ERP产品成本估算完整版
(ERPMRP管理)MRP估算及成本结算技术文件
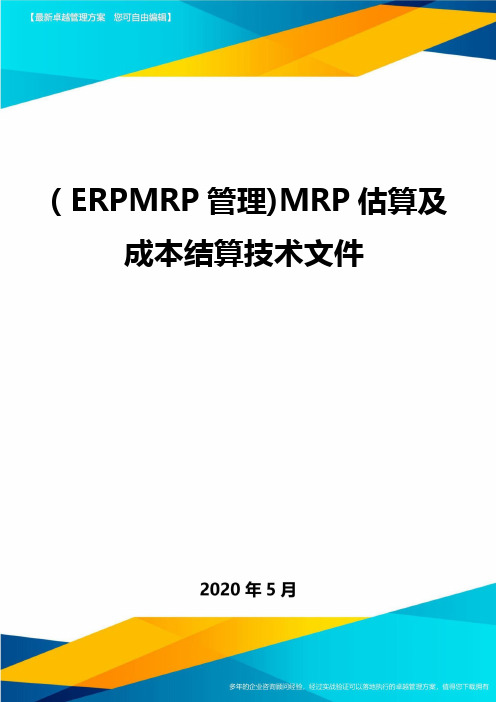
(ERPMRP管理)MRP估算及成本结算技术文件工厂达人MRP估算及成本结算技术文件说明:本文主要讲解工厂达人的MRP估算的使用方法,及使用系统结算成本时,系统如何设置,财务如何做账。
附:整个业务流程中各种单据在财务的做账时机及凭证科目一.基本流程:4.2.1二.基础设定1.系统设定1-1“成本核算方式”设定:用于生产型企业时成本核算方式取用“月加权平均”。
备注:移动加权平均成本单位成本=月加权平均成本单位成本=1-2“生产成本确认方式”设定:此处有手动计算和系统计算两种方式提供选择,此讲义为选择系统计算。
MRP选项的设置,影响MRP估算的计算。
1-3“费用分摊材料成本”设定:此处提供“取产品标准成本”和“取产品现行平均成本”两种方式进行选择,用户可根据企业的实际情况和需求进行选择。
1-3-1当选择“取产品标准成本”时,做《费用分摊单》时,若费用分摊方式选择“按材料成本”时,此时的材料成本计算方式为“取产品标准成本”。
1-3-2当选择“取产品现行平均成本”时,做《费用分摊单》时,若费用分摊方式选择“按材料成本”时,此时的材料成本计算方式为“取产品现行平均成本”。
2.其它设定2-1会计科目设定:2-1-1生产成本科目:生产成本科目可根据企业实际情况和会计作帐原则,在符合国家会计制度的要求下进行设制。
此处我们共建立四个生产成本科目,分别是:2-1-2制造费用科目:制造费用是除直接材料、直接人工之外的一切生产成本,一般包括水、电、气、折旧费,管理人员的薪资、其它易耗品等等。
制造费用无法直接计入成本,费用发生时分别记帐,月底时将需要分摊的部分归集到辅助生产成本科目下的制造费用科目,再分摊到本月生产的产品中。
制造费用科目的设定可根据企业的实际情况进行设定。
2-2自动转帐设定:所有制造费用在发生时都是分科目进行记帐,月底时统一将所有制造费用科目结转到“辅助生产成本—制造费用”科目中。
系统提供了“自动转帐”功能,协助您每月月底时,自动生成这张结转凭证。
ERP系统与成本管理一成本管理
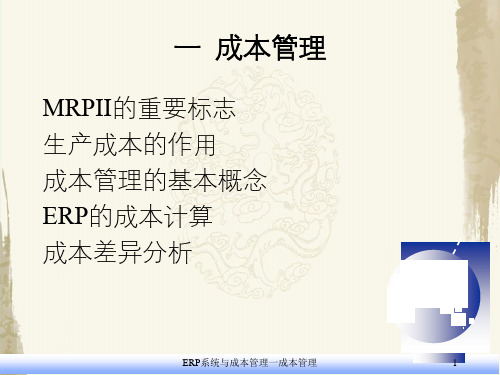
F 根据以上信息,可以预见未来所需的材 料费及人工费。再考虑应付款的付款期 限,从而得到准确的现金流计划。
ERP系统与成本管理一成本管理
30
财务管理的转变
F 对产生派工单的未完成订单核算成本即可得出 当前在制品的价值。工时报告和派工单结合在 一起,可以作为工时效率考核的基础。
ERP系统与成本管理一成本管理
23
成本差异分析与成本控制
F 直接材料成本差异 F 直接人工成本差异 F 制造费差异
ERP系统与成本管理一成本管理
24
直接材料成本差异
F 直接材料成本差异等于材料的实际用量 与实际价格的乘积减去标准用量与标准 价格的乘积所得的差。造成这种差异既 有价差的原因,也有量差的原因。如采 购价格和运输费用的变化,材料代用或 变更,自制件改外购件或反之等等皆为 价差原因。而材料报废或损耗,材料利 用率变化,产品结构变化等等均为量差 原因
– 成本= 材料费(采购件费)+ 采购间接费(采购部 门的管理费、运输及保管费等)
– 其中采购间接费=采购件费×采购间接费率
F 本层发生的成本=直接人工费 + 制造费
– 直接人工费=工作中心记录的人工费率×工艺路线记 录的工时数
– 制造费=工作中心记录的制造费率×工艺路线记录的 工时数
ERP系统与成本管理一成本管理
ERP系统与成本管理一成本管理
16
制造费
F 是指企业各生产单位为组织和管理生产而发生 和各项间接费用。包括管理人员工资和福利费 、车间房屋建筑和机器设备的折旧费、租赁费 、修理费、办公费、水电费、燃料费、动力费 、机物料消耗、劳动保护费等。
F 在制造费用中,与产量有直接关系的称为可变 制造费用,如燃料与动力、机物料消耗等;与 产量无直接关系的称为固定制造费用,如管理 人员工资、办公费、修理费、折旧费、采暖费 、照明费等
erp 成本核算流程

erp 成本核算流程ERP 成本核算流程在当今的企业管理中,ERP(Enterprise Resource Planning,企业资源计划)系统已成为提升运营效率和管理精度的重要工具。
其中,成本核算流程是ERP 系统中的关键环节,它直接影响着企业的成本控制、决策制定以及盈利能力。
接下来,让我们详细了解一下 ERP 成本核算流程。
一、基础数据准备这是成本核算的前置工作,就像盖房子要先打好地基一样。
首先,要确保各类物料的主数据准确无误,包括物料编码、名称、规格、计量单位等。
这些数据的准确性直接关系到成本计算的准确性。
同时,还需要维护好工作中心、工艺路线等数据。
工作中心是指完成特定作业的场所或设备,而工艺路线则规定了产品在各个工作中心的加工顺序和消耗的工时。
另外,员工的薪资数据、设备的折旧费用等间接成本的相关信息也不能有差错。
二、成本中心的设置成本中心是企业中能够归集成本的单元。
可以按照部门、车间、生产线等进行划分。
通过合理设置成本中心,可以清晰地了解各个部门或环节的成本消耗情况。
比如,生产部门可以设置为一个成本中心,用于归集直接材料、直接人工和制造费用;而行政管理部门则可以作为另一个成本中心,归集管理费用。
三、成本要素的定义成本要素就像是把成本进行分类的标签。
常见的成本要素包括直接材料、直接人工、制造费用等。
直接材料是指构成产品实体的原材料,其成本容易直接追溯到具体的产品上。
直接人工是指直接参与产品生产的工人工资及相关福利。
制造费用则是那些无法直接追溯到产品上的间接生产费用,如车间水电费、设备维修费等。
四、成本核算方法的选择企业可以根据自身的生产特点和管理需求,选择合适的成本核算方法。
常见的有品种法、分批法、分步法等。
品种法适用于大量大批、单步骤生产的企业,比如发电、采掘等。
分批法适用于单件小批生产的企业,如船舶制造、专用设备制造等。
分步法适用于大量大批、多步骤生产的企业,如纺织、冶金等。
五、材料成本核算当原材料被领用投入生产时,ERP 系统会根据预先设定的计价方法(如先进先出法、加权平均法等)计算材料成本,并将其分配到相应的产品或生产订单上。
ERP系统成本核算原理及方法

ERP系统成本核算原理及方法企业资源计划(ERP)是个较完整的集成化管理信息系统,实现了采购、销售、生产、库存等与财务的集成,实现了资金流与物流的同步和一致,提高了成本核算的准确性和及时性。
在采购、销售、生产等业务与财务的集成中,生产与财务的集成(即成本集成)是最难的。
在我国一些已经实施了ERP的企业中,实施了业务与财务集成的企业很少,而实施了成本集成的企业更是寥寥无几。
成本集成是ERP系统实施的难点,本文将论述ERP系统的成本计算原理,并以国际著名的ERP软件BAAN IV为参考,以离散型企业为背景,提出成本集成的会计处理方法。
一、ERP系统成本计算原理物料清单(Bill of Material,简称BOM)又称产品结构,不但列明了生产某一种产品需要的全部物料,而且将所有的物料(原材料、零件、部件、产品)按实际生产装配过程进行分层排列,这种层次关系反映了物料的加工顺序和物料之间的需求关系。
物料清单不但标明了每种物料的层次、编号、规格、单位,而且列出了每种物料在该产品中的用量标准;不但考虑了所需的原料、毛坯、消耗品,而且考虑了产品产出率、废品率。
在ERP系统中,物料清单既是运算物料需求、编制物料采购和生产计划的基础,也是进行成本计算的基础。
在BOM中,最顶层的物料为产品,最底层的物料为采购物料,其他物料为制造物料,产品按BOM由底层到高层的顺序进行加工装配。
对于离散型企业,ERP系统的成本计算采用分项逐步结转分步法,按照产品加工步骤的先后顺序,逐步计算并结转半成品成本,前一步骤的半成品成本,随着半成品实物的转移结转到后一步骤的产品成本中,直到最后步骤累计计算出产品成本。
二、ERP系统成本核算方法ERP系统每一种制造物料(包括半成品、产成品)的加工和装配都要生成相应的生产订单,通过生产订单来进行管理。
生产订单的处理步骤包括:生产订单的生成、生产订单的下达、发料、报告工时、报告完工、产品入库、订单结算等。
ERP成本计算方法(转)

ERP成本计算方法(转)企业在实际工作中,往往每个月都要进行成本统计。
但每当月末时,不可能每个成品都已经完工,但相关的费用可能已经支出,如员工的工资、车间的固定支出等等。
这些费用若全部计算到在成品中,明显不是很合理。
ERP软件设计师们为了满足企业的这一需求,根据企业的常见处理方式,实现了多种分配方式。
在此,笔者将陆续介绍一些常见的处理方式在ERP系统中的体现,同时列出操作过程中常见的一些问题。
约当产量法是在企业应用中最广,也是最能反映实际情况的做法。
现在大部分ERP产品都支持这种方法。
所谓约当产量,是指在产品按其完工程度折合成完工产品的数量。
比如,在产品50件,平均完工程度为60%,则相当于完工30件。
案例一:某产品本月完工26件,在产品10件,平均完成程度为40%,共发生成本支出3000元。
则,本月完工的产品,应承担多少比例的成本?根据约当产量的计算规则,本月完工产品相当与是26件+10件*40%=30件。
则每个产品本月发生的成本为3000元/30件=100元。
ERP操作要点:采取这种方式,道理不难理解,ERP也比较容易实现。
但是,在ERP实际操作中,可能会遇到一些问题。
1、完工程度如何测定?从以上的原理分析中,我们可以看到,必须要有产品的平均完工程度,ERP系统才能够算出本月的约当产量。
这个平均完工程度如何测算呢?是ERP系统所关心的问题。
结合实际的操作,ERP一般有以下几种做法:(1)人为的设置。
有些企业的做法是,无论其实际完工程度为多少,在月末,在产品的完工程度都为50%。
按照这种方法的话,案例一的本月完工成品即为31件。
可见,跟实际发生的成本有点差异。
一般用于单位产品成本差异不是很大,平均完工程度难以测量的情况下使用,还是蛮有效的。
(2)在系统成本结转前,根据实际情况反映到系统中去。
每到月末,生产管理人员去现场实际查看,然后算出完成程度,再输入到系统中去,然后让系统进行运算。
如此做的好处是能够反映实际情况,缺点就是工作量比较大,特别是本月在产品种类比较多时,工作量会很大。
ERP需求-成本

ERP專案系統功能需求表
評比: 5分: 功能完整,具彈性、擴充性 4分: 功能完整,但無彈性 3分: 雖不完整,但可套用 2分: 需小幅修改 1分: 需大幅修改
ERP專案系統功能需求表
評比: 5分: 功能完整,具彈性、擴充性 4分: 功能完整,但無彈性 3分: 雖不完整,但可套用 2分: 需小幅修改 1分: 需大幅修改
ERP專案系統功能需求表
評比: 5分: 功能完整,具彈性、擴充性 4分: 功能完整,但無彈性 3分: 雖不完整,但可套用 2分: 需小幅修改 1分: 需大幅修改
ERP專案系統功能需求表
評比: 5分: 功能完整,具彈性、擴充性 4分: 功能完整,但無彈性 3分: 雖不完整,但可套用 2分: 需小幅修改 1分: 需大幅修改
ERP專案系統功能需求表
評比: 5分: 功能完整,具彈性、擴充性 4分: 功能完整,但無彈性 3分: 雖不完整,但可套用 2分: 需小幅修改 1分: 需大幅修改。
erp成本计算方法

ERP中价值流的体现——管理会计中几种成本计算方法分析---- 无论是否实施了ERP系统,在实际的企业运作过程中,都经常会碰到一些尴尬的情况。
例如销售人员总是有一些例外的订单交给生产部门,而生产部门却又无法及时按要求生产,最后都归咎于生产部门。
针对这种情况,企业管理者作了如下改革:将例外订单的生产成本责任中心由生产部门变成销售部门,生产部门只负责根据例外订单的要求圆满完成生产任务。
这样的改变使得销售人员不再随便签定例外订单,即使签定例外订单,也要有很高的利润。
如此一来,企业既可以按计划生产,又可以在真正需要例外生产的时候,经销售人员进行成本计算后按客户要求生产,从而在企业内部建立了良好的团队合作精神,使企业能够轻松面对不断变化的市场。
---- 通常,管理者将企业的研究开发、设计、生产、营销、配送和售后服务等职能看作一个价值链,产品通过整个过程的流动,体现出其附加价值。
价值链被视为一个整体,管理者控制着整个价值流的总成本。
在上面例子中,例外订单生产成本责任中心的改变,实际上是管理者对价值流控制与计划的体现。
---- 在ERP系统中,价值流的体现主要通过管理会计来表现。
通过管理会计模块,可以方便地查询公司的成本构成和各种影响因素,帮助工程师分辨出可降低成本的高价值活动,为管理人员提供管理决策依据。
管理会计通过制定标准(Standards)、预算(Budgets)和分析差异(Variances)的方法进行经营管理、解释经营结果。
由于制定标准需要采集准确数据,需要ERP其它模块的数据支持,因此在ERP实施过程中,一般将CO(Controlling)模块放在第二个阶段或更后一些时候实施。
管理会计与财务会计的区别---- 财务会计主要为企业外部的决策者——投资者、债权人和政府有关部门提供信息,---- 管理会计主要为满足企业内部管理者对会计信息的需要,行使计划、控制与决策职能。
区别见图表1。
---- 在表1中我们可以了解到,管理者和会计师更加关注预算和其他管理会计方法。
易飞ERP高级成本计算
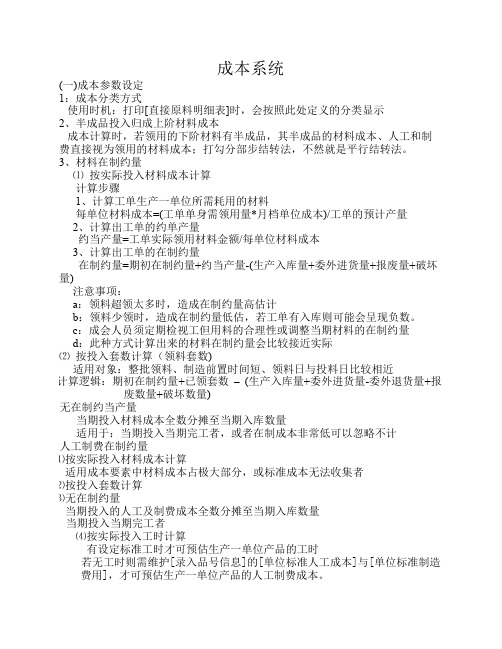
成本系统(一)成本参数设定1:成本分类方式使用时机:打印[直接原料明细表]时,会按照此处定义的分类显示2、半成品投入归成上阶材料成本成本计算时,若领用的下阶材料有半成品,其半成品的材料成本、人工和制费直接视为领用的材料成本;打勾分部步结转法,不然就是平行结转法。
3、材料在制约量⑴ 按实际投入材料成本计算计算步骤1、计算工单生产一单位所需耗用的材料每单位材料成本=(工单单身需领用量*月档单位成本)/工单的预计产量2、计算出工单的约单产量约当产量=工单实际领用材料金额/每单位材料成本3、计算出工单的在制约量在制约量=期初在制约量+约当产量-(生产入库量+委外进货量+报废量+破坏量)注意事项:a:领料超领太多时,造成在制约量高估计b:领料少领时,造成在制约量低估,若工单有入库则可能会呈现负数。
c:成会人员须定期检视工但用料的合理性或调整当期材料的在制约量d:此种方式计算出来的材料在制约量会比较接近实际⑵ 按投入套数计算(领料套数)适用对象:整批领料、制造前置时间短、领料日与投料日比较相近计算逻辑:期初在制约量+已领套数– (生产入库量+委外进货量-委外退货量+报废数量+破坏数量)⑶ 无在制约当产量当期投入材料成本全数分摊至当期入库数量适用于:当期投入当期完工者,或者在制成本非常低可以忽略不计4、人工制费在制约量⑴按实际投入材料成本计算适用成本要素中材料成本占极大部分,或标准成本无法收集者⑵按投入套数计算⑶无在制约量当期投入的人工及制费成本全数分摊至当期入库数量适用于:当期投入当期完工者⑷按实际投入工时计算有设定标准工时才可预估生产一单位产品的工时若无工时则需维护[录入品号信息]的[单位标准人工成本]与[单位标准制造费用],才可预估生产一单位产品的人工制费成本。
若公司有标准公司为依据,还需用考虑[工资率与制费分摊]标准:取[录入工作中心]的标准工资率及标准制费分摊率实际:取[录入工作中心成本]的单位人工及单位制费计算逻辑:半成品归上阶If 工艺管理子系统->录入工单工艺->标准工时 <> 0 thenBeginIf 成本计算子系统->设置成本子系统参数->工资率与制费分摊依据= 标准 then标准:取[录入工作中心]的标准工资率及标准制费分摊率单位人工 = [录入工作中心]的标准工资率单位制费 = [录入工作中心]的标准制费分摊率Else实际:取[录入工作中心成本]的单位人工及单位制费单位人工 = [录入工作中心成本]的单位人工单位制费 = [录入工作中心成本]的单位制费If 基本信息子系统->录入工作中心->制费分摊依据 = 人时Begin每单位人工制费=[(标准人时*单位人工)+(标准人时*单位制费)]/工单的预计产量End;If 基本信息子系统->录入工作中心->制费分摊依据 = 机时Begin每单位人工制费=[(标准人时*单位人工)+(标准机时*单位制费)]/工单的预计产量End;If 基本信息子系统->录入工作中心->制费分摊依据 = 人时Begin每单位人工制费=[(标准人时*单位人工)+(标准人时*单位人工*单位制费)]/工单的预计产量End;约当产量=(本期投入人工成本+本期投入制造费用)/每单位人工制费在制约量= 期初在制约量+约当产量-(生产入库量(委外进货量)+报废数量+破坏数量)End ElseBeginIf 产品结构子系统->录入产品工艺路线->标准工时 <> 0 then计算原理同上ElseBegin必须输入 存货管理子系统->录入品号信息->单位标准人工成本、单位标准制造费用每单位人工制费 =单位标准人工成本+单位标准制造费用End;End;5、加工费用在制约约量⑴按实际投入材料成本计算适用成本要素中材料成本占制造成本的大多数,或标准加工费用无法收集者⑵ 按投入套数计算(领料套数)⑶ 无在制约当产量当期投入加工费用全数分摊到当期入库数量适用于:当期投入当期完工者⑷按标准成本加工费用计算每单位加工费用计算时会抓取[录入品号信息]的[会计]页签字段几个条件:[半成品投入归上阶材料成本]是否勾选及工单是否有走工艺管理子系统计算逻辑计算工单生产一单位所须加工费用If 有使用工艺系统 thenBeginIf半成品归上阶材料成本未勾 thenBegin说明:本阶投入的加工费用可能还在其他工艺尚未入库 而下阶段所投入的加工费用不归上阶材料成本因此也要同时计算在制每单位加工费用= 标准加工费用End;If半成品归上阶材料成本勾选 thenBegin说明:本阶投入的加工费用可能还在其他工艺尚未入库而需要计算在制 而下阶段所投入的加工费用已归上阶材料成本了,因此没有下阶加工费要计算 每单位加工费用= 本阶加工End;End ElseBeginIf半成品归上阶材料成本未勾 thenBegin说明:本阶所发生的加工费用已经全数入库了,所以只需要计算下阶的在制就可以了下阶的每单位加工费用= 标准加工费用- 本阶加工End;If半成品归上阶材料成本勾选 thenBegin说明:本阶所发生的费用已经全数入库,所以已无在制 ,而下阶投入的加工费用又因为已归上阶材料成本了,所以也没有下阶的加工费用每单位加工费用= 0End;End;约当产量=工单实际加工费用/每单位加工费用在制约量=期初在制约量+约当产量-(生产入库量(委外进货量)-委外退货量-报废数量-破坏数量)范例:1Z--1X、1Y 若预计外包生产100Z,Z的单位标准加工为35元,当月份支付加工费用为2000元,且无完工进货数量,则加工费用在制约量?使用工艺系统且半成品归上阶材料成本未勾答:每单位加工费用=品号信息[标准加工费用]=35约当产量 = 2000/35 = 57.14在制约量 = 0 + 57.14 – 0 = 57.146、委外工单分摊人工制费委外工单基本产生加工费用,但是一产品大部分是委外的,由外协厂产品生产完送回时,再由内部人员做简单的包装或贴标签在入库,但最后一程序不开工单,如果要把内部所消耗的人工或费用可以直接摊到这张委外工单时,可以把这工作中心的人工与制费分摊到这张委外工单(二)成本计算前置作业流程1、检查未完工工单(成本人员、生管人员)位置:打印[工单委外子系统\报表管理、生产进度表] (工单状态=未生产、已领料、生产中)目的:检查当月还有多少未完工的工单,检查应该完工或需指定完工却仍未完工的单据,如果存在已发料记录又不需要生产了的,需把余料退回仓库,在指定工单结束。
易飞ERP高级成本计算

成本系统(一)成本参数设定1:成本分类方式使用时机:打印[直接原料明细表]时,会按照此处定义的分类显示2、半成品投入归成上阶材料成本成本计算时,若领用的下阶材料有半成品,其半成品的材料成本、人工和制费直接视为领用的材料成本;打勾分部步结转法,不然就是平行结转法。
3、材料在制约量⑴按实际投入材料成本计算计算步骤1、计算工单生产一单位所需耗用的材料每单位材料成本=(工单单身需领用量*月档单位成本)/工单的预计产量2、计算出工单的约单产量约当产量=工单实际领用材料金额/每单位材料成本3、计算出工单的在制约量在制约量=期初在制约量+约当产量-(生产入库量+委外进货量+报废量+破坏量)注意事项:a:领料超领太多时,造成在制约量高估计b:领料少领时,造成在制约量低估,若工单有入库则可能会呈现负数。
c:成会人员须定期检视工但用料的合理性或调整当期材料的在制约量d:此种方式计算出来的材料在制约量会比较接近实际⑵按投入套数计算(领料套数)适用对象:整批领料、制造前置时间短、领料日与投料日比较相近计算逻辑:期初在制约量+已领套数– (生产入库量+委外进货量-委外退货量+报废数量+破坏数量)⑶无在制约当产量当期投入材料成本全数分摊至当期入库数量适用于:当期投入当期完工者,或者在制成本非常低可以忽略不计4、人工制费在制约量⑴按实际投入材料成本计算适用成本要素中材料成本占极大部分,或标准成本无法收集者⑵按投入套数计算⑶无在制约量当期投入的人工及制费成本全数分摊至当期入库数量适用于:当期投入当期完工者⑷按实际投入工时计算有设定标准工时才可预估生产一单位产品的工时若无工时则需维护[录入品号信息]的[单位标准人工成本]与[单位标准制造费用],才可预估生产一单位产品的人工制费成本。
若公司有标准公司为依据,还需用考虑[工资率与制费分摊]标准:取[录入工作中心]的标准工资率及标准制费分摊率实际:取[录入工作中心成本]的单位人工及单位制费计算逻辑:半成品归上阶If 工艺管理子系统->录入工单工艺->标准工时 <> 0 thenBeginIf 成本计算子系统->设置成本子系统参数->工资率与制费分摊依据= 标准 then 标准:取[录入工作中心]的标准工资率及标准制费分摊率单位人工 = [录入工作中心]的标准工资率单位制费 = [录入工作中心]的标准制费分摊率Else实际:取[录入工作中心成本]的单位人工及单位制费单位人工 = [录入工作中心成本]的单位人工单位制费 = [录入工作中心成本]的单位制费If 基本信息子系统->录入工作中心->制费分摊依据 = 人时Begin每单位人工制费=[(标准人时*单位人工)+(标准人时*单位制费)]/工单的预计产量End;If 基本信息子系统->录入工作中心->制费分摊依据 = 机时Begin每单位人工制费=[(标准人时*单位人工)+(标准机时*单位制费)]/工单的预计产量End;If 基本信息子系统->录入工作中心->制费分摊依据 = 人时Begin每单位人工制费=[(标准人时*单位人工)+(标准人时*单位人工*单位制费)]/工单的预计产量 End;约当产量=(本期投入人工成本+本期投入制造费用)/每单位人工制费在制约量= 期初在制约量+约当产量-(生产入库量(委外进货量)+报废数量+破坏数量)End ElseBeginIf 产品结构子系统->录入产品工艺路线->标准工时 <> 0 then计算原理同上ElseBegin必须输入存货管理子系统->录入品号信息->单位标准人工成本、单位标准制造费用每单位人工制费 =单位标准人工成本+单位标准制造费用End;End;5、加工费用在制约约量⑴按实际投入材料成本计算适用成本要素中材料成本占制造成本的大多数,或标准加工费用无法收集者⑵按投入套数计算(领料套数)⑶无在制约当产量当期投入加工费用全数分摊到当期入库数量适用于:当期投入当期完工者⑷按标准成本加工费用计算每单位加工费用计算时会抓取[录入品号信息]的[会计]页签字段几个条件:[半成品投入归上阶材料成本]是否勾选及工单是否有走工艺管理子系统计算逻辑计算工单生产一单位所须加工费用If 有使用工艺系统 thenBeginIf半成品归上阶材料成本未勾thenBegin说明:本阶投入的加工费用可能还在其他工艺尚未入库而下阶段所投入的加工费用不归上阶材料成本因此也要同时计算在制每单位加工费用= 标准加工费用End;If半成品归上阶材料成本勾选thenBegin说明:本阶投入的加工费用可能还在其他工艺尚未入库而需要计算在制而下阶段所投入的加工费用已归上阶材料成本了,因此没有下阶加工费要计算每单位加工费用= 本阶加工End;End ElseBeginIf半成品归上阶材料成本未勾thenBegin说明:本阶所发生的加工费用已经全数入库了,所以只需要计算下阶的在制就可以了下阶的每单位加工费用= 标准加工费用- 本阶加工End;If半成品归上阶材料成本勾选thenBegin说明:本阶所发生的费用已经全数入库,所以已无在制,而下阶投入的加工费用又因为已归上阶材料成本了,所以也没有下阶的加工费用每单位加工费用= 0End;End;约当产量=工单实际加工费用/每单位加工费用在制约量=期初在制约量+约当产量-(生产入库量(委外进货量)-委外退货量-报废数量-破坏数量)范例:1Z-- 1X、1Y 若预计外包生产100Z,Z的单位标准加工为35元,当月份支付加工费用为2000元,且无完工进货数量,则加工费用在制约量?使用工艺系统且半成品归上阶材料成本未勾答:每单位加工费用=品号信息[标准加工费用]=35约当产量 = 2000/35 = 57.14在制约量 = 0 + 57.14 – 0 = 57.146、委外工单分摊人工制费委外工单基本产生加工费用,但是一产品大部分是委外的,由外协厂产品生产完送回时,再由内部人员做简单的包装或贴标签在入库,但最后一程序不开工单,如果要把内部所消耗的人工或费用可以直接摊到这张委外工单时,可以把这工作中心的人工与制费分摊到这张委外工单(二)成本计算前置作业流程1、检查未完工工单(成本人员、生管人员)位置:打印[工单委外子系统\报表管理、生产进度表] (工单状态=未生产、已领料、生产中)目的:检查当月还有多少未完工的工单,检查应该完工或需指定完工却仍未完工的单据,如果存在已发料记录又不需要生产了的,需把余料退回仓库,在指定工单结束。
ERP成本计算子系统如何计算成本
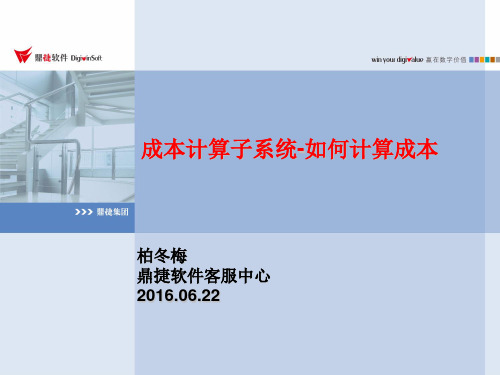
在制约量的计算-在制约量的定义
按前之计算基础,…….(900+280+5,000)/60 =103 元 您认为103 元合理吗? 将计算基础调整=(900+280+5,000)/(60+40*0.8)=67.2 元 在制约量=(40*80%)=32 工单当月未完工才可能会有在制 系统提供多种在制约量计算方式
成本计算子系统-如何计算成本
柏冬梅 鼎捷软件客服中心 2016.06.22
课程大纲
1
在制约量的计算
2
维护工单成本计算来源
3 生产入库,委外进货的成本计算逻辑
在制约量的计算-在制约量的定义
在制约量 针对当月未结束工单,为使其单位成本更接近实际成本,对于在 制品的认定——预估完成约量 即现场WIP(Work in Process),视同完成品
成本作业介绍-成本异常检测表
本报表于[成本计算前]及[成本计算后]检查使用
成本作业介绍-工单成本作业介绍
设置成本子系统参数 录入工单工时
汇总工作中心工时 录入工作中心成本
异常检测 计算成本年月低阶码
计算生产成本 维护工单/产品成本
作业目的
每月根据工单单身,计算成 本年月低阶码,供成本计算 使用
成本作业介绍-计算成本年月低阶码
底 成
采购管理子系统
本
进货单
计
退货单
价
影响成本码=N 工单/委外子系统
领料单 退料单
存货管理子系统 库存交易单
影响成本码=N
人工成本
工单/委外子系统
成
领料单
+
制造费用
本
退料单
计
加工费用
算
利用ERP软件实现订单成本核算

随着中国企业加入全球化竞争的序列,高利润的年代似乎已经过去,取而代之的是所谓的微利时代。
企业产品成本的准确数据,可向管理当局提供更多信息,帮助其作出更好决策,如定价等,同时还有利于计划控制和业绩评价,所以成本计算在会计系统中有着重要作用。
目前企业生产的普遍特点是小批量、多品种,个性化的需求越来越多,这给成本的计算增加了难度。
因此如何准确地计算成本对企业的财务人员是一个巨大的挑战。
手工计算的工作量太大,而且准确性又难以保证,所以利用ERP软件来计算成本是最佳方法。
下面我们通过举例来看一下如何利用ERP软件来实现订单成本的核算,本文使用的软件环境为用友U861ERP管理软件(核算必备模块为库存、存货、采购、销售、物料清单、生产订单以及成本等)。
假设有一家汽车生产企业,主要生产整车和发动机。
生产流程大致为:首先,发动机厂生产的发动机完工后入半成品库(发动机也可对外出售)。
然后,总装厂领用各种材料及半成品进行总装,完工后入产成品库。
公司要求按订单计算发动机和整车的生产成本。
一、前期准备工作第一步:制订产品BOM该公司每道生产工序完工后,将产品及其成本都转入下一工序,按照成本要素归集的方法,使用逐步结转分步法。
这种方法最为复杂,完全按照产品结构与工艺流程计算成本,但这种计算方法最符合U8成本管理核算思想,通过多层次BOM即可实现。
因此,首先我们要制订一份准确的产品BOM(bill of material),即物料清单。
在软件的物料清单模块中,录入产品结构,通过表体的领料部门指明生产部门(对应工作中心)。
BOM这项工作十分重要,可以说是成本计算的基石。
第二步:参数配置在成本模块中对参数进行配置(见表1)。
表1参数配置项目内容计算方法品种法和分步法(确定后不得修改)是否启用生产制造数据来源是(确定后不得修改)存货数据来源于存货系统出库类别生产耗用入库类别产成品入,半成品入人工费用来源手工输入制造费用来源手工输入折旧数据来源手工输入公共材料分配率按产品完工数量直接人工分配率按产品完工数量制造费用分配率按产品完工数量在产品成本分配率只计算原材料成本此外,还要定义成本中心,成本中心指企业内部可以归集成本费用的末级部门或工作中心,是基本的成本核算单位。
erp产品的成本核算-标准成本
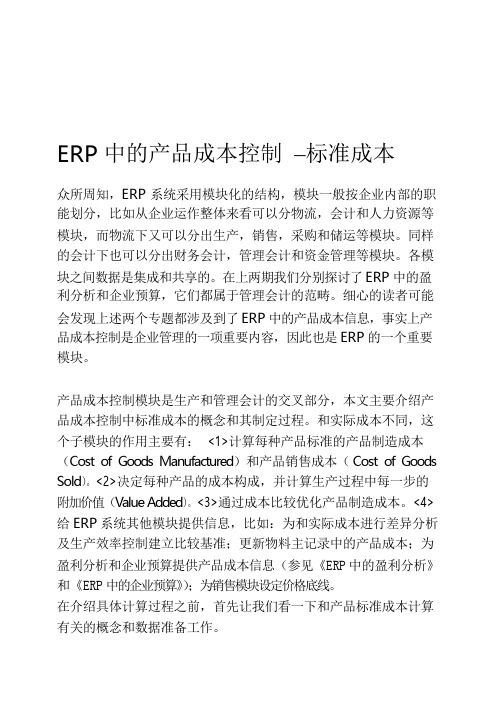
ERP中的产品成本控制–标准成本众所周知,ERP系统采用模块化的结构,模块一般按企业内部的职能划分,比如从企业运作整体来看可以分物流,会计和人力资源等模块,而物流下又可以分出生产,销售,采购和储运等模块。
同样的会计下也可以分出财务会计,管理会计和资金管理等模块。
各模块之间数据是集成和共享的。
在上两期我们分别探讨了ERP中的盈利分析和企业预算,它们都属于管理会计的范畴。
细心的读者可能会发现上述两个专题都涉及到了ERP中的产品成本信息,事实上产品成本控制是企业管理的一项重要内容,因此也是ERP的一个重要模块。
产品成本控制模块是生产和管理会计的交叉部分,本文主要介绍产品成本控制中标准成本的概念和其制定过程。
和实际成本不同,这个子模块的作用主要有:<1>计算每种产品标准的产品制造成本(Cost of Goods Manufactured)和产品销售成本(Cost of Goods Sold)。
<2>决定每种产品的成本构成,并计算生产过程中每一步的附加价值(V alue Added)。
<3>通过成本比较优化产品制造成本。
<4>给ERP系统其他模块提供信息,比如:为和实际成本进行差异分析及生产效率控制建立比较基准;更新物料主记录中的产品成本;为盈利分析和企业预算提供产品成本信息(参见《ERP中的盈利分析》和《ERP中的企业预算》);为销售模块设定价格底线。
在介绍具体计算过程之前,首先让我们看一下和产品标准成本计算有关的概念和数据准备工作。
计算产品成本的数据准备物料清单(Bill of Material/BOM)物料清单是一个完整的,正式的,结构化的关于组成一个产品的部件清单。
该清单包含每个部件的物料编号,数量和计量单位。
物料洗衣机WP830机械支承系统机械传动系统控制系统外箱体电动机电源开关控制台安全开关定子吊杆支承程序控制器转子机械电动式程控器端盖微电脑程控器波轮洗涤桶盛水桶图1:物料清单(BOM)离合器清单是MRP的基础,对于产品成本来说物料清单决定了哪些材料将被计算进产品的成本,以及计算的顺序。
- 1、下载文档前请自行甄别文档内容的完整性,平台不提供额外的编辑、内容补充、找答案等附加服务。
- 2、"仅部分预览"的文档,不可在线预览部分如存在完整性等问题,可反馈申请退款(可完整预览的文档不适用该条件!)。
- 3、如文档侵犯您的权益,请联系客服反馈,我们会尽快为您处理(人工客服工作时间:9:00-18:30)。
ERP产品成本估算”无工不富,无农不稳”,曾几何时,制造企业被认为是社会财富的根本来源,这种实体经济的观点已经被颠覆, 现在帝国主义这只大吸血虫一般都喜欢大玩虚拟经济利用金融战将不发达国家多年积累的社会财务瞬间攫取据为己有,中国至今也就落得个”血泪工厂”的制造大国。
素以严谨谦虚著称的国外某管理软件的某个老外,就曾跑到中国来直指国内管理软件没有蕴涵所谓“先进”的管理思想。
成本管理一般被认为企业尤其制造业管理的中心, 成本是企业财务体系是否健全、现代化的标志,一个实施成功的ERP项目应该能帮助企业财务、物流、生产等核心业务的规范化。
一个完善的ERP成本模块无非是包括成本预测、成本预算、成本核算、成本控制、成本考核和成本分析等功能,SAP系统被公认的最大的强处在于集团财务和供应链的高度集成(MM/SD/PP/FI/CO,正是ERP的5大核心模块),其中尤其是成本管理,功能值得称道。
成本预测和成本预算在产品成本模块(CO-PC),首先就是进行产品成本估算, 产品成本估算的结果可以作为生产成本预测、销售利润预测、产品定价乃至企业生产运作决策依据,这也是成本估算的作用,下面结合几个简单实际例介绍下成本估算部分。
在前面介绍成本估算单(Costing sheet)时,讲述了定义成本组件结构(Tcode:OKTZ)时如何将成本组件(即国内所谓的成本项目)和生产费用要素关联, 图1-[1]-> 图1- [4]中显示是产品成本估算的相关配置,包括定义成本估算变式,设置物料成本相关属性,成本估算时如何选择BOM和工艺路线,图1-[5]的配置则是针对无BOM的产品成本估算,本人一向主张化简为繁,虽然目前顾问都喜欢将简单事情复杂化,为了方便读者理解,我将成本估算分为以下几个步骤。
步骤一:定义物料成本相关属性(1).定义物料类型的相关属性(Tcode:OMS2),给某物料类型定义默认的价格控制标志,跨工厂物料状态,是否允许外部采购等。
(2).定义物料状态(Tcode:OMS4),物料状态有什么作用呢,首先看图2中物料状态的设置。
通过在物料主数据中设置物料状态可以限制物料的业务操作,比如在图2的Purchasing设置B(Error),则该料被禁止采购,这很有实际意义,比如某些物料专门有供应商A供应,但该供应商A评估不合格,就可以在物料主数据中设置B自动禁止采购单下达;你还设置物料禁止被维护在BOM项目中,在原材料更新快速的电子行业,经常能听到替代料限用料和禁用料这些词汇,处于成本的考虑,一些过时的原件可能被用做新料的替代消耗,但处于质量考虑,另一些更过时的元件应该被禁止使用等待报废;你可在Material requirements页设置该料能不能被允许用在独立需求计划中,或者干脆被禁止参与MRP运算,在PP模块可以很方便地设置某个仓位不参与MRP,此处则是针对单个物料,在Inventory management页选择B则表示该料被禁止物料移,当收到供应商某些怀疑质量有问题的原料后,这些问题可以通过一定小维护解决,就可以首先禁止这些物料被发到产线上去,但是依旧参与Run MRP,实际上通过图2你可以发现系统设计者几乎考虑了企业所有可能涉及的物料交易,图2-[1]则是和成本估算相关的设置,状态B和状态D的细小区别都被考虑,状态B仅仅当物料被用做BOM中做部件时才发出错误信息,其本身是允许做成本估算的(Tcode:CK11N),而D则干脆被禁止做成本估算。
关于物料状态应用非常广泛,不再一一举例,需要强调的是,在物料主数据的物料状态被分成两类:I.跨工厂状态,在主数据Basic data1基本视图的X-plant matl status字段维护。
II.特定工厂状态,在Costing 1成本1视图的Plant-sp.matl status字段维护。
在一个大型跨国集团中,物料编码应该保持高度一致,在世界各地都有庞大业务的集团要做到此点非常不容易,SAP甚至提供了专门的物料主数据MDM管理模块来处理这件事情,集团所有的物料被设计为共享相同的基本视图,而会计成本视图内容通常和具体工厂相关,如果一个物料的状态被维护成跨工厂状态,则对整个集团生效,否则仅对特定工厂起作用, (3).设置物料特殊采购类型在SAP系统中,将物料分为自产和外购,通过物料主数据MRP2视图的Procurement type 标识, Procurement type分4种情况:E:In-house production->表示该物料主要是自产,如果外购回出现ME 092的警告消息;MRP跑出后出现生产计划->生产工单;自产料在成本估算时如系统没有找到BOM,默认会给一个错误提示(可以忽略关闭这个消息)F:External procurement->表示该物料主要是外购,跑MRP需求自动为采购申请->采购订单X:Both procurement types->自产和外购都可空:No procurement->禁止外购注: Procurement和Purchasing 两个词的中文翻译都是“采购”,在供应链中它们还是有区别的,此出不细述, Procurement在此实际上应该表示物料的获取途径包括自产和采购,但是此节还将其翻译为采购为了将Procurement type进一步细分,系统还提供了多种特殊采购(Special procurement)类型,下面是系统默认的集中特殊采购类型。
10:Consignment->比如供应商VMI30:Suncontracting->F+30表示该料为委外加工50:Phantom assembly->虚拟料件52:Direct production/collective order->用于母子工单,当BOM层次越多,涉及的加工单/子加工单就越多,此时可以考虑使用母子工单减化流程,当然也可考虑使用虚拟件70:Withdrawal from alternative plant->可将消耗转向另一工厂80:Production in alternative plant->将生产定向到另一工厂图3表示的是特殊采购类型50虚拟件的设置,可以看到As BOM component下的Phantom item 标志被选上,如果某料的采购类型和特殊采购类型是E/50则表示该料为虚拟件,一般认为,虚拟件的主要作用有:a. 将实物存在不需要采购销售和库存管理的,比如某些半成本,为了避免建立更多半成品工单,将它设置为虚拟件。
b.为了简化BOM的建立,做为产品结构中的一种过渡件方式,可以将多个产品生产流程同时需要的一组或者一类规格的料件组成一个虚拟BOM,该BOM的Head Material即虚拟件,使用虚拟BOM清晰地表达可产品的工艺路线,方便后续维护,当生产工艺或生产版本变化时,如果多个产品结构使用到该虚拟件,只要更改其虚拟BOM就行,由于BOM数据的二维存储,不使用虚拟BOM就得一个个更改产品结构,虚拟BOM在此处类似程序设计中的代码重用。
c.变式BOM中的某些特征件可以作为虚拟件。
d.某些服务可建立成为一个虚拟料放在BOM中,对于生产流程简单的企业,为了简化流程,活用虚拟件可以不为产品建立工艺路线,直接将相关人工等费用项目也做个虚拟料搞定,实际上广义的BOM本身就包括工艺路线。
图3-[4]如果选择了withdr. Altern. Plant则需要设置目标工厂,举个实例,生产工厂P1的产品A 的子件B的采购类型和特殊采购类型是F/70,其中对应的目标工厂为采购工厂P2,则产品A 成本估算时其下层子件B的价格策略也将定向到采购工厂P2。
这是单个物料的跨工厂计算成本,SAP系统还允许直接跨工厂运用成本估算结果,假设X集团在中国有一个生产工厂产品都建立有相关BOM,而国外的多家公司仅仅负责销售是不维护BOM的,在这些销售公司做利润预测时不但需要产品的标准成本而且需要详细的标准成本估算结构(即标准成本的料工费组成明细),销售工厂就可取生产工厂的成本估算结果。
步骤二:定义BOM选择BOM的分类方法很多,此处不讨论,就功能来说,有设计BOM,维修BOM,生产BOM,采购BOM,销售BOM,配置BOM,还有专用于MRP的计划BOM和成本估算的成本BOM,在供应链模块,物料主数据管理和BOM应用的水平直接体现企业实施ERP系统的成熟程度,企业可以自身生产组织形式和现有的管理水平状况定义BOM的层次,BOM的层次直接影响计划系统和成本核算的准确,合理定义BOM才能有效地发挥ERP系统的功能和优势。
系统提供了多种类的BOM,那么成本估算时将选择何种BOM呢?如图4。
注意两个概念:BOM Applcation和BOM选择ID。
图4-[1]:注意BOM Application PC01,做成本估算用,对应的选择ID 05,05包括3个选择优先级,01优先级->6:Costing BOM,02优先级-->1:生产BOM,03优先级->3:通用BOM。
Tcode:OKKN看系统默认的标准成本估算变式PP01,使用的BOM选择正是PC01,即表示标准成本估算时首先抓取6:成本BOM,一些企业可能并不维护专门的成本BOM,如果没有则取02优先级1:生产BOM,以此类推。
*企业甲认为在产品生产过程特别是新产品试产中,存在大量各种损耗,这些潜在损耗运行MRP需要考虑,因此在生产BOM中加入了损耗率,而成本估算时不考虑这些不确定的损耗,为此可以建立一套不计损耗的成本BOM专门用做成本估算。
图4-[3]:在SAP中,系统预定义了9种BOM功能类型,可以在Tcode:CS01的Usage看到BOM用途:1 :生产BOM2:工程/设计BOM,可和PDM系统集成3:通用BOM4:工厂维护BOM5:销售和分销,即销售BOM6:成本核算,成本BOM7:空的->未知预留干啥用8:稳定性研究M:外部军需品图5显示的是BOM应用PC01的明细内容,注意图5-[2],选择“Alt. det.mult. BOM”和”P rodu ction versions”标志的意思是当某类BOM涉及多个工程版本号时如何确定成本估算应该选择哪个版本,设计BOM和生产BOM的版本更新是很正常的,SAP系统提供了专门的ECN(Engineering Change Management)子模块管理BOM的变更,图5-[2]表示存在多BOM 时将根据多BOM选择条件设置(见图6)和物料的生产版本决定成本估算时选择的BOM 版本。
除了按照用途Usage将BOM分类外,SAP BOM还有两个概念,一个ECN中的BOM Revison,即BOM ECN版本,一般产品从旧版本A1升级到新版本A2时,A1就失效;另一种叫Alternative BOM,比如某电子产品A即有全新投料自产的,也有回收旧产品的原料生产的,还有给几个重要原料外包的,就可为产品A建立3套BOM,这3套BOM同时有效,当然对应的工艺路线也不同;当然如果不激活ECN,将Alternative BOM稍微打扮一下当ECN Revision用似乎也可以。