SMT车间作业流程及生产工艺
SMT车间生产工艺流程图

SMT车间生产工艺流程图一、引言SMT(表面贴装技术)是一种电子元器件自动化贴装技术,广泛应用于电子制造业。
本文将详细介绍SMT车间的生产工艺流程图,包括原材料采购、贴片、焊接、检测等环节。
二、原材料采购1. 原材料准备:根据生产计划,采购所需的电子元器件、PCB板、焊接材料等原材料。
2. 供应商选择:选择可靠的供应商,确保原材料的质量和供货稳定性。
3. 采购流程:与供应商进行洽谈、签订采购合同,按照合同约定的时间和数量进行采购。
三、贴片工艺1. PCB板准备:将采购的PCB板送至SMT车间,进行表面处理,确保贴片粘附的质量。
2. 贴片机操作:将电子元器件通过贴片机自动精确定位,粘贴到PCB板上的预定位置。
3. 贴片质量控制:通过视觉检测系统对贴片进行质量检测,确保贴片的准确性和质量。
4. 回流焊接:将贴片后的PCB板送至回流焊接设备,进行焊接,确保电子元器件与PCB板的可靠连接。
四、焊接工艺1. 焊接准备:将焊接材料(如焊锡膏)准备好,根据焊接工艺要求,对焊接设备进行调试和校准。
2. 焊接操作:将贴片后的PCB板送至焊接设备,进行焊接操作,确保焊接的质量和可靠性。
3. 焊接质量控制:通过焊接后的视觉检测系统对焊接点进行质量检测,确保焊接的准确性和质量。
五、检测工艺1. AOI检测:采用自动光学检测设备对焊接后的PCB板进行自动光学检测,检测焊接点的质量和准确性。
2. X光检测:采用X光设备对焊接点进行非破坏性检测,检测焊接点的焊接质量和连接可靠性。
3. 功能测试:对焊接后的电子产品进行功能测试,确保产品的性能和功能符合要求。
六、包装与出货1. 包装准备:根据产品要求,选择适当的包装材料,对产品进行包装。
2. 包装操作:将经过检测的电子产品进行包装,确保产品在运输过程中不受损。
3. 出货:将包装好的产品按照订单要求进行出货,确保及时交付给客户。
七、总结SMT车间的生产工艺流程图涵盖了原材料采购、贴片、焊接、检测、包装与出货等环节。
SMT车间作业流程图及工艺

SMT车间作业流程图及工艺
SMT生产工艺Check List
验证内容:SMT 其它
拟制:审核:批准:
一、过程关键工序控制:
①合格率=合格数÷投入总数以该工序实际生产的数量填写,无该工序时不填写。
二、IPQC检验合格率
①合格率=合格数÷检查数
三、可生产性及改善建议
四、生产结论
□生产正常,不需作任何更改。
□不可以正常生产,必须重新改进后再生产。
拟制:审核:批准:
精品文档精心整理
附3 废水、噪声、粉尘、固体废弃物处理工艺流程图1、废水处理
2、噪声处理
3、粉尘处理
4固体废弃物处理
精品文档可编辑的精品文档。
SMT车间生产工艺流程图

SMT车间生产工艺流程图标题:SMT车间生产工艺流程图引言概述:SMT(表面贴装技术)是一种表面组装技术,广泛应用于电子产品的生产中。
SMT车间生产工艺流程图是指在SMT生产过程中,各个工艺环节的流程图示,帮助生产人员清晰地了解整个生产流程,提高生产效率和质量。
本文将详细介绍SMT车间生产工艺流程图的内容。
一、原材料准备阶段1.1 采购原材料- 确定所需原材料种类和规格- 选择信誉良好的供应商进行采购- 确保原材料的质量符合生产要求1.2 原材料检验- 对采购回来的原材料进行外观和规格检查- 进行化学成分和物理性能测试- 对合格的原材料进行标记和存放1.3 原材料清洁处理- 对原材料进行清洁处理,去除表面油污和杂质- 使用专业设备进行清洁处理,确保原材料表面光洁度- 将清洁后的原材料进行分类和存放二、PCB制板阶段2.1 PCB设计- 根据产品要求进行PCB设计- 确定PCB的层数和布线规则- 通过设计软件生成PCB文件2.2 PCB制板- 根据PCB设计文件进行制板- 选择合适的基板材料和工艺- 进行电路板的印刷、蚀刻和钻孔等工艺2.3 PCB检验- 对制作好的PCB进行外观检查- 进行电路连通性测试- 确保PCB质量符合要求,无缺陷三、贴片阶段3.1 贴片机设定- 根据SMT生产工艺要求设置贴片机参数- 确定贴片机的速度和精度- 进行贴片机的校准和测试3.2 贴片操作- 将元器件按照BOM表进行分类和准备- 将元器件放置在贴片机的上料器上- 启动贴片机进行自动贴片作业3.3 贴片检验- 对贴片完成的PCB进行外观检查- 进行元器件的位置和极性检查- 确保所有元器件都正确贴片并焊接牢固四、焊接阶段4.1 焊接工艺设定- 根据焊接要求设定焊接工艺参数- 确定焊接温度、时间和压力等参数- 进行焊接设备的校准和测试4.2 焊接操作- 将焊接好的PCB放置在焊接设备上- 启动焊接设备进行焊接作业- 确保焊接质量符合要求4.3 焊接检验- 对焊接完成的PCB进行外观检查- 进行焊接点的连通性测试- 确保焊接质量良好,无虚焊和短路等问题五、检测与包装阶段5.1 功能测试- 对焊接完成的PCB进行功能测试- 确保电路板的功能正常- 对测试结果进行记录和分析5.2 清洁处理- 对测试通过的PCB进行清洁处理- 去除焊接残留物和污垢- 确保PCB表面光洁度5.3 包装出货- 对清洁处理完成的PCB进行包装- 确保包装符合运输要求- 将包装好的PCB进行出货结论:SMT车间生产工艺流程图是SMT生产过程中的重要工具,能够帮助生产人员清晰地了解整个生产流程,提高生产效率和质量。
SMT车间生产工艺流程图

SMT车间生产工艺流程图一、引言SMT(表面贴装技术)是一种电子元器件表面贴装的技术,广泛应用于电子制造业。
为了提高生产效率和质量,制定一份详细的SMT车间生产工艺流程图是必要的。
本文将详细描述SMT车间的生产工艺流程,包括以下几个部分:物料准备、印刷、贴装、回流焊接、检测和包装。
二、物料准备1. 物料采购:根据生产计划和需求,采购所需的电子元器件、PCB板和焊接材料等。
2. 物料接收:接收采购的物料,并进行验收和入库,确保物料的质量和数量符合要求。
3. 物料配送:根据生产计划,将需要的物料按照工单和产品进行配送到相应的工作站。
三、印刷1. PCB板准备:将需要进行贴装的PCB板取出,并进行清洁和检查,确保表面平整和无损坏。
2. 印刷准备:准备印刷机和印刷模板,根据工单要求调整印刷机的参数和印刷模板的位置。
3. 印刷过程:将焊膏均匀地印刷在PCB板的焊盘上,确保焊盘的覆盖率和厚度符合要求。
4. 印刷检测:对印刷后的PCB板进行检测,包括焊膏覆盖率、焊盘位置和焊盘形状等。
四、贴装1. 贴装准备:准备贴装机和贴装料带,根据工单要求调整贴装机的参数和贴装料带的位置。
2. 贴装过程:将电子元器件从贴装料带上取出,并精确地贴装在PCB板的焊盘上。
3. 贴装检测:对贴装后的PCB板进行检测,包括元器件位置、极性和焊盘连接等。
五、回流焊接1. 回流焊接准备:准备回流焊接炉,根据工单要求调整回流焊接炉的参数和温度曲线。
2. 回流焊接过程:将贴装完成的PCB板放入回流焊接炉中,通过加热使焊膏熔化,实现元器件和焊盘的连接。
3. 回流焊接检测:对回流焊接后的PCB板进行检测,包括焊点质量、焊接温度和焊盘连接等。
六、检测1. 外观检测:对焊接完成的PCB板进行外观检查,包括焊点质量、元器件位置和焊盘连接等。
2. 电气检测:使用测试设备对PCB板进行电气性能测试,确保电路的正常工作。
3. 功能检测:根据产品要求,对PCB板进行功能性能测试,确保产品的质量和可靠性。
SMT生产作业流程介绍
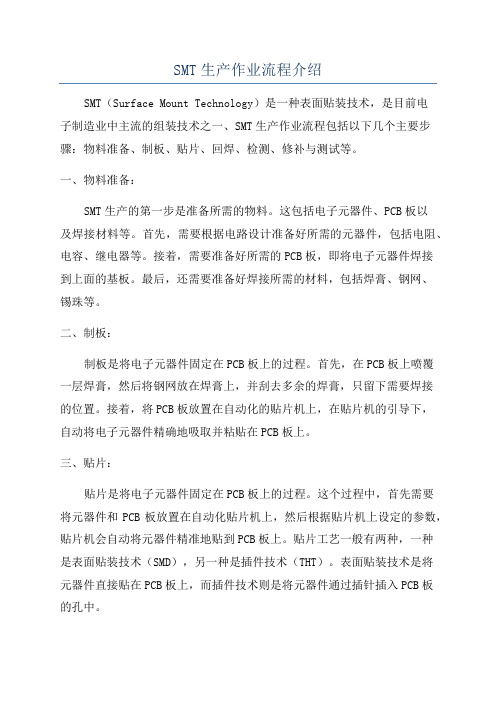
SMT生产作业流程介绍SMT(Surface Mount Technology)是一种表面贴装技术,是目前电子制造业中主流的组装技术之一、SMT生产作业流程包括以下几个主要步骤:物料准备、制板、贴片、回焊、检测、修补与测试等。
一、物料准备:SMT生产的第一步是准备所需的物料。
这包括电子元器件、PCB板以及焊接材料等。
首先,需要根据电路设计准备好所需的元器件,包括电阻、电容、继电器等。
接着,需要准备好所需的PCB板,即将电子元器件焊接到上面的基板。
最后,还需要准备好焊接所需的材料,包括焊膏、钢网、锡珠等。
二、制板:制板是将电子元器件固定在PCB板上的过程。
首先,在PCB板上喷覆一层焊膏,然后将钢网放在焊膏上,并刮去多余的焊膏,只留下需要焊接的位置。
接着,将PCB板放置在自动化的贴片机上,在贴片机的引导下,自动将电子元器件精确地吸取并粘贴在PCB板上。
三、贴片:贴片是将电子元器件固定在PCB板上的过程。
这个过程中,首先需要将元器件和PCB板放置在自动化贴片机上,然后根据贴片机上设定的参数,贴片机会自动将元器件精准地贴到PCB板上。
贴片工艺一般有两种,一种是表面贴装技术(SMD),另一种是插件技术(THT)。
表面贴装技术是将元器件直接贴在PCB板上,而插件技术则是将元器件通过插针插入PCB板的孔中。
四、回焊:回焊是将焊接材料熔化,使电子元器件固定在PCB板上的过程。
将贴片好的PCB板放入回流焊炉中,通过加热回流炉,使焊膏熔化,并与元器件及PCB板表面形成可靠的焊接连接。
回焊过程中需要控制好温度和时间,以保证焊接质量。
五、检测:检测是对焊接完成的PCB板进行质量检验的过程。
通过视觉检测系统、X射线检测、AOI检测等方法,对焊点和元器件的焊接质量进行检查。
同时也需要检查电路板上是否存在短路、开路等问题。
如果发现有焊接不良的问题,需要进行修补。
六、修补:修补是在检测过程中发现问题后对焊接不良的元器件进行修复的过程。
SMT车间生产工艺流程图

SMT车间生产工艺流程图一、引言SMT(表面贴装技术)是一种电子组装技术,广泛应用于电子产品的制造过程中。
该技术通过将电子元件直接贴装在印刷电路板(PCB)上,实现电子产品的组装和制造。
本文将详细介绍SMT车间生产工艺流程图,包括以下几个步骤:物料准备、面板准备、贴装、焊接和检验。
二、物料准备1. 物料采购:根据产品的需求,采购所需的电子元件、PCB和焊接材料等。
2. 物料检验:对采购回来的物料进行检验,确保其质量符合要求。
3. 物料上架:将经过检验的物料按照规定的存放位置进行上架,方便后续的取料。
三、面板准备1. PCB准备:根据产品的设计要求,选择相应的PCB板,并进行清洁和防静电处理。
2. 贴片工艺准备:根据产品的贴片工艺要求,设置贴片机的参数和程序。
3. 钢网准备:根据贴片工艺要求,选择合适的钢网,并进行清洁和调整。
四、贴装1. 贴片机操作:将准备好的PCB板放置在贴片机上,并通过设定的程序进行贴装操作。
2. 贴片检验:对贴片完成后的PCB板进行检验,确保贴片的位置和质量符合要求。
3. 二次贴装:对于一些特殊的电子元件,需要进行二次贴装操作,以确保其正确安装在PCB板上。
五、焊接1. 回流焊接:将贴片完成的PCB板放入回流焊接设备中,通过加热和冷却的过程,将电子元件焊接在PCB板上。
2. 焊接检验:对焊接完成的PCB板进行检验,确保焊接的质量和连接可靠。
六、检验1. 外观检验:对焊接完成的PCB板进行外观检查,确保没有明显的缺陷和损伤。
2. 功能测试:对焊接完成的PCB板进行功能测试,确保电子元件的正常工作。
3. 电气测试:对焊接完成的PCB板进行电气测试,确保电路的连接和电性能符合要求。
七、总结SMT车间生产工艺流程图涵盖了物料准备、面板准备、贴装、焊接和检验等多个环节。
通过严格按照流程图进行操作,可以确保电子产品的质量和性能符合要求。
同时,也需要注意物料的质量控制和工艺参数的准确设置,以提高生产效率和产品的可靠性。
SMT车间作业流程及生产工艺

SMT车间作业流程及生产工艺SMT(表面贴装技术)车间是电子制造业中的重要环节,主要负责印刷电路板(PCB)的表面贴装工艺。
下面将介绍SMT车间的作业流程及生产工艺。
第一步是准备工作,包括准备所需的材料和设备。
首先,需要准备好电子元件和PCB板,以及胶水、钢网、贴片机和回流焊接炉等设备。
其次,需要对设备进行调试和校准,以确保其正常工作。
第二步是印刷,即将胶水均匀地印在PCB板的焊盘上。
首先,将钢网固定在印刷机上,然后将胶水倒入印刷机的供胶器中。
接着,将PCB板放置在印刷机的工作台上,通过机器的运动控制系统进行印刷。
印刷机会将胶水从胶水供胶器中挤压出来,并通过钢网上的孔洞将胶水印在PCB板的焊盘上。
完成印刷后,需要对PCB板进行烘干,以使胶水快速固化。
第三步是贴片,即将电子元件精确地粘贴在PCB板上的焊盘上。
首先,将贴片机与设备系统连接,然后通过贴片机的图像识别系统识别每个电子元件的位置。
接着,将电子元件放置在贴片机的吸嘴中,并通过机器的运动控制系统将电子元件精确地贴在PCB板的焊盘上。
在贴片过程中,需要确保电子元件与焊盘的对准度和粘贴牢固度。
完成贴片后,需要对PCB板进行复卷和切割,以将板子切成适当的尺寸。
第四步是回流焊接,即将PCB板放入回流焊接炉中进行焊接。
焊接炉通过控制高温和高湿环境,在短时间内将焊膏熔化并使其与焊盘和电子元件产生化学反应,从而实现焊接。
在焊接过程中,需要控制好焊接温度和焊接时间,以确保焊接质量和可靠性。
第五步是检查,即对焊接完成的PCB板进行质量检查。
首先,通过目视检查和自动光学检测,对PCB板上的焊点、电子元件和焊盘进行检查,确保其质量符合要求。
其次,通过功能和性能测试,对PCB板的功能和性能进行检测,确保其正常工作。
总结起来,SMT车间的作业流程包括准备工作、印刷、贴片、回流焊接和检查。
每个步骤都有相应的工艺要求和操作流程,需要严格控制和执行。
只有保证每个步骤的质量和准确度,才能生产出具有高质量和可靠性的PCB板。
smt车间操作流程

smt车间操作流程SMT(Surface Mount Technology)是一种表面贴装技术,是电子元器件表面贴装的一种方法。
在SMT车间中,操作流程是非常重要的,它直接影响到产品的质量和生产效率。
下面我将为大家介绍一下SMT车间的操作流程。
首先,SMT车间的操作流程通常包括以下几个步骤:物料准备、贴片、回焊、检测和包装。
在物料准备阶段,操作人员需要准备好所需的电子元器件、PCB板和焊膏等材料。
在贴片阶段,操作人员将电子元器件粘贴到PCB板上,这个过程需要使用贴片机来自动完成。
在回焊阶段,操作人员将PCB板放入回焊炉中进行焊接,以确保电子元器件与PCB板之间的连接牢固。
在检测阶段,操作人员会对焊接后的产品进行检测,以确保产品质量符合要求。
最后,在包装阶段,操作人员将产品进行包装,以便于运输和销售。
在SMT车间的操作流程中,每个步骤都需要严格执行,以确保产品质量和生产效率。
首先,在物料准备阶段,操作人员需要仔细检查所使用的材料,确保其质量符合要求。
其次,在贴片和回焊阶段,操作人员需要根据生产工艺要求进行操作,确保电子元器件与PCB板之间的连接牢固。
在检测阶段,操作人员需要使用专业的检测设备对产品进行检测,以确保产品质量符合要求。
最后,在包装阶段,操作人员需要将产品进行适当的包装,以确保产品在运输和销售过程中不受损坏。
总的来说,SMT车间的操作流程是一个复杂而重要的过程,需要操作人员具备专业的技术和严谨的态度。
只有严格执行操作流程,才能确保产品质量和生产效率。
希望以上介绍能帮助大家更好地了解SMT车间的操作流程。
SMT整个工艺流程细则
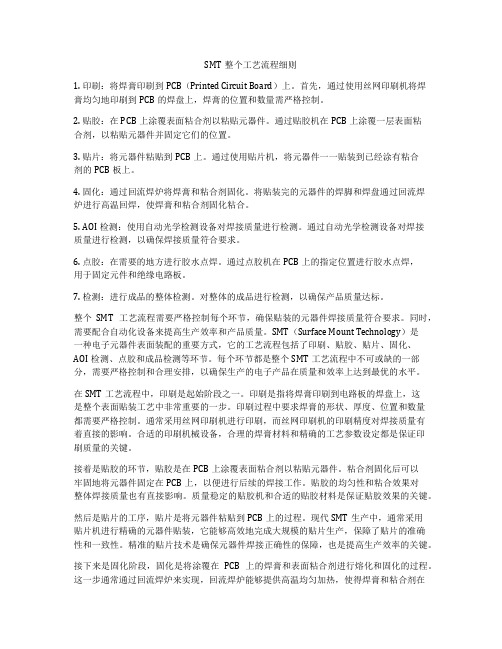
SMT整个工艺流程细则1. 印刷:将焊膏印刷到PCB(Printed Circuit Board)上。
首先,通过使用丝网印刷机将焊膏均匀地印刷到PCB的焊盘上,焊膏的位置和数量需严格控制。
2. 贴胶:在PCB上涂覆表面粘合剂以粘贴元器件。
通过贴胶机在PCB上涂覆一层表面粘合剂,以粘贴元器件并固定它们的位置。
3. 贴片:将元器件粘贴到PCB上。
通过使用贴片机,将元器件一一贴装到已经涂有粘合剂的PCB板上。
4. 固化:通过回流焊炉将焊膏和粘合剂固化。
将贴装完的元器件的焊脚和焊盘通过回流焊炉进行高温回焊,使焊膏和粘合剂固化粘合。
5. AOI检测:使用自动光学检测设备对焊接质量进行检测。
通过自动光学检测设备对焊接质量进行检测,以确保焊接质量符合要求。
6. 点胶:在需要的地方进行胶水点焊。
通过点胶机在PCB上的指定位置进行胶水点焊,用于固定元件和绝缘电路板。
7. 检测:进行成品的整体检测。
对整体的成品进行检测,以确保产品质量达标。
整个SMT工艺流程需要严格控制每个环节,确保贴装的元器件焊接质量符合要求。
同时,需要配合自动化设备来提高生产效率和产品质量。
SMT(Surface Mount Technology)是一种电子元器件表面装配的重要方式,它的工艺流程包括了印刷、贴胶、贴片、固化、AOI检测、点胶和成品检测等环节。
每个环节都是整个SMT工艺流程中不可或缺的一部分,需要严格控制和合理安排,以确保生产的电子产品在质量和效率上达到最优的水平。
在SMT工艺流程中,印刷是起始阶段之一。
印刷是指将焊膏印刷到电路板的焊盘上,这是整个表面贴装工艺中非常重要的一步。
印刷过程中要求焊膏的形状、厚度、位置和数量都需要严格控制。
通常采用丝网印刷机进行印刷,而丝网印刷机的印刷精度对焊接质量有着直接的影响。
合适的印刷机械设备,合理的焊膏材料和精确的工艺参数设定都是保证印刷质量的关键。
接着是贴胶的环节,贴胶是在PCB上涂覆表面粘合剂以粘贴元器件。
SMT各工序作业指导教程
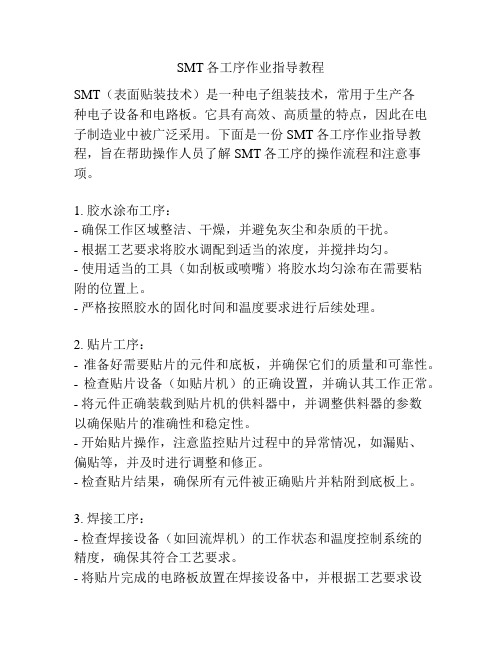
SMT各工序作业指导教程SMT(表面贴装技术)是一种电子组装技术,常用于生产各种电子设备和电路板。
它具有高效、高质量的特点,因此在电子制造业中被广泛采用。
下面是一份SMT各工序作业指导教程,旨在帮助操作人员了解SMT各工序的操作流程和注意事项。
1. 胶水涂布工序:- 确保工作区域整洁、干燥,并避免灰尘和杂质的干扰。
- 根据工艺要求将胶水调配到适当的浓度,并搅拌均匀。
- 使用适当的工具(如刮板或喷嘴)将胶水均匀涂布在需要粘附的位置上。
- 严格按照胶水的固化时间和温度要求进行后续处理。
2. 贴片工序:- 准备好需要贴片的元件和底板,并确保它们的质量和可靠性。
- 检查贴片设备(如贴片机)的正确设置,并确认其工作正常。
- 将元件正确装载到贴片机的供料器中,并调整供料器的参数以确保贴片的准确性和稳定性。
- 开始贴片操作,注意监控贴片过程中的异常情况,如漏贴、偏贴等,并及时进行调整和修正。
- 检查贴片结果,确保所有元件被正确贴片并粘附到底板上。
3. 焊接工序:- 检查焊接设备(如回流焊机)的工作状态和温度控制系统的精度,确保其符合工艺要求。
- 将贴片完成的电路板放置在焊接设备中,并根据工艺要求设置焊接时间和温度。
- 控制焊接过程中的速度和温度变化,确保焊接的质量和一致性。
- 检查焊点的焊接质量,如焊接强度、焊接面积等,并修复任何不良焊点。
- 进行质量检查,并将焊接完成的电路板移至下一个工序。
4. 检测和测试工序:- 确保检测和测试设备的可靠性和准确性,并根据工艺要求进行正确的设定和校准。
- 对贴片和焊接完成的电路板进行外观检查,检查是否有缺陷、损坏或不良连接等问题。
- 进行电气测试和功能测试,确保电路板的性能和功能正常。
- 记录和报告任何异常情况,并做好相应的处理和修正措施。
- 所有检测和测试结果必须符合质量要求才能进行下一步的组装或包装。
以上是SMT各工序作业指导教程的简要介绍,操作人员在进行SMT工艺时,应严格按照工序的要求进行操作,并密切关注质量控制和安全事项。
SMT车间生产工艺流程图

SMT车间生产工艺流程图一、引言SMT(表面贴装技术)是电子创造中常用的一种组装技术,它通过将电子元器件直接粘贴在印刷电路板(PCB)上,实现电子产品的组装。
为了确保生产工艺的高效性和质量的稳定性,制定一份标准化的SMT车间生产工艺流程图是至关重要的。
二、工艺流程1. 材料准备在SMT车间生产工艺流程中,首先需要准备所需的材料。
这包括PCB板、电子元器件、焊接材料(如焊锡膏)、辅助材料等。
材料的选择应根据产品的要求和规格进行。
2. 焊锡膏印刷接下来的步骤是将焊锡膏印刷在PCB板上。
这一步骤使用印刷机进行,通过模板将焊锡膏均匀地印刷在PCB板的焊盘上。
3. 贴装在焊锡膏印刷完成后,进入贴装阶段。
这一步骤涉及将电子元器件粘贴到焊锡膏上。
这可以通过自动贴片机实现,该机器能够根据预先设定的程序将元器件精确地贴到PCB板上。
4. 炉前检查在贴装完成后,进行炉前检查以确保元器件的正确性和位置的准确性。
这通常是使用自动光学检查机进行的,它能够检测元器件的位置、偏移、缺失等问题。
5. 焊接接下来是焊接阶段,将贴好的元器件与PCB板焊接在一起。
这一步骤通常使用回流焊接机进行,将PCB板送入炉中进行加热,使焊锡膏熔化并与元器件和PCB板连接。
6. 冷却与清洁焊接完成后,需要进行冷却和清洁。
冷却可以通过自然冷却或者使用冷却设备来实现。
清洁则可以使用去离子水或者其他清洁剂来清洁焊接后的PCB板,以去除焊锡膏残留物。
7. 电气测试在冷却和清洁完成后,进行电气测试以确保焊接的电子元器件正常工作。
这一步骤通常使用测试设备进行,能够检测电子元器件的电气性能和功能。
8. 包装与出货最后一步是将已经通过电气测试的PCB板进行包装,并准备出货。
包装可以根据客户的要求进行,通常使用防静电袋、泡沫箱等进行包装,以确保产品在运输过程中的安全性。
三、总结SMT车间生产工艺流程图是指导SMT车间生产流程的重要工具。
通过准确细致地描述SMT车间的生产工艺流程,能够确保生产过程的高效性和质量的稳定性。
SMT车间作业流程

SMT车间作业流程1. 引言SMT(表面贴装技术)车间是电子制造中最重要的环节之一。
该车间使用表面贴装技术将电子零件精确地安装在印刷电路板(PCB)上。
本文档将介绍SMT车间的作业流程,包括物料准备、设备设置、质量控制和成品包装等方面。
2. 物料准备在SMT车间之前,需要进行物料准备工作。
这包括:•采购所需的电子零件和印刷电路板(PCB)。
•对电子零件进行分类和标识,以便在后续的装配过程中能够准确选择。
•检查PCB的质量和正确性,以确保其符合设计要求。
3. 设备设置一旦物料准备完毕,下一步是设置SMT设备。
这些设备通常包括以下内容:•贴片机:用于将电子零件精确地安装在PCB上。
根据不同的要求,可以选择手动操作或自动操作的贴片机。
•回流炉:用于将贴片焊接在PCB上,以确保电子零件牢固地粘着在PCB上。
•卤化锡喷泉:用于清洗贴片焊接完毕后的PCB,以去除焊接过程中可能留下的残留物。
在设备设置阶段,操作员需要根据生产需求进行设备调整和参数设置。
这确保了设备在装配过程中的准确性和高效性。
4. 装配过程装配过程是SMT车间的核心部分。
在这个阶段,需要进行以下步骤:4.1 贴片贴片是将电子零件精确地安装在PCB上的过程。
具体步骤如下:1.将PCB放置在贴片机上,并根据PCB的尺寸和形状进行适当的夹持和定位。
2.将预先分类和标识的电子零件加载到贴片机的供料器中。
3.调整贴片机的参数,以确保电子零件精确地安装在PCB上。
4.启动贴片机,它会自动将电子零件精确地放置在PCB上。
4.2 焊接焊接是将电子零件固定在PCB上的过程。
具体步骤如下:1.使用回流炉将PCB和电子零件一起加热。
2.加热后,焊接炉中的焊料会熔化,使电子零件与PCB牢固地连接在一起。
3.控制回流炉的加热曲线,以确保焊接的质量和可靠性。
4.3 清洗清洗是为了去除焊接过程中可能留下的残留物和污垢。
具体步骤如下:1.将焊接完毕的PCB放置在卤化锡喷泉中。
SMT车间生产工艺流程图
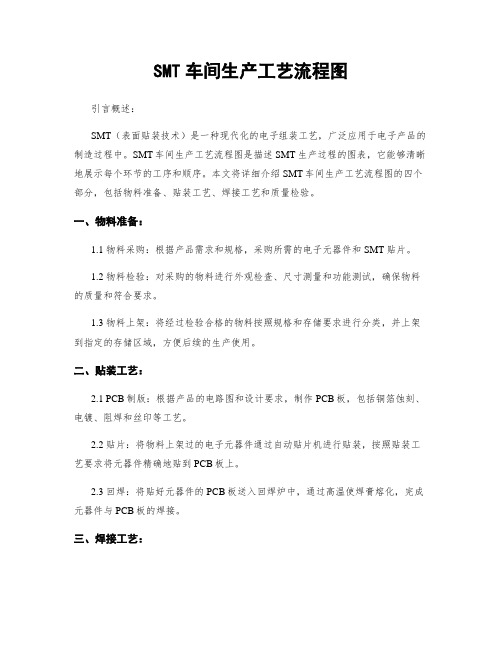
SMT车间生产工艺流程图引言概述:SMT(表面贴装技术)是一种现代化的电子组装工艺,广泛应用于电子产品的制造过程中。
SMT车间生产工艺流程图是描述SMT生产过程的图表,它能够清晰地展示每个环节的工序和顺序。
本文将详细介绍SMT车间生产工艺流程图的四个部分,包括物料准备、贴装工艺、焊接工艺和质量检验。
一、物料准备:1.1 物料采购:根据产品需求和规格,采购所需的电子元器件和SMT贴片。
1.2 物料检验:对采购的物料进行外观检查、尺寸测量和功能测试,确保物料的质量和符合要求。
1.3 物料上架:将经过检验合格的物料按照规格和存储要求进行分类,并上架到指定的存储区域,方便后续的生产使用。
二、贴装工艺:2.1 PCB制版:根据产品的电路图和设计要求,制作PCB板,包括铜箔蚀刻、电镀、阻焊和丝印等工艺。
2.2 贴片:将物料上架过的电子元器件通过自动贴片机进行贴装,按照贴装工艺要求将元器件精确地贴到PCB板上。
2.3 回焊:将贴好元器件的PCB板送入回焊炉中,通过高温使焊膏熔化,完成元器件与PCB板的焊接。
三、焊接工艺:3.1 焊接检验:对焊接完成的PCB板进行外观检查和焊点质量检验,确保焊接质量良好。
3.2 修复和返修:对焊接不良的PCB板进行修复或返修,包括重新焊接、更换元器件等操作,确保焊接质量达到要求。
3.3 清洗和干燥:将焊接完成的PCB板送入清洗机中进行清洗,去除焊接过程中产生的残留物,并通过烘箱进行干燥,确保PCB板的清洁度和干燥度。
四、质量检验:4.1 外观检查:对焊接完成的PCB板进行外观检查,包括焊点质量、元器件位置和PCB板表面的损坏等。
4.2 功能测试:对PCB板进行功能测试,检查电路连接是否正常,元器件是否工作正常。
4.3 抽样检验:对生产过程中的PCB板进行抽样检验,确保整个生产过程的质量稳定性和一致性。
总结:SMT车间生产工艺流程图是SMT生产过程的重要工具,它能够帮助生产人员清晰地了解每个环节的工序和顺序。
smt车间操作流程

smt车间操作流程
SMT(Surface Mount Technology)是一种表面贴装技术,是现代电子制造中常用的一种组装技术。
SMT车间操作流程是指在SMT 生产线上进行电子元件的贴装和焊接的具体操作步骤。
下面将详细介绍SMT车间操作流程。
首先,SMT车间操作流程的第一步是准备工作。
在开始生产之前,操作人员需要检查生产线设备是否正常运转,检查所需的电子元件和PCB板是否齐全,确保生产线的正常运行。
接着,操作人员需要将PCB板放置在传送带上,传送带会将PCB板送至贴装机。
在贴装机上,操作人员会将电子元件粘贴在PCB 板上,这个过程需要非常精准和细致,以确保元件的正确位置和方向。
然后,PCB板会被传送至回流炉进行焊接。
在回流炉中,PCB板会被加热至一定温度,使焊膏熔化并将电子元件固定在PCB板上。
这个过程需要控制好温度和时间,以确保焊接的质量和稳定性。
最后,焊接完成后,PCB板会被传送至检测台进行质量检测。
在检测台上,操作人员会使用各种测试设备对PCB板进行检测,确保电子元件的连接和焊接质量符合标准要求。
总的来说,SMT车间操作流程是一个复杂而精细的过程,需要
操作人员具备丰富的经验和技术,以确保生产线的正常运行和产品质量的稳定性。
通过不断的改进和优化,SMT车间操作流程可以更加高效和可靠地完成电子元件的贴装和焊接,为电子制造业的发展做出贡献。
SMT车间生产工艺流程图

SMT车间生产工艺流程图SMT(表面贴装技术)车间是电子创造工厂中的重要部门,负责将电子元件精确地贴装到印刷电路板(PCB)上。
为了确保生产过程的高效性和准确性,制定和遵循一套标准的工艺流程图是至关重要的。
下面是一个典型的SMT车间生产工艺流程图的标准格式,用于指导SMT车间的操作流程。
1. 准备工作- 检查和准备所需的设备和工具,如贴片机、回流焊炉、检测设备等。
- 检查和准备所需的材料,如PCB板、电子元件、焊接材料等。
- 检查并确保工作区域的清洁和整洁。
2. PCB准备- 检查PCB板的质量和完整性。
- 清洁PCB板以去除任何污垢或者油脂。
- 检查并修复PCB板上的任何损坏或者缺陷。
3. 贴片工艺- 将PCB板放置在贴片机上,并根据工艺要求设置贴片机的参数。
- 检查并校正贴片机的准确性和稳定性。
- 将电子元件按照BOM(物料清单)的要求放置在贴片机的供料器中。
- 启动贴片机,让其自动将电子元件精确地贴装到PCB板上。
- 检查贴片的准确性和质量,如元件位置、焊盘覆盖度等。
4. 回流焊接- 将贴片后的PCB板放置在回流焊炉中,并根据工艺要求设置回流焊炉的参数。
- 启动回流焊炉,让其加热至设定的焊接温度。
- 确保PCB板在回流焊炉中停留足够的时间,以确保焊点的质量。
- 冷却PCB板,使其达到室温。
5. 检测和修复- 使用检测设备对焊接后的PCB板进行全面的功能和质量检测。
- 检查焊点的完整性、连接性和覆盖度。
- 如果发现任何缺陷或者不良品,及时修复或者替换。
- 再次进行全面的功能和质量检测,确保修复后的PCB板符合要求。
6. 包装和出货- 将符合要求的PCB板进行包装,以防止损坏和污染。
- 根据客户要求,进行适当的标识和标记。
- 准备出货文件和记录,如装箱单、发货清单等。
- 安排物流运输,确保及时交付给客户。
以上是一个典型的SMT车间生产工艺流程图的标准格式,用于指导SMT车间的操作流程。
每一个步骤都需要严格遵循,并确保质量和效率的最大化。
SMT车间生产工艺流程图

SMT车间生产工艺流程图一、引言SMT(表面贴装技术)是一种电子制造技术,广泛应用于电子产品的生产过程中。
本文将详细介绍SMT车间的生产工艺流程图,包括各个环节的步骤和所需设备。
二、SMT车间生产工艺流程图概述SMT车间生产工艺流程图主要包括以下几个环节:PCB准备、贴装、焊接、检测和包装。
每个环节都有特定的步骤和所需设备。
三、PCB准备1. PCB(Printed Circuit Board,印刷电路板)准备是SMT车间生产的第一步。
在这个环节,需要进行以下步骤:a. PCB板的检查和清洁:确保PCB板的质量和表面的干净。
b. PCB板的固定:使用夹具或者自动装载设备将PCB板固定在工作台上。
四、贴装1. 贴装是SMT车间生产的核心环节,主要包括以下步骤:a. 贴装元件准备:将需要贴装的元件按照规定的规格和数量准备好。
b. 自动贴装:使用自动贴装机将元件精确地贴到PCB板上。
c. 贴装质量检查:使用视觉检测系统或者其他检测设备对贴装质量进行检查。
五、焊接1. 焊接是将贴装好的元件与PCB板进行连接的过程,包括以下步骤:a. 焊接设备准备:准备好焊接设备,包括焊接台、焊接烙铁等。
b. 手工焊接:使用焊接烙铁对元件进行手工焊接。
c. 焊接质量检查:使用检测设备对焊接质量进行检查,确保焊接牢固可靠。
六、检测1. 检测是SMT车间生产的重要环节,用于确保产品质量,包括以下步骤:a. 视觉检测:使用视觉检测系统对PCB板上的元件进行检查,确保贴装和焊接质量。
b. 功能测试:对已经焊接完成的电子产品进行功能测试,确保其正常工作。
七、包装1. 包装是将生产完成的电子产品进行包装和标识的过程,包括以下步骤:a. 包装准备:准备好包装材料、标签等。
b. 产品包装:将电子产品放入包装盒中,并进行密封。
c. 标识:在包装盒上标注产品型号、序列号等信息。
八、总结SMT车间生产工艺流程图涵盖了PCB准备、贴装、焊接、检测和包装等环节的详细步骤和所需设备。
SMT生产作业流程介绍
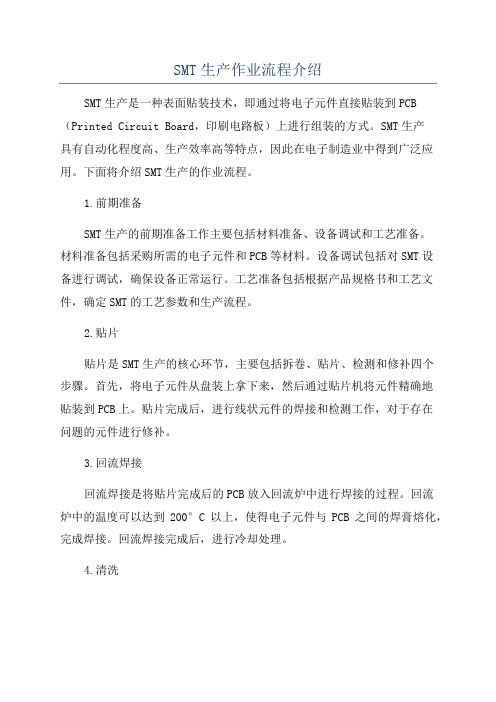
SMT生产作业流程介绍SMT生产是一种表面贴装技术,即通过将电子元件直接贴装到PCB (Printed Circuit Board,印刷电路板)上进行组装的方式。
SMT生产具有自动化程度高、生产效率高等特点,因此在电子制造业中得到广泛应用。
下面将介绍SMT生产的作业流程。
1.前期准备SMT生产的前期准备工作主要包括材料准备、设备调试和工艺准备。
材料准备包括采购所需的电子元件和PCB等材料。
设备调试包括对SMT设备进行调试,确保设备正常运行。
工艺准备包括根据产品规格书和工艺文件,确定SMT的工艺参数和生产流程。
2.贴片贴片是SMT生产的核心环节,主要包括拆卷、贴片、检测和修补四个步骤。
首先,将电子元件从盘装上拿下来,然后通过贴片机将元件精确地贴装到PCB上。
贴片完成后,进行线状元件的焊接和检测工作,对于存在问题的元件进行修补。
3.回流焊接回流焊接是将贴片完成后的PCB放入回流炉中进行焊接的过程。
回流炉中的温度可以达到200°C以上,使得电子元件与PCB之间的焊膏熔化,完成焊接。
回流焊接完成后,进行冷却处理。
4.清洗清洗是为了去除焊接过程中产生的焊渣和残留物,以提高焊接质量。
清洗过程主要使用去离子水和有机溶剂进行。
清洗后,需要进行干燥处理,确保元件表面不含有水分和污染物。
5.检测和测试检测和测试是SMT生产中非常重要的环节。
通过使用专用的检测设备,对贴片和回流焊接后的PCB进行检测,以发现可能存在的缺陷和问题。
测试环节则是对组装后的PCB进行功耗、信号传输等各项性能测试。
6.包装和出货最后一步是将测试合格的PCB进行包装,然后准备出货。
包装可以根据产品的性质选择合适的包装方式,如盒装、纸箱装等。
以上是SMT生产过程的主要环节。
在实际生产过程中,还需要根据具体产品的要求进行调整和优化。
SMT生产的高度自动化和高效率使得其在电子制造业中得到广泛应用,同时也对工作人员的专业技能和操作流程提出了更高的要求。
SMT车间生产工艺流程图

SMT车间生产工艺流程图一、引言SMT(表面贴装技术)是现代电子创造中常用的一种组装技术,它通过将电子元器件直接焊接在印刷电路板(PCB)上,使得电路板的创造更加高效和精确。
本文将详细介绍SMT车间的生产工艺流程图,包括原材料准备、印刷、贴装、回流焊接和检测等环节。
二、原材料准备1. PCB准备:从仓库中取出已经检验合格的PCB板,确保其质量和数量符合生产需求。
2. 元器件准备:根据生产计划,从元器件仓库中取出所需的电子元器件,确保其质量和数量符合要求。
三、印刷1. 程序准备:将设计好的电路板文件导入到SMT设备的控制系统中,并设置印刷参数。
2. 调整设备:根据PCB板的尺寸和元器件的要求,调整印刷机的印刷头位置和印刷压力等参数。
3. 印刷操作:将PCB板放置在印刷机的工作台上,启动设备进行印刷。
印刷机会将焊膏均匀地涂在PCB板的焊盘上。
四、贴装1. 贴装准备:将印刷好的PCB板放置在贴装机的工作台上,同时准备好所需的电子元器件。
2. 调整设备:根据元器件的尺寸和位置要求,调整贴装机的吸嘴位置和吸嘴大小等参数。
3. 贴装操作:贴装机会自动将各个元器件从元器件供料系统中取出,并精确地贴到PCB板的焊盘上。
贴装完成后,检查是否有元器件贴装不许确的情况,并进行调整。
五、回流焊接1. 焊接准备:将贴装好元器件的PCB板放置在回流焊接炉中,同时准备好焊接所需的热风和氮气。
2. 调整设备:根据焊接温度和时间要求,调整回流焊接炉的温度和传送速度等参数。
3. 焊接操作:启动回流焊接炉,炉内的热风会加热PCB板和焊膏,使得焊膏熔化并与焊盘和元器件产生良好的焊接连接。
焊接完成后,取出焊接好的PCB板。
六、检测1. 目视检测:对焊接好的PCB板进行目视检查,确保焊接质量良好,没有焊接不良、短路或者开路等问题。
2. 自动检测:使用自动检测设备对PCB板进行电气测试,检测电路的连通性和元器件的正确性。
3. 修复和返工:如果发现焊接不良或者电路故障,进行修复或者返工操作,确保产品质量符合要求。
SMT车间作业流程
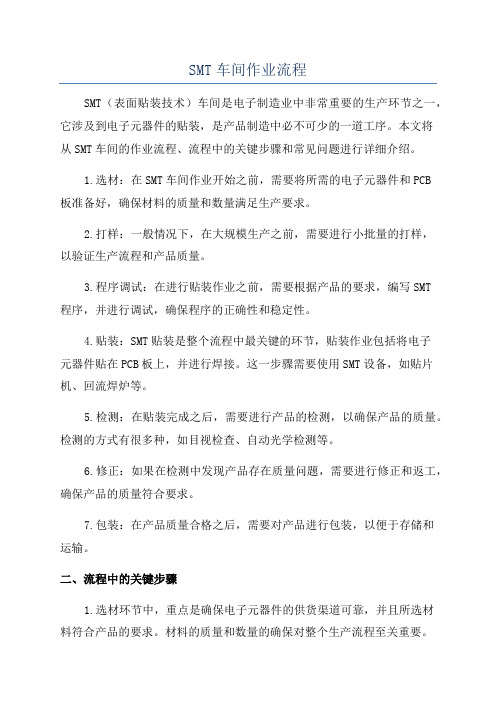
SMT车间作业流程SMT(表面贴装技术)车间是电子制造业中非常重要的生产环节之一,它涉及到电子元器件的贴装,是产品制造中必不可少的一道工序。
本文将从SMT车间的作业流程、流程中的关键步骤和常见问题进行详细介绍。
1.选材:在SMT车间作业开始之前,需要将所需的电子元器件和PCB板准备好,确保材料的质量和数量满足生产要求。
2.打样:一般情况下,在大规模生产之前,需要进行小批量的打样,以验证生产流程和产品质量。
3.程序调试:在进行贴装作业之前,需要根据产品的要求,编写SMT程序,并进行调试,确保程序的正确性和稳定性。
4.贴装:SMT贴装是整个流程中最关键的环节,贴装作业包括将电子元器件贴在PCB板上,并进行焊接。
这一步骤需要使用SMT设备,如贴片机、回流焊炉等。
5.检测:在贴装完成之后,需要进行产品的检测,以确保产品的质量。
检测的方式有很多种,如目视检查、自动光学检测等。
6.修正:如果在检测中发现产品存在质量问题,需要进行修正和返工,确保产品的质量符合要求。
7.包装:在产品质量合格之后,需要对产品进行包装,以便于存储和运输。
二、流程中的关键步骤1.选材环节中,重点是确保电子元器件的供货渠道可靠,并且所选材料符合产品的要求。
材料的质量和数量的确保对整个生产流程至关重要。
2.贴装环节中,关键是要确保贴装精度和贴装质量。
在选择SMT设备的时候,应该考虑设备的准确度和性能。
同时,贴装过程中要严格控制温度和湿度,以免对产品质量产生影响。
3.检测环节是保证产品质量的关键环节。
在进行检测时,要使用可靠的检测设备,并制定合理的检测标准。
另外,及时修正和返工对于保证产品质量也非常重要。
三、常见问题及解决方法1.SMT贴装过程中,可能会出现元器件漏贴或贴片不准的问题。
这时,可以通过调整或更换贴片机的零部件,如吸嘴、吸嘴真空或机器调节来解决。
2.如果出现元器件错位或贴复位不准的问题,可能是贴片机补料不准或气压不稳定所致。
可以对贴片机进行校准或调试,并确保气源的稳定性。
- 1、下载文档前请自行甄别文档内容的完整性,平台不提供额外的编辑、内容补充、找答案等附加服务。
- 2、"仅部分预览"的文档,不可在线预览部分如存在完整性等问题,可反馈申请退款(可完整预览的文档不适用该条件!)。
- 3、如文档侵犯您的权益,请联系客服反馈,我们会尽快为您处理(人工客服工作时间:9:00-18:30)。
1
有无金手指等要求特殊的地方,培训、定位。
2
使用工具是否符合要求。
3
工具是否按要求工艺参数进行使用。
4
后焊时有无大焊盘,能否符合工艺要求参数。
5
是否要做工装夹具(后焊)。
3
是否可用分板机进行分板。
18
是否考虑了足够的补焊操作空间。
19
收板定位是否可使用板架。
20
防止元件被碰坏,培训、定位、拿板和装箱。
四、生产结论
□生产正常,不需作任何更改。
□不可以正常生产,必须重新改进后再生产。
拟制: 审核: 批准:
10、召开生产总结会,全面收集和汇总生产中的各项问题,从设计、工艺、物料、可加工性方面展开分析。
11、拉长记录会议纪要,填写生产报告,报告中的数据和问题必须正确,主管审核才可存档;
中国最大的资料库下载
SMT生产工艺Check List
验证内容:SMT 其它
产品型号
编 码
日 期
拉长
技术员
IPQC
SMT
基本资料
序号
项目
有
无
说明
1
PCB光板。
2
成品样板。
3
元件位置图。
4
PCB的Gerber File或SMT编程文件。
5
客户BOM。
6
公司清单。
7
工位图(仅中试产品)。
8
特殊元件安装说明。
辅料要求
1
锡膏/红胶。
2
助焊剂/锡丝。
PCB评估
1
PCB是否为喷锡板。
2
IC管脚料盘喷锡是否均匀。
3
PCB是否为真空包装。
1
PCB是否方便定位和生产。
2
材料包装是否满足飞达要求。
多功能机
1
PCB是否方便定位和生产。
2
材料包装是否满足飞达要求。
3
是否有带定位销的元件。
4
带定位销的元件的定位孔是否符合要求。
中间定位
1
是否需要中间定位、安排几位、如何安排。
2
有无手贴元件。
3
手贴元件是否距其它元件太近,如何解决。
回流焊
1
客户是否提供可参考的温度曲线要求。
SMT车间作业流程
作业流程图
作业要点及说明
负责人
Yes
OK
Yes
No
NoN
NG
Yes
PASS
1、由拉长和IPQC、物料员确认是否为新产品或车间内首次生产的产品;
2、如果是旧产品且无更改,则直接排计划上线生产;
拉长
IPQC
物料员
3、由主管召开生产准备会,参加人员包括技术员、拉长、IPQC;
4、由主管负责安排人员的准备工作,注意事项,传达客户相关信息,制作《项目进度计划表》;
7、主管跟进试制过程,及时解决反馈生产中的问题点,并记录问题;
8、如果问题较严重影响生产进度,则要停线,并召集技术员、拉长、IPQC开会,分析异常,提出改善措施,必要进还要通知工程部人员参加,直到问题解决后才可恢复生产;
9、生产完成后送IPQC抽检,IPQC必须按照客户的BOM、工艺说明、图纸进行抽检。
2
客户是否提供温度曲线测试板的制作要求。
3
是否对温度有特殊要求的元件。
4
回流焊时,单板是否变形。
收板定位
1
是否能使用板架放置。
2
是否有外观易混元件,培训、定位。
3
是否有手贴元件,培训、定位、重点检查。
4
是否有细间距IC等要求较高元件。
5
为防止元件被碰坏,培训、定位、拿板和装箱。
6
是否有无法克服的品质问题,培训、定位。
主管
技术员
拉长
IPQC
5、各相关员在接到生产信息后,分别准备;
5.1 CP、Check list、BOM和工艺、钢网、物料;
5.2SMT程序、设备;
5.3生产日期及出货排程;
5.4产品检验标准;
5.5培训工人,讲解生产注意事项;
物料员
技术员
主管
IPQC
拉长
6、各相关人员开会确认准备情况,如没有问题则由主管决定开始上线生产,相关人员必须在线跟进生产,如有问题IPQC应及时写《生产反馈单》给主管;
是否有难上锡的元件,对钢网特殊开孔。
8
元件是否与PCB相匹配。
9
是否有元件焊盘宽大,PCB焊盘窄,造成虑焊、少焊。比如电感等。
10
BOM单上位号与印制板上图号、位号不一样。
11
来料是否有氧化现象,是否给生产带来困难。
印锡/印胶
1
PCB是否方便定位和生产(双面板采用托盘定位)。
2
印胶焊盘是否符合IPC标准。
5
PCB是否有Mark点。
6
钢网厚度/锡膏厚度/开口大小。
材料评估
1
最小的元件是什么,机器能否贴。
2
最大的元件是什么,机器能否贴。
3
最高的元件是什么,机器能否贴。
4
最小的间距是多少,机器能否贴。
5
是否有方向难辩认元件,培训工人。
6
是否有外观易混元件,在站位上分隔开。
7
拟制: 审核: 批准:
一、过程关键工序控制:
主要工序
投入数
产出数
合格数
合格率
主要不良点
丝印
贴片机操作
校位
补 焊
Q C
分 板
抽 检
1合格率=合格数÷投入总数 以该工序实际生产的数量填写,无该工序时不填写。
二、IPQC检验合格率
外观检查
检查数: 合格数: 合格率:
主要问题描述
1合格率=合格数÷检查数
三、可生产性及改善建议