柴油加氢技术
生物柴油加氢工艺流程
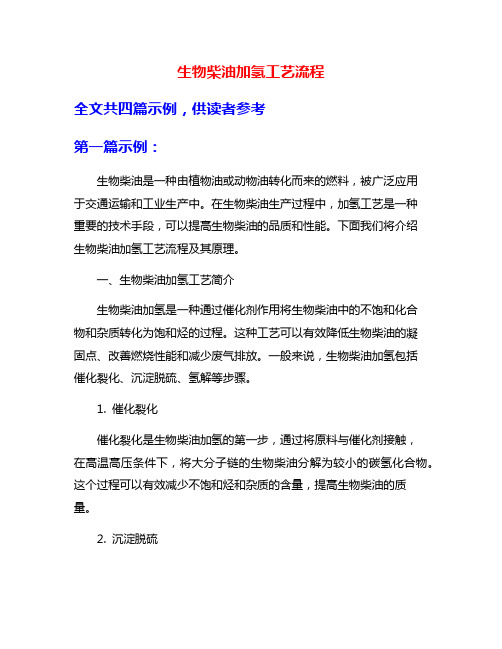
生物柴油加氢工艺流程全文共四篇示例,供读者参考第一篇示例:生物柴油是一种由植物油或动物油转化而来的燃料,被广泛应用于交通运输和工业生产中。
在生物柴油生产过程中,加氢工艺是一种重要的技术手段,可以提高生物柴油的品质和性能。
下面我们将介绍生物柴油加氢工艺流程及其原理。
一、生物柴油加氢工艺简介生物柴油加氢是一种通过催化剂作用将生物柴油中的不饱和化合物和杂质转化为饱和烃的过程。
这种工艺可以有效降低生物柴油的凝固点、改善燃烧性能和减少废气排放。
一般来说,生物柴油加氢包括催化裂化、沉淀脱硫、氢解等步骤。
1. 催化裂化催化裂化是生物柴油加氢的第一步,通过将原料与催化剂接触,在高温高压条件下,将大分子链的生物柴油分解为较小的碳氢化合物。
这个过程可以有效减少不饱和烃和杂质的含量,提高生物柴油的质量。
2. 沉淀脱硫沉淀脱硫是生物柴油加氢工艺的第二步,用于去除生物柴油中的硫化物。
硫化物是生物柴油中的一种有害物质,容易损坏催化剂和污染环境。
通过将生物柴油与脱硫剂反应,可以将硫化物转化为不溶于油中的硫酸盐或硫代硼酸盐,然后通过沉淀分离的方式将其去除。
3. 氢解1. 提高生物柴油的品质和性能,减少废气排放。
2. 可以降低生物柴油的凝固点,提高其在低温条件下的流动性。
3. 减少生物柴油的不饱和烃和杂质含量,减少燃料的积炭和系统堵塞。
4. 延长动力系统和催化转化器的使用寿命,降低维护成本。
生物柴油加氢工艺是一种有效的技术手段,可以提高生物柴油的品质和性能,减少废气排放,符合现代工业生产和环境保护的要求。
未来随着生物能源技术的不断发展,生物柴油加氢工艺将在全球范围内得到更广泛的应用。
第二篇示例:生物柴油是一种由植物油或动物油经过一系列化学反应加工而成的燃料,与传统石油燃料相比,生物柴油具有低碳排放、可再生资源等优点,因此备受关注。
而加氢工艺是生物柴油生产过程中的关键环节,通过加氢反应可以改善生物柴油的质量,提高其燃烧效率,减少有害物质排放。
催化柴油加氢转化技术特点及开工过程注意事项

催化柴油加氢转化技术特点及开工过程注意事项催化柴油加氢转化技术是一种将低质量柴油转化为高质量柴油的工艺。
该技术通过将柴油与氢气在催化剂的存在下进行反应,使其中的硫、氮、氧等杂质得到去除,得到质量更好的柴油产品。
下面我们将详细介绍催化柴油加氢转化技术的特点及开工过程的注意事项。
一、催化柴油加氢转化技术特点1. 增加柴油的Cetane数:催化柴油加氢转化技术中,催化剂具有一定的选择性,能够使低Cetane数的柴油中的芳烃分子经过加氢反应得到消除或减小,从而提高柴油的Cetane数,提高柴油的燃烧性能和起动性能。
2.去除硫化物:柴油中的硫化物是污染大气环境和腐蚀发动机的主要物质之一、催化柴油加氢转化技术中的催化剂能够催化低质杂硫化物的加氢反应,将其转化为硫化氢气体,从而实现柴油中硫的脱除。
3.去除氮化物:氮化物主要存在于柴油中的芳香族化合物中,对空气质量有一定影响。
催化柴油加氢转化技术通过氢化反应,将芳香族化合物中的氮化物转化为氨和氨基化合物,从而实现氮化物的脱除。
4.增加柴油的氧化稳定性:通过催化柴油加氢转化技术使柴油中的芳香族化合物被氢化为饱和链烷烃,从而减少了柴油中的不饱和度,使柴油的氧化稳定性得到了显著提高。
1.催化剂的选择:选择合适的催化剂是催化柴油加氢转化技术成功开工的关键。
催化剂应具有较高的活性和稳定性,能够催化低质杂质的加氢反应,同时能够抵抗催化剂毒剂的腐蚀。
2.反应温度控制:催化柴油加氢转化反应是一个放热反应,反应温度的控制是非常重要的。
过高的反应温度可能导致催化剂失活,同时也会增加单位时间内的柴油耗量。
因此,需要在催化剂的稳定工作温度范围内进行反应温度的控制。
3.氢油比的控制:氢在催化柴油加氢转化过程中起到氢化和脱硫的作用,氢油比的控制对反应效果有直接影响。
过低的氢油比会导致催化剂表面缺氢现象,从而降低了柴油质量的提高效果;而过高的氢油比会增加成本,影响经济性。
因此,需要合理控制氢油比。
柴油加氢可行性研究报告

柴油加氢可行性研究报告一、前言柴油是一种广泛应用于交通运输和工业生产的燃料,然而,由于其高含硫量和产生的污染物排放,柴油燃料已经成为环境保护的焦点。
在此背景下,柴油加氢技术被认为是一种有效的环保和能源节约方式。
因此,本报告将探讨柴油加氢技术的可行性,包括技术原理、应用前景以及经济和社会影响等方面。
二、技术原理柴油加氢技术是一种利用氢气将柴油分子结构进行变换,去除其中的硫和氮等杂质,从而提高柴油的质量和燃烧效率的技术。
该技术的主要原理是利用氢气与柴油中的硫、氮等杂质发生化学反应,将其转化为相对较为稳定的物质,从而降低污染物排放。
柴油加氢技术的关键是加氢反应器,其主要由催化剂、反应器筒体、加热器、冷却器、压缩器等部件组成。
当柴油燃料与氢气一起进入反应器内,经过催化剂的作用,原始的含硫和氮的柴油会经过一系列的化学反应,最终得到低硫和低氮的高质量柴油。
三、应用前景1.环保效益:柴油加氢技术可以明显降低柴油燃料中的硫和氮含量,从而有效减少柴油燃烧所产生的二氧化硫、氮氧化物等大气污染物排放。
2.节能效益:由于加氢后的柴油具有更高的燃烧效率,因此可以减少燃油消耗,从而节约能源。
3.车辆维护成本降低:低硫和低氮的柴油燃料可以减少车辆排放系统的腐蚀和损坏,从而降低车辆维护成本。
4.社会影响:柴油加氢技术的应用还可以提高柴油的利用效率,缓解能源供需紧张局面,减少化石能源对环境的影响。
四、经济影响尽管柴油加氢技术具有明显的环保和能源节约效益,但其推广应用仍面临一定的经济压力。
柴油加氢技术需要投入大量的资金来建设加氢装置,并且每吨柴油加氢处理的成本也相对较高。
此外,柴油加氢技术涉及到复杂的反应过程和催化剂的研发,需要进行大量的科研投入。
因此,从经济角度考虑,柴油加氢技术的推广应用需要政府和企业的支持和鼓励。
从长远来看,柴油加氢技术的投资可以带来可观的回报。
随着环保意识的不断增强,柴油加氢技术的应用前景广阔。
在未来,随着柴油加氢技术的成熟,其成本也将逐步降低,从而增加其在柴油燃料生产领域的竞争力。
柴油加氢技术总结_锅炉技术总结范文

柴油加氢技术总结_锅炉技术总结范文柴油加氢技术是一种新型的能源利用技术,能够有效地降低柴油对环境的污染程度,提高燃料利用效率,具有广泛的应用前景。
经过多年技术研究和实践,目前柴油加氢技术已成熟,以下是柴油加氢技术的总结:一、柴油加氢技术概述柴油加氢技术是一种利用氢气将柴油分子中的碳氢键断裂,再与氢原子结合生成新的高氢化合物的过程。
该技术能够改善柴油的性能和组成,提高柴油的热值和燃烧效率,降低柴油的凝固点和燃烧产物中的污染物含量。
柴油加氢技术是一种改变柴油分子结构的过程,其原理是通过加氢反应将长链烃分子裂解成更短的链烃分子,降低分子量,增加分子中的氢原子含量,使其更易于燃烧。
1.改善燃油性能2.提高燃料利用效率通过柴油加氢技术,可以降低柴油的凝固点,增加柴油的可流动性,使柴油更易于燃烧,从而提高燃料利用效率。
3.降低柴油对环境的污染柴油加氢技术能够降低柴油对环境的污染程度,使其燃烧产生的污染物含量更少,具有更好的环保性能。
目前,柴油加氢技术已经得到了广泛应用。
在燃油加氢方面,一般采用常压或低压加氢工艺,通常使用的反应器有固定床反应器和流化床反应器等。
五、柴油加氢技术的优势和不足1.柴油加氢技术的优势主要体现在其能够有效地降低燃料的污染程度,提高燃料利用效率,同时也可以降低柴油的凝固点。
2.柴油加氢技术的不足主要在于其投资成本较高,而且加氢反应条件要求严格,操作难度较大。
未来柴油加氢技术的发展趋势主要包括以下几个方面:1.技术研究不断深入随着柴油加氢技术的应用越来越广泛,未来将有更多的研究机构和企业投入到该领域的技术研究中,是技术不断深入发展。
2.技术应用更加广泛未来柴油加氢技术将会在更多的领域得到应用,并且在不断发展的新能源领域中,具有较大的发展前景。
3.推广普及加氢技术未来柴油加氢技术将会得到更多的推广和普及,更多的汽车需求将使用加氢技术的柴油燃料,从而提高柴油燃油的效率和环保性能。
综上所述,柴油加氢技术是一种具有较大发展前景的新兴能源技术,尤其对于环保和低碳经济有着十分重要的作用,未来该技术将会得到更广泛的应用和推广。
分析柴油加氢改质降凝技术的开发及工业应用

分析柴油加氢改质降凝技术的开发及工业应用随着工业化进程的加快,柴油作为重要的燃料已经在各个领域得到广泛的应用。
柴油在低温环境下会出现结晶、凝固等问题,给燃料的使用带来了一定的困扰。
为了解决这一问题,加氢改质降凝技术应运而生。
本文将对柴油加氢改质降凝技术的开发过程以及工业应用进行深入分析。
一、柴油加氢改质降凝技术的开发过程1. 技术背景柴油凝固问题一直是燃料行业的难题之一。
在冬季寒冷地区,低温下柴油会出现结晶、凝固,导致燃料流动性下降,影响燃料喷射系统正常工作,甚至造成引擎无法启动的情况。
解决柴油凝固问题迫在眉睫。
2. 技术原理加氢改质降凝技术是通过在催化剂的作用下,将柴油中的饱和烃和不饱和烃进行加氢反应,使其分子结构发生改变,进而降低柴油的凝固点。
该技术能够有效降低柴油的凝固温度,改善柴油的低温流动性,使其适应更加严苛的低温环境。
3. 技术研发柴油加氢改质降凝技术的研发需要从催化剂的筛选、反应工艺的优化、产品性能的测试等多个方面展开。
需要选择适合的催化剂,以提高反应效率和选择性;需要对反应条件进行优化,包括温度、压力、氢气流量等参数的调节;通过实验室和工业试验来验证改质效果,并逐步进行技术改进,达到工业化生产的要求。
4. 技术突破经过多年的研发和实践,柴油加氢改质降凝技术取得了重要的突破。
目前,已经可以生产出具有良好低温流动性的改质柴油,并在不同地区进行了工业应用。
还不断改进技术,提高产品的性能,降低生产成本,推动了技术的进一步发展。
1. 城市公交城市公交车是柴油车的主要应用领域之一。
在寒冷的冬季,柴油车辆的启动和行驶会受到严重的影响,加氢改质降凝技术的应用能够有效提高柴油车辆在低温下的可靠性和稳定性,保障公共交通的正常运营。
2. 铁路运输铁路运输是柴油机车的重要应用场景,铁路线路通常会穿越不同的气候区域,加氢改质降凝技术可以有效应对温度变化带来的燃料凝固问题,保证铁路运输的安全和稳定。
3. 农业机械农业生产对柴油机械的依赖性很高,而且农村地区通常气温较低,柴油加氢改质降凝技术能够解决农业机械在低温条件下的启动和工作问题,保障农业生产的顺利进行。
柴油加氢工艺流程
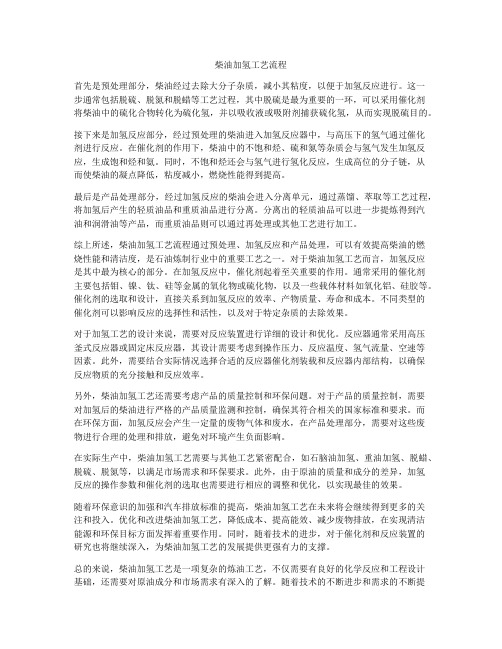
柴油加氢工艺流程首先是预处理部分,柴油经过去除大分子杂质,减小其粘度,以便于加氢反应进行。
这一步通常包括脱硫、脱氮和脱蜡等工艺过程,其中脱硫是最为重要的一环,可以采用催化剂将柴油中的硫化合物转化为硫化氢,并以吸收液或吸附剂捕获硫化氢,从而实现脱硫目的。
接下来是加氢反应部分,经过预处理的柴油进入加氢反应器中,与高压下的氢气通过催化剂进行反应。
在催化剂的作用下,柴油中的不饱和烃、硫和氮等杂质会与氢气发生加氢反应,生成饱和烃和氨。
同时,不饱和烃还会与氢气进行氢化反应,生成高位的分子链,从而使柴油的凝点降低,粘度减小,燃烧性能得到提高。
最后是产品处理部分,经过加氢反应的柴油会进入分离单元,通过蒸馏、萃取等工艺过程,将加氢后产生的轻质油品和重质油品进行分离。
分离出的轻质油品可以进一步提炼得到汽油和润滑油等产品,而重质油品则可以通过再处理或其他工艺进行加工。
综上所述,柴油加氢工艺流程通过预处理、加氢反应和产品处理,可以有效提高柴油的燃烧性能和清洁度,是石油炼制行业中的重要工艺之一。
对于柴油加氢工艺而言,加氢反应是其中最为核心的部分。
在加氢反应中,催化剂起着至关重要的作用。
通常采用的催化剂主要包括钼、镍、钛、硅等金属的氧化物或硫化物,以及一些载体材料如氧化铝、硅胶等。
催化剂的选取和设计,直接关系到加氢反应的效率、产物质量、寿命和成本。
不同类型的催化剂可以影响反应的选择性和活性,以及对于特定杂质的去除效果。
对于加氢工艺的设计来说,需要对反应装置进行详细的设计和优化。
反应器通常采用高压釜式反应器或固定床反应器,其设计需要考虑到操作压力、反应温度、氢气流量、空速等因素。
此外,需要结合实际情况选择合适的反应器催化剂装载和反应器内部结构,以确保反应物质的充分接触和反应效率。
另外,柴油加氢工艺还需要考虑产品的质量控制和环保问题。
对于产品的质量控制,需要对加氢后的柴油进行严格的产品质量监测和控制,确保其符合相关的国家标准和要求。
柴油加氢工艺及催化剂
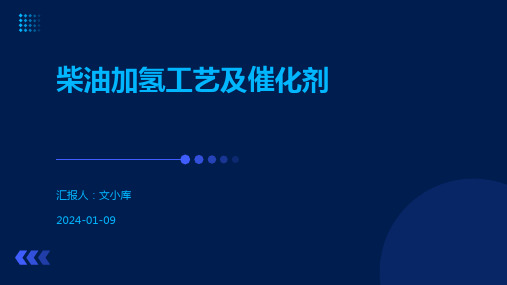
再生
催化剂在加氢反应过程中会发生失活,研究有效的再生 方法,如化学再生、热再生等,以恢复催化剂的活性, 延长其使用寿命。
回收利用
催化剂经再生后仍可继续使用,应研究催化剂的回收利 用技术,实现资源的循环利用,降低生产成本并减少环 境污染。
THANKS
谢谢您的观看
它通过在高温高压条件下,利用氢气与柴油中的硫、氮等杂质以及烃类化合物的 反应,将其转化为硫化氢、氨气和水蒸气等气体,从而脱除杂质并改善柴油的燃 烧性能。
柴油加氢工艺的原理
柴油加氢的基本原理是加氢反应,即将氢气与柴油中的硫、 氮等杂质以及烃类化合物进行反应,生成硫化氢、氨气和水 蒸气等气体,同时将烃类化合物中的不饱和烃转化为饱和烃 ,提高油品的稳定性。
探索新型制备方法
要点一
传统制备方法
采用沉淀法、溶胶-凝胶法、微乳液法等传统方法制备柴油 加氢催化剂,这些方法虽然成熟,但存在成本高、周期长 等缺点。
要点二
新型制备方法
研究新型的制备方法,如模板法、自组装法、离子液体法 等,以简化制备过程、降低成本、提高催化剂性能和缩短 研发周期。
加强催化剂的再生与回收利用
VS
浸渍法是一种常用的催化剂制备方法 ,通过将载体浸入含有活性组分的溶 液中,再经洗涤、干燥和煅烧等后处 理,得到催化剂。该方法操作简便, 适用于制备高分散度的催化剂。浸渍 法的优点是活性组分在载体上分布均 匀,有利于提高催化剂的活性。
溶胶-凝胶法
一种新型的催化剂制备方法
溶胶-凝胶法是一种新型的催化剂制备方法,通过将金 属盐溶液与沉淀剂反应,生成凝胶态的溶胶,再经干 燥和煅烧等后处理,得到催化剂。该方法具有操作简 便、成本低廉等优点,适用于制备高纯度、高分散度 的催化剂。溶胶-凝胶法的优点是活性组分在载体上分 布均匀,有利于提高催化剂的活性。
柴油加氢精的工艺有哪些

柴油加氢精的工艺有哪些
柴油加氢精制工艺有以下几种:
1. 传统加氢精制工艺:包括催化加氢裂解、催化裂化、催化重整等步骤。
2. H-Oil工艺:采用催化加氢裂解和热调整技术,通过将原油加热至裂化温度后再进行催化加氢裂化操作。
3. L-Design工艺:是一种低温热调整工艺,通过将原油送入加湿催化剂床进行加湿和加热,再将其送入经过加热的加氢催化剂床进行加氢裂化。
4. VRDS工艺:采用催化加氢重整、溶剂精制等步骤,能够有效降低硫和氮含量,提高柴油的品质。
5. 二次加氢精制工艺:对传统加氢精制工艺的改进,通过在催化裂化之后再次进行催化加氢,可进一步降低硫、氮和芳烃含量。
以上是一些常见的柴油加氢精制工艺,具体选用哪种工艺取决于原油的性质以及产品要求等因素。
汽柴油加氢技术总结汇报
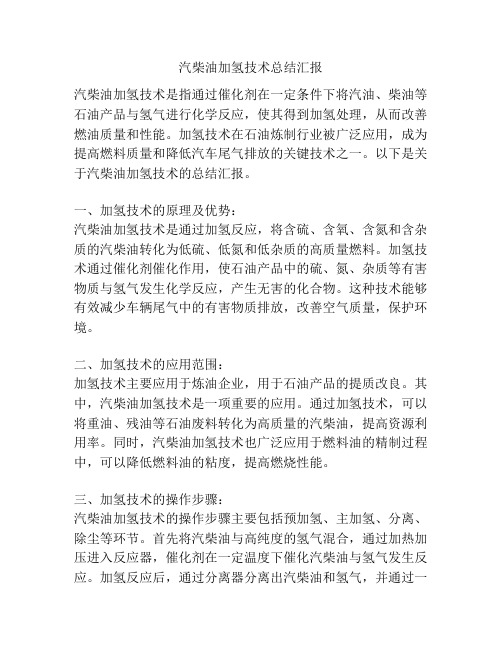
汽柴油加氢技术总结汇报汽柴油加氢技术是指通过催化剂在一定条件下将汽油、柴油等石油产品与氢气进行化学反应,使其得到加氢处理,从而改善燃油质量和性能。
加氢技术在石油炼制行业被广泛应用,成为提高燃料质量和降低汽车尾气排放的关键技术之一。
以下是关于汽柴油加氢技术的总结汇报。
一、加氢技术的原理及优势:汽柴油加氢技术是通过加氢反应,将含硫、含氧、含氮和含杂质的汽柴油转化为低硫、低氮和低杂质的高质量燃料。
加氢技术通过催化剂催化作用,使石油产品中的硫、氮、杂质等有害物质与氢气发生化学反应,产生无害的化合物。
这种技术能够有效减少车辆尾气中的有害物质排放,改善空气质量,保护环境。
二、加氢技术的应用范围:加氢技术主要应用于炼油企业,用于石油产品的提质改良。
其中,汽柴油加氢技术是一项重要的应用。
通过加氢技术,可以将重油、残油等石油废料转化为高质量的汽柴油,提高资源利用率。
同时,汽柴油加氢技术也广泛应用于燃料油的精制过程中,可以降低燃料油的粘度,提高燃烧性能。
三、加氢技术的操作步骤:汽柴油加氢技术的操作步骤主要包括预加氢、主加氢、分离、除尘等环节。
首先将汽柴油与高纯度的氢气混合,通过加热加压进入反应器,催化剂在一定温度下催化汽柴油与氢气发生反应。
加氢反应后,通过分离器分离出汽柴油和氢气,并通过一系列的脱硫、脱氮、脱杂等工艺处理,最终得到高质量的汽柴油产品。
四、加氢技术的优势与不足:加氢技术具有以下优势:1. 改善燃料质量:通过加氢处理,汽柴油的硫含量、氮含量和杂质含量得到有效降低,提高了燃料的质量。
2. 降低尾气排放:加氢技术能够减少燃料中的有害物质含量,从而降低了汽车尾气中的污染物排放,改善环境质量。
3. 提高能源利用率:通过将废料油转化为汽柴油,提高了资源利用效率,减少了能源浪费。
不足之处:1. 技术要求高:加氢技术对催化剂稳定性、反应条件、操作参数等要求较高,需要专业技术人员掌握和操作。
2. 设备投资大:加氢技术需要投入大量设备和催化剂,投资成本较高。
柴油加氢技术总结_锅炉技术总结范文
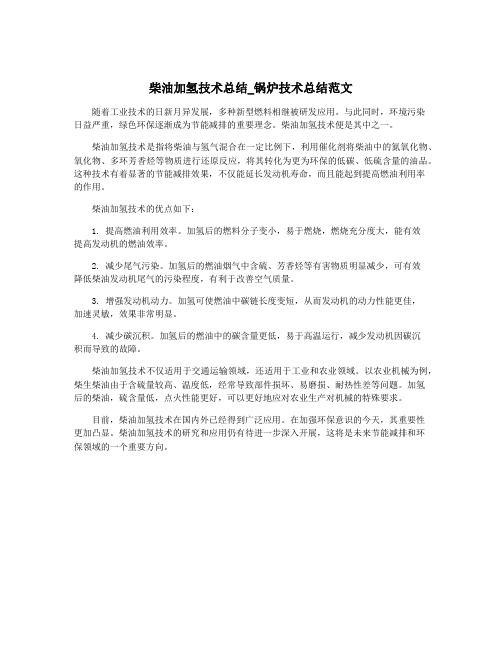
柴油加氢技术总结_锅炉技术总结范文
随着工业技术的日新月异发展,多种新型燃料相继被研发应用。
与此同时,环境污染
日益严重,绿色环保逐渐成为节能减排的重要理念。
柴油加氢技术便是其中之一。
柴油加氢技术是指将柴油与氢气混合在一定比例下,利用催化剂将柴油中的氮氧化物、氧化物、多环芳香烃等物质进行还原反应,将其转化为更为环保的低碳、低硫含量的油品。
这种技术有着显著的节能减排效果,不仅能延长发动机寿命,而且能起到提高燃油利用率
的作用。
柴油加氢技术的优点如下:
1. 提高燃油利用效率。
加氢后的燃料分子变小,易于燃烧,燃烧充分度大,能有效
提高发动机的燃油效率。
2. 减少尾气污染。
加氢后的燃油烟气中含硫、芳香烃等有害物质明显减少,可有效
降低柴油发动机尾气的污染程度,有利于改善空气质量。
3. 增强发动机动力。
加氢可使燃油中碳链长度变短,从而发动机的动力性能更佳,
加速灵敏,效果非常明显。
4. 减少碳沉积。
加氢后的燃油中的碳含量更低,易于高温运行,减少发动机因碳沉
积而导致的故障。
柴油加氢技术不仅适用于交通运输领域,还适用于工业和农业领域。
以农业机械为例,柴生柴油由于含硫量较高、温度低,经常导致部件损坏、易磨损、耐热性差等问题。
加氢
后的柴油,硫含量低,点火性能更好,可以更好地应对农业生产对机械的特殊要求。
目前,柴油加氢技术在国内外已经得到广泛应用。
在加强环保意识的今天,其重要性
更加凸显。
柴油加氢技术的研究和应用仍有待进一步深入开展,这将是未来节能减排和环
保领域的一个重要方向。
柴油加氢实训心得

柴油加氢实训心得一、前言在柴油加氢实训中,我深入学习了柴油加氢技术的基本原理、操作流程以及设备维护等方面的知识。
通过实际操作,我对柴油加氢的过程和影响因素有了更深入的理解,本文将全面、详细、完整地探讨柴油加氢实训的心得体会。
二、柴油加氢实训的基本原理柴油加氢是一种通过将柴油与氢气反应,降低柴油中铜、镍等杂质含量,增加烃类化合物、减少芳香烃和多环芳烃的加工过程。
该过程主要分为两个步骤:氢解和氢化。
2.1 氢解在柴油加氢装置中,柴油首先与氢气在催化剂的作用下进行氢解反应。
这个过程中,高温催化剂能够将柴油中的大部分烷烃链进行切割,生成烃烃链。
这样可以增加烃类的含量,提高柴油的可燃性和流动性。
2.2 氢化在氢解反应之后,柴油中的烃烃链进一步与氢气发生氢化反应。
氢气能够与柴油中的不饱和烃烃链发生反应,将其还原为饱和烃烃链,从而降低柴油中的芳香烃和多环芳烃含量。
这个过程中,催化剂能够起到促进反应的作用。
三、柴油加氢实训的操作流程在柴油加氢实训中,我们按照以下步骤进行操作:3.1 点燃炉膛首先,我们需要点燃炉膛。
在点燃之前,要确保炉膛内没有残留的氢气等可燃物,并逐步将氢气与空气混合,使其达到可燃浓度。
然后使用点火设备进行点火。
3.2 加热炉膛在点燃之后,需要控制氢气的供应,使其与燃烧产生的烟气充分混合。
同时,还需要控制炉膛的温度,使其逐渐升温到加氢反应的适宜温度。
3.3 加氢反应当炉膛的温度达到适宜的加氢温度后,将柴油加入加氢炉中。
柴油经过加热后,会与氢气在催化剂的作用下进行加氢反应。
加氢反应过程中,需要控制氢气的流量和柴油的进料速度,以保证反应的效果。
3.4 沉淀杂质加氢反应结束后,柴油中的杂质会通过与催化剂沉淀下来。
这些沉淀物可以通过过滤和离心等操作进行分离,得到纯净的柴油。
四、柴油加氢实训的设备维护为了确保柴油加氢实训的正常进行,我们需要对设备进行定期维护。
4.1 催化剂更换催化剂是柴油加氢实训中非常重要的一部分。
柴油加氢脱硫技术现状研究

柴油加氢脱硫技术现状研究随着全球环保意识的增强和各国政府对环境保护的重视,柴油加氢脱硫技术已成为一种重要的大气污染治理技术。
柴油加氢脱硫技术是利用加氢反应将硫化物转化为硫化氢,从而实现柴油中硫化物的脱除。
本文将对柴油加氢脱硫技术的现状进行研究,分析其技术原理、发展趋势以及在环保领域的应用前景。
一、柴油加氢脱硫技术原理柴油加氢脱硫技术是利用氢气和催化剂对含硫化物的柴油进行加氢反应,其中硫化物被转化为硫化氢,从而实现脱除。
其主要反应方程式如下:R-S-R' + 2H2 → 2RH + H2SR表示烷基或芳香基,R'表示氢原子或烷基。
在催化剂的作用下,硫化物和氢气经过加热和压力的条件下进行反应,生成硫化氢和硫化烃。
硫化氢从柴油中脱除后,可通过后续的工艺过程进一步处理,以减少对环境的影响。
目前,柴油加氢脱硫技术已经成熟并广泛应用于炼油、化工和燃料行业。
在炼油工业中,柴油加氢脱硫技术已被应用于重油加氢脱硫、柴油加氢脱硫和船用燃料加氢脱硫等工艺。
在化工行业中,柴油加氢脱硫技术也逐渐被应用于有机硫化物的加氢脱硫。
而在燃料行业中,柴油加氢脱硫技术也被应用于燃料油的加氢脱硫,以满足环保对于燃料标准的要求。
在技术方面,目前柴油加氢脱硫技术已经形成了一系列成熟的工艺流程和设备,包括加氢反应器、催化剂、脱硫剂、氢气制备系统、变压变温控制系统等。
尤其是催化剂的研究和应用方面取得了显著的进展,高效催化剂的研发和应用使得柴油加氢脱硫技术在反应速率、选择性、稳定性等方面得到了显著提高。
在应用方面,柴油加氢脱硫技术在油田、能源等行业已经得到了广泛应用。
特别是随着环保意识的增强,柴油加氢脱硫技术在燃料领域的应用前景更加广阔。
通过柴油加氢脱硫技术进行燃料脱硫处理,不仅可以改善燃料的环保性能,还可以提升机械设备的使用寿命和运行效率,对于减少大气污染和保护环境具有重要意义。
随着环保压力的增大和技术的不断进步,柴油加氢脱硫技术的发展趋势也呈现出以下几个特点:1. 高效催化剂的研发应用:高效催化剂能够提高加氢反应的速率和选择性,降低加氢反应的温度和压力,从而降低成本并提高效率。
柴油加氢改质装置节能降耗技术分析与对策

柴油加氢改质装置节能降耗技术分析与对策一、柴油加氢改质装置的技术原理柴油加氢改质装置,简称加氢装置,是通过在柴油发动机的进气道中加入氢气,利用氢气与柴油混合燃烧,从而提高燃烧效率,减少尾气排放,降低燃油消耗的一种技术手段。
其技术原理主要包括以下几个方面:1. 燃烧效率提高:通过向柴油中加入氢气,可以使得燃油在燃烧过程中更加充分,提高燃烧效率,从而减少燃油的消耗。
2. 尾气排放降低:氢气在燃烧过程中可以与氧气充分混合,从而减少燃烧产生的有害气体,降低尾气排放。
3. 发动机功率提升:利用氢气的高热值特性,可以提高柴油发动机的实际功率输出,实现动力提升的效果。
2. 排放水平降低:氢气的加入可以改善柴油发动机的燃烧过程,减少有害气体的排放,对环境保护具有显著效果。
在实际应用柴油加氢改质装置时,需要克服一些技术难题,从而实现更好的节能降耗效果。
以下是针对柴油加氢改质装置的技术对策:1. 加氢装置的稳定性:加氢装置在柴油发动机中的工作稳定性是关键,需要解决在车辆长时间运行或在极端环境下出现的稳定性问题。
2. 加氢装置的安全性:在加氢改质过程中,需要保证氢气供应系统的安全和稳定,避免出现安全隐患。
3. 加氢装置的成本控制:加氢装置需要在成本可控的基础上提供良好的节能降耗效果,因此需要在技术和成本的平衡上进行合理的控制。
4. 加氢装置与柴油发动机的匹配问题:加氢装置需要与柴油发动机良好的匹配,保证在不影响发动机正常工作的情况下提供更好的节能降耗效果。
四、结语柴油加氢改质装置的节能降耗技术具有很大的应用前景,需要不断进行技术创新和实践应用,从而为我国能源资源的可持续发展作出更大的贡献。
柴油加氢技术总结

柴油加氢技术总结2#柴油加氢装置开工总结宋火军1.开工前的准备1.1 学习装置理论知识生产低硫、低芳烃、低密度、高十六烷值得清洁柴油是今后世界范围内的柴油生产总趋势。
如何满足符合日趋苛刻的车用柴油标准,生产出符合环保要求的清洁柴油将成为炼油技术进步的一个重要课题。
柴油燃料质量升级的趋势与汽油类似,最主要的是对于硫含量的控制,同时对于柴油产品指标中的十六烷值、芳烃含量、冷流动性、密度等也提出了更为严格的要求。
二次加工的柴油含有相当多的硫、氮及烯烃类物质,油品质量差,安定性不好,储存过程容易变质,对直馏柴油而言,由于原油中硫含量升高,环保法规日趋严格,已经不能直接作为产品出厂,也需要经过加氢精制处理。
柴油加氢精制的生产原理就是在一定温度、压力、氢油比、空速条件下,借助加氢精制催化剂的作用,有效的使油品中的硫、氮、氧、非烃类化合物转化为响应的烃类和H2S、NH3和H2O。
另外,少量的重金属则截留在催化剂中,同时使烯烃和部分芳烃饱和,从而得到安定性、燃烧性、情节性都较好的优质柴油产品和粗汽油(裂解料)。
本装置中大量循环氢的存在能保证气相为连续相,液相为分散相,被气相打散的液相在固定床催化剂上从上至下以液滴的形态流过催化剂床层,从而发生一系列的加氢反应。
循环氢在其中的关键作用是:(1)维持反应所需的氢分压,用来维系气相中的氢气向油相溶解的推动力。
(2)控制催化剂床层的温升。
(3)稀释反应物流杂质的浓度,促进深度脱杂质的反应。
1.2 学习开工方案在开工前两个月,车间开始组织操作人员学习开工方案,让每个人对开工都心里有数,了解每一个步骤,提高了操作人员的操作水平,为这次成功的开工打下了基础。
1.3 联系调度,提供合格氮气,在系统催化剂干燥时能满足供应。
1.4 硫化剂与试车用直馏柴油准备充足。
2.催化剂干燥催化剂在包装、储运和装填中,都难免吸附一定水分,吸附水会降低催化剂的活性和强度。
因此催化剂要在预硫化前进行脱水。
柴油加氢脱硫技术现状研究

柴油加氢脱硫技术现状研究1. 引言1.1 背景介绍柴油加氢脱硫技术是一种重要的环保技术,旨在降低柴油中硫含量,减少尾气排放中的硫氧化物对环境的污染。
随着全球环保意识的增强和政府对环境保护法规的不断完善,柴油加氢脱硫技术逐渐成为柴油加工行业的研究热点。
背景介绍中,首先需了解我国柴油消费量大、车辆保有量高的现状。
我国是全球最大的柴油消费国之一,私家车和商用车的保有量呈增长态势,因此柴油车尾气排放对环境质量的影响显得尤为重要。
在这种背景下,研究柴油加氢脱硫技术对改善柴油车尾气排放质量,减少对环境的污染具有重要意义。
柴油加氢脱硫技术在提高柴油品质、延长柴油车使用寿命等方面也具有重要作用。
深入研究柴油加氢脱硫技术的原理、应用和发展现状,探讨存在的问题和发展趋势,对推动我国柴油加工行业的可持续发展具有重要意义。
1.2 研究意义研究意义是指柴油加氢脱硫技术对环境保护和能源发展的重要意义。
随着环境污染日益严重,柴油加氢脱硫技术可以有效降低柴油燃烧过程中产生的硫氧化物,减少大气污染物的排放,对改善空气质量具有积极意义。
柴油加氢脱硫技术也能提高柴油的品质,降低机动车尾气中的有害物质浓度,对汽车尾气排放控制具有重要意义。
柴油加氢脱硫技术的研究还对我国的能源结构调整和环保产业发展具有重要的促进作用。
随着我国经济的快速发展和工业化进程的加快,对于清洁能源的需求日益增加,柴油加氢脱硫技术的应用将有望逐步推动我国的能源结构向清洁化和高效化方向转变。
深入研究柴油加氢脱硫技术的原理和应用,探索其发展现状和未来趋势,对促进我国能源结构调整和环保产业发展有着重要的现实意义和战略意义。
1.3 目的和意义柴油加氢脱硫技术是一种通过加氢反应将柴油中的硫化物转化为硫化氢,从而实现脱硫的高效技术。
在当前环境保护和能源清洁利用的背景下,研究柴油加氢脱硫技术的目的主要有以下几个方面:1. 降低柴油中硫含量,减少尾气中的硫氧化物排放,对改善大气质量、减少酸雨的形成具有重要意义。
分析柴油加氢改质降凝技术的开发及工业应用
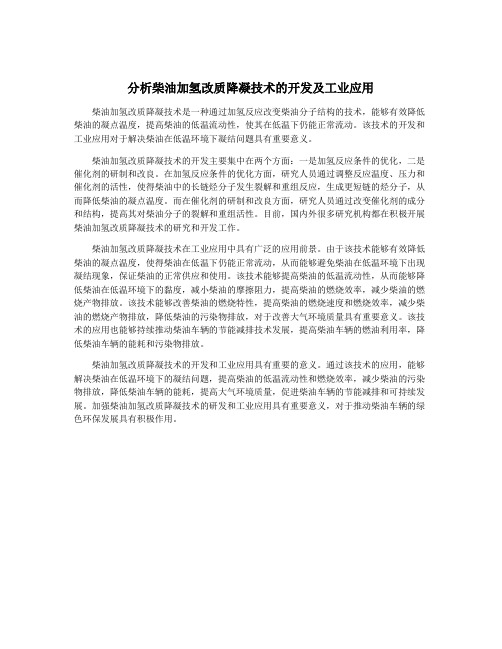
分析柴油加氢改质降凝技术的开发及工业应用柴油加氢改质降凝技术是一种通过加氢反应改变柴油分子结构的技术,能够有效降低柴油的凝点温度,提高柴油的低温流动性,使其在低温下仍能正常流动。
该技术的开发和工业应用对于解决柴油在低温环境下凝结问题具有重要意义。
柴油加氢改质降凝技术的开发主要集中在两个方面:一是加氢反应条件的优化,二是催化剂的研制和改良。
在加氢反应条件的优化方面,研究人员通过调整反应温度、压力和催化剂的活性,使得柴油中的长链烃分子发生裂解和重组反应,生成更短链的烃分子,从而降低柴油的凝点温度。
而在催化剂的研制和改良方面,研究人员通过改变催化剂的成分和结构,提高其对柴油分子的裂解和重组活性。
目前,国内外很多研究机构都在积极开展柴油加氢改质降凝技术的研究和开发工作。
柴油加氢改质降凝技术在工业应用中具有广泛的应用前景。
由于该技术能够有效降低柴油的凝点温度,使得柴油在低温下仍能正常流动,从而能够避免柴油在低温环境下出现凝结现象,保证柴油的正常供应和使用。
该技术能够提高柴油的低温流动性,从而能够降低柴油在低温环境下的黏度,减小柴油的摩擦阻力,提高柴油的燃烧效率,减少柴油的燃烧产物排放。
该技术能够改善柴油的燃烧特性,提高柴油的燃烧速度和燃烧效率,减少柴油的燃烧产物排放,降低柴油的污染物排放,对于改善大气环境质量具有重要意义。
该技术的应用也能够持续推动柴油车辆的节能减排技术发展,提高柴油车辆的燃油利用率,降低柴油车辆的能耗和污染物排放。
柴油加氢改质降凝技术的开发和工业应用具有重要的意义。
通过该技术的应用,能够解决柴油在低温环境下的凝结问题,提高柴油的低温流动性和燃烧效率,减少柴油的污染物排放,降低柴油车辆的能耗,提高大气环境质量,促进柴油车辆的节能减排和可持续发展。
加强柴油加氢改质降凝技术的研发和工业应用具有重要意义,对于推动柴油车辆的绿色环保发展具有积极作用。
柴油加氢流程

柴油加氢流程
柴油加氢是一种常见的炼油工艺,通过加氢反应可以提高柴油
的品质,减少硫、氮等有害物质的含量,提高燃烧效率,降低环境
污染。
下面我们将介绍柴油加氢的流程。
首先,原料柴油通过预处理单元进行预处理,去除其中的杂质
和硫、氮等有害物质。
在预处理单元中,柴油会被加热至一定温度,然后进入加氢反应器。
在加氢反应器中,柴油与氢气在催化剂的作用下发生加氢反应,硫、氮等有害物质被还原成相对无害的化合物,同时分子结构也发
生改变,提高了柴油的品质。
加氢反应的温度、压力和催化剂的选
择都对反应的效果有着重要影响。
经过加氢反应后的柴油进入分离装置,通过升温、蒸馏等操作,将加氢后的柴油与副产物进行分离,得到提质后的柴油产品。
同时,副产物中的氢气也会被回收利用,提高了资源利用效率。
最后,提质后的柴油产品需要经过一系列的检测和处理,确保
其符合相关的质量标准,然后可以被用于各种柴油发动机的燃烧,
提供动力。
总的来说,柴油加氢流程是一种重要的炼油工艺,通过加氢反
应可以提高柴油的品质,减少环境污染,对于能源的可持续发展具
有重要意义。
加氢流程的优化和改进也是炼油企业不断努力的方向,希望能够在未来为社会提供更加清洁、高效的柴油产品。
柴油质量升级的加氢技术

19
劣质柴油加氢改质异构降凝FHI工艺技术
●FHI技术特点 FHI技术选用具有强异构功能的催化剂,采用单剂或两剂串联一次通过
工艺流程,在中压或高压条件下,对直馏柴油和/或二次加工柴油进行加氢 处理,在实现深度脱硫、脱氮、脱芳和选择性开环的同时,可以使进料中 的正构烷烃等高凝点组分进行异构化反应,并使进料中的重馏分发生适度 的加氢裂化反应,从而在显著降低柴油产品硫、氮和芳烃(尤其是稠环芳烃) 含量的同时,能够大幅度降低凝固点,并使密度、T95和十六烷值等指标 得到明显改善。
2020/8/13
9
劣质柴油中压加氢改质(MHUG)技术
●技术特点
MHUG技术在中压6.0MPa~10 Mpa条件下,主要加工重 油催化柴油或重油催化柴油与直馏轻蜡油的混合油,不仅 可以改善柴油的颜色和安定性,而且可以可使柴油的十六 烷值提高12~20个单位,同时还可以兼产部分低硫、低氮、 高芳潜的优质化工石脑油。
364
359
10160
300
4.4
2.0
206
320
348
高干点直柴::MIP催柴:焦汽 =62.2:24.3:13.5
原料油
精制柴油
0.8579
0.8569
369
364
9100
296
5
生产低硫柴油的柴油深度加氢脱硫技术
FH-UDS催化剂工业应用结果 (硫含量<350μg/g)
应用厂家
茂名分公司
上海石化公司
2020/8/13
12
最大限度提高劣质柴油十六烷值的MCI工艺
●技术特点
最大限度提高劣质柴油十六烷值MCI(Maximally Index Improvement) 技术采用专用催化剂,对劣质柴油(特别是重油催化柴油)进行深度加氢脱 硫、脱氮、稀烃饱和、芳烃部分饱和、开环,且开环后很少裂解,从而在改 善油品安定性的同时,使柴油的十六烷值提高8~15个单位以上,并保持柴 油产品收率在95%以上。MCI技术另一个特点是操作条件和运行方式与传 统的催化柴油加氢精制工艺技术相近,用户只需对现有的催化柴油加氢精制 略作改造甚至无需改造,便可以满足MCI技术的操作要求。
国内外柴油加氢技术现状及发展趋势

国内外柴油加氢技术现状及发展趋势柴油加氢技术是一种将柴油中的硫、氮、氧和其他杂质通过加氢反应转化为低硫、低氮、低芳烃的技术。
这项技术在国内外都得到了广泛的应用和研究,其发展也呈现出一些明显的趋势。
国内外柴油加氢技术已经相对成熟,其应用范围逐渐扩大。
在国内,随着环保要求的提高,柴油加氢技术已经成为降低柴油中有害气体排放的重要手段。
许多炼油企业已经采用了加氢装置来处理柴油,以满足国家环保标准。
同时,国内柴油加氢催化剂的研发也取得了一定的进展,催化剂的活性和稳定性得到了提高。
国外柴油加氢技术的发展更为成熟。
在美国、欧洲等发达国家,柴油加氢技术已经广泛应用于炼油行业,并取得了较好的效果。
这些国家对柴油的环保要求更为严格,因此对柴油加氢技术的研究也更加深入。
柴油加氢技术不仅可以降低柴油中的有害物质排放,还可以提高柴油的燃烧性能和质量,减少机械磨损和能源浪费。
柴油加氢技术的发展趋势主要表现在以下几个方面。
首先,催化剂的研发将成为重点。
催化剂是柴油加氢技术中的关键因素,其性能直接影响到加氢反应的效果。
目前,国内外的研究机构和企业都在加大对催化剂的研发力度,希望能够开发出更高效、更稳定的催化剂。
其次,柴油加氢技术将更加注重环保性能。
随着环保要求的提高,柴油加氢技术需要更好地解决柴油中有害气体的排放问题,减少对环境的污染。
因此,未来柴油加氢技术将更加注重降低硫、氮等有害物质的含量。
此外,柴油加氢技术还将更加注重节能减排。
通过改善柴油的燃烧性能和质量,可以提高柴油的能源利用率,减少能源的浪费。
国内外柴油加氢技术已经取得了一定的成就,但仍有进一步发展的空间。
未来,柴油加氢技术将更加注重催化剂的研发、环保性能和节能减排。
相信随着科技的进步和环保意识的提高,柴油加氢技术将在国内外得到更广泛的应用,为降低柴油污染、提高能源利用效率做出更大的贡献。
- 1、下载文档前请自行甄别文档内容的完整性,平台不提供额外的编辑、内容补充、找答案等附加服务。
- 2、"仅部分预览"的文档,不可在线预览部分如存在完整性等问题,可反馈申请退款(可完整预览的文档不适用该条件!)。
- 3、如文档侵犯您的权益,请联系客服反馈,我们会尽快为您处理(人工客服工作时间:9:00-18:30)。
柴油加氢技术2.柴油加氢精制工艺原理质量低劣的柴油原料,在一定的温度、(一般在290℃--350℃)压力、(3.0MPa--16 MPa)和氢气,在加氢精制催化剂作用下,将油品中的含S、含N、含O等非烃化合物转化为易除去的H2S、NH3、H2O,将安定性很差的烯烃和某些芳烃饱和,金属有机物氢解,金属杂质截留,从而改善油品的安定性质、腐蚀性能和燃烧性能,得到品质优良的柴油产品,此工艺过程称为柴油加氢精制。
在工艺过程中主要有以下化学反应:脱硫反应:在加氢条件下,石油馏分中的含硫化合物转化为相应的烃和硫化氢,从而脱除了硫。
脱氮反应:在加氢过程中,各种氮化物与氢气反应转化为NH3和相应的烃,从而被除掉。
脱氧反应:含氧化合物通常很容易进行加氢反应生成水和相应的烃。
脱金属:金属有机化合物不论是否分解均吸附在催化剂表面上而被除去。
一般柴油加氢精制装置采用固定床单段一次通过式加氢工艺。
设计操作压力3.0--8.0MPa,空速1.0--2.5h-1,氢油体积比为300--600,以焦柴、催柴、直柴等混合柴油为原料,生产优质柴油,同时切割出少量的石脑油和副产部分瓦斯、酸性气。
3.柴油加氢装置原则工艺流典型流程图见图二流程说明:进装置原料(混合柴油)先至原料缓冲罐,被升压泵抽送经过原料过滤器把会导致反应器上部催化剂床层堵塞的固体杂质过滤掉,进入滤后原料缓冲罐。
滤后柴油原料经反应进料泵抽出与氢气(循环氢+新氢)混合后经与反应产物换热器换热,加热炉加热后进入反应器。
在反应器中混合原料在加氢精制催化剂作用下进行加氢脱硫、脱氮、烯烃及芳烃饱和等反应。
在催化剂床层之间设有控制反应温度的冷氢。
反应产物出反应器后与混合原料换热至约140℃进入高压空冷器,在高压空冷器入口注入脱氧水以溶解掉反应过程中产生的铵盐,防止堵塞高压空冷器。
反应产物经高压空冷、水冷冷却至40℃进入高压分离器进行汽液水分离,其顶部出来的气体作为循环氢去循环氢压缩机循环进反应系统,底部的酸性水去双塔汽提单元,中部出来的生成油去低压分离器进行闪蒸汽、液分离。
分离出来的气体作为燃料气经脱硫后进入瓦斯管网,分离出的生成油经与分馏塔底精制柴油换热器换热,加热至220℃左右进入脱H2 S汽提塔,汽提塔顶富气去富气脱硫单元,塔顶全回流不出产品,汽提塔底油经塔底泵(或自压)与反应器出口生成油换热器换热,加热至约250℃去分馏塔;分馏塔采用塔底重沸炉的形式,重沸炉有四路进料,控制炉出口温度为300℃左右。
塔顶产品为石脑油,塔底柴油经与低分出口生成油换热、空冷、水冷冷却至50℃左右出装置。
A.原料系统原料由罐区原料泵输送至装置界区,界区可设计一条原料界区外返回线,可以在引原料进装置前建立原料带罐循环,一是冲洗原料来线,二来方便引原料进装置。
原料进装置后用原料油流量计计量和累计,由液控阀控制进原料缓冲罐的量。
原料被升压泵升压至1.0MPa左右后进原料过滤器,过滤后的原料经液控阀控制进滤后原料缓冲罐,滤后原料用反应进料泵升压后送入反应系统,由泵出口流量控制阀控制进反应系统的量,即进料量。
(如果罐区来原料压力较高,可直接进原料过滤器,省去滤前原料缓冲罐。
)原料缓冲罐顶部采用氮气或瓦斯密封,一般由分程压控阀控制一定压力。
隔绝空气。
B.反应进料加热系统进料泵出口的原料与从循环氢压缩机出口的循环氢和新氢机出口的新氢混合后先后进入原料---反应产物换热器换热,然后进入反应加热炉对流段,再进入炉辐射段,加热到反应器入口所需的温度。
加热炉出口温度(反应器入口温度)一般由瓦斯流量(压力)或炉膛温度串级控制。
C.反应器系统原料自加热炉出来后,从顶部进入反应器,在反应器中与催化剂接触,产生一系列脱O、脱N、稀烃饱和反应,这些反应均为放热反应,因此,反应混合物自上而下流经CAT床层时,温度逐步上升,为了限制温升和控制反应速率,在CAT床层之间打入从循环氢压缩机出来的冷的循环氢来调节床层温度,用温控阀来控制流量,经验表明,加氢处理操作若任一床层的温升超过55℃时,就会有操作不稳定而存在危险的可能,因此,正常操作时,任一床层的温升一般不超过50℃。
反应器内一般有2--3个床层,在进料管以下和床层之间设有分配盘,以保证物流一进入催化剂床层就有良好的气液分布,反应物流的良好分可防止出现热点和最大限度的发挥CAT的性能,以及保持CAT的寿命。
在每一个床层的上部和下部床层平面上设有几个测温点,用之检测物流通过床层的温差,在床层上相同高度但不同平面部位所测出的温度变化能表明物流是否有沟流现象。
在反应器的入口管、急冷氢管和反应产物出口管上都设有测压点,可分别测量各个床层或,整个床层的压降。
在反应器外壁的不同高度分别设有表面测温点,用以检测反应器筒体温度。
D.反应产物的冷却反应产物从底部出来后,进反应产物与原料换热器管程与原料(或分馏进料)换热,冷却至140℃左右,与注入的水混合一起进空冷冷却后,再进水冷冷却至40℃左右后进冷高分。
E.高压分离系统在高分内,反应产物分离为生成油、含硫污水、和富氢气,富氢气从分离器顶部出来作为循环氢进入循环氢脱硫塔或直接进入循环机入口分液罐。
含硫污水经界控去污水处理。
生成油经液控去低压分离器。
冷高分操作温度冷高分的温度通过高压空冷、水冷来调节,温度降低时,在分离器中较多的轻烃冷凝下来并溶解在液相中,因此,循环氢中轻烃减少,提高了循环氢的纯度,因此,冷高分操作温度尽可能保持低些。
一般冷高分设计入口温度45℃左右。
F.循环氢系统冷高分顶分离出的循环氢进入循环氢压缩机入口分液罐,分液罐内设有丝网除雾器,把循环氢中所携带的的液体分离掉,如分液罐液面高,就会将液体带入压缩机而导致压缩机严重损坏,因此,在冷高分液面不稳或因仪表风压力下降、液控阀卡等原因而造成冷高分液面超高时,一定要对分液罐及时排凝。
循环气从分液罐顶出口进入压缩机入口,被压缩升压至反应系统所要求的压力,与补充氢混合返回系统,压缩机出口分三路:一路去进料泵出口与原料混合,一路去反应器做冷氢,一路去高压空冷入口防喘振线。
G.补充氢系统装置用补充氢---新氢先进入新氢压缩机的入口分液罐,分离后的新氢进入新氢压缩机的入口,经压缩升压到所需要的压力后,经压控补充进循环氢系统,补入点可以在循环氢压缩机入口,也可以在循环氢压缩机出口。
H.注水系统原料中的硫化物和氮化物在加氢过程中分别生成H2S和NH3,而H2S和NH3在160℃左右的温度下生成NH4HS,NH4HS在100℃以下为固体,为了防止NH4HS固体堵塞和腐蚀空冷,故在空冷入口注入洗涤水,使NH4HS溶解在水中从冷高分排出,洗涤水注入点的反应产物温度必须在100℃和水的露点之间。
在大部分装置中注水点还有一个在进高压空冷前的反应产物换热器的管程入口,在装置运行中末期间断投用,此注水点的目的是溶解冲洗掉换热器管束中生成的盐垢,特别是氯盐,提高换热效果。
洗涤水可以是冷却后的脱氧水,软化水,凝结水或是净化后的酸性水,但不能是新鲜水,以防止高压空冷结盐。
I.低压闪蒸系统主要作用是降压闪蒸出部分富气,降低分馏塔负荷,低压分离器的压力要能够使低压分离器内液体自压至分馏塔,以及使富气自压去低压气体脱硫单元,较低的操作压力可使较多的溶解汽在低分内闪蒸出来。
40℃左右的生成油从冷高分出来,降压后进入闪蒸罐,在0.85Mpa左右的压力下闪蒸出富气和油,富气去脱硫后进瓦斯管网,生成油换热后进脱硫化氢塔。
低分出口可设一条去原料返回的线,装置停电或催化剂湿法预硫化时用。
J.脱硫化氢塔进料的换热系统低分生成油进入脱硫化氢塔进料换热器与分馏塔底精制柴油换热,换热至220℃左右进脱硫化氢塔。
K.脱硫化氢系统设立脱硫化氢塔的目的是低分来的生成油未去常压分馏塔前在此先除去硫化氢和轻质气体,避免对下游设备的腐蚀,并回收轻组份,吹汽冷凝水也可自压去污水处理装置。
一般采用蒸汽吹脱的工艺,塔顶产物经空冷、水冷冷却后,进入回流罐,进行气、油、水三相分离,分离出的富气脱硫后进瓦斯管网,分离出的轻石脑油全回流,分离出的酸性水经界控排去污水处理装置。
塔底油自压或经塔底泵升压后加热或换热至260℃左右进分馏塔。
L.馏塔系统作为产品分馏塔,为防止精制柴油带水,一般采用塔底重沸炉工艺,塔顶产物经冷却后,进入回流罐,进行气、油、水三相分离,分离出的低压富气去火炬,分离出的轻石脑油一部分回流用来调节塔顶温度,一部分出装置做汽油调和组分或乙烯、制氢原料。
塔底产品经换热、冷却至50℃左右出装置作柴油调和组分。
4.加氢精制的工艺条件加氢反应的特点:加氢反应均是可逆、放热反应,一般说来在高压、低温下对化学平衡有利。
但为了提高反应速度,要求在一定的温度下进行。
反应中消耗大量的氢气,原料油来源、性质不同,加氢精制操作条件也不同,直馏油比二次加工油缓和,轻的比重的缓和,反应生成物中的硫化氢、氨、水等均易除掉。
影响加氢精制的主要因素影响加氢精制的主要因素有反应温度、压力、氢分压、空速、氢油比。
4.1反应压力反应压力的影响是通过氢分压来体现的,系统中的氢分压决定于操作压力、氢油比、循环氢纯度以及原料油的汽化率。
提高反应压力对加氢精制来说有利于脱除原料油中的S、N、O、和烯烃的饱和,提高产品质量,但压力过高消耗增大。
因此在保证产品质量合格的情况下,可以降压操作,降低能耗。
4.2反应温度提高反应温度可加快加氢反应速度,并有利于脱除原料油中的S、N、O、和烯烃的饱和,在其它条件不变的情况下,提高反应温度,可以提高产品质量,但反应温度过高,会加快CAT上积炭的沉积,降低CAT的活性,缩短生产周期,增加能耗。
并由于油品部分裂解,将影响产品颜色。
在操作中,根据原料性质、组成的不同,一般根据反应器温升≯50--70℃的原则,调整反应器入口温度。
4.3氢分压、氢纯度循环氢中氢气摩尔比率与反应压力的乘积,称为氢分压。
氢分压对CA T 脏污速率具有重要影响,提高氢分压能抑制CAT的失活,获得CAT的长周期运转,还有利于提高反应速度,提高产品质量。
提高氢分压的方法:提高总的反应压力提高新氢的氢纯度增加循环氢量增加废氢排放量或经过循环氢脱硫,提高循环氢纯度,降低冷高分的操作温度。
可提高循环氢纯度。
一般设计循环氢纯度>80%(V)循环氢中氢纯度提高10%,相当于平均反应温度降低2.8℃和延长生产周期20—30%,氢分压提高10%,相当于平均反应温度降低1.1℃。
H2S能够抑制脱硫反应。
由于H2S浓度增加循环氢中氢纯度降低,循环氢中H2S浓度由0增加到5%,如果操作压力为6.0MPa,相当于平均反应温度增加22℃。
4.4空速单位体积(重量)催化剂,在单位时间内所通过的原料油体积(重量)之比称为空速。
空速按单位可分为体积空速和重量空速。
体积空速= M3/h原料/ M3/h催化剂重量空速= t/h原料/ t/h催化剂空速的高低直接影响脱硫率,降低空速意味着增加了原料油同CAT的接触时间,加大了加氢深度,有利于脱除杂质提高产品质量,但空速低,降低了装置处理量,不利于经济效益。