120t区域精炼工艺3-16详解
韶钢120 tRH精炼技术的应用研究

图 1 钢 水 真 空 循 环脱 气装 置 基 本 工 作 原 理 示 意
●
2 R H钢水真空循环精炼技术 的应用
21 R . H精炼 工艺路 线的选 择
从 而提高脱 氢 的速 度 ; 于吹 氧加 铝 升 温后 的钢水 对 更需 加快环 流速 度 , 快脱 氧及夹杂 物去 除 ; 加 合金投 人后 为保证 合金 均匀 , 同时钢 中各种 夹杂物 上浮 , 需
适 当增 加环 流气 量 以加 速成 分的均匀 及夹杂 物 的有 效 上 浮. 为此 通过 一 段 时 间 的摸 索 , 析对 比 , 定 分 制
R H投入 试生产 后 , 针对 船板 钢 和 管线 钢 , 用 采 了高炉铁水一 混 铁炉一 铁 水 预处 理一 转 炉一 R 真 H 空一 l 号宽 板坯 连铸机 和高 炉 铁水一 混 铁 炉一 转 炉
— —
[ = 刎
/ P
() 1
式 中:H ——钢水含氢量, 1 一; [] ×0
总第 13期 7
王进 文 , : 等 韶钢 10t H精炼技术 的应用研究 2 R
4 3
异 , 降管返 回钢包 . 经脱气 的钢液又 不断 从上 经下 未
不 同生 产条件 下 的脱 气处 理周期 , 轻处 理 3 n 本 0mi,
0rn 以达到去气、 a 去夹杂的 目的, 提高钢水 升管进入真空槽, 从而连续循环. 1 R 图 为 H工作原 处理 4 i,
方面 , 由于钢 液在浸 渍管 中 的流速 比较 大 , 并且 吹气
侧 的搅拌 也很剧 烈 , 渍 管 内壁 不 断地 受 到 冲刷 而 浸 使 其 内径 变大 . 于是 , 倘脱 氧产 物少 , 渍 管 内径 随 浸 着 炉龄 的增加 而增 大 ; 之 , 反 浸渍 管 内径减 小 . 流 环 气 流量 控制在 整个 冶 炼 控 制过 程 中是 非 常重 要 的 ,
炼钢厂120吨精炼炉的技术要点研究
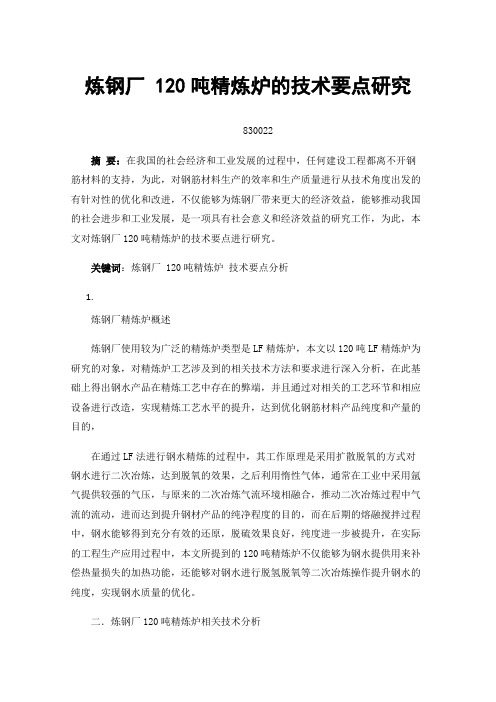
炼钢厂 120吨精炼炉的技术要点研究830022摘要:在我国的社会经济和工业发展的过程中,任何建设工程都离不开钢筋材料的支持,为此,对钢筋材料生产的效率和生产质量进行从技术角度出发的有针对性的优化和改进,不仅能够为炼钢厂带来更大的经济效益,能够推动我国的社会进步和工业发展,是一项具有社会意义和经济效益的研究工作,为此,本文对炼钢厂120吨精炼炉的技术要点进行研究。
关键词:炼钢厂 120吨精炼炉技术要点分析1.炼钢厂精炼炉概述炼钢厂使用较为广泛的精炼炉类型是LF精炼炉,本文以120吨LF精炼炉为研究的对象,对精炼炉工艺涉及到的相关技术方法和要求进行深入分析,在此基础上得出钢水产品在精炼工艺中存在的弊端,并且通过对相关的工艺环节和相应设备进行改造,实现精炼工艺水平的提升,达到优化钢筋材料产品纯度和产量的目的,在通过LF法进行钢水精炼的过程中,其工作原理是采用扩散脱氧的方式对钢水进行二次冶炼,达到脱氧的效果,之后利用惰性气体,通常在工业中采用氩气提供较强的气压,与原来的二次冶炼气流环境相融合,推动二次冶炼过程中气流的流动,进而达到提升钢材产品的纯净程度的目的,而在后期的熔融搅拌过程中,钢水能够得到充分有效的还原,脱硫效果良好,纯度进一步被提升,在实际的工程生产应用过程中,本文所提到的120吨精炼炉不仅能够为钢水提供用来补偿热量损失的加热功能,还能够对钢水进行脱氢脱氧等二次冶炼操作提升钢水的纯度,实现钢水质量的优化。
二.炼钢厂120吨精炼炉相关技术分析作为近年来炼钢厂主要采用的精炼方式,通过120吨精炼炉进行精炼的过程中,工艺技术具有设备结构简单,生产成本低和产品质量高的优势,并且适合于多种钢材的精炼和制备,生产过程能够随不同的种类进行灵活的设计,使得钢水冶炼得质量能够有效提升,涉及到的相关工艺技术包括钢炮移送技术,吹氩搅拌技术,电极加热技术,测温取样技术等,在实际的工作操作过程中,钢水首先要到达120吨精炼炉的接收部位,在进入精炼炉之后,首先进行的处理环节是对钢水进行吹氩搅拌,实现钢水的脱硫脱氧操作,之后钢水进入精炼炉的处理区域,由电弧加热之后,形成泡沫渣,为后续的埋弧加热处理做准备,完成上述工艺之后,利用吹氩搅拌的方式,提升钢水的均匀度,并且补偿它在流动过程中的热量损失,热量损失的补偿由电弧加热升温实现,在对钢水进行加热升温的同时,完成测温取样、合金加料和喂丝等后续的钢水处理操作,之后进入真空系统进行连铸等工艺的处理,通过上文的分析可以看出,120吨精炼炉在炼钢厂炼钢的应用过程中,极大的丰富了炼钢厂钢产品的种类,不仅能够完成传统钢筋制品的制备,还能够生产质量更高的高碳硬线钢,冷扎板等钢产品,企业的生产力和经济效益在应用120吨精炼炉之后取得了非常大的进步,企业的业务领域也得到了充分拓展。
炼钢-精炼工艺介绍
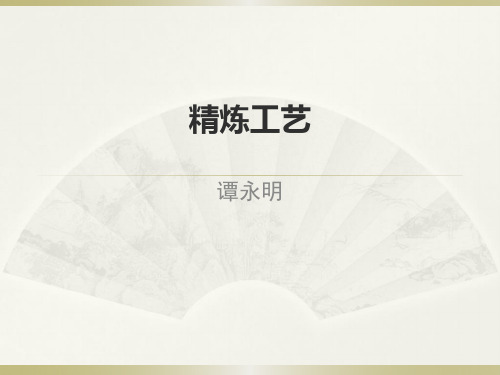
CAS底吹排渣工艺
4、CAS工艺
排渣效果(裸露钢液面面积)主要与渣层厚度、渣粘度和底吹氩 能力等有关。在底吹排渣过程中,随着底吹氩气流量增大,排渣 面积增大,但当底吹氩气流量达到一定值后,进一步增大底吹氩 气流量,其排渣效果变化不大。应选择较佳的底吹氩排渣流量, 防止钢水散热过多和减少氩气消耗量。
1.3增碳剂 袋装20Kg/包,要求固定碳含量≥94%,S≤0.5%,H2O≤0.5% 粒度3-8mm。
1、精炼过程用原料
1.4常用气体 1.4.1惰性气体 氮气、氩气等为冶金用惰性气体。主要用于二次钢水的保
护与隔离,以及对钢水精炼时的搅拌、吸气、去杂质等。 对人体的危害表现为窒息性伤害,浓度达到25g/m3时有危 险。 要求:干燥、干净、无杂质、水分<1%、纯度≥99.9%、 氧气<6PPm、氮气<20PPm、氧气+氮气≯20PPm 1.5钢包炉用材料 1.5.1冶金石灰: 采用转炉炼钢用活性石灰,保存期不得大于10天。
Si
74.0~80.0 72.0~80.0
化学成份,%
Mn
Cr
P
不大于
0.4
0.3
0.035
0.5
0.5
0.04
Si-Ca-Ba包芯线:
Si%
Ca% Ba% P%
≥50
≥14
≥14
≤0.02
Si-Ca包芯线:
Si%
Ca%
≥50
≥28
Al线:
P% ≤0.02
S% ≤0.03
S% ≤0.03
1、精炼过程用原料
二级 一级 特级
CaO% ≥85.0 ≥90.0 ≥92.0
SiO2% ≤3.5 ≤2.5 ≤1.5
120t区域精炼工艺3-16详解

2018年10月12日
31
真空状态下,脱氢效果与以下因素有关: ☆初始含量:初始含量越低,达到最终含量的处理时间越短。 钢液中初始含量并不取决于大气中的氢分压,钢液中〔H〕 主要是空气中水蒸气和原材料中水分带入的。 ☆处理时间:处理时间越长,最终〔H〕含量越低,但是当 〔H〕含量降低到一定程度,随着处理时间的延长,最终 〔H〕含量变化不大。因为此时钢水静压力和传质速度是其 限制环节。 ☆真空度:真空度提高,气相中氢分压降低,有利于脱氢反 应。 ☆吹氩搅拌:通过吹氩搅拌,相应增加了气液反应界面;提 高了熔池内传质速度;氩气泡上浮时,溶解在钢中的〔H〕 会以原子的形式进入氩气泡,氩气泡相当于一个个微小的真 空室。 ☆表面活性元素:〔O〕、〔S〕等表面活性元素含量的降 低,有利于〔H〕原子通过气液界面。
2018年10月12日
3
4.喷吹 喷吹也称喷射,是将反应剂利用气流直接加入冶金 熔体中的一种炉外精炼方法。由于它简便、高效, 所以也经常作为一种精炼手段,组合到其他炉外精 炼方法中。 喷吹技术利用气体的搅拌作用增加了粉状精炼剂和 钢液的接触界面,显著改善冶金反应的动力学条件。 因此可以实现快速脱硫、脱磷、脱氧,提高合金收 得率,促使夹杂物变性等功能。 RH配备喷吹功能,可以进行深脱硫,生产超低硫钢。
2018年10月12日
4
5.喂线 喂线是通过喂线机将钙、铝、硅钙、钡系合金等制成的包芯 线或铝等金属线高速加入到钢液的方法。具有如下特点: ·合金收得率高; ·能解决特种合金的加入问题; ·避免合金加入时的吸氮; ·投资费用少,应用范围广,操作简便。 喂线技术可单独应用。也可应用到各种精炼方法中。目前各 种炉外精炼方法中都添加了喂线设施,并且以推广到中间包 喂线、结晶器喂线。 采用不同的包芯线、金属线,喂线技术可具有脱氧、脱硫、 夹杂物变性、防止水口堵塞等功能。
120 t精炼炉水冷下料管改造
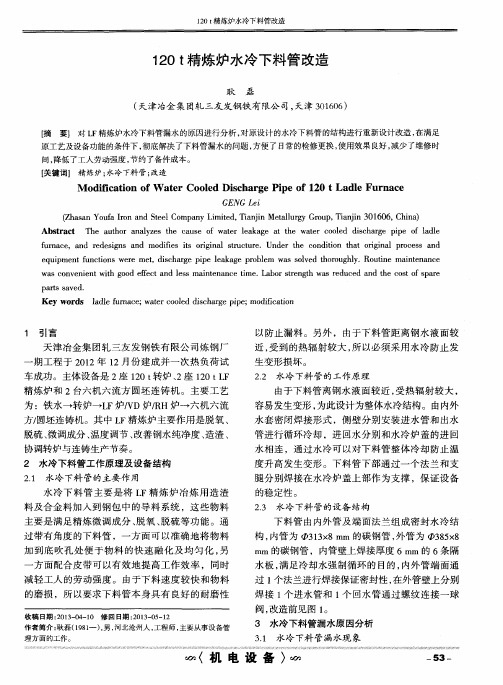
下 料 管 由内外 管 及 端 面 法 兰组 成 密 封水 冷 结
构, 内管 为 3 1 3 x 8 mm 的碳 钢管 , 外管为 q 5 3 8 5 x 8
GENG Le i
( Z h a s a n Y o u f a I r o n a n d S t e e l C o m p a n y L i m i t e d , T i a n j i n Me t a l l u r g y G r o u p , T i a n j i n 3 0 1 6 0 6 , C h i n a )
方/ 圆坯连铸机。其 中 L F精炼炉主要作用是脱氧 、 脱硫 、 微调 成分 、 温 度调 节 、 改善 钢 水纯 净度 、 造渣 、
协调 转炉 与连 铸生 产节 奏 。
2 水冷 下料 管 工作原 理及 设备 结构
2 . 1 水 冷 下料 管的 主要 作 用
管进行循环冷却 ,进 回水分别 和水冷炉盖的进 回
e q u i p me n t f u n c t i o n s we r e me t ,d i s c h a r g e p i p e l e a k a g e p r o b l e m wa s s o l v e d t ho r o u g h l y .Ro u t i n e ma i n t e n a n c e
车成 功 。主体 设备 是 2座 1 2 0 t 转炉 、 2座 1 2 0 t L F 精 炼 炉 和 2台六 机 六 流方 圆坯 连 铸 机 。主要 工 艺 为 :铁 水 转 炉一 L F炉, 、 , D炉/ R H炉一 六 机六 流
由于下 料 管 离 钢水 液 面 较 近 , 受 热 辐 射较 大 , 容 易发 生变 形 , 为此 设计 为 整体 水冷 结构 。由内外 水 套 密 闭焊 接形 式 ,侧 壁 分别 安 装 进水 管和 出水
120t区域精炼工艺3-16
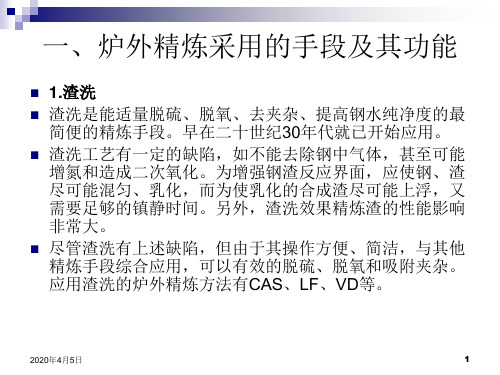
2020年4月5日
12
LF精炼工艺
1.温度控制工艺 1.1埋弧加热:减少吸氮;提高加热效率。 1.2加热终了温度确定:TLF终了=T中+ΔT1+ΔT2
TLF终了-最后一次加热结束后的钢包钢水温度。 T中-中间包标准温度。 ΔT1-过程温降。 ΔT2-补偿温度。
2020年4月5日
13
2.还原渣精炼工艺
采用不同的包芯线、金属线,喂线技术可具有脱氧、脱硫、 夹杂物变性、防止水口堵塞等功能。
2020年4月5日
5
6.升温 加热是调节钢液温度的一项常用手段。 炉外精炼设备大多配备加热手段。 采用电弧加热的方法有LF等炉外精炼方 法,有些DH、RH的真空室内也设有电 阻加热。还采用化学热法升温,即利用 加铝(或碳、硅)吹氧氧化的化学热, 使钢液升温,如CAS—OB、RH—OB、
一、炉外精炼采用的手段及其功能
1.渣洗 渣洗是能适量脱硫、脱氧、去夹杂、提高钢水纯净度的最
简便的精炼手段。早在二十世纪30年代就已开始应用。 渣洗工艺有一定的缺陷,如不能去除钢中气体,甚至可能
增氮和造成二次氧化。为增强钢渣反应界面,应使钢、渣 尽可能混匀、乳化,而为使乳化的合成渣尽可能上浮,又 需要足够的镇静时间。另外,渣洗效果精炼渣的性能影响 非常大。
2020年4月5日
4
5.喂线 喂线是通过喂线机将钙、铝、硅钙、钡系合金等制成的包芯 线或铝等金属线高速加入到钢液的方法。具有如下特点: ·合金收得率高; ·能解决特种合金的加入问题; ·避免合金加入时的吸氮; ·投资费用少,应用范围广,操作简便。 喂线技术可单独应用。也可应用到各种精炼方法中。目前各 种炉外精炼方法中都添加了喂线设施,并且以推广到中间包 喂线、结晶器喂线。
转炉炼钢工艺3-11
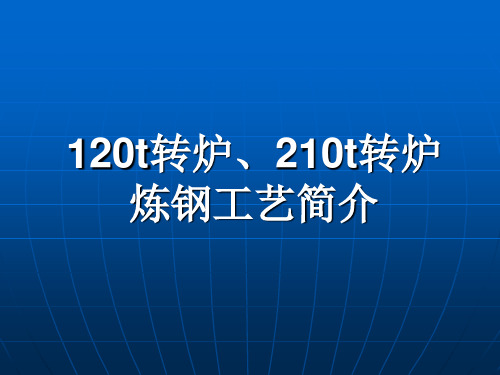
9500mm
φ7800mm 210t 211m3 1.0 m3/t(0.879)
熔池直径
熔池深度 出钢口内径 出钢口与水平的夹角
4910mm
1376mm 155mm 10°
6000mm
1800mm(装入量210t) 180mm 10°
1.2 120t、210t转炉炉型对照
项目 炉衬 熔池 厚度 炉身 120t转炉 800mm 800mm 210t转炉 1000mm 900mm
调整前后氧枪喷头参数对照
项目 调整前 φ44.5mm φ59 mm 喉口直径 45.5mm 出口直径 59.6mm
马赫数
半锥角
2.02
3.5°
2.05
3.5° 16° 16°
供气强度 2.8—3.5Nm3/t.min 2.8—3.5Nm3/t.min
中心夹角 14.5 °
调整后氧枪喷头使用效果
铁水成分
[As] As是一种非常容易偏析的元素,它会导致钢材的 塑性变差和钢板表面的微裂纹。这种情况会带来 连铸或轧制过程钢材的内部和表面质量问题,最 终会危害产品的质量和性能。 奥钢联从一个方坯连铸机工程项目发现在 As+Sn=0.1% 时,方坯完全失去了塑性,导致 了严重的裂纹甚至在矫直过程中方坯出现了漏钢。 As还是一种高度有毒的元素,会导致潜在的环境 污染和人体健康问题。高As含量的钢在国际贸易 中会受到抵制,由于认为这会对人体健康造成危 害。
济钢210转炉底吹供气元件调整
目前济钢炼钢厂转炉底吹供气元件均为毛细 管式底吹透气砖,存在供气过程中底吹流量调整 幅度小,供气元件易堵塞的缺点。双环缝式底吹 供气元件,即保留了毛细管式供气元件的气体流 接触面较为光滑的金属管内壁的优点,减少阻力, 避免气流对耐火材料的冲刷,而且在较低气源压 力下供气元件不易堵塞,供气强度调整幅度大 (调整范围在0.03m3/t.min~0.2m3/t.min), 炉役全过程供气状态稳定
炼钢厂基本工艺流程图
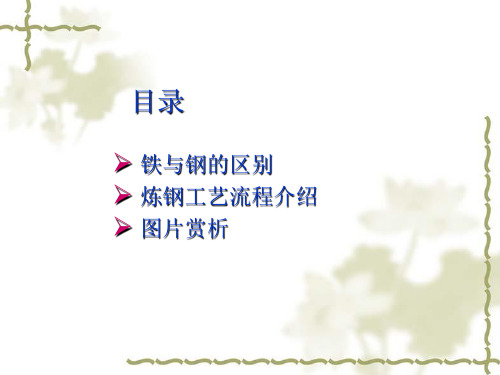
➢ 铁与钢的区别 ➢ 炼钢工艺流程介绍 ➢ 图片赏析
铁和钢的区别
➢ 化学成分
铁:C 4.1~4.3%,Si 0.25~0.50%, Mn 0.2~0.5%, P ≤0.12%,S ≤0.035%
钢:C <2.1% P ≤0.045%,S ≤0.050% 例:普通碳素结构钢Q195
C 0.06~0.12%,Si 0.12~0.30%, Mn 0.25~0.50%, P≤ 0.045%, S0.050%
铁水[S]: 0.035→≤0.010%
• 3:搅拌形式:KR、喷粉 • 4:目前较为先进的是铁水‘三脱’,目的是解放
转炉,提高钢水纯净度
铁水准备
N2
Mg粒
脱硫渣
铁水 铁水脱硫示意图
三、转炉
• 1:功能:降碳、提温、去S,P、脱H,O,N
去夹杂物、合金化
• 2:顶底复吹,顶枪吹氧,底吹Ar,N2,O2 • 3: 渣料:石灰、白云石、铁皮、萤石等,岀
• 1. 浇铸温度控制 • 2. 钢水成份控制 • 3. 拉速控制 • 4. 冷却控制 • 5. 液面控制 • 6. 连铸新技术、新措施
1. 浇注温度控制
连铸钢水工艺要求是,保证浇铸性能的前提下具有 较低的过热度。出钢温度是控制连铸浇铸温度的 基础与保证,提高出钢温度的命中率。钢水保温 的方法有以下几种办法:
• 2:加入石灰、预熔渣、萤石、铝粉、矾土(主要
成分:AL2O3)、电石造渣
• 3:贵重及收的率不稳定的合金元素尽量在LF炉
配,例如:Nb、V、Ni、Ti、Al、B等
• 4:缺点:增碳、增硅、回磷、增氮
电极准备 设备准备 通电准备 冷却水准备 合金及辅料准备 液压准备
测温取样 供电操作 造渣操作 吹氩操作 合金调整 温度调整
120T精炼炉设备功能
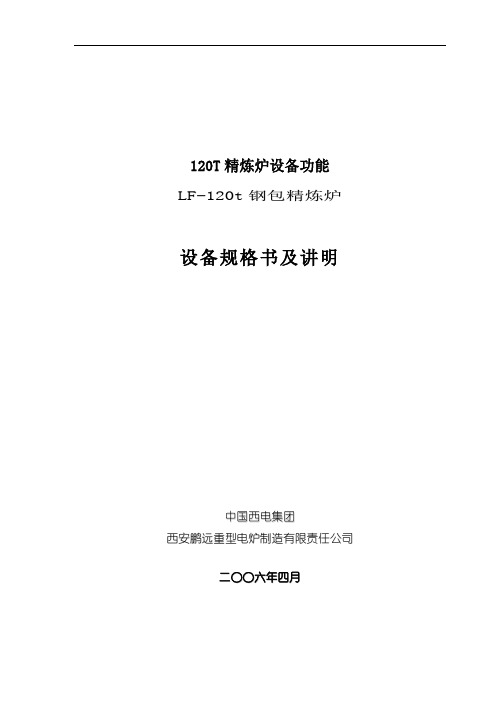
120T精炼炉设备功能L F-120t钢包精炼炉设备规格书及讲明中国西电集团西安鹏远重型电炉制造有限责任公司二○○六年四月目录1.1 钢包车及拖缆装置1.2 电极升降机构(电极横臂及升降机构)1.3 电极旋转机构1.4 水冷炉盖及集烟除尘装置1.5 炉盖顶升机构及机架1.6 液压系统1.7 集中润滑系统1.8 水冷系统1.9 压缩空气系统1.10 电极存放及连接装置1.11 喂丝机及导管(双线喂丝)1.12 氩气搅拌系统1.13 合金加料系统1.14 短网系统1.15 精炼炉变压器1.16 电气及自动化系统1.17 除尘管道1.1钢包车及拖缆装置钢包车是使钢包即达各个工位的运送工具。
车体为优质钢板焊接结构,传动方式为机械传动,即为电动机+减速器+联轴器+车轮组成。
车体上设有轨道清理装置。
在轨道两端有止动装置及钢包车一端装有缓冲装置。
在事故状态下,可通过车体上的挂钩将钢包车拖出。
车体设置声光报警并加防护板。
拖缆装置是向钢包车提供动力、氩气等的装置,拖缆的一端固定在地面上,另一端固定在车体上,随钢包车一同运行。
如此可保证钢包全程吹氩,拖缆胶管采纳棉布捆扎,防止钢液或渣飞溅烧损胶管。
钢包车的要紧组成车梁2件×4小横梁(带事故挂钩) 2件×4支撑梁2件×4主动轮2件×4从动轮2件×4电动机1台×4减速机1台×4联轴器1套×4轨道清理装置4套×4传动支架2套×4限位装置1套×4缓冲装置 1套×4拖缆装置的要紧组成固定滑车1套×4移动滑车7套×4支架1套×4钢丝绳装配1套×4拖缆装配1套×4引线支架1套×4要紧技术参数钢包车运行速度2~20m/min钢包车驱动方式机械式、变频调速钢包车定位精度±10mm钢包车承载能力200t1.2电极升降机构(电极横臂及升降机构)电极升降机构的功能是对钢水加热,补偿因转炉出钢,钢包衬吸热,钢包吊到加热工位时钢水的温降、补偿合金化、造渣、吹氩等造成的钢水温降及提高钢水温度,达到连铸要求的钢水温度。
120吨转炉工艺技术操作规程

3.9、供氧:零位按+100mi控制,根据化渣情况合理调整枪位。
1、按分阶段定量装入
炉龄(次)
1〜5
6〜
铁水
炉容比
V/T1
0.905
炉口直径
d0
mm
2618
溶池直径
d1
mm
4774—
溶池深度
h1
mm
1300
出钢口直径
d2
mm
160
炉底总厚度
mm
720
炉底直径
mm
4190
炉衬总厚度
mm
炉底:970+70大面处:740+115出钢面:640+70
氧枪参数:
长度21.9m
直径:①273,①168
工作压力:0.75-1.0 MPa
出钢温度:1700—1780C;
3.5、开新炉补SiFe量:按含[Si]1.0%配加
1.0—铁水含[Si]%
SiFe量=X铁水量+(1300-1)x4(Kg)
SiFe含Si%
t:铁水实际温度 一般情况下:(仅供参考)
铁水含[Si]%
0.3
O.4
O.5
O.6
0.7
0.8
SiFe配加量Kg
950
800
700
T100 300 600 800 1300 1300 1300C
⑤开吹5000NrVh,逐渐增加到8000NrVh左右流量吹氧,按对比温差,增减氧气流量,
150分钟结束。
2.4、烘炉后炉况检查:
2.4.1、烘炉结束,提起氧枪至最高位;
2.4.2、抽出测温热电偶;
120tLF-钢包精炼炉001要点
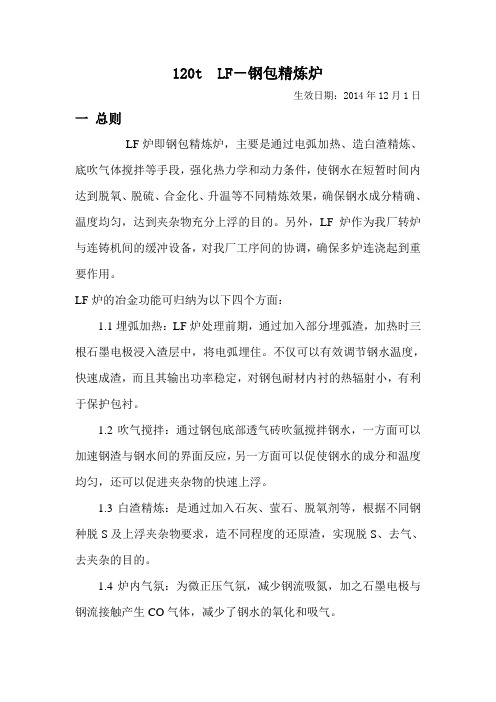
120t LF-钢包精炼炉生效日期:2014年12月1日一总则LF炉即钢包精炼炉,主要是通过电弧加热、造白渣精炼、底吹气体搅拌等手段,强化热力学和动力条件,使钢水在短暂时间内达到脱氧、脱硫、合金化、升温等不同精炼效果,确保钢水成分精确、温度均匀,达到夹杂物充分上浮的目的。
另外,LF炉作为我厂转炉与连铸机间的缓冲设备,对我厂工序间的协调,确保多炉连浇起到重要作用。
LF炉的冶金功能可归纳为以下四个方面:1.1埋弧加热:LF炉处理前期,通过加入部分埋弧渣,加热时三根石墨电极浸入渣层中,将电弧埋住。
不仅可以有效调节钢水温度,快速成渣,而且其输出功率稳定,对钢包耐材内衬的热辐射小,有利于保护包衬。
1.2吹气搅拌:通过钢包底部透气砖吹氩搅拌钢水,一方面可以加速钢渣与钢水间的界面反应,另一方面可以促使钢水的成分和温度均匀,还可以促进夹杂物的快速上浮。
1.3白渣精炼:是通过加入石灰、萤石、脱氧剂等,根据不同钢种脱S及上浮夹杂物要求,造不同程度的还原渣,实现脱S、去气、去夹杂的目的。
1.4炉内气氛:为微正压气氛,减少钢流吸氮,加之石墨电极与钢流接触产生CO气体,减少了钢水的氧化和吸气。
二钢包精炼炉技术参数:2.1 钢包精炼炉主要设备参数序号参数名称单位参数备注1 钢包公称容量t 120净空高度mm ≥4002钢包回转台定位精度mm ±0.1/10行走速度rpm 0-1.0 变频可调最大载重量t 2503 加热装置电极直径mm Φ450 高功率电极电极分布圆直径mm Φ780电极最大行程mm 2500电极升降速度m/min 4.5/3(6/4.5) 自动/手动4 钢水升温速率℃/min ≥5.05 变压器额定容量MVA 25一次电压KV 35二次电压V397~367~27711级(前5档恒功率,后6档恒电流)二次电流KA ~39.33冷却方式强迫油循环水冷调压方式有载调压6 短网阻抗阻抗mΩ≤2.6三相不平衡系数% ≤47 液压系统工作压力MPa 12工作介质水~乙二醇电极升降调节电液-比例电极调节响应时间ms ≤3008 氩气系统供气压力MPa 1.2工作压力MPa 0.55~1.0最大耗量 L/min 850×1.39冷却水系统进水/回水压力MPa0.4~0.6/0.2~0.3进水温度℃ ≤32 回水温度 ℃ ≤55 冷却水耗量 m 3/h 420 10炉盖有效提升高度 mm ≥650 提升方法液压缸 密封裙边高度 mm ~200 烟气补捉率 % ≥90 11加料装置料仓数量个 10容积 m 36×8+4×16三 精炼工位操作处理流程:四 钢包精炼炉原材料技术要求:钢包在吊座包工位测温、取样、定氧、喂Al 线喂丝位 设备操作、测温取样、渣料加入、吹氩搅拌、供电操作、白渣操作、吹氩操作、合金成分微调、测温取样、温度调整、待成分合适后提升炉盖,回转台转离精炼位处理位检查钢包 电极准备 设备确认 渣料准备 (接手动吹氩管操作) 开底吹氩阀门,接手动,底吹正常后转动回转台铝线调整、钙处理、测温、取样、软吹操作等,待所有精炼任务结束后将回转台转到吊包位,关闭底吹氩,加覆盖剂等候吊包喂丝位 开至吊座包工位、吊包出站(拔掉底吹氩管)4.1 造渣材料钢包精炼炉造渣主要使用活性石灰、萤石及(精炼渣)。
某钢公司120吨 LF钢包精炼炉短网及电气控制简介

某钢公司120吨 LF钢包精炼炉短网及电气控制简介作者:李涛马胜武来源:《科学与财富》2017年第26期摘要:LF(Ladle Furnace)炉是70年代初期在日本发展起来的精炼设备。
由于它设备简单,投资费用低,操作灵活和精炼效果好而成为冶金行业的后起之秀,在日本得到了广泛的应用与发展。
LF炉所处理的钢种几乎涉及从特钢到普钢的所有钢种,生产中可视质量控制的需要,采用不同的工艺操作制度。
在各种二次精炼设备中,LF炉的综合性价比高。
精炼炉作为一个复杂的冶炼系统,炉内温度受各种因素的影响。
从初炼炉(如EAF、BOF)出钢开始,出钢过程中的能量损失,受到钢包物理参数影响。
运输时间的长短,吹氩量的多少也影响钢水温度。
合金料,循环冷却水,烟气烟尘,电极,变压器等构成了整个精炼炉温度模型的基础。
关键词:短网;变压器;PLC;精炼炉一、LF钢包精炼炉主要功能1、电弧加热升温2、钢水成分微调3、脱硫、脱氧、去气、去除夹杂4、均匀钢水成分和温度5、改变夹杂物的形态6、作为转炉、连铸的缓冲设备,保证转炉、连铸匹配生产。
二、某钢精炼炉作业工序流程钢包吊至钢包车上→连接吹氩管、试气→钢包车开至加热工位→炉盖和电极下落到位→测温取样确定加热制度及成分微调→加渣料及合金料→送电加热精炼→测温取样→炉盖、电极升起→钢包车开出加热工位→喂丝→加保温剂→软吹氩及气洗→断开吹氩管及吊出钢包三、短网从变压器二次端头到电极的二次母线设备总称短网。
短网的电参数对精炼炉的正常运行起作决定性的作用,精炼炉的生产率、炉衬寿命、功率损耗及功率因数等在很大程度上都取决于短网的电参数的选择。
某钢精炼炉短网主要由水冷补偿器、水冷电缆、导电横臂、电极、电极夹持器等部件组成。
短网具有以下特点:1)电流大.2)长度短。
3)结构复杂。
4)工作环境恶劣。
四、电气及自动化控制1.高压电控系统用于精炼炉变压器一次侧电源合闸和分断,充分考虑对高次谐波的抑制及各种过电压对炉变绝缘及高压元件的影响。
120t区域精炼工艺3-16

2019年11月22日
3
4.喷吹 喷吹也称喷射,是将反应剂利用气流直接加入冶金 熔体中的一种炉外精炼方法。由于它简便、高效, 所以也经常作为一种精炼手段,组合到其他炉外精 炼方法中。
喷吹技术利用气体的搅拌作用增加了粉状精炼剂和 钢液的接触界面,显著改善冶金反应的动力学条件。 因此可以实现快速脱硫、脱磷、脱氧,提高合金收 得率,促使夹杂物变性等功能。 RH配备喷吹功能,可以进行深脱硫,生产超低硫钢。
2019年11月22日
19
一般情况下,脱氧结束后Mn/Si要>3,保证 生成的硅化物在钢水中以液态存在。
脱氧产物应有效的从熔池中上浮并被精炼渣 所吸附。 自由氧含量比全氧含量更易降低。 精炼渣的特性能满足脱氧的要求。
2019年11月22日
20
•对于全氧来说,其去除速度主要取决于夹杂物的上浮速度和渣的吸 附能力。
2019年11月22日
16
适当的Al2O3含量:在渣中的Al2O3含量低于30% 时,增加其含量,可以增加渣的流动性,改善动力 学条件,但是Al2O3含量过高,不利于夹杂物的吸附。
低氧势:(FeO+MnO+Cr2O3)含量一般应控制在 2.0%以下,以保证脱氧、脱硫效果。
CaF2:萤石有利于化渣,但是对包衬的侵蚀严重, 因此应尽量减少其用量。
一、炉外精炼采用的手段及其功能
1.渣洗 渣洗是能适量脱硫、脱氧、去夹杂、提高钢水纯净度的最
简便的精炼手段。早在二十世纪30年代就已开始应用。 渣洗工艺有一定的缺陷,如不能去除钢中气体,甚至可能
增氮和造成二次氧化。为增强钢渣反应界面,应使钢、渣 尽可能混匀、乳化,而为使乳化的合成渣尽可能上浮,又 需要足够的镇静时间。另外,渣洗效果精炼渣的性能影响 非常大。
120吨钢包精炼炉工艺技术操作规程

中天钢铁集团第五炼钢厂中天钢铁集团有限公司120吨LF精炼炉工艺技术操作规程编制:苏旺张文惠宋晓东审核:陈军召万文华徐和平批准:吴献阳编号:生效日期:2010 年12月 1日受控印章:分发号:版本号:1.0 120吨LF精炼炉工艺技术操作规程目录第一部分钢包精炼工艺技术规程1.精炼工艺流程 (1)2.LF主要技术及设备参数 (2)3.LF处理功能及处理钢水类型 (7)4.LF处理前提条件 (8)5.LF工艺路线钢种及目标化学成分 (8)6.LF钢包炉测渣厚标准 (10)7.氩气介质标准 (10)8.钢包吹氩处理标准 (11)9.加热标准 (11)10.测温、取样、定氧标准 (14)11.造渣标准 (15)12.发泡剂加入标准 (15)13.成分微调标准 (16)14.喂丝处理标准 (17)15.钢水保温处理标准 (19)16.LF回余钢水处理标准 (19)17.LF处理工艺路线钢种温度标准 (20)18.电极更换标准 (20)19.加保温剂标准 (20)第二部分钢包精炼工艺操作规程1.操作前的检查与准备 (22)2.检查水冷炉盖有无漏水,炉盖上电极孔陶瓷环能否正常使用 (22)3.测温、取样操作 (23)4.送电加热 (23)5.造渣合金化 (24)6.LF处理结束 (25)7.喂丝操作 (25)8.接、滑电极操作 (26)9.异常情况处理 (27)10.记录 (28)第一部分 钢包精炼工艺技术规程1. 精炼工艺流程1.1 经LF 炉处理的钢水图1 经LF 炉处理的钢水工艺流程图1.2 保温处理的钢水图2 保温处理的钢水工艺流程图注:a) 定氧根据钢种生产技术操作标准要求进行。
b) 对Als 有要求的钢种在钢水到站后喂入铝线。
c) 喂入包芯线根据钢种生产技术操作标准进行。
2.LF主要技术及设备参数表1 LF主要技术及设备参数2.1主要技术参数电极电流密度(国产电极):27A/cm2电极最大电流:45KALF变压器功率(连续负载):26MV A电耗:0.46KWh/t℃LF炉气稀释后的烟气温度:130℃稀释后的烟气流量:60000Nm3/h颗粒度:<2μm:50%;<0.5μm:10%烟尘量:1~2kg/t稀释后烟气平均含尘量:10g/Nm3烟尘成分:主要为CaO,带有部分金属氧化物炉气成分:空气+2%CO22.2主要设备参数2.2.1料仓数量10个容积:12m3×2+4m3×82.2.2称量料斗数量:3个容积: 1.5m32.2.3钢包车车轮数量:4个运行距离:南车/北车15.5m/16.5m钢包车长度: 6.6m钢包车宽度: 4.9m钢包车高度: 2.22m轨距: 4.2m马达数量/功率(每台):2台/22KW2.2.4变压器型号HSSPZ-25000/35型式箱盖式运行方式额定容量时连续运行,超载20%时,连续运行2h额定容量25000kV A+20%一次额定电压35kV 50Hz二次电压395~190V 13级50Hz其中:395~345V为恒功率级;345~190V为恒电流级二次额定电流41837A联结组别YNd11阻抗电压8~10%端子出线方式侧出2.2.5电极提升立柱电极分布园直径Φ750mm电极升降最大行程~3000mm(可适当调整)电极升降速度自动上升/下降手动上升/下降6/4.8 m/min 6/4.8 m/min电极调节器性能参数电极响应时间启动时间≤0.15s制动时间≤0.10s非灵敏区5%~10% 2.2.6导电式电极臂电极夹持器直径:Φ750mm铜导电臂中电流密度:<5A/mm2电极夹持器液压缸数量:1个行程:52mm孔径:Φ230mm操作压力:11MPa2.2.7水冷炉盖估计耐材重量:1900kg炉盖外径:Φ4222mm炉盖高度(包括抽气管道):2197mm中心耐材盖下衬/上衬厚度:270/200mm电极孔直径:Φ520mm 观察孔汽缸数量:1个最大行程:220mm孔径:Φ222mm 取样门汽缸数量:1个最大行程:255mm孔径:Φ222mm水冷炉盖升降速度100mm/s水冷炉盖升降行程≥650mm水冷炉盖紧急提升响应时间<5s水冷炉盖升降型式液压升降2.2.8液压系统液压介质水-乙二醇系统工作压力12Mpa系统过滤精度10μ主泵电机容量3×30kW主泵电机转速1000r/min泵额定压力21MPa泵工作压力16 MPa泵流量100L/min循环泵电机容量1×3kW工作压力0.5 MPa流量59L/min冷却水进口压力0.6MPa冷却水进口温度<40℃冷却水出口温度50℃冷却水流量16m3/h蓄能器额定压力21 MPa蓄能器工作压力12 MPa油箱容积3000L2.2.9上料系统上料方式用10t桥吊吊运物料袋或钟式料罐料仓给料方式VVVF电机振动给料称量斗给料方式电机振动给料振动给料器给料能力80t/h称量斗精度≤0.3%加料精度1%加料时间2min皮带机带宽500mm皮带机带速 1.6m/s皮带机输送量80t/h散装料及铁合金料仓材质Q345B3.LF处理功能及处理钢水类型3.1LF钢包炉处理功能3.1.1钢水升温或钢水保温。
120t×3氧气转炉炼钢车间工艺设计(PPT)

d2
4 F2
(d 1外 ) 2
4 55.6
15.9 2 180 mm
根据标准热轧无缝钢管产品规格选取中层钢管为 203 6mm Q 120 F 0.00476 m 47 .6cm ⑶外层钢管管径 V出 7m / s V 7 3600
水 2 2 3 出
板 1 2
方 1 2
1 2 0 3 0 0
⑶连铸机的理论小时产量 Q 60 NBDV 式中 Q——连铸机理论小时产量,t/h; B——铸坯宽度,m; D——铸坯厚度,m; V——工作拉速,m/min; ——铸坯密度,t/m3,取=7.7; N——流数。
8760 1920 100 % 78 8760
式中 T1——每炉钢的平均冶炼时间,min,本设计40min。 T2——一年有效作业天数,d; 1440——一天的日历时间,min; 365——一年的日历天数,d; η——转炉的作业率,%。
5.3 年产钢量
在选定转炉公称容量和转炉工作制后,即可计算出车间 的年产钢水量
W nNq 2 10512 120 2522880
7.1氧枪喷头尺寸 120 ⑴计算氧流量Q 每吨钢耗氧量出钢量 60 18 400 吹氧时间 ⑵马赫数M=2.0 ⑶喷孔数取5孔 0.101 P 0.790 MPa ⑷ 设计工况氧压 0.1278 ⑸喉口直径 d 喉 36 1. ⑹喷孔出口直径 d 1.6875 dd 476875 36 47 mm d 36 L 90 mm ⑺喷孔扩张段长度 2 tan 2 tan 3.5 ⑻喷孔喉口直线段长度 L喉=5mm ⑼喷孔倾角β =15°
120t×3氧气转炉炼钢车间工艺设计
120t转炉热式第一炉
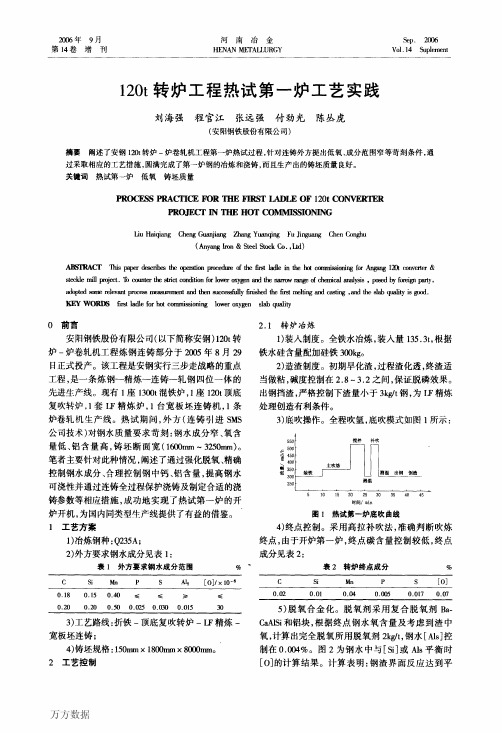
r娜删range steckle mill project.To counter the strict condition for lower oxygen and the
of chemical analysis,posed by foreign party,
adopted眺relevant the.slab删哆is process m嘲【sL田mH吐and then吼砌∞胬6IⅡy finished the first melting and casting,and
2)IF精炼脱氧。"精炼采用强化快速脱氧方 式,利用电石、硅钙粉脱氧,并利用炉渣改质、控制精 炼渣成分和流动性等精炼手段,使渣中氧化铁和氧 化锰含量控在0.8%以下,抑制炉渣含氧向钢水传 递。渣中较高的她03可有效捕获钢中脱氧产物, 从而达到强化快速脱氧的目的。
3)LF精炼脱硫。影响精炼脱硫两个重要参数 为碱度和不稳定氧化物,碱度越高,不稳定性氧化物 越少,脱硫效果越好。由精炼渣成分可知:R=(CaO 十MgO)/(A1203+Si02)=2.0,FeO含量小于0.8%,S 含量控制为0.007%。
有新的变化,2CaO·Si02—3CaO·№03,CaO·Fe203和 少量石灰粉减弱炉渣的反应能力;缩短了钢液在钢
2CaO·Fez03成分多,则渣中№03含量高,炉渣不易
粘稠,钢、渣界面面积大反应迅速,将进一步脱磷,当
包中的停留时间;在操作上严格控制出钢温度,避免
碳高、温度高造成磷高;出钢时采用CaO—c巩一
sooa.
KEY WORDS first ladle for hot cortmfissioning lower oxygen slab quality
0前言
2.1转炉冶炼
RH炉真空精炼技术操作规程

炼钢厂安全技术操作规程汇总第四部分RH炉真空精炼技术操作规程目录前言: (4)1.RH真空处理的工艺流程 (5)2. RH真空处理模式、周期 (6)3.各种能源介质的参数 (7)4.RH钢水真空处理 (8)4.1处理前的准备工作 (8)4.2开始处理 (9)4.3提升气体 (9)4.4真空泵的操作 (9)4.5合金化 (10)4.6温度控制 (11)4.7测温取样 (12)4.8处理结束 (12)5.检漏操作标准 (13)6. RH浸渍管的喷补 (14)7. RH真空室的更换 (16)7.1准备 (16)7.2操作 (16)8. RH各部位耐材干燥烘烤加热 (17)8.1要求 (17)8.2真空室在线天然气加热操作 (17)8.3真空室升温制度 (17)8.4底部烘烤制度 (17)8.5插入管烘烤制度 (18)9. RH各部位使用更换及修理 (19)9.1插入管更换 (19)9.2 底部更换 (20)10. RH内衬砌筑标准 (21)10.1 砌筑基本要求 (21)10.2插入管砌筑与浇注 (22)10.3循环管砌筑 (22)10.4炉底与下部槽砌筑................................................................ - 22 -10.5上部槽砌筑 (23)11.验收标准 (25)11.1新插入管验收标准 (25)11.2新底部验收标准 (25)11.3新上部验收标准 (25)12.紧急事故处理对策 (26)12.1处理中液压升降不能动作 (27)12.2真空处理中钢包穿包 (27)12.3真空处理中突然穿真空槽.................................................... - 27 -12.4真空处理中突然停电 (27)12.5真空处理中突然停机械冷却水............................................ - 28 -12.6真空处理中突然停冷凝水或蒸汽........................................ - 28 -12.7真空处理中突然停仪表压缩空气........................................ - 28 -12.8氧枪使用过程中或提枪后发现漏水处理办法 ................... - 29 - 12.9氧枪使用中断链条或驱动失灵------------------------------------- 29 -附录炼钢厂安全技术操作规程汇总总目录第一部分. 铁水KR脱硫技术操作规程第二部分.转炉炼钢技术操作规程第三部分.LF炉炼钢技术操作规程第四部分.RH炉真空精炼技术操作规程第五部分.一号连铸机技术操作规程第六部分.二号连铸机技术操作规程前言:本RH炉主要功能有:1)、脱气(氢、氮)处理及去除钢中夹杂物;2)、轻处理碳脱氧;3)微调钢水成份;4)自然脱碳、强制脱碳;5)加铝吹氧升温,进行钢水温度调整。
- 1、下载文档前请自行甄别文档内容的完整性,平台不提供额外的编辑、内容补充、找答案等附加服务。
- 2、"仅部分预览"的文档,不可在线预览部分如存在完整性等问题,可反馈申请退款(可完整预览的文档不适用该条件!)。
- 3、如文档侵犯您的权益,请联系客服反馈,我们会尽快为您处理(人工客服工作时间:9:00-18:30)。
2018年10月12日
22
5.吹氩搅拌工艺
均匀成分 均匀温度 扩散脱氧 脱硫 夹杂物去除
2018年10月12日
23
吸气
LF处理过程中的吸气主要由于气体分子在电弧的 高温作用下,产生气体分子电离,同时在高温区 域气体的溶解度增加,易造成吸气。 由于在搅拌过程中造成钢水液面裸露,发生吸气 以及二次氧化现象。 处理时间越长,吸气越严重。 应保证埋弧加热,减少吸气量。
2018年10月12日
17
加热工艺对精炼渣的要求
要求高碱度精炼渣。高碱度精炼渣的导电性能良好,电弧 稳定,一般要求碱度≥2。 确保埋弧加热,提高热电效率。 控制适当的渣层厚度,渣层过薄,无法保证埋弧加热,能 耗增加,同时对钢包内衬的侵蚀加剧;渣层过厚,用于渣 料消耗的能耗增加,同时由于电极被渣层包覆,电极区域 的温度过程,将会发生如下反应: CaO+3C→CaC2+CO 从而使电极消耗增加。一般情况下,控制渣层厚度为电弧 长度的2倍左右为宜。
2018年10月12日
20
•对于全氧来说,其去除速度主要取决于夹杂物的上浮速度和渣的吸 附能力。 1.搅拌时通过钢液的流动,促进夹杂物的碰撞、聚合,直径增大,利 于上浮; 2.在搅拌条件下,夹杂物与乳化渣碰撞,被渣滴吸附,随渣滴上浮排 除。由于吸附夹杂,渣滴本身也长大,上浮速度加快; 3.气体搅拌时,夹杂物吸附在气泡上,随气泡上升并排除。 4.由于Al2O3比硅化合物更容易通过碰撞、聚合长大,因此更易去除。
2018年10月12日
18
3.LF脱氧
沉淀脱氧 Al+O→Al2O3 扩散脱氧 Al+O2- →Al2O3 Al2O3+CaO→(CaO)x(Al2O3)y
2018年10月12日
19
一般情况下,脱氧结束后Mn/Si要>3,保证 生成的硅化物在钢水中以液态存在。 脱氧产物应有效的从熔池中上浮并被精炼渣 所吸附。 自由氧含量比全氧含量更易降低。 精炼渣的特性能满足脱氧的要求。
27
2018年10月12日
VD炉主要设备
VD炉主要设备有:真空罐、真空系统、真 空罐盖车、底吹系统、加料系统等。
2018年10月12日
28
VD的作用
均匀钢水温度和钢水成分。 真空脱气。 协调转炉连铸生产节奏。 钢水深脱氧、脱硫。 去除钢水中夹杂。 夹杂物变性处理。 成分微调。
12
2018年10月12日
LF精炼工艺
1.温度控制工艺 1.1埋弧加热:减少吸氮;提高加热效率。 1.2加热终了温度确定:TLF终了=T中+ΔT1+ΔT2 TLF终了-最后一次加热结束后的钢包钢水温度。 T中-中间包标准温度。 ΔT1-过程温降。 ΔT2-补偿温度。
2018年10月12日
13
2.还原渣精炼工艺
2018年10月12日
3
4.喷吹 喷吹也称喷射,是将反应剂利用气流直接加入冶金 熔体中的一种炉外精炼方法。由于它简便、高效, 所以也经常作为一种精炼手段,组合到其他炉外精 炼方法中。 喷吹技术利用气体的搅拌作用增加了粉状精炼剂和 钢液的接触界面,显著改善冶金反应的动力学条件。 因此可以实现快速脱硫、脱磷、脱氧,提高合金收 得率,促使夹杂物变性等功能。 RH配备喷吹功能,可以进行深脱硫,生产超低硫钢。
2018年10月12日
1
2.搅拌 搅拌是绝大部分炉外精炼方法都采用的基本手段。 冶金反应的速率与钢液被搅动的程度有关,因为搅拌可以扩大反应界面, 加快传质,改善动力学条件,从而提高钢—渣—气的反应速度。炉外精 炼方法,除了要创造最佳的热力学条件外,还必须提供最佳的动力学条 件,因此搅拌几乎成为各种炉外精炼的必选。 搅拌作为一种炉外精炼手段,搅拌强度、持续时间应当可以按精炼要求 控制。 较早出现的搅拌方法,是利用钢液本身的位能,依靠钢液的冲击,促使 钢水搅动。 真空碳氧反应产生的CO气泡产生熔池搅拌,但搅拌强度较弱,持续的时 间也不可能太长,精确控制也比较困难。 RH、DH等方法利用压差造成部分钢水位能差异,利用钢液回流搅动熔 池,是一种简便可行的办法。 单纯的搅拌可以均匀成分、温度,促进夹杂物聚合、上浮。
2018年10月12日
31
真空状态下,脱氢效果与以下因素有关: ☆初始含量:初始含量越低,达到最终含量的处理时间越短。 钢液中初始含量并不取决于大气中的氢分压,钢液中〔H〕 主要是空气中水蒸气和原材料中水分带入的。 ☆处理时间:处理时间越长,最终〔H〕含量越低,但是当 〔H〕含量降低到一定程度,随着处理时间的延长,最终 〔H〕含量变化不大。因为此时钢水静压力和传质速度是其 限制环节。 ☆真空度:真空度提高,气相中氢分压降低,有利于脱氢反 应。 ☆吹氩搅拌:通过吹氩搅拌,相应增加了气液反应界面;提 高了熔池内传质速度;氩气泡上浮时,溶解在钢中的〔H〕 会以原子的形式进入氩气泡,氩气泡相当于一个个微小的真 空室。 ☆表面活性元素:〔O〕、〔S〕等表面活性元素含量的降 低,有利于〔H〕原子通过气液界面。
2018年10月12日
24
三、VD工艺
2018年10月12日
25
VD工艺流程
钢水到站 吹氩 பைடு நூலகம்温、定氧、定氢 抽真空
保真空
破真空
测温、取样、定氧、定氢
喂线
吹氩结束
加保温剂
出站
2018年10月12日
26
VD主要技术参数
真空泵抽真空能力:370kg/h(67Pa) 抽真空时间(无预排空条件下):≤5min 工作真空度:67Pa 极限真空度:26.7Pa VD蒸汽消耗:12.1t/h 蒸汽温度:≥190℃ 蒸汽锅炉能力:19t/h 破真空时间:2min
5.在精炼处理过程中,钢水被渣中的FeO、MnO以及大气中的氧二次 氧化。
2018年10月12日
21
4.Ca处理
对于Al脱氧镇静钢,钢中夹杂物主要是固态Al2O3夹杂物,熔点高,
不易去除。通过向钢液中加入钙合金或高CaO渣料,将钢中固态的 Al2O3转变为液态的铝酸钙球形夹杂,易于从钢液中排除。残余的夹 杂物对钢材性能的影响也比固态Al2O3小。同时,含CaO很高的夹杂 物中S的平衡浓度很高,可以吸附大量的S,当其温度降低时,CaS 析出,生成复合夹杂物,该夹杂物为球形,熔点高,轧制时状态不 变形。 Ca处理必须在精炼处理结束后进行。 喂入Ca线的速度要适当。喂线速度受钢水温度、钢带厚度、熔池深 度等方面的影响,同时应考虑钢带表面钢水冷凝层厚度的影响。 控制生成低熔点的铝酸钙夹杂。 为了避免生产大量的CaS,应控制钢中的S含量。 喂入CaSi线后,将会还原Si、Mn等元素。
2018年10月12日
4
5.喂线 喂线是通过喂线机将钙、铝、硅钙、钡系合金等制成的包芯 线或铝等金属线高速加入到钢液的方法。具有如下特点: ·合金收得率高; ·能解决特种合金的加入问题; ·避免合金加入时的吸氮; ·投资费用少,应用范围广,操作简便。 喂线技术可单独应用。也可应用到各种精炼方法中。目前各 种炉外精炼方法中都添加了喂线设施,并且以推广到中间包 喂线、结晶器喂线。 采用不同的包芯线、金属线,喂线技术可具有脱氧、脱硫、 夹杂物变性、防止水口堵塞等功能。
2018年10月12日
5
6.升温 加热是调节钢液温度的一项常用手段。 炉外精炼设备大多配备加热手段。 采用电弧加热的方法有LF等炉外精炼方 法,有些DH、RH的真空室内也设有电 阻加热。还采用化学热法升温,即利用 加铝(或碳、硅)吹氧氧化的化学热, 使钢液升温,如CAS—OB、RH—OB、 VOD等。
2018年10月12日
14
精炼渣的要求:
合适的成分 低的熔化温度 低氧势 合适的粘度 高碱度 适当的渣量
2018年10月12日
15
要取得良好的精炼效果,控制好精炼渣的成分至关重要。 对于LF处理来说,主要要控制以下几个方面: 适当的高碱度:高碱度渣有利于脱氧、脱硫和吸附夹杂, 但是随着碱度的增加,渣的流动性降低 ,降低了精炼反应的 动力学条件。同时,由于高碱度的精炼渣会形成点状夹杂, 对轴承钢等钢种产生较大的影响,因此应根据实际需要控制 适当的碱度。 低SiO2含量:SiO2含量的增加,势必增加石灰的加入量, 造成消耗的增加和处理时间的延长,同时SiO2含量过高时, 在高温和低氧势的精炼处理过程中,易发生Si的还原,最终 影响成分的精确控制或造成成分出格。
2018年10月12日 6
二、LF精炼工艺
2018年10月12日
7
LF工艺流程
1.只经LF处理的钢水
到等待位
吹氩
到处理位
测温、取样、定氧
加渣料
预加热及补加渣料
合金微调
主加热
测温、取样、定氧
喂线
吹氩结束
加保温剂
钢水出站
2018年10月12日
8
2.经LF/VD(RH)处理的钢水
到等待位
吹氩
到处理位
10
2018年10月12日
LF炉主要设备
LF设备主要包括:加热电源、炉盖、电极 及控制装置、钢包车、钢包、除尘系统、 底吹搅拌装置、加料系统。
2018年10月12日
11
LF的作用
提高生产能力 降低出钢温度 提高合金收得率 均匀钢水的成分和温度 精确控制钢水的成分和温度 协调炉机节奏 钢水的脱硫和脱氧 去除钢中的夹杂物以及夹杂物的变性处理
测温、取样、定氧
加渣料
预加热及补加渣料
合金微调
主加热
测温、取样、定氧
吹氩结束
钢水出站
2018年10月12日
9
LF主要技术参数
公称容量:120t 最大钢水处理量:150t 最小钢水处理量:100t 电极电流密度(国产电极):27A/cm2 电极直径:450mm 电极最大电流:45KA LF变压器功率(连续负载):26MVA 最大升温速度:5℃/min