SPC工具分享.pptx
合集下载
SPC(五大工具)精品PPT课件
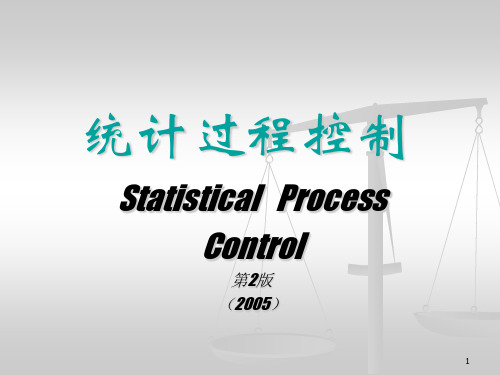
累计 频率%
29 49 68 81 87 100
频 数
累 计 频 率
18
排列图(巴雷特图)
4 分析图形
结论 :由排列图可见,处于 80%以内的因素有三项,即 空调,供电,供水为本季度 顾客投诉较多的项目
5 注意事项
--主要因素不要超过3个 --不太重要的因素可合并
到“其他” 缩短横标 --若各因素发生次数相差不大
4
检测和预防
--对最终产品质量靠质量检验保证,即 剔除不合格品;
--对最终工作/服务质量靠检查和重新工作 这就是一种容忍浪费的意识,既容忍将时
间、材料等资源投入到生产不一定有用的 产品或服务中 --在第一步就预防产生无用的输出 “第一次就做好”,这是一种避免浪费的 意识
5
SPC-由产品控制 过程控制的需要
--抽样技术 --产品判断 --试验管理 --测量系统分析 --不合格品控制 业绩,成本和效率分析
11
统计过程控制原理
采集数据 --测量过程和产品特性
分析数据 --应用统计原理和工具分析特性
评价变差 --寻找过程及产品特性的改进机会
改进实施 --基于统计数据分析和变差评估确定改进 措施并实施过程改进
方图
散布图
控制图
16
排列图(巴雷特图)
原理:关键的少数,次要的多数—2/8原理
步骤:1 收集一定时间内的数据 例:某大厦物业管理公司物业部8—10月收 到的顾客投诉共95次,分布如下表;
顾客投诉事项 供电系统不良 空调系统不良 供水系统不良 电梯系统不良
次数 19 28 17 6
则应重新考虑因素的分类 -- 纵坐标的频数还可为价值,重量,件数等
C B A
Spc培训(五大工具)ppt课件
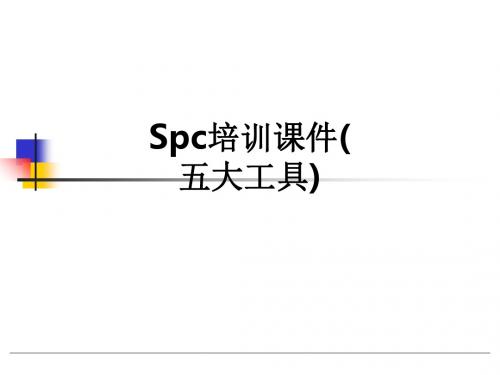
19
μ ± Kσ μ ±0.67σ
在内之或然率 50.00%
在外之或然率 50.00%
μ ±1σ μ ±1.96σ μ ±2σ μ ±2.58σ μ ±3σ
68.26% 95.00% 95.45% 99.00% 99.73%
31.74% 5.00% 4.55% 1.00% 0.27%
控制限的宽度就是根据这一原理定为3。 1924年,休哈特博士建议用界限 µ± 3σ作为 控制界限来管理过程。即我们常说的3σ管理。
LCL=D3R=
*
极差(R 图)
日期
时间 1 2 3 4 5
读 数 和
X=
子组容量 A2 2 1.88 3 1.02 4 .73 5 .58 6 .48 7 .42 8 .37 9 .34 10 .31
D3 * * * * * .08 .14 .18 .22
D4 3.27 2.57 2.28 2.11 2.00 1.92 1.86 1.82 1.78
38
2. 计算控制限
首先计算极差的控制限,再计算均值的控制限 。
2-1 计算平均极差(R)及过程均值(X)
R=(R1+R2+…+Rk)/ k(K表示子组数量) X =(X1+X2+…+Xk)/ k 2-2 计算控制限 计算控制限是为了显示仅存在变差的普通原因时子组的均 值和极差的变化和范围。控制限是由子组的样本容量以及反 映在极差上的子组内的变差的量来决定的。 计算公式: UCLx=X+ A2R UCLR=D4R LCL x=X - A2R LCLR=D3R
29
3.3 使用控制图的准备
1、确定测量系统 a 规定检测人员、环境、方法、数量、频率、设备 或量具。 b 确保检测设备或量具本身的准确性和精密性。 2、使不必要的变差最小 确保过程按预定的方式运行 确保输入的材料符合要求 恒定的控制设定值
SPC分析控制过程的主要工具(共113张)

预防-避免浪费。第一步就避免生产无 用的产品,而应用SPC方法是最重要 的保证。
第3页,共113页。
人
机
料
检入
产品
过程(guòchéng)活动
顾客
法
检出
环
检
取样
需求和期望
SPC
第4页,共113页。
SPC是一种(yī 反馈系统 zhǒnɡ)
1、过程定义 共同作用于产生输出的供方、生产者、
机、料、法、环、检、顾客之集合。 过程的性能取决于供方与顾客之间的沟
85%
如果仅存在变差的普通原因,随着时 间的推移,过程的输出形成一个稳定 的分布并可预测
第12页,共113页。
统计过程控制概论
有关过程变差的理解
★特殊性 Specical cause(也称偶然性)原因(yuányīn)引起的变异:
属于可以避免的,也必须避免的变异,如不同批原料之间
15%
的差异、未经培训的不熟练的操作人员、设备的故障等。
特殊原因能造成分布图形变化,使预测失效。
第16页,共113页。
数据的收集、整理与分析
过程或数据分布的形态
峰态分析
σ变化,而μ不变
正常分配形态
数据的分布服从正态分布(μ,σ) 2 既分布平均值为μ,标准差为σ,
根据这两个特性值就可以确定出这一组 数据的分布形态。
我们希望是正态分布的过程
版权所有,严禁(yánjìn)翻印
1、监视X均值与目标值是否一致? 2、对过程进行长期性能分析。 过程的改进 ,普通变差减小后,控制限
也相应变小。
第26页,共113页。
控制 图的益处 (kòngzhì)
控制图在现场为操作人员采取措施时提供可靠的信息。 稳定状态的过程控制图,其性能是可预测的,能给供
第3页,共113页。
人
机
料
检入
产品
过程(guòchéng)活动
顾客
法
检出
环
检
取样
需求和期望
SPC
第4页,共113页。
SPC是一种(yī 反馈系统 zhǒnɡ)
1、过程定义 共同作用于产生输出的供方、生产者、
机、料、法、环、检、顾客之集合。 过程的性能取决于供方与顾客之间的沟
85%
如果仅存在变差的普通原因,随着时 间的推移,过程的输出形成一个稳定 的分布并可预测
第12页,共113页。
统计过程控制概论
有关过程变差的理解
★特殊性 Specical cause(也称偶然性)原因(yuányīn)引起的变异:
属于可以避免的,也必须避免的变异,如不同批原料之间
15%
的差异、未经培训的不熟练的操作人员、设备的故障等。
特殊原因能造成分布图形变化,使预测失效。
第16页,共113页。
数据的收集、整理与分析
过程或数据分布的形态
峰态分析
σ变化,而μ不变
正常分配形态
数据的分布服从正态分布(μ,σ) 2 既分布平均值为μ,标准差为σ,
根据这两个特性值就可以确定出这一组 数据的分布形态。
我们希望是正态分布的过程
版权所有,严禁(yánjìn)翻印
1、监视X均值与目标值是否一致? 2、对过程进行长期性能分析。 过程的改进 ,普通变差减小后,控制限
也相应变小。
第26页,共113页。
控制 图的益处 (kòngzhì)
控制图在现场为操作人员采取措施时提供可靠的信息。 稳定状态的过程控制图,其性能是可预测的,能给供
SPC五大工具课件

统计学基础
在先期质量策划中必须确定每一 过程使用的统计工具,并包含在
控制计划中
--摘自TS16949之8.1.1
统计学基础
160
100
140
90
120
80 70
100
60
80
50
60
40
40
30 20
20
10
0
0
AB C D E F G70源自605040
30
20
10
0.1
0.3
0.5
0.7
0.9 0
--对最终产品质量靠质量检验保证,即 剔除不合格品;
--对最终工作/服务质量靠检查和重新工作 这就是一种容忍浪费的意识,既容忍将时
间、材料等资源投入到生产不一定有用的 产品或服务中 --在第一步就预防产生无用的输出 “第一次就做好”,这是一种避免浪费的 意识
SPC-由产品控制 过程控制的需要
产品控制
累计 频率%
29 49 68 81 87 100
频 数
累 计 频 率
排列图(巴雷特图)
4 分析图形
30
结论 :由排列图可见,处于 25 80%以内的因素有三项,即 空调,供电,供水为本季度 20
顾客投诉较多的项目
15
5 注意事项 10 --主要因素不要超过3个
--不太重要的因素可合并
5
到“其他” 缩短横标 --若各因素发生次数相差不大 0
判断产品质量的接收 与拒收,随机抽取的 数据取自于某批产品
质量管理常用统计工具
排列图
头脑风暴法
抽样技术
散布图
因果分析图 对策表 直方图 控制图
排列图(巴雷特图)
SPC-完整版ppt课件

第六步:实施数据采集计划
根据“合理子组”原则采集数据。将采集到 的所有数据填入事先准备好的数据表或控制图。
第七步:整理核对数据
检查核对数据是否符合要求,准备制作控制 图。
注意:控制图数据是一组动态的 时间序列。
SHIRO原则”
“合理子组”原则含义
使得每个子组内的变差尽量小(组内差异只由普通 原因造成);
SHIRONGWEI
21
§5.2 数据收集计划
数据必须“真实-可信-可用”,方能到成质量改进的目 的,为了实现此目标,制定数据采集计划是必要的(当 然不一定是书面的)。 计划应考虑以下内容和因素: 任务及目的(你打算收集什么数据) 在哪里?由谁? 采用什么方式:全数检查?还是抽样? 采集多少数据? 时间:何时期的数据?采集频率?何时开始和结束? 分层因素如何确定? 数据表格的准备
控制图结构 控制图的作用 两类错误 休哈特“3σ原则” 统计控制状态 统计过程控制原则 漏斗实验 控制图解析——模式 控制图 8条判异准则 分析用控制图和监控用控制图 常规控制图的分类 如何选择控制图
SHIRONGWEI
16
§4.2 控制图的作用
控制图是SPC用于改进品质的工具,其作用:
展示过程
即时记录过程,反映过程状况和变化,可谓一部“生产史”。
控制过程
透过控制图结构和规则,指引人员识别并消除特殊原因, 达成维护控制之目的。
评估决策
控制图作为统计工具,展示提供的过程信息是客观可信 的,借助控制图信息作出的品质决策是科学可靠的。
预防改进
控制图具有预警性质,且借由以上三项,就达到预防改 进之目的。
SHIRONGWEI
19
质量管理的基本原则
一切用数据说话!
根据“合理子组”原则采集数据。将采集到 的所有数据填入事先准备好的数据表或控制图。
第七步:整理核对数据
检查核对数据是否符合要求,准备制作控制 图。
注意:控制图数据是一组动态的 时间序列。
SHIRO原则”
“合理子组”原则含义
使得每个子组内的变差尽量小(组内差异只由普通 原因造成);
SHIRONGWEI
21
§5.2 数据收集计划
数据必须“真实-可信-可用”,方能到成质量改进的目 的,为了实现此目标,制定数据采集计划是必要的(当 然不一定是书面的)。 计划应考虑以下内容和因素: 任务及目的(你打算收集什么数据) 在哪里?由谁? 采用什么方式:全数检查?还是抽样? 采集多少数据? 时间:何时期的数据?采集频率?何时开始和结束? 分层因素如何确定? 数据表格的准备
控制图结构 控制图的作用 两类错误 休哈特“3σ原则” 统计控制状态 统计过程控制原则 漏斗实验 控制图解析——模式 控制图 8条判异准则 分析用控制图和监控用控制图 常规控制图的分类 如何选择控制图
SHIRONGWEI
16
§4.2 控制图的作用
控制图是SPC用于改进品质的工具,其作用:
展示过程
即时记录过程,反映过程状况和变化,可谓一部“生产史”。
控制过程
透过控制图结构和规则,指引人员识别并消除特殊原因, 达成维护控制之目的。
评估决策
控制图作为统计工具,展示提供的过程信息是客观可信 的,借助控制图信息作出的品质决策是科学可靠的。
预防改进
控制图具有预警性质,且借由以上三项,就达到预防改 进之目的。
SHIRONGWEI
19
质量管理的基本原则
一切用数据说话!
S P C演示文件
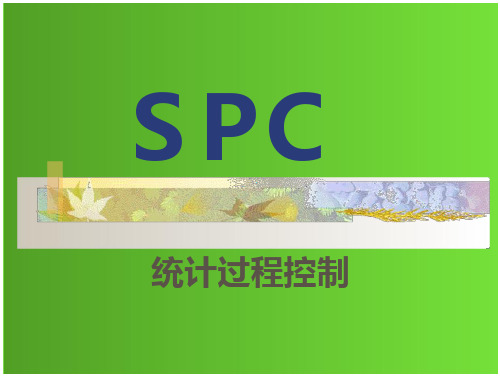
一、正态分布
讨论正态分布,最简单的莫过于用两个参数:均值(µ)与标准
差(σ)来表示。均值(µ)与标准差(σ)的变化对于正态分布的影响见图
由图1可见, 若 均 值 (µ) 增大为µ ´ ,则
曲线向右移动,分布中心发生变化。
由图2可见,若标准差(σ)越大,则加工 质量越分散。标准差(σ)与质量有着密切的
2. 过程性能指数的含义
过程性能指数是利用样本均值和样本标准差通过计算得到的, 反映了当前的取样数据所对应的过程的性能,此时的过程可能处 于稳态,也可能出现了异常,即过程存在偶因也可能还存在异因, 过程性能指数恰好反映了当时过程的性能。过程性能指数是对实 时过程性能的描述。
3. 过程能力指数与过程性能性能指数都是对过程满足标准、规范 程度的反映。
ε为偏移量, K为偏离度。
所以提高Cp、 CpK有下列途径: (1) 减小偏移量,在实际生产过程中采取调整工艺参数的手段,尽
可能使质量特性值的分布中心μ接近目标值M。
(2) 减小σ,即减少偶波,这涉及到质量因素的五个方面:人、机、
料、法、环,需要进行深入的调查研究,确定进一步改进的方 向,并由高层领导确定最终的改造方案。 (3) 在可能的情况下,适当的加大公差的范围。
过程性能指数Pp反映了当前过程加工的均匀性、一致性,
即当前的“过程能力”,是实时分析。 Pp越大,则当前过程的
质量波动越小,过程的性能越强,合格率越高。 Ppk则反映了 当前过程样本均值x与公差中心M存在偏移的情形, Ppk越大越 接近Pp,则样本均值x与与公差中心M二者的偏离程度越小,说 明当前过程的管理水平越高。Ppk离Pp越远,则样本均值x 与 公 差中心M二者的偏离程度越大,说明当前的管理水平亟待提高 ,以实现合格率的迅速提升。 Ppk是当前的“过程能力”与 “ 管理能力”二者综合作用的结果, Pp与Ppk二者的着重点不 同 ,需要同时加以考虑,联合应用,对过程进行分析与判断。
讨论正态分布,最简单的莫过于用两个参数:均值(µ)与标准
差(σ)来表示。均值(µ)与标准差(σ)的变化对于正态分布的影响见图
由图1可见, 若 均 值 (µ) 增大为µ ´ ,则
曲线向右移动,分布中心发生变化。
由图2可见,若标准差(σ)越大,则加工 质量越分散。标准差(σ)与质量有着密切的
2. 过程性能指数的含义
过程性能指数是利用样本均值和样本标准差通过计算得到的, 反映了当前的取样数据所对应的过程的性能,此时的过程可能处 于稳态,也可能出现了异常,即过程存在偶因也可能还存在异因, 过程性能指数恰好反映了当时过程的性能。过程性能指数是对实 时过程性能的描述。
3. 过程能力指数与过程性能性能指数都是对过程满足标准、规范 程度的反映。
ε为偏移量, K为偏离度。
所以提高Cp、 CpK有下列途径: (1) 减小偏移量,在实际生产过程中采取调整工艺参数的手段,尽
可能使质量特性值的分布中心μ接近目标值M。
(2) 减小σ,即减少偶波,这涉及到质量因素的五个方面:人、机、
料、法、环,需要进行深入的调查研究,确定进一步改进的方 向,并由高层领导确定最终的改造方案。 (3) 在可能的情况下,适当的加大公差的范围。
过程性能指数Pp反映了当前过程加工的均匀性、一致性,
即当前的“过程能力”,是实时分析。 Pp越大,则当前过程的
质量波动越小,过程的性能越强,合格率越高。 Ppk则反映了 当前过程样本均值x与公差中心M存在偏移的情形, Ppk越大越 接近Pp,则样本均值x与与公差中心M二者的偏离程度越小,说 明当前过程的管理水平越高。Ppk离Pp越远,则样本均值x 与 公 差中心M二者的偏离程度越大,说明当前的管理水平亟待提高 ,以实现合格率的迅速提升。 Ppk是当前的“过程能力”与 “ 管理能力”二者综合作用的结果, Pp与Ppk二者的着重点不 同 ,需要同时加以考虑,联合应用,对过程进行分析与判断。
质量管理体系五种核心工具SPCPPT课件

Statistical Process Control 统计过程控制 (四)
SPC,即统计过程控制,是一套从生产过程中,定期抽取样本,测量各样本的质量特性值,然后将测得的数据加以统计分析,判断过程是否处于稳定受控状态,从中发现过程异常原因(特殊原因),从而及时采取有效对策,使过程恢复到正常稳定受控状态。 本教材所述的基本统计方法包括与统计过程控制及过程能力分析有关的方法。主要介绍了用来分析及监控过程非常有效的工具--控制图。
2.过程控制系统
什么是过程?过程指的是共同作用以产生输出的供方、生产者、人、设备、输入材料、方法和环境以及使用输出的顾客之集合。
我们工作 的方式/ 资源的融合
人 设备 材料 方法 环境
有反馈的过程控制系统模型
输入 过程/系统 输出
顾客
产品 或 服务
3.变差的普通原因及特殊原因
变差的概念: 没有两件产品或特性是完全相同的,也许差距很大,也许小得无法测量,但差距总是存在的。 任何过程都存在许多引起变差的原因。如:机加工一根轴的直径,影响直径变差的原因有: 机床(间隙、轴承磨损) 刀具(强度、磨损率) 材料(直径、硬度) 操作者(进洽速率、对中准确度) 维修(润滑、易损零件的更换) 环境(温度、湿度、动力供应是否恒定) 造成变差的原因有短期的影响和长期的影响。
一、持续改进及统计过程控制概述
预防与检测 过程控制系统 变差的普通原因及特殊原因 局部措施和对系统采取措施 过程控制和过程能力 过程改进循环及过程控制 控制图--过程控制的工具 控制图的益处
1、预防与检测
检测——容忍浪费 在生产部门,通过检查最终产品并剔除不合格产品。不合格的总是不合格。 在管理部门,经常靠检查或重新检查工作来找出错误。 这实质上是“死后验尸”,造成时间和材料等的浪费。 预防——避免浪费 通过对生产过程的监视和控制,第一步就可以避免生产无用的输出,是避免浪费的有效方法。 当今,汽车制造商、供方及销售商采用有效的预防措施,持续不断改进,提供内、外部顾客满意的产品和服务作为主要目标。
SPC,即统计过程控制,是一套从生产过程中,定期抽取样本,测量各样本的质量特性值,然后将测得的数据加以统计分析,判断过程是否处于稳定受控状态,从中发现过程异常原因(特殊原因),从而及时采取有效对策,使过程恢复到正常稳定受控状态。 本教材所述的基本统计方法包括与统计过程控制及过程能力分析有关的方法。主要介绍了用来分析及监控过程非常有效的工具--控制图。
2.过程控制系统
什么是过程?过程指的是共同作用以产生输出的供方、生产者、人、设备、输入材料、方法和环境以及使用输出的顾客之集合。
我们工作 的方式/ 资源的融合
人 设备 材料 方法 环境
有反馈的过程控制系统模型
输入 过程/系统 输出
顾客
产品 或 服务
3.变差的普通原因及特殊原因
变差的概念: 没有两件产品或特性是完全相同的,也许差距很大,也许小得无法测量,但差距总是存在的。 任何过程都存在许多引起变差的原因。如:机加工一根轴的直径,影响直径变差的原因有: 机床(间隙、轴承磨损) 刀具(强度、磨损率) 材料(直径、硬度) 操作者(进洽速率、对中准确度) 维修(润滑、易损零件的更换) 环境(温度、湿度、动力供应是否恒定) 造成变差的原因有短期的影响和长期的影响。
一、持续改进及统计过程控制概述
预防与检测 过程控制系统 变差的普通原因及特殊原因 局部措施和对系统采取措施 过程控制和过程能力 过程改进循环及过程控制 控制图--过程控制的工具 控制图的益处
1、预防与检测
检测——容忍浪费 在生产部门,通过检查最终产品并剔除不合格产品。不合格的总是不合格。 在管理部门,经常靠检查或重新检查工作来找出错误。 这实质上是“死后验尸”,造成时间和材料等的浪费。 预防——避免浪费 通过对生产过程的监视和控制,第一步就可以避免生产无用的输出,是避免浪费的有效方法。 当今,汽车制造商、供方及销售商采用有效的预防措施,持续不断改进,提供内、外部顾客满意的产品和服务作为主要目标。
- 1、下载文档前请自行甄别文档内容的完整性,平台不提供额外的编辑、内容补充、找答案等附加服务。
- 2、"仅部分预览"的文档,不可在线预览部分如存在完整性等问题,可反馈申请退款(可完整预览的文档不适用该条件!)。
- 3、如文档侵犯您的权益,请联系客服反馈,我们会尽快为您处理(人工客服工作时间:9:00-18:30)。
控制图原理
控制图原理
3、基础知识 (2)、正态分布 (Normal Distribution)
当抽取的数据个数趋于无穷大而区间宽度趋向于0时,外形轮廓的折线就趋向于光滑的曲线, 即:概率密度曲线。
特点:面积之和等于1。 fN (x; 2 , µ ) = (1/ 2)exp(- (x- µ) 2 /2 2 )
目录
目
录
Contents
A 控制图原理
B
判定规则
C 常用控制图
D 过程能力分析改进
控制图原理
1、什么是控制图
是对质量特性值进行测定、记录、评估, 从而监察过程是否处于控制状态的一种用 统计方法设计的图。
控制图的组成
UCL(Upper Control Limit) 上控制限 LCL(Lower Control Limit) 下控制限 CL (Central Line)中心线 按时间顺序抽取的样品统计量数值的描点序列
(1)、控制限的确定
上控制限:UCL= µ +3 中心线: CL= µ
下控制限:LCL= µ 3 (2)、控制图原理的两类错误
控制图判稳与判异的原理是基于小概率事件一次 不发生的原理。
1、虚发报警
过程正常、偶尔出界判异常,a概率,造成寻找根本不 存在原因损失
2、漏发报警
过程异常、但是抽取的点在控制线内,
常规控制图及用途
类别
计 量 值 控 制 图
计 数 值 控 制 图
名称 平均值与极 差控制图 中位数与极 差控制图
个别值与移动 极差控制图
平均值与标准差 控制图
不良数控制图
不良率控制图 缺陷数控制图 单位缺陷数控制图
表示符号
X R
X~ R
X ~ Rm
X
Pn P C U
主要用途和特点
属于双值控制图,它所提供的情报系统完整,适用于 产品批量大,加工过程稳定的情况,适用于每次取样小 于10。
不合格品数 、不合格品率
计量值的数据收集
抽样频率在初始阶段相对高一点,在过程中如发现质量受 控较稳定时,可视情况酌情减少抽样频率,甚至放弃该点 的计量监控。例如在第一个月,每小时抽5个;经过1个月 的监控,质量已稳定,已经有2周时间是CPK值达到了2.0以 上,可采用4个小时抽5个(注:一般不宜采用减少每次抽 样数);又经过一个月,发现CPK还是在2.0以上,且没有大 幅的周期变化的特性,则可放弃该点做计量控制。
控制图原理
2、基本原理 质量波动理论
“人、机、料、法、环” + “软(件)、辅(助材料)、公用系统 质量波动因素 = 偶然因素 +异常因素
偶然因素:过程固有、始终存在、影响微小、难以除去 异常因素:并非固有、时有时无、影响较大、不难去除
小概率原理
小概率事件在一次试验中几乎不可能发生、若发生则判断异常。 超出UCL为千分之一。
用途与特点同上,但处理简单,检出过程不稳定的能力比 不上平均值与极差控制图。适用于每次取样小于10。
● 用于产品批量小,单件加工时间长之产品;有些产品需 要经过一段很长的时间,才能生产完成,才可得到一个 测量值;
● 所选取的样本为一种极为一致的产品,如液体或气体; ● 破坏性的试验,每检验一个,就报废一个; ● 控制一些过程参数,如温度、压力等; ● 适用于每次取样为1,n=1
常规控制图及用途
常见符号
序 号
名称
代号
序 号
名称
代号
01
母体数(批量数)
N
02
样本数(抽样数)
n
03
平均数(均值)
(Bar)
同X—δ图,理论根据充分,对生产过程不稳定检出力强, 样本10<n>25
控制的对象是不良品的件数,每组样本大小相同,适用于 大批量生产。
控制产品的不良率,每组样本抽取大小可以相同,也可以 不相同。
控制对象是产品缺陷数,每个样本大小一定。
样本大小不固定,测量单位数量(如单位面积、单位长 度)的缺陷数来控制产品的质量。
统计过程控制
课程目的
所有产品和服务都是过程的结果。 统计过程控制就是根据产品质量的统计观点,运用数理统
计方法对生产制造过程和服务过程的数据加以收集、整理 和分析,从而了解、预测和监控过程的运行状态和水平。
统计过程控制主要解决两个方面的问题: 一、过程运行状态是否稳定(控制图) 二、过程能力是否充足(过程能力分析)
它们之间是互相独立。
质量管理中的应用
不论µ 与取值如何,产品质量特性落在[µ 3, µ +3]范围内的概率为99.73%。 落在[µ 3, µ +3]范围外的概率为1 99.73%=0.27%, 落在大于µ +3一侧的概率为0.27%/2=0.135% 1。
控制图原理
控制图原理
4、控制图基础知识
查出异因,采取必要措施,加以消除,以恢复统计过程控 制状态。
判定规则
判定规则
判定规则
判定规则
判定规则
案例
案例
案例
常规控制图及用途
计量控制图
计量值的数据收集:按一定时间间 隔抽取一定的样本,然后进行测量, 再将测量到的数据记录下来。计量 型数据具有连续性,故它的抽样计 划与计数值有很大的差异。它通常 根据产品要求,对产品的重要特性
3、如何减少两类错误的损失
经验证明,最优距离为3 ,损失最小
分析用控制图与控制用控制图
控制用控制图
当过程达到了我们所确定的状态后,才能将分析用控制图 的控制线延长作为控制用控制图。
由于后者相当于生产中的立法,故由前者转为后者时应有 正式交接手续。
进入日常管理后,关键是保持所确定的状态。 经过一个阶段的使用后,可能又会出现新的异常,这时应
两个重要的参数: µ (mu)--- 位置参数和平均值(mean value) ,表示 分布的中心位置和期望值
(sigma) --- 尺度参数,表示分布的分散程度和标准偏差 (standard deviation),
两个参数的意义µ (mu)---反映整 Nhomakorabea的综合能力
(sigma) --- 反映实际值偏离期望值的程度,其值越大,表示数据越分散。
定时抽取固定样本个数。
时间、重量、长度、硬度、粘度
计数控制图
根据计数值的理论,计数值具有不连 续性,是以某一批产品为母体来抽取 样本数的,但这会使生产人员无法确 定下一批检验时间。因此,难以做到 质量的预测。因此,建议计数值也尽 量做到连续抽样,这样可以预知下批 的检验时间,也可以根据图形预测下 一步的质量状态。