无铬钝化最前沿技术探讨
六价铬钝化 三价铬钝化 无铬钝化
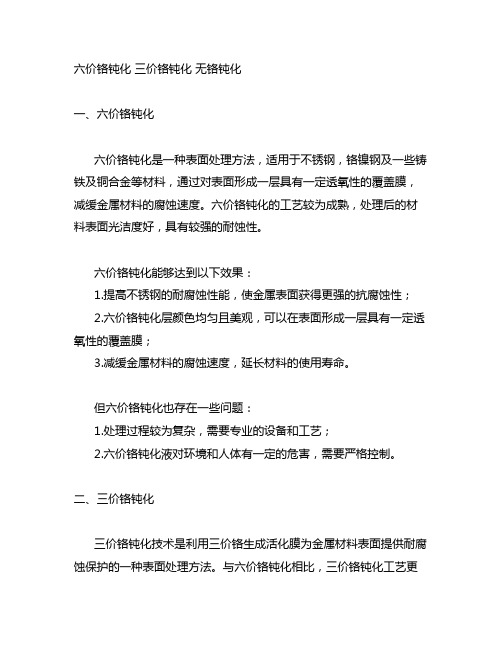
六价铬钝化三价铬钝化无铬钝化一、六价铬钝化六价铬钝化是一种表面处理方法,适用于不锈钢,铬镍钢及一些铸铁及铜合金等材料,通过对表面形成一层具有一定透氧性的覆盖膜,减缓金属材料的腐蚀速度。
六价铬钝化的工艺较为成熟,处理后的材料表面光洁度好,具有较强的耐蚀性。
六价铬钝化能够达到以下效果:1.提高不锈钢的耐腐蚀性能,使金属表面获得更强的抗腐蚀性;2.六价铬钝化层颜色均匀且美观,可以在表面形成一层具有一定透氧性的覆盖膜;3.减缓金属材料的腐蚀速度,延长材料的使用寿命。
但六价铬钝化也存在一些问题:1.处理过程较为复杂,需要专业的设备和工艺;2.六价铬钝化液对环境和人体有一定的危害,需要严格控制。
二、三价铬钝化三价铬钝化技术是利用三价铬生成活化膜为金属材料表面提供耐腐蚀保护的一种表面处理方法。
与六价铬钝化相比,三价铬钝化工艺更加环保,对人体和环境的危害更小。
三价铬钝化相较于六价铬钝化,可以减少对环境的污染,是目前广泛应用的一种防锈方式。
三价铬钝化具有以下优点:1.具有较强的耐蚀性,能有效地减缓腐蚀速度;2.符合环保要求,对环境和人体的危害较小;3.能够提高材料的使用寿命,延长产品的寿命。
但也需要注意的是,三价铬钝化还有待改进的地方:1.处理效果相对六价铬钝化略有差异,对一些特殊情况需要特殊处理;2.处理成本相对较高,需要经过一定的投入。
三、无铬钝化无铬钝化是一种新型的环保钝化技术,主要通过对金属材料表面进行特殊处理,形成覆盖膜以达到耐蚀的效果。
无铬钝化技术在未来被认为是一种趋势。
无铬钝化技术遵循“无污染、无危害、无排放”的理念,可以有效地减少对环境和人体的危害。
无铬钝化的优势在于:1.符合环保要求,对环境和人体的危害极小;2.具有良好的防腐蚀性能,能够保护材料表面不受氧化和腐蚀。
不过,无铬钝化技术也存在一些问题:1.目前技术还不够成熟,需要不断改进和完善;2.处理成本相对较高,仍然需要进一步降低。
结语六价铬钝化、三价铬钝化和无铬钝化各有优缺点。
化学镀镍层无铬钝化工艺的研究

2 ・ 8
Ma .2 1 y 02
P a i n i ih n lt ng a d F n s i g
V 13 o 5 S ra . 3 o. 4 N . eilNo 2 0
文章编 号 :0 13 4 ( 0 2 0 — 0 8 0 10 -8 9 2 1 ) 50 2 —5
e p rme t . n o d r t mp o e t e p sia in efc ,n ue c s o o a su p r a g n t o e ta xe i n s I r e o i r v h a sv to fe t if n e fp ts i m e l m n a ae c nc n r — to tmp r t r n i r lo me s r d.Re ut h we h tte o t lc mp sto fpa sv - in,e e au e a d tme we e a s a u e s ls s o d t a h p i o o iins o s ia ma to out n we e s dum y r xd f1 / s d u c r n t f1 /L, o u ph s hae o 0 g L, in s l i r o i o h d o i e o 0g L,o i m abo a e o 5g s dim o p t f5 /
TANG e g,HU a g Hu ,HUANG a e,PAN a — h n Fn Gu n — i Hu — Zh n c a g,
W EIZ i g n h — a g,Z ENG i f h m cl n ier ga d LgtId s y un d n n esy o T cn l y u nzo S ho o C e ia E gne n n i n ut ,G a go gU i r t f eh oo ,G a gh u i h r v i g
铝及铝合金无铬钝化的研究进展

to
research and develop highly practicable and for aluminum and aluminum alloys.The
at
environment—friendly non—chromate research
status
passivation technologies
摘要:
研究并开发实用性强、环境友好的铝及铝合金无铬钝化工艺是未来发展的趋势。综述了国内外铝及
铝合金无铬钝化体系的研究状况及其特点,为铝及铝合金无铬钝化的后续研究提供参考,并展望了未来的研
究方向。
关键词:
Abstract:
铝;铝合金;无铬;钝化
It is
a
tendency of
the future
development
参考文献
L.Corrosion
behaviour of
pretreated
and painted aluminium
sheets[J].Electrochimica [13]
DECK P
Acta,1997,42(6):969—978.
D,MOON M,SUJDAK R J.et a1.Investigation of
1
铝及铝合金无铬钝化
1.1钛盐钝化 钛的性质与铬的非常相似,在几乎所有的自然 环境中都不腐蚀。其极好的抗腐蚀性源于在其表面 上所形成的连续稳定、结合牢固和具有保护性能的 氧化膜层。钛的高反应活性及与氧极强的亲和力使 得其表面暴露于空气或潮湿环境中能立即形成该氧 化膜。事实上,同铬酸盐氧化一样,只要环境中存在 微量的氧或水(潮气),由于钛与氧极强的亲和力,遭 到破坏的氧化钛膜就能够立即自我修复,从而提高 耐蚀性。 钛酸盐类化学氧化膜[4咱]将来有可能替代铬酸 盐类化学氧化膜。吕勇武等[73用钛盐作为成膜主 盐,制备的转化膜的颜色为金黄色,用扫描电镜观察 到转化膜呈针叶状结构,且具有优良的耐蚀性。郭 瑞光等凹3的研究表明:钛酸盐化学转化膜拥有许多 与铬酸盐化学转化膜相同的性质,如稳定、牢固、自 愈性良好、能够防止铝合金的腐蚀等。钛酸盐转化 膜能起到保护作用是基于它抑制了铝合金表面阳极 反应的发生和提高了点蚀电位。为了避免废水处 理,Deck等[93介绍了非水洗钛盐处理方法,并分析
无铬达克罗技术的研究进展

De eo m e to s a c n Th n- h o i m v lp n fRe e r h o e No c r m u Da r m e c n l g co tTe h o o y
K hn — i EC agme,WA G Q a —un HU Y n , H U L—i N unq a , og Z O i n q
b ify p o p ce . rel r s e t d K e wo d y r s:n n c r n u d c o e e hn l g o — h o i m a r m tt c oo y; d e o e e h oo y;c ro in r ssa c a r m ttc n lg o r so e itn e
ts a d a p ia in r a a e i to u e u n p le t a e r n r d c d.Th l p o e le r e e r h d b o ta tn o — h o i m o e f m r p ris ae r s a c e y c nr si g n n c r n u i d c o tf m t r dt n ld c o tfl a rme l wi ta i a a r me m.Th u t e fo t fn r—hrmi m c o tt c n lg r i h o i e f rh refrso o lc o u Da r me e h o o a e y
引言
2 0世 纪 7 0年代美 国研 究开 发 了一种 较 为先 进 的表 面处 理工 艺—— 达 克罗处理 技术 , 到 2 纪 直 0世 9 0年 代这项 技术 才被 引入 中 国。19 9 3年 2月 , 国 我 首次 引进 国外达 克罗 生 产 技术 , 随后 南 京 、 海 、 上 云 南 和 天津 等地 陆续 引进 了达 克 罗 涂 覆 设 备 和技 术 工 艺 , 开始试 验研 究 。 并
电镀锌层无铬钝化工艺的研究

图4 两 种 复 合 镀 层 磨 损 后 的形 貌
3 结 论
( 1 )微粒 的 导 电性 对 复合 镀 层 的形 貌 、 相 结 构
和显微 硬 度均有 一 定影 响 , 但对 耐磨 性 影响 不 明显 。
Байду номын сангаас
梅建庭 , 刘华. Ni — P — S i C化 学 复 合 镀 层 耐 磨 性 与 显 微 硬 度 的研
参 考 文献
唐致远, 郭 鹤桐 . 复 合 电镀 在 国内 的应 用 [ J ] . 电镀 与 环保 ,
1 99 1, 1 1( 6 ): 1 4 1 5 .
Ni — Al ( ) 。复合 镀 层 的 磨 损 率 为 1 . 5 8 , 较 Ni — A1 复合 镀层 的 1 . 6 1%几乎 无差 别 , 反 映 出两种 复合 镀
摘要 : 开 发 一 种 绿 色无 铬 的 钝 化 工 艺 , 所 得 钝 化 膜 的性 能接 近铬 酸 盐钝 化 膜 的 。研 究 了 电镀 锌 层 在 钛 磷 硅 钼 复 合 体 系 中的
钝化 工艺, 并 采 用扫 描 电 子 显 微 镜 、 硫 酸 铜 点 滴 实验 和 中性 盐 雾 实验 等 方 法 测 试 了钝 化 膜 的形 貌 和 耐 蚀 性 。 通过 正 交 实验 确 定 了钝 化 液 的 最 优 配 方 为 : 三氯化钛 t 0 mL / L , 磷酸 l _ 8 mL / L, 硅酸钠 1 8 g / L, 钼 酸钠 0 . 8 5 g / L。其 中硅 酸 钠 的 质 量 浓度 对
收稿 日期 : 2 0 1 2 - 0 3 — 2 1
・
化 学转 化 膜 ・
电 镀 锌 层 无 铬 钝 化 工 艺 的 研 究
无铬钝化与三价铬钝化的研究进展

综述与专论
" " [ 摘" 要] " 六价铬钝化工艺, 毒性大, 严重污染环境, 电镀行业研究并采用无毒或低毒的钝化工艺势在必行。目前无铬钝 化和三价铬钝化已取得积极的进展, 三价铬钝化已应用于生产, 并获得良好的效果。无铬钝化作为环保工艺, 是将来钝化工艺 发展的新方向。结合近年来无铬钝化和三价铬钝化的发展, 对无铬钝化、 三价铬钝化及封闭处理等进行了较详细的阐述。 [ 关键词] " 无铬钝化; 三价铬钝化; 封闭处理; 耐蚀性; 研究进展 [ 中图分类号] ’()*$+ $,) " " " [ 文献标识码] - " " " [ 文章编号] )%%) . /!!% ( #%%, ) %, . %%%! . %$
形成的盐在溶液中用作腐蚀阻化剂。维尔考克斯 ( G;:E8J ) 等
!!"
=> 引> 言
长期以来, 铬酸盐钝化已广泛地用于电镀和表面处理, 但六 价铬毒性大, 又是致癌物质, 严重污染环境。随着人们对环境保 护意识的增强, 六价铬的应用已逐渐受到严格限制, 因此研究和 开发无毒或低毒的物质以替代铬酸盐钝化工艺势在必行
[ )N, ]
目前, 无铬钝化和三价铬钝化已取得了积极的进展, 三价铬钝化 已应用于生产, 并取得了良好的效果, 无铬钝化无疑是发展的方 向。
?> 无铬钝化
R、S8、G、=8、 T3、 =1、U4 等的无机盐 V 氧化物) 、 有机物钝化、 氧化物钝化 ( 硅酸盐磷化等) 和有机金属化合物钝化等。
无铬钝化技术研究的进展

第38卷第4期2003年4月钢 铁I RON AND ST EELV o l.38,N o.4A p ril2003・综合论述・无铬钝化技术研究的进展3周渝生(宝山钢铁股份有限公司)摘 要 评述了文献报道和各种不同的无铬钝化工艺的特点及其发展现状。
目前还没有一种无铬钝化工艺能够完全代替铬酸盐钝化工艺,某些无铬钝化工艺在某些方面已经与铬酸盐钝化相当,但其市场前景、应用范围及用户环保效果还需要进一步研究。
关键词 无铬钝化 铬酸盐钝化 表面处理技术①REV IE W OF CHROM ATE-FREE PASSIVAT I ON FOR M ETAL SZHOU Yu sheng(B ao shan Iron and Steel Co.,L td1)ABSTRACT T he developm en t and featu res of ch rom ate2free p assivati on fo r m etals are summ arized.KEY WORD S ch rom ate2free p assivati on,ch rom ate p assivati on,su rfacing techn ique1 前言大多数工业应用的金属及镀层金属(如铁、锌、铝、锡、铅、镁等及其合金)均可通过形成化学转化膜来保护其表面。
用于提高耐蚀性的化学转化膜技术主要有铬酸盐钝化和磷化等。
其中铬酸盐钝化处理可形成铬 基体金属的混合氧化物膜层,膜层中的铬主要以三价铬和六价铬形式存在,三价铬作为骨架,而六价铬则有自修复作用,因而耐蚀性很高。
由于铬酸盐成本低廉,使用方便,因而铬酸盐钝化处理在钢铁、航空、电子和其他部门得到了广泛的应用。
电镀锌、热镀锌钢板因其耐腐蚀性好、价格较便宜而被广泛应用于汽车、建材、家电、容器等领域。
为了进一步提高耐腐蚀性,目前几乎所有的电镀锌、热镀锌钢板都采用了铬酸盐的钝化处理。
钝化液的主要成分为:六价铬,硫酸或硝酸。
对镀锌层无铬钝化技术的研究进展探讨

对未来研究的建议和展望
进一步研究无铬钝化技术在不同环境条件下的耐 腐蚀性能和粘附性。
探讨无铬钝化技术在提高锌涂层耐腐蚀性能的同 时,对其他性能如硬度、耐磨性等方面的影响。
针对不同基材和镀锌工艺,研究开发适用于各种 情况的无铬钝化剂。
开展绿色制造和环保方面的研究,优化生产工艺 ,降低能耗和废弃物排放。
《对镀锌层无铬钝化技术的研究 进展探讨》
xx年xx月xx日
目录
• 研究背景和意义 • 镀锌层无铬钝化技术的研究现状 • 无铬钝化技术的理论基础 • 无铬钝化技术的实验研究 • 无铬钝化技术的工业应用 • 研究结论和展望
01
研究背景和意义
镀锌层无铬钝化技术的应用领域
汽车工业
镀锌钢板在汽车工业中广泛应用于提高防腐蚀性能。无铬钝化技术可以替代传统的铬酸盐 钝化,以减少对环境和健康的危害。
05
无铬钝化技术的工业应用
工业应用的主要领域和实例
汽车制造业
在汽车制造过程中,镀锌零件需要进行无铬钝化处理以增强防腐 蚀性能。例如,汽车轮毂、发动机零件和底盘等。
家电制造业
在家电制造中,镀锌材料被广泛应用于金属外壳和内部结构部件 。无铬钝化处理可提高其耐腐蚀性能和外观质量。
建筑行业
在建筑领域,镀锌钢材广泛应用于桥梁、高速公路、建筑结构和管 道系统。无铬钝化技术可以提高其耐腐蚀性能和延长使用寿命。
工业应用的潜力和未来发展趋势
潜力
随着环保意识的不断提高和技术的不断发展,无铬钝化技术的工业应用前景广阔 。未来,无铬钝化技术将在更多领域得到广泛应用,如新能源、海洋工程和航空 航天等。
发展趋势
未来,无铬钝化技术将朝着提高耐蚀性、增强稳定性和降低成本的方向发展。同 时,随着新材料的不断涌现,无铬钝化工艺将不断优化,以满足不同材料和工况 的需求。
压铸铝无铬钝化剂

压铸铝无铬钝化剂
随着环保意识的不断提高,对于无害化、低污染的材料和工艺的需求也日益增加。
在铝合金压铸领域,钝化剂被广泛应用以提高铝合金的耐腐蚀性和表面质量。
然而,大部分传统的钝化剂中含有六价铬,这种物质具有毒性和环境污染风险,已经被许多国家禁止使用。
因此,开发无铬钝化剂成为铝合金压铸行业的一个重要研究方向。
目前,压铸铝无铬钝化剂主要包括无铬转化涂料和无铬钝化溶液两种类型。
无铬转化涂料适用于小型零件和复杂形状的零件,可以在表面形成一层纳米级的无机膜,提高零件的耐腐蚀性和涂装附着力。
而无铬钝化溶液适用于大型零件和生产线上的连续生产,可以在短时间内完成钝化处理并达到优良的防腐效果。
此外,压铸铝无铬钝化剂还可以增加涂装的多种选择性,具有更好的环保性能和经济性。
因此,无铬钝化剂将在未来得到更广泛的应用。
- 1 -。
铝合金无铬钝化技术

铝合金无铬钝化技术
铝合金无铬钝化技术是一种利用无铬化合物代替传统铬酸钝化剂对铝合金表面进行处理的技术。
由于铬酸盐钝化剂在使用和废弃过程中对环境和人体有一定的危害,因此寻找一种更加环保的替代方案一直是铝合金表面处理领域的研究重点。
铝合金无铬钝化技术主要有以下几种:
钝化剂:利用无铬化合物代替传统的铬酸盐钝化剂,如钛盐、锌盐、钨盐等。
氧化法:在铝合金表面形成氧化层,氧化层可以提高铝合金的耐腐蚀性,常用的氧化剂有硫酸、硝酸、氢氧化钠等。
电化学法:通过电解的方式在铝合金表面形成氧化层,电解液中一般采用无铬化合物,如硫酸盐、草酸等。
薄膜覆盖法:利用有机物覆盖铝合金表面形成一层保护膜,如有机硅、聚酰亚胺、聚醚酮等。
无铬钝化技术的优点是环保、无毒、无害,同时钝化层的耐蚀性能与传统的铬酸盐钝化层相当,能够有效提高铝合金的耐蚀性和耐磨性。
镀锌层无铬钝化

无 铬 钝 化 简 介(无机物钝化)
锆盐钝化 — 代替铬酸盐用于铝基表 面的处理已被确认, 锆基无铬钝化液也可 处理锌基表面,作为涂层的前处理。锆的 稳定化合物为氟锆酸盐,其钝化液主要含 有H2ZrF6 ,另需加入少量的HF,操作时应 予充分注意。
无 铬 钝 化 简 介(无机物钝化)
稀土金属盐稀土金属铈、镧和钇等的 盐被认为是有色金属在含氯溶液中的有效 缓蚀剂。含 CeCl3溶液处理锌表面,生成 了一层黄色转化化膜,有效地降低锌的氧 还原的速度。该膜层为含铈的氧化物和氢 氧化物,具有很好的耐蚀性。
-E(V) 0 20 40 60 80 100 120 140 160 180 200 220 240
钼酸盐、单宁酸/HEDP 钝化
1.02 1.01
1 0.99 0.98 0.97 0.96
时间(s)
钝化膜溶膜曲线
钼酸盐、单宁酸/HEDP 钝化
未钝化试样(24h)
钝化试样 (72h)
盐雾试验的表面形貌
25 20 15 10
5 0
10 30 60 90 120 150 180 钝化时间(s)
钝化时间与腐蚀率
钼酸盐、单宁酸/HEDP 钝化
腐蚀率(%)
30
25
20
15
10
5
0
30
40
50
60
70
80
钝化温度(℃)
钝化温度与腐蚀率
腐蚀率(%)
钼酸盐、单宁酸/HEDP 钝化
15 14 13 12 11 10
硅酸盐、植酸/聚乙烯醇钝化
由于这种钝化膜层具有双层结构,外层是 致密的聚乙烯醇膜,表面形成隔离层,使腐蚀 介质很难通过膜层对锌层进行腐蚀。内层是硅 酸盐钝化膜,改善锌镀层与外层聚乙烯醇膜的 结合力,另外由于植酸/硅酸盐的缓蚀作用, 在钝化层表面出现划伤时也可得到保护。
锑无铬钝化

锑无铬钝化锑无铬钝化是一种环保、高效的表面处理技术,广泛应用于金属制品的防腐、美观和提高耐磨性能。
本文将介绍锑无铬钝化的原理、特点及其应用指导,为读者提供有益的知识。
锑无铬钝化的原理是利用锑化合物在金属表面形成一层防护膜,达到锑无铬钝化的效果。
这种防护膜具有紧密结构,能阻隔外界氧气、湿气和化学物质的侵蚀,有效延长金属制品的使用寿命。
锑无铬钝化的特点有以下几个方面。
首先,它是一种环保的表面处理技术,与传统的铬酸盐钝化技术相比,不含有害物质,对环境无污染。
其次,锑无铬钝化能够显著提高金属制品的耐腐蚀性能,大大延长使用寿命。
再次,它具有优异的装饰性能,能使金属制品表面呈现出丰富多样的颜色,满足不同客户的审美要求。
最后,锑无铬钝化的成本相对较低,可降低生产成本,提高企业竞争力。
锑无铬钝化技术在多个领域都有广泛的应用。
首先,在汽车制造业中,锑无铬钝化能够用于汽车车身、发动机零部件等金属制品的防腐处理,提高其耐候性和抗腐蚀性能。
其次,在电子产业中,锑无铬钝化可用于电子元件和连接器等金属零部件的防腐处理,保证电子设备的可靠性。
再次,在建筑业中,锑无铬钝化可用于钢结构、铝合金门窗等金属制品的防腐和装饰处理,提高建筑物的美观度和耐久性。
此外,锑无铬钝化还广泛应用于航空、航天等高端制造领域。
针对锑无铬钝化技术的应用,有一些指导意义的注意事项。
首先,操作人员应严格遵守操作规程,保证操作过程的安全性。
其次,应根据不同金属材料的特性和使用环境的要求,合理选择合适的锑无铬钝化剂和处理方法。
再次,根据实际需要,可进一步采用涂覆和封闭技术,提高膜层的稳定性和耐久性。
最后,应加强对锑无铬钝化技术的研究和创新,提高其在不同领域的适用性和效果。
总之,锑无铬钝化是一种环保、高效的表面处理技术,具有广泛的应用前景。
通过加强对锑无铬钝化技术的研究和推广,可以进一步促进金属制品的防腐和装饰性能的提升,推动相关产业的可持续发展。
镀锌 无铬钝化

镀锌无铬钝化镀锌是一种常见的金属表面处理方法,用于提高金属材料的耐腐蚀性能。
而无铬钝化是一种环保型的钝化处理方法,用于取代传统的铬酸钝化处理方法。
本文将详细介绍镀锌和无铬钝化的原理、工艺和应用。
一、镀锌镀锌是将金属材料(通常为钢铁)表面覆盖一层锌层的过程。
镀锌的主要目的是提高金属材料的耐腐蚀性能,延长其使用寿命。
镀锌可以分为热镀锌和电镀锌两种方法。
热镀锌是将金属材料浸入熔融的锌中,通过化学反应在材料表面形成一层锌层。
热镀锌具有镀层厚度均匀、附着力强等优点,适用于大型金属构件的防腐处理。
电镀锌是通过电解的方式在金属材料表面沉积一层锌层。
电镀锌工艺复杂,但可以控制镀层的厚度和均匀性,适用于小型金属制品的防腐处理。
二、无铬钝化无铬钝化是一种新型的钝化处理方法,用于替代传统的铬酸钝化处理方法。
无铬钝化主要是指在金属表面形成一层无毒无害的钝化膜,以提高金属材料的耐腐蚀性能。
无铬钝化主要有三种方法:无铬酸钝化、无铬离子钝化和无铬溶液钝化。
这些方法都不含有害的六价铬离子,对环境友好,符合环保要求。
三、镀锌无铬钝化的优势镀锌无铬钝化是将镀锌和无铬钝化两种工艺相结合的一种处理方法。
它综合了镀锌和无铬钝化的优点,具有以下几个方面的优势:1. 良好的耐腐蚀性能:镀锌能有效保护金属表面,而无铬钝化能形成一层致密的钝化膜,进一步提高金属材料的耐腐蚀性能。
2. 环保节能:无铬钝化不含有害物质,对环境友好,符合现代环保要求。
而且无铬钝化工艺相对简单,能够降低能源消耗。
3. 经济实用:镀锌无铬钝化工艺成本相对较低,适用于大规模生产。
同时,镀锌无铬钝化的处理周期短,能够提高生产效率。
四、镀锌无铬钝化的应用镀锌无铬钝化广泛应用于各个领域,特别是在建筑、汽车、电子等行业。
具体应用包括以下几个方面:1. 建筑领域:镀锌无铬钝化处理后的钢材具有良好的耐候性和耐腐蚀性能,常用于建筑结构、屋面、外墙等部位。
2. 汽车领域:镀锌无铬钝化能够提高汽车零部件的耐腐蚀性能,延长其使用寿命。
镀锌板无铬钝化液研究综述
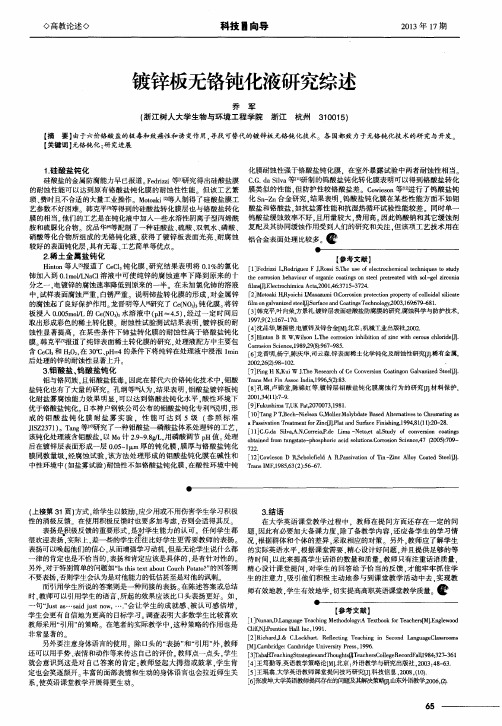
科技 嚣向导
2 0 1 3 年1 7 期
镀锌板无铬钝化液研究综述
乔 军
( 浙 江 树 人大 学 生物 与 环 境 工 程 学 院
浙江
杭州
3 1 O 0 1 5 )
【 摘 要】 由于六价铬酸盐的极毒和致癌性和诱变作 用 , 寻找 可替代 的镀锌板无铬钝化技术 。各 国都致 力于无铬钝化技 术的研 究与开发 。 【 关键词 】 无铬钝化 ; 研究进展
铝合金表面处理比 较多。 ●
【 参考文献】 H i n t o n 等 人 报道 了 C e C 1 钝化膜 . 研 究结果表 明将 O . 1 %的氯 化 [ 1 ] F e d r i z z i L , R o d i r g u e z F J , R o s s i s . T h e u s e o f e l e c t r o c h e m i c a l t e c h n i q u e s t o s t u d y 铈加入到 0 . 1 m o Y L N a C 1 溶液 中可使 纯锌的腐蚀速 率下降 到原来 的十 t h e c o r r o s i o n b e h a v i o u r o f o r g a n i c c o a t i n g s o n s t e e l p r e t r e a t e d w i t h s o l - g e l z l r e o n i a 分之一 . 电镀锌的腐蚀速率降低到原来的一半 。在未加氯化铈 的溶液 f i l ms [ J ] . E l e c t r o c h i mi c a Ac t a , 2 0 01 , 4 6 : 3 7 1 5 — 3 7 2 4 . 中. 试样表面腐蚀严重 , 白锈严重 。说明铈盐转化膜 的形成 , 对金属锌 [ - 2 ] M o t o a k i H , R y o i c h i I , M a s a z u m i O . C o r r o s i n a p r o t e c t i o n p r o p e r t y o f c o l l o i d a l s i l i c a t e i l m o n g a l v a n i z e d s t e e l [ J ] Su r f a c e nd a C o a t i n g s T e c h n o l o g y , 2 0 0 3 , 1 6 9 : 6 7 9 - 6 8 1 . 的腐蚀起 了良好保护作用 。 龙晋明等人 研究 了 C e ( N O 3 ) , 钝 化膜。 将锌 f 3 ] 韩克平, 叶向荣, 方景礼 . 镀锌层表面硅酸盐防腐膜的研究腐 蚀科学与防护技术, 板 浸入 0 . 0 0 5 mo l / L的 C e ( N O 3 ) 水溶 液中 ( p H 4 . 5 ) , 经过 一定 时间后 『 1 9 9 7 , 9 ( 2 ) : 1 6 7 — 1 7 0 . 取 出形成彩色 的稀土转化膜。耐蚀性试 验测试 结果 表明 . 镀锌板 的耐 [ 4 ] 沈品华, 屠振密. 电镀锌及锌合金I M ] . 北京 : 机械工业 出版社, 2 0 0 2 . 蚀 性显著提高 .在某些 条件下铈盐转化膜 的耐蚀性高 于铬酸盐钝化 [ 5 ] H i n t o n B R W, Wi l s o n L T h e c o r r o s i o n i n h i b i t i o n o f z i n c w i t h c e r o u s c h l o i r d e 叨. 膜。 韩克平时艮 道 了纯锌表面稀土转化膜的研究 , 处理液 配方 中主要包 C o r r o s i o n S c i e n c e , l 9 8 9 , 2 9 ( 8 】 : 9 6 7 — 9 8 5 . 含c e c l 和H O . 在3 0 o C 、 p H = 4的条件下将纯锌在处理液 中浸泡 l m i n [ 6 ] 龙晋 明, 杨பைடு நூலகம், 陈庆华, 司云森钟 表面稀土化学钝化及耐蚀性研究阴. 稀有金属, 后处理 的锌 的耐蚀性显著上升 2 0 0 2 , 2 6 ( 2 ) : 9 8 - 1 0 2 . .
镀锌 无铬钝化
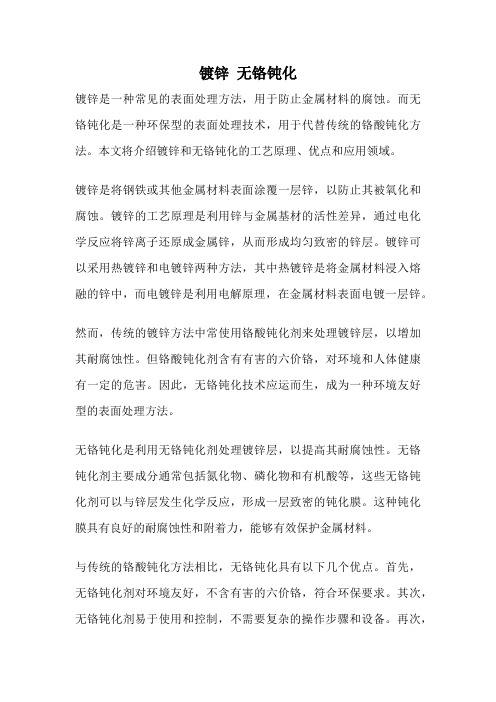
镀锌无铬钝化镀锌是一种常见的表面处理方法,用于防止金属材料的腐蚀。
而无铬钝化是一种环保型的表面处理技术,用于代替传统的铬酸钝化方法。
本文将介绍镀锌和无铬钝化的工艺原理、优点和应用领域。
镀锌是将钢铁或其他金属材料表面涂覆一层锌,以防止其被氧化和腐蚀。
镀锌的工艺原理是利用锌与金属基材的活性差异,通过电化学反应将锌离子还原成金属锌,从而形成均匀致密的锌层。
镀锌可以采用热镀锌和电镀锌两种方法,其中热镀锌是将金属材料浸入熔融的锌中,而电镀锌是利用电解原理,在金属材料表面电镀一层锌。
然而,传统的镀锌方法中常使用铬酸钝化剂来处理镀锌层,以增加其耐腐蚀性。
但铬酸钝化剂含有有害的六价铬,对环境和人体健康有一定的危害。
因此,无铬钝化技术应运而生,成为一种环境友好型的表面处理方法。
无铬钝化是利用无铬钝化剂处理镀锌层,以提高其耐腐蚀性。
无铬钝化剂主要成分通常包括氮化物、磷化物和有机酸等,这些无铬钝化剂可以与锌层发生化学反应,形成一层致密的钝化膜。
这种钝化膜具有良好的耐腐蚀性和附着力,能够有效保护金属材料。
与传统的铬酸钝化方法相比,无铬钝化具有以下几个优点。
首先,无铬钝化剂对环境友好,不含有害的六价铬,符合环保要求。
其次,无铬钝化剂易于使用和控制,不需要复杂的操作步骤和设备。
再次,无铬钝化膜的耐腐蚀性和附着力较好,可以提高镀锌层的使用寿命。
此外,无铬钝化技术还可以应用于不同种类的金属材料,具有广泛的适用性。
无铬钝化技术在许多领域都得到了广泛的应用。
在汽车工业中,无铬钝化技术可以用于镀锌钢板的表面处理,提高汽车车身的耐腐蚀性。
在电子行业中,无铬钝化技术可以用于镀锌接插件、电子元器件等的表面处理,提高其导电性和耐腐蚀性。
在建筑行业中,无铬钝化技术可以用于镀锌钢管、钢结构等的表面处理,延长其使用寿命。
镀锌和无铬钝化是两种常见的表面处理方法。
镀锌可以通过热镀锌和电镀锌两种方法实现,用于防止金属材料的腐蚀。
而无铬钝化是一种环保型的表面处理技术,通过使用无铬钝化剂处理镀锌层,提高其耐腐蚀性。
对镀锌层无铬钝化技术的

镀锌层无铬钝化的性能评价
耐腐蚀性能的评估
评估方法
一般采用中性盐雾试验(NSS)和循环伏安法(CV)等方法对镀锌层无铬钝化膜的耐腐蚀性能进行 评估。
结果分析
经过无铬钝化处理的镀锌层具有良好的耐腐蚀性能,可有效延缓腐蚀速率,提高产品的使用寿命。
表面质量的评价
评估方法
采用电子显微镜(SEM)和表面粗糙度 仪等设备对镀锌层无铬钝化膜的表面质 量进行观察和测量。
未来的研究领域将包括开发新的无铬 钝化剂、优化无铬钝化工艺、评估无 铬钝化技术的环境影响和经济效益等 。
03
技术应用
随着人们对环保和耐腐蚀性的需求不 断增加,无铬钝化技术的应用前景将 更加广阔,未来将有更多的行业开始 采用这一技术。
THANKS
感谢观看
传统的镀锌层铬酸盐钝化技术虽然成熟,但存在 环境污染和健康危害等问题。
无铬钝化技术的发展逐渐成为关注焦点,具有环 保、低毒、高耐腐蚀等优点。
技术现状与发展趋势
目前,无铬钝化技术主要分为有机物钝 化、无机物钝化、纳米材料钝化等。
随着环保意识的提高和技术的不断发展 ,无铬钝化技术将会有更广泛的应用前 景。
05
CATALOGUE
无铬钝化技术在生产中的应用案例分析
在汽车行业的应用案例
汽车零部件的防腐蚀
无铬钝化技术可以用于汽车零部件的防腐蚀 处理,提高零部件的耐久性和可靠性,降低 维修成本。
环保和安全性
无铬钝化技术不含铬,减少了环境污染和对 人体的危害,更符合现代汽车生产中的环保
要求。
在家电行业的应用案例
对镀锌层无铬钝 化技术的探讨
2023-11-10
目 录
• 引言 • 无铬钝化技术概述 • 镀锌层无铬钝化工艺研究 • 镀锌层无铬钝化的性能评价 • 无铬钝化技术在生产中的应用案例分析 • 结论与展望
铁基电镀锌层的无铬钝化处理研究
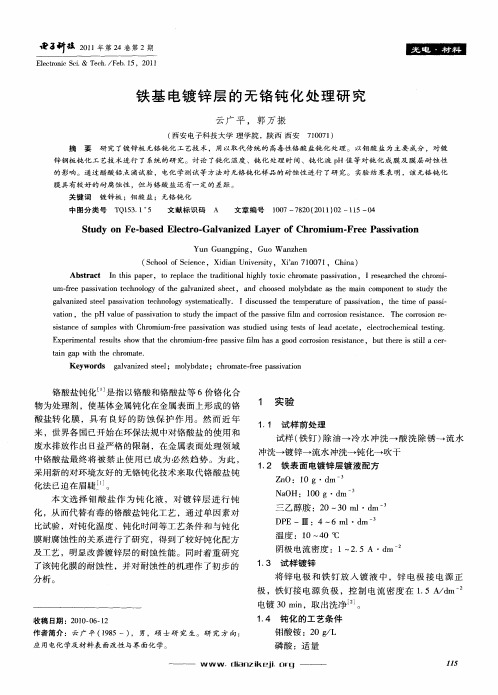
中图分类号
S ud n Fe. s d El c r . l a z d La e f Chr mi t y o . e e t o. ba Ga v nie y r o o um . e s i a i n . e Pa sv to Fr
u — e a sv t n tc n lg fte g la ie h e , a d c o s d moy d t st e man c mpo e tt t d h m f e p s iai e h oo y o h av n z d s e t n h o e lb ae a h i o r o n n o su y te g v n z d se lp siai n tc n lg y t maial . Ids u s d t e tmp r tr fp s iain。 t etmeo a s— l a a ie te a sv t e h oo s se t l o y c y ic s e h e eau e o a sv t o h i fp s i v t n. t e p v l eo a sv to osud h mp c ftep siefl a d c ro in rssa c . Th o rso e ai o h H au fp s iain t t y te i a t a sv m n or so e itn e o h i ec ro in r— ssa c fs mp e t r mi m - e a sv t n wa td e sn e t fl a c tt ee to h mia e t g itn eo a lswih Ch o u f e p s ia i s su id u ig t ss o e d a eae, lcr c e c ltsi . r o n Ex e i na e u t h w h tte c rmi m — e a sv l h sag o or so e itn e, b tte ei t lac r p rme tlr s lss o t a h h o u f ep sief m a o d c ro inr ssa c r i u h r ssi e — l ti a t h h o t. an g p wih t e c样 前处 理 .
铝合金表面无铬钝化的研究

可 以在 铝合金 线材 表面形 成致 密 、均 匀 、具 有一定 厚 度 的钝 化膜 。同时 ,该 钝 化 膜 还 能起 到 一 定 的抛 光 作用 ,为铝合 金材 料 的后 续 使 用 提供 一 个 质量 较 好 的 表 面 。
1 实 验
1.1 实 验 药 品 硫酸 ,硫酸 钠 ,无水 硫 酸铜 ,尿素 。
Key words: aluminum alloy;chrom ium—free passivation;corrosion resistance
中图分 类号 :TG 174 文 献标 志码 :A 文章编 号 :1000-4742(2018)03—0034—03
0 前 言
铝合 金具有 密 度 低 、强度 高 、塑 性好 等优 点 ,已 广泛 应用 于航 空 、航 天 、汽 车 、机 械 制 造 等 行 业 _1]。 铝合 金表 面存 在一 层 自然 氧 化 膜 ,但 其耐 腐 蚀 能力 有 限 ,这使 得铝 合金 在使用 过程 中容易 受到腐 蚀 ,造 成 原料 的极度 浪 费 。因此 ,铝合 金 在 使用 前 必 须 经 过 防腐蚀 处理 。传 统 的处 理方 法是对 铝合金 进行 铬 酸 盐钝化 。经 过 铬 酸 盐 钝 化 处 理 的线 材 具 有 耐 腐 蚀 、美 观 、自修 复等 优点 。铬酸 盐钝 化是 目前 较 为成 熟 的钝 化工 艺 ,但 铬 酸盐 钝 化 液 中含 有 对 人体 和环 境 极为有 害 的 Cr(III)。就此 问题 ,从 2003年起 ,世 界各 国先后 颁布 了禁用 铬酸 盐钝化 液 的相 关规 定 。
间 10~ 20 S。
关键 词 : 铝合金 ;无 铬钝 化 ;耐蚀性
Abstract: The effects of the mass concentration of sulfuric acid, sodium sulfate, anhydrous cupric sulfate and urea,and passivation tem perature as well as passivation time on the corrosion resistance of chrome—free passivation film s on alum inum alloy were investigated. Result showed
无铬钝化液配方成分分析,钝化原理及工艺指标控制

无铬钝化液配方成分分析,钝化原理及工艺指标控制导读:本文详细介绍了无铬钝化液的研究背景,理论基础,参考配方等,本文中的配方数据经过修改,如需更详细资料,可咨询我们的技术工程师。
无铬钝化液广泛应用金属材料表面处理,禾川化学引进国外配方破译技术,专业从事钝化液成分分析、配方还原、研发外包服务,为钝化液相关企业提供一整套配方技术解决方案。
一.背景一种活性金属或合金,其中化学活性大大降低,而成为贵金属状态的现象,叫钝化。
金属由于介质的作用生成的腐蚀产物如果具有致密的结构,形成了一层薄膜(往往是看不见的),紧密覆盖在金属的表面,则改变了金属的表面状态,使金属的电极电位大大向正方向跃变,而成为耐蚀的钝态。
如Fe→Fe++时标准电位为-0.44V,钝化后跃变到+0.5~1V,而显示出耐腐蚀的贵金属性能,这层薄膜就叫钝化膜。
铝合金表面的化学转化膜工艺大体可以分为两种: 一种是铬酸盐钝化处理法,一种是非铬酸盐钝化处理法虽然铬酸盐钝化处理具有许多优越之处,但是由于(Cr)毒性高,易致癌,对环境污染大,许多国家已经严格限制铬酸盐的使用与排放,并且随着欧盟指令的生效使得铬酸盐在金属表面处理中的使用受到极大的限制因此,研制新型无铬钝化工艺取代传统铬酸盐钝化十分必要。
禾川化学技术团队具有丰富的分析研发经验,经过多年的技术积累,可以运用尖端的科学仪器、完善的标准图谱库、强大原材料库,彻底解决众多化工企业生产研发过程中遇到的难题,利用其八大服务优势,最终实现企业产品性能改进及新产品研发。
样品分析检测流程:样品确认—物理表征前处理—大型仪器分析—工程师解谱—分析结果验证—后续技术服务。
有任何配方技术难题,可即刻联系禾川化学技术团队,我们将为企业提供一站式配方技术解决方案!二.钝化液2.1钝化原理金属铁,铝在稀硝酸或稀硫酸中能够很快溶解,但在浓硝酸或浓硫酸中溶解现象几乎完全停止,碳钢通常很容易生锈,若在钢中加入适量的Ni、Cr,就成为不锈钢了。
无铬钝化的研究进展

无铬钝化的研究进展摘要:综述了国内外研究的几种主要无铬钝化工艺,指出随着对环保要求的提高,用低毒性的钝化剂代替高毒性的六价铬酸盐的研究受到重视。
1. 引言大多数工业应用的金属及镀层金属(如铁、锌、铝、锡、铅、镁等及其合金)均可形成化学转化膜,用于提高耐蚀性的化学转化膜主要有磷化和铬酸盐钝化等。
其中铬酸盐钝化处理由于可形成铬/基体金属的混合氧化物膜层,膜层中铬主要以三价铬和六价铬形式存在,三价铬作为骨架,而六价铬则有自修复作用,因而耐蚀性很好。
由于铬酸盐成本低廉,使用方便,因而铬酸盐钝化处理在航空、电子和其他部门得到了广泛的应用。
但铬酸盐毒性高且易致癌,随着环保意识的增强,铬酸盐的使用受到严格的限制,急需开发低毒性的铬酸盐替代品。
本文就目前国内外研究的几种主要无铬钝化工艺进行了讨论。
2. 钼酸盐与钨酸盐钝化2.1 钼酸盐钝化钼、铬同属VIA族,钼酸盐已广泛用作钢铁及有色金属的缓蚀剂[1]和钝化剂。
钼酸盐钝化处理的方法主要有阳极极化处理、阴极极化处理和化学浸泡处理等。
英国Loughborough大学研究了钼酸盐钝化处理过程中的电化学特性[2~6],还研究了锌表面的化学浸泡处理[7]。
结果表明,尽管钼酸盐钝化的效果不如铬酸盐钝化,但可以明显提高锌、锡等金属的耐蚀性。
日本神户钢铁公司研究出一种提高镀锌钢抗白锈能力的钼酸盐钝化方法,并取得专利[8,9]。
钝化液中含钼酸或钼酸盐,24h盐雾试验(按照标准JISZ2371)后,耐蚀性最好的达到5级,即出白锈面积0~1%。
用钼酸盐/磷酸盐体系处理电镀锌层表面,在无添加剂的情况下可以产生与深黄色铬酸盐钝化相似的耐蚀效果,而有添加剂时则可缩短最佳钝化时间使之小于5min[10]。
Tang等 [11,12]研究出一种用钼酸盐/磷酸盐体系处理锌的工艺,申请了专利[13],钝化处理液含钼酸盐,以Mo计2.9~9.8g/L,用可与钼酸盐形成杂多酸的酸(如磷酸)调节pH值。
这种处理方法在锌层表面形成0.05~1.00μm厚的膜层,膜厚与铬酸盐钝化膜同数量级,并可产生相应的装饰效果。
- 1、下载文档前请自行甄别文档内容的完整性,平台不提供额外的编辑、内容补充、找答案等附加服务。
- 2、"仅部分预览"的文档,不可在线预览部分如存在完整性等问题,可反馈申请退款(可完整预览的文档不适用该条件!)。
- 3、如文档侵犯您的权益,请联系客服反馈,我们会尽快为您处理(人工客服工作时间:9:00-18:30)。
2.5 盐雾试验比较
镀锌板目前因其本身具有较高耐腐蚀性能已被广大高质量家电企业所采用。为检验硅烷化 处理对于镀锌板的耐腐蚀性能以及附着力表现,设计试验对镀锌试片采用各种前处理工艺,并
对其喷涂相同厚度的粉末涂料进行涂装,通过 500 小时盐雾试验对其进行附着力比较。
★
★
⑦水洗
★
☆
⑧水洗
★
☆
注:★需要 ☆不需要
由表 1 可见,硅烷化处理与磷化处理相比较可省去表调及磷化后两道水洗工序。因硅烷化 处理时间短,因此在原有磷化生产线上无需设备改造,只需调整部分槽位功能即可进行硅烷化 处理:(1)对于悬链输送方式改造,可将①预脱脂、②脱脂、④水洗、保留;③水洗改为脱脂 槽;⑤表调、⑥磷化改为水洗槽;⑦水洗改为硅烷化处理;⑧备用。在改换槽位功能的同时提
根据 GB/T10125 人造气氛腐蚀试验--盐雾试验对试验镀锌试片进行 500 小时中性盐雾试验。 试片漆膜平均厚度为 70±2μm。对镀锌板进行附着力比较试验,同样用划刀延划叉部位向边缘
部位剥离,考察其可剥离宽度。图 5 所示为此项试验结果。
普通锌系磷化 镀锌专用磷化 硅烷化
通过试验结果可以看出,普通锌系磷化可剥离宽度最大,镀锌专用磷化可剥离宽度较普通 锌系磷化小,硅烷化可剥离宽度几乎为零,附着力表现最佳。由此可得出结论,在镀锌板上运
②缩合反应:
成膜反应是影响硅烷化质量的关键步骤,成膜反应进行的好坏直接影响涂膜耐蚀性及对漆 膜的附着力。因此,对于处理剂的 pH 值等参数控制显的尤为重要。并且对于硅烷化前的工件 表面状态提出了更高的要求:1、除油完全;2、进入硅烷槽的工件不能带有金属碎屑或其他杂
质;3、硅烷化前处理最好采用去离子水。
③成膜反应:
其中 R 为烷基取代基,Me 为金属基材
成膜后的金属硅烷化膜层主要由两部分构成:其一即在金属表面,硅烷处理剂通过成膜反 应形成金属硅烷复合膜,二是通过缩合反应形成大量低聚硅氧烷,从而形成完整硅烷膜,金属
表面成膜状态微观模型可描述为图 1 所示结构。
2 硅烷处理与磷化的比较
硅烷处理与磷化及铬钝化比较在工位数量、处理条件、使用成本以及与漆膜附着力性能方 面优势明显。并且在环保方面更适应国家对于各家电涂装生产企业的要求,真正达到节能减排
复使用。有效提高油漆对基材的附着力。可共线处理铁板、镀锌板、铝板等多种基材。
美国已于上世纪 90 年代就开始对金属硅烷前处理技术进行理论研究,欧洲于上世纪 90 年 代中期也开始着手对于硅烷进行试探性研究。我国在本世纪初迫于环保方面的巨大压力,各大
研究机构及生产企业也着手对硅烷进行研究。
1 基本原理
用硅烷化处理工艺后,可显著提高镀锌板与漆膜间的附着力,提高镀锌涂装产品的质量。
2.6 温水浸泡比较
铝及铝合金材料本身具有重量轻、高强度等优点,目前已被家电零部件配套厂商所使用, 传统的铝材表面处理主要为阳极氧化和铬钝化两种。但阳极氧化处理存在使用成本高,设备投 入大等缺点,而铬钝化本身存在对环境的巨大危害性。硅烷处理本身为环保型处理产品,对环 境友好,同时使用成本与铬钝化相当,大大低于阳极氧化成本,因此可看做为铝件涂装前处理
的理想替代产品。
根据 GB/T1720 漆膜附着力测定法,对铝板进行不同处理并涂覆聚酯粉末涂料(厚度 50±2 μm),温水(40±2℃)浸泡 1200 小时后,对其进行划圈试验。.通过试验结果可以看出,未处
理板为 7 级;铬钝化板为 4 级;硅烷处理板为 1 级。硅烷处理附着力最佳。
3 硅烷处理线设计
实验,具体实施为图 4 所示。
铁系磷化 锌系磷化 硅烷化
通过附着力比较试验结果后可以明显看到,铁系磷化可剥离宽度较锌系磷化与硅烷化差别 明显。铁系磷化为大面积可剥离,而锌系磷化与硅烷化处理板其可剥离宽度基本为零。因此可 明显看出锌系磷化和硅烷化处理与漆膜附着力相当,同时两者附着力明显优于铁系磷化。采用
的目的。
2.1 工位工序方面比较
硅烷化处理对传统磷化处理在操作工艺上有所改进,在工艺过程方面现有磷化处理线无需 改造即可投入硅烷化生产。表 1 对传统磷化工艺和硅烷化处理进行比较。
表 1 磷化与硅烷化工位布置比较
①预脱脂 ②脱脂 ③水洗
传统磷化 ★ ★ ★
硅烷化 ★ ★ ★
④水洗
★
★
⑤表调
★
☆
⑥表面成膜
处理时间 是否需要除渣槽
传统磷化 60-70kg/吨
30-40m2 4-5min
是
硅烷化 30-50kg/吨 200-300m2 0.5-2min
否
使用硅烷化工艺(无铬铬化)能省去磷化加温设备、除渣槽、板框压滤机及磷化污水处理 等设备,节省设备初期投入。在配槽用量方面硅烷化较磷化也减少 20%-50%,更关键的是在每 平方单耗方面硅烷化的消耗量为传统磷化的 15%-20%。在减少单位面积消耗量的同时,在处理
时间上硅烷化较磷化也有较大幅度的缩短,从而提高生产率,减少设备持续运作成本。
2.3 微观形貌比较
因为各种磷化及硅烷化的成膜机理大有不同,因此金属表面的膜层状态及形貌也各不相同。 从微观形貌方面,通过电子扫描电镜(SEM)图 3 观察可发现在金属表面生成的膜层的区别。
金属裸板 铁系磷化
锌系磷化 硅烷化
由以上电镜照片可明显看出,各种处理之间膜层形貌存在较大差异。其中锌系磷化槽液主 体成份是:Zn2+、H2PO3-、NO3-、H3PO4、促进剂等。形成的磷化膜层主体组成(钢铁件)成分为 Zn3(PO4)2·4H2O、Zn2Fe(PO4)2·4H2O。磷化晶粒呈树枝状、针状、孔隙较多。相比较锌系磷化而 言,传统铁系磷化槽液主体组成:Fe2+、H2PO4-、H3PO4 以及其它一些添加物。磷化膜主体组成(钢 铁工件):Fe5H2(PO4)4·4H2O,磷化膜厚度大,磷化温度高,处理时间长,膜孔隙较多,磷化晶 粒呈颗粒状。硅烷化处理为有机硅烷与金属反应形成共价键反应原理,硅烷本身状态不发生改 变,因此在成膜后,金属表面无明显膜层物质生成。通过电镜放大观察,金属表面已形成一层 均匀膜层,该膜层较锌系磷化膜薄,较铁系磷化膜均匀性有很大提高此膜层即为硅烷膜。
高链速进行生产,以加快前处理生产节拍,提高生产率。改造后工位设置见图 2 所示。
1.预脱脂 2.脱脂 3.脱脂 4.水洗 5.水洗 6.水洗 7.硅烷化 8 备用
1.1.2 处理条件方面比较
传统磷化处理因沉渣、含磷及磷化后废水等环保问题,一直是各涂装生产企业为之困扰的 问题。随着国家对环保及节能减排的重视程度不断提高,在未来时间里,涂装行业的环保及能 耗问题会越来突出。硅烷技术的推出,对于整个涂装行业的前处理环保及节能降耗问题,进行
3.1.2 工艺流程
冷轧板、镀锌板、铝板浸泡线工艺流程:
预脱脂→脱脂→水洗→水洗→(纯水洗)→硅烷处理→烘干→喷粉
镀锌板、铝板浸泡线工艺流程:
预脱脂→脱脂→水洗→水洗→(纯水洗)→硅烷处理→烘干→喷粉
因冷轧板本身没有镀锌层及表面氧化膜的保护,在工序间容易返锈。对于冷轧板喷淋线工 艺流程可进行改进,烷处理前增加一步较低浓度的预硅烷处理过程。
价键连接。
为缩短处理剂现场使用所需熟化时间,硅烷处理剂在使用之前第一步是进行一定浓度的预 水解。
①水解反应:
在水解过程中,避免不了在硅烷间会发生缩合反应,生成低聚硅氧烷。低聚硅氧烷过少, 硅烷处理剂现场的熟化时间延长,影响生产效率;低聚硅氧烷过多,则使处理剂浑浊甚至沉淀,
降低处理剂稳定性及影响处理质量。
以及性能等方面进行比较。
[关键词] 无铬铬化,无铬钝化,硅烷;表面处理;磷化
鸣谢撰稿人:
武汉大学
程锡坤教授
中国材料保护研究所 罗苏总工
中南大学
王倚重教授
中国有色金属协会
林祖芳教授
安登金属表面处理公司 程永青总工
0 前言
家电行业目前喷漆或喷粉前处理根据板材不同多采用磷化以及铬钝化处理。但以上两种处 理方法均存在较大缺陷。在环保方面:磷化含锌、锰、镍等重金属离子并且含有大量的磷,铬 钝化处理本身就含有严重毒性的铬,已不能适应国家对于涂装行业的环保要求。在使用成本方 面:磷化处理过程中会产生大量磷化渣,需要一套除渣装置与之配套。并且磷化使用温度大多 为 30-50℃,因此还需要辅助加热设备及热源对磷化槽进行加热。同时磷化及铬钝化后需要大 量溢流水对工件进行漂洗。由于在环保性及使用成本方面存在缺陷,一种新型的环保、节能、
3.1 硅烷处理喷淋线设计
3.1.1 设计理念
为了适应国家对于环境日益严格的要求,涂装前处理线设计理念为无磷、不含重金属和亚 硝酸盐、常温或降温处理的环保节能型涂装前处理线。其特点在于:
1.采用无磷脱脂,环保性好;
2.采用硅烷常温处理,无需加温,节省能源;
3.采用硅烷代替磷化,消除了磷和重金属污染,对环境友好;
金属表面无铬钝化(硅烷化)处理在 铝表面行业的应用
[摘要] 针对家电行业,铝型材加工行业,以及其它金属表面处理行业目前涂装前处理行业所 广泛采用的磷化及铬钝化处理存在的缺陷,提出一种节能环保型涂装前处理新技术。该技术具 有无有害重金属离子,不含磷,无需加温,无渣,处理时间短,控制简便,可共线处理铁板、 镀锌板、铝板多种基材等优点。同时将硅烷处理与传统处理在工位布置、工艺条件、使用成本
硅烷含有两种不同化学官能团,一端能与无机材料(如玻璃纤维、硅酸盐、金属及其氧化 物)表面的羟基反应生成共价键;另一端能与树脂生成共价键,从而使两种性质差别很大的材 料结合起来,起到提高复合材料性能的作用。硅烷化处理可描述为四步反应模型:(1)与硅相 连的 3 个 Si-OR 基水解成 Si-OH;(2)Si-OH 之间脱水缩合成含 Si-OH 的低聚硅氧烷;(3)低聚 物中的 Si-OH 与基材表面上的 OH 形成氢键;(4)加热固化过程中伴随脱水反应而与基材形成共