FMEA培训教材ppt课件
FMEA培训教材(英文版)(ppt 79页)
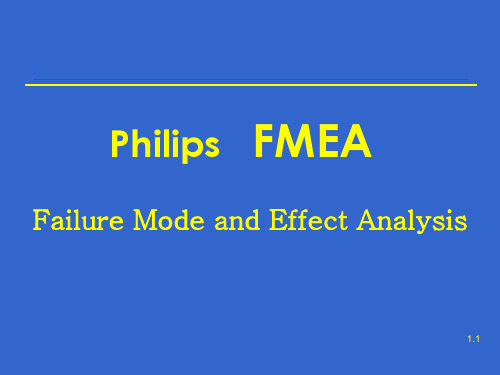
1.5
FMEA – Purpose
Failures
FMEA
CR
Time
(Productionstart)
1.6
FMEA – Purpose
actionable level Represents all wants, both spoken
and unspoken.
1.20
Describe Function
Verb
Indicates action, occurrence, being
Generate Control Display
Startingdate/ revisiondate?
1.12
Managing FMEA’s
FMEA’s are living documents and are updated ...
Modification to a product or process is planned
Component is to be used in new environment
team.
1.17
Blockdiagram
Service
Assembly
Part
Screw Component/
Weld
Part
X
Assembly
Y
User
Other systems
Adhesive
Part
Z
1.18
Example blockdiagram (Settop Wildfire)
《MFMEA培训教材》课件
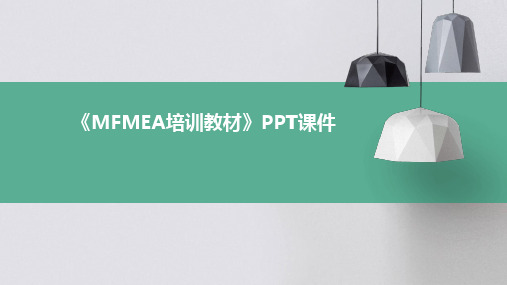
$number {01}
目录
• MFMEA基本概念 • MFMEA实施流程 • MFMEA分析方法 • MFMEA应用案例 • MFMEA总结与展望
01
MFMEA基本概念
MFMEA定义
MFMEA定义:MFMEA(失效模式与影响分析)是一种系统 化的方法,用于识别、评估和解决产品或过程中潜在的失效 模式及其对系统性能的影响。
MFMEA通过分析产品或过程中可能出现的失效模式,评估 其对整个系统性能的影响,并确定预防和减轻这些影响的措 施,从而提升产品和过程的可靠性和安全性。
MFMEA目的和意义
MFMEA目的
MFMEA的主要目的是识别、评 估和降低产品或过程中潜在的失 效风险,提高产品和过程的可靠 性和安全性。
意义
通过MFMEA,企业可以提前发 现和解决潜在问题,减少产品或 过程中的故障和缺陷,提高客户 满意度和产品竞争力。
未来,MFMEA将更加注重数据 分析和人工智能技术的应用,提 高故障模式识别的准确性和效率 。
针对复杂系统和产品的多层次、 多维度分析需求,MFMEA将进 一步发展其分层和集成分析能力 。
THANKS
在问题,提高产品质量和可靠性。
04
MFMEA的流程包括明确分析对象、确定分析层次 、列出故障模式、分析故障原因和影响、评估风险
优先级、制定改进措施等步骤。
MFMEA未来发展方向
随着技术的不断进步和应用领域 的拓展,MFMEA将进一步发展 并应用于更广泛的领域。
针对快速迭代开发和上市的需求 ,MFMEA将发展更高效的分析 方法和工具,缩短分析周期和降 低成本。
详细描述
故障影响评估应考虑产品或过程的功能要求、使用环境以及相关法律法规等因素,以确定故障对产品 或过程的影响程度。
FMEA精典讲义PPT课件
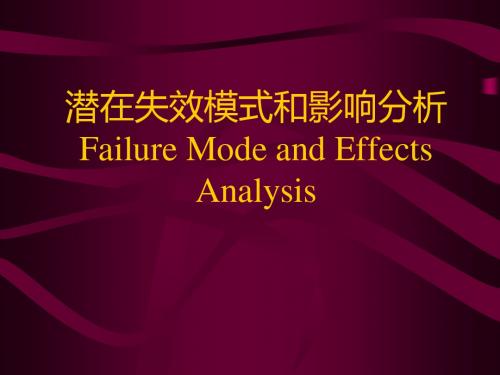
有原因, 确定对这些因素的控制,量化严重度、频度和不易探测度。 进行排序, 建议措施,进而建立改进设计和开发试验的优先控制系统降低
失效的风险。确定潜在的产品特殊特性。
响
因
控制
险
措施
现行 控制
原
现行
风
建议
因
控制
险
措施
现行 控制
18
建立设计FMEA
对工程师进行运用设计FMEA的培训, 理解设计控制概念。 了解对于顾客确定关键和特殊特性方法。 设计FMEA是一个创造性的工作,需要采用跨功能的小组。 应考虑包括每个零部件,审查产品的每个特性和功能。 需要调查研究和发挥创造力。
它用于军事项目合约。 • 1970年晚期,汽车工业将FMEA作为在对其零件设计和生产制造的会审项目的一部分。 • 1980年初,产品事故责任的费用突升和不断的法庭起诉事件发生,使FMEA成为降低事
故的不可或缺的重要工具。并由开始的500多家公司扩展到其供应商。 • 1993年包括美国三大汽车公司和美国质量管理协会在内的,美汽车工业行动集团组织采
确定特殊特性, 确定设计验证计划
第 II 阶段
设计验证计划 和报告
生产工艺流程图
开展过程FMEA
确定风险和可行性
把产品特性与生产过程相联系, 明确特殊特性
揭示变差来源, 最后确定特殊特性
第 II 阶段 第III 阶段 第III 阶段
9
设计FMEA
目的 • 设计的分析技术,分析和说明潜在失效模式及其原因和机理; 有助于对设计要求、设计方案进行分析评价; 有助于对制造、装配要求的初始设计确定; 确保潜在失效模式及其影响(对系统/整车运行)在设计和开发过程中得到
《MFMEA培训教材》PPT课件
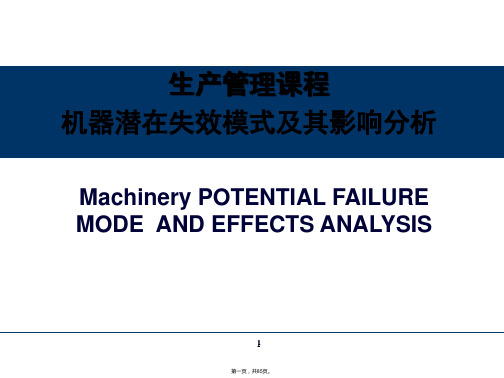
第十二页,共85页。
一个团队,应该是有思考性、自主性、合作性的组织。团队 的成员拥有共同的目标,是在一条船上共患难的水手!
对于团队,有个很新颖的解释:TEAM--Together Everybody can Achieve More! (只有在一起,每个人才能做到
更多!)
113
第十三页,共85页。
同角色的组合达至完美!
适合FMEA的小组成员:
-装配、制造人员(带来现场的经验) -设计人员(包括其它部件、子系统、系统和总成) -工艺人员(包括其它部件、子系统、系统和总成)
-可靠性分析/试验人员(带来失效的经验) -材料工程师(带来材料的要求) -质量工程师(带来质量控制的要求及相关的解决方案) -服务人员(带来客户处抱怨)
第三十一页,共85页。
8.核心小组
•列出所有被授权识别和执行任务的负责人姓名及所在部门(建议包含所有成 员的姓名,部门,电话号码,地址等)。
9a.子系统名称
输入对被分析的子系统名称的描述。
自动装货设备,锭子,水力的,电子的,工作站-5-左边。
设备等级术语
举例
•设备
转移生产线
•系统
设备工作站
•子系统
所有的MFMEA都关注设计。
MFMEA 作为专门的技术应用以识别并帮助最大程度地
减少潜在的隐患一直是非常重要的 !
8
第八页,共85页。
成功实施MFMEA项目的最重要因素之一是时间性。其含义是指 “事件发生前”的措施,而不是“事实出现后”的演练。为实现最大价 值,MFMEA必须在设备的失效模式被纳入到设备设计之前进行。事先 花时间很好地完成MFMEA分析,能够最容易、低成本地对设备进行更 改,从而最大程度地降低后期更改的危机。MFMEA能够减少或消除实 施可能会带来更大隐患的预防/纠正性更改的机会。
FMEA培训ppt课件
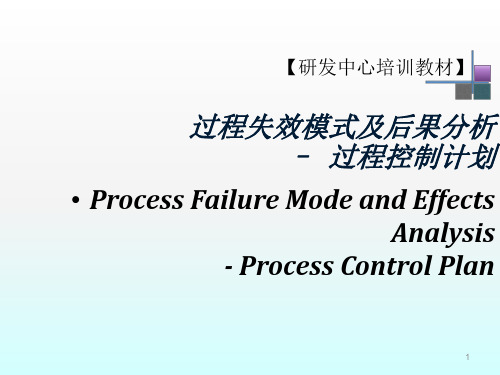
宏观的描述:装护板
将护板取出
微
对护板进行检查
观
的
护板放置到底座上
活
动
操作工拿出5颗螺钉
将螺钉放置到护板上
操作工将螺钉打紧
①
③
⑤
④
②
32
PFMEA -- 过程定义
详细叙述各个流程的作用(用动词+名词的方式)
------进行这样的分析是为后面用头脑风暴的方法来分析失效模式做准备
工步 列出要研究的各个工步 将护板取出 对护板进行检查 护板放置到底座上 操作工拿出5颗螺钉 将螺钉放置到护板上 操作工将螺钉打紧
关键日期—(5) FMEA计划完成日期,APQP进度计 划安排日期。 FMEA编号/版本—(6) 用于追溯FMEA的内部编号与版本 编制人—(7) FMEA编制人的姓名、电话及所属 公司 日期—(8) 原始稿编制日期、修订号和日期
22
製程名稱: 核心小組:
工程放行日期: 製 表 人 員:
措施執行的結果
已采取的 措施
严频探 R
重度测 度数度 (S)(O)(D)ss FMEA 开发思路
团队组建
•多功能小组 •成员来自各个级别的人员,如客户、产品设计、过程设计 、生产 线等 •确定小组组长 • 获得领导支持
过程定义
过程流程图 识别过程中每一工步的目的(采用“动词+名词”形式)
采取降低风险的行动
• 更改产品/过程设计,降低严重度(伤害性风险与设计风险); • 更改产品/过程设计,降低频度数; • 采用防错技术,提高可探测性,降低不可探测度数; • 提高在线检测技术和不合格品控制,提高可探测性,降低不可探测风险; • 变更过程控制计划; • 改进加工工艺、工装刀具。
FMEA失效模式分析培训教材(PPT52页)
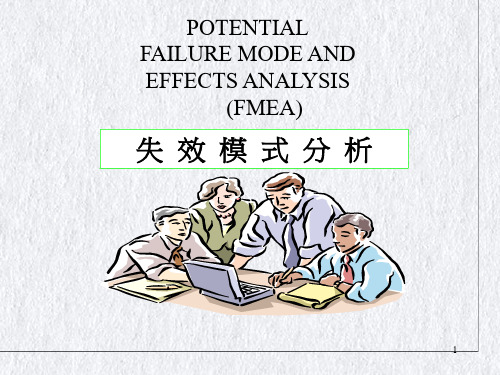
降低功能 -- 間 歇 功 能 -- 不 預 期 功 能
原因為何?
其發生 頻率為何?
能夠做什麼? -- 設 計 變 更 -- 製 程 變 更 -- 特 別 管 制 -- 標 準 , 程 序 書
或指引變更
如何能 預防及發現
這種 原因及錯誤?
這種方法 發現這種問題
经验和教训,对可能出现问题的项目的分析)。这种系统化的方法体现
了一个工程师在任何设计过程中正常经历的思维过程,并使之规范化、
文件化。
8
设计FMEA能够透过以下几方面支持设计过程,以降低失效风险: .有助于对设计要求和设计方案进行客观评价; .有助于对制造和装配要求的最初设计; .提高在设计/开发过程中,考虑潜在失效模式及其对系统和运行冲击
1
FMEA概要
何谓FMEA: 是描述为一组系统化的活动,其目的是: A:发现和评价产品/过程中潜在的失效及其失效效应 B:找到能够避免或减少这些潜在失效发生的措施 C:将上述整个过程文件化 它是对设计过程的更完善化,明确必须做何种设计和过程 才能满足顾客的需要。
2
FMEA的實施
由于尽可能的持续改进产品和过程是企业的趋势,所以使用FMEA作为专门技 术应用,以识别并帮助减少潜在的隐忧一直是非常重要的。对于产品抱怨的研 究结果表明,全面实施FMEA能够避免许多抱怨事件的发生。
7
設 計FMEA
簡
介
设计FMEA主要是由负责设计的工程师/小组采用的一种分析技术,用
来保证在可能的范围内已充分地考虑到,并指明各种潜在的失效模式及
其相关的起因/机理。应该评估最终的产品以及每个与之相关的系统、
子系统和零组件。FMEA以其最严密的形式总结了设计一个零部件、子
FMEA培训教材(PPT 99页)

DFMEA
第一版
原始稿日期
第二版
第三版
最新修订日期
DFMEA
8)核心小组 列出有权确定和/或执行任务的责任部门的 名称和个人的姓名(建议所有参加人员的姓 名、部门、电话、地址等都应记录在一张分发 表上。)
项目/功能要求 ➢ 填入被分析项目的名称和其他相关信息(如编号、零
件级别等)。利用工程图纸上标明的名称并指明设计水
察觉的现象相同。
➢ 潜在失效的后果,就是失效模式对系统功能的影响,可以使用顾客感受的语 言来描述.
➢ 要根据顾客可能发现或经历的情况来描述失效的后果,要记住顾客既可 能是内部的顾客也可能是最终用户。
➢ 如果失效模式影响可能影响安全性或对法规的符合性,要清楚地予以说 明。
➢ 失效的后果应按照所分析的具体的系统、子系统或部件来说明,还应记住 不同级别的部件、子系统和系统之间存在着一种系统层次上的关系。例 如,一个零件可能会断裂,这样会引起总成的振动、从而导致一个系统 间歇性运行。系统的间歇性运行可能会造成性能的下降并最终导致顾客 的不满。分析的意图就是在小组所拥有的知识层次上,尽可能的预测到 失效的后果。
知识的人员组成,(如设计、分析/试验、制造、装配、服务、 回收、质量及可靠性等方面有丰富经验的工程师)。 ➢ FMEA由责任单位的工程师开始启动,责任单位可能是原 设备制造厂(OEM,即生产最终产品)、供方或分承包方 ➢ FMEA工基本概念是预防为主,一定要在任何未知的设计 或制造的故障产生之前实施。 ➢ FMEA是一个重复的,周期性永不间断的改进程序
概要
FMEA的历史 20世纪50年代,美国格鲁曼公司开发了FMEA,用于飞
机制造业的发动机故障防范,取得了较好的成果.美 国航空及太空总署(NASA)实施阿波罗登月计划时, 在合同中明确要求实施FMEA.
FMEA培训教材(课堂PPT)

车辆可运行,部分顾客(50%)能够察觉 到外观或噪音
车辆可运行,少部分顾客(<25%)能够 察觉到外观或噪音
无影响
等级
10 9 8 7 6 5 4 3 2 1
影响
影响到安全 和/或法律 法规的失效
过程后果的严重度(制造/装配影响)
在无任何警告的情况下危及操作者 (加工或装配)
? 潜在失效模式
烧焦/穿孔
? 潜在失效后果 前照灯无法使用
? 后果分析
S*O*D
RPN=1 Or RPN=1000
YES
地
2
PFMEA的分析思路
编制过程步骤
确定功能要求 识别风险
确定失效模式 确认后果 确认原因
确定目前控制
评价S 评价O 评价D
地
15
RPN (S*O*D)
三种 评价
完成?
否
筛选最重要
电机系统
车身系统
引擎 供油 系統 系統
制动 系统
照明 系統
空调 系统
前车
后车
地
2
过程 步骤
要求
潜在 失效模式
17
S
潜在 失效后果
严 重 度
级 别
潜在失效 起因/机理
OD
现行过 程控制 预防
频 度
现行过 程控制 探测
探 测 度
R P N
建议措施
责任与 目标 完成日期
措施结果
严
采取措施 重
度
频 度
探 测 度
4、编制人:填入FMEA编制的主要负责人。
5、车型年/类型:填入被用到或被设计时分析到汽车的年型和车型(如果 已知)。
FMEA培训教材PPT完整版(2024)

产品设计阶段FMEA案例分析
案例一
某型号汽车发动机设计FMEA分 析。针对发动机系统可能出现的 故障模式进行分析,如气缸磨损 、活塞环断裂等,制定相应的改
进措施。
案例二
某型号手机电池设计FMEA分析 。针对电池可能出现的过热、短 路等故障模式进行分析,优化电 池结构和电路设计,提高电池安
全性。
26
过程控制阶段FMEA流程
定义过程范围和功能
01
识别潜在的故障模式
02
评估故障影响的严重度、发生
度和检测度
03
计算风险优先数(RPN)并排 序
04
制定并实施控制措施
2024/1/29
05
跟踪验证控制措施的有效性并
更新FMEA
06
27
过程控制阶段FMEA案例分析
案例一
某汽车制造厂涂装车间过程FMEA分 析
为生产过程FMEA提供支持
产品设计阶段FMEA的输出可以为生产过程 FMEA提供重要的输入和支持。
20
产品设计阶段FMEA流程
组建FMEA团队
由多部门、多学科的专业 人员组成,包括设计、制 造、质量、采购等。
2024/1/29
定义系统和子系统
明确产品的结构和功能, 划分系统和子系统。
识别故障模式
针对每个子系统或部件, 识别所有可能的故障模式 。
9
组建FMEA团队并分配任务
02
01
03
2024/1/29
组建多学科团队
包括设计、制造、质量、采购等相关领域专家。
分配角色与责任
明确团队成员的角色和责任,确保任务有效执行。
提供培训与支持
为团队成员提供FMEA培训,确保掌握相关知识和技 能。
新PFMEA培训POWERPOINTPPT课件
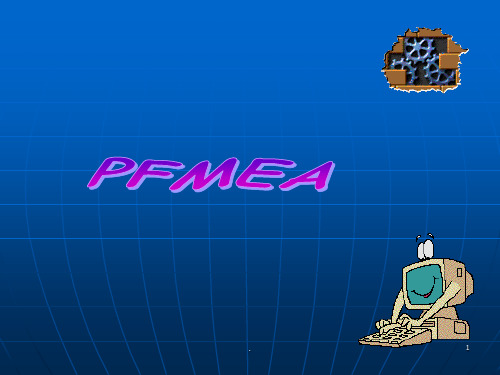
.
25
PFMEA
潜在的失效起因/机理
如果失效的许多起因并不是相互独立的、唯 一的,要纠正或控制一个起因,需要考虑许 多起因中哪些是根本起因、起主要作用,哪 些起因容易得到控制。应描述这些起因,以 便针对那些相关的因素采取纠正措施。
.
26
PFMEA
潜在的失效起因/机理
原
主要原因
因
实验
不
是
DOE
相 互
.
1
PFME A
为什么要做FMEA
FMEA是一种系统分析的方法,在分 析过程中使问题得到合理化解决的工具。
FMEA是一种系统化的工作技术和模式 化的思考形式。
.
2
PFME A
为什么要做FMEA
FMEA就是及早地指出根据经验判断出的弱 点和可能产生的缺陷,及其造成的后果和风 险,并在决策过程中采取措施加以消除。
.
3
PFME A
为什么要做FMEA
实施FMEA就是根 据经验和抽象思维来 确定缺陷,在研究过 程中系统地剔除这些 缺陷的工作方法。
.
4
PFME A
为什么要做FMEA
这种方法是一种预防和
避免缺陷发生的方法,一
般是一次性的投入;而传
统的解决缺陷方法是不间
断耗费,两者相比,
FMEA工作方法显得更合
理,更经济。
.
5
PFMEA
顾客的定义
过程FMEA中“顾客”的定义通常 是指“最终使用者”。(也可以是下 游的制造或装配工序)
.
6
PFME
A 小组的努力来完成 FMEA
• 相关领域的代表:设计、装配、制造、质量、服务、 供方……
• 过程FMEA应成为促进各领域之间交换意见的催化剂
FMEA培训教材-PPT文档资料-课件

FMEA & FMECA
FMEA: Failure Mode and Effects Analysis
失效模式及其影响的分析
FMECA:
Failure Mode, Effects and Criticality Analysis
失 效 模 式, 影 响 及 其 关 键 性 的 分 析
14
FMEA
Pa rt/Pro d u ct Own er: Pro cess Own er:
Part/ Proce s s
Failure Mode
S E Failure Effects V
Caus es
O C C Controls
Prep a red By : FM EA Da te (Orig ):
DR EP T N Actions
量。
16
FMEA
FMEA 的 等 级
步骤#1
过程-第一阶层
步骤 #2
步骤 #3
步骤 #1
过程-第二阶层
步骤 #2
步骤 #3
FMEA - 第一阶 层
FMEA - 第 二阶 层
步骤 #1
过 程 - 第三 阶 层
步骤 #2
步骤 #3
FMEA - 第 三阶 层
17
FMEA
FMEA 类 型
设计/产品
用 于 分 析 产 品,鉴 别 潜 在 的 在 发 展 周 期 早 期 与 设 计 意 图 相 关 的 产 品 失 效 模 式(部件,次装配)。
控制图
4
特殊起因
3
统 计 的 过 程 控 制 (SPC) 方 式: 当 特 殊 起 因 发 生 和 消 除 时 确 认 它 们。
FMEA培训教材ppt完整版

FMEA培训教材ppt完整版•FMEA概述与基本原理•失效模式识别与评估方法•故障原因分析技巧与工具应用•风险等级划分标准与应对措施制定目录•FMEA在产品设计阶段应用实践•FMEA在生产过程监控和持续改进中作用•总结回顾与展望未来发展趋势01FMEA概述与基本原理FMEA定义及发展历程FMEA定义故障模式与影响分析(FailureModes and Effects Analysis)发展历程起源于军事领域,后广泛应用于航空、汽车、电子等各个行业FMEA核心思想与目标核心思想预防性分析,识别潜在故障模式及其对系统的影响,提前采取措施降低风险目标提高产品可靠性、减少维修成本、增强客户满意度032. 功能分析识别系统或部件的功能及潜在故障模式01适用范围产品设计、生产过程、服务流程等各个环节021. 定义范围明确分析对象及目标评估故障模式对系统性能、安全、经济等方面的影响3. 故障影响分析综合考虑故障发生概率、严重度及可检测性,对故障模式进行风险等级排序4. 风险等级评估针对高风险故障模式,制定预防措施和应急计划5. 制定措施定期回顾FMEA 结果,更新措施并持续改进6. 跟踪与持续改进02失效模式识别与评估方法产品无法实现设计功能或性能不达标,如电子设备无法开机、机械部件卡滞等。
功能性失效安全性失效可靠性失效产品存在安全隐患,可能导致人身伤害或财产损失,如汽车刹车失灵、电器短路引发火灾等。
产品在规定条件下和规定时间内无法完成规定功能,如电池寿命短、设备频繁故障等。
030201常见失效模式类型介绍失效模式识别技巧与工具技巧了解产品工作原理及结构特点分析历史故障数据及维修记录•运用头脑风暴等方法集思广益工具故障树分析(FTA)事件树分析(ETA)因果图(Cause-Effect Diagram)01020304•方法选择:根据失效模式的性质和影响程度选择合适的评估方法,如风险矩阵、风险指数等。
实施流程1. 明确评估目标和范围2. 收集相关数据和信息3.选择合适的评估方法并建立评估模型4.对失效模式进行定量或定性评估5.根据评估结果制定相应的改进措施并跟踪验证03故障原因分析技巧与工具应用故障树分析法概述故障树的建立故障树的定性分析故障树的定量分析故障树分析法(FTA )原理及应用01020304介绍FTA 的基本概念、原理、作用及适用范围。
FMEA培训教材ppt
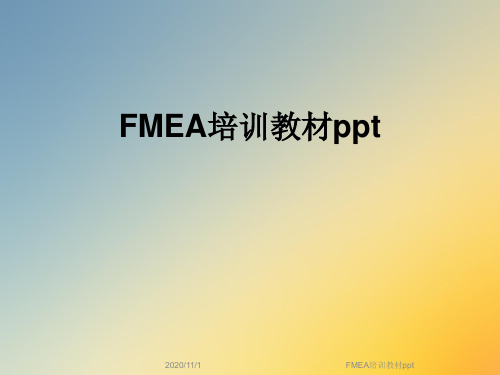
FMEA培训教材ppt
制程失效定义: 产品在经过一制造程序时,因制程而造成 其特性无法满足产品规格或甚至损坏者,即为制程失效.
失效效应的严重等级分为四級:
(A).I级:致命失效
此类失效模式发生可能会导致整个系統
FMEA培训教材ppt
2020/11/1
FMEA培训教材ppt
目录
•什么叫FMEA •FMEA分类和特点 •FMEA技术的发展与应用 •RPN评价 •FMEA的应用(以PFMEA为 例)
FMEA培训教材ppt
FMEA由来
AIAG 全称Automotive Industry Action Group,即汽车工业行动小组。该组织 成立于1982年,由美国三大汽车公司通用、福特和克莱斯勒共同创建,是全 球公认的著名的非盈利组织。
3
- 第二章﹕過程FMEA (Process Failure Mode & Effect Analysis )
PFMEA分析方法的流程 先期规划 主流程 结果应用
FMEA培训教材ppt
组成FMEA团队 资料收集
制定执行方案
先期规划
产品设计 制造工艺 使用维修 环境
表格格式 分析层次 失效定义 成果整合
注意
不要混淆 DFMEA与PFMEA的起因和失效
过程潜在的失效模式及后果分析
过程FMEA(PFMEA)
PFMEA简介
1.确定与产品相关的过程潜在失效模式 2.评价失效对顾客的潜在影响 3.确定潜在或装配过程失效的起因﹐确 定减少失效发生或找出失效条件的过程 控制变量 4.编制潜在失效模式分级表﹐然后建立 考虑纠正措施的优选体系 5.将制造或装配过程的结果编制成文件
- 1、下载文档前请自行甄别文档内容的完整性,平台不提供额外的编辑、内容补充、找答案等附加服务。
- 2、"仅部分预览"的文档,不可在线预览部分如存在完整性等问题,可反馈申请退款(可完整预览的文档不适用该条件!)。
- 3、如文档侵犯您的权益,请联系客服反馈,我们会尽快为您处理(人工客服工作时间:9:00-18:30)。
能影响的文件化体系 评定产品或过程潜在失效模式的文件,采取相应措
施来消除或降低潜在失效的影响
7
FMEA-ASIR
11
FMEA-ASIR
workshop
四阶段:
WS1:RPN&确认顾客质量重要需求 WS2:确定分析的对象 WS3:失效模式与效应分析 WS4:确定潜在要因、现行管制有效性与改善
参见标准的FMEA模版/ 例举具体案例进行演示
12
FMEA-ASIR
扁鹊的医术
魏文王问名医扁鹊说:「你们家兄弟三人,都精 于医术,到底哪一位最好呢?」 扁鹊答说:「长兄最好,中兄次之,我最差。」 文王再问:「那么为什么你最出名呢?」 扁鹊答说:「我长兄治病,是治病于病情发作之 前。由于一般人不知道他事先能铲除病因,所以 他的名气无法传出去,只有我们家的人才知道。 我中兄治病,是治病于病情初起之时。一般人以 为他只能治轻微的小病,所以他的名气只及于本 乡里。而我扁鹊治病,是治病于病情严重之时。 一般人都看到我在经脉上穿针管来放血、在皮肤 上敷药等大手术,所以以为我的医术高明,名气 因此响遍全国。」 文王说:「你说得好极了。」
13
FMEA-ASIR
【结论】 事后控制不如事中控制,事中控制不如 事前预防,可惜大多数的事业经营者、 管理者均未能体认到这一点先防范未然, 等到错误的决策造成了重大的损失才寻 求弥补,亡羊补牢,为时已晚。
14
FMEA-ASIR
失效模式与效应分析(Failure Mode&Effect Analysis, FMEA)是一种系统化之工程设计辅 助工具,协助工程师进行新产品、新技术开发、 工程分析,使其在工程设计时早期发现潜在缺 陷及其影响程度,及早谋求解决之道,避免失 效之发生或降低其发生时产生之影响,提高系 统之可靠度。
2
FMEA-ASIR
FMEA概念篇
首先请欣赏现场包装的影象资料
智者千虑必有一失, 寓者千虑必有一得;
3
FMEA-ASIR
FMEA概念篇
补充钣金件产品的实际案例或者 生活中的案例
问题案例
联亨 联亨
OSP总测工段 02401048 OSP总测工段 02401048
1 机柜模块采集线接反,导致采集不到模块信息 1 机柜防雷板上连接正极铜排线与地线接反
21500375 2009-5-13 漏装物料 机柜来料少2pcs压接铆钉。 21010959 2009-5-13 结构不良 机柜内门上的结构件来料没有折边。
FMEA分
析
製程項目 ( item)
潛在失效模式 功能要求 (Pontential (Functional Failure Requirement) Model)
FMEA的起源
FMECA Failure Mode Effects and Criticality Analysis
>>1950’s起源于宇航和美国军方 >>对关注的问题加以分类和排列 >>将评定结果作为预防的目标 >>坚持安全的观点
《礼记·中庸》:“凡事预则立,不预则废。”
6
FMEA-ASIR
FMEA的起源
【观念篇-建立正确观念】
三个基本观念
FMA FEA Criticality Analysis Corrective Action
强调事前预防(设计与制程) 动态
FMEA的分类(DFMEA /PFMEA /DPFMEA)
8
FMEA-ASIR
失 效 模 式 分 析 (Failure Model and Effects Analysis,简称FMEA)是一有系统的跨功能小组进行的 事先预防活动 认识-产品及制程的潜在失效模式。 评估-产品及制程的失效之影响。 消除或减少潜在失效发生的改善措施,确认其成效。
4.1问卷调查的方式,可分为Closed/Open两种方式); 4.2如何设计问卷具备相当的技巧: a.需要调查的项目放至最前,被调查人的信息放于最后; b.设立激励项目;(有高度意愿参与) c.设定一个考察项目,确认调查之有效性
10
FMEA-ASIR
FMEA的10大要素
5.QFD及DOE充分运用于FMEA分析中; 6.用制程展开找出CCP(关键制程管制); 7. 盘点现有管制方法,对重要的站别或制程作预防对策;其 它一般站别或制程现场管理; 8.E.C.R.S.在Process mapping中就要求同时使用以优化制 造流程.Eliminate combination reset simplify 9.对高风险项目(RPN高)作建议对策之实施,仅可改善P或D 值,使其下降,较难改变S的值(RPN-Risk Priority Number)风险关键指 数 10.FMEA不是一门功课,需要改变为一项工作,确认效果最 为重要.
預防
偵測
(Prevention) (Detection)
功率节点打螺 未鎖緊
扭力不夠 4
電鎖扭力變 1 組長早中晚分別扭力計
钉
异
量測扭力
4
FMEA-ASIR
意识进展的五个阶段
质量是检验出来的
质量是制造出来的
过程
质量是设计出来的
关键
质量是管理出来的
质量是习惯出来的
5
FMEA-ASIR
FMEA-ASIR
潜在失效模式分析FMEA
1
FMEA-ASIR
F重点) FMEA的应用篇(说明重点) FMEA的操作步骤篇(RPN&顾客的重要需求&讨论/发表) FMEA的案例讲解与工具综合运用篇(确定分析对象-流
程分析与流程展开;失效模式与效应;原因分析、管制与改善)
9
FMEA-ASIR
FMEA的10大要素
1.事先的预防是重点; 2.从VOC(客户的需求)转至VOE(产品设计),进而转至 VOM(制造流程设计); 3.发生率:原因造成失效的概率
管制的有效性:[设计]在于 研发端R&D的Review/Testing; [制程]在于工厂端Monitor/Inspecting;
潛在失效潛 在效應 (Potential
Effect(s) of Failure
嚴重 分類 潛在原因/失 度(S) Class 效機制 發
(Pontent 生 Cause(s)/Mec 度
hanism(s) of (P)
Failure
現行的製程管制(Current Process Design Controls)