超低碳超低氮生产工艺技术开发研究方案
超低排放计划实施方案

超低排放计划实施方案一、背景分析。
随着工业化进程的加快和城市化进程的不断推进,我国环境污染问题日益严重,大气污染成为了人们关注的焦点。
为了改善环境质量,我国提出了超低排放计划,旨在减少工业企业的大气污染物排放,实现大气环境质量的改善。
二、目标确定。
1. 实施超低排放计划,减少工业企业大气污染物排放。
2. 提高工业企业的环保意识,推动绿色发展。
3. 加强监管力度,确保超低排放计划的有效实施。
三、实施方案。
1. 加强政策引导,建立奖惩机制。
政府应出台相关政策,对实施超低排放的企业给予奖励,对未达标排放的企业进行惩罚,形成良好的激励机制。
2. 加大技术改造力度,提高污染治理设施的效率。
鼓励企业增加投入,更新设备,提高污染治理设施的处理效率,确保达到超低排放标准。
3. 强化监督检查,加大执法力度。
加强对工业企业的监督检查,对超低排放计划的实施情况进行全面排查,对违规企业进行严厉处罚,确保超低排放计划的有效实施。
4. 加强宣传教育,提高环保意识。
通过开展环保宣传教育活动,提高广大企业和公众对环保工作的重视程度,增强环保意识,共同参与超低排放计划的实施。
四、保障措施。
1. 健全法律法规,强化环保法制建设,建立健全的法律法规体系,加强环保执法力度,确保超低排放计划的顺利实施。
2. 完善监测体系,加强大气环境监测。
建立健全的大气环境监测网络,对工业企业的大气排放进行实时监测,及时发现问题并采取有效措施加以解决。
3. 加强协作机制,形成合力。
政府部门、企业和社会各界应加强合作,形成合力,共同推动超低排放计划的实施,共同为改善大气环境质量贡献力量。
五、总结。
超低排放计划的实施,是我国环保工作的重要举措,对改善大气环境质量具有重要意义。
各级政府部门、企业和社会各界应共同努力,积极参与超低排放计划的实施,为实现绿色发展、美丽中国贡献自己的力量。
只有通过共同努力,才能实现环境保护和经济发展的双赢局面。
钢铁、焦化、铁合金行业超低排放技术推广方案(二)

钢铁、焦化、铁合金行业超低排放技术推广方案一、实施背景随着中国工业化、城市化的快速发展,钢铁、焦化、铁合金行业已成为国民经济发展的重要支柱产业。
然而,这些行业的生产过程会产生大量的污染物,如粉尘、废气、废水等,对环境和人类健康产生严重影响。
为了降低污染排放,提高空气质量,国家制定了超低排放标准,要求这些行业进行产业结构改革,采用清洁生产技术,减少对环境的影响。
二、工作原理超低排放技术推广方案的工作原理主要是通过对钢铁、焦化、铁合金生产过程中的各种污染物进行治理,以达到超低排放标准。
具体包括以下几个方面:1. 粉尘治理:采用袋式除尘、静电除尘、湿法除尘等技术,对生产过程中产生的粉尘进行收集和处理。
2. 废气治理:采用吸附、催化燃烧、生物处理等技术,对生产过程中产生的废气进行处理。
3. 废水治理:采用物理、化学、生物等技术,对生产过程中产生的废水进行处理,以达到一级排放标准。
三、实施计划步骤1. 确定治理目标:根据国家超低排放标准,确定钢铁、焦化、铁合金行业的治理目标,包括排放浓度、排放速率、排放量等指标。
2. 制定治理方案:根据治理目标,制定具体的治理方案,包括采用的工艺流程、设备选型、运行维护等内容。
3. 建设治理设施:根据治理方案,建设相应的治理设施,包括废气治理设施、废水治理设施等。
4. 调试运行:对治理设施进行调试运行,确保设施的正常运行,并达到预期的治理效果。
5. 监测与评估:对治理设施的运行情况进行监测和评估,确保设施的稳定性和可靠性。
四、适用范围本推广方案适用于钢铁、焦化、铁合金行业,要求企业根据自身实际情况选择合适的治理技术,制定相应的治理方案。
同时,政府部门应加强对这些行业的监管力度,确保治理设施的正常运行和超低排放标准的执行。
五、创新要点1. 采用先进的治理技术:本方案采用的治理技术包括袋式除尘、静电除尘、湿法除尘、吸附、催化燃烧、生物处理等,均为当前较为先进的治理技术,能够达到超低排放标准。
水泥生产环节全流程超低排放技术研究报告

水泥生产环节全流程超低排放技术研究报告一、水泥生产过程与排放物分析水泥生产过程包括原料的破碎、研磨、配料、烧成、冷却和磨碎等工序,其中烧成工序是最主要的排放源。
水泥熟料烧成过程中产生的排放物主要包括二氧化碳、氮氧化物、硫化物、氢氟化物、颗粒物等。
其中二氧化碳排放是水泥生产中最主要的污染源,占总排放量的70%以上。
二、水泥生产超低排放技术研究现状1. 燃烧技术改进:采用高效低氮燃烧器、增加空气预热系统、优化炉体结构等方式降低燃烧过程中的氮氧化物排放。
2. 催化净化技术:利用催化剂降低氮氧化物和硫化物的排放,例如SCR技术和SNCR技术。
3. 原料替代与混凝土减量:使用替代原料和燃料,如废水泥、废轮胎等,减少二氧化碳排放。
4. 改进熟料配方与熟料粉磨技术:优化熟料配方,降低原料烧成温度,减少排放物。
改进熟料粉磨技术,提高磨矿效率,减少能耗和排放。
5. 除尘技术改进:采用高效除尘设备,如电除尘器、袋式除尘器等,降低颗粒物排放。
三、水泥生产超低排放技术关键问题1. 技术成本:现有超低排放技术成本较高,如何降低技术成本是当前研究的重点。
2. 技术适用性:不同水泥生产装置存在差异,如何根据具体情况选择合适的超低排放技术是关键。
3. 操作管理:超低排放技术需要严格的操作管理和监测,如何做好技术保障是当前面临的挑战。
四、未来发展方向1. 多领域协同研究:水泥生产超低排放技术需要多领域的协同研究,包括材料、化工、环保等领域。
2. 集成创新:发展全流程超低排放技术,实现水泥生产的零排放。
3. 产业标准与政策支持:制定水泥生产超低排放的标准和政策,推动技术研究和应用。
结语水泥生产超低排放技术是当前环保领域的重要课题,通过不断的技术研究和创新,可以降低水泥生产过程中的排放物,实现环境友好型生产。
希望未来能有更多研究机构和企业投入到这个领域,共同推动水泥生产超低排放技术的发展。
钢铁、焦化、铁合金行业超低排放技术推广方案(一)

钢铁、焦化、铁合金行业超低排放技术推广方案一、实施背景近年来,我国钢铁、焦化、铁合金行业发展迅速,但与此同时,环境污染问题也日益严重。
据统计,这些行业排放的污染物占全国工业排放的30%以上,严重影响了空气质量和社会环境。
为了解决这一问题,有必要加快推进超低排放技术的应用和推广。
二、工作原理超低排放技术是指将污染物在燃烧过程中产生的有害气体和粉尘降低到最低限度的技术。
这些技术的具体工作原理包括:1. 干法除尘:利用重力、离心力等物理方法将粉尘从烟气中分离出来。
2. 湿法除尘:用水或其他液体洗涤烟气中的粉尘,使其沉淀或凝聚成泥浆状,再经脱水、干燥等处理后回收。
3. 静电除尘:利用静电场使粉尘颗粒带电,并在电场力的作用下被吸附收集。
4. 布袋除尘:用纤维织物作为过滤材料,使粉尘颗粒在滤布表面形成一层过滤层,从而达到除尘效果。
5. 脱硫脱硝:通过化学反应将硫氧化物和氮氧化物转化为无害的硫酸盐和硝酸盐。
三、实施计划步骤1. 建立项目试点:选择一些钢铁、焦化、铁合金企业作为试点,安装超低排放设施并投入使用,监测其运行效果。
2. 制定推广计划:根据试点项目的运行情况和实际效果,制定超低排放技术推广计划。
3. 技术培训:组织相关企业进行超低排放技术培训,提高企业对超低排放技术的认识和应用能力。
4. 推广实施:按照推广计划,在钢铁、焦化、铁合金企业中全面推广超低排放技术,并定期进行检查和监测,确保实施效果。
5. 评估总结:对超低排放技术的实施效果进行评估和总结,为今后的工作提供参考和借鉴。
四、适用范围本方案适用于钢铁、焦化、铁合金行业中的各类企业和生产环节,包括烧结、球团、炼铁、炼钢、焦化等。
具体适用范围可按照地区和企业类型进行分类:1. 地区范围:适用于各省市钢铁、焦化、铁合金企业所在的地区。
2. 企业类型:适用于所有类型的钢铁、焦化、铁合金企业,包括民营、股份制、国有等企业。
五、创新要点1. 技术创新:采用先进的超低排放技术,使污染物排放量降至最低限度。
超低排放技术方案

超低排放技术方案首先是大气污染物治理技术。
大气污染物主要包括颗粒物(PM2.5、PM10)、二氧化硫(SO2)、氮氧化物(NOx)等。
针对颗粒物的治理技术主要包括机械除尘、静电除尘、湿法除尘等。
其中,静电除尘采用在气流中加电场的方式,使颗粒物带电并被收集,具有高效、经济的特点。
对于SO2的治理,常用的方法是石灰石石膏法和海水脱硫法。
这两种方法分别利用石灰或者海水与SO2反应生成硫酸钙或者硫酸钠,从而达到脱硫的效果。
对于NOx的治理,常用的方法是选择性催化还原法,利用氨在催化剂的作用下与NOx反应生成氮和水。
其次是水污染物治理技术。
水污染物主要包括重金属、有机物、氮磷等。
对于重金属的治理,常用的方法有沉淀、吸附和隔离等。
其中,沉淀是利用金属离子与沉淀剂反应生成不溶性沉淀物,从而减少金属离子的浓度。
吸附是利用吸附剂吸附金属离子,常用的吸附剂有活性炭、聚合物等。
对于有机物的治理,常用的方法包括生化处理和物理吸附等。
生化处理是利用微生物将有机物降解为无害的物质,常见的方法有好氧生物处理和厌氧生物处理等。
物理吸附则是利用活性炭等吸附剂将有机物吸附,从而达到去除有机物的目的。
对于氮磷的治理,主要利用生化法和化学沉淀法。
生化法主要利用硝化和反硝化过程将氨氮转化为硝态氮和氮气,磷酸盐通过生物吸附和化学还原得到去除。
再次是固体废物处理技术。
固体废物主要包括垃圾、煤矸石等。
对于垃圾的处理,常用的方法有焚烧和填埋。
焚烧是利用高温燃烧将垃圾转化为无害物质和能量,可以减少垃圾的体积和有害物质的排放。
填埋是将垃圾掩埋在地下,采用生物降解和厌氧条件降解有机物,将废物体积减少并避免有害物质排放。
对于煤矸石的处理,常用的方法是浸泡氧化法(WAO)。
WAO是指用氧化剂与煤矸石发生氧化反应,将其转化为无害的物质。
最后是低碳技术。
低碳技术主要包括降低能源消耗和使用清洁能源。
降低能源消耗的方法有节能改造、提高能源利用效率、绿色建筑等。
节能改造主要包括对现有设备进行优化和升级,采用高效节能设备等。
超低排放改造工程方案

超低排放改造工程方案前言在当前环境保护意识不断提升的背景下,工业企业的污染排放问题备受关注,超低排放成为企业转型升级的必经之路。
本文旨在探讨超低排放改造的具体方案,并对其实施过程中的实际效果进行评估。
超低排放改造方案超低排放改造方案主要包括以下几个步骤:1. 确定排放指标首先,需要确定超低排放改造的具体目标,即排放指标。
排放指标既要符合国家法规要求,也要能够满足企业实际生产需求。
在此基础上,再制定出一套排放标准体系,明确每个环节的排放要求和操作流程。
2. 优化设备布局企业应根据其生产工艺流程以及排放标准体系,对设备进行布局优化。
优化设备布局可以有效地提高设备稳定性和效益,并且能够降低排放浓度,达到减少环境污染的目的。
3. 升级设备升级生产设备是实现超低排放的核心步骤。
通过升级设备,将老旧的、低效的设备替换为新型高效节能设备,可以达到降低能耗、提高生产效率的目的,同时确保达到超低排放标准。
4. 安装在线监测系统在超低排放改造工程中,为了能够实时监测并控制排放浓度,需要安装在线监测系统。
该系统可以帮助企业快速发现设备故障和生产异常情况,提高运行效率,并能够及时对排放浓度进行监测和调整,保证企业排放达标。
5. 排放管线更新在超低排放改造工程中,排放管线更新也是非常重要的步骤。
优化管线系统可以有效地降低管网阻力,并增强排放能力,从而达到更好的环保效果。
超低排放改造实施效果评估超低排放改造实施效果的评估需要根据企业排放指标数据进行分析。
通常,评估的主要指标包括排放浓度、污染物排放物量、能耗减少量等。
评估结果可作为企业继续完善环保措施的重要依据,同时也可以补充完善排放标准体系,推动环保法规的落实。
结论超低排放改造工程是一项环保十分重要的任务,需要企业积极响应国家政策,进行全面的技术改造和系统改进。
通过执行超低排放改造方案和实施效果评估,企业可以在对环境造成最小影响的前提下,提高生产效率和经济效益。
超低排放改造实施方案

超低排放改造实施方案随着环境保护意识的不断提高,超低排放改造已成为工业企业的重要任务之一。
超低排放是指在保持工业生产的前提下,通过技术手段将大气污染物排放控制在极低水平,以达到减少环境污染、改善空气质量的目的。
为了有效实施超低排放改造,我们制定了以下实施方案。
首先,对污染源进行全面排查和评估。
通过对企业的生产设备、工艺流程、排放口等进行全面排查,了解污染源的性质、规模和排放浓度等情况,为后续改造提供准确的数据支持。
其次,制定具体的改造方案。
根据排查评估结果,针对不同的污染源制定相应的改造方案,包括技术改造、设备更新、工艺优化等措施,确保在不影响正常生产的前提下,实现排放达标。
接着,加强技术研发和装备更新。
通过引进先进的污染治理技术和设备,提高污染物的收集、处理和排放控制效率,确保达到超低排放标准。
同时,加强管理和监督。
建立健全的超低排放管理制度,强化对污染治理设施的运行维护和监测检测,确保超低排放标准的持续达标。
最后,加强宣传和培训。
加强对员工的环保意识培训,提高他们的环境保护意识和责任感,形成全员参与、共同推动超低排放改造工作的良好氛围。
在实施超低排放改造的过程中,需要充分发挥政府的引导作用,加大政策支持和资金投入,为企业提供必要的支持和帮助。
同时,企业也要积极主动地履行社会责任,采取有效措施,全面提高排放标准,为改善环境质量贡献自己的力量。
综上所述,超低排放改造实施方案的制定和实施是一项系统工程,需要全社会的共同参与和努力。
只有通过各方的共同努力,才能实现超低排放的目标,为改善环境质量作出积极贡献。
希望各相关部门和企业能够高度重视超低排放改造工作,积极落实相关政策,共同推动超低排放改造工作取得实质性进展。
研究“超低排放”新技术改造方案
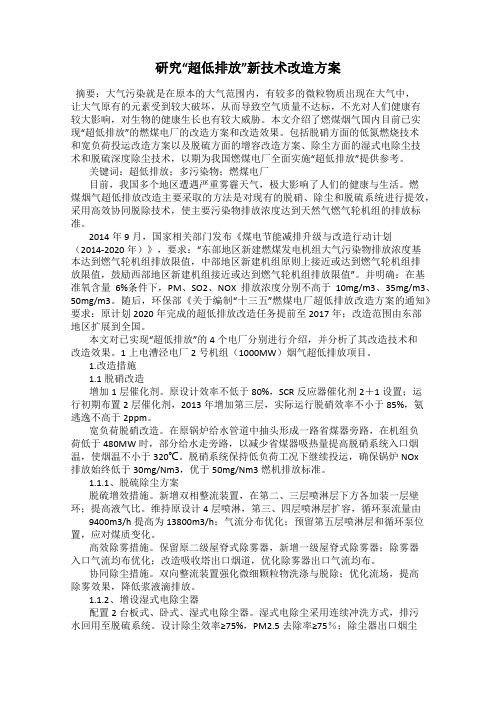
研究“超低排放”新技术改造方案摘要:大气污染就是在原本的大气范围内,有较多的微粒物质出现在大气中,让大气原有的元素受到较大破坏,从而导致空气质量不达标,不光对人们健康有较大影响,对生物的健康生长也有较大威胁。
本文介绍了燃煤烟气国内目前已实现“超低排放”的燃煤电厂的改造方案和改造效果。
包括脱硝方面的低氮燃烧技术和宽负荷投运改造方案以及脱硫方面的增容改造方案、除尘方面的湿式电除尘技术和脱硫深度除尘技术,以期为我国燃煤电厂全面实施“超低排放”提供参考。
关键词:超低排放;多污染物;燃煤电厂目前,我国多个地区遭遇严重雾霾天气,极大影响了人们的健康与生活。
燃煤烟气超低排放改造主要采取的方法是对现有的脱硝、除尘和脱硫系统进行提效,采用高效协同脱除技术,使主要污染物排放浓度达到天然气燃气轮机组的排放标准。
2014年9月,国家相关部门发布《煤电节能减排升级与改造行动计划(2014-2020年)》,要求:“东部地区新建燃煤发电机组大气污染物排放浓度基本达到燃气轮机组排放限值,中部地区新建机组原则上接近或达到燃气轮机组排放限值,鼓励西部地区新建机组接近或达到燃气轮机组排放限值”。
并明确:在基准氧含量6%条件下,PM、SO2、NOX排放浓度分别不高于10mg/m3、35mg/m3、50mg/m3。
随后,环保部《关于编制“十三五”燃煤电厂超低排放改造方案的通知》要求:原计划2020年完成的超低排放改造任务提前至2017年;改造范围由东部地区扩展到全国。
本文对已实现“超低排放”的4个电厂分别进行介绍,并分析了其改造技术和改造效果。
1上电漕泾电厂2号机组(1000MW)烟气超低排放项目。
1.改造措施1.1脱硝改造增加1层催化剂。
原设计效率不低于80%,SCR反应器催化剂2+1设置;运行初期布置2层催化剂,2013年增加第三层,实际运行脱硝效率不小于85%,氨逃逸不高于2ppm。
宽负荷脱硝改造。
在原锅炉给水管道中抽头形成一路省煤器旁路,在机组负荷低于480MW时,部分给水走旁路,以减少省煤器吸热量提高脱硝系统入口烟温,使烟温不小于320℃。
超低碳超低硫钢生产工艺研究

2.1 优 化原 材料 结构 原辅料结构 的优 化保 证 了超低 碳 、超 低 硫钢 的
成功生产 。主要包括 :装炉制度 、原辅料 的洁净度 控 制 ,如废钢 、石 灰 、合 金 、精 炼渣 等 ,用 以减 少 生产 过 程 中钢水增碳 、回硫 。为此 ,对人 炉原辅 料结构及 合 金 的质 量提出了严格要求 。 2.1.1 铁水 (见表 1)
6
南 钢科 技与 管理
2016年第 1期
超低碳超 低硫钢生产工艺研究
邱 永清 赵晋斌 (研 究 院 )
摘 要 :介绍了第一炼钢厂采用铁水预处理脱硫一BOF.RH—LF.CCM 工艺流程生产超低碳、超低硫、低磷、低氮
钢的生产实践。通过合理的转炉过程和终点控制 、RH真 空脱碳 、LF炉快速造 渣脱硫 、连铸过 程全保 护 浇注等 技术手段 ,成功 生产 了[C]≤0.01% 、[S]≤0.002% 、[P]≤0.013% 、[N]≤0.004% 高纯净度 的钢水 ,并在 板坯 连铸 机 上 实 现 了 多炉 连 浇 。 该 工 艺成 功 的 应 用在 抗 震 建 筑 用低 屈 服 点钢 的 生 产 中 ,为 南钢 生产 超 低 碳 、超 低 硫 钢 开 辟 了一 条 很 好 的 途 径 。 关键词 :超低碳超低硫钢 真空度 脱硫 造渣
CaO
SiO2
P
S
不 小 于
不 大 于
90
2.5
O.O2
O.10
物 理 指 标
活性度 (n11)
本钢超低氮钢生产工艺的研究

摘要 : 本文从 氮在钢液 中的危 害出发 , 根据 C O气泡脱 氮及真 空脱 氮原理及钢液 与空气接 触造 成增 氮的特 点, 详细论述 了 转炉、 H及 浇铸过程 中脱氮及 控制增氮的方法 , R 降低 了钢 中氮的含量 , 大地提 高 了钢材 的质量。 极
关键 词 : 炼钢 ; 超低 氮 钢 ; 氮 脱
() 1 钢包水 口与长水 口之 间的密 封材料 , 采用 含焦 油沥
青 的 Mg 0充 填 物 。
42 1 真空脱氮机理研究 ..
目前工业真空 脱气 设 备 的真空 度一 般 可 以达 到 6 P , 7a 在这个真空度下 , 液中平衡的氮含量 应该为 1p m。真空 钢 0p 处理时 , 液中氮的平衡 分压远 大于真 空室 内氮 的分压 , 钢 所 以会 自发 的进行脱氮 。
30 ‘
~ 一
2 超低 氮 钢生产 工艺 流程
本钢生产 超低 氮 钢工 艺流 程 : 铁水 脱硫一复 吹转 炉 冶
终
・
2 : j
. ・ .
.◆
・
!
炼一R T H— B精炼一板坯连铸。
3 改进 前各 工序 氮含 量 的变化
。
芸2 0
含
遣
p 【 m 1】
厂工程师 。 ຫໍສະໝຸດ () 6 出钢合金化 出钢过程不进行脱氧及合金化操 作 , 因为钢 液中 [ 是 O]
是表面活性元素 , 它能阻止空气中 { 2} N 向钢 液中溶解扩散 ,
若钢水 中[ ] O 含量过低 , 容易 造成钢 水从大气 中吸氮严重。
维普资讯
/
一 ・一.. 。 . .
・ ・・ ◆ . ・
’ ’ ・
超低排放改造工程方案

超低排放改造工程方案一、项目背景随着全球城市化和工业化的发展,环境污染已成为全球性问题。
空气污染是目前最为严重的环境问题之一,其中工业污染排放是主要因素之一。
为了改善环境质量,各国都提出了降低工业排放的要求,中国也不例外。
中国作为世界上人口最多、经济发展最快的国家之一,对空气质量的要求尤为严格。
为了满足国家的环保要求,许多企业和工厂都在进行超低排放改造工程,以减少工业排放对环境的影响。
二、项目概况本项目为某钢铁厂超低排放改造工程,该厂位于中国东部的一个工业城市,是当地重要的钢铁生产企业之一。
由于该厂的生产设备老化,存在排放浓度高、污染物排放量大等问题,严重影响了周边环境的空气质量。
为了改善环境,提高企业形象,该厂决定进行超低排放改造工程。
三、项目目标本项目的目标是通过技术改造,将该钢铁厂的排放达到国家超低排放标准,以减少对环境的污染,改善周边空气质量。
具体目标包括:1. 减少硫化物、氮氧化物、悬浮颗粒物等污染物的排放浓度;2. 降低工业废气的排放量;3. 提高工业废气处理设备的处理效率和稳定性;4. 减少对周边环境的负面影响;5. 提高企业形象,获得政府和社会的认可。
四、项目方案1. 技术改造针对该钢铁厂的工业废气排放问题,我们制定了以下技术改造方案:(1)更新高炉炉顶喷吹除尘技术,采用新型除尘器,提高除尘效率;(2)更新焦化车间焦炉喷吹除尘技术,采用先进的除尘设备;(3)针对排放中的硫化氢和氮氧化物,更新熔融镁炉技术,提高硫化氢和氮氧化物的吸附潜力;(4)更新烧结烟气处理系统,提高烟气的净化效率;(5)更新燃气高炉的处理系统,采用先进的脱硫、脱硝装置,减少硫化物和氮氧化物的排放;(6)对烧结机、烧结烟气、燃气高炉以及其它工业设备进行技术改造和更新,以提高设备的稳定性和可靠性。
2. 环保设施建设为了保证技术改造的顺利实施,我们还需要对环保设施进行建设和更新,包括新型除尘设备、脱硫脱硝设备、粉尘回收装置等。
超低碳超低氮生产工艺技术开发研究方案
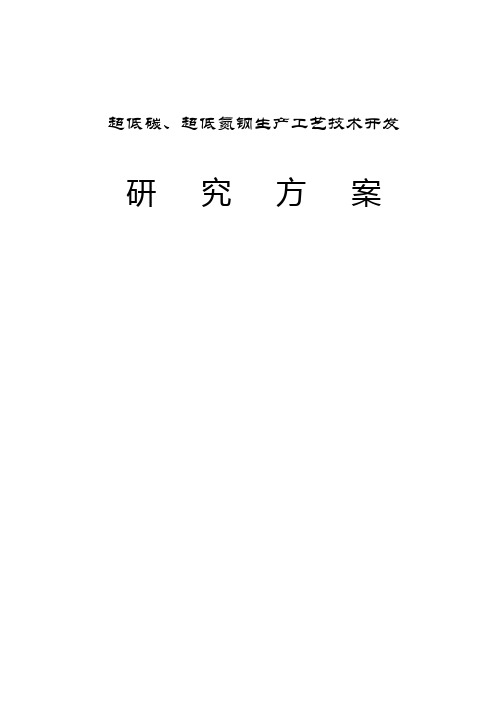
超低碳、超低氮钢生产工艺技术开发研究方案目录一、超低碳、超低氮钢生产工艺技术开发研究计划 (1)1.技术目旳 (1)2.技术原则 (1)3.研究内容 (1)4.研究措施 (1)5.试验环节 (1)二、超低碳、超低氮钢冶炼热模拟试验室研究 (3)(一)超低碳化精炼热模拟研究 (3)1.技术基础 (3)2.试验室研究内容 (3)3.试验方案初步设计 (3)(二)超低氮化精炼热模拟研究 (3)1.技术基础 (3)2.试验室研究内容 (4)3.试验方案初步设计 (4)三、超低碳、氮钢冶炼工业试验研究 (6)1.工业试验研究内容 (6)2.工业试验措施 (6)3.工业试验初步设计 (6)超低碳、超低氮钢生产工艺技术开发研究方案一、超低碳、氮钢冶炼工艺技术开发研究计划1. 技术目旳开发冷轧薄板钢超低碳、超低氮含量旳冶炼工艺技术。
目旳值(RH-KTB/WPB精炼结束时):[C]≤10ppm,[N]≤13ppm。
2. 技术原则(1)以武钢试行“预直炼”冶炼工艺为优化基础;(2)从钢液中碳、氮深脱热动力学入手,研究工艺原因和限制环节,为优化工艺参数、改善工艺条件提供根据;(3)充足运用已经有旳研究成果,防止不必要旳反复研究;(4)按流程工序分解目旳,分目旳、总目旳同步实现。
3. 研究内容(1)超低碳化技术1)RH-KTB条件下,深脱碳热动力学(脱碳机理、理论模型、参数优化等);2)实现[C]≤10ppm精炼条件和措施;3)防止二次精炼过程中增碳措施;4)技术经济指标稳定化问题。
(2)超低氮化技术1)RH-KTB条件下,深脱氮热动力学(脱氮机理、理论模型、参数优化等);2)防止RH-KTB过程旳吸氮技术;3)转炉超低氮化吹炼及防止吸氮技术;4)实现[N]≤13ppm精炼条件和措施;5)技术经济指标稳定化问题。
4. 研究措施(1)技术目旳分解。
按武钢试行旳“预直炼”冶炼工艺流程,参照已经有旳研究成果,将目旳分解。
分解旳工序目旳列于表1。
超低氮燃烧技术实施计划方案

超低氮燃烧技术实施计划方案实施背景:随着工业化和城市化的不断发展,人们对能源的需求不断增加,而传统的燃烧方式不仅浪费能源,还会对环境造成严重污染。
因此,超低氮燃烧技术的出现,为解决能源浪费和环境污染问题提供了有效的解决方案。
实施计划步骤:1.制定实施计划方案:在制定超低氮燃烧技术实施计划方案时,需要考虑到实施的可行性、实施过程中的风险和挑战等因素,以确保实施计划方案的顺利实施。
2.选取适当的燃烧设备:超低氮燃烧技术需要使用适当的燃烧设备,以确保燃烧效率和能源利用率的最大化。
3.调整燃烧参数:超低氮燃烧技术需要通过调整燃烧参数,以确保燃烧产生的氮氧化物排放量达到最小化。
4.监测和控制排放:实施计划方案需要对燃烧过程中产生的氮氧化物排放进行监测和控制,以确保排放达到国家标准。
创新要点:1.采用新型燃烧设备:超低氮燃烧技术采用新型燃烧设备,以确保燃烧效率和能源利用率的最大化。
2.优化燃烧参数:超低氮燃烧技术通过优化燃烧参数,以确保燃烧产生的氮氧化物排放量达到最小化。
3.加强监测和控制:实施计划方案需要加强对燃烧过程中产生的氮氧化物排放的监测和控制,以确保排放达到国家标准。
预期效果:1.降低氮氧化物排放:超低氮燃烧技术的实施计划方案可以有效地降低氮氧化物排放量,达到环保要求。
2.提高能源利用率:超低氮燃烧技术的实施计划方案可以提高燃烧效率和能源利用率,降低能源浪费。
3.改善环境质量:超低氮燃烧技术的实施计划方案可以改善环境质量,减少对人类健康的危害。
达到收益:1.节约能源:超低氮燃烧技术实施计划方案可以节约能源,提高能源利用效率。
2.降低运营成本:超低氮燃烧技术实施计划方案可以降低运营成本,提高企业盈利能力。
3.提高企业形象:超低氮燃烧技术实施计划方案可以提高企业形象,增强企业社会责任感。
优缺点:优点:1.降低氮氧化物排放,改善环境质量。
2.提高能源利用率,减少能源浪费。
3.节约运营成本,提高企业盈利能力。
轧钢加热炉超低氮排放技术使用计划方案

轧钢加热炉超低氮排放技术使用计划方案一、实施背景随着我国钢铁产业的快速发展,钢铁企业的环保要求也越来越高。
其中,钢铁生产过程中的超低氮排放是环保的重要内容之一。
目前,许多钢铁企业在生产过程中采用传统的加热方式,导致氮氧化物排放量较高,对环境造成了严重污染。
因此,为了实现钢铁企业的环保要求,必须引入超低氮排放技术,提高加热炉的效率,减少环境污染。
二、实施计划步骤1.确定适用范围:钢铁企业生产过程中需要使用加热炉的环节。
2.制定技术方案:根据钢铁企业的生产情况,制定适合的超低氮排放技术方案。
3.实施技术方案:在加热炉中安装超低氮排放技术设备,并进行试运行和调试。
4.监测排放效果:对排放效果进行监测,确保排放水平符合国家和企业的要求。
5.达到收益:通过使用超低氮排放技术,减少氮氧化物排放,达到环保效果,提高企业的经济效益。
三、适用范围本技术方案适用于所有需要使用加热炉的钢铁企业。
四、创新要点本技术方案的创新点在于引入超低氮排放技术,通过减少氮氧化物的排放,实现钢铁企业的环保要求。
五、预期效果通过使用超低氮排放技术,可以达到以下效果:1.减少氮氧化物的排放,实现环保效果。
2.提高加热炉的效率,降低生产成本。
3.提高企业的经济效益,提高企业的竞争力。
六、达到收益通过使用超低氮排放技术,可以达到以下收益:1.减少环境污染,提高企业形象。
2.降低生产成本,提高企业的经济效益。
3.提高企业的竞争力,增强企业的市场占有率。
七、优缺点优点:1.减少氮氧化物的排放,实现环保效果。
2.提高加热炉的效率,降低生产成本。
3.提高企业的经济效益,提高企业的竞争力。
缺点:1.需要投入一定的资金用于购买超低氮排放技术设备。
2.需要对加热炉进行改造和调试,可能会影响生产进度。
八、下一步需要改进的地方目前,超低氮排放技术还存在一些技术难点,需要进一步进行研究和改进。
同时,需要加强对超低氮排放技术的推广和普及,提高企业对环保的认识和重视程度。
球团厂氮氧化物超低排放改造方案讨论
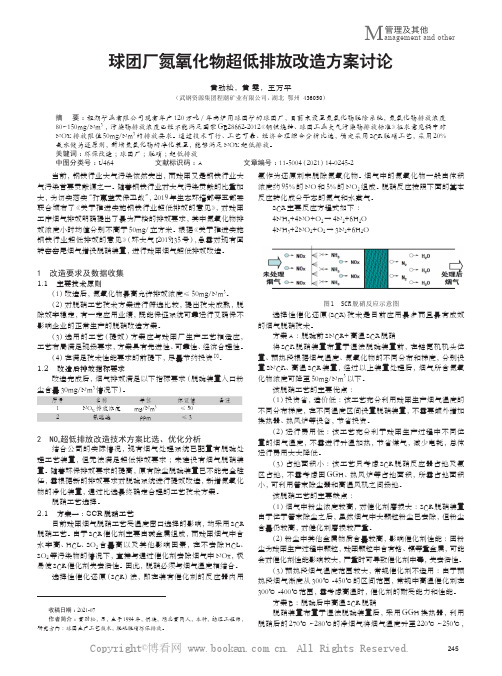
氨作为还原剂来脱除氮氧化物。烟气中的氮氧化物一般由体积 浓度约 95% 的 NO 和 5% 的 NO2 组成。脱硝反应按照下面的基本 反应转化成分子态的氮气和水蒸气。
SCR 主要反应方程式如下 : 4NH3+4NO+O2 → 4N2+6H2O 4NH3+2NO2+O2 → 3N2+6H2O
1 改造要求及数据收集
理工艺装置,但无法满足超低排放要求 ;未建设有烟气脱硝装 置。随着环保排放要求的提高,原有除尘脱硫装置已不能完全胜 任,需根据新的排放要求对脱硫系统进行提效改造,新增氮氧化 物的净化装置,通过比选最终确定合理的工艺技术方案。
脱硝工艺选择。 2.1 方案一 :SCR 脱硝工艺
目前球团烟气脱硝工艺受温度窗口选择的影响,均采用 SCR 脱硝工艺。由于 SCR 催化剂主要由碱金属组成,而球团烟气中含 水率高、HCL、SO2 含量高以及其他影响因素,在不去除 HCL、 SO2 等污染物的情况下,直接与通过催化剂去除烟气中 NOx,极 易使 SCR 催化剂失去活性。因此,脱硝必须与烟气温度相结合。
方案 A :脱硫前 SNCR+ 高温 SCR 脱硝 将 SCR 脱硝装置布置于湿法脱硫装置前,在链篦机机头位 置、预热段根据烟气温度、氮氧化物的不同分布和梯度,分别设 置 SNCR、高温 SCR 装置,经过以上装置处理后,烟气所含氮氧 化物浓度可降至 50mg/Nm3 以下。 该脱硝工艺的主要优点 : (1)投资省,造价低 :该工艺充分利用球团生产烟气温度的 不同分布梯度,在不同温度区间设置脱硝装置,不需要额外增加 换热器、热风炉等设备,节省投资。 (2)运行费用低 :该工艺充分利于球团生产过程中不同位 置的烟气温度,不需进行升温加热,节省煤气,减少电耗,总体 运行费用大大降低。 (3)占地面积小 :该工艺只考虑 SCR 脱硝反应器占地及氨 区占地,不需考虑因 GGH、热风炉等占地面积,所需占地面积 小,可利用管束除尘器和高温风机之间场地。 该脱硝工艺的主要缺点 : (1)烟气中粉尘浓度较高,对催化剂磨损大 :SCR 脱硝装置 由于位于管束除尘之后,虽然烟气中大颗粒粉尘已去除,但粉尘 含量仍较高,对催化剂磨损较严重。 (2)粉尘中其他金属物质含量较高,影响催化剂性能 :因粉 尘为球团生产过程中颗粒,球团颗粒中含有铬、镉等重金属,可能 会对催化剂性能影响较大,严重时可导致催化剂中毒,失去活性。 (3)预热段烟气温度范围较大,常规催化剂不适用 :由于预 热段烟气渐度从 300℃ -450℃的区间范围,常规中高温催化剂在 300℃ -400℃范围,需考虑高温时,催化剂的耐受能力和性能。 方案 B :脱硫后中高温 SCR 脱硝 脱硝装置布置于湿法脱硫装置后,采用 GGH 换热器,利用 脱硝后的 270℃ ~280℃的净烟气将烟气温度升至 220℃ ~250℃,
转炉冶炼超低碳超低氮钢的工艺技术

转炉冶炼超低碳、超低氮钢的工艺技术吴 杰 刘振清(武汉钢铁(集团)公司技术中心,武汉430080)摘 要 分析了武钢90t 顶底复吹转炉冶炼<01005%C ,≤01005%N 超低碳、氮钢的两种冶炼工艺技术,即常规工艺:K R 脱S →LD →RH 2K T B →CC 和双联工艺:K R 脱S →LD 脱S i 、P →LD 复吹脱碳→RH 2K T B →CC 。
实践表明,常规工艺冶炼时中间包钢水平均C 含量为2515×10-6、平均N 含量为1815×10-6;双联工艺冶炼时,中间包钢水平均C 含量为16×10-6、平均N 含量为19×10-6,双联工艺吹炼终点[P](60×10-6)比常规工艺(110×10-6)低。
关键词 超低碳 超低氮 转炉 RH 2K T B 精炼 冶炼Metallurgy T echnology for U ltra 2Low C arbon and U ltra 2LowNitrogen SteelWu Jie and Liu Zhenqing(T echnical Center ,Wuhan Iron and S teel G roup C orp ,Wuhan 430080)Abstract T w o kinds of metallurgical process for melting a <01005%C 2≤01005%N ultra 2low carbon and ultra 2low nitrogen steel by a 90t top and bottom combined blown converter a Wuhan Iron and S teel :single slag process K R desulphu 2ration 2LD 2RH 2K T B 2CC and tw o 2step steelmaking process K R desulphuration 2LD desiliconisation and dephosphorization 2LD combined blown decarburation 2RH 2K T B 2CC have been analyzed.The practice results showed that during steelmak 2ing with single slag process the average C content in liquid steel in tundish was 2515×10-6and the average N content was1815×10-6and with tw o 2step process the average C content in liquid steel in tundish was 16×10-6,the average N content was 19×10-6,and the end [P]with tw o 2step process (60×10-6)was lower that with single slag process (110×10-6).Material I ndex Ultra 2Carbon ,Ultra 2Nitrogen ,C onverter ,RH 2K T B Refining ,S teelmaking 当代转炉典型的超低碳、超低氮钢的生产工艺流程主要分为常规工艺和双联工艺两种[1]。
超低排放方案范文

超低排放方案范文随着全球环境问题日益严重以及对空气污染、温室气体排放限制的要求越来越高,超低排放方案成为了保护环境和可持续发展的必然选择。
超低排放方案是指通过采取一系列技术措施,减少或消除工业、农业、交通等领域对大气、水体和土壤的污染物排放,从而实现环境质量的改善和生态系统的修复。
以下将介绍超低排放方案在不同领域的应用。
首先,在工业领域中,超低排放方案的重点是减少工业废气和废水的污染物排放。
工业废气的超低排放方案主要包括改善燃烧设备的效率和减少氮氧化物、二氧化硫和颗粒物等污染物的排放。
这可以通过采用高效燃烧设备、燃烧优化技术、烟气脱硫、脱硝和粉尘去除等方法来实现。
同时,废水处理方案则采用了物理、化学和生物等多种技术,如生物膜法、高级氧化法和反渗透等技术,从而实现废水的高效处理、回用和排放达标。
其次,在农业领域中,超低排放方案的目标是减少农业活动对土壤和水体的污染。
农业废物处理方案采用了资源化利用和农业面源污染控制相结合的措施,如采用沼气、生物质和有机肥料等方式处理农业废弃物,减少因废弃物堆积带来的环境问题。
此外,还采用了水肥一体化、精准施肥、灌溉与排水技术等措施,减少农业面源污染对水体和土壤的负面影响。
再次,在交通领域中,超低排放方案的重点是减少车辆排放对大气的污染。
针对机动车尾气污染,采用了车用燃料改进、排放控制技术和车辆限制措施等方法。
例如,推广使用清洁能源车辆(如电动汽车和混合动力汽车),提高尾气净化设施的效率,推行汽车定期检测和维护等措施,从而减少车辆排放的污染物。
此外,利用交通规划和优化调度等方法,优化交通流量,降低交通拥堵,减少排放物的产生和集中排放的影响。
最后,在能源领域中,超低排放方案主要集中在减少化石能源的使用和增加清洁能源的比重。
这可以通过发展可再生能源、提高能源利用效率、优化能源结构等途径来实现。
例如,推广使用太阳能、风能和水能等可再生能源,减少对化石能源的依赖;加强能源供给侧,提高燃煤电厂的燃烧效率和排放控制水平;推动地热能、生物质能和海洋能等清洁能源的开发和利用。
- 1、下载文档前请自行甄别文档内容的完整性,平台不提供额外的编辑、内容补充、找答案等附加服务。
- 2、"仅部分预览"的文档,不可在线预览部分如存在完整性等问题,可反馈申请退款(可完整预览的文档不适用该条件!)。
- 3、如文档侵犯您的权益,请联系客服反馈,我们会尽快为您处理(人工客服工作时间:9:00-18:30)。
超低碳、超低氮钢生产工艺技术开发研究方案目录一、超低碳、超低氮钢生产工艺技术开发研究计划 (1)1.技术目标 (1)2.技术原则 (1)3.研究内容 (1)4.研究方法 (1)5.实验步骤 (1)二、超低碳、超低氮钢冶炼热模拟实验室研究 (3)(一)超低碳化精炼热模拟研究 (3)1.技术基础 (3)2.实验室研究内容 (3)3.实验方案初步设计 (3)(二)超低氮化精炼热模拟研究 (3)1.技术基础 (3)2.实验室研究内容 (4)3.实验方案初步设计 (4)三、超低碳、氮钢冶炼工业实验研究 (6)1.工业试验研究内容 (6)2.工业试验方法 (6)3.工业试验初步设计 (6)超低碳、超低氮钢生产工艺技术开发研究方案一、超低碳、氮钢冶炼工艺技术开发研究计划1. 技术目标开发冷轧薄板钢超低碳、超低氮含量的冶炼工艺技术。
目标值(RH-KTB/WPB精炼结束时):[C]≤10ppm,[N]≤13ppm。
2. 技术原则(1)以武钢试行“预直炼”冶炼工艺为优化基础;(2)从钢液中碳、氮深脱热动力学入手,研究工艺因素和限制环节,为优化工艺参数、改善工艺条件提供依据;(3)充分利用已有的研究成果,避免不必要的重复研究;(4)按流程工序分解目标,分目标、总目标同时实现。
3. 研究内容(1)超低碳化技术1)RH-KTB条件下,深脱碳热动力学(脱碳机理、理论模型、参数优化等);2)实现[C]≤10ppm精炼条件和措施;3)防止二次精炼过程中增碳措施;4)技术经济指标稳定化问题。
(2)超低氮化技术1)RH-KTB条件下,深脱氮热动力学(脱氮机理、理论模型、参数优化等);2)防止RH-KTB过程的吸氮技术;3)转炉超低氮化吹炼及防止吸氮技术;4)实现[N]≤13ppm精炼条件和措施;5)技术经济指标稳定化问题。
4. 研究方法(1)技术目标分解。
按武钢试行的“预直炼”冶炼工艺流程,参照已有的研究结果,将目标分解。
分解的工序目标列于表1。
(2)实验室研究。
重点为RH-KTB/WPB热动力学问题(即反应进行的方向、限度和速度),同时研究RH-KTB/WPB与前后工序有效匹配的最佳条件。
(3)工业试验研究。
大生产条件下验证试验工艺方案,依试验结果修正工艺参数和改进工艺条件,逐步优化试验,直至确定最优工艺方案。
至少试验3~5个回合,每回合一个浇次。
5. 实验步骤(1)通过实验室研究和借鉴现成成果,确定实现目标值的条件和影响因素;(2)进行工业试验,逐步修正和完善工业条件和参数;(4)进行小批量生产试验,稳定工艺条件和参数,提高成功率;(5)转入大生产,制定工艺规范,总结验收。
表1 碳、氮高纯化冷轧薄板钢冶炼工艺试验工序目标二、超低碳、氮钢冶炼热模拟实验室研究(一)超低碳化精炼热模拟研究1. 技术基础随着RH-OB、RH-KTB等真空下强制吹氧脱碳技术开发与应用,真空下碳氧反应的研究格外受到重视,结合RH-KTB研究,已经取得一些可喜的成果:(1)向RH下部钢水面强制吹氧,可以在很大[C]含量范围内,提高脱碳速率,在十几分钟之内可以把[C]降至10ppm左右;(2)为了达到极低碳目标,尽可能增大真空泵抽气能力(确保足够长的高真空处理时间)、大环流上升管内径(增大Ar气量和钢水环流量)和良好的动力学条件(提高钢水的搅拌能和体积传质系数)。
同时应注重配套技术的进步;(3)随之建立的理论模型对深脱碳过程的因素和参数分析、对过程的控制、预报和优化等都起着积极作用。
2. 实验室研究内容(1)模拟KTB的条件,研究深脱碳规律(尤其是[C]<30ppm区);(2)模拟PB的条件,研究喷粉对深脱碳的影响;3. 实验方案初步设计(1)真空强制脱碳时低碳钢液的脱碳实验。
设备:25Kg多功能真空感应炉。
原料:工业纯铁、优质废钢、FeO粉、Al粒等。
真空度:2000Pa、110Pa、67Pa。
吹Ar:底部吹Ar压力(20~40KPa),纯度>99.9%。
方法:装22Kg按不同[C]配置的金属料,在2000Pa真空度下熔化,加FeO粉供氧,吹Ar均匀化,测温取样;然后把真空度提高到实验值,按一定间隔时间取样;再用Al控制[O],精炼一定时间后(高真空度下保持),取样定碳定氧。
目的:真空度、真空处理时间、[O]0、[C]0、吹氩量等对深脱碳的影响。
(2)密封吹Ar喷粉过程中钢液脱碳动力学研究实验。
设备:250Kg中频感应炉;送粉速度有送粉设备可控硅调速器无级调速;刚玉质喷枪内径4mm,外径60mm;水冷Ar密封罩。
原料:优质薄板材返回料;FeO粉(或铁精矿粉)、特殊熔剂等。
方法:200Kg废钢装入感应炉,熔化后测温取样,定碳定氧,吹氧脱碳至[C]<50ppm,然后加铝脱氧。
安置密封罩吹氩,清除罩内空气,插枪到指定位置,开始喷吹(喷吹压力0.15MPa,插入深度为熔池深2/3处),粉剂用量约4Kg/t钢(与WPB工艺接近),粉剂为50%FeO(精矿粉)+50%特殊熔剂。
喷吹过程中取钢样和炉气样。
目的:以钢液面P CO、吹Ar量、[O]、[C]、T等为参数,研究喷粉过程中钢液碳含量的变化。
分析:[O]用ZrO2固体电解质定氧方法确定;气相色谱仪分析炉气成分。
(二)超低氮化精炼热模拟研究1. 技术基础近代真空冶金理论研究,重要的成就之一是推动了真空各种工艺条件下脱氮、吸氮热动力学。
例如,针对RH-KTB工艺技术,大多数研究者基本肯定了以下的成果:(1)存在多种脱氮途径,如真空脱氮、CO和Ar气泡携带脱氮、熔渣脱氧等;(2)脱氮区域主要在真空室下部钢液自由表面;CO-钢液界面;Ar-钢液表面;熔渣-钢液界面等;(3)在高浓度[S](100~150ppm),特别是较高[O]和较少脱碳量(低于300~400ppm)时,当[N]已经进入超低氮区域([N]<20ppm),所有途径的脱氮效果都有限;(4)要想获得超低氮冶金效果主要靠强化转炉内脱氮和抑制转炉出钢、二次精炼、连铸过程等吸氮;(5)吸氮随表面活性元素(O、S等)以及易氮化元素(Ti、Ni、V、Al、RE等)含量不同,过程机构有所差别,但多为液相边界层传质及界面反应混合限制。
吸氮速率影响程度也不一样。
2. 实验室研究内容(1)真空脱氮动力学研究,包括真空度、气相压力、钢水条件(氧、硫含量、温度等)对脱氮动力学的影响;(2)气泡(CO、Ar气泡)携带法脱氮研究,探明转炉和KTB条件下吹氧脱碳过程中,脱氮速度与脱碳速度的关系;(3)吹氩喷粉过程中钢液脱氮动力学研究;(4)炉渣脱氮可能性研究,造一种高氮容量的渣,[N]扩散到渣/钢界面,然后与渣中一些化合物反应转入渣相去除掉。
3. 实验方案初步设计(1)真空碳氧反应条件下低氮钢液的脱氮实验。
设备:25Kg多功能真空感应炉。
原料:工业纯铁等。
真空度:2000Pa、110Pa、67Pa。
方法:装22Kg纯铁在2000Pa真空度下熔化(真空开始时[N]0接近KTB实际值),熔化后,将真空度提高到试验值,不用Al脱氧取前几个样,加Al脱氧后取最后一个试样。
目的:研究不同真空度下的脱氮规律,验证真空度不仅影响热力学,同时也影响动力学。
分析:氧、氮分析在LECO-436氧氮分析仪上进行。
(2)气相压力对钢液脱氮动力学影响实验。
设备:25Kg多功能真空感应炉原料:工业纯铁、FeS等Ar压力:40KPa(纯度>99.9%)方法:装22Kg纯铁在2000Pa真空度下熔化,然后把真空度提高到试验值,吹Ar 压力40KPa,用Al控制[O],在一定时间间隔内分别取样分析[N]。
目的:研究不同气相压力下[N]随时间变化;同时得到温度、S、O等对脱氮的影响。
(3)密封吹Ar喷粉过程中钢液脱氮动力学研究实验。
设备:250Kg中频感应炉;送粉速度由送粉设备可控硅调速器无级调速;刚玉质喷枪内径4mm,外径60mm;水冷Ar密封罩。
原料:废钢0.2%C、0.005%S、0.010%P;初始[S]由FeS调整;喷粉剂组成方案:①85%钝化石灰+15%CaF2(粒度0.175~0.147mm/80~100目)②54%CaO-20%Al2O3-10%SiO2-8%MgO-8%CaF③在①、②分别配入一定量的FeO粉(氧源:50KgFe3O4→200ppm[O],形成CO核心)方法:200Kg 废钢装入感应炉,熔化后加FeSi 、Al 脱气,取样及测温定氧,安置密封罩吹Ar ,清除罩内空气,插枪到指定位置,开始喷吹(喷吹压力0.15MPa ,插入深度为熔池深2/3处),粉剂用量按4Kg/t 钢计(与WPB 工艺相近)。
喷吹过程中取钢样和炉气样。
目的:以钢液面氮分压、吹Ar 量、[O]、[S]、[N]0、T 等为参数,研究喷粉过程中钢液氮含量的变化。
分析:[O]用ZrO 2固体电解质定氧方法确定;[S]由碳-硫分析仪测定;气相色谱仪分析炉气成分。
(4) 熔剂氮容量(-3N C )测定实验。
设备:钼丝炉、铂坩埚。
原料:上述三种粉剂。
方法:将25g 渣放入铂坩埚内,在钼丝炉高温区熔化,恒温在1823K ,并用CO 调整P O2、P N2(测定炉气成分),并测定渣中氮的溶解度。
用1/2N 2+3(O 2-)=(N 3-)+3/4O 2、-3N C =(%N 3-)、214322N O P P 等式计算出-3N C 。
目的:确定氮容量大的熔剂,作为脱氮渣。
以上实验计划列入表2。
表2 实验室试验研究计划三、超低碳、氮钢冶炼工业实验研究1. 工业试验研究内容(1)重点研究RH阶段KTB和PB过程热动力学因素和条件对终了[C]、[N]目标值的影响;(2)研究RH前包括铁水预处理、转炉复合吹炼工艺条件等对RH终了[C]、[N]目标值的影响;(3)研究RH过程相关工艺条件(如无碳钢包衬及覆盖渣、真空室耐材、防止和清除真空室壁上冷凝钢问题、不增碳取样器、极低含量分析精度、过程监测及控制等)对目标值的影响;(4)研究现有的理论模型,进行必要的修正,提出相应的新模型,用以指导过程的控制、预报及抑制等;(5)研究最优的工艺条件和参数、确定完善的冶炼制度和工艺方法。
2、工业试验方法(1)工业试验流程:KR →转炉预直炼→RH-KTB/WPB →CC (工序目标见表1) (2)寻求RH-KTB/WPB最佳深脱碳、氮效果(尤其是提高超低碳、氮区进一步深脱碳、氮速率问题)试验(3)RH-KTB/WPB最佳深脱碳、氮速率与前工序的关系试验(4)理论模型修正及新模型应用试验3、工业试验方案初步设计(1)强制脱氮试验。
铁水预处理可以强制脱氮,使铁水中[N]<25ppm,有利随后转炉脱碳时进一步深入脱氮。
方法:利用KR高效脱S,转炉预直炼强制脱P,促进铁水脱氮;KR、转炉预直炼工艺条件和操作方法可执行已进行的试验方案。