流化床制备三氯氢硅工艺参数的优化
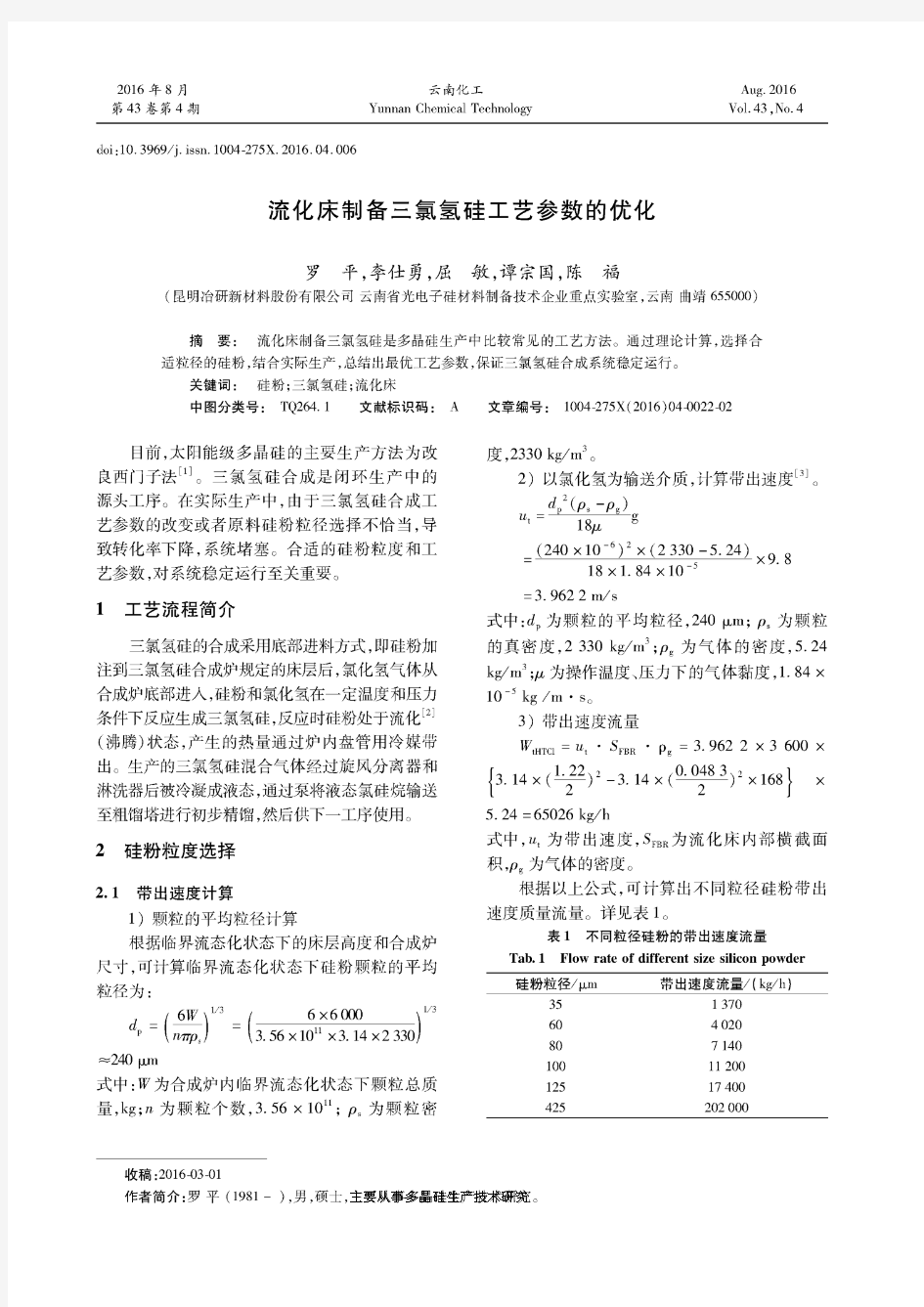
- 1、下载文档前请自行甄别文档内容的完整性,平台不提供额外的编辑、内容补充、找答案等附加服务。
- 2、"仅部分预览"的文档,不可在线预览部分如存在完整性等问题,可反馈申请退款(可完整预览的文档不适用该条件!)。
- 3、如文档侵犯您的权益,请联系客服反馈,我们会尽快为您处理(人工客服工作时间:9:00-18:30)。
2016年8月第43卷第4期
云南化工
Yunnan Chemical Technology
Aug. 2016
Vol.43,No.4
doi :10. 3969/j. issn. 1004-275X. 2016.04.006
流化床制备三氯氢硅工艺参数的优化
罗平,李仕勇,屈敏,谭宗国,陈福
(昆明冶研新材料股份有限公司云南省光电子硅材料制备技术企业重点实验室,云南曲靖655000)
摘要:流化床制备三氯氢硅是多晶硅生产中比较常见的工艺方法。通过理论计算,选择合 适粒径的硅粉,结合实际生产,总结出最优工艺参数,保证三氯氢硅合成系统稳定运行。
关键词:硅粉;三氯氢硅;流化床
中图分类号:TQ264. 1 文献标识码:A 文章编号:1004-275X( 2016) 044022-02
目前,太阳能级多晶硅的主要生产方法为改 良西门子法[1]。三氯氢硅合成是闭环生产中的 源头工序。在实际生产中,由于三氯氢硅合成工 艺参数的改变或者原料硅粉粒径选择不恰当,导 致转化率下降,系统堵塞。合适的硅粉粒度和工 艺参数,对系统稳定运行至关重要。度,2330 kg/m3。
2)以氯化氢为输送介质,计算带出速度[3]。
ut =de2(ps -Pg)
18/jl g
(240 xl(T6)2 x(2 330 -5.24)
18 xl. 84 xlO-5 X'
1工艺流程简介
三氯氢硅的合成采用底部进料方式,即硅粉加 注到三氯氢硅合成炉规定的床层后,氯化氢气体从 合成炉底部进入,硅粉和氯化氢在一定温度和压力 条件下反应生成三氯氢硅,反应时硅粉处于流化[2] (沸腾)状态,产生的热量通过炉内盘管用冷媒带 出。生产的三氯氢硅混合气体经过旋风分离器和 淋洗器后被冷凝成液态,通过泵将液态氯硅烷输送 至粗馏塔进行初步精馏,然后供下一工序使用。
2娃粉粒度选择
2.1带出速度计算
1)颗粒的平均粒径计算
根据临界流态化状态下的床层高度和合成炉 尺寸,可计算临界流态化状态下硅粉颗粒的平均 粒径为:
_ / 6W\l/3_ / 6 x 6 000 \1/3
p= \^mpj =\3.56x l011x3.14x2 330J ~240 (ju n
式中:疋为合成炉内临界流态化状态下颗粒总质 量,kg;ra为颗粒个数,3.56 x 1011;ps为颗粒密
=3. 962 2 m/s
式中为颗粒的平均粒径,240 pm; ps为颗粒 的真密度,2 330 kg/m3;Pg为气体的密度,5.24 kg/m3;At为操作温度、压力下的气体黏度,1. 84 x
10 _5 kg /m • s0
3)带出速度流量
K h t c i= '• SF B R• pg= 3. 962 2 x 3 600 x
1/i/1. 22 n20 1/1/0. 048 3x2 11
j3. 14x(^—) -3. 14 x (——-——)x 168 \x 5.24 =65026 kg/h
式中,为带出速度,S FBR为流化床内部横截面 积,pg为气体的密度。
根据以上公式,可计算出不同粒径硅粉带出 速度质量流量。详见表1。
表1不同粒径硅粉的带出速度流量
Tab. 1 Flow rate of different size silicon powder
娃粉粒径/pm带出速度流量/( kg/h)
35 1 370
60 4 020
807 140
10011 200
12517 400
425202 000
收稿:2016-03-01
作者简介:罗平(1981 -),男,硕士,主要从事多晶硅生产技术研究
2016年第4期罗平等:流化床法制备三氯氢硅工艺参数优化• 23•
从理论来看,硅粉粒径越大,被气体带出的可 能性越小。但考虑到反应炉内流化状态的建立,需选择合适的硅粉粒径,以最大程度地提高硅粉 利用率,同时减少硅粉被带出量。
2.2桂粉粒度选择
若硅粉的粒径分布范围太广,且小粒径的硅 粉量特别多,(比表面积大)虽有利于反应,但很 容易达到硅粉的带出速度,导致硅粉被大量带出 合成炉,降低了硅粉利用率且容易形成堵塞;若大 于平均粒径硅粉过多(比表面积减小)会影响反 应效果,相应也加大了合成炉浓相段冷却盘管磨 损,降低盘管使用周期。
经过计算,硅粉理论带出速度质量流量为65 026 kg/h。从表1可知,硅粉粒径为100 pm,计算 出的带出速度质量流量小于理论计算值,而硅粉 粒径为425 pm,计算出的带出速度质量流量高于 理论计算值。若要趋于反应稳定和产出最大化,则需选择接近理论带出速度质量流量的硅粉粒 径,因此,最适合反应的硅粉呈正态分布,粒径为 100 ~425 pm。实际生产中,使用粒径为100 ~ 425 pm硅粉后,三氯氢硅合成系统连续稳定运行 3个月以上,系统未发生堵塞。
3工艺参数调整
3.1降低反应原料水含量
游离氧及水分对三氯氢硅的合成反应极为有 害,因为Si -0键比Si -C1键更为稳定,反应产 物极易发生氧化或水解。水解产生的硅胶会堵塞 管道,使操作发生困难,同时造成三氯氢硅的产率 降低。如果硅粉和氯化氢含水量愈大,则产物中 三氯氢硅含量愈低。在实际生产过程中,硅粉通 过干燥后,水含量降低至50 pg/k g以内;氯化氢 通过冷凝器、雾沫分离器除水后,使氯化氢中水含 量降低至100网/k g以内,再进三氯氢硅合成炉 进行反应。
3.2反应温度调整
反应温度低于260 °C时,合成气中二氯二氢 硅含量增加[4];而反应温度大于320 °C时,合成气 中的四氯化硅含量增加。以上两种情况均会造成 合成三氯氢硅的含量降低。因此,将反应温度从 270 °C调整至300 °C,有利于提高三氯氢硅合成率。3.3工艺参数调整后生产情况
经过原料含水量、温度参数调整后,氯硅烷产 量及硅粉单耗情况见表2。
表2氯硅院产量和硅粉单耗
Tab. 2 Chlorosilaneyield and silicon powder consumption
时间氯硅烷产量/t硅粉消耗八硅粉单耗2014年11月702. 05208. 420. 30 2014年12月913.01261.460. 29 2015年1月772.73170. 000. 22 2015年2月830. 43191.000. 23 2015年3月783.33188. 000. 24
通过2015年1月工艺参数调整后,氯硅烷产 量稳定,系统连续稳定运行3个月且硅粉单耗均 低于0.25 t/t氯硅烷,有效节约了生产成本。同
时连续3个月产品质量较好,合成氯硅烷中三氯 氢硅质量占比超过87%。不过质量波动较大,仍 存在较大的优化空间。
随着合成系统连续运行时间的增加,合成炉 中失活硅粉不断聚集,反应效果逐步下降,系统中
金属氯化物聚集后排放量增大,导致硅粉单耗不 断增加。根据经验,合成炉运行3个月后,择机可 进行合成炉切换生产,对系统进行检修及维护
保养。
4结论
实际生产表明,在各项公辅条件不变的情况 下,经过计算和总结分析,降低硅粉和氯化氢的含 水量,桂粉粒径范围为100 ~425 pm,反应温度为 300 °C,氯化氢的进气量一定的条件下,系统能够 稳定连续运行,硅粉利用率大幅提高,产品质量 较好。
参考文献:
[1]梁骏吾.电子级多晶硅的生产工艺[J].中国工程科
学,2000,2(12) :36 -38.
[2]吴占松,马润田,汪展文.流态化技术基础及应用
[M].北京:化工工业出版社,2006.
[3]万瑜.新型流化床布风板操作弹性的实验研究
[D].华中科技大学,2009:23 -27.
[4]刘兴平.Aspen Plus软件在三氯氢硅低压合成技术
改造中的应用[J].广东化工,2014(8):45 -46.
(下转第54页)