日本转炉脱磷生产工艺新技术
转炉炼钢流程中的脱磷工艺
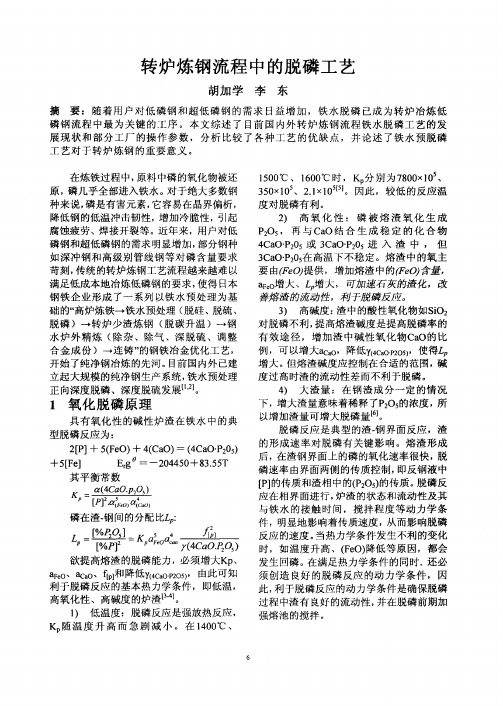
磷 在渣. %P
:
a ̄
7 C . ・ y4 a Q ) ( OP 0 2
欲提 高熔 渣 的脱磷 能力 ,必须增 大K 、 p ae、aa、f]口 F 0 co t 降低1 C .O) 由止 可 失 p , P 5 ( O2 , 4 匕 l J 利 于脱磷 反应 的基 本热 力学 条件 , 即低温 , 高 氧化 性 、高碱度 的炉 渣 【 3 。 1 低温 度 :脱磷 反应 是强 放热 反应 , ) KD 温 度 升 高 而 急 剧 减 小 。 在 10  ̄ 随 4 0C、
3 高碱 度 : 中的酸 性氧化 物如 SO2 ) 渣 i 对脱 磷 不利 , 高熔渣 碱 度是 提 高脱磷 率 的 提 有 效 途 径 ,增 加 渣 中 碱 性氧 化物 C O的 比 a 例 ,可 以增大 a ,降低 丫CO 25 co (a.o) 4 P ,使得三 p 增 大 。 熔渣碱 度 应控 制在 合适 的范 围 , 但 碱 度过 高 时渣 的流 动性差 而 不利 于脱磷 。 4 大 渣 量 :在 钢渣 成 分 一 定 的情 况 ) 下 ,增 大渣 量意 味着稀 释 了P05 2 的浓度 , 所 以增 加渣 量 可增 大脱磷 量 【。 o J 脱 磷 反应 是 典型 的渣 界 面 反应 ,渣 钢 的形 成 速 率对 脱 磷 有 关 键影 响 。熔 渣 形成 后 ,在渣 钢 界面上 的磷 的氧 化速 率很 快 , 脱 磷速 率 由界 面两侧 的传 质控 制 , 即反钢 液 中 【] P 的传 质 和渣相 中 的(2 ) Po5的传质 。 磷反 脱 应 在相 界面 进 行 , 炉渣 的状 态和 流动 性及其 与 铁 水 的接触 时 间 ,搅 拌程 度 等 动 力 学条 件 ,明显地 影响着 传质 速度 , 从而 影 响脱磷 反应 的速度 。 当热 力学条 件 发生 不利 的变化 时 ,如温 度升 高 、(e ) F O 降低 等原 因,都会 发 生 回磷 。在满足 热力 学条 件 的 同时 . 还必 须 创 造 良好 的脱 磷 反 应 的动 力 学 条 件 , 因 此 , 于脱 磷 反应 的动力 学 条件 是确 保脱磷 利 过 程 中渣 有 良好 的流 动性 , 并在 脱磷 前期加 强熔 池 的搅 拌 。
转炉脱磷造渣工艺
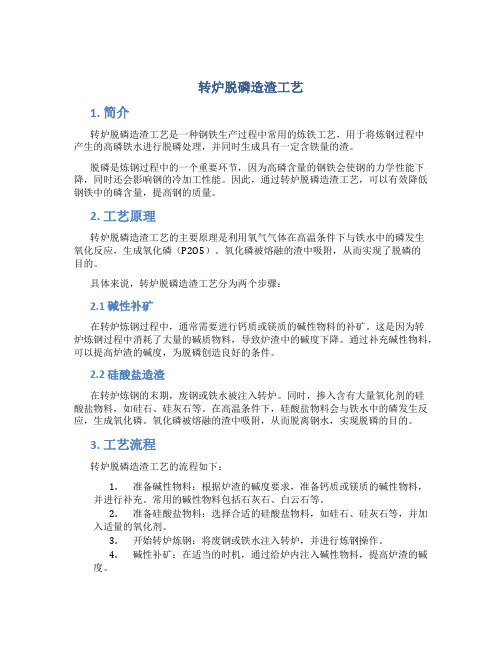
转炉脱磷造渣工艺1. 简介转炉脱磷造渣工艺是一种钢铁生产过程中常用的炼铁工艺,用于将炼钢过程中产生的高磷铁水进行脱磷处理,并同时生成具有一定含铁量的渣。
脱磷是炼钢过程中的一个重要环节,因为高磷含量的钢铁会使钢的力学性能下降,同时还会影响钢的冷加工性能。
因此,通过转炉脱磷造渣工艺,可以有效降低钢铁中的磷含量,提高钢的质量。
2. 工艺原理转炉脱磷造渣工艺的主要原理是利用氧气气体在高温条件下与铁水中的磷发生氧化反应,生成氧化磷(P2O5)。
氧化磷被熔融的渣中吸附,从而实现了脱磷的目的。
具体来说,转炉脱磷造渣工艺分为两个步骤:2.1 碱性补矿在转炉炼钢过程中,通常需要进行钙质或镁质的碱性物料的补矿。
这是因为转炉炼钢过程中消耗了大量的碱质物料,导致炉渣中的碱度下降。
通过补充碱性物料,可以提高炉渣的碱度,为脱磷创造良好的条件。
2.2 硅酸盐造渣在转炉炼钢的末期,废钢或铁水被注入转炉。
同时,掺入含有大量氧化剂的硅酸盐物料,如硅石、硅灰石等。
在高温条件下,硅酸盐物料会与铁水中的磷发生反应,生成氧化磷。
氧化磷被熔融的渣中吸附,从而脱离钢水,实现脱磷的目的。
3. 工艺流程转炉脱磷造渣工艺的流程如下:1.准备碱性物料:根据炉渣的碱度要求,准备钙质或镁质的碱性物料,并进行补充。
常用的碱性物料包括石灰石、白云石等。
2.准备硅酸盐物料:选择合适的硅酸盐物料,如硅石、硅灰石等,并加入适量的氧化剂。
3.开始转炉炼钢:将废钢或铁水注入转炉,并进行炼钢操作。
4.碱性补矿:在适当的时机,通过给炉内注入碱性物料,提高炉渣的碱度。
5.硅酸盐造渣:当转炉炼钢接近末期时,通过给炉内注入硅酸盐物料,利用氧化剂促进磷的氧化反应。
6.淋渣:根据炉内的渣情况,选择合适的时间进行淋渣操作。
淋渣可以通过人工或机械设备进行。
7.渣铁分离:在脱磷过程中,渣中生成的氧化磷会被吸附在渣中,从而脱离钢水。
通过合适的方法,将渣与钢水分离。
8.尾渣处理:处理分离出来的尾渣,并对其进行资源化利用或安全处理。
关于炼钢业的环保问题:日本高级钢冶炼环保技术

关于炼钢业的环保问题:日本高级钢冶炼环保技术文章来源:法钢特种钢材(上海)有限公司日本是世界先进的钢铁生产国家,其在炼钢方面存在的矛盾问题是,一方面采用大型设备进行大批量生产来提高生产效率,另一方面为满足产品高级化、多品种化需求,不得不降低生产效率和增加能源消耗。
以京都议定书为代表的CO2减排、减少能耗、节省资源等全球性的环保要求不断高涨,在这种情况下,钢铁业需要研究根本性对策以实现低环境负荷生产。
日本住友金属和歌山钢厂在高级钢冶炼环保技术方面开发出良好工艺,现介绍如下。
1 炉渣、粉尘的循环利用技术1.1 炉渣循环利用在传统转炉精炼法中,由于脱磷能力小,所以要投入大量的脱磷剂,因此产生大量的炉渣,排出的炉渣废弃物增加了环境负荷。
虽然炉渣可以在土建工程和路基建设中得到循环利用。
但是由于炉渣的市场需求量不断变化,所以对炉渣发生量的控制就成为一个急需解决的问题。
对流精炼法由于利用顶底吹转炉分别进行脱碳和脱磷精炼,所以可以实现脱磷处理条件的最佳化,并且脱碳处理使用完的精炼剂可以在脱磷处理中进行再利用,所以渣量大幅度减少。
对流精炼法由于精炼剂再利用和脱磷处理条件最佳化,使炉渣的发生量从97kg/t钢下降到52kg/t钢,渣量约减少了一半。
1.2 粉尘循环利用在钢铁厂的产品制造过程中会产生镀锌废钢,为在厂内将这些被锌污染的废钢处理掉,就将这些废钢作为转炉的钢铁料使用。
因此,转炉吹炼中产生的粉尘含Zn。
由于转炉产生的粉尘量很大,分离回收Zn的成本很高,所以不得不采用填埋方法处理含Zn粉尘,但这种方法增加了环境负荷。
由于脱磷反应比脱碳反应的温度低,供氧速度小,所以烟尘中Zn损失小。
因此,在进行脱磷处理时投入含Zn废钢,就可以生成少量高浓度含Zn粉尘。
这样,就比较容易从回收粉尘中分离出Zn。
对流精炼法利用粉尘集尘装置回收少量高浓度含Zn粉尘,再利用回转窑将粗锌和铁粉进行分离,将粗锌销售给锌精炼厂做原料,铁粉用作厂内高炉的炼铁原料。
转炉炼钢脱磷工艺分析

II
第三章 试验方案的设计.............................................................................................................. 27 3.1 沙钢双渣脱磷的现状........................................................................................................ 27 3.1.1 双渣操作的好处......................................................................................................... 27 3.1.2 沙钢双渣脱磷情况.....................................................................................................27 3.1.3 脱磷的效果及回磷问题............................................................................................ 28 3.2 目前存在的问题................................................................................................................. 29 3.2.1 前期脱磷结果............................................................................................................. 29 3.3 影响前期脱磷的主要因素............................................................................................... 30 3.3.1 钢水中硅的氧化......................................................................................................... 30 3.3.2 前期渣碱度的控制.....................................................................................................30 3.3.3 倒前期渣时间的控制................................................................................................ 31 3.4 180t 转炉冶炼终点脱磷情况.......................................................................................... 32 3.4.1 增碳剂加入量的控制................................................................................................ 32 3.4.2 冶炼终点脱磷情况.....................................................................................................32 3.5 180t 转炉冶炼工艺改进方案.......................................................................................... 32 3.5.1 冶炼前期控制............................................................................................................. 33 3.5.2 冶炼终点控制............................................................................................................. 33 结论..............................................................................................................................................35 参考文献..................................................................................................................................... 36 致 谢....................................................................................................................................... 37
专用转炉脱磷定义
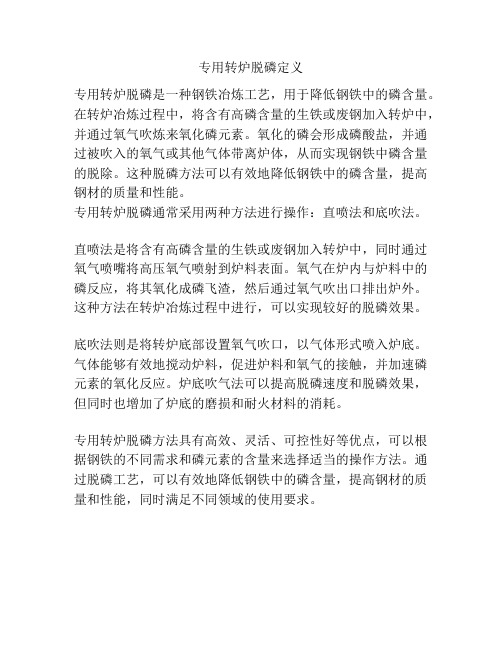
专用转炉脱磷定义
专用转炉脱磷是一种钢铁冶炼工艺,用于降低钢铁中的磷含量。
在转炉冶炼过程中,将含有高磷含量的生铁或废钢加入转炉中,并通过氧气吹炼来氧化磷元素。
氧化的磷会形成磷酸盐,并通过被吹入的氧气或其他气体带离炉体,从而实现钢铁中磷含量的脱除。
这种脱磷方法可以有效地降低钢铁中的磷含量,提高钢材的质量和性能。
专用转炉脱磷通常采用两种方法进行操作:直喷法和底吹法。
直喷法是将含有高磷含量的生铁或废钢加入转炉中,同时通过氧气喷嘴将高压氧气喷射到炉料表面。
氧气在炉内与炉料中的磷反应,将其氧化成磷飞渣,然后通过氧气吹出口排出炉外。
这种方法在转炉冶炼过程中进行,可以实现较好的脱磷效果。
底吹法则是将转炉底部设置氧气吹口,以气体形式喷入炉底。
气体能够有效地搅动炉料,促进炉料和氧气的接触,并加速磷元素的氧化反应。
炉底吹气法可以提高脱磷速度和脱磷效果,但同时也增加了炉底的磨损和耐火材料的消耗。
专用转炉脱磷方法具有高效、灵活、可控性好等优点,可以根据钢铁的不同需求和磷元素的含量来选择适当的操作方法。
通过脱磷工艺,可以有效地降低钢铁中的磷含量,提高钢材的质量和性能,同时满足不同领域的使用要求。
转炉炼钢脱磷工艺理论与实践
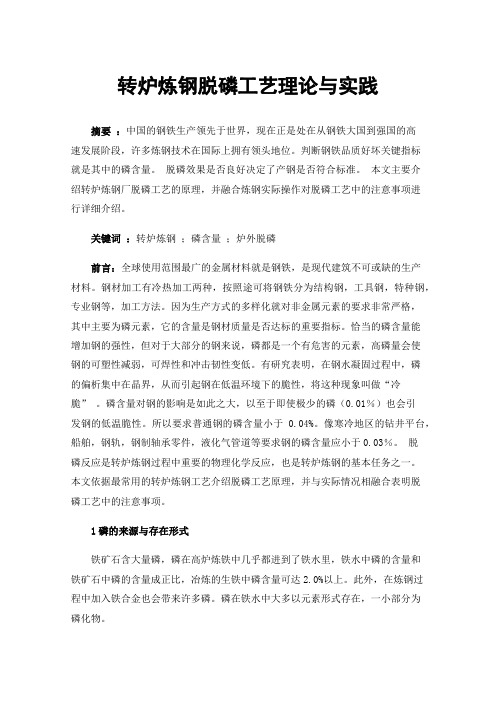
转炉炼钢脱磷工艺理论与实践摘要:中国的钢铁生产领先于世界,现在正是处在从钢铁大国到强国的高速发展阶段,许多炼钢技术在国际上拥有领头地位。
判断钢铁品质好坏关键指标就是其中的磷含量。
脱磷效果是否良好决定了产钢是否符合标准。
本文主要介绍转炉炼钢厂脱磷工艺的原理,并融合炼钢实际操作对脱磷工艺中的注意事项进行详细介绍。
关键词:转炉炼钢;磷含量;炉外脱磷前言:全球使用范围最广的金属材料就是钢铁,是现代建筑不可或缺的生产材料。
钢材加工有冷热加工两种,按照途可将钢铁分为结构钢,工具钢,特种钢,专业钢等,加工方法。
因为生产方式的多样化就对非金属元素的要求非常严格,其中主要为磷元素,它的含量是钢材质量是否达标的重要指标。
恰当的磷含量能增加钢的强性,但对于大部分的钢来说,磷都是一个有危害的元素,高磷量会使钢的可塑性减弱,可焊性和冲击韧性变低。
有研究表明,在钢水凝固过程中,磷的偏析集中在晶界,从而引起钢在低温环境下的脆性,将这种现象叫做“冷脆” 。
磷含量对钢的影响是如此之大,以至于即使极少的磷(0.01%)也会引发钢的低温脆性。
所以要求普通钢的磷含量小于0.04%。
像寒冷地区的钻井平台,船舶,钢轨,钢制轴承零件,液化气管道等要求钢的磷含量应小于0.03%。
脱磷反应是转炉炼钢过程中重要的物理化学反应,也是转炉炼钢的基本任务之一。
本文依据最常用的转炉炼钢工艺介绍脱磷工艺原理,并与实际情况相融合表明脱磷工艺中的注意事项。
1磷的来源与存在形式铁矿石含大量磷,磷在高炉炼铁中几乎都进到了铁水里,铁水中磷的含量和铁矿石中磷的含量成正比,冶炼的生铁中磷含量可达2.0%以上。
此外,在炼钢过程中加入铁合金也会带来许多磷。
磷在铁水中大多以元素形式存在,一小部分为磷化物。
2 转炉炼钢脱磷原理与条件2.1 转炉炼钢脱磷原理在转炉吹炼过程中,铁水中的磷被氧化成P 2O 5变成炉渣。
P 2O 5是一种酸性含氧物质,能和炉渣中的碱性含氧物质FeO 、CaO 、 MnO 、MgO 等形成磷酸盐化合物。
转炉炼钢脱磷工艺的探讨

转炉炼钢脱磷工艺的探讨【摘要】本文从脱磷的热力学分析入手,对冶炼过程中温度、炉渣碱度、渣中(FeO),等对磷含量的影响进行了探讨。
同时探讨了回磷的原因、影响的因素和防止的措施。
【关键词】转炉炼钢;脱磷工艺;探讨磷在钢中是以【Fe3P】或【Fe2P】形式存在,一般以【P】表示。
磷含量高时,会使钢的朔性和韧性降低,即使钢的脆性增加,这种现象低温时更严重,通常把它称为“冷脆”。
且这种影响常常随着氧,氮含量的增加而加剧。
磷在连铸坯中的偏析仅次于硫,同时它在铁固溶体中扩散速度又很小。
不容易均匀化,因而磷的偏析和难消除。
由于炼铁过程为还原性气氛,脱磷能力较差。
因此脱磷是炼钢过程的重要任务之一。
在20世纪90年代中后期,为解决超低磷钢的生产难题,世界上各大钢厂都曾经进行过转炉铁水脱磷实验研究。
1、铁水预处理方法1.1喷吹苏打粉处理日本住友公司鹿岛厂开发的“住友碱精炼法”是成功用于工业生产的苏打精炼法。
工艺流程:从高炉流出的铁水先经脱硅处理,即将高炉铁水注入混铁车内,用氮气输送和喷吹烧结矿粉,喷入量为每吨铁水40公斤,最大供粉速度为每分钟400公斤,最大吹氧量为每分钟50立方米,脱硅量约为0.4%。
脱硅处理后的铁水硅含量可降到0.1%以下。
然后用真空吸渣器吸出脱硅渣,进行脱磷处理,以氮气为载气向铁水中喷入苏打粉,苏打粉用量为每吨18公斤,最大供粉量为每分钟250公斤,最大吹氧量为每分钟50立方米,处理后铁水中【P】≤0.001%,【S】≤0.003%,再用真空吸渣器吸出脱磷渣,并将其送到苏打回收车间,经水浸后可回收约80%的Na2O,最后将处理过的铁水倒入转炉冶炼。
1.2喷吹石灰系熔剂处理由于石灰系熔剂具有成本低,对环境污染小的优点,因此受到重视,并不断对其深入研究,以使其满足精炼铁水的需要。
工艺流程:向高炉铁沟中加入铁磷进行脱硅处理,加入量为每吨铁水27公斤,处理后铁水含硅量由0.5%降到0.15%,氧的利用率为80%-90%。
脱磷工艺

1.3脱磷工艺钢水炉外脱磷的同时要氧化钢中的合金元素,因此脱磷一般在合金化以前进行。
目前,钢水脱磷的主要方法有:出钢过程中的加脱磷剂脱磷,利用出钢过程中的强烈搅拌以及高的氧分压,冲混脱磷;顶渣加喷粉脱磷,通过吹气使得渣金能够充分混合,达到有效脱磷;出钢后直接将脱磷剂加入钢包中脱磷等方式。
脱磷后要将脱磷渣扒除(以防止回磷和合金元素的损失)再合金化,LF升温,脱硫,RH脱气等操作。
其巾日本NKK采用钢包中喷吹转炉渣和偏硅酸钠脱磷,生产成品钢w(P)为20×10-6“的钢,如图所示。
图5 日本超低磷钢生产的工艺流程1.3.1脱磷冶炼工艺的发展国家正在大力发展高炉炉铁水预处理技术和精炼钢水炉技术后,分享最初的冶炼到炼钢炉完成任务的一部分,炼钢炉的功能越来越多地集中在一个简单的关碳变暖。
当初的承诺变暖的炼钢炉,脱硅,脱硫,脱磷,脱氧,脱碳合金,调整提炼的成分和温度的任务是在时间和空间的分离,分别执行不同的炼油设备线。
解放的炼钢炉,钢决策过程分解成更多更细的子进程和亚单位,转换器的效率大大提高。
钢铁生产过程中磷的去除主要是在铁水预处理,转炉或电炉氧化期,二次精炼三个阶段进行,三个阶段脱磷的特点如表1.1所示表 1.1 各工序脱磷特点比较低磷钢生产分低磷钢[%,P<0.01和超低磷钢[%,P <0.003生产两个过程。
低磷钢生生产能力主要依靠铁水脱磷预处理和氧气转炉炼钢去除钢中磷100410%×下面。
超低磷钢铁冶炼两种方式:其一是在欧洲和北美的崛起,没有铁水预处理转炉冶炼低温钢钢包精炼后,高碱度,高氧化残留物的使用激起脱磷,然后改变包,LF炉加热,在RH的再利用。
使用这种方法,60至70钢水磷含量410%×左右。
另一种方法是在日本的崛起,完整的铁水预处理,在铁水中的磷含量降低到0.02%左右,因此,钢水有不少于20410%×钢的磷含量,然后进行二次精炼处理,以非常低的硫,磷的生产,H,O,钢的N-水平。
转炉脱磷少渣炼钢工艺技术发展与现状概述

转炉脱磷少渣炼钢工艺技术发展与现状概述引言钢铁是现代社会重要的基础材料之一,而磷是钢铁中的一个有害杂质。
传统的炼钢工艺中,磷的含量往往难以控制,导致钢材性能下降。
为了解决这个问题,转炉脱磷少渣炼钢工艺被广泛应用。
本文将对转炉脱磷少渣炼钢工艺的发展与现状进行概述。
转炉脱磷少渣炼钢工艺的原理转炉脱磷少渣炼钢工艺是通过将含有磷的原料在高温下与氧化剂反应,将磷转化为易脱离熔渣的磷酸盐,从而实现脱磷的目的。
其基本原理如下:1.熔融脱磷:在高温条件下,钢中的磷溶解于熔渣中,通过加入适量的熔剂,形成易分离的磷酸盐熔渣。
2.氧化脱磷:在高温条件下,将空气、氧气或含氧气的气体通入转炉中,氧化钢中的磷,将其转化为磷酸盐。
3.过渡氧化脱磷:在转炉炉脱磷过程中,通过在转炉中加入适量的铁素体,将磷转化为铁磷,再将其转化为磷酸盐。
转炉脱磷少渣炼钢工艺的发展历程转炉脱磷少渣炼钢工艺起源于20世纪50年代,经过多年的研究和改进,逐渐成熟并得到广泛应用。
其发展历程主要包括以下几个阶段:1.早期工艺的发展:早期的转炉脱磷少渣炼钢工艺主要采用人工喷镁的方式进行脱磷,但由于操作不稳定、生产效率低等问题,限制了其在实际生产中的应用。
2.化学脱磷工艺的应用:20世纪60年代,化学脱磷工艺开始应用于转炉脱磷少渣炼钢中。
该工艺是通过加入一定比例的化学试剂,如石灰石、白云石等,与熔渣中的磷反应,形成易分离的磷酸盐。
3.氧化脱磷工艺的引入:20世纪70年代,随着氧气和氧气枪在炼钢工艺中的应用,氧化脱磷工艺得到了推广。
该工艺是通过在转炉中加入氧气,氧化钢中的磷,将其转化为磷酸盐。
4.过渡氧化脱磷工艺的发展:20世纪80年代,随着对转炉脱磷少渣炼钢工艺的进一步研究和优化,过渡氧化脱磷工艺得到了广泛应用。
该工艺是通过在转炉中加入铁素体,将磷转化为铁磷,再将其转化为磷酸盐。
5.现代工艺的创新与应用:近年来,随着科技的进步和钢铁工业的发展,转炉脱磷少渣炼钢工艺逐渐采用自动化控制、机器学习等现代技术,提高了工艺的稳定性和生产效率。
转炉脱磷造渣工艺
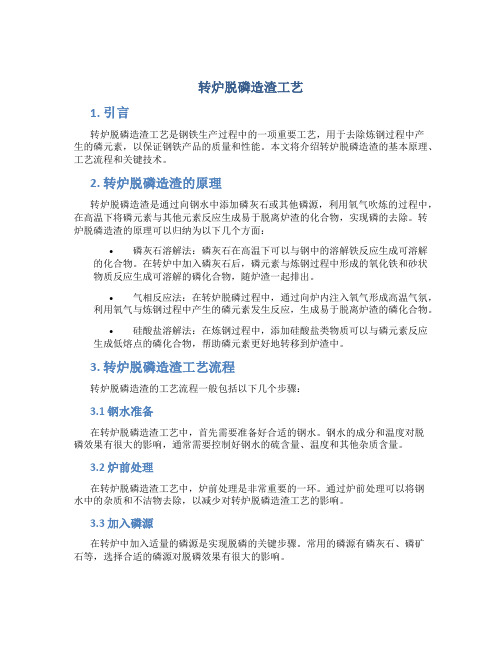
转炉脱磷造渣工艺1. 引言转炉脱磷造渣工艺是钢铁生产过程中的一项重要工艺,用于去除炼钢过程中产生的磷元素,以保证钢铁产品的质量和性能。
本文将介绍转炉脱磷造渣的基本原理、工艺流程和关键技术。
2. 转炉脱磷造渣的原理转炉脱磷造渣是通过向钢水中添加磷灰石或其他磷源,利用氧气吹炼的过程中,在高温下将磷元素与其他元素反应生成易于脱离炉渣的化合物,实现磷的去除。
转炉脱磷造渣的原理可以归纳为以下几个方面:•磷灰石溶解法:磷灰石在高温下可以与钢中的溶解铁反应生成可溶解的化合物。
在转炉中加入磷灰石后,磷元素与炼钢过程中形成的氧化铁和砂状物质反应生成可溶解的磷化合物,随炉渣一起排出。
•气相反应法:在转炉脱磷过程中,通过向炉内注入氧气形成高温气氛,利用氧气与炼钢过程中产生的磷元素发生反应,生成易于脱离炉渣的磷化合物。
•硅酸盐溶解法:在炼钢过程中,添加硅酸盐类物质可以与磷元素反应生成低熔点的磷化合物,帮助磷元素更好地转移到炉渣中。
3. 转炉脱磷造渣工艺流程转炉脱磷造渣的工艺流程一般包括以下几个步骤:3.1 钢水准备在转炉脱磷造渣工艺中,首先需要准备好合适的钢水。
钢水的成分和温度对脱磷效果有很大的影响,通常需要控制好钢水的硫含量、温度和其他杂质含量。
3.2 炉前处理在转炉脱磷造渣工艺中,炉前处理是非常重要的一环。
通过炉前处理可以将钢水中的杂质和不洁物去除,以减少对转炉脱磷造渣工艺的影响。
3.3 加入磷源在转炉中加入适量的磷源是实现脱磷的关键步骤。
常用的磷源有磷灰石、磷矿石等,选择合适的磷源对脱磷效果有很大的影响。
3.4 氧气吹炼在加入磷源后,转炉中开始进行氧气吹炼处理。
氧气的注入可以改变钢水中的气氛,促进磷元素与其他元素的反应,生成易于脱离炉渣的化合物。
3.5 炉渣处理转炉脱磷造渣过程中产生的炉渣需要进行处理。
一般情况下,炉渣会经过冷却、处理、分离等步骤,将渣中的磷元素尽可能去除,以保证炉渣的质量和性能。
4. 转炉脱磷造渣的关键技术转炉脱磷造渣的关键技术包括以下几个方面:4.1 磷源选择选择合适的磷源对于脱磷工艺的效果至关重要。
转炉双联法脱磷技术

1.5、转炉双联法与常规冶炼的比较
23
24
25
26
转炉双联法与常规冶炼的比较
由表2可见,转炉双联法冶炼工艺主要有点:
●降低能源消耗; ●降低熔剂和其他物料的消耗; ●减少渣量,金属收得率高,减轻渣处理工作量; ●缩短转炉的冶炼周期、 ●提高转炉炉龄和提高锰矿中锰的收得率等方面,
27
1.6、本章小结
双联法工艺转炉的主要配置特点
(8)转炉出钢方法 ●转炉炉前的主操作平台可考虑开孔,脱磷炉出脱磷 铁水后,脱磷铁水要马上兑入脱碳转炉内,其最 短捷的工艺路线是在转炉炉前的操作平台上开孔, 从孔中吊起脱磷铁水罐即可就近兑入脱碳炉。 ●在二个转炉的操作平台的合适位置上各开一个铁水 吊装孔,并设置盖板。脱磷转炉前的平台孔打开, 并设活动栏杆,脱碳转炉前的平台孔被盖板盖住。
4
1.1、转炉法铁水脱磷的发展过程
⑤这一技术得到推广 住友金属和歌山厂、川崎制铁水岛厂、NKK福山厂以及新日铁室 兰厂等均采用转炉双联法冶炼工艺进行大规模生产。典型的转炉 法工艺流程为:高炉铁水→铁水脱硫预处理→转炉脱磷→转 炉脱碳→二次精炼→连铸。
⑥宝钢
● 2002年11月11日 宝钢一炼钢2号300t转炉应用转炉脱磷、少渣 冶
②吨钢减少10kg的石灰消耗 ③住友金属采用了炉渣处理后通过炉顶料仓加入脱磷炉,
返回量为10~15kg/t ④新日铁君津厂和福山厂是采用留渣作业。 ⑤宝钢一炼钢采用的是将脱碳炉炉渣通过废钢料槽随废钢一道加
入到脱磷炉中。
12
1.3、双联法工艺转炉配置特点
转炉采用双联法冶炼工艺的风险较小,因 为其设备配置和工艺布置同传统转炉炼钢车间 基本一致。双联法冶炼工艺使用与否相当灵活, 转炉不进行双联作业也可改为常规操作。
探析转炉脱磷影响因素及其工艺发展
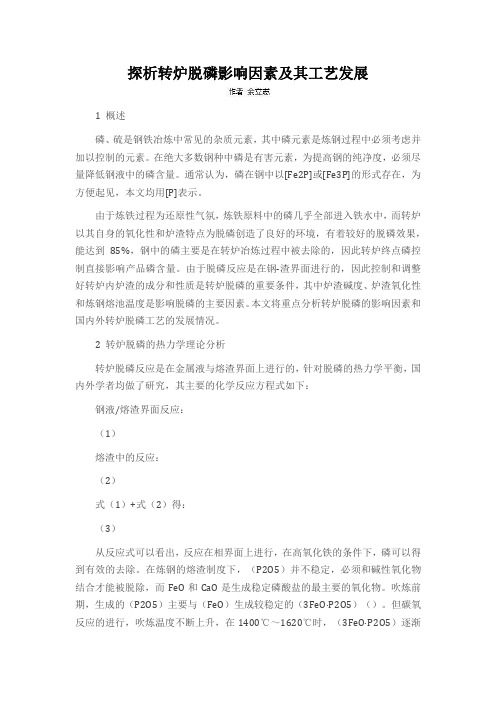
探析转炉脱磷影响因素及其工艺发展1 概述磷、硫是钢铁冶炼中常见的杂质元素,其中磷元素是炼钢过程中必须考虑并加以控制的元素。
在绝大多数钢种中磷是有害元素,为提高钢的纯净度,必须尽量降低钢液中的磷含量。
通常认为,磷在钢中以[Fe2P]或[Fe3P]的形式存在,为方便起见,本文均用[P]表示。
由于炼铁过程为还原性气氛,炼铁原料中的磷几乎全部进入铁水中,而转炉以其自身的氧化性和炉渣特点为脱磷创造了良好的环境,有着较好的脱磷效果,能达到85%,钢中的磷主要是在转炉冶炼过程中被去除的,因此转炉终点磷控制直接影响产品磷含量。
由于脱磷反应是在钢-渣界面进行的,因此控制和调整好转炉内炉渣的成分和性质是转炉脱磷的重要条件,其中炉渣碱度、炉渣氧化性和炼钢熔池温度是影响脱磷的主要因素。
本文将重点分析转炉脱磷的影响因素和国内外转炉脱磷工艺的发展情况。
2 转炉脱磷的热力学理论分析转炉脱磷反应是在金属液与熔渣界面上进行的,针对脱磷的热力学平衡,国内外学者均做了研究,其主要的化学反应方程式如下:钢液/熔渣界面反应:(1)熔渣中的反应:(2)式(1)+式(2)得:(3)从反应式可以看出,反应在相界面上进行,在高氧化铁的条件下,磷可以得到有效的去除。
在炼钢的熔渣制度下,(P2O5)并不稳定,必须和碱性氧化物结合才能被脱除,而FeO和CaO是生成稳定磷酸盐的最主要的氧化物。
吹炼前期,生成的(P2O5)主要与(FeO)生成较稳定的(3FeO·P2O5)()。
但碳氧反应的进行,吹炼温度不断上升,在1400℃~1620℃时,(3FeO·P2O5)逐渐分解,使磷又回到钢液当中。
为了有效地彻底脱磷,必须用石灰造高碱度钢渣,使磷在高碱度下生成更稳定的磷酸盐渣3CaO·(P2O5)或4CaO·(P2O5),其中4CaO·(P2O5)()更稳定,3CaO·(P2O5)次之,但通常达到平衡时的反应产物是4CaO·(P2O5)。
转炉炼钢脱磷工艺理论与实践

4/5[P] + 2(FeO) = 2/5(P2O5)+2Fe(l) 标准吉布斯能△ Gθ = -142944+65.48T(J/mol)。
2.1.2 P2O5 在炉渣中的固定 氧 化 生 成 的 P2O5 如 要 在 渣 中 稳 定 存 于 炉 渣 中,必 须 与
炉 渣 中 的 CaO 等 碱 性 氧 化 物 反 应 生 成 稳 定 的 磷 酸 盐 化 合 物 3CaO·P2O5 或 4CaO·P2O5,反应方程式为 : 2[P]+5[O]+3(CaO)=(3CaO·P2O5)
标准吉布斯能△ Gθ = -1486160+6360T。 或者 : 2[P]+5[O]+4(CaO)=(4CaO·P2O5) 标准吉布斯能△ Gθ = -1372200+550.1T。 由反应方程式可以看出,转炉炼钢脱磷原理在于磷的氧化 进入渣中和转化为稳定的磷酸盐,脱磷速度主要取决于钢—渣 界面磷的氧化反应 [3]。 2.2 转炉炼钢脱磷的基本条件 根据转炉炼钢脱磷的反应方程式,结合炼钢实际生产可知, 脱磷效果与转炉铁水中的氧量、炉渣碱度和温度有关,归纳脱磷 的基本条件如下 : (1)磷在炉渣中的固定是脱磷的重要环节,P2O5 一定要与渣 中的 CaO 等碱性氧化物结合才能稳定存在炉渣中,因此可以说 CaO 是含磷产物的稳定剂,炉渣碱度越高越有利于脱磷。在酸性 炉渣不能完成脱磷,但炉渣碱度太高不易熔化反而不利于脱磷。 (2)脱磷的量主要与磷的氧化反应有关,钢液中的 [O] 含量 以及炉渣中的(FeO)都是脱磷反应的氧化剂,增加 [O]、(FeO) 含 量 都 有 利 于 脱 磷。研 究 表 明 炉 渣 碱 度 2.5 ~ 3.0 和(FeO) 15% ~ 20% 条件,磷在炉渣中分配比最大,脱磷效果最好。 (3)炉渣量大可以稀释磷酸盐的浓度,促进 P2O5 与 CaO 充 分反应并正向进行,达到更好的脱磷效果,但炉渣量过大不利吹 氧入钢水和热传递。为达到更好的脱磷效果兼顾炼钢质量,先将 前期脱磷的炉渣先从转炉倒出,再次造渣以加强脱磷效果。 (4)脱磷反应是强放热化学反应,低温有利于脱磷反应正向 进行,温度过高则会逆向进行产生“回磷”现象。但是低温下石 灰熔化不良,转炉渣的黏度增大会导致脱磷效果变差,粘度过大 的泡沫渣但同样不利于脱磷。 2.3 转炉脱磷注意事项 转炉炼钢脱磷的条件综合起来简称“三高一低”,即“高碱 度、高 FeO 量、大渣量、低温”,转炉炼钢基本上可以完成 80% 以上的脱磷任务。脱磷反应基本上都是在转炉炼钢前期进行的, 该条件下更容易实现脱磷。实际炼钢过程中也时常会出现高磷 不合格的钢水,主要是因为转炉炼钢后期温度过高导致脱磷条 件变差和回磷,生产过程应进行以下预防措施 : (1)保证转炉炼钢末期炉渣碱度足够高。 (2)做好挡渣工作,尽量减少钢包下渣。
日本又搞出新技术,高炉“吃”转炉渣,降低焦比

日本又搞出新技术,高炉“吃”转炉渣,降低焦比日本钢铁巨头神户制钢开发了一种新技术,使用转炉渣,有助于降低制造产业的高炉生产成本。
炉子透气性由于回收应用有限,因此必须利用炼钢副产物的转炉渣来提高高炉的渗透性。
目的是通过减少维持高炉的透气性所需的焦炭量来降低成本。
神户制钢位于日本兵库县的加古川工厂已经朝着实施新技术的方向进行了最后的调整。
减少焦炭的使用神户制钢开发了“高炉风口吹转炉渣技术”。
将转炉渣制成细粉状,与细煤粉一起从风口吹入高炉内部,该创新正在神户工厂的第三座高炉(炉膛容量为2112立方米)上应用。
公司官员证实,在保持稳定运营的同时实现了降低成本的目标。
从16年4月到17年10月- 神户的第三座也是最小的高炉关闭了一年半。
官员说,为了充分利用新技术,加古川高炉得要更大。
新技术可以改善高炉“鸟巢”的透气性。
将转炉渣吹入高炉随着新技术的应用,转炉渣中的氧化亚铁(FeO)倾向于下降到自由流动状态。
结果,“鸟巢”中渣层的厚度显着减小- 即它变得更薄- 从而增加了高炉的渗透性。
钢铁公司进一步证实,通过提高炉子的渗透性已经减少了焦炭消耗。
在神户制钢运行的高炉中,对于1吨生铁生产,需要使用15千克BOF炉渣。
这成功地将焦炭比(每1吨生铁生产的焦炭消耗量)降低了几公斤。
成本竞争力神户制钢公司彻底改革了高炉操作方法,旨在通过注入大量粉煤尽可能地减少焦炭。
然而,如果粉煤量增加,“鸟巢”往往会膨胀。
煤粉和转炉渣同时吹过风口,以防止“鸟巢”的增长。
新技术旨在进一步提高熔炉操作的性能。
通常,每吨粗钢生产110-140千克转炉渣。
尽管转炉渣用作路基材料,但与高炉矿渣水泥相比,回收应用受到限制。
使用转炉渣的新应用技术的优点是它提高了炼铁厂的回收率。
神户制钢的消息来源已经证实,对于生产1吨生铁,用于改善高炉操作的透气性最佳转炉渣的吹入量约为15-20千克。
正在积极考虑粉碎转炉渣的预处理,着眼于利用现有设施。
神户制钢经营三座高炉- 加古川第二座高炉的炉膛容量为5400立方米,而另一座高炉的容量为4844立方米。
转炉熔渣气化脱磷循环炼钢关键技术开发及应用

转炉熔渣气化脱磷循环炼钢关键技术开发及应用转炉熔渣气化脱磷循环炼钢关键技术开发及应用近年来,随着工业化进程的不断发展,钢铁行业作为重要的基础产业之一,对环境保护和资源利用提出了更高的要求。
炼钢过程中的熔渣是一种含有大量磷元素的高温废弃物,若不能有效处理,将对环境造成严重的污染。
为了解决这一问题,转炉熔渣气化脱磷循环炼钢技术应运而生。
本文将深入探讨该技术的关键技术开发及应用。
一、转炉熔渣气化脱磷循环炼钢技术的概念与原理转炉熔渣气化脱磷循环炼钢技术是一种通过将炼钢过程中产生的熔渣进行气化处理,将熔渣中的磷元素转化为磷酸氢盐,并通过回收再利用的方式达到脱磷的目的的一种技术。
该技术主要包括气化反应、循环过程和脱磷回收等关键步骤。
在气化反应阶段,炼钢转炉熔渣经过预处理后注入气化炉中,与高温气体发生反应,产生气体燃料和磷酸氢盐。
这一阶段实质上是一种高温熔融质和气体的化学反应过程,需要掌握适当的气化温度和反应剂的选择。
在循环过程中,磷酸氢盐在炉内高温环境中发生水解反应,释放出磷酸和H2O。
磷酸部分被回收,用于炼钢过程中的脱磷处理,而水分则通过水蒸汽的形式排出。
这一过程实质上是一种有效的循环利用,使得磷元素得到了最大程度的回收再利用。
在脱磷回收阶段,磷酸与转炉熔渣中的磷元素发生反应,形成难溶性的磷酸盐,并通过物理分离的方式进行回收。
脱磷回收的效率与磷酸的浓度、反应时间和反应温度等因素密切相关,要实现高效的脱磷回收,需要综合考虑这些因素的影响。
二、转炉熔渣气化脱磷循环炼钢技术的关键技术开发转炉熔渣气化脱磷循环炼钢技术的关键技术开发主要包括反应器设计、催化剂研发、废气处理以及磷酸盐回收等方面。
反应器设计是该技术的核心环节。
反应器设计需要考虑到温度、压力、反应物料的流动性以及反应过程中产生的废气排放等因素,以确保反应器能够稳定运行,同时兼顾能效和安全性。
催化剂的研发对于反应过程中的效率和选择性具有重要影响。
催化剂的选择应考虑到催化活性、选择性和稳定性等因素,以提高反应速率和产物质量,并减少不良反应的产生。
转炉连续脱磷脱碳工艺的开发2001-7-31

分类号:B J84世界金属导报/2001年/07月/31日/第006版/转炉连续脱磷脱碳工艺的开发廖建国1.前言随着对洁净钢需求量的扩大,以铁水预处理为基础的多段组合精炼得到迅速发展。
但是,在使用铁水罐车或铁水包作预处理容器的情况下,由于必须在低温下进行脱磷脱碳精炼,因此存在着转炉热浴度不足、废钢添加量受限制等实质性问题。
另外,在使用转炉进行预处理时,虽然可以提高转炉的热浴度,但必须同时使用两座转炉作为脱磷炉和脱碳炉。
新日铁公司开发了一种能用一座转炉进快速脱磷脱碳的新的精炼工艺(M U R C:M u l t i-R e f i n i n g C o n v e r t e r)。
本文就M U R C法的概况和8t试验转炉的实验结果进行介绍。
2.M U R C法的概况M U R C法就是在同一座炉子中对铁水同时进行连续脱S i、脱P处理和脱碳处理的工艺,其中包括了在处理过程中倾动炉子进行中间扒渣的工序。
由于预先装入废钢,因此M U R C法能在高氧化性气氛下进行操作,而且由于是在同一座转炉中进行处理,因此能保持转炉的热浴度。
另外,利用转炉的强搅拌和高速吹氧的特性,在高氧位势下对低碱度渣进行快速脱磷精炼的同时,由于将脱碳渣全部留在炉内就装入下一炉的铁水,因而可有效地用于脱磷精炼,由此能实现石灰单耗最低的精炼,大幅度减少炉渣的产生量。
3.实验方法使用8t试验转炉进行实验。
先在每t铁水中装入0~180k g的废钢,然后装入用别的感应熔化炉熔化的铁水5~7t。
先用氧枪进行顶吹氧,并加入规定的废钢进行脱硅、脱磷处理,然后倾动炉子,从炉口扒出炉渣,将炉子竖直后再进行顶底吹氧,经脱碳精炼后出钢。
在对脱碳炉渣进行热循环操作的情况下,可将炉渣全部剩留在炉内就装入下一炉铁水。
脱硅脱磷处理时的顶吹氧流量以1000N m~3/h为标准,还有部分以400N m ~3/h和1500N m~3/h为标准进行实验。
底吹气体只使用N_2,其流量标准分别为200N m~3/h和350N m~3/h。
转炉脱磷、造渣工艺

是中期是碳剧烈氧化期,不能变化太快,抑制脱碳反应
突然温度降低,防止喷溅。据上所述,碳的大量氧化,
低磷,在因钢为坯中复的杂偏零析件度要很求大,钢而板在很α和高γ的固塑溶体性内。的IF扩钢散速度 却[很P小]<,0使.0它15不%容易均匀化。因此,按照用途不同对钢中磷含
量有严格要求:
东大冶金
1. 脱P反应
1. 脱P反应
.cn , 110004
2[P]+5[O]= P2O5 2[P]+5(FeO)=(P2O5)+5Fe 3(FeO)+(P2O5)=(3FeO·P2O5) (聚磷酸铁)
EMTI
Shenyang NEU Metallurgical Technology Corporation Limited
技术精益求精 · 创新永无止境
转炉脱磷、造渣工艺
沈阳东大冶金科技股份有限公司
东大冶金110004
磷在钢中以[Fe2P]形式存在,也可以用[P]表示。磷虽然能
前期渣中的(FeO)含量对脱磷反应的进行有重要 作用,这是因为:
12
东大冶金
3. 氧气转炉各期脱磷
.cn , 110004
影响前期脱磷的主要因素是碱度。而高的(FeO)含量 只是一个不可缺少的条件——也是在操作上前期快速成渣 的手段。换言之,就是控制喷枪,使(FeO)在10~15%左 右。炉渣前期 碱度为1.5左右,碱度提高更有利于脱磷,但 因前期温度低,客观上不可能造成高碱度炉渣。并且在此 (FeO)含量范围,碱度在0.82~1.5范围内,炉渣具有较低 的粘度,而碱度高于1.5时,粘度值随碱度增加而快速提 高,炉渣流动性显著变差,不利于脱磷。总之,通常必须 根据铁水条件把前期渣碱度控制在1.5左右;而(FeO) 在10~15%左右或更高些。
转炉脱磷及深脱磷
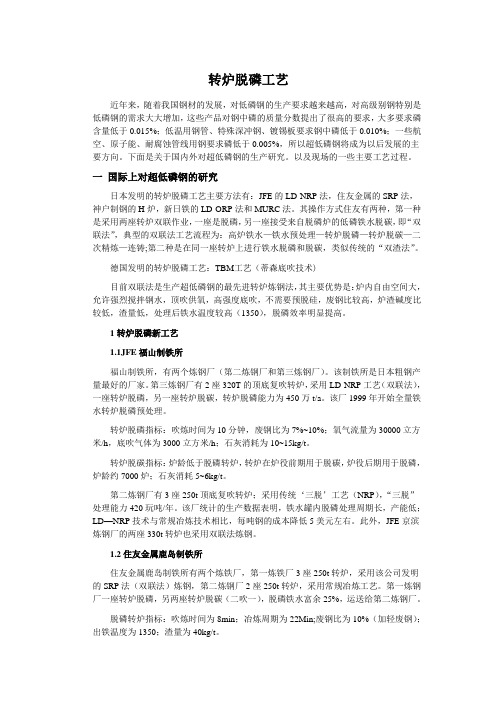
转炉脱磷工艺近年来,随着我国钢材的发展,对低磷钢的生产要求越来越高,对高级别钢特别是低磷钢的需求大大增加,这些产品对钢中磷的质量分数提出了很高的要求,大多要求磷含量低于0.015%;低温用钢管、特殊深冲钢、镀锡板要求钢中磷低于0.010%;一些航空、原子能、耐腐蚀管线用钢要求磷低于0.005%,所以超低磷钢将成为以后发展的主要方向。
下面是关于国内外对超低磷钢的生产研究。
以及现场的一些主要工艺过程。
一国际上对超低磷钢的研究日本发明的转炉脱磷工艺主要方法有:JFE的LD-NRP法,住友金属的SRP法,神户制钢的H炉,新日铁的LD-ORP法和MURC法。
其操作方式住友有两种,第一种是采用两座转炉双联作业,一座是脱磷,另一座接受来自脱磷炉的低磷铁水脱碳,即“双联法”,典型的双联法工艺流程为:高炉铁水—铁水预处理—转炉脱磷—转炉脱碳—二次精炼—连铸;第二种是在同一座转炉上进行铁水脱磷和脱碳,类似传统的“双渣法”。
德国发明的转炉脱磷工艺:TBM工艺(蒂森底吹技术)目前双联法是生产超低磷钢的最先进转炉炼钢法,其主要优势是:炉内自由空间大,允许强烈搅拌钢水,顶吹供氧,高强度底吹,不需要预脱硅,废钢比较高,炉渣碱度比较低,渣量低,处理后铁水温度较高(1350),脱磷效率明显提高。
1转炉脱磷新工艺1.1JFE福山制铁所福山制铁所,有两个炼钢厂(第二炼钢厂和第三炼钢厂)。
该制铁所是日本粗钢产量最好的厂家。
第三炼钢厂有2座320T的顶底复吹转炉,采用LD-NRP工艺(双联法),一座转炉脱磷,另一座转炉脱碳,转炉脱磷能力为450万t/a。
该厂1999年开始全量铁水转炉脱磷预处理。
转炉脱磷指标:吹炼时间为10分钟,废钢比为7%~10%;氧气流量为30000立方米/h,底吹气体为3000立方米/h;石灰消耗为10~15kg/t。
转炉脱碳指标:炉龄低于脱磷转炉,转炉在炉役前期用于脱碳,炉役后期用于脱磷,炉龄约7000炉;石灰消耗5~6kg/t。
- 1、下载文档前请自行甄别文档内容的完整性,平台不提供额外的编辑、内容补充、找答案等附加服务。
- 2、"仅部分预览"的文档,不可在线预览部分如存在完整性等问题,可反馈申请退款(可完整预览的文档不适用该条件!)。
- 3、如文档侵犯您的权益,请联系客服反馈,我们会尽快为您处理(人工客服工作时间:9:00-18:30)。
为进一步加强MURC工艺的脱磷能力,该厂又开发了F—M(Flexible MURC) 的工艺,即全部铁水在脱磷后倒入钢包,以排出炉内的炉渣,最后将铁水返回转炉内进行脱碳的方法。
用F—M(Flexible MURC) 时,虽然延长了转炉内的周期时间,由于全部脱磷渣都已排
除,减少了脱碳时炉内的w(p) ,脱磷能力也得到了提高。以该厂为例,使用MURC生产,
2002年,宝钢一炼钢2号300吨转炉应用转炉脱磷工艺、少渣冶炼技术成功地冶炼出第一炉成分合格的超低磷钢。攀钢提出在转炉内加入复合脱磷剂的新处理方法,使用后脱磷达到89. 4%,且能够实现成品w(p) <=0.01 5 %,同时无需二次造渣和加大渣量,既有利于降低转炉热损,又缩短了低磷钢的冶炼周期。已成功投入生产的宝钢一炼钢300吨转炉采用转炉脱磷,少渣冶炼工艺,与混铁车脱磷相比,具有工艺合理、技术指标好等优点,而且工程投资仅为混铁车脱磷的1/8,为今后宝钢生产超低磷钢、管线钢及生产优质宽厚板连铸坯提供了有利的技术装备条件。基于转炉脱磷工艺技术的难点,包钢、太钢二钢等厂也开展了转炉脱磷的工业试验,取得了一定成效。
当停吹w(c)>0.5%时,平均w(p) 为0.01%,最大w(p) 达到0.014%;而采用F—M(Flexible
MURC) 时,即使停吹w(c)>0.5%,脱碳后停吹时钢中平均w(p) 仅为0.007%,最大w(p)<=
0. 01%,同时,渣量减少了约15%。
4. 结束语
日本的—些企业利用转炉进行预处理脱磷,达到了较好的效果,对我国钢铁企业的发展具有一定的借鉴。
随着世界转炉炼钢技术的发展及炼钢设备的多样化,使传统的转炉炼钢过程逐步转向单一化,这样不仅可以提高钢水的质量、缩短冶炼周期、降低原材料消耗和能耗,而且有利于冶炼过程的控制和管理,更好地发挥转炉脱磷工艺的优点。 目前我国正处于调整钢铁产业结构的时期,适时结合我国钢铁企业的具体情况,进行技术改进,提高钢材的纯净度水平,更好地优化我国钢铁冶炼工艺。(火文)
表3 转炉脱磷工艺流程比较
工艺
流程
SRP
铁水兑入转炉—转炉脱磷—转炉出半成品—(扒渣)—半成品返回加料跨—半成品兑入脱碳转炉—转炉脱碳—转炉出钢—精炼—连铸
LD—ORP
加料—脱磷—出铁—再加料—脱碳—出钢—精炼—连铸
MURC
加料—脱磷—排渣—脱碳—出钢—渣热循环利用—精炼—连铸
传统工艺
铁水兑入转炉—转炉吹炼—出钢—精炼—连铸