SPC改进追踪记录表
核内部稽改善追踪表 (1)

日期部门项次不符合发现改善对策预计完成时间改善佐证负责人175L集尘机点检表中,风机机油更换频率1500H/三个月,频率描述存在矛盾;最近保养时间显示为2011年11月更正设备点检内容资料:风机无使用机油部分删除2014.4.15集尘维护点检表蒋华275L空压机点检表中,润滑油之规范及使用保养项目中,保养方法存在初次500H及每1000H的更换频率,此要求只会存在一个点检记录,实际查阅发现同时存在两项记录;且点检方式没有直接记录数据(设备可显示使用时间);更正设备点检内容资料:取消保养方法存在初次500H及每1000H的更换频率2014.4.15空压机维护点检表蒋华375L冷却冰水系统点检表中,显示4/9厂家进行了维护保养及冷冻油更换,查该设备的保养记录时,没有登记此次保养记录更正资料2014.4.15设备保养记录蒋华475L胶片冷却机的切胶刀已于3/29由管理部更换,实际点检表上最近保养时间2013.01.20,未更新更换时间更正设备点检内容资料2014.4.15胶片冷却机维护点检表蒋华内部稽核改善追踪表04.12制造部575L密炼机润滑油最新更换时间为3/25,点检表中最近保养日期2013.01.30,点检表中未更新时间更正设备点检内容资料:取消保养方法存在初次500H及每1000H的更换频率2014.4.15密炼机维护点检表蒋华6100KG包装台秤和2000KG叉车秤的校秤记录表,“误差栏位”人员填写方式不一致统一填写方式2014.4.15校秤记录表周晓新7切胶机液压油更换频率为使用2000H,实际设备无时间记录功能,也没有其他方面记录显示使用时间,此频率无从点检更正设备点检内容资料2014.4.15切胶机维护点检表蒋华8冷却机工具领用表,4/12下午15:20左右查看此记录,显示4/12之归还时间及归还人员已经记录;且4/1~4/11之工具归还,无主管确认签名要求按时填写,主管及时签名2014.4.15工具领用表周晓新975L现场包装用台秤,编号P1-Y-01无校秤记录要求按时填写,主管及时签名2014.4.15校秤记录表周晓新2014.04.12制造部。
附录2 过程改进建议及处理跟踪表

输入:
建议人姓名、所属部门
发现问题的项目名称和编号、建议日期
问题描述
尽可能清晰的描述问题
说明所遭遇的问题对产品、过程的影响,以及相关的问题
建议描述
1)尽可能明确的描述所建议的过程改进。
2)如果可能,给出所影响特定过程元素,和更改的文字和条目。
3)在列举多个问题的地方,指出每个提议相关联的问题。
改进说明
过程改进建议管理一览表
序号
信息来源
提出人
提出日期
改进PA
来源项目
建议改进区域
改进提案
EPG评审意见1
EPG评审日期
改进负责人
改进类别
改进内容描述
解决期限
完成状况
完成日期
EPG评审意见2
EPG评审日期
1
2
3
4
5
6
7
8
9
10
11
12
13
14
15
16
17
18
19
20
21
22
23
24
25
26
27
28
29
30
31
32
33
34
35
36
37
38
39
40
41
42
43
44
45
46
47
48
49
50
1)说明改进的原过程
2)说明改进的内容
3)识别高优先级的PIP
过程改进建议表
姓名
日期
所属部门
表ID
项目名称
问题描述(简要地介绍所遭遇的问题和影响)
建议描述(尽可能完整的描述更改建议,包括影响的表格和过程等)
全套SPC质量管理表格(很全面)

2
0.75 0.85 0.75 0.85 0.65
3
0.75 0.80 0.80 0.70 0.75
4
0.60 0.70 0.70 0.75 0.65
5
0.70 0.75 0.65 0.85 0.80
6
0.60 0.75 0.75 0.85 0.70
7
0.75 0.80 0.65 0.75 0.70
备注及原因追 查:
n d2 D3 D4 A2
X UCL CL LCL
2
3
4
5
6
7
8
9
10
3.08 2.33 0.22 0 1.78 2.11 0.31 0.58
1.13 1.69 2.06 2.33 2.53 2.7 2.85 2.97 0 0 0 0 0 0.08 0.14 0.18 3.27 2.57 2.28 2.11 #### 1.92 1.86 1.82 1.88 1.02 0.73 0.58 0.48 0.42 0.37 0.34
制程能力分析
0.09 Std.Dev.=
R 管 制 图
0.50 0.40 0.30 0.20 0.10 0.00 1 2 3 4 5 6 7 8 9 10 11 12 13 14 15 16 17 18 19 20 21 22 23 24 25
Sigma = 0.08 PPK= 0.72 PP = 0.78 Ca = 8.00% CPK= 0.80 CP = 0.87 Grade = D
0.00 0.00 0.00 0.00 0.00 0.00
#### #### #### #### #### #### ####
0.38 0.38 0.38 0.38 0.38 0.38 0.38 0.38 0.38 0.38 0.38 0.38 0.38 0.38 0.38 0.38 0.38 0.38 0.38 0.38 0.38 0.38 0.38 0.38 0.38 0.38 0.18 0.18 0.18 0.18 0.18 0.18 0.18 0.18 0.18 0.18 0.18 0.18 0.18 0.18 0.18 0.18 0.18 0.18 0.18 0.18 0.18 0.18 0.18 0.18 0.18 0.18
生产现场改善计划追踪表范例

1.扩大不良提案的宣传,提升产 品质量意识; 2.安排《检验标准》、《作业指 满足公司质量标 导》的培训,要求100%达标; 准 3.有效推行《员工绩效管理办法 》
计划进度
3 4 5 6 7 8 9 10 11 月月月月月月月月月
1.员工没有认识到5S5的
5S活动成果不能很 好的保持和执行
重要性; 2.班组长不能很好的处 理生产组织与推行5S的
1.严格按日排产执行;
2.班组长及时跟进工装维修进
度;
整体工作效率提
3.引进、学习快速换模方法,缩 高
短调试时间;
4.执行《员工绩效管理办法》
余料浪费较多
1.缺乏余料管理文件支 持,至使余料管理不 善; 2.缺乏工艺改进意识
1.编制《余料使用、管理办法 》; 2.重点加强公司针对现场的工艺 改进力度
训及实际操作;
生产到达1小时
2.实施快速换模的改善
以内
包装效率不高,浪 费大量的人工工时
产品修边、表面处理控 制不稳定,人员无法高 效的作业
分批纳入“IE改善项目”,实施 一次性合格率高
优先改善
于90%
环 现场定置不理想 工作区域存在不合理性
1.员工提升、发展机会
士气
多数员工缺乏归属 感
不多; 2.没有合理利用绩效考 核、不利于调动员工工
产品落地普遍
1.缺乏标准作业指导; 2.配备必要的辅助物 件; 3.5S推进不彻底
1.编制《作业指导书》,培训推 广实施; 2.分析实际。制作必要的产品隔 无落地件 离、流出辅助物件; 3.加强5S推进、检查力度
1.技术员对设备保养执
机
行不力;
2.班组长对设备保养组
设备/工装保养不 织、监控部到位;
SPC(统计过程控制)模板

SPC(统计过程控制)模板
SPC(统计过程控制)模板是用于监控和控制过程稳定性的工具。
SPC模板通常包括一系列图表和计算方法,可以帮助分析人员确定过程是否处于控制状态,以及如果不在控制状态,如何对其进行调整。
通常使用的SPC模板包括以下几种常见图表:
1. 控制图:控制图是SPC的核心工具之一,用于追踪过程的变化。
常见的控制图包括X-Bar图、R图和S图,用于监控过程的平均值和变异性。
2. 范围图:范围图用于监控过程的变异性。
范围图通常与X-Bar 图或S图配合使用,可以帮助识别过程中的特殊因素或异常变动。
3. 累积和图:累积和图用于检测过程中的漂移或累积误差。
该
图表显示过程的累积和,可以帮助识别潜在的问题。
4. 直方图:直方图用于分析过程的分布情况。
通过将数据分组
并绘制直方图,可以了解过程的分布形状和偏度。
除了图表外,SPC模板还可以包括以下计算方法:
1. 操作界限:操作界限是用于确定过程是否处于控制状态的参
考线。
通过计算过程的平均值、标准偏差和规格限制,可以确定上限
和下限。
2. 过程能力指数:过程能力指数是用于评估过程的稳定性和能
力的指标。
常见的过程能力指数包括Cp、Cpk、Pp和Ppk,用于确定过程是否符合规格要求。
SPC模板可以根据具体的需求进行自定义和调整,以满足不同过
程的监控和控制要求。
一旦SPC模板建立起来,就可以通过定期收集
和分析过程数据,及时发现和解决潜在问题,提高过程质量和稳定性。
工艺改进跟踪记录表

产品编号 工艺研发负责部门
序号 工序/步骤 改进问题
问题原因
工艺改进跟踪记录表
产品名称 工艺研发负责人
制表日期: 项目编号 产品规格 工艺文件编号
计量单位
改进内容/对策 改进意见提出者 拟实施时间 实际实施时பைடு நூலகம் 实施情况 实施取得效果 验收人
总体实施完成情况 意见及建议
经办部门或检查人员签字
批准人:
审核人:
制表人:
说明:本表格主要用于跟踪记录和分析工艺改进方案的实施情况及实际效果,便于工艺研发负责人实时掌控工艺改进进度以及工艺质 量,并对工艺研发项目进行持续改善、不断提高工艺质量。
问题改善跟踪表

物探/采购 1 (金丹) 2
问题点 毛坯到货率低 岗位职责不清
温岭市双江车辆部件有限公司
第 周( 月 日至 月 日)问题改善跟踪表
原因分析
限电问题,导致厂商生产进 度受阻
改善措施
责任人 金丹
跟进人
计划完成 时间
实际完 成时间
没有明确的岗位职责说明书
设立岗位说明书
董连勇
8月10日 8月10日
1 毛坯漏加工及工废件多
张华侨
生产/装配 2 (胡光明) 3
毛坯供应不及时 牡丹泵弹片不合理
金工车间未按订单加工毛坯 件
按新的订单生产计划进度表进行加工
张华侨
林刚
胡光明 8月17日 胡光明 8月17日
4
员工辞职现象较严重
1、加强与员工的沟通;2、采取工资 激励机制。
胡光明
罗老师
在制品的质量管控失控,
沟通不畅;岗位职责不明
王杰
陈小鹏
4
库存数量不清,造成发货 短装
初盘数量不准
重新进行复盘
陈小鹏 陈文燕
杜振海 1
外协件未受控
1、采购对厂商管控不力;2 1、加强对厂商的管控;2、设立
、未设立IQC对来料进行管控
IQC,加强来料质量管控
ห้องสมุดไป่ตู้
2
造成质量管控困难
金工车间生产加工排序不合 理,
生产加工工序尽可能地排成流水线型
生产/金工 (张华侨)
1
有批量性不良品流至下道 生产加工工序安排不合理, 生产加工工序尽可能地排成流水线型 张华侨
工序
杜振海
2
外来毛坯件质量较差:杂料 1、采购对厂商管控不力;2
五金加工企业制程不良追踪改善表

1.模具拉伸镶件磨损,拉伸凸凹模局 1.更换拉伸镶件,模具定期保养
部间隙过大,拉伸时产品起皱,从 2.加强抽检力度,发现不良立即
而导致产品变形不良
隔离,杜绝不良流出
胡xx
7/10
1.现场物料周转,作业过程中方法不 1.宣导员工跟物料员现场物料周
2.5%
2.15% 2.10%2.12%2.01% 对
转,作业过程中注意三伤问题,
贴合后歪斜
毛xx 苏xx
7/10
支架来料13.71MM尺寸偏小,导致 加强来料管控,拦截支架13.71
1.5% 0.87%
1.0% 0.59%
0.88% 1.01%0.89% 0.49%
具里面导致在运输中有压伤的;
3.对员工做教育训练,并监督相
4.清洗过漂洗时产品没有完全在清洗 关工站将产品完全放在清洗治具
治具里面,治具一层叠一层时有压 里面;
茶xx
7/8
0.5%
伤;
4.自动化优化程序;
0.0%
5.烘干时,烘干机出炉时,产品没有 5.培训检验员检验项目及标准流
0.0% 6/28 6/29 6/30 7/1 7/2 7/3 7/4
不良原因
改善对策
责任人 完成日期
1.模具冲头,刀口磨损或崩缺,产生 1.研磨或更换冲头刀口,模具定
毛刺
期保养,备品准备充足;
2.模具中有毛刺或废料遗留在模具工 2.模具上增加风枪吹净模具工作
作表面上,未及时清理干净导致产 表面上的毛刺及废料;
胡xx 7/6
品压伤。
3.加强抽检力度,发现不良立即
隔离,杜绝不良流出。
1.5% 0.92%1.06%1.26%1.12%0.91%0.89%1.04% 1.0%
(精益生产)生产现场改善计划追踪表
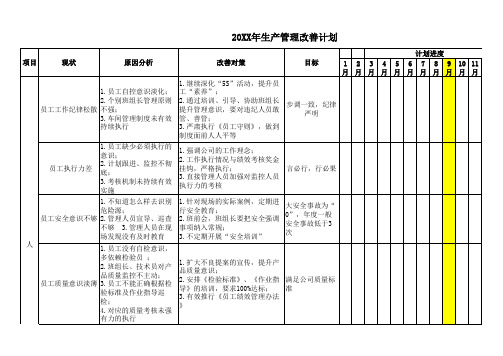
到位
3.设备巡查不能持续坚
持;
4.有关设备保养的考核
1.纳入每周常规检查;
2.加强对班组长日常工作的督查
、考核;
完好率100%;
3.5S每周检查、记录上报;
4.组织《设备操作规程》的培训
未有效执行
设备稼动率不高
1.班组长、技术员安排 不紧凑; 2.设备、模具维修频次 较高; 3.个别班组长对员工的 管理、组织能力较差
1.扩大不良提案的宣传,提升产 品质量意识; 2.安排《检验标准》、《作业指 满足公司质量标 导》的培训,要求100%达标; 准 3.有效推行《员工绩效管理办法 》
计划进度
3 4 5 6 7 8 9 10 11 月月月月月月月月月
1.员工没有认识到5S5的
5S活动成果不能很 好的保持和执行
重要性; 2.班组长不能很好的处 理生产组织与推行5S的
产品落地普遍
1.缺乏标准作业指导; 2.配备必要的辅助物 件; 3.5S推进不彻底
1.编制《作业指导书》,培训推 广实施; 2.分析实际。制作必要的产品隔 无落地件 离、流出辅助物件; 3.加强5S推进、检查力度
1.技术员对设备保养执
机
行不力;
2.班组长对设备保养组
设备/工装保养不 织、监控部到位;
1.严格按日排产执行;
2.班组长及时跟进工装维修进
度;
整体工作效率提
3.引进、学习快速换模方法,缩 高
短调试时间;
4.执行《员工绩效管理办法》
余料浪费较多
1.缺乏余料管理文件支 持,至使余料管理不 善; 2.缺乏工艺改进意识
1.编制《余料使用、管理办法 》; 2.重点加强公司针对现场的工艺 改进力度