8大浪费
8大浪费

8大浪费:1.缺陷Defect:对产品进行检查、补救等措施表现:额外的时间和人工进行检查、返工等工作;由此引起无法准时交货;企业的运作是补救式的,而不是预防式的(救火方式的运作)起因:生产系统不稳定;过度依赖人力来发现错误;员工缺乏培训2.过量生产Over-production:生产多于需求或生产快于需求表现:库存堆积;过多的设备;额外的仓库;额外的人员需求;额外场地起因:生产能力不稳定;缺乏交流(内部、外部);换型(换模)时间长;开工率低;生产计划不协调;对市场的变化反应迟钝3.等待Waiting:人员以及设备等资源的空闲表现:人等机器;机器等人;人等人;有人过于忙乱;非计划的停机起因:生产、运作不平衡;生产换型时间长;人员和设备的效率低;生产设备布局不合理;缺少部分设备4.动作Motion:对产品不产生价值的任何人和设备的动作表现:人找工具;大量的弯腰、抬头和取物;设备和物料距离过大引起的走动;需要花时间确认或辨认;人或机器“特别忙”起因:办公室、生产场地和设备规划不合理;工作场地没有组织;人员及设备的配置不合理;没有考虑人机工程学;工作方法不统一;生产批量太大5.库存Inventory:任何超过客户或后道工序需求的供应表现:需要额外的进货区域;停滞不前的物料流动;发现问题后需要进行大量返工;需要额外资源进行物料搬运(人员、场地、货架、车辆等);对客户要求的变化不能及时反应。
起因:生产能力不稳定;不必要的停机;生产换型时间长;生产计划不协调;市场调查不准确6.搬运Transportation:不产生价值的材料的运输表现:放置、堆积、移动、整列等动作浪费,由此而带来物品移动所需空间的浪费、时间的浪费和人力工具的占用等不良后果;搬运距离很远的地方,小批量的运输;出入库次数多的搬运;搬运过程中破损、刮痕的发生起因:生产线配置不当;未均衡化生产;坐姿作业;设立了固定的半成品放置区;生产计划安排不当7.过度加工Extra processing:一指多余的加工,另一方面是指超过顾客要求的精密加工,造成资源的浪费表现:瓶颈工艺;没有清晰的产品/技术标准;无穷无尽的精益求精;需要多余的作业时间和辅助设备起因:工艺更改和工程更改没有协调;随意引进不必要的先进技术;由不正确的人来做决定;没有平衡各个工艺的要求;没有正确了解客户的要求8.未充分利用的资源Unused resources:有消耗/支出,但没有完全发挥作用表现:使用但作用不大;不使用也没有关系;可以发挥的作用但没有发挥;较有价值但闲置或无用武之地起因:设计/配置不合理;无计划采购;状况改变后无用;错误的采购或招聘;没有正确使用。
增值和8大浪费
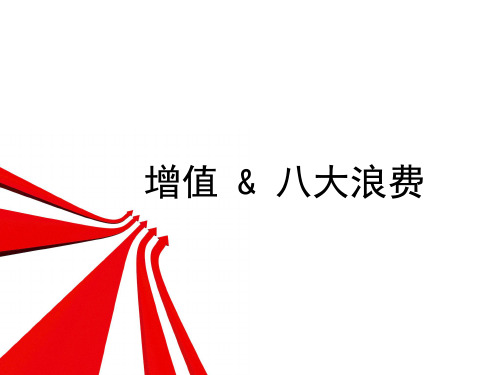
• 过多处理 • 搬运 • 等待 • 未使用的创意
我们日常工作中有超过 90+% 的行为均属于浪费
1:不良
2: 等待
3:过多动作
识别浪费
4:库存
5:过多搬运
6:过多生产
7:过度处理
生产周期的缩短: 通过识别和消除浪费开始!!!
8:未使用的创意
1: 不良品 (次品)
定义: 在送到客户之前需要返工或修理的产品
料 多余复印的一些资料 不清晰的指示或目标 整理文件资料
识别浪费 找出根本原因 减少/消除浪费
减少浪费的七个好处
1): 减少半制品,容易发现问题 2): 平衡生产线,提高生产效率 3): 确保质量,减少不良品 4): 最大化的优化和使用空间 5): 改善部门交流和沟通 6): 减少批量生产,实现一件流 7): 加强竞争,促进持续改善
增值 & 八大浪费
目录
1. 增值与非增值 2. 八大浪费在生产中的实例 3. 减少浪费有何好处
1:增值
提高
活动
增值&非增值
非增值
2:非增值必要的 3:非增值不必要的
减少
消除
增值 浪费
工作动作
工作
必要但不增值
必要 非增值但是
的:
双手操作拿部件的过程, 将相应的部件放在需要加 工的产品上
增值&非增值实例
课程回顾
增值与非增值 8种浪费在生产中的实例 减少浪费有何好处
增值行为:
改变部品/制品的形状或性能的行 为。 (图片中组装的过程)
不必要 非增值但是
的,
即是浪费:增加了成本但没 有增值的行为。 (图片中将部件从盒子里拿 出来放在桌面上需要的时候 再进行加工的过程)
5S及8大浪费

4S: Standardization–清洁
• 巩固前3个S的已有成就; • 完善规范、标准、制度; • 形成持续改善(消除浪费),并向其它领域进
一步深入
Implementation Guide
Employee Environment & Involvement
Workplace Organization
安全第一
Eliminate Waste
消除浪费
Each item has its own position. Each Operation has its standard and specifications. 每样资源有各自的位 置,每个操作都有标 准和规范
3S.Sweeping:
execute the rules 清扫:执行规定
诀窍在于-----
6. 资料
7. 办公用品
明确摆放点设立原则
使用频率高的东西,就近安放;
使用率低的首先考虑多余空间,其次考虑就近原则;
几乎不用的丢弃或入库。
2S: Simplifying – 整顿
整洁!有序!便于存取! 一目了然!
诀窍在于-----
• 建立划线、涂色、作标记等可视控制 • 颜色代码的规定 • 创造条件将物品整齐有序地安放好
工具箱
Clear up at any time. All resources are in the
stipulated places. All the operations follow their
standard and specifications. 随时清洁而且—资源都处在批准和指定的地方, 所有操作都遵循标准和规范
锤子在这里!
工具箱
生产管理之8大浪费

■未注意部属的眼力与健康,造成不良品
■缺乏纪律,纵容粗心或不当的工作
■容许部属用不适当的材料(太好或太 差)
12
■未能追踪不良工作起何人,以致不能纠正 ■不能适才适用,特别是新人
■领料太多,多余料未退料
■领错材料,用错材料
■未能检查水、气、油等管路裂开破损, 导致遗漏
■未检查材料是否排列整齐,正确放置
生产管理中的8种浪费
1
1、时间的浪费
2
■缺乏适当的计划,使人员在换规格时产生
等待或者停工 ■班长未能彻底了解接受之命令与指示
■缺乏对全天工作内容的认识
■对班长的命令或指示不清楚 ■未能确实督导工具、材料、模具等应放
置于一定场所
■不应加班的工作,造成加班 3
■未检视每一工作是否供给合适的工具和资 源
■未研究部属个人的不同,以发挥他最大 的潜力
25
■评价一个人只重资格、种族、宗教、关 系、地域
■明知部属的的心理或者生理不适当,却 未加以调动
■生病的部属仍让他工作
■当可能且适当的时间,未能给予升迁
■未考虑影响薪资与工作条件的问题
■未训练一个后补者
26
4、欠缺对员工日常管理之数据
27
5、欠缺人员效率管理之数据
■未促使其他部属对新人表示关心、帮
助、友善的态度
23
■未尽可能的接近新人 ■没有告知新人,工厂生活情况与规划,
如安全,发薪日期,厕所位置,饮用 水,浴室等 ■未安排完整的训练计划
24
3、未使部属尽其所能
■未指导部属如何做好工作 ■未尽可能的说明工作,使其发生兴趣 ■未对部属的进步与个人生活表示关心 ■没有容纳部属错误的雅量 ■纵容部属派系存在或抱团
8大浪费
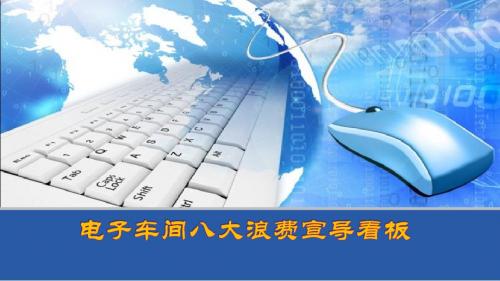
搬运的浪费
从JIT(Just In Time/准时制生产方式)的角度来看, 搬运是一种不产生附加价值的动作,而不产生价值的工 作都属于浪费。 搬运的浪费具体表现为放置、堆积、移动、整理等 动作浪费,由此而带来物品移动所需空间的浪费、时间 的浪费和人力工具的占用等不良后果。 在搬运过程中,经常会发生物品的损伤,两个分离 的流程之间就需要搬运。为消除这样的搬运浪费,任何 与主生产线分离的所谓离岛作业,应尽其可能并入主生 产线内。
•品质控制点设定错误
•认为可整修而做出不良 •检查方法、基准等不完备
•一个流的生产方式
•品保制度的确立及运行 •定期的设备、模治具保养
•设备、模夹治具造过分加工的浪费
过分加工的浪费也叫加工的浪费,主要包含两层含义:
第一是多余的加工和过分精确的加工,例如实际加工 精度过高造成资源浪费;
上面提到库存是万恶之源,而制造过多或提早完成, 在丰田则被视为最大的浪费。
精益生产强调“适时生产”:必要的东西在必要的 时候,做出必要的数量,此外都是浪费。而所谓必要 的东西和必要的时间,就是指顾客(或下道工序)已 决定要的数量与时间。
制造过多的浪费
制造过多的后果:
制造过多与过早的浪费在8大浪费中被视为最大的浪费: 1、它只是提早用掉了费用(材料费、人工费)而已,并不能得 到多少实在的好处。 2、 它会把“等待的浪费”隐藏起来,使管理人员漠视等待的发 生而使之永远存在下去。失去了不断改善、进而增强企业“体质” 的机会。 3、 它会使工序间积压在制品,会使制造周期变长,且所需要的 空间变大(车间像仓库,到处都是原材料、在制品、完成品,或 有许多面积不小的所谓中转库是十分典型的现象)
世 界 上 最 大 的 浪 费,莫 过于 动 作 的 浪 费。 ——吉尔布雷斯
八大浪费培训PPT课件
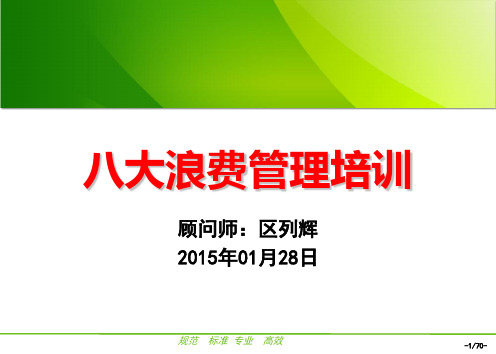
降低成
-6/70-
成本节减思想:降低成本
需求 < 供给
通过降低成本来降低销售价格
销售价格
利润 成本
规范 标准 专业 高效
-7/70-
竞争力提升 品质提升 制造成本降低 企业形象提升
改善 消除浪费 标准化
设 改善等
心、
动作改善、作业流程改善、物流改善、 备模夹治具改善、品质改善、管理
八大浪费、三无工程(无责任、无关
-29/70-
3.搬运的浪费
整个冲压过程包括取产品、冲压、 放置产品,其中取产品与摆放产 品占了50%的作业时间,并且这 些动作并不产生价值。
冲压完的产品要先放到周转车 上,再搬运到点焊工位点焊, 这些搬运过程都是浪费,为什 么不把冲压与焊接设备放在一 起呢?
规范 标准 专业 高效
-30/70-
3.搬运的浪费
规范 标准 专业 高效
-35/70-
八大浪费
1.制造过多的浪费 2.等待的浪费 3.搬运的浪费 4.加工的浪费 5.库存的浪费 6.动作的浪费 7.不良的浪费 8.管理的浪费
规范 标准 专业 高效
-36/70-
SUCCESS
THANK YOU
2019/8/1
规范 标准 专业 高效
-37/70-
5.库存的浪费
制
移动
40%
造
所谓的附加值指的是通过加工或组装提 高产品的价值,其余的都是非附加值,就 浪费。
活
附加价值动作
15%
TOYOTA汽车公司
动
非效率的 ‘工作’ 40%
11 /72
定义 95%以上是浪费
规范 标准 专业 高效
-11/70-
生产车间常见的八大浪费
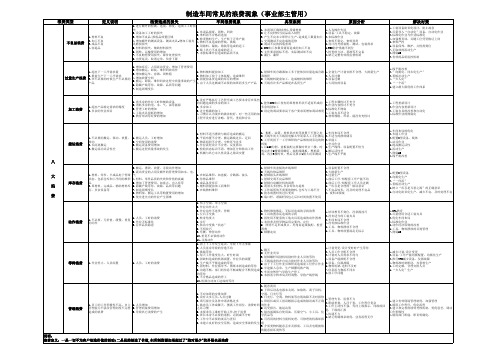
3.日光灯、空调、物料架等出现故障不及时报修 4.班组长或员工因误解指示造成的错误或不正确 的作业 5.迟交报告,拖延决策 7.纵容部属私自使用油、压缩空气、小工具、化 学药品等 8.可再用的材料当废料处理,可修理的机器却报
1.管理失责,监督不力 2.职能重叠,人浮于事,工作程序复杂 3.工作主动性不强,等待上级指示,同级的回 复,下级的汇报 4.协调不力 5.缺乏明确规章制度,业务流程无序
浪费类型
定义说明
不良品浪费
1.材料不良 2.加工不良 3.成品不良 4.客退品
制造车间常见的浪费现象(事业部主管用)
浪费造成的损失
车间浪费现象
1.进行额外的检测、选别、修复、追加工工时损
失 2.设备加工工时的损失 3.增加不良品/报废品放置区域 4.增加额外的测试设备、测试夹具;增加工装夹 具磨损损失 5.材料的损失,辅助材料损失 6.周转、运输费用的增加 7.不良赔偿费用损失,降价处理损失
1.因上下工序发生延误,导致下序无事做
2.人员富余导致的劳逸不均 3.换线等待 4.每天工作量变化大,时忙时闲 5.因缺料造成的机器闲置,作业员的闲置 6.生产线不平衡造成的等待 7.因材料、作业指导书、图纸未到造成的等待 8.沟通不畅,部门间信息不畅或配合不默契造成 的等待 9.不合格品造成的停工
3.射频接头在线堆积
3.过量生产
状态,包括仓库和工序间的堆积 4.材料,零件品质的失效和价值的衰减
2.待修品堆积
4.射频交调不良品堆积
4.前后工序/相配套工序产能不均
库存浪费 品
5.增加了管理费用,如盘点、出入库等
3.成品备货库存
浪
2.原材料、完成品、辅助材料库 6.隐藏产线等待,故障、品质等问题
八大浪费

到底为什么要有库存量,最大的理由是“ 到底为什么要有库存量,最大的理由是“怕出问 ——出现故障怎么办 会不会因部分设备出问题, 出现故障怎么办? 题”——出现故障怎么办?会不会因部分设备出问题,而 影响整条生产线或工厂的生产呢? 影响整条生产线或工厂的生产呢?于是乎为了不使影响扩 库存便成了必要,众多的问题也被隐藏起来, 大,库存便成了必要,众多的问题也被隐藏起来,所有进 赚钱(发现问题、解决问题就是赚钱) 步、赚钱(发现问题、解决问题就是赚钱)的步调自然变 慢了。无怪乎精益生产方式称库存为万恶之源, 慢了。无怪乎精益生产方式称库存为万恶之源,绝对不允 许它存在,如果现在已经有了库存,也要行进一切办法, 许它存在,如果现在已经有了库存,也要行进一切办法, 将之降低,力争零库存。( 。(注 零库存的“ 将之降低,力争零库存。(注:零库存的“零”并非指数 学意义上的“完全没有”的意思,而是指把库存“ 学意义上的“完全没有”的意思,而是指把库存“尽量减 到最少的必要程度” 到最少的必要程度”。)
八大浪费之七:制造过多( 八大浪费之七:制造过多(早)的浪费
上面提到库存是万恶之源,而制造过多或提早完成, 上面提到库存是万恶之源,而制造过多或提早完成,则被视为最 大的浪费。 大的浪费。 精益生产方式所强调的是“适时生产” 也就是在必要的时候, 精益生产方式所强调的是“适时生产”,也就是在必要的时候, 做出必要的数量的必要的东西。此外都属于浪费。 做出必要的数量的必要的东西。此外都属于浪费。而所谓必要的东西 和必要的时候,就是指顾客已决定要买的数量与时间。 和必要的时候,就是指顾客已决定要买的数量与时间。假设客户只要 100个 而每个1 如果生产了150 150个 这售价却不会是150 150元 100个,而每个1元,如果生产了150个,这售价却不会是150元,因为 多余的50个并没有卖出去,仅是变成库存,因此利润也就无从产生, 50个并没有卖出去 多余的50个并没有卖出去,仅是变成库存,因此利润也就无从产生, 换句话说,多做了是浪费。 换句话说,多做了是浪费。 而制造过早同样也是浪费, 而制造过早同样也是浪费,但为什么有很多工厂会一而在地过多 与过早制造呢?最大的原因在于他们不明白这是一种浪费, 与过早制造呢?最大的原因在于他们不明白这是一种浪费,反而以为 多做能提高效率,提早做好能减少产能损失(不做白不做, 多做能提高效率,提早做好能减少产能损失(不做白不做,机器还不 是一样停着?),显然这是一种极大的误解。 ?),显然这是一种极大的误解 是一样停着?),显然这是一种极大的误解。
八大浪费培训课件ppt

4) 动作太大
10) 伸背动作
5) 左右手交换 11) 弯腰动作
6) 步行多
12) 重复/不必要的动作
一般来说作业者
有一半的时间是 “无效的” !
任何不产生价值的人员和设备的动作
15/32
精益生产专家
在日常生活中,随处都可以看到浪费 粮食的 现象。 也许你 并未意 识到自 己在浪 费,也 许你认 为浪费 这一点 点算不 了什么
在日常生活中,随处都可以看到浪费 粮食的 现象。 也许你 并未意 识到自 己在浪 费,也 许你认 为浪费 这一点 点算不 了什么
一、浪费定义
What
is
the
wastes?
什么是浪费: ◇在制造活动中,不增加价值的所有行为,是浪费; ◇尽管是增加价值的活动,所用的资源超过了
“绝对最少”的界限,也是浪费。
产生搬运、堆积的浪费,并使得先入先出的物流管 理变得困难。增加周转包装的需要,并造成质量问题。 ◆ 材料、人工、库存变大,周转资金增加,管理成本增加。
9/22 8/32
在日常生活中,随处都可以看到浪费 粮食的 现象。 也许你 并未意 识到自 己在浪 费,也 许你认 为浪费 这一点 点算不 了什么
2)库存的浪费(在制品WIP)
7/22 6/32
1)
在日常生活中,随处都可以看到浪费 粮食的 现象。 也许你 并未意 识到自 己在浪 费,也 许你认 为浪费 这一点 点算不 了什么
制造过多(早)的浪费
多做能提高效率,提早做好能减少 产能损失是一个很大的误解。
•生产多于下游客户所需 Making More Than Needed •生产快于下游客户所求 Making Faster Than Needed
8种浪费PPT课件
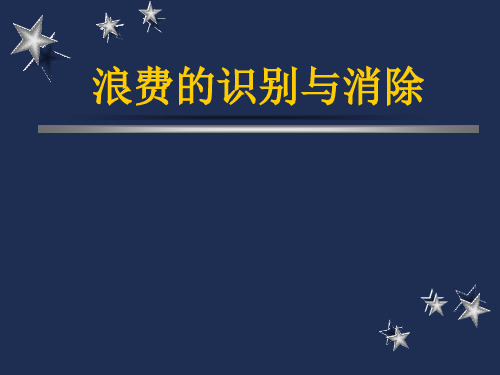
课程安排
– 浪费的3个原因 – 配套战略
• 人员支持性实践 • 降低变差 • 过程/员工控制 – 现场练习 – 过程检查
浪费的识别和消除
哲学
浪费的识别和消除是精益生产的 的核心
成功的实施要求所有的员工都受 到识别和消除他们工作中浪费的 培训
进先出” – Massive Rework Campaigns When
Problems Surface 出现问题时的大量返工作业 –Long Lead Time for Engineering Changes
工程更改导入期长 –Off Line Storage Area 线外储存空间
Waste of Inventory 存货造成的浪费
存货的浪费
定义:
Any Supply in Excess of Customer RequirementsNecessary to Produce Goods or Services Just in Time 任何超出客户要求的供应品,客户要求是指准时生产及提供服务所需。
存货的浪费
特点:
–Stagnated Material Flow 停滞的物料流 –FISH instead of FIFO“先进后出” 取代“先
纠正的浪费
定义: Repair of a Product or Service to Fulfill
Customer Requirements 维修产品或补偿服务以满足客户的要求
纠正的浪费
特点: • 维修和返工的空间 • 增加的检验 • 复杂的生产流程 • 有疑问的质量 • 影响装运/交付 • 客/供关系差 • 由于返工,报废,额外运费造成低效益 • 组织是被动反应(救火,赶工而不是预防导向)
8大浪费
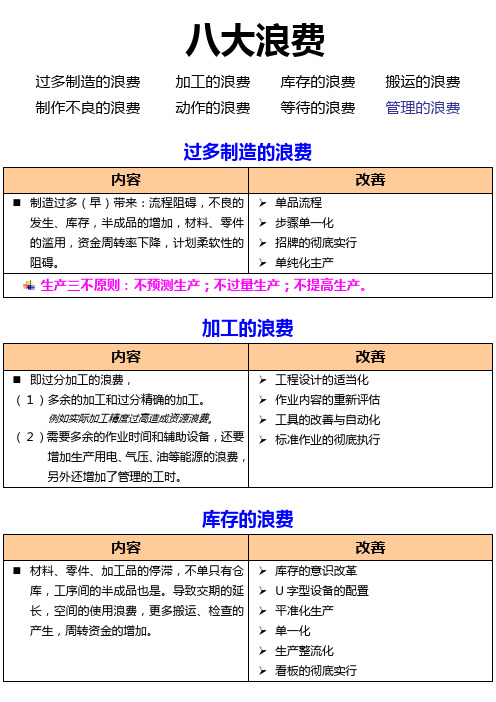
八大浪费过多制造的浪费加工的浪费库存的浪费搬运的浪费制作不良的浪费动作的浪费等待的浪费管理的浪费过多制造的浪费内容改善⏹制造过多(早)带来:流程阻碍,不良的发生、库存,半成品的增加,材料、零件的滥用,资金周转率下降,计划柔软性的阻碍。
➢单品流程➢步骤单一化➢招牌的彻底实行➢单纯化主产生产三不原则:不预测生产;不过量生产;不提高生产。
加工的浪费内容改善⏹即过分加工的浪费,(1)多余的加工和过分精确的加工。
例如实际加工精度过高造成资源浪费。
(2)需要多余的作业时间和辅助设备,还要增加生产用电、气压、油等能源的浪费,另外还增加了管理的工时。
➢工程设计的适当化➢作业内容的重新评估➢工具的改善与自动化➢标准作业的彻底执行库存的浪费内容改善⏹材料、零件、加工品的停滞,不单只有仓库,工序间的半成品也是。
导致交期的延长,空间的使用浪费,更多搬运、检查的产生,周转资金的增加。
➢库存的意识改革➢U字型设备的配置➢平准化生产➢单一化➢生产整流化➢看板的彻底实行降低库存三要领:回要多;批量要小;交期要快。
搬运的浪费内容改善⏹具体表现为放置、堆积、移动、整列等动作浪费,由此而带来物品移动所需空间的浪费、时间的浪费和人力工具的占用等不良后果。
➢U字型设备的配置➢流程作业➢站著工作➢多能工活性指数提升搬运三不原则:不乱流、不粗流、不停留制作不良的浪费内容改善⏹材料的损失、不良品变成废品--设备、人员和工时的损失;额外的修复、鉴别、追加检查的损失;有时需要降价处理产品,或者由于耽误出货而导致工厂信誉的下降。
➢自动化(半自动化)➢愚巧化(防呆化)➢作业标准➢全数检查➢无停滞的流程作业不接受不良品、不制造不良品、不传递不良品。
减少不良的二十字真言:保持新鲜、迅速确实、三线一体、不要碰触、要一致性。
动作的浪费内容改善⏹1、两手空闲的浪费⏹2、单手空闲的浪费⏹3、作业动作停止的浪费⏹4、作业动作太大的浪费⏹5、拿的动作交替的浪费⏹6、步行的浪费⏹7、转身角度太大的浪费⏹8、动作之间没有配合好的浪费➢流程生产的组成➢“表准作业”与标准作业➢动作改善原则的彻底实行⏹9、不了解作业技巧的浪费⏹10、伸背动作的浪费⏹11、弯腰动作的浪费⏹12、重复动作的浪费动作三不原则:不插秧、不摇头、不弯腰。
OE文化系列之一:“8大浪费”

大家好!
OE这个词,我们应该听了很多次了,大家都知道这是一种很有效的方法论,可能有的同事对他还没有深入的了解,那么,请跟我来,一起分享全球管理先进经验!
今天和大家分享OE文化的一个重要方面:消除8种浪费
OE(Operational Excellence),中文翻译“卓越运营”,是用客观、辩证、实事求是的态度,使用一系列科学的工具,有效率地消除浪费,提高生产力的方法论,是企业可持续发展的文化。
OE集中整合了精益生产(Lean)、六西格玛(6Sigma)的核心理念和可口可乐系统的最佳实践经验,追求持续改善和不断挑战现状。
而精益生产(Lean)的核心是减少浪费。
OE总结了8种浪费:
看一看,是不是我们身边或多或少都存在这样的情况呢?
8种浪费的第一个英文字母组合起来,就是一个单词:DOWNTIME。
那么发现了8种浪费怎么办呢?如何能消除浪费并推广使用呢,别着急,敬请期待OE文化介绍之二:I-Card使用(Improve Card) 。
信息分类- 内部使用。
八大浪费案例

八大浪费案例一、案例背景介绍咱就说啊,在现代企业或者日常工作学习生活中呢,浪费那可是无处不在的。
这八大浪费啊,真的是像隐藏在暗处的小怪兽,偷偷地消耗着资源。
比如说在一些小工厂里,老板可能都没太在意这些浪费情况,员工们也稀里糊涂的,就这么一天天的,资源就被浪费掉啦。
也有一些大公司的小部门,管理不太精细的时候,也容易出现这些问题。
二、问题详细描述1. 过量生产的浪费就好比有个生产小玩具的车间,市场上对这个小玩具的需求明明就那么多,可车间为了显示自己产量高,或者怕机器闲着,就一个劲地生产。
结果呢,生产出来的玩具堆在仓库里,占用了大量的空间不说,还积压了资金。
好多玩具可能最后都因为款式过时或者质量下降,只能低价处理,甚至扔掉,这多可惜呀。
2. 库存的浪费我有个朋友在一个服装厂工作,他们厂有好多布料库存。
这些库存呢,一方面占用了仓库的空间,还得有人专门去管理,增加了管理成本。
而且有些布料放久了,可能会出现质量问题,比如褪色、发霉之类的。
可为啥会有这么多库存呢?有时候是为了应对可能会出现的大订单,但实际上大订单没那么多,就造成了库存积压。
3. 等待的浪费在建筑工地上经常能看到这种情况。
比如说,建筑材料没有按时运到工地,工人们就只能在那里干等着,啥活也干不了。
一天下来,工人的工资还是要照付的,机器设备也闲置着,这就造成了人力和物力的双重浪费。
还有在办公室里,有时候一个项目需要等领导签字,领导又忙别的去了,文件就在那里放着,相关人员也只能等着,耽误了整个项目的进度。
4. 搬运的浪费像一些大型超市的仓库,货物摆放不合理。
员工每次补货的时候,要从仓库的这头跑到那头去拿东西,然后再搬到货架上。
这来来回回的搬运,不仅浪费了时间,还增加了员工的体力消耗。
要是能把货物按照补货的频率或者类别摆放得更合理一点,就不会有这么多不必要的搬运了。
5. 过度加工的浪费我见过一个做木质家具的小作坊,他们给一个简单的小桌子做了超级复杂的雕花。
生产现场八大浪费

学习目标
认识浪费 不同的经营思想 企业每天都在“烧”钱 全面生产系统(5MQS)的浪费 工厂中常见的8大浪费
2
不同的经营思想
成本中心型: 以计算或实际的成本为中心,加上预先设定
的利润,得出售价。 计算公式: 售价=成本+利润
卖方市场;消极被动; 企业类别:
高新产品 垄断产品 国内的铁路、民航等
12
工厂中常见的 8大浪费
N 制造现场的
O
浪费
说明
管理部门的浪费
制造不良的浪费,之 低可靠性带来的各
1 不良的浪费 后还有进行检测的浪 种事中、事后的浪
M U D A 费
费
与产品价值核心的功 2 加工的浪费 能不相关的加工与作
作业浪费
业都是浪费
3
动作的浪费
步行、放置、大幅度 的动作
动作的浪费
4 搬运的浪费 物料搬运的浪费
能力不平衡造成的各种等待、停滞 流程混乱造成的浪费
M
1. 资料的浪费
资料不用便是浪费
管 2. 会议的浪费
理 3. 管理的浪费
的 4. 通信的浪费
浪 费
5. 工作单的浪费
会议本身的目的不明确就是浪费 管理是浪费,目标、职责不清 信息的目的性不明确就是浪费 工作单的编制填写确认保管就是浪 费
11
5MQS的浪费
7
全面生产系统的浪费
什么是浪费:
✓ 不增加价值的活动,是浪费; ✓ 尽管是增加价值的活动,所用的资源超过了
“绝对最少”的界限,也是浪费。
8
全面生产系统的浪费
生产要素的5MQS: Man(人) Machine(机器) Material(物料) Method(作业方法) Management(管理) Quality(品质) Safety(安全)
精益生产之8大浪费

浪费描述为8种类型:
• 过量生产 • 返工 • 搬运 • 过量加工 • 库存 • 等待 • 动作 • 缺乏员工参与
精益工具都是为消除浪费而设计的。
努力并持续的消除浪费,从现在就开始。
思维方式的改变
传统企业
增值
非增值活动95%
传统的生
产改进
增值
非增值活动95%
较小的改进
精益消灭 浪费
增值
非增值 活动
重大的改进
思维方式的变化:从压缩增值活动的时间到压缩非增值活动的时间。
为什么要消除浪费
• 减少浪费让客户、公司和员工都受益
对象
益处
对客户
产品满足所有预期
对公司
减少成本 提高质量 提高操作员柔性 提高声誉
• 尽管是增加价值的活动,但所用的资源超过了 “绝对最少”的界限,也是浪费(资源浪费)
增值与非增值
增值
定义:任何增加产品或服 务价值,或为满足顾客要 求必需进行的活动。
典型例子: • 加工 • 规定的检验
非增值
定义:指任何不会增加额 外价值或无此需要的活动 典型例子: • 搬运 • 检验 • 返工 • 存放 • 等待
原因:
• 生产能力不稳定 • 万一………. • 缺乏沟通(内部、外部) • 本地优势化观点 • 成本计算(贪图便宜) • 缺乏协调一致的计划
返工的浪费
定义 • 对产品或服务进行再处理才能满足客户的要求
返工的浪费
特点:
• 有维修和返工区域 • 增加额外的检查 • 复杂的产品流程 • 有疑问的质量
危害: • 与供应商/客户之间关系不好 • 由于返工,报废,加急运费而
8大浪费-中文

Non-utilized creativity未使用的创造力
定义:
未被充分利用的 人的创造力
19
Non-utilized creativity未使用的创造力
How:
1. 肯定,赞扬和鼓励
例1 例2
2. 合理化建议 3. 头脑风暴,团队
20
Transportation材料搬运的浪费
定义:
非直接到生产点的 任何材料移动.
具体步骤:
1. 部门/工序/动作分解和时间测量; 2. 识别与增值无关的动作.
34
案例和练习
案例: 贴标签 改善前--每小时贴1200个标签/人,平均3秒一个 解:部门/工序/动作分解和时间测量; 识别与增值无关的动作.
伸手取标签0.8秒, 取产品0.8秒, 把标签取来对准产品0.5秒 贴标签0.2秒, 抹平标签0.1秒, 放下产品0.6秒. 一类浪费 二类浪费 增值 增值 增值 二类浪费 必须,可减少 可改进 必须,可减少 必须,不可少 必须,不可少 可改进 35
案例和练习
练习、
搬运 人工加料 制糖粒 2次/分钟 1人 自动出糖 包装 数糖粒 糖粒 入袋 5人 称重 20~30 封口 平米
海南春光食品有限公司
烘干和配料 卫生处理 和粉碎 搬运
节省场地 参观室 减少搬运距离 缩短生产周期 参观 出口 参观 入口
动作分解: 1.取椰子 去外壳 2.切外壳 9人 (8人操作 3.弃外壳 1人清扫) 4.半成品 20~30 入周转箱 5.清扫废 平米 壳入蓝子
32
消除浪费的总则
ELIMINATE消除
工序步骤, 人员, 设备, 库存, 信息…….
COMBINE合并
工序步骤, 工作要素, 库存……..
- 1、下载文档前请自行甄别文档内容的完整性,平台不提供额外的编辑、内容补充、找答案等附加服务。
- 2、"仅部分预览"的文档,不可在线预览部分如存在完整性等问题,可反馈申请退款(可完整预览的文档不适用该条件!)。
- 3、如文档侵犯您的权益,请联系客服反馈,我们会尽快为您处理(人工客服工作时间:9:00-18:30)。
工作台可以开 网口解决废扎 带
让我们每天进步一点点
②搬运的浪费
大部分人皆会认同搬运是一种无效的动作,也
有人会认为搬运是必须的动作,因为没有搬运 ,如何做下一个动作?很多人都有这种想法。 正因为如此,大多数人默认它的存在,而不设 法消除它。有些人想到用输送带的方式来克服 ,这种方式仅能称之为花大钱减少体力的消耗 ,但搬运本身的浪费并没有消除,反而被隐藏 了起来。搬运的浪费若分解开来,又包含放置 、堆积、移动、整理等动作的浪费。 案例
要达到同样作业的目的,会有不同的动
作,哪些动作是不必要的呢?是不是要 拿上、拿下如此频繁?有没有必要有反 转的动作、步行的动作、弯腰的动作、 对准的动作、直角转弯的动作等?
所以我们来认识一下12种浪费的动作
12种浪费动作
两手空闲 单手空闲 作业动作停止 动作太大 左右手交换 步行多 转身角度大 移动中变化“状态” 不明技巧 伸背动作 弯腰动作 重复/不必要的动作
搬运改善的案例
日本三洋大型课为减少搬运,把四个车间合并
成两个,一些零部件的加工由原来在别处加工 变成在生产线旁进行加工,从而减少搬运。在 不可能完全消除搬运的情况下,应重新调整生 产布局,尽量减少搬运的距离。大家可以考虑 一下我们公司的生产布局应该怎样变更?如何 最大限度地减少搬运?
搬运的浪费
LEAN MANUFACTURING TRAINING
精益生产培训
EIGHT WASTE CONTROLING METHOD
8大浪费的控制方法
百日改善活动一级培训教材 设备动力部IE组
工厂一般的浪费
(1)等待的浪费 (2)搬运的浪费 (3)不良品的浪费 (4)动作的浪费 (5)加工的浪费 (6)库存的浪费 (7)制造过多(早)的浪费。 ( 8)管理的浪费
库存的浪费
⑦制造过多(早)的浪费
上面提到库存是万恶之源,而制造过多或提早完成,在丰田则被视 为最大的浪费。
精益生产强调“适时生产” 弊端: 提早用掉费用(材料费、人工费) 会将等待的浪费隐藏起来 会使工序间积压在制品,所需空间变大 产生搬运、堆积的浪费,使得先进先出变的困难 增加踏板和其他的容器 利息负担增加
加工的浪费(可以考虑合并的工序)
节拍:90S
节 拍 : 40 S
⑥库存的浪费
精益生产方式认为:“库存是万恶之源” 库存浪费作成以下的浪费:
产生不必要的搬运、堆积、放置、防护处理、找寻等浪费。 使先进先出的作业困难。 损失利息及管理费用。 物品的价值会减低,变成呆滞品。 占用厂房空间,造成多余的工场、仓库建设投资的浪费。 设备能力及人员需求的误判
进行三次搬运,造成 设备的浪费、人员的 浪费、场地的浪费
③不良品的ห้องสมุดไป่ตู้费
产品制造过程中,任何的不良品产生,皆造成 材料、机器、人工等的浪费。任何修补都是额 外的成本支出。精益的生产方式,能及早发掘 不良品,容易确定不良的来源,从而减少不良 品的产生。这一条比较好 理解,关键是第一 次要做正确,但实施起来却很困难。大家不妨 仔细想一想,除了产品生产,管理工作中是否 也存 在类似的浪费情况?
①等待的浪费( 等待就是闲着没事,等着下一个动作的来临 )
造成等待的原因通常有:作业不平衡、
安排作业不当、停工待料、品质不良等 。 等待上级指示、等待下级汇报、等待外 部回复、等待现场联系
☆例如在产品检测过程中,调试人员和氦检人 员站在产品旁边等待,这种情况是否还有?
等待的浪费
等待流水线流动
不良品的浪费
精益生产方式的思想之一就是要用一切办 法来消 除、减少一切非增值活动,例如 检验、搬运和等待等造成的浪费,具体 方法就是推行“零返修率”,必须做一 个零件合格一个零件,第一次就做好, 更重要的是在生产的源头就杜绝不合格 零部件、原材料流入生产后道工序,追 求零废品率 。
不良品的浪费
④动作的浪费
动作的浪费
单手作业
⑤加工的浪费
在制造过程中,为了达到作业的目的,
有一些加工程序是可以省略、替代、重 组或合并的,若是仔细地加以检查,你 将可发现,又有不少的浪费等着你去改 善。
案例
加工浪费控制案例(日本三洋家用空调线)
原来的热交换器组装流水线,是需要一个员工把穿完
管的热交换器装箱后,用手推车运送到涨管设备旁, 然后由另一个员工操作设备涨管,最后再由第三名员 工把涨完管后的热交搬运到另一条悬臂运输线上。经 过革新,他们把热交组装线的传送带延伸到涨管设备 旁,可减少一名运输工人,今后还准备把涨管设备迁 移到悬臂线旁,由涨管工人直接把热交送到悬挂臂上 ,又节省一名搬运工人。通过两次对工序进行重组和 合并,操作人员由3人减为1人。 类似这种需要改进的地方在我们公司内有多少?是熟 视无睹?是不愿意去改进?还是心有余力而力不足? 怎样在力所能及的范围内先进行改进,然后再加以推 广?
制造过多(早)的浪费
⑧管理的浪费
所谓管理是指问题发生后,管理人员事后想办
法来补救的浪费。
科学的管理是事先有预见、有规划,在事情推
进过程中有管理控制。
管理浪费存在主要原因有四点:
1. 管理中民主发扬不足
2.
3. 4.
管理过程中粗枝大叶
掌握的管理技术不够 管理创新与全员参与改善的氛围没有
让我们每天进步一点点