产线退料流程
车间退料作业规范
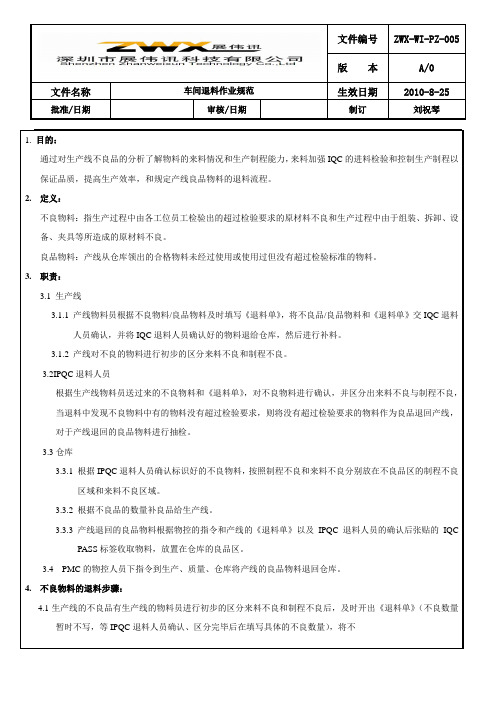
版本A/0 文件名称车间退料作业规范生效日期2010-8-25 批准/日期审核/日期制订刘祝琴1. 目的:通过对生产线不良品的分析了解物料的来料情况和生产制程能力,来料加强IQC的进料检验和控制生产制程以保证品质,提高生产效率,和规定产线良品物料的退料流程。
2.定义:不良物料:指生产过程中由各工位员工检验出的超过检验要求的原材料不良和生产过程中由于组装、拆卸、设备、夹具等所造成的原材料不良。
良品物料:产线从仓库领出的合格物料未经过使用或使用过但没有超过检验标准的物料。
3.职责:3.1 生产线3.1.1 产线物料员根据不良物料/良品物料及时填写《退料单》,将不良品/良品物料和《退料单》交IQC退料人员确认,并将IQC退料人员确认好的物料退给仓库,然后进行补料。
3.1.2 产线对不良的物料进行初步的区分来料不良和制程不良。
3.2IPQC退料人员根据生产线物料员送过来的不良物料和《退料单》,对不良物料进行确认,并区分出来料不良与制程不良,当退料中发现不良物料中有的物料没有超过检验要求,则将没有超过检验要求的物料作为良品退回产线,对于产线退回的良品物料进行抽检。
3.3仓库3.3.1 根据IPQC退料人员确认标识好的不良物料,按照制程不良和来料不良分别放在不良品区的制程不良区域和来料不良区域。
3.3.2 根据不良品的数量补良品给生产线。
3.3.3 产线退回的良品物料根据物控的指令和产线的《退料单》以及IPQC退料人员的确认后张贴的IQCPASS标签收取物料,放置在仓库的良品区。
3.4 PMC的物控人员下指令到生产、质量、仓库将产线的良品物料退回仓库。
4.不良物料的退料步骤:4.1生产线的不良品有生产线的物料员进行初步的区分来料不良和制程不良后,及时开出《退料单》(不良数量暂时不写,等IPQC退料人员确认、区分完毕后在填写具体的不良数量),将不文件名称车间退料作业规范生效日期2010-8-25批准/日期审核/日期制订刘祝琴良物料和退料单交给IPQC退料人员进行确认、区分。
生产线退料流程
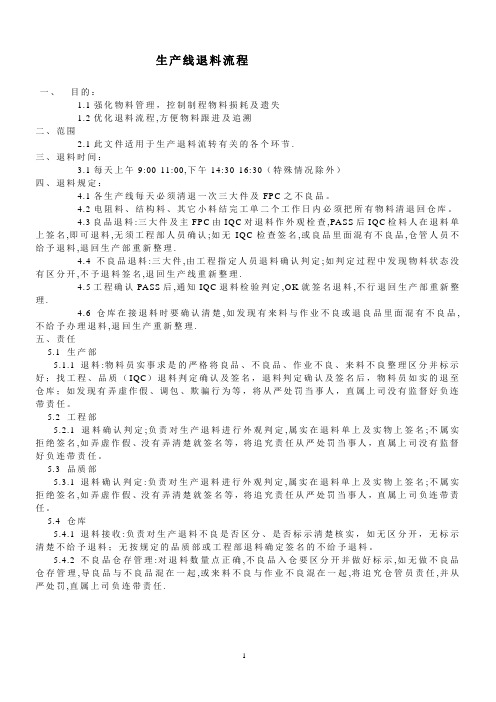
生产线退料流程一、目的:1.1强化物料管理,控制制程物料损耗及遗失1.2优化退料流程,方便物料跟进及追溯二、范围2.1此文件适用于生产退料流转有关的各个环节.三、退料时间:3.1每天上午9:00-11:00,下午14:30-16:30(特殊情况除外)四、退料规定:4.1各生产线每天必须清退一次三大件及FPC之不良品。
4.2电阻料、结构料、其它小料结完工单二个工作日内必须把所有物料清退回仓库。
4.3良品退料:三大件及主FPC由IQC对退料作外观栓查,PASS后IQC检料人在退料单上签名,即可退料,无须工程部人员确认;如无IQC检查签名,或良品里面混有不良品,仓管人员不给予退料,退回生产部重新整理.4.4不良品退料:三大件,由工程指定人员退料确认判定;如判定过程中发现物料状态没有区分开,不予退料签名,退回生产线重新整理.4.5工程确认PASS后,通知IQC退料检验判定,OK就签名退料,不行退回生产部重新整理.4.6仓库在接退料时要确认清楚,如发现有来料与作业不良或退良品里面混有不良品,不给予办理退料,退回生产重新整理.五、责任5.1 生产部5.1.1退料:物料员实事求是的严格将良品、不良品、作业不良、来料不良整理区分并标示好;找工程、品质(IQC)退料判定确认及签名,退料判定确认及签名后,物料员如实的退至仓库;如发现有弄虚作假、调包、欺骗行为等,将从严处罚当事人,直属上司没有监督好负连带责任。
5.2 工程部5.2.1 退料确认判定;负责对生产退料进行外观判定,属实在退料单上及实物上签名;不属实拒绝签名,如弄虚作假、没有弄清楚就签名等,将追究责任从严处罚当事人,直属上司没有监督好负连带责任。
5.3 品质部5.3.1退料确认判定:负责对生产退料进行外观判定,属实在退料单上及实物上签名;不属实拒绝签名,如弄虚作假、没有弄清楚就签名等,将追究责任从严处罚当事人,直属上司负连带责任。
5.4 仓库5.4.1退料接收:负责对生产退料不良是否区分、是否标示清楚核实,如无区分开,无标示清楚不给予退料;无按规定的品质部或工程部退料确定签名的不给予退料。
SAP工单领退料操作手册

工厂
生产工厂
工单编号
需要发料的工单号
反冲
因为是对工单中的反冲物料进行发料,所以要选此项
2.3
1、点击“运行”
2、在申请数量栏位填写本次申请发料的数量。
3、在备注栏位输入备注信息。
4、点击Print Form按钮,点击打印预览
3
3
MB1B -
3
保存后:
栏位说明:
栏位及按钮
4、运行操作,来到下一页面
栏位说明:
栏位及按钮
说明
状态
红灯表示线边仓物料不足,绿灯表示物料已足够
明细
物料溯源明细
发货仓位
生产仓位
操作步骤:
1、选择状态为红灯的,或是全选
2、点击打印,出现打印预览页面
3、再点击点击打印预览,打印即可。2 ZRPP2Fra bibliotek自定义程序
2
栏位说明:
栏位及按钮
说明
领料申请单(计划)
说明
移动类型
输入移库的移动类型311
工厂
生产工厂
库存地点
发料仓
接受库存地点
生产仓储地点
操作步骤:
1、进入MB1B
2、输入移动类型311
3、输入工厂
4、输入库存地点(发料仓)回车进入下一画面
5、输入接收库存地点(生产仓储地点)
6、输入要发的物料和数量,保存即可。
注:如果有退料的情况,操作是一样的,只是发料仓与生产仓储地点要填反过来。
工单领(退)料
操作手册
版本
修订内容
修改人
审批人
生效日期
01
02
03
说明:此工单领料是针对从仓库领到产线的线边仓。
领退料作业指导书

4.1 材料:主要材料:电池片、E辅助材料:PET标签纸、助焊剂、3M胶带、托盘、纸箱、纸护角、塑料护角、
塑料护边、珍珠棉、打包带、PE缠绕膜;
生产耗材:焊锡丝、酒精、美工刀片、美纹纸胶带、抹布、高温海绵、表单;
4.2 设备工装治具:液压车、美工刀、撬棍;
领退料作业指导书
文件编号:
版本号:
生效日期:
1.目的
定义组件生产车间物料领取退料的作业方法,确保产品品质。
2.范围
适用于合肥晶澳太阳能科技有限公司物料领退的操作。
3.权责
3.1 生产人员严格按照作业指导书执行;
3.2 工艺部负责制定并修改作业指导书;
3.3 质量部负责检查、监督工艺文件的执行;
4.准备工作
通知现场质量人员确认。
页号:2/3
编制:
校对:
审核:
批准:
领退料作业指导书
文件编号:
版本号:
生效日期:
7.操作注意事项
7.1 班组长注意观察每天的温湿度,湿度小于70%,温度25℃±5℃,并记录《温湿度记录表》,
有异常及时通知动力部门;
7.2 电池片运转过程中,液压车托运量不要超过2托(32箱),箱子堆放不可超过4层,并用缠
5.5.6 物料员使用液压车将所领纸箱、托盘送至包装工序,填写包装工序领退料明细,并请接收
人员签字确认;
5.5.7 物料员将其它生产耗材、辅助材料领取后送至备料间。
5.6 物料员按照所领取物料包装箱上的标签将信息录入MES系统,并打印一份三张组件条码,使
用扫描枪将条码扫入MES系统,以便确认条码无误,并能正常扫出;
5.7 物料员将每份条形码中的1张粘贴到相对应的随工单上“条形码黏贴处”(随工单上所写信
退料控制流程

退料控制流程1. 目的: 对本公司退料进行控制,确保物料补料的及时性以及满足生产的需求。
2. 适用范围: 对本公司不合格产品,生产超发物料及不良品的退换补料。
3. 职责: 3.1仓库负责物料的退料的清点工作及办理相关退料手续;负责供应商来料不合格物料退货单和生产申请补料单的开具。
3.2质量部负责物料的品质检验工作及相关的检验报告。
3.3产线或外协厂负责超损物料和生产中产生的不良品退货与仓库办理相关手续。
.4.程序: 4.1生产退料 4.1.1生产将不良品物料汇总,填写《不良物料退换单》,交IQC检验. 4.1.2 IQC将生产退回的不良品,将检验的结果在《不良物料退换单》上注明是来料不良或加工坏,仓库凭生产部门《不良物料退换单》并有相关人员签字收料及办理相关手续.4.1.3生产部门为了加快清尾进度可凭《原材料物料申请单》由生产和物控部主管签字,先到物控申请先预补料再安排退料或生产退完不良品物料到物控开料单. 4.2来料不合格品退料 4.2.1物控根据IQC判定的来料不合格检验单,经部门主管审核后,交于物控部,物控部及时与采购联系由采购通知供应商退料4.2.2仓库根据物控开具《物料退货单》并经物控部主管审核,经供应商核实数量签收后,才可将物料退回供应商.仓库再根据物料退货单开《物品放行条》出货4.2.3办理退料后仓库按物料退货单进行记账,同时将单据妥善保存,以备公司及供应商查账.5.相关质量记录. 5.1《不良物料退换单》5.2《原材料出库单》5.3《物品放行条》作业指导书生产退料作业流程通过规范本公司各车间生产物料退库的作业步骤、流程、责任,确保退库物料作业有序、处理及时、帐目清晰。
2. 范围:适用于本公司所有生产领料后,需退库的物料。
3. 权责: 3.1.PMC 部:制作、生成、打印、传递K3 单据;K3 单据和系统审核;3.2.制造部:退料送检;按K3 单据办理物料退库;3.3.研发部:按手工单据办理模具车间边角料退库; 3.4.中心仓:按K3 单据接收退库物料;签认、传递K3 单据;物料保存; 3.5.品管部:退料检验;质量异常处理; 4. 定义: 4.1.手工单据:指不是K3 系统生成或制作的,普通印刷的纸质单据。
生产退换料流程
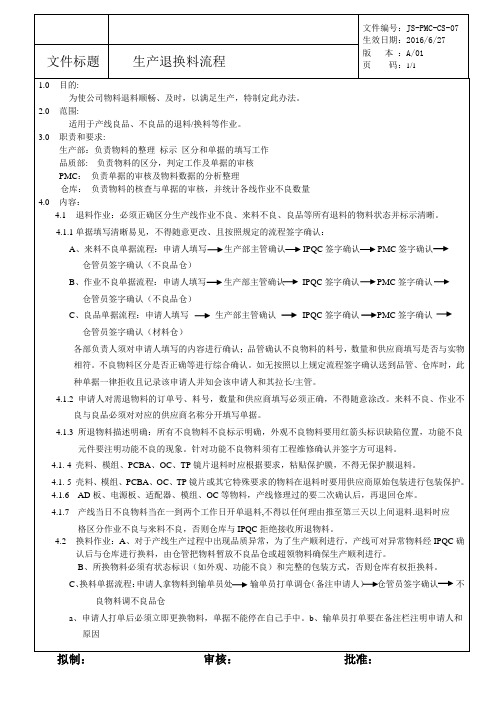
为使公司物料退料顺畅、及时,以满足生产,特制定此办法。
2.0范围:
适用于产线良品、不良品的退料/换料等作业。
3.0职责和要求:
生产部:负责物料的整理标示区分和单据的填写工作
品质部:负责物料的区分,判定工作及单据的审核
PMC:负责单据的审核及物料数据的分析整理
仓库:负责物料的核查与单据的审核,并统计各线作业不良数量
4.1. 4壳料、模组、PCBA、OC、TP镜片退料时应根据要求,粘贴保护膜,不得无保护膜退料。
4.1. 5壳料、模组、PCBA、OC、TP镜片或其它特殊要求的物料在退料时要用供应商原始包装进行包装保护。
4.1.6 AD板、电源板、适配器、模组、OC等物料,产线修理过的要二次确认后,再退回仓库。
4.1.7产线当日不良物料当在一到两个工作日开单退料,不得以任何理由推至第三天以上间退料.退料时应
格区分作业不良与来料不良,否则仓库与IPQC拒绝接收所退物料。
4.2换料作业:A、对于产线生产过程中出现品质异常,为了生产顺利进行,产线可对异常物料经IPQC确认后与仓库进行换料,由仓管把物料暂放不良品仓或超领物料确保生产顺利进行。
B、所换物料必须有状态标识(如外观、功能不良)和完整的包装方式,否则仓库有权拒换料。
C、换料单据流程:申请人拿物料到输单员处输单员打单调仓(备注申请人)仓管员签字确认不良物料调不良品仓
a、申请人打单后必须立即更换物料,单据不能停在自己手中。b、输单员打单要在备注栏注明申请人和
原因
拟制:审核:批准:
仓管员签字确认(不良品仓)
C、良品单据流程:申请人填写生产部主管确认IPQC签字确认PMC签字确认
仓管员签字确认(材料仓)
各部负责人须对申请人填写的内容进行确认;品管确认不良物料的料号,数量和供应商填写是否与实物相符。不良物料区分是否正确等进行综合确认。如无按照以上规定流程签字确认送到品管、仓库时,此种单据一律拒收且记录该申请人并知会该申请人和其拉长/主管。
生产退料检验流程
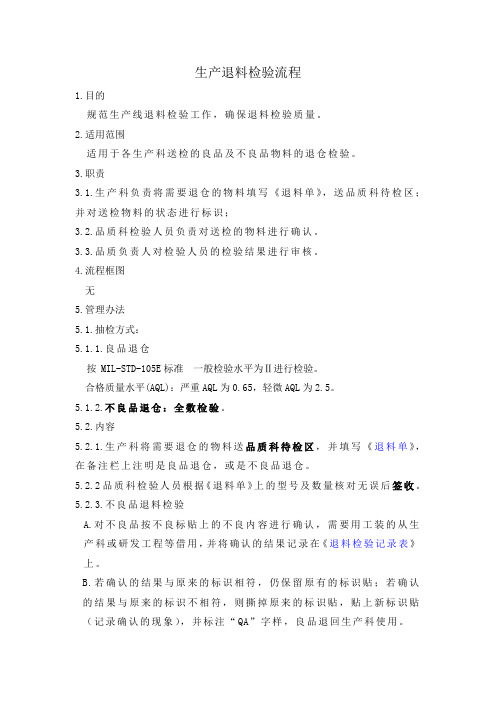
生产退料检验流程1.目的规范生产线退料检验工作,确保退料检验质量。
2.适用范围适用于各生产科送检的良品及不良品物料的退仓检验。
3.职责3.1.生产科负责将需要退仓的物料填写《退料单》,送品质科待检区;并对送检物料的状态进行标识;3.2.品质科检验人员负责对送检的物料进行确认。
3.3.品质负责人对检验人员的检验结果进行审核。
4.流程框图无5.管理办法5.1.抽检方式:5.1.1.良品退仓按MIL-STD-105E标准一般检验水平为Ⅱ进行检验。
合格质量水平(AQL):严重AQL为0.65,轻微AQL为2.5。
5.1.2.不良品退仓:全数检验。
5.2.内容5.2.1.生产科将需要退仓的物料送品质科待检区,并填写《退料单》,在备注栏上注明是良品退仓,或是不良品退仓。
5.2.2品质科检验人员根据《退料单》上的型号及数量核对无误后签收。
5.2.3.不良品退料检验A.对不良品按不良标贴上的不良内容进行确认,需要用工装的从生产科或研发工程等借用,并将确认的结果记录在《退料检验记录表》上。
B.若确认的结果与原来的标识相符,仍保留原有的标识贴;若确认的结果与原来的标识不相符,则撕掉原来的标识贴,贴上新标识贴(记录确认的现象),并标注“QA”字样,良品退回生产科使用。
5.2.4.良品退料检验5.2.4.1.按规定的抽样方式对送检的良品进行抽样,对抽取的物料按相关作业指导书进行确认,判断该批送检的物料是否为良品。
5.2.4.2.若确认的良品中有不良品,但没有超出允收标准时,则判此批合格,并对不良品进行标识(标注“QA”字样)退生产部;良品中有超出允收标准的不良品时,则判此批不合格,退生产部返工处理。
5.2.5.待处理品退仓,检验员与QE工程师共同确认可否使用,并将检验结果标识到物品上同时做好检验记录。
5.2.6.检验完毕,检验员将所借工装退还生产部,将检验的内容详细记录在《退料检验记录表》上,交相应品质负责人审核。
5.2.7.品质负责人对检验人员的检验结果进行审核,若发现有不符的情况,须进行修改,在修改处签名;同时在《退料单》上签字确认。
退料流程
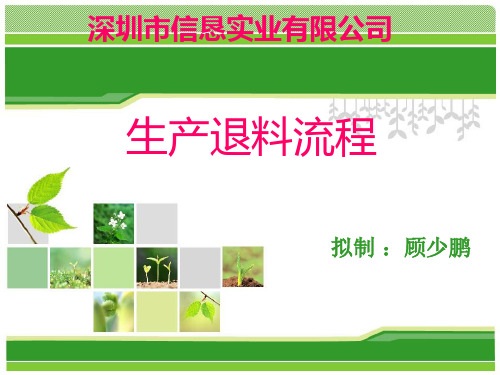
深圳市信恳实业有限公司生产退料流程拟制:顾少鹏•目的:为了使生产退料顺畅、及时、规范,以满足生产需求。
特制定此流程。
•范围:生产部品质部工程部仓库计划•生产部:负责物料的整理标示初步区分和单据的填写工作.•品质部: 负责物料的区分,判定工作及单据的审核.•工程部:负责四大件(PCBA LCD TP CAM)物料的判定工作及单据的审核.•PMC:负责单据的审核及物料数据的分析整理.•仓库:负责物料的核查与单据的审核,并统计库存不良品数量,定时通知供应商过来处理。
•退料部门:应正确区分生产线作业不良、来料不良等所有退料的物料状态并标示清晰;•单据填写清晰易见,不得随意更改、且按照规定的流程签字确认:• A 来料不良、良品退回仓库单据流程:申请人填写生产部负责人审核IPQC签字确认PE确认IQC 确认PMC签字确认仓管员签字确认仓库主管审核。
备注客责原因需客户签字。
•B作业不良单据流程:申请人填写生产部主管审核IPQC 确认PE签字确认PMC签字确认仓库部签字确认仓库主管审核备注四大件作业不良需要总监或副总确认•各部负责人须对申请人填写的内容进行确认(四大件填写不良状态标示卡);良品物料IPQC确认良物料的外观OK ,料号和供应商填写是否与实物相符。
PE须对不良物料功能方面进行确认;IPQC确认不良物料的料号供应商填写是否与实物相符。
不良物料区分是否正确等进行综合确认。
如无按照以上规定流程签字确认送到IPQC、仓库时,此种单据一律拒收且记录该申请人并知会该申请人和主管。
•申请人对需退物料的订单号、料号,数量和供应商填写必须正确,不得随意涂改。
来料不良、良品与作业不良及必要时对应的供应商名称应分开开单填写。
•所退物料描述明确:所有不良物料不良标示明确,外观不良物料要用红箭头标识缺陷位置,功能不良元件要注明功能不良的现象。
针对功能不良物料须有产线维修确认并由工程签字方可退料。
•壳料,屏,按键/TP镜片退料时应根据要求,粘贴保护膜,不得无保护膜退到品管处。
退料管理规范
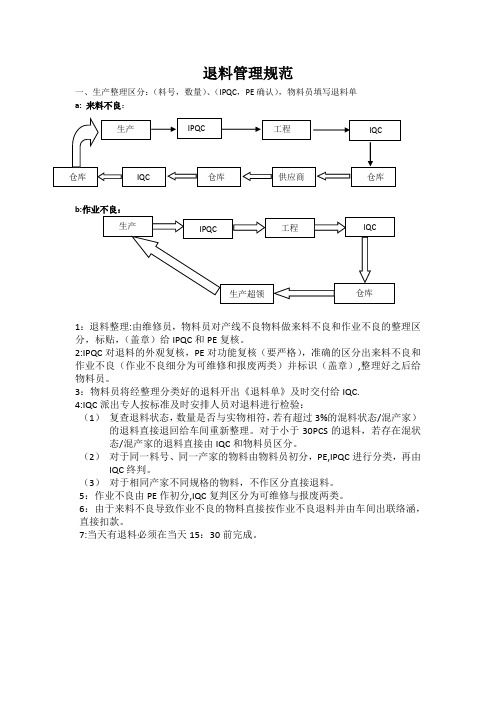
退料管理规范
一、生产整理区分:(料号,数量)、(IPQC,PE确认),物料员填写退料单
a: 来料不良:
b:作业不良:
1:退料整理:由维修员,物料员对产线不良物料做来料不良和作业不良的整理区分,标贴,(盖章)给IPQC和PE复核。
2:IPQC对退料的外观复核,PE对功能复核(要严格),准确的区分出来料不良和作业不良(作业不良细分为可维修和报废两类)并标识(盖章),整理好之后给物料员。
3:物料员将经整理分类好的退料开出《退料单》及时交付给IQC.
4:IQC派出专人按标准及时安排人员对退料进行检验:
(1)复查退料状态,数量是否与实物相符,若有超过3%的混料状态/混产家)的退料直接退回给车间重新整理。
对于小于30PCS的退料,若存在混状
态/混产家的退料直接由IQC和物料员区分。
(2)对于同一料号、同一产家的物料由物料员初分,PE,IPQC进行分类,再由IQC终判。
(3)对于相同产家不同规格的物料,不作区分直接退料。
5:作业不良由PE作初分,IQC复判区分为可维修与报废两类。
6:由于来料不良导致作业不良的物料直接按作业不良退料并由车间出联络涵,直接扣款。
7:当天有退料必须在当天15:30前完成。
生产线工艺退料管理暂行办法
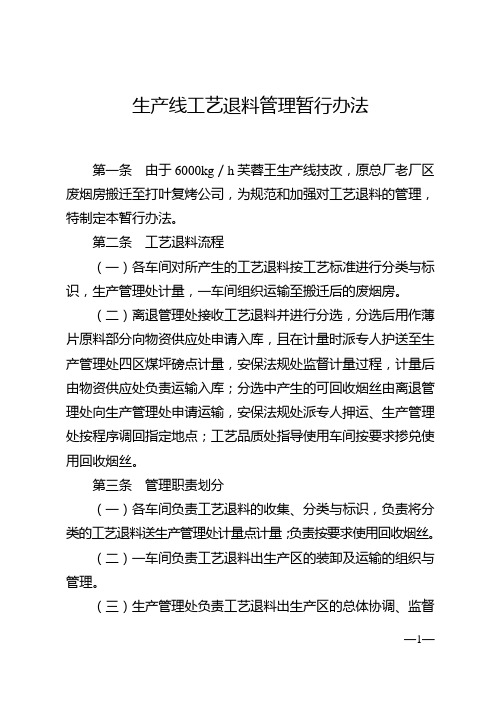
生产线工艺退料管理暂行办法第一条由于6000kg/h芙蓉王生产线技改,原总厂老厂区废烟房搬迁至打叶复烤公司,为规范和加强对工艺退料的管理,特制定本暂行办法。
第二条工艺退料流程(一)各车间对所产生的工艺退料按工艺标准进行分类与标识,生产管理处计量,一车间组织运输至搬迁后的废烟房。
(二)离退管理处接收工艺退料并进行分选,分选后用作薄片原料部分向物资供应处申请入库,且在计量时派专人护送至生产管理处四区煤坪磅点计量,安保法规处监督计量过程,计量后由物资供应处负责运输入库;分选中产生的可回收烟丝由离退管理处向生产管理处申请运输,安保法规处派专人押运、生产管理处按程序调回指定地点;工艺品质处指导使用车间按要求掺兑使用回收烟丝。
第三条管理职责划分(一)各车间负责工艺退料的收集、分类与标识,负责将分类的工艺退料送生产管理处计量点计量;负责按要求使用回收烟丝。
(二)一车间负责工艺退料出生产区的装卸及运输的组织与管理。
(三)生产管理处负责工艺退料出生产区的总体协调、监督与考核工作,负责数据计量;负责可回收烟丝调回指定地点的组织与过程管理。
(四)离退管理处负责工艺退料的加工分选、质量控制及日常管理工作;负责入库申请、护送入库原料至生产管理处四区煤坪磅点计量以及可回收烟丝的运输申请;负责工艺退料和可回收烟丝的台帐建立和管理。
(五)物资供应处负责分选后入库原料的装车、运输与入库;负责相应的管理工作。
(六)技术中心产品研究所负责制定可回收烟丝的掺配标准。
(七)工艺品质处负责废品房工艺退料和可回收烟丝加工和贮存所需的有关工艺技术文件的组织与实施;负责对车间收集的工艺退料以及分选后回收烟丝和用作薄片的原料符合工艺标准的情况进行监督抽查与考核;负责对回收烟丝的掺配进行指导和监督检查。
(八)安保法规处负责工艺退料出门的监督检查;负责运输过程监管;负责将可回收烟丝从废烟房押运至生产区指定地点(包括计量过程的押运);负责入库原料在四区煤坪磅点的计量监督。
退料流程管理规范
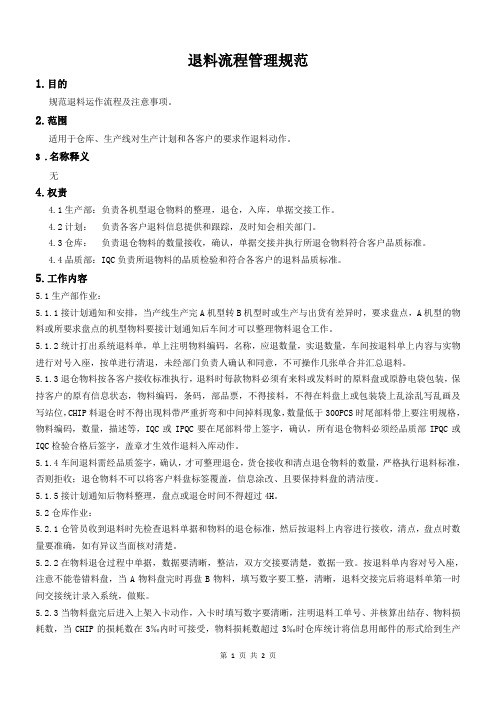
退料流程管理规范1.目的规范退料运作流程及注意事项。
2.范围适用于仓库、生产线对生产计划和各客户的要求作退料动作。
3 .名称释义无4.权责4.1生产部:负责各机型退仓物料的整理,退仓,入库,单据交接工作。
4.2计划:负责各客户退料信息提供和跟踪,及时知会相关部门。
4.3仓库:负责退仓物料的数量接收,确认,单据交接并执行所退仓物料符合客户品质标准。
4.4品质部:IQC负责所退物料的品质检验和符合各客户的退料品质标准。
5.工作内容5.1生产部作业:5.1.1接计划通知和安排,当产线生产完A机型转B机型时或生产与出货有差异时,要求盘点,A机型的物料或所要求盘点的机型物料要接计划通知后车间才可以整理物料退仓工作。
5.1.2统计打出系统退料单,单上注明物料编码,名称,应退数量,实退数量,车间按退料单上内容与实物进行对号入座,按单进行清退,未经部门负责人确认和同意,不可操作几张单合并汇总退料。
5.1.3退仓物料按各客户接收标准执行,退料时每款物料必须有来料或发料时的原料盘或原静电袋包装,保持客户的原有信息状态,物料编码,条码,部品票,不得接料,不得在料盘上或包装袋上乱涂乱写乱画及写站位,CHIP料退仓时不得出现料带严重折弯和中间掉料现象,数量低于300PCS时尾部料带上要注明规格,物料编码,数量,描述等,IQC或IPQC要在尾部料带上签字,确认,所有退仓物料必须经品质部IPQC或IQC检验合格后签字,盖章才生效作退料入库动作。
5.1.4车间退料需经品质签字,确认,才可整理退仓,货仓接收和清点退仓物料的数量,严格执行退料标准,否则拒收;退仓物料不可以将客户料盘标签覆盖,信息涂改、且要保持料盘的清洁度。
5.1.5接计划通知后物料整理,盘点或退仓时间不得超过4H。
5.2仓库作业:5.2.1仓管员收到退料时先检查退料单据和物料的退仓标准,然后按退料上内容进行接收,清点,盘点时数量要准确,如有异议当面核对清楚。
5.2.2在物料退仓过程中单据,数据要清晰,整洁,双方交接要清楚,数据一致。
领料、退料、补料程序

清清环保电器有限公司领料、退料、补料程序(讨论稿)1.0目的:为使公司物料领退换顺畅、及时,以满足生产和方便管理。
特制定此办法2.0范围:生产部品质部技术部仓库各车间3.0职责和要求:车间:负责物料的整理标示区分和单据的填写工作品质部: 负责物料的区分状况,判定状况及单据的审核技术部:负责特殊情况下材料状况和单据的审核生产部:负责单据的审核及物料数据的分析整理仓库:负责各类状态物料的出入库,并统计各车间各类异常领料和不良退料数量每周、月及年汇总。
4.0内容一、正常订单领料1、生产线根据订单资料,原则上提前一至两天开具《领料单》,领料单必须经生产线主管、仓库主管审批、总经理助理核准后生效,领料单必须注明物品名称、料号、型号、颜色、数量以及订单号。
2、仓库接到《领料单》根据生产线进度提前备料,生产线需提前1天到仓库完成领料。
3、原则上,无论通用配件还是专用配件领用必须根据订单数量,不允许多领,仓库进行监督。
但是为避免因为小的易耗零部件频繁补领造成仓库和车间不必要的麻烦,通用小配件生产部门可根据车间生产线情况适当多领用一些。
4、小件配件原则上一次性领完,若因库存不够等其他原因不能一次性领完,可分批领料。
5、大件物料或跟线物料第一次领料时,应考虑生产单的产能和区域空间情况,以备足一天的用量为原则。
6、不能一次性领完的物料,生产线可根据生产进度情况进行领料。
7、生产线领料时,领料员对物料数量务必与仓管员当面点清数量,离开仓库后,仓库一概不承认数量短缺,产生的一切后果由生产单位负责。
8、生产单位领料时,生产单据务必按照订单号分开,不允许混订单领料,各仓管员务必监督。
9、因特殊原因需先借物料的,所借物料必须在24小时内开具《领料单》。
10、生产线如遇注塑配件生产急用,但注塑部又未来得及入库,生产线可直接到注塑车间领取。
11、注塑车间接到领料通知及时安排进行发料,并做好详细记录,由领用人签字确认,同时要及时通知品质部确认。
产线退料处理
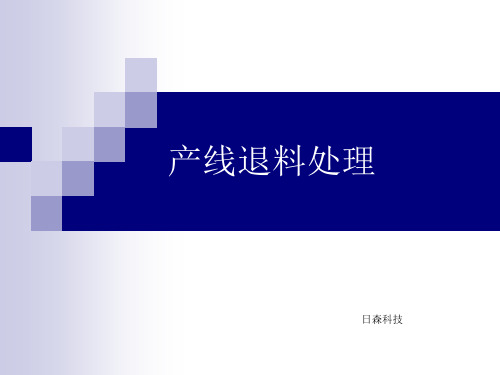
2,选择退库物料 选择退库物料
1.4来料不良退料
注意仓库
注意数量
2.1制程不良退料
注意是蓝字其它入库单而不是红字其他出库单 注意仓库
2.2补料
2.3补料
2.4补料
2.5补料
3,点确定 ,
1,选择生产订单 ,
2,选择物料 ,
2.6补料
注意补料标志
3.1剩余物料退料
生产订单生成材料出库单,在生产过程中发现来料不良退库的情况,用材料出库单(红字),仓库选来料不良品仓。具体操作方法 :
产线退料处理
日森科技
产线退料处理方法
1.来料不良退料 2.制程不良退料 3.剩余物料退料
1.1来料不良退料
生产订单生成材料出库单,在生产过程中发现来料不良退库的情况,用材料出库单(红字),仓库选来料不良品仓。具体操作方法 :
1.2来料不良退料
1.3来料不良退料
3,点确定 点确定
1,选生产订单 选生产订单
ห้องสมุดไป่ตู้
3.2剩余物料退料
3.3剩余物料退料
3,点确定 点确定
1,选生产订单 选生产订单
2,选择退库物料 选择退库物料
3.4剩余物料退料
注意仓库
注意数量
产线物料管控流程

产线物料管控流程一、物料领用、使用及借用1、生产领用物料按照《物料计划需求表》上的内容进行领用,领料完毕要与仓库管理员共同确认领料信息。
各物料员收到物料时要在《领料记录单》登记清楚物料的名称、规格、型号、数量、注明日期、领用人等内容与各线班长共同确认以上物料信息并签收。
2、各线要严格按照本部门计划进行领料,对无计划领用,物料员、仓管员有权不给予发放物料,同时不允许维护物料多领多占,影响物料的正常使用。
3、车间产品、物料、仪器、工具、设备外借时要在《生产线借出物料清单》记录,归还时要确认完好程度。
4、生产物料未用完的除报废,近期不再生产此种型号时,要将余料经确认退给车间物料员或仓库。
5、生产线出现来料不够、不良与人为损坏的物料,如间接影响到生产线的,要及时告知班长,批量超过5%及来料不够时班长要及时告知主管、质量工程师到现场确认并拍照反馈给到供应商。
不良与人为损坏的物料每天由物料员收集给到QC判定后与仓库及时更换。
6、生产如需购买生产所需物品,负责人可向部门计划主管做计划申请,填写《请购单》即可。
7、质量QC抽检要经过当线指定人员当面确认并在《抽检往/来记录表》上登记。
8、如在当批清线时发现丢失物料,生产人员没有发现缺少物料情况,如在废弃物箱内找到,确认工序生产物料对生产人员进行处罚,如果没有找到物料所有参与生产人员包括班长共同按照物料原价进行赔偿。
未经检验的产品不得入库。
9、生产入库的成品,物料员应核对型号、数量、外包装标识是否正确及完好,且有《入库单》必须有QC负责人签字证明此产品是否合格才方可入库。
11、物料员应进行经常性动态盘点,做到日清日结,保持账、物相符,月尾、年中、年末应配合班长做好盘点工作。
二、原料物资1、领用物料后,进入车间必须分类并摆放整齐,统一放置于固定区域,要做到既不影响生产,也能迅速拿取,避免混乱、损坏等。
2、每个物料箱两侧必须有与箱内物料一致的标签,要有数量及领用时间。
作业流程

物料的收、发、退、补料运作流程目的:为了规范物料的管理及控制物料的流失,以确保生产的正常运行。
适用范围:适用于生产部各车间生产线物料的管理。
作业流程:1、物料的收料:(1)各生产线物料员凭打单员打出的领料单分别到货仓相应的仓区进行领料,收料时一定要按照物料清单和领料单上的物料名称、规格及编号进行签领.(2)原则上收料时,只对尾数全点,对原封箱只予抽箱清点,但对于贵重物料一定要全点收货,若遇包装不足时应及时通知仓管员处理。
(3)物料员按生产计划提前三天收料,将从仓库收到的物料摆放于物料周转仓内,并分区域标识清楚。
若有个别物料欠料或未齐套时,要知会物料线长,由他填写物料齐套表发相关负责人,要于生产开拉前将所有欠料追齐。
2、物料的发料:开拉时物料员将物料周转仓内物料发到生产线上,由线长指定组长或供料员签收并摆放到相应工位上使用。
1、物料的退料:在生产过程中,从生产线上检出的坏料,由线长指定组长或供料员按原包装整理好,分清楚来料坏和生产坏退给物料员签名,再由物料员开退料单经相关管理及IQC确认签名后退仓,由仓管员确认签名。
2、物料的补料:物料员根据已确认的退料单到生产部ERP操作员处生成补料单,再凭打单员打出的补料单到货仓相应仓区领取物料。
3、物料的监控:当组长或供料员在点料签收时,如发现有来料少的情况,物料员不但要将少数部分补足数外,再视物料的价值而作出相应警告或惩罚处理;如组长或供料员点数无误签收后,拉上再发现有类似少料情况,则对该线线长及所指定的组长或供料员同时给予惩罚,按该少的物料的价值如数赔偿方可进行申请补料。
拟制:审核:批准:日期:日期:日期:底板生产作业流程目的:为了规范底板生产的管理及作业流程。
适用范围:适用于底板车间各生产线。
作业流程:1、开拉前线长或主管根据PMC生产计划的生产日期及生产机型,提前到生产工程组领取相应的开拉样板、《作业指导书》和夹具,并核对各种技术资料等文件。
2、开拉前线长或主管组织相关管理、PE人员召开开拉前准备会议,对已填写好的《生产线重要工作检查跟踪表》、《底板、组装开拉前工作表》进行商讨,核对无误并经审核、批准后方可进行生产。
生产线物料领退料作业指导书

生产线物料领退料作业指导书1.目的确保生产过程能及时领退料,并对物料耗用进行有效地控制。
2.适用范围适用于公司各生产车间领退料的管理。
3.职责3.1 仓库主管和生产物料主管负责监督本文件的有效执行。
3.2 生产线当值领班和仓库物料领班负责对线上岗位操作员和仓库发料员领退料的协调工作。
3.3 生产负责填写领料单,生产线各岗位操作员与仓库发料员负责对物料的具体数量、名称、批号、版本信息、规格等进行确认,并填写退料单。
3.4 QC/岗位操作员负责对使用物料作开机前的首检,以及转换物料的检查确认。
岗位操作员负责对生产过程中物料使用抽查。
参见《岗位的物料使用检查表》和《物料使用记录表》。
4.定义版本信息:指同种物料的不同分销区域的识别代码。
例如果汁促销的南区版为“S”,北区版为“N”。
5.程序5.1 生产线人员依据每周生产计划,按生产岗位实际剩余物料数量,以连续生产18小时所耗用物料数量开出领料单,领料单共三联,仓库联、财务核算联、领料联,应严格按相同岗位的物料用一张领料单开出,要注:品名、单位、版本信息(在备注栏内注明)、计划领用数量、交仓库发料员备料和发料。
5.2 果肉、果汁、香精类在冷库存放的物料可参照《糖浆配制SOP》来处理。
5.3 仓库发料员依据领料单在规定的时间段(白班从10:00到14:00,晚班从22:00到2:00)按先进先出的原则将生产线所需物料发放到物料指定摆放区域,并在领料单上注明物料生产批号和实际发料数量(有零散物料会造成计划领用数和实际发料数量不一致),物料由仓库发料员将其转到指定的物料转运区。
在同一操作岗位不能同时有两种以上的物料存在,当操作岗位上一种物料还没用完,另一种物料不能直接发到岗位,以免用混物料.另外物料转运区不同版本的物料(如相同口味不同版本产品的促销盖、标签、纸箱、纸托、瓶坯等)不能存放在同一物料转运区,如果要发料此类物料,必须将先前存放的物料转到操作岗位物料存放区,否则不允许发出此类物料。