汽车非承载式车身车架纵梁设计规范
《车辆产品系族划分原则及技术要求》
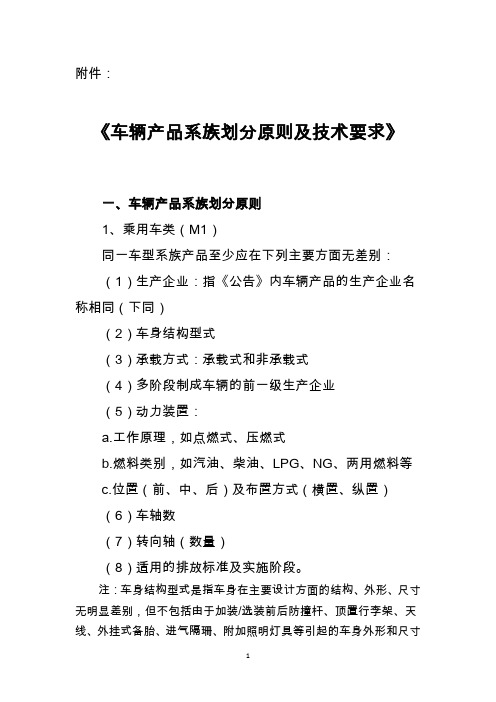
附件:《车辆产品系族划分原则及技术要求》一、车辆产品系族划分原则1、乘用车类(M1)同一车型系族产品至少应在下列主要方面无差别:(1)生产企业:指《公告》内车辆产品的生产企业名称相同(下同)(2)车身结构型式(3)承载方式:承载式和非承载式(4)多阶段制成车辆的前一级生产企业(5)动力装置:a.工作原理,如点燃式、压燃式b.燃料类别,如汽油、柴油、LPG、NG、两用燃料等c.位置(前、中、后)及布置方式(横置、纵置)(6)车轴数(7)转向轴(数量)(8)适用的排放标准及实施阶段。
注:车身结构型式是指车身在主要设计方面的结构、外形、尺寸无明显差别,但不包括由于加装/选装前后防撞杆、顶置行李架、天线、外挂式备胎、进气隔珊、附加照明灯具等引起的车身外形和尺寸变化;对于轿车,至少B柱之前车身结构相同。
2、客车类(M2、M3)同一系族产品至少应在下列主要方面无差别:(1)生产企业(2)多阶段制造车辆的前一级生产企业(3)产品用途分类(客车、城市客车)(4)GB/T 15089-2001《机动车辆及挂车的分类》定义的级别(A级、B级、I级、II级、III级)(5)车身/底盘:承载式车身主要结构相同;非承载式车身,底盘基本构成部件的设计和构造相同a.承载方式,如:承载式、非承载式等b.结构形式,单层/双层,低地板,整体式/铰接式c.车身型式,骨架车身与冲压车身等(6)动力装置:a.工作原理,如点燃式、压燃式b.燃料类别,如汽油、柴油、LPG、NG、两用燃料等c.位置(前、中、后)及布置方式(横置、纵置)(7)车轴数(8)驱动轴(数量、位置、连接)(9)转向轴(数量、位置)(10)适用的排放标准及实施阶段。
3、货车及底盘(非整体式)(N1、N2、N3 )同一系族产品至少应在下列主要方面无差别:(1)生产企业(2)多阶段制成车辆的前一级生产企业(3)GB/T 15089-2001《机动车辆及挂车的分类》定义的类别(N1、N2、N3)(4)车身/底盘:承载式车身主要结构相同;非承载式车身,底盘基本构成部件的设计和构造相同。
《车辆产品系族划分原则及技术要求》
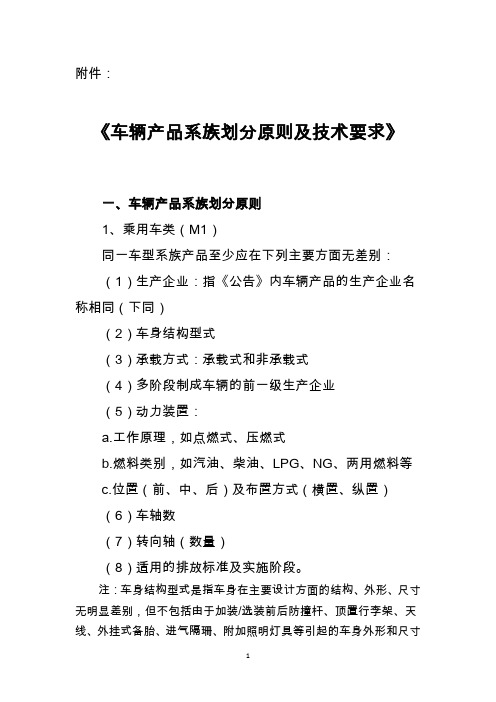
附件:《车辆产品系族划分原则及技术要求》一、车辆产品系族划分原则1、乘用车类(M1)同一车型系族产品至少应在下列主要方面无差别:(1)生产企业:指《公告》内车辆产品的生产企业名称相同(下同)(2)车身结构型式(3)承载方式:承载式和非承载式(4)多阶段制成车辆的前一级生产企业(5)动力装置:a.工作原理,如点燃式、压燃式b.燃料类别,如汽油、柴油、LPG、NG、两用燃料等c.位置(前、中、后)及布置方式(横置、纵置)(6)车轴数(7)转向轴(数量)(8)适用的排放标准及实施阶段。
注:车身结构型式是指车身在主要设计方面的结构、外形、尺寸无明显差别,但不包括由于加装/选装前后防撞杆、顶置行李架、天线、外挂式备胎、进气隔珊、附加照明灯具等引起的车身外形和尺寸变化;对于轿车,至少B柱之前车身结构相同。
2、客车类(M2、M3)同一系族产品至少应在下列主要方面无差别:(1)生产企业(2)多阶段制造车辆的前一级生产企业(3)产品用途分类(客车、城市客车)(4)GB/T 15089-2001《机动车辆及挂车的分类》定义的级别(A级、B级、I级、II级、III级)(5)车身/底盘:承载式车身主要结构相同;非承载式车身,底盘基本构成部件的设计和构造相同a.承载方式,如:承载式、非承载式等b.结构形式,单层/双层,低地板,整体式/铰接式c.车身型式,骨架车身与冲压车身等(6)动力装置:a.工作原理,如点燃式、压燃式b.燃料类别,如汽油、柴油、LPG、NG、两用燃料等c.位置(前、中、后)及布置方式(横置、纵置)(7)车轴数(8)驱动轴(数量、位置、连接)(9)转向轴(数量、位置)(10)适用的排放标准及实施阶段。
3、货车及底盘(非整体式)(N1、N2、N3 )同一系族产品至少应在下列主要方面无差别:(1)生产企业(2)多阶段制成车辆的前一级生产企业(3)GB/T 15089-2001《机动车辆及挂车的分类》定义的类别(N1、N2、N3)(4)车身/底盘:承载式车身主要结构相同;非承载式车身,底盘基本构成部件的设计和构造相同。
车架纵梁说明书
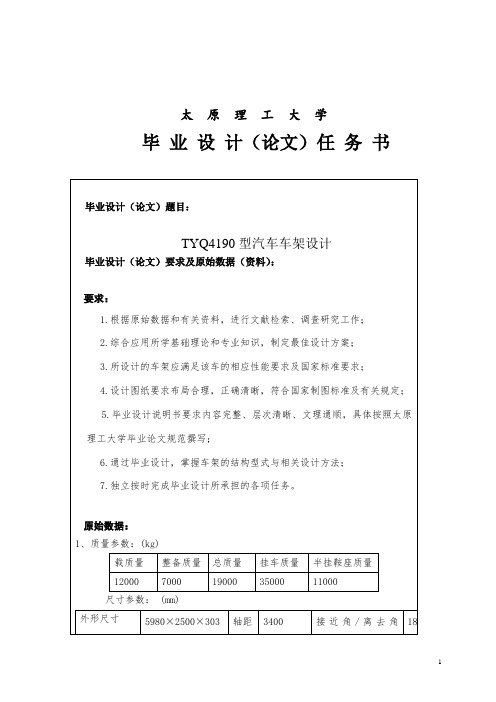
太原理工大学毕业设计(论文)任务书毕业设计(论文)题目:TYQ4190型汽车车架设计毕业设计(论文)要求及原始数据(资料):要求:1.根据原始数据和有关资料,进行文献检索、调查研究工作;2.综合应用所学基础理论和专业知识,制定最佳设计方案;3.所设计的车架应满足该车的相应性能要求及国家标准要求;4.设计图纸要求布局合理,正确清晰,符合国家制图标准及有关规定;5.毕业设计说明书要求内容完整、层次清晰、文理通顺,具体按照太原理工大学毕业论文规范撰写;6.通过毕业设计,掌握车架的结构型式与相关设计方法;7.独立按时完成毕业设计所承担的各项任务。
原始数据:1、质量参数:(kg)载质量整备质量总质量挂车质量半挂鞍座质量12000 7000 19000 35000 11000尺寸参数: (mm)外形尺寸5980×2500×303轴距3400 接近角/离去角18/30 (度) 2车箱内部尺寸轮距2027/182最小离地间隙2402、其它参数:1)、最高车速:98km/h2)、最大爬坡度(%): 303)、车轮及轮胎:12.00R204)、轴数:2毕业设计(论文)主要内容:1 本设计的目的及意义2 车架结构方案的选择与设计3 车架总成设计、保险杠总成设计4 车架总成的有限元分析5 其它零件设计6 详细撰写毕业设计说明书学生应交出的设计文件(论文):1.车架及相关零部件图纸一套;2.毕业设计说明书。
(按太原理工大学学生毕业论文撰写规范写)3.翻译与课题相关的外文资料1~2篇4.模拟专利申请书1份5.完成总成的三维模型主要参考文献(资料):1吉林大学汽车工程系编著.汽车构造(下册) 第五版. 北京:人民交通出版社2王望予.汽车设计(第4版).北京:机械工业出版社3 机械设计手册(上.中册).北京:化学工业出版社4(日)武田信之著.方泳龙译.载货汽车设计.北京:人民交通出版社5 QC/T 265-2004《汽车零部件编号规则》专业班级学生要求设计(论文)工作起止日期指导教师签字日期2011-3-21教研室主任审查签字日期系主任批准签字日期摘要随着汽车运输市场的规范,稳定发展。
前纵梁总成结构设计-20111115

作业指导书第1页共10页前纵梁总成结构设计编号部门版本目录1.适用范围 (2)2.目的 (2)3.功能及要求 (2)4.设计方法及要求 (2)版次编制日期校对日期审批日期图1图2 图34.3.2 结构强度和刚度设计由于在碰撞过程中前纵梁总成承受的载荷非常的大,图45为某车型在碰撞过程中主要传力梁系截面和对应的各梁系载荷图,从图中我们可以看到,在碰撞发生的初期,前纵梁的前端(图中1#和2#截面)承受了近95000N 的载荷。
另外,碰撞时纵梁承受的载荷与整车质量成正比,整车质量越重,纵梁承受的载荷越大,图6为一大型SUV 车型在碰撞时各梁系的载荷图,从图中可以看出其纵梁所承受的载荷值非常的大。
图9图8由于纵梁的长度较长,一般都会将纵梁分为前后两段,有些车型甚至分为三段,在纵梁前后段搭接处需要注意重合区域的长度,一般在重合区域内应至少能布置下两排焊点,重合区域长度最好达到图11图12为了将碰撞能量传递到门槛并提高车身的抗扭转性能,在纵梁总成里都会设计一个横向的梁架结构件粉色零件)将纵梁总成与门槛总成连接起来。
图13另外纵梁长度的设定也很重要,很多车型的纵梁会一直延伸至前地板总成的最后端,如图14型将纵梁后段的一部分放到前地板总成里,通过在前地板上开焊接工艺孔将前纵梁与地板纵梁连接起来,如图示。
还有一些车型将纵梁分为两段或是三段,每一段的料厚不同,通过激光焊接拼焊到一起,如图色表示纵梁的三段,每一段的厚度是不同的,位置靠前的料厚要更厚一些,这种结构的优点是零件材料厚度与受力状况匹配的更为合理,不会造成强度浪费的情况,也有利于车身的减重,但是这种工艺的应用需视客户的工艺条件图14。
车架总成(半承载)设计规范
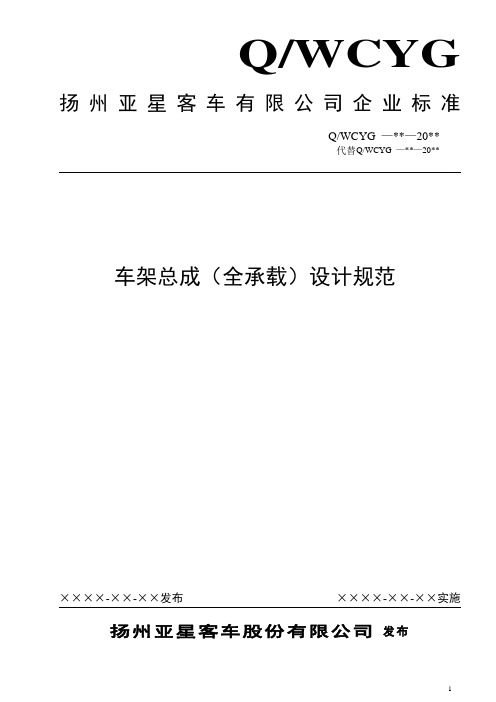
Q/WCYG车架总成(全承载)设计规范扬州亚星客车股份有限公司发布前言本标准是根据国家有关客车方面的法规、标准等要求,结合我公司产品开发流程,并参考高等院校汽车专业教材相关章节制定而成,作为扬州亚星客车股份有限公司车架总成(半承载)设计的主要依据。
本标准由扬州亚星客车股份有限公司提出并归口。
本标准由扬州亚星客车股份有限公司汽车研究院起草。
本标准主要起草人:本标准由扬州亚星客车股份有限公司汽车研究院负责解释。
前言的内容可包括:(宋体,五号,段落1.5倍行距)a)任务来源;b)制定过程及征求意见情况;c)指明该标准采用国际标准、国外先进标准的程度;d)该标准导致废止或代替其他标准文件的全部或一部分的说明;e)实施该标准过渡期的要求;f)哪些附录是标准的附录,哪些附录是提示的附录的说明;g)附加说明:——本标准由汽车研究院提出。
——本标准由汽车研究院归口。
——本标准起草部门。
——本标准主要起草人。
——本标准首次发布、历次修改和复审确认年、月车架(半承载)总成设计规范1 范围本标准规定了半承载式车架总成的术语和定义、设计规范、车架的制造工艺及材料、车架防腐蚀要求、车辆VIN码和产品标牌在车架上的固定(位置)、车架总成的变动、设计评审要求、设计输出图样和文件的明细等基本设计准则。
本标准适用于半承载车架总成设计过程控制,外购底盘车架改制可参照执行。
本标准不适用于全承载车架总成设计过程控制。
2 规范性引用文件下列文件对于本文件的应用是必不可少的。
凡是注日期的引用文件,仅所注日期的版本适用于本文件。
凡是不注日期的引用文件,其最新版本(包括所有的修改单)适用于本文件。
GB 7258-2012 机动车运行安全技术条件GB1184-80 形状和位置公差GB3323-87 钢熔化焊对接接头射线照相焊缝质量分级Q/WCYG ZT C QY G 25-2012《外购零部件防腐蚀要求》3 术语和定义下列术语和定义适用本文件。
车架内外纵梁一体成形模具设计与应用
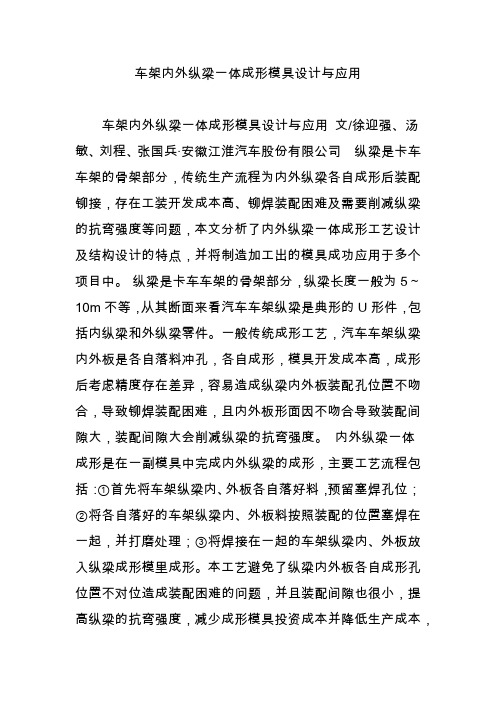
车架内外纵梁一体成形模具设计与应用车架内外纵梁一体成形模具设计与应用文/徐迎强、汤敏、刘程、张国兵·安徽江淮汽车股份有限公司纵梁是卡车车架的骨架部分,传统生产流程为内外纵梁各自成形后装配铆接,存在工装开发成本高、铆焊装配困难及需要削减纵梁的抗弯强度等问题,本文分析了内外纵梁一体成形工艺设计及结构设计的特点,并将制造加工出的模具成功应用于多个项目中。
纵梁是卡车车架的骨架部分,纵梁长度一般为5~10m不等,从其断面来看汽车车架纵梁是典形的U形件,包括内纵梁和外纵梁零件。
一般传统成形工艺,汽车车架纵梁内外板是各自落料冲孔,各自成形,模具开发成本高,成形后考虑精度存在差异,容易造成纵梁内外板装配孔位置不吻合,导致铆焊装配困难,且内外板形面因不吻合导致装配间隙大,装配间隙大会削减纵梁的抗弯强度。
内外纵梁一体成形是在一副模具中完成内外纵梁的成形,主要工艺流程包括:①首先将车架纵梁内、外板各自落好料,预留塞焊孔位;②将各自落好的车架纵梁内、外板料按照装配的位置塞焊在一起,并打磨处理;③将焊接在一起的车架纵梁内、外板放入纵梁成形模里成形。
本工艺避免了纵梁内外板各自成形孔位置不对位造成装配困难的问题,并且装配间隙也很小,提高纵梁的抗弯强度,减少成形模具投资成本并降低生产成本,应用前景广阔。
零件工艺性分析图1 内外纵梁零件图(A 外梁、B内梁)图1为内外纵梁零件图,零件材料都为B510L (屈服强度≥355MPa,抗拉强度为510~630MPa,延伸率≥24%),内纵梁厚度为3.0mm,外纵梁厚度为5.0mm,外观尺寸为5722mm(内梁为5007mm)×170mm×131mm,台阶落差为50mm,内纵梁内外R角为3mm及6mm,外纵梁内外R角为5mm及10mm。
该产品的主要技术要求:生产节拍(≥3.5SPM)、张口度(0~2mm)、上下翼面不齐度(±1mm)、扭曲度(3mm)、翘曲度(4mm)、台阶落差(±2mm)及面品(在全长范围内,上下翼面及腹面不得有起皱、拉毛、暗伤和裂纹等缺陷)。
车体结构设计指南

车体结构设计指南车体结构设计指南计指南主要介绍了车体设计的原则,包括车体设计的工作内容;介绍了车身设计的流程以车体设计各个阶段需要输出的文件;逐一介绍了车体的结构以及各个部分的功能;还介绍了车体设计应该达到的质量和性能要求。
一. 设计原则与设计流程1. 设计原则车体设计需要车体骨架的稳定性及碰撞安全性,特别是车体骨架的强度;保证车体骨架的刚度和强度,避免车体上出现应力集中区域;车体设计需设计人机工程方面的设计要求,需满足相应国家法规的要求;车体结构应具有良好的工艺性,包括冲压、焊装、涂装、和总装四大工艺;在设计时需面向产品功能确定公差和进行公差分配,进行尺寸链的计算;车体设计需保证车体有足够的刚度、强度,保证的车体的固有振动频率,保证车体的NVH性能;车体结构设计和选材需符合车体的轻量化要求和低成本要求;车体结构应具有良好的密封性能。
2. 设计流程目前,车体结构设计根据总布置确定的车身主断面、设计硬点及造型确定的外表面,结合了逆向设计和正向结构设计的思路进行的。
因而车体结构设计主要流程为:平台开发流程加上车身开发流程。
二车体开发流程总则1. 平台开发流程为了规范JAC乘用车车体设计,指导乘用车车体正确、规范的开发。
特制定JAC乘用车新产品车体开发流程。
整个流程分为:平台开发流程、上车身开发流程、输入输出文件等三大部分。
2. 流程定义⑴平台开发流程用以指导JAC乘用车底盘平台的开发。
开发内容主要包括:发动机舱总成、前围总成、地板总成和侧围轮罩分总成。
整个开发主要采用逆向加正向进行⑵上车身开发流程用以指导JAC乘用车车身的开发。
开发内容主要包括:侧围总成、车门总成、顶盖总成、发动机盖总成、翼子板总成、后围总成、行李厢盖总成。
整个开发是在底盘平台的基础上进行的全新的车身的开发⑶输入输出文件主要包括在整个车身开发过程中所需的输入文件以及车身开发过程中输出的文件。
规范化输出文件的格式、内容、依据等。
3. 流程说明⑴各阶段输出数模的界定⑵ 流程中输入输出文件位置的说明⑶ 其他三平台开发流程目标或输出文件初步工艺数模:用于工艺部门进行模夹具的招标。
汽车前机舱纵梁设计规范
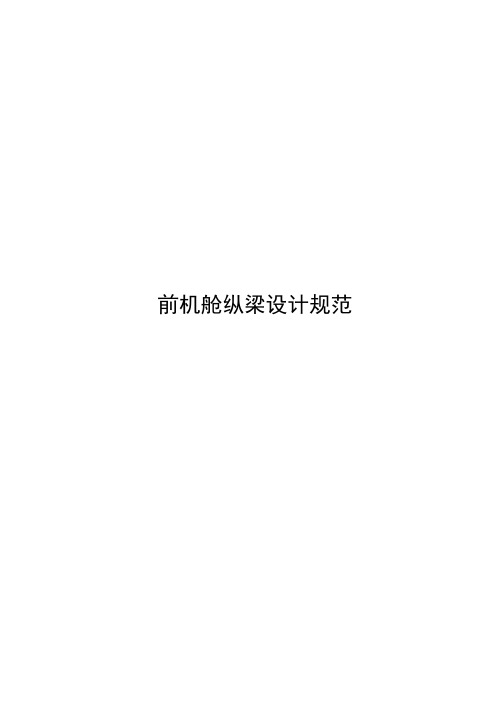
前机舱纵梁设计规范前机舱纵梁设计规范1范围本标准包含机舱前纵梁总成设计要点及其判定标准等。
本标准适用于轿车、SUV等新车型前机舱纵梁设计。
2 规范性引用文件ECE R33 关于正面碰撞车辆结构特性认证的统一规定3 术语和定义3.1 前纵梁前纵梁作为碰撞中的主要吸能部件,是汽车发动机舱框架的重要组成部分,它与前保险杠、A柱及前挡板相联接,焊接在车身下部,其上再焊接轮罩等构件。
3.2 断面断面是反映整车性能、结构、配合、法规等方面要求的截面。
主要规定了车身主要部位的结构形式、搭接关系、间隙设定、主要控制尺寸及公差、装配、人机工程、法规等各方面信息,是车身设计工程可行性分析的重要手段和车身结构设计的重要依据。
3.3 NVH NVH是指车辆工作条件下乘客感受到的噪声(noise)、振动(vibration)以及声振粗糙度(harshness),是衡量车身质量的一个综合性指标。
4 功能介绍4.1一般功能该系统提供发动机变速箱悬置、前副车架、前防撞梁、蓄电池支架、保险丝盒、底盘及空调的管路,线束等总成的安装结构。
4.1.1整车中相关区域固定点前纵梁子系统提供整车各个功能块的安装结构。
下图1表达了前纵梁子系统在整车中的相关区域。
底盘电器前防撞梁轮胎前悬架线束副车架内外饰空调系统前轮罩挡泥皮空调管路动力总成发动机和变速箱悬置图1 整车中相关区域4.1.2车身中相关区域固定点前纵梁子系统需要满足结构和安全等要求。
下图2表达了前纵梁子系统在车身中的前端区域。
水箱横梁前轮罩总成前挡板总成图2 车身中相关区域4.2特殊功能该系统的特殊功能是保证汽车的安全性要求,首先是发生正面碰撞或偏置碰撞时,能够按一定规律变形,有效吸收并分散碰撞能量,从而最大程度地保证车辆和乘员的安全。
其次是通过对车身的NVH(即噪音(Noise)、震荡(Vibration)、平稳(Harshness)三项标准)的有效控制,使乘员感到可靠和舒适。
4.3 性能要求考虑到本系统的一般功能,固定时需满足可靠耐久性。
承载式车架和非承载式车架的优缺点
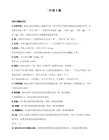
非承载式车身和承载式车身按照有无刚性车架划分,什么叫车架,是首先要弄清楚的问题。车架就是支承车身的基础构件,一般称为底盘大梁架。发动机、变速器、转向器及车身部分都固定其上,它除了承受静载荷外还要承受汽车行驶时产生的动载荷,因此车架必须要有足够的强度和刚度,以保证汽车在正常使用时受到各种应力下不会破坏和变形。
横梁有槽形、管形或口形,以保证车架的扭转刚度和抗弯强度。横梁还用以安装发动机、变速器、车身和燃油箱等。为适应பைடு நூலகம்同的车型,横梁布置有多种型式,如为了提高车架的扭转刚度采用X型布置的横梁。边梁式结构简单,工艺要求低,制造容易,使用广泛。但由于粗壮的大梁纵贯全车,影响整车布置和空间利用率,大梁的横截面高度使车厢离地距离加大,乘客上下车不方便,另外重量也大,整车行驶经济性变差。这些缺点对小客车、轿车是缺点,对于越野车可能就是优点,因为越野车要求有很强的通过性,行驶崎岖路面时要有一定大的离地间隙,而非常颠簸的道路会令车体大幅扭动,只有带刚性车架的承载式车身结构才能抵御这种冲击力。因此越野车上普遍采用非承载式车身。
车架有边梁式、钢管式等形式,其中边梁式是采用最广泛的一种车架。
边梁式车架由两根长纵梁及若干根短横梁铆接或焊接成形,纵梁主要承负弯曲载荷,一般采用具有较大抗弯强度的槽形钢梁。也有采用钢管,但多用于轻型车架上。一般纵梁中部受力最大,因此设计者一般将纵粱中部的截面高度加大,两端的截面高度逐渐减少,这样一来可使应力分布均匀,同时也减轻了重量。
还有一种介于非承载式车身和承载式车身之间的车身结构,被称为半承载式车身。它的车身本体与底架用焊接或螺栓刚性连接,加强了部分车身底架而起到一部分车架的作用。
非承载式车身和承载式车身都有优缺点,使用在不同用途的汽车上。一般而言,非承载式车身用在货车、客车和越野车上,承载式车身一般用在轿车上,现在一些客车也采用这种形式。
大客车车架纵梁强度程序化计算模型探讨

大客车车架纵梁强度程序化计算模型探讨作者:西安公路交通大学马建摘要:本文建立了适合计算机程序化处理的大客车车架纵梁弯矩与应力的计算方法,对比分析了新计算模型与传统计算模型的优缺点,并用C语言编制了计算程序。
通过实车算例,阐述了载荷简化的基本方法,对新计算模型进行了验证。
关键词:大客车车架纵梁强度计算模型对非承载式和半承载式大客车车身而言,车架纵梁是整个车身结构中的基础承载部件,车架纵梁设计是大客车设计中至关重要的环节。
在对车架纵梁进行强度分析时,除有限元方法外,一般多采用经典力学解法,特别在车架的初步方案设计阶段,由于较成熟的结构方案尚未形成,还无法采用有限元法做全面的强度分析,设计者必须依靠经典力学计算确定纵梁的结构尺寸。
大客车车架所承受的载荷比较复杂。
除受前后悬架支承力作用外,尚承受发动机、油箱、备胎等部件载荷的作用,承受乘员和座椅载荷的作用,并承受前后围、左右侧围及顶棚载荷、地板及车架自重载荷的作用等。
强度分析的任务是在以上载荷的作用下,求出纵梁任一截面所承受的弯矩,通过初步选定的纵梁截面形式,由弯矩和抗弯截面系数求出这一截面的应力。
1力学模型简化及其与传统模型的比较1.1 计算模型简化假设条件如下:(1)车架左右纵梁承受相同种类、相同位置的载荷作用,所有作用力均通过截面的弯心,即忽略不计局部扭矩的影响;(2)左右纵梁在材质上、结构上、支承上对称;(3)悬挂在车架上的各总成,按其实际位置,简化成若干集中力作用在车架上;(4)前后围、左右侧围及顶棚重量简化成作用在牛腿(或扁担梁)位置的集中力;(5)在简化地板、座椅、乘员等载荷时,若地板直接接触车架,可以将这些载荷视为若干分段均布载荷作用在车架上,这是由于在车长方向上,座椅数是非均匀布置的,不可将其简化成沿车架总长上的均布载荷。
若地板铺设在扁担梁上,通过扁担梁与车架接触,则可将地板、座椅、乘员等载荷简化成作用在扁担梁位置上的集中力;(6)当车架前后截面尺寸不变时,车架自重简化成均布载荷形式,否则,简化成分段局部载荷形式。
副车架总成技术条件

副车架总成技术条件1 范围本标准规定了汽车车架的技术要求、试验方法、检验规则、标志、包装、运输及贮存。
本标准适用于非承载车身的轻型汽车车架。
2 规范性引用标准下列文件中的条款通过本标准的引用而成为本标准的条款,凡是注日期的引用文件,其随后所有的修改单 ( 不包括勘误的内容 ) 或修订版均不适用于本标准,然而,鼓励根据本标准达成协议的各方研究是否可使用这些文件的最新版本。
凡是不注日期的引用文件,其最新版本适用于本标准。
GB/T 1730 漆膜硬度测定法摆杆阻尼试验GB/T 1731 漆膜柔性测定法GB/T 1732 漆膜耐冲击测定法GB/T 3323 金属熔化焊焊接接头射线照相GB/T 9286 色漆和清漆漆膜的划格试验QC/T 518 汽车用螺纹紧固件紧固力矩GB/T 13452.2 — 2008 色漆和清漆漆膜厚度的测定QC/T 484-1999 汽车油漆涂层3 技术要求3.1 一般要求3.1.1 车架应符合本标准的要求,并按经规定程序批准的产品图样和设计文件制造。
3.1.2 组成车架总成的各零件应为检验合格的零件。
3.2 外观要求3.2.1 车架表面不应有影响外观的裂纹和使用性能、尖角和毛刺等缺陷。
3.2.2 冲压件不应有影响外观裂纹和使用性能的皱褶等缺陷。
3.2.3 焊缝平整光滑,不允许有裂纹、气孔、夹渣、咬边等缺陷。
3.2.4 漆膜应平整光滑,不允许有漏底、起皱、划碰伤等缺陷。
3.3 装配要求3.3.1 各零部件应装配完整 , 无错装、漏装现象。
3.3.2 下臂轴套与车架压装配合要求:轴套凸缘与车架下臂套管 X 向间隙 3/4 圆周≤ 0.1 ,1/4 圆周≤ 0.5 。
3.3.3 下臂轴套与车架之间的拉拖力≥ 15kN( 暂定 ) 。
3.3.4 螺纹紧固件紧固力矩符合 QC/T 518 的规定。
3.4 尺寸的要求3.4.1 各安装点尺寸符合设计要求,其中前悬架各安装点尺寸、车身悬置各安装点尺寸、后悬架各安装点尺寸及动力总成各安装点尺寸的重要度应为 B 级。
汽车厂质量保证部技术文件车架纵梁检验作业指导书
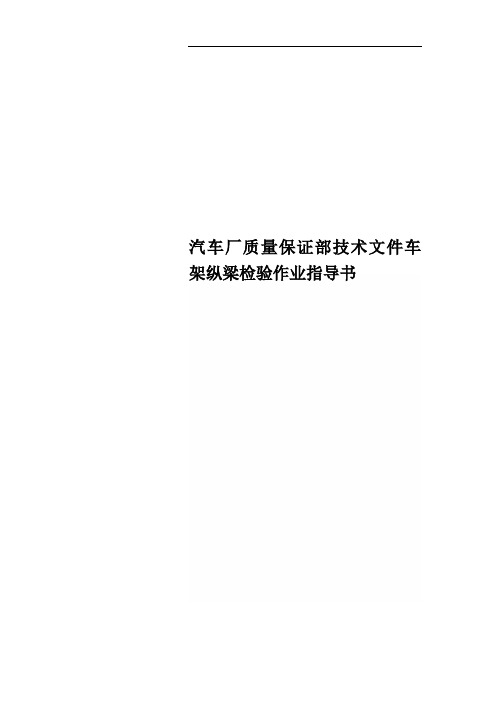
汽车厂质量保证部技术文件车架纵梁检验作业指导书一汽解放青岛汽车厂质量保证部技术文件编号:IPQC-JYZD-2-2009 批准:车架纵梁检验作业指导书2008年12月31日发布 2009年1月1日实施一汽解放青岛汽车厂质量保证部发布前言本检验作业指导书依据有关汽车标准及一汽解放青岛汽车厂技术文件制定。
是一汽解放青岛汽车厂质量保证部技术文件之一。
本检验作业指导书与国家标准、企业标准及相关技术文件相一致。
从实施之日起,原《IPQC-JYZD-2-2008车架纵梁检验作业指导书》同时废止。
各相关部门检验车架纵梁时,都需要按本检验作业指导书的规定执行。
本标准由一汽解放青岛汽车厂质量保证部起草。
本检验作业指导书起草人:吴立新本检验作业指导书审核人:石建通1 主要内容与适用范围本指导书做为车架纵梁各工序质量检验及控制的技术性说明。
本指导书适用于纵梁加工各工序有关部门。
2 术语和定义2.1 落料用冲模沿封闭线冲切板料,冲下来的部分为制件。
2.2 冲孔用冲模沿封闭线冲切板料,冲下来的部分为废料。
2.3 弯曲把平板毛坯、型材弯成一定曲率及角度形成一定形状的冲压工序。
3 制件的检验标准及要求3.1 板料检验纵梁外板及内护板下料尺寸、(侧弯)直线度与工艺要求相符,板料表面平整,不允许有影响定位的严重弯曲、翅头存在,无锈蚀、严重麻纹、明显锤印、切割焊瘤、严重划伤等质量缺陷。
检验频次及其它要求:操作者100%目视,工序检查员按首、中、末检验。
3.2 落料冲孔质量检验3.2.1 落冲模夹紧可靠,各模段对接平顺,相对错位不超过0.2mm。
检验频次及其它要求:落冲前工序检查员检验确认。
3.2.2 纵梁外板或内护板边缘平直无明显错位,落冲边及所有孔落冲毛刺不大于0.2mm,外板前端第一工艺孔到料前端头尺寸公差控制在±2mm,工艺孔位置度为Φ0.5mm,对采用后定位落冲的纵梁外板及内护板,其最后一工艺孔距板料后端头尺寸公差控制在±3mm。
(整理)客车车身结构.

第5章客车车身结构及其设计5-1 车身结构及其分类5.1.2、客车车身分类方法2、按承载形式分按车身承载形式,客车车身结构可分为非承载式、半承载式和承载式三大类。
非承载式和半承载式车身结构都是属于有车架式的,而承载式车身则属于无车架式的。
从设计的角度看,这类分法是比较合理的。
按承载形式对车身结构进行分类,表征了不同形式的车身结构的组成以及车身制造工艺过程中的差异。
图5-4 非承载式客车的底盘及车身(2)半承载式客车车身图5-5 客车半承载式车身1-顶灯地板;2-换气扇框;3-顶盖横梁;4-顶盖纵梁;5-前风窗框上横梁;6-前风窗立柱;7-前风窗中立框;8-前风窗框下横梁;9-前围搁梁;10-车架前横梁;11-前围立柱;12-后风窗框下横梁;13-后围搁梁;14-后围裙边梁;15-侧围窗立柱;16-车轮拱;17-斜撑;18-腰梁;19-侧围搁梁;20-侧围立柱,21-侧围裙边梁;22-上边梁;23-车架横梁;24-门立柱;25-车架悬臂梁;26-门槛;27-车架纵梁(3)承载式客车车身图5-6奔驰O404大客车的承载式车身1-侧窗立柱;2-顶盖纵梁;3-顶盖横梁;4-顶盖斜撑;5-上边梁;6-前风窗框上横梁;7-前风窗立柱;8-仪表板横梁;9-前风窗框下横梁;10-前围搁梁;11-后风窗框上横梁;12-后风窗框下横梁;13-后围加强横梁;14-后围立柱;15-腰梁;16-角板;17-侧围搁梁;18-斜撑;19-底架横格栅;20-侧围裙边梁;21-裙立柱;22-门立柱;23-门槛;24-底架纵格栅图5-6所示是奔驰O404大客车的承载式车身结构,其底架是薄钢板冲压或用型钢焊制的纵横格栅,以取代笨重的车架。
格栅是高度较大(约500mm)桁架结构,因而车身两侧地板上只能布置坐席,而坐席下方高大的空间可用做行李舱,故适用于大型长途客车。
整体承载式车身结构的特点是所有的车身壳体构件都参与承载,互相牵连和协调,充分发挥材料的潜力,使车身质量最小而强度和刚度最大。
做汽车的都该了解下,汽车纵梁的制造工艺及装备

做汽车的都该了解下,汽车纵梁的制造工艺及装备载货汽车纵梁是各种轻型、中型及重型载货汽车车架的主要构件,载货汽车车架一般由左右两根纵梁和几根横梁组成,车架作为整个汽车的基体,是组装发动机、传动系统、悬架、转向系统等各部件的骨架,承受来自车身内外的各种载荷作用。
同时,由于载货车车架的结构尺寸较大,各部件之间的装配工艺比较严格,其结构形式及加工工艺直接影响到重型载货汽车的品质。
在车架的主要构成部件中,左右纵梁是整个车架的主体,是汽车其他部件的装配基础,同时也是汽车的关键承载部件。
车型的多样化和发动机等核心部件的改型等因素造成车架纵梁的形状、尺寸和孔的大小及数量、分布等都有不同程度的差别,同时由于载货汽车的承重要求造成其纵梁材料一般较厚、尺寸较长(几乎与整车相当),所以载货汽车纵梁的制造工艺极为复杂,其制造成本相对也比较高。
随着汽车工业的飞速发展及科技的不断进步,纵梁的制造工艺及相应工装设备也不断改进和优化。
随之涌现出各种柔性化的纵梁制造技术及工艺,汽车纵梁的生产方式逐渐由“单一品种、大批量、小批次”向“多品种、小批量、多批次”转变,本文主要对现代载货汽车纵梁的制造工艺及相应的加工设备做简要论述。
制造工艺及装备随着汽车工业的日益发展,载货汽车纵梁的数量和品种也不断增加,纵梁的制造工艺和加工设备也不断创新和完善。
总体来说,载货汽车纵梁的制造工艺主要分为3个工序内容:落料、孔加工和成形加工。
其整体制造工艺流程则为上述三种工序内容的部分或全部组合。
1. 各工序内容及相应加工设备(1)落料一般汽车厂直接采购的原材料钢板都是大块板料(见图1),需要根据不同的产品将板料加工出所需的形状和尺寸,此工序即为落料。
根据加工设备的不同,落料工序主要分为剪切落料、模具落料和切割落料三种形式。
剪切落料的设备是剪板机(见图2),根据其加工板料长度的不同,有3m、6m、8m和12m等不同规格;剪板机无需开发模具,在设备规格允许范围内可获得不同厚度、长度和宽度规格的料片;但剪板机只能下矩形料片,只适用于等截面U形梁的生产,对于变截面梁则不适用。
工艺商用车车架纵梁加工工艺方法比较

⼯艺商⽤车车架纵梁加⼯⼯艺⽅法⽐较欢迎阅读本篇⽂章,⽂末有福利哦!商⽤车车架纵梁产品结构特点纵梁与其他冲压件对⽐,其特点有以下⼏⽅⾯:(1)外形长、板料厚。
根据车型功能不同,纵梁长度范围⼤概为5~12m,厚度范围为4~10mm。
例如,牵引车车架纵梁长度⼀般在6~8m,载货⾃卸车架纵梁长度⼀般在8~12m。
(2)孔数多。
商⽤车80%以上的重要总成和部件在车架纵梁上进⾏装配。
例如,发动机、变速箱、车桥、驾驶室及外挂件等,纵梁孔数⼀般为200~400个。
(3)结构不复杂但精度要求⾼。
以U形结构为主,由于纵梁的孔和型⾯⼤部分都是装配孔、装配⾯,所以尺⼨精度要求⾼。
(4)材料强度⾼。
钢板屈服强度δs为500~700MPa。
商⽤车车架纵梁与内加强板⼀般有单层板、双层板、三层板三种主要结构形式,⼀般内加强板厚度都不⼤于纵梁厚度。
根据不同车型承载需要,配置不同层次和不同板厚的加强板。
按截⾯分类有等截⾯和变截⾯两种,按腹⾯分类有等直和弯曲两种,具体如图1所⽰。
图1 加强板形状分类商⽤车纵梁加⼯⼯艺⽅法传统冲压⼯艺⼤型压床结合模具进⾏冷冲压加⼯是国内主要卡车制造商初期⽣产纵梁采⽤的⽣产⼯艺,这种⽣产模式适⽤于品种少批量⼤的⽣产。
在60到90年代,卡车产品种类少,⽣产批量⼤,模具冲压⽣产的效率⾼、稳定性好,解放公司卡车⼚在2004年前⼀直采⽤此⼯艺⽣产纵梁。
加⼯⼯艺流程为:倍尺钢板→酸洗→模具落料冲孔→模具压弯。
其优点是:(1)单⼀品种⼤批量⽣产效率⾼。
(2)⽣产⾯积⼩,物流环节少。
(3)落料冲孔,外形尺⼨孔位精度⾼,⼀致性好。
(4)产品适应性较强,直槽纵梁和变截⾯纵梁都能⽣产。
缺点是:(1)模具投资⼤,制造周期长。
⼀套商⽤车纵梁落料冲孔模具和压弯模具共计约需要500万左右,模具的制造周期为8~12个⽉,在新产品准备时,⽆法满⾜快速投产的需要。
(2)倍尺料封闭落料材料利⽤率低。
在封闭落料冲孔时,双侧侧搭边值为30mm,对⽐净尺料每件重15kg左右,按⽉产1万辆计算,每⽉多产⽣废料近300t。
现代汽车构造 任务17.3 客车车身

按车身承载形式可分为非承载式车身、 半承载式车身和承载式车身三类。 一、 非承载式车身 这种车身属于有车架式车身结构。这 种结构在车架上设置底横梁,而底横梁支 撑在悬伸梁上,悬伸梁与车架纵梁两侧用 螺栓连接;车身两侧的骨架立柱与底横梁 焊接形成整体车车身骨架
图17-9 依维柯汽车车身结构图(非承载式)
二、半承载式车身 半承载式车身是将车架横梁加宽并直 接与车身侧壁骨架刚性连接而成,这种结 构可降低重心,减轻客车自重,如图1710、图17-11所示。此时的“车架”可称 为底架 。
图17-10 大型客车的承载底架
图 17-11 客车半承载式车身骨架及底盘
三、承载式车身 大客车广泛采用无车架的承载式车身 结构。目的是减轻客车自身 质量以及使车 身结构合理化。 根据客车车身上部与下部受力程度的 不同,可将承载式车身分为基础承载式和 整体承载式两种。 1、基础承载式 它具有贯通式纵梁和一些与车身等宽的 横梁,车身骨架与这些横梁刚性连接,使整
个车身与底架形成一个刚性空间承载系统, 如图17-10所示。 2、整体承载式 这种结构的整个车身壳体构件都参与 承载。车身底部取消了贯通式纵梁,采用矩 形管焊接成格子栅栏式底架结构,并使上 下构件相互牵连和协调。在受载荷时自动 调节。使整个车身达到稳定平衡状态,如 图17-12所示。