无副车架的渣土自卸汽车车架结构强度有限元分析
探讨汽车副车架强度模态分析及结构优化

探讨汽车副车架强度模态分析及结构优化汽车副车架是汽车重要的承载结构之一,在汽车的安全性、舒适性和性能方面起着重要作用。
其强度和刚度对汽车的整体性能有着直接的影响。
对汽车副车架的强度模态分析及结构优化是至关重要的。
本文将就此话题展开探讨。
一、汽车副车架的结构及工作原理汽车副车架是指安装在汽车底盘上的用于支撑底盘组件的结构。
其主要作用是传递车辆的荷载,同时还要满足汽车悬挂系统的需求,以确保汽车在行驶过程中的舒适性和稳定性。
在日常使用中,汽车副车架还要承受来自路面的冲击和振动,并且要能够抵抗车辆制动时产生的扭矩和冲击力。
汽车副车架需要具有足够的强度和刚度,以确保汽车在各种工况下都能够安全可靠地行驶。
二、汽车副车架的强度模态分析1. 强度分析汽车副车架在使用过程中要承受各种不同方向的受载情况,主要包括拉伸、压缩、弯曲和剪切等载荷。
需要对汽车副车架进行强度分析,以确定其在不同工况下的应力分布和变形情况。
强度分析的目的是确认汽车副车架在设计工况下不会出现塑性变形或者破坏,从而保证汽车的安全性和可靠性。
通过有限元分析等方法,可以对汽车副车架进行受力分析,计算其在各种工况下的应力和变形,从而确定其是否满足设计要求。
2. 模态分析模态分析是指通过对汽车副车架进行振动特性的分析,确定其固有频率和振型。
汽车副车架在行驶过程中会受到来自路面的激励力,因此需要对其进行振动分析,以确认其固有频率和振型与激励频率不发生共振,从而避免产生过大的振动响应。
通过模态分析,可以确定汽车副车架的主要振动模态,并评估其对汽车驾驶舒适性和稳定性的影响。
三、汽车副车架的结构优化1. 结构轻量化汽车副车架在保证足够强度和刚度的前提下,需要尽可能减小自身的重量。
轻量化可以降低汽车的整体质量,提高汽车的燃油经济性和加速性能,同时还能减少对环境的影响。
轻量化的方法包括采用高强度、轻质材料、优化结构布局和加强节点等。
2. 结构优化通过有限元分析等方法对汽车副车架进行结构拓扑优化、形状优化和材料优化。
探讨汽车副车架强度模态分析及结构优化
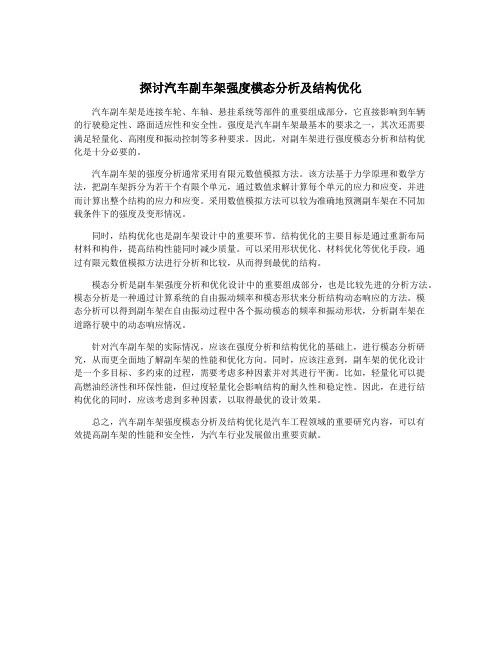
探讨汽车副车架强度模态分析及结构优化汽车副车架是连接车轮、车轴、悬挂系统等部件的重要组成部分,它直接影响到车辆的行驶稳定性、路面适应性和安全性。
强度是汽车副车架最基本的要求之一,其次还需要满足轻量化、高刚度和振动控制等多种要求。
因此,对副车架进行强度模态分析和结构优化是十分必要的。
汽车副车架的强度分析通常采用有限元数值模拟方法。
该方法基于力学原理和数学方法,把副车架拆分为若干个有限个单元,通过数值求解计算每个单元的应力和应变,并进而计算出整个结构的应力和应变。
采用数值模拟方法可以较为准确地预测副车架在不同加载条件下的强度及变形情况。
同时,结构优化也是副车架设计中的重要环节。
结构优化的主要目标是通过重新布局材料和构件,提高结构性能同时减少质量。
可以采用形状优化、材料优化等优化手段,通过有限元数值模拟方法进行分析和比较,从而得到最优的结构。
模态分析是副车架强度分析和优化设计中的重要组成部分,也是比较先进的分析方法。
模态分析是一种通过计算系统的自由振动频率和模态形状来分析结构动态响应的方法。
模态分析可以得到副车架在自由振动过程中各个振动模态的频率和振动形状,分析副车架在道路行驶中的动态响应情况。
针对汽车副车架的实际情况,应该在强度分析和结构优化的基础上,进行模态分析研究,从而更全面地了解副车架的性能和优化方向。
同时,应该注意到,副车架的优化设计是一个多目标、多约束的过程,需要考虑多种因素并对其进行平衡。
比如,轻量化可以提高燃油经济性和环保性能,但过度轻量化会影响结构的耐久性和稳定性。
因此,在进行结构优化的同时,应该考虑到多种因素,以取得最优的设计效果。
总之,汽车副车架强度模态分析及结构优化是汽车工程领域的重要研究内容,可以有效提高副车架的性能和安全性,为汽车行业发展做出重要贡献。
自卸车底盘车架的改装设计及有限元分析_赵美云

重量、整备重量和 装 载 重 量。 假 设 各 载 荷 在 其 作 用 区 域内均匀分布,根据 车 架 各 个 部 分 所 受 的 载 荷 和 横 截 面积,算出在安放驾驶室的地方施加 0.049 MPa的均 布载荷,在剩余部分施加0.155 MPa的均布载荷。
从图6和图7可 以 看 出:最 大 变 形 发 生 在 车 厢 后 端,最大变形量 为 1.5 mm;最 大 应 力 产 生 在 中 间 段, 最大应力为139.44 MPa,小 于 许 用 值 360 MPa,因 此 车架强度满足要求。 在 计 算 车 架 应 力 强 度 时,是 根 据 支 梁 模 型 的 简 化 图 计 算 的 ,横 梁 等 一 些 条 件 无 法 考 虑 , 因此计算出的结果和 分 析 的 结 果 不 在 同 一 点,但 都 是
收 稿 日 期 :2012-05-07; 修 回 日 期 :2012-07-07 作者简介:赵美云 (1977-),女,河南西平人,讲师,在读博士生,主要研究方向为摩擦学及表面工程、设备故障诊断与状态监测等。
· 46 ·
机 械 工 程 与 自 动况下的最大弯矩为:
Mdmax=k×n×Mmax 。 ……………………… (4) 对于槽形断面,其断面系数为 : [6]
W =t×h(h+6b)/6 。 ……………………… (5)
纵梁危险截面的最大应力为:
σ=Mdmax/W 。 ……………………………… (6) 若σ≤ [σ],则 该 车 架 纵 梁 的 改 装 设 计 满 足 要 求 。
用 汽 车 ,2009(12):48-50. [4] 刘 岩 .自 卸 汽 车 车 架 设 计 [J].专 用 汽 车 ,1981(1):15-18. [5] 闻邦椿.机械设计手 册(第 3 卷)[M].第 5 版.北 京:机 械
探讨汽车副车架强度模态分析及结构优化

探讨汽车副车架强度模态分析及结构优化摘要:随着社会上经济的发展汽车成为人们出行的必备交通工具,而汽车也在社会上变得越来越普及。
现在就以轿车的副车架为研究的对象,在很多的软件当中建立起来的模型模拟,然后对这些结构进行新型的分析,在进行分析的过程中采取的方法主要就是对强度和自由度进行的分析,在进行分析之后,得出的结果也说明了,汽车的副车架本身的强度是符合要求的,并且汽车的副车架跟发动机之间是有一定的联系,针对这样的问题也有相应的解决方法进行解决。
关键词:汽车的副车架的结构;强度化分析;拓扑结构优化前言:随着人们经济水平的提高,人们对于吃、穿、住、用、行等方面的要求也在不断的提高,随着科技的发展和技术水平的进步,大多数人对汽车的品牌、汽车的舒适度和安全性能还有一系列有关车方面的要求也变得越来越高,而在这其中汽车舒适度和安全性能这两个方面是相互影响、相互制约的,汽车的副车架是现在大部分汽车底盘的最主要的承载件,使用的越来越普及,因为它在使用的过程中比较的频繁,所以应该具有较好的强度和动态特性。
目前,世界上的很多人认为,在使用频率作为优化目标进行优化的过程中进行了很多方面的研究,而且在研究的过程中取得了很多的成果。
在相关的书籍中曾经有过记载,在选择使用轻型车车架的频率来当作拓扑结构优化的主要目标,在这当中进行多部拓扑结构进行优化以此来得到副车架横梁的最佳的拓扑结构。
还有在相关的书籍中记载里,在对汽车的副车架进行频率的拓扑结构的优化时,根据所得到的密度的图纸进行相关数据方面的分析,他的分析出来的计算的结果和实验的数值的数据一致,使得本来应该拥有的频率得到应有的优化,这样也就让更多的人们对汽车的副车架有了更多的了解。
一、汽车的副车架在有限模型方面的建立汽车的副车架在制作的过程中采用的原材料的形成过程是非常复杂的,在汽车的副车架和车架之间,应用四个轴向竖直的橡胶衬套相互连接在一起,纵臂上下摆臂,以及其他的后悬架零部件安装在汽车的副车架上。
公矿自卸车车架结构强度有限元分析
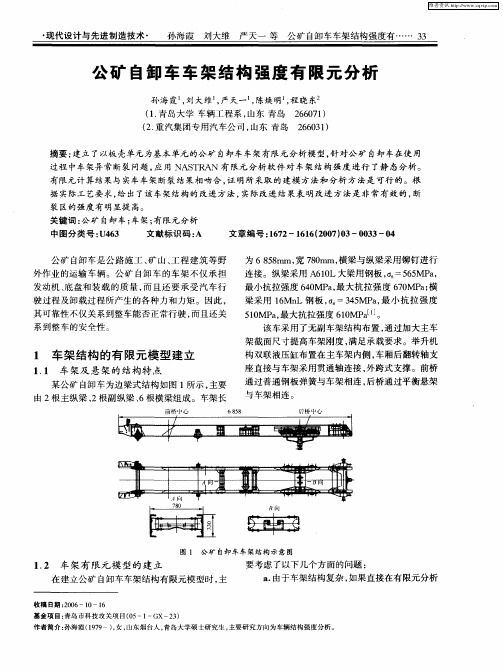
1 5 载 荷 的 处 理 .
车辆 满 载 时作 用 于 车架 上 的载 荷包 括 动 力 总
件 的重 合部 位的 网格节 点 和单元 应重 合 。
关键 词 : 公矿 自卸 车 ; 车架 ; 限元 分析 有
中图分 类号 : 4 3 U 6 文献 标识码 : A 文章编 号 :6 2 6 6 2 0 )3 0 3—0 1 7 —1 1 (0 7 0 —0 3 4
公矿 自卸 车是 公 路 施 工 、 山 、 程 建筑 等 野 矿 工
为 68 8 5 mm, 7 0 m, 梁与纵 梁采 用铆 钉进 行 宽 8m 横 连 接 。纵 梁采 用 A 1 L大梁 用钢板 ,s 6 MP , 60 o =5 5 a 最 小抗 拉强度 6 0 a最 大抗 拉 强 度 6 0 a 横 4 MP , 7 MP ; 梁 采用 1 Mn 6 L钢 板 , =3 5 a 最 小 抗 拉 强 度 4 MP , 5 0 a最 大抗 拉强 度 6 0 a1。 1 MP , 1 MP [l 该 车采 用 了无副 车架结 构布 置 , 过加 大主车 通
座 直接 与车架 采 用贯通 轴连 接 , 跨式 支撑 。前桥 外 通 过普 通钢板 弹簧与车 架相 连 , 后桥通 过平衡 悬架
与车架 相连 。
图 1 公 矿 自卸 车 车 架结 构 示 意 图
12 车架有限元模 型的建立 .
在 建立公 矿 自卸 车车架结 构 有 限元 模 型时 , 主
维普资讯
20 0 7年 2月 中国制造 业信 息化 软 件 中建 立 车架 的三维 几何模 型 , 则相 当 困难 。本 文将 整个 车架 的 I E —D AS三 维模 型导人 具 有强 大 的几何 处理 功能 及 网格 划 分 功能 的有 限元 前 后 处 理软件 H pr s y e h中 , Me 然后 在 该 软 件 中对 车架 模 型 进行几 何清理 及 简化 , 去除 车架 上用 于装配 的小 孔, 因为这些 小 孔 仅 仅 影 响 车架 的 局部 强 度 , 对 但 网格 质量 影响 却很 大 。 b 在 确 定 了车 架 的三 维 几 何 模 型 之 后 , 用 . 利
探讨汽车副车架强度模态分析及结构优化

探讨汽车副车架强度模态分析及结构优化汽车副车架是汽车结构中的重要组成部分,它承担着车辆的重量、扭矩和振动的传递,同时在车辆碰撞时发挥着重要的承载作用。
汽车副车架的强度分析和结构优化对于车辆的安全性和性能至关重要。
本文将就汽车副车架强度模态分析及结构优化进行探讨。
我们来看一下汽车副车架的强度模态分析。
汽车副车架主要受到来自发动机和车辆行驶时的负载作用,因此在强度模态分析中,需要考虑副车架在不同工况下的受力情况。
通过有限元分析等方法,可以对副车架的应力、应变和振动特性进行分析,找出其在不同工况下的受力状态和强度情况。
这对于设计和改进副车架的结构和材料具有很大的指导作用。
结构优化是提高汽车副车架强度的重要手段。
通过结构优化,可以改进副车架的设计方案,使其在不增加重量的情况下提高强度和刚度。
可以采用新的材料和工艺,提高副车架的耐疲劳性和抗冲击能力。
还可以通过减少副车架的零部件数量和连接处,降低副车架的制造成本和装配难度。
这些优化措施将有助于提高汽车副车架的整体性能和使用寿命。
在进行汽车副车架强度模态分析和结构优化时,需要注意以下几点。
需要充分考虑副车架的受力特点和工况,不同的车型和用途对副车架的要求是不同的,因此在分析和优化过程中需要进行针对性的研究。
要充分利用现代化的分析和优化工具,如有限元分析软件、拓扑优化算法等,以更有效地进行副车架强度模态分析和结构优化。
在进行结构优化时,需要综合考虑副车架的强度、刚度、重量和成本等多方面因素,以找出最合适的设计方案。
汽车副车架强度模态分析及结构优化是提高汽车安全性和性能的重要手段。
通过对副车架的受力特点和工况进行分析,可以找出其在实际使用中的弱点和问题,通过结构优化提出改进方案,从而使汽车副车架在保证安全的前提下具有更高的强度和刚度。
希望本文的内容对于相关领域的研究者和从业者有所帮助,促进汽车副车架结构的不断优化和提升。
载重货车车架设计及有限元分析
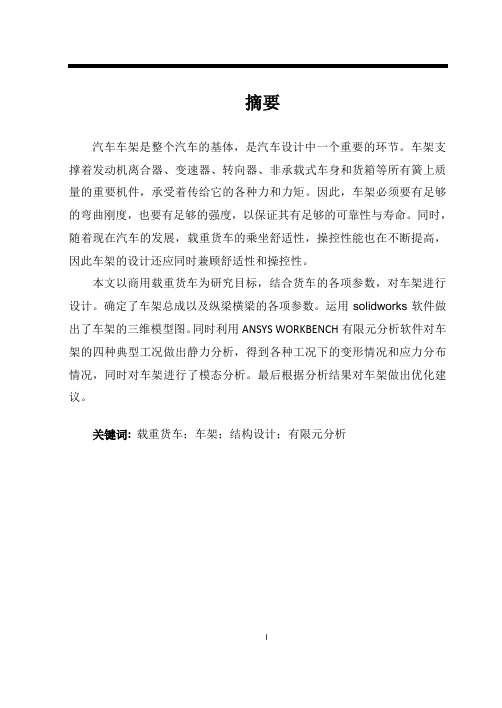
摘要汽车车架是整个汽车的基体,是汽车设计中一个重要的环节。
车架支撑着发动机离合器、变速器、转向器、非承载式车身和货箱等所有簧上质量的重要机件,承受着传给它的各种力和力矩。
因此,车架必须要有足够的弯曲刚度,也要有足够的强度,以保证其有足够的可靠性与寿命。
同时,随着现在汽车的发展,载重货车的乘坐舒适性,操控性能也在不断提高,因此车架的设计还应同时兼顾舒适性和操控性。
本文以商用载重货车为研究目标,结合货车的各项参数,对车架进行设计。
确定了车架总成以及纵梁横梁的各项参数。
运用solidworks软件做出了车架的三维模型图。
同时利用ANSYS WORKBENCH有限元分析软件对车架的四种典型工况做出静力分析,得到各种工况下的变形情况和应力分布情况,同时对车架进行了模态分析。
最后根据分析结果对车架做出优化建议。
关键词: 载重货车;车架;结构设计;有限元分析IABSTRACTThe vehicle frame is the base of the car, is one of the most important parts in the automobile design. Frame supports the engine clutch, transmission, steering gear, non bearing body and the container all spring quality the important parts, bear and pass it on to all kinds of force and moment. Therefore, the frame must have enough bending stiffness, also want to have enough strength, to ensure sufficient reliability and life. At the same time, with now the development of automobile and truck ride comfort, handling performance also continues to increase, so design of the frame should also combine comfort and handling.In this paper, the commercial truck as the research objective, combined with the parameters of the truck, the frame design. Frame assembly and the longitudinal beam parameters were determined. The 3D model chart of the frame was made by SolidWorks software.. At the same time, the finite element analysis software ANSYS Workbench of the frame of four kinds of typical working conditions to make static analysis, obtained under various conditions of deformation and stress distribution, and the modal analysis of the frame. Finally, according to the results of the analysis of the frame to make optimization recommendations.Keywords:Truck; frame;structure design;finite element analysisII目录摘要 (I)ABSTRACT .................................................................................... I I 1 绪论 .. (1)1.1车架总成概述 (1)1.2国内外研究情况及其发展 (2)2 车架总成设计 (6)2.1参考车型及其参数 (6)2.2车架类型的选择 (6)2.3车架设计的技术要求 (11)2.4车架的轻量化 (13)2.5车架的参数设计 (13)3 车架的有限元静力学分析 (19)3.1车架几何模型的建立 (19)3.2车架有限元模型的建立 (19)3.3车架的静力学分析 (21)3.4 基于静力分析的车架轻量化 (32)4 车架的模态分析 (34)4.1车架模态分析的基本理论 (34)4.2车架有限元模态分析结果 (36)4.3车架外部激励分析 (40)5 总结与展望 (42)III5.1总结 (42)5.2工作展望 (43)参考文献 (45)致谢 (47)IV1 绪论1.1车架总成概述汽车车架是整个汽车的基体,是将汽车的主要总成和部件连接成汽车整体的金属构架,对于这种金属构架式车架,生产厂家在生产设计时应考虑结构合理,生产工艺规范,要采取一切切实可行的措施消除工艺缺陷,保证它在各种复杂的受力情况下不至于被破坏。
117468_赵坤_自卸式半挂车车架建模及有限元分析_前期报告_1428238022999

河北工业大学城市学院毕业设计(论文)前期报告学生姓名:赵坤学号: 117468 系别:机械工程系专业:车辆工程设计(论文)题目:自卸式半挂车车架建模及有限元分析设计(论文)地点:河北工业大学城市学院指导教师:王金刚职称:教授2015年 04 月 03 日一、文献综述(不少于2000字)1.课题背景随着社会的发展,自卸车在二十世纪五十年代应运而生,自卸车的问世是一场重大的技术革新,是有效节省劳动力、降低劳动强度、提高生产效率的特色产品。
自卸车又称翻斗车,是指通过液压或机械举升而自行卸载货物的车辆,是应用较多、环境适应能力强的一种专用车,可以运输绝大部分的散货,由于运输货物相对比较固定,所以具有均衡性强的特点,在粮食、采矿、建筑、矿粉运输、电厂、钢厂的许多行业都有广泛的应用[1]。
目前国内自卸车主要用于能源物流运输(煤碳、砂石、矿石等)和工地道路施工作业,其中煤碳、砂石料、铁粉运输比例占有相当大的比重。
半挂车,是车轴置于车辆重心(当车辆均匀受载时)后面,并且装有可将水平或垂直力传递到牵引车的联结装置的挂车[2]。
其设计结构合理,且外型美观,制动效果好,可靠性高。
其次,半挂车设计符合人体工程学,具有装载质量大,装载物品稳当、结实的特点。
缩短了汽车的总长,提高了整车的行驶稳定性和机动性,更重要的是它的区段运输、甩挂运输、滚装运输还能对我国物流的组织形式起到一定程度的促进作用[3]。
与汽车相比,半挂车更能够提高公路运输的综合经济效益。
运输效率可提高30-50%,油耗下降20-30%,成本降低30-40%[4]。
正因为自卸车和半挂车各自特点和优势,所以二者的结合更是绝佳的配合,节省了劳动力、提高了运输效率、降低了成本,成为汽车行业的一枝独秀。
2.项目的国内外发展情况自卸半挂车最早源于国外,日本、北美、西欧的技术比较先进,在发达国家随着基础设施的日趋完善,自卸半挂车市场品种齐全、产品技术含量高,一些新材料诸如高强度钢板、新型铝合金材料、塑料等的使用,使车身的重量变得更轻,在降低了能耗的同时,更增加了美感和抗变形能力[5]。
基于有限元的大型矿用自卸车车架的强度分析和设计

架 的风险 点 ,为 自卸 车车架结构 的设计和 改进 提供
一 定的依据 ,并为 电传动矿 用 自卸车大型 复杂承载
构件强 、刚度分析提供列一种行之有效的分析方 法。
图 1 XDE240与 XE4000在山西某煤矿联合作业
举升座
图 2 矿用自卸车车架结构
1 车架有限元 分析
车架主 体为钢板 焊接箱型 结构 ,几何布 置样式 从俯 视 角度 可以看 出为两纵 四横 的形式具 体包括两 根 贯通 式纵 梁 。以及 由保险杠 、龙 门梁 、中部抗扭 管 、尾 部管组 件组 成的 “四横 ”结构 ,如图 2。 中 部抗扭 管位 于车架的中部 ,与车架左右纵 粱相连接 , 包括 三个铸 件分 别是举升缸 、左 /右举 升座和 推力 架铸 件 ;尾 部组件处 于车架尾部 ,连 接左右纵 梁并 起 到封 闭整 个车架 的作用 .其上 部与货厢铰接 作为 货厢 的 网转 中心 ,下部 与两个后 悬挂 油缸及横 拉杆 分 别在垂 向及横 向上 连接着后桥 壳 ,保证整车 正常 工作要求 。
在车 架上, 导致 车架 同时 承受 重力 、冲 击载荷 、扭 泛 且实 用高效 ,采 用有限元分析 法对大型 矿车车架
转载荷和 交变载 荷的 作用 ,因此要 求 车架 具有很 好 进 行工况仿 真分析和 结构优 化可以节省大 量的试验
的刚度 、强度和抗疲 劳等 特性 。电传动矿 用 自卸车 成 本和 设计 周期 。本文 以徐 工 XDE240电传 动矿 用
(2)
3 运 行 工 况
本文充 分考 虑矿 车车 架所面 临 的恶 劣工 况后 , 确定 了四种 具有 代表 性的工 况 ,由于 该车 自制 170 t,载重 23()t,满载 400 t,因此仅 对满载工 况进行 仿真计算 ;代表工况如下 :(1)正常行驶工况 ;(2) 举升 工况 ;(3)行驶 突遇坑 洞障碍 ;(4)紧急制动 工况 。具体的 约束条件 、加载 情况及分 析结果 ,如 图 3。其 中 ,约束的条 件主 要依据 前 /后悬挂 支撑 的情 况 ,在分析具 体工况时 ,根据不 同的工况对 约 束进行调整 ,以保证仿真结果的真实性和可靠性 。
基于ANSYS的自卸车车架有限元分析及优化设计

收 稿 日期 :0 2 0 — 6 2 1— 3 2
作 者简介 : 屈葵林( 9 1 ) 男 , 17 一 , 广西桂林人 , 工程师 , 硕士学位 , 研究方向为车辆工程 。
58
《 装备制造技术)0 2 ) 1 年第 6 2 期 础上释放车架右边 中间的 2 吊耳 的约束 ,如图 5 个
摘 要: A Y 用 NS S有 限元 分析 法对 自卸车车架进 行 了分析 , 出了自卸车车架在应用 中比较容 易出现 问题 的部位 。 出 找 提
了改 进 的 建 议 。
关键词 : NS S有 限元 分析 ; A Y 自卸车车架; 优化设计
中图分类号 : 4 94 2 U 6 .0 文献标识码 : A 文章编号 :6 2 5 5 ( 0 2 0 — 0 8 0 1 7 — 4 X 2 1 )6 0 5 — 2
Eq i me t u p n Ma u a t n e h o o y No6, 01 n f cr gT c n lg . 2 2 i
基 于 A S S的 自卸车车架有 限元分析及优化设计 N Y
屈 葵 林 ( 中国重汽集团柳州运力专用汽车有限公司, 广西 柳州 55 1 ) 4 12
有 限元 法 是一 种 在 工程 分 析 中经 常用 来 解 决 疑 横梁组成。在建立有限元计算模型时 , 考虑到 自卸车 难复杂问题 的近似数值分析方法 ,因其在机械结构 车架 大 多是槽 钢 ,截 面厚度 与截 面 尺寸 和构 件 的长
强度和刚度分析方面 , 具有较高的计算精度 , 在材料 度相 比小很多 ,因此可 以将 车架构件看做 由模板组 应 力 、 变 的线 性 范 围研 究 中 , 到广 泛 的应 用 。本 合 而成 , 应 得 采用 板壳 单元 建立 有 限元计 算模 型 。 文选用 A S S有限元分析软件 , 自卸车车架进行 NY 对 由于车架模 型比较复杂 ,采用 了主副车架分开 分析。 建模 、 再将模型写入 A CI S I合并的方式 , 得到 了如图 A S S有限元分析软件将实体建模 、 NY 系统组装 、 1 所示 的模型图。其 中主车架纵梁简化成了单层结 有 限元前后处理 、有限元求解 和系统动态分析等结 构 , 照实 际情 况赋 予 了 7n l 按 n 的厚 度 。 l 合为一体 , 能够高效 、 准确地建立所分析的零部件 的 三维实体模 型 , 自动生成有限元网格 , 根据输入 的约 束和载荷工况 , 对有限元进行 自动求解 , 并将结果用 图形显示 出来 。其能够满足绝大部分工程设计分析 的需要 , 在汽车设计领域 中的车身 、 车架的仿真计算 和发 电机 曲轴 及 传 动 系统 的计算 中 ,得到 了广 泛 的
车架有限元分析

摘要现代汽车绝大多数都有作为整车骨架的车架,车架是整个汽车的基体。
汽车绝大多数部件和总成(如发动机、传动系统、悬架、转向、驾驶室、货箱及有关操纵机构)都是通过车架来固定其位置的。
车架的功用是支撑连接汽车的各零部件,并承受来自车内外的各种载荷。
因此,车架的静、动态特性是其结构设计、改进和优化的依据,是确保整车性能优良的关键因素之一。
本文以6470型SUV车架作为研究对象,分析论证了CAD/CAE技术在汽车车架设计中的应用,主要内容如下:(1)选取一个SUV车型,通过查找和测量得到其主要的车型参数。
(2)运用CAD软件Unigraphics(简称UG)建立车架的三维模型。
(3)通过UG软件和ANSYS件的无缝连接将车架的三维模型导入ANSYS软件中。
(4)运用ANSYS软件的强大的有限元分析功能对该车架进行网格划分,施加适当的约束和载荷,对车架进行有限元静态分析,从而校核了该车架的强度和刚度,分析结果,校核该车架的强度和刚度能否满足要求。
在建模和有限元分析过程中,就CAD三维实体的建模方法、有限元理论的数学基础、有限元软件ANSYS、CAD软件与有限元接口技术、有限元分析方法的前期后期处理等方面做了研究工作,为后续工作做了较好的技术准备。
关键词:车架;CAD/CAE;ANSYS;有限元分析;静力分析AbstractMost modern cars are used as vehicle skeleton frame, which is through the matrix. Most parts and assemblies of a vehicle(such as engine, transmission, suspension, steering, cab, containers and related control mechanism and so on)are all over the frame to a fixed location. The function of a vehicle frame is to support the connection parts, and to take from inside and outside the vehicle loads. So, the static and dynamic analysis characteristics of frame is not only the base of its structure design, improvement and optimization, but also one of the key factors to ensure that vehicle performance.Finite element analysis has become an essential technology in the design of vehicle structure. As for compute-intensive and the analysis step,intuitive linear analysis of frame is very difficult. And ANSYS Finite element analysis software program can discrete elements into countless units to facilitate analysis, calculation and optimized results.On this article, 6,470 SUV frame is the objects to be researched to analyze and demonstrate CAD/CAE technique and its application in the design of automobile frame. Mainly as follows:(1) Select a SUV models,Find and measure its main parameters;(2)Establish the three dimensional model of the frame by UG;(3) Import the three dimensional frame model in UG into ANSYS through the seamless connection between UG and ANSYS;(4) Use the powerful finite element analysis for the frame element mesh, impose the appropriate constraints and loads and make the finite element static analysis of frame to check the strength and rigidity of the frame,During the modeling and finite element analysis,a lot of research work about the three-dimension solid modeling method, mathematical basis of finite element theory, interface technology of finite element, late and early processing of finite element analysis method is done, preparing for the follow-up work to be done better.Keywords: Frame, CAD/CAE; ANSYS; Finite Element Analysis; Static Analysis目录摘要 (I)Abstract (II)第1章前言 (5)1.1汽车车架介绍 (5)1.2国内外研究现状 (6)1.3研究意义及目的 (7)第2章软件介绍 (9)2.1 UG简介 (9)2.1.1 UG发展综述 (9)2.1.2 UG软件的优势 (9)2.2 ANSYS简介 (10)2.2.1有限元软件ANSYS发展综述 (10)2.2.2 ANSYS的技术特点 (10)2.2.3 ANSYS的功能 (11)第3章车架的建模 (13)3.1车架结构的简化 (13)3.2实体车架模型的建立 (13)第4章车架的有限元分析 (17)4.1 静力分析基础 (17)4.2车架静力学分析模型的建立 (18)4.3 悬架的模拟 (22)4.4 载荷的处理 (23)4.5车架静力分析工况及约束处理 (24)4.5.1 满载弯曲工况分析 (25)4.5.2 满载扭转工况分析 (30)4.5.3 满载制动工况分析 (33)4.5.4满载转弯工况分析 (34)第5章传统车架计算方法与有限元法比较 (37)第6章论文总结 (41)致谢........................................................ 错误!未定义书签。
探讨汽车副车架强度模态分析及结构优化
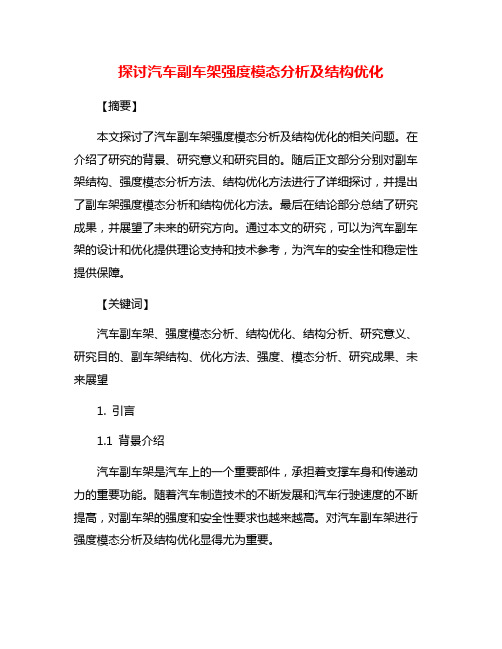
探讨汽车副车架强度模态分析及结构优化【摘要】本文探讨了汽车副车架强度模态分析及结构优化的相关问题。
在介绍了研究的背景、研究意义和研究目的。
随后正文部分分别对副车架结构、强度模态分析方法、结构优化方法进行了详细探讨,并提出了副车架强度模态分析和结构优化方法。
最后在结论部分总结了研究成果,并展望了未来的研究方向。
通过本文的研究,可以为汽车副车架的设计和优化提供理论支持和技术参考,为汽车的安全性和稳定性提供保障。
【关键词】汽车副车架、强度模态分析、结构优化、结构分析、研究意义、研究目的、副车架结构、优化方法、强度、模态分析、研究成果、未来展望1. 引言1.1 背景介绍汽车副车架是汽车上的一个重要部件,承担着支撑车身和传递动力的重要功能。
随着汽车制造技术的不断发展和汽车行驶速度的不断提高,对副车架的强度和安全性要求也越来越高。
对汽车副车架进行强度模态分析及结构优化显得尤为重要。
汽车副车架结构复杂,受到多种力的作用,如静载、动载、撞击载荷等。
传统的计算方法难以满足精确的分析需求,因此需要借助现代计算机辅助工程技术进行分析。
通过强度模态分析方法和结构优化方法,可以对汽车副车架的受力情况进行深入研究,找出其弱点并进行优化改进,提高副车架的整体性能和安全性。
本文旨在通过对汽车副车架强度模态分析及结构优化的研究,为汽车制造行业提供参考和借鉴,提高汽车副车架的设计水平和质量。
也希望通过本文的研究成果,为未来进一步深入探讨汽车结构优化提供基础和方向。
1.2 研究意义汽车副车架是汽车重要的结构组件之一,承担着支撑车身和保护乘客的重要任务。
副车架的强度和稳定性直接影响着汽车的行驶安全和乘坐舒适性。
对汽车副车架的强度模态分析及结构优化具有重要的研究意义。
通过对副车架的结构分析,可以深入了解副车架的构造特点和受力情况,为进一步的强度模态分析和结构优化提供基础。
强度模态分析可以帮助工程师评估副车架在不同工况下的受力情况,确定其承载能力和安全性,为汽车设计提供科学依据。
基于道路试验的自卸汽车车架结构疲劳寿命估算

基于道路试验的自卸汽车车架结构疲劳寿命估算作者:罗昆苑伍德司敏杰刘大维来源:《青岛大学学报(工程技术版)》2021年第04期摘要:为估算自卸汽车车架的疲劳寿命,本文在自建的考察自卸汽车可靠性的试验场地进行了车架关键点位的应变测试试验,得到了车架关键点位的动应力。
通过对车架关键点位的动应力进行雨流计数法统计分析,获得自卸汽车车架关键测点位置的应力谱,结合雨流计数分析得到的应力谱结果,采用DASP专业数据分析软件对车架进行了疲劳寿命估算,结果表明,该自卸汽车车架的最小疲劳寿命的里程约为536 700 km,车架结构满足使用要求。
该研究为结构改进以提高车架的使用寿命提供参考依据。
关键词:自卸汽车; 车架; 疲劳寿命; 应力试验中图分类号: U463.32; U469.4 文献标识码: A作者简介:罗昆(1996),男,硕士研究生,主要研究方向为汽车动态仿真与控制技术。
通信作者:刘大维(1957),男,博士,教授,碩士生导师,主要研究方向为汽车动态仿真与控制技术、地面车辆系统与控制技术。
Email:*************车架作为自卸汽车主要承载部件,需要承载驾驶室、发动机、变速箱、蓄电池、油箱和上装等载荷的作用,并且自卸汽车工作环境复杂,路面条件恶劣[1-3]。
车架同时还承受因路面不平而引起的各种附加载荷的作用,因此易导致疲劳损坏,严重影响自卸汽车的行驶安全性及使用寿命[4-7]。
目前,对自卸汽车车架的研究主要集中在静强度分析,对自卸汽车车架的疲劳寿命研究较少。
刘伦伦等人[8]运用Hypermesh软件对主副一体式自卸车车架进行强度分析;李茗等人[9]提出采用主副纵梁上下翼面贴合的车架断面结构来增加车架刚度并对车架纵梁的强度和刚度进行校核;周庆辉等人[10]对前举升式自卸汽车副车架进行轻量化优化设计;马锡勇等人[11]对宽体自卸车车架进行强度分析并进行试验验证;宋夫杰等人[12]对自卸汽车车架进行无副车架的设计并对其在各种工况下的强度进行分析;阳清泉等人[13]应用Hypermesh软件得到车架动载荷下的应力分布并建立整车多体动力学模型得到车架动态外载荷的时间历程,结合车架材料的SN曲线,利用Msc.Fatigue软件得到了车架的疲劳寿命,通过SEAMweld方法得到可靠的焊缝疲劳寿命;吉志勇等人[14]对比分析车轮六分力和轮心振动激励下车架的疲劳寿命情况;姜鑫等人[15]建立了一套采用虚拟试验进行车架结构疲劳分析及优化的研究方法。
大型矿用自卸车车架结构有限元建模研究

大型矿用自卸车车架结构有限元建模研究近年来,大型矿用自卸车的发展不断加快,车架的设计和检验备受重视,因此有必要进行有效的有限元建模研究。
有限元方法是一种建立计算机模型以模拟复杂物理系统的计算方法,通过有限元分析可以获得设计参数等结构受力情况,构成了一种有效的结构评估技术。
本文以某型号大型矿用自卸车为研究对象,采用有限元建模方法,研究车架设计参数、结构受力状况等,为该车架的结构设计提供技术支持。
首先,根据现有的设计规范和车架的实际情况,对该车架的结构进行定量分析。
结构成分包括车架主体、悬挂系统、桥壳、轴承和轮胎等,各成分受力情况不同,其材料及尺寸也不相同,必须根据实际情况进行精确的建模工作,并对材料和尺寸等参数进行校核。
其次,通过分析车架的外形及结构主要成分受力情况,将车架模型拆分为有限个单元,确定有限元模型的结构类型和结构尺寸,然后采用有限元分析软件进行模拟计算,综合考虑车架结构的受力情况,即可得到有效的结果。
最后,运用有限元方法对大型矿用自卸车车架进行建模,从而获得车架各个结构成分受力情况,以及车架结构的稳定性及耐久性的数据,为大型矿用自卸车的可靠性设计和检验提供有力的技术支持。
综上所述,有限元建模技术可以有效地分析大型矿用自卸车车架的结构受力情况,有助于提高车架抗压强度,延长使用寿命,从而提高其可靠性,为解决大型矿用自卸车结构受力问题提供了有力的技术支持。
通过有限元建模研究,可以在节约时间和费用的同时保证车架结构的稳定性和耐久性,进一步实现对大型矿用自卸车的安全性、可靠性和可控性的提高,提高矿用自卸车的工作效率,加快矿山设施建设进程。
本研究将为大型矿用自卸车车架结构有限元建模研究及其设计与检测提供有力技术支持,有助于大型矿用自卸车的安全及可靠性的提高。
探讨汽车副车架强度模态分析及结构优化

探讨汽车副车架强度模态分析及结构优化【摘要】这篇文章通过对汽车副车架强度模态分析及结构优化的研究,探讨了副车架在设计中的重要性。
在我们介绍了研究背景、研究目的及研究意义。
在我们详细探讨了副车架结构设计原理、强度模态分析方法、结构优化策略,以及通过实例分析和效果评价来验证优化结果。
在我们总结了强度模态分析在副车架设计中的应用,结构优化对性能的影响,并展望了未来的研究方向。
这篇文章旨在为汽车副车架设计提供更为科学的理论支持,并为相关领域的研究者提供参考。
【关键词】汽车副车架、强度模态分析、结构优化、设计原理、实例分析、效果评价、性能影响、研究展望1. 引言1.1 研究背景汽车副车架作为汽车底盘的重要部件之一,承担着连接车身和底盘传递扭矩和路面承载的功能。
随着汽车工业的发展和消费者对于车辆性能和安全性要求的提高,汽车副车架的设计和优化显得尤为重要。
在实际应用中,副车架常常会面临着受力不均匀、受振动影响等各种问题,导致其强度和稳定性存在一定的隐患。
进行汽车副车架强度模态分析及结构优化已成为当今汽车工程领域的研究热点之一。
通过对副车架的结构设计原理进行探讨和分析,可以更好地理解副车架的受力机制和承载特点;而副车架强度模态分析方法的研究则可以帮助工程师准确评估副车架在不同工况下的受力和振动情况,为优化设计提供依据;而结构优化策略的制定则可以有效提高副车架的强度和稳定性,从而改善整车性能和安全性。
1.2 研究目的汽车副车架是汽车底盘的重要组成部分,承载着车身和发动机等重要组件的重量,并且在车辆运行过程中承受着来自路面不平、颠簸等各种复杂载荷。
其强度和稳定性对车辆的安全性和性能有着至关重要的影响。
本研究旨在通过对汽车副车架的强度模态分析及结构优化,探讨如何有效提升副车架的抗压能力和抗扭性能,进而提高整车的安全性和稳定性。
具体来说,研究目的包括以下几点:1. 研究副车架结构设计原理,深入探讨其受力和变形机理,为后续的强度模态分析和优化设计提供理论支持。
_有限元技术在载货车辆车架分析中的应用
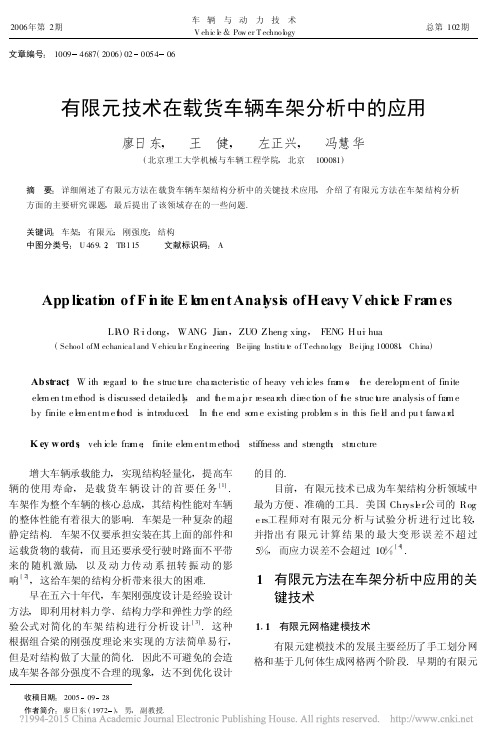
2006年第2期车辆与动力技术V ehic l e &Pow er T echno l ogy总第102期收稿日期:20050928作者简介:廖日东(1972),男,副教授.文章编号:10094687(2006)02005406有限元技术在载货车辆车架分析中的应用廖日东, 王 健, 左正兴, 冯慧华(北京理工大学机械与车辆工程学院,北京 100081)摘 要:详细阐述了有限元方法在载货车辆车架结构分析中的关键技术应用,介绍了有限元方法在车架结构分析方面的主要研究课题,最后提出了该领域存在的一些问题.关键词:车架;有限元;刚强度;结构中图分类号:U 469.2;TB115 文献标识码:AApp li cati on of F i n ite E l e m entAnal ysis ofHeavy Vehicl e Fra m esLI A O R i -dong ,WANG Jian ,ZUO Zheng -xing ,FENG H ui -hua(Schoo l ofM echanica l and V ehicu l a r Eng i neering ,Be ijing Instit u t e o f T echno logy ,Be iji ng 100081,China )Abst ract :W ith r egar d to t h e struc t u re cha r acteristic o f heavy veh icles fra m e ,t h e derelop m ent of finite ele m en tm ethod is discussed detailedl y ,and t h e m a j o r r esea r ch dir ec tion o f t h e struc t u re analysis o f fr a m eby finite e l e m entm e t h od is introduced.In t h e end so m e existing proble m s in this fie l d and pu t far wa r d .K ey w ords :veh icle fra m e ;finite ele m entm ethod ;stiffness and str ength ;str ucture 增大车辆承载能力,实现结构轻量化,提高车辆的使用寿命,是载货车辆设计的首要任务[1].车架作为整个车辆的核心总成,其结构性能对车辆的整体性能有着很大的影响.车架是一种复杂的超静定结构.车架不仅要承担安装在其上面的部件和运载货物的载荷,而且还要承受行驶时路面不平带来的随机激励,以及动力传动系扭转振动的影响[2],这给车架的结构分析带来很大的困难.早在五六十年代,车架刚强度设计是经验设计方法,即利用材料力学、结构力学和弹性力学的经验公式对简化的车架结构进行分析设计[3].这种根据组合梁的刚强度理论来实现的方法简单易行,但是对结构做了大量的简化.因此不可避免的会造成车架各部分强度不合理的现象,达不到优化设计的目的.目前,有限元技术已成为车架结构分析领域中最为方便、准确的工具.美国Chrysl e r 公司的Rog -e rs 工程师对有限元分析与试验分析进行过比较,并指出有限元计算结果的最大变形误差不超过5%,而应力误差不会超过10%[4].1 有限元方法在车架分析中应用的关键技术1.1 有限元网格建模技术 有限元建模技术的发展主要经历了手工划分网格和基于几何体生成网格两个阶段.早期的有限元 第2期廖日东等:有限元技术在载货车辆车架分析中的应用网格是采用梁单元手工建立的,因其规模简单,计算快捷而得到了技术人员的认可,一个车架模型可以用100左右个节点来构成.为了降低模型的规模,需要对原模型做一定的简化,如:用直梁代替曲梁,省去非承载件(减振器支架和弹簧限位块等),圆整构件表面孔及台肩,合并相近节点等[5],如图1所示.尽管采用梁单元模型进行有限元分析可以得到较好的变形结果,但应力分析的能力却是有限的[6].此外,梁单元不能很好地描述较为复杂的车架结构,难以反映横梁与纵梁接头区域的应力分布,且忽略了扭转时截面的翘曲变形[7].图1 手工建立的梁单元模型板壳单元的出现弥补了梁单元模型的缺陷.使用梁单元和板壳单元的组合模型在几何和力学特性上更加逼近于真实结构[8].如图2所示,该模型可以考虑焊接形式、螺栓或铆钉位置、卷边、突起、交支撑等不同的结构形式.尽管这种模型无论从存储规模上还是从计算耗时上要求都相当的高,但随着计算机和软件技术的发展,实现这一目标也已经不成为困难.图2 手工划分的板壳模型随着有限元模型规模的增大,有限元前处理在分析过程中占据了越来越大的比重.这在时间和工作量上大大增加了技术人员的负担.因此,在CAD 建模的基础上出现了一种新型的网格划分方法———基于几何体生成网格的方法.基于几何体的网格生成方法是生成有限元网格最快、最有效的方法.网格尺寸可以直接在边、表面、实体上定义,实体的变动会自动的反映到网格的节点和单元中,大大提高了网格尺寸控制的灵活性.有限元网格的单元尺寸对计算精度有很大影响,一般来说,有限元网格越密,对精确解的数值逼近就越好,但是,越是细密的网格需要的计算成本就越高.文献[9]指出,模型所需单元数目是求解精度和计算成本相平衡的结果,这一结果取决于结构的性质、边界条件以及分析类型.李德信等人在SX360重型自卸车架的网格模型中用20×20mm 细化单元来模拟变截面区域,用80×80mm 的一般单元来模拟其余区域,用过渡单元来连接一般单元和细化单元的方法,保证了有限元计算的精度[10],如图3所示.图3 采用局部网格加密的模型图4 基于中面建立的有限元模近几年,有限元分析对网格划分这一环节的要求越来越严格.首先对实体进行提取中面的操作,然后基于中面模型来划分网格.为了得到更加精确的计算结果,有限元网格主要是在离散误差收敛性分析的基础上建立的.模型的网格密度要与预期的应力应变变化相适应,网格应该在负荷结构急剧变化的区域加密,这些急剧变化的区域一般发生在尖角、弯边、切口、连接点、集中载荷和约束点等处.对外形复杂的部位细化网格可以提高计算精度,而其它部位加大网格则可以提高计算效率.合理的网格优化可以提高计算效率而又保证计算精55车辆与动力技术2006年 度.图4为北京理工大学为北方奔驰某型载重汽车建立的车架有限元模型,该模型采用基于实体中面划分网格的方法,分别使用了梁单元、板壳单元、实体单元、刚性单元以及接触单元等多种单元类型,节点87307个,单元130321个.1.2 车架边界条件的施加技术车架计算的成败很大程度上取决于边界条件的处理.不同的分析工况决定着模型的载荷与约束形式.根据车辆实际运行时的受力情况,车架的应力分析一般仅考虑纯弯曲工况和弯曲扭转组合工况(简称弯扭工况).纯弯曲工况是指车辆的4个车轮在同一水平面上处于静止状态或匀速直线运动状态时的受力工况;弯扭工况是指车辆的右前轮抬起332mm 、左后轮抬起172mm 时的受力工况[11].由于模型简化以及求解方法的种种限制,早期的车架结构仅仅是把外载以集中载荷的形式施加在某个节点上,但像压力之类的分布载荷则需要其他方法.实际上,车辆行驶时由于行驶条件的复杂多变,车辆承受的载荷也是复杂多样的.车架承受的载荷主要包括以下几种:①车架和货箱之间的有效负荷,②驾驶室和乘员的载重,③动力传动系的动态激励,④悬挂系统的动态激励,⑤燃料箱及其他附件的载重作用,⑥车架自重.这些载荷有静态载荷也有动态载荷,其中,车架本身的自重由系统根据材料的比重自动处理为分布载荷加载到结构上,而驾驶室和乘员的重量以及车载附件的重量可以通过集中质量的形式施加在车架上,其重心位置以及与车架间的连接部位用多点约束分摊到相应的节点上.因为这些作用力是静态的,且作用点均为已知,这种简化可以起到减小有限元规模的作用.类似的简化在车架分析方面还有很多,如载货汽车的车架通过钢板弹簧与车轮相连,由于轮胎的变形相对很小,可以处理为车架通过悬架弹簧与大地相连接[12].在满足一定工程精度的条件下这样的简化是可行的.施加载荷时应尽量避免在一点施加集中载荷的出现,因为集中载荷是一种理想化的情况,它会产生一个无穷大的应力集中.可取的方法是用施加等效的均布载荷且加密周围的网格来代替,以在危险点附近得到较好的应力状况.对于车架和货箱之间的等效载荷,历辉和季万琼对此做了详细的探讨[13],解决了货箱纵梁向车架的传力以及货箱纵梁和车架纵梁之间力的分配问题.过去对车架进行有限元计算时一般不考虑货箱的结构形式,相应的只是以均布力的形式施加在车架上.这种简化的计算结果,应力值一般比实验值要大.由实验得知,货箱纵梁与车架纵梁是共同来承受弯曲的,因此,货箱的结构形式以及刚度特性对车架变形和应力分布影响很大,且车架与货箱之间的作用力以集中力形式传递.此外,车架强度随货箱载荷作用位置的移动也发生着变化,在后悬后部和前悬前部作用垂直向下的载荷时,车架上的应力主要是正应力;而其它部位作用同样载荷时,车架上应力主要是负应力[14].这为有效改善车架应力分布状况提供了参考.求解车架的平衡方程时,需要有足够的约束条件以消除车架的整体刚体位移,才能避免刚度矩阵的奇异性,求出车架因受力而引起的节点位移,但是又不能使车架结构产生过多约束.车架的约束条件其实是通过悬架和轮胎与大地相连来实现的,因此,忽略轮胎的变形后可以直接约束悬架的下端点.悬架的刚度和车架整体刚度比起来要小很多,仅约束悬架还是无法保证车架不发生刚体位移,可以通过在车架两端施加不同方向的软弹簧来实现车架的受力平衡,如图5所示.图5 使用弹簧元来约束车架刚体位移1.3 部件连接以及相互作用的模拟由于计算模型和计算精度的要求不同,连接特征的处理方法也存在着很大的差异.过去的做法是使用刚性连接来代替柔性连接,或将车架当作一个整体零件来处理.这样处理和实际情况有较大的误差,增大了车架结构的刚度和强度.如果不考虑零件间的装配和搭接作用,连接处的刚度可能会比实际情况增大几十倍甚至上百倍[15].目前,车辆行驶路面复杂多变,而且车速又高,铆钉及螺栓失效、连接板撕裂现象多有发生.分析原因可能是汽车行驶时车架受到扭转,使连接板产生应力集中,铆钉受到很大拉力造成[16].通常对车架强度起决56 第2期廖日东等:有限元技术在载货车辆车架分析中的应用定作用的是连接区域的正应力,如果忽略连接处的柔度将无法准确计算该区域的应力分布,给计算结果带来误差[17].关于铆接和螺栓联接的模拟,文献[18]中通过分析比较,认为以点对点的方式建立螺栓单元夸大了连接部位螺栓点的局部应力特征.实际上螺栓在预紧力作用下发生自锁,螺孔周向的点大致与螺栓点的位移相协调,因此,可以采用梁单元与多点约束相结合的连接处理方式,如图6所示.梁单元可以很好的反映出拉压和剪切变形.文献[15]中采用接触算法来进行模拟,计算的应力变形结果更加接近实际情况.由于连接处存在一定程度的应力集中,使得连接处总应力偏大,计算得到的车架将更加趋于安全.但这样做必然会带来运算时间的增加和资源的耗费.图6 螺栓联接的模拟对于焊接的模拟,由于焊接处刚度相对较大,所以将焊点和堆焊处理为刚性单元和多点约束.通过计算发现,影响焊点模拟精度的主要因素是焊点间的间距[19].当节点间距离较小时,采用刚性单元与采用多点约束的计算结果非常接近,而当节点间距离较大时,刚性单元偏柔软,而多点约束则偏刚硬.目前,一些通用商业软件如V irtual Lab 都相应开发了功能强大的焊接单元库,不仅可以考虑焊点和焊缝的区别,还可以选择象角焊、T 形焊等不同的焊接形式,精确度也是相当高的.对于主副纵梁之间的相互作用问题,当假设上下面完全固接时,用材料力学理论便可分析上下梁之间力的分配,但实际上主副梁之间是存在接触和滑移的.周中坚等人研究了货箱纵梁和车架纵梁之间的垫层接触[20],采用上下梁同时建模的方法,中间大变形的非金属垫层采用梁单元来模拟,不仅可以考虑垫层的大变形,还可以考虑上下表面的滑移变形,其计算结果与实测应力比较吻合,如图7所示.上下梁之间的作用方式是一种典型的接触传力,可以采用非线性接触理论来定义车架模型.尽管这种方法可以较真实地表达出传力关系,但必然会增加运算时间和资源耗费.文献[18]中根据薄壳及平板结构假设理论,采用多点约束中的滑移面方法来解决.对于接触点对间的滑移关系,可设为叠合面间法向方向刚性连接,切向方向相对滑动.图7 考虑垫层连接1.4 钢板弹簧的有限元模拟车架是同悬挂系统一起工作的,悬挂系统对车架的刚强度影响很大.为了得到车架结构的真实应力分布,必须考虑悬挂系统的变形情况.在结构计算分析中常把悬挂元件与车架组合起来一起计算,车架的约束来自于与钢板弹簧相连的车轴、轮胎及地面.对于钢板弹簧模型的建立主要有以下几种方法:①把钢板弹簧理想化为两根垂直的弹簧单元和一个刚性单元,如图8所示.刚性梁单元起导向作用,弹簧单元起缓冲作用.这种模型计算结果比实际值偏高,实用性较差[21].图8 钢板弹簧等效模型②将钢板弹簧简化为变截面的梁单元,各单元的截面积可取实际结构的截面积.由于忽略了钢板之间的滑移,截面惯性矩要小于原结构的截面惯性矩,具体数值视钢板弹簧而定[22].③将钢板弹簧等效为一根水平放置的矩形截面梁[5].等效梁宽度B 取钢板弹簧片宽度,通过下式可以求得梁单元的截面高:H =3KL 3/4EB ,其中 K 为钢板弹簧铅垂方向上的装车刚度;B 为截面宽度,即为钢板弹簧的实际宽度;E 为等效梁的弹性模量;L 为等效梁的长度,即钢板弹簧活动吊耳与固定吊耳之间的水平距离.④副簧使悬架拥有较大的变刚度特性,当悬57车辆与动力技术2006年 架变形到一定行程后,副簧才参与支撑[23].文献[24]中考虑了副簧与副簧座的接触作用,将模拟前后板簧的弹簧单元下端分别固连在相应的刚性单元上,约束刚性单元的中心节点.该方法采用非线性静力求解,结果较为精确但计算十分耗时.也可以把副簧的作用简化为支反力施加到主簧上,这种做法为线性静力求解,可以使计算成本大大降低,但无法考虑副簧发生作用的时间历程.2 车架结构有限元分析主要课题2.1 结构静力学刚强度有限元分析 对车架进行静力学分析的目的是为了计算其在最大载荷作用下的变形与应力,以便进行刚度和强度的校核[25].使用有限元方法进行求解的过程中会遇到结构的性质、载荷与支撑条件、单元类型等问题.通常,车辆行驶的边界条件较为复杂,与车架结构强弱有直接关系的主要是弯曲工况和弯扭工况.2.2 结构模态有限元分析当外界激励频率与结构固有频率相互接近时,在小阻尼情况下结构将产生共振并伴随有较高的噪声,这将影响到整车以及部件的工作性能、寿命和可靠性.因此,应尽可能掌握结构的固有振动频率,避免共振的发生.固有频率和振型向量是表征振动系统特性的主要物理量,也是车架动态结构设计必不可少的参数.为了得到车架的固有特性,首先要对车架进行模态分析.对于车架这种具有上万自由度的复杂结构,求出全部固有频率和振型向量是相当困难的,也是没有必要的.结构的振动可以表达为各阶固有振型的线性组合,其中低阶的振型对结构的动力影响程度比高阶振型大.因此,低阶振型决定了结构的动态特性,只要计算少数的低阶模态参数便可满足动态分析的工程要求[26].模态分析对有限元网格的质量要求较高,建模时应尽量使单元大小均匀,减少畸形单元的出现.对车架动态特性的评价指标主要有:车架低阶频率应高于悬架下结构的固有频率,而低于发动机怠速运转频率,以避免发生共振现象;车架弹性模态频率应尽量避开发动机经常工作的频率范围;车架振型应尽量光滑,避免突变[8].这些指标对车架结构的合理修改起到一定的指导作用.模态试验分析可识别车架结构振动的模态参数,与有限元计算值比较,可以用来验证有限元模型的正确性.准确的有限元模型是确保计算结果正确的关键.但由于实际情况的复杂性,使有限元模型必须做很多简化,这便会产生误差.校正模型以及检验模型的准确性,就必须借助于模态试验.当有限元数值计算结果与试验结果相近时,建立的有限元模型才可用于后续的静态和动态分析.如果与试验结果相差很大,则要对有限元模型进行修改和优化,使计算结果与试验结果的差距在可接受的范围内[27].2.3 结构动响应有限元分析随着载货车辆工作环境的愈发复杂,仅仅把静强度作为车架结构强度衡量的唯一准则,已不能满足结构设计的要求.在车辆高速行驶状态下,车架的振动问题便会显得日益严重.振动一方面会影响乘坐人员的舒适性,另一方面也会影响车辆本身零部件的寿命.以往,车辆振动是在样车研制出来后才进行研究的,这样做显然存在一定的设计风险.现在通过有限元动态分析方法求出整车的动态特性模型及参数,从而预估车辆的动态特性响应[28].在许多文献[25,26,29,30]中为了使计算简便常采取静载荷乘以动载系数的方法来模拟车辆行使过程中的瞬态受力情况,这种方法主要是考虑动态载荷峰值来进行结构设计.车架受到的动态激励中,路面不平度对车架的动态响应影响最大,运用功率谱密度的方法可以描述路面的概率统计特性.根据I SO/ TC108/SC2N67中提出的“路面不平度表示方法”以及我国GB7031《车辆振动输入路面平度表示方法》中规定,路面功率谱密度G q(n)采用下式作为拟和表达式:G q(n)=G q(n0)nn0-w,其中 n为空间频率,为路面波长λ的倒数;n0为参考空间频率,取为0.1m-1;G q(n0)为参考空间频率下的路面谱值,称为路面不平度系数,单位为m2/m-1;W为频率指数,对于分级路面,其值取为2.由于速度功率谱具有常值特性,为“白噪声”信号,因此在路面谱激励下的随机响应分析中通常采用速度功率谱.3 结束语随着汽车轻量化和降低成本的要求日益迫切,58 第2期廖日东等:有限元技术在载货车辆车架分析中的应用对车架进行合理的设计,改善结构强度,发挥结构的最大功效,已经变得越来越重要.同时,这对运用有限元方法进行结构行为预测也提出了更严格的要求.如何提高有限元预测的分析精度,保证计算结果的可信度,已成为我们关注的最重大的课题.目前,运用有限元方法来进行结构分析还存在着许多问题有待解决.首先,如何建立合理的物理模型来描述实际问题,如结构的受载情况、结构真实的材料特性、结构表面粗糙度和细小裂纹的处理等.其次,如何建立精确的数学模型来描述物理模型,如使用恰当的单元类型来进行模拟、选择合适的单元尺寸来离散结构区域等.再次,结构加工制造过程的模拟,如纵梁冲压后回弹引起的制造误差、成型加工引起的残余应力等.参考文献:[1] 霍尔斯特皮佩特.汽车车身技术[M].北京:科学普及出版社,1992.[2] 蒋国平,周孔亢,王国林.汽车整车振动特性研究综述[J].广西大学学报,2001(9):194-197.[3] 吕江涛.SX360型自卸车车架静动态有限元分析及结构改进[D].西安:西安理工大学,2000.[4] M e l osh J.R.F i n ite E l em en t A na l y sis of A uto m ob ileS truc t ures[C].SAE T ransacti ons,740319,1974. [5] 杨宇光,胡 锫.客车车架结构强度计算分析[J].长春光学精密机械学院学报,1998(6):58-62. [6] 陈铭年,庄继德.汽车车架计算方法和结构优化变量综述[J].汽车工程,1996(5):285-289.[7] 宋 云,陈全世,王霄峰.轻型电动客车车身-车架的有限元结构分析及试验研究[J].汽车技术,1997(10):23-27.[8] 黎西亚,李成刚,胡于进.车架有限元分析技术发展综述[J].专用汽车,2001(1):13-15.[9] 凯默尔.现代汽车结构分析[M].北京:人民交通出版社,1987.[10] 李德信,吕江涛,应锦春.SX360自卸车车架异常断裂原因分析[J].汽车工程,2002(4):348-352.[11] 冯国胜,贾素梅.轻型车有限元分析及应用[J].机械强度,1996(6):78-80.[12] 倪 樵,马 力.改型载货车车架的静动力分析[J].专用汽车,2001(2):28-29.[13] 历 辉,季万琼.货车车架的等效载荷简化[J].汽车工程,1994(5):310-314.[14] 陈 龙,周孔亢,薛念文,等.农用运输车车架载荷研究[J].农业工程学报,2001(5):71-74. [15] 夏 平,黄菊生,吴安如.铆接汽车车架的接触法分析与计算[J].机械设计,2005(3):35-37. [16] 孙启会,闵 鹏.有限元法在汽车车架分析中的应用[J].重型汽车,2001(5):20-21.[17] 王海霞,汤文成,钟秉林.客车车骨架有限元建模技术及结果分析[J].机械强度,2002(1):77-80.[18] 张 勇,张 力,胡 崛,等.重型车车架组合结构的有限元分析[J].机械与电子,2005(2):16-18.[19] 桂良进,范子杰,陈宗渝,等.“长安之星”微型客车车架刚度研究[J].汽车技术,2003(6):28-30.[20] 周中坚,卢耀祖,陈耀均.货车车架有限元计算时货箱底部纵梁影响的模拟[J].上海汽车,1997(6):29-35.[21] 罗开玉,李伯全,鲁金忠,等.轻型客车悬架机构模拟研究[J].机械设计与研究,2003(4):66-68.[22] 李金伯,周中坚.车辆前钢板弹簧的有限元计算模拟[J].上海汽车,1998(1):29-30.[23] 约森赖姆佩尔.悬架元件及底盘力学[M].吉林:吉林科学技术出版社,1992.[24] 陆 波.板簧模型对车架强度计算的影响分析[J].汽车技术,2002(4):9-10.[25] 王 伟,陈 淮,王红霞,等.汽车车架的静态强度分析[J].郑州工业大学学报,2000(9):15-18.[26] 张铁山,胡建立,唐 云.CAD/CAE技术在汽车车架设计中的应用[J].上海工程技术大学学报,2001(9):216-220.[27] 梁新华,朱 平,林忠钦,等.有限元法与试验法相结合进行客车车架结构分析[J].机械设计与研究,2004(12):65-71.[28] 黄 华,茹丽妙.重型运输车车架的动力学分析[J].车辆与动力技术,2001(2):40-4.[29] 冯国胜.汽车车架结构参数的优化设计[J].计算结构力学及其应用,1994(5):218-224.[30] 李建国.车架强度的计算与动载系数的使用[J].专用汽车,1993(3):19-22.59。
车架有限元分析范文

车架有限元分析范文车架有限元分析是一种用于计算机辅助设计和优化车架结构的工程分析方法。
通过对车架结构进行适当的离散化处理,将复杂的连续体结构转化为由有限个节点和单元组成的离散系统,然后利用数学和力学原理对这个离散系统进行数值计算和分析。
有限元分析方法首先需要将车架结构进行三维建模。
建模时需要考虑到车架的外形尺寸、材料性质、连接方式等。
然后,将车架模型分割成有限个小的单元,如三角形或四边形单元。
每个单元有一组节点,它们的位置决定了单元的形状和尺寸。
在建立了有限元模型后,需要给单元节点分配适当的约束条件和加载条件,以模拟实际工况下的力学行为。
约束条件可以是固定边界条件或限制位移条件,加载条件可以是施加在车架上的荷载、压力或温度差等。
接下来,有限元分析方法将根据车架模型和加载条件构建一个刚度矩阵。
这个刚度矩阵描述了车架模型在各个节点上的刚度和幅度。
然后,通过计算刚度矩阵和加载条件的乘积,得到车架结构在受到施加的荷载下的应变和应力分布。
通过有限元分析方法,可以获得车架模型在不同工况下的应力、应变、位移等信息。
这些信息可以用来评估车架结构的强度、刚度和稳定性,并指导优化设计过程。
例如,可以在一些应力集中的区域增加材料或调整结构形状,以提高车架的承载能力和刚度。
另外,有限元分析方法还可以用于模拟车架在不同工况下的动态响应。
通过对车架结构进行动态分析,可以评估车架在行驶过程中的振动和冲击响应,并优化车架结构以提高乘坐舒适性和行驶稳定性。
总之,车架有限元分析是一种有效的工程分析方法,能够帮助设计人员评估车架结构的强度、刚度、稳定性和动态响应,从而指导优化设计过程,提高车架的性能和可靠性。
车架有限元强度分析及轻量化设计

图1㊀车架截面参数longjunhua@㊂Automobile Parts 2021.020852021.02 Automobile Parts086图2㊀车架受力简化示意T 2处力矩平衡原理,计算出支反力T 1T 1=[F 1k (k /2-n )+F 2w (m -w /2-v )]/m (2式中:T 1为前桥中心处对车架的支反力,N ;T 2为中后桥中心处对车架的支反力,N ;F 1为底盘簧上质量在车架上的均布载荷,N /m ;F 2为装在车架上的分布载荷,N /m ;y 为上装质心位置,m ㊂根据平衡方程,得出L 处的截面弯矩和剪力分别为:M =F 1(L +s )2/2+F 2(L -v )2/2-F 1L(3Q =F 1(L +s )+F 2(L -v )-T 1(4当剪力Q =0时,M 出现极值M 0;当支反力R 1㊁R 处M 亦出现拐点M 1,M 2㊂最大弯矩M max 取三者之间的最大值,考虑实际使用条件和安全系数,最大弯矩M max 取2倍静载荷条件㊂故单根纵梁断面的最大弯曲应力为:δmax =2M maxW XɤσS (5式中:σS 为材料的屈服强度㊂根据式(1)和式(5)来初步确定车架的截面尺寸㊂2㊀车架有限元模型的建立根据上述确定的车架截面利用Catia 软件进行车架总体设计,完成设计后通过有限元仿真软件Hyperworks 进行车架总体强度分析㊂图3㊀车架有限元模型3㊀车架强度分析结果3.1㊀载荷与边界重卡牵引车车架在行驶过程中主要承受4种工况,分别是弯曲工况㊁转向工况㊁制动工况㊁扭转工况,这4种工况施加载荷见表1,边界条件见表2㊂表1㊀4种工况下载荷情况㊀弯曲工况/g转向工况/g制动工况/g扭转工况/gx 00-0.70y0-0.200z-2.5-1-1-1注:x 表示前进方向,y 表示转弯方向,z 表示垂直地面方向㊂Automobile Parts 2021.02087图4㊀弯曲工况车架应力云图图5㊀转向工况车架应力云图图6㊀制动工况车架应力云图图7㊀扭转工况车架应力云图4种工况下最大应力见表3㊂表3㊀4种工况下最大应力㊀弯曲工况转向工况制动工况扭转工况最大应力/MPa 344.8324.7285310最大应力位置第二横梁附近,油箱连接处第二横梁附近,油箱连接处第二横梁附近,油箱连接处第四横梁附近,悬置安装处由表3可知,车架纵梁和横梁材料为B510L ,材料的屈服强度355MPa [1],以上4种工况最大应力334.8MPa ,小于材料的屈服强度,满足强度评判要求㊂4 轻量化设计根据应力云图,对车架受力不大的地方进行轻量化设计㊂具体措施为:将第三横梁处下连接板厚度10mm 改为8mm ,纵梁上连接板厚度8mm 改为6mm ,左右位置各两次,如图8所示㊂2021.02 Automobile Parts088图8㊀车架轻量化位置车架减重后应力云图如图9 图12所示㊂图9㊀减重后弯曲工况车架应力云图图10㊀减重后转向工况车架应力云图图11㊀减重后制动工况车架应力云图图12㊀减重后扭转工况车架应力云图可以看出,车架减重后与减重前4种工况下,车架承受的最大应力相当,满足强度要求㊂车架共减轻15.4kg ,4种工况下最大应力见表4㊂表4㊀4种工况下最大应力kg㊀原质量改后质量共减重横梁下连接板7.9ˑ2 6.3ˑ2纵梁上连接板24.4ˑ218.3ˑ215.4结论文中首先通过理论公式对车架纵梁截面进行选择按此截面设计完成车架总成后,通过有限元仿真分析对车架总成进行实际道路上各种工况下的强度分析㊂根据应力结果,提出了横梁和纵梁连接板的减轻方案,结果显示,减重后和减重前应力相当,满足强度要求㊂通过对车架的有限元分析,前期设计之初可以大大缩短时间,提高产品准确率㊂参考文献:[1]邓祖平,王良模,彭曙兮,等.基于HyperWorks 的某轻型卡车车架有限元分析及结构改进[J].机械设计与制造,2012(5):84-86.DENG Z P,WANG L M,PENG S X,et al.Finite element analysis and structure improvement on a light-duty truck frame based on hy-per works[J].Machinery Design &Manufacture,2012(5):84-86.[2]黄黎,段智方,庞建中.重型半挂牵引车车架结构的有限元分析[C]//第三届中国CAE 工程分析技术年会论文集,2007.[3]张建,戚永爱,唐文献,等.基于有限元法的某卡车车架优化设计[J].机械设计与制造,2012(5):48-50.ZHANG J,QI Y A,TANG W X,et al.Optimal design of some truck frame based on FEA [J].Machinery Design &Manufacture,2012(5):48-50.[4]景俊鸿,邵刚.中㊁重卡车架轻量化设计[J].合肥工业大学学报(自然科学版),2009,32(Z1):14-17.JING J H,SHAO G.Lightweight design of the middle and heavy truck s frame[J].Journal of Hefei University of Technology(Natural Science Edition),2009,32(Z1):14-17.。
- 1、下载文档前请自行甄别文档内容的完整性,平台不提供额外的编辑、内容补充、找答案等附加服务。
- 2、"仅部分预览"的文档,不可在线预览部分如存在完整性等问题,可反馈申请退款(可完整预览的文档不适用该条件!)。
- 3、如文档侵犯您的权益,请联系客服反馈,我们会尽快为您处理(人工客服工作时间:9:00-18:30)。
当车辆满载时,作用于车架上的载荷包括驾驶室、发动机、变速箱、液压缸、燃油箱、蓄电池、车箱及货物的载荷。计算过程中各个部分载荷如下:驾驶室质量1;500;kg,发动机质量950;kg,变速箱质量430;kg,液压缸质量300;kg,燃油箱质量300;kg,蓄电池质量150;kg,车箱质量4;000;kg,货物满载质量为2.2×104;kg。
1;车架结构的有限元模型
1.1;几何模型的建立
本文以某无副车架的渣土自卸汽车为研究对象,某无副车架渣土自卸汽车的车架结构如图1所示。该
车架主要由2根主纵梁,2根副纵梁和5根横梁组成。车架长7;600;mm,前端宽992;mm,后端宽842;mm,整个车架是一个前宽后窄的变宽结构,横梁与纵梁之间采用铆钉连接。主纵梁的截面厚度为8;mm,副纵梁的截面厚度为5;mm,车架的驾驶室承载、举升油缸、翻转支座及各个横梁的布置基本继承原结构。
1.2;建立有限元模型
1);在HyperMesh软件中,打开车架三维几何模型,并进行网格划分。主副縱梁及各横梁等钢板结构部件采用边长为10;mm的四边形和三角形的混合板壳单元进行划分;对于驾驶室承载、弯管梁、举升支座以及V推横梁等铸件,采用边长为10;mm的四面体单元进行划分。
2);在车架主副纵梁、横梁、举升支座及翻转支座等构件之间采用铆钉、螺栓及焊接这3种连接方式。将各构件之间的每个装配孔边缘的单元节点与装配孔中心采用刚性单元,建立约束关系来模拟铆钉和螺栓装配关系[14];将构件之间相邻网格的节点采用刚性单元rigids建立约束关系来模拟焊接装配关系[15-16]。
关键词:;;渣土自卸汽车;;车架;;有限元分析;;轻量化
中图分类号:;U463.32;文献标识码:;A
收稿日期:;2019-08-20;;修回日期:;2019-11-15
基金项目:;;山东省重点研发计划项目(2017CXGC0510)
作者简介:;;宋夫杰(1992-),男,山东聊城人,硕士研究生,主要研究方向为汽车动态仿真与控制技术。
4);车架的纵梁及横梁所采用的材料为ZQS500L钢板,车架材料的性能参数如表1所示。车架结构的有限元模型如图2所示,包括3;682;585个单元数和1;067;864个节点数。
1.3;边界条件的确定
在本文建立的车架有限元模型中,前桥的作用力通过前钢板弹簧传递到车架上,因此将前桥的约束点确定在前钢板弹簧的中心处,而后桥约束点确定在后钢板弹簧的两端节点处。
无副车架的渣土自卸汽车车架结构强度有限元分析
作者:宋夫杰程晓东陈贯祥刘大维
来源:《青岛大学学报(工程技术版)》2020年第01期
摘要:;;针对渣土自卸汽车车架存在的安全问题,本文以某无副车架的渣土自卸汽车为研究对象,建立了无副车架的渣土自卸汽车的车架几何模型,并对该车架的几何模型进行网格划分,建立有限元分析模型,同时采用HyperMesh有限元分析软件,对车架的结构强度进行静态分析。根据有限元计算结果,对车架结构进行改进设计。研究结果表明,在3种工况条件下,改进结构与原结构相比,最大应力值分别下降了31.01%,37.29%,36.63%,34.76%和42.89%,改进结构使车架应力大区域的强度有明显提高,而且主副纵梁、横梁及翻转支座等构件的应力值也明显减小;在举升工况下,V推支座横梁与主副纵梁铆钉连接处的改进结构与原结构相比,应力值小于材料的屈服极限,基本满足材料的屈服极限要求;改进车架结构的质量与原结构相比,增重30;kg,与有副车架的结构相比,减重70;kg,实现了汽车轻量化。该研究为企业实现汽车轻量化提供了参考依据。
3);由悬架系统变形情况可以得到车架在实际使用过程的真实应力分布情况。本文利用HyperMesh软件中的Beam梁单元模拟钢板弹簧,根据钢板弹簧的弯曲刚度和长度,确定模拟钢板弹簧的梁单元截面尺寸及形状,保证梁单元与实际钢板弹簧具有同样的力学特征。钢板弹簧与车架之间由吊耳连接,采用刚性单元RB;刘大维(1957-),男,吉林长春人,博士,教授,硕士生导师,主要研究方向为汽车动态仿真与控制技术、地面-车辆系统与控制技术。Email:;qdldw@
渣土自卸汽车是适用于城市内运输要求的专用自卸汽车。渣土自卸汽车的车架,不但承担发动机、底盘及装载物的质量,而且还要承受汽车行驶及卸载过程中产生的各种力和力矩[1],因此整车能否正常行驶及整车是否具有足够的安全性能与车架是否可靠有密切关系。随着有限元技术的飞速发展以及计算机硬件的进步,有限元技术在车架等汽车零部件的设计与分析中被广泛应用[2-8]。许多研究者应用有限单元法进行计算,研究结构损坏的原因,找出危险区域和部位,提出改进设计的方案,并进行相应的计算分析,直到找到最优的方案为止。针对某半挂牵引车车架,刘大维等人[9-10]采用Nastran有限元分析软件,建立了有限元分析模型,并对其在各种工况下的车架强度进行分析。同时,对半挂牵引车在使用过程中出现的车架异常断裂问题,建立了以板壳单元为基本单元的半挂牵引车车架有限元分析模型,对车架强度进行静态及模态分析,为半挂牵引车车架的设计及改进提供了参考依据;赵文杰[11]在汽车车架故障诊断中应用模态分析技术进行了进一步深层次的研究;王勇等人[12]对某重型载货汽车车架动态特性进行了深入分析;宫唤春等人[13]为使车架具有更好的动态性,根据某电车车架的模态分析结果,对其结构进行了修改,定量地提出了改进措施,进一步改良了车架性能。基于此,本文主要对无副车架的渣土自卸汽车车架结构强度进行有限元分析,建立了无副车架的渣土自卸汽车的车架几何模型,并对该车架的几何模型进行网格划分,同时采用HyperMesh有限元分析软件,对车架结构强度进行了强度静态分析。该研究满足承载要求,为车架结构的设计与改进提供了理论依据。
在计算过程中,车架有限元模型的质量平均分配到各单元上;驾驶室、发动机、变速箱、燃油箱、蓄电池的质量简化为均布载荷,并按其作用的位置分配到相应的支撑单元上;液压缸的质量按其作用位置简化为集中载荷,分配到相应的支撑节点上;由整车装载质量产生的载荷,通过车箱传给车架。在静载状态下,车箱和车架之间的作用力以均布载荷的形式传递,而在举升等动载状态下,以集中力的形式传递,两种状态下力的传递并非完全传递,而是与车箱的刚度有关。以钢-钢结构连接的车箱与车架,车箱刚度对车架刚度有一定的贡献,因此车箱和车架共同承担总载荷,其承受载荷的比例约为3∶7;以木-钢结构连接的车箱与车架,由于车箱刚度较小,不超过总载荷的6%,且由车箱承担,因此总载荷基本上是由车架承受[18]。本文所研究的无副车架的渣土自卸汽车,其车架与车箱之间的连接属于钢-钢连接,因此,车架所承受的载荷按照总载荷的7/10计算。