WCMBR-30使用说明书
美国迪克斯顿科技产品说明书:WMM30系列25-30W医用墙挂电源

WMM30 Series25 to 30W Medical Wall Mount Power SuppliesThe WMM30 Class II 25 to 30W wall mount power supplies are certi fi ed to IEC/ES/EN60601-1 and EN60601-1-11, are compliant to EN60601-1-2 (Ed4) and designed to meet IEC60335-1 (Household Appliances). Requiring no earth ground, the WMM30 series is ideally suited for Medical, Clinical and Home Healthcare applications. Four interchangeable AC plugs are available (sold separately) for use in North America, Europe, UK and Australia. Alternative output connectors and cable assemblies are available on request.* Options When no option code is stated:5V output model has a straight 5.5 x 2.1 x 12mm (OD x ID x L) connector, positive center pin and a 16 AWG 1220mm long cable 9V output model has a straight 5.5 x 2.1 x 12mm (OD x ID x L) connector, positive center pin and a 16 AWG 1800mm long cable 12V and 15V output models have a straight 5.5 x 2.1 x 12mm (OD x ID x L) connector, positive center pin and an 18 AWG 1800mm long cable 18V and 24V output models have a straight 5.5 x 2.1 x 12mm (OD x ID x L) connector, positive center pin and an 22 AWG 1800mm long cableA variety of connector and output cable options are available, please contact your local sales of fi cehttps:///en/power/dtm /wmmNotesSee website for detailed specifi cations, test methods and installation manual(1) Measured at 25%, 50%, 75% and 100% load conditions(2) Derate linearly from 100% to 90% load from 90Vac input to 80Vac input(3) Measured from 60 - 100% and 60 - 20% load(4) Ripple and noise is measured at 20MHz BW. Add 0.1uF ceramic capacitor and 10uF Electrolytic capacitor in parallel across the outputOutline Drawing Interchangeable AC plugs (Sold separately)ACC-WMM30-A (North America)ACC-WMM30-E (Europe)ACC-WMM30-U (UK)ACC-WMM30-S (Australia)WMM30_Datasheet_ 260665 September 2nd, 2020 V2TDK-Lambda France SASTDK-Lambda AmericasTDK Electronics do Brasil LtdaTel:+33 1 60 12 71 65********************.com /frTel: +55 11 3289-9599****************************.com /enTel: +1 800-LAMBDA-4 or 1-800-526-2324****************************.com Italy Sales OfficeTel:+39 02 61 29 38 63*************************.com /itNetherlands******************.com /nlTDK-Lambda Germany GmbHTel:+49 7841 666 0**************************.com /deAustria Sales OfficeTel:+43 2256 655 84******************.com /atSwitzerland Sales OfficeTel:+41 44 850 53 53******************.com /chNordic Sales OfficeTel:+45 8853 8086******************.com/dkTDK-Lambda UK Ltd.Tel:+44 (0) 12 71 85 66 66****************************.com /ukTDK-Lambda Ltd.Tel:+9 723 902 4333******************.il/ilC.I.S.Commercial Support:Tel:+7 (495) 665 2627Technical Support:Tel:+7 (812) 658 0463******************/ruTDK-Lambda CorporationTel: +TDK-Lambda Singapore Pte Ltd.Tel: +65 6251 7211*********************.com TDK-Lambda (China) Electronics Co. Ltd.Tel: +86 21 6485-0777****************************.com TDK India Private Limited, Power Supply DivisionTel: +91 80 4039-0660***************************.comFor additional information, please visit https:///en/power/。
WCRMX Outdoor Slim一体化天线接收器说明书
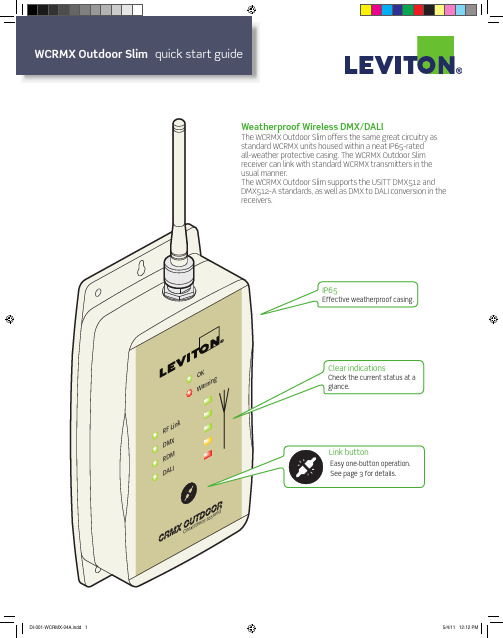
WCRMX Outdoor Slim quick start guideConnectionsCorrect use of the cable bushingsThe supplied cable bushings will, when installed correctly, provide IP65 rated protection.1 Insert the appropriately sized cable into the bushing. Feed anadditional 3/8” (1CM) of cable into the box.32*Shown with back cover removed.85-264VAC power input/output Warning! To avoid death, injury orproperty damage, Disconnect line power before connecting, disconnecting, or whenever opening the enclosure.DMX+DMX-Not UsedDALI outNeutral in (85-264V AC)Line power inHot in (85-264V AC)DALI out COMMON}DMX connects to the screwless pluggable terminal on the side of the enclosure at the top cable entry through the nipple/bushing. Line power and DALI connects to the screwless pluggable terminal at the bottom cable entry of the enclosure through the nipple/bushing. The side bottom cable entry is not used.DMX cable specificationsMin outer diameter: 0.3” (8mm)Max outer diameter: 0.5” (13mm)Conductor size: 28-20 AWG (0.08-0.5mm2)Insulation strip length: 0.2-0.25” (5-6mm)Line/DALI cable specifications Min outer diameter: 0.3” (8mm)Max outer diameter: 0.5” (13mm)Conductor size: 28-16 AWG (0.08-1mm2)Min insulation strip length: 0.2” (4mm)NOTE : The Line Power/DALI terminalblock can be detached to facilitate easier cable termination.Place a cable tie around the bushing asindicated on the drawing. Tighten the cable tie and cut off theexcess material.Pull the cable 3/8" (1cm)out of the enclosure so that the cable tied part of the bushing folds into the main part of the bushing as indicated on the drawing.Operation WCRMX Outdoor Slim uses the same great circuitry as standard WCRMX units and can link with any standard WCRMX units:Specifications Power input:85-264VAC 47-70Hz Maximum consumption: 3WOperation temperature range: -4°F to 122°F (-20°C to +50°C)Environmental:IP65 (protected from water jets)Control panelRF Link OK WarningDMX RDM DALICoexistence assuredOK- On when operational status is good.Warning - On when a con -dition occurs which might need attention, e.g. a lost radio link.Signal quality indicators The amber indicator turns on at roughly 20% of maxi -mum signal quality and the top green indicator turns on at roughly 90%. The red indicator turns on only if a problem occurs with the link to the transmitter.LINK button - See operation above.EU Declaration of ConformityMarking by the symbol indicates compliancewith the Essential Requirements of the R&TTE Directive of the European Union (1999/5/EC). This equipment meets the following conformance standards: EN 301 489-1; 301 489-17; EN 300-328-1; EN 300-328-2; EN 609 50To link transmitter and receiver(s)1 Ensure the antenna is connected.2 Power on the transmitter and receiver(s).3 Ensure that the RF LINK indicator on the receiver(s) is/areoff.4 If necessary press and hold the button on the receiver(s) to break any previous link(s).5 Press and release the button on the transmitter.6 The transmitter will search for any unlinked receivers and its RF LINK indicator will flash for ten seconds.7 The RF LINK indicator will change to a steady on-state on successfully linked receiversTo unlink• Unlink one receiver : Press and hold the button on the receiver for more than 3 seconds to unlink it from a transmitter.• Unlink all receivers : Press and hold the button on the transmitter for more than 3 seconds to unlink all of its receivers.NOT SUITABLE FOR PERMANENT INSTALLATIONRF Link on Transmitter On = Normal operation.Fast flashing (~3Hz)= In linking process.Slow flashing (~1Hz)= In un-linking process.RF Link on ReceiverOn = Linked and receiving RF signal.Off = Unlinked.Fast flashing (~3Hz)= In linking process or linked, but with lost RF signal.DMX - On when a DMX signal is present.RDM - Not supported with Leviton product.DALI - Flashes to indicate DALI activity.DALI ConverterThe integrated DMX to DALI converter in the SLIM receiver will output the levels from DMX slots 1 through 64 simultaneously as arc levels on the DALI interface using short-addresses 0 through 63. The DALI interface can drive maximum 10 DALI ballasts at 2mA each. Connection to a DALI loop with more devices require an external DALI power supply.Mounting Dimensions。
WCMBR-30使用说明书
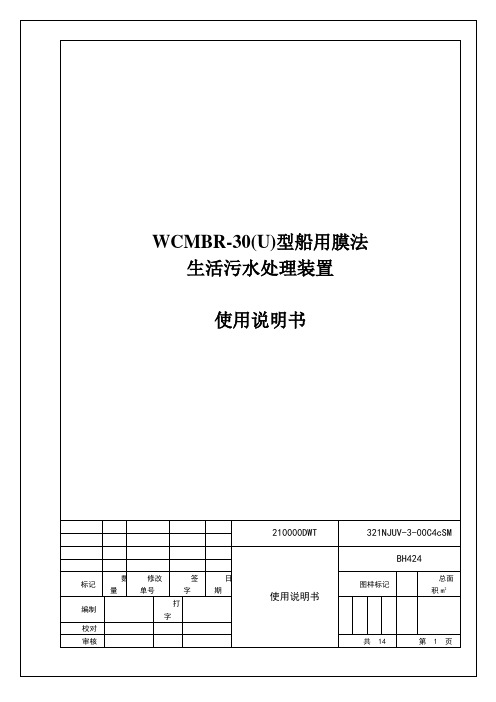
标志1. 本装置可使用于检查船舶或非检查船舶。
2. 本装置可使用于淡水冲洗或海水冲洗厕所污水。
3. 本装置柜体的压力试验为。
4. 本装置排放水指标符合IMO、MEPC159(55)的排放标准。
警告1. 本装置不得安装在爆炸性大气中,即非防爆型。
2. 本装置柜内壁涂环氧沥青漆,不得在柜上再焊接。
目录1 概述................................... 错误!未定义书签。
2 组成和技术特性......................... 错误!未定义书签。
3 系统原理............................... 错误!未定义书签。
4 主要功能单元的结构、作用及工作原理 ..... 错误!未定义书签。
5 运行方式............................... 错误!未定义书签。
6 操作................................... 错误!未定义书签。
7 安装................................... 错误!未定义书签。
8 故障及排除............................. 错误!未定义书签。
1 概述用途本装置适用于处理来自船上人员厕所的生活污水,又称“黑水”,使之达到IMO、MEPC159(55)的排放标准,排至舷外。
工作条件1.2.1 环境条件1.2.1.1 工作环境温度:0℃~+50℃1.2.1.2 环境相对湿度:≤90%1.2.2 电源:AC440V、60Hz、3φ2 组成和技术特性组成本装置主要由如下主要部件组成主要技术参数⑴型号:WCMBR-30(U)型⑵使用人数:额定使用人数: 30人⑶处理能力:平均2310L/d⑷排放水质: TSS≯35mg/lBOD5≯25 mg/lCOD≯125 mg/l大肠菌≯100个/100mlPH=6~⑸排放水压力:⑹压缩空气(用户提供):~,h⑺膜冲洗水:清洁水,压力:~接口2.3.1 电源接口:AC440V 60Hz 3φ2.3.2 物理接口:(法兰标准:GB/T2506-89 )⑴污水入口 DN150病房污水入口 DN100⑵通气口 DN65⑶冲洗水口 DN40⑷溢流口 DN40⑸膜冲洗水口 DN25⑹压缩空气入口 1/2”⑺应急排放口 DN40⑻排放口 DN323 系统原理(请参照系统图321NJUV-3-00C4cXT)本装置采用序批式-膜法处理原理处理有机污染物质,其处理流程为:污水入口→缓冲柜→序批柜→清水柜→膜组→消毒→排放→↑回流生活污水首先进入缓冲柜,以适应生化处理,同时该柜能容纳三倍的水力高峰负荷,当柜内液位达到中位时,粉碎泵启动,将污水转驳至置有软性填料的序批柜,进行接触氧化、生物处理,处理后的污水由流程泵转驳至清水柜内或直接排放至舷外,当转驳至清水柜时,若液位达到中位时,排放泵启动,将处理水泵入膜组,经膜组过滤后的排放水经紫外线消毒装置后排出舷外。
XSR30无纸记录仪

XSR30 无纸记录仪·使用手册
热电阻:Pt100,Cu100,Cu50,BA1,BA2,G53 热电偶:K,S,R,B,N,E,J,T 其它输入信号或分度号需在订货时注明。
3.3 报警输出
继电器输出:触点容量 220V AC,3A,阻性负载 共用 8 点报警,可按通道的各报警点值设定
3.4 外供电源
4. 安装与接线……………………………………...4
4.1 外形及开孔尺寸……………………………………….4 4.2 接线端子图…………………………………………….5 4.3 输入信号接线………………………………………….5
5. 功能说明………………………………………...6
5.1 输入信号选择及量程…………………………………6 5.2 显示修正……………………………………………….7 5.3 数字滤波……………………………………………….7 5.4 工程量单位选择…………………………………….…7 5.5 报警……………………………………….…………....8 5.6 输出上限及输出下限………..……………………......8 5.7 工位号………………………..……………………......8 5.8 通讯接口…………………………………….……….…8
7.2 通道组态………….…………………………………..25 7.2.1 工位号的修改……………………………..……26 7.2.2 信号类型……………..………………………...26 7.2.3 工程单位…………..…………………………...26 7.2.4 量程上限、量程下限..…………………………27
XSR30 无纸记录仪 使用手册
06-A 版
装箱清单 序号 名称 1 XSR30无纸记录仪 2 接线端子 3 安装导轨 6 128M或64M优盘 7 上位机转换软件 8 使用说明书
智能涡街流量计使用说明书(三线制)
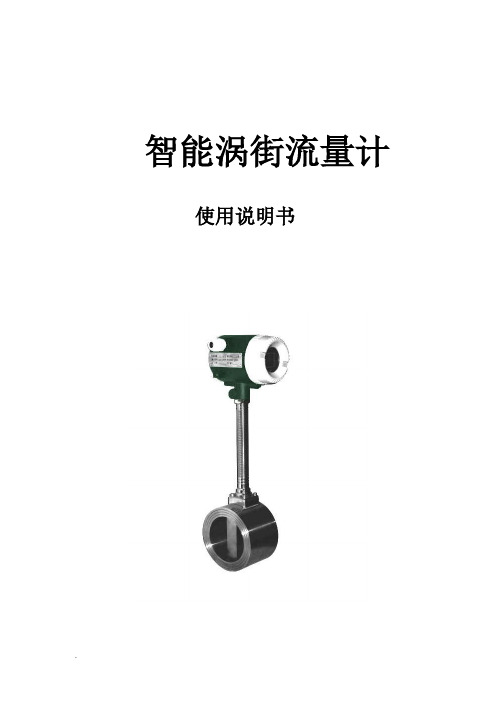
智能涡街流量计使用说明书目录一,产品概述二,测量原理三,结构与技术参数四,流量计的选型五,流量计的安装六,流量计的电气连接七,故障排除与日常维护一、 产品概述1. 概述涡街流量仪表是根据卡门涡街理论,利用了流体的自然振动原理,以压电晶体或差动电容作为检测部件而制成的一种速度式流量仪表。
该仪表具有无可动部件、测量范围度大、介质适应性广、测量精度高、检定周期长、传输信号距离远、压力损失小、结构简单、运行可靠、使用寿命长、安装维护方便等许多显著优点。
可广泛应用于石油化工、治金机械、食品、造纸,以及城市管道供热、供水、煤气等行业的各种液体、气体、蒸气等单相流体的工艺计量和节能管理。
2. 产品特点● 采用抗机械震动,抗冲击和抗脏污的结构新设计。
● 采用最先进的集成电路,信号处理精度高,高抗干扰性,可靠性高。
● 可选用加宽量程型号,获得优越的小流量性能和扩宽的流量范围。
● 可选用电容式流量计,抗震性能好,最高测量温度达到400 ℃。
二、 测量原理涡街流量计是由设计在流场中的旋涡发生体、检测探头及相关的电子线路等组成。
当液体流经三角柱形旋涡发生体时,它的两侧就成了交替变化的两排旋涡,这种旋涡被称为卡门涡街(图1),在此基础上得出了频率与流体的流速的关系: F= St ×V/d式中:f ————————————涡街发生频率(Hz )V ————————旋涡发生体两测的平均流速(m/s )St-----------------------斯特罗哈尔系数(常数)这些交替变化的旋涡就形成了一系列替变化的负压力,该压力作用在检测深头上,便产生一系列交变电信号,经过前置放大器转换、整形、放大处理后,输出与旋涡同步成正比的脉冲频率信号(或标准信号)旋涡发生体探头交变力图1三、 结构与技术参数1. 流量计的结构形式流量计是由表体与检测放大器及连接这两部分的连接杆组成,表体及其组成部件和连接杆均由1Cr18Ni9Ti 不锈钢材质制成,具有防腐耐用之优点;仪表根据安装方式不同分三种结构形式,分别是满管式、简易插入式、球阀插入式,结构形式如下图所示:图2 结构示意图2.流量计的外形尺寸流量计表体屏蔽罩检测放大器连接导线图33、流量计的技术参数●测量介质:液体、气体、蒸汽●测量范围:(见表2)●公称通径:(见表2)非标产品可根据用户要求特殊定做●温度范围:压力式 -40℃~350℃电容式 -60℃~400℃●压力规格:PN1.6Mpa; PN2.5Mpa; PN4.0Mpa,更高的压力规格可特殊定做●范围度:正常范围1:10 扩展范围1:15●测量精度: 液体、气体示值±1%蒸汽示值±1.5%插入式流量计示值±2.5%参数公称通径(mm)H L15 290 6520 290 6525 290 6532 290 7040 293 7550 299 7565 307 7580 315 90100 325 90125 338 100150 351 120200 376 150250 400 160300 425 160●供电: 24VDC,6.14v锂电池●输出信号: 脉冲信号 4~20mA电流信号●充许振动加速度:电压式≤0.2g 电容式≤1.0g●环境温度: -40℃~55℃(非防爆场所) -20℃~55℃(防爆场所) ●环境湿度:相对湿度5~85%●大气压力:86~106Kpa●信号远传距离: ≤500m●信号线接口:内螺纹M20×1.5●防爆等级(ia)ⅡCT2-T5●防护等级:数量级IP65 潜水型IP68仪表材质:仪表外壳采用铝合金,表体部分采用1Cr18Ni9Ti不锈钢结构形式通径(mm)工况流量范围(m3/h)液体气体蒸汽满管式25 0.9-10 10-100 12-120 40 2.5-26 25-250 30-300 50 3.5-38 40-400 50-500 65 5.2-65 68-680 85-850 80 8-100 100-100 120-1200 100 12-150 160-1600 190-1900 125 20-250 230-2300 280-2800 150 32-380 380-3800 440-4400 200 50-620 670-6700 790-7900 250 80-1150 1060-10600 1200-12000 300 120-1300 1540-15400 1780-17800插入式400 180-2700 2700-27000 3200-32000 500 280-4200 4240-42400 4950-49500 600 410-6100 6100-61000 7100-71000 800 720-10800 10850-108500 12660-126600 1000 1130-16900 17000-170000 20000-200000 1200 1630-24400 24400-244000 28500-285000 1500 2550-38000 38200-382000 44500-445000四、流量计的选型1、选型表LUGB(E)□□-□-□□-□压电式/电容式涡街流量计型谱安装方式2 法兰卡装式3 简易插入式直径≥250mm可做插入式流量计4 球阀插入式被测介质2 液体3 气体4 蒸气(250℃以下)5 高温(350℃以下)高压蒸汽6 特高温(400℃以下)蒸汽(电容式)公称通径(mm)-02 25 -04 40 -05 50 -06 65 -08 80 -10 100 -12 125 -15 150 -20 200 -25 250 -30 300 -40 400 ::-150 1500介质压力1.6Mpa-2 2.5Mpa-4 4.0Mpa以上输出信号脉冲频率信号D 4-20mADC标准信号特殊规格-F 分体式-B 本安防爆型-N 耐腐蚀型-Q 潜水型-X 现场显示型型谱举例:125口径压电式法兰卡装型涡街流量变送器,测量介质蒸汽,温度220度,压力0.8Mpa,仪表型号为LUGB24-12-D2、选型的方法仪表的选型是仪表应用中非常重要的工作,选型的正确与否直接影响仪表的计量精度。
CPM-R针标机使用说明书
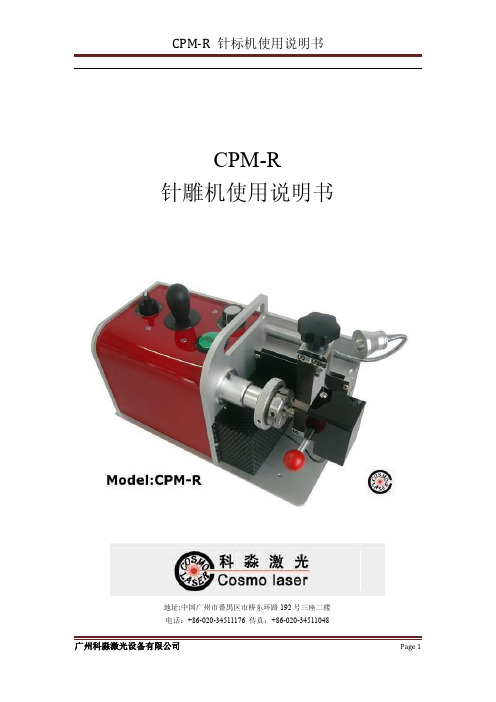
CPM-R针雕机使用说明书地址:中国广州市番禺区市桥东环路192号三座二楼电话:+86-020-******** 传真:+86-020-********目录第一章概述 (6)1.1针雕机功能简介 (6)1.2控制软件简介 (7)1.2.1 软件运行要求 (7)1.2.2 驱动程序安装 (7)1.2.3 软件的安装 (9)1.2.4 软件功能 (9)1.2.5 操作界面 (10)第二章针雕机操作说明 (12)2.1 操作台概述 (13)2.1.1 操作台控制部件汇总 (13)2.1.2 操作台操作 (14)2.1.3 放置雕刻样品 (16)第三章开启软件 (18)3.1 软件运行与界面介绍 (18)3.2 针雕机电源线与数据线的连接 (22)3.3 针雕机与电脑的连接 (24)3.3.1 选择COM端口号 (24)3.3.2 连接COM口 (24)3.3.3 开启针雕机电源 (27)第四章文字打标详细功能介绍 (29)4.1 文字的编辑 (29)4.1.1 文字输入 (29)4.1.2 字体设置 (29)4.1.3 字体信息 (32)4.2 设置打标尺寸 (33)4.2.1 尺寸设置 (33)4.2.2 尺寸说明 (33)4.3 文字的打标预览 (34)4.3.1 打标预览 (34)4.3.2 文字反转的喷沙效果 (35)4.3.3 预览区的拖动 (36)4.4针雕机软件的连接 (36)4.4.1 初始状态 (36)4.4.2 连接状态说明 (37)4.4.3 针雕机成功连接 (37)4.5 打标位置的对齐 (38)4.5.1 手动对齐 (38)4.5.2 精确对齐 (38)4.5.3 针头位置对齐 (39)4.5.4 针头和打印表面的对位 (39)4.6 开始打标 (42)4.7.1 针雕机完成打标任务 (43)4.7.2 打标完成状态说明 (44)4.8重叠重复打标 (44)4.8.1 重叠打标 (44)4.8.2重复打标 (45)4.8.3 连续打印 (45)4.8.4 打标完成后自动回位功能 (47)4.9 保存与读入 (47)4.9.1 保存打印字体的大小与格式 (47)4.9.2 读取上次保存好的字体字印 (48)第五章图片打标详细功能介绍 (50)5.1图片打标 (50)5.1.1 进入图片打标窗口 (50)5.2 图片大小设定 (51)5.2.1 图案点数 (51)5.2.2 图案点数的设置 (52)5.3 图片编辑 (53)5.3.1 画图 (53)5.3.2 点画法 (54)5.3.3 拖画法 (54)5.3.4 其他辅助功能按钮 (54)5.5图片打标 (66)附录1 (67)附录2 (69)第一章概述1.1针雕机功能简介雕刻类型:戒指和手镯的内外圈应用字体:电脑里所带的字体都可以显示雕刻高度:英文字数0.5-15mm/中文1-15mm图片类型:黑白位图(BMP)雕刻外圈直径:15-80mm雕刻内圈直径:15-60mm供电要求:AC220V 50-60Hz 0.5A (可根据要求改为AC110V供电)耗电功率:75W设备尺寸:380mm×180mm×230mm(高)净重:8.5KG软件:Cosmark (由广州科淼激光有限公司提供)1.2控制软件简介1.2.1 软件运行要求操作系统要求:本软件需要运行在WINDOWS 98 或以上的Microsoft Windows操作系统中,建议运行环境为Windows XP。
BXM-30R立式压力蒸汽灭菌器操作规程
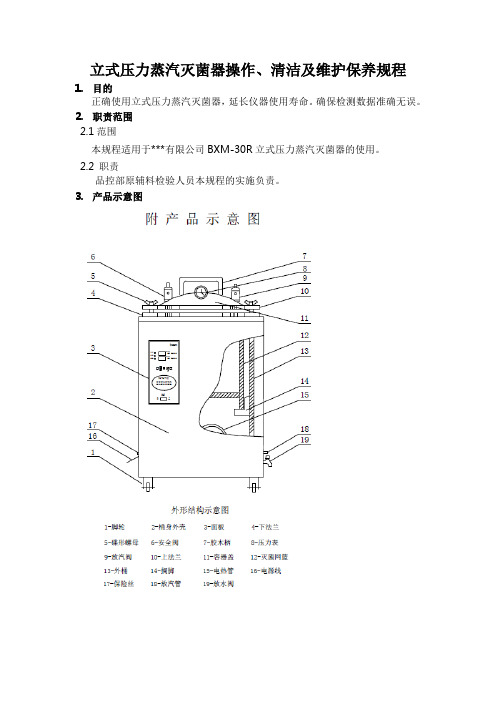
立式压力蒸汽灭菌器操作、清洁及维护保养规程1.目的正确使用立式压力蒸汽灭菌器,延长仪器使用寿命。
确保检测数据准确无误。
2.职责范围2.1范围本规程适用于***有限公司BXM-30R立式压力蒸汽灭菌器的使用。
2.2 职责品控部原辅料检验人员本规程的实施负责。
3.产品示意图4.操作A加水在灭菌器外桶内加入清水,所加水位必须至灭菌桶搁脚(14)处。
连续使用时,必须在每次灭菌后补足水量,以免干烧而发生重大事故。
B堆放将待消毒的物品,予以妥善包扎、有顺序的放入灭菌网篮(12)内,相互之间留有间隙。
这样有利于蒸汽的穿透,提高灭菌效果。
C密封将灭菌网篮放入桶体内,对正盖与桶体的螺栓槽。
用力均匀地将相对方位(5)蝶形螺母旋紧,使容器盖与桶体密合。
用橡胶管连接在放汽管上,然后插没到一个装有冷水的容器里,在加热升温过程中,当温控仪显示温度小于102℃时,电磁阀将自动放汽,排除灭菌桶内的冷空气。
当显示温度大于102℃时,自动放汽停止。
D加热面板说明:1、开启电源开关接通电源,数显控制仪显示。
上排显示测量温度及计时时间值,下排显示温度及计时时间的设定值。
计时时间设定范围为4~120分钟(从计时灯闪烁开始计时,本公司设置为30min):温度设定范围为0~126℃(本公司设置为125℃)。
2、温度和时间的设定:A、按“SET”键:上排显示S_T,下排显示温度设定值。
B、按“ < ”移动键即可选定某位,被选中某个数字位时,该数字位在下排显示屏上呈“闪烁”状态。
C、按“▲”和“▼”键即可设定所需要温度值。
D、再按“SET”键:上排显示S_C,下排显示计时时间设定值。
E、按“ < ”移动键即可选定某位,被选中某个数字位时,该数字位在下排显示屏上呈“闪烁”状态。
F、按“▲”和“▼”键即可设定所需要时间值。
G、再按“SET”键二下,上排显示0_5,下排显示温度设定值。
等几秒系统会自动复位,上排显示测量温度,下排显示温度设定值。
CPM 机器人模型 30、40、50 和 60 机器的拔除器和压缩梁泡沫泡沫安装说明说明书

Knowledge BaseArticle Type: InstructionsInstalling Stripper andCompression beam bushings onCPM machines, models, 30, 40 50and 60 machinesWARNINGNever work on, clean or service this unit, control panel or any machine or open or remove any protective cover, guard, grate, door, or maintenance panel until the power or energy sources has been turned off, locked out / tagged out, and all moving parts have come to a complete stop and or blocked to prevent movement. Machinery is dangerous –avoid personal injury and or death by following manufacture, Local, and OHSA safety procedures. Contact Columbia Machine for safety decals, guards, horns and beacons.Description:Instructions on “How to” properly install CPM Stripper and Compression beam bushings, and product comparison on fiber, plastic and steel bushings.Installing CPM Stripper and Compression beambushings, plastic (run dry) or steel (greased)∙All CPM series machines from 30, 40, 50, 60∙See part details below for part #s and other details.When installing the new beam bushings here are some guide lines:∙Make sure columns are smooth.∙Make sure the bushings are kept as matched pairs.∙Before installing, fill a clean bucket or bowl with about 5 inches of clean hydraulic oil.∙Drop the pairs in oil, and then install.∙This oil SHOULD NOT be used continuously, or on a regular bases.∙Do not sand bushing before installing, install bushings as received. Plastic bushings:∙Regular heating of columns and the need for oiling means you have other problems going on.1. First, the oil will help when removing the old bushings andhelp on installation of the new replacements.2. The oil film on the face (against the column) will help stopheating during start up and brake in.3. If columns ever heat up, a lightweight oil like WD-40 can beapplied to columns.Steel bushings:∙The steel bushing are greased once a shift or as needed based on the grease film left on the column surface.Typical CPM Bushing LayoutWhen replacing bushings, it isadvisable the replace the sealsProduct ComparisonCPM Column Bushings for Stripper and Compression BeamsPart Number: 675.200.19.000 (used from 1994 to 2005)Simple Description: Fiber bushingMaterial Description: Fabric reinforced resin with incorporatedsolid lubricant.Expected Life:Heavy production (multiple shifts, 5+ days/week): 3 mos.Moderate production (single shift, 5 days/week): 6 mos.+Number needed for machine: 8 (4 on each beam)Advantages: no greasing, only initial oil lubrication, lower costDisadvantages: replaced more often/wear out quicker comparedto cast iron, flange occasionally breaks off requiring raising of column to remove bushingPart Number: 675.200.19V (used 2005 to present)Simple Description: Plastic bushingMaterial Description: Low friction polymer bearing material.Expected Life:Heavy production (multiple shifts, 5+ days/week): 3 mos.Moderate production (single shift, 5 days/week): 6 mos.+Number needed for machine: 8 (4 on each beam)Advantages: no greasing, only initial oil lubrication, lower cost,flange does not break off, possible longer life over fabric bushingDisadvantages: replaced more often/wear out quicker comparedto cast ironPart Number: 485.2.16S (used 1980 to present)Simple Description: Metal bushingMaterial Description: Cast iron.Expected Life:Heavy production (multiple shifts, 5+ days/week): 3 yearsModerate production (single shift, 5 days/week): 5 yearsNumber needed for machine: 8 (4 on each beam)Advantages: long lifeDisadvantages: requires periodic greasing, grease build-up onmachine, more expensive than plastic or fiber。
30磅国家吸收室操作手册说明书

30 Lb. Country Smokehouse Assembly and Operating Manual1500 Clinton St. Bldg. 123, Buffalo, NY 14206Tel: (716) 824-5814 • Fax: (716) 824-646530 Lb. Country Smokehouse Operating ManualTable of Contents PageIntroduction 1Smoking Meat 1Important Safeguards 2Operating Instructions 2Troubleshooting 3Cleaning 5Warranty 5Limitation of Liability 5Specifications/Parts List 6Assembly Instructions 7IntroductionCongratulations! You have purchased a smokehouse designed, engineered and constructed by a company with 30 years experience in creating products for making homemade sausage. The materials used will give you years of trouble-free service, provided that you carefully follow the use and maintenance instructions in this manual. Please remember that this smokehouse must always be monitored when in use. Like any piece of cooking equipment, it generates heat that, if not controlled, may lead to fires and possible injuries.Smoking MeatSmoking meat can accomplish two things simultaneously: it can prepare meat for long term storage and impart unique flavor profiles depending on the ingredients and methods used. There are so many different recipes and methods that they cannot be adequately covered in this manual. We recommend that you purchase a complete book on sausage makingto get the most out of this smokehouse. The most thorough text of this subject is Great Sausage Recipes and Meat Curing by Rytek Kutas. This book is available on our website as well as through many bookstores and some local libraries.Important Safeguards1. Read ALL of these instructions thoroughly before using.2. Save these instructions for future reference.3. Never leave your smokehouse unattended.4. Never use your smokehouse indoors.5. Close supervision is necessary when this smokehouse is used near children. NOTE: This machine is not intended for use by children.6. Smokehouses are major appliances and should only be used by a person that isfamiliar with smoking procedures.7. This smokehouse operates at 110 volt, 9 amps and should be serviced only by aqualified electrician. Failure to do so may result in electrical shock, bodily injury orproperty damage.8. As with any electrical appliance, basic safety precautions should always be followed. Your smokehouse is really a cooking utensil and needs your complete attention. It is no different from using an oven, barbecue grill or frying pan at home. We all knowwhat can happen if they are left unattended for any length of time. Follow basic safety precautions and enjoy your smokehouse.9. To protect against electrical shock, do not immerse cord, plugs or heating element in water or other liquid. Avoid using this smokehouse in the rain.10. Unplug this smokehouse when not in use.11. Unplug this smokehouse before cleaning or servicing.12. Do not operate any appliance with a damaged cord or plug, after the appliance malfunctions, or has been damaged in any manner.13. Extreme caution must be used when moving any appliance. Do not move this smoke house while operating.14. If there are any questions about this appliance, contact the manufacturer.Operating InstructionsOur smokehouses are about as simple to operate as your kitchen stove. The proper and efficient operation of this smokehouse rests with you. This appliance is equipped with one control or thermostat and a thermometer located on the upper left hand outside panel. The thermostat control has a range from 50° F to 200° F. The ideal temperature when smoking sausage is 165° F. This can be monitored by checking the thermometer.THE SMOKEHOUSE TEMPERATURE SHOULD NEVER EXCEED 170° F AT ANY TIME WHEN SMOKING MEATS.The 30 Lb. capacity smokehouse is designed to hold 30 lbs. of meat (sausage, bacon, hams, hindquarters). If overloaded, the time from start to finish will greatly increase.ONLY OPERATE THIS APPLIANCE AFTER YOU HAVE READ AND UNDERSTAND THESE INSTRUCTIONS. IF YOU HAVE ANY DOUBTS, CONTACT THE MANUFACTURER.Operating Instructions, cont’d1. Fully open the damper located on the top of the smokehouse by turning the lever on the damper stack. Preheat the smokehouse to 130° F by turning the smokehousecontrol, located below the door, to between Low and Medium. Monitor the insidetemperature on the dial thermometer inserted through the hole in the door. Adjust the temperature by turning the smokehouse control in 1/8 turn increments until the desired temperature is reached.2. While you are waiting for the smokehouse to preheat, dampen the sawdust. Do notsoak it or get it too wet or it will create extra moisture that will condense on the inside of the smokehouse. On the other hand, if it is too dry, it may create an open flamewhich may scorch the meat and/or damage the smokehouse. There are three waysto check if your sawdust has reached the proper dampness: 1. There should be novisible water collecting in the bottom of the sawdust pan, 2. All of the sawdust should now be a darker color, 3. When you pick up a little more than a pinch of sawdust and squeeze it in your fingers, water should not drip out. The amount of sawdust usedgreatly depends upon individual taste. Using one full pan is a good place to start, but you can use more if you desire a stronger taste. Set it aside for Step 4.3. After approximately 15 minutes, place the product you will be smoking in thesmokehouse, close the door and let the product dry for 30-45 minutes at 130° F.4. Open the smokehouse door and carefully place the sawdust pan with sawdust in it.(TIP: Pack the dampened sawdust in the pan and create a hole in the middle ofsawdust. This will help to keep the sawdust smoldering and create a heavy smudge.) Close the door, leave the damper open and turn the smokehouse control to High.5. When you see smoke coming from the smokestack (this could take up to 10 minutes), lower the temperature to 140-145° F and hold at this temperature by turning thesmokehouse control in 1/8 turn increments until the desired temperature is reached. Close the smokestack to 1/4 open (repeat Step 4 if smoke stops).6. Raise the temperature every 1 1/2 hours until the smokehouse temperature reaches 160-165° F. Hold at this temperature until the internal temperature of the product you are smoking reaches 152° F.7. When 152° F is reached, turn off the smokehouse and carefully remove sausage.8. Shower with cold water until the internal temperature reaches 120° F.9. Refrigerate sausage overnight. Product is now ready to eat or freeze.TroubleshootingWhat happens during the smoking process?During the smoking process, smoke emits acids which cling to the meat and to the outside layer of skin. This acid helps preserve the meat by preventing the growth of surface mold and bacteria compounds.How long does it take to smoke a sausage?A 19 mm casing takes approximately 7 hours, a 32-35 mm casing takes approximately 8 hours, a 3 1/2” synthetic casing may take up to 12 hours, and a ham can take a couple of days.Troubleshooting, cont’dHow do I know when the meat is smoked?You can identify that your meat is fully smoked by the distinctive color that develops as a result of the carbon compounds combining with the meat pigments. Also, the cures that are used will give smoked meat a red color.How do I use the sawdust or wood chips?The sawdust or wood chips should be dampened, yet not soaked. Dampened sawdust will burn for a longer period of time and will impart gentle flavors into the meat. To dampen, place sawdust in a bucket or bowl and squirt with a water bottle. You should mix the saw-dust as you add the water to make sure all of the sawdust is moistened.Can I cold smoke with my Sausage Maker smokehouse?It all depends on what you mean by “cold smoke”. Cold smoking refers to a smoking process in which the heat source is in one area while the smoke is forced into another area where the meat product is. In other words, the meat will have a smoked flavor, but willnot be exposed to heat. If you are referring to making sausage and keeping the tempera-ture within the 170 degree area, then yes, this is what our smokehouses are designed for. Smoking sausage is a slow process. The temperature of the smokehouse should be between 165 degrees and 170 degrees. When the temperature rises higher, between 190 degrees and 200 degrees, the fat breaks down, and over 200 degrees you will melt the fat.Can I use liquid smoke and still use my smoker?Yes, you can. Just add liquid smoke to your spices and mix with the meat. Then proceed to use the smokehouse at the low temperatures as instructed.Can I put more sausage in my smokehouse than suggested?No. If overloaded, the time from start to finish will be greatly increased. Also, if the meat is touching there will be discoloration where the smoke was not able to penetrate the meat.Can I do BBQ Ribs in my smokehouse?No. The Sausage Maker Smokers are made for the sole purpose of smoking meat and are meant for temperatures no higher than 190 degrees. If the temperature goes higher the fat melts, which can cause the heating element to burn out or may cause a fire in the smoke-house itself.Why was there liquid on the bottom of my smokehouse after smoking?Your temperature was too high and it melted the fat in the meat.My sausage does not look good, it is shriveled. What do you think was theproblem?There could be several reasons for these results. The temperature may have risen too high and either melted or repositioned the fat. Also, the sausage may not have been showered with cold water immediately after it was finished smoking. Finally, the sausage casings may not have been stuffed to their full capacity.Most of my sausage has a nice mahogany color, but there are areas of whitespots. Why?If the sausage was touching during smoking, the smoke was not able to penetrate that area, leaving a white spot after smoking. There is no problem with your sausage.Cleaning and MaintenanceYour smokehouse has been designed to give you years of trouble-free service, provided that it is properly maintained. After each use, unplug the smokehouse and allow it to cool. Do not try to clean it while it is still hot. Wipe it down with a good cleaner or detergent. If possible, avoid scouring the surface as this will mar the finish and promote sticking in sub-sequent uses. The Sausage Maker, Inc. carries a smokehouse cleaner that does a great job. If you have excessive amounts of dripping or if there is liquid in the bottom of your smokehouse, it should be cleaned up immediately.WarrantyThe Sausage Maker, Inc., through its Distributors, warrants each new product sold by it to the initial user to be free of defects in material and workmanship for a period of one year from the date of sale of the equipment. With respect to the sale of spare parts, such warranty period shall be three (3) months from the date of sale.The Sausage Maker, Inc. will provide a new or repaired part, at its election, in place of any part which is found upon inspection to be defective in material and workmanship during the period described above. Purchaser must present proof of purchase and purchase date at the time of exercising this warranty.This warranty does not apply to failures occuring as a result of abuse, misuse, negligent repairs, corrosion, erosion and normal wear and tear, alterations or modifications made to the product without express written consent of The Sausage Maker, Inc. or failure to follow the recommended operating practices and maintenance procedures as provided in the products operating and maintenance publications.The warranty provided herein does not apply to equipment sold hereunder but manufactured by others as they are warranted by their respective manufacturers directly to the user. This warranty is in lieu of all other warranties (except of title) expressed or implied and there are no warranties of merchantability or of fitness for a particular purpose. Limitation of LiabilityThe remedies of the user set forth under the provisions outlined above are exclusive and the total liability of The Sausage Maker, Inc. or its distributors with respect to this sale of the equipment and service furnished hereunder, in connection with the performance or breach thereof, or from the sale, delivery, installation, repair or technical direction covered by or furnished under this sale, whether based on contract, warranty, negligence, indemnity, strict liability or otherwise shall not exceed the purchase price of the unit of equipment upon which such liability is based.The Sausage Maker, Inc. and its Distributors shall in no event be liable to the user, any successors in interest or any beneficiary or assignee relating to this sale for any conse-quential, incidental, indirect, special or punitive damages arising out of this sale for any breach thereof, or any defects in, or failure of, or malfunction of the equipment underthis sale whether based upon loss of use, lost profits or revenue, interest, lost goodwill, work stoppage, impairment of other goods, loss by reason of shutdown or non-operation, increased expenses of operation, cost of purchase or replacement power claims of user or customers of the user for service interruption whether or not such loss or damage is basedSpecifications/Parts ListSpecifications & Dimensions:• 120 Volt, 1000 Watt Heating Element with Control• Inside Dimensions: 16 1/4” W x 15” D x 31 1/2” H (max.), 14” H (min) • Outside Dimensions: 22 1/2” W x 19 3/4” D x 55 1/4” H• Shipping Weight: 62 Lbs.Equipped With: Part # • Textured Aluminum walls and Stainless Steel bottom inside• 1” Non-sagging insulation• 4 Chrome Plated Shelves 32731 • 3 Hickory Hardwood Dowels 41200 • 7 3/4” Stainless Steel Sawdust Pan 41600 • Baby Dial Thermometer 49400Optional Equipment:• Stainless Steel Shelves 32733 • Smokehouse Cleaner & Degreaser 31450 • Stainless Steel Cleaner & Polish 31542 • USDA Approved Hickory Smoking Sawdust 31450Provided Parts• 4 Legs• Chimney• 2 Screws (on underside of roof)• 12 Screws (attached to smokehouse walls)• Silicone SealantPart 1: Attach Legs1. Lift the roof off of the unit and set the roof aside for Part2. Turn the unit on its back.2. Lay out all four legs as shown in the picture below. The first two legs are for the leftand right, respectively, of the front of the smokehouse and the second two legs are for the left and right, respectively of the back of the smokehouse.1 23. There are 12 screws in the sides of the smokehouse walls. Remove these screws and set them aside.4. Align the legs with the outside corners of the smokehouse walls, lining up the holes in the legs with the new holes in the side of the smokehouse. Screw in the providedscrews to secure the legs to the smokehouse walls.Part 2: Install Chimney1. Turn the roof on its side. Near the hole for the chimney you will see 2 screws. Detach the screws and set them aside.2. Turn the roof upright again. Insert the chimney into the hole in the roof. It will only fit one way, allowing for the tabs to line up with the screw holes on the underside of the roof.3. Turn the roof on its side again. The tabs, which are now on the underside of the roof, should be in line with the screw holes.4. Bend the tabs backwards so that they are flush against the sides of the roof. Screw the chimney into place with the screws that you set aside.5. Seal the edges where the roof and the chimney meet, shown in the image below witha red line, to prevent heat and smoke from escaping during use. The sealant isprovided.6. Once the sealant has dried properly (reference instructions on the bottle of silicone sealant), your smokehouse is ready to use. Set the roof back onto the unit and follow the smokehouse’s operating instructions to start the smoking process.10The Sausage Maker, Inc.1500 Clinton St. Bldg. 123, Buffalo, NY 14206 Tel: (716) 824-5814 • Fax: (716) 824-6465 。
艾桑(Eaton)防电缆保护设备XXCFXXX30-RJ 操作手册说明书
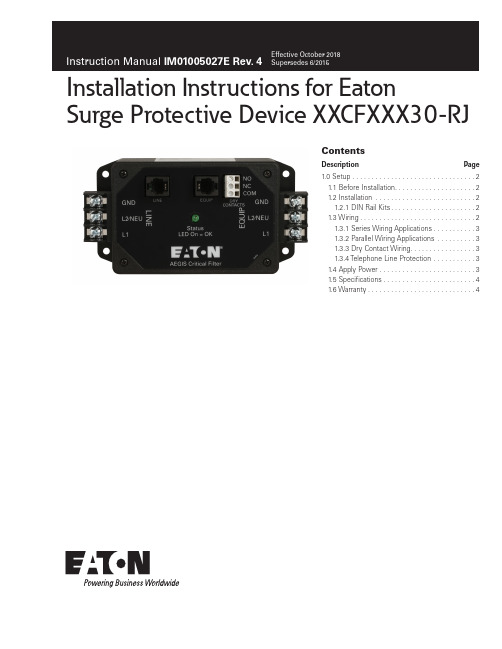
ContentsDescription Page 1.0 Setup ................................21.1 Before Installation .....................21.2 Installation ..........................21.2.1 DIN Rail Kits ......................21.3 Wiring ..............................21.3.1 Series Wiring Applications ...........31.3.2 Parallel Wiring Applications ..........31.3.3 Dry Contact Wiring .................31.3.4 Telephone Line Protection ...........31.4 Apply Power .........................3 1.5 Specifications ........................41.6 Warranty . (4)nstallation Instructions for EatonSurge Protective Device XXCFXXX30-RJ2Instruction Manual IM01005027E Rev. 4Effective October 2018Installation Instructions for EatonSurge Protective Device XXCFXXX30-RJEATON WARNINGHAZARDOUS VOLTAGES PRESENTIMPROPER INSTALLATION OR MISAPPLICATION OF THESE DEVICES MAY RESULT IN SERIOUS INJURY TO INSTALLER AND/OR DAMAGE TO ELECTRI-CAL SYSTEM OR RELATED EQUIPMENT. READ AND UNDERSTAND ALL INSTRUCTIONS BEFORE BEGINNING INSTALLATION. PROTECTIVE EYE-WEAR SHOULD BE WORN WHENEVER WORKING AROUND HAZARDOUS VOLTAGES.NOTICEALL INSTRUCTIONS AND MEASUREMENTS MUST BE COMPLETED BY A LICENSED/QUALIFIED ELECTRICIAN IN ACCORDANCE WITH THE U.S. NATIONAL ELECTRICAL CODE, STATE AND LOCAL CODES OR OTHER APPLI-CABLE COUNTRY CODES. THE U.S. NATIONAL ELECTRICAL CODE AND STATE AND LOCAL REQUIREMENTS (OR OTHER APPLICABLE COUNTRY CODES) SUPERSEDE THIS INSTRUCTION.Catalog NumberVoltage RangeModeVPRMCOVInSCCRPeak Surge CurrentXXCF12030-RJ 248 - 149 Vdc 1 100 -127 Vac L-N L-G N-G 5005005001501501505kA 10kA 80kAXXCF23030-RJ 2150 - 300 Vdc 1128 - 230 VacL-N, L-G, N-G8008008002752752753kA 10kA 80kA1 UL 1449 4rd Edition does not list SPD products rated less than 110 Vac or DC voltages.2UL 1449 4th Edition, UL 1283 7th Edition1.0 SetupVerify that system voltages do not exceed those listed in Section 1.5, Specifications. • All AC measurements should be completed with an RMS voltme-ter.• All DC measurements should be completed with a DC voltmeter.•DO NOT INSTALL FILTER IF MEASURED VOLTAGE EXCEEDSMAXIMUM OPERATING LIMITS.Choose location for filter installation so that maximum separation can be maintained between input leads, output leads and ground leads.1.1 Before InstallationREMOVE POWER FROM ELECTRICAL SYSTEM BEFORE MOUNTING FILTER.•Filter MUST be mounted within enclosure to assure personnel safety from exposed terminals.IMPORTANT:FILTER SHOULD BE LOCATED SO THAT THE SHORTEST POSSIBLE CONDUC-TOR LENGTH MAY BE USED.•Filter should be mounted to allow maximum separation between input and output wiring.•Filter contains no position-oriented components and can be mounted upside down or sideways.•Filter should be placed in electrical circuit so that it is the last device in the circuit before equipment to be protected.1.2 InstallationFILTER MUST BE CONNECTED TO ELECTRICAL SYSTEM WITH A CIRCUIT BREAKER:For AC Applications•1 – Single Pole / Single Throw 40A circuit breaker(s). The Interrupting Rating of the Circuit Breaker Shall Not Be LessThan the Available Fault Current. Circuit Breaker Ratings of 40A, 240V/415V, 10kA Min. AIC Rating.ote:N Pre-existing breaker(s) of the rated load size may be utilized if provi-sion for multi-conductor connections are made according to N.E.C. 110-14A.•If Neutral wire is to be utilized as L2/NEU then circuit breaker should be provided for that phase.For DC Applications•DC units to be installed after an overcurrent protective device that is rated not to exceed 100% of the current rating of the unit.•Form C contacts are rated at 0.5 Amps at 125 VAC or 1.0 Amps at 30 VDC. These connections are to be used for alarm hook up.T able 1. Relay state when energized.Catalog Part NumberNormally ClosedNormally OpenXXCFXXX30-RJ Open ClosedREMOVE POWER FROM ELECTRICAL SYSTEM BEFORE INSTALLING FILTER.Mechanically mount filter.•Mount filter using mounting flange holes or optional DIN bracket listed below.•Filter should be mounted to allow maximum separation between input and output wiring.•Filter contains no position oriented components and can be mount-ed upside down or sideways.•Filter should be placed in electrical circuit so that it is the last device in circuit before equipment to be protected.1.2.1 DIN Rail Kits Mounting bracket and foot adaptable to DIN Rail systems DIN EN 50022, DIN EN 50035 and DIN EN 50045 are available through Eaton Order Center and can be ordered separately.• Eaton Cat# DINRAILKIT-30ACF•Eaton Innovative Technology Cat# DINRAILKIT-30ITCF1.3 WiringNOTICEAN INSULATED GROUNDING CONDUCTOR THAT IS IDENTICAL IN SIZE AND INSULATION MATERIAL AND THICKNESS TO THE GROUNDED AND UNGROUNDED CIRCUIT SUPPLY CONDUCTORS, EXCEPT THAT IT IS GREEN WITH OR WITHOUT ONE OR MORE YELLOW STRIPES, IS TO BE INSTALLED AS PART OF THE CIRCUIT THAT SUPPLIES THE FILTER. SEE TABLE 250-122 OF THE NATIONAL ELECTRIC CODE (NEC) REGARDING THE APPROPRIATE SIZE OF THE GROUNDING CONDUCTOR.THE GROUNDING CONDUCTOR IS TO BE GROUNDED TO EARTH AT THE SERVICE EQUIPMENT OR OTHER ACCEPTABLE BUILDING EARTH GROUND SUCH AS THE BUILDING FRAME IN THE CASE OF HIGH-RISE STEEL FRAME STRUCTURE.ANY ATTACHMENT-PLUG RECEPTACLES IN THE VICINITY OF THE FILTER ARE TO BE GROUNDING TYPE, AND THE GROUNDING CONDUCTORS SERV-ING THESE RECEPTACLES ARE TO BE CONNECTED TO EARTH GROUND AT THE SERVICE EQUIPMENT OR OTHER ACCEPTABLE BUILDING EARTH GROUND SUCH AS THE BUILDING FRAME IN THE CASE OF HIGH-RISE STEEL FRAME STRUCTURE.PRESSURE TERMINAL OR PRESSURE SPLICING CONNECTORS AND SOL-DERING LUGS USED IN THE INSTALLATION OF THE FILTER SHALL BEIDENTIFIED AS BEING SUITABLE FOR THE MATERIAL OF THE CONDUCTORS. CONDUCTORS OF DISSIMILAR METALS SHALL NOT BE INTERMIXED IN A TERMINAL OR SPLICING CONNECTOR WHERE PHYSICAL CONTACT OCCURS BETWEEN DISSIMILAR CONDUCTORS UNLESS THE DEVICE IS IDENTIFIED FOR THE PURPOSE AND CONDITIONS OF USE.CONDUCTORS SHOULD BE TWISTED TOGETHER TO REDUCE IMPEDANCE FACTOR. EXCESSIVE WIRE LENGTH AND SHARP BENDS DEGRADE FILTER PERFORMANCE; THEREFORE, AVOID EXCESSIVE WIRE LENGTH AND SHARP BENDS.3Instruction Manual IM01005027E Rev. 4Effective October 2018Installation Instructions for EatonSurge Protective Device XXCFXXX30-RJEATON Table of Maximum Suggested Operating UnitsModel Number Power ProtectionData ProtectionLine to Neutral (MCOV)Line to Ground (MCOV)Neutral to Ground* (MCOV)Maximum All Modes (@60 Hz) Amps Pins Peak Voltage L-L, L-G Max. Continuous Operating Current (mA)Max. Data Rate (Mbps)XXCF12030-RJ 150150150401-4, 2-31341001XXCF23030-RJ27527527540*Note: If Neutral to Ground voltage is greater than 5 VAC then a problem may exist in electrical system. Filter may be installed; however, a qualified person should be consulted to correct problem.1.3.1 Series Wiring Applications•Connect incoming system GROUND wire to terminal labeledGND on unprotected end (labeled as LINE ).•Connect load side GROUND wire to terminal labeled GND on protected end (labeled as EQUIP ).For AC Applications•Connect incoming system NEUTRAL wire to terminal labeled L2/NEU on unprotected end (labeled as LINE ).•Connect load side NEUTRAL wire to terminal labeled as L2/NEU on protected end (labeled as EQUIP ).•Connect incoming system HOT wire to terminal labeled L1 on unprotected end (labeled as LINE ).•Connect load side HOT wire to terminal labeled as L1 on protected end (labeled as EQUIP ).For DC Applications•Connect incoming system NEGATIVE wire to terminal labeled L2/NEU on unprotected end (labeled as LINE ).•Connect incoming system POSITIVE wire to terminal labeled L1 on unprotected end (labeled as LINE ).1.3.2 Parallel Wiring ApplicationsIMPORTANT:FILTER SHOULD BE LOCATED SO THAT THE SHORTEST POSSIBLE CON-DUCTOR LENGTH MAY BE USED. CONDUCTORS SHOULD BE TWISTED TOGETHER TO REDUCE IMPEDANCE FACTOR. EXCESSIVE WIRE LENGTH AND SHARP BENDS DEGRADE FILTER PERFORMANCE; THEREFORE, AVOID EXCESSIVE WIRE LENGTH AND SHARP BENDS.•Connect incoming system GROUND wire to terminal labeled GND on unprotected end (labeled as LINE ).For AC Applications•Connect incoming system NEUTRAL wire to terminal labeled L2/NEU on unprotected end (labeled as LINE ).•Connect incoming system HOT wire to terminal labeled L1 on unprotected end (labeled as LINE ).For DC Applications•Connect incoming system NEGATIVE wire to terminal labeled L2/NEU on unprotected end (labeled as LINE ).•Connect incoming system POSITIVE wire to terminal labeled L1 on unprotected end (labeled as LINE ).ote:N For grounded or isolated control transformer secondary, DO NOT CONNECT Ground terminal on either LINE or EQUIP side.1.3.3 Dry Contact WiringConnect ALARM leads to Normally Open (N/O) or Normally Closed (N/C) terminals as required.1.3.4 Telephone Line ProtectionConnecting telephone line to protection.•Assemble RJ-14 modular plugs to LINE and EQUIP telephone cables.•Connect circuit as follows: Circuit 1 = Pins 2 and 3; Circuit 2 = Pins 1 and 4.• Insert modular plugs into LINE and EQUIP modular jacks.•Assure that telephone circuits are operational.ote:N For ungrounded or isolated control transformer secondary, DO NOT CONNECT Ground terminal on either LINE or EQUIP side.1.4 Apply PowerApply power to system. Indicator light(s) should glow and alarm contacts should move to normal state. If the light(s) does not glow, remove power and contact supplier.Instruction Manual IM01005027E Rev. 4 Effective October 2018Installation Instructions for Eaton Surge Protective Device XXCFXXX30-RJEatonElectrical Sector1000 Eaton Boulevard Cleveland, OH 44122United States877-ETN-CARE (877-386-2273) © 2018 EatonAll Rights ReservedPrinted in USAPublication No. IM01005027E / TBG000473 October 2018Eaton is a registered trademark.All other trademarks are property of their respective owners.Agency ApprovalsXXCFXXX30-RJ UL1449 4th Edition, UL1283 7th Edition Type 2 SPDTerminal Connections Wire clamping terminals, 10-18 AWG (UL), 10-22 AWG (CSA)Torque 12 in-lbOperating Temperature-40F(-40C) to +140F(+60C)System voltagesDC48 - 149 Vdc, 150 - 300 VdcAC100 - 127 Vac, 128 - 230 VacCircuit Breaker40A, 240V/415V, 10kA Min. AIC Rating(Eaton P/N:FAZ-C40/1-NA-SP)Amps*30Input Power Frequency50/60 HzWarranty 5 Years, 10 Years if registered on /spd RoHS Compliant Yes* Amp rating is for series connection only. Parallel connection is not current dependent.Purchaser’s right under the warranty shall consist solely of requiring Eaton to repair, or at Eaton’s sole discretion, replace, free of charge, F.O.B. factory, and defective items received at said factory or failure to give any advice or recommendations by Eaton shall not constitute any warranty by or impose any liability upon Eaton. The foregoing constitutes the sole and exclusive liability of Eaton AND IS IN LIEU OF ANY AND ALL OTHER WARRANTIES EXPRESSED, IMPLIED OR STATUTORY AS TO THE MERCHANTABILITY, FITNESS FOR PURPOSE SOLD, DESCRIPTION, QUALITY, PRODUCTIVENESS OR ANY OTHER MATTER.In no event shall Eaton be liable for special or consequential dam-ages or for delay in performance of the warranty.This warranty does not apply if the prod1uct has been misused, abused, altered, tampered with, or used in applications other than specified on the nameplate. At the end of the warranty period, Eaton shall be under no further warranty obliga-tion expressed or implied.The product covered by this warranty certificate can only be repaired or replaced by the factory. For help on troubleshooting the Critical Protection Product, or for warranty information, call 1-800-809-2772, Option 4, sub-option 2. Repair or replacement units will be returned collect. If Eaton finds the return to be a manufacturer’s defect, the product will be returned prepaid.。
SMD-30 30-XS伺服驱动器硬体操作说明书
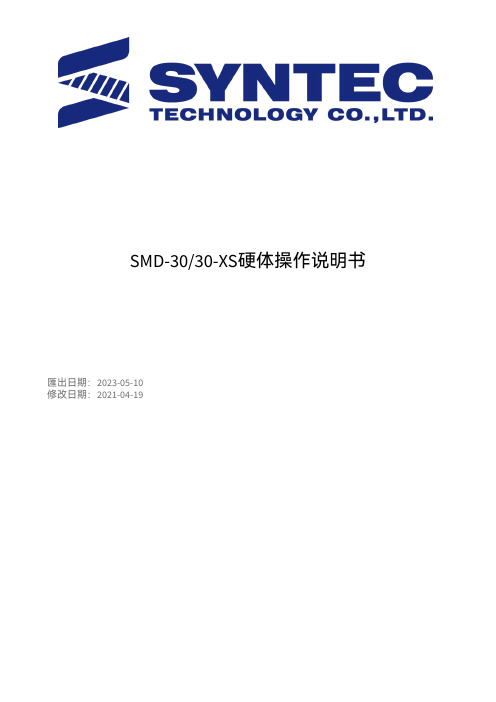
SMD-30/30-XS硬体操作说明书匯出日期:2023-05-10修改日期:2021-04-192023/05/10, 21:101 序言感谢您长期对本公司产品的使用与支持。
本公司伺服团队不断致力於各项产品的研发,期许本公司产品与服务能给使用者带来最大的效益。
新代高性能驱动器系列产品为本公司最新推出之伺服驱动器,本产品使用高品质之元件与材料,并经过严格测试,采用精密向量控制,具有高精确度、高稳定性、高效率之特性。
本使用说明内容包括驱动器的硬体规格、安装、配线与讯号,能提供给使用者最正确的指引与操作,为充分发挥产品应有的优异性能与维护人员及设备的安全,在使用前请详细阅读本使用手册,并且妥善保存,以备日後调校与保养时使用,若有任何疑虑,请与本公司联络,本公司专业人员将竭诚为您服务。
2 适用机型本单轴操作手册适用於新代SMD-30/30-XS 驱动器。
3 硬体规格3.1 说明每部驱动器在出厂前均经过详细品管检查与防撞包装处理,请使用者收到产品後应先检查外观有无撞击损伤,并将外盒与产品上之序号做比对是否一致,若有不符,请第一时间与本公司联络。
型号说明3.2 外观介绍SMD-30/30-XS驱动器功能模塊說明A M3串行通讯端口连接上位控制器与下一站驱动器,串行通讯100MbpsB Mini USB端口连接个人计算机C I/O讯号端口外接电池端口连接I/O设备(急停、警示灯…等)连接绝对型编码器供电用电池D STO讯号端口STO接口,2组安全输入,1组安全功能回授E编码器回授由上至下分别为第一与第二埠。
第一端口与第二端口为连接马达编码器。
F外供电源连接三相交流电200V~230V(RST)G控制电源若有安规需求,可将控制电源自L1,L2独立供电,连接单相交流电200~230V,输入电压规格需与RST相同。
H回生电阻两种接法,择一使用即可:1. 外部回生电阻连结至P、B22. 内建煞车为将B1、B2短路I电机电源供给连接马达侧提供马达电源(UVW)J记忆用电池提供绝对式编码器记忆功能所需之电源3.3 外形尺寸3.4 驱动器规格新代驱动器SMD-30/30-XS电源额定电源电压三相200~230V 50/60Hz电源电压容许-15 ~ +10%范围电源频率变动±5%范围输出额定输出电流7.6A x 2过电流能力150% 60s、200% 1s控制方式三相全波整流,SVPWM-VVVF控制回生电阻内建、可外接外接,请参考回生电阻选用章节回授编码器支援串列介面:Tamagawa、SYNNET、NIKON、FeeDAT选配扩充编码器模组:支援Tamagawa、SYNNET、NIKON、ABZ、串列、SSI、BiSS (不支援UVW省配线型编码器)(若要使用扩充编码器模组,请参考伺服10PX1/10PX3扩充模组操作文件) PC通讯介面MINI-USB控制器串列通Mechatrolink III讯介面输出入信号数位输入4点,可规划数位输出2点,可规划STO双通道安全扭矩停止开关(2I 1O)冷却方式风扇冷却环境温度0℃ ~ 55℃(若环境温度超过45℃以上时,请强制周边空气循环)、储存:-20~65℃ (非冻结)湿度最大90% RH (非结露)、储存:90%RH以下 (非结露)安装地点室内(避免阳光直射);无腐蚀性气体、易燃性气体、油雾或尘埃海拔1000公尺以下至海平面振动最大 5.9 m/s2重量 3.9 kg•••••••••••••••••••••4 搬运与安装4.1 搬运搬运时必须拿取驱动器的机身,不能只拿取上盖或其中部分,否则可能造成掉落的危险。
Bosch 30英寸自动开关门微波炉说明书

Notes: All height, width and depth dimensions are shown in inches. BSH reserves the absolute and unrestricted right to change product materials and specifications, at any time, without notice. Consult the product’s installation instructions for final dimensional data and other details prior to making cutout.
Enough room to fit a 4 qt. casserole dish.
Install under a counter or in a wall cabinet.
White touch control LCD matches Bosch wall ovens.
General Properties Cavity material Max. microwave power Capacity Cavity capacity Technical Details Watts Circuit breaker Volts Frequency Power cord length Plug type Dimensions & Weight Overall appliance dimensions (HxWxD) Required cutout size (HxWxD) Net weight
© BSH Home Appliances Corporation. All rights reserved. Bosch is a registered trademark of Robert Bosch GmbH.
萨尔洛大型30英寸水润走行背部喷头巡弋机手册说明书

CONGRATULATIONS on the purchase of your new Sarlo Mower. Your Sarlo is a powerful, all -purpose power mower, designed, engineered and tested to provide years of trouble -free operation. With proper handling and maintenance according to instructions in this manual, your Sarlo will deliver years of dependable service, maximum performance and safety. Be sure to read and understand all instructions before operation. Inspect mower components, mounting hardware and lubrication before each use. Our commitment is that every Sarlo will perform to 100% of its capabilities. We are confident your Sarlo will serve you well for many years to come. Respectfully,Tony Sarlo, PresidentSarlo Power Mowers, Inc. ♦ P.O. Box 1169 ♦ Fort Myers, Florida 33902 Sarlo ®BigMo ™ 30” Hydro Walk -BehindOWNER ’S MANUALIMPORTANT:Date Purchased: Mower Model #: Mower Serial #: Engine Model #: Engine Serial #: Dealer:OVERVIEW: (Fig. 1.)1.Discharge Chute2.Front Height of Cut Adjustment3.Deck Drive Belt Guard4.Operator Presence Control Bale5.Wheel Drive Control Bale6.Engine Throttle Control7.Mower Blade Engagement Control (PTO Switch)8.Ignition Switch9.Engine Pull Start10.Hour Meter11.Hydro Release Lever12.Rear Height of Cut AdjustmentKnow Before You Mow!Fig. 1 WARRANTY:SARLO POWER MOWERS, INC. hereby warrants to the original retail purchaser ALL NEW products of its own manufacture to be free from defects in material and workmanship for a period of 2 years from the date of the original purchase, subject to the following conditions:1.Engines are warranted by the respective engine manufacturer. Refer to the engine manufacturer’s warranty.2.Transmission parts are warranted by the manufacturer, not Sarlo Power Mowers, Inc.3.The warranty on belts, tires, throttle controls or any other item that is subject to normal wear is limited to 90 days.4.No warranty is extended to any equipment which has been misused, neglected or damaged by accident. Sarlo shall not be responsible fordamage in transit or handling by any common carrier, and under no circumstances, within or without the warranty period, will the company be liable for damage for loss, or damages resulting from delay or any consequential damage included but not limited to any cost or expense of providing substitute equipment or service during periods of malfunction or non-use.5.Sarlo Power Mowers will repair or replace, free of charge, any part or parts of the mower found upon examination by any Factory Author-ized Dealer or by the factory to be defective in materials and/or workmanship for the term of the warranty.6.The consumer is responsible for: (1) Normal maintenance such as greasing, gear case lubrication, minor adjustment and, (2) Transporta-tion of any Sarlo product to and from the place warranty work is performed.7.The Sarlo warranty WILL NOT APPLY to any product repaired or altered by anyone other than an Authorized Service Distributor orAuthorized Service Dealer.8.Sarlo reserves the right to incorporate any changes in design into its products without obligation to make changes on units previouslymanufactured.9.The warranty is valid only if the Factory Warranty Card is returned and registered.SAFETY:While Sarlo Power Mowers, Inc. is dedicated to building dependable, high-performance turf equipment, our number one concern is SAFETY.Users must carefully read this Owner’s Manual before operating the machine. Never permit anyone to operate the mower without a thorough understanding of the controls and operation of the equipment.The improper or irresponsible use of mowing equipment can cause serious injury and even death. Owners and users can prevent accidents or injuries to themselves, other people and/or to property. Use common sense.BEFORE YOU MOW:Wear appropriate clothing and sturdy shoes or boots. Do NOT operate the mower when barefoot or in open-toed sandals. Long hair, loose-fitting clothing and jewelry may get caught and tangled in moving parts, causing serious injury or death.Wear safety glasses and use hearing protection during operation. Do NOT listen to music or wear headphones while operating the mower.Inspect the area where the mower will be used. Evaluate the terrain, paying special attention to slopes, water hazards, drop-offs, ditches and embankments. Pay attention to hazards, obstructions, holes, ruts and bumps. Tall grass often hides dangerous obstacles. Look for items such as rocks, sticks, wire or toys. When struck by rapidly rotating blades, foreign objects become extremely dangerous projectiles, thrown from the mower at high speeds.NEVER carry passengers, transport equipment or carry fuel on the mower. Avoid mowing and shut the mower down when bystanders or pets are present. Always be aware of the direction of the mower’s discharge. Rapidly turning blades and thrown objects present a danger to operators, people and property nearby.Check the machine each time before starting. Inspect the tire pressure, fluid levels and the air filter. Service the engine according to the separate instructions supplied by the engine manufacturer. Always disconnect the spark plug wire when inspecting or servicing the mower. Look for any signs of damage or wear to the mower. Remove excess dirt or debris before operation. Inspect the cutting blades, making sure they are sharp and undamaged. Check for the presence and tightness of all bolts, nuts, pins and screws. Tighten or replace missing items. TEST the Safety Interlock System, also known as the Operator Presence Controls before each use to ensure that the mower’s safety features are functioning properly. KNOW BEFORE YOU MOW.FUELING:Always allow the engine to cool before fueling or refueling. Never operate a gas engine inside an enclosed area. Take special care when handling fuel. It is extremely flammable and the vapors are explosive.Use only approved fuel containers and do not smoke. Never refuel or drain the machine indoors or inside an enclosed trailer.Don’t open the gas cap or fill with theFig. 2 engine running.SAFETY ALERT SYMBOLS:Your Sarlo mower is equipped with Safety Alert Symbols designed to remind and warn operators of specific safety concerns.Familiarize yourself with the location and intent of each safety symbol and use extreme caution when in proximity to these areas of concern.You will find safety warnings and basic operating instruc-tions at the mower controls adjacent to the throttle and choke adjustment levers. (Fig. 2)Failure to follow these safety precautions and operating instructions may result in damage to the machine and/or serious injury to operators and others.Cutting deck edges are identified by DANGER symbols on each side of the deck. (Fig. 3) Keep hands, feet and any dangling or loose clothing away from the underside of the deck.The rotary cutting blades turn at approximately 18,500 fps; contact with the spinning blades will cause serious injury or death.NEVER operate the mower with the Side-Discharge Deflector Shield in the raised position without the grass catcher, or if the deflector has been damaged or removed. Debris may be thrown from the turning blades, causing serious injury or property damage. (Fig. 4)Only operate the mower with the Side-Discharge deflector or the grass catcher attachment mounted and securely in place.Fig. 3Fig. 4Fig. 5Fig. 7Fig. 9Fig. 6Additionally, caution must be used when operators are inproximity to the turning belt and pulley system that drivesthe cutting blade shaft. (Fig. 5) Fingers, hands, jewelryand loose -fitting clothing can catch in the rapidly moving machinery, causing injury or death.The BigMo is equipped with a hydrostatic transmission and an electric clutch blade brake. The Mower Blade Engagement Control is a PTO (Power Take -Off) switch. To enable the blades to turn for operation, compress the Operator Presence Control Bale and pull the Mower Blade Engagement Control knob up. To disengage blades, push the knob down or in. BigMo is alsoequipped with a 2-position Hydro Release Lever on the rear of the machine that puts the transmission in Neutral for easy transport. (Fig. 6)ALWAYS be certain that the PTO control is disengaged, the engine is off, the key is removed, and the spark plug wire is disconnected before inspecting or servicing the mower.This Made in the U.S.A. decal has nothing to do with operator safety. It ’s just something we ’re darn proud of.SAFETY INTERLOCK SYSTEM:For additional safety protection, your Sarlo mower isequipped with Operator Presence Controls, also known as a Safety Interlock System.The OPC system is designed to prevent the mower from running with blades turning when left unattended, creating unsafe conditions. The Wheel Drive Control Bale automat-ically returns to Neutral upon release. The Operator Presence Bale must be held continuously in order to engage the mower blades. (Fig. 8) If the Operator Presence Bale is released while the PTO or mower blades are engaged, the engine will stop running. If the PTO and mower blades are disengaged, the operator may release the mower and leave the operator ’s position with the engine running normally.Starting the mower requires that the Mower Blade Engagement Control be in the OFF (down) position and the Wheel DriveControl Bale must be in the RELEASED (Neutral) position. The Safety Interlock System should be checked for proper function before each use and any deficiency corrected before use. Disabling the Safety Interlock System will immediately void the warranty of your mower. GETTING STARTED:Follow the assembly instructions included with this Own-er ’s Manual to install the handlebars, and to connect the hydro control rod to your BigMo. Next, check oil and add fuel.Before operating the mower, become familiar with all of the mower and engine controls. You may refer to the photo and list of components in page 2 of this Owner ’s Manual. Understanding the function, location and operation of these controls is key to the safe and efficient operation of the equipment. OPERATION:Starting the Engine (Cold): Turn the key in the Ignition Switch clockwise to “Run ” and move the Engine Throttle Control Lever to its forward -most position (choke). (Fig.9)Fig. 8If the Mower Blade Engagement Control is in the“Off ” (down) position, it is not necessary to hold the Operator Presence Bale. The Wheel Drive Control Bale should be released (in neutral). Vigorously pull engine start handle until engine starts. After engine starts and stabilizes, move the Engine Throttle Control Lever back to the FAST position. If the engine is warm, there is no need to use the choke.Stopping the Engine: Turn off the mower deck and stop blade rotation by pushing DOWN on the Mower Blade Engagement Control. Move the Engine Throttle Control Lever back to the SLOW position. Release the Operator Presence Bale and turn the key in the Ignition Switch counter -clockwise to the OFF position. Remove the key.Emergency Stopping: In an emergency, immediately release all machine controls and carefully back away from the mower.Operating the Wheel Drive: The travel speed and direction (forward and reverse) of your mower iscontrolled by the Wheel Drive Control Bale. Your mower is also equipped with an automotive -style differential to make it exceptionally easy to steer and turn. The Wheel Drive Control Bale automatically returns to Neutral whenever it is released.To move the machine FORWARD, rest your fingers of both hands on the stationary Cross Bar and hook yourthumbs behind the Wheel Drive Control Bale. (Fig. 10)Gently press the bale forward and the mower will begin to move forward. Moving the bale further forward will increase the forward travel speed of the mower. When the Wheel Drive Control Bale is brought even with the stationary Cross Bar, the mower will travel at its maximum forward speed.To move the machine IN REVERSE, firmly place one hand on the stationary Cross Bar to steer and stabilize themower. Using your other hand, gently pull back on the WheelDrive Control Bale. Moving the bale further backward will increase the reverse travel speed of the mower.Release the Wheel Drive Control Bale to return to Neutral. Engaging the Mower Blades: After confirming that the area to mow is free of hazards and bystanders, move the Engine Throttle Control to FAST, pull the Operator Pres-ence Bale back to its engaged position and pull UP on the Mower Blade Engagement Control. (Fig. 11) If the mower blades are engaged, the Operator Presence Bale must be held continuously in the engaged position. If the Operator Presence Bale is released while the mower blades are engaged, the engine will stop running.Fig. 10Stopping the Mower Blades: In an emergency, the mower blades may be stopped by releasing the Operator Pres-ence Bale. Under normal con-ditions, push DOWN on the Mower Blade Engagement Control and release the Oper-ator Presence Bale. The en-gine will continue to run.Adjusting the Height of Cut: Your Sarlo mower offers sev-en cutting heights ranging from 1.5 to 4.5-inches, in half -inch increments. The height of cut can be changed quickly and easily without the need for tools. The mower utilizesadjusters at both the front and rear of the machine to ensure a flat and level cut. All adjusters should be placed in the same position.CAUTION! BEFORE ADJUSTING HEIGHT OF CUT, TURN OFF ENGINE AND REMOVE KEY!To adjust the FRONT height of cut, remove the circle cotter retaining rings from the tops of both Caster Fork shafts along with any loose spacers and set aside. With the front of the mower deck lifted and secure-ly supported with the wheels off the ground, slide the Caster Fork and Wheel assemblies downward until they disen-gage the support bearings in the frame. (Fig. 12)If the forks have not been serviced, lightly lubricating the shafts may help with this pro-cess. Determine your desired cutting height, bearing in mindthat the more spacers placed on the underside of the fork raises the cutting position. For example: Spacers Bottom Cutting Height 0 1.5” 1 2.0” 2 2.5” 3 3.0” 4 3.5” 5 4.0”64.5”To adjust the REAR height of cut, locate the two black knobs (one on each side of the rear of the machine) near the base of the handlebar support. Remove the knobs and any washers and set aside. (Fig. 13) Hold up lightly on the rear height of cut lift bar, and remove the carriage bolts from the adjusters on both sides of the machine.Fig. 11Fig. 12At this point, the Rear Axle Swing Arm of the mower is free to move up and down,allowing the rear height of cut position to be changed. The forward most hole in the adjuster is Position 6 (High). The rear most hole in theadjuster is Position 0 (Low).Pulling up or pushing down on the Height of Cut Lift Bar, pivot the adjuster until the holes are aligned at the position desired. Reinstall bolts with washers andsecurely tighten knobs. Thenumber position chosen on the rear adjusters shouldcorrespond with the number of spacers present on the underside of the front caster forks.For example, if using 4 spacers under the front caster forks, select position 4 on the rear adjusters.Disengaging the Transmission: The hydrostatic transmission of your Sarlo mower has a Release Lever on the back of the frame that allows it to be easily rolled without the engine running.To release the hydraulic pump, rotate the lever counter-clockwise to the “Free Wheel ” position. (Fig. 14) To return to normal self -propel function, rotate the lever back to the “Drive ” position. The Hydro Release Lever may also be operated using the foot.Adjusting the Hydro Control Rod: The speed of the mower ’s hydro drive may be altered with simple adjust-ments to the Hydro Control Rod.The mower is adjusted at the factory to run at its maxi-mum forward speed of 6 mph at “full grip.” Landscapers will likely appreciate the speed but it may be too fast for others, especially homeowners.To adjust/reduce the maximum (full grip) speed of the mower, shorten the length of the hydro control rod. When the rod is shortened, it changes the at -rest position of the hydro bale forward.When the operator then grips the bale, it stops -out (goes full grip) against the crossbar sooner than before, because there is less travel. This limits the amount ofstroke on the hydro pump , which in turn reduces the maximum speed of the machine.To change the length of the hydro control rod, loosen the jam nut at the end of the rod next to the ball joint. (Fig. 15)Since the rod is threaded RH/LH at the ends, the center tube can be turned, either taking up, or letting out the overall length of the rod.Small changes in the length of the rod produce a noticeable change in the forward ground speed of the mower. Owners should adjust speed to individualwalking preferences. MAINTENANCE:Engine: For all Engine Maintenance Requirements and Specifications, please refer to the manufacturer ’s separate engine manual provided with your mower.Transmission: The hydrostatic transmission in your mower was designed for extended use in a commercial environment. It is a sealed unit and requires no routine maintenance.General Lubrication: Your Sarlo mower has threegrease fittings; one on each of the front caster wheels and one on the mower blade spindle. (Fig. 16) The grease fitting for the blade spindle is accessed from the underside of the mowing deck.The caster wheels should each be greased every 100 hours of operation . The mower blade spindle should be greased every 40 hours of operation .Sarlo recommends the use of high -temperature/high -pressure “red ” lithium grease.Caster Fork Service: To make removal of the caster forks easier (for height of cut adjustments), it is recom-mended that operators occasionally remove the fork and wheel assemblies from their support bearings in the frame. Clean the shafts thoroughly of all accumulated dirt, rust and debris with fine sandpaper, then lubricate the shafts and bearing bores with a light lubricant such as WD -40 or PB -Blaster.Fig. 13 Fig. 14Fig. 15Fig. 16Drive Chain Lubrication: The wheel drive axle on your mower is driven by a roller chain that should be thorough-ly lubricated at regular intervals. Dirtier environments require that the chain be lubricated more frequently. Sarlo recommends a foaming molybdenum aerosol grease like the kind commonly used for motorcycle chains. The chain should be lubricated every 100 hours of operation. Sharpening the Cutting Blade: A sharp blade is the first step in achieving a beautiful cut.CAUTION! BEFORE SERVICING BLADES OR PER-FORMING ANY WORK UNDERNEATH THE CUTTING DECK, TURN OFF ENGINE AND REMOVE KEY!Tilt the mower back and support securely to access the underside of the mowing deck. This task is done more easily with the help of a friend. (Fig. 17)Block the blade from rotation and using a 15/16” box-end wrench or socket, remove the center retention bolt along with its special cupped locking washer and set aside.On a suitable grinder, reshape the original cutting edge and angle and smooth away any nicks or dings. Always seek to remove the minimal amount of material.Reinstall the blade to the spindle making certain that the airlift “wings” are to the upside and that the cupped side of the washer faces “up” against the blade. The blade reten-tion bolt should be tightened using a torque wrench with a minimum setting of 55 Ft. Lbs.Tire Air Pressure: For best traction and minimal track-ing, the rear tires of your mower should be inflated to 12-16 PSI. The front caster tires are urethane-filled (no-flats) and require no inflation maintenance.Belt Tensioning:The belt system is easy to access for cleaning and belt replacement. The belt has automatic spring tensioning and requires no adjustment. Never access the belt and pulley system unless the engine is turned off and the blades have stopped turning. Cleaning: Clean your Sarlo after each use. Let the unit cool, then wipe the grass and debris from mower and engine. Tip the mower back to clean underneath deck. Check the mower condition to prepare it for the next use. Check the blade and mounting hardware at frequent inter-vals for wear and tightness. If a pressure washer is used for cleaning, we strongly advise caution around hubs and bearings where pressurized water and contaminants could be forced inside, leading to premature failure. SERVICE, PARTS & ACCESSORIES:Your Sarlo mower has been built with the finest materials available to provide you with long life and enjoyable ser-vice. Please replace any and all worn items with genuine SARLO original equipment parts for safety and for best performance.Parts and accessories may be purchased through your local Sarlo dealer. In the event no dealer is available, parts can be ordered directly from our factory.Accessories: The BigMo Standard Side Discharge may be equipped with an optional grass catcher/bagger or a mulch kit and mulch blades.To place an order for genuine parts and accessories, or to locate the Sarlo dealer nearest you, please contact us at Sarlo Power Mowers, Inc.Sarlo Power Mowers, Inc.P.O. Box 1196Fort Myers, FL 33902Phone: 1-800-749-5296---SARLO BigMo TM Service Parts List:(Continued on Next Page)Fig. 17Date: Description:。
Festo EXCM-30 机械安装操作手册说明书

EXCM-30说明机械安装80292921306NH [8025435]平面门架EXCM-302Festo –GDCE-EXCM-30-ZH –1306NH –中文原版操作手册的译本GDCE-EXCM-30-ZH危险标识和避免危险的提示:警告可能造成重大伤亡的危险。
小心可能造成轻伤或严重财产损失的危险。
其它符号:注意财产损失或功能丧失。
其它文件中的建议、提示、参考。
必需或适用的附件。
环保使用说明。
文本标记:•可按任意顺序进行的工作。
1.应按规定顺序进行的工作。
–一般列举项。
EXCM-30Festo –GDCE-EXCM-30-ZH –1306NH –中文3目录–EXCM-301产品使用的安全和前提条件5................................................1.1安全5....................................................................1.1.1一般安全提示5....................................................1.1.2按规定使用5.....................................................1.2产品使用前提条件6........................................................1.2.1技术方面的前提条件6..............................................1.2.2专业人员的资质6..................................................1.2.3应用范围及认证6..................................................2运输和存放7..............................................................2.1存放条件7................................................................2.2检查供货范围7............................................................3概要8....................................................................3.1特征8....................................................................3.1.1马达的安装位置9..................................................3.2功能和应用10..............................................................3.3作用原理10................................................................3.4结构11....................................................................3.4.1马达EXCM-30-…-B …的安装位置11...................................3.4.2马达EXCM-30-…-T …的安装位置12...................................3.5马达13....................................................................3.5.1安装选项13.......................................................3.5.2马达派生型13.....................................................3.6接口14....................................................................3.6.1马达接口14.......................................................3.6.2控制器接口14.....................................................4装配和安装15..............................................................4.1安装准备15................................................................4.1.1安装位置15.......................................................4.1.2安装面要求15.....................................................4.1.3尺寸EXCM-30-…-B …16..............................................4.1.4尺寸EXCM-30-…-T …17..............................................4.1.5型材安装件的数量18................................................4.1.6型材安装件的安装孔19..............................................4.2平面门架的安装20..........................................................4.2.1型材安装件的使用20................................................4.2.2安装件21.........................................................EXCM-304Festo –GDCE-EXCM-30-ZH –1306NH –中文4.3附加元件和附件23..........................................................4.3.1附加元件的安装23..................................................4.3.2调整Y 轴的限位挡块24.............................................4.4马达连接25................................................................4.4.1安装原理25.......................................................4.4.2外购马达26.......................................................4.5安装26....................................................................4.5.1连接马达电缆和编码器电缆26........................................4.5.2传感器的安装26....................................................4.5.3调整马达电缆引线的位置27..........................................5调试29....................................................................6维护和保养30..............................................................6.1清洁30....................................................................6.2润滑31....................................................................7拆卸和维修32..............................................................7.1拆卸32....................................................................7.2维修32....................................................................7.3附件32....................................................................7.4报废处理32................................................................A 技术性附录33..............................................................A.1技术参数33................................................................A.1.1一般参数33.......................................................A.1.2认证33...........................................................A.1.3材料33...........................................................A.1.4产品重量34.......................................................A.1.5动态参数(EXCM-30-…-ST 或EXCM-30-…-SB)34.......................A.1.6工作和环境条件35..................................................1产品使用的安全和前提条件Festo –GDCE-EXCM-30-ZH –1306NH –中文51产品使用的安全和前提条件1.1安全1.1.1一般安全提示•请您遵守相应章节的一般安全提示。
HR30系列微型水抗性插座说明书

1Miniature Waterproof Plastic ConnectorsHR30 Series2004.6s Features 1. Small sizeShort in length when fully terminated and mated.2. Water and dust protectedIP67 protection rating: Complete protection against dust penetration and against water penetration when submerged 1 meter deep for half hour. Mated with corresponding connector or protective cap.3. Simple pull lock releaseBuilt-in lock/release mechanism securely locks mated connectors while allowing quick disconnection by simply pulling on the plug’s release collar. Molded-in grooves prevent hand slippage when pulled.The round configuration of the collar allows easy side-by-side panel mounting and will not snag on objects when the cable is pulled-out.4. Light weight, corrosion resistantGlass reinforced thermoplastic compounds and non-corrosive components are used in all assemblies.5. Contact protection and self- alignmentMultiple polarizing keys protect the contacts from miss-alignment or attempted insertion of the wrong connector,while assuring correct mating between the corresponding connectors.6. Visual alignment indicatorsPermanent alignment indicators in a contrasting color on all connectors aid in correct alignment and engagement.7. Built-in cable strain relief s ApplicationsTest and measuring equipment, portable devices,instrumentation, industrial devices, recreational equipment,I/O applications and other applications requiring use of lightweight, corrosion resistant quick mate/ release cableconnections.Push-pull- single action lockØ15.542.1Ø12.632.33 and 6 pos.10 and 12 pos.Mated dimensionsLock/release operationPolarized interfacePush-pull locking collar2s Product Specificationss Ordering informationHR 3 0 - 6 P A - 6 S C3s Plugsq Solder T ypeHR30-7P-12SC (Shown)Shown with terminated and installed contacts.Note: Crimp contacts are not included. Please order applicable contacts separately.HR30-6P-6S (Shown)4s Receptaclesq Solder TypeGasketBCADE(Thread)F(Hex nut)Lock washer123456HR30-6R-6P (Shown)q Through hole TypeHR30-8R-12SD (Shown)DCAB2Through hole post(0.2∞0.5)EF(Hex nut)GasketLock washerHR30-7R-12PC (Shown)Shown with terminated and installed contacts.Shown with terminated and installed contacts.Shown with terminated and installed contacts.Shown with terminated and installed contacts.Shown with terminated and installed contacts.Shown with terminated and installed contacts.5q Solder T ypeB(Fully tightened)AApplicablecable diameterHR30-7J-12PC (Shown)HR30-6J-6P (Shown)Shown with terminated and installed contacts.Note: Crimp contacts are not included. Please order applicable contacts separately.6q For Plugs11.4CØAØBØDØEHR30-6R-CHR30-6P-CNote : When using these caps, do not use the gasket that is normally supplied with the receptacle. The “B” diameter end of the receptacle cap will serve as the gasket.7Note :Use wire size AWG 26 to 30 with a jacket diameter of 1 mm max.s Crimp ContactsB Connecting Combinations0.82111.151.2A-A cross-sectionAAPlugsHR30-*P-**Caps for Plug HR30-*P-CReceptacles HR30-*R-**JacksHR30-*J-**Caps for Receptacle HR30-*R-CCable(Shown for reference only.)CapCapPanel(Shown for reference only.)Male contactFemale contactNote 1 :When selecting connectors, take into account the shell size, contact count and gender of the contacts.Note 2 :When using the protective caps for the receptacles, do not use the gaskets normally supplied with the receptacle. Protective caps mustbe fully inserted to assure specified IP67 water and dust protection.8B Applicable Fixturesq Solder termination fixtureNote :The back shell tightening collar is used to tighten the back shell to the specified torque.Refer to assembly procedures.q Tightening collar for back shellSolder termination fixture Back shell tightening collar Note: The back shell tightening collar is used to tighten the back shell to specified torque.Refer to assembly procedures.HR30-6P-6S-T01HR30-6R-6P-T01HR30-6P-T029s Applicable ToolsNotes 1.The contact configuration depicts a view from the wiring side.2. Mounting to the panel is accomplished by tightening the hexagonal nut from the rear side of the panel.Manual contact crimping tool HT-102/HR30-1 Automatic contact crimping machine CM-105 Contact extraction tool HR30-TP10B Assembly Procedures1112B General usage notesB Precautions1. Do NOT apply force in excess of 30N in the directions shown below.2. To maintain the water/dust protection performance and the cable clamp force, use a cable that is within the range of applicable cable diameter.3. Consult HRS representative when using different cables.Panel30 N max.30 N max.30 N max.The contents of this catalog are current as of date of publication. Contents are subject to change without notice for the purpose of improvements.5-23,OSAKI 5-CHOME,SHINAGAWA-KU,TOKYO 141-8587,JAPANPHONE: 81-3-3491-9741, FAX: 81-3-3493-2933®。
DUBOX 22-30AWG 手工终端连接工具说明书

DUBOX TMLOOSE PIECE HAND TOOLHand Tool Part NumberHT-2234 22 - 30 AWGFor termination Of Dubox TM 76357-x01LF TerminalsFCI MANUAL P/N 10123594-9090FCI USA, Inc. Manual P/N 10123594-9090 Issued: Date (12/20/2012) Page 1 of 9FCI USA, Inc.Manual P/N 10123594-9090 Issued: Date (12/20/2012) Page 2 of 9HT-2234 HAND TOOLFCI USA, Inc.Manual P/N 10123594-9090 Issued: Date (12/20/2012) Page 3 of 9Table of ContentsHAND TOOL ILLUSTRATION ........................................................................................................ 2 TABLE OF CONTENTS ................................................................................................................... 3 INTRODUCTION ............................................................................................................................. 4 SCOPE OF MANUAL ...................................................................................................................... 4 HAND TOOL FEATURES ............................................................................................................... 4 SPECIFICATIONS .......................................................................................................................... 5 CRIMP SPECIFICATIONS ............................................................................................................... 5 SAFETY PRECAUTIONS ................................................................................................................ 5 SETTING UP THE HAND TOOL ..................................................................................................... 5 ATTACHING THE TOOL HEAD ..................................................................................................... 5 CRIMPING PROCEEDURES .. (7)LOADING THE DUBOX TMTERMINAL ...................................................................................................... 7 CRIMPING PROCESS .................................................................................................................................... 8 TERMINAL HOLDER ADJUSTMENT ............................................................................................ 9 ALIGNMENT ..................................................................................................................................................... 9 ROUTINE MAINTENANCE ............................................................................................................. 9 PARTS REPLACEMENT .. (9)REFERENCE DRAWINGSTA-317REFERENCE DOCUMENTSFORM #E-3245 - -Customer Application Machine Warranty and Service Policy“Section I” Equipment owned by FCI USA LLC.FORM #E-3244 - -Customer Application Machine Warranty and Service Policy“Section II” Equipment purchased by the customer.FORM # E-3247- - FCI Electronics Address ListData herein have been verified and validated and are believed adequate for the intended use of the applicator. If the applicator or procedures are used for purposes over and above the capabilities specified herein, confirmation of their validity and suitability should be obtained; otherwise, FCI USA LLC does not guarantee results and assumes noobligation or liability. This publication is not a license to operate under, nor a recommendation to infringe upon, any process patents.FCI USA, Inc.Manual P/N 10123594-9090 Issued: Date (12/20/2012) Page 4 of 9INTRODUCTIONSCOPE OF MANUAL:This manual contains the information necessary to understand, install, operate and maintain the HT-2234 Dubox TM hand tools. This information is intended for the use by both the operator and service personnel. However, certain procedures within the manual should be performed by service personnel only. These procedures are identified by a warning instruction.Refer to the table of contents for a breakdown of each subject matter covered in each section.WARNINGS , CAUTIONS , and NOTES within the text of this manual are used to emphasize important and critical instructions.WARNING: An operating procedure, practice, etc. which if not carefully followed, could result in personal injury, or affect the operator’s health.CAUTION: An operating procedure, practice, etc. which, if not strictly observed, could result in damage of equipment.NOTE: An operating procedure, condition, etc. which it is essential to highlight.We recommend that the operators and service personnel responsible for maintenance of the FCI hand tools become thoroughly familiar with all aspects of the hand tool construction and operation. If operational or maintenance problems arise which are beyond the scope of this manual, contact your district service representative.HAND TOOL FEATURES:The HT-2234: Designed to terminate a single 22 – 30 awg pre-stripped discrete wire to a loose-piece 22 – 30 awg Dubox TM terminal, P/N 76357-x01LF. Two sets of crimp tooling are provided: One set is used to terminate 22 – 24 awg wires while the other is utilized to terminate 26 - 30 awg wires. Labeling above each set of crimp tooling indicates the appropriate wire range for that location.The HT-2234 hand tool used to ergonomically terminate 1 crimp per cycle without lengthy set-up times.∙ A terminal holder is provided with two cavities that correspond to the conductor size being terminated. ∙ Ratcheting handle ensures the complete crimping process has been fully completed and can be releasedif required.∙ Spring-loaded wire-stops are installed on each tooling cavity to assist with correct wire placement. ∙ The tool head can be easily separated from the handles for cleaning and tool maintenance.FCI USA, Inc.Manual P/N 10123594-9090 Issued: Date (12/20/2012) Page 5 of 9SPECIFICATIONS:Length … … … … … … … … … … … … … … … … … … … … … … … 197.5 mm ( 7.78”) Width … … … … … … … … … … … … … … … … … … … … … … … 65.2 mm ( 2.57”) Height … … … … … … … … … … … … … … … … … … … … … … … 145.5 mm (5.72”) Weight … … … … … … … … … … … … … … … … … … … … … … … 240 grams (.53 lbs)Color … … … … … … … … … … … … … … … … … … … … … … … .. Black with Blue HandlesCRIMP SPECIFICATIONS: Refer to FCI application specification “TA -317”SAFETY PRECAUTIONS:CAUTION: Verify that the hand tool is free of any debris, such as wire strands and that it manually operates correctly.CAUTION: This tool is designed to be operated by hand. Never install the HT-2234 hand tool in an air or pneumatic assisted device as damage to the tool and increased safety concerns will result.CAUTION: It is suggested to wear lightweight gloves when handling hand tools and terminals.SETTING UP THE HAND TOOL :ATTACHING THE TOOL HEAD:1. Push on both attachment pins from the front to disengage the locking feature of the pins, as shown inFigure 1 above. Turn the tool around and manually pull out on each of the pin heads to fully retract the pins until each pin locks into the retracted position, as shown in Figure 2 above.FCI USA, Inc.Manual P/N 10123594-9090 Issued: Date (12/20/2012) Page 6 of 92. Fully close the handles until the ratchet mechanism releases to allow opening of the handle assembly, asshown in Figure 3 above. Fully open the previously released handle assembly, as shown in Figure 4 above.3. Position the crimp tooling assembly and insert this assembly into the handle cavity, as shown in Figure5 above. Following the example provided in Figure6 above, align the mounting pin holes of the crimp tooling assembly with those of the attachment pins and fully insert each of the two (2) pins until each of the pins have passed through the crimp tooling assembly and handle, locking into the closed position. Following this step, the heads of each of the two (2) pins will once again be fully seated against the frame of the handle and locked into the closed position.Note: The crimp tooling assembly will install and function correctly when the head is reversed from the steps covered above.4. Without a terminal or wire in place, dry cycle the assembled tool to verify the tooling is free to fullyclose and open.FCI USA, Inc.Manual P/N 10123594-9090 Issued: Date (12/20/2012) Page 7 of 9CRIMPING PROCEEDURES:LOADING THE DUBOX TM TERMINAL:Figure 6 Figure 71. Verify that the crimp tool is open. If not, manually close the handle, as shown in Figure6 above, untilyou observe the last ‘click’. Release of the levers as illustrated in Figure 7 will allow the crimping die(s) to open automatically.2. Rotate the locator outward and down to its ‘load position’, as shown in Figure 8. Insert the Dubox TMcontact into the required cavity with the crimp features facing away from the tool (outward), as shown in Figure 9 above for 22 – 24 awg conductors. Rotate the locator upward until the locator comes to a hard stop and is held in place with the magnet feature, as show above in Figure 10.Note: This is only possible when the crimping die is in the fully open position.FCI USA, Inc.Manual P/N 10123594-9090 Issued: Date (12/20/2012) Page 8 of 9CRIMPING PROCESS:1. Close the hand tool till you observe t he first ‘click’ of the ratchet, as indicated in Figure 11 above. Using the correct wire gauge for the selected tooling cavity, insert the stripped wire into the slot of the appropriate wire stop until the insulation makes contact with the wire stop, as shown in Figure 12.Note: To determine the striping length, please refer to the application specification for the Dubox TM terminal, TA-317.2. While continuing to lightly hold the wire in position against the wire stop, close the levers as shown inFigure 13 until the levers are fully closed and the ratchet makes the final “click”, releasing the hand levers (handles) and die set to open as shown above in Figure 14.FCI USA, Inc.Manual P/N 10123594-9090 Issued: Date (12/20/2012) Page 9 of 93. Remove the terminated contact by pulling the terminated wire straight from the hand tool.TERMINAL HOLDER ADJUSTMENT(S):TERMINAL HOLDER ALIGNMENT(S): The terminal holder assembly is designed to locate a loose-piece Dubox TM terminal within the tooling to obtain a satisfactory termination form. When the terminal holder is fully closed, a magnet stops against a setscrew to position the terminal over the anvils and obtain the optimal crimp form. Slight adjustment of 1/16th of a turn either clockwise or counter-clockwise to the installed setscrew with a 1.5mm Allen wrench will alter the configuration of both the front and rear bellmouths.NOTE: Terminate a sample and review before making additional adjustment(s).ROUTINE MAINTENANCE1. Use of a small brush and vacuum are the preferred methods to keep the hand tool clean of debris and should be performed each shift, or sooner if necessary.2. Lightly lubricate the top tooling and handle assemblies on a monthly schedule with light weight oil.SERVICEFor service or technical help please call the FCI USA, Inc. service line at 1-800-843-6911.PARTS REPLACEMENTFor spare part orders please call your FCI USA LLC distributor. Additionally, call1-800-222-2194 and ask for CUSTOMER SERVICE. Please have part number(s) ready for the customer service person.。
RG30配置使用说明
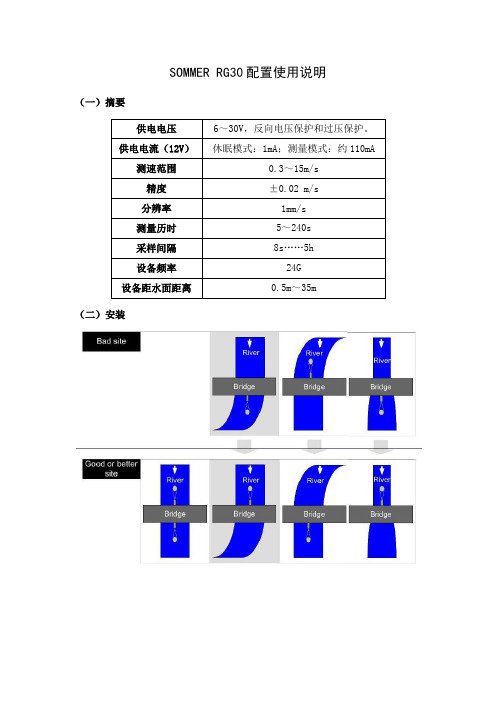
SOMMER RG30配置使用说明(一)摘要(二)安装注:被测水面直径最小应为投射点直径的两倍。
(三)设备配置超级终端:需要再次迅速键入另外一组“???”)。
注:参数确认“Enter”,中止“Esc”,子菜单关闭“X”,不区分字母大小写。
主菜单关闭后,传感器开始初始化进程“Start init!”。
初始化完成后显示“Init done!”。
A Measurement trigger1.interval(间隔触发);2.TRIG input(电平突变触发,0...0.6V低电平到2 (30V)高电平);3.SDI-12/RS485(指令触发)。
B Measurement Interval1,2,…18000:测量短时间隔内;0:连续测量输出,在任何情况下一个完整的测量周期要在下一个开始之前完成(连续且无任何打断)。
C Velocity1.Viewing directionDownstream:传感器顺流;Upstream:传感器逆流。
2.Possible flow directionsJust downstream:只计算一个方向的流速;Two(tide):计算两个方向的流速。
3.River inclination0…90度,大多数河流的角度可默认为0或1。
4.Pivot angle偏离主流向的摆动角,0…90度。
5.Maximum velocity0.001…99999.999。
最大流速(影响测量精度)。
6.River typeConsistent:动作缓慢的和同质水面,小带宽;Normal:缓慢的移动和异构的水面,中带宽度;Turbulent:快速移动和同质的水,表面宽的带宽;Bank area:快速移动和异构的水面,非常宽的带宽;Splash water:非濺水面,全带宽。
7.Measurement time5…240s,建议至少10s,注意时间太长耗电。
8.Measurement typeContinuous:测量快,能耗低;Sequenced:适用于流速变化快,测量历时较长。
- 1、下载文档前请自行甄别文档内容的完整性,平台不提供额外的编辑、内容补充、找答案等附加服务。
- 2、"仅部分预览"的文档,不可在线预览部分如存在完整性等问题,可反馈申请退款(可完整预览的文档不适用该条件!)。
- 3、如文档侵犯您的权益,请联系客服反馈,我们会尽快为您处理(人工客服工作时间:9:00-18:30)。
标志1. 本装置可使用于检查船舶或非检查船舶。
2. 本装置可使用于淡水冲洗或海水冲洗厕所污水。
3. 本装置柜体的压力试验为。
4. 本装置排放水指标符合IMO、MEPC159(55)的排放标准。
警告1. 本装置不得安装在爆炸性大气中,即非防爆型。
2. 本装置柜内壁涂环氧沥青漆,不得在柜上再焊接。
目录1 概述............................................................................. 错误!未定义书签。
2 组成和技术特性 ......................................................... 错误!未定义书签。
3 系统原理 ..................................................................... 错误!未定义书签。
4 主要功能单元的结构、作用及工作原理 .................. 错误!未定义书签。
5 运行方式 ..................................................................... 错误!未定义书签。
6 操作............................................................................. 错误!未定义书签。
7 安装............................................................................. 错误!未定义书签。
8 故障及排除 ................................................................. 错误!未定义书签。
1 概述用途本装置适用于处理来自船上人员厕所的生活污水,又称“黑水”,使之达到IMO、MEPC159(55)的排放标准,排至舷外。
工作条件1.2.1 环境条件1.2.1.1 工作环境温度:0℃~+50℃1.2.1.2 环境相对湿度:≤90%1.2.2 电源:AC440V、60Hz、3φ2 组成和技术特性组成本装置主要由如下主要部件组成主要技术参数⑴型号:WCMBR-30(U)型⑵使用人数:额定使用人数: 30人⑶处理能力:平均2310L/d⑷排放水质:TSS≯35mg/lBOD5≯25 mg/lCOD≯125 mg/l大肠菌≯100个/100mlPH=6~⑸排放水压力:⑹压缩空气(用户提供):~,h⑺膜冲洗水:清洁水,压力:~接口2.3.1 电源接口:AC440V 60Hz 3φ2.3.2 物理接口:(法兰标准:GB/T2506-89 )⑴污水入口DN150病房污水入口DN100⑵通气口DN65⑶冲洗水口DN40⑷溢流口DN40⑸膜冲洗水口DN25⑹压缩空气入口1/2”⑺应急排放口DN40⑻排放口DN323 系统原理(请参照系统图321NJUV-3-00C4cXT)本装置采用序批式-膜法处理原理处理有机污染物质,其处理流程为:污水入口→缓冲柜→序批柜→清水柜→膜组→消毒→排放→↑回流生活污水首先进入缓冲柜,以适应生化处理,同时该柜能容纳三倍的水力高峰负荷,当柜内液位达到中位时,粉碎泵启动,将污水转驳至置有软性填料的序批柜,进行接触氧化、生物处理,处理后的污水由流程泵转驳至清水柜内或直接排放至舷外,当转驳至清水柜时,若液位达到中位时,排放泵启动,将处理水泵入膜组,经膜组过滤后的排放水经紫外线消毒装置后排出舷外。
根据国际公约规定的规则海区可灵活使用序批式处理或膜法处理。
4 主要功能单元的结构、作用及工作原理粉碎泵粉碎泵用于将缓冲柜内的污水转驳至序批柜进行生物处理;或通过应急排放接口将污水直接排放至舷外。
粉碎泵为开式叶轮的离心泵,在叶轮及泵的进口处带有刀刃,粉碎污水中的污物,叶轮背面带有短叶,以平衡泵产生的轴向力。
泵的轴封采用机械密封。
泵体间的连接用1:5锥度交合用4只螺柱紧固,以便在进行泵的检拆时能方便地将泵卸下,而人体不易接触到污物,连接片采用O形橡胶密封圈密封。
排放泵排放泵为离心泵,兼作流程泵,其有二个功能:⑴将经序批处理过的污水转驳至清水柜内或直接排放至舷外;⑵将清水柜内处理水泵入膜组进行过滤处理。
气泵气泵用于向缓冲柜、序批柜内提供充足的氧气,以利于活性污泥的繁殖。
气泵由主机、气包、底座、润滑、冷却等部件组成,主机部件有泵体、转子、滑片等主要零件组成。
转子回转中心与缸体成偏心配置,转子有四条槽,槽内装有自润滑滑片,当电机通过联轴器带动转子转动时,滑片在离心力的作用甩出与缸壁接触,形成四个气室,每个室的容积随着转子的转动而改变,依次使气室内产生真空,中途经补气,然后压缩到额定压力后排出不含油的压缩空气。
紫外线消毒装置紫外线消毒装置用于对排放水进行消毒。
紫外线消毒装置主要包括紫外线控制装置、紫外线灯管等。
膜组膜组由中空纤维超滤膜组成,用于过滤清水柜内的排放水。
加药泵定量泵用于将清洗液泵入膜组,对膜组进行清洗。
该泵的泵头由几个聚四氟乙烯滚轮组成,由一个电动机通过减速齿轮驱动,液体由加药泵从塑料桶通过一根硅胶管由滚轮挤压到膜组内,在泵运转时,始终有一个滚轮压住尼龙管,保证液体不返回到塑料桶内。
电气控制箱警示:本装置操作人员必须首先熟读电气控制使用说明书,在没有弄懂操作程序前不得合上电源和任意按动电气控制箱上的按钮和拨弄《转换开关》!警告:电气控制箱为强电控制设备,操作不当会引起人身伤害甚至生命危险!必须由专业人员才可接触电气控制系统。
电控箱控制本装置各运动部件的启、停,开、关,运行由PLC程序控制。
4.7.1 粉碎泵粉碎泵由控制箱《手动-停止-自动》转换开关控制,转向“手动”时,粉碎泵连续运行,转向“自动”时,粉碎泵受缓冲柜内液位控制,柜内液位达到中位时,粉碎泵启动,直至低位时停止。
4.7.2 排放泵排放泵由控制箱《手动-停止-自动》转换开关控制,转向“手动”时,排放泵连续运行,转向“自动”时,排放泵受序批柜或清水柜内液位控制,当序批柜内液位至高液位时,排放泵启动,同时电动阀DV1打开、DV3旁通打开,直至低位时停止;当清水柜内液位至中液位时,排放泵启动,同时电动阀DV2打开、DV3直通打开,直至低位时停止。
4.7.3 气泵气泵由控制箱《手动-停止-自动》转换开关控制,转向“手动”时,气泵连续运行;转向“自动”时,受PLC程序控制启、停。
4.7.4 紫外线消毒装置紫外线消毒装置由控制箱《手动-停止-自动》转换开关控制,转向“手动”时,连续运行;转向“自动”时,当排放泵启动,将清水柜内处理水泵入膜组进行过滤处理时,消毒装置启动;排放泵停止时,紫外线消毒装置停止运行。
4.7.5 加药泵定量泵用于将3%NaOH溶液或者是次氯酸钠溶液泵入膜组,对膜组进行清洗。
加药泵由控制箱《加药泵启动》、《加药泵停止》按钮控制,按下《启动》按钮时,加药泵连续运行;按下《停止》按钮时,加药泵停止运行。
5 运行方式培菌警示:本装置在启动正常运行前,必须进行培菌程序。
膜不能在原污水状态下运行。
将《运行模式》转换开关转向“培菌”程序,打开原污水入口阀,污水进入缓冲柜,当F1水位指示灯亮时,说明已有污水进入,当F2水位指示灯亮时,表明缓冲柜水位已上升到F2点,此时粉碎泵P1自动启动,将污水转驳至序批柜内,缓冲柜水位因P1启动运行而下降,至F1时,P1自动停。
再进入原污水,缓冲柜因水位升到F2而又重复上述动作,直至序批柜液位R2指示灯亮,缓冲柜液位F2指示灯亮,关闭污水入口阀。
启动气泵PQ1、PQ2,P1、PQ1自动进行“间歇运行”《开20min,停20min》,PQ2连续运行。
运行2天后,执行一次《公海排放》程序,排去少量上清液后,如上所述加入新鲜污水。
可以从取样口取出序批的污水,用100ml量筒观察活性污泥的培养状态如何,静止沉淀30分钟后,如达到1/3,则说明“培菌”工作完成。
一般生的原污水培菌需要2-3周时间,如能加入“种泥”菌种可缩短培养时间。
装置经过一段较长时间的停歇,也可用“培菌”程序,因为柜内已有休眠的活性污泥,培菌过程仅需1-2天。
培菌过程中膜组不参加工作。
正常运行在“培菌”程序完成后,可将程序转向《正常运行》,打开污水入口阀,当缓冲柜内液位达F2时,P1泵启动,将污水转驳至序批柜内,直至液位至R2时停止(此过程为“进水期”),进水期PQ1、PQ2连续运转;进水期完成后,进入“曝气期”,PQ1、PQ2连续运转,上述两过程共计45分钟;45分钟后,进入“静止期”,PQ1、PQ2停止,;30分钟后,DV1打开,P2泵启动,以下有两种选择:5.2.1 膜法处理:手动关闭阀VQ7,打开VQ5、VQ6,将转换开关转向《膜法处理》,DV3旁通打开,P2将处理水泵入清水柜,直至液位至R1或L3时停止,当清水柜内液位超过L2时,VS2、DV2、DV3直通打开,1分钟后紫外线、P2泵启动,手动调节V1、V3,控制出水量和浓缩液回流量(一般预先都调定为50%),排放水经膜组过滤后经消毒后排放至舷外,直至液位至L1时,P2、紫外线消毒装置停止,VS2、DV2、DV3 关闭,延时1分钟后,VS1打开,冲刷膜,10秒后关闭,重复一次。
也可定期手动打开冲洗水阀V2,V4,关闭VQ5、V3、V1,用清水对膜进行清洗,从视流管中看到水变清为止。
5.2.2 公海排放:当船航行于公海或非规则海区时,可关闭阀VQ5、VQ6,打开阀VQ7,将转换开关转向《公海排放》,DV3直通打开,可将经过曝气、沉淀后的上清液直接排放至舷外,此方式可延长膜的使用寿命。
在正常运行过程中,如果F1、R1脱水4小时以上,装置将自动进入休眠状态,PQ开20分钟,停20分钟,直至污水进入,休眠才自动中止。
应急排放当遇到紧急情况,装置不能正常运行时,可手动关闭VQ2、VQ4,打开VQ1,VQ3,将粉碎排放泵转换开关转向“自动”,当液位至F2时启动,F1时停止,缓冲柜内的污水经粉碎后直接排放至舷外。
化学清洗膜组参加装置正常运行3个月以后或当排放流量降低时,需对其进行一次化学清洗。
关闭阀V1、V2、V3、V4、VQ5,打开加药考克C1、C2,启动加药泵,使药闭式循环10分钟后,停止加药泵,关闭C1、C2。
3~8小时浸泡完成,手动打开阀VQ7,VQ5、V2,关闭阀V1、V4、VQ6,将残余液排至舷外,5分钟后关闭阀V2。
化学药剂采用二种溶液:一是采用3%的NaOH溶液,二是采用次氯酸钠溶液。
5.4.1 3%NaOH溶液配制程序:本装置配有10升容量的塑料带盖方桶,先加满清水,然后加入0.75kg100%的NaOH 固体粉剂,用木棒搅匀,让其静放2小时以上,盖上盖子,连接上加药泵的硅胶管即可使用。