电镀锡资料
电镀锡工艺专业介绍

市场需求
随着电子、汽车、航空航天等行业的快速发展, 电镀锡工艺的市场需求将继续增长,为行业发展 提供广阔空间。
技术创新
电镀锡工艺将不断进行技术创新和改进,提高生 产效率和产品质量,降低成本,增强市场竞争力。
电镀锡工艺的创新与突破
定制化服务
针对不同领域和客户需求,提供定制化的电镀锡解决方案,满足客 户的个性化需求。
跨界合作与产业链整合
加强与其他行业的合作与交流,整合产业链资源,推动电镀锡工艺 的创新与发展。
THANKS FOR WATCHING
感谢您的观看
汽车工业
汽车零部件的电镀锡处理, 如发动机部件、刹车片、 油箱等,以提高耐腐蚀性 和延长使用寿命。
电镀锡的发展历程与趋势
发展历程
电镀锡工艺自20世纪初开始发展,经历了手工电镀、自动电镀到如今的数字化 电镀等阶段,不断提高生产效率和镀层质量。
发展趋势
随着环保意识的加强和技术的不断进步,电镀锡工艺正朝着环保化、高效化、 智能化方向发展,如开发低毒性的电镀锡添加剂、提高电镀锡自动化程度等。
新材料的应用
01
研发新型的电镀锡材料,提高电镀锡层的性能和稳定性,满足
不同领域的需求。
工艺优化
02
通过改进电镀锡工艺参数和流程,提高电镀锡层的均匀性和附
着力,降低不良品率。
环保技术的研发
03
研发环保型的电镀锡技术,减少对环境的污染和破坏,实现绿
色生产。
电镀锡工艺的未来展望
智能化生产
通过引入智能化技术和设备,实现电镀锡工艺的自动化和智能化 生产,提高生产效率和产品质量。
电镀锡工艺描述
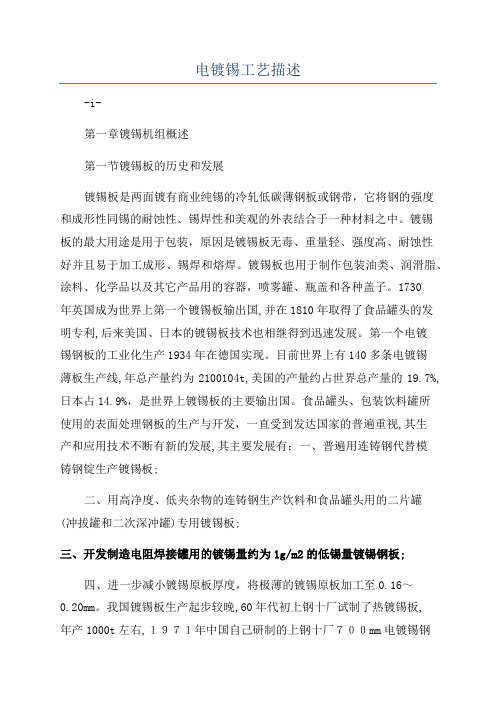
电镀锡工艺描述-i-第一章镀锡机组概述第一节镀锡板的历史和发展镀锡板是两面镀有商业纯锡的冷轧低碳薄钢板或钢带,它将钢的强度和成形性同锡的耐蚀性、锡焊性和美观的外表结合于一种材料之中。
镀锡板的最大用途是用于包装,原因是镀锡板无毒、重量轻、强度高、耐蚀性好并且易于加工成形、锡焊和熔焊。
镀锡板也用于制作包装油类、润滑脂、涂料、化学品以及其它产品用的容器,喷雾罐、瓶盖和各种盖子。
1730年英国成为世界上第一个镀锡板输出国,并在1810年取得了食品罐头的发明专利,后来美国、日本的镀锡板技术也相继得到迅速发展。
第一个电镀锡钢板的工业化生产1934年在德国实现。
目前世界上有140多条电镀锡薄板生产线,年总产量约为2100104t,美国的产量约占世界总产量的19.7%,日本占14.9%,是世界上镀锡板的主要输出国。
食品罐头、包装饮料罐所使用的表面处理钢板的生产与开发,一直受到发达国家的普遍重视,其生产和应用技术不断有新的发展,其主要发展有:一、普遍用连铸钢代替模铸钢锭生产镀锡板;二、用高净度、低夹杂物的连铸钢生产饮料和食品罐头用的二片罐(冲拔罐和二次深冲罐)专用镀锡板;三、开发制造电阻焊接罐用的镀锡量约为1g/m2的低锡量镀锡钢板;四、进一步减小镀锡原板厚度,将极薄的镀锡原板加工至0.16~0.20mm。
我国镀锡板生产起步较晚,60年代初上钢十厂试制了热镀锡板,年产1000t左右,1971年中国自己研制的上钢十厂700mm电镀锡钢带试验性生产系统建成,但当时国内还不能生产镀锡专用钢,加上轧制精度较低,因此只能生产低档用途的镀锡板。
70年代,罐头食品是我国主要出口产品之一,但由于镀锡板全靠进口,并由国家分配指标,因此供应紧缺。
1978年武钢从西德引进的300m/min、1100mm宽带钢高速镀锡机组投产,但由于设计定由1700mm5机架连轧机生产原板,在技术上、经济上均不合理,因而未能正常生产。
80年代部分镀锡原板曾由硅钢厂20辊轧机生产,年产3~4万t。
PCB电镀铜锡工艺资料
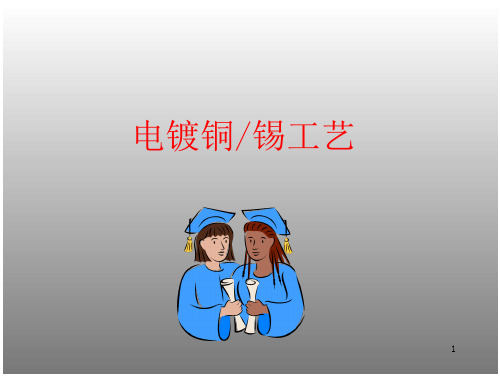
34
电镀铜溶液的控制
n 赫尔槽试验(Hull Cell Test)
n仅高电流密度区烧焦,试片的其它区域仍然正常----Copper Gleam 125T-2(CH) Additive 低 n改正方法:添加1ml/l Copper Gleam 125T-2(CH) Additive
: 濃度太低,Байду номын сангаас液導電性差,鍍液分 散能力差。
濃度太高,降低Cu2+的遷移率,電流 效率反而降低,❹對銅鍍層的延伸 率不利。
: 濃度太低,鍍層出現台階狀的粗糙 鍍層,易出現針孔和燒焦;濃度太 高,導致陽極鈍化,鍍層失去光澤 。
: (後面專題介紹)
11
操作條件對酸性鍍銅效果的影響
溫度
溫度升高,電極反應速度加快,允許電流密度提高,鍍 層沉積速度加快,但加速添加劑分解會增加添加劑消耗,鍍層結 晶粗糙,亮度降低。
31
电镀铜溶液的控制
n 赫尔槽试验 (Hull Cell Test)
阴极-
阳极+
32
电镀铜溶液的控制
n 赫尔槽试验(Hull Cell Test)参数
n — 电流: 2A n — 时间: 10分钟 n — 搅拌: 空气搅拌 n — 温度: 室温
33
电镀铜溶液的控制
n 赫尔槽试验(Hull Cell Test)
28
电镀铜溶液和电镀线的评价
n 热冲击测试
测试步骤
(1) 裁板16""x18"’ (2) 进行钻孔; (3) 经电镀前处理磨刷; (4) Desmear + PTH + 电镀; (5) 经电镀后处理的板清洗烘干; (6) 每片板裁上、中、下3小片100mm x 100mm测试板;
电镀锡及锡合金

4
在电子工业中,利用锡熔点低,具有良好的可焊接性、
导电性和不易变色,常以镀锡代镀银,广泛应用于电子元器, 连接件、引线和印制电路板的表面防护。铜导线镀锡除提高
可焊性外,还可隔绝绝缘材料中硫的作用。
锡镀层还有其它多种用途,如将锡镀层在232℃以上的 热油中重熔处理后,可获得光亮的花纹锡层(冰花镀锡层), 常作为日用晶的装饰镀层。 在某些条件下,锡会产生针状单晶“晶须”,会造成电路短 路,另外,在低温环境中,锡容易发生“锡疫”,转变为粉末
13
(2) 硫酸
具有抑制锡盐水解和亚锡离子氧化、提高溶液
导电性和阳极电流效率的作用。 当硫酸含量不足时,Sn2+离子易氧化成Sn4+离子。它们在 溶液中易发生水解反应: SnSO4 + 2H2O→Sn(OH) 2↓+ H2SO4
2SnSO4 +O2 + 6H2O → 2Sn(OH)4↓+ 2H2SO4
无光亮镀锡 1 40~55 60~80 0.3~1.0 1~3 2 60~100 40~70 0.5~1.5 1~3 60~80 4.0~8.0 6.0~10 4.0~20 15~30 0.5~1 3 45~60 80~120 4 40~70 140~170
光亮镀锡 5 50~60 75~90 6 35~40 70~90
苯甲酰丙酮等。光亮剂的基本结构多为下列类型:
16
17
上述结构通式中的Rl、R2、R3,和R4分别代表不同的取代基。 对同一结构,改变R,可以得到多种不同的有机化合物,它 们都有一定的增光作用。主光亮剂大多不溶于水。 b.辅助光亮剂 实验证明仅仅使用主光亮剂并不能获得
高质量的光亮镀层,需要同时添加脂肪醛和不饱和羰基化合
电镀锡工艺专业介绍

电镀锡工艺专业介绍引言电镀锡是一种将锡金属沉积到其他金属表面的工艺,主要用于提供保护、表面装饰和改善导电性能。
电镀锡广泛应用于电子、电器、汽车和航空等领域。
本文将介绍电镀锡工艺的基本原理、工艺流程和应用领域。
一、电镀锡的基本原理电镀锡的基本原理是利用电解原理将锡离子沉积到金属表面。
在电解液中,通过将阳极上的金属离子还原为金属沉积在阴极上,从而实现电镀锡的目的。
电解液中的主要成分包括锡盐、添加剂和溶剂。
二、电镀锡的工艺流程电镀锡的工艺流程主要包括预处理、电镀和后处理三个主要步骤。
2.1 预处理预处理是为了准备金属表面,使其适合进行电镀。
预处理包括以下几个环节:1.去油脂:使用碱性清洗剂或有机溶剂去除金属表面的油脂和污垢。
2.酸洗:使用酸性溶液去除金属表面的氧化层和其他杂质。
3.激活:使用活化剂处理金属表面,提高其对锡的吸附性。
2.2 电镀电镀是将锡离子沉积到金属表面的过程。
电镀工艺中的关键参数包括电流密度、电解液浓度和温度等。
电镀的过程中,金属表面通过吸附处于溶液中的锡离子,形成金属镀层。
2.3 后处理后处理主要是对电镀层进行清洗和保护,以提高镀层的质量和稳定性。
后处理过程主要包括以下几个环节:1.冷却:将电镀件冷却至室温,准备进行下一步处理。
2.中和:使用碱性溶液中和电镀液中的酸性成分。
3.清洗:使用去离子水或中性清洗剂清洗电镀件,去除残留的酸性和碱性物质。
4.保护:在电镀层上涂覆一层保护剂,以提高镀层的抗氧化性和耐腐蚀性。
三、电镀锡的应用领域电镀锡广泛应用于以下几个领域:1.电子行业:电镀锡常用于电子元器件的连接端子和焊盘,提供优良的导电性和抗氧化性。
2.电器行业:电镀锡常用于家电产品的外壳和内部焊接部位,提供抗腐蚀保护和装饰效果。
3.汽车行业:电镀锡常用于汽车零部件的表面涂层,提供耐腐蚀保护和美观效果。
4.航空航天行业:电镀锡常用于航空航天器件的连接和绝缘层制备,提供稳定的电性性能和保护。
结论本文简要介绍了电镀锡工艺的基本原理、工艺流程和应用领域。
电镀锡工艺专业介绍

电镀锡工艺专业介绍1. 引言电镀锡工艺是一种将锡层附着在金属表面的工艺,以提供保护和改善外观的功能。
通常,电镀锡工艺可以应用于各种金属,如钢铁、铜、铝等。
本文将介绍电镀锡工艺的基本原理、工艺流程以及应用领域。
2. 基本原理电镀锡是一种通过电解将金属锡溶解于电解液中,然后在待镀金属表面上通过电流沉积金属锡的工艺。
其基本原理如下:•阳极:阳极是由纯锡制成的,其位置放置在电解液中。
阳极中的锡与电解液中的锡离子相互作用,形成可溶性的锡氧化物。
•阴极:阴极是待镀金属制成的,如钢铁、铜、铝等。
当电流通过电解液时,锡离子从阳极移动到阴极上,然后以金属锡的形式沉积在阴极表面。
•电解液:电解液是一种含有锡盐和各种添加剂的溶液,其作用是提供需要的条件,使锡离子能够在电解过程中移动到阴极上,并使得金属锡沉积在阴极表面。
通过控制电流密度、电解液成分和温度等参数,可以获得不同厚度和质量的锡镀层。
3. 工艺流程电镀锡工艺的步骤通常包括以下几个主要环节:3.1 准备工作在进行电镀锡之前,需要对待镀金属进行清洗和预处理,以去除表面的污垢和氧化物,并提高镀层与基材的附着力。
准备工作一般包括以下步骤:1.清洗:使用碱性或酸性溶液清洗金属表面,去除油脂、灰尘和其他杂质。
2.脱脂:将金属表面浸泡在脱脂剂中,去除残留的油脂和脂肪。
3.酸洗:使用酸性溶液处理金属表面,去除氧化物和其他不良物质。
3.2 电镀过程完成准备工作后,可以进行电镀锡的过程。
具体的电镀步骤如下:1.配制电解液:按照工艺要求,将锡盐和其他添加剂溶解在适当比例的溶液中。
2.调节参数:根据需要,调节电流密度、温度和电镀时间等参数。
3.沉积锡层:将待镀金属作为阴极放置在电解槽中,与阳极连接,并启动电流供应。
锡离子会从阳极移动到阴极上,在表面沉积出一层金属锡。
4.冲洗:在电镀完成后,将金属从电解槽中取出,经过冲洗,以去除残留的电解液和其他副产物。
5.烘干:将镀有锡层的金属通过热风或其他方式进行烘干,使其表面完全干燥。
电镀锡基本培训资料(doc 11页)
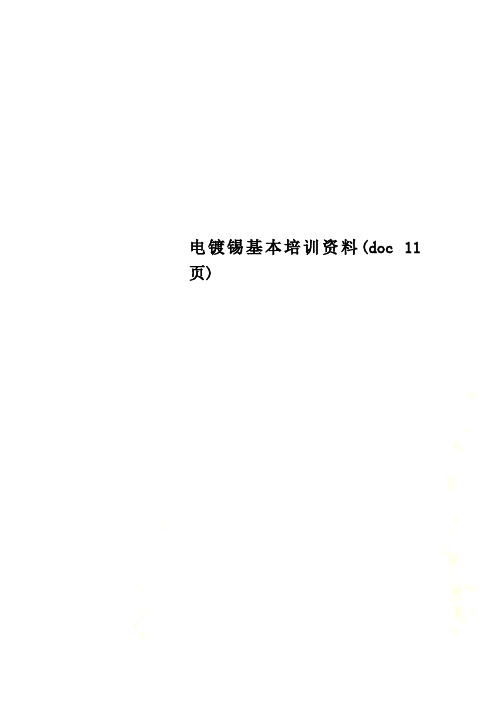
电镀锡基本培训资料(doc 11页)镀锡层均匀性差镀锡层的均匀性差主要由溶液温度偏高引起的,当溶液温度高于35℃时会更明显。
镀锡层均匀性差对质量影响很大,这是因为锡镀层的厚度相对较薄,不均匀的镀层局部处会更薄,该处有可能出现雾状和焊接性能差。
解决方法:(1)控制溶液温度,必要时采取冷却措施;(2)采取移动阴极。
移动阴极不但能提高镀层均镀能力,还可提谪阴极电流密度,防止镀层烧焦、针孔、条状,以及暗灰色等症状出现,并对提高镀层光亮度等方面都有一定的作用。
沉积速度缓慢硫酸亚锡是光亮镀锡溶液中的主盐,提供锡离子来源,其含量对镀层和镀锡过程中允许的电流密度有较大的影响,在允许范围内提高亚锡离子浓度可相应提高阴极电流密度,有利于加快镀层的沉积速度,相应地提高了生产效率。
但当超过工艺规范要求,亚锡离子浓度过高或过低时对镀层质量会有如下的不良反映。
(1)硫酸亚锡含量过高时出现的主要症状:镀液分散能力降低;镀层结晶粗糙、色泽暗淡;光亮区范围变窄。
(2)硫酸亚锡含量过低时出现的症状:允许的电流密度范围明显缩小;镀层沉积速度缓慢;生产效率相应降低;镀层容易烧焦。
本故障原估计是电流密度过大引起的,但又考虑到锡镀层并不粗糙,且电流密度调小后这一现象也未见改观,因此进行化验分析。
发现硫酸亚锡含量已低于30g/L,检查发现阳极已钝化。
原来溶液中锡含量的降低是阳极钝化引起的,据进一步追究,阳极钝化原是该阳极由杂锡自熔浇铸的。
故当阳极锡头回炉时要用专用锅,不可与其他金属熔化锅混用,并要仔细检查,以免与锡近似的镉、铅、锌等金属混入。
由此可见,镀锡工艺中保持阳极纯度的重要性。
锡阳极的纯度应不低于99.9%的高纯度,否则除易引起钝化之外,还会污染镀液。
为此阳极板还必须用阳极袋套,来阻止阳极泥污染溶液。
溶液出现黄色硫酸盐光亮镀锡溶液出现黄色通常由有机质污染引起,而有机质多由添加的分解物形成(其中也不排除随工件的带入),这时溶液的黏度也会随之增加,镀层出现结晶粗糙,有条纹和针孔,脆性增大、结合力降低等现象。
电镀锡工艺_培训资料

一、工艺的指导思想⏹最终用途决定工艺⏹工艺的一致性⏹在产品质量和生产成本之间找到最佳的平衡点⏹安全问题二、镀锡板简介电镀锡板因其基板具有合适的强度、优良的焊接性和冲压性,表面镀层具有良好的耐腐蚀性,易于涂布、印刷而广泛应用于食品、饮料、喷雾剂、化工和油漆等的包装以及各种器具的制造。
电镀铬板又被称作无锡钢(Tin Free Steel),简称TFS,是指“代替镀锡板使用,而表面又不镀锡的薄钢板”。
一般分为铬系无锡钢(TFS-Cr)和镍系无锡钢(TFS-Ni)两类。
目前流行的为铬系无锡钢,欧洲通称为ECCS。
这种材料最初是由锡资源缺乏的国家开发成功,后作为镀锡板的一种代用品,被许多国家在制罐行业中推广。
它与镀锡板相比,具有生产成本低、表面附着力强、涂印效率高、耐硫性好等显著优点,广泛用于杂品罐及瓶盖等。
三、镀锡板的分类(GB/T 2520-2000)和性能按成品形状:板、卷按钢级:一次冷轧、二次冷轧按钢基:L、MR、D :L型钢残留元素(Cu、Ni、Cr、Mo及其它元素)成分特别少,具有极优良耐蚀性,MR型残留元素成分较宽,耐蚀性好,用作一般用途,D型是铝镇静钢,在深冲加工或经受容易产生拉伸应变纹情况下使用按退火方式:箱式、连续按表面外观:光亮、石纹、银光、无光按镀锡量:等厚、差厚按钝化种类:阴极电化学、化学按表面质量:Ⅰ级、Ⅱ级镀锡板的性能机械性能(调质度):镀锡板的机械性能是指镀锡原板即钢基板的机械性能。
它主要由钢基板的化学成分、轧制工艺和退火工艺决定。
耐蚀性:耐蚀性是镀锡板最重要的性能。
镀锡板大量用于制造食品罐,如水果罐、奶粉罐、午餐肉罐等,由于盛装的食品种类繁多,其腐蚀也有不同特点,因此要求镀锡板具有适应其内装物特点的耐蚀性。
原板的化学成分和表面纯净度影响镀锡原板耐蚀性。
一般要求硫、磷、铜含量越少越好,但也有特殊情况,如对盛有可口可乐类含CO2的饮料,硫含量高些反而提高原板的耐蚀性,对盛有桔子等含柠檬酸的食品,铜含量多些对耐蚀性也有利。
电镀锡阳极

电镀锡阳极电镀锡阳极是一种用于电镀工艺中的阳极材料。
电镀锡阳极的主要作用是在电镀过程中提供锡离子,使其被还原并镀在被处理物体的表面,从而形成一层锡膜。
这一层锡膜可以提高被处理物体的耐腐蚀性能、电导性能和外观质量。
电镀锡阳极通常由纯度较高的锡材料制成,可以是锡板、锡棒或锡丝等形式。
制备电镀锡阳极的工艺一般包括以下几个步骤:选择合适的锡材料,根据需要对锡材料进行切割或加工,然后进行清洗和除油处理,最后进行阳极制备。
在电镀过程中,电镀锡阳极被置于电镀槽中,并与电源连接。
通过电解液中的电流,锡阳极上的锡离子被还原,并沉积在被处理物体的表面。
锡膜的形成过程主要涉及离子迁移、电化学反应和金属沉积等物理和化学过程。
通过控制电解液中的温度、浓度和电流密度等参数,可以调节锡膜的厚度和质量。
电镀锡阳极具有一定的优点和应用价值。
首先,锡膜具有良好的耐腐蚀性能,可以有效保护被处理物体的表面不受环境中的腐蚀介质侵蚀。
其次,锡膜具有良好的电导性能,可以提高被处理物体的导电性能。
此外,锡膜还能赋予被处理物体良好的外观质量,使其具有一定的装饰性。
电镀锡阳极在许多领域都有广泛的应用。
其中,电子工业是电镀锡阳极的重要应用领域之一。
在电子器件的制造过程中,锡膜可以用作电子元器件的保护层、连接层或导电层,以提高器件的性能和可靠性。
此外,电镀锡阳极还被广泛应用于汽车工业、航空航天工业、家电制造等领域。
然而,电镀锡阳极的制备和使用也存在一些问题和挑战。
首先,电镀锡阳极的制备过程较为复杂,需要严格控制各种参数,以保证锡膜的质量和均匀性。
其次,在电镀过程中,锡阳极容易出现腐蚀、溶解或结构损坏等问题,从而影响电镀效果和阳极的使用寿命。
此外,电镀锡阳极的回收和处理也是一个环境保护和资源利用的问题。
电镀锡阳极作为一种重要的电镀材料,在电镀工艺中发挥着重要的作用。
通过控制制备工艺和优化电镀参数,可以获得高质量的锡膜,并应用于各种领域。
然而,电镀锡阳极的制备和使用也面临一些挑战,需要进一步研究和改进。
电镀锡基础知识培训

阳极: Sn 2e Sn2 (阳极的溶解过程) 阴极: Sn2 2e Sn (工件上析出镀层的过程)
6Lake_dong@
四、电流效率
以上已经说明在阴—阳极电化学反应中,阳极上除了金属溶解消 耗电流外,析出氧气也要消耗电流。阴极上除了金属镀层析出消耗电 流外,析出氢气也要消耗电流。
通过加入络合剂或添加剂能使金属子还原析出镀层的电位向负方 向移动的现象称之为阴极的极化现象。例如:原来析出金属镀层的电 位为-1.2伏,加入了络合剂或添加剂以后使析出金属镀层的电位为-1.8 伏。这说明阴极极化了,其极化的值为 - (1.8-1.2)= -0.6伏。阴极极化了,使析出金属镀层相对困难了,需 要消耗比原来较高的电能。
4. 从微电子框架的基材特性说,镀前处理尤为重要。在用基材一 般是铜基和铁镍合金(Ni42Fe)。Ni42Fe在焊片(D/B)、 焊线(W/B)和塑封后固化的工序中极易氧化钝态。所以在电 镀过程中去氧化工序成了工艺成败的核心问题。
14Lake_dong @
七、电镀过程三部曲和电镀工序功能
2.1 镀层外观:必须是呈银白色、灰白色,色泽均匀一致, 无水迹,框架无变形,塑封体乌亮,塑封体完整无缺 角、无塌棱,无气孔等缺陷。
2.2 厚度控制 纯锡镀层 11±2 微米 厚度中心值的大小和厚度误差的适用性由塑封体大小和 电极导线(管子引出线)规格所决 定。一般说塑封体 越小,引线越细,则镀层厚度和厚度误差精度的控制越 严要求。
浸泡后高压水喷淋去除溢料两步工序工件装料盒挂上lot牌浸泡68稀硫酸室温浸泡1520分钟疏松溢料三级逆流漂洗沥水浸泡syd71211053090分钟视溢料严重程度而定热水60三级逆流漂洗68稀硫酸中和三级逆流漂洗吹去水珠高压水喷淋去除溢料飞边电解高压水喷淋去除溢料一步工序上料loading电解去溢料水洗高压水喷淋吹干烘干下料19lakedong163com九电镀工艺流程挂镀自动线上挂具化学电解除油23级热自来水逆流漂洗去氧化2级自来水逆流漂洗2级纯水逆流漂洗活化电镀3级自来水逆流漂洗中和2级自来水逆流漂洗2级热纯水逆流漂洗线内吹干烘干下挂具或线外甩干烘干检验线外挂具退镀高速自动线上料电解去毛刺自来水洗去氧化自来水洗纯水洗预浸电镀水洗中和自来水洗纯水洗吹干烘干下料钢带退镀水洗吹干烘干上料20lakedong163com十电镀生产线的技术管理挂镀自动线手工线的技术管理
电镀镀锡 甲基磺酸

电镀镀锡甲基磺酸
电镀镀锡是一种通过电解将锡金属沉积在物体表面的表面处理方法。
它可以提供一层保护性的锡层,对于防腐蚀、增加导电性和改善
外观有着重要作用。
甲基磺酸是一种有机化合物,化学式为CH3SO3H。
它常用作电镀
液中的酸性组分,可以调节液体的酸碱度,提高电镀过程的效率和质量。
甲基磺酸在电镀液中的作用主要有以下几个方面:
1. 增加电镀液的酸度:甲基磺酸可以作为强酸添加到电镀液中,增加
电镀液的酸度,提供适宜的酸性环境,有利于锡的沉积。
2. 缓冲酸碱度:甲基磺酸具有缓冲酸碱度的作用,可以稳定电镀液的
酸度,防止酸碱度的波动对电镀过程的影响。
3. 抑制氧化反应:甲基磺酸可以抑制电镀液中氧化反应的发生,减少
氧化物的生成,保证电镀层的质量。
4. 调节电镀速度:甲基磺酸的添加可以调节电镀液中的离子浓度和电
流密度,影响电镀速度和质量。
总之,甲基磺酸在电镀镀锡过程中起到了调节酸碱度、抑制氧化
反应、提高电镀速度等作用,对于电镀锡的质量和效果具有重要意义。
电路镀锡方法

电路镀锡方法电路镀锡方法电路板是现代电子产品中必不可少的组成部分,而其制作过程中的镀锡工艺则是保证电路板质量和性能的重要环节。
本文将详细介绍电路镀锡方法。
一、准备工作1.1 选材首先需要选用合适的基材,在市场上常见的有FR-4玻璃纤维增强板、金属基板、陶瓷基板等,根据实际需求选择合适的基材。
1.2 设计图纸在进行电路板制作之前,需要先制定一份设计图纸,明确每个元件在电路板上的位置和连接方式。
1.3 制版根据设计图纸进行制版。
通常使用光刻法或直接打印法来制作电路板。
二、化学镀锡法2.1 原理化学镀锡法是利用化学反应使得金属原子沉积在基材表面上形成金属膜。
该方法具有成本低、操作简单、环保等优点。
2.2 步骤(1)清洗:将基材表面油污和氧化物清除干净,以便于后续处理。
(2)预处理:将基材表面进行化学处理,以便于后续的电镀工艺。
(3)镀锡:将经过预处理的基材浸入含有金属离子的溶液中,利用化学反应使得金属原子沉积在基材表面上形成金属膜。
(4)清洗:将镀好锡的基材进行清洗,以去除多余的溶液和离子。
2.3 注意事项(1)镀锡液的配方需要根据实际需求进行调整,以保证所得到的金属膜质量和厚度符合要求。
(2)操作时需要注意安全,避免接触皮肤和吸入有害气体。
三、电解镀锡法3.1 原理电解镀锡法是利用电解作用使得金属原子从阳极移动到阴极上,并在阴极表面沉积形成金属膜。
该方法具有成本较高、操作复杂等特点。
3.2 步骤(1)清洗:将基材表面油污和氧化物清除干净,以便于后续处理。
(2)预处理:将基材表面进行化学处理,以便于后续的电镀工艺。
(3)电解:将经过预处理的基材作为阴极,将金属片作为阳极,浸入含有金属离子的溶液中,利用电解反应使得金属原子从阳极移动到阴极上,并在阴极表面沉积形成金属膜。
(4)清洗:将镀好锡的基材进行清洗,以去除多余的溶液和离子。
3.3 注意事项(1)电解液的配方需要根据实际需求进行调整,以保证所得到的金属膜质量和厚度符合要求。
电镀锡工艺(电化学相关资料)

第六章电镀锡的预处理第一节概述带钢在电镀锡以前的表面状态及洁净程度是获得优良镀锡层的先决条件。
在锈蚀或粘有油污的带钢表面上,就不能获得光亮,结合力良好,耐蚀性能优越的镀层。
生产实践表明,镀层出现脱落、起泡、花斑等缺陷,往往是由于镀锡前的预处理不当造成的。
所以,带钢电镀锡前的预处理是镀锡板生产过程中一个很重要的环节,必须十分重视。
预处理的任务是除去带钢表面上的油污或者其他有机物质,和带钢表面上的氧化物,如铁锈等,使带钢在进行电镀锡前具有一个清洁的无氧化物存在的活化表面。
预处理工艺包括带钢的脱脂和酸洗,以及其附设的刷洗和冲洗等。
脱脂又分化学脱脂和电解脱脂。
要根据带钢表面污垢状况来选择适当的工艺和操作方法。
第二节化学脱脂一、目的化学脱脂又叫化学除油。
在电镀锡生产中习惯称作化学脱脂。
化学脱脂是为生产二次冷轧镀锡板而设置的。
送到镀锡车间的二次冷轧带钢,其表面上残留有较厚的轧制油和轧辊磨损物。
轧制油又常被润滑油和液压油污染。
这些油污必须首先采用化学脱脂和刷洗的方法,然后采用电解脱脂的方法才能除去。
经过化学脱脂和刷洗后,二次冷轧带钢表面上的油污大约能除去90~95%。
生产普通镀锡板时,在其原板上的油污过多的情况下,也可首先经过化学脱脂,再经过电解脱脂。
但一般情况下可以不必经过化学脱脂。
这时,在化学脱脂槽内充以70~85℃的水来保护设备,这样也可以减少后面的电解脱脂工序的热量损耗。
二、设备化学脱脂设备包括一个脱脂槽、沉没辊、托料辊、脱脂液循环系统及其后面的l号刷洗机等。
槽子的结构分为上下两部分。
在槽子上部有一溢流孔,用来控制液面的位置。
槽子下部分的底部有一个供清扫槽内脏物的门,侧面还有一个窥孔窗,用来观察穿带时的带钢情况和检查沉没辊情况。
底部还有液体输入口和排放孔。
槽子下部两侧还设有装卸沉没辊的圆形孔,沉没辊经该孔插入和抽出。
槽子上部和下部都是钢板焊接而成的。
钢板都衬有硬橡胶,槽子内壁有5毫米厚,外部有3毫米厚的硬橡胶,以防止化学液体腐蚀。
电镀锡资料

镀锡层均匀性差镀锡层的均匀性差主要由溶液温度偏高引起的,当溶液温度高于35℃时会更明显。
镀锡层均匀性差对质量影响很大,这是因为锡镀层的厚度相对较薄,不均匀的镀层局部处会更薄,该处有可能出现雾状和焊接性能差。
解决方法:(1)控制溶液温度,必要时采取冷却措施;(2)采取移动阴极。
移动阴极不但能提高镀层均镀能力,还可提谪阴极电流密度,防止镀层烧焦、针孔、条状,以及暗灰色等症状出现,并对提高镀层光亮度等方面都有一定的作用。
沉积速度缓慢硫酸亚锡是光亮镀锡溶液中的主盐,提供锡离子来源,其含量对镀层和镀锡过程中允许的电流密度有较大的影响,在允许范围内提高亚锡离子浓度可相应提高阴极电流密度,有利于加快镀层的沉积速度,相应地提高了生产效率。
但当超过工艺规范要求,亚锡离子浓度过高或过低时对镀层质量会有如下的不良反映。
(1)硫酸亚锡含量过高时出现的主要症状:镀液分散能力降低;镀层结晶粗糙、色泽暗淡;光亮区范围变窄。
(2)硫酸亚锡含量过低时出现的症状:允许的电流密度范围明显缩小;镀层沉积速度缓慢;生产效率相应降低;镀层容易烧焦。
本故障原估计是电流密度过大引起的,但又考虑到锡镀层并不粗糙,且电流密度调小后这一现象也未见改观,因此进行化验分析。
发现硫酸亚锡含量已低于30g/L,检查发现阳极已钝化。
原来溶液中锡含量的降低是阳极钝化引起的,据进一步追究,阳极钝化原是该阳极由杂锡自熔浇铸的。
故当阳极锡头回炉时要用专用锅,不可与其他金属熔化锅混用,并要仔细检查,以免与锡近似的镉、铅、锌等金属混入。
由此可见,镀锡工艺中保持阳极纯度的重要性。
锡阳极的纯度应不低于99.9%的高纯度,否则除易引起钝化之外,还会污染镀液。
为此阳极板还必须用阳极袋套,来阻止阳极泥污染溶液。
溶液出现黄色硫酸盐光亮镀锡溶液出现黄色通常由有机质污染引起,而有机质多由添加的分解物形成(其中也不排除随工件的带入),这时溶液的黏度也会随之增加,镀层出现结晶粗糙,有条纹和针孔,脆性增大、结合力降低等现象。
电镀锡(铬)产品知识题库_林永增

电镀锡电镀锡((铬)产品知识库序号问题解答关键词1镀锡板的发展过程?现代工业生产的镀锡板是两面镀有商业纯锡的冷轧低碳薄钢板或钢带。
第一张镀锡板始于14世纪,约1880年代的镀锡工业革命,出现镀锡原板(Black Plate)替代铁片,1934年德国发明连续电镀锡替代原先的热浸镀锡技术,1937年连续电镀锡开始商业化,20世纪六七十年代发明二次冷轧材和无锡板,90年代又发展覆膜铁,如日本东洋制罐的TULC产品(覆膜铁)。
镀锡板 发展过程 电镀2为什么镀锡板俗称马口铁?镀锡板俗称马口铁,该通俗叫法来源于澳门(MACAO)的译音,MACAO是当时马口铁进入中国的主要口岸。
马口铁 俗称 镀锡板3镀锡板包括几类产品?20世纪六七十年代前,曾使用过热浸镀锡板,现在都采用电镀生产工艺,镀锡板按照镀层可以分为电镀锡(简称ETP,Electrolytictinplate)和无锡板(简称TFS,Tin Free Steel),其中TFS目前商业化的产品是电镀铬(简称ECCS,Electrolytic ChromiumCoated Steel)。
镀锡板 类型 TFS4中国最早的镀锡板生产线?中国第一条电镀锡机组,是1979年武钢引进建设的10万吨卤素法高速机组,最早国产电镀锡产品;中国第一条TFS机组,是1999年中山中粤马口铁公司采用自有技术改造的镀锡/镀铬两用机组,最早制造电镀铬产品。
镀锡机组 镀铬机组5宝钢的DR材镀锡板?2005年宝钢建成二次冷轧机组(简称DCR),最早国产DR材(二次冷轧材)电镀锡板、DR材TFS,改写DR材镀锡板依靠进口的历史,也极大丰富了镀锡产品的规格品种。
二次冷轧 DR材 DCR机组6什么是DR材镀锡板及其优点?DR材镀锡板采用的原板为二次冷轧材,二次冷轧板是在一次冷轧和退火处理之后,通过二次冷轧机组将带钢进一步轧薄,与一次冷轧相比,具有极薄、高强的优点:(1)二次冷轧使带钢进一步减薄,钢板最小厚度可以达到0.10mm;(2)提高材料的机械性能,硬度和强度值增加。
电镀锡 (2)

电镀锡简介电镀锡是一种常见的表面处理方式,主要用于金属制品的防锈和美化。
它通过在金属表面镀上一层薄薄的锡层,形成一种保护层,防止金属与外界氧气、水分等物质接触,从而延长金属制品的使用寿命。
电镀锡的原理电镀锡的原理基于电化学反应,包括阳极、阴极和电解质三个关键元素。
阳极是锡的金属块,阴极是需要被镀锡的金属制品,而电解质则是一种含有锡离子的溶液。
在电解质中,锡离子会被氧化成为正离子,并向阴极移动。
当锡离子到达阴极表面时,它们会失去电荷并还原成金属锡。
这种电流的流动会在阴极表面形成一层锡质的沉积物,即电镀锡。
电镀锡的优势抗腐蚀性能电镀锡具有良好的抗腐蚀性能,能够有效防止金属表面氧化、腐蚀和生锈。
这是因为锡层可以隔离金属与空气、水分等物质的接触,减少氧气和水分对金属的侵蚀。
美观性能电镀锡可以让金属制品呈现出亮丽的银白色表面,提升其外观质感和美观度。
这使得电镀锡广泛应用于首饰、钟表、厨房用具等需要呈现精致外表的产品上。
导电性能锡是一种良好的导电材料,在电子行业中应用广泛。
电镀锡可以提供良好的导电性能,使得金属制品能够更好地导电,从而满足电子产品对导电性能的要求。
电镀锡的应用电镀锡在多个领域都有广泛的应用,下面列举了几个典型的应用场景。
电子行业电子行业是电镀锡的主要应用领域之一。
电镀锡可以用于保护电子产品的引线、焊盘等金属部件,提高它们的导电性能并减少氧化腐蚀的影响。
同时,电镀锡能够提供较好的焊接性能,使得电子元器件在焊接时能够更好地连接。
食品包装电镀锡在食品包装行业也有重要的应用。
食品罐头的内部一般镀有一层锡,这是为了防止罐头与食品直接接触,减少了金属离子对食品的污染。
同时,锡层还能够提高罐头的耐腐蚀性,延长其货架期。
制造业在制造业中,电镀锡被广泛应用于各种金属制品的表面处理。
例如,汽车零部件、家用电器、五金制品等都可以通过电镀锡来提高其抗腐蚀性能、美观性能和导电性能。
电镀锡的注意事项良好的表面处理在进行电镀锡之前,金属制品的表面必须要进行良好的清洁和预处理工作。
- 1、下载文档前请自行甄别文档内容的完整性,平台不提供额外的编辑、内容补充、找答案等附加服务。
- 2、"仅部分预览"的文档,不可在线预览部分如存在完整性等问题,可反馈申请退款(可完整预览的文档不适用该条件!)。
- 3、如文档侵犯您的权益,请联系客服反馈,我们会尽快为您处理(人工客服工作时间:9:00-18:30)。
镀锡层均匀性差镀锡层的均匀性差主要由溶液温度偏高引起的,当溶液温度高于35℃时会更明显。
镀锡层均匀性差对质量影响很大,这是因为锡镀层的厚度相对较薄,不均匀的镀层局部处会更薄,该处有可能出现雾状和焊接性能差。
解决方法:(1)控制溶液温度,必要时采取冷却措施;(2)采取移动阴极。
移动阴极不但能提高镀层均镀能力,还可提谪阴极电流密度,防止镀层烧焦、针孔、条状,以及暗灰色等症状出现,并对提高镀层光亮度等方面都有一定的作用。
沉积速度缓慢硫酸亚锡是光亮镀锡溶液中的主盐,提供锡离子来源,其含量对镀层和镀锡过程中允许的电流密度有较大的影响,在允许范围内提高亚锡离子浓度可相应提高阴极电流密度,有利于加快镀层的沉积速度,相应地提高了生产效率。
但当超过工艺规范要求,亚锡离子浓度过高或过低时对镀层质量会有如下的不良反映。
(1)硫酸亚锡含量过高时出现的主要症状:镀液分散能力降低;镀层结晶粗糙、色泽暗淡;光亮区范围变窄。
(2)硫酸亚锡含量过低时出现的症状:允许的电流密度范围明显缩小;镀层沉积速度缓慢;生产效率相应降低;镀层容易烧焦。
本故障原估计是电流密度过大引起的,但又考虑到锡镀层并不粗糙,且电流密度调小后这一现象也未见改观,因此进行化验分析。
发现硫酸亚锡含量已低于30g/L,检查发现阳极已钝化。
原来溶液中锡含量的降低是阳极钝化引起的,据进一步追究,阳极钝化原是该阳极由杂锡自熔浇铸的。
故当阳极锡头回炉时要用专用锅,不可与其他金属熔化锅混用,并要仔细检查,以免与锡近似的镉、铅、锌等金属混入。
由此可见,镀锡工艺中保持阳极纯度的重要性。
锡阳极的纯度应不低于99.9%的高纯度,否则除易引起钝化之外,还会污染镀液。
为此阳极板还必须用阳极袋套,来阻止阳极泥污染溶液。
溶液出现黄色硫酸盐光亮镀锡溶液出现黄色通常由有机质污染引起,而有机质多由添加的分解物形成(其中也不排除随工件的带入),这时溶液的黏度也会随之增加,镀层出现结晶粗糙,有条纹和针孔,脆性增大、结合力降低等现象。
为避免这种现象的出现,溶液经一定时间使用之后需进行一次净化处理,使溶液中过高的有机杂质及时除去。
具体做法:先用活性炭吸附,然后进行过滤,经调整成分并短时间电解处理之后即可使用。
锡阳极加速溶解某厂硫酸盐光亮镀锡溶液中锡离子的浓度比原工艺配方高出l/3,经了解原是两个月前加硫酸时误将g/L单位认作mL/L单位,结果总数加入量增加一倍。
由于硫酸对锡具有化学溶解作用,致使溶液中锡盐浓度也随之提高,既浪费了材料,又增加了污水的治理费用。
硫酸是硫酸亚锡光亮镀锡溶液中不可缺少的主要成分之一,其存在所起的作用与不足时对镀层质量的影响主要反映在以下方面。
(1)硫酸含量满足工艺配方要求时。
硫酸的存在可抑制二价锡离子的氧化、促使镀液稳定、有利于提高镀液的导电能力和均镀能力、改善阴极极化、促使镀层结晶细密以及能加速阳极化学溶解、提高阳极电流效率等,但也要防止含量过高,否则会影响阴极电流效率,而且污水处理负担加重。
(2)硫酸含量低于工艺配方要求时。
当硫酸含量不足时,最明显的是镀液会出现不溶性的沉淀物,镀层出现结晶粗糙,这是由亚锡离子氧化成四价锡离子引起的结果,此时可加入适量的絮凝剂通过搅拌后进行过滤。
并加入适量硫酸调整。
因此,硫酸盐镀锡溶液中硫酸浓度的控制是十分重要的镀层出现粗糙通常镀层出现粗糙原因较多,如明胶含量不足,主盐浓度过高,阴极电流密度过高和溶液中固体杂质过多。
但另一种可能原因常被大家所忽视,即四价锡的影响。
某次故障就是排除以上四种引起镀层粗糙的可能原因之外而估计到的。
四价锡浓度过高时会随着二价锡离子一起沉积到镀层之中去,结果除会影响镀层的可焊性之外,还会使镀层结晶粗糙、疏松等症状。
四价锡是由二价锡遇到空气中氧的作用被氧化而产生的,为避免四价锡过多产生,要防止抽风机抽力过大或溶液使用空气搅拌,其次溶液温度也不宜过高。
这一故障现象可通过活性炭吸附处理后进行过滤,并重新调整其他成分予以解决。
镀层光亮度差镀锡层表面光亮度差的原因众多,如溶液中光亮剂少,溶液温度过高,主盐浓度过高等,但某次实例是由于镀层过薄,颜色发青(由基底映出)。
后经焊接试验得到证实,因为可焊性也很差。
锡层在锡与底层铜的界面上会互相渗透,形成熔点温度比锡高的合金扩散层,在此扩散层之外的镀层若过薄,尤其低于3~4μm时,是难以焊接的。
经增加镀层厚度之后,镀层的光亮度有很大提高。
焊接性能也彻底改善。
由此可见,引起镀层故障的原因是多方面的,在解决这类故障时要广开思路,寻找线索,不要有局限性。
镀层出现黄膜某次,锡层表面有黄膜,不是成片的,而多在工件的盲孔、狭缝口等部位。
这显然与镀后处理有关,工件表面未曾充分清洗干净,使这一部位镀层遭到氧化,出现黄色膜层。
黄膜除严重影响外观之外,还会影响镀层的可焊性。
这一批工件采取洗刷方法处理故障,但锡层表面的自然光泽也因此而遭到破坏。
后改用湍流冲洗:自制如图7—9所示水嘴一个,进水口连接自来水胶管,打开阀门进水后湍流射出,在猛烈冲洗下使残留在工件的孔隙、狭缝内的溶液充分排挤出来。
镀层出现锈迹在电化学中,锡的标准电位比铁正,钢铁件镀锡属阴极性镀层,只有在镀层无孔隙的条件下才能有效地保护基体不受腐蚀,但这往往做不到,特别是在高电流密度下所获得的镀层更是如此,故钢铁件镀锡之前除需要增加中间镀层,如氰化镀铜之外、锡镀层的厚度也应适当增加,以提高其防护性能,在工艺上镀后增加热熔处理来提高镀锡层的防护性能。
镀液铜离子积累使镀层焊接性能变差某工件除镀层的可焊性差之外,镀层的颜色也较暗,笔者参加会诊时发现镀槽的极梗上有很多铜绿。
估计这一故障很有可能是由铜离子污染引起的,因为镀锡溶液遭到无机杂质污染之后,除镀层会发暗、孔隙增加之外,也会严重影响镀层的可焊性,至于溶液污染是否有如此严重尚待考察。
于是笔者有意识地注意铜绿的产生过程,后见到一位操作者拿着铜丝刷子直接在槽中蘸着溶液洗刷铜梗,由此可见铜梗上的铜绿原来是由此产生的。
经日积月累,溶液中的铜离子必然会越来越多,溶液完全有可能已被污染到极限程度。
后经长时间的电解处理才缓慢地得到恢复。
这一故障的形成除操作者有责任,不该如此亏待溶液之外,生产、技术管理者同样要负监督和教育责任。
镀层光亮度差、结晶粗糙引起镀锡层结晶粗糙、光亮度差的因素很多,但主要与配制材料的纯度差有关。
如某厂用工业级原料和自来水配制的溶液未曾镀出过合格产品,下面就对此问题进行分析,并提出如下要求。
(1)硫酸亚锡纯度要求。
硫酸亚锡必须要用分析纯的,使用前要观察表面颜色,如见有泛黄则不可使用,这是二价锡被氧化成四价锡的结果。
四价锡极易水解而生成偏锡酸,镀液配成后变为浑浊。
积累淤渣,电流效率也会随之下降,此时所获镀层灰暗发雾,结晶粗糙、疏松。
(2)硫酸纯度要求。
硫酸也要用分析纯的,工业级硫酸中含有对镀液有害的多种杂质。
(3)水质纯度要求。
自来水中含有氯、钙、镁等多种对镀液有害的离子,这些离子被吸附在镀层中时,即会影响镀层的光亮度,严重时还会影响镀层的焊接性能,故配制镀液时一定要用去离子水。
除了上述种种可能原因之外,平时对溶液的维护、防止有害杂质从空气中和工件上的带入也很重要。
溶液中光亮剂过快失效这一现象有可能是由溶液温度过高引起的,也可以从夏季光亮剂消耗快,冬季光亮剂消耗慢这一规律来解释。
溶液温度过高时不但会加速光亮剂的分解,还会引起镀层光亮区域变窄,镀层光亮度和均匀度降低,镀层出现条纹、花斑,甚至泛黄、发脆、脱落等弊病,溶液也会由此而出现混浊。
溶液温度过低对镀层质量也是不利的。
当镀液温度过低时,电流密度要相应调小,否则工件极易烧焦,从而引起沉积速度缓慢,且对镀层的结合力也不利,并会影响镀层的光亮度。
为满足镀液的正常温度需要,冬季室内无取暖设备的厂家,镀液要适当加温,而夏季又需要考虑溶液的冷却装置。
硫酸亚锡光亮镀锡的镀液温度宜控制在10~25℃的范围内,最佳的温度范围是15~20℃。
光亮剂过快失效的另一弊端是溶液中光亮剂的分解产物也会过快积累,从而又会进一步恶化溶液的洁净程度,给产品质量带来不良后果新配制溶液出现浑浊(1)硫酸亚锡较难溶于水,在中性条件下二价锡易氧化生成四价锡,四价锡极易水解生成偏锡酸浑浊物。
为此,在配制镀液时要按以下程序进行。
①试配。
在正常情况下配成的镀液应是澄清的,但有时配成的镀液呈混浊状态,这是硫酸亚锡质量问题引起的,有可能是制造工艺问题,也可能是出厂日期久远所致,故在配制大槽镀液之前宜先在小槽中按正常的配制程序进行试配,如配成的镀液未见异常,方可再配大槽,否则对硫酸亚锡的质量按上述可能引起的原因作进一步检验;②先在槽中加入1/3~1/2的去离子水;③在不断搅拌下缓慢加入需要量的分析纯硫酸(一定要缓慢,以防因升温过快塑料槽遇高温变形);④待凉至30℃左右;⑤在不断搅拌下将硫酸亚锡慢慢地撒入槽中,也可将硫酸亚锡用多层塑料纱窗布包裹后悬挂在槽中,在不断搅拌下让其慢慢地自然溶解(不宜用压缩空气搅拌,以防止二价锡离子加速氧化);⑥待凉至室温;⑦在搅拌下按计量加入已溶于少量去离子水中的添加剂;⑧补充去离子水至规定液位;⑨继续搅拌30min;⑩电解处理:Dk=0.2A/dm2;t=12h。
按照上述程序和方法配制镀液还可避免硫酸亚锡沉人槽底结块而引起溶解困难等问题的发生。
(2)镀液配制过程中对搅拌的要求。
为使镀液中各成分均匀一致,在镀液配制过程中要认真进行搅拌,切不可敷衍了事。
为减轻镀液中的硫酸亚锡与空气过分接触而遭到氧化,搅拌时不要过于剧烈,可以间歇式搅拌,并防止镀液出现“浪尖”。
(3)镀液配制后对电解处理的要求。
镀液配制后要充分地进行电解处理,处理时电流密度无需太大,用小电流处理,不但镀液中材料消耗省,又能除去溶液中的有害杂质,并能起到镀液的“磨合”与“协调”作用。
镀锡层表面氧化膜的处理镀锡多为焊接上的需要而进行,当镀成时间过久,表面发生氧化后即会失去优良的焊接性能,这时有的采取洗刷,这一方法对于形状简单的大件来说尚可被接受,但当遇到形状复杂件的小件则难以应付。
为此,有的单位干脆进行返修重镀,甚至报废,这样做是极大的浪费。
为彻底解决这种难题,笔者认为首先要从镀锡工艺着手,来延缓锡层的抗氧化能力,重点注意以下几点。
(1)加强溶液维护。
防止有害的有机、无机杂质侵入,减轻这些杂质与锡共沉,从而保证镀层中锡的纯度,减缓锡的变色速度。
(2)加强镀后处理。
镀成后要充分进行冷、热水冲洗,尽可能把工件表面所吸附的有机光亮剂的分解产物充分清洗干净,并当即干燥。
(3)密封保管。
经充分干燥后要当即存放在密封的干燥器内,从而有力地防止大气中有害气体的污染。
当镀锡层出现变色后可采用清洗的手段来除去,具体方法简述如下。
(1)自来水浸润2min。
(2)稀盐酸中除去氧化膜。