铜及铝板带轧制过程中轧机不稳定因素探讨(正式版)
轧钢机械振动的原因与故障处理分析郭超福

轧钢机械振动的原因与故障处理分析郭超福发布时间:2021-04-14T14:07:29.517Z 来源:《中国科技信息》2021年4月作者:郭超福[导读] 钢铁工业是建设国民经济、发展社会各行业、人民生活和工作的基础企业。
轧钢的生产是钢铁生产重要组成部分。
为了保证轧钢生产的安全性和效率,在轧钢生产中需要各种机械设备的稳定安全运行。
但是,一些轧钢运行经常出现机械振动故障,严重影响轧钢生产的安全性和效率。
新疆八一钢铁股份有限公司轧钢厂棒线分厂郭超福摘要:钢铁工业是建设国民经济、发展社会各行业、人民生活和工作的基础企业。
轧钢的生产是钢铁生产重要组成部分。
为了保证轧钢生产的安全性和效率,在轧钢生产中需要各种机械设备的稳定安全运行。
但是,一些轧钢运行经常出现机械振动故障,严重影响轧钢生产的安全性和效率。
关键词:轧钢机械;振动故障;分析;措施轧钢机械被广泛应用于工作中。
在使用过程中,轧辊的旋转会产生压力来改变钢的形状,以更好地满足工业产品的设计要求。
因此,在实际使用过程中,管理人员应定期对轧钢机械进行检测维护,及时对设备隐患进行消缺,有效提高轧钢机械工作效率。
轧钢机械安全运行管理也是工人生产安全的保证。
在管理过程中,在管理设备的硬件部分,有效保证设备的正常运行,并定期对设备进行监控维修保养使设备保持良好状态,提高了工业生产水平。
一、轧钢机械振动的故障判断标准事实上,振动在轧钢机械运行过程中是常见的,但有些振动是正常的,有些是异常的,我们需要对异常振动进行有针对性的处理,在此之前我们有必要识别轧机故障,准确判断振动是否故障。
根据相关工作经验和理论研究,轧机振动缺陷判断标准和指标分为定量判断和定性分析三类比较定量、类比以及相对判断。
这些方法有助于确定故障的原因,在实际操作中,故障的原因必须通过综合各种因素来确定,如机械操作过程中状态的变化。
由此可见,轧钢机械振动故障的判断必须结合实际情况,这不仅非常复杂而且困难。
铜及铝板带轧制过程中轧机不稳定因素探讨示范文本

文件编号:RHD-QB-K3168 (安全管理范本系列)编辑:XXXXXX查核:XXXXXX时间:XXXXXX铜及铝板带轧制过程中轧机不稳定因素探讨示范文本铜及铝板带轧制过程中轧机不稳定因素探讨示范文本操作指导:该安全管理文件为日常单位或公司为保证的工作、生产能够安全稳定地有效运转而制定的,并由相关人员在办理业务或操作时进行更好的判断与管理。
,其中条款可根据自己现实基础上调整,请仔细浏览后进行编辑与保存。
在铜及铝板带轧制过程中难免会发生不稳定现象,导致这种现象的原因较多,其问题主要集中在轧机上,从而对带材高精度生产造成严重影响。
由于有色金属板的性能区别于钢铁的性能,因此对轧机的要求有所不同。
本研究中,笔者对轧机轧制过程中不稳定现象从工艺、设备等的角度进行分析,以供同行工作者参考。
当前,随着科学技术的日益发展,在有色金属的加工技术中,对板带材精度和质量随之提出了更高的要求。
为确保轧机轧制在板带轧制过程中的稳定性,消除外扰因素很重要,只有认真发现铜及铝板带轧制过程中存在的一些问题,才能消除由于这些不稳定因素的发生导致产品质量出现问题的现象。
轧机系统稳定性受轧制材料的质量的影响1.1轧制过程中发生辊颤与材料相关采用铸轧坏料在铝粗轧机进行轧制的调试时,通常采用轧制速度及压下量等常规轧制工艺参数,整个轧机有时会发生颤动的现象,这使工艺参数的调整受到影响。
出现这种现象主要是因铸轧坯料铸轧后表面氧化膜化厚,其主要因放置时间较长所致,材料表面性能及其内部组织在长时间后均会发生变化,使轧材与辊面的摩擦系统不断降低,再加上摩擦力与咬入力小较,而导致打滑的现象发生,而导致轧辊颤振。
1.2来料偏差不宜过大一般试验过程中经常采用厚度偏差不同的带坯,而轧制厚度偏差的带坯为0.1~0.12mm时,相比0.15mm的轧制厚差带坯,轧机稳定性较高。
轧机系统稳定性受工艺润滑剂的影响经常发生辊颤还有一个重要原因是由于润滑剂与所选择的工艺参数不匹配,对于轧机系统的振动因被轧金属与辊缝处辊面之间的摩擦因素而受到影响主要体现在以下几个方面:(1)在轧机系统的垂直运动中辊缝的润滑油膜能起到一定的阻尼作用,其阻尼作用在油膜摩擦系数越低的情况下越小,则会降低系统的稳定性质,轧机在外部等量扰动的情况下极易发生振动;(2)在充分润滑的条件下,会减小辊缝摩擦,而在干扰因素不稳定的情况下,辊缝状态的波动会增大,则会严重影响到系统的稳定性;(3)辊缝的摩擦系数越小,轧机轧制压力所受到的摩擦压力也就越小,轧制压力受到轧制张力的影响也就越大,从而会降低轧机系统的稳定性,使轧机容易发生振动。
轧制缺陷及质量控制
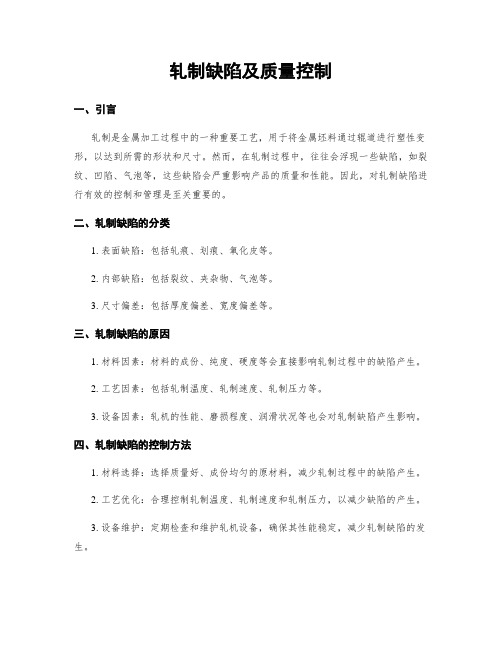
轧制缺陷及质量控制一、引言轧制是金属加工过程中的一种重要工艺,用于将金属坯料通过辊道进行塑性变形,以达到所需的形状和尺寸。
然而,在轧制过程中,往往会浮现一些缺陷,如裂纹、凹陷、气泡等,这些缺陷会严重影响产品的质量和性能。
因此,对轧制缺陷进行有效的控制和管理是至关重要的。
二、轧制缺陷的分类1. 表面缺陷:包括轧痕、划痕、氧化皮等。
2. 内部缺陷:包括裂纹、夹杂物、气泡等。
3. 尺寸偏差:包括厚度偏差、宽度偏差等。
三、轧制缺陷的原因1. 材料因素:材料的成份、纯度、硬度等会直接影响轧制过程中的缺陷产生。
2. 工艺因素:包括轧制温度、轧制速度、轧制压力等。
3. 设备因素:轧机的性能、磨损程度、润滑状况等也会对轧制缺陷产生影响。
四、轧制缺陷的控制方法1. 材料选择:选择质量好、成份均匀的原材料,减少轧制过程中的缺陷产生。
2. 工艺优化:合理控制轧制温度、轧制速度和轧制压力,以减少缺陷的产生。
3. 设备维护:定期检查和维护轧机设备,确保其性能稳定,减少轧制缺陷的发生。
4. 润滑控制:选择合适的润滑剂,保证轧制过程中的润滑效果,减少磨擦和磨损,降低缺陷产生的可能性。
五、质量控制措施1. 检测方法:采用超声波、X射线、磁粉探伤等非破坏性检测方法,及时发现和排除轧制缺陷。
2. 检测设备:使用高精度的检测设备,确保对轧制缺陷的检测准确性和可靠性。
3. 检测标准:制定严格的轧制缺陷检测标准,明确缺陷的类型、数量和尺寸要求。
4. 检测频率:根据产品的重要性和应用领域,确定合理的检测频率,确保产品质量的稳定性和可靠性。
六、案例分析以某钢铁公司为例,该公司采用了先进的轧制设备和严格的质量控制措施,成功地控制了轧制缺陷的发生。
通过优化工艺参数,选择高质量的原材料,并定期进行设备维护和润滑控制,该公司的产品质量得到了有效提升。
同时,该公司还建立了完善的质量检测体系,采用先进的检测设备和严格的检测标准,确保产品质量的稳定性和可靠性。
轧制缺陷及质量控制

轧制缺陷及质量控制一、引言轧制是金属加工中的一种重要工艺,用于将金属坯料通过轧机进行塑性变形,以获得所需的形状和尺寸。
然而,在轧制过程中,由于各种因素的影响,会产生一些缺陷,如裂纹、夹杂物、表面缺陷等,这些缺陷会严重影响产品的质量和性能。
因此,对轧制缺陷进行有效的控制和管理,是确保产品质量的关键。
二、轧制缺陷的分类1. 表面缺陷:包括轧痕、轧花、氧化皮、划伤等。
2. 内部缺陷:包括夹杂物、裂纹、孔洞等。
3. 尺寸偏差:包括厚度偏差、宽度偏差等。
三、轧制缺陷的原因分析1. 材料因素:原材料的质量和成份会直接影响轧制过程中的缺陷产生。
如含有夹杂物、氧化皮等。
2. 工艺参数:轧制过程中的轧制力、轧制速度、轧制温度等参数的控制不当,会导致缺陷的产生。
3. 设备状况:轧机的磨损、不平衡等问题会影响轧制质量。
4. 操作人员:操作人员的技术水平和经验也会对轧制质量产生影响。
四、轧制缺陷的质量控制方法1. 前期控制:在轧制前对原材料进行严格的检查和筛选,确保材料的质量符合要求。
2. 工艺参数控制:根据产品的要求和轧制材料的特性,合理设置轧制力、轧制速度、轧制温度等参数,以减少缺陷的产生。
3. 设备维护:定期对轧机进行检修和维护,确保设备的正常运行,减少设备因素对轧制质量的影响。
4. 操作人员培训:加强对操作人员的培训和技术指导,提高其对轧制过程中缺陷产生原因的认识和处理能力。
5. 检测方法:采用先进的无损检测技术,如超声波检测、磁粉检测等,对轧制产品进行全面的检测,及时发现和排除缺陷。
6. 质量管理体系:建立完善的质量管理体系,包括质量控制计划、质量检验记录、质量问题分析等,确保轧制产品的质量稳定可控。
五、案例分析某钢铁厂在轧制过程中,时常浮现轧制缺陷问题,导致产品质量不稳定,客户投诉频繁。
经过对生产过程的分析和改进,采取了以下措施:1. 强化原材料的筛选工作,严格控制夹杂物和氧化皮的含量。
2. 优化工艺参数,合理调整轧制力、轧制速度和轧制温度,降低缺陷的产生率。
铝箔轧制工艺影响因素研究
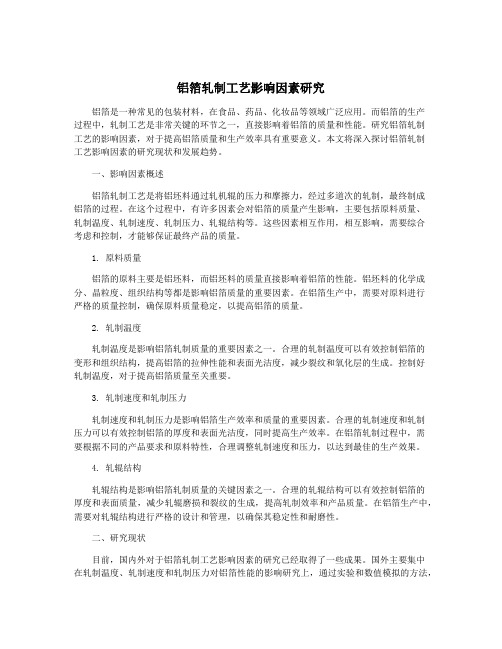
铝箔轧制工艺影响因素研究铝箔是一种常见的包装材料,在食品、药品、化妆品等领域广泛应用。
而铝箔的生产过程中,轧制工艺是非常关键的环节之一,直接影响着铝箔的质量和性能。
研究铝箔轧制工艺的影响因素,对于提高铝箔质量和生产效率具有重要意义。
本文将深入探讨铝箔轧制工艺影响因素的研究现状和发展趋势。
一、影响因素概述铝箔轧制工艺是将铝坯料通过轧机辊的压力和摩擦力,经过多道次的轧制,最终制成铝箔的过程。
在这个过程中,有许多因素会对铝箔的质量产生影响,主要包括原料质量、轧制温度、轧制速度、轧制压力、轧辊结构等。
这些因素相互作用,相互影响,需要综合考虑和控制,才能够保证最终产品的质量。
1. 原料质量铝箔的原料主要是铝坯料,而铝坯料的质量直接影响着铝箔的性能。
铝坯料的化学成分、晶粒度、组织结构等都是影响铝箔质量的重要因素。
在铝箔生产中,需要对原料进行严格的质量控制,确保原料质量稳定,以提高铝箔的质量。
2. 轧制温度轧制温度是影响铝箔轧制质量的重要因素之一。
合理的轧制温度可以有效控制铝箔的变形和组织结构,提高铝箔的拉伸性能和表面光洁度,减少裂纹和氧化层的生成。
控制好轧制温度,对于提高铝箔质量至关重要。
3. 轧制速度和轧制压力轧制速度和轧制压力是影响铝箔生产效率和质量的重要因素。
合理的轧制速度和轧制压力可以有效控制铝箔的厚度和表面光洁度,同时提高生产效率。
在铝箔轧制过程中,需要根据不同的产品要求和原料特性,合理调整轧制速度和压力,以达到最佳的生产效果。
4. 轧辊结构轧辊结构是影响铝箔轧制质量的关键因素之一。
合理的轧辊结构可以有效控制铝箔的厚度和表面质量,减少轧辊磨损和裂纹的生成,提高轧制效率和产品质量。
在铝箔生产中,需要对轧辊结构进行严格的设计和管理,以确保其稳定性和耐磨性。
二、研究现状目前,国内外对于铝箔轧制工艺影响因素的研究已经取得了一些成果。
国外主要集中在轧制温度、轧制速度和轧制压力对铝箔性能的影响研究上,通过实验和数值模拟的方法,深入探讨了这些因素对铝箔质量的影响规律。
最新整理铜及铝板带轧制过程中轧机不稳定因素探讨.docx

最新整理铜及铝板带轧制过程中轧机不稳定因素探讨在铜及铝板带轧制过程中难免会发生不稳定现象,导致这种现象的原因较多,其问题主要集中在轧机上,从而对带材高精度生产造成严重影响。
于有色金属板的性能区别于钢铁的性能,因此对轧机的要求有所不同。
本研究中,笔者对轧机轧制过程中不稳定现象从工艺、设备等的角度进行分析,以供同行工作者参考。
当前,随着科学技术的日益发展,在有色金属的加工技术中,对板带材精度和质量随之提出了更高的要求。
为确保轧机轧制在板带轧制过程中的稳定性,消除外扰因素很重要,只有认真发现铜及铝板带轧制过程中存在的一些问题,才能消除于这些不稳定因素的发生导致产品质量出现问题的现象。
轧机系统稳定性受轧制材料的质量的影响1.1轧制过程中发生辊颤与材料相关采用铸轧坏料在铝粗轧机进行轧制的调试时,通常采用轧制速度及压下量等常规轧制工艺参数,整个轧机有时会发生颤动的现象,这使工艺参数的调整受到影响。
出现这种现象主要是因铸轧坯料铸轧后表面氧化膜化厚,其主要因放置时间较长所致,材料表面性能及其内部组织在长时间后均会发生变化,使轧材与辊面的摩擦系统不断降低,再加上摩擦力与咬入力小较,而导致打滑的现象发生,而导致轧辊颤振。
1.2来料偏差不宜过大一般试验过程中经常采用厚度偏差不同的带坯,而轧制厚度偏差的带坯为0.1~0.12mm时,相比0.15mm的轧制厚差带坯,轧机稳定性较高。
轧机系统稳定性受工艺润滑剂的影响经常发生辊颤还有一个重要原因是于润滑剂与所选择的工艺参数不匹配,对于轧机系统的振动因被轧金属与辊缝处辊面之间的摩擦因素而受到影响主要体现在以下几个方面:(1)在轧机系统的垂直运动中辊缝的润滑油膜能起到一定的阻尼作用,其阻尼作用在油膜摩擦系数越低的情况下越小,则会降低系统的稳定性质,轧机在外部等量扰动的情况下极易发生振动;(2)在充分润滑的条件下,会减小辊缝摩擦,而在干扰因素不稳定的情况下,辊缝状态的波动会增大,则会严重影响到系统的稳定性;(3)辊缝的摩擦系数越小,轧机轧制压力所受到的摩擦压力也就越小,轧制压力受到轧制张力的影响也就越大,从而会降低轧机系统的稳定性,使轧机容易发生振动。
影响中厚板轧制稳定性的因素分析与优化

DOI:10.3969/j.issn.l006-110X.2021.02.015影响中厚板轧制稳定性的因素分析与优化李学明,周焱民(新余钢铁股份有限公司,江西338001)[摘要]本文研究了WINCC界面控制技术、TDC程序联锁控制技术、支撑辊平衡力动态控制技术、位移传感器磁环固定技术、压下AGC缸液压油进岀同步控制技术、刚度测试程序优化技术等在中厚板轧机上的应用。
这些技术解决了新钢中厚板轧机辊缝下降不稳定、刚度试验值不准确、厚度计故障率高的问题,提高了轧制稳定性和运行效率。
生产实践证明,钢板尺寸控制精度得到提高,起到了优化轧制质量的目的。
[关键词]中厚板;轧制;控制系统;稳定性Analysis and optimization of factors affectingrolling stability of medium and heavy plateLI Xue-rning and ZHOU Yan-min(Xidyu Yoo and Steel Co.,Ltd.,JINNGXY338001)Abstract Ir this panee,the anplicatioo of a series of cootroO—Ghniquas is sud—a in mlOm thiGe plate mi—,coosist of WINCC Oterface cootroO technolovUt TDC prooram O—C og-O v cootroO technolovUt bacCup roO baladcc force dyuamic controO—Ghdolovu displacemeaf seascc maadetic riny Oxation —61^(000*screw-dowd AGC cylindee hyUranUc oil in and oof syuc-roooos cootroO tec-dolovUt stiddess test prooram ootioizatioo tec-dolovu lc•These—Ghniques have solvel the proOlems of roO yn desceddiny ims—bla,inacchrate sti—dess test value and high failure rate of thichdess§31X01,—mlOm and heave p U—mi—of Xinsteel companyt and—nprovel rolliny swnifm and ooeratioo efdOedd•ProOuctioo practice has provel that the precisioo of steel plate size cootroO can be ioprovelt which plays the puraose of oo-oiziny rolliny口^—丫.Key words mlOm and heavy p—tc,oOOy,cootroO system,swnifm0引言面对中厚板产品市场竞争激烈的现实,各中厚板生产企业将发展重点从单纯追求产量、规模转移到提高产品质量、精度等方面,以期在激烈的市场竞争中占有一席之地516。
铜带轧机调试过程中的问题及解决办法
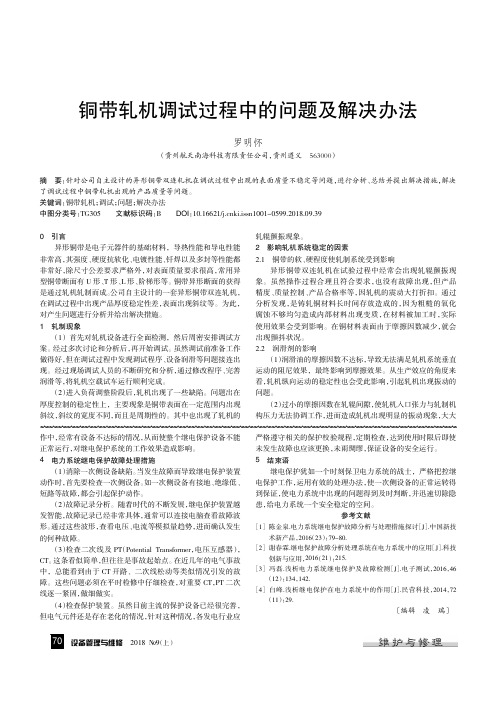
设备管理与维修2018翼9(上)铜带轧机调试过程中的问题及解决办法罗明怀(贵州航天南海科技有限责任公司,贵州遵义563000)摘要:针对公司自主设计的异形铜带双连轧机在调试过程中出现的表面质量不稳定等问题,进行分析、总结并提出解决措施,解决了调试过程中铜带轧机出现的产品质量等问题。
关键词:铜带轧机;调试;问题;解决办法中图分类号:TG305文献标识码:BDOI :10.16621/ki.issn1001-0599.2018.09.390引言异形铜带是电子元器件的基础材料,导热性能和导电性能非常高,其强度、硬度抗软化、电镀性能、钎焊以及多封等性能都非常好,除尺寸公差要求严格外,对表面质量要求很高,常用异型铜带断面有U 形、T 形、L 形、阶梯形等。
铜带异形断面的获得是通过轧机轧制而成。
公司自主设计的一套异形铜带双连轧机,在调试过程中出现产品厚度稳定性差,表面出现斜纹等。
为此,对产生问题进行分析并给出解决措施。
1轧制现象(1)首先对轧机设备进行全面检测,然后周密安排调试方案。
经过多次讨论和分析后,再开始调试。
虽然调试前准备工作做得好,但在调试过程中发现调试程序、设备润滑等问题接连出现。
经过现场调试人员的不断研究和分析,通过修改程序、完善润滑等,将轧机空载试车运行顺利完成。
(2)进入负荷调整阶段后,轧机出现了一些缺陷。
问题出在厚度控制的稳定性上,主要现象是铜带表面在一定范围内出现斜纹,斜纹的宽度不同,而且是周期性的。
其中也出现了轧机的轧辊颤振现象。
2影响轧机系统稳定的因素2.1铜带的软、硬程度使轧制系统受到影响异形铜带双连轧机在试验过程中经常会出现轧辊颤振现象。
虽然操作过程合理且符合要求,也没有故障出现,但产品精度、质量控制、产品合格率等,因轧机的震动大打折扣。
通过分析发现,是铸轧铜材料长时间存放造成的,因为粗糙的氧化腐蚀不够均匀造成内部材料出现变质,在材料被加工时,实际使用效果会受到影响。
在铜材料表面由于摩擦因数减少,就会出现颤抖状况。
铝材轧制过程中常见问题的解决方法

铝材轧制过程中常见问题的解决方法技术工作总结——铝材轧制过程中常见问题的解决方法铝原料轧制过程中的质量控制技术对现行的的生产型企业来讲是十分重要的。
我们现在所采用的原料轧制技术是沿用上世纪七十年代中期上海铝材厂传授下来的成熟的轧制技术(当时这种技术属国内比较先进的生产技术),从铝锭和角料进炉开始到成品铝带出厂,系列铝加工轧制技术均能够得到充分运用和发挥,通过三十多年来的生产实践和运用,在不更换现有生产设备的情况下,改良轧制过程中的工艺技术,发现和解决生产中常见问题十分关键。
按照现时确定的轧制原料工工序,应包含熔炼、浇铸、热轧、冷通及精轧。
1熔炼方面我公司所熔炼的原料是铝锭加角料,在原料的进炉前,我认为必须对角料进行检验,主要是检查角料中的包杂情况进行抽检,其次是对角料中是否含水份情况进行一一巡视,决不能向炉膛内投进一块含有水分的角料块,经过多年来的问题排查发现,角料含水是造成后道产品气泡等质量问题的原因之一。
实践中,我认识到在熔炼过程中,必须注意的是除气、排渣问题,如果除气、排渣处理不好,产品到了后道,或者成品到用户以后,就会出现后续产品有气泡、亮点、白丝等诸多质量问题。
我采用的解决的方法是通过空心管向铝液中吹入氮气,这样处理得比较好的话,气泡、亮点、白丝等质量问题就会消除。
为了提高出水率,在铝液达到一定温度后,继续向铝液中投放一定数量的角料块,在温度允许的前提下,角料会在铝液中迅速融化成铝液,既省时有省料,还没有烧损,是一个提高经济效益的好方法,但是,要重视的问题就是,同样要做好除气排渣的工作,否则会出现产品起皮现象。
熔炼方面按照技术要求去做,产品质量问题就会随之消灭。
2浇铸方面铝液经过一定时间的静止后,就可以浇铸。
此时的模具一定要经过安全检查,按照操作规程操作,将模具倾斜到一定角度,铝液慢慢的向模具内倒入,不可太快。
太快易造成铝液中夹杂的气体不能排出,引起坯块密度小于2.7×103Kg/m3(结构疏松),其强度低于sb=80~100MPa,轧制后尤其是到了后续加工制品时会出现各种质量等问题。
铝热轧卷轧制错层因素分析

0 前言
热轧是变形铝及铝合金板带材生产流程中非常 重要和关键的生产工序,通过热轧将铸造组织转变 为加工组织。热轧不但为冷轧工序提供坯料,而且 还能直接轧制成品厚度。热轧的组织、表面质量和 板形状况对后部工序有着强烈的遗传性,甚至对最 终产品的质量状况起着决定性作用[1]。
热轧卷错层是影响产品外观质量的重要问题。 人们通常通过提高设备精度、拓宽设备功能、优化 工艺模型和管理方法的改进来解决这一问题。
接关系。通过设备相关部件的排查,提出了处理方法和改良措施,并成功应用于铝热轧卷实际生产中。
关键词:铝热轧卷;轧制力差;错层;原因分析
中图分类号:TG339
文献标识码:B
文章编号:1005-4898 (2019) 01-0035-03
doi:10.3969/j.issn.1005-4898.2019.01.10
通过检查,发现以上因素不是造成铝卷错层的 根本原因。
(6) 经对 iba 数据分析对比,确定缺陷的产生 与卷取过程中的力控、位控不当和轧制过程头尾板 型控制差有关,这些原因都容易造成卷取前期和卷 取后期不平稳,最终形成错层缺陷。具体分析基于 以下原因:
表 1 为错层卷和正常卷 iba 数据的对比情况。 从 iba 对照数据上看,错层卷的轧制力波动值明显 大于正常卷,且波动的周期不是一个固定值。
21381-4 HF308
8.97
1.74
无错层
由表 1 中数据可以看出,错层卷的最大轧制力 波动周期和最大轧制力波动幅值都较大,这是错层 卷原因的直接体现。
3 轧制力波动原因的查找
通过上述排查,我们明确了轧制力波动是造成 错层产生的直接原因。为了进一步了解轧制力波动 与错层产生之间的关系,明确造成错层的根本原 因,我们进行了下列试验。
铝带热轧过程中的跑偏分析及控制技术
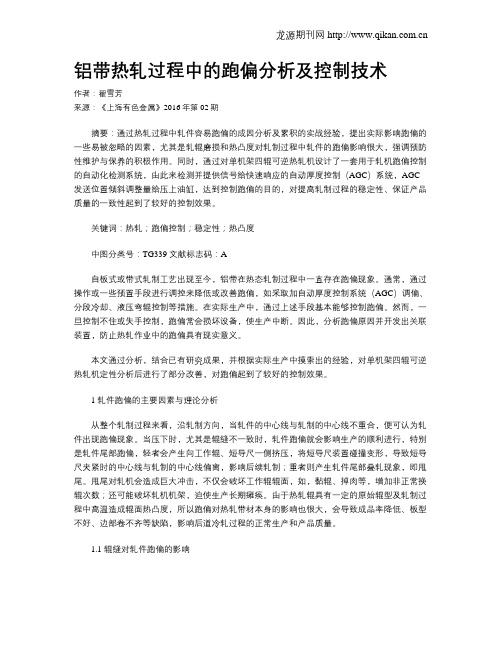
铝带热轧过程中的跑偏分析及控制技术作者:翟雪芳来源:《上海有色金属》2016年第02期摘要:通过热轧过程中轧件容易跑偏的成因分析及累积的实战经验,提出实际影响跑偏的一些易被忽略的因素,尤其是轧辊磨损和热凸度对轧制过程中轧件的跑偏影响很大,强调预防性维护与保养的积极作用。
同时,通过对单机架四辊可逆热轧机设计了一套用于轧机跑偏控制的自动化检测系统,由此来检测并提供信号给快速响应的自动厚度控制(AGC)系统,AGC 发送位置倾斜调整量给压上油缸,达到控制跑偏的目的,对提高轧制过程的稳定性、保证产品质量的一致性起到了较好的控制效果。
关键词:热轧;跑偏控制;稳定性;热凸度中图分类号:TG339 文献标志码:A自板式或带式轧制工艺出现至今,铝带在热态轧制过程中一直存在跑偏现象。
通常,通过操作或一些预置手段进行调控来降低或改善跑偏,如采取加自动厚度控制系统(AGC)调偏、分段冷却、液压弯辊控制等措施。
在实际生产中,通过上述手段基本能够控制跑偏。
然而,一旦控制不住或失手控制,跑偏常会损坏设备,使生产中断。
因此,分析跑偏原因并开发出关联装置,防止热轧作业中的跑偏具有现实意义。
本文通过分析,结合已有研究成果,并根据实际生产中摸索出的经验,对单机架四辊可逆热轧机定性分析后进行了部分改善,对跑偏起到了较好的控制效果。
1 轧件跑偏的主要因素与理论分析从整个轧制过程来看,沿轧制方向,当轧件的中心线与轧制的中心线不重合,便可认为轧件出现跑偏现象。
当压下时,尤其是辊缝不一致时,轧件跑偏就会影响生产的顺利进行,特别是轧件尾部跑偏,轻者会产生向工作辊、短导尺一侧挤压,将短导尺装置碰撞变形,导致短导尺夹紧时的中心线与轧制的中心线偏离,影响后续轧制;重者则产生轧件尾部叠轧现象,即甩尾。
甩尾对轧机会造成巨大冲击,不仅会破坏工作辊辊面,如,黏辊、掉肉等,增加非正常换辊次数;还可能破坏轧机机架,迫使生产长期瘫痪。
由于热轧辊具有一定的原始辊型及轧制过程中高温造成辊面热凸度,所以跑偏对热轧带材本身的影响也很大,会导致成品率降低、板型不好、边部卷不齐等缺陷,影响后道冷轧过程的正常生产和产品质量。
铝板带轧制常见故障分析及处理

2012-6-6
11
• b、原因分析 • ①、产生厚度中心点飘移的原因:出口测厚 仪测量数据不真实和操作人员对厚度中心点 设定不恰当所致。 影响出口测厚仪测量准确性的因素有:校 核测厚仪的标准板厚度不准确引起厚度中心 点设定不准确,测厚仪厚度补偿系数不准确 ;放射源发出的射线被其他物件所挡;测厚 仪自动清零功能不稳定。
2012-6-6
9
b、厚度控制
①FF-AGC:Feed-forward Automatic Gauge Control ②MF-AGC : Mass Flow - Automatic Gauge Control ③MV-AGC : Multi-Variable - Automatic Gauge Control ④MN-AGC : MoNitor - Automatic Gauge Control ⑤TLC : Tension Limit Control ⑥RE-AGC : Roll Eccentricity - Automatic Gauge Control
2012-6-6
24
1.3.6 自动板形控制
• 自动板形控制过程如下图
板形辊
分区冷却
弯辊控制
倾辊控制 板形检测 一次板形 二次板形 高次板形
板 形 控 制 调 节 器
目标板型
图1.
2012-6-6
自动板形控制系统过程图
25
1.3.7 板形问题案例
• 断带原因分析
2012-6-6
26
1.4 表面质量
• 出现板形不良的直接原因是轧件宽向上延 伸不均。
2012-6-6
20
• 出现板形不良的根本原因是:轧件在轧 制过程中,轧辊产生了有害变形,致使 辊缝形状不平直,从而产生波浪。
铜及铝板带轧制过程中轧机不稳定因素探讨

铜及铝板带轧制过程中轧机不稳定因素探讨铜及铝板带轧制是制造铜及铝材料的重要工艺之一,但在实际的生产过程中常常会遭遇到轧机不稳定的问题,这不仅影响了生产的进展,还可能导致铜及铝板带的质量问题。
因此,本文将探讨铜及铝板带轧制过程中轧机不稳定的因素。
1. 轧辊的磨损轧辊作为铜及铝板带轧制过程中最核心的部件之一,其磨损程度直接影响轧机的稳定性。
如果轧辊磨损过度,其直径和尺寸就会发生变化,这会导致轧辊的转速和轧制力的变化,进而影响铜及铝板带的轧制质量。
如果轧辊磨损严重,就需要更换新的轧辊或进行修复。
2. 机械结构的松动铜及铝板带轧制过程中,机械结构的松动也是导致轧机不稳定的因素之一。
如果轧机的主机、传动系统、承载系统等关键组件出现松动的情况,就会引发轧辊的晃动、振动等现象,导致铜及铝板带的轧制不稳定。
因此,在轧机工作前应对其各个部分进行彻底的检查和维护,确保机械结构的紧固和稳定。
3.滚道的磨损与变形滚道作为承载物的重要组成部分,直接关系到轧机的稳定性和铜及铝板带的轧制效果。
如果滚道出现磨损或变形,轧辊就会失去支撑,造成轧制力的不稳定,影响铜及铝板带的轧制效果。
因此,在日常的轧机维护中,需要对滚道进行定期检查和维护。
4. 温度的变化在铜及铝板带轧制过程中,温度是极其重要的因素之一。
如果轧机所处的环境温度过低或过高,就会对铜及铝板带的轧制造成影响。
高温环境容易导致轧辊扭曲变形;低温环境则可能导致轧辊表面出现冰霜,磨损程度增加。
因此,在铜及铝板带轧制过程中,需要控制好温度,确保轧机稳定工作。
铜及铝板带轧制过程中轧机不稳定的因素是多方面的,要想保证铜及铝板带的质量,需要从轧机的各个方面做好维护和管理。
轧制缺陷及质量控制

轧制缺陷及质量控制一、引言轧制是金属加工中的一种重要工艺,用于将金属块材变形成所需的形状和尺寸。
然而,在轧制过程中,由于材料的特性和操作条件的不同,会产生一些缺陷,如裂纹、气泡、夹杂物等,这些缺陷会降低产品的质量和性能。
因此,进行轧制缺陷的控制和质量的监控是非常重要的。
二、轧制缺陷的分类1. 表面缺陷:包括划痕、麻点、皮膜剥离等。
2. 内部缺陷:包括裂纹、气泡、夹杂物等。
三、轧制缺陷的原因1. 材料因素:材料的化学成分、结构和纯度等会影响轧制过程中的缺陷形成。
2. 设备因素:轧机的结构、参数设置、润滑和冷却等条件会对轧制缺陷产生影响。
3. 操作因素:操作人员的技术水平、操作规程的执行等也会对轧制缺陷产生影响。
四、轧制缺陷的控制方法1. 材料选择:选择质量好、纯度高的原材料,减少缺陷的可能性。
2. 设备维护:定期对轧机进行维护和保养,确保设备的正常运行。
3. 工艺控制:控制轧制的温度、速度、压力等参数,减少缺陷的产生。
4. 检测方法:使用先进的无损检测技术,如超声波检测、磁粉检测等,及时发现和修复轧制缺陷。
5. 培训与管理:加强操作人员的培训,提高其技术水平和质量意识,严格执行操作规程。
五、质量控制体系建立完善的质量控制体系对于轧制过程中的缺陷控制至关重要。
以下是一个典型的质量控制体系的组成部分:1. 质量目标:明确轧制产品的质量要求,包括物理性能、化学成分等指标。
2. 质量计划:制定轧制过程中的质量控制计划,包括检测方法、检测频率等。
3. 质量检测:通过各种检测方法对轧制产品进行全面的检测,及时发现缺陷并采取措施修复。
4. 不良品处理:对于出现缺陷的产品,及时进行分类、记录和处理,以防止不良品流入市场。
5. 过程改进:根据质量检测结果和不良品处理情况,对轧制过程进行改进和优化,提高产品质量。
6. 内部审核:定期进行内部审核,评估质量控制体系的有效性和符合性。
7. 外部认证:通过第三方机构的认证,证明质量控制体系符合相关标准和要求。
钢管轧制存在质量问题的原因及改进措施

一穿轧制存在的质量问题1、毛管外径偏大或偏小原因:①辊距偏大或偏小②导板板距偏大或偏小③顶头位置向前或靠后④顶头直径偏大或偏小⑤轧辊径向串动量太大⑥上导板座没有固定,上下跳动量大改进措施:根据轧制表的参数选择合适的辊距,导板距,顶头伸入量及顶头直径,加强轧辊和导板的固定,正常轧制时,辊距和导板距保证相对稳定,不能轻易调整,若钢管偏厚或偏薄,可采取进、退顶杆的方法。
2、壁厚严重不均原因:①一穿三个轧辊的外径大小不一②三个轧辊偏离轧制线③三个轧辊调整后不成等边三角形,轧辊前后距轧机牌坊距离不一致;④定心辊未抱住顶杆甩动严重⑤定心孔不对中⑥穿孔机受料槽、一穿轧机、定心机架、顶杆小车的机械中心线不对⑦轧辊轧制过程中跳动太大;⑧顶杆位置过后;⑨轧辊直径过小,轧制大规格钢管时产生滑动现象;改进措施:①安装轧辊时先要测量三个轧辊的辊径,保持三个轧辊的辊径一致;②调整轧制中心线,俣证轧制中心线与穿孔中心线重合,然后可使轧制中心线略低于穿孔中心线0-5mm;③将三个轧辊调整后成等边三角形,保证三个轧辊在轧制过程中受力一致,轧辊前后距牌坊距离一致;④调整定心辊,保证在空载时能抱住顶杆,并使顶杆的水平线与穿孔中心线重合;⑤保证定心孔对中;⑥要求设备测试中心线,保证穿孔机受料槽、一穿轧机、定心机架、顶杆小车的机械中心线在一条水平直线上;⑦临时用铁片调整间隙,保证跳动值不超标。
⑧调整到合适的顶杆位置;⑨更换轧辊,选择合适辊径的轧辊,当辊径小于一定值,予以报废。
3、头尾外径不一致(头大尾小)原因:①坯料加热温度不均匀,头部温度偏低;②穿孔过程中轧辊在辊箱中抖动③穿孔中误动作侧压进装置④管坯开始变形时顶头的轴向阻力加大,轴向延伸受阻,延伸变形减小,横向变形(扩径)加大⑤管坯尾部顶透时轴向阻力减小,使延伸变形容易,同时横向辗轧减小,因而尾部直径变小改进措施:按加热制度加热,保证钢温一致;采取措施固定轧辊,使轧辊在辊箱中不串动;提高操作水平,减少误动作,加强调整,保证轴向变形与横向变形同步。
铝箔轧制工艺影响因素研究

铝箔轧制工艺影响因素研究铝箔是一种非常常见的铝材制品,它具有轻质、导热性好、耐腐蚀等优点,因此在食品包装、医药包装、建筑材料等领域得到了广泛的应用。
铝箔的生产主要是通过铝箔轧制工艺来实现的,而铝箔轧制工艺的影响因素对于铝箔产品的质量和性能具有重要的影响。
本文将会从轧制工艺的角度对铝箔轧制工艺影响因素进行研究。
一、轧制工艺的影响因素铝箔轧制工艺是通过对铝材进行轧制来获得所需的薄板,其中影响铝箔轧制工艺的因素主要包括轧机设备、轧制参数和原料质量等几个方面。
1.轧机设备:轧机设备是影响轧制工艺的关键因素之一。
轧机的类型、品牌和性能都会对轧制工艺产生影响。
不同类型的轧机在轧制过程中所施加的压力、温度控制等方面会有所不同,因此对于轧制工艺来说选择合适的轧机设备十分重要。
2.轧制参数:轧制参数包括轧制温度、轧制速度、轧辊间距等参数。
不同的轧制参数对于铝箔的质量、表面光洁度、厚度均匀性等方面会产生影响。
轧制温度是一个非常重要的参数,过高或者过低的温度都会影响铝箔的性能。
轧制速度也会影响铝箔的机械性能和表面质量。
3.原料质量:铝箔的原料主要是铝卷料,因此原料的质量对于铝箔的质量也有着重要的影响。
原料质量的好坏不仅会影响铝箔的表面光洁度和机械性能,还会影响轧制工艺的稳定性。
二、影响因素的研究1.轧机设备的选择轧机设备的选择对于铝箔的轧制工艺具有至关重要的影响。
不同类型的轧机具有不同的轧制性能,对于不同规格和要求的铝箔产品需要选择合适的轧机设备来进行轧制。
对于小规格的铝箔产品可以选择冷轧机进行轧制,而对于大尺寸、高强度的铝箔产品则需要选择热轧机进行轧制。
轧机的性能也会影响轧制的稳定性和质量。
通过研究铝箔轧制工艺的影响因素,可以对铝箔产品的生产工艺进行优化,提高产品的质量和性能,满足市场需求。
三、研究展望随着铝箔产品在食品包装、医药包装等领域的不断应用,对于铝箔产品的质量和性能要求也在不断提高。
因此铝箔轧制工艺的研究将会成为一个重要的课题。
铝箔轧制缺陷产生的原因和解决措施
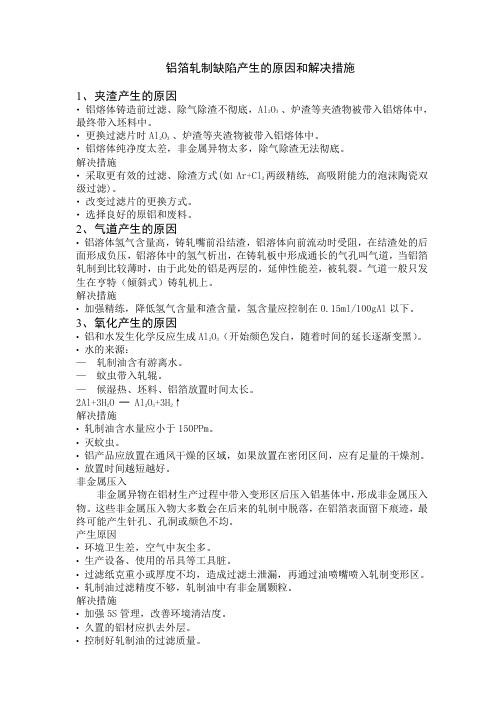
铝箔轧制缺陷产生的原因和解决措施1、夹渣产生的原因• 铝熔体铸造前过滤、除气除渣不彻底,Al2O3 、炉渣等夹渣物被带入铝熔体中,最终带入坯料中。
• 更换过滤片时Al2O3 、炉渣等夹渣物被带入铝熔体中。
• 铝熔体纯净度太差,非金属异物太多,除气除渣无法彻底。
解决措施• 采取更有效的过滤、除渣方式(如Ar+Cl2两级精练, 高吸附能力的泡沫陶瓷双级过滤)。
• 改变过滤片的更换方式。
• 选择良好的原铝和废料。
2、气道产生的原因• 铝溶体氢气含量高,铸轧嘴前沿结渣,铝溶体向前流动时受阻,在结渣处的后面形成负压,铝溶体中的氢气析出,在铸轧板中形成通长的气孔叫气道,当铝箔轧制到比较薄时,由于此处的铝是两层的,延伸性能差,被轧裂。
气道一般只发生在亨特(倾斜式)铸轧机上。
解决措施• 加强精练,降低氢气含量和渣含量,氢含量应控制在0.15ml/100gAl以下。
3、氧化产生的原因• 铝和水发生化学反应生成Al2O3(开始颜色发白,随着时间的延长逐渐变黑)。
• 水的来源:— 轧制油含有游离水。
— 蚊虫带入轧辊。
— 候湿热、坯料、铝箔放置时间太长。
2Al+3H2O ═ Al2O3+3H2↑解决措施• 轧制油含水量应小于150PPm。
• 灭蚊虫。
• 铝产品应放置在通风干燥的区域,如果放置在密闭区间,应有足量的干燥剂。
• 放置时间越短越好。
非金属压入非金属异物在铝材生产过程中带入变形区后压入铝基体中,形成非金属压入物。
这些非金属压入物大多数会在后来的轧制中脱落,在铝箔表面留下痕迹,最终可能产生针孔、孔洞或颜色不均。
产生原因• 环境卫生差,空气中灰尘多。
• 生产设备、使用的吊具等工具脏。
• 过滤纸克重小或厚度不均,造成过滤土泄漏,再通过油喷嘴喷入轧制变形区。
• 轧制油过滤精度不够,轧制油中有非金属颗粒。
解决措施• 加强5S管理,改善环境清洁度。
•久置的铝材应扒去外层。
• 控制好轧制油的过滤质量。
废料(断带)产生原因•断带后碎铝箔未处理干净,附在机架内,轧制时入口侧的碎铝箔掉下,被带入轧制变形区,造成该区域铝箔变形不均而压裂(正常区域只有两层铝箔,有废料的区域至少三层),产生断带现象。
轧机打滑的原因

轧机打滑的原因轧机打滑是指在轧制过程中,轧辊与卷料之间失去正常的摩擦力,导致轧制效果不佳或无法进行轧制的现象。
轧机打滑的原因有多种,主要包括以下几点:1. 材料粘附:轧机打滑的一个常见原因是卷料表面粘附有杂质或润滑剂,使得轧辊与卷料之间的摩擦力降低。
例如,在冷轧过程中,卷料表面可能存在油脂、氧化物或氧化皮等物质,这些物质会降低轧辊与卷料之间的摩擦力,导致轧机打滑。
2. 轧辊表面磨损:轧辊表面的磨损程度会直接影响轧机的轧制效果。
当轧辊表面磨损严重时,轧辊与卷料之间的接触面积减小,摩擦力也会相应减小,从而导致轧机打滑。
轧辊表面磨损的原因可以是长时间使用、使用不当或轧辊材质质量不合格等。
3. 轧辊与卷料之间的润滑不良:轧机正常运行需要一定程度的润滑,以减小摩擦力并防止轧辊表面磨损。
如果轧辊与卷料之间的润滑不良,例如润滑油不足或润滑剂质量不合格,会导致轧机打滑。
4. 轧机设备故障:轧机设备本身的故障也可能导致轧机打滑。
例如,轧机传动系统出现故障、轧机辊系间隙不合适或轧辊安装不稳定等,都可能导致轧机打滑。
5. 工艺参数调整不当:轧机打滑还可能与工艺参数的调整不当有关。
例如,轧机的轧制速度过快,轧辊与卷料之间的摩擦力无法及时传递,导致轧机打滑。
此外,轧机的轧制压力、温度等参数也需要根据具体情况进行调整,以确保正常的轧制效果。
针对轧机打滑的原因,可以采取一些措施来解决:1. 清洁卷料表面:在轧制之前,可以通过清洗、酸洗等方法清除卷料表面的杂质和润滑剂,以减少轧机打滑的可能性。
2. 维护轧辊表面:定期对轧辊进行磨削和抛光,以保持轧辊表面的平整度和光滑度,减小轧机打滑的风险。
3. 使用合适的润滑剂:选择合适的润滑剂,并根据轧机要求进行适量的润滑。
润滑剂应具有良好的润滑性能和附着性,以保证轧机的正常运行。
4. 定期维护和检查轧机设备:对轧机设备进行定期的维护和检查,及时发现并修复可能存在的故障,以确保轧机的正常运行。
- 1、下载文档前请自行甄别文档内容的完整性,平台不提供额外的编辑、内容补充、找答案等附加服务。
- 2、"仅部分预览"的文档,不可在线预览部分如存在完整性等问题,可反馈申请退款(可完整预览的文档不适用该条件!)。
- 3、如文档侵犯您的权益,请联系客服反馈,我们会尽快为您处理(人工客服工作时间:9:00-18:30)。
文件编号:TP-AR-L3168
In Terms Of Organization Management, It Is Necessary To Form A Certain Guiding And Planning Executable Plan, So As To Help Decision-Makers To Carry Out Better Production And Management From Multiple Perspectives.
(示范文本)
编订:_______________
审核:_______________
单位:_______________
铜及铝板带轧制过程中轧机不稳定因素探讨(正
式版)
铜及铝板带轧制过程中轧机不稳定
因素探讨(正式版)
使用注意:该安全管理资料可用在组织/机构/单位管理上,形成一定的具有指导性,规划性的可执行计划,从而实现多角度地帮助决策人员进行更好的生产与管理。
材料内容可根据实际情况作相应修改,请在使用时认真阅读。
在铜及铝板带轧制过程中难免会发生不稳定现
象,导致这种现象的原因较多,其问题主要集中在轧
机上,从而对带材高精度生产造成严重影响。
由于有
色金属板的性能区别于钢铁的性能,因此对轧机的要
求有所不同。
本研究中,笔者对轧机轧制过程中不稳
定现象从工艺、设备等的角度进行分析,以供同行工
作者参考。
当前,随着科学技术的日益发展,在有色金
属的加工技术中,对板带材精度和质量随之提出了更
高的要求。
为确保轧机轧制在板带轧制过程中的稳定
性,消除外扰因素很重要,只有认真发现铜及铝板带轧制过程中存在的一些问题,才能消除由于这些不稳定因素的发生导致产品质量出现问题的现象。
轧机系统稳定性受轧制材料的质量的影响
1.1轧制过程中发生辊颤与材料相关
采用铸轧坏料在铝粗轧机进行轧制的调试时,通常采用轧制速度及压下量等常规轧制工艺参数,整个轧机有时会发生颤动的现象,这使工艺参数的调整受到影响。
出现这种现象主要是因铸轧坯料铸轧后表面氧化膜化厚,其主要因放置时间较长所致,材料表面性能及其内部组织在长时间后均会发生变化,使轧材与辊面的摩擦系统不断降低,再加上摩擦力与咬入力小较,而导致打滑的现象发生,而导致轧辊颤振。
1.2来料偏差不宜过大
一般试验过程中经常采用厚度偏差不同的带坯,而轧制厚度偏差的带坯为0.1~0.12mm时,相比0.15mm的轧制厚差带坯,轧机稳定性较高。
轧机系统稳定性受工艺润滑剂的影响
经常发生辊颤还有一个重要原因是由于润滑剂与所选择的工艺参数不匹配,对于轧机系统的振动因被轧金属与辊缝处辊面之间的摩擦因素而受到影响主要体现在以下几个方面:(1)在轧机系统的垂直运动中辊缝的润滑油膜能起到一定的阻尼作用,其阻尼作用在油膜摩擦系数越低的情况下越小,则会降低系统的稳定性质,轧机在外部等量扰动的情况下极易发生振动;(2)在充分润滑的条件下,会减小辊缝摩擦,而在干扰因素不稳定的情况下,辊缝状态的波动会增大,则会严重影响到系统的稳定性;(3)辊缝的摩擦系数越小,轧机轧制压力所受到的摩擦压
力也就越小,轧制压力受到轧制张力的影响也就越大,从而会降低轧机系统的稳定性,使轧机容易发生振动。
从上述分析中可以看出:轧机在辊缝摩擦系数较小的情况下容易发生振动。
轧机系统稳定性受轧制速度的影响
厂在调试一台冷轧机过程中,可看到轧机有严重的辊颤现象。
对轧机各部分性能进行检查,发现问题出现在轧制时轧机速度上,如将速度设定在
4m/s时,其始终保持着3.9~4.1的传动速度,期间有出现周期性摆动,而导致轧机辊颤,并且有带材厚薄不均的现象。
通过对轧机主传动和卷取机电气反复调整后,在速度稳定的情况下,消除了辊颤的现象。
轧机系统的稳定性及其外部的扰动能量决定着其是否会发生自激振动,轧机系统会受到轧机轧
制速度高低的影响,其主要体现在:(1)在轧制速度不断提高的情况下,轧机周围会有越来越多的扰动因素,并且扰动强度也越来越高,那么要确保其平稳就必须保证其速度较低;(2)轧制速度较低时,轧机谐振频率会高于外扰频率,不容易出现共振;而当轧制速度越高的情况下,其工作辊入口张力变化与运动的关系将越紧密,系统的自激关系也就越强烈,从而会增强各种外扰频率,轧机系统稳定性越差的情况下,便容易出现振动。
此外,轧机辊缝中的润滑情况也会受到轧制速度的影响。
润滑液膜在速度越高的情况下厚度越大,因此在辊缝一定时,带材的厚度公差会直接受到速度高低的影响。
轧机系统稳定性受压辊压力和轧机刚度不足的影响
4.1压辊压力不足
通常轧辊前后均有压紧辊,该辊组会有一定的压紧力,否则在带材跳动的情况下容易产生轧机辊颤。
4.2轧机刚度不足
随着液压下补偿功能的日趋完善,通常设计者为了使设备重量减轻,而对于轧机自然刚度设计较小。
这样一来必然会导致来料带材的硬度或厚度出现不均,轧机在轧制过程中会增大其受力波动振幅,即使得到一定的补偿,也会影响到轧机的稳定性。
轧机系统稳定性受轧辊磨削精度的影响
轧机是否稳定同样受轧辊磨削精度的影响,通常来说轧机会受到工作辊的圆柱度、圆度的影响。
理论上来说这一扰动因素可用轧辊偏心补偿进行消除。
但实际上无论是进口轧机还是国产轧机都很难消除这一干扰,而要减小其干扰采取的主要措施是提
高磨削精度,在提高轧速速度的情况下,扰动频率会随之升高。
为减少周期性扰动,以避免辊径出现对称磨损,允许磨制两个支承辊时其辊径有一定的差值,这样可以避免因辊型而导致轧机发生颤动。
如以带钢轧机为例,要避免轧机因“诱导速度”而导致“第二种垂直振动”的发生,在速度为700~1700m/min,高频频率为577Hz的情况下,辊径差应保持在2~
6mm之间。
防止和解决辊颤现象的最好方法是合理分配轧制道次
以一台设计刚投产的轧机为例,在调试阶段并未出现辊颤,而在投产后出现辊颤,引起辊颤的原因除了轧辊磨制存在问题以外,还由于道次压下量未合理分配所致。
在可逆轧制时,无论是单机架HC 轧机、六辊CVC轧机或单机架四辊轧机、20辊轧
机,其张力和道次分配必须合理才能避免辊颤的发生。
四辊轧机工作辊传动稳定分析
在铜及铝板带生产过程中四辊轧机通常是最常用的轧机,我们就以四辊轧机为例做传动稳定分析。
在四辊轧机工作辊传动过程中,若充分考虑到工作辊与支承辊轴承处的摩擦力及其滚动摩擦的影响,支承辊上的支反力与摩擦圆半径相切,并在工作辊与支承辊偏离0.1~0.3m的滚动摩擦力臂的距离,而在两者之间的压扁弧上所建立的是支承辊与工作辊之间的摩擦力。
根据以上公式中得出以下结论:
(1)通常情况下T0>T1,,e=3~10mm,一般按照e0>e进行校核。
为避免对工作辊产生较大
的水平力,要确保e值不能太大。
(2)可逆轧制时,一般工作辊偏移向出口端或向入口端,具有相同的效果。
在e0>e的条件下,应确保无论反向轧制或正向轧制,T0>T1。
(3)在向不带张力轧制的情况下,e。
(临界偏移距)为负值。
通常向出口方向偏移一个数值,以增强工作辊的稳定性。
对于以上的理论分析只作用于轧机校核,如果从工艺计算来进行分析,使轧辊辊面与轧制金属之间的摩擦系数要大于轧制时轧制力与轧制切向分力之比是防止轧辊颤振的最有效方式。
通常来说,这样便能确保轧制过程的稳定性。
所以,无论是两辊轧机还是多辊轧机,对于这一问题在工艺计算中都必须充分考虑。
总之,轧机系统的不稳定性是因多方面影
内部管理系列 | INTERNAL MANAGEMENT 编号:TP-AR-L3168响所致,在轧制过程中轧机系统发生不稳定性时,要从多方面进行具体分析,处理过程中才能对症下药,才能使轧机可以生产出高质量的产品。
此处输入对应的公司或组织名字
Enter The Corresponding Company Or Organization Name Here
第2页。