。
情境的新旧是相对于学生而言,某个情境学生以前没有接触过,就是新情境,而学生以前是有所了解的,那么对于他们来说就是旧的……历史知识都是在具体的情境下产生的,可以说,历史学科是一门天生就跟情境紧密地结合在一起的学科。
”[2]2017 版新课标强调“以新情境下的问题解决为重心,学生能否应对和解决陌生的、复杂的、开放性的真实问题情境,是检验其核心素养水平的重要方面……新情境可以有多重类型,包括:学习情境、生活情境、社会情境、学术情境。
”[3] 本课针对的是高三一轮复习课,其中设计的情境主要指依托史料、图表、历史叙述、史论等问题的学习情境。
(二)任务的设置和问题的创设复习课中课堂任务的设置建议以历史情境为依托,以新课标和高考考试大纲为依据;在复习课的授课过程中,建议以任务为驱动,通过问题的分解,来完成任务,从而更好地完成课堂目标。
问题的创设,要基于所创设的任务。
2017 版新课标要求“学业质量水平4 是学业水平等级性考试的命题依据”[4],所以高三一轮复习课问题的设置要参考学业质量水平3 和4 进行设计。
情境一任务2测验
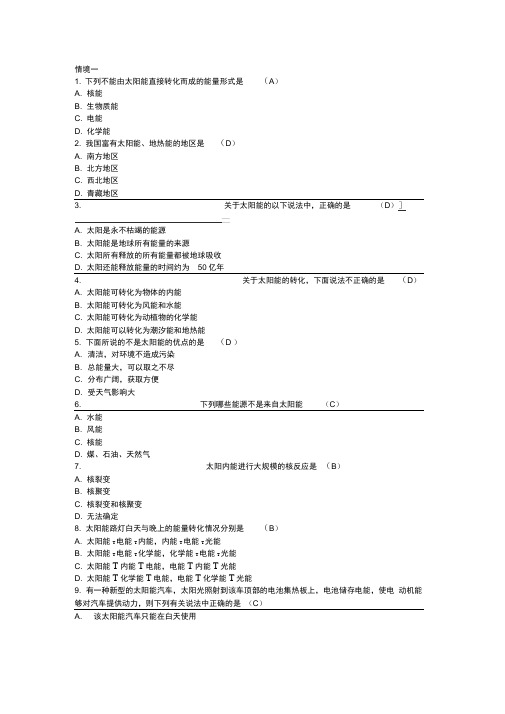
情境一1. 下列不能由太阳能直接转化而成的能量形式是(A)A. 核能B. 生物质能C. 电能D. 化学能2. 我国富有太阳能、地热能的地区是(D)A. 南方地区B. 北方地区C. 西北地区D. 青藏地区3. 关于太阳能的以下说法中,正确的是(D)]—A. 太阳是永不枯竭的能源B. 太阳能是地球所有能量的来源C. 太阳所有释放的所有能量都被地球吸收D. 太阳还能释放能量的时间约为50亿年4. 关于太阳能的转化,下面说法不正确的是(D)A. 太阳能可转化为物体的内能B. 太阳能可转化为风能和水能C. 太阳能可转化为动植物的化学能D. 太阳能可以转化为潮汐能和地热能5. 下面所说的不是太阳能的优点的是(D )A. 清洁,对环境不造成污染B. 总能量大,可以取之不尽C. 分布广阔,获取方便D. 受天气影响大6. 下列哪些能源不是来自太阳能(C)A. 水能B. 风能C. 核能D. 煤、石油、天然气7. 太阳内能进行大规模的核反应是(B)A. 核裂变B. 核聚变C. 核裂变和核聚变D. 无法确定8. 太阳能路灯白天与晚上的能量转化情况分别是(B)A. 太阳能T电能T内能,内能T电能T光能B. 太阳能T电能T化学能,化学能T电能T光能C. 太阳能T内能T电能,电能T内能T光能D. 太阳能T化学能T电能,电能T化学能T光能9. 有一种新型的太阳能汽车,太阳光照射到该车顶部的电池集热板上,电池储存电能,使电动机能够对汽车提供动力,则下列有关说法中正确的是(C)A. 该太阳能汽车只能在白天使用A.①②B.②③C.②④D.③④ C 电离层的作用 D 外层的作用 A )、人们根据月相变化B. 该太阳能汽车同样需要排放尾气C. 该太阳能汽车是将太阳能转化为电能,再将电能转化为动能D. 该太阳能汽车电动机产生的热量越多越好 10.太阳的主要成份是(C ) 和氦。
A.氧B.氮C.氢D. 氯11.太阳常数为 (C )/ m 2oA.367 ± 7WB.1000 ± 7W 氮C.1367 ± 7WD.3000 ± 7W12.在任何时刻,从日轮中心到观测点间所连的直线和通过观测点的 (D )之间的夹角叫太阳高度角。
角膜曲率计的测量原理、分类及步骤(验光技术)

《验光技术》情境一 客观验光 任务3角膜曲率测量
7
h’/h=f’/F’B, 当F’B较大时,则F’B约等于b, 则h’/h=f’/b,又r=2f’,所以只要固定h、b,测 出h’,即算出r值。r=2b×h’/h,呈线性关系。
《验光技术》情境一 客观验光 任务3角膜曲率测量
8
■ 因为眼球震动,很难测量。 ■ 所以需要双象系统。
5. 记录光标象的形状
《验光技术》情境一 客观验光 任务3角膜曲率测量
41
角膜曲率的记录举例(1)
OD 42.50 at180/43.50at90; 1.00D 顺规, 光 标清晰完整
OS 47.37at180/41.37at90; 6.00D 逆规, 光 标扭曲
《验光技术》情境一 客观验光 任务3角膜曲率测量
《验光技术》情境一 客观验光 任务3角膜曲率测量
13
(一)Bausch & Lomb角膜曲率计
■ 德国Hermann Von Helmholtz(1821-1894),发明的 世界第一台角膜曲率计
■ 是双象系统可变的一位角膜曲率计
《验光技术》情境一 客观验光 任务3角膜曲率测量
14
《验光技术》情境一 客观验光 任务3角膜曲率测量
42
角膜曲率的记录举例(2)
OD 41.75@180/43.75@70; 2.00D 不规则散光; 光标扭曲
OS 43.12@135/41.87@45; 1.25D 斜轴散光, 光标扭曲
《验光技术》情境一 客观验光 任务3角膜曲率测量
43
角膜曲率的记录举例(3)
OD 42.00/43.00at90; 1.00D顺规, 光标清晰完整 OS 42.00/42.00at90; 球性,光标清晰完整
2024届高考一轮复习语文学案课件 情境任务作文审题立意——审准情境,完成任务

2.在具体情境中落实写作主体和读者对象指令 (1)充分展现情境 请看202X年全国Ⅰ卷优秀作文《善识敢荐,心有大局》的开头部分, 先看称谓和问候语部分:“各位老师、同学:大家好!”准确的称谓、亲 切的问候,已有带入情境之感。再看开头一段: 针对今天读书会的话题,刚才大家侃侃而谈。有的同学观赏齐桓公的 不计前嫌、善用人才,也有的同学佩服管仲的贤能有为,但就我来说,对 鲍叔的感触最为深入,由于鲍叔善识敢荐,心有大局。 这段文字写得尤妙。它不仅点题,而且以三言两语就展现了读书讨论 的情境,可谓一箭双雕。
(2)写作主体指令,即写作主体是谁。高考作文“写作指令”对写 作主体的要求不仅是“考生”的实际身份,而且是置于真实具体的写作 情境中的交际主体,因此对写作主体就有时期背景、身份、年龄、职业、 经历等方面的显性或隐性规定。审题时一定要明确这一点。
(3)写作对象指令,即读者对象是谁。过去,高考作文写作是长期 缺失读者对象意识的。如果有,也是投阅卷者所好。现在,写给谁的, 任务指令中已经很明确、具体了。
命题的变化,不仅带来审题的变化(既审材料又审任务),更带来了 写作中的变化。过去,为了保证符合题意,要求在行文中“扣 题”“见料”;现在,情境任务型作文中,不只是要求“扣题”“见 料”,更要在行文中展现情境,落实任务指令。只有展现了情境,落 实了任务,才算真正做到“符合题意”。
1.第一必须保证落实内容指令 (1)拟题要含“内容”任务。如202X年全国Ⅰ卷作文题,写作标题 最好带“劳动”二字。 (2)开头点明“任务”。 (3)段段扣“任务”。行文进程中,要有任务意识,每段文字都要 有回扣任务的关键词或主题词。 (4)结尾回扣“材料”,再次点明“任务”。
(202X·新高考Ⅱ)阅读下面的材料,根据要求写作。 中国共产主义青年团成立100周年之际,中央广播电视总台推出微纪录
情境一、温度的检测

1) 冰点槽法 2) 补偿导线法 3) 计算修正法 4) 补偿电桥法 5) 软件处理法
11
三、测量参考电路
测量时可将热电偶的热端插入盐浴炉内检测炉 温T,冷端通过补偿导线与测量仪表的输入铜导 线相连,插入冰瓶确保T =0℃,通过测量仪表 测得的热电动势,即可确定炉内的实际温度。 测量炉温电路如图1-11所示。
1-7.简述热电阻测温原理,常用热电阻有哪些?它们的性能特点是什么?
1-8.热敏电阻有哪几种类型?简述它们的特点及用途。
1-9.描述常用的三种温度传感器的异同点。
1-10.联系实际,描述一个测温系统。指出它的测温范围、使用的器件。并 说出为什么使用该测温器件?
1-11.简要描述使用的测温传感器的原理、接线方法和注意事项等。
另外,热电偶的鲁棒性、可靠性和快速响应时间使其 成为各种工作环境下的首选。当然,热电偶在温度测 量中也存在一些缺陷,例如线性特性较差。除此之外, RTD和IC能提供更高的灵敏度和精度,可以很理想 地用于精确测量系统。热电偶信号电平很低,常常需 要放大或高分辨率数据转换器进行处理。
5
一、认识热电偶温度传感器
PN结传感器利用了理想二极管的PN结在恒定电流下,正向 电压随温度成近似线性关系的原理。将温敏二极管或三极 管、放大电路、温度补偿电路等功能集成在一块芯片上, 可制成集成温度传感器,其具有线性度好、灵敏度高、体 积小、稳定性好、输出信号大且规范化等优点。集成温度 传感器按输出形式分为电压输出型和电流输出型两种,电 压型的灵敏度一般为10mV/℃,电流型的灵敏度一般为 1A/℃,并且具有绝对零度输出电量为零的特性。AD590 是电流输出型温度传感器的典型产品,其利用电路产生一 个与绝对温度成正比的电流作为输出,温度灵敏系数为, 测温范围-55~+150℃,供电电压范围+4~+30V。
学习情境一任务---药材的净制

•
查看视频,请点击课程网站中的视频资源库
任务 药材的净制
• 筛选-竹筛的使用
净制药材 举例4
• 筛选 是根据药材和杂质的体 积大小不同,选用不同规格 的筛或罗,以除去药材中的 杂质,或将大小不等的药材 进行分档的操作。 • 操作时,将药材放于筛选器 具内进行筛选,以除去杂质 或将药材大小分档。 • 筛选用的器具,传统常使用 竹筛、铁丝筛、铜筛、罗等。 • 竹筛常分六种型号。主要用 于药材的分档,也用于除去 药材中的杂质。
任务 药材的净制
2. 净制的目的
(1)除去杂质及虫蛀霉变品
(2)将药材分档
(3)区分疗效不同的药用部位
(4)除去非药用部位
3. 分类
净制包括清除杂质、分离和清除非药用部位。
任务 药材的净制 一、清除杂质
(一)挑选
1. 挑选的含义
挑选是用手挑拣去混在药材中的杂质、霉败品;或区
分不同药用部位;或按药材大小、粗细进行“分档”的 操作。 2. 操作方法 将药材置于药匾内或摊在台面上,挑拣出木屑、砂石
教师行动 根据实训结果,总 结、评价 填写《教师评价表》 布置新任务
任务 药材的净制
相关知识链接……
净制是中药炮制的第一道工序。
1. 净制的含义
中药材在切制、炮炙或调剂、制剂前,均应选取规定的 药用部位,除去非药用部位、杂质及霉变品、虫蛀品、灰 屑等,区分疗效不同的药用部位,使其达到药用净度标准。 上述炮制方法,统称为净制。 经净制后的中药材称为“净药材”。只有净药材方可用 于临床。
刷反复搓洗或刷洗除去。 (2)漂:若药物中含有多量的盐分、腥臭味或有毒成分,可用多量水
浸漂,每天换水2~3次(古代用常流水漂洗),漂至无咸味,或无腥臭味,
礼赞:让革命文化入脑入心——以任务一“故事厅:礼赞心中最崇敬的人”为例

[摘要]打通革命文化与儿童生活的壁垒,是革命文化主题学习的关键环节。
教学统编语文教材六年级下册第四单元时,教师围绕大任务“‘奋斗的历程’读讲写交流会”,设计三个子任务,引导学生展开语文实践活动。
进行子任务一“故事厅”的教学时,教师通过走向整合、语言实践、重在转化三个关键环节,引导学生基于单元整合,展开积极的语文学习活动,感悟革命领袖风范、讲述革命英雄故事、分享让人感动的人和事,使学生获得语文核心素养的发展。
[关键词]革命文化;语言实践;整合教学[中图分类号]G623.2[文献标识码]A[文章编号]1007-9068(2024)10-0006-03革命文化主题单元的教学,如果停留在读读课文、写写字词、说说感受的层面,学生就很难深入感受革命文化震撼人心的力量。
教学统编语文教材六年级下册第四单元时,教师可围绕大任务“‘奋斗的历程’读讲写交流会”,设计“故事厅”“诗歌集”“心愿墙”三个子任务,引导学生展开语文实践活动。
(具体请看本期的《在整合的语文实践活动中传承革命文化》一文)本文以子任务一“故事厅:礼赞心中最崇敬的人”为内容,探究如何引导学生展开深度学习,促进学生语文核心素养的发展。
在教学中,教师将精读课文《十六年前的回忆》《为人民服务》、略读课文《董存瑞舍身炸暗堡》以及综合性学习“开展阅读分享会”板块和五篇阅读材料结合起来,通过阅读分享活动,引领学生感悟革命领袖风范,讲述革命烈士故事,体会革命英雄的伟大形象,使学生受到革命文化的熏陶和洗礼。
一、走向整合:在“故事厅”情境任务中开展积极的语文学习(一)目标统整根据本单元课文内容特点,我们对单元的人文主题和语文要素进行分析,结合《义务教育语文课程标准(2022年版)》对实用性阅读与交流学习任务群的教学提示,确定教学目标:一是讲述、分享革命故事;二是传承革命文化。
统整目标让教师的教与学生的学的线索更清晰可见。
我们结合文本内容,将具体目标分解到每个课时中,设计具体的学习活动(见表1)。
情境·任务·应用——“实用性阅读与交流”任务群在《自相矛盾》中的应用

Course Education Research课程教育研究2023年第12期课程标准是教师开展教学活动的“指南针”,而在当下的小学语文教学中,存在着教学零散性较强、忽视学生认知规律等问题,导致核心素养培养落实不到位的情况。
因此,在小学语文教学中,教师有必要依托课程标准中提出的学习任务群思想对教学方式做出改进,立足“学习任务群”的内涵来开展教学,增强学生在教学中的自主性,取得更好的教学效果。
教师要加强对教学内容的分析,建立适合的学习任务群落实逻辑,从而真正落实新课程标准提出的要求。
一、学习任务群的内涵学习任务群是指一组有着特定学习主题、相互之间有内在逻辑关联的学习任务,学习任务群指向了学生核心素养的发展,具有情境性、实践性以及综合性的特征。
在义务教育语文课程标准中,给出了六个学习任务群,要求教师在实际的教学中根据不同学段学生的特点,有所侧重地安排学习任务群。
从实施方式上来看,学习任务群是高于单元教学、学习任务的概念,在实际的教学中,需要教师对教学内容进行深入的分析,结合学生阶段性成长的需求,安排适合的学习任务群展开教学。
当然,不同学习任务群之间也是有所关联的,如在开展“实用性阅读与交流”任务群的教学时,也需要学生展开思辨的阅读和表达,或者对语言文字的积累和梳理。
因此,教师要在以一个学习任务群为主的前提下,实施其他学习任务群为辅的教学,从而保证学生对知识和思想方法的全面吸收,真正达成对学生语文核心素养的培养。
二、“实用性阅读与交流”任务群特征分析“实用性阅读与交流”任务群是课程标准中提出的发展型学习任务群之一,强调引导学生在语文学习中使用倾听、阅读、观察等多种方式来展开阅读,并且在这个过程中使学生学会如何清楚地表达自己的观点、传递出有效的信息,增强学生的社会交往能力。
和其他的学习任务群相比,“实用性阅读与交流”任务群具有以下特点:一是教学要指向学生交流沟通的需要。
这就要求教师在教学中将如何促进学生的表达放在首位上,在学生阅读的过程中注重还原真实的情境,让学生学会根据实际情况来把握作者的观点,学习如何对语言材料进行有效的选择、组织以及表达,使学生逐渐获得语言沟通能力上的提升。
- 1、下载文档前请自行甄别文档内容的完整性,平台不提供额外的编辑、内容补充、找答案等附加服务。
- 2、"仅部分预览"的文档,不可在线预览部分如存在完整性等问题,可反馈申请退款(可完整预览的文档不适用该条件!)。
- 3、如文档侵犯您的权益,请联系客服反馈,我们会尽快为您处理(人工客服工作时间:9:00-18:30)。
(2) 有利于及早发现毛坯缺陷并以便及时报 废或修补,减少浪费。 (3) 有利于合理利用机床设备 由于各加工阶段的主要任务不同,加工方 法、加工设备、不同等级的技术工人的配 备也就不同。为合理地使用设备和发挥技 术工人的积极性,粗加工用功率大、精度 较低、效率高的设备和技术等级低的工人。 精加工则与之相反,从而发挥机床的各自 特点,满足高效、低耗生产的要求。
小结
具有一定技术要求的加工表面,
一般都不是只通过一次加工就能达 到图纸要求的,对于精密零件的主 要表面,往往要通过多次加工才能 逐步达。 在被加工零件各表面加工方法分 别初步选定以后,还应综合考虑为 保证各加工表面位置精度要求而采 取的工艺措施。
加工阶段的划分
划分加工阶段
粗加工阶段 在此阶段主要是尽量切除大部分余量,主要考虑 生产率。
各种加工方法所能达到的经济精度和表面粗糙度 任何一种加工方法能获得的加工精度和表面粗糙 度都有一个相当大的范围,而高精度的获得一般要 以高成本为代价,不适当的高精度要求,会导致加 工成本急剧上升。
在I段,当零件加工精度要求很高时,零件成本 将要提高很多,甚至成本再提高,其精度也不能 再提高了,存在着一个极限的加工精度。
在此阶段主要是为主要表面的精加工做准备,并 半精加工阶段 完成次要表面的终加工(钻孔、攻丝、铣键槽 等)。 精加工阶段 在此阶段主要是保证各主要表面达到图纸要求, 主要任务是保证加工质量。
在此阶段主要是为了获得高质量的主要表面和尺 光整加工阶段 寸精度。
划分加工阶段的目的 (1)有利于保证零件加工质量 零件在加工中由于受切削力、切削热和内应力 的作用,不可避免地要产生变形,影响加工质 量。划分加工阶段并使各加工阶段有一定的时 间间隔,便于残余应力得到释放,从而减少这 些变形带来的影响,或者在加工阶段之间安排 诸如热处理、校直、自然时效等工序来消除各 种变形的影响,提高加工质量。
工件的结构形状和尺寸 以内圆表面加工为例,回转体零件 上较大直径的孔可采用车削或磨削; 箱体上IT7级的孔常用镗削或铰削,孔 径较小时宜用铰削,孔径较大或长度 较短的孔宜选用镗削。
生产率和经济性 选择加工方法一定要考虑生产类型, 这样才能保证生产率和经济性要求。 对于较大的平面,铣削加工生产率较 高,而窄长的工件宜用刨削加工;对于 大量生产的低精度孔系,宜采用多轴钻; 对批量较大的曲面加工,可采用机械靠 模加工、数控加工和特种加工等加工方 法。
由于工序的集中和分散各有特点,究竟按 何种原则确定工序数量,这要根据生产纲 领、机床设备及零件本身的结构和技术要 求等作全面的考虑。但从技术的发展方向 来看,随着数控机床、加工中心的发展和 应用,今后将更多地趋向于工序集中。
第二节 机械加工工艺规程设计
第二节 机械加工工艺规程设计
加工顺序的安排 要满足零件图样的全部技术要求及生 产的高效率和低成本,不仅要正确选择 定位基准和每个表面的加工方法,而且 要合理地安排工序顺序。这不仅指安排 好机械加工间的顺序,而且要合理地安 排好机械加工与热处理、表面处理及与 辅助工序(如清洗、检验等)间的工序 顺序。
先面后孔 箱体、支架等类零件上具有轮廓尺寸 远比其它表面尺寸为大的平面,用它 作定位基准面稳定可靠,故一般先加 工这些平面以作精基准,供加工孔和 其它表面时使用。
任务实施
小批生产工艺路线 工序 工序 号 名称 安 工序内容 装 设备
I
1 车削 II
粗车,精车端面C,粗镗、精镗Φ60H9内孔, 倒角、粗车、半精车Φ200外圆
导入新课
零件在加工过程中,各表面是如何进 行加工及安排的呢?
学习任务4
工艺路线的拟定
能力目标
能根据零件要求,正确选择表面加工方法; 能够初步正确拟定工艺路线。
知识目标
掌握表面加工方法的选择; 掌握加工阶段的划分及加工顺序安排的原则。
环节一:提出任务
环节一:相关学习内容
表面加工方法的选择
粗车 - 半精车 -精车 -精细车 (金刚车) 粗车 - 半精车 - 粗磨 -精磨 -超精磨(或镜面磨) 粗车 - 半精车 -粗磨 -精磨 研磨
0.012-0.1 ( 或RZ0.1)
0.025-0.4 0.006-0.025 ( 或RZ0.05) 0.006-0.1 ( 或RZ0.05)
8
IT6-7
工艺路线安排: 1.人工时效 2.划线(以导轨面为划线基准) 3.粗铣J面(以所划尺寸线为基准) 4.粗铣导轨面,粗铣主轴安装面K、L(以J为基准) 5.粗刨G、H、I面(以J面为基准) 6.二次时效 7.半精刨J 面(以导轨面为基准) 8.半精铣导轨面,精铣主轴安装面K、L(以J面为基准) 9.导轨面高频淬火 10.粗磨导轨面(以J面为基准) 11.精刨底面J面(以导轨面为基准) 12.精磨导轨面,精磨主轴箱安装面K、J (自为基准) 13.半精刨G、H、I面(以导轨面为基准)
拉键槽 用钻模钻6-Φ20孔 修孔口的锐边及毛刺 拉床 钻床
2
3 4 5
车削
拉削 钻削 钳
I
I I I
图示车床床身,小批生产,其主要加工内容 (1)加工导轨面A、B、C、D、E、F:粗铣、半精铣、粗磨、精磨。 (2)加工底面J:粗铣、半精刨、精刨。 (3)加工压板配合面及齿条安装面G、H、I:粗刨、半精刨。 (4)加工主轴箱安装面K、L:粗铣、精铣、精磨。 (5)其他:划线、人工时效、导轨面高频淬火、二次时效。 试将上述加工内容排成合理的工艺路线,并指出各工序的定位基准。
IT11-13
IT8-10 IT7-8 IT7-8 IT7-8 IT6-7 IT5
12.5-50
3.2-6.3 0.8-1.6 0.25-0.2 0.4-0.8 0.1-0.4 主要用于淬火 钢,也可用于 未淬火钢,但 不宜加工有色 金属 适用于淬火钢 以外的各种金 属
粗车 - 半精车 -粗磨 -精磨 超精加工(或轮式超精磨)
主要用于要求 较高的有色金 属加工
9
IT5 以上
极高精度的外 圆加工
10
IT5 以上
表格应用的举例:要求孔的加工精度为IT7级,粗 糙度1.6~3.2,确定孔的加工方案
①钻一扩一粗铰一精铰
方案①用得最多,在大批、大量生产中常用在 自动机床或组合机床上,在成批生产中常用在 立钻、摇臂钻、六角车床等连续进行各个工步 加工的机床上。该方案一般用于加工小于80mm 的孔径,工件材料为未淬火钢或铸铁,不适于Байду номын сангаас加工大孔径,否则刀具过于笨重。 方案②用于加工毛坯本身有铸出或锻出的孔, 但其直径不宜太小,否则因镗杆太细容易发生 变形而影响加工精度,箱体零件的孔加工常用 这种方案。 方案③适用于淬火的工件。 方案④适用于成批或大量生产的中小型零件, 其材料为未淬火钢、铸铁及有色金属。
选择表面加工方法时,一般先根据表面的 加工精度和表面粗糙度要求,选定最终加工 方法,然后再确定精加工前的准备工序的加 工方法,即确定加工方案。 由于获得同一精度和同一粗糙度的方案有 好几种,选择时还要考虑生产率和经济性, 考虑零件的结构形状、尺寸大小、材料和热 处理要求及工厂的生产条件等。
在选择零件各表面的加工方法时,主要应从 以下几个方面来考虑。 零件的结构 包括组成零件各表面的性质和尺寸的大小及结 构的复杂程度。各种典型表面都有其相适应的 加工方法。 例如,外圆表面的加工,主要以车、磨为 主;孔的加工,则以钻、铰、车、镗、磨等为 主;平面加工又以铣、刨、插、拉、车、磨等 为主;精密螺纹加工是以车、磨、研为主;齿 形的主要加工方法有滚、插、拉、磨、剃、珩、 研等。
机械加工顺序安排 基面先行 作为其它表面加工的精基准一般安排在工 艺过程一开始就进行加工,以便尽快为后 续工序的加工提供精基准。
先主后次 零件的主要工作表面(一般是指加工精 度和表面质量要求高的表面)、装配基 面应先加工,从而及早发现毛坯中可能 出现的缺陷。
先粗后精 一个零件的切削加工过程,总是先进行 粗加工,再进行半精加工,最后是精加 工和光整加工。
工序的集中与分散
工序集中:就是在每个工序中加工内容很多, 尽可能在一次安装中加工许多表面,或尽量 在同一台设备上连续完成较多的加工要求。 这样,零件工艺过程中工序少,工艺路线短。 工序分散:把加工表面分的很细,每个工序 加工内容少,表现为工序多,工艺路线长。
按工序集中原则组织工艺过程, 采用数控机床、加工中心 就是使每个工序所包括的加工内 按工序集中原则组织工艺过 工序 容尽量多些,将许多工序组成一 程,生产适应性反而好,转 集中 个集中工序。 产相对容易,虽然设备的一 最大限度的工序集中,就是在 次性投资较高,但由于有足 原则 一个工序内完成工件所有表面的 够的柔性,仍然受到愈来愈 加工。 多的重视。 传统的流水线、自动线生 按工序分散原则组织工艺过程, 产基本是按工序分散原则组 工序 就是使每个工序所包括的加工内 织工艺过程的,这种组织方 分散 容尽量少些。 式可以实现高生产率生产, 最大限度的工序分散就是每个 原则 但对产品改型的适应性较差, 工序只包括一个简单工步。 转产比较困难。
经济精度就是指在正常加工条件下 (采用符合质量标准的设备、工艺装 备和标准技术等级的工人,合理的加 工时间)所能达到的精度。相应的粗 糙度称为经济粗糙度。
表 1- 外圆柱面加工方法
序 号 加工方法 经济精度(公 差等级表示) 经济粗糙度 Ra值/ um 适用范围
1
2 3 4 5 6 7
粗车
粗车 - 半精车 粗车 - 半精车 - 精车 粗车 - 半精车 - 精车 -滚压 (或抛光) 粗车 - 半精车 -磨削 粗车 - 半精车 -粗磨 -精磨
②粗镗一半精镗一精镗
③粗镗一半精镗一磨孔
④钻(扩)一拉
工件的材料和热处理 加工方法的选择,常受工件材料性质 的限制。经淬火后的表面,一般应采用磨 削加工;材料未淬硬的精密零件的配合表 面,可采用刮研加工;对硬度低而韧性较 大金属,如铜、铝、镁铝合金等有色金属, 为避免磨削时砂轮的嵌塞,一般不采用磨 削加工,而采用高速精车、精镗、精铣等 加工方法。