焦炉煤气湿法脱硫工艺设计(初样)
湿法脱硫工艺

综述湿法脱硫工艺摘要:煤气是工业原料之一,煤气原料气处理是其他产业的基础,发展也很全面。
脱硫工艺在煤气净化精制中重要的步骤对后续产品的质量操作工艺与设备影响很大,对整个煤气净化具有举足轻重的作用。
目前脱硫的方法很多脱硫程度不尽相同,设备也因此而异,应用的催化剂也有很多种,针对此做出一些归纳与综述,以便做有关工艺设计参考用,介绍了国内外脱硫技术最新进展,阐述了各种不同脱硫技术的性能、特点、反应原理和应用现状,并预测了脱硫技术的发展趋势。
关键词:焦炉煤气;净化;湿法脱硫;前言脱硫工艺概述脱硫脱氰是焦炉煤气净化的主要工艺过程,通常有干法脱硫和湿法脱硫两种工艺,但干法脱硫工艺的局限性较大,制约了其在焦炉煤气净化中的应用,而湿法脱除H2S 和HCN 的技术则早已被广泛采用,在焦炉煤气脱硫脱氰净化中,通过与废液处理技术相结合,采用湿法脱硫技术可组成各种不同的焦炉煤气脱硫脱氰工艺流程。
在生产实际应用中可以结合干法脱硫与湿法脱硫技术的优点,将两种脱硫方法结合起来应用,利用湿法硫先将焦炉煤气中的大部分H2S 脱除,然后再利用干法脱硫对其中的H2S 进行精脱,从而达到满意的脱硫净度。
这样既利用了湿法脱硫可以在线调整的优点,又利用了干法脱硫效率高的优点,并克服了由于干法脱硫时脱硫剂硫容量因素而造成的脱硫剂失效过快的问题。
对于脱硫净度的问题,可以根据后续用户对净化后焦炉煤气中H2S和HCN 含量的不同要求,选择相应脱硫效率的脱硫工艺。
在冶金企业,焦炉煤气的绝大部分用作一般轧钢加热炉的燃料,此时要求H2S 含量≤250 mgPm3 ,HCN 含量≤150 mgPm3 ,因此选用AS 循环洗涤法脱除H2S和HCN 就能满足要求。
而当焦炉煤气用作城市煤气、氨用和甲醇用合成原料气时,则必须选择湿式氧化法中的改良ADA 法、TH法、FRC 法等脱硫效率更高的脱硫工艺。
在煤炭炼焦过程中,煤炭中约30 %~35 %的硫转化成H2S、CS2 、COS 等硫化物,与NH3 和HCN 等一起形成煤气中的杂质,要脱除H2S 和HCN ,必须采用有碱性的脱硫液或脱硫剂,碱源可分为两类: ①外加碱源,如乙醇胺、碳酸钠及氢氧化铁等分别是萨尔费班法、真空碳酸盐或改良ADA 法及干法脱硫工艺的碱源,同时需不断向脱硫液中补充碱源,才能保持其碱度。
焦炉煤气脱硫工艺

焦炉煤气脱硫工艺(总19页)本页仅作为文档封面,使用时可以删除This document is for reference only-rar21year.March煤化工工艺大作业焦炉煤气脱硫工艺的探讨院系:资源与环境学院班级:化工09—4班姓名:荆智鹏学号: 14指导老师:徐秀梅焦炉煤气脱硫工艺的探讨作者:荆智鹏摘要:煤化工是以煤为原料经化学加工使煤转化为其他化学产品的过程。
从煤气化工段的工艺气中发现,除了含有生产甲醇和其他下游产品所需的CO, H2 和CO2 外,还含有大量多余的CO2 及少量H2S, COS,SO2 等成分,这些碳的氧化物和硫化物是生产甲醇或其他化学品所不需要的,必须将这些杂质除去。
另外,硫化物通过克劳斯工艺生产硫磺,CO2 可以回收送往尿素厂合成尿素,提高经济效益变废为宝。
以天然气或石脑油为原料,采用蒸汽转化法造气,变换气中CO2 的含量约在15-23mol%左右。
以重油或煤原料,采用部分氧化法制气时,变换气中 CO2 的含量高达35mol%以上。
H2S 及有机硫的含量则与原料含硫量有关,约在1000ppm 和10000ppm 之间。
通过净化,使硫化物含量小于0.2-0.5ppm, CO2 小于10ppm。
关键词:煤气脱硫湿法干法催化剂科学的讲,在湿式氧化法脱硫中,副盐的生成是无法回避的,它是化学反应的副产物,是客观存在的。
但是,我们通过多年实际生产状况总结发现,同等规模条件下,不同的工况条件、不同的工艺技术、不同的设备配置以及使用不同的催化剂,副盐生成量的多少却大不一样,而且差别很大。
这一现象引起我们高度的重视,也再次促使我们进一步探讨和研究脱硫中副盐形成的机理,因为只有清楚的了解副盐产生的机理,我们才能有效的找到解决和处理它的措施。
虽然我们不能避免它的形成,但我们可以采取一系列有效措施来减少或抑制它的生成。
从而减少脱硫液中由于副盐的存在而影响企业的正常生产。
特别在大规模的生产中(气量大、H2S含量高),这种现象尤为突出,副盐的生成不仅严重影响了脱硫效率、增加了辅料消耗而且也影响了环保。
焦化厂脱硫工艺流程

焦化厂脱硫工艺流程一、背景介绍焦化厂是一种能源生产企业,其主要产品为焦炭和煤气。
但是,焦化过程中会产生大量的二氧化硫等有害气体,对环境和人体健康造成威胁。
因此,在焦化厂中必须采取脱硫措施。
二、脱硫工艺分类目前,常用的焦化厂脱硫工艺主要包括湿法脱硫法和干法脱硫法两种。
三、湿法脱硫工艺流程1. 燃烧前处理:将原料煤进行粉碎、筛分等处理,以提高其燃烧效率。
2. 燃烧过程:将经过预处理的原料煤放入高温反应器中进行燃烧,产生大量二氧化硫等有害气体。
3. 熄火后处理:将产生的废气通过喷淋装置喷洒液体吸收剂(如碳酸钠溶液),使其中的二氧化硫被吸收。
4. 液体再生:将吸收剂中所含有的二氧化碳等物质去除,并将其回收再利用。
5. 废水处理:将吸收剂中所含有的废水进行处理,以达到排放标准。
四、干法脱硫工艺流程1. 燃烧前处理:同湿法脱硫工艺。
2. 燃烧过程:同湿法脱硫工艺。
3. 干法脱硫:将产生的废气通过干式吸附剂(如活性炭、氧化钙等)进行吸附,使其中的二氧化硫被吸附。
4. 再生:将已经饱和的吸附剂进行再生,以去除其中的二氧化硫等物质,并回收再利用。
5. 废物处理:将已经使用过的吸附剂进行处理,以达到排放标准。
五、两种工艺比较1. 湿法脱硫工艺具有脱除效率高、适应性强等优点,但是会产生大量废水和废渣,需要进行额外的处理。
2. 干法脱硫工艺具有节能、环保等优点,但是其脱除效率相对较低。
六、结论在选择焦化厂脱硫工艺时,需要根据实际情况进行综合考虑,选择适合自己企业的工艺。
同时,需要加强废水、废渣等废物的处理,以达到环保标准。
焦化厂焦炉煤气精脱硫工艺分析与设计技术实施方案
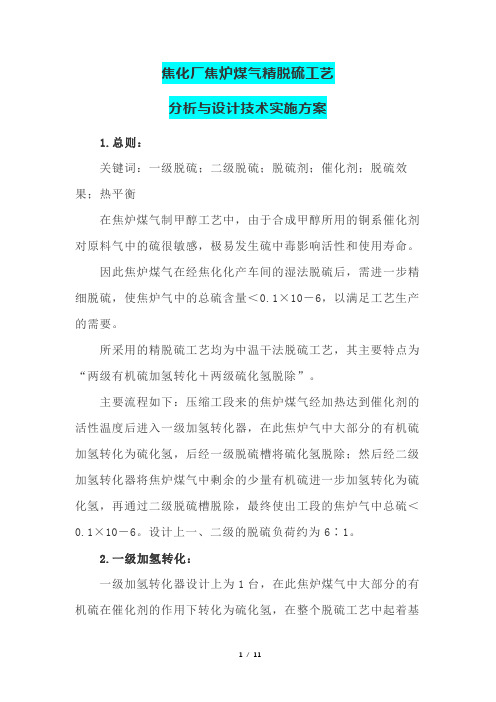
焦化厂焦炉煤气精脱硫工艺分析与设计技术实施方案1.总则:关键词:一级脱硫;二级脱硫;脱硫剂;催化剂;脱硫效果;热平衡在焦炉煤气制甲醇工艺中,由于合成甲醇所用的铜系催化剂对原料气中的硫很敏感,极易发生硫中毒影响活性和使用寿命。
因此焦炉煤气在经焦化化产车间的湿法脱硫后,需进一步精细脱硫,使焦炉气中的总硫含量<0.1×10-6,以满足工艺生产的需要。
所采用的精脱硫工艺均为中温干法脱硫工艺,其主要特点为“两级有机硫加氢转化+两级硫化氢脱除”。
主要流程如下:压缩工段来的焦炉煤气经加热达到催化剂的活性温度后进入一级加氢转化器,在此焦炉气中大部分的有机硫加氢转化为硫化氢,后经一级脱硫槽将硫化氢脱除;然后经二级加氢转化器将焦炉煤气中剩余的少量有机硫进一步加氢转化为硫化氢,再通过二级脱硫槽脱除,最终使出工段的焦炉气中总硫<0.1×10-6。
设计上一、二级的脱硫负荷约为6∶1。
2.一级加氢转化:一级加氢转化器设计上为1台,在此焦炉煤气中大部分的有机硫在催化剂的作用下转化为硫化氢,在整个脱硫工艺中起着基础性作用。
设计上一级加氢转化器选用的催化剂是铁钼加氢转化催化剂,其活性成分是氧化钼和少量的氧化铁,使用前需预先进行升温硫化才能有较好的催化活性。
实际运行表明,只要对催化剂硫化充分,生产中温度控制合适,一级加氢转化器即能够将焦炉煤气中大部分的有机硫进行加氢转化生成硫化氢,满足生产需要。
目前存在的主要问题是,大部分的甲醇生产厂家都反映催化剂的使用寿命不够理想:好的状况下可使用2年,一般的在使用1年后催化剂活性就会大大削弱,有机硫加氢转化能力降低甚至会消失,即使提高催化剂床层的运行温度也不会有大的改观。
如此增加了催化剂的更换频率和脱硫成本。
理论上催化剂的活性是不会下降或消失的,造成这种现象有多方面原因。
催化剂的生产厂家认为是催化剂在使用前硫化不彻底所致,但这并非主要原因:因为催化剂在使用过程中始终是处在一个多硫和强还原性的氛围中,即使在投用前预硫化不十分彻底,但在使用过程中也会不断地有硫化反应发生,直至硫化彻底。
焦炉烟气脱硫脱硝工艺流程
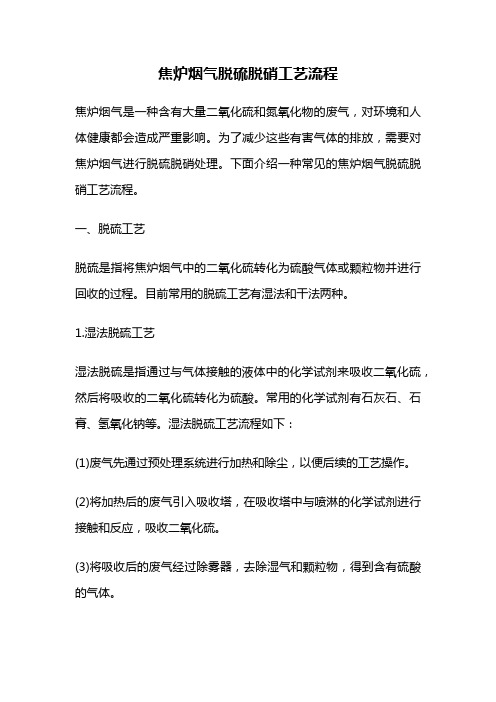
焦炉烟气脱硫脱硝工艺流程焦炉烟气是一种含有大量二氧化硫和氮氧化物的废气,对环境和人体健康都会造成严重影响。
为了减少这些有害气体的排放,需要对焦炉烟气进行脱硫脱硝处理。
下面介绍一种常见的焦炉烟气脱硫脱硝工艺流程。
一、脱硫工艺脱硫是指将焦炉烟气中的二氧化硫转化为硫酸气体或颗粒物并进行回收的过程。
目前常用的脱硫工艺有湿法和干法两种。
1.湿法脱硫工艺湿法脱硫是指通过与气体接触的液体中的化学试剂来吸收二氧化硫,然后将吸收的二氧化硫转化为硫酸。
常用的化学试剂有石灰石、石膏、氢氧化钠等。
湿法脱硫工艺流程如下:(1)废气先通过预处理系统进行加热和除尘,以便后续的工艺操作。
(2)将加热后的废气引入吸收塔,在吸收塔中与喷淋的化学试剂进行接触和反应,吸收二氧化硫。
(3)将吸收后的废气经过除雾器,去除湿气和颗粒物,得到含有硫酸的气体。
(4)最后,将含有硫酸的气体进行净化和回收,同时将剩余的废液进行处理和排放。
2.干法脱硫工艺干法脱硫是指利用固体吸收剂吸收二氧化硫,然后将吸附的硫化合物进行回收或转化为稳定的物质。
常用的固体吸收剂有活性炭、氧化铁、氧化钙等。
干法脱硫工艺流程如下:(1)废气经过预处理系统后,与喷雾的固体吸收剂进行接触和反应,吸附二氧化硫。
(2)将吸附后的固体吸收剂进行回收或转化为稳定的物质,如通过加热脱附二氧化硫。
(3)最后,将剩余的固体吸收剂进行处理和排放。
二、脱硝工艺脱硝是指将焦炉烟气中的氮氧化物转化为氮气和水的过程。
目前常用的脱硝工艺有选择性催化还原法和非选择性催化还原法两种。
1.选择性催化还原法选择性催化还原法是指将氧化剂加入焦炉烟气中,将氮氧化物转化为氮气和水。
常用的氧化剂有氨气和尿素等。
选择性催化还原法脱硝工艺流程如下:(1)预处理系统将废气进行加热和除尘。
(2)在催化剂层中,将氨气或尿素加入焦炉烟气中,氮氧化物和氨气或尿素在催化剂的作用下发生反应,生成氮气和水。
(3)最后,将剩余的氨气或尿素进行处理和回收利用。
焦炉煤气制甲醇脱硫工段初步设计
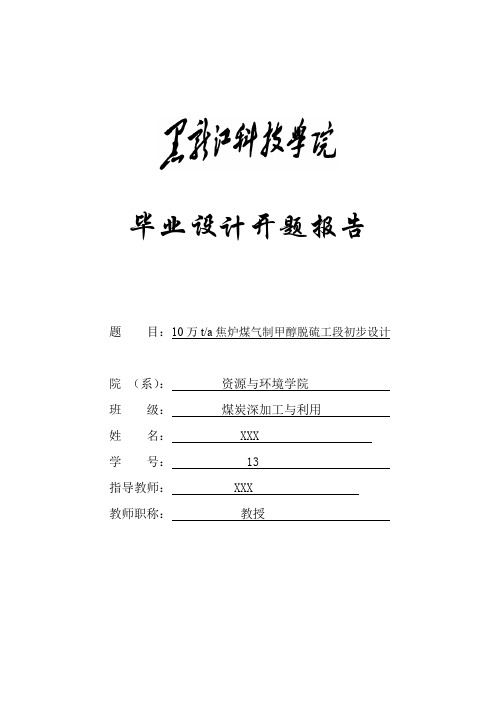
设计采用当前焦炉煤气制甲醇脱硫工段较为广泛的技术——栲胶法脱硫,对焦炉煤气脱硫技术和脱硫工艺流程进行详细的论述,对焦炉煤气脱硫流程进行深入剖析。
4、设计方案(研究/设计方法、理论分析、计算、实验方法和步骤等):
煤气的脱硫方法从总体上来分有两种:热煤气脱硫和冷煤气脱硫。在我国,冷煤气脱硫是比较成熟的技术。焦炉煤气的净化主要是要脱除煤气中的H2S,脱硫的方法有两种:干法脱硫和湿法脱硫。5 M' K3 p+ ~1 n3 s- [
③、CO2的影响
栲胶脱硫液具有相当高的选择性。在适宜的操作条件下,它能从含99℅的CO2原料气中将200mg/m3(标)的H2S脱除至45mg/m3(标)以下。但由于溶液吸收CO2后会使溶液的PH值下降,使脱硫效率稍有降低。!
(5)、脱硫工艺流程
①、半水煤气由气柜进入静电除焦塔经过电离除去大量焦油及其他杂质后送萝茨鼓风机,经过加压后送冷却塔底部与上部循环水逆流接触冷却后送脱硫塔底部,半水煤气从脱硫塔底部向上与脱硫塔顶部加入的栲胶液逆流接触进行脱硫。经过脱硫的半水煤气进入清洗塔底部与清洗塔上部加入的循环水逆流接触,清洗半水煤气中夹带的杂质与栲胶液,从清洗塔上部出来后送后工段使用。
脱硫贯穿甲醇生产的整个工艺过程。是甲醇生产的关键。
2、国内外发展情况(文献综述)
据世界卫生组织和联合国环境规划署统计,目前每年含硫燃料燃烧排放到大气中的二氧化硫超过2亿吨,已成为大气环境的首要污染物。我国是燃煤大国,随着燃煤量的增加,二氧化硫的排放量也不断增加。消减二氧化硫的排放量,防治大气二氧化硫污染已迫在眉睫,成为我国现在及未来相当长时期内的主要社会问题之一。
㈡、NaVO3含量
* M0 {0 \2 i8 ]NaVO3的含量取决于脱硫液的操作硫容,即与富液中的HS-浓度符合化学计量关系。应添加的理论浓度可与液相中HS-的摩尔浓度相当,但在配制溶液时往往要过量,控制过量系数在1.3~1.5左右。
年产180万吨焦炭焦化厂焦炉煤气脱硫工段初步设计
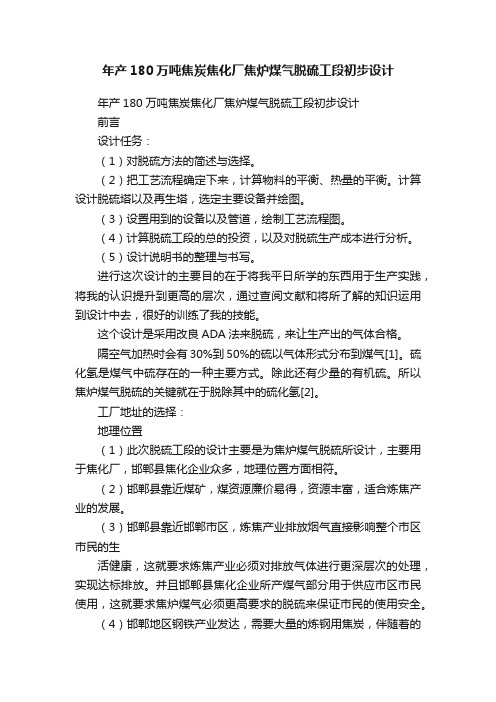
年产180万吨焦炭焦化厂焦炉煤气脱硫工段初步设计年产180万吨焦炭焦化厂焦炉煤气脱硫工段初步设计前言设计任务:(1)对脱硫方法的简述与选择。
(2)把工艺流程确定下来,计算物料的平衡、热量的平衡。
计算设计脱硫塔以及再生塔,选定主要设备并绘图。
(3)设置用到的设备以及管道,绘制工艺流程图。
(4)计算脱硫工段的总的投资,以及对脱硫生产成本进行分析。
(5)设计说明书的整理与书写。
进行这次设计的主要目的在于将我平日所学的东西用于生产实践,将我的认识提升到更高的层次,通过查阅文献和将所了解的知识运用到设计中去,很好的训练了我的技能。
这个设计是采用改良ADA法来脱硫,来让生产出的气体合格。
隔空气加热时会有30%到50%的硫以气体形式分布到煤气[1]。
硫化氢是煤气中硫存在的一种主要方式。
除此还有少量的有机硫。
所以焦炉煤气脱硫的关键就在于脱除其中的硫化氢[2]。
工厂地址的选择:地理位置(1)此次脱硫工段的设计主要是为焦炉煤气脱硫所设计,主要用于焦化厂,邯郸县焦化企业众多,地理位置方面相符。
(2)邯郸县靠近煤矿,煤资源廉价易得,资源丰富,适合炼焦产业的发展。
(3)邯郸县靠近邯郸市区,炼焦产业排放烟气直接影响整个市区市民的生活健康,这就要求炼焦产业必须对排放气体进行更深层次的处理,实现达标排放。
并且邯郸县焦化企业所产煤气部分用于供应市区市民使用,这就要求焦炉煤气必须更高要求的脱硫来保证市民的使用安全。
(4)邯郸地区钢铁产业发达,需要大量的炼钢用焦炭,伴随着的就是造成大量焦炉气。
(5)邯郸县地处邯郸地区中心位置,交通便捷,适合焦化厂的建设,同时也就需要焦炉气脱硫技术的应用。
综上所述,焦化厂设在邯郸县地区,并且与脱硫工段配套,可以达到提高生产效益的同时,能更充分的利用各项资源,实现环境保护绿色发展。
气象因素邯郸常年平均气温15℃极端温度23℃极端低温为-10℃。
,平均气压为标准大气压。
平均相对湿度为68℃。
年降水量在450~850毫米。
焦炉煤气精脱硫工艺分析

焦炉煤气精脱硫工艺分析一、工艺原理:焦炉煤气中的H2S主要通过煤气中的Fegl肟羧酸盐、CaS等吸收剂进行吸收。
Fegl肟羧酸盐是一种高效的硫化物吸收剂,可在较低的温度下将煤气中的H2S和COS吸收。
而CaS则可以将煤气中的剩余H2S去除。
二、工艺流程:1.气体预处理:首先对焦炉煤气进行预处理,去除其中的悬浮颗粒物和水分,以净化煤气。
2.前骤吸收:采用Fegl肟羧酸盐作为吸收剂,通过吸收剂床将煤气中的H2S、COS等硫化物吸收。
床层中的吸收剂会与煤气中的硫化氢进行反应,生成硫化铁,并将其捕集。
3.普鲁士蓝阳极液循环:将废液中的硫化铁氧化为硫酸铁,通过循环泵送到反应床顶部,实现循环利用。
4.精脱硫:采用CaS作为吸收剂,通过床层吸收煤气中剩余的硫化氢,并将其转化为CaS。
此过程需要保持一定的温度和压力,以促使吸收反应的进行。
5.再复焦炉:将经过精脱硫的煤气送入焦炉进行再加热,以提高炉内温度。
三、工艺特点:1.高效: 采用Fegl肟羧酸盐和CaS作为吸收剂,可以高效地吸收煤气中的硫化物,使硫化氢的去除率达到90%以上,保证煤气的质量。
2.安全:精脱硫过程中对温度和压力的要求较高,可以有效地防止硫化氢的泄漏,保证了生产环境的安全。
3.循环利用:工艺中的废液通过循环泵送到反应床顶部,实现了废液中的硫化铁的循环利用,减少了废液的排放,具有较好的环保效益。
总结起来,焦炉煤气精脱硫工艺通过床层吸收剂的反应,有效地去除焦炉煤气中的硫化氢等硫化物,以保证煤气的质量达到环保要求。
该工艺具有高效、安全、循环利用等特点,在焦化行业得到广泛应用。
工艺方法——焦炉煤气脱硫技术
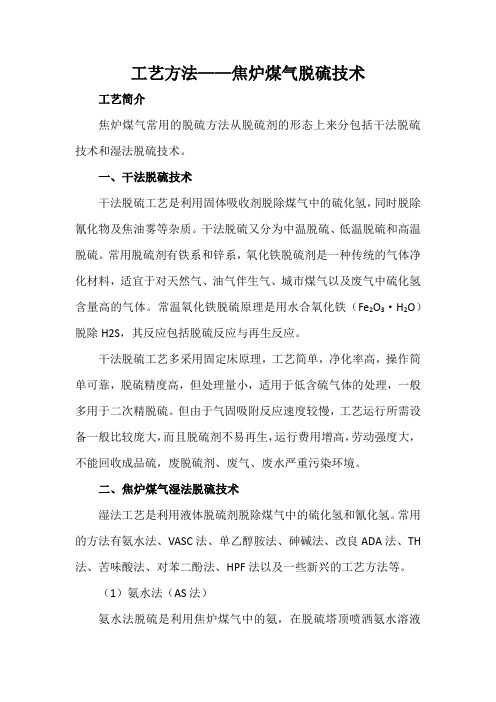
工艺方法——焦炉煤气脱硫技术工艺简介焦炉煤气常用的脱硫方法从脱硫剂的形态上来分包括干法脱硫技术和湿法脱硫技术。
一、干法脱硫技术干法脱硫工艺是利用固体吸收剂脱除煤气中的硫化氢,同时脱除氰化物及焦油雾等杂质。
干法脱硫又分为中温脱硫、低温脱硫和高温脱硫。
常用脱硫剂有铁系和锌系,氧化铁脱硫剂是一种传统的气体净化材料,适宜于对天然气、油气伴生气、城市煤气以及废气中硫化氢含量高的气体。
常温氧化铁脱硫原理是用水合氧化铁(Fe2O3·H2O)脱除H2S,其反应包括脱硫反应与再生反应。
干法脱硫工艺多采用固定床原理,工艺简单,净化率高,操作简单可靠,脱硫精度高,但处理量小,适用于低含硫气体的处理,一般多用于二次精脱硫。
但由于气固吸附反应速度较慢,工艺运行所需设备一般比较庞大,而且脱硫剂不易再生,运行费用增高,劳动强度大,不能回收成品硫,废脱硫剂、废气、废水严重污染环境。
二、焦炉煤气湿法脱硫技术湿法工艺是利用液体脱硫剂脱除煤气中的硫化氢和氰化氢。
常用的方法有氨水法、VASC法、单乙醇胺法、砷碱法、改良ADA法、TH 法、苦味酸法、对苯二酚法、HPF法以及一些新兴的工艺方法等。
(1)氨水法(AS法)氨水法脱硫是利用焦炉煤气中的氨,在脱硫塔顶喷洒氨水溶液(利用洗氨溶液)吸收煤气中H2S,富含H2S和NH3的液体经脱酸蒸氨后再循环洗氨脱硫。
在脱硫塔内发生的氨水与硫化氢的反应是:H2S+2NH3·H2O→(NH4)2S+2H2O。
AS循环脱硫工艺为粗脱硫,操作费用低,脱硫效率在90%以上,脱硫后煤气中的H2S在200-500mg·m-3。
(2)VASC法VASC法脱硫过程是洗苯塔后的煤气进入脱硫塔,塔内填充聚丙烯填料,煤气自下而上流经各填料段与碳酸钾溶液逆流接触,再经塔顶捕雾器出塔。
煤气中的大部分H2S和HCN和部分CO2被碱液吸收,碱液一般主要是Na2CO3或K2CO3溶液。
吸收了酸性气体的脱硫富液与来自再生塔底的热贫液换热后,由顶部进入再生塔再生,吸收塔、再生塔及大部分设备材质为碳钢,富液与再生塔底上升的水蒸汽接触使酸性气体解吸。
焦炉煤气脱硫方案

焦炉煤气脱硫方案
一.工艺选择
由于焦炉煤气中含硫化氢较高,出口要求硫化氢含量又较低,因此本工艺选择湿式催化法和干式吸附法相结合的工艺方法以确
保脱硫效率合格率98%以上。
二.主要工艺参数
脱硫气量:13000NM3
进口煤气硫化氢含量:≤5000mg/NM3
出口煤气硫化氢含量:≤50mg/NM3
进口煤气温度:≤30℃
三.脱硫工艺流程
见附图
四.主要设备的规格参数和估算重量
序号名称规格数量重量(T) 备注
1 脱硫塔Φ2.6*27m
2 30*2不含填料150M3
2 清洗塔Φ2.0*16m 113.2
3再生槽Φ6.5/Φ7.5*9m 138
4喷射器XJs-2 21
5 富液槽80M315.1或混凝土
6制备槽Φ1.6*1.6m 10.3
7贫液槽80M315.1或混凝土
8熔硫釜Φ1.0*3.8m 13.5其中不锈钢2吨9泡沫泵Q=30 H=40 1
10 脱硫泵Q=370H=45 4 各一开一备
11再生泵Q=370H=60 3 二开一备
12水封Φ0.630.35*3
13精脱硫塔Φ7.2*12.9m 132.2不含脱硫剂80M314安装管道、阀门、电器、仪表、爬梯、平台等另计。
煤气WSA法(湿法硫酸)脱硫工艺

在煤气化厂 ⑴ 上海焦化厂 (中国),规模, 40 吨/日; ⑵ 柳州化肥厂 (中国),规模, 50 吨/日; ⑶ VFT n.v (比利时),规模,4 吨/日; ⑷ Krupp-Koppers ARAL Aromatics GMbH (德国), 8 吨/日; ⑸ Babcock King-Wilkinson Ltd (威尔士),规模,11 吨/日; ⑹ Daelim Engineering Co., Ltd(南韩 ),规模,4 吨/日。 ⑺ Sasol Synfuels (Pty) Ltd., Secunda (南非)
-4-
工艺气体离开冷凝器的温度约 100C,能直接送入烟道,排放的 SO2 浓度控制在 960mg/Nm 以下, 低于国家环保排放标准 GB16297-1996 二氧化硫的排放要求。WSA 冷凝器的一个很显著的特点就是, 气体中含酸雾极少。 冷却空气离开 WSA 冷凝器的温度约 200C, 部分热空气作为焚烧炉的燃烧气, 其余可与工艺气混 合送入烟道增加浮力排出或用于锅炉水预热。 由于来自焦炉煤气真空碳酸钾洗的含硫气体,很多含有大量的 HCN,在焚烧炉中生成氮氧化物 NOX,要脱除氮氧化物,可通过在 SO2 反应器上游引入一个 SCR 反应器,来脱除在焚烧炉后流出气体 中的氮氧化物。这种情况下,在 SCR 反应器的上游要注入化学计量量的氨。 反应器中热回收为蒸汽。通常,为避免腐蚀锅炉,废热锅炉产生蒸汽最低在 35-40kg。 除了在设计温度要求是耐热钢材(不锈钢或钼合金),构造材料一般均是碳钢。燃烧室和废热 锅炉内部有耐火衬里保护。接触冷凝酸的冷凝器部分,有氟聚合物衬里保护。底部部分是耐酸砖衬 里。酸冷却器通常是由哈司特镍合金 C 制成。 装置处理含有水蒸气的气体,在 SO2 转化前不需要进行冷却/冷凝工艺,因此,不产生液体流出 物,没有废水、废液、废固等二次污染物产生。
年产180万吨焦炭焦化厂焦炉煤气脱硫工段初步设计

年产180万吨焦炭焦化厂焦炉煤气脱硫工段初步设计1. 引言煤气脱硫是焦化厂的关键环节之一,其目的是去除焦炉煤气中的硫化氢(H2S)等有害气体,以保护环境和提高产品质量。
本文档将对年产180万吨焦炭焦化厂焦炉煤气脱硫工段进行初步设计。
2. 工艺流程脱硫工段的工艺流程如下:1.煤气进入煤气清洗塔进行初步清洗,去除煤炭中的颗粒物和部分硫化氢。
2.清洗后的煤气流入脱硫塔,在脱硫塔中接触脱硫剂(一般为氨水或氨碱溶液),使硫化氢与脱硫剂发生反应生成硫化铵,从而达到脱硫效果。
3.脱硫后的煤气经过精细处理,去除残余的脱硫剂和吸收剂,以及其他有害气体。
4.经过处理后的煤气可进入煤气发电机组进行发电,或者作为其他用途的能源。
以下是工艺流程的示意图:脱硫工艺流程图脱硫工艺流程图3. 设备选型3.1 煤气清洗塔煤气清洗塔主要用于去除煤炭中的颗粒物和部分硫化氢。
选用耐腐蚀性能好、操作稳定可靠的材料制作,如不锈钢。
具体参数如下:•高度:10米•直径:5米•进气温度:150℃•进气流量:10,000 Nm3/h•去除颗粒物效率:>90%•去除硫化氢效率:>50%3.2 脱硫塔脱硫塔是脱硫工艺的核心设备,需要选用具有良好脱硫效果和操作稳定性的设备。
常见的脱硫剂有氨水和氨碱溶液。
具体参数如下:•高度:15米•直径:6米•进气温度:120℃•进气流量:8,000 Nm3/h•脱硫效率:>90%•脱硫剂浓度:10-15%3.3 精细处理设备精细处理设备用于去除脱硫后煤气中的残余脱硫剂和吸收剂,以及其他有害气体。
具体参数如下:•高度:10米•直径:4米•进气温度:80℃•进气流量:6,000 Nm3/h•残余脱硫剂去除效率:>95%•残余吸收剂去除效率:>90%4. 控制策略为了保证脱硫工段的稳定运行,需要设计合理的控制策略。
以下是脱硫工段的基本控制策略:1.温度控制:监测进气温度和出口温度,保持适当的温度范围,以保证反应效果和设备的安全运行。
焦化煤气PDS法脱硫
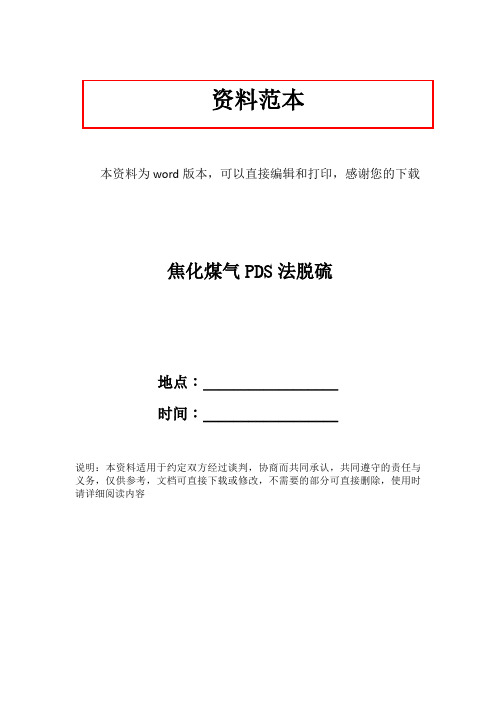
资料范本本资料为word版本,可以直接编辑和打印,感谢您的下载焦化煤气PDS法脱硫地点:__________________时间:__________________说明:本资料适用于约定双方经过谈判,协商而共同承认,共同遵守的责任与义务,仅供参考,文档可直接下载或修改,不需要的部分可直接删除,使用时请详细阅读内容煤气中的硫绝大部分以H2S的形式存在,而H2S随煤气燃烧后转化成SO2,空气中SO2含量超标会形成局域性酸雨,危害人们的生存环境,我国对燃烧发生炉煤气炉窑规定其SO2的最高排放浓度为900mg/m3;另一方面,SO2对诸如陶瓷、高岭土等行业的最终产品质量影响较大,鉴于以上因素,发生炉煤气中H2S的脱除程度业已成为其洁净度的一个重要指标。
1、煤气脱硫方法发生炉煤气中的硫来源于气化用煤,主要以H2S形式存在,气化用煤中的硫约有80%转化成H2S进入煤气,假如,气化用煤的含硫量为1%,气化后转入煤气中形成H2S大约2-3g/Nm3左右,而陶瓷、高岭土等行业对煤气含硫量要求为20-50mg/Nm3;假如煤气中的H2S燃烧后全部转化成SO2为2.6g/m3左右,比国家规定的SO2的最高排放浓度指标高出许多。
所以,无论从环保达标排放,还是从保证企业最终产品质量而言,煤气中这部分H2S都是必须要脱除的。
煤气的脱硫方法从总体上来分有两种:热煤气脱硫和冷煤气脱硫。
在我国,热煤气脱硫现在仍处于试验研究阶段,还有待于进一步完善,而冷煤气脱硫是比较成熟的技术,其脱硫方法也很多。
冷煤气脱硫大体上可分为干法脱硫和湿法脱硫两种方法,干法脱硫以氧化铁法和活性炭法应用较广,而湿法脱硫以砷碱法、ADA、改良ADA和栲胶法颇具代表性。
2、干法脱硫技术煤气干法脱硫技术应用较早,最早应用于煤气的干法脱硫技术是以沼铁矿为脱硫剂的氧化铁脱硫技术,之后,随着煤气脱硫活性炭的研究成功及其生产成本的相对降低,活性炭脱硫技术也开始被广泛应用。
湿法脱硫操作规程样本

脱硫岗位操作规程1、生产工艺流程概述从洗脱苯来约30—35℃焦炉煤气串联进入脱硫塔(A、B)下部,与塔顶喷淋下来脱硫液逆流接触进行洗涤,并发生化学反映,从而使煤气中硫化氢脱除,脱硫后煤气送往各顾客。
脱硫塔下部液位通过脱塔液封槽高度来进行控制。
由脱硫塔液封槽流出脱硫液进入富液槽。
脱硫富液由富液泵加压后经溶液换热器进行换热(冬季加热,夏季冷却),温度控制约为35℃,然后进入喷射氧化再生槽。
脱硫液在通过喷射器时,靠自身压力将空气吸入并进入再生槽底部。
在再生槽内,空气与脱硫液充分接触并发生化学反映,形成硫泡沫,从而使脱硫液得到再生。
由于硫泡沫比重比脱硫液轻,硫泡沫漂浮在脱硫槽中脱硫液液面上,随脱硫液一起流入再生槽环隙中并在此靠重力进行分离。
再生槽环隙液位是靠液位调节器进行控制,通过调节环隙液位高度,从而只使硫泡沫溢流到硫泡沫室。
分离了硫泡沫脱硫液为贫液,贫液经液位调节器后流入贫液槽中。
脱硫液所使用脱硫剂为纯碱,定期将纯碱加入到配碱槽中,加水、加热、搅拌,溶化后由碱液泵送至贫液槽。
同步,脱硫所使用催化剂PDS+对苯二酚也在碱液槽中进行配制,并送入贫液槽中,与纯碱一起补加到系统中。
脱硫贫液由贫液泵加压后,分别送至脱硫塔上部,再次对焦炉煤气进行洗涤脱硫。
由喷射氧化再生槽浮选出硫泡沫自动流入硫泡沫槽,在此经搅拌、加热、沉降、分离后,硫泡沫经硫泡沫泵加压后送至熔硫釜持续进行熔硫,生产硫磺外售。
由熔硫釜排出清液溢流进入缓冲槽。
然后由碱液泵送至富液槽,循环使用。
2、岗位职责和任务2.1 负责本岗位所有设备、管道装置正常运营。
2.2 稳定系统生产操作,保证脱硫后煤气硫化氢含量达到技术规定(≤20mg/Nm3)。
2.3 负责各运转设备开停车操作,并调节其流量、压力、温度,使其符合工艺指标;浮现异常及时报告并做出相应应急解决。
2.4 控制好各槽体液位和溶液换热器出口脱硫液温度;依照生产需要稳定循环量,控制好再生槽环隙液位,通过液位调节器操作,保证硫泡沫正常分离。
第五节焦炉煤气脱硫脱氰

第五节 焦炉煤气脱硫脱氰焦炉煤气中含硫化氢4~8g /m 3,氰化氢0.5~2g /m 3。
两者都是有害杂质,既腐蚀设备,又污染环境,危害人体健康。
因此,焦炉煤气必须脱硫脱氰。
目前,世界各国对焦炉煤气中硫化氢和氰化氢的含量作了限制,规定焦炉煤气用于冶炼优质钢时,硫化氢允许含量为1~2g /m 3;用作城市煤气时,硫化氢允许含量低于20mg /m 3,氰化氢含量低于5.0mg /m 3;供化工合成工业时,硫化氢允许含量为1~2mg /m 3。
焦炉煤气脱硫脱氰有干法和湿法两种工艺。
一、干法脱硫干法脱硫是一种比较古老的脱硫方法。
这种方法的工艺和设备都比较简单,操作和维修也比较容易,至今一些小焦化厂仍在使用。
但该法为间歇操作,占地面积大,脱硫剂的更换和再生工作的劳动强度大,现代化的大型焦化厂已不再采用。
干法脱硫通常以氢氧化铁为脱硫剂。
当焦炉煤气通过脱硫剂时,煤气中的硫化氢与氢氧化铁接触,生成硫化铁,这是吸收反应。
硫化铁与煤气中氧接触,在有水分的条件下,硫化铁转化为氢氧化铁并析出元素硫,这是再生反应。
干法脱硫的过程就是吸收反应和再生反应的多次循环。
其反应式为:Fe 2O 3·H 2O+3H 2S→Fe 2S·H 2O+3H 2OFe 2S 3·H 2O+23O 2→Fe 2O 3·H 2O+3S 干法脱硫的主要设备有箱式和塔式两种。
箱式脱硫器如图4-18所示。
它是用钢板焊制或用钢筋混凝土制成的长方形箱体,内壁涂沥青或沥青漆。
为了防止漏气,箱盖做成水封式,或用由螺栓压紧的橡皮垫圈密封。
箱高1. 5~2m ,箱内水平木格上装有四层脱硫剂,每层厚0. 3~0. 4m ,上下各留有空间,使气流分布均匀图4-18 箱式脱硫器塔式脱硫器如图4-18所示。
它是由钢板制成的直立圆筒,直径为6~9m ,高为12~18m 。
塔内叠置10~14个吊筐,筐中央留有圆孔,上下连接形成一条圆形直立通道。
焦炉煤气湿法脱硫工艺及进展
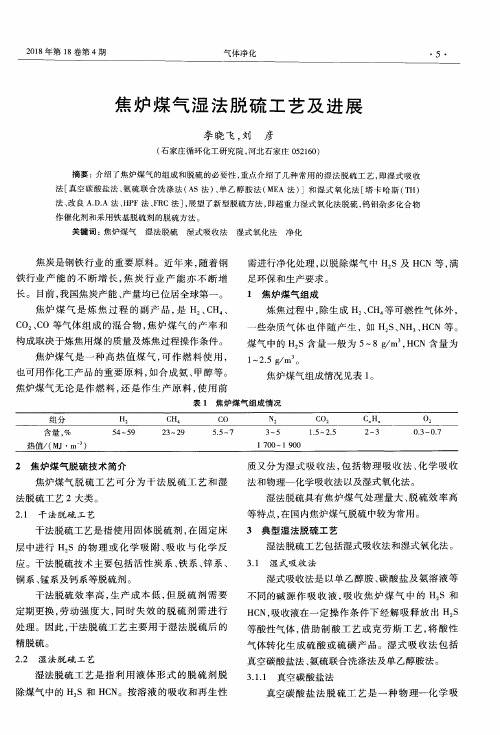
焦 炭是 钢铁 行 业 的重 要 原料 。近 年来 ,随 着 钢 需 进行净 化处 理 ,以脱 除 煤气 中 H,s及 HCN等 ,满
铁行 业 产 能 的不 断 增 长 ,焦 炭 行 业 产 能 亦 不 断 增 足环 保 和生产 要求 。
HCN,吸收 液在 一 定 操 作 条件 下 经 解 吸释 放 出 H。S 等酸性 气 体 ,借 助 制 酸 工 艺 或 克 劳 斯 工 艺 ,将 酸性 气体转 化 生 成 硫 酸 或 硫 磺 产 品 。湿 式 吸 收 法 包 括 真空碳 酸 盐法 、氨硫 联合洗 涤 法及单 乙醇胺法 。 3.1.1 真空 碳 酸盐法
硫 含 量较 高 的气 体 。该 法 脱 硫 操 作环 境 差 ,回收 的 水杨 酸 络合 盐 用 作 FD 法 的脱 硫 剂 ,该 工 艺 已经 应
硫 磺 质量 较差 ,收率 低 。
用 于工业 生产 。
3.2.4 FRC法
5 结 语
FRC法 是 以 2,4,6一三硝 基 苯 酚 (苦 味 酸 )作 为
源 ,苦 味酸 为催 化剂 ,来脱 除煤 气 中 的 H:s和 HCN。 煤 气制 甲醇 对焦 炉 煤气 洁净 度 要 求 较 高 ,故 需 要 脱
焦炉 煤 气 是 一 种 高 热 值 煤 气 ,可 作 燃 料 使 用 , 也可用作化工产品的重要原料 ,如合成氨 、甲醇等。 焦 炉煤 气 无 论 是 作 燃 料 ,还 是 作 生 产 原 料 ,使 用 前
1~2.5 m 。
焦炉 煤气组 成 情况见 表 1。
表 1 焦 炉 煤 气 组成 情 况
定 期更 换 ,劳 动 强 度 大 ,同 时 失 效 的脱 硫 剂 需 进 行 处 理 。 因此 ,干 法脱 硫 工 艺 主 要 用 于 湿法 脱 硫 后 的 精 脱硫 。
焦炉煤气脱硫工艺选择与方案设计

焦炉煤气脱硫工艺选择与方案设计摘要:随着工业化进程的不断加快,煤炭等化石能源的使用量也在不断增加,而煤炭的燃烧会产生大量的二氧化硫等有害气体,对环境和人类健康造成严重的影响。
因此,煤气脱硫技术的研究和应用变得越来越重要。
目前,焦炉煤气脱硫技术已经得到广泛应用,但是不同的脱硫工艺有着不同的优缺点,如何选择合适的脱硫工艺并设计出最优方案,成了研究的重点。
关键词:焦炉煤气;脱硫工艺;方案设计1焦炉煤气脱硫工艺对比分析目前,在实际应用中具有代表性的脱硫工艺包括 A.S 法煤气脱硫工艺、HPF 法脱硫工艺以及碳酸钠+PDS脱硫工艺。
(一)A.S 法煤气脱硫工艺A.S 法煤气脱硫工艺是一种常用的焦炉煤气脱硫技术,其主要原理是利用氨水与二氧化硫反应生成硫酸铵,从而达到脱硫的目的。
主要流程包括:氨水喷淋、反应吸收、过滤分离、再生吸收等步骤:将氨水喷淋到煤气中,与二氧化硫发生反应,生成硫酸铵;将含有硫酸铵的煤气进入吸收塔中,与吸收液进行反应吸收,使二氧化硫被吸收;将吸收液中的硫酸铵和水分离出来,得到含有硫酸铵的液体;将含有硫酸铵的液体进入再生塔中,通过加热和通入空气的方式,使硫酸铵分解为二氧化硫和氨水,再次用于煤气脱硫。
A.S 法煤气脱硫工艺能够将煤气中的二氧化硫脱除率达到90%以上,脱硫效率高。
该工艺适用于各种煤气,包括高温、高湿、高硫等煤气,具有很好的适应性。
且操作简单,设备投资和运行成本低,易于维护和管理。
同时不会产生二次污染,对环境友好,同时也能够回收利用氨水和硫酸铵,节约能源和资源。
(二)HPF 法脱硫工艺HPF法脱硫工艺是一种高效的焦炉煤气脱硫技术,其全称为高压喷雾吸收法该工艺主要通过高压喷雾将煤气中的SO2与水溶液中的氢氧化钠反应生成硫酸钠,从而达到脱硫的目的。
HPF法脱硫工艺的优点在于其脱硫效率高、操作简单、设备投资少、运行费用低等方面。
同时,该工艺对煤气中的其他污染物也具有一定的去除效果,如NOx、HC l等。
焦炉煤气湿法脱硫工艺设计初样

1 绪 论1.1概述焦炉煤气粗煤气中硫化物按其化合态可分为两类:无机硫化物,主要是硫化氢(H 2S ),有机硫化物,如二硫化碳(2CS ),硫氧化碳(COS ),硫醇(25C H SH )和噻吩(44C H S )等。
有机硫化物在温度下进行变换时,几乎全部转化为硫化氢。
所以煤气中硫化氢所含的硫约占煤气中硫总量的90%以上,因此,煤气脱硫主要是指脱除煤气中的硫化氢,焦炉煤气中含硫化氢8~15g/m 3,此外还含0.5~1.5g/m 3氰化氢。
硫化氢在常温下是一种带刺鼻臭味的无色气体,其密度为1.539kg/nm 3。
硫化氢及其燃烧产物二氧化硫(2SO )对人体均有毒性,在空气中含有0.1%的硫化氢就能致命。
煤气中硫化氢的存在会严重腐蚀输气管道和设备,如果将煤气用做各种化工原料气,如合成氨原料气时,往往硫化物会使催化剂中毒,增加液态溶剂的黏度,影响产品的质量等。
因此,必须进行煤气的脱硫。
1.2焦炉煤气净化的现状煤气的脱硫方法从总体上来分有两种:热煤气脱硫和冷煤气脱硫。
在我国,热煤气脱硫现在仍处于试验研究阶段,还有待于进一步完善,而冷煤气脱硫是比较成熟的技术,其脱硫方法也很多。
冷煤气脱硫大体上可分为干法脱硫和湿法脱硫两种方法,干法脱硫以氧化铁法和活性炭法应用较广,而湿法脱硫以砷碱法、ADA 、改良ADA 和栲胶法颇具代表性。
湿法脱硫可以处理含硫量高的煤气,脱硫剂是便于输送的液体物料,可以再生,且可以回收有价值的元素硫,从而构成一个连续脱硫循环系统。
现在工艺上应用较多的湿法脱硫有氨水催化法、改良蒽醌二磺酸法(A.D.A 法)及有机胺法。
其中改良蒽醌二磺酸法的脱除效率高,应用更为广泛。
但此法在操作中易发生堵塞,而且药品价格昂贵,近几年来,在改良A.D.A 的基础上开发的栲胶法克服了这两项缺点。
它是以纯碱作为吸收剂,以栲胶为载氧体,以2NaVO 为氧化剂。
基于此,在焦炉煤气脱硫工艺的设计中我采用湿式栲胶法脱硫工艺。
- 1、下载文档前请自行甄别文档内容的完整性,平台不提供额外的编辑、内容补充、找答案等附加服务。
- 2、"仅部分预览"的文档,不可在线预览部分如存在完整性等问题,可反馈申请退款(可完整预览的文档不适用该条件!)。
- 3、如文档侵犯您的权益,请联系客服反馈,我们会尽快为您处理(人工客服工作时间:9:00-18:30)。
1 绪 论1.1概述焦炉煤气粗煤气中硫化物按其化合态可分为两类:无机硫化物,主要是硫化氢(H 2S ),有机硫化物,如二硫化碳(2CS ),硫氧化碳(COS ),硫醇(25C H SH )和噻吩(44C H S )等。
有机硫化物在温度下进行变换时,几乎全部转化为硫化氢。
所以煤气中硫化氢所含的硫约占煤气中硫总量的90%以上,因此,煤气脱硫主要是指脱除煤气中的硫化氢,焦炉煤气中含硫化氢8~15g/m 3,此外还含0.5~1.5g/m 3氰化氢。
硫化氢在常温下是一种带刺鼻臭味的无色气体,其密度为1.539kg/nm 3。
硫化氢及其燃烧产物二氧化硫(2SO )对人体均有毒性,在空气中含有0.1%的硫化氢就能致命。
煤气中硫化氢的存在会严重腐蚀输气管道和设备,如果将煤气用做各种化工原料气,如合成氨原料气时,往往硫化物会使催化剂中毒,增加液态溶剂的黏度,影响产品的质量等。
因此,必须进行煤气的脱硫。
1.2焦炉煤气净化的现状煤气的脱硫方法从总体上来分有两种:热煤气脱硫和冷煤气脱硫。
在我国,热煤气脱硫现在仍处于试验研究阶段,还有待于进一步完善,而冷煤气脱硫是比较成熟的技术,其脱硫方法也很多。
冷煤气脱硫大体上可分为干法脱硫和湿法脱硫两种方法,干法脱硫以氧化铁法和活性炭法应用较广,而湿法脱硫以砷碱法、ADA 、改良ADA 和栲胶法颇具代表性。
湿法脱硫可以处理含硫量高的煤气,脱硫剂是便于输送的液体物料,可以再生,且可以回收有价值的元素硫,从而构成一个连续脱硫循环系统。
现在工艺上应用较多的湿法脱硫有氨水催化法、改良蒽醌二磺酸法(A.D.A 法)及有机胺法。
其中改良蒽醌二磺酸法的脱除效率高,应用更为广泛。
但此法在操作中易发生堵塞,而且药品价格昂贵,近几年来,在改良A.D.A 的基础上开发的栲胶法克服了这两项缺点。
它是以纯碱作为吸收剂,以栲胶为载氧体,以2NaVO 为氧化剂。
基于此,在焦炉煤气脱硫工艺的设计中我采用湿式栲胶法脱硫工艺。
1.3栲胶的认识栲胶是由植物的皮,果,茎及叶的萃取液熬制而成的。
其主要成分为丹宁,约占66%,以栲胶来配制脱硫液效果最佳。
栲胶的主要成分为多种水解丹宁,是有许多结构相似的酚类衍生物所组成的多酚基化合物,由于其含有许多活泼的烃基,所以具有很强的吸氧能力,在脱硫过程中起着载氧的作用。
碱性栲胶脱硫液是由栲胶,碳酸钠及偏钒酸钠等主要成分构成的水溶液。
栲胶水溶液在空气中易被氧化,即丹宁中较活泼的羟基易被空气中的氧氧化,生成醌态化合物。
特别是当溶液的PH 值大于9的时候,丹宁的氧化特别显著。
由于栲胶水溶液在较高浓度时成为典型的胶体溶液,并且在较低温度时容易出现3NaVO 及3NaHCO 沉淀,因此在配制脱硫液前必须对栲胶水溶液进行熟化预处理。
即将含栲胶20~33g/l ,Na 2CO 3380~133g/l 的栲胶谁溶液直接通蒸汽与空气,在80~90°C 的条件下氧化10~24h ,破坏其胶性。
然后加3NaVO 及软水或稀氨水,配制成含栲胶1.0~2.6g/l ,Na 2CO 3 22.3g/l ,3NaHCO 3.24 g/l, 3NaVO 2~2.5g/l 脱硫液,送入脱硫液储存槽,稀释后使用。
脱硫过程中,酚类物质经空气再生氧化成醌态,因其具有较高电位,故能将低价钒氧化成高价钒,进而使吸收在溶液中的硫氢根氧化、析出单质硫。
同时丹宁能与多种金属离子(如钒、铬、铝等)形成水溶性络合物;在碱性溶液中丹宁能用与铁、铜反应并在其材料表面形成丹宁酸性薄膜,因而具有防腐蚀作用。
由于栲胶水溶液是胶体溶液,在将其配制成脱硫液之前,必须对其进行预处理,以消除共胶体性和发泡性,并使其由酚态结构氧化成醌态结构,这样脱硫溶液才具有活性。
在栲胶溶液氧化过程中,伴随着吸光性能的变化。
当溶液充分氧化后,其消光值则会稳定在某一数值附近,这种溶液就能满足脱硫要求。
通常制备栲胶溶液的预处理条件列举在表1中:表1 制备栲胶溶液的与处理条件将纯碱溶液用蒸汽加热,通入空气氧化,并维持温度80~90℃,恒温10h以上,让丹宁物质发生降解反应,大分子变小,表面活性物质变成非表面活性物质,达到预处理目的。
栲胶法脱硫工艺,将碱性栲胶溶液打入溶液循环槽,自循环槽出来,经过滤加压后S,由裂脱塔出来的溶液进入裂脱再生塔,再生好的进入系统的裂脱塔,吸收气体中的H2溶液由塔底流到溶液循环槽,经过滤加压循环使用。
脱硫溶液从循环槽出来后经过滤加S,由变脱塔出来的溶液进入变脱溶液再生塔,再生好的压送到变脱塔,吸收气体中的H2溶液由变脱再生塔出来,进入变脱溶液循环槽,再经过滤加压,如此循环使用。
1.4 栲胶法脱硫的优缺点1.4.1优点栲胶法脱硫是目前工业化生产中应用较多的湿式脱硫方法,它本身有许多优越之处,但是与此同时,也存在着许多的不足。
栲胶是聚酚类(丹宁)物质,可替代ADA作为载氧体,价格低廉,栲胶本身还是良好的络合剂,不需要添加酒石酸钾钠的络合剂。
此法的吸收效果与ADA相近,且具有不容易堵塞脱硫塔填料,栲胶资源丰富,价格便宜以及脱硫液活性好,性能稳定,腐蚀性小等优点。
此外,脱硫效率大于98℅,所析出的硫容易浮选和分离。
栲胶法脱硫整个脱硫和再生过程为连续在线过程,脱硫与再生同时进行,不需要设置备用脱硫塔。
煤气脱硫净化程度可以根据企业需要,通过调整溶液配比调整,适时加以控制,净化后煤气中S含量稳定。
H2(1)栲胶资源丰富、价格低廉、无毒性、脱硫溶液成本低,因而操作费用要改良ADA法低。
(2)脱硫溶液的活性好、性能稳定、腐蚀性小。
栲胶本身既是氧化剂,又是钒的络合剂,脱硫溶液的组成比改良ADA法简单,且脱硫过程没有硫磺堵塔问题。
(3)脱硫效率大于98℅,所析出的硫容易浮选和分离。
(4)栲胶法脱硫整个脱硫和再生过程为连续在线过程,脱硫与再生同时进行,不需要设置备用脱硫塔。
(5)煤气脱硫净化程度可以根据企业需要,通过调整溶液配比调整,适时加以控制,净S含量稳定。
化后煤气中H21.4.2缺点(1)配制脱硫液和往系统中补加时都要经过加热溶化制备过程。
(2)设备较多,工艺操作也较复杂,设备投资较大。
1.4.3硫化物对作为原料气生产工艺过程有何危害(1)对催化剂的危害硫使甲烷化催化剂,高(中)温变换催化剂,甲醇合成催化剂何氨合成催化剂的主要毒物之一,能使它们的活性和寿命降低;(2)对产品质量的危害碳铵生产过程中,当变换气中硫化氢含量高时,在碳化母液中积累增高。
使母液粘度增大,碳铵结晶变油,不仅造成分离困难,同时,由于生成FeS沉淀致使碳铵颜色变黑;(3)在尿素生产过程中,硫化氢进入尿素合成塔时会生成硫脲,污染尿素产品,降低产品质量;(4)对铜洗操作的危害铜氨液吸收硫化氢生成C uS沉淀,这种沉淀物颗粒很细,悬浮在溶液中导致溶液粘度增大,发泡性增强,铜耗上升,破坏铜洗系统的正常运行;(5)对金属腐蚀硫化氢能使碳钢设备及管线发生失重腐蚀,应力腐蚀,氢脆和氢鼓泡,使设备及管线寿命减短;S,(6)对人体的毒害硫化氢是强烈的神经毒物,接触人的呼吸道粘膜后,即分解成Na2加之本身的酸性对人体的呼吸道粘膜有明显的刺激作用。
硫化氢经呼吸系统进入血液中来不及氧化时就会引起会全身中毒反应,随硫化氢浓度的增加会造成呼吸麻痹,窒息以致停止呼吸而死亡。
因此,为了提高企业最终产品质量和保持人们优良的生存环境,对粗煤气进行脱硫是非常必要的。
1.4.4粗煤气脱硫系统的正常开车操作要点(1)检查各设备,管道,阀门,分析取样及电器,仪表等,必须正常完好。
(2)检查系统内所有阀门的开关位置,应符合开车要求;(3)与供水,供电,供气部门及造气,压缩工段联系,作好开车准备;(4)将脱硫液成分调整在工艺指标范围内;(5)氨规程进行系统吹净,清洗,试漏和置换工作(系统未经检修处于保压状况下对的开车,不进行该项工作);(6)调净气柜出口水封积水;(7)开启各气体冷却塔和清洗塔进水阀,并调节好水量及各塔液位;(8)开启贫液泵进口阀,启动贫液泵,向脱硫塔打入脱硫液,并调节好液位;(9)开启富液泵进口阀,启动富液泵,向再生槽送液;(10)根据脱硫液循环量和再生液槽液位,调节好贫液泵,富液泵的打液量,并控制好贫液槽,富液槽液位计流量;(11)开启罗茨鼓风机,并调节好粗煤气流量;(12)根据粗煤气流量大小,调节好液气比。
适当开启清洗塔,放空阀,焦炉煤气脱硫合格后,与压缩工段联系,并关闭放空阀,向压缩机一段送气;(13)根据再生槽的硫泡沫形成情况,调节液位调节器,保持硫泡沫的正常溢流;(14)分析粗煤气中氧含量合格后,开启静电除焦油塔。
1.4.5脱硫后硫化氢含量高的主要原因(1)进入系统的粗煤气中硫化氢含量过高,或进塔粗煤气气量过大;(2)脱硫液循环量小;(3)脱硫液成分不当;(4)脱硫液再生效率低或悬浮硫含量高;(5)进脱硫塔的粗煤气或贫液温度高;(6)脱硫塔内气液偏流,影响脱硫效率;1.4.6脱硫后硫化氢含量高的处理方法(1)联系造气工段更换含硫量低的煤炭,降低进脱硫系统粗煤气中的硫化氢含量或适当减少粗煤气气量;(2)适当加大脱硫液循环量;(3)把脱硫液成分调整扫工艺指标要求范围内;(4)检修喷射再生器或适当提高溶液进再生器的压力,增加自吸空气量,提高溶液的再生凶案绿;检修离心机滤网,减少漏泡沫量,增加再生槽硫泡沫的溢流量,减少溶液中悬浮硫含量;(5)加大气体冷却器的冷却水,降低进系统粗煤气温度;(6)检查清理脱硫塔喷头及填料,确定气液分布均匀。
1.5 设计任务的依据工艺参数:粗煤气入吸收塔时H2S的含量,C1=10 g/m3净化气中H2S的含量,C2=0.15 g/m3入吸收塔焦炉煤气量,G= 24000m3/h入冷却塔焦炉煤气温度,t1=50 ℃出冷却塔入吸收塔焦炉煤气温度,t2=35 ℃入吸收塔焦炉煤气压力,1.39atm(表)设计目标:净化煤气中H2S浓度≤0.15 g/m32 生产流程及方案的确定焦炉煤气的净化主要是要脱除煤气中的H2S,脱硫的方法有两种:干法脱硫、湿法脱硫。
干法脱硫既可以脱除无机硫,又可以脱除有机硫,而且能脱至极精细的程度,但脱硫剂再生较困难,需周期性生产,设备庞大,不宜用于含硫较高的煤气,一般与湿法脱硫相配合,作为第二级脱硫使用。
湿法脱硫可以处理含硫量高的煤气,脱硫剂是便于输送的液体物料,可以再生,且可以回收有价值的元素硫,从而构成一个连续脱硫循环系统。
现在工艺上应用较多的湿法脱硫有氨水催化法、改良蒽醌二磺酸法(A.D.A法)及有机胺法。
其中改良蒽醌二磺酸法的脱除效率高,应用更为广泛。
但此法在操作中易发生堵塞,而且药品价格昂贵,近几年来,在改良A.D.A的基础上开发的栲胶法克服了这两项缺点。
3 生产流程说明3.1反应机理反应机理是脱硫的根本,也是整个脱硫过程中的核心部分。