高效磨削用砂轮地貌的优化设计研究
磨削技术论文:超高速磨削及其优势探析
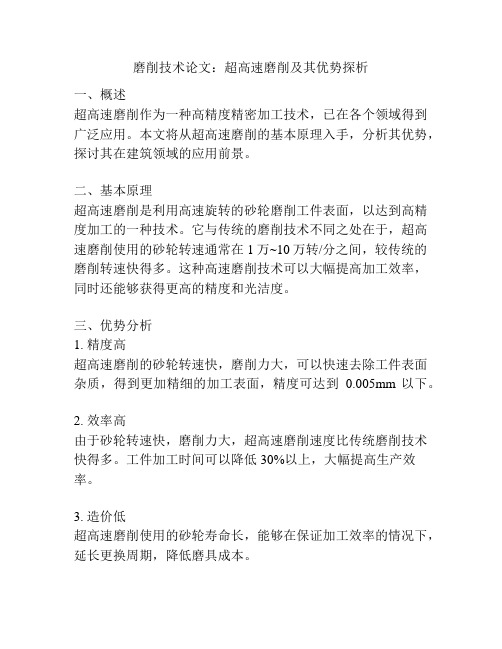
磨削技术论文:超高速磨削及其优势探析一、概述超高速磨削作为一种高精度精密加工技术,已在各个领域得到广泛应用。
本文将从超高速磨削的基本原理入手,分析其优势,探讨其在建筑领域的应用前景。
二、基本原理超高速磨削是利用高速旋转的砂轮磨削工件表面,以达到高精度加工的一种技术。
它与传统的磨削技术不同之处在于,超高速磨削使用的砂轮转速通常在1万~10万转/分之间,较传统的磨削转速快得多。
这种高速磨削技术可以大幅提高加工效率,同时还能够获得更高的精度和光洁度。
三、优势分析1. 精度高超高速磨削的砂轮转速快,磨削力大,可以快速去除工件表面杂质,得到更加精细的加工表面,精度可达到0.005mm以下。
2. 效率高由于砂轮转速快,磨削力大,超高速磨削速度比传统磨削技术快得多。
工件加工时间可以降低30%以上,大幅提高生产效率。
3. 造价低超高速磨削使用的砂轮寿命长,能够在保证加工效率的情况下,延长更换周期,降低磨具成本。
4. 应用范围广超高速磨削是一种高效、环保、精细化的磨削技术,可适用于各种材料的加工,包括金属、非金属材料、陶瓷材料等。
5. 环保超高速磨削使用的是无毒、无害、无污染的磨料,减少了对环境的污染。
四、应用前景在建筑领域,超高速磨削技术可以用于加工各类构件。
它能够大幅节约加工时间,提高生产效率。
同时,它还能精细加工各类构件表面,达到工艺标准,节约原材料,降低生产成本。
在未来,超高速磨削技术有望得到更加广泛的应用。
五、案例分析1. XXX公司的构件加工中,采用超高速磨削技术,成功优化了加工效率,降低了产品成本,得到了客户的一致好评。
2. XX公司将超高速磨削技术应用于钢筋加工中,减少了加工时间,提高了钢筋的精度和尺寸的一致性,受到了建筑公司的赞扬。
3. XX公司采用超高速磨削技术加工门窗构件,成功提高了构件的表面精度和光洁度,降低了产品的废品率,提高了客户的满意度。
4. XX公司采用超高速磨削技术加工凸轮、传动齿轮等构件,减少了加工时间,提高了精度和表面光洁度,获得了广泛应用。
工程硕士:磨粒有序化排布超硬砂轮磨削力工程的研究

工程硕士:磨粒有序化排布超硬砂轮磨削力工程的研究第1章绪论1.1 课题背景1.1.1 课题的提出由于普通砂轮存在着磨粒易脱落、磨削比能高、修整频繁、加工塑性金属材料易堵塞等问题,已不能完全满足在航空航天、国防军工、能源、化工、汽车等重要部门中不断涌现出的许多难加工材料进行高速、高效、高精度的加工要求,如钛合金、高温合金、TiAl、NiAl 及难熔金属硅化物等金属间化合物基高温结构材料、超高强度钢以及结构陶瓷和功能陶瓷等。
因此,致力于研究开发新型超超硬磨料成为人们研究的热点问题[3]。
与磨粒随机排布的普通砂轮相比,由于简单的制造技术,单层磨料电镀超硬砂轮表现出较为明显的优势,使超硬砂轮的份额在生产中占据相当大的比例,在高速甚至超高速磨削中的地位是不可忽视的。
单层高温钎焊超硬磨料钎焊砂轮因其具有很高的磨粒把持强度和磨粒裸露高度,在当今磨削技术中也占有不可忽视的地位。
但都存在一些问题,电镀砂轮镀层较厚时易造成堵塞、砂轮基体的结构设计及制造精度严重影响砂轮的回转精度和几何形状精度问题。
精密和超精密磨削所用砂轮会随着磨料颗粒的减小而增大控制电镀层厚度的困难程度,镀层过厚会将微磨粒完全包裹,导致磨削性能的下降。
当磨料粒度达到微米级时,对基体同轴度、平面度、圆柱度等形位误差要求更加严格,从而增加了砂轮的制造难度和成本。
更值得注意的是:无论是电镀砂轮或是钎焊超硬磨料砂轮,磨粒在砂轮基体表面大都是呈无规则的随机分布的,因此在磨削的过程中,真正去除工件材料的有效磨粒很少,大量无效的磨粒的存在使砂轮的制造成本显著增加,此外大量多余磨料的存在还使参与磨削的有效磨粒受到严重干扰,为砂轮的磨削性能造成很大的影响,如加工效率降低、加工表面质量差、砂轮寿命降低等。
为此想到,若能规划和控制磨粒在砂轮表面的数量和位置,通过对磨粒的可控排布,使磨粒在磨削接触区内按需发挥磨削作用,这样不仅可以节省大量超硬磨料,还可以有效减少砂轮堵塞、降低磨削温度等,从而获得最佳的磨削性能。
CBN砂轮120m_s高速磨削表面粗糙度实验研究
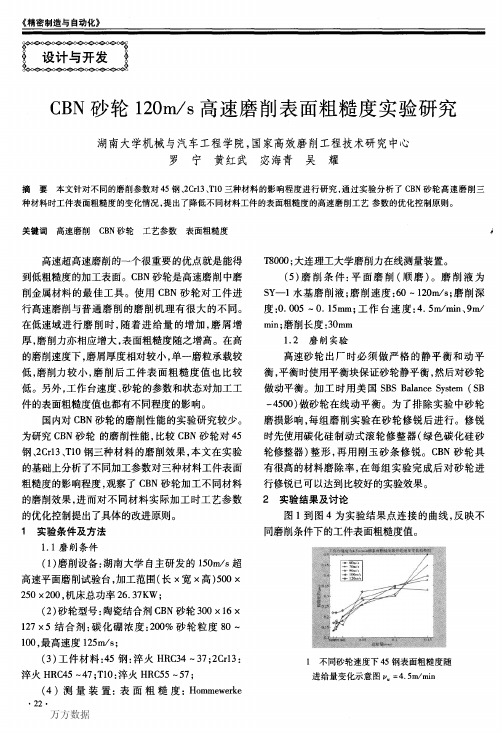
《精密制造与自动化》CBN砂轮120m/s高速磨削表面粗糙度实验研究湖南大学机械与汽车工程学院,国家高效磨削工程技术研究中心罗宁黄红武宓海青吴耀摘要本文针对不同的磨削参数对45钢、2Crl3、T10三种材料的影响程度进行研究,通过实验分析了CBN砂轮高速磨削三种材料时工件表面粗糙度的变化情况,提出了降低不同材料工件的表面粗糙度的高速磨削工艺参数的优化控制原则。
关键词高速磨削CBN砂轮工艺参数表面粗糙度高速超高速磨削的一个很重要的优点就是能得到低粗糙度的加工表面。
CBN砂轮是高速磨削中磨削金属材料的最佳工具。
使用CBN砂轮对工件进行高速磨削与普通磨削的磨削机理有很大的不同。
在低速域进行磨削时,随着进给量的增加,磨屑增厚,磨削力亦相应增大,表面粗糙度随之增高。
在高的磨削速度下,磨屑厚度相对较小,单一磨粒承载较低,磨削力较小,磨削后工件表面粗糙度值也比较低。
另外,工作台速度、砂轮的参数和状态对加工工件的表面粗糙度值也都有不同程度的影响。
国内对CBN砂轮的磨削性能的实验研究较少。
为研究CBN砂轮的磨削性能,比较CBN砂轮对45钢、2Crl3、TIO钢三种材料的磨削效果,本文在实验的基础上分析了不同加工参数对三种材料工件表面粗糙度的影响程度,观察了CBN砂轮加工不同材料的磨削效果,进而对不同材料实际加工时工艺参数的优化控制提出了具体的改进原则。
1实验条件及方法1.1磨削条件(1)磨削设备:湖南大学自主研发的150m/s超高速平面磨削试验台,加工范围(长×宽×高)500×250×200,机床总功率26.37KW;(2)砂轮型号:陶瓷结合剂CBN砂轮300×16×127×5结合剂:碳化硼浓度:200%砂轮粒度80一100,最高速度125m/s;(3)工件材料:45钢:淬火HRC34—37;2Crl3:淬火HRC45~47;TIO:淬火HRC55—57;(4)测量装置:表面粗糙度:Hommewerke・22.TS000;大连理工大学磨削力在线测量装置。
超精密研磨砂轮结构的优化设计

作者简 介 : 隐彪(92 , , 郭 16 一) 男 福建人 , 门大学教授 . 厦 工学博士 , 研究方 向 : 精密加工 、 机电一体化技术 。
维普资讯
摘
要: 超精密平 面研磨中工件的加 工精度受到研磨轮 结构参数 的影响。为 了 得到最高的加工精度
和最合 理 的砂 轮磨 损 曲线 , 必须研 究研磨 轮 的结构 参数 。通过 研 究研 磨轮 的加 工精度 系数 曲线和磨 损 系
数 曲线得 出 : 于大 量生产 的研磨 机床 , 对 研磨轮 磨损 是加 工精 度 的主要 影响 因素 , 研磨轮 应 采用正 三 角形
圉 1 正三角形放射线研磨轮
l 研 磨轮 加工精度 系数
平 面无 沟槽结 构研磨 轮 可 以得 到最好 的研 磨精度 表面, 但是 无 沟槽 结构也 带来 研磨 中排 屑的不便 , 响 影
到工件的加工表面精度。由文献[ ] 3的研究结果得出: 设计放射线结构研磨轮可以得 到高的研磨精度和小的
( 2 )
式 中
一 ≠一 研磨 轮上 切 削点 的切 削轨 迹 和 工件 ,
式 中
= =
外 周 的交角 。 为了正确评价 研磨 轮 的磨 损 情 况 , 入 研磨 轮 上 引
任一点的有效切削长度和研磨 轮上半径为 R的切 削 圆有效工作长度比, 即研磨轮磨损系数 ( ) R。
+ :R () 9
并经坐标变换 = 一r y1 可得到研磨轮放 , =Y ,
射 线 和轨迹 的交 点方程
r r n(, ) 、 一2t 2≠ ± a ±
高速超高速磨削用CFRP砂轮基体优化设计

碳纤维增强复合材料 CFRP 是一种以树脂作为基体材 料ꎬ碳纤维作为增强材料的复材ꎬ可通过调节材料中碳纤维 的体积分数、纤维排布、使用高性能树脂材料等手段满足不 同结构对材料性能的要求[7] ꎮ CFRP 与金属材料材料属性 见表 1ꎮ 相较于钢等金属材料ꎬCFRP 的密度较小ꎬ仅为钢 的 1 / 5ꎬ比强度和比模量较高ꎬ热膨胀系数较小ꎮ
表 1 常用砂轮基体材料的材料属性[8]
材料
密度 ρ / 泊松比 弹性模量 热导率 λ / 热膨胀系数 α /
( kg / m3 ) υ
E / GPa ( W / ( m∙K) ) (10-6 / K)
钢 7 850 0.27 200
45
12
铝合金 2 752 0.33
70
204
20
CFRP 1 500 0.3
Optimization Design of a CFRP Grinding Wheel Body for High Speed and Ultra-High Speed Grinding
ZHU Xinleꎬ FU Yucanꎬ YANG Luꎬ ZHANG Liang ( College of Mechanical and Electrical Engineeringꎬ Nanjing University of Aeronautics and
砂轮修整系统的运动性能分析与优化设计

砂轮修整系统的运动性能分析与优化设计引言:砂轮修整系统是一种常见的工业设备,广泛应用于各类机械加工中。
它通过修整砂轮来提高其加工效果和使用寿命,从而提高加工质量和效率。
本文就砂轮修整系统的运动性能进行了详细的分析与优化设计,旨在探索如何提高其性能,提升工业生产效益。
一、砂轮修整系统的工作原理砂轮修整系统主要由修整头、修整轴、主轴、控制系统等组成。
其工作原理是通过修整头的高速旋转,产生一定的磨削力,对砂轮进行修整。
修整头通常采用钢材制成,其表面有一定的砂浆,用来磨削砂轮表面。
修整轴与主轴通过一定的传动装置相连,使得修整头能够与砂轮形成一定的相对运动。
控制系统用来控制修整过程的时间、修整轴的转速等参数,以确保修整效果的稳定性和精度。
二、砂轮修整系统的运动性能分析1. 修整头的材料选择与设计:修整头的材料选择直接影响着修整系统的性能。
一方面,修整头需要具备一定的硬度和耐磨性,以保证其使用寿命。
另一方面,修整头的强度和刚度也需要充分考虑,以抵御高速旋转时的离心力和冲击力。
因此,设计合适的材料和结构对于提高修整头的性能至关重要。
2. 修整轴与主轴的传动系统设计:修整轴与主轴的传动系统设计对于修整头的旋转速度和稳定性有着重要的影响。
传统的传动系统多采用皮带传动或齿轮传动,但其存在传动损耗大、噪音大等问题。
近年来,随着电机技术的不断发展,采用直接驱动的电动传动系统逐渐成为一种新的选择。
该系统通过电机直接驱动修整轴,减小了传动损失,提高了传动效率和系统的稳定性。
3. 控制系统的优化设计:控制系统是砂轮修整系统的关键部分,它对修整过程的时间和修整轴的转速进行控制,直接决定了修整效果的稳定性和精度。
在优化设计中,需要考虑如何提高控制系统的响应速度、精确度和稳定性。
可以借助先进的传感器技术,实时监测砂轮的磨损情况,并根据实际情况进行自动调整。
同时,采用先进的控制算法和优化策略,提高系统的自适应能力和修整效果。
三、砂轮修整系统的性能优化设计通过分析砂轮修整系统的运动性能,我们可以得到以下一些优化设计的思路:1. 优化修整头的材料和结构,提高其硬度、耐磨性和刚度,延长使用寿命;2. 采用电动传动系统,减小传动损失,提高传动效率和系统的稳定性;3. 引入先进的传感器技术,实时监测砂轮的磨损情况,实现自动调整修整参数;4. 运用先进的控制算法和优化策略,提高系统的自适应能力和修整效果。
CBN及CBN砂轮磨削技术参数优化

CBN及CBN砂轮磨削技术参数优化CBN(Cubic Boron Nitride)是继人造金刚石问世之后,于1957年,由美国GE公司首先合成出的又一种超硬材料。
我国在1966年试制成功CBN,至今已有四十余年的历史了。
CBN的硬度仅低于金刚石,除了高硬度、高耐磨性、低摩擦系数等性质外,还具有比金刚石优越的耐热性和对铁族金属材料的化学惰性。
利用它这些优异的性能作研磨材料所制成的CBN磨具,特别适合于各类铁族金属材料的磨加工。
它和金刚石用于加工硬而脆的非铁系材料相互补充,使超硬材料的应用范围大大拓宽。
和普通磨料的磨具相比,CBN磨具具有高速、高效、高加工质量、长寿命、低成本的特点,可作为高速数控磨床高效、高精度磨削的首选工具。
在汽车、压缩机、机床、工具、轴承等工业领域有着广泛的应用。
1 CBN的性质1-1 CBN的晶体结构六方氮化硼(hBN)经高温高压合成,晶体结构由层状转变为立方结构,密度由2.25g/cm3增加到3.48g/cm3,各种性质都发生了突变。
1-2 CBN的主要特性在将CBN作研磨材料使用时,我们主要关注CBN的硬度、耐磨性、强度和导热性等性质。
1-2-1 硬度CBN的硬度仅次于金刚石,而远高于其它普通磨料。
高的硬度意味着切削能力更强、更锋利。
1-2-2 耐磨性CBN有高的耐磨性,意味着它比普通磨料更难磨损,保持磨粒形状的能力是CBN作为高性能磨料的主要特性之一。
1-2-3 抗压强度CBN的抗压强度很高,这意味着在高强度、大去除量磨削等恶劣条件下使用时,它能保持颗粒完整而不易破碎,因而使CBN磨具寿命更长。
1-2-4 导热性CBN有良好的导热性,在磨削时可实现冷切削。
从而大大减少被磨工件烧伤的可能性。
另外,CBN还有高的热稳定性和较低的热膨胀系数。
特别是CBN与铁、碳没有明显的化学亲和力,决定着它在磨削铁族金属时的价值。
而金刚石在一定温度下与铁发生化学反应而使其结构破坏,这就是金刚石不能加工铁族金属材料的原因。
刀具磨削砂轮调研报告总结

刀具磨削砂轮调研报告总结刀具磨削砂轮是工业生产中必不可少的磨削工具之一,广泛应用于金属加工和制造业。
磨削工艺对于提高刀具的精度和寿命具有重要作用。
本报告通过对刀具磨削砂轮的调研和研究,总结了刀具磨削砂轮的现状、问题和发展趋势,以期为相关行业的生产和研究提供参考。
调研结果显示,刀具磨削砂轮市场竞争激烈,砂轮的种类繁多,常见的有磨削切削的平面砂轮、磨削或磨削内外表面的锥形砂轮、磨削剃齿面的刀具砂轮等。
目前,磨削砂轮的硬度、粒度、结构和粘结剂等方面的性能得到了不断改进,具有更高的磨削效率和更好的加工质量。
然而,仍存在一些问题需要解决。
首先,砂轮磨削过程中易产生高温,导致工件表面生成热应力和热损伤,甚至可能引发火灾。
因此,研究和应用具有散热功能的刀具磨削砂轮成为一个新的发展方向。
其次,由于砂轮与工件之间的摩擦力,磨削过程中易产生振动和噪音,影响加工质量和工人的健康。
因此,减小振动和噪音的刀具磨削砂轮引起了广泛关注。
此外,砂轮的寿命和刀具的磨削效果也是研究的重点和难点。
未来,刀具磨削砂轮的发展趋势主要包括以下几个方面。
首先,磨削砂轮的材质将会不断创新,引入新材料和新技术,以提高磨削效率和加工质量。
其次,磨削砂轮将会更加智能化,通过传感器和控制系统实现对磨削过程的监测和控制。
此外,研究和应用磨削液体进一步改善磨削过程中的散热和润滑条件也是发展的方向之一。
最后,刀具磨削砂轮的环保性和可持续性将成为越来越重要的考虑因素,研发和应用可再生资源和环保材料的刀具砂轮将受到更多的关注。
总之,刀具磨削砂轮作为重要的工具,对于提高刀具的精度和寿命具有重要作用。
在竞争激烈的市场环境下,刀具磨削砂轮不断改进和创新,解决砂轮磨削过程中存在的问题,以适应工业生产的需求。
未来,刀具磨削砂轮的发展趋势将趋向智能化、智能化、环保化和可持续化。
对于相关行业的生产和研究,应充分考虑和应用刀具磨削砂轮的最新科技成果,以提高工作效率和产品质量。
砂轮磨削过程中的表面质量优化设计

砂轮磨削过程中的表面质量优化设计引言:砂轮磨削是一种常见的金属加工方法,可用于零件加工、工艺整形和精加工等多个领域。
然而,在砂轮磨削过程中,往往会出现表面质量不理想的情况,如毛刺、烧伤、裂纹等缺陷。
因此,如何优化砂轮磨削过程中的表面质量成为一个重要的研究方向。
一、砂轮的选择砂轮是砂轮磨削过程中最重要的工具,其选择对表面质量有着直接的影响。
一般来说,砂轮的硬度越高,表面质量越好。
因此,在选择砂轮时,应根据被磨削材料的硬度和粘结剂的类型确定砂轮的硬度,以保证砂轮能够更好地适应被磨削材料的特性。
二、切割参数的优化切割参数是指砂轮磨削过程中的主要参数,包括砂轮的转速、进给速度和进给深度等。
这些参数的选择与调整对表面质量有着重要的影响。
一般而言,较高的转速和较低的进给速度可以提高表面质量,但同时也会增加刀具磨损和加工时间。
因此,需要根据具体情况进行合理的优化设计,以达到最佳的表面质量。
三、冷却液的应用在砂轮磨削过程中,冷却液的应用对表面质量的优化起着至关重要的作用。
冷却液的作用是降低摩擦热并冷却被磨削材料,从而减少烧伤和裂纹等缺陷的产生。
合理选择适合材料的冷却液,并确保冷却液的供应充分和稳定,可以有效提高砂轮磨削的表面质量。
四、成形砂轮的应用成形砂轮是一种特殊的砂轮,它可以通过成形器具进行修整,以达到更好的加工效果。
使用成形砂轮进行磨削可以避免砂轮作业表面形状不均匀的问题,从而提高表面质量。
此外,成形砂轮还可以根据被磨削工件的形状特点进行精确修整,从而实现定制化加工,进一步提高表面质量。
五、磨削液的调控磨削液作为一种重要的辅助材料,对砂轮磨削过程中的表面质量有着重要影响。
磨削液的主要功能是冷却和润滑,可以减少摩擦热和磨损,提高加工效率和表面质量。
合理调控磨削液的浓度、温度和流量等参数,可以最大限度地发挥磨削液的作用,提高砂轮磨削过程中的表面质量。
结论:砂轮磨削过程中的表面质量优化设计是一个复杂的工程问题,涉及到多个因素的综合考虑。
风砂轮的超高速磨削与加工技术

风砂轮的超高速磨削与加工技术超高速磨削与加工技术是现代制造业中不可或缺的重要环节之一。
在各个行业中,特别是在精密制造和高科技领域中,对零部件的精度和表面质量的要求越来越高。
风砂轮作为一种常用的磨削工具,在超高速磨削与加工技术中发挥着重要的作用。
本文将围绕风砂轮的超高速磨削与加工技术展开讨论,探究其原理、优势和应用前景。
首先,我们来了解一下风砂轮的基本原理。
风砂轮是一种通过高速旋转的砂轮与被加工物之间的摩擦力来磨削材料的工具。
与传统的磨削工具相比,风砂轮具有旋风式的工作方式,通过高速旋转的方式将空气吹入砂轮与被加工物之间,形成压缩的气流。
这种气流会带走加工过程中产生的热量,起到冷却的作用,从而减小了热变形的可能性。
同时,气流还可以将切屑和砂粒带走,保持砂轮表面的清洁,提高加工的效率和精度。
超高速磨削与加工技术具有许多优势。
首先,由于风砂轮在磨削时产生的气流可以有效降低温度,减少热变形,因此可以实现高精度的加工。
其次,超高速磨削和加工技术可以在短时间内完成大量的精密加工,提高生产效率。
此外,由于风砂轮的磨削力度可调节,因此可以根据不同材料和加工要求进行精确控制,实现更加精细的加工。
最后,超高速磨削和加工技术还可以降低后续加工工序的难度,减少产品的加工周期和成本。
风砂轮的超高速磨削与加工技术在许多领域都有着广泛的应用前景。
首先,它在精密制造领域中可以用于加工各种高精度零部件,如航空航天领域中的涡轮叶片、汽车制造中的发动机零部件等。
其次,超高速磨削和加工技术还可以用于加工各种硬脆材料,如陶瓷、硬质合金等,这些材料在传统的磨削方法中往往难以实现高精度加工。
此外,风砂轮的超高速磨削与加工技术还可以应用于医疗器械、光学仪器、电子器件等领域,提高产品的质量和性能。
然而,风砂轮的超高速磨削与加工技术也存在一些挑战和问题需要解决。
首先,由于超高速磨削和加工的过程中会产生较大的热量,使砂轮和被加工物的温度升高,增大了热变形的可能性。
风砂轮的磨削中心距选择与优化

风砂轮的磨削中心距选择与优化对于需要进行磨削加工的工件而言,风砂轮是常用的磨削工具之一。
风砂轮的磨削效果与许多因素有关,其中之一便是磨削中心距。
正确选择和优化磨削中心距可以提高磨削加工的效率和质量。
本文将探讨风砂轮的磨削中心距选择与优化的相关问题。
一、风砂轮磨削中心距的定义风砂轮磨削中心距是指砂轮刀刃与工件加工表面之间的距离。
这一参数是磨削加工中的重要因素,直接影响到磨削过程的稳定性和加工质量。
二、磨削中心距的选择原则1. 考虑磨削力和表面质量在选择磨削中心距时,需要综合考虑磨削力和表面质量。
较大的磨削中心距可以降低磨削力,但可能导致表面粗糙度较大;较小的磨削中心距则可以提高表面质量,但可能增大磨削力。
因此,需要根据具体情况进行综合考虑。
2. 考虑砂轮的尺寸和形状风砂轮有不同的尺寸和形状,选择合适的磨削中心距需要考虑砂轮的特性。
例如,使用直径较大的砂轮时,可以选择较大的磨削中心距,以提高加工效率;而使用具有较小刀刃的砂轮时,则需要选择较小的磨削中心距,以获得更好的加工精度。
3. 考虑工件材料和形状工件的材料和形状也会对磨削中心距选择产生影响。
例如,对于硬度较高的材料,通常需要选择较小的磨削中心距,以降低磨削力并提高表面质量;而对于形状较复杂的工件,则需要根据具体情况选择适当的磨削中心距。
三、磨削中心距的优化方法1. 实验参数优化法通过实验方法进行优化是一种常用的研究手段。
通过对不同磨削中心距下的加工效果进行测试和分析,可以找到最佳的磨削中心距。
在实验过程中,需要控制其他参数的影响,以保证实验结果的准确性。
2. 数值模拟优化法数值模拟是另一种优化方法。
通过使用计算机模拟软件,可以对不同磨削中心距下的砂轮与工件之间的相互作用进行模拟,并预测磨削过程中的加工质量和效率。
根据模拟结果,可以选择最佳的磨削中心距。
3. 经验优化法经验优化法是一种简便实用的方法。
通过积累和总结磨削加工的经验,可以快速选择和优化磨削中心距。
风砂轮的磨削中心选择与工艺参数优化

风砂轮的磨削中心选择与工艺参数优化摘要:本文主要描述了在风砂轮磨削中心选择和工艺参数优化的重要性,并提出了一种集成了多参数优化方法的研究框架。
通过分析不同类型风砂轮磨削中心的特点和应用领域,以及磨削工艺参数的选择与优化方法,本文旨在提供一种能够满足工艺控制要求、提高磨削精度和效率的磨削中心选择与工艺参数优化方法。
1.引言风砂轮磨削中心作为一种非常重要的金属加工设备已经在工业生产中得到广泛应用,其先进的加工精度和高效率对于提高产品质量和降低生产成本具有重要意义。
然而,由于磨削工艺参数的选择和优化对于磨削中心的加工效果具有至关重要的影响,因此,选择合适的磨削中心和优化工艺参数对于提高磨削效率和产品质量至关重要。
2.风砂轮磨削中心选择风砂轮磨削中心的选择是磨削加工的关键步骤。
在选择时,我们需要考虑以下几个因素:2.1 加工需求根据不同的加工需求,我们可以选择不同类型的风砂轮磨削中心。
例如,对于需要高加工精度和表面质量的工件,我们可以选择高精度磨削中心。
而对于需要高效率和高产量的大批量加工,我们可以选择高速风砂轮磨削中心。
2.2 设备性能风砂轮磨削中心的设备性能也是选择的重要考虑因素之一。
包括设备的刚性、稳定性、定位精度等。
这些因素都会直接影响到加工的效率和加工质量。
2.3 成本因素除了加工需求和设备性能之外,成本因素也是选择的一项重要考虑因素。
包括设备的购买成本、维护成本以及加工成本等。
我们需要根据自身经济状况和加工需求综合考虑,选择最适合的风砂轮磨削中心。
3.风砂轮磨削工艺参数的选择与优化在选择了合适的风砂轮磨削中心之后,我们需要优化磨削工艺参数以提高加工效率和加工质量。
以下是一些常见的工艺参数:3.1 速度风砂轮的转速是磨削工艺参数中最关键的因素之一。
适当的转速选择可以提高磨削效率和加工质量。
通常情况下,对于硬质材料,需要选择较高的转速;而对于软质材料,需要选择较低的转速。
3.2 进给速度进给速度决定了砂轮从工件上移动的速度。
超高速磨削及其砂轮技术发展

超高速磨削及其砂轮技术发展1李长河1,蔡光起21 青岛理工大学机械工程学院,山东青岛(266033)2东北大学机械工程与自动化学院,辽宁沈阳(110004)E-mail:sy_lichanghe@摘要:高速超高速磨削加工是先进制造方法的重要组成部分,集粗精加工与一身,达到可与车、铣和刨削等切削加工方法相媲美的金属磨除率,而且能实现对难磨材料的高性能加工。
本文主要论述了高速超高速磨削工艺技术的特点;分析了超高速砂轮用电镀或涂层超硬磨料(CBN、金刚石)的特点以及修整方法,介绍了在高速及超高磨床上得到广泛应用的德国Hofmann公司生产的砂轮液体式自动平衡装置。
关键词:超高速磨削,砂轮,关键技术1. 超高速磨削的特点超高速磨削技术是现代新材料技术、制造技术、控制技术、测试技术和实验技术的高度集成,是优质与高效的完美结合,是磨削加工工艺的革命性变革。
德国著名磨削专家T.Tawakoli.博士将超高速磨削誉为“现代磨削技术的最高峰”。
日本先端技术研究学会把超高速加工列为五大现代制造技术之一。
在1996年国际生产工程学会(CIRP)年会上超高速磨削技术被正式确定为面向21世纪的中心研究方向之一,是当今在磨削领域最为引人注目的技术[1]。
高速加工(High-speed Machining)和超高速加工(Ultra-High Speed Machining)的概念是由德国切削物理学家Carl.J.Salomon博士于1931年首先提出,他发表了著名的Salomon曲线,创造性地预言了超越Talor切削方程式的非切削工作区域的存在,提出如能够大幅度提高切削速度,就可以越过切削过程产生的高温死谷而使刀具在超高速区进行高速切削,从而大幅度减少切削工时,成倍地提高机床生产率。
他的预言对后来的高速甚至超高速磨削的发展指明了方向,为高速超高速磨削技术研究开辟了广阔的空间,对于高速超高速磨削技术的实用化也起到了直接的推动作用。
- 1、下载文档前请自行甄别文档内容的完整性,平台不提供额外的编辑、内容补充、找答案等附加服务。
- 2、"仅部分预览"的文档,不可在线预览部分如存在完整性等问题,可反馈申请退款(可完整预览的文档不适用该条件!)。
- 3、如文档侵犯您的权益,请联系客服反馈,我们会尽快为您处理(人工客服工作时间:9:00-18:30)。
效磨粒间距 P、砂轮圆周速度 V s、工件进给速度 V w
和磨削深度 ap 四个变量, 各项的指数反映了各变量
对磨削比能的影响程度. 以此模型作为优化的目标
函数, 可综合反映砂轮表面地貌动静态参数以及磨
削用量的影响.
1. 2 约束条件及其函数
在实际磨削过程中, 由于加工设备、加工条件以
及工件的质量要求等等技术条件的限制, 所选择的
第 19 卷 第 1 期 2001 年 3 月
应用科学学报
JOU RNAL O F A PPL IED SC IEN CES
V o l. 19, N o. 1 M arch 2001
文章编号: 0255 8297 (2001) 01 0048 05
高效磨削用砂轮地貌的优化设计研究
傅玉灿1 徐鸿钧2
0. 001~ 0. 05 0. 003~ 0. 05
0. 1~ 30 0. 1~ 30
工件速度 V w (m m in)
1~ 30 1. 0~ 10 0. 05~ 0. 5 0. 5~ 10
砂轮速度 V s (m s)
20~ 60 80~ 200 20~ 60 80~ 200
优化设计的砂轮地貌
浓 度 出 露 有效磨粒间距
(1. 中国科学技术大学 力学和机械工程系, 安徽 合肥 230027; 2. 南京航空航天大学 机械系, 江苏 南京 210016)
摘 要: 针对有关磨削过程建模仿真传统思路的局限性, 提出了按照加工要求和用量条件优化设计砂轮地貌和按 优化地貌制作砂轮的创新思想. 依此思想并按照高效磨削的要求, 建立了砂轮地貌的优化模型, 所建模型的最大优 势在于它在优化地貌的同时也优化了用量条件和磨削过程. 以模型优化结果指导磨削加工过程, 理论上可确保在 不烧伤条件下获得最高的材料去除率指标. 作为优化模型的一个实际应用, 设计了实验用的超硬磨料开槽砂轮. 关键词: 优化; 高效磨削; 砂轮地貌 中图分类号: T G7 文献标识码: A
综合目标函数和约束函数, 便可得到一个完整 的优化数学模型为
在高效磨削过程中, 人们总希望在获得较大材 料去除率的同时消耗的能量最小, 因此, 可取单位时 间内切除单位体积材料所消耗的能量即磨削比能最
小为优化目标. 磨削比能表达式为
es=
F tV s V w apB
(1)
式中 es 为磨削比能 (J ) , F t 为切向磨削力 (N ) , B 为
砂轮宽度 (mm ) 由式 (1) 可见, 目标函数建立的关键
导致工件表层急剧温升并很快发生烧伤, 因此优化
时, 要考虑热流密度对设计变量的限制, 即优化出工
件不发生烧伤条件下的最小磨削比能, 由此便可构
造出磨削弧区平均热流密度的约束函数为
q=
RwK 2J
0
P-
13
4V w4V
1 4 s
3
ap8
d
s
3
8 ≤qlim
(13)
该约束函数中 qlim 的选取依冷却条件的不同而定, 它
1 期
傅玉灿等: 高效磨削用砂轮地貌的优化设计研究
49
臼井英治按后续切削刃概念解析法得出的磨削
1 砂轮地貌优化理论模型的建立
从分析砂轮表面的动静态参数与磨削过程的关
系入手, 可以确定动态有效磨粒间距 P、砂轮圆周速 度 V s、工件进给速度 V w 和磨削深度 ap 为设计变 量. 1. 1 优化目标及其函数
收稿日期: 2000 01 08; 修订日期: 2000 06 04 基金项目: 国家自然科学基金资助项目 (59675057) 作者简介: 傅玉灿 (1972 ) , 男, 福建泉州人, 博士.
© 1994-2009 China Academic Journal Electronic Publishing House. All rights reserved.
反映了磨削时弧区换热条件对磨削过程的影响, 当
换热条件较好时, 即使在较大的磨削用量条件下, 也
1 和表 2 所示.
表 1 与不同磨削工艺相匹配的砂轮地貌参数
磨削工艺
普通磨削 高速磨削 缓进深切磨削 高效深切磨削
磨削工艺
普通磨削 高速磨削 缓进深切磨削 高效深切磨削
用 量 条 件
磨削深度 ap (mm )
式中 l 为磨削弧区半长度, J 为热功当量, R w 为流 入工件的磨削热比例. 将式 (2) 代入式 (11) 并整理可
1. 2. 1 表面粗糙度 R a
得
© 1994-2009 China Academic Journal Electronic Publishing House. All rights reserved.
均匀分布考虑, 则
1
W=
ΠΘ 5. 28D
3
dg
(5)
式中 D 为砂轮浓度, Θ为磨料密度, d g 为磨粒直径.
当工件表面轮廓呈特殊几何形状, 如规则的三角形
时, R m ax = 4R a [3 ]. 令 R a 小于加工要求的表面粗糙度
R a0, 即可得到平面磨削表面粗糙度的约束函数为
2
6
2
0. 34W 5 (co tΗ) 5
在于确定切向磨削力 F t, 由磨削几何学和单颗磨粒
受力分析可以建立平面磨削时切向磨削力的理论公
式[1, 2 ]
3
F t=
Π4 K B P -
1 4
Vw Vs
47 1
ap8
d
8 s
sin
Η
(2)
式中 P 为动态有效磨粒间距 (mm ) , d s 为砂轮直径
(mm ) , Η为磨粒圆锥半角, K 为与材料有关的系数,
1- V V
Πh
2 i
dg 2
-
hi 3
≥4tanΗP 2
Vw Vs
2
3
ap2
d
s
1 2
(10)
1. 2. 3 磨削弧区平均热流密度
磨削弧区平均热流密度是指磨削时磨削弧区工
件表面单位面积上的磨削热, 表达式为
q=
R w F tV s J 2lB
(11)
糙度、容屑空间和磨削弧区平均热流密度为约束条 件.
多负面影响. 有鉴于此, 本文按照逆向考虑问题的思 路, 提出砂轮表面磨料按照不同的加工要求相对有 序合理排布的新概念, 并在此基础上进一步提出按 照加工要求和用量条件优化设计砂轮地貌或按照加 工要求和砂轮地貌优化选择用量条件的创新思想. 按照这一思想, 不仅有条件可以真正实施对磨削过 程的建模仿真研究, 而且可以一步到位实现对磨削 过程的优化和磨削结果的预估. 最后, 根据新思路完 成开槽砂轮地貌的优化设计和实验研究.
fa B
5
Vw Vs
2 5
1 ≤R a0 (6)
ds
1. 2. 2 容屑空间
参照刀具设计的理论, 定义砂轮上相对每一磨
粒的空隙体积内能容纳的切屑体积为砂轮的容屑系
数, 它表明砂轮磨削时的容屑能力, 容屑系数 C s 可 用下式表达[4 ]
C s=
Qp Q ch
(7)
式中 Q p 为砂轮上对应于每一磨粒的空隙体积, Q ch 为砂轮上对应于每一磨粒切下的切屑体积. 仍假设
可用抗拉强度比进行修正.
将式 (2) 代入式 (1) 并化简可得单位砂轮宽度上
的磨削比能为
ห้องสมุดไป่ตู้
es=
K 0P -
1 4
Vw Vs
-
1
4 ap-
11
8 d s8
(3)
式 中 K 0 为 与 工 件 材 料 和 磨 粒 有 关 的 系 数, K 0 =
Π 4K
s
in Η.
由式
(3)
可见,
磨削比能模型包含有动态有
A Study on the O ptim iza tion D esign of the Gr ind ing W heel Topography for the H igh Eff ic iency Gr ind ing
FU Yu2can1, XU Hong2jun
(1. D ep a rm en t of M echan ics and M echan ica l E ng ineering , U n iversity of S cience and T echnology of Ch ina, H ef ei 230027, Ch ina; 2. M echan ica l E ng ineering D ep a rtm en t, N anj ing U n iversity of A erom au tics and A stronau tics, N anj ing 210016, Ch ina)
磨粒为球体, 当磨粒出露高度为 h i 时近似有
Q p=
1- V V
Πh
2 i
dg 2
-
hi 3
(8)
Q ch= 4tanΗP 2
Vw Vs
23
ap2
d
s
1 2
(9)
正常磨削时, 容屑系数 C s≥1, 即单颗磨粒凸出 结合剂所拥有的容屑空间Q p 必须大于单颗磨粒切 下的切屑体积 Q ch, 则容屑空间的约束函数为
设计变量的范围是有限的, 在进行优化时, 必须考虑
这些条件对设计变量的限制. 本文确定工件表面粗
表面粗糙度的理论计算式为[ 1 ]
2
6
2
R max= 1. 36W 5 (co tΗ) 5
fa B
5
Vw Vs
2 5
1 (4) ds
式中 R m ax 为表面最大高度不平度, f a 为纵向进给