4IE经典管理手法
IE七大手法介绍
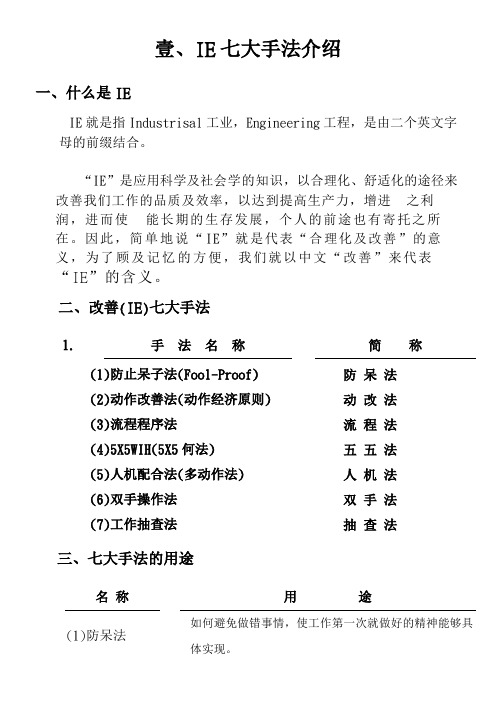
壹、IE七大手法介绍一、什么是IEIE就是指Industrisal工业,Engineering工程,是由二个英文字母的前缀结合。
“IE”是应用科学及社会学的知识,以合理化、舒适化的途径来改善我们工作的品质及效率,以达到提高生产力,增进之利润,进而使能长期的生存发展,个人的前途也有寄托之所在。
因此,简单地说“IE”就是代表“合理化及改善”的意义,为了顾及记忆的方便,我们就以中文“改善”来代表“IE”的含义。
二、改善(IE)七大手法1. 手法名称简称(1)防止呆子法(Fool-Proof) 防呆法(2)动作改善法(动作经济原则) 动改法(3)流程程序法流程法(4)5X5WIH(5X5何法) 五五法(5)人机配合法(多动作法) 人机法(6)双手操作法双手法(7)工作抽查法抽查法三、七大手法的用途名称用途如何避免做错事情,使工作第一次就做好的精神能够具(1)防呆法体实现。
广东逸华企业管理顾问改善人体动作的方式,减少疲劳使工作更为舒适、更有(2)动改法效率,不要蛮干。
(3)流程法研究探讨牵涉到几个不同工作站或地点之流动关系,藉以发掘出可资改善的地方。
(4)五五法借着质问的技巧来发掘出改善的构想。
研究探讨操作人员与机器工作的过程,藉以掘出可资改(5)人机法善的地方。
研究人体双手在工作时的过程,藉以发掘出可资改善的(6)双手法地方。
(7)抽查法借着抽样观察的方法能很迅速有效地了解问题的真象。
四、改善(IE)七大手法与品管(QC)七大手法之差别“品管(QC)七手法”较着重于对问题的解析与重点的选择,但对如何加以改善则较少可应用。
“改善(IE)七手法”较着重于客观详尽了解问题之现象,以及改善方法的应用,以期达到改善的目标。
有了“改善(IE)七手法”正可弥补品管(QC)手法的缺陷而达到相辅相成之效果,使得改善的效果更为落实也更容易实现。
同时最重要的是改善(IE)七手法亦可单独使用,因其本身具有解析、发掘问题的技巧之故。
IE常用手法分析

IE 手法介绍与应用技能一.IE 手法介绍(一) 工时法:定义:教人如何利用时间,时间分析,改善不良的工时方法。
(二) 5*5法定义:又称质疑创意法。
借着质问的技巧来发掘出改善的构想。
(三) 搬运法:定义:对象“取,放,方向变更,地点变化,安装”移动的方法。
(四) 布置法:定义:即日常所谈的layout ,将人,机,物有系统的安排或规划。
(五) 改善IE 基本ECCS 法:定义:Eliminate 排除combine 结合 Change 更换 Simplify 精简 (六) 动改法:定义:改善人体动作方式,减少动作的疲皮,不变干。
(七) 双手法:定义:研究人体双手在工作时的过程,探讨使用身体部份动作距离,重量阻力,困难缺失的分析调整。
(八) 人机法:定义:研究操作人员与机器工作的过程,探讨人等机或机等人的互动情形,作分析改善。
(九) 流程法:定义:探讨不同的工作站或整条Line 流程之“人,机物”,动线顺畅之探讨。
(十) 抽查法:定义:借着抽样观察的方法,了解作业缺乏的真象,以寻求改善空间。
(十一) 防错法:定义:如何防止作业错误,养成一次做好的习惯。
成功的人找方法;失败的人找借口。
二:IE 与改善手法的应用内容范围分析1. 罗马不是一天造成的2. 条条道路通罗马,但最快的只有一条。
IE 人员必备的条件一. 身为IE 您是经营者的化身,公司的原动力。
二. 身为IE 者必须有强烈数据理念。
三. 身为IE 者必须了解物料特色,产口结构,产品的流程,产品查核的重点。
四. 身为IE 者必须了解设备的操作,模治具的作业,识图的能力,了解基本电路。
五. 身为IE 者必须具备改善能力,QC 技能,现场改善技能,创意手法。
六. 身为IE 者必须具备管理能力管理的四大笔循环,管理的五大机能。
七. 身为IE 者必须具备行政能力资源整合,数据分析,勾通协调,人际关系,会议运作,档案管理。
八. 身为IE 者必须了解公司基本机能制度,SIP ,SOP ,表现制度,流程制度。
IE七大手法 四 5×5WIH(5X5何法) 标杆精益
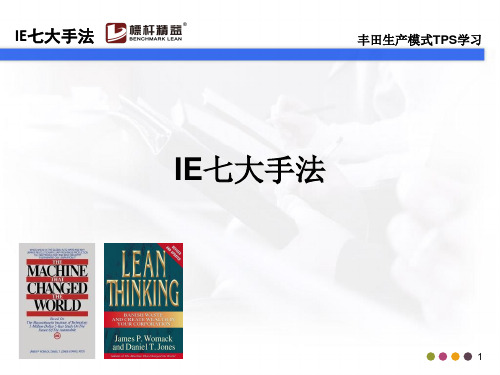
33
IE七大手法
丰田生产模式TPS学习
为协助大家产生创意,我们收集了一些实际上的改善创 意经验,归纳成十二种创意思考法则,都是经过很多改善专 家的丰富经验整理升华而得到的结晶,可提供给大家作为改 善的提示。
34
IE七大手法
丰田生产模式TPS学习
五五法应用12法则:创意思考法则
创意思考法则:产生创意的方法或技巧。这些方法、技巧可
学贵有疑,小疑则小进,大疑则大进;疑者, 觉悟之机也。
——陈献(明代学者)
18
IE七大手法
丰田生产模式TPS学习
质问的技巧:
质问的一般对象: ➢ 对“目的”(what)的质问; ➢ 对有关“人”(man)的方面的问题; ➢ 对“工作顺序”(when)的质问; ➢ 对“地点”(where)的质疑。
19
只要有问题存在,就可以运用5W1H去发掘问题的根本原 因(n次因)。
10
IE七大手法
丰田生产模式TPS学习
五五法实例:黎叔家的电视
话说在黎叔的家人在看电视节目兴运现场实况转播,正 看得津津有味,浑然忘我的时候,突然电视机坏了,没办法 只好请了维修中心的人来修理,维修人员检查了半天,终于 发现原来毛病是有一个电子零件 —— 电阻坏了。于是维修 人员就拿了一个新的电阻换上,黎叔很高兴他们一家人又可 以享受看电视的乐趣。
27
IE七大手法
丰田生产模式TPS学习
质问的技巧:对“工作顺序”(when)的质问
变更时间的顺序,包括操作发生时刻、时期、耗费时间, 是不是可以启发改善的头绪?一般有以下的质问方式:
➢ 在何时做的? ➢ 为何要在当时做? ➢ 改在别的时候做是否更有利? ➢ 在何时做最好?何时要完成?需要几天才算合理? ➢ 何时最切时宜?将来有何转变?等等。 这一质问的目的是在寻求可能的“合并”,“重组/变更” 的改善方向。
IE七大手法
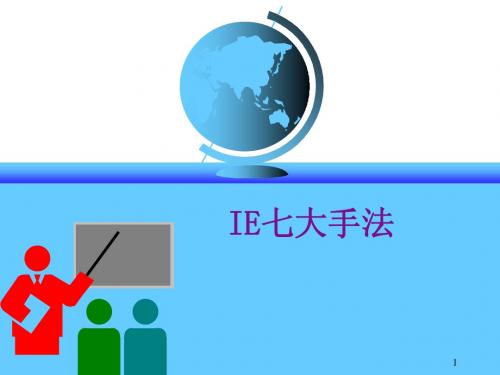
IE手法—工作简化的 IE手法—工作简化的循环 手法 简化
6
有效实施
「工作简化」
实际 利益
机种——增加生产 机种——增加生产 ——增加生 降低成本 个人——工时缩短 ——工时缩 个人——工时缩短 收益增加
管理上 收获
机种-提高工作 机种- 情绪 聪明才智 个人-聪明才智 有发展机会
提高 工作效率
IE七大手法——防 IE七大手法——防错法 七大手法——
IE七大手法 IE七大手法
1
前言
1Hale Waihona Puke 质量代表了一个国家的科学技术、生产水平、管理水平和文 化水平。 产品质量的提高,意味着经济效益的提高。当今世界经济的发 展正经历着由数量型增长向质量型增长的转变,市场竞争也由价格 竞争为主转向质量竞争为主。 几乎所有企业都希望以最小的投入(INPUT)得到最大的产出 (OUTPUT),从而获得得最大的利润。那么如何在品质保证的基础上, 使企业获得更好的效益呢?只有降低成本和提高企业的生产力,把 这些“投入”做一个最有效的组合,从而达到品质稳定、效率高、 交期准、浪费少、成本低,这也是IE工程师的职责所在。
1。意义 防错法又称防愚法,其意为防止愚笨的人做错事的方法。 狭义: 如何设计一个东西(一套方法),使错误绝不会发生。 广义: 如何设计一个东西(一套方法),而使错误发生的机会减至最低的程度。 因此,更具体的说”防错法”是: 1>。 具有即使有人为疏忽也不会发生错误的构造 2>。 具有外行人来做也不会做错的构造 3>。 具有不管是谁或在何时工作能不出差错的构造 2。功用 1>。 积极: 使任何的错误,绝不会发生。 2>。 消极: 使错误发生的机会减至最低程度。 3。应用范围 任何工作无论是在机械操作、产品使用上等皆可应用到。 —不需要注意力。 —不需要经验与直觉。
IE精益生产的七大手法
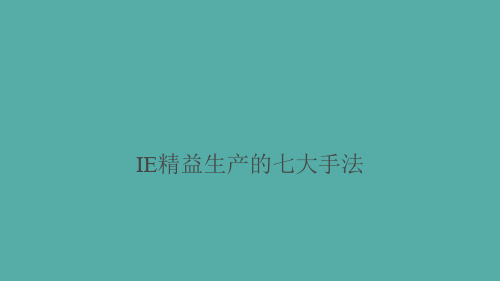
IE精益生产的七大手法
前言
1
质量代表了一个国家的科学技术、生产水平、管理水平和文化 水平.
产品质量的提高,意味着经济效益的提高.当今世界经济的发展正 经历着由数量型增长向质量型增长的转变,市场竟争也由人格竟争 为主转向质量竟争为主.
而所有企业的目的均系希望以最小的投入(INPUT)得到最大的产 出(OUTPUT),以致独得最大的效益.那么如何在质量保证的基础上, 使企业独得最大的效益呢?只有降低成本和提高企业的生产力,把 这些“投入”做最有效的组合,以达到质量稳定、效率高、交期准、 浪费少、成本低.这就是近代工业界工业工程(IE)所要做
IE七大手法之四 — 五五法
17
1.手法名称: 5 * 5W 1H法;又称5 * 5何法;又称质疑创意法;简称五五法.
2.目的: 学习本手法的目的是在:
熟悉有系统的质问的技巧,以协助吾人发掘出问题的真正 根源所在以及可能的创造改善途径. 3.名词释义 3.1 基本观念 * 头脑就像降落伞,○○○只有在开放的情况下才工作○○○. * 工作改善最大的阻碍,并不在于技术不足,而是在于一个人的想法~当他觉得是以最好的方 法在工作着,并且以为满足. * 当您认为工作已无法改善了,那就代表您已落伍了,虽然您是专家,拥有高深的学识. * 一个虽没有多大学识的人,只要他认为工作仍有改善的可能,那么他就比您更 适合这工作.
工业工程(IE)七大手法

IE七大手法之一 — 防呆法
9>. 警告原理: 如有不正常的現象發生,能以聲光或其他方式顯示出各種“警 告”的訊號,以避免錯誤即將發生.
10>. 緩和原理: 以藉各種方法來減少錯誤發生后所造成的損害,雖然不能完 全排除錯誤的發生,但 是可以降低其損害的程度.
EXL:
1.主板包装时加保利龍或紙板以減少產品在搬運中之碰傷.(緩和原理) 2.設立多層之檢查方法,考試后檢查一次看看,有沒有犯錯的地方.(保險原理) 3.自動消防洒水系統,火災發生了開始自動洒水滅火.(警告原理) 4.汽車之安全帶,騎機車戴安全帽.(保險原理) 5.筆放在桌上老是給別人不經意中拿走,怎麼辦呢?貼上姓名條或加條繩子固定 在桌上.(隔離原理、警告原理、緩和原理) 6.在工廠使用SFC自動控制系統(自動原理、警告原理)
2>. 具有外行人來做也不會做錯的構造
—不需要經驗與直覺.
3>. 具有不管是誰或在何時工作能不出差錯的構造 —不需要專門知識與高度 的技能.
2.應用範圍
任何工作無論是在機械操作、產品使用上,以及文書處理等皆可應用到.
工业工程(IE)七大手法
IE七大手法之一 — 防呆法
3.基本原則 在進行”防呆法”時,有以下四原則可供參考:
工业工程(IE)七大手法
2020/11/11
工业工程(IE)七大手法
前言
質量代表了一個國家的科學技術、生產水平、管理水平和文 化水平.
產品質量的提高,意味著經濟效益的提高.當今世界經濟的發 展正經歷著由數量型增長向質量型增長的轉變,市場竟爭也由人格 竟爭為主轉向質量竟爭為主.
而所有企業的目的均系希望以最小的投入(INPUT)得到最大的 產出(OUTPUT),以致獨得最大的效益.那麼如何在品質保證的基礎 上,使企業獨得最大的效益呢?只有降低成本和提高企業的生產力, 把這些“投入”做最有效的組合,以達到品質穩定、效率高、交期 準、浪費少、成本低.這就是近代工業界工業工程(IE)所要做
现场改善培训IE七大手法
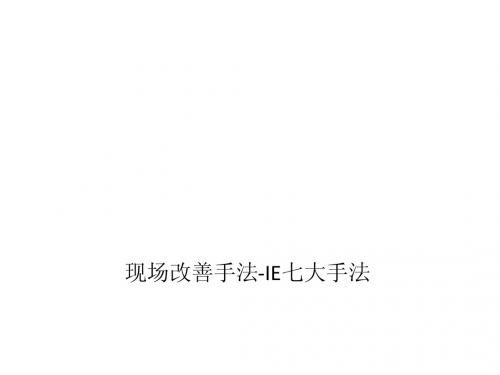
方.
6.流程法 可资改善的地方.
7.抽查法
借着抽样观察的方法能很迅速有效地了解问题的真象.
IE七大手法-防错法
错误vs后果
错误 后果
将柴油加入汽油箱 撞红灯
or
忘记拔掉电熨斗的插头
将原件放进了复印机的进纸处并正面冲下
IE七大手法-防错法
最常见的错误
01、漏掉某个作业步骤。 02、作业失误。 03、工件设置错误。 04、缺件。 05、用错部品 06、工件加工错误。 07、误操作。 08、调整失误。 09、设备参数设置不当。 10、工装夹具准备不当。
底盘的 凹槽
底盘的 凹槽
标签
Model T6 AC 110V 10 W
标签
Model T6 AC 110V 10 W
IE七大手法-防错法
防错范例设计
例 :某产品需安装铭牌,且要求安装方向必 须文字向上,但安装工人经常将铭牌装倒。
例:
固定铭牌的小轴的中心被移离中 心,使得它不能装倒。由于装倒 产生的错误被消除了。 重新设计为非对称意味着修订或修 改部件、工具或夹具的功能或外观 使相反面不再相同。用这种方法它 们不再会错误的互换,消除由不适 当的方向或布置带来的错误。
1. 方法研究 2. 作业测定(直接劳动) 3. 奖励工资制度 4. 工厂布置 5. 表格设计 6. 物料搬运 7. 信息系统开发 8. 成本与利润 9. 作业测定(间接劳动) 10.物料搬运设备选用 11.组织研究
基础IE改善手法
工序程序图
程序分析
流程程序图 线路图
方 法 研 究 工 作 研 究
两手一起作业才能 启动机器,避免了 手被压伤的可能。
IE七大手法-防错法
十大应用原理
IE七大手法
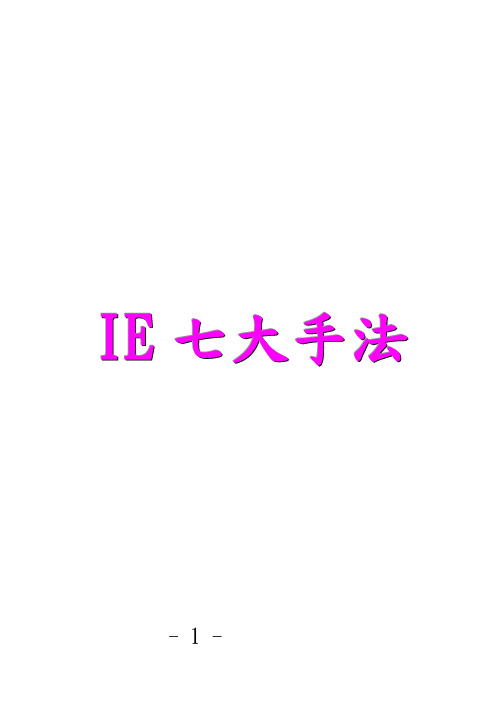
I E七大手法- 1 -- 2 -I E七大手法----現場管理實踐I n d u s t r i a l E n g i n e e r i n g工業工程—與現場改善I E是一門應用科學,它兼有管理及技朮和知識領域,將傳統的工程技朮融合於現代的科學管理技巧之中,以設計改善,設定,人,材料,設備等系統的結合.為了明示,預測,評价該系統所產生的結果,而使用工學分析或設計原理與技法,並融合數學,自然科學,社會科學等專門知識與經驗,---運用I E手法,能夠有效地提高生產及工作效率,降低成本,使每一個生產要素的作業都發揮到极限,它是优秀管理人員必備技能之一.- 3 -對I E 的認識IE 是指通過設計,改善和設定一套,人,機,物,法的工作系統,以求得更高生產力的專門技朮.上面所提到的“設計”是指制訂新的系統;“改善”是指把原有的系統修改得更完美; “設定”是指將設計或改善之系統,並能穩 固的發揮.I E既是一門改善技朮,又是一門有關人的行動方式技朮,更是一門科學的管理技朮之一.I E七大手法---現場管理實踐★流程分析法★動作分析法- 4 -- 5 -★動作經濟原則 ★時間研究 ★工作抽查法 ★人機配置法 ★工作簡化法 ★ IE 七大手法(4).xls流程分析法:1.工序分析:1-1.工序分析的含義:- 6 -工序分析是指:對流程各站的作業進行觀察,調查,甚至分解其內容,用專門的記號將作業內容,順序等畫成圖表,然后加以評价,以謀求工序的綜合性,根本性的改善手法.1-2.工序分析的種類:1.制品分析是指:以材料,制品等生產對象在生產和檢查過程中,所發生的變化為中心進行的分析;2.作業人員分析是指:以作業人員施予制品等生產對象的動作為中心進行的分析.3.組合作業分析是指:關於作業人員與機械或者是多個作業人員共同作業時,彼此之間的相互關系如何?以此為中心進行分析.- 7 -1-3.工序分析的目的----現場管理實踐1.熟悉各工序的狀況;2.把握各工序流程的順序,闡明工序的前后關系;3.知道各工序的大致時間,工序的平衡狀態如何;4.找出流程,白干的工序;5.找出工時過大,有潛在問題的工序;6.找出停滯等待空閑的工時;1-4.工序分析時應持有的態度1.對各流程工序方法,都持懷疑的態度;2.對各種現象都養成究明原因的習慣3.時常邀請相關人員出謀划策.- 8 -1-5.流程工序分析后的基本改善方法1.排除法:從另外一個高的角度來看,就能發現無用的作業;2.結合法:將類似的作業一起分析,具有不可小窺的作用;3.交換法:改變作業順序,替換作業人員4.精減法:削減作業的次數,距離.1-6.流程.工序分析用的各種,通用記號(符號)有\ 助於IE人員對各工序,分析的簡單,快速,速短,分析時間.- 9 -- 10 -▽停滯只有時間發生變化,無謂的等待,法定上認可必須經過制度表★△單品的貯存★▽為部件制品的貯存★▼為工序間的停滯★為加工中一時的停滯- 11 -- 12 -IE七大手法(9).xls- 13 -IE七大手法(10).xls- 14 -流程分析法:1-8.工序分析實戰時的注意事項:1.目標明確,不要弄錯對象,是以作業人員為中心,還是以制品為中心,一開始就要明確下來.2.確定進行分析,為了取得改善成果,先要明確分析的目的,如果分析目的不明確,自然就不會有改善方案出來.3.確定分析范圍,以免產生分析遺漏,范圍不確定,要么分析過頭,產生混亂,要么分析不夠,產生遺漏.4.在現場中與作業人員一起思考和分析,自己一個人分析,不與實際作業,必然會產生,疏漏和錯誤,听取作業人員的意見是分析中不可缺少的一環,絕不可一意孤行.5.工序流程在分析過程中就想好,改善方案,與其等到分析結果出來以后,再來考慮改善方案,不如邊分析邊想改善方案,提高工作效率.6.考慮改善方案時,首先要考慮工序整体的改善方案.- 15 -IE七大手法之二二.動作分析法------方法研究2-1.動作分析的含義動作分析又是方法研究發展而來,其目的是追求最完善最有效率的生產系統及工作方法,並加以確定.按作業人員的動作順序觀察其動作方法,用記號將手,眼睛,身体或其他部分的動作記錄下來,作成圖表來分析動作的好坏及尋找改善著眼點的方法.2-2.動作分析的種類1.目視觀察的方法.直接觀察作業人員的作業狀態並記錄下來,主要有兩手作業分析,基本動作分析等兩種.A.兩手作業分析:觀察作業,關聯地把握住兩手動作的順序,動法,用作業,移動,保持,等待,記號.對各動作加以分類和圖表化,找出動作順序,動法中的問題點,以及單手等待,白干,蠻干的地方,加以改善的方法.- 16 -B.基本動作分析:觀察手,腳的動作,以及眼睛,頭腦的轉動,將動作的順序,動法與兩手,眼睛相關聯起來,詳細分析,用基本動作記號對各動作加以分類,找出動作順序,及動法中的問題點,以及單手等待,白干,蠻干的地方,最終加以改善的方法.2.錄像觀察的方法:將作業狀態記錄在膠片或錄像帶上,然后播放出來,進行分析,主要有高速攝影,普通攝影,低速攝影,VTR(磁帶式錄像機)等四種.A.錄像觀察主要是用在無法直接,目視觀察分析動作的項目上,如作業場所大,又是多人共同作業或是循環周期較長,或者是不規則的作業等.B.錄像觀察不僅能用在動作分析上,還能在材料,制品流程,機械運作搬運,和布局的改善上廣泛運用.C.讓相關人員參與觀看,認為有問題的地方反復重複播放,並將問題解決為止.- 17 -IE七大手法動作分析法----方法研究3.PTS(Predetermine Time Searched) 法此法,並非直接求出作業時間,而是將作業分解成數個基本細小動作,然后從<<標准動作時間表>>中把各個相同動作的時間值找出,所有動作時間之和就構成標准作業時間,這種方法稱之為PTS法.—標准動作時間法IE七大手法動作分析法-----方法研究方法研究分析技巧- 19 -☆:工作抽樣及PTS雖是作業測定的分析手法,但同樣使用在方法研究的手法中.IE七大手法動作分析法----方法研究方法研究的實施步驟及目的.1.找出動作上的問題點,降低作業疲勞,提高作業效率2.設定最佳動作的順序,方法,以及謀求身体相關部分同時動作.3.設定最适合的夾具,治具以及動作范圍內的最佳布局4.改善動作的順序和方法,以決定最佳標准作業方法- 20 -5.利用現有的資料整理出問題點,並把握原因.6.將找出的問題,使用I E的技巧來加以直接觀察,並作成數据分析7.用記號圖表,記錄動作之后,對動作順序的說明變得容易進行.IE七大手法(17).xlsIE七大手法(18).xlsIE七大手法(19).xlsIE七大手法-----現場管理實踐動作分析實踐時注意:1.選定分析作業對象,要啟代表性,對整個流程有影響.2.選擇與作業相适合的手法分析3.選定與分析手法相適合的作業人員- 21 -4.用既定記號和正確的方法,進行記錄和分析5.從各種角度研究分析結果,並找出改善方案IE七大手法-------現場管理實踐三.動作經濟原則☆經濟動作分析- 22 -動作經濟原則是指:為了追求最佳的作業動作,使作業人員花費最小限度的時間及作業之疲勞,就能達到最大限度的效率,並且依据這些基本原則,誰都可以簡單輕松地應用工作.動作經濟原則有:1.動作能量活用原則2.動作量節約原則3.動作方法改善原則經濟動作應做到:1.減少作業的動作次數☆.不是為了達到作業目的的動作☆.一些使動作有延遲傾向的,可以去除的輔助動作☆.非作業狀態的動作多余的動作,不但浪費時間及空間,更會消耗体力2.謀求同時兩手作業3. 縮短作業動作距離4.作業動作應簡單,輕松IE七大手法-----現場管理實踐- 23 -動作經濟原則★動作經濟原則的三要素1.動作方法2.作業場所3.夾具,機器- 24 -- 25 -IE七大手法-----現場管理實踐二.作業測定—時間研究為了達成某一作業目的,以具体的時間值為尺度,對作業效率進行評价的分析手法.适過時間的研究運用,工程分析,作業簡化,動作研究,動作經濟原則,按照作業的順序,正確求出實際作業所花費的時間並找出作業上的問題點的方法.<一>時間,研究的准備要想時間研究對作業測定能得到效果,對於時間進行研究之前,對下列事項應先予了解及時准備1.工廠的工場布置方法2.產品的制程,分階狀況- 26 -3.各工序的作業方法4.材料,零件的供應品質,穩定狀況5.人員流動狀況對以上5項先做了解,尤其管理制度不佳的工廠應針對問題進行改善,再加上后的工作准備.時間研究才有效果,才能研究作出真正的標准工時6.時間研究方法及用具的決定;7.時間研究的觀測方法;8.記錄及整理9.改善項目之提出10.制訂標准時間的方法<二>時間測定工具-----馬表法(S t o p W a t c h)一般做作業測定大致分為,直接法和間接法,直接法,有馬表法,攝相法,間接法,有PTS,WF,MTM等,其中,馬表法應用最為普及馬表法是運用馬表“直接”測定作業方法繼續而直接的觀測作業,對稍有IE基礎的工程人員利用IE的作業觀念及手法,是容易發現“不合理”的作業.從而進行改善.但是對於短時間的作業或作業內容,不固定的作業就不- 27 -太適用.馬表一般分為機械式和電子液晶式兩種馬表的最大單位一般用“分”1/100分計及1/60分計兩種.1/100分為1DM 即1分鐘=100DM用秒表換算可用如下公式:例38秒=38秒÷60秒=0.63分等於63DM用來測定時間的秒表多為十進位制需要進行換算,換算關系如下圖所示:<三>時間測定的方法及分析種類:1.重複作業的時間分析,單元作業時間分析將重複作業中比較有規則的作業,事先分成若干個單元- 28 -作業,然后用秒表逐一測出其時間,最終計算出每個作業的平均時間的方法,一般的時間分析多採用這種方法T1+T2+T3+T N = T1W1+W2+W3+W N WN2.非重複性,作業的時間分析---單位作業時間分析一些不重複,缺乏規則的作業,可事先將其划分成若干個獨立的單位,然后用秒表測出每個單位的作業時間的方法.以上兩種為秒表測定法3.簡易的時間分析:在有規則的重複作業中,先求出“多個時間里完成了多少個”“完成多少個花費了多少個時間”然后計算出每一個的大致作業時間許多企業,工廠因客觀條件的限制大都用該種方法進行時間分析.4.膠片分析(動作記錄分析)V T R分析用攝相將作業記錄以錄象帶上,然后播放出來,精測其作業時間,由於具有重複播放和一目了然等眾多優點,現在使用該方法的人越來越多.<四>時間分析的目的:- 29 -1.用於尋找作業上的問題點A.找出高於必需程度的過長作業時間,以及作業中白干的時間,將其改善成效率高的作業方法B.調查作業時間的波動程度,改善作業方法,使作業時間,波動時間小,並讓作業時間標准化.2.用於比較兩個以上作業方法的優劣與否A.同一結果但不同的作業方法的比較,B.作業改善前后比較,C.不同作業人員,相同作業方法比較D.把握作業人員的熟練程度3.用於作業標准時間的設定,作業標准時間的設定離不開時間分析.<五>時間分析實踐時,注意事項1.向被測試定者充分說明時間測定的目的,謀求得到理解和配合;2.測定作業時間要2-3次,才能測出該作業的真正時間,3.測定好的時間值不要隨意修改,4.選定與分析的目標,<六>運作分析- 30 -運作分析是指:定量把握人員設備的運作狀態對非運作狀態的原因進行追查的手法.運作分析的種類:1.連續觀測法觀測者,緊緊跟隨被測對象左右,觀測一整天或連續多天2.瞬間觀測法非連續觀測,每個工作日對被觀測者,觀測3-4次.3.其他方法:通過記錄儀或錄像設備,錄下運作情況,然后進行分析,通過對每個時間段的產出計算或者每個生產目的產量計算,也可求得運作效率,4.運作分析的作用.A.需要找出人員設備運作中白干的部份,加以改善時;B.需要把握人員和機器非作的時間和原因時;C.在制定生產計划設定价格,確定作業人數,確定設備數,確定標准時間等過程,需要把握運作效率時5.運作分析在作業管理中的作用.A.可抓住作業改善的重點作業人員的主体作業和機器的運作,才是創造价值的要素,除此- 31 -之外許多要素都會阻礙生產的進行,有必要加以排除和改善.B.設定標准作業時間:設定標准時間是由“真正時間”和“盈余時間”兩個方面構成,真正時間是主体作業所需要的時間,可以通過測定得知,而盈余時間是各種停滯,准備,等待的總和,具有偶發無規律等特點,較難直接測取時間值,通常給於“寬放率”C.把握作業,負荷.在產量達到一定限度時,人和機器承受多大的負荷可客觀地計量把握.IE七大手法(30).xls標准時間設定作業工時越短,付出的人事成本越低,但是標准工時的確立并不是以最快的某個人為基准,需要綜合考慮.通常所提的工時----就是完成一項工作所花費的時間,標准工時-----是指在既定作業條件下,用標准作業方法完成單件作業對象所花費的時間它是現場日常管理所必不可缺的項目之一即定作業條件是指以下几個方面:1.使用即定的設備2.使用即定的作業環境- 32 -3.作業人員對該項作業有一定的熟練成度4.作業人員的平均作業水平,都能達到.A.標准時間設定評价作業效率時,即不能“以快制慢”,也不能以“以快搶慢”只有先確定標准工時后,才能進行評价.標准工時=主作業時間+准備時間一.標准工時的設定:1.秒表設定法;2.設定標准工時法3.采樣法4.標准資料法5.經驗估算法二.標准工時設定的目的:1.為了比較改善作業方法,或選擇更好的作業方法時;- 33 -2.為了平衡不同小組相互之間的作業工時;3.能制定生產計划提供必要的依据;4.工時,費用計算需要標准工時=主作業時間+准備時間=真正時間+盈余時間=雙測時間x評价余數+盈余時間----------主作業時間x評比系數+寬放率A.評价系數是指:----因為各種因素影響,被測定作業人員從事該項作業時,與基准速度相比較,該作業人員所能達到的熟練程度. 可用下式:評价系數=基准速度÷實際作業速度x100%影響實際作業速度的因素有很多,在測定實際作業時,應如何確認該作業速度接近基准速度是一個重要的環節,測定人員應有較丰富的工作經驗和技巧,才能得也合理的數据. 基准速度是指:例如:用10秒鐘將4粒螺絲,分別用電批鎖在邊長為150mm的產品的4個角上,此時的速度為手部的作業基准速度為手部的作業基准速度.- 34 -三.確定標准工時應考慮以下因素:1.作業人員的熟練程度2.設備夾具,治具的動作情況3.准備時間如何(事前准備,中途准備,材料准備)4.標准作業方法建立5.標准作業方法及制造條件變更后,標准工時示同步變更6.確定標准工時的人,要熟悉測定對策,作業方法和計算方法;7.整個生產均衡率的達成,考慮.生產均衡率的作業編成隨著生產流水線的大量應用,生產作業的要求和速度,對前后兩個工序的作業配合,要求也越來越高,對前后作業的工時要盡可能保持一至(或相近),如果一條流水線有多個作業工序,出現工時相差很遠速度跟不上,就會出現所謂的“瓶頸”或有的工序出現空閑等待整條流水線混亂,申此而生.生產線平衡分析是指:分析生產線中各工序(各站)的時間差異狀態,并將差異時間給予消除,使生產線保持順暢的方法.------線平衡分析的作用- 35 -1.可以提高人員機械設備的運作效率;2.可以謀求,省人,省力;3.可以謀求機械化和自動化;4.可以編短作業工時5.可以提高生產效率-------線平衡分析的适用場合1.為了縮短每個產品的作業工時;2.為了新產品進行投產的作業編成;3.生產量有變動時,為了決定適當人員;--------線平衡率(均衡率)計算方法線均衡率= 各工序(各站)真正工時*100%最長工時(各站中)*各工序數之和- 36 -。
精益生产之IE七大手法(PPT-53张)可修改全文

35
基本原则
(二)有关工作场所之布置环境之原则 1.工具物料应置 于固定处所
2.工具物料装置应依工序排列并置于近处.
22
二.动改法(动作改善法)
3.利用重力喂料,愈近愈佳.
4.利用重力坠送
23
二.动改法(动作改善法)
5.适当之照明
6.工作台椅高度应适当舒适
24
二.动改法(动作改善法)
基本原则
(三)有关于工具设备之原则 1.尽量以足踏/夹具替代手之工作
• 5W是指: WHERE 何处,在什么地方,在什么地方,~空间
•
WHEN 何时,在什么时候, ~时间
•
WHAT 何者,是什么东西/事~生产对象
•
WHO 何人,是什么人做/生产主体
•
WHY 为何,为什么如此
• 1H是指HOW如何,怎么做的
• 5×是五次,表示对问题的质疑不要只问一次而要多问几次,不是刚好只问5次可多亦可 少,类似我们的“打破砂锅问到底”之精神.
(6)双手法
研究人体双手在工作进行的过程,藉以发掘出可资改善的地方.
(7)抽查法
借着抽样观察的方法能很迅速有效地了解问题的真象
3
那些工作需要改善 ?!
下面的几个因素,可以做为找出那些工作需要改善的啟示.
成本 工作量 永续性 人数 熟练度 进度 工作品质 浪費 危险性 疲劳 环境
金钱,工作时间以及机器使用上花费最多的工作 工作量最多的工作 需要持续很久的工作 有很多员工从事的工作 共大把要高熟练的人担任的工作改由低熟度的 未能按预定的进行而需要加班的工作 未能达到所要求品质基准的工作 劳力度或时间浪费较多的工作 发生很多灾害的工作,或者容易发生灾害的工作 肉体上或者精神上很容易疲劳的工作 在灰尘,噪音,恶臭,气温等恶劣环境下的工作
IE七大手法介绍
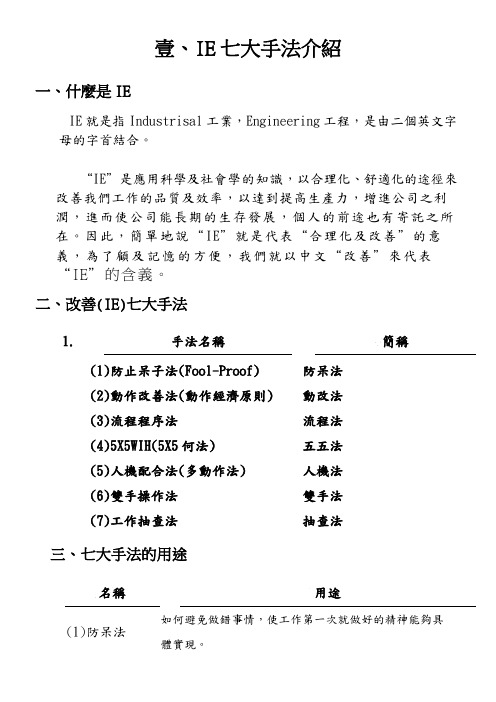
壹、IE七大手法介紹一、什麼是IEIE就是指Industrisal工業,Engineering工程,是由二個英文字母的字首結合。
“IE”是應用科學及社會學的知識,以合理化、舒適化的途徑來改善我們工作的品質及效率,以達到提高生產力,增進公司之利潤,進而使公司能長期的生存發展,個人的前途也有寄託之所在。
因此,簡單地說“IE”就是代表“合理化及改善”的意義,為了顧及記憶的方便,我們就以中文“改善”來代表“IE”的含義。
二、改善(IE)七大手法1. 手法名稱簡稱(1)防止呆子法(Fool-Proof) 防呆法(2)動作改善法(動作經濟原則) 動改法(3)流程程序法流程法(4)5X5WIH(5X5何法) 五五法(5)人機配合法(多動作法) 人機法(6)雙手操作法雙手法(7)工作抽查法抽查法三、七大手法的用途名稱用途如何避免做錯事情,使工作第一次就做好的精神能夠具(1)防呆法體實現。
廣東逸華企業管理顧問有限公司改善人體動作的方式,減少疲勞使工作更為舒適、更有(2)動改法效率,不要蠻幹。
(3)流程法研究探討牽涉到幾個不同工作站或地點之流動關系,藉以發掘出可資改善的地方。
(4)五五法藉著質問的技巧來發掘出改善的構想。
研究探討操作人員與機器工作的過程,藉以掘出可資改(5)人機法善的地方。
研究人體雙手在工作時的過程,藉以發掘出可資改善的(6)雙手法地方。
(7)抽查法藉著抽樣觀察的方法能很迅速有效地瞭解問題的真象。
四、改善(IE)七大手法與品管(QC)七大手法之差別“品管(QC)七手法”較著重於對問題的分析與重點的選擇,但對如何加以改善則較少可應用。
“改善(IE)七手法”較著重於客觀詳盡瞭解問題之現象,以及改善方法的應用,以期達到改善的目標。
有了“改善(IE)七手法”正可彌補品管(QC)手法的缺陷而達到相輔相成之效果,使得改善的效果更為落實也更容易實現。
同時最重要的是改善(IE)七手法亦可單獨使用,因其本身具有分析、發掘問題的技巧之故。
ie七大手法
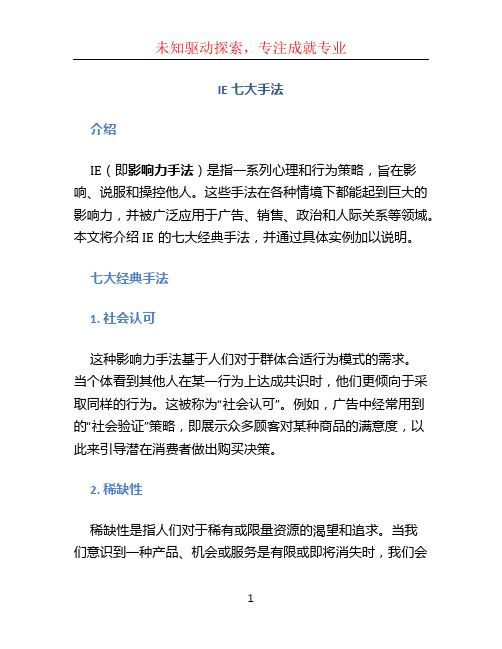
IE七大手法介绍IE(即影响力手法)是指一系列心理和行为策略,旨在影响、说服和操控他人。
这些手法在各种情境下都能起到巨大的影响力,并被广泛应用于广告、销售、政治和人际关系等领域。
本文将介绍IE的七大经典手法,并通过具体实例加以说明。
七大经典手法1. 社会认可这种影响力手法基于人们对于群体合适行为模式的需求。
当个体看到其他人在某一行为上达成共识时,他们更倾向于采取同样的行为。
这被称为“社会认可”。
例如,广告中经常用到的“社会验证”策略,即展示众多顾客对某种商品的满意度,以此来引导潜在消费者做出购买决策。
2. 稀缺性稀缺性是指人们对于稀有或限量资源的渴望和追求。
当我们意识到一种产品、机会或服务是有限或即将消失时,我们会更倾向于积极行动,以免错失机会。
这个手法常被用于促销、限时优惠和拍卖等营销策略中。
3. 权威性权威性手法利用人们对于权威人士或领域专家的信任和尊重。
通过引用权威人士的观点、发布专家见解以及提供专业认证等方式,来增加自己的说服力。
例如,当一位知名专家背书某种产品时,消费者通常更倾向于购买。
4. 反对手法反对手法通过制造争议、反驳对方观点或激发争论,来引起人们的关注和兴趣。
这种手法常在辩论、政治竞选和广告中使用。
通过对当前观点的质疑和突出问题的对立面,来吸引更多人参与讨论并增加自身影响力。
5. 一致性根据心理学家罗伯特·西奥迪尼(Robert Cialdini)的研究,人们倾向于保持一致的行为和态度。
一旦我们在某个问题上表达了某种观点或做出了某种承诺,我们会想要保持一致,避免前后矛盾。
这个手法可通过利用事先获得的小承诺或以一种与个人价值观相契合的方式来说服他人。
6. 归因归因是指人们倾向于将结果归因于特定的原因或因素。
通过强调某种因果关系来解释成功或失败的原因,可以影响他人对于某件事情的看法和态度。
这种手法常被用于推销产品或推动特定行为。
7. 亲和力亲和力手法基于人们对于与其有着共同特点、兴趣或目标的人们建立关系的需求。
IE四大手法

IE四大手法
IE四大手法
一.IE的定义:
IE即工业工程,它利用自然科学、数学、社会科学,特别是工业技术的理论与方法,将人员、物料、信息、设备、能源等要素进行集成、规划、设计、改善、创新.为实现生产制造管理和服务系统的低成本、高效益的管理目标提供有利的技术支持。
换句话说:说是想各种办法消除浪费、降低成本、物尽其用、人尽其才,实现利润最大化的目标。
二.IE的四大手法
1.简化:即消除不必要的中间环节,如公司进行的扁平化,理在车间的组织方式为:课长---主任---组长----班长----作业员,信息的传循
逐级循增,往往会产生延误,误解,甚至面目全非,如果直接向课长
报告会省却很多时间且直接明确,得到及时的处理,对于生产线的作
业员来讲将单手改为双手或改为与脚配合都可使作业得到简化。
2.删除:将无实际意义的动作取消,这里讲一个做事的观念:“做对的事情”“将事情做对”“做事之前多问几个为什么”“怎样才能做好”。
3.合并:“将3个人的作业内容由两个人做”这时举例理解,由于一个工位的作业内容少,工时很短,将该作业转移至其它工位或其它几个
工位来做,称之为合并。
4.重组:将原有的作业顺序重新安排、布置,通常由于人员变动过大,由30~40人减至十几人或现有的作业顺序达不到预定的产量进行重组
以达到既规定的目的。
4IE经典管理手法
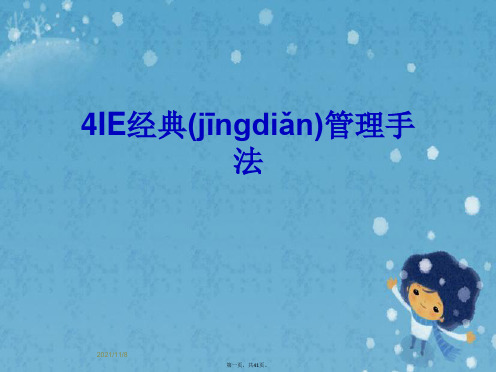
又称举措改善法,简称为〝动改措原那么
*举措温馨原那么
*举措简化原那么
此原那么以最少的劳力抵达最大的义务效果,其
原为吉尔博斯最先提出,后经研讨整理增删,其中以
巴恩斯将之补充完成。
2021/11/8
第七页,共41页。
IE七大(qī dà)手法之一——动改法
原那么1:两手同时末尾并同时终了举措
2021/11/8
第三页,共41页。
IE的来源(láiyuán)
早在1881年左右,泰勒就已具有工业工程的观念,首先建议 [时学研讨],而纪尔布雷斯夫妇那么为[工业研讨]的开创人。
直到1930年代他们的研讨才遭到群众的注重,而正式成为工 时学。
工时学是工业工程的范围中最基本的一局部(júbù),也是传统 工业工程的基本观念。
原那么2:除休息时间外,两手不应同时闲暇
原那么3:两臂的举措应对称反向中止
原那么4:尽可以以最低级举措义务
说明:
欲使举措迅速、轻松、容易、省力,只需从延伸
举措的距离,以及(yǐjí)添加举措消耗的体力方面着手。
因此,应选择级别最低的举措,添加举措的范围,
并使物料及工具可以接近手的举措范围内。
3.运用范围 任何义务无论是在机械操作、产品运用上,以及文书处置等皆可运用到。
2021/11/8
第十三页,共41页。
IE七大(qī dà)手法之二——防错法
6。运用原理
1>. 端根原理:将会构成错误的缘由从基本上扫除掉,运用不发作错误
2>. 保险原理:采用二个以上的举措必需共同或依序执行才干完成义务。
6>.隔离原理:籍分隔不同区域的方式,来一抵达维护某些地域,使不恩 能构成风险或错误的现象发作,隔离原理亦称维护原理。
基层主管培训教材-TWI(4 IE手法3)

物流改善著眼點
• NO. 著 眼 點
構
思
• 1 該搬運的目的為何?
※不能免掉嗎?
• 2 那是最適當搬運手段嗎?
※ 沒有別的方法嗎?
• 3 有沒有用最短距離搬運?
※變更工廠佈置會怎麼樣 ?
• 4 集中一起搬運。
※ Unit化?
• 5 能否減少作業次數?
※ 使用台車、料架?
• 6 能否避免空車搬運?
※變更搬運路線?
活性係數分析表
停滯階段活性係數的總合 平均活性係數=
停滯次數
平均活性係數= =
0+3+4+0+3+4+3+4+2+4 10
2710=2.7
活性係數檢討對策
平均活性係數 改善對策
不滿0.5
活用容器;手推車
0.51.3
活用動力搬運車;叉舉車
1.32.3
活用活用輸送帶;導入托車列車方式
2.3以上
由設備、方法等方面力求搬運工時節省
•
時間,可憑感覺摘記。
• (註)細小部分其頻率非常多時,亦可以記錄 次數(正字)
•
表示之。
停止時間觀測 單位別
規格別
觀測日
Cycle Time=
工程別
作業者
觀測者
加工部品
備 註 欄 ( 停 止 內 容 、 停 止 時 間 、 其 他)
作業指示
7.00
A-123 作業準備
4.00
檢查尺寸
0.75
材料裝配調整 正正正正 時間約0.05分 正正一
突計 間等 發畫 接待 停停 停停 止止 止止
非 正 常 停
止
IE七大手法在企业中的应用

IE七大手法在企业中的应用IE七大手法在企业中的应用(1)IE七大手法介绍众所周知,日本是一个国小、人多、资源缺乏的国家。
二次大战后,厂房、道路、桥梁都受到严重破坏,经济面临全面崩溃,全年1/3时间停产,加上600万日军和移民拥回而失业人数激坛。
再看今天的日本,面积不到38万平方公里,人口不过1亿多,但国民生产总值占世界国民生产总值的10%,据1980年的统计,日本国民的人均生产总值为1。
087万美元,居世界第二位。
为什么日本能在如此短的时间内崛起呢?当然有很多的原因,但有一点,我们必须得提出来,日本的IE应用对国家的经济可以说是起到了不可磨灭的作用,本专题就是在此情形下来研究IE—工业工程。
“IE”是应用科学及社会学的知识,以合理化、舒适化的途径来改善我们工作的品质及效率,以达到提高生产力,增进公司之利润,进而使公司能长期的生存发展,个人的前途也有寄托之所在。
第一部分、IE七大手法介绍一、什么是IEIE就是指Industrisal工业,Engineering工程,是由二个英文字母的前缀结合。
“IE”是应用科学及社会学的知识,以合理化、舒适化的途径来改善我们工作的品质及效率,以达到提高生产力,增进公司之利润,进而使公司能长期的生存发展,个人的前途也有寄托之所在。
因此,简单地说“IE”就是代表“合理化及改善”的意义,为了顾及记忆的方便,我们就以中文“改善”来代表“IE”的含义。
二、改善(IE)七大手法三、七大手法的用途四、改善(IE)七大手法与品管(QC)七大手法之差别“品管(QC)七手法”较着重于对问题的分析与重点的选择,但对如何加以改善则较少可应用。
“改善(IE)七手法”较着重于客观详尽了解问题之现象,以及改善方法的应用,以期达到改善的目标。
有了“改善(IE)七手法”正可弥补品管(QC)手法的缺陷而达到相辅相成之效果,使得改善的效果更为落实也更容易实现。
同时最重要的是改善(IE)七手法亦可单独使用,因其本身具有分析、发掘问题的技巧之故。
质量管理4M1E法

质量管理4M1E法什么是4M1E法?4M1E法指Man(人),Machine(机器),Material(物料),Method(方法),简称人、机、料、法,告诉我们工作中充分考虑人、机、事、物四个方面因素,通常还要包含1E:Environments (环境),故合称4M1E法。
也就是人们常说的:人、机、料、法、环现场管理五大要素。
现场管理五大要素(4M1E)分析所谓人(Man),就是指在现场的所有人员,包括主管、司机、生产员工、搬运工等一切存在的人。
现场中的人,班组长应当注意什么呢?首先应当了解自己的下属员工。
人,是生产管理中最大的难点,也是目前所有管理理论中讨论的重点,围绕这“人”的因素,各种不同的企业有不同的管理方法。
人的性格特点不一样,那么生产的进度,对待工作的态度,对产品质量的理解就不一样。
有的人温和,做事慢,仔细,对待事情认真;有的人性格急躁,做事只讲效率,缺乏质量,但工作效率高;有的人内向,有了困难不讲给组长听,对新知识,新事物不易接受;有的人性格外向,做事积极主动,但是好动,喜欢在工作场所讲闲话。
那么,作为他们的领导者,你就不能用同样的态度或方法去领导所有人。
应当区别对待(公平的前提下),对不同性格的人用不同的方法,使他们能“人尽其才”。
发掘性格特点的优势,削弱性格特点的劣势,就是要你能善于用人。
如何提高生产效率,就首先从现有的人员中去发掘,尽可能的发挥他们的特点,激发员工的工作热情,提高工作的积极性。
人力资源课程就是专门研究如何提高员工在单位时间内工效,如何激发员工的热情的一门科学。
简单的说,人员管理就是生产管理中最为复杂,最难理解和运用的一种形式。
机(Machine),就是指生产中所使用的设备、工具等辅助生产用具。
生产中,设备的是否正常运作,工具的好坏都是影响生产进度,产品质量的又一要素。
一个企业在发展,除了人的素质有所提高,企业外部形象在提升;公司内部的设备也在更新,。
为什么呢?好的设备能提高生产效率,提高产品质量。
- 1、下载文档前请自行甄别文档内容的完整性,平台不提供额外的编辑、内容补充、找答案等附加服务。
- 2、"仅部分预览"的文档,不可在线预览部分如存在完整性等问题,可反馈申请退款(可完整预览的文档不适用该条件!)。
- 3、如文档侵犯您的权益,请联系客服反馈,我们会尽快为您处理(人工客服工作时间:9:00-18:30)。
2020/6/19
15
IE七大手法之三——工序分析法
什么是工序分析
以工序为分析单位对对象物品(材料、半成品、产品、副材料等)
经过什么样的路径,按照发生的顺序分为加工、搬运、检查、停 滞、
存放,与各工序的条件(加工条件,经过时间,移动距离等)
一起进行分析,是现场分析方法中的一种。
4IE经典管理手法
IE的起源
早在1881年左右,泰勒就已具有工业工程的观念,首 先提倡[时学研究],而纪尔布雷斯夫妇则为[工业研究] 的创始人。
直到1930年代他们的研究才受到大众的重视,而正式 成为工时学。
工时学是工业工程的领域中最基本的一部分,也是传 统工业工程的基本观念。
2020/6/19
8>.层别原理:为避免将不同工作做错,而设法加以区别出来。
2020/6/19
14
IE七大手法之二——防错法
9>.警告原理:如有不正常的现象发生,能以声光或其它方式显示出各种 “警告”的讯号,以避免错误即将发生。
10>.缓和原理:以各种方法来减少错误发生后所造成的损害,虽然不能 完全排除错误的发生,但是可以降低起损害的程度。
生产线的均衡是非常重要的
2020/6/19
25
IE七大手法之四——生产线作业编成
组装生产线编成 一个员工在单位时间内 的工作量基本保持相同 作业的分工和组合较容易;
加工生产线的编成 同一设备在同一时间内能够 处理的对象为一个种类; 各台机械设备在单位时间内 的加工能力从开始就存在 不平衡 以机械设备为主体存在,人
变更; 搬运方式的系统化:探讨巡回运输方式; 缩短搬运时间、装载时间、周期;
2020/6/19
19
IE七大手法之三——工序分析法
优化检查工序保证质量、减少检验工序
就算增加检验工序,也不能提高产品质量 (作业方法、工具不完备,作业者不熟练、注意力不集中) 检查工序往哪里、用什么方法、怎样反馈?
减少滞留量、次数、时间
工序分析的目的
工序分类
缩短制造周期 改善生产工序
加工 搬运
改善布局
检查(数量/质量)
改善工序管理系统
停滞
存放
2020/6/19
16
IE七大手法之三——工序分析法
工序改善 目的:
2020/6/19
降低成本 提高生产率 材料损失德减少和质量保证 减少半成品 有效利用空间 提高安全等环境条件
7
IE七大手法之一——动改法
原则1:两手同时开始并同时结束动作 原则2:除休息时间外,两手不应同时空闲 原则3:两臂的动作应对称反向进行 原则4:尽可能以最低级动作工作 说明:
欲使动作迅速、轻松、容易、省力,只有从缩短 动作的距离,以及减少动作消耗的体力方面着手。
因此,应选择级别最低的动作,缩小动作的范围, 并使物料及工具可能靠近手的动作范围内。
推广的阻力
q在一些闭塞的企业中,企业领导的观念不够开放,不愿公开企业各方
面的问题,也不愿提供全的资料,没有资料工业工程师就无从下手解决 问题。
q守旧的观念,拒绝改变,因此工业工程师即无从施展所长。
q一件新事物要经过学习的过程,人们才能驾轻就熟地应用,而学习的
起步总是比较困难且成效不显著,因此人们即使费力些,也宁可继续使 用习惯了的旧方法、旧东西。
4>.相符原理:籍用检核是否相符合的动作,来防止错误的发生。
5>.顺序原理:避免工作之顺序或流程前后倒置,可依编号顺序排列,可 以减少或避免错误的发生。
6>.隔离原理:籍分隔不同区域的方式,来一达到保护某些地区,使不恩 能造成危险或错误的现象发生,隔离原理亦称保护原理。
7>.同一件工作,如需做二次以上,最好采用“复制”方式来达成,省时 有不错误。
EXL: 1.鸡蛋之隔层装运盒减少搬运途中的损伤。(缓和原理) 2.设立多层之检查方法,考虑后检查一次看看,有没有犯错的地方。(保险
原理)
3.自动消防洒水系统,火灾发生了开始自动洒水灭火。(自动原理) 4.汽车之安全带,骑机车戴安全帽。(保险原理) 5.加保利龙或纸板以减少产品在搬运途中之碰伤。(缓和原理) 6.原子笔放在桌上老是给别人不经意中拿走,怎么办呢?贴上姓名条或加条
2020/6/19
18
IE七大手法之三——工序分析法
产品设备作业内容的最佳化 在各工序上考虑最佳(低费用、高性能、自动化)设备; 简化(生手也容易做到)各工序上选定最佳的加工条件; 研讨减少搬运量及装载次数 减少搬运量:减少削、冲压等费用; 减少搬运次数:增加1次搬运量、装载次数、取消中间环节; 改善搬运方式:利用最有利的包装方法、容器、推车进行改善; 搬运距离、路线的合理化;直线化、圆形化、工序组合变更、布置
2020/6/19
6
IE七大手法之一——动改法
1.手法名称 又称动作改善法,简称为“动改法”,是: *省力动作原则 *省时动作原则 *动作舒适原则 *动作简化原则
此原则以最少的劳力达到最大的工作效果,其原为 吉尔博斯最先提出,后经研究整理增删,其中以巴恩 斯将之补充完成。
2020/6/19
对搬运
是否可以去掉搬运工序 是否可以改变布置,使搬运路线单一化或者缩短距离 改变搬运手段,换一下搬运工具会怎么样 把使用的托盘,箱子等改变一下会怎么样 改成利用重力会怎么样 搬运能力是否不足
2020/6/19
23
IE七大手法之三——工序分析法
改变停滞,储存的状态及数量会怎么样
减少批次等待数量,缩短停滞,储存的时间或者期限会怎么样
21
IE七大手法之三——工序分析法
对包装 把包装省略会怎么样 两重包装是否可以变更为单面包装 包装材料,包装箱等是否可以标准化
对材料 改变材质会怎么样:用普通钢、塑料等 改变材料的形状或者尺寸(长度、厚度)会怎么样 改变材料的切割方法是否可以提高数率 改变原料配合会怎么样,省略包装会怎么样
对检查 是否可以取消检查工作 改变检查位置会怎么样 改变检查方式或者设备、使用工具等会怎么样 改变部门负责方式、1个小组、集中方式等检查场所会怎么样
人的动作可分为下列五级:
2020/6/19
8
IE七大手法之一——动改法
级别
一
二
三
四
五
运动轴
指关节
手腕
肘
肩
身躯
人体运动 部份
动作范围
速度 体力消耗
手指
手指的长 度
1 最少
+手掌
手掌的大 小
2 少
+前臂
前臂的长 度
3 中
+上臂
上臂的长 度
4 多
+肩
上臂+ 身躯弯
曲 5 最多
动作力量
最弱
弱
中
强
最强
疲劳度
前端并梢重,手柄方便抓握。
2020/6/19
12
IE七大手法之二——防错法
1.意义 防错法又称防愚法,其义为防止愚笨的人作错事。也就是说,连愚笨的人也不
回做错事的设计方法。 狭义:如何设计一个东西(一套方法),使错误绝不会发生。 广义:如何设计一个东西(一套方法),而使错误发生的机会减至最低的程度。 因此,更具体的说“防错法”是: 1>.具有即使有人为疏忽也不会发生错误的构造 ——不需要注意力。 2>.具有外行人来做也不会做错的构造 ——不需要经验也直觉。 3>.具有不管水或在何时工作能不出差错的构造 ——不需要专门知识与高度的技能。 2.功用 1> .积极:使任何的错误,绝不会发生。 2>.消极:使错误发生的机会减少至最低程度。
速度适当,以一定的节拍规律进行; 速效手的动作范围,保持手部适当高低;物品的拜访按工艺顺序
放置; 结素开始第亿 动作在同一位置,首尾相接:
2020/6/19
10
IE七大手法之一——动改法
原则9:降低动作注意力 动作中的停顿、迟疑不只造成作业节奏的混乱,同时造成精神上的
疲劳。 可以采取如下方法:
对停滞 改变防锈,储存方式等,是否可以减少储存中的损失,磨损
是否可以实现真正的流水线作业化
使工序运动化,是否可以去掉搬运工序
搬运能力是否不足
2020/6/19
24
IE七大手法之四——生产线作业编成
生产线的定义
①投入~铲除间分割成负数的工序 ②各工序相对独立,同时作业 ③物品以一定的速度向成品方向移动
4
工业工程师
q 工厂中,每为专业工程师专司其职,谁来沟通不同的专业工程师 呢?
q 老板关心赚钱与产量,员工关心薪水也劳力的付出,那么谁来作 老板和员工的桥梁?
q 人人关心交货及质量,是否有人关心今天比昨天做得更好,明天 比今天走得又更好?如果有,那么这种改善的工作谁来做?
q 人人关心机器、物料、·······,谁来关心最忠言的[人]?如何使这些 人做得更舒服、做得更多、赚得更多,而且受到尊重?
3.应用范围 任何工作无论是在机械操作、产品使用上,以及文书处理等皆可应用到。
2020/6/19
13
IE七大手法之二——防错法
6。应用原理
1>. 端根原理:将会造成错误的原因从根本上排除掉,使用不发生错误
2>. 保险原理:采用二个以上的动作必须共同或依序执行才能完成工作。
3>. 自动原理:以各种光学、电学、力学、机构学、化学等原理来限制 某些动作的执行或不执行,意义避免错误之发生,目前这些自动开关非 常普通,非常简单的“自动化”之应用。
q 大家关心产量,关心总成本?
q 各个小单位都有本位主义,由谁来考虑整个工厂的最佳点?工业 工程师的座右铭:
Is always a better way /永远有个更好的方法!