较大不锈钢分半薄板件的车削加工工艺
不锈钢薄壁零件的加工工艺分析

不锈钢薄壁零件的加工工艺分析作者:刘兆华来源:《教育教学论坛·上旬》2012年第05期摘要:在机械加工行业中,不锈钢薄壁工件的加工是比较困难的。
由于其材料的切削性能和工件结构刚性均比较差,在加工过程中容易产生振动和变形,其形位和尺寸公差难以得到保证,如果解决方法不得当,会造成大量废品,甚至会使加工无法进行下去。
本文结合一加工实例详述了加工工艺分析、刀具材料、切削用量及切削液选择等问题,对于此类零件加工具有一定参考价值。
关键词:机械加工;薄壁零件;加工工艺中图分类号:G712 文献标志码:A 文章编号:1674-9324(2012)05-0205-03薄壁套类零件的加工特点:第一,薄壁套类零件的刚性很差,车削过程中由于切削力(特别是径向切削力)的作用,极易产生变形与振动,从而影响工件的尺寸精度、形状精度及表面粗糙度。
第二,因为零件壁薄,加之不同材料及加工条件的变化,使车削时受热膨胀变形的规律不易掌握。
所以,工件的尺寸精度不易控制。
第三,在夹紧力的作用下零件容易产生变形,常态下零件的弹性复原能力,将直接影响零件的尺寸精度和形状精度[2]。
而不锈钢薄壁工件的加工难度则更大。
图1是某产品中的一个主要零件,材料为1Cr17Ni2不锈钢,属于薄壁套类零件,数量500件。
以此为例,就其加工工艺方法作一个分析。
一、加工方法选择及工艺分析1.加工方法选择及工序安排。
如图1所示鼠笼支座属于薄壁的套类零件(壁厚只有2.5mm)。
根椐图纸的要求及零件的结构形状,该零件的主要加工方法是车削,是该零件保证尺寸、形位及表面精度的主要工序。
虽然内孔Φ62±0.0095的尺寸及其表面粗糙度Ra0.4的精度要求较高,但只要正确选择刀具材料(如超硬刀具)、车刀几何参数、切削用量、切削液等的条件,是可以满足要求的。
目前,超硬切削的工件表面粗糙度一般可达Ra0.2~Ra0.4,圆度可达0.0005mm,尺寸精度可控制在0.003mm以内。
浅谈不锈钢材料的车削加工
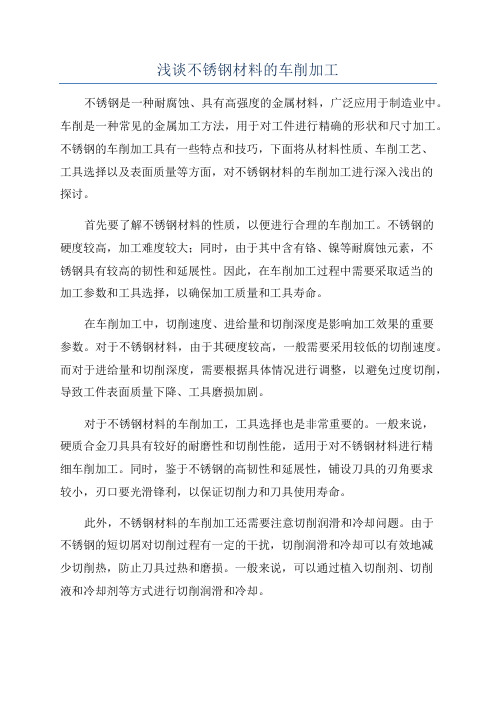
浅谈不锈钢材料的车削加工不锈钢是一种耐腐蚀、具有高强度的金属材料,广泛应用于制造业中。
车削是一种常见的金属加工方法,用于对工件进行精确的形状和尺寸加工。
不锈钢的车削加工具有一些特点和技巧,下面将从材料性质、车削工艺、工具选择以及表面质量等方面,对不锈钢材料的车削加工进行深入浅出的探讨。
首先要了解不锈钢材料的性质,以便进行合理的车削加工。
不锈钢的硬度较高,加工难度较大;同时,由于其中含有铬、镍等耐腐蚀元素,不锈钢具有较高的韧性和延展性。
因此,在车削加工过程中需要采取适当的加工参数和工具选择,以确保加工质量和工具寿命。
在车削加工中,切削速度、进给量和切削深度是影响加工效果的重要参数。
对于不锈钢材料,由于其硬度较高,一般需要采用较低的切削速度。
而对于进给量和切削深度,需要根据具体情况进行调整,以避免过度切削,导致工件表面质量下降、工具磨损加剧。
对于不锈钢材料的车削加工,工具选择也是非常重要的。
一般来说,硬质合金刀具具有较好的耐磨性和切削性能,适用于对不锈钢材料进行精细车削加工。
同时,鉴于不锈钢的高韧性和延展性,铺设刀具的刃角要求较小,刃口要光滑锋利,以保证切削力和刀具使用寿命。
此外,不锈钢材料的车削加工还需要注意切削润滑和冷却问题。
由于不锈钢的短切屑对切削过程有一定的干扰,切削润滑和冷却可以有效地减少切削热,防止刀具过热和磨损。
一般来说,可以通过植入切削剂、切削液和冷却剂等方式进行切削润滑和冷却。
最后,不锈钢材料的车削加工后还需要进行相应的表面处理,以提高工件的表面质量和防锈性能。
一般可以采用研磨、抛光等方式进行表面处理,以增加工件的光洁度和美观度。
总之,不锈钢材料的车削加工是一项综合性的任务,需要考虑材料性质、车削工艺、工具选择以及表面质量等多个方面的因素。
只有合理选择加工参数和工具,严格控制加工过程,才能获得满意的加工效果和产品质量。
同时,注重切削润滑和冷却、以及后续表面处理,也是保证不锈钢材料车削加工成功的关键。
不锈钢的车削技巧

不锈钢的车削技巧主要包括以下几个方面:1.刀具选择:选择适合不锈钢车削的刀具非常重要。
通常,选择具有较高耐热性、耐磨性和与不锈钢亲和作用小的刀具材料,如高碳、高钒或钼系的高速钢。
此外,刀具的几何形状和角度也需要根据具体加工要求进行选择。
2.切削用量选择:切削用量包括切削速度、进给量和切削深度。
对于不锈钢的车削,切削速度通常较低,一般为普通碳钢切削速度的40%~60%。
进给量和切削深度也需要根据具体情况进行选择,以避免刀具过度磨损和工件表面质量下降。
3.冷却液选择:使用合适的冷却液可以有效降低切削温度,减少刀具磨损和提高工件表面质量。
对于不锈钢的车削,通常选择具有较好冷却和润滑性能的冷却液。
4.操作技巧:在车削不锈钢时,需要注意以下几点操作技巧:首先,保持刀具的锋利,及时更换磨损的刀具;其次,避免使用过大的切削用量,以减少刀具的受力;最后,注意工件的装夹方式和切削力的方向,以避免工件变形或振动。
此外,还需要注意以下几点:1.由于不锈钢的塑性大、韧性高,车削时容易产生积屑瘤和鳞刺,这不仅影响工件的表面粗糙度,还会使刀具的磨损加快。
因此,需要选择合适的刀具材料和几何角度,以及合理的切削用量来避免这些问题的产生。
2.不锈钢的导热性差,导致切削热无法及时散出,使刀具的刃口温度升高,加剧刀具磨损。
为了降低切削温度,可以采用浇注冷却液的方法。
3.在车削过程中,应随时注意观察切削情况,如发现异常现象(如振动、噪声、温度升高等),应及时采取措施进行调整。
4.对于不同种类和规格的不锈钢材料,其车削性能也会有所不同。
因此,在实际加工前,最好先进行一些试验性切削,以确定最佳的切削参数和工艺方案。
总之,掌握不锈钢的车削技巧需要综合考虑多个因素,包括刀具选择、切削用量、冷却液和操作技巧等。
通过合理的选择和调整这些参数,可以提高加工效率、降低生产成本并获得高质量的工件。
不锈钢薄板类工件的车削工艺

2
2 5 。 ;后 角选 用 5 。 ~8 。 ;主 偏 角选 用7 5 。 或6 0 。 ;
.
拦 旦主 持 楚. 宝 . 垄 .
嘉
不锈钢薄板类工件的车削工艺
天津赛 瑞机 器设备有 限公 司 ( 3 0 0 3 0 1 ) 刘 天津 菱云刀 具设计有 限公 司 ( 3 0 0 3 8 4 ) 王 鹏 毅
薄 ,只有 ( 1 5 ±0 . 1 )mm,工件在机床上无法一次 装夹完成加工。采用常规的装夹方式 ,工件装夹无 论夹外 圆或是撑 内圆,个别处在装夹时受 力稍有不
式普车 ( 型号为C 5 1 1 6 A)。由于设备使用时 间较
长 ,设 备 的 回转 工 作 台 和卡 爪 均 有 一 定磨 损 老化 。 工 件 直接 装夹 在 设 备 上 ,加 工 误 差 较大 ,精 度很 难 保证。
3 . 材料分析
此 密封环材 质为 1 Cr l 8 Ni 9 ,按 不 锈 钢 成 分 分 类 ,属于 铬 镍 不 锈 钢 ;按 不 锈 钢 金相 组 织 分 类 ,属 于 奥 氏体 不 锈 钢 ;从切 削加 工 性 能 方面 来 说 ,属 于
圆 一 三次倒个撑 内圆 ,精车外 圆及 下端面 一 成
品。
经过 上 述 反 复 翻 面 加 工 工艺 过 程 ,加 工试 制 出 两 件 产 品 。检 验 发 现 ,端 面 厚 度 不 均匀 ,无 法保 证 在 公 差范 围之 内 ,平行 度达 不 到要 求 , 出现加 工变
使 切 削力 增 加 。 同时 ,加 工 硬 化严 重 ,热 强 度高 , 进 一 步 增 大 了切 削抗 力 ,切 屑 的卷 曲折 断 也 比较 困
车削不锈钢零件的工艺分析与加工方法

车削不锈钢零件的工艺分析与加工方法摘要:不锈钢是机械装备制造领域的重要材料,因为其具有抗腐蚀性强、耐磨性佳的优势,所以以其为材料制作的零件韧性大、强度高、使用寿命长。
但受材料本身的影响,车削不锈钢零件时常会对刀具的切削性能、加工效率造成影响。
由于不锈钢零件加工对于机械装备而言有着重要意义,所以相关工作人员需采用科学合理的手段解决当下存在的问题,进一步提高车削效果。
本文就车削不锈钢零件的工艺与加工进行研究,以期为相关工作人员进行不锈钢零件的切削以及为研发人员改进切削加工技术提供参考。
关键词:车削;不锈钢零件;加工工艺;机械制造引言:目前,如何进行不锈钢零件的车削加工成为相关工作人员需要深入探讨的课题。
因为不锈钢零件的抗腐蚀性、机械性能较高,在进行车削加工时容易受到一些因素的影响,导致刀具出现磨损、“刀瘤”,不仅影响了刀具的切削性能,还引起了不锈钢零件加工效果与理想不符的情况。
为解决这些问题,下列进行了深入研究,以期解决上述存在的问题,进一步提高不锈钢零件的车削加工效率、质量,并为切削加工技术的不断改进提供参考。
1.不锈钢的车削特性以化学成分为依据,可以将不锈钢划分两个大类,一为铬不锈钢,二为镍不锈钢。
前者一般视情况而定选择含铬量,常见的为12%、17%、27%等。
含铬量通常与其靠腐蚀性能成正比。
铬镍不锈钢的含铬量、含镍量分别在17%~20%之间,8%~11%之间。
不锈钢的机械性能可直接影响其切削加工。
首先,在切削过程中会受到导热性的影响。
具体表现为:不锈钢本身的导热性越差,那么在车削过程中,热量会聚集于刀具上,而不是切屑中,所以刀具的切削性能会受到一定的影响,导致工作效率相对较低。
其次,不锈钢中含有碳化物杂质,其具有较强的磨蚀性,所以在切削时很容易出现磨损问题。
再次,不锈钢可在高温条件下保持较高强度和硬度,而刀具不能。
一旦超过其极限,便会产生塑性变形。
第四,不锈钢具有较强的粘附性,如果其黏附至刀具上时,便会产生“刀瘤”,导致车削工作的开展受到影响。
不锈钢工件加工工艺简介

不锈钢工件加工工艺简介不锈钢是一种耐腐蚀、耐高温、耐磨损的金属材料,因其具有优良的物理和化学性能,在工程领域中得到广泛应用。
不锈钢工件的加工是指对不锈钢材料进行切削、成形、焊接等加工工艺,以满足工程应用的需要。
不锈钢工件加工工艺包括车削、铣削、磨削、钻孔、焊接、抛光等工艺步骤,下面将对不锈钢工件加工工艺进行简要介绍。
一、车削加工工艺车削是一种常用的加工不锈钢工件的方法,通过车床对工件进行旋转切削,使工件表面得到精密加工。
在车削加工中,不锈钢工件通常采用硬质合金刀具,利用切削原理对工件表面进行切削,以得到所需尺寸和形状。
车削加工不锈钢工件需要注意刀具的选择、切削速度和进给量的控制,以确保工件表面光洁度和尺寸精度。
对于不锈钢工件,由于其硬度和韧性较高,车削过程中需要保持合理的切削参数,避免刀具损坏和工件变形。
铣削是一种使用铣刀进行切削的加工方法,适用于不锈钢工件的平面加工、凹槽加工和轮廓加工等。
在不锈钢工件的铣削加工中,需要选择合适的刀具类型、切削参数和切削方式,以保证工件加工表面粗糙度和尺寸精度。
铣削加工可以采用立式铣床、卧式铣床、数控铣床等设备进行加工,根据不同的工件形状和要求选择合适的设备和工艺路线。
磨削是一种利用磨具对不锈钢工件进行加工的方法,能够获得精密的表面质量和尺寸精度。
磨削加工常用于不锈钢工件的表面精加工、内外圆孔加工和平面磨削等。
在磨削加工中,需要选择合适的磨具类型、磨削参数和冷却润滑方式,以避免工件表面产生热裂纹和变形。
焊接是将金属材料通过加热熔化和冷却凝固的方式连接在一起的加工方法,适用于不锈钢工件的连接和结构加工。
在焊接加工中,需要选择合适的焊接方法、焊接材料和焊接参数,以确保焊缝质量和连接强度。
不锈钢材料具有一定的焊接难度,焊接过程中需要控制温度和避免氧化,以减少焊接变形和气孔等缺陷。
抛光是一种通过摩擦和磨擦使不锈钢工件表面得到光滑和亮度的加工方法。
抛光加工可以采用机械抛光、化学抛光和电化学抛光等方式进行,以获得不同表面粗糙度和光洁度的要求。
不锈钢数控车削加工工艺

02
01
03
04
05
V
=
πX D X n
(m/min)
式中:D 工件切削部分的最大直径(mm) n 主轴每分钟转数min-1。
数控车削的工艺分析
切削速度:
(例题) 主轴转速2000min-1、车削直径Ø50,求此时的切削速度?
(答) fr=Vf÷n=100÷2000=0.05mm/r 求出每转进给量为0.05mm/r
数控车削的工艺分析
切削用量的确定
(例题) 主轴转速1350min-1、钻头直径Ø12,求切削速度。
(答) 代入公式 vf=fr×n=0.2×1350=270mm/min 由此得出主轴每分钟进给量为270mm/min。
基本特征
数控车削时,工件做回转运动,刀具做直线或曲线运动,刀尖相对工件运动的同时,切除一定的工件材料从而形成相应的工件表面。其中,工件的回转运动为切削主运动,刀具的直线或曲线运动为进给运动。两者共同组成切削成形运动。
加工范围
数控车床即装备了数控系统的车床。由数控系统通过伺服驱动系统去控制各运动部件的动作,主要用于轴类和盘类回转体零件的多工序加工,具有高精度、高效率、高柔性化等综合特点,适合中小批量形状复杂零件的多品种、多规格生产。 数控车床按车削中心是在普通数控车床基础上发展起来的一种复合加工机床。除具有一般二轴联动数控车床的各种车削功能外,车削中心的转塔刀架上有能使刀具旋转的动力刀座,主轴具有按轮廓成形要求连续(不等速回转)运动和进行连续精确分度的C轴功能,并能与X轴或Z轴联动,控制轴除X、Z、C轴之外,还可具有Y轴。可进行端面和圆周上任意部位的钻削、铣削和攻螺纹等加工,在具有插补功能的条件下,还可以实现各种曲面铣削加工。
1
不锈钢零件的车削加工工序分析

的金 属组 织 巾 , 含有 分散 的碳 化物 杂质 , 使 刀具 容 易
磨 损 。另 外 , 不锈 钢 在 高温状 态下 能产 生 塑性变 形 。
刀 具上 的切 削 力增 大 , 不 均 衡 的切 削过 程 使 刀 具 的 振 动加 强 。此外 , 不 锈 钢 的铸 件 和锻 件 毛 坯 的 硬度 较 高 的氧化 皮 以及 不 连续 和不 规 则 的 外形 , 都 会 给
切 削带来 闲难 。 综上 所述 , 根 据不 锈钢 材质 的特性 , 加 T不 锈钢
不 锈钢 还有 较强 的粘 附性 , 使 材 料 粘 附 在 刀具 上 而 产“ 刀瘤 ”, 这 一 切 都 给 车 削 带 来 闲难 , 影 响 零 件 表 面 光沽度 。 I 大 】 此, 加 T不锈 钢零 件 时 , 合 理选 择 刀具 材料 、 刀具几 何 角度 、 切 削用 量 , 并 合 理 安 排 零 件 安 装定 位装 夹 方式 , 以保 证零 件 的最终 图纸 要求 。
l 7 %和 2 7 %等, 其抗 腐 蚀性 能 随 着 含铬 量 的增 加 而 增 加 。常 用 的铬 镍 不 锈 钢 , 含铬 量 1 7 % 一2 0 %, 含 镍量 8 % ~1 1 %, 这 种 铬 镍 不 锈 钢 的 抗 腐 蚀 性 能及
机 械性 能都 比铬 不锈 钢高 。 不 锈钢 的物 理一 机械 性 能对其 切 削有很 大 的影
莱钢科 技
2 0 1 4年 2月
不 锈 钢 零 件 的 车 削 加 工 工 序 分 析
颜 莉
( 设备 检修 中心 )
摘
要: 通过 分析 不锈 钢物 理一 机械 性 能对切 削加 工的影 响 , 制 定方案 并采 取措 施避 免或 减 少
数控车削加工薄壁零件的技巧
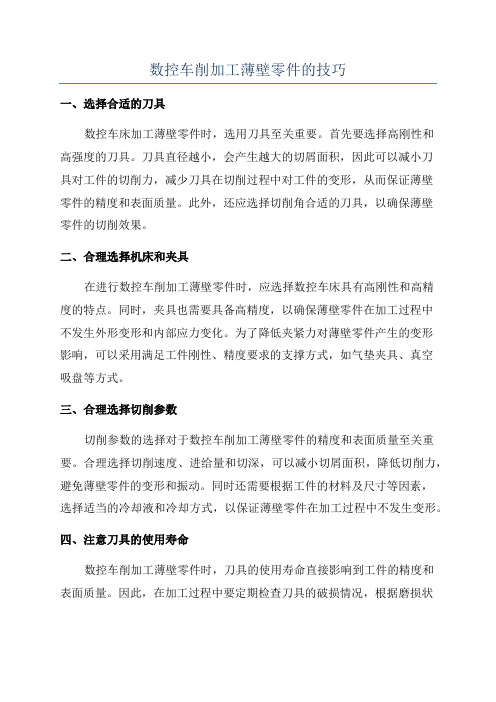
数控车削加工薄壁零件的技巧一、选择合适的刀具数控车床加工薄壁零件时,选用刀具至关重要。
首先要选择高刚性和高强度的刀具。
刀具直径越小,会产生越大的切屑面积,因此可以减小刀具对工件的切削力,减少刀具在切削过程中对工件的变形,从而保证薄壁零件的精度和表面质量。
此外,还应选择切削角合适的刀具,以确保薄壁零件的切削效果。
二、合理选择机床和夹具在进行数控车削加工薄壁零件时,应选择数控车床具有高刚性和高精度的特点。
同时,夹具也需要具备高精度,以确保薄壁零件在加工过程中不发生外形变形和内部应力变化。
为了降低夹紧力对薄壁零件产生的变形影响,可以采用满足工件刚性、精度要求的支撑方式,如气垫夹具、真空吸盘等方式。
三、合理选择切削参数切削参数的选择对于数控车削加工薄壁零件的精度和表面质量至关重要。
合理选择切削速度、进给量和切深,可以减小切屑面积,降低切削力,避免薄壁零件的变形和振动。
同时还需要根据工件的材料及尺寸等因素,选择适当的冷却液和冷却方式,以保证薄壁零件在加工过程中不发生变形。
四、注意刀具的使用寿命数控车削加工薄壁零件时,刀具的使用寿命直接影响到工件的精度和表面质量。
因此,在加工过程中要定期检查刀具的破损情况,根据磨损状况及时更换刀具。
另外,要合理安排刀具的刀具卸刀和出刀次数,避免刀具的过度磨损。
五、加工顺序的确定在数控车削加工薄壁零件时,工艺的合理规划是非常重要的。
应该根据零件的形状和要求,合理确定加工顺序,优先进行刚性要求高的部位的加工,再进行壁厚较薄的部位的加工,以避免由于前期加工引起的零件形变对后续加工的影响。
综上所述,数控车削加工薄壁零件的技巧包括选择合适的刀具、合理选择机床和夹具、合理选择切削参数、注意刀具的使用寿命以及确定合理的加工顺序。
只有掌握了这些技巧,才能够有效地提高薄壁零件的加工质量和生产效率。
不锈钢材料的车削技巧
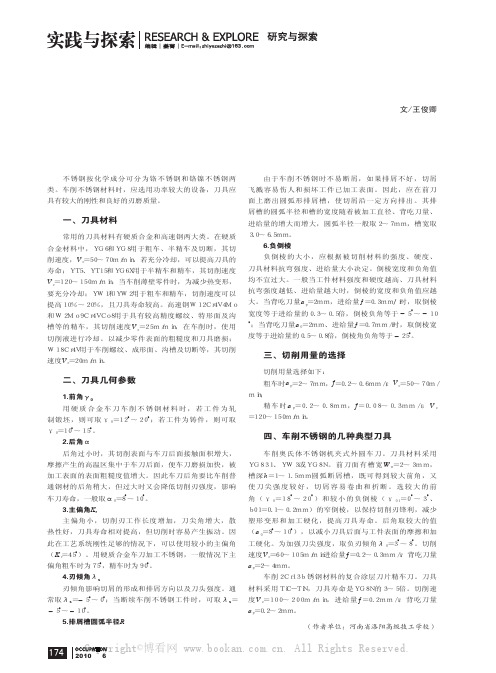
OCCUPATION1742010 6不锈钢按化学成分可分为铬不锈钢和铬镍不锈钢两类。
车削不锈钢材料时,应选用功率较大的设备,刀具应具有较大的刚性和良好的刃磨质量。
一、刀具材料常用的刀具材料有硬质合金和高速钢两大类。
在硬质合金材料中,YG6和YG8用于粗车、半精车及切断,其切削速度,V c=50~70m/min,若充分冷却,可以提高刀具的寿命;YT5、YT15和YG6X用于半精车和精车,其切削速度V c=120~150m/min,当车削薄壁零件时,为减少热变形,要充分冷却;YW1和YW2用于粗车和精车,切削速度可以提高10%~20%,且刀具寿命较高。
高速钢W12Cr4V4Mo和W2Mo9Cr4VCo8用于具有较高精度螺纹、特形面及沟槽等的精车,其切削速度V c=25m/min,在车削时,使用切削液进行冷却。
以减少零件表面的粗糙度和刀具磨损;W18Cr4V用于车削螺纹、成形面、沟槽及切断等,其切削速度V c=20m/min。
二、刀具几何参数1.前角γ0用硬质合金车刀车削不锈钢材料时,若工件为轧制锻坯,则可取γ0=12˚~20˚;若工件为铸件,则可取γ0=10˚~15˚。
2.后角α后角过小时,其切削表面与车刀后面接触面积增大,摩擦产生的高温区集中于车刀后面,便车刀磨损加快,被加工表面的表面粗糙度值增大。
因此车刀后角要比车削普通钢材的后角稍大,但过大时又会降低切削刃强度,影响车刀寿命,一般取α0=8˚~10˚。
3.主偏角K r主偏角小,切削刃工作长度增加,刀尖角增大,散热性好,刀具寿命相对提高,但切削时容易产生振动。
因此在工艺系统刚性足够的情况下,可以使用较小的主偏角(K r=45˚)。
用硬质合金车刀加工不锈钢,一般情况下主偏角粗车时为75˚,精车时为90˚。
4.刃倾角λs刃倾角影响切屑的形成和排屑方向以及刀头强度。
通常取λs =﹣5˚~0˚;当断续车削不锈钢工件时,可取λs =﹣5˚~﹣10˚。
5.排屑槽圆弧半径R由于车削不锈钢时不易断屑,如果排屑不好,切屑飞溅容易伤人和损坏工件已加工表面。
数控车床车削大直径薄壁零件方法探析
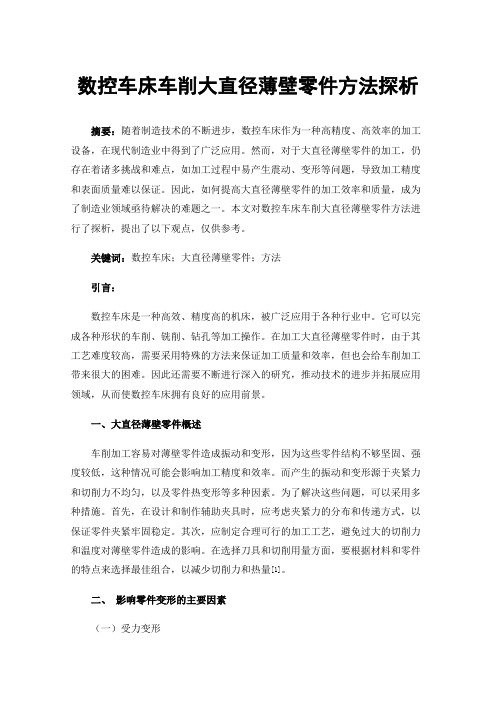
数控车床车削大直径薄壁零件方法探析摘要:随着制造技术的不断进步,数控车床作为一种高精度、高效率的加工设备,在现代制造业中得到了广泛应用。
然而,对于大直径薄壁零件的加工,仍存在着诸多挑战和难点,如加工过程中易产生震动、变形等问题,导致加工精度和表面质量难以保证。
因此,如何提高大直径薄壁零件的加工效率和质量,成为了制造业领域亟待解决的难题之一。
本文对数控车床车削大直径薄壁零件方法进行了探析,提出了以下观点,仅供参考。
关键词:数控车床;大直径薄壁零件;方法引言:数控车床是一种高效、精度高的机床,被广泛应用于各种行业中。
它可以完成各种形状的车削、铣削、钻孔等加工操作。
在加工大直径薄壁零件时,由于其工艺难度较高,需要采用特殊的方法来保证加工质量和效率,但也会给车削加工带来很大的困难。
因此还需要不断进行深入的研究,推动技术的进步并拓展应用领域,从而使数控车床拥有良好的应用前景。
一、大直径薄壁零件概述车削加工容易对薄壁零件造成振动和变形,因为这些零件结构不够坚固、强度较低,这种情况可能会影响加工精度和效率。
而产生的振动和变形源于夹紧力和切削力不均匀,以及零件热变形等多种因素。
为了解决这些问题,可以采用多种措施。
首先,在设计和制作辅助夹具时,应考虑夹紧力的分布和传递方式,以保证零件夹紧牢固稳定。
其次,应制定合理可行的加工工艺,避免过大的切削力和温度对薄壁零件造成的影响。
在选择刀具和切削用量方面,要根据材料和零件的特点来选择最佳组合,以减少切削力和热量[1]。
二、影响零件变形的主要因素(一)受力变形当工件壁薄时,夹紧力会引起变形,从而影响尺寸和形状的准确度。
为了避免这种情况,需要采用合适的夹紧方法进行加工,以确保工件的精度和质量。
(二)受热变形在切削加工过程中,由于工件材料特性和壁薄结构,产生大量热量,导致工件热变形使尺寸难以控制。
这需要采取降温措施或者改进加工方式以减少热源。
三、零件变形的控制措施(一)装夹方式在加工工件时,夹紧方式是确保精度和质量的关键因素之一。
浅谈不锈钢材料的车削加工

浅谈不锈钢材料的车削加工不锈钢是一种耐腐蚀、耐热、耐高温的材料,广泛应用于机械制造、汽车制造、航空航天、建筑装饰等行业。
在不锈钢的车削加工中,需要特别注意材料的性质、工艺参数以及切削工具的选择。
不锈钢的性质决定了它的车削加工相对复杂。
首先,不锈钢的硬度较高,所以切削力比较大,对车削刀具的耐磨性提出了更高的要求。
其次,由于不锈钢具有较好的导热性,切削时容易产生热量,导致刀具快速磨损和加工表面产生尺寸偏差,因此需要采取合理的降温和冷却措施。
此外,不锈钢还具有较好的韧性和塑性,容易产生切削硬化,使切削加工更加困难。
在不锈钢的车削加工中,选择合适的车削工艺参数非常重要。
首先,应根据不锈钢的成分和硬度,选择合适的切削速度、进给速度和切削深度。
一般来说,低硬度的不锈钢适合选择较高的切削速度和进给速度,以提高生产效率;而高硬度的不锈钢则需要选择较低的切削速度和进给速度,以避免过度切削或切削过热。
此外,还需根据加工的具体要求和工件的尺寸,选择合适的刀具和切削方式。
切削工具的选择也对不锈钢的车削加工起着至关重要的作用。
不锈钢的硬度和耐热性,要求使用高强度、高耐磨性的刀具。
一般来说,硬质合金刀具可以满足这些要求,但也需要根据具体的加工情况选择合适的刀具材料和刀具几何形状。
此外,应根据切削参数和加工要求,合理选择切削润滑剂和冷却液,以降低切削温度、延长刀具使用寿命和提高加工质量。
总之,不锈钢材料的车削加工相对复杂,需要注意材料的性质、工艺参数和切削工具的选择。
在实际生产中,需要根据不锈钢的具体类型和加工要求,采取合适的加工工艺和切削方式,以提高加工效率和加工质量。
此外,还需加强刀具的研发和刀具涂层技术的应用,以适应不锈钢材料的车削加工需求。
不锈钢数控车削加工工艺
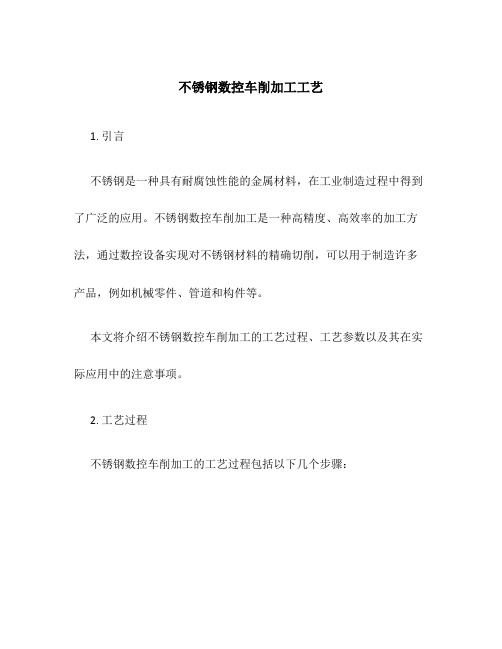
不锈钢数控车削加工工艺1. 引言不锈钢是一种具有耐腐蚀性能的金属材料,在工业制造过程中得到了广泛的应用。
不锈钢数控车削加工是一种高精度、高效率的加工方法,通过数控设备实现对不锈钢材料的精确切削,可以用于制造许多产品,例如机械零件、管道和构件等。
本文将介绍不锈钢数控车削加工的工艺过程、工艺参数以及其在实际应用中的注意事项。
2. 工艺过程不锈钢数控车削加工的工艺过程包括以下几个步骤:2.1 零件准备在进行车削加工之前,首先需要准备好要加工的不锈钢零件。
清洁表面,并确保其表面没有明显的凹陷和磨损。
2.2 工艺规划在进行数控车削加工之前,需要进行工艺规划。
工艺规划包括确定零件的加工顺序、选择合适的刀具和切削参数等。
2.3 加工装夹将不锈钢零件安装在数控车床上,进行加工装夹。
确保零件固定牢固且位置准确。
使用合适的夹具和固定装置,以避免零件在加工过程中发生移动或变形。
2.4 加工参数设置根据零件的要求和刀具的特性,设置合适的加工参数。
包括切削速度、进给速度和切削深度等。
合理的加工参数可以提高加工效率和加工质量。
2.5 车削加工根据工艺规划和加工参数,使用数控设备进行车削加工。
通过控制刀具的运动轨迹和加工参数,将不锈钢材料逐渐切削,得到所需形状和尺寸的零件。
2.6 质量检验在完成车削加工后,进行质量检验。
检查零件的尺寸、表面质量和精度等。
确保加工的零件符合要求。
3. 工艺参数不锈钢数控车削加工的工艺参数对加工质量和效率有着重要影响。
以下是一些常用的工艺参数:•切削速度:通常以米/分钟为单位。
根据不锈钢材料的硬度和刀具的材质来确定合适的切削速度。
•进给速度:刀具在单位时间内在工件上的移动速度。
根据不同的切削工况和加工精度要求,选择合适的进给速度。
•切削深度:刀具每次切削所去除的材料层厚度。
根据零件的要求和刀具的稳定性,选择合适的切削深度。
•刀具半径补偿:在车削过程中,考虑到刀具的几何特性和零件的轮廓,需要进行刀补。
针对不锈钢零件的车削加工

针对不锈钢零件的车削加工随着企业的快速发展,对加工材料的多样化需求不断增加,像高温合金、不锈钢以及钛合金等难加工的材料被广泛的应用于各行各业当中。
在对这些材料加工的过程中,一定要分析出不同材料中存在的加工差异性。
本文针对不锈钢零件精密深孔数控车加工的方法进行了探讨,不锈钢作为一种难加工的材料,在建筑、电力、航空、航天、船舶等行业有着广泛的应用。
在实际的加工过程中易硬化、易产生积屑瘤等特性,而且导热性较差,所以针对这种现象对不锈钢零件的加工工艺方法进行了探讨,通过使用数控车加工可以更加精准的加工不锈钢零件,提高了工作效率。
标签:不锈钢;零件;车削加工一、不锈钢零件车削加工难点分析由于零件结构的特殊构成,在内腔车削时只能采用螺纹胎具的定位方式进行装夹,工作断面与轴向定位面的距离由于工件加工的特殊要求,重心不规则,所以在装夹系统中就很容易失衡。
同时也就增加了刀具的装夹的难度。
同时对于尺寸精度、同轴度、垂直度都有很高的要求,如果在加工的过程中出现一点误差,都可能会对零件的实用性能造成严重的影响。
所以对于不锈钢精密深孔的数控车加工要对刀具的选择、切削参数以及工艺路线的设置等都要有严格的要求,这些因素都会影响到该零件加工之后是否合格。
二、不锈钢具有的切削特点不锈钢的切削加工性比中碳钢差得多,在切削过程中有如下几方面特点:1.加工硬化严重:在不锈钢中,以奥氏体和奥氏体+铁素体不锈钢的加工硬化现象最为突出。
因为不锈钢的塑性大,塑性变形时品格歪扭,强化系数很大;且奥氏体不够稳定,在切削应力的作用下,部分奥氏体会转变为马氏体;再加上化合物杂质在切削热的作用下,易于分解呈弥散分布,使切削加工时产生硬化层。
前一次进给或前一道工序所产生的加工硬化现象严重影响后续工序的顺利进行。
2.切削力大:不锈钢在切削过程中塑性变形大,尤其是奥氏体不锈钢,使切削力增加。
同时,不锈钢的加工硬化严重,热强度高,进一步增大了切削抗力,切屑的卷曲折断也比较困难。
薄壁零件的车削方法
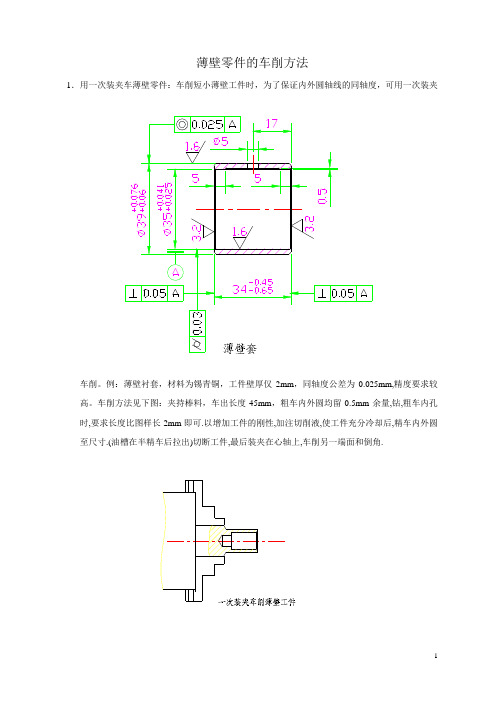
薄壁零件的车削方法1.用一次装夹车薄壁零件:车削短小薄壁工件时,为了保证内外圆轴线的同轴度,可用一次装夹车削。
例:薄壁衬套,材料为锡青铜,工件壁厚仅2mm,同轴度公差为0.025mm,精度要求较高。
车削方法见下图:夹持棒料,车出长度45mm,粗车内外圆均留0.5mm余量,钻,粗车内孔时,要求长度比图样长2mm即可.以增加工件的刚性,加注切削液,使工件充分冷却后,精车内外圆至尺寸.(油槽在半精车后拉出)切断工件,最后装夹在心轴上,车削另一端面和倒角.2.用扇形卡爪及心轴装夹薄壁工件:例:薄壁套筒如图,车削方法:粗车留精车余量1~1.5mm,精车时,装夹在扇形软卡中,精车内孔及φ72H7,外圆φ980-0.1及端面A符合图样要求,然后以内孔和大端面为基准,夹在弹性胀力心轴上,即可精车外圆.3.在花盘上车削薄壁工件:直径较大,尺寸精度和形位精度都较高的圆盘薄壁工件.可装夹在花盘上加工.车削方法:先装夹在三爪卡盘上粗车内孔及外圆,各留1~1.5mm余量,长度尺寸车至92+0.3+0.2,并精磨两端面至长度92.然后装夹在花盘上精车内孔及外圆,精车内孔的装夹方法见图.先在花盘端面上车出一凸台,凸台的直径和工件之间留0.5~1mm的间隙,(不用作定心).用螺栓,压板压紧工件端面,压紧力要均匀.找正后,即可车削φ132H7, φ262H7内孔及内端平面.精车外圆时的方法见下图:将三点接触压板(压板上有三条槽以让开压板)适当压紧,松开并取下压板及螺钉,即可车削外圆,使之符合图样要求.上面的压紧方法,因为压紧力在轴向,所以不容易引起变形.4.在专用夹具上车削薄壁零件:如图,工件装上夹具后,当拧紧螺钉2时,压紧圈1便沿着斜面将工件压紧,即可车削工件的内孔,外圆及端面.5.增加辅助支承车削薄壁零件:车削内孔精度要求高的薄壁零件时,可采用辅助支承来增加工件的刚性.6.增加工艺肋车削薄壁工件.在工件的装夹部位特制几根工艺支撑肋,使夹紧力作用在肋上,可减少变形.二.减少工件变形的方法:1.工件分粗精车,消除粗车时切削力过大而产生的变形,粗车后,使工件得到自然冷却,消除在精车时可能产生的热变形。
浅析超大薄板精密机械加工工艺

浅析超大薄板精密机械加工工艺机械制造业的发展水平是国家工业化程度的主要标志之一,机械加工水平的高低是影响其发展的重要因素,选择合适的加工方法,合理安排加工顺序,降低加工成本的同时确保加工精度。
在工件加工的整个过程中,各个环节对技术的要求是各不相同的,合理制定机械加工工艺值得研究探讨。
机械加工中,超大薄板加工、细长轴加工等都是比较典型的加工难题,需要制定正确的加工工艺,才能保证产品最终质量合格。
以外形尺寸为3200×1800×30、材料为304不锈钢板的精密机械加工工艺为例进行探讨。
成品技术要求:两大面的表面粗糙度要求均为Ra1.6,大面最终平面度要求为0.4。
零件特征为超大超重薄板工件,且表面结构有较高的质量要求。
其工艺包括零件的毛坯准备、机床上装卡找正、加工顺序、刀具调整与接刀等多道工序,还有成品半成品吊装搬运与放置等事项,每道工序都会影响到零件的加工质量,在实际生产加工中都须予以重视。
1 原材料准备原材料(毛坯)准备是把握零件质量的首关,须执行不合格原材料(毛坯)不投产的规定。
零件加工前必须对原材料进行确认,材料要求为304不锈钢,采购的钢板必须附带有效的、可追溯的材质证明;原材料切割下料后需校正平面度(可通过滚压整形等方法),令平面度≤1.6;毛坯应先粗加工出非精密要求的轮廓,减少后加工的加工应力,并可避免后加工影响大板的平面度及表面精度;粗加工后做消除应力处理(消除原材料轧制应力、热切割应力、矫形应力等),一般选择热处理方法(去应力热处理以随机自动记录数据曲线作为质量保证),消除应力时,应采取保持校正平面度的技术措施;粗加工并热处理后的毛坯自由放置在加工机床的工作台上(或等同)检测精度和加工余量进行确认。
2 大板的装卡与找正大板的装卡与找正是大板加工精度保证的重要环节,装卡的每个步骤都很关键,装卡的方法、顺序直接影响大板最终的加工精度。
装夹时必须夹死,防止工件在切削力、重力、惯性力等的作用下发生移位或晃动,以免破坏工件的定位。
不锈钢车削参数
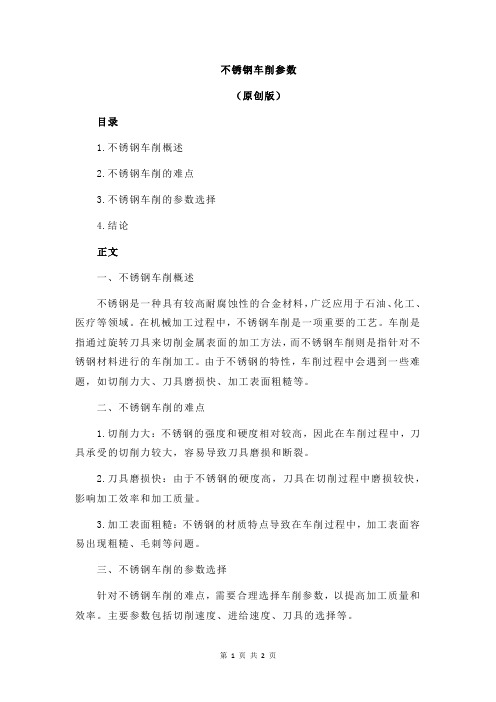
不锈钢车削参数(原创版)目录1.不锈钢车削概述2.不锈钢车削的难点3.不锈钢车削的参数选择4.结论正文一、不锈钢车削概述不锈钢是一种具有较高耐腐蚀性的合金材料,广泛应用于石油、化工、医疗等领域。
在机械加工过程中,不锈钢车削是一项重要的工艺。
车削是指通过旋转刀具来切削金属表面的加工方法,而不锈钢车削则是指针对不锈钢材料进行的车削加工。
由于不锈钢的特性,车削过程中会遇到一些难题,如切削力大、刀具磨损快、加工表面粗糙等。
二、不锈钢车削的难点1.切削力大:不锈钢的强度和硬度相对较高,因此在车削过程中,刀具承受的切削力较大,容易导致刀具磨损和断裂。
2.刀具磨损快:由于不锈钢的硬度高,刀具在切削过程中磨损较快,影响加工效率和加工质量。
3.加工表面粗糙:不锈钢的材质特点导致在车削过程中,加工表面容易出现粗糙、毛刺等问题。
三、不锈钢车削的参数选择针对不锈钢车削的难点,需要合理选择车削参数,以提高加工质量和效率。
主要参数包括切削速度、进给速度、刀具的选择等。
1.切削速度:切削速度是车削过程中重要的参数之一,选择合适的切削速度可以有效降低切削力,减少刀具磨损。
一般来说,不锈钢的切削速度可选择为高速钢刀具的 2-3 倍。
2.进给速度:进给速度是指刀具在车削过程中的移动速度,选择合适的进给速度可以提高加工效率,同时避免过度切削导致的表面粗糙。
进给速度的选择应根据刀具的性能、加工材料硬度等因素综合考虑。
3.刀具选择:针对不锈钢的特性,选择合适的刀具是关键。
一般可选择高速钢刀具或硬质合金刀具,其中硬质合金刀具具有更高的硬度和耐磨性,适用于加工不锈钢等高硬度材料。
四、结论总之,不锈钢车削是一项具有一定难度的加工工艺,需要合理选择切削参数,如切削速度、进给速度和刀具选择等,以提高加工质量和效率。
- 1、下载文档前请自行甄别文档内容的完整性,平台不提供额外的编辑、内容补充、找答案等附加服务。
- 2、"仅部分预览"的文档,不可在线预览部分如存在完整性等问题,可反馈申请退款(可完整预览的文档不适用该条件!)。
- 3、如文档侵犯您的权益,请联系客服反馈,我们会尽快为您处理(人工客服工作时间:9:00-18:30)。
aa zs uhcue sh o peed t tnw e rcs n it e f e ok i e,h u-fteac n l e sc ass e r i io i hn oes g sy rpe ste to-o r e y a t w k c s ro p i t p o t w h h c o l n
igo ev r c l ah ,h r c si gs q e c , ec oc f ec t n os dt ec t n a a tr . n f h e ia t e t ep o e sn u n e t h ie o ut gt l a u t gp r mee s t t l e h h t i o n h i Ke wo d san e s te; a n ; ie t n n t; e ia lte c at y r : t ls e ll mi a b s ci a u i v r c l ah ; rf i s ol s t
抗 磨 板是 水 轮机 主轴 密 封 装配 中的关 键零 件 , 材 质 为 奥 氏 体 不 锈 钢 1 r NiT , 其 工 作 面 与 橡 胶 l 9i C 8 密 封 块 接 触 。 水 轮 机 工 作 时 , 磨 板 随 水 轮 机 主 轴 抗
利 用 清 洁水 润 滑 , 减 小 密 封 块 的磨 损 , 证 工作 为 保
f h i e a o e o t o c a sd b rc s n i ot n I a op t f ad t ui s ot o t t vl fh i h ef ec ue ytepo es gds r o .t l us ow r eslt n e e n r t jn c s a h i t i s r h o o th
p o e sn c n c o ovn ep o lmsme t n d a o efo te c c e a s mb y te i s l t n o e w r — r c s i gt h i f l ig t r b e n o e b v m h y l - s e l , h t a i ft o k e s h i r n a l o h
密 封 的 可 靠 , 抗 磨 板 工 作 面 的 表 面 粗 糙 度 、 面 对 平 度 、 半 面间 隙要 求较 高 , 磨 板 加工 质 量 的好 坏 , 分 抗
w oepo es gq ai eemie ep p r ftesaigo emana l f eh do tr ie T i p p r h s rc si u ly d tr n st r et o e l ft i xeo y r—ubn . s a e n t h o y h n h h t h
四川 工程 职 业 技 术 学 院 学
德 阳重装 基 地建 设 主 : 彩 持赵 云
J 刚 A IH A N IE RN E H lA o 上G OU L SC U NE G N E IGT C Nc L U E OF c
较大不锈钢分半薄板件的车削加工工艺
俩 勇
( 东方 电机有 限公 司 ,四川 德 阳 6 8 0 ) 10 0
The Tu ni o e sn a to r e a n e sS e l r ng Pr c s i g Cr f fLa g r St i l s t e
Bieto a m i a U n t s c i n lLa n is
HeYo ng
翻
( cunG n rl ci r oLd oD nf g l tc c i r oLd, eagScun6 8 0 hn) S h a e e hn y . t.f og n e r hny C . t. yn , i a 10 0C i i a Ma e C a E c i Ma e D h a
工 顺序 、 刀具 的选 择 、 削参 数 的选 择 等 方 面提 出解 决 上 述 问题 的加 工 工 艺 。 切
[ 关键 词]不锈钢; : 薄板; 分半件; 立车; 工艺
中 图分 类号 : H1 1. 文献标识 码 : 文章编 号 : N字 0 — 0 ( 0 0)4 0 6 0 T 6 1 B CK 7 0 32 1 0 — 3 — 4
Ab t a t Th  ̄e n i e r lt s e ld i ema na l f h y r — u b n til s te af l mi a s r c : es e d a t a aea s mb e t i x eo eh d o t r iei san e ss l l_a n . w p nh t s e h
【 要]水轮机主轴密封装配抗磨板为不锈钢薄板分半件, 摘 : 其加工质量的好坏, 了 决定 水轮机主轴密封的
性 能 。本 文 针 对该 类 工件 加 工产 生容 易产 生 工件 变形 , 工作 面 平 面度 超 差 , 下表 面 的平 行 度超 差 和 因 上
加 工变形而造成合缝面 间隙超差 等问题的原因进行 了分析, 并从工件 的装配组 圆、 立车加工时的装压 、 加