迁钢2号高炉新技术设计与生产实践
高炉技改项目推进情况汇报
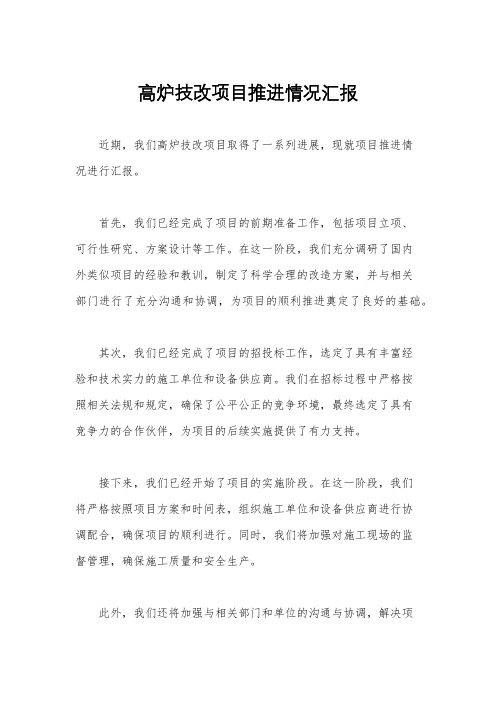
高炉技改项目推进情况汇报
近期,我们高炉技改项目取得了一系列进展,现就项目推进情
况进行汇报。
首先,我们已经完成了项目的前期准备工作,包括项目立项、
可行性研究、方案设计等工作。
在这一阶段,我们充分调研了国内
外类似项目的经验和教训,制定了科学合理的改造方案,并与相关
部门进行了充分沟通和协调,为项目的顺利推进奠定了良好的基础。
其次,我们已经完成了项目的招投标工作,选定了具有丰富经
验和技术实力的施工单位和设备供应商。
我们在招标过程中严格按
照相关法规和规定,确保了公平公正的竞争环境,最终选定了具有
竞争力的合作伙伴,为项目的后续实施提供了有力支持。
接下来,我们已经开始了项目的实施阶段。
在这一阶段,我们
将严格按照项目方案和时间表,组织施工单位和设备供应商进行协
调配合,确保项目的顺利进行。
同时,我们将加强对施工现场的监
督管理,确保施工质量和安全生产。
此外,我们还将加强与相关部门和单位的沟通与协调,解决项
目实施中的各种问题和困难,确保项目的整体推进。
同时,我们将及时总结和分享项目推进中的经验和教训,不断优化改进项目实施过程,确保项目的顺利完成。
最后,我们将加强对项目进展情况的跟踪和监督,及时发现和解决项目推进中的问题和风险,确保项目的整体进度和质量。
总之,我们将以高度的责任感和使命感,全力推进高炉技改项目,确保项目的顺利实施和取得良好的效果。
我们相信,在全体参与者的共同努力下,高炉技改项目一定会取得成功,为企业的发展和社会的进步做出应有的贡献。
迁钢2^#高炉溜槽破损检修处理实践

u me i n c r e me n t r h y t h m a n d t u y e r e a r e a a d j u s t m e n t w a s c a r i e d o u t s t r i c t l y a c c o r d i n g t o t h e a c t u a l o p e r a t i n g
4 8小 时计 划检 修 , 实 际停 风 4 7小 时 5 3分 钟 , 停 风
后 发现 布料 溜槽 磨 漏严 重 , 炉 内料 面形 状 不规 则 , 验 证 了检 修前 布料 溜 槽 磨 损 的 推测 , 及 时 对送 风 方 案
条件 外 围波 动 影 响 , 4月份 高 炉 焦 炭 负荷 从 月 初 的
文 章 编 号 :1 6 7 1 —3 8 1 8 ( 2 0 1 3 ) 0 5— 0 0 3 1 — 0 6 中图分类号 : T F 3 2 1 文献标识码 : A
M AI NTENANCE PRACTI CE oF DAM AG ED CHARGI NG CH UTE
F oR No. 2 B F I N QI A N’ AN S T E E L
第 5期
总第 2 0 7期
高炉炼铁技术创新实践及未来展望

千里之行,始于足下。
高炉炼铁技术创新实践及未来展望高炉炼铁技术是钢铁工业中非常重要的一个环节,对于钢铁产量和质量有着直接影响。
随着科技的不断发展和进步,高炉炼铁技术也在不断创新和实践。
本文将介绍高炉炼铁技术的创新实践及未来展望。
高炉炼铁技术主要包括焦炭冶炼、铁矿石还原和炉渣处理三个方面。
近年来,针对这几个环节进行了一系列的技术创新,以提高钢铁产量和质量,减少能源消耗和环境污染。
首先,在焦炭冶炼方面,高炉炼铁技术实践了煤炭气化技术,将煤炭转化为合成气或制备气,用来代替部分焦炭。
这样可以减少焦炭的消耗量,提高炉温和炉效,提高炼铁效果和节约能源。
其次,在铁矿石还原方面,高炉炼铁技术实践了混合还原技术,将不同种类的铁矿石混合使用,以提高还原效率和减少还原剂的消耗。
同时,还运用了制粒和球团矿技术,提高了炉料的密实度和还原性能,使得炼铁效果更好。
再次,在炉渣处理方面,高炉炼铁技术实践了炉渣处理技术,包括高炉渣套料、炉渣粉磨和炉渣稳定化等。
这些技术可以减少炉渣的生成和排放,降低对环境的污染,同时还能回收利用一部分有价值的元素。
未来,高炉炼铁技术仍将继续创新和发展。
一方面,可以进一步拓宽原料的来源,包括使用青海盐湖等资源,以降低对传统铁矿石的依赖程度。
另一方面,可以进一步提高炉渣的利用率,实现钢铁工业的循环经济。
此外,还可以用高效节能的加热方式替代传统的冶炼方法,以进一步降低能源消耗和环境污染。
第1页/共2页锲而不舍,金石可镂。
综上所述,高炉炼铁技术的创新实践为钢铁工业的发展提供了重要支撑。
未来,随着技术的不断进步和创新,高炉炼铁技术将更加高效、环保和可持续,为钢铁产量和质量的提高做出更大贡献。
同时,需要在技术创新的同时,加强对环境保护的重视,实现钢铁工业的可持续发展。
迁钢2#高炉长期休风快速恢复实践
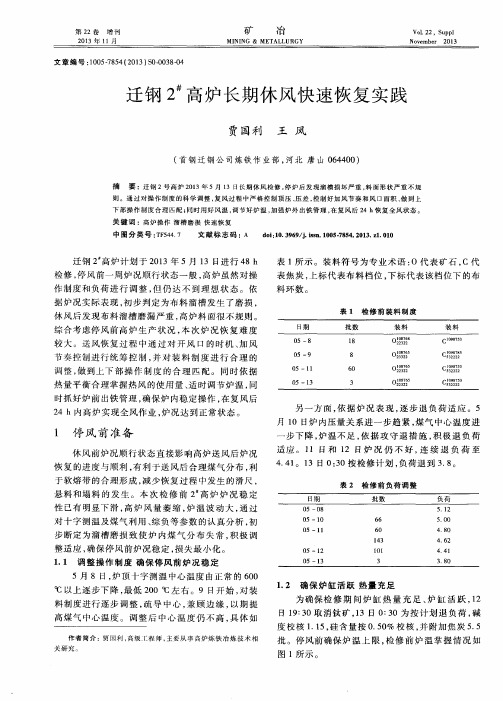
增 刊
矿
冶
Vo 1 . 2 2 ,S u p p l No v e mb e r 2 0 l 3
2 0 1 3年 1 1月
MI NI NG & MET AL 7 8 5 4 ( 2 0 1 3 ) S O 一 0 0 3 8 - 0 4
2 4 h内高 炉实 现全 风作业 , 炉况 达 到正常 状态 。
另 一方 面 , 依 据 炉 况 表现 , 逐 步退 负 荷 适 应 。5 月1 0日炉 内压 量关 系进一 步趋 紧 , 煤 气 中心温 度进 步下 降 , 炉 温不 足 , 依 据 攻守 退 措 施 , 积 极 退 负荷
下 部 操作 制度 合 理 匹 配 ; 同 时 用好 风 温 , 调节好炉温 , 加 强 炉外 出铁 管 理 , 在复风后 2 4 h 恢 复 全风 状 态 。
关 键 词 :高炉操作 溜槽磨损 快速恢复
中图分类号 : T F 5 4 4 . 7
文献 标 志码 : A
d o i : 1 0 . 3 9 6 9 / j . i s s n . 1 0 0 5 - 7 8 5 4 . 2 0 1 3 . z 1 . 0 1 0
较 大 。送 风恢 复过 程 中通 过对 开 风 口的 时机 、 加 风
节 奏控制 进行 统筹 控 制 , 并 对装 料 制 度 进行 合 理 的 调整, 做 到上下 部 操 作 制度 的合 理 匹 配 。同 时依 据
热量 平衡 合理 掌握热 风 的使用 量 、 适 时调 节炉温 , 同
时 抓好炉 前 出铁管 理 , 确保 炉 内稳定操 作 , 在复 风后
1 停 风 前 准 备
休风 前炉 况顺行 状态 直接 影 响高炉送 风后 炉况 恢 复 的进 度 与顺利 , 有利 于送 风后合 理煤 气分 布 , 利
梅钢2号高炉优化上部制度实践
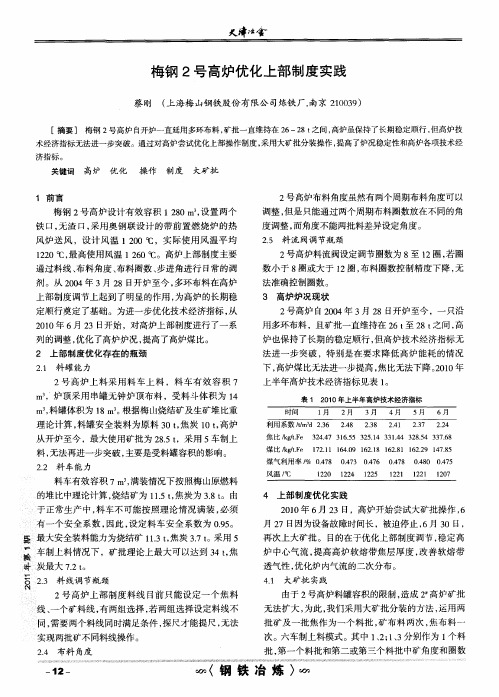
4 上部制度优化实践
21 6 2 00年 月 3日,高炉开始尝试大矿批操 作 , 6
月2 7日因为设备故 障时间长 ,被迫停止 , 3 6月 0日,
2 上部制度优化存在的瓶颈
21 料罐 能力 .
法进一 步突破 ,特 别是在 要求 降低高 炉能耗 的情况 下, 高炉煤 比无法进一步提高 , 比无 法下 降。00年 焦 21 上半年高炉技术经济指标见表 1 。
表 1 21 0 0年上半年高炉技术经济指标 时间 1月 2月 3 月 4月 5月 6月
1 — 2
(钢 铁 冶 炼 )
梅钢 2 号高炉优化上部制度实践
进行 区别设置 。确保炉顶料 面搭 建合理 的平 台。其 中 最大能力为第一 周期矿料重 2 , 二周期矿料重 1 3t第 3 t两车 中一车为烧 结矿及 生矿 , 外一车为 生矿及 杂 ( 另
料, 无法再进一步突破 , 主要是受料罐容积 的影响 。
22 料 车能力 .
利用系数 / 3 2 6 2 8 2 8 2 1 2 7 2 4 t d . . . . . . / 3 m 4 3 4 3 2
焦 比 / .e 344 3 6 5 2 . 3 1 4 2 .4 3 .8 k F 2. 7 1 . 3 51 3 . 3 85 3 76 5 4 4 煤 比 / .e 1 21 140 121 128 122 178 l F 7 .1 6 . 【 9 6 .8 6 .1 6 .9 4 .5
再 次上大矿批 。 目的在 于优化 上部制度调节 , 稳定 高
迁钢公司3号高炉降低焦比实践

河北省首钢迁安钢铁有 限责 任公 司 ( 简称 迁钢公司)3号高炉于 2 0 1 0年 1月 8 日开炉 ,
1 技术指标恶化原 因分析
2 0 1 1 年 1 — 6月迁钢公司 3号高炉焦 比稳定
该高炉有效容积为 4 0 0 0 m 。入炉料结构为高碱 度烧结矿 、球团和生矿 ,焦炭为 7 0 % 的一级干
熄焦 炭 和 3 O % 的二级 干 熄 焦 炭 。迁 钢公 司 3号
高炉开炉后 ,随着入炉原燃料质量的不断改善和
操作制度的优化 ,高炉焦炭消耗迅速下降 ,同年 1 O月焦比达到约 2 8 3 k g / t 。进入 2 0 1 1年 ,随着 操作炉型的变化和原燃料质量 的波动 ,炉内压差 升高 ,煤气分布出现不稳定征兆 ,高炉焦炭消耗 不断提高 ( 焦比升至 3 2 0 k g / t ) ,铁水 日产量不 断下降。为此 ,对迁钢公 司 3号高炉操作 制度 进行了重新摸索 ,并加强 了精料工作 ,高炉焦炭 消耗升高的趋 势得 到抑制 ,焦 比水平下降约 2 0
严重恶化 了炉缸的透液性 ,焦炭质量不能支撑较 重的负荷 。炉况恶化表现为十字测温的中心温度
逐步下降 ,从 6 0 0 o C 以上下降到 3 0 0 o C 以下 , 煤气分布发生较大变化 ,增加了高炉操作难度 。
Q i a n a n i s a d j u s t e d nd a he t w o r s e n t r e n d o f e c o n o mi c t e c h n i c a l i n d e x e s i s r e s t r a i n e d e f e c i t v e l y b y
me ns a o f b e n e i f c i a t e d b u r d e n a d mi n i s t r a i t o n,o p i t mi z a t i o n f o b u r d e n d i s t i r b u i t o n a n d b l o w i n g s y s t e m. I n a r e l a i t v e l y l o n g - t e r m p e r i o d ,t he B F o p e r a i t o n c o n d i i t o n i s ma i n t a i n e d v e r y w e l 1 . A t he t s a me t i me ,t he o p e r a t i o n r u l e a f t e r t h e c h a n g e o f BF p of r i l e i s e x p l o r e d, l e a d i n g t o he t c o k e r a i t o l e v e l s t o 3 0 0 k g / t . Ke yW o r d s l a r g e B F,c o n s u mp i t o n r e d u c i n g,c o k e r a i t o
高炉炼铁生产管理创新与技术进步

高炉炼铁生产管理创新与技术进步随着现代工业的发展,高炉炼铁作为铁矿石的重要生产方式,承担着重要的任务。
在高炉炼铁生产中,如何创新管理模式,推进技术进步,提高生产效率和产品质量,已成为行业发展的关键问题。
本文将从管理创新和技术进步两方面来探讨高炉炼铁生产的发展趋势。
一、高炉炼铁生产管理创新1.工艺流程优化在高炉炼铁生产中,工艺流程的优化是提高生产效率的重要途径。
通过对生产过程进行分析,不断优化工艺流程,可以提高炉内矿石的还原性能,增加炉渣的碱度,减少燃料消耗和炉缸内压力等,从而提高炉况的稳定性和生产效率。
2.智能化管理随着信息技术的发展,高炉炼铁生产管理也逐渐向智能化方向发展。
采用先进的传感技术和数据分析算法,可以对高炉炼铁生产过程进行在线监测和控制,实现生产过程的自动化和智能化管理,提高生产效率和产品质量。
3.能源节约与环保在高炉炼铁生产中,能源消耗和环境污染一直是困扰行业发展的问题。
通过引进节能环保技术,如余热回收利用、尾气净化技术等,可以有效减少能源消耗和排放污染物,提高生产的可持续发展能力。
4.人力资源管理高炉炼铁生产需要大量的技术工人和管理人员,如何合理配置人力资源,提高员工的技术水平和管理能力,对于保障生产的稳定进行是至关重要的。
建立健全的人力资源管理制度和培训体系,可以提高员工的工作积极性和生产效率。
二、高炉炼铁生产技术进步1.新型高炉技术随着现代冶金技术的发展,一些新型高炉技术逐渐应用于高炉炼铁生产中,如底吹炼铁技术、蓄热式高炉技术等。
这些新型高炉技术能够提高炉内的矿石还原效率,减少冶金副产物的生成,降低燃料的消耗,从而提高生产效率和产品质量。
2.炉料质量控制高炉炼铁生产过程中,炉料的质量直接影响炉内还原和熔融过程,因此炉料的质量控制是提高生产效率的关键。
采用先进的炉料配料技术和原料分析技术,可以确保炉料的合理配比和质量稳定,提高炼铁生产的稳定性和生产效率。
3.炉渣处理技术炼铁生产中生成的炉渣不仅影响了炉内的正常操作,还对环境造成了污染。
攀钢2号高炉优化操作实践

攀钢2号高炉优化操作实践胡方友(攀枝花新钢钒股份有限公司)摘要攀钢2号高炉通过采取调整风口、改善入炉原料质量、优化高炉操作、处理炉前隐患等措施,使各项技术经济指标逐渐得到优化。
关键词高炉强化冶炼顺行攀钢2号高炉有效容积l 200 m3,设有18个风口,1个铁口,2个渣口,3座顶燃式热风炉,采用双钟式炉顶,马基式旋转布料器,2007年底大修后开始第四代炉役的生产。
本文着重分析了2号高炉在2008年期间炉况逐渐变差的原因,并重点总结了在2009年期间针对炉况差而采取的优化措施。
1 炉况差的原因2号高炉投产后,高炉不易接受风量,炉缸活跃度降低,炉内顺行变差,出现了长期、崩滑料的现象,加减风频繁,致使高炉冶炼强度逐渐降低、利用系数降低、焦比升高、铁损增加(见表1)。
究其原因,初步分析有如下几点。
1.1 开炉初期炉型变化不规则。
大修开炉初期,有1座热风炉检修未完工,长期是2 座热风炉送风。
2号高炉采用低风温、低负荷操作,疏松边缘的COCO+OO↓OCCC↓装料制度,风口设置为直径130mm的2个、140mm的16个。
2号高炉2008年上半年东南和东北炉喉煤气CO2分布如图l所示。
可见2号高炉顺行虽好,但是边缘气流并不稳定。
在3座热风炉送风后,逐渐把风温用到1 200℃。
负荷加重以后,多次采取加重边缘的装料制度如OCOC+COCO+OO↓OCCC↓2 OOOO+COCO+2OO↓OCCC↓等,批重从20.8t减到20.3 t,料线2.8 m降到3.0 m。
炉缸1、2、3段水温差和炉身下2层温度都很低,使曲线带变窄成一条直线。
时间从22 h逐渐缩短到19 h,焦炭反应性从33%左右增到38%左右,反应后强度从55%左右降到52%左右,M40从78%降低到76%;喷吹煤粉质量也差,较平时12%左右高,入炉粉末最高达13.12%。
1.3设备的影响高炉砂坝和下渣沟整体上抬,砂坝太高而使砂坝和下渣沟常常糊死,同时后渣带铁多,经常坏渣口,最多的一个月坏了13个,最少的一个月也坏了4个,导致高炉经常因渣铁出不净而带来其他事故和频繁大减风。
宝钢股份不锈钢分公司

目录1、首钢2号高炉铁口维护及出铁管理实践――――――――――――――首钢炼铁厂马洪斌武胜利2、论提高高炉风温的根本途径――――――――――武汉宏图发展炼铁技术有限公司段润心段中坚3、红外热成像技术在高炉长寿中的应用―――――――宝钢股份不锈钢分公司张振伟杨细中康晖4、全烧高炉煤气实现1250℃送风温度的两种工艺系统―――――――――――安徽工业大学许永贵5、高炉喷吹废塑料堵枪模拟研究―――――――――――――――――安徽工业在学冶金与资源学院龙世刚冯新华庞建明王思维孙刘恒6、华钢1号高炉强化冶炼生产实践――――――――――――――华西钢铁有限公司炼铁厂胡兵兵7、高强耐热链箅板的研制与应用――――――――――――――山东泰山钢铁集团有限公司陈培敦泰钢集团新材料研究所王振国陈茂敬8、高炉用铸铁机发展趋势与应用――――――――――――――――世林(漯河)冶金设备有限公司冯力刘升强冯国兴李鹏飞王怀柱贾晓涛苏州大学机械工程学院熊滨生9、武钢4#高炉微水节能热风阀的研制与应用――――――――――世林(漯河)冶金设备有限公司冯力王银河张进郑州大学机械工程学院熊宾生张二岗武汉钢铁公司炼铁厂卓玉武李东10、基于金相测定法的高炉铸铁冷却壁水管防渗碳效果检测与研究――――――――――世林(漯河)冶金设备有限公司徐汝兰陈君圣赵小平冯力郑州大学机械工程学院熊滨生刘自军12、八钢炼铁技术进步的回顾与展望――――――――――――宝钢集团八钢公司炼铁分公司袁万能宝钢集团八钢公司技术开发中心李涛刘新娣13、我国高炉炼铁应成为世界先进水平―――林州市马氏炼铁技术研究开发公司马铁林郭俊奎马杰14、高炉鼓风湿分及其测量与控制技术―――――――――――――――首钢炼铁厂王自亭刘利峰钢铁研究总院炼铁室沙永志曹永志王凤岐15、COREX熔融还原炼铁工艺使用烧结矿的可行性研究――――――首钢迁钢公司炼人分厂贾国利16、达钢超高碱度烧结生产实践―――――――四川省达州钢铁集团公司烧结厂李翔时肖鹏伍雁梅17、技术进步推动达钢烧结生产再突破――――四川省达州钢铁集团公司烧结厂伍雁梅李翔时肖鹏19、大型高炉内燃式热风炉耐火材料破损调查―――――――――――武钢研究院徐国涛邓棠刘黎武钢炼铁厂张洪雷20、武钢炼铁系统“十五”以来节能降耗、减排治污技术进步―――――――――武钢股份有限公司生产技术部杨志泉21、南钢炼铁厂烧结系统近年来的工艺技术进步―――――――――南钢股份有限公司炼铁厂孙志鹏22、宝钢炼铁系统节能技术进步――――――――――――宝钢股份宝钢分公司炼铁厂刘绍良李勇23、大型高炉高余压发电技术的实践――――――――――――宝钢股份公司宝钢分公司炼铁厂李军24、马钢300m²烧结机带冷烟气余热发电工程简介――――――――――――马钢股份有限公司第二炼铁总厂汪保平吴朝刚顾云松25、邯钢4号高炉中心煤气流不稳定原因分析及改进措施――――邯钢公司技术中心侯金珠刘志朝26、试论我国球团矿的发展―――――――――――――――――――――――北京科技大学孔令坛27、高炉热风炉蓄热体――格子砖高辐射率覆层技术及应用―――――――――――山东慧敏科技开发有限公司周慧敏28、高磷铁矿石脱磷技术研究现状与展望―――――――――――――中南大学资源加工与生物工程学院彭志伟李光辉金勇士姜涛杨永斌29、八钢炼铁厂节能降成本实践――――――――新疆八一钢铁有限公司炼铁分公司周文胜田宝山30、全面贯彻“十字”方针,建立“高效”完整理念,提高节能减排的绩效――――――――中冶赛迪工程技术股份有限公司项仲庸31、大型高炉煤气能量回收透平膨胀机的研发――陕西鼓风机集团公司郑秀萍孙标杨歧平周成武32、提高高炉冶炼强度的顶压能量回收系统――陕西鼓风机集团公司印建安章本照柳黎光沈新荣33、PWM技术在高炉探尺装置的应用――――――――――马钢股份有限公司第二炼铁总厂陈海明34、武钢高炉长寿技术实践――――――――――――――――――――武钢研究院宋木森于仲洁武钢炼铁厂熊亚非李怀远35、南钢改进型顶燃式热风炉掺混转炉煤气的应用―――――――――――南昌长力钢铁股份公司炼铁厂胡小清王伟祥万淑霞甘超华36、配加蛇纹石烧结试验及生产分析―――――――――――――――马钢股份公司质监中心孙泰珍37、河南济钢2×75m2烧结机设计特点及生产实践―――――――――――河南济源钢铁集团有限公司炼铁厂伍荣燕李环东38、河南济钢200万t原料场设计特点及生产实践―――――――――――河南济源钢铁集团有限公司炼铁厂伍荣燕李环东39、国外炼铁状况及我国炼铁发展方向―――――――――――――――钢铁研究总院炼铁室沙永志40、南钢1050m3高炉热风炉高风温长寿技术的应用―――南昌长力钢铁股份有限公司徐冬华舒红英41、宣钢炼铁厂1#高炉自动控制系统改造―――――――――――――宣钢集团有限公司炼铁厂陈艳张如伟贾世清高俊峰42、宣钢炼铁厂西铁区高炉炉冷却水系统改造与生产实践―――――――――――――宣钢集团有限公司炼铁厂黄晓东李荣玲王云江河北工业职业技术学院宣钢分院黄炜43、提高烧结矿强度、优化粒及组成实践――――――――――――宣钢集团有限公司炼铁厂王翠琴45、武钢高炉K、Na、Zn平衡计算―――――――――――――――――武钢研究院邹祖桥宋木森武钢炼铁厂赵思唐复显46、含铁废料在杭钢烧结中的应用―――――――――――杭钢集团公司炼铁厂罗文陈一忠张红雨47、长袋低压脉冲袋式除尘技术在杭钢烧结的应用――――杭钢集团公司炼铁厂张红雨徐晓燕罗文48、莱钢2#1000m3高炉高效生产实践――――――莱钢股份公司炼铁厂马振军李国潘林刘卫国49、莱钢型钢烧结厂质量管理的基本思路―――――――――莱钢股份公司烧结厂陈鑫李强陈书峰50、莱钢型钢烧结厂自动控系制统研究与研究――――――――――――莱钢股份公司烧结厂卢秀红52、烧结厂提高管带机可靠性及输送能力的研究与应用――――――――――――莱钢股份公司烧结厂江龙宏刘利谷华李强吕袅毕欣成张发忠53、试谈各大中型企业生产中的产、质矛盾―――――――――――――莱钢股份公司烧结厂徐春玲56、风机常见故障诊断技术――――――――――――――莱钢股份公司烧结厂乔汉东谭松涛熊伟57、试谈配料方案与质量预测的优化――――――――――――莱钢股份公司烧结厂时逢雷徐春玲60、降低3×105m2烧结机工序能耗的实践――――莱钢股份公司烧结厂成昌省吴志军李克峰曹斌61、莱钢265m2烧结机故障停机的要因分析与改进措施――――――――莱钢集团公司银山型钢烧结厂王新章62、烧结机点火温度自动化控制――――――莱钢股份公司烧结厂王珂赵相轩张惠李连海王继永63、莱钢烧结厂265m2烧结机配加蛇纹石工业试验的研究与实践―――――莱钢股份公司烧结厂杨军64、烧结机冷返矿波动对生产的影响及对策―――莱钢股份公司烧结厂王子秀王延义姜兴军袁波66、无线工控在堆取料机上的应用―――――――――――――――――莱钢股份公司烧结厂王如旭67、型钢265m2烧结机高配比褐铁矿烧结技术的应用――――――――――莱钢股份公司烧结厂陈书峰崔永诗翟所莲68、悬臂筛网振动筛的小焦筛分工艺线上的应用―――――――――――莱钢股份公司烧结厂乐建华69、一种新型烧结机头尾密技术的研究与实践――――――莱钢股份公司烧结厂赵红光杨军侯纪宝70、莱钢265m2烧结机降低烧结矿固体燃耗的研究与实践―――――――――――莱钢股份公司烧结厂李连海张惠王继永夏建刚王炜71、莱钢2×265m2烧结机润滑系统改造――――――――――――――莱钢股份公司烧结厂卢秀红72、2685型椭圆振动筛常见故障分析及处理――――――莱钢股份公司烧结厂周忠源刘传振孝保忠73、3×105m2烧结机一次混合机的技术改造――――――――――――莱钢股份公司烧结厂乐建华77、莱钢3×105m2烧结机两期配料室供料的生产实践――――――――――莱钢股份公司烧结厂王延义李兴义王子秀姜兴军78、非高炉炼铁技术及在我国发展的展望―――――――――――――――东北大学钢铁冶金研究所赵庆杰储满生王治卿董文献79、济钢1750m3高炉炼铁技术进步――――――――――――济钢集团总公司技术中心王良周贾勇80、扩散燃烧式硅砖热风炉烘烤器――――中钢集团鞍山热能研究院设备研制厂徐正徐立伟吕英华81、华钢450m31#高炉钛球护炉实践――――――――――江苏省华西钢铁有限公司炼铁分厂华昇82、1#高炉降硅生产实践――――――――――――――――――江苏省华西钢铁有限公司殷秀标85、蒸发空冷器的管控实践――――――――――――――――――――莱钢股份公司炼铁厂张亚宇86、烧结机篦条糊堵现象的研究与应用――――――莱钢股份公司烧结厂杨军李强亓玉辉胡守忠87、干煤粉气化与粉矿流化床直接还原的联合工艺―――宝钢股份有限公司宝钢研究院钱晖周渝生88、现有主要炼铁工艺的优缺点和研究方向――――――――――――――宝钢股份有限公司宝钢研究院周渝生钱晖张友平李肇毅范建峰89、一铁总厂原燃料变化的应对措施―――――――――――――马钢公司第一炼铁总厂黄龙李嘉90、高炉脱湿鼓风技术应用中的几个技术问题―――――――陕西鼓风机集团有限公司孙鸿声刘侃91、高炉炭砖的损毁及其研究进展―――――――武汉科技大学耐火材料与高温陶瓷湖北重点实验室陈希来李亚伟李远兵金胜利葛山赵雷李淑静92、长钢高炉提高煤比研究及生产实践―――――――――长治钢铁集团公司炼铁厂张联斌许满胜93、炉前技术发展与大功率、高效能、环保型开口机研发应用―――――――――三峡工业设计研究院张秀萍胡华平于君成迁安钢铁公司炼铁分厂张春义宝钢炼铁厂敖爱国94、炼铁发展循环经济的探讨―――――――――――――――――――冶金工业规划研究院刘文权95、迁安2号高炉工艺优化与技术创新―――――北京首钢设计院毛庆武张福明姚轼钱世崇倪苹96、重钢5号高炉风温操作实践―――――――――重钢股份有限公司炼铁厂雷有高尹卫国刘向辉97、烧结矿粘结相自身强度的研究――东北大学材料与冶金学院李光森金明芳姜鑫储满生沈峰满98、八钢富蕴蒙库球团厂2007年节能减排工作成效显著――――――――――新疆八一钢铁集团富蒙库铁矿有限责任公司孙万里陈保峰100、宣钢中型炉电子秤现状及常见故障分析―――――――――――――宣钢炼铁厂张晓霞杨永斌101、烧结混合料制粒胶体核心的研究与应用――――――――――莱钢集团银山型钢烧结厂张子元102、应用系统方法,降低炼铁能耗――――――宣钢集团公司炼铁厂张慧霞冯艳国褚利娟岑亚虎104、高炉水淬渣的二氧化硫吸收性能研究――――――――――宁波太极环保设备有限公司刘常胜105、马钢-铁烧结系统降低固体燃耗的技术措施―――――――――――马钢第一炼铁总厂张永中106、HismeIt法冶炼高磷矿可能性分析――――――――――――――武汉科技大学钢铁冶金及资源利用省部共建教育部生点实验室毕学工周进东黄志成金焱熊玮107、宣钢8#高炉冷却系统运行状况研究分析与生产实践――――――宣钢集团公司炼铁厂田德林108、宣钢8#高炉供料系统运行状况分析―――――――――――――宣钢集团公司炼铁厂田德林胡智龙李永红於建忠马步城苏爱民109、铜/钢复合抗变形冷却壁在宣钢1#高炉的开发应用―――宣钢炼铁厂谢相久成巨海张德新河北省万全县丰华有色金属加工厂牛建平闫丽峰110、宣钢9#高炉低硅冶炼生产实践―――――――――――――――宣钢集团公司炼铁厂田德林111、宣钢1#高炉长寿技术措施―――――――――唐钢集团宣钢炼铁厂王斌王素涛陈喜勇赵成112、宣钢9#高炉低成本战略操作实践――――――――――――――宣钢集团公司炼铁厂郭金海113、宣钢炼铁厂西铁区节水综合改造的设计和实施―――――――――――唐钢集团宣钢炼铁厂张如艳岑亚虎王斌安钢115、采用炉顶煤气循环和风口喷吹技术降低COREX/FINEX燃料消耗的理论分析―――――上海大学材料学与工程学院姚晓光郑少波宝钢股份研究院徐万仁116、烧结烟气净化技术进步,节能减排效果显著――――――北京科大联创冶金技术有限公司张滔包钢集团公司炼铁厂高英117、高炉炼铁过程的数学模拟―――――――――――――东北大学钢铁冶金研究所储满生沈峰满安阳钢铁集团公司技术中心胡涛李子林118、铁矿热压含碳球团及其冷态强度的影响因素――――――――――――东北大学钢铁冶金研究所储满生吕继平付磊柳正根艾名星赵庆杰119、邢钢1#高炉末期生产实践―――――――――――――――邢钢炼铁厂李炳岳史建超杨山林120、宣钢1800m3高炉自动控制系统设计与优化――――――――――――宣钢集团公司炼铁厂郝广春闫建英李建龙贾伟山121、宣钢1800m3高炉自动化控制系统的故障诊断――――宣钢集团公司炼铁厂李锦龙刘岩贾伟山122、烧结原料成分对烧结强度的影响―――――――――东北大学材料与冶金学院金明芳李光森尚策姜鑫沈峰满123、4#高炉炉况失常处理总结―――――124、浅析炼铁厂冲渣水泵的节能改造―――――――――――――――武钢集团鄂钢炼铁厂陈昌武125、炉料结构中合理应用含MgO原料的研究―――――――――――――东北大学材料与冶金学院姜鑫张枥穆林沈峰满鞍钢集团炼铁总厂窦力威126、重钢750m3高炉提高喷煤比的研究――――――――重庆钢铁股份公司刘孝华赵仕清张海丰127、铁矿热压含碳球团高温抗压强度的实验研究――――――――――――东北大学钢铁冶金研究所付磊吕继平柳政根王兆才张伟储满生128、对于我国高炉铜冷却壁冷却技术的改进意见―――――――汕头华兴冶金备件厂有限公司陈钢129、天钢3200m3高炉炉前技术进步―――――――――――――――――天钢有限公司炼铁厂林杨130、高风温热风炉技术――――――――――――――――――――――天钢有限公司董文明李博131、天钢烧结机头烟尘治理实践――――――――天钢有限公司炼铁厂朱鸿林胡晓拱耀瑜朱延国132、天钢360m2烧结机低温厚料生产实践――――――天钢有限公司炼铁厂杨选民崔金丽孙海宁133、天钢2000m3高炉炉体维护的探索―――――――――――――――天钢有限公司炼铁厂杨正祥134、应对自产球团短缺对策的研究与实践―――――――――太钢集团公司技术中心蔡湄夏温继东135、太钢4350m3高炉高煤比攻关实践――――――――――――太钢集团公司炼铁厂王红斌张华136、太钢链蓖机――回转窑球团生产线适宜膨润土种类的选择研究―――――――――太钢集团公司范建军张晋生刘炯刘慈光赵国栋衡旭文137、太钢450m2烧结机配矿试验研究―――――――――――太钢集团公司技术中心贺淑珍蔡湄夏139、川威集团5#高炉焖炉及开炉技术的进步――――――――――川威集团公司炼铁厂向健陈仁宏付相兵陈军刘忠建140、达钢450m3高炉全贫煤、贫瘦煤喷吹生产实践―――――――――达钢集团公司严礼祥杨祖伟141、达钢3#高炉大凉事故的分析与处理――――――――――达钢集团公司钢研所严礼祥杨祖伟142、一种用于人造富矿的高镁熔剂――――――――――――――武钢股份有限公司烧结厂翁得明143、铁矿煤球团自产还原气生产直接还原铁工艺及估算―――――――山西省焦炭集团公司苏亚杰太钢集团公司煤气厂杜英虎中国日用化学研究院陈寿林144、高炉热风炉应用高发射率覆层的节能诊断及节能效果―――――――――北京科技大学冶金与生态工程学院王苗苍大强白皓宗燕兵山东慧敏科技开发有限公司周惠敏刘新华山东石横特钢集团有限公司张海涛145、马钢新区炼铁厂自动化系统设计与实施―――――――马钢股份公司第三炼铁总厂钱亚平卢鸣146、国产TRT马钢4000m3高炉上的应用――――――――马钢股份有限公司第三炼铁厂洪伟黄方147、马钢三铁总厂厚料层烧结生产实践―――――――――――马钢股份公司第三炼铁总厂洪永年148、马钢新区A#高炉开炉及达产实践――――――――马钢股份公司第三炼铁总厂王幼平吴宏亮149、马钢新区含铁尘泥的循环利用―――――――――――――马钢股份公司第三炼铁总厂田文杰150、提高和稳定链篦机――回转窑成品球团矿抗压强度的途径―――――――――马钢股份公司第三炼铁总厂技术中心黄世来杨胜义夏征宇151、深入开展工艺化工作,提高技术指标水平―――――――――――宣钢公司炼铁厂李俊娥李展152、重钢炼铁厂3#高炉风口出水管优化改进―――――――――――――――重钢炼铁厂梁绍新153、750m3高炉生产节能降耗探讨―――――――――――――――――――――重钢炼铁厂毕绍虎154、高品位铁精矿的应用现状及制备技术―――――――――――东北大学李艳军韩跃新赵庆杰155、高炉无料钟布料参数对落点分布的影响―――北京科技大学冶金与生态工程学院高绪东程树森156、无钟高炉布料测试新技术及料面三维图像重建―――――――――――――北京科技大学冶金与生态工程学院杜鹏宇程树森157、冷却壁非稳态位移研究――――――北京科技大学冶金与生态工程学院解宁强宁晓钧程树森158、冷却壁非稳态温度场研究―――――北京科技大学冶金与生态工程学院解宁强宁晓钧程树森159、冷却壁非稳态应力场研究―――――北京科技大学冶金与生态工程学院解宁强宁晓钧程树森160、冷却水温度变化对高炉埋纯铜管铸铜冷却壁温度场的影响――――――――――北京科技大学冶金与生态工程学院解宁强程树森绍兴曙光机械有限公司阮新伟161、高炉配料自动控制方法研究――――――上海宝信软伯股份公司自动化部陶钧朱学其林文喜162、降低武钢三烧工序能耗的生产实践――――――――――――――――武钢公司烧结厂范维国163、炼焦煤细分技术在武钢的应用―――――――――――――武钢焦化公司陈翔盛军波梁治学164、浅谈烧结厂实行清洁生产的经验――――――――――――――武钢股份公司烧结厂陈云吴英165、湿式除尘器在武钢四烧――混进口的应用实践――武钢股份公司烧结厂林继新蒋国波陈宝军166、应用排队论提高港口物流能力的方法研究―――――――――――――――武钢工业港张远利167、宣钢炼铁厂创新管理实践―――――――――――――――宣钢集团公司炼铁厂崔成军刘素平168、宣钢炼铁厂7号高炉热风炉的损坏原因及对策―――――――宣钢集团公司炼铁厂周政德程贵169、宣钢7#高炉操作实践―――――――――――――宣钢集团公司炼铁厂程贵李俊娥周政德170、宣钢7#高炉提高风温措施―――――――――宣钢集团公司炼铁厂施宏匡禕李俊娥赵英云172、宣钢7号高炉冷却壁水管烧漏原因分析与对策――――――――――――宣钢集团公司炼铁厂匡禕程贵李俊娥侯志勇赵英云174、鼓风动能对高炉冶炼的影响及控制――宣钢集团公司炼铁厂杨金来侯志勇李展匡禕赵英云175、低频微波水分分析仪(LFM)在烧结厂中应用的评价―――――――――――――必和必拓公司176、提高堆积混匀效果的实验研究及应用―――――――济钢集团总公司王杰李俊杨传举李建沛177、2007年二号高炉年修装料及开炉――――――――武钢股份有限公司炼铁厂陆隆文赵思尹腾178、ABB DCS在宣钢中型炉炼铁生产中的应用――――――――宣钢炼铁厂张晓霞常欣张洪芹179、AC800F控制系统对炉顶设备的监控――――――――――――宣钢炼铁厂张晓霞张洪芹常欣181、熔融还原炼铁的发展思路―――――――――――――――首钢技术研究院钢铁研究所刘文运182、长寿高效高炉缸炉底设计存在问题评析―――北京科技大学冶金与生态工程学院赵宏博程树森183、“扬冷避热梯度布砖法”长寿保温型炉缸炉底设计理念―――――――――北京科技大学冶金与生态工程学院赵宏博程树森184、炉缸炉底侵蚀、结厚及活跃状态在线监测系统的开发―――――――――――北京科技大学冶金与生态工程学院赵宏博程树森185、提高360m2烧结机料层厚度生产实践―――――――――本钢板材股份有限公司炼铁厂孙秀丽186、干熄焦炭在迁钢2650m3高炉应用及效益分析―――首钢迁钢公司马金芳万雷王卫平吕金华187、迁钢高炉特殊炉况的降料面操作――――――――――――――――――首钢迁钢公司贾军民188、热风烧结技术在本钢360m2烧结机上的应用――――――――――本钢集团公司戴树平李万新189、焦炉煤气综合利用技术现状―――――――――――――――――――――首钢环保产业事业部技术中心廖洪强张振国包向军余广炜赵鹏190、炼焦配煤技术研究进展――首钢环保产业事业部技术中心张振国包向军廖洪强余广炜赵鹏191、配型煤炼焦技术研究进展――――――――――――首钢环保产业事业部技术中心张振国包向军廖洪强余广炜赵鹏192、钢铁企业节能减排新技术――清洁发展机制项目(CDM)―――――――――首钢环保事业部宣晓梅余广炜廖洪强193、基氏流动度分析在炼焦配煤中的应用――――――――首钢环保事业部付建华张振国薛立民194、石油、石化、冶金、桥梁、电力行业防腐涂料施工推荐主案――――――――――扬州美涂士金陵特种涂料有限公司卞大荣卞直兵冯有富195、ET-98无机磷酸盐富锌(铝)涂料性能与应用――――――――――――扬州美涂士金陵特种涂料有限公司卞大荣卞直兵冯有富196 西格里炭砖的特点及其应用效果――――――――――――德国西格里(SGL)炭素集团程坤明197、高炉冶炼专家系统推理知识库的建立――――――首钢自动化信息限公司自动化研究所刘莎莎198、首秦烧结过程点火优化控制模型―――――――――――首钢集团自信公司自动化研究所周卫199、加拿大低AI2O3矿粉实验研究―――――――――――――首钢技术研究院赵志星安钢徐萌北京科技大学冶金与生态工程学院安钢张曦东200、迁钢2号高炉低燃料比的操作技术―――――――――――――首钢迁钢公司炼铁厂许佳万雷201、迁钢2号高炉新技术设计与生产实践―――首钢迁钢公司炼铁分厂马金芳王卫平万雷郑敬先北京首钢设计院黄晋202、迁钢2号高炉在低焦比条件下对焦炭质量的要求――――――――――首钢迁钢公司龚鑫万雷203、首钢迁钢公司2号高炉高风温富氧冶炼实践―――――――――――――首钢迁钢公司赵铁良204、关于解决二系列链篦机生球爆裂问题探索―――――――――――――――首钢球团厂沈国良205、降低球团皂土消耗的试验研究―――――――――――――――――首钢矿业公司技术处王耀207、优化烧结生产组织的探讨―――――――――――――――――首钢矿业烧结厂高新洲扈恩征209、大型高炉在高喷煤比条件下对焦炭的质量要求―――――――――首钢迁钢公司贾国利龚卫民210、高炉综合护炉技术开发应用―――――――――――――――宝钢梅山钢铁公司炼铁厂陶中明211、采用小球烧结法,促进烧结节能减排―――――――――――――钢铁研究总院单继国石红梅212、迁钢炼铁降焦实践――――――――――――――――――――――――首钢迁钢公司贾军民213、高风温热风炉设计理念的调整及相关问题讨论―――――――――――中冶京诚工程技术有限公司吴启常沈明陈秀娟214、置换氮气,实现混合喷吹―――――――――――――吉林钢铁有限公司技术处曹金友周光才215、通钢集团吉林钢铁竖炉球团配用复合膨润土工业性试验――――――――――通钢集团吉林钢铁公司烧结厂金永吉吴从方刘晓东216、提高烧结机利用系数的措施――――――――――通钢集团吉林钢铁公司烧结厂褚立民程自宇217、改善竖炉球团矿质量的研究――――――――――通钢集团吉林钢铁公司烧结厂吴从方刘晓东218、球团焙烧炉大修新型耐火材料应用实践―――鞍钢股份有限公司炼铁总厂王志李恒旭徐福玉219、鞍钢7号高炉锌危害分析与控制――――――――――――――鞍钢股份有限公司炼铁总厂王宝海张洪宇肇德胜刘振宇赵鹏220、鞍钢西区烧结机改造与开工实践―――――鞍钢股份有限公司炼铁总厂宫作岩马贤国张明洲221、鞍钢铜冷却壁高炉热负荷管理――――――鞍钢股份有限公司炼铁总厂王宝海张洪宇车玉满222、MgO含量对鞍钢炼铁总厂烧结矿烧结指标及冶金性能的影响――――――――――鞍钢股份有限公司炼铁总厂于素荣刘艳辉刘跃民鞍钢集团科技发展部韩晓东223、炼铁总厂360m2烧结机节能降耗生产实践―――――――――――――鞍钢股份有限公司炼铁总厂刘艳辉段立群于淑荣鞍钢集团科技发展部韩晓东224、全干法除尘工艺在鞍钢新4号高炉的应用―――――鞍钢股份有限公司炼铁总厂范传昌李东生鞍钢集团科技部朱建伟鞍钢能源动力总厂钟山225、铁矿球团适宜MgO/SiO2比值的试验研究―――――――――鞍钢股份有限公司炼铁总厂黄永君鞍钢股份有限公司技术中心周明顺翟立委李艳茹226、通过改变布料方法来实现高炉的稳定与长寿―――――鞍钢股份有限公司炼铁总厂尚策张延辉227、风机旋转失速的故障诊断与处理―――――――――――――――――鞍钢设备保障部路俏俏鞍钢计量厂胡军。
迁钢公司2号高炉炉缸热流及侵蚀变化在线监测技术

t p rt ea d teeoi r l fN . F hat o i n I n a d Se lC . t.ae e ea r n h rs n po e o o 2 B er fQ a a r n t o,Ld r m u o i f h n o e
大型高炉在操 作过程 中要 注意活跃炉缸 中心和减弱铁水环 流。 关键词 高炉 “ 传热法 ”炉缸 冷却水温差 侵蚀 监测
The Te h l g f O n- ne M o t rn ft e He rh c no o y o Li nio i g o h a t The m a r l Fl w nd Er so o a o i n Cha e o . a tFur c fS u a g ng fNo 2 Bl s na e o ho g n
( i nI na dSelC . t. ( nvri f ce c n eh o g e ig Qa a r n t o,Ld ) U iesyo i eadT c nl yB in ) n o e t S n o j
A sr c T e p o l ms o h n t r g o e wo k n t t s o F h at y s p r t l ah r g b t t h r b e n t e mo i i ft r i g s u fB e rh b e a ae y g t e n a o n h a i t mp r t r i e e c f o l g sa e o mp r t r ft e ma o p e r k r n l z d I i e e a u e d f r n e o oi tv rt f c n e e a u e o r l u ls i b c sa e a ay e . t s h c n i i d c t d t a ,b ah rn h b v wo k n s o a a a h a c l t n b ss h h n e f h n i ae h t y g t e g t e a o e t i d fd t st e c lu a i a i ,t e c a g so e i o t tmp r t r it b t n, e o in p o l , sa n h r a f w sr n t a e mo e a c r tl e e au e d sr u i i o r s r f e lg a d t e o i m l l t gh c n b r c u a ey o e
迁钢公司2号高炉降料面停炉全干法除尘系统的生产实践

施, 将会烧毁箱体除尘布袋 。同时 ,还会 因长时 间更换 箱 体除尘 布 袋而影 响高炉 恢复 生产 。 国内
其 他钢 厂 曾 出现 过此 类事 故 。本 次全 干法 除尘 系 统 配合 高 炉 降料 面 停 炉 操 作 在 迁 钢 公 司 尚属 首
次 ,因为准 备充 分 、措施 得 当 、组 织 精细 且操 作
迁 钢 公 司 2号 高 炉 降 料 面 停 炉 全 干 法 除 尘 系 统 的 生 产 实 践
崔化师 姜文豪
( 迁钢公 司)
摘 要 介 绍了高炉全干法除尘系统配合高炉 降料 面过程 中增加散热 器降温 能力 的方法及 重力 除尘器后 温
除尘布袋 温度 除尘灰
度 与箱体入 口荒煤气温度的变化情况 ,分析 了高炉降料面对全干法除尘系统 的影 响、操作要 点及 注意事项 。 关键 词
Pr d to a tc n Bl wi g- wn t Lo rn a g v lo o uci n Pr c ie o o n Do wih we i g Ch r e Le e f Dr i g Du tSe r to se n No 2 BF f y n s pa a i n Sy tm i . O
首钢 迁 钢公 司 2号 高 炉采 用 全 干 法 除 尘 技 术 ,通过 重力 除尘 器后 的散 热器 来控 制 除尘 箱 体 入 口荒 煤 气 温 度 ,保 证 其 在 正 常 范 围 内。2 1 00 年 9月 1 日开始 ,2号 高 炉停 炉检 修 7天 ,停 8 炉过 程 中干法 除尘 系统需 配 合高 炉完 成 降料 面操 作 ,由于 高 炉 降 料 面 过 程 中 ,炉 顶 温 度 不 易 控 制 ,极有 可能 出现 炉顶 温度 突然 升 高而 导致 荒 煤 气温度 升 高 的情 况 ,如 果 不 采 取 有 效 的 控 制 措 为满 足 用户需 要 ,干 法除 尘系统 必需 保证 高 炉 煤气 的尘 含量 在 5msm 以下 ,箱 体人 口荒煤 /。 气 温度 正 常要求 为 10~20o 2 2 C,瞬 间可 承 受最 高 温度 理论 上为 20℃ ,散 热器 根据 炉顶平 均温 6 度 3 1o 5 C、重 力 除尘 器 前 温 度 2 5o 和 重力 除 9 C
转炉炼钢新工艺、新技术介绍

转炉炼钢新工艺、新技术介绍
1. 全新工艺:
(1)结合电磁加热与旋流燃烧法,开发新型高混镍炼钢车间;
(2)利用ELIM全熔混熔法结合智能化高温处理技术,开发新的低Nb、Ti、V 低碳钢车间;
(3)将现代化技术与新型转炉及冶炼设备相结合,提高转炉炼钢工艺稳定性和质量水平。
2. 新技术:
(1)引入新鲜管理思想,通过严格控制热处理技术,满足不同用户需求;
(2)应用优化转炉流体动力学计算和智能调节技术,调节炉内温度和化学成份,提高厚度均匀性;
(3)应用智能温度场控制技术,利用计算机模拟和实时检测炉内温度的分布,控制炉温的变化趋势,以提高钢材的出炉精度。
迁钢2650m 3全干法除尘高炉降料面实践

关键词 : 高炉 ; 干法除尘 ;降料面
中 图 分 类 号 : F5 7 T 3 文献标识码 : B
Op r t g p a tc ft e c a g r p i g l e o h 5 e a i r c ie o h h r e d o p n i ft e2 6 0 m BF wih n n t
南
方
金
属 2 1 年 第 3期 01 ∞ 如 加 : 2
S U H R T L O T E N ME A S
效 容 积.
表 1 降料面 前炉内装料调整情况
面操作. 降料面过程供耗时 1 , 中高压 回收煤气 9 其 h
1. . 15h 累计 耗 风 27万 m , 9 累计 打水 186t达 到 2 . 了安 全 、 高效 、 速 的 停 炉要 求 , 使用 干法 除尘 工 快 为
艺的高炉降料面操作积累了大量宝贵经验.
赵满祥 ,贾军 民
( 北京科技大学 冶金 与生态工程学院 , 北京 10 8 ) 0 0 3
摘
要: 对迁钢 260m 5 全干法除尘高炉降料面操作 实践 进行 了总结. 风量 、 打水量 的精确控制使炉顶煤气 满足 了
干法除尘工艺要求 , 最终通过准确把握停气 、 并 出渣铁 时机等关 键环节 达到 了安全 、 快速 、 高效 地将 料面 降至风 I = 1
u me,t e s se wo k d w l a n ii ae .An ec ag r p i gl ec u d b we e ob lw t e ty r o es f l h y tm r e el sa t p t d c d t h e d o pn i o l e l r d t eo h ee h l aey, h r n o u q iky a d e e t ey b r e r cs l o tol g t e t s fra rc t n — f a d sa - p i g u c l n f c i l y f t r p e i y c n rli h i o i u t g o n l g t p n . v u h e n me i a
电炉短流程高品质钢生产控氮技术探索与创新实践

电炉短流程高品质钢生产控氮技术探索与创新实践目录一、内容描述 (2)二、电炉短流程高品质钢生产概述 (3)1. 电炉短流程工艺特点 (4)2. 高品质钢生产需求 (5)三、控氮技术在电炉短流程生产中的应用重要性 (6)1. 氮对钢性能的影响 (7)2. 控氮技术在提高钢质量中的作用 (8)四、电炉短流程高品质钢生产控氮技术探索 (9)1. 原料控制 (10)(1)原料选择与储存 (12)(2)原料预处理方法 (13)2. 冶炼过程控氮技术 (14)(1)电炉操作优化 (15)(2)冶炼气氛控制 (16)(3)合金元素加入时机与方式优化 (17)3. 精炼与连铸过程控氮技术 (19)(1)精炼手段选择与应用 (20)(2)连铸工艺参数优化 (21)五、创新实践 (22)1. 新型控氮工艺技术研究与应用 (23)(1)氮气浓度在线监测技术 (24)(2)低氮氧化物排放技术 (26)(3)精准控氮技术优化方案 (27)2. 生产实践案例分析 (28)六、效果评估与改进建议 (29)1. 生产效果评估 (31)(1)产品质量提升情况分析 (32)(2)生产效率及能耗变化分析 (33)2. 持续改进与优化建议 (34)(1)原料采购与质量控制优化建议 (35)(2)工艺参数调整与优化建议七、结论与展望 (37)一、内容描述本报告旨在深入探讨电炉短流程高品质钢生产的控氮技术,分析当前技术现状与发展趋势,并详细阐述我们在这一领域的创新实践与探索。
随着现代工业的飞速发展,高品质钢的需求日益增长,电炉短流程生产工艺因其高效、节能等优点而受到广泛关注。
在高品质钢的生产过程中,氮含量的控制是一个关键难题,它直接影响到钢材的性能与品质。
针对这一问题,我们团队积极开展了一系列实验研究和技术攻关,成功开发出一种高效的电炉短流程控氮技术。
该技术通过精确控制冶炼过程中的氮含量,有效降低了钢中的氮含量,提高了钢材的强度和韧性等性能指标。
高炉低燃料比技术集成

德国 AMEH 5A高炉(2032) 大分二高炉(5555) 鹿岛二号炉(4800) 韩国浦项3号炉(3495) 韩国浦项3号炉(3495)
2009 2006 2003 2002 2002.5
迁钢2#(2650 m3)
迁钢2#(2650 m3)
27.62
28.73
295.0
286.88
164.2
172.66
热风炉提高风温前后操作参数对比
日期 提高风温前 提高风温后 燃烧时间 (min) 110~120 100~105 煤气量 (Nm³/h) 65000~72000 70000~75000 拱顶温度 ℃ 1390 1420 空气预热温度 ℃ 600 660 换炉次数 (次/日) 21 24
高 风 温 技 术
迁钢2号高炉低焦比低燃料比生产技术
完成单位:迁钢公司 总工室
答辩人:贾国立
2010年1月
1
目录
项目背景 低焦比、低燃料比技术 技术创新点 效益计算
结论
2
项目背景
迁钢2号高炉采用了全干法布袋煤气除尘系统,TRT压差发电,煤粉并 罐喷吹系统,热风炉煤气、助燃风双预热等新技术。
13
迁钢2号热风炉2008年8~10月风温
8月风温为攻关前的数据,其平均风温为1242℃,9月下旬到10月中旬为攻 关第一阶段的风温,平均风温为1254℃,10月下旬为攻关第二阶段的风温, 平均风温为1260℃。攻关期间10月平均风温最高为1270℃,其使用过程的最 高风温实现1280℃。
方案。
12
合理提高风温的途径
通过模拟确定预热温度在660℃时使用煤气量最经济,温度场、流场均 匀性得到明显提高。 通过模拟得到煤气流量增加3000NM3/h左右效果最好,火焰偏析状况改 善,可提高拱顶温度20~40℃。 采用自动燃烧系统提高了燃烧的稳定性,燃烧时间缩短了5-10分钟,相 应送风时间延长了5-10分钟。 优化了操作制度,确定合理的换炉次数,降低格子砖温度在燃烧和送风 期间波动。
迁钢公司大型高炉煤气干法布袋除尘系统生产实践

赵久梁 章启夫 朱伟明 王勇建 程
摘 要
华 史赞忠 姜文豪
( 迁钢公 司) ( 北京 首钢 国 际工程 技 术有 限公 司)
介绍 了迁钢公司高炉煤气干法 布袋 除尘 系统 的配置和运行 效果及取得 的经 济效益 ,提 出了系统运 生产实践
的优势 逐渐 显现 。虽然 在 运 行 中遇 到 许 多 问题 , 但 也陆 续得 以解 决 。随后 又将 2号 高炉 的成功 经
验 应用 于 3号 高 炉 ,使 3号 高 炉 煤 气 干 法 布 袋 除尘 系统 一次 性成 功投产 ,投产 近半 年来 系统 运 行 稳定 ,除尘 效果 良好 ,经济效 益 可观 。
迁 钢公 司高 炉煤 气干 法布袋 除尘 系统 主 要设 备为 布袋箱 体及 布袋 、箱 体 出人 口全 封 闭电 动插
中 ,布袋箱体工艺参数见表 2 ,除尘布袋性能参
数 见表 3 。
表 2 布 袋 箱 体 工 艺参 数
注 :除尘布袋使用的另 一种滤料 为特氟美针刺毡 ,型号为 T b 14 1( M .3 — 表面防水处理 ) 。
A s a t S s m o f u ain,o e ain lef in y a d e o o c b n f s o h a g G d y bt c r y t c n g rt e i o p r t a f c e c n c n mi e e t f t e lr e BF r o i i
行 中出现的问题 ,并 提出了解决方案 。
关键词 大型高炉 干法除尘
ThePr d to a tc fLa g o uci n Pr c ie o r e BFG y Ba le n Dr g Fit ri
迁钢高炉实践心得体会

自从我有幸参与到迁钢高炉的实践工作中,这段经历让我受益匪浅。
这不仅是一次技术上的学习,更是一次思想上的洗礼。
以下是我对迁钢高炉实践的心得体会。
一、实践背景迁钢高炉是迁安市钢铁有限公司的核心设备,具有年产100万吨铁水的能力。
在我国钢铁行业转型升级的背景下,迁钢高炉作为一家具有代表性的现代化钢铁企业,其生产实践具有重要的示范意义。
我有幸成为迁钢高炉实践的一员,深感责任重大。
二、实践过程1. 实践前的准备在实践开始前,我们进行了为期一周的理论学习。
通过学习,我们对高炉的基本原理、操作流程、设备结构等方面有了初步的了解。
同时,我们还学习了相关的安全生产知识,为实践做好了充分的准备。
2. 实践过程中的观察与学习实践过程中,我们主要参与了以下几个方面的工作:(1)高炉操作:在导师的指导下,我们学习了如何调整高炉的风量、炉温、炉渣等参数,以确保高炉稳定生产。
(2)设备维护:我们学习了高炉设备的维护保养方法,了解了设备的故障原因及处理措施。
(3)生产工艺优化:通过观察生产现场,我们发现了一些影响高炉生产效率的因素,并提出了相应的优化建议。
(4)安全生产:我们参与了高炉生产过程中的各项安全检查,确保生产安全。
3. 实践过程中的收获(1)技术提升:通过实践,我们对高炉生产过程中的各个环节有了更加深入的了解,提高了自己的技术水平。
(2)团队协作:在实践过程中,我们学会了与团队成员有效沟通、协作,共同解决问题。
(3)安全意识:通过实践,我们深刻认识到安全生产的重要性,增强了自身的安全意识。
三、实践心得体会1. 技术是基础高炉生产是一项技术性很强的工作,掌握相关技术是保证生产顺利进行的关键。
通过实践,我深刻体会到技术的重要性。
在今后的工作中,我将继续努力学习,提高自己的技术水平。
2. 团队协作是关键高炉生产涉及多个部门、多个岗位,团队协作至关重要。
在实践过程中,我们学会了如何与团队成员沟通、协作,共同完成生产任务。
这种团队精神将使我受益终身。
莱钢2# 1880m3高炉无计划长期休风快速恢复实践

莱钢2# 1880m3高炉无计划长期休风快速恢复实践
李春路;鲍永良;张吉刚;郎达慧;王雪朋
【期刊名称】《莱钢科技》
【年(卷),期】2007(000)005
【摘要】莱钢2#1880m3高炉在无计划休风时间较长的情况下,复风后采取了提高炉缸热量、控制好风口火焰温度及抓好炉前出铁等措施,大大缩短了高炉的恢复时间,将损失降低到最低水平.
【总页数】4页(P100-103)
【作者】李春路;鲍永良;张吉刚;郎达慧;王雪朋
【作者单位】莱芜钢铁集团有限公司型钢炼铁厂;莱芜钢铁集团有限公司型钢炼铁厂;莱芜钢铁集团有限公司型钢炼铁厂;莱芜钢铁集团有限公司型钢炼铁厂;莱芜钢铁集团有限公司型钢炼铁厂
【正文语种】中文
【中图分类】TF3
【相关文献】
1.莱钢1 000 m3高炉长期休风快速恢复炉况实践 [J], 刘卫国;马振军;张永生;胥长城
2.菜钢2#1 880 m3高炉无计划长期休风快速恢复实践 [J], 张吉刚;李春路;鲍永良;王雪朋;胥长城
3.济钢1750m3高炉无计划休风快速恢复炉况实践 [J], 杨云;刘存芳;曹学杰
4.迁钢2#高炉长期休风快速恢复实践 [J], 贾国利;王凤
5.玉钢1080 m^3高炉长期无计划休风炉况快速恢复实践 [J], 陈勇
因版权原因,仅展示原文概要,查看原文内容请购买。
高炉冲渣水余热换热站设备系统改造

·改造与应用·高炉冲渣水余热换热站设备系统改造王冬宝①(北京首钢股份有限公司 河北唐山064400)摘 要 高炉冲渣水余热换站设备系统是对外供热的关键核心,直接影响居民取暖、设备保温、设备低碳运行的质量。
首先,确定打破冲渣水专用过滤器备件、材料以及维修技术受制于原设备厂家的局面,降低设备运行成本,提高设备的稳定性、耐用性;其次,针对蒸汽使用的特点、蒸汽管道含水的特点、管道的布置情况等,组建研究团队进行蒸汽疏水装置改造,降低蒸汽疏水装置的故障率;最后,针对汽水换热器的使用情况及出现的问题,对汽水换热器进行了重新设计,以提升换热效率,降低运行故障率。
这为其他钢厂高炉冲渣水余热换站设备系统的运行、维护、检修提供了可靠的改造经验。
通过一段时间的运行,证明了该改造是成功的,不但降低了高炉冲渣水余热换站设备系统的故障率,而且提高了对外供热的质量,降低了经济成本。
关键词 高炉 过滤器 蒸汽疏水装置 换热器中图法分类号 TG155.4 文献标识码 ADoi:10 3969/j issn 1001-1269 2023 Z2 0491 前言1.1 研究背景首钢迁钢公司现有高炉3座,其中1号、2号高炉容量为2650m3,3号高炉容量为4000m3,均采用明特法水冲渣处理工艺,工艺流程如图1所示。
高炉熔渣与铁水分离后,经渣沟进入熔渣粒化区,水渣冲制箱喷出的高速水流使熔渣水淬粒化冷却。
炉渣在水渣沟内进一步粒化缓冲后,流入装有水渣分离器的搅笼池中,由带有螺旋叶片的搅笼机(也称螺旋机)将水渣混合物中的炉渣分离出来,经脱水后成为干渣。
干渣由皮带机输送到堆场,外运销售。
过滤器将冲渣水过滤成干净水,送入贮水池和吸水井,再抽回冲制箱循环使用[1]。
图1 冲渣工艺流程图迁钢三座高炉日产铁量约2 2万吨,高炉产渣渣比约为1:3,高炉日产熔渣7000吨,水渣约8000吨(水渣含水量约15%)。
1#高炉冲渣水含热量为36 7MW,2#高炉冲渣水含热量为36 7MW,3#高炉冲渣水含热量为57 7MW。
- 1、下载文档前请自行甄别文档内容的完整性,平台不提供额外的编辑、内容补充、找答案等附加服务。
- 2、"仅部分预览"的文档,不可在线预览部分如存在完整性等问题,可反馈申请退款(可完整预览的文档不适用该条件!)。
- 3、如文档侵犯您的权益,请联系客服反馈,我们会尽快为您处理(人工客服工作时间:9:00-18:30)。
摘要:迁钢2号高炉是首钢搬迁转移400万吨钢生产能力建设的迁钢二期工程项目,高炉有效容积为2650 m3。
迁钢2号高炉工程设计遵循“先进、可靠、实用、效益”的方针,积极采用当今国内外高炉炼铁先进技术,在借鉴迁钢1号高炉成功技术的基础上,使迁钢2号高炉在工艺技术、装备、控制方面达到国内外先进水平。
迁钢2号高炉2007年1月4日建成投产一年来,主要经济指标超过了设计能力,达到了同立级高炉的先进水平。
关键词:高炉;设计;生产实践1 概况2003年首钢总公司为贯彻落实国务院、北京市关于首钢产业结构调整、技术升级,服务首都经济的要求,部署实施首钢搬迁转移400万吨钢生产能力的方案——建设首钢迁钢工程,工程包括炼铁、炼钢、热轧及配套公辅设施。
首钢迁钢炼铁工程分成两期建成,一期工程建设一座2650 m3高炉(1号高炉),二期工程再建一座2650 m3高炉(2号高炉),最终形成一、二期年产生铁合计445万吨生产规模。
迁钢2号高炉设计遵循“先进、可靠、实用、效益”的方针,采用国内外成熟的并已经行之有效的技术和装备,充分做好环境保护、防火和安全卫生工作,贯彻高炉生产的“精料、高风温、高压、富氧、喷煤”的先进经验,以使高炉在工艺技术、装备、控制方面达到国内外先进水平。
新建高炉将成为“高效、低耗、优质、长寿、节能、安全、环保"型的现代化高炉。
2 高炉主要技术经济指标设计迁钢2号高炉在设计过程中遵循耗资少,占地面积小,结构紧凑的原则,优化结构布局,注重布局的合理、高效,使迁钢2号高炉在国内外同立级高炉中结构布局均处于领先行列。
迁钢2号高炉炉容同迁钢1号高炉相同,迁钢2号高炉在注重借鉴和使用迁钢1号高炉成功技术的基础上,对部分工艺技术进行了优化、改进和完善,进一步提高迁钢2号高炉的工艺技术、装备、控制水平。
根据迁安矿区原燃料条件和高炉操作条件,结合首钢厂区的生产实践,在高炉设计中采用先进、成熟、可靠、实用的工艺技术和设备,主要技术经济指标设计比照国内外同级别高炉的先进水平。
设计的主要技术经济指标见表1。
3 迁钢2号高炉采用的新技术迁钢2号高炉设计中采用国内外先进、可靠、实用的新技术、新工艺、新设备及新材料,以我国和首钢高炉的设计与生产实践为基础,使新技术应用后的高炉整体技术装备具有国内领先水平。
在满足工艺流程短捷、顺畅、合理的情况下,使总图布置紧凑合理,占地面积尽可能减小。
在尽量节约投资的条件下,引进部分国外先进、国内目前尚不能生产的关键部位的耐火材料和自动化控制系统和设备,使高炉寿命在不中修的条件下,达到一代炉龄15年以上。
积极采用长寿、精料、高风温、大喷煤、适量富氧等先进技术和工艺,实现高炉长寿化、高效化、现代化、自动化、清洁化。
3.1 精料技术本系统采用传统原料场和高炉料仓合并建设的联合料仓、无中继站胶带上料工艺,料仓为双列布置,烧结矿直接入称量罐的工艺布置形式。
烧结矿、球团矿、块矿、焦炭在仓下分散筛分,分散称量;杂矿仓下只设称量斗,分散称量。
称量后的所有物料均通过N1—2及N1—1主胶带机送往炉顶装料设备。
烧结矿、焦炭采用24台高效振动筛,强化仓下炉料的筛分,提高处理能力和筛分效率,使<5mm的入炉烧结矿控制在5%以内。
增加了焦丁回收装置,回收10~25 mm的焦丁,与矿石混装入炉,提高高炉透气性,降低焦比。
3.2 炉料分布控制技术采用首钢自行开发研制的水冷气封并罐式无料钟炉顶设备,布料流槽的悬挂装置采用了新型的锁紧装置,彻底杜绝了流槽脱落的发生,避免了因流槽脱落而发生的高炉休风的现象,提高了高炉作业率。
设料流调节阀,在自动控制下实现环行(多环)和螺旋布料的功能,在控制室人工控制下完成环形、点状和扇形布料。
可以根据炉况变化,及时调整布料制度,抑制边缘煤气流的过分发展,保护炉衬和冷却器。
采用多环布料技术可以提高高炉煤气利用率,降低焦比,延长高炉寿命。
传动齿轮箱采用新型水冷结构,冷却水量提高到10 t/h 以上,使氮气消耗量降低到约500Nm3/h,提高冷却效率,延长设备使用寿命,改善煤气质量,提高煤气发热值。
3.3 高炉长寿技术(1)高炉内型。
在总结国内外同类容积高炉内型尺寸的基础上,根据迁安矿山地区的原燃料条件和操作条件,以适应高炉强化生产的要求,设计合理的矮胖炉型。
设计中对高炉炉型进行了优化,加深了死铁层深度,以减轻铁水环流对炉缸内衬的冲刷侵蚀;适当加大了炉缸高度和炉缸直径,以满足高炉大喷煤操作和高效化生产的要求;降低了炉腹角、炉身角和高径比,使炉腹煤气顺畅上升,改善料柱透气性,稳定炉料和煤气流的合理分布,抑制高温煤气流对炉腹至炉身下部的热冲击,减轻炉料对内衬和冷却器的机械磨损。
(2)根据首钢多年的设计和生产实践,在炉缸、炉底交界处至铁口中心线以上,引进美国UCAR公司的热压小块炭砖,适当减薄炉缸内衬厚度,提高冷却系统的能力。
在炉底采用国产优质的莫来石质陶瓷垫;风口采用法国SAVOIE公司生产的大型组合砖。
满铺炉底采用国产大型微孔炭砖和国产高导热大块半石墨质高炉炭砖;炉底采用软水冷却。
(3)炉缸冷却壁(1—5段)采用工业水冷却。
其中第1、4、5段冷却壁采用常压工业水冷却;第2、3段冷却壁采用高压工业水冷却。
炉腹至炉身上部冷却壁(6—15段)采用软水密闭循环冷却。
软水密闭循环冷却系统又分成前排管、凸台管等小系统。
C型冷却壁(第16段)采用常压工业水冷却(4)在炉腹、炉腰、炉身下部采用3段铜冷却壁,材质为TU2轧制铜板,冷却通道钻孔成型,铜冷却壁厚度125 mm,铜冷却壁沟槽内镶填SiC捣料。
以提高冷却效率,这是一种新型无过热长寿冷却壁。
(5)在炉身中上部采用高效单排管冷却壁,冷却壁本体厚度250mm,材质为球墨铸铁QT400—20。
冷却壁沟槽内镶填SiC捣料,以提高冷却壁的挂渣性能。
(6)在炉身上部至炉喉钢砖下沿,增加1段“C”型球墨铸铁水冷壁,水冷壁直接与炉料接触,取消了耐火材料内衬。
(7)炉腹、炉腰、炉身下部区域采用Si3N4一SiC专和高密度粘土砖组合砌筑,砖衬总厚度400 mm;炉身中上部采用高密度粘土砖。
(8)采用最新开发设计的送风装置,以适应1250℃高风温的要求。
加强了送风组件的密封,对送风支管结构进行了改进和优化。
(9)采用新型十字测温装置,在线监测炉内煤气流的分布和温度变化,配合多环布料技术,使高炉操作稳定顺行,提高煤气利用率,延长高炉寿命。
炉体系统设计完善的高炉温度、压力、流量的检测,以加强高炉各系统的监视,为操作人员提供准确可靠的参数和信息,并预留人工智能专家冶炼系统接口及界面。
(10)迁钢2号高炉在借鉴迁钢1号高炉使用经验的情况下,改进优化了高炉炉缸压浆料的材质和铁口孔道结构。
3.4 提高炉前机械化水平(1)采用圆形出铁场,其最大外径为77.9 m,铁口标高为10.2 m,渣铁沟内衬采用浇注料,主沟采用贮铁式结构。
出铁场设有公路引桥,出铁场平坦化布置,便于炉前机械操作及运输。
出铁场内设2台30 t/5 t环行起重机,LK=20.6 m,轨面标高为▽21.95 m,用于出铁场内的日常生产操作及检修时使用。
(2)采用首钢自行开发研制的矮式液压泥炮,采用新型炮嘴组合机构,进一步提高炮嘴寿命。
(3)采用首钢自行开发研制的新一代多功能全液压开口机。
3.5 热风炉高风温技术达涅利一康力斯热风炉(霍戈文公司)以其合理的结构和承受高温能力在我国得到广泛应用,迁钢2号高炉采用了荷兰达涅利一康力斯内燃式热风炉的技术。
根据迁钢1号高炉的使用情况,迁钢2号高炉对热风管道混风四爪内衬结构和热风管道竖管区域进行改进,消除送风系统在使用中出现的局部结构热点问题。
根据高炉煤气发热值低的特点,迁钢2号高炉设计了双预热系统。
迁钢2号高炉热风炉主要技术性能和参数见表2;迁钢2号高炉热风炉换热器使用参数见表3;迁钢2#高炉预热炉主要设计参数见表4。
迁钢热风炉采用计算机集中控制、软水冷却、液压传动、烟气残氧分析、混合煤气发热值测试等先进工艺技术。
3.6 紧凑型长距离制粉喷煤技术工艺迁钢2号高炉设计最大煤比180 kg/t,高炉喷煤系统采用直接喷吹工艺,将制粉和喷吹系统合建在一个厂房内。
喷煤系统按工艺流程分为上煤系统、干燥剂供应系统、制粉系统和喷吹系统。
喷吹系统采用达涅利公司的并罐式喷吹系统:煤粉收集器下通过2个溜管与2个喷吹罐相连,溜管上设有阀门及补偿器,喷吹罐上设有称量装置,可实现煤粉的连续计量,喷吹罐后设有单管路喷吹系统,单管路上设有混合器,可实现对喷吹浓度的调节。
煤粉经喷煤总管送入炉前分配器中,由分配器分配到各个喷枪,进而喷入高炉。
分配器到高炉的支管路通过设计支管路的长度和阻损,实现各风口的均匀喷吹。
风口设有防堵探测器,由P LC实现自动控制,保证系统安全。
3.7 螺旋法水渣处理工艺及长寿渣沟3.7.1 螺旋法水渣工艺为机械脱水工艺的一种方法。
由于螺旋法水渣工艺关键设备只有一台螺旋机,所以其维护检修较为方便,需要检修较多的是两个轴承,设计时考虑了方便的检修措施。
采用了在水渣贮水池上加设小平流池的工艺,设置抓渣吊车,将沉淀下来的细渣进行清除,降低了冲渣水中的细渣含量,减轻其对管道的磨损和冲渣喷嘴的堵塞现象,同时降低了贮水池中沉淀物的堆积速度,为系统正常运转创造了必要的条件。
螺旋法水渣工艺较传统的渣池节省占地面积,能耗低,运行费用低;工艺流程简单,布置较灵活。
3.7.2 为了提高水渣沟衬板的使用寿命,减少检修维护量,在设计中采用新型的复合衬板代替普通的耐磨铸铁衬板。
新型复合衬板是在普通Q235一A钢板的表面采用等离子喷焊工艺喷焊Ni60+WC工作层,钢板厚度为25 mm,耐磨层厚度为8 mm。
新型复合衬板硬度极高(硬度可以达到HRC70—80),使用寿命可以达到18个月,是普通耐磨铸铁衬板使用寿命的3倍以上。
3.8 粗煤气系统及压差发电(TRT)技术高炉煤气由4根导出管引出,经上升管汇合成一根下降管进入除尘器。
除尘器为重力沉降式,煤气中大于150 μm的尘粒沉降在除尘器中。
炉尘经过2组4个球阀进入卧式加湿卸灰机,经过卸灰装置打水湿润后,由汽车运往料场。
2号高炉煤气净化采用干法除尘技术,后配备炉顶压差发电(TRT)设施。
3.9 节水技术新建联合泵站,设常压水供水系统,高压水供水系统、软水密闭循环系统、高炉鼓风机净循环系统、水冲渣浊循环系统、煤气洗涤水浊循环系统及高炉安全供水系统等。
高炉采用软水密闭循环冷却,热风炉高温阀门采用软水密闭循环冷却;煤气清洗和水力冲渣的水循环使用。
通过以上节水措施,可以实现炼铁生产过程用水“零”排放,水循环利用率为97.38%,吨铁耗用新水≤0.71 m3/t。
3.10 大型电动轴流鼓风机及交变频启动控制技术高炉鼓风机站内设置一台AV100—19全静叶可调电动轴流式压缩机及其配套辅机,并预留2台鼓风机的位置。