三安Φ8mm盘螺轧制工艺的制定及优化
盘螺负偏差轧制的开发与实践
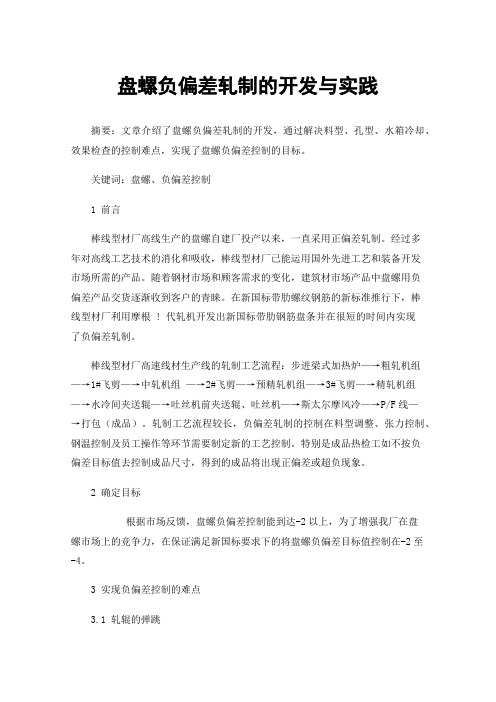
盘螺负偏差轧制的开发与实践摘要:文章介绍了盘螺负偏差轧制的开发,通过解决料型、孔型、水箱冷却、效果检查的控制难点,实现了盘螺负偏差控制的目标。
关键词:盘螺、负偏差控制1 前言棒线型材厂高线生产的盘螺自建厂投产以来,一直采用正偏差轧制。
经过多年对高线工艺技术的消化和吸收,棒线型材厂已能运用国外先进工艺和装备开发市场所需的产品。
随着钢材市场和顾客需求的变化,建筑材市场产品中盘螺用负偏差产品交货逐渐收到客户的青睐。
在新国标带肋螺纹钢筋的新标准推行下,棒线型材厂利用摩根 ! 代轧机开发出新国标带肋钢筋盘条并在很短的时间内实现了负偏差轧制。
棒线型材厂高速线材生产线的轧制工艺流程:步进梁式加热炉—→粗轧机组—→1#飞剪—→中轧机组—→2#飞剪—→预精轧机组—→3#飞剪—→精轧机组—→水冷间夹送辊—→吐丝机前夹送辊、吐丝机—→斯太尔摩风冷—→P/F线—→打包(成品)。
轧制工艺流程较长,负偏差轧制的控制在料型调整、张力控制、钢温控制及员工操作等环节需要制定新的工艺控制。
特别是成品热检工如不按负偏差目标值去控制成品尺寸,得到的成品将出现正偏差或超负现象。
2 确定目标根据市场反馈,盘螺负偏差控制能到达-2以上,为了增强我厂在盘螺市场上的竞争力,在保证满足新国标要求下的将盘螺负偏差目标值控制在-2至-4。
3 实现负偏差控制的难点3.1 轧辊的弹跳新国标螺纹钢成分中加入微合金含量增加,使轧件变形抗力增加,轧机弹跳值也相应增大,而我厂粗中轧轧机为利旧设备,弹跳值大,容易使轧件料型控制不均匀。
轧辊的弹跳主要受轧件变形抗力的影响,轧件的变形抗力又受轧件材质、轧制温度、压下量的影响,生产过程中主要是受轧件温度影响。
3.2 孔型磨损高线轧制中各道次料型尺寸的控制由原来的正公差控制变为负公差控制,加大了轧辊的压下量,而且新工艺调整降低了入精轧温度,加速了孔型磨损(特别是精轧),增加料型调整难度。
如果调整工测量辊缝存在误差时,负偏差值将难以控制在目标值内。
盘螺屈服强度检验方法的探讨与提高盘螺屈服强度的方案

盘螺屈服强度检验方法的探讨与提高盘螺屈服强度的方案吕利伟,高振兴(河北钢铁集团唐钢公司牛产制造部,河北唐山063009)摘要:盘螺的生产工艺特点和盘卷交货状态,决定了在进行盘螺屈服强度检验时存在选择检验方法的矛盾。
探讨了当前盘螺屈服强度检验方法的合理性,以及通过轧后控冷提高盘螺屈服强度。
关键字:屈服强度;规定塑性延伸强度;组织强化;轧后控冷Discussion o n Yield Strength Test Methods for Ribbed Bar s in Coi l and Improved Process D es ig n for Its Yield StrengthLv Liwei,Ga o Zhenxing(Manufacturing Dep ar tme nt,H ebe i I ro n&S t ee l C o.,L t d.T a n g s h a n Branc h)Ab st ra ct:Th e process fea tu r es a nd d el i v e ry status of the ribbed bars l ea d to a co n t r a di c t i o n whe n cho osi ng test me t ho d s f or it s y ie l d s t r en g t h.T h i s p ape r di s c u s s e s the rati on ali ty of the test met ho d s.A n d it g i v es a ll impro ve d process design for it s y ie l d s t r en g t h,t h r ou g h t he c o n t r o l l ed cooling aft er r o l li n g.Ke y w ord:yi eld st re n gt h;R p0.2;s t ru ct ur e st r e n gt h e n i ng;c o n t r o l le d coo ling aft er r o ll in g1前言在高速线材生产线生产的、以盘卷交货的螺纹钢筋,简称盘螺。
螺纹钢精轧生产工艺

螺纹钢精轧生产工艺
螺纹钢精轧是一种机械制造工艺,通过对螺纹钢进行精确的轧制,使其表面形成规则的螺纹纹路。
下面将介绍螺纹钢精轧的工艺流程和关键技术。
首先,将钢坯经过预处理,去除表面的氧化皮和杂质物质。
然后,将钢坯送入加热炉进行加热,使其达到适宜的轧制温度。
同时,在加热过程中,通过控制气氛和温度,以及采用合适的加热方式,可以保证钢坯的温度均匀,避免产生不均匀的热应力。
加热后的钢坯进入轧机,经过一系列的轧制工序,形成螺纹纹路。
螺纹钢精轧一般采用连续轧制工艺,通过多台轧机的串联,实现连续生产。
这样既提高了生产效率,又能保证轧制质量的稳定性。
在轧制工序中,一个关键技术是轧辊的选择和磨削。
轧辊是将钢坯变形成螺纹的工具,其表面应具有充分的硬度和精度。
同时,钢坯在轧制过程中会产生热应力和磨损,轧辊也要能够承受这些力和磨损。
因此,在选择轧辊材料和设计轧辊结构时,需要综合考虑材料的机械性能和使用寿命。
另一个关键技术是轧制工艺参数的控制。
轧制过程中,轧机的线速度、压力和温度等参数需要精确控制,以保证螺纹钢的几何尺寸和物理性能。
这需要依靠先进的控制系统和精确的传感器来实现。
最后,轧制后的螺纹钢需要经过冷却和定长切割等工序,最终成品可以直接用于建筑、桥梁等领域。
同时,还需要进行检测和质量控制,以确保产品的合格率。
综上所述,螺纹钢精轧是一种复杂的生产工艺,需要依靠先进的设备和严格的工艺控制。
只有在各个环节都做到精细化管理,才能生产出高质量的螺纹钢产品。
提高Φ10 mm盘螺屈服强度的工艺优化措施

螺纹钢主要用于钢筋混凝土构件的骨架,在使用中要求有一定的机械强度、弯曲变形性能及工艺焊接性能。
盘螺是通过高速线材轧机轧制的螺纹钢,以盘卷形式交货。
盘条螺纹钢牌号与宜条螺纹钢相同(HRB400、HRB500等)性能要求也一致。
与直条螺纹钢相比,其工艺特点是:通过大量轧制变形和轧后控冷得到足够的性能,可以不采用飢的沉淀强化。
自2018年以来,柳钢生产的①10mm HRB400E盘螺出现了多次屈服强度偏低的现象,屈服强度385〜410MPa,抗拉强度610-660MPa o本文探讨在不增加合金加入成本的前提下,通过改进现有的轧制、控冷工艺以提高屈服强度的可行性。
分析与讨论(-)成分与性能数据分析成分是影响钢材力学性能的重要因素。
柳钢HRB400E盘螺成分设计为,a(C):0.23%; to(Si):0.35%;(o(Mn): 1.45%;a (Ceq):0.48%;m(P)Im(S):0.03/0.02o 统计近期生产的010mmHRB400E盘螺力学性能(见图1)及其成分(见图2)的控制情况,从各个成分的控制上看,主要元素均在内控范围内且比较稳定,不合格部分试样的c元素有所波动,不合格试样中Mn、Si和碳当量与整体控制平均值接近,P、S要比整体控制平均值低。
而这组成分设计实际生产的盘螺屈服强度平均值为445MPa,抗拉强度为658MPa,符合国家标准要求且有一定的余量。
因此认为,成分设计上没有问题。
Edg翌®醫哽屈服强度—•—整体屈服平均值5330522015105O0L90990S932S29翌®a4g-o—抗拉强度.整体抗拉平均值05101520253035图]①10mm盘螺性能不合格试样力学性能情况2019年第2期I39—上限——下限不合格部分一•一整体控制平均值I£ S3塗旨贰0§貝03§354 7心7肌加淞%加芻S 902 S3 S 3GS ) 301234567891011121314151617181920212223 2425262728293033y9迟 S与 V SEE 1S S 83S S S 0o s )39.0S.0寸.O E.o z.o r o o1.6 1.6 1.61.6 1.6 1.61.6 1.6 1.61.6 1.6 1.61.6 1.6 1.60123456那 10111川 1415161川 1删12223恥翎2829300123456那 10111213141516171819皿 1肪淞呦恥300123456789101112131415161718192021222324252627282930PSCeq图2①10 mm 盘螺性能不合格试样的成分情况(-)拉伸曲线及金相组织从性能不合格试样的拉伸曲线上看(见图 3),搭接点和非搭接点的屈服拐点都不明显。
“一罐到底”工艺实践

福建三安炼钢厂推行“一罐到底”工艺的实践李美满(福建三安钢铁有限公司炼钢厂,福建泉州362411)摘要:介绍了炼钢厂推行铁水“一罐到底”工艺及其重要性、铁水“一罐到底”制的炼钢工序对铁水的要求、“一罐到底”制在炼钢生产存在的问题及相应的技术和管理措施。
关键词:一罐到底;生产实践;炼钢节能;经济效益福建三安钢铁有限公司由综合厂、烧结厂、炼铁厂、炼钢厂、轧钢厂和公辅设施组成。
炼铁厂有1号、2号(550 m3)、3号(1250 m3)共3座高炉,设计年产铁水216万t;炼钢厂有2座在线倒灌站、1座600 t混铁炉、3座50t氧气顶底复吹转炉、3台R=6 m弧的160 mm×160 mm四机四流连铸机,设计年产粗钢225万t。
铁水“一罐到底”技术,是近几年在钢铁行业发展起来的一种全新的铁水供应技术。
其核心技术是高炉出铁及铁水运输,炼钢厂混铁炉大班指挥行车起吊向转炉兑铁水均使用同一个铁水罐,中途不倒罐[1]。
高炉铁水罐直接进转炉,节省了炼钢的铁水包,减少了铁水二次倒罐环节,避免了倒罐造成的铁水温降、铁水飞溅损失和环境污染,同时节约了相关设备的投资运行。
经生产实践,取得了较为理想的经济效益和社会效益[1-3]。
1 推行铁水“一罐到底”工艺的重要性从2012年11月开始,在三安炼钢厂试用“一罐到底”新工艺。
“一罐到底”作为炼钢厂一项重点挖潜增效(目前,铁水包是以吨铁水一元的形式承包给兄弟单位。
216万t铁不使用铁包直接“一罐到底”,降低成本216 万元)措施加以实施,为此,炼钢厂成立了“一罐到底”QC技术攻关小组,同时也是公司生产制造部的重点推动工作项目。
铁水从高炉输送到炼钢厂转炉[1],要经过出铁、运输、过磅、取样、吊运、倒罐、空罐返回和等待的一系列工序,其每一工序和铁水罐的自身状态对于铁水温降都有影响,从而增加了控制铁水输送过程及减小铁水温降的难度。
由转炉冶炼工艺可知,转炉冶炼的热量基本来源于铁水的物理热和化学热;在化学热一定的情况下,铁水的物理热是决定冶炼能否顺行的关键因素,特别是公司当前正处于低成本战略的关键时期,如果铁水温度波动大,使转炉炉前一批料矿石摄入量不准确,造成终点温度过低或过高,导致钢水后吹严重,吹损大,钢铁料消耗高,成本高,钢水质量无保障,炉龄下降,并危及安全生产等严重后果。
盘螺生产线简介

盘螺生产线简介日照钢铁盘螺生产线2009年10月目录第一章盘螺生产线工艺流程及工艺控制特点 (1)一、盘螺生产线简介 (1)二、生产工艺及产品结构 (1)三、主轧线工艺流程及先进技术 (2)1、生产线工艺流程: (2)2、采用先进技术 (2)第二章主轧线设备情况介绍 (3)一、主轧线机械设备 (3)1、加热炉区域设备 (3)2、轧钢区域设备 (5)3、精整区设备 (9)二、主轧线液压润滑设备 (10)1.加热液压站 (10)2.粗中轧液压站 (10)3.预精轧保护罩液压站 (10)4.精轧保护罩液压站 (11)5.集卷站液压系统 (11)6.卸卷站液压系统 (11)7.打包机液压系统 (11)8.工字轮液压站系统 (11)9、粗中轧稀油站: (11)10、预精轧轧稀油站: (11)11、精轧机稀油站: (12)12、油气润滑系统 (12)13、干油润滑系统 (12)14、压缩空气、氮气 (12)三、三电控制系统 (12)1、高/低压供电系统: (12)2、传动控制系统 (13)3、加热炉自动化系统 (14)4、主轧线自动化系统 (14)5、精整区域自动化系统 (16)四、历次技改技措情况 (16)1、风冷辊道变频改造 (16)2、精轧机前水冷装置 (17)3、公辅供电系统改造 (17)4、辅控PLC网络改造 (17)5、增加了飞剪专用变压器 (17)6、风机改造 (17)7、板框压滤机 (18)8、化学除油器技改项目 (18)第三章公辅设施及生产准备介绍 (18)一、公辅环保及消防系统 (18)1、净环水系统 (18)2 、浊环水系统 (19)3、污泥处理系统 (20)4、消防系统 (20)5、给排水管道 (20)二、行车 (20)三、生产准备 (21)附件一:相关设备参数 (22)第一章盘螺生产线工艺流程及工艺控制特点一、盘螺生产线简介盘螺生产线由唐山钢铁设计院设计,中冶集团北京冶金设备院设计并制造主轧线设备,预精轧、精轧区设备由哈尔滨飞机工业公司制造。
Φ50~Φ80mm圆钢提高作业率的生产实践
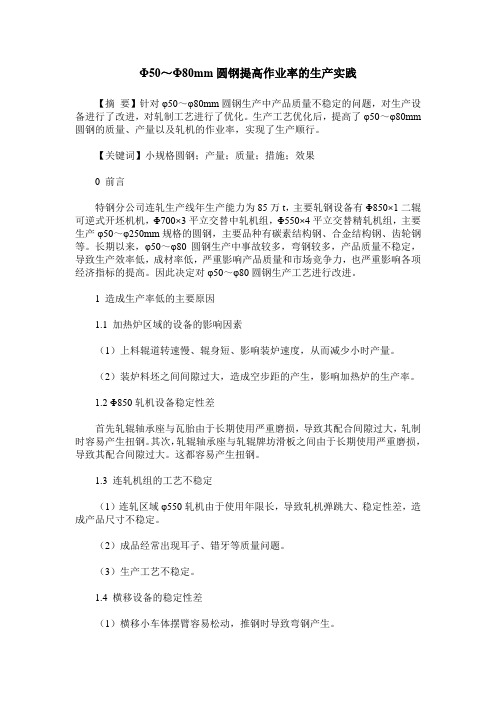
Φ50~Φ80mm圆钢提高作业率的生产实践【摘要】针对φ50~φ80mm圆钢生产中产品质量不稳定的问题,对生产设备进行了改进,对轧制工艺进行了优化。
生产工艺优化后,提高了φ50~φ80mm 圆钢的质量、产量以及轧机的作业率,实现了生产顺行。
【关键词】小规格圆钢;产量;质量;措施;效果0 前言特钢分公司连轧生产线年生产能力为85万t,主要轧钢设备有Φ850×1二辊可逆式开坯机机,Φ700×3平立交替中轧机组,Φ550×4平立交替精轧机组,主要生产φ50~φ250mm规格的圆钢,主要品种有碳素结构钢、合金结构钢、齿轮钢等。
长期以来,φ50~φ80圆钢生产中事故较多,弯钢较多,产品质量不稳定,导致生产效率低,成材率低,严重影响产品质量和市场竞争力,也严重影响各项经济指标的提高。
因此决定对φ50~φ80圆钢生产工艺进行改进。
1 造成生产率低的主要原因1.1 加热炉区域的设备的影响因素(1)上料辊道转速慢、辊身短、影响装炉速度,从而减少小时产量。
(2)装炉料坯之间间隙过大,造成空步距的产生,影响加热炉的生产率。
1.2 Φ850轧机设备稳定性差首先轧辊轴承座与瓦胎由于长期使用严重磨损,导致其配合间隙过大,轧制时容易产生扭钢。
其次,轧辊轴承座与轧辊牌坊滑板之间由于长期使用严重磨损,导致其配合间隙过大。
这都容易产生扭钢。
1.3 连轧机组的工艺不稳定(1)连轧区域φ550轧机由于使用年限长,导致轧机弹跳大、稳定性差,造成产品尺寸不稳定。
(2)成品经常出现耳子、错牙等质量问题。
(3)生产工艺不稳定。
1.4 横移设备的稳定性差(1)横移小车体摆臂容易松动,推钢时导致弯钢产生。
(2)横移辊道比盖板高,并且盖板高低不平,有焊肉,容易产生刮伤及弯钢。
(3)横移盖板西侧辊道边子高低不平,上钢时,钢坯如果推的靠西,过钢时容易造成刮伤。
1.5 热锯区域的设备稳定性差(1)辊道高度不一致,辊道轴承碎,更换不及时,容易造成辊道抱死,导致钢运行速度减慢,影响小时产量。
棒材小螺纹切分轧制提高稳定性技术改进
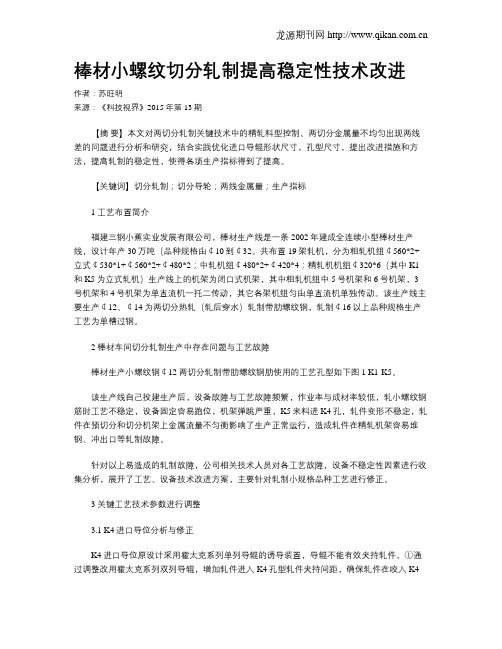
棒材小螺纹切分轧制提高稳定性技术改进作者:苏旺明来源:《科技视界》2015年第13期【摘要】本文对两切分轧制关键技术中的精轧料型控制、两切分金属量不均匀出现两线差的问题进行分析和研究,结合实践优化进口导辊形状尺寸,孔型尺寸,提出改进措施和方法,提高轧制的稳定性,使得各项生产指标得到了提高。
【关键词】切分轧制;切分导轮;两线金属量;生产指标1 工艺布置简介福建三钢小蕉实业发展有限公司,棒材生产线是一条2002年建成全连续小型棒材生产线,设计年产30万吨(品种规格由¢10到¢32。
共布置19架轧机,分为粗轧机组¢560*2+立式¢530*1+¢560*2+¢480*2;中轧机组¢480*2+¢420*4;精轧机机组¢320*6(其中K1和K5为立式轧机)生产线上的机架为闭口式机架,其中粗轧机组中5号机架和6号机架,3号机架和4号机架为单直流机一托二传动,其它各架机组匀由单直流机单独传动。
该生产线主要生产¢12、¢14为两切分热轧(轧后穿水)轧制带肋螺纹钢,轧制¢16以上品种规格生产工艺为单槽过钢。
2 棒材车间切分轧制生产中存在问题与工艺故障棒材生产小螺纹钢¢12两切分轧制带肋螺纹钢肋使用的工艺孔型如下图1 K1-K5。
该生产线自己投建生产后,设备故障与工艺故障频繁,作业率与成材率较低,轧小螺纹钢筋时工艺不稳定,设备固定容易跑位,机架弹跳严重,K5来料进K4孔,轧件变形不稳定,轧件在预切分和切分机架上金属流量不匀衡影响了生产正常运行,造成轧件在精轧机架容易堆钢、冲出口等轧制故障。
针对以上易造成的轧制故障,公司相关技术人员对各工艺故障,设备不稳定性因素进行收集分析,展开了工艺、设备技术改进方案,主要针对轧制小规格品种工艺进行修正。
3 关键工艺技术参数进行调整3.1 K4进口导位分析与修正K4进口导位原设计采用霍太克系列单列导辊的诱导装置,导辊不能有效夹持轧件。
①通过调整改用霍太克系列双列导辊,增加轧件进入K4孔型轧件夹持间距,确保轧件在咬入K4孔型前一段形成两面夹持,提高轧件咬入的稳定性,防止轧件的扭转;②对K4进口导辊优化设计,由原来的平导辊改为箱形凹槽的导辊如图2。
8毫米板先进操作法

中厚板厂8mm钢板‚1234‛高温快速轧制先进操作法一、实施背景受国际金融危机影响,自2008年以来,钢铁企业效益逐年下滑。
今年以来,受产能严重过剩、下游需求严重萎缩、资金紧张等诸多因素影响,钢铁产品价格更是一路走低,钢铁企业正面临一场生死存亡的严峻考验。
(资料照片)在当前严峻的市场形势下,很多产品没有利润,但薄规格产品盈利情况较好。
为此,中厚板厂决定在3.5米区进行8mm钢板开发,进一步增强3.5米区的市场竞争能力,打造薄规格板生产优势。
(3.5米区轧机照片)二、实施难度(一)8mm板是钢铁行业内公认生产难度大的产品采访中厚板厂3500热轧车间主任:8mm薄规格板之所以价格高,是因为它由于规格薄,对设备精度和职工操作水平要求很高,生产难度极大,多企业无法生产或者生产不稳定。
特别是3.5米区,进行粗轧机改造后,外方专家没有进行10mm 以下规格的调试,因此开发生产难度很大。
(二)3.5米区生产8mm板的最大困难在精轧机工序1、在轧制过程中,由于8mm钢板温降快、头尾温差大、板型难以控制。
(长钢板照片)2、由于3.5米区精轧机无液压弯辊、窜辊等先进板型控制手段,板幅较宽、长度较长的薄规格板质量难以保证。
三、实施方法(一)面对困难,创新制定‚一二三四‛高温快速轧制法采访中厚板厂3.5米区轧钢车间轧钢工王洪久:虽然轧制8mm板对我们来说是个新课题,难度很大,但8mm有市场、有效益,这就是最大动力。
我和同事们结合精轧机技术特点和操作要领,对生产中易出现的问题,各个击破,最终总结出‚8mm钢板‘一二三四’高温快速轧制法‛。
(二)‚一二三四‛高温快速轧制法的操作步骤此操作法以精轧机温度制度为控制核心,以高温快轧为方法,主要内容概括为:一安排、二检查、三关闭、四策略,简称‚1234‛高温快速轧制法‛。
一安排:炉内8mm坯料前安排过渡料;(坯料照片)二检查:检查PDI轧制模式和中间坯厚度;三关闭:关闭从RX3辊道至热矫直机的所有辊道冷却水;关轧机工作辊三段式冷却水电磁阀开口度至70%;关闭精轧机机后侧喷水。
提高10mm盘螺屈服强度的工艺优化措施

螺纹钢常被用来制作钢筋混凝土构件,在具体的使用过程中必须符合相关的施工标准,即机械的强度、变形性能和焊接性能都要达到要求。
盘螺属于螺纹钢的一种,是采取高速线材轧机而轧制成的盘卷形状的成品。
HRB400类型的盘螺螺纹钢与HRB500类型的直条螺纹钢在性能上要求相同。
但是,盘螺螺纹钢与直条螺纹钢对比,具有自身的工艺特点:采取大量经过轧制变形、轧后控冷的方式来控制其性能,不需要通过钒的沉淀来对其性能进行加强。
近两年来,对于10mm型号为HRB400E的盘螺的屈服强度降低的现象时有发生。
本文研究通过不增加合金成本的情况下,采取对现存的轧制、控冷等工艺来实现提高10mm盘螺屈服强度目标。
1现状及成因分析1.1成分及性能分析钢材的性能很大程度上由组成成分决定。
型号为HRB400E的柳钢的盘螺成为包括:占比为0.23%的ω(C)、占比为0.35%的ω(Si)、占比为1.45%的ω(Mn)、占比为0.48%的ω(Ce)、配比为的m(P)与 m(S)的比例。
本次研究对最近生产的Φ10 mm的型号为HRB400E 的盘螺力学性能与成分组成及控制情况进行分析,发现该盘螺的组成成分的主要元素都趋于稳定,而且都在可控制的范围内。
对于一些不符合标准的元素,则出现了波动的情况,而其中的Mn、Si以及碳之间的含量和整体控制的范围比较靠近,P与S元素的含量则低于整体控制的平均值。
然而,在盘螺的实际生产过程中,这些成分的屈服强度平均值的设计为445MPa,抗拉的强度为658 MPa,其数值完全达到国家的标准,并且还有部分剩余量。
所以,盘螺的设计组成成分的数值是合理的。
1.2试样拉伸情况及金相的组织对盘螺性能不合标准的试样进行拉伸,发现试样的搭接点与非搭接点都出现了屈服拐点不明显的情况。
经过资料查找发现盘螺进行吐丝动作后会持续一段冷却的时间,而且冷却的速度比较快,其相变的整个过程会有一种名叫贝氏体的组织生成。
当这种贝氏体的组织含量比较高的情况下,盘螺的屈服现象就不会很明显。
三安Φ8mm盘螺轧制工艺的制定及优化

90科技资讯 SCIENCE & TECHNOLOGY INFORMATION工 业 技 术中华人民共和国住房和城乡建设部颁布的混凝土结构设计规范GB50010—2010《混凝土结构设计规范》于2011年7月1日开始正式执行。
GB50010规定:混凝土结构设计中不再设计使用HPB235线材。
纵向受力普通的钢筋和箍筋中可以使用HPB300线材:混凝土结构设计中HRB335螺纹钢只可以在纵向受力普通的钢筋和箍筋中使用,不能作为梁、柱纵向受力钢筋使用。
IV级、V级盘螺产品将迅速在设计中得到广泛应用。
建筑用钢材将逐步向高强度过渡。
为应对国家设计规范和市场变化,需开发系列盘螺产品。
1 工艺制定及优化1.1工艺制定的方向提高并稳定盘螺的性能有两种途径:一是提高钢坯成分,加钒;二是不加钒,通过精确控轧控冷,调整轧钢工艺。
现在钢铁市场的竞争必须建立在低成本的基础之上。
因此调整轧钢工艺,通过优化控轧控冷工艺来稳定和提高高速线材生产线盘螺质量成为当前解决问题的关键。
随着市场需求的变化和三安钢铁产品结构的调整,在三安钢铁有限公司轧钢厂高速线材生产线生产盘螺已势在必行,于2011年进行了盘螺试生产。
在试生产过程中盘螺的屈服强度极不稳定,HRB400E的屈服强度最高为490M P a ,而最低为395MPa,最低值低于了国家标准要求,在其后对全线设备进行了处理后,组织了一次批量生产,但性能还是不稳定。
为此我们对影响产品力学性能的原因进行了分析并对相应的控轧控冷参数进行了修改和调整。
1.2HRB 400盘螺力学性能问题分析三安钢铁有限公司轧钢厂高速线材生产线全轧线共有26架轧机,加热炉为蓄热式步进梁式,轧机布置为:粗轧6架、中轧6架、预精轧4架及精轧机10架(见图1),其生产工艺流程为:加热炉加热—粗轧—1#飞剪—中轧—2#飞剪—预精轧—1#水箱—3#飞剪—精轧—2#~4#水箱—夹送辊—吐丝机—斯太尔摩风冷线。
控制轧制工艺主要是通过控制轧制工艺参数,如加热温度、变形速度与应变速率、终轧温度等。
提高HRB400盘螺力学性能的轧制工艺优化
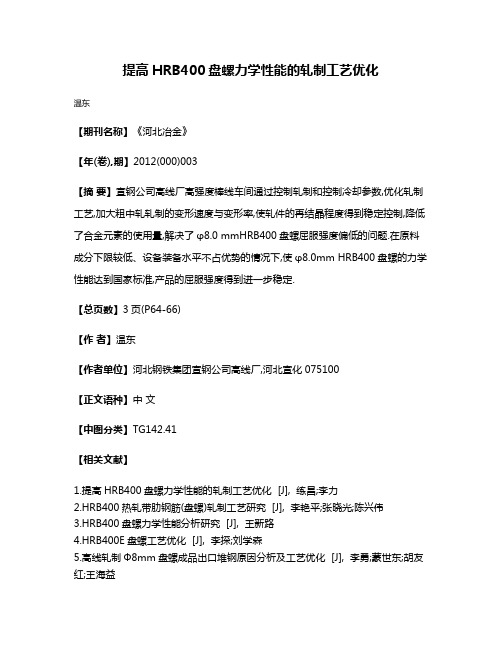
提高HRB400盘螺力学性能的轧制工艺优化
温东
【期刊名称】《河北冶金》
【年(卷),期】2012(000)003
【摘要】宣钢公司高线厂高强度棒线车间通过控制轧制和控制冷却参数,优化轧制工艺,加大粗中轧轧制的变形速度与变形率,使轧件的再结晶程度得到稳定控制,降低了合金元素的使用量,解决了φ8.0 mmHRB400盘螺屈服强度偏低的问题.在原料成分下限较低、设备装备水平不占优势的情况下,使φ8.0mm HRB400盘螺的力学性能达到国家标准,产品的屈服强度得到进一步稳定.
【总页数】3页(P64-66)
【作者】温东
【作者单位】河北钢铁集团宣钢公司高线厂,河北宣化075100
【正文语种】中文
【中图分类】TG142.41
【相关文献】
1.提高HRB400盘螺力学性能的轧制工艺优化 [J], 练昌;李力
2.HRB400热轧带肋钢筋(盘螺)轧制工艺研究 [J], 李艳平;张晓光;陈兴伟
3.HRB400盘螺力学性能分析研究 [J], 王新路
4.HRB400E盘螺工艺优化 [J], 李探;刘学森
5.高线轧制Ф8mm盘螺成品出口堆钢原因分析及工艺优化 [J], 李勇;蒙世东;胡友红;王海益
因版权原因,仅展示原文概要,查看原文内容请购买。
φ8.0mm盘螺尾部吐丝失控的原因及处理

φ8.0mm盘螺尾部吐丝失控的原因及处理摘要:针对柳钢高线φ8.0mm盘螺频繁出现尾部吐丝乱圈、圈形失控、严重影响轧制节奏的问题,进行了理论和实践两方面的分析。
根据现场实际工况从工艺、设备等方面进行逐一排查,最终找出φ8.0mm盘螺尾部吐丝频繁乱圈的产生原因,并给出了解决问题的方案。
关键词:尾部吐丝;圈形失控;解决方案1 概述柳钢高线自2016年10月开始生产抗震盘螺,尤其是2017年3月后φ8.0mm规格盘螺降低吐丝温度后频繁出现尾部吐丝乱圈、圈形失控、极不规则的现象。
该现象的主要特征是:尾部吐丝后倒数第12或13圈呈椭圆形、而且此圈形大小与前后圈形存在着明显差别;尾部圈形小且椭圆在上集卷落圈很困难,需要人工干预才能落料集卷(见图1、图2)。
现场生产时出现尾部吐丝小圈的情况毫无征兆,往往之前都是正常轧制正常集卷,在任何参数都没有改变的情况下,突然出现一根或两根尾部吐丝小圈的情况,待处理完集卷故障后又恢复正常轧制正常集卷。
(图1)(图2)尾部小圈现象的频繁出现,使现场操作人员的精神高度紧张,处理集卷、废卷的劳动强度大大增加。
为了减少尾部小圈造成的损失,现场一旦发现尾部小圈,轧钢操作工立即人为停止STM风冷线辊道处理故障、这样产生非正常工艺生产的“爬行钢”需判废,或人为启动1#和2#飞剪碎断轧机区域轧件,严重的影响了生产节奏,增加了废品率和故障处理时间,成为限制产能发挥的瓶颈。
2 原因分析φ8.0mm规格盘螺尾部圈形不规整,通过观察基本上出现在尾部倒数第12圈或13圈,圈形呈椭圆形,盘卷倒数第1圈到盘卷倒数12或13圈直线长度大概在39.60-42.90米。
通过查阅图纸可知精轧机28#架到3#夹送辊直线距离42.56米,由此可知φ8.0mm规格盘螺尾部倒数第12圈或13圈出现不规整小圈是由于轧件尾部在螺纹成品孔脱槽瞬间受到横肋槽切割附加拉力造成的。
横肋是成品前孔的椭圆轧件进入成品孔的基圆时,金属受挤压而形成的,当轧件脱槽时凸起的横肋往往受到横肋槽的切割,就会有一个拉力附加到轧件上,从而影响轧件顺利脱槽。
盘螺工艺流程

盘螺工艺流程
《盘螺工艺流程》
盘螺是一种古老的手工艺品,具有悠久的历史和独特的制作工艺。
盘螺的工艺流程相当复杂,需要经过多道工序才能完成。
下面就让我们来了解一下盘螺的工艺流程。
首先,选择合适的原材料非常重要。
盘螺的原材料有很多种,包括木头、竹子、麻绳等。
在选择原材料的时候,要考虑到颜色、质地和适合的工艺要求。
接下来是制作模具。
盘螺通常是通过模具来制作的,所以制作模具是非常重要的一步。
制作模具需要根据设计图纸来设计模具的结构和形状,然后通过木工工具进行精细加工,最终得到符合要求的模具。
然后是原料加工。
根据模具的形状和尺寸,将原材料进行切割和加工,以便后续的制作工序。
接着是组合制作。
在盘螺的制作过程中,往往需要将不同形状的原料进行组合,然后进行固定和打磨,最终得到成型的盘螺。
最后是上光和涂饰。
盘螺的表面需要进行上光处理,使其表面更加光滑细腻。
同时,根据需要还可以进行彩绘、雕刻等工艺,以丰富盘螺的艺术效果。
通过以上的工艺流程,完成了盘螺的制作。
盘螺工艺流程不仅
需要工匠们的精湛技艺,更需要耐心和细致的态度。
盘螺工艺不仅是一种手工艺品,更是一种对传统文化和工艺精神的传承和表达。
高速线材8mm规格盘螺头部缺陷原因分析与控制
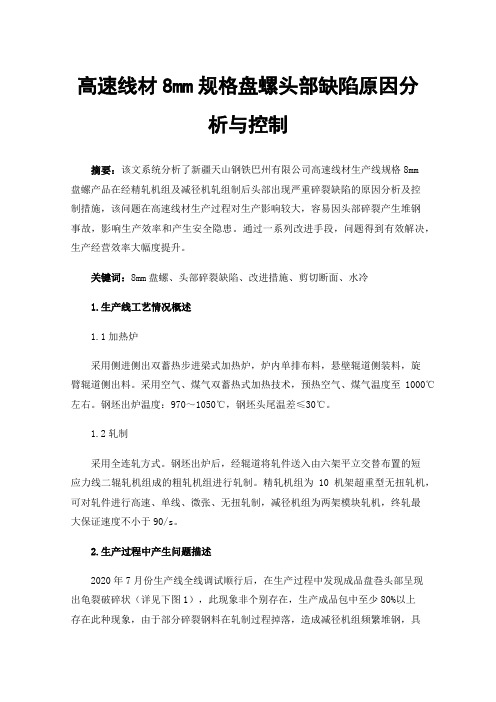
高速线材8mm规格盘螺头部缺陷原因分析与控制摘要:该文系统分析了新疆天山钢铁巴州有限公司高速线材生产线规格8mm盘螺产品在经精轧机组及减径机轧组制后头部出现严重碎裂缺陷的原因分析及控制措施,该问题在高速线材生产过程对生产影响较大,容易因头部碎裂产生堆钢事故,影响生产效率和产生安全隐患。
通过一系列改进手段,问题得到有效解决,生产经营效率大幅度提升。
关键词:8mm盘螺、头部碎裂缺陷、改进措施、剪切断面、水冷1.生产线工艺情况概述1.1加热炉采用侧进侧出双蓄热步进梁式加热炉,炉内单排布料,悬壁辊道侧装料,旋臂辊道侧出料。
采用空气、煤气双蓄热式加热技术,预热空气、煤气温度至1000℃左右。
钢坯出炉温度:970~1050℃,钢坯头尾温差≤30℃。
1.2轧制采用全连轧方式。
钢坯出炉后,经辊道将轧件送入由六架平立交替布置的短应力线二辊轧机组成的粗轧机组进行轧制。
精轧机组为10机架超重型无扭轧机,可对轧件进行高速、单线、微张、无扭轧制,减径机组为两架模块轧机,终轧最大保证速度不小于90/s。
2.生产过程中产生问题描述2020年7月份生产线全线调试顺行后,在生产过程中发现成品盘巻头部呈现出龟裂破碎状(详见下图1),此现象非个别存在,生产成品包中至少80%以上存在此种现象,由于部分碎裂钢料在轧制过程掉落,造成减径机组频繁堆钢,具体体现为头部碎裂部分卡进口导卫导致堆钢,严重制约正常生产秩序。
由于8mm 盘螺轧制后仍较细,轧件在精轧机及其后续通道运行中稍有阻力,就会造成轧件头部堆钢[1]。
图1 头部龟裂破碎情况图2 3#剪剪切断面1.原因分析由于生产过程中其他规格产品虽有类似现象,但整体较8mm盘螺轻,既使头部龟裂,也未发现有龟裂后掉落的现象,所以8mm盘螺产品头部龟裂后掉块问题既是轧制线轧制过程的普遍性问题,也属改规格生产个性问题。
3.1钢坯通过对比该问题出现前后各钢种成分控制、外观质量、炼钢加入合金等材料后,前后完全一致,排除了因坯料原因造成盘螺产品头部龟裂掉块原因。
高线散冷工艺改造与盘螺性能优化思路探究
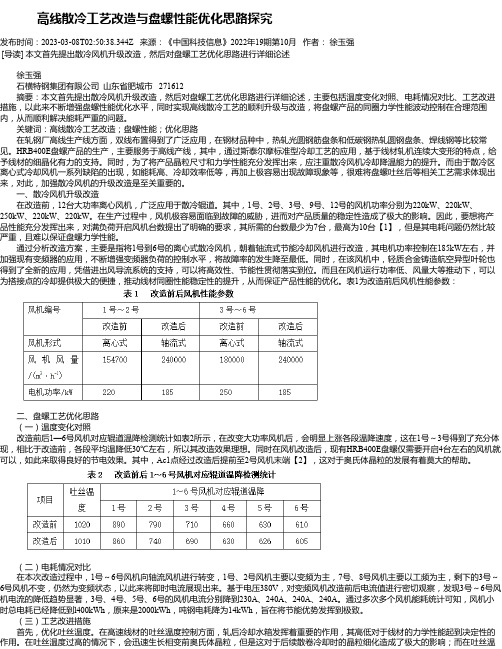
高线散冷工艺改造与盘螺性能优化思路探究发布时间:2023-03-08T02:50:38.344Z 来源:《中国科技信息》2022年19期第10月作者:徐玉强[导读] 本文首先提出散冷风机升级改造,然后对盘螺工艺优化思路进行详细论述徐玉强石横特钢集团有限公司山东省肥城市 271612摘要:本文首先提出散冷风机升级改造,然后对盘螺工艺优化思路进行详细论述,主要包括温度变化对照、电耗情况对比、工艺改进措施,以此来不断增强盘螺性能优化水平,同时实现高线散冷工艺的顺利升级与改造,将盘螺产品的同圈力学性能波动控制在合理范围内,从而顺利解决能耗严重的问题。
关键词:高线散冷工艺改造;盘螺性能;优化思路在轧钢厂高线生产线方面,双线布置得到了广泛应用,在钢材品种中,热轧光圆钢筋盘条和低碳钢热轧圆钢盘条、焊线钢等比较常见。
HRB400E盘螺产品的生产,主要服务于高线产线,其中,通过斯泰尔摩标准型冷却工艺的应用,基于线材轧机连续大变形的特点,给予线材的细晶化有力的支持。
同时,为了将产品晶粒尺寸和力学性能充分发挥出来,应注重散冷风机冷却降温能力的提升。
而由于散冷区离心式冷却风机一系列缺陷的出现,如能耗高、冷却效率低等,再加上极容易出现故障现象等,很难将盘螺吐丝后等相关工艺需求体现出来,对此,加强散冷风机的升级改造是至关重要的。
一、散冷风机升级改造在改造前,12台大功率离心风机,广泛应用于散冷辊道。
其中,1号、2号、3号、9号、12号的风机功率分别为220kW、220kW、250kW、220kW、220kW。
在生产过程中,风机极容易面临到故障的威胁,进而对产品质量的稳定性造成了极大的影响。
因此,要想将产品性能充分发挥出来,对满负荷开启风机台数提出了明确的要求,其所需的台数最少为7台,最高为10台【1】,但是其电耗问题仍然比较严重,且难以保证盘螺力学性能。
通过分析改造方案,主要是指将1号到6号的离心式散冷风机,朝着轴流式节能冷却风机进行改造,其电机功率控制在185kW左右,并加强现有变频器的应用,不断增强变频器负荷的控制水平,将故障率的发生降至最低。
- 1、下载文档前请自行甄别文档内容的完整性,平台不提供额外的编辑、内容补充、找答案等附加服务。
- 2、"仅部分预览"的文档,不可在线预览部分如存在完整性等问题,可反馈申请退款(可完整预览的文档不适用该条件!)。
- 3、如文档侵犯您的权益,请联系客服反馈,我们会尽快为您处理(人工客服工作时间:9:00-18:30)。
三安Φ8mm盘螺轧制工艺的制定及优化
摘要:三安钢铁有限公司轧钢厂高速线材生产线针对盘螺HRB400E力学性能偏低的情况,通过控制轧制和控制冷却参数,优化轧制工艺,解决了盘螺屈服强度偏低的问题,且通过对盘条通条性能进行优化,产品质量有显著的提高。
在原料成分下限较低、设备装备水平不占优势的情况下,使盘螺的力学性能达到国家标准,产品的屈服强度得到进一步稳定。
关键词:盘螺轧制工艺优化
1 前言
中华人民共和国住房和城乡建设部颁布的混凝土结构设计规范GB50010—2010《混凝土结构设计规范》于2011年7月1日开始正式执行。
GB50010规定:混凝土结构设计中不再设计使用HPB235线材。
纵向受力普通的钢筋和箍筋中可以使用HPB300线材:混凝土结构设计中HRB335螺纹钢只可以在纵向受力普通的钢筋和箍筋中使用,不能作为梁、柱纵向受力钢筋使用。
IV级、V级盘螺产品将迅速在设计中得到广泛应用。
建筑用钢材将逐步向高强度过渡。
为应对国家设计规范和市场变化,需开发系列盘螺产品。
2 工艺制定及优化
2.1 工艺制定的方向
提高并稳定盘螺的性能有两种途径:一是提高钢坯成分,加钒;二是不加钒,通过精确控轧控冷,调整轧钢工艺。
现在钢铁市场的竞争必须建立在低成本的基础之上。
因此调整轧钢工艺,通过优化控轧控冷工艺来稳定和提高高速线材生产线盘螺质量成为当前解决问题的关键。
随着市场需求的变化和三安钢铁产品结构的调整,在三安钢铁有限公司轧钢厂高速线材生产线生产盘螺已势在必行,于2011年进行了盘螺试生产。
在试生产过程中盘螺的屈服强度极不稳定,HRB400E 的屈服强度最高为490MPa,而最低为395MPa,最低值低于了国家标准要求,在其后对全线设备进行了处理后,组织了一次批量生产,但性能还是不稳定。
为此我们对影响产品力学性能的原因进行了分析并对相应的控轧控冷参数进行了修改和调整。
2.2 HRB400盘螺力学性能问题分析
三安钢铁有限公司轧钢厂高速线材生产线全轧线共有26架轧机,加热炉为蓄热式步进梁式,轧机布置为:粗轧6架、中轧6架、预精轧4架及精轧机10架(图1),其生产工艺流程为:加热炉加热---粗轧---1#飞剪---中轧---2#飞剪---预精轧---1#水箱---3 #飞剪---精轧---2#~4# 水箱---夹送辊---吐丝机---斯太尔摩风冷线。
控制轧制工艺主要是通过控制轧制工艺参数,如加热温度、变形速度与应变速率、终轧温度等。
在经过奥氏体向铁素体和珠光体的相变后,形成细化的铁素体晶粒和较细小的珠光体球团,从而达到提高钢的强度、韧性和
焊接性能的目的。
控制冷却是为了细化铁素体晶粒,减小珠光体片层间距,阻止碳化物在高温下析出,以提高析出强化效果。
2.2.1 存在问题
在试轧Φ8 mm HRB400E 盘螺的过程发现不足之处:盘螺成品性能合格率较低,成品性能不达国标,判废及改判率高;盘螺屈服点不明显,Rp0.2较低;精轧机设备负荷大,精轧电流101%左右,精轧机各架辊箱所受的长时间负载以及瞬间冲击加大,精轧机辊箱、锥箱故障增多;屈服强度和抗拉强度波动较大,成品通条性不均匀,头、中、尾和搭接处与非搭接处成品性能差距大。
2.2.2 对以上问题的分析
造成问题的主要原因有以下三点:盘螺轧制工艺存在进精轧机温度偏高,使用的水冷器结构简单,水冷导槽呈密闭状,穿水冷却的能力不足;在保证成品性能情况下,轧制速度过快,导致精轧机负荷过大(精轧机电流开轧时最大达到101%);盘卷在辊道上运行时由于线材两侧重叠搭接,搭接点不能错开,搭接处温度偏高,造成盘卷的通条冷却速度的不均匀。
2.3改进措施
⑴控制好加热温度,保证开轧温度。
加热温度和开轧温度直接影
响原始奥氏体晶粒大小,也影响粗中轧、预精轧及精轧道次之间奥氏体再结晶程度及其晶粒大小。
因此对加热炉炉温控制进行了优化。
①为了保证燃料燃烧充分,提高燃烧效率,重新制定了空燃比。
正常过钢时,加热段空气过剩系数为1~1.1,均热段空气过剩系数为1。
残氧量控制在1.5%。
②修订加热炉各段温度控制范围:加热段炉温980-1000~C,均热段炉温1000-1030~C。
③开轧温度由1000-1020~C 降为980-1000~C。
⑵改造穿水器。
精轧机由于轧速快,轧件通过精轧机变形热大于轧件散热,属于升温轧制。
在实际生产过程中,1#水箱水冷的冷却能力有限,影响成品性能的提高。
要获得更高的成品性能,必须降低进精轧温度。
为此,对1#水箱进行改造。
使用棒材Ф26内孔的穿水器(图3)代替高线预精轧后穿水器(图2),采用改进后的水冷器,水量设置可以提高较多,加强高线预精轧后穿水冷却的能力。
表3为使用改造后穿水器后批量生产成品性能的情况。
⑶精轧机改由25#出成品。
采用精轧机末架26#出成品时,成品性能都能达到要求,但精轧机电机负载过大,电流大,对设备造成损伤。
而采用从24#出成品,25#、26#两架轧机空过时,精轧机电机负载较轻,但无形中降低了线材轧机的生产能力。
第24#出口速度仅为50m/s,试用阶段,班产量一直徘徊在600t之内。
设计一套精轧机25#出盘螺Φ8 mm线材的孔型系统,满足生产所需是十分必要的。
通过对各道次孔型和导卫的重新设计,满足正常生产的要求且解决了精轧机电机负载过高这一问题。
经过剖析Φ6.5mm线材的孔型系统,进行合理的工艺参数选择,设备强度(主要是点击功率)校验。
原来第8架轧制盘螺Φ8mm线材时电机负荷较轻。
现在通过加大入口坯料,为第9架轧制盘螺Φ8 mm线材,正是充分挖掘设备潜力。
25#出口速度达到了70m/s,由于轧速提高,轧件在相对高速情况下变形,线材表面质量有所提高。
又由于末架轧速提高,使夹送辊、吐丝机的速度相应提高,接近了设计速度的中间值,对设备运行有利。
投产后班产量就达到了900t,取得明显的经济效益。
通过生产实践证明,设备性能满足生产要求,实测工艺参数与设计基本吻合,该孔型系统的设计方法正确,工艺参数选择基本合理。
⑷对风冷线的改造。
采取的措施主要有:①将高速线材生产线风冷线上的12台冷却风机改造为变频风机,吨钢电耗由174 kwh/t降低到159kwh/t。
通过调整风机开启的台数、风量,以及辊道输送速度,控制变相时的冷却曲线,达到控制成品的金相组织,保证产品力学性能;②生产过程中不同季节开启不同风机,保证冷床两侧风量大,中间风量小。
盘螺因两侧搭接在一起,热量多,两侧风量大有利于带走热量。
在冷床上的6个跌落段,调节跌落段前后辊道速度。
跌落段位置在风机的交接位置。
冷床前段设置三个连续分段,后段设置三个连续分段。
前三个连续的跌落段高度相等(l00~150mm),后三个连续的跌落段高度相等(200~250mm),此高度既能保证盘螺头部不会产生倾
翻,又能保证一定的高度差。
调节每个跌落段前后的辊道速度,在前后辊道速度不一致和跌落段的高度差的作用下,可以让盘螺的搭接点产生相对的位移,从而均匀的冷却,提高盘螺的通条性能;③在风冷辊道上增加几组侧边辊,使盘卷在辊道上运行时搭接点能够错开;④在风冷线上的1-3#风机处增加喷雾模式,解决盘卷头部性能偏低。
3 优化并确定轧制工艺
对盘螺成品性能、通条性能探究及攻关,采用轧前穿水,控制水箱开度,轧后风冷、风冷头部喷雾等方式综合控制轧制,通过大量试验摸索制定较为适宜的稳定的工艺方案。
如表1、2所示:
4 取得效果
工艺优化前,盘螺性能较低且不稳定,优化后性能较高且稳定,8mm HRB400E盘螺的力学通条性能比较见表3。
表3中的数据为工艺调整前后随机抽出的批号的性能对比,从表中可以计算出,工艺调整后中8.0mmHRB400E盘螺的屈服强度由平均411MPa提高到437.5MPa;抗拉强度由633MPa降到622MPa、延伸率由26.2%提高到30.6%。
从几组数据看,工艺调整后,抗拉强度变化不明显,但屈服强度和延伸率变化较大。
优化前后的拉伸曲线如图4、图5所示。
5 结语
通过严格控制和调整三安钢铁有限公司轧钢厂高速线材生产线开轧、精轧入口温度和提高水冷、风冷速度等控制轧制和控制冷却参数,使机架间再结晶程度得到了有效控制,使终轧后的控冷工艺进一步得到优化,有力地保证了相变产物的组织与形态,产品综合性能得到稳定和提高,有效地降低钢坯的合金元素使用量。
解决了生产该产品抗拉强度与屈服强度几乎成反比的问题,在技术上有了更深的认识。
参考文献
[1] 温东,提高HRB400盘螺力学性能的轧制工艺优化[J],河北冶金,2012年3期
[2] 张志斌,斯泰尔摩凤冷线的改进[J],山西科技,2012年2期
[3] 练昌,李力,提高HRB400盘螺力学性能的轧制工艺优化[J],水钢科技,2013年124期。