数控车床螺纹切削循环指令编程
螺纹切削循指令G82
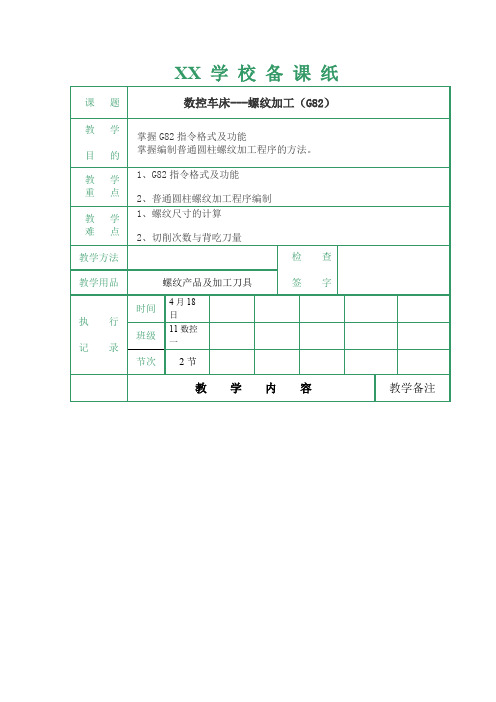
XX 学校备课纸课题数控车床---螺纹加工(G82)教学目的掌握G82指令格式及功能掌握编制普通圆柱螺纹加工程序的方法。
教学重点1、G82指令格式及功能2、普通圆柱螺纹加工程序编制教学难点1、螺纹尺寸的计算2、切削次数与背吃刀量教学方法教学用品螺纹产品及加工刀具检查签字时间4月18日班级11数控一执行记录节次2节教学内容教学备注板书提问口语提问<教学准备>老师学生相互问好、点名考勤。
<复习引入>1:G32、G80、命令的格式为?答:G32 X____ Z____ F ____G80 X____ Z____ I ____F____2: 数控车削的表面质量和那些参数有关?答:转速与进给量旷课学生登记用时2分钟通过复习G32切削螺纹指令编程格式,总结G32编程的特点,编写的程序冗长繁琐。
引出简化螺纹编程指令G82-单行螺纹切削循环通过问题2联想,假如转速慢进给量大的情况下工件表面是什么样子的?10分钟XX 学校备课纸教学内容教学备注板书<新课讲授>一、数控切削螺纹的程序指令:直螺纹切削循环G82 X_ Z_ R_ E_ I_ C_ P_ F_在有退刀槽的的工件中指令格式简化为:G82 X_ Z_ I_ F_参数说明:X、Z:螺纹终点坐标F:螺纹导程,即主轴转一圈,刀具相对于工件的进给值,故螺纹切削时转速不宜过高。
I:螺纹起点与终点半径查讲解格式其中着重XZ坐标字F和G01、G02等指令中X ZF的不同用时10分钟画略图二、G82走刀轨迹讲解和普车加工步骤一致讲解由于刀具刀尖的形状和外圆刀具的不同所引起。
XX 学校备课纸教学内容教学备注做重点说明.板书板书注:在数控车床上车螺纹时,沿螺距方向的,向进给应和车床主轴的旋转保持严格的速比关系,考虑到刀具从停止状态到达指定的进给速度或从指定的进给速度降为零,驱动系统必有一个过渡过程,因此沿轴向进给的加工路线长度,除保证螺纹长度外,还应增加刀具导入距离δ和导出距离δ’,δ和δ’的数值与车床拖动系统的动态特性、螺纹的螺距和精度有关。
数控车床螺纹切削循环指令编程
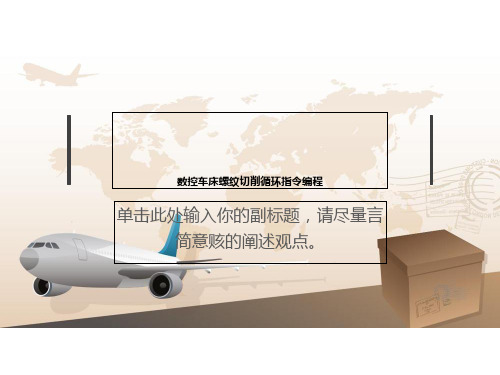
M 20—5g 6g— S
旋合长度代号 顶径公差带代号
中径公差带代号
公称直径
普通螺纹代号
4.螺纹标记含义(2)
(2)内螺纹标记 内螺纹标记如图所示。
M20×1.5—6H—S— LH
螺纹旋向 螺纹短旋合长度 中径和顶径公差带代号 螺距(指细牙) 公称直径 普通螺纹代号
4.螺纹标记含义(3)
(3)关于螺纹标记的几点说明: 1)对于粗牙螺纹螺距,可以省略标注其螺距项, 而细牙螺纹则必须标注; 2)对于多线螺纹,采用“公称直径×Ph导程P螺距 ”方式标注,或者在后面增加括号用英文进行说明 ,如两线为“two starts”,三线为“three starts”;
4.螺纹车刀的安装与找正(2)
4.螺纹车刀的安装与找正(3)
为了保证装刀要求,在装夹外螺纹车刀时 常采用角度样板找正螺纹刀尖角度,如图 所示,将样板靠在工件直径最大的素线上, 以此为基准调整刀具角度。
4.螺纹车刀的安装与找正(4)
4.螺纹车刀的安装与找正(5)
5.螺纹车削刀具切入与 切出行程的确定(1)
4.螺纹标记含义(4)
(3)关于螺纹标记的几点说明: 3)对于左旋螺纹,应在旋合长度之后标注 “LH”代号,右旋螺纹不需要标注; 4)对于螺纹旋合长度,分为三组,即短旋合长 度(S)、中等旋合长度(N)和长旋合长度( L),一般采用中等旋合长度。
二、螺纹加工工艺设计
1.螺纹加工走刀路线设计(1)
数控车床螺纹切削循环指令编程
单击此处输入你的副标题,请尽量言 简意赅的阐述观点。
项目11 数控车床螺纹切 削循环指令编程
一、螺纹基础知识
1.常见螺纹类型(1)
(1)按照用途分类 螺纹按用途不同可 分为联接螺纹和传动螺纹。
数控车床循环指令详解
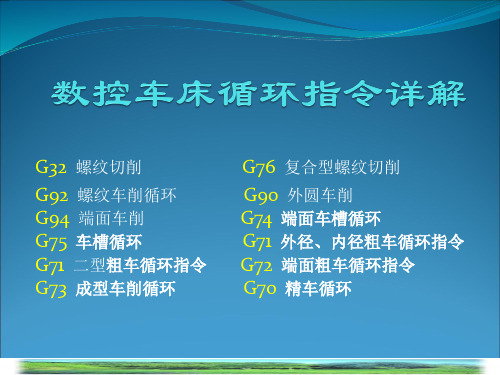
(4)Q nf是指定精加工路线的最后一个程序段的段号; (5)U u是X方向上的精加工余量,直径值; (6)W w是Z方向上的精加工余量。 (7)粗车过程中从程序段号Pns~Qnf之间的任何F 只有G71指令中指定的F、S、T功能有效。
图16.6
G71有两种情况,也就是一型和二型。
一型:也就是沿X轴同一方向递增或递减。一型
工序3 精车加工 精车
G00 X150; Z150; N4; S300 M03 T0303; G00 X48 Z-64; G01 X2 F0.05; G00 X150; Z150; M05; M30;
工序4 切断 程序结束
地址 内容
说明
1851
X向间隙数值。数值为半径值。
1852
Z向间隙数值
3204 0/1 PAR设置0是为中括号[ ]。 设置1是为小括号( )
G32 螺纹切削
G92 螺纹车削循环 G94 端面车削 G75 车槽循环 G71 二型粗车循环指令 G73 成型车削循环
G76 复合型螺纹切削
G90 外圆车削 G74 端面车槽循环 G71 外径、内径粗车循环指令 G72 端面粗车循环指令 G70 精车循环
该指令用于车削等螺距直螺纹、锥螺纹。
格式:G32 X(U)__ Z(W)__ F__
格式:G92 X(U) Z(W) R F
XZ螺纹终点坐标,R表示螺纹起始点与终点在X 向的坐标增量值(半径值),圆柱螺纹切削R为0可 省略。一般外锥螺纹R为负值,内锥螺纹R为正值。
T0202 (螺纹刀) M3 S400 G0 X22 Z5 G92 X20 Z-15 R-0.625 I14 F2 X19.6 I14 X19.2 I14 X18.9 14 X18.75 14 X18.631 I14 X18.631 I14 (精车) G0 X100 Z100 M5 M30
数控车床螺纹车削指令
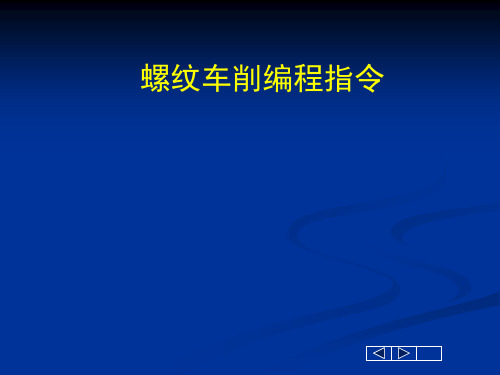
(3)在螺纹(锥螺纹)加工过程中不要使用恒线速控制功 能。从粗加工到精加工,主轴转速必须保持一常数。否 则,螺距将发生变化。 (4)对于锥螺纹,当锥度斜角在45°以下时,螺距F为Z 轴方向的螺纹导程;当锥度斜角在45°~90°时,螺距 F为X轴方向的螺纹导程。 (5)G32指令不允许循环操作,螺纹加工前或加工后的程 序段要求有退刀及返回程序,可使用G00或G01退刀程序 和返回程序。 (6)螺纹起点与终点径向尺寸的确定 径向起点(螺纹大径)由外圆车削保证。按螺纹公差确 定其尺寸范围。 径向终点(螺纹小径)一般分数次进给达到。
缺点
两侧切削刃同时切削工件,切 削力较大,而且排削困难,造 成两切削刃容易磨损。在切削 螺距较大的螺纹时,由于切削 深度较大,刀刃磨损较快,从 而造成螺纹中径产生误差。 导程小于3mm的螺纹加工。
应用
导程大于3mm的螺纹加工。
注:加工高精度、大螺距的螺纹,可采用G92、G76混用的办法,即 先用G76进行螺纹粗加工,再用G92进行精加工。需要注意的是粗精 加工时的起刀点要相同,以防止螺纹乱扣的产生。
其中:X、Z 为螺纹终点绝对坐 标值。 U、W 为螺纹终点相对螺 纹起点坐标增量。 F为螺纹导程(螺距), 单位:mm/r。
2、两种特殊格式
G32 X... Z... F... 圆锥螺纹 G32 Z... F... 圆柱螺纹 G32 X... F... 端面螺纹
RL 3.605 1800 RL 2 1800
三、常用的螺纹加工进给次数与背吃刀量表
米制螺纹
螺距 牙深 1次 背 吃 刀 量 及 切 削 次 数 2次 3次 4次 5次 1.0 0.649 0.7 0.4 0.2 1.5 0.947 0.8 0.6 0.4 0.2 2.0 1.299 0.9 0.6 0.6 0.4 0.1 2.5 1.624 1.0 0.7 0.6 0.4 0.4 3.0 1.949 1.2 0.7 0.6 0.4 0.4 3.5 2.273 1.5 0.7 0.6 0.6 0.4 4.0 2.598 1.5 0.8 0.6 0.6 0.4
数控车床螺纹切削循环G92

数控车床螺纹切削循环G92(FANUC-6T)1、G92指令格式:螺纹切削循环G92为简单螺纹循环,该指令可切削锥螺纹和圆柱螺纹,其循环路线与前述的单一形状固定循环基本相同,只是F后边的进给量改为螺距值即可,其指令格式为:G92 X(U)—Z(W)—I—F—图4—40a所示为圆锥螺纹循环,图b所示为圆柱螺纹循环。
刀具从循环点开始,按A、B、C、D进行自动循环,最后又回到循环起点A。
图中虚线表示按R快速移动,实线表示按F指定的工作进给速度移动。
X、Z为螺纹终点(C点)的坐标值;U、W为螺纹终点坐标相对于螺纹起点的增量坐标,I为锥螺纹起点和终点的半径差。
加工圆柱螺纹时I为零,可省略。
图4-40 螺纹循环G922.(1)螺纹牙型高度(螺纹总切深)螺纹牙型高度是指在螺纹牙型上,牙顶到牙底之间垂直于轴线的距离。
图4—41所示,它是车削时;车刀总切入深度。
图4—41 螺纹牙型高度根据GBl92~197—81普通螺纹国家标准规定,普通螺纹的牙型理论高度H=0.866P,实际加工时,由于螺纹车刀刀尖半径的影响,螺纹的实际切深有变化。
根据GBl97—81规定螺纹车刀可,在牙底最小削平高度H/8处削平或倒圆。
则螺纹实际牙型高度可按下式计算:h=H一2(H/8)=0.6495P式中: H--螺纹原始三角形高度,H=0.866P(mm);p--螺距(mm)。
(2)螺纹起点与螺纹终点径向尺寸的确定螺纹加工中,径向起点(编程大径)的确定决定于螺纹大径。
例如要加工M30x2—6g外螺纹,自GBl97—81知:螺纹大径基本偏差为ES=-0.038mm;公差为Td=0.28mm;则螺纹大径尺寸为φ30-0.318-0.038mm.所以螺纹大径应在此范围内选取,并在加工螺纹前,由外圆车削来保证。
径向终点(编程小径)的确定决定于螺纹小径。
因为编程大径确定后,螺纹总切深在加工中是由编程小径(螺纹小径)来控制的。
螺纹小径的确定应考虑满足螺纹中径公差要求。
螺纹切削循环指令

螺纹切削循环指令螺纹切削循环指令是数控加工中常用的一种循环指令,用于在工件上加工螺纹。
本文将从螺纹加工的原理、G76指令的语法、参数和应用等方面进行详细介绍。
一、螺纹加工的原理在数控加工中,螺纹加工是一种常见的加工方式。
它是通过工具在工件上进行旋转和移动,使工件表面形成螺纹形状。
螺纹加工的过程中,工具和工件之间需要保持一定的相对位置和角度,以保证加工出来的螺纹符合要求。
二、G76指令的语法G76指令是数控加工中用于螺纹加工的一种循环指令。
它的语法如下:G76 X_ Z_ I_ K_ P_ Q_ R_ L_其中,X_、Z_、I_、K_分别表示螺纹加工的起点坐标、终点坐标、螺纹半径、导程;P_表示螺纹加工的切削深度;Q_表示每次切削的进给量;R_表示每次切削的进给速度;L_表示螺纹加工的总长度。
三、G76指令的参数1. 起点和终点坐标:螺纹加工的起点和终点坐标是指螺纹的起始位置和结束位置,一般来说,起点坐标和终点坐标需要在同一直线上,并且保证工件表面平稳。
2. 螺纹半径和导程:螺纹半径和导程是指螺纹的半径和螺距。
螺纹半径和导程的大小决定了螺纹的形状和尺寸,一般需要根据工件的需求进行设置。
3. 切削深度:切削深度是指每次切削的深度,一般需要根据工件的材料和硬度进行调整,以保证切削效果和加工速度。
4. 进给量:进给量是指每次切削的进给距离,一般需要根据工件的材料和硬度进行调整,以保证加工效率和切削质量。
5. 进给速度:进给速度是指每次切削的进给速度,一般需要根据工件材料和硬度进行调整,以保证切削效果和加工速度。
6. 总长度:总长度是指螺纹加工的总长度,一般需要根据工件的需求进行设置,以保证加工效率和螺纹尺寸符合要求。
四、G76指令的应用G76指令是数控加工中用于螺纹加工的一种循环指令,它的应用范围非常广泛。
在实际加工中,可以使用G76指令进行内螺纹、外螺纹、左螺纹、右螺纹等各种类型的螺纹加工。
除此之外,还可以根据工件的需求进行相应的参数调整,以满足不同加工要求。
数控车螺纹加工指令编程

用G92进行圆柱螺纹加工
X Z
45°
3(F)
W 4(R)
1(R)
2(F)
2
XU
2
O
Z
格式:G92 X(U)_Z(W)_F_;
用G92进行圆锥螺纹加工
45°
X
Z
W
4(R)
3(F) 2(F)
R
1(R)
2
XU
2
O
Z
格式:G92 X(U)_Z(W)_R_F_;
例:如下图所示圆柱螺纹,螺纹导程为1.0 mm。 δ1=2 mm , δ2=1mm。 试编写螺纹加工程序
例:如下图所示圆锥螺纹,螺纹导程为1.5 mm。 δ1=2 mm , δ2=1mm。 试编写螺纹加工程序
四、简单螺纹切削循环指令G92 该指令的循环路线与前述的G90指令基本相同, 只是F后面的进给量改为螺纹导程即可。 格式:G92 X(U)_Z(W)_R_F_; 其中:X、Z为螺纹终点坐标值
U、W为螺纹起点坐标到终点坐标的增量值 R为锥螺纹大端和小端的半径差。
例:如下图所示圆锥螺纹,螺纹导程为1.5 mm。 δ1=2 mm , δ2=1mm。 试编写螺纹加工程序
五、螺纹切削循环指令G76 格式:G76 X_Z_I_K_D_F_A_P_; 其中:X为终点处的X坐标值 ;Z为终点处的Z坐标值;
I为螺纹加工起点和终点的差值; K为螺纹牙型高度,按半径值编程; D为第一次循环时的切削深度; F为螺纹导程; A为螺纹牙型顶角角度,可在0°~120°之间任意 选择; P为指定切削方式,一般省略或写成P1,表示等 切削量单边切削。
六、螺纹加工方法
螺纹加工常用切削循环方式。 两种方式:直进法(G32、G92)
FANUC数控车床螺纹切削复合循环编程实例

1、螺纹切削复合循环(G76)G76 P010060 Q300G76 Z*** P2600 Q800 F4解释:第一行的P01、00、6001 :代表的是精加工循环次数00 : Z方向的退尾量60 :螺纹角度普遍都是60°的Q300:代表最后一刀的切深数值千进位 300也就是:精加工余量第二行的X、Z为终点坐标P2600:是螺纹牙高 *螺距Q800 :第一刀的切深量同上Q算法一样,F4 :螺距2、螺纹切削复合循环(G76)指令格式 : G76 Pm r a QΔdmin RdG76 X(U)_ Z(W)_Ri Pk QΔd Ff指令功能:该螺纹切削循环的工艺性比较合理,编程效率较高,螺纹切削循环路线及进刀方法如图32所示。
图32 螺纹切削复合循环路线及进刀法指令说明:①m表示精车重复次数,从1—99;②r表示斜向退刀量单位数,或螺纹尾端倒角值,在—之间,以为一单位,(即为的整数倍),用00—99两位数字指定,(其中f为螺纹导程);③a表示刀尖角度;从80°、60°、55°、30°、29°、0°六个角度选择;④Δdmin:表示最小切削深度,当计算深度小于Δdmin,则取Δdmin 作为切削深度;⑤d:表示精加工余量,用半径编程指定;Δd :表示第一次粗切深(半径值);⑥X 、Z:表示螺纹终点的坐标值;⑦U:表示增量坐标值;⑧W:表示增量坐标值;⑨I:表示锥螺纹的半径差,若I=0,则为直螺纹;⑩k:表示螺纹高度(X方向半径值);3、G76螺纹车削实例图33所示为零件轴上的一段直螺纹,螺纹高度为,螺距为6,螺纹尾端倒角为,刀尖角为60°,第一次车削深度,最小车削深度,精车余量,精车削次数1次,螺纹车削前先精车削外圆柱面,其数控程序如下:图33 螺纹切削多次循环G76指令编程实例O0028 /程序编号N0 G50 ; /设置工件原点在左端面N2 G30 U0 W0; /返回第二参考点N4 G96 S200 T0101 M08 M03; /指定切削速度为200m/min,调外圆车刀N6 G00 ; /快速走到外圆车削起点(,)N7 G42 G01 ;N8 ; /外圆车削N9 G40 G00 ;N10 G30 U0 W0;N12 G97 S800 T0202 M08 M03; /取消恒切削速度,指定主轴转速800r/min,调螺纹车刀N14 G00 ; /快速走到螺纹车削循环始点(,)N16 G76 P011160 ; /循环车削螺纹N18 G76 ;N20 G30 U0 W0 M09;N22 M30;4、附加FANUC系统后台编辑功能BG-EDT 后台编辑运行程序时,按操作--BC-EDG--DIR--输入程序号--搜索.就可以编辑O-SRH O搜索(用来调用程序的);SRH ↓ 在本程序段内向下搜索关键字(如程序太长时,要更改进给速度,可按F,然后按个SRH,就可以一下子找到F指令;SRH↑ 在本程序中向上搜索,。
数控车床螺纹切削循环G92-推荐下载
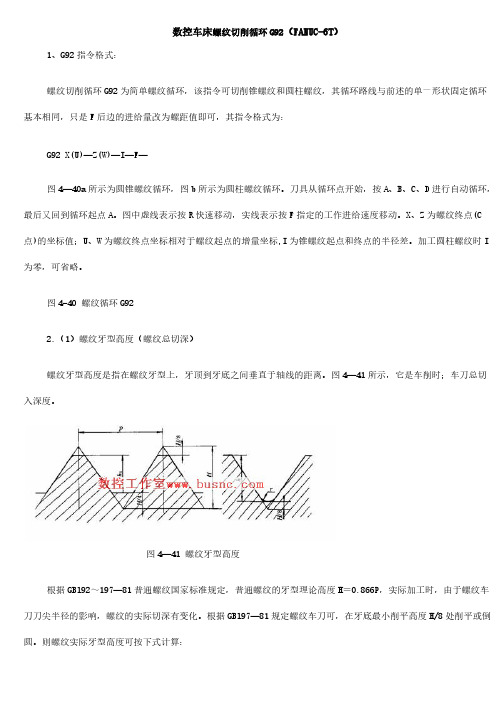
数控车床螺纹切削循环G92(FANUC-6T)1、G92指令格式:螺纹切削循环G92为简单螺纹循环,该指令可切削锥螺纹和圆柱螺纹,其循环路线与前述的单一形状固定循环基本相同,只是F后边的进给量改为螺距值即可,其指令格式为:G92 X(U)—Z(W)—I—F—图4—40a所示为圆锥螺纹循环,图b所示为圆柱螺纹循环。
刀具从循环点开始,按A、B、C、D进行自动循环,最后又回到循环起点A。
图中虚线表示按R快速移动,实线表示按F指定的工作进给速度移动。
X、Z为螺纹终点(C 点)的坐标值;U、W为螺纹终点坐标相对于螺纹起点的增量坐标,I为锥螺纹起点和终点的半径差。
加工圆柱螺纹时I 为零,可省略。
图4-40 螺纹循环G922.(1)螺纹牙型高度(螺纹总切深)螺纹牙型高度是指在螺纹牙型上,牙顶到牙底之间垂直于轴线的距离。
图4—41所示,它是车削时;车刀总切入深度。
图4—41 螺纹牙型高度根据GBl92~197—81普通螺纹国家标准规定,普通螺纹的牙型理论高度H=0.866P,实际加工时,由于螺纹车刀刀尖半径的影响,螺纹的实际切深有变化。
根据GBl97—81规定螺纹车刀可,在牙底最小削平高度H/8处削平或倒圆。
则螺纹实际牙型高度可按下式计算:h=H一2(H/8)=0.6495P式中: H--螺纹原始三角形高度,H=0.866P(mm);p--螺距(mm)。
(2)螺纹起点与螺纹终点径向尺寸的确定螺纹加工中,径向起点(编程大径)的确定决定于螺纹大径。
例如要加工M30x2—6g外螺纹,自GBl97—81知:螺纹大径基本偏差为ES=-0.038mm;公差为Td=0.28mm;则螺纹大径尺寸为φ30-0.318-0.038mm.所以螺纹大径应在此范围内选取,并在加工螺纹前,由外圆车削来保证。
径向终点(编程小径)的确定决定于螺纹小径。
因为编程大径确定后,螺纹总切深在加工中是由编程小径(螺纹小径)来控制的。
螺纹小径的确定应考虑满足螺纹中径公差要求。
螺纹切削单一固定循环指令g92

06 G92指令的未来发展与展 望
技术发展趋势
智能化
随着人工智能和机器学习技术的不断发展,G92指令将进一步实现 智能化,能够自动识别和优化切削参数,提高加工效率和精度。
集成化
未来,G92指令将更加集成化,能够与其他数控加工指令和软件进 行无缝对接,实现更高效、便捷的加工过程控制。
定制化
针对不同材料、不同加工需求,G92指令将提供更加定制化的解决方 案,满足个性化加工需求。
螺纹切削单一固定循环指令G92
contents
目录
• G92指令概述 • G92指令的格式与参数 • G92指令的应用场景 • G92指令的注意事项与优化建议 • G92与其他螺纹切削指令的比较 • G92指令的未来发展与展望
01 G92指令概述
G92指令的定义
G92指令是数控车床中用于切削螺纹 的单一固定循环指令。
THANKS FOR WATCHING
感谢您的观看
它通过一个程序段来定义切削螺纹的 整个过程,简化了编程步骤。
G92指令的用途
G92指令主要用于车削圆柱螺纹和圆锥螺纹。 它能够实现直进法或斜进法切削螺纹,满足不同加工需求。
G92指令的特点
G92指令具有简单、方便、高效的特点。
它只需要一个程序段就可以完成整个切削过程, 减少了编程工作量。
G92指令可以通过调整参数实现多种切削效果, 如切削深度、螺纹长度等,提高了加工灵活性。
05 G92与其他螺纹切削指令 的比较
与G76指令的比较
加工方式
G92是单一固定循环指令,而G76是多段固 定循环指令。
编程方式
G92的编程方式相对简单,只需要指定螺纹的起点 和终点即可。而G76需要指定更多的参数,如刀具 半径、主轴转速等。
螺纹加工的编程
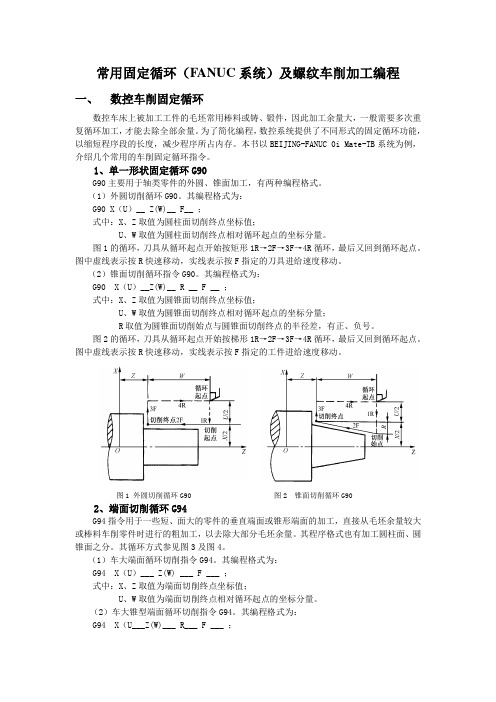
常用固定循环(FANUC系统)及螺纹车削加工编程一、数控车削固定循环数控车床上被加工工件的毛坯常用棒料或铸、锻件,因此加工余量大,一般需要多次重复循环加工,才能去除全部余量。
为了简化编程,数控系统提供了不同形式的固定循环功能,以缩短程序段的长度,减少程序所占内存。
本书以BEIJING-FANUC 0i Mate-TB系统为例,介绍几个常用的车削固定循环指令。
1、单一形状固定循环G90G90主要用于轴类零件的外圆、锥面加工,有两种编程格式。
(1)外圆切削循环G90。
其编程格式为:G90 X(U)__ Z(W)__ F__ ;式中:X、Z取值为圆柱面切削终点坐标值;U、W取值为圆柱面切削终点相对循环起点的坐标分量。
图1的循环,刀具从循环起点开始按矩形1R→2F→3F→4R循环,最后又回到循环起点。
图中虚线表示按R快速移动,实线表示按F指定的刀具进给速度移动。
(2)锥面切削循环指令G90。
其编程格式为:G90 X(U)__Z(W)__ R __ F __ ;式中:X、Z取值为圆锥面切削终点坐标值;U、W取值为圆锥面切削终点相对循环起点的坐标分量;R取值为圆锥面切削始点与圆锥面切削终点的半径差,有正、负号。
图2的循环,刀具从循环起点开始按梯形1R→2F→3F→4R循环,最后又回到循环起点。
图中虚线表示按R快速移动,实线表示按F指定的工件进给速度移动。
图1 外圆切削循环G90 图2 锥面切削循环G902、端面切削循环G94G94指令用于一些短、面大的零件的垂直端面或锥形端面的加工,直接从毛坯余量较大或棒料车削零件时进行的粗加工,以去除大部分毛坯余量。
其程序格式也有加工圆柱面、圆锥面之分。
其循环方式参见图3及图4。
(1)车大端面循环切削指令G94。
其编程格式为:G94 X(U)___ Z(W) ___ F ___ ;式中:X、Z取值为端面切削终点坐标值;U、W取值为端面切削终点相对循环起点的坐标分量。
(2)车大锥型端面循环切削指令G94。
螺纹切削循环指令编程
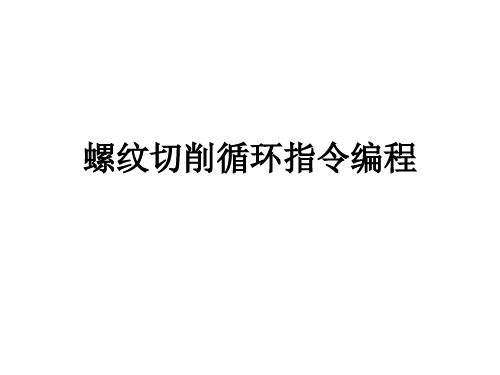
3、车削螺纹前圆柱体(孔)预加工尺寸控制 、车削螺纹前圆柱体(
4、螺纹车刀的安装与找正 、
4、螺纹车刀的安装与找正 、
4、螺纹车刀的安装与找正 、
4、螺纹车刀的安装与找正 、
4、螺纹车刀的安装与找正 、
5、螺纹车削刀具切入与切出行程的确定 、
5、螺纹车削刀具切入与切出行程的确定 、
三、螺纹切削单一固定循环指令编 程(G92) )
4、编程举例 、
4、编程举例 、
四、螺纹切削复合循环指令编程 (G76) )
1、指令格式 、
1、指令格式 、
1、指令格式 、
2、刀具走刀路线分析 、
2、刀具走刀路线分析 、
2、刀具走刀路线分析 、
3、指令应用说明 、
4、编程举例 、
4、编程举例 、
零件加工工艺分析: 零件加工工艺分析: ●对零件进行外圆表面粗、精加工并倒角至图纸尺 寸; ●螺纹退刀槽加工; ●M20×2.5螺纹粗、精加工; ●工件切断并保证全长。 零件加工所使用的刀具: 零件加工所使用的刀具: ⑴外圆车刀T0101; ⑵切槽刀T0202(刀宽为3mm); ⑶60°螺纹车刀T0303。
1、指令格式 、
1、指令格式 、
2、刀具走刀路线分析 、
3、指令应用说明 、
3、指令应用说明 、
4、编程举例 、
编写如图所示工件加工程序, 编写如图所示工件加工程序,工件 毛坯为¢32mm. 毛坯为¢32mm.
4、编程举例 、
零件加工工艺路线分析: 零件加工工艺路线分析: ⑴工件外圆表面的粗加工与精加工并倒角; ⑵螺纹退刀槽加工; ⑶螺纹的粗加工与精加工。 零件加工所使用的刀具: 零件加工所使用的刀具: ⑴外圆车刀T0101; ⑵切槽刀T0202(刀宽为3mm); ⑶60°螺纹车刀T0303。
- 1、下载文档前请自行甄别文档内容的完整性,平台不提供额外的编辑、内容补充、找答案等附加服务。
- 2、"仅部分预览"的文档,不可在线预览部分如存在完整性等问题,可反馈申请退款(可完整预览的文档不适用该条件!)。
- 3、如文档侵犯您的权益,请联系客服反馈,我们会尽快为您处理(人工客服工作时间:9:00-18:30)。
1.螺纹加工走刀路线设计(2)
1.螺纹加工走刀路线设计(3)
(2)斜进式螺纹加工 刀具沿着螺纹一侧顺次 进刀。这种加工方法适合于大螺距螺纹加工, 在螺纹精度要求不是很高的情况下加工更为方 便,可以做到一次成型。在加工较高精度螺纹 时,可以先采用斜进法粗加工,然后用直进法 进行精加工。但要注意刀具起始点定位要准确, 否则会产生“乱牙”现象,造成零件报废。
3.螺纹公差等级及尺寸偏差计算(4)
(2)螺纹基本偏差 螺纹公差带位置是由基 本偏差确定的,螺纹基本牙型是计算螺纹偏差 的基准。内、外螺纹的公差带相对于基本牙型 的位置,与圆柱体公差带位置一样,由基本偏 差确定。 ●对于外螺纹,基本偏差是上偏差(es);
●对于内螺纹,基本偏差是下偏差(EI)。
3.螺纹公差等级及尺寸偏差计算(5) 在普通螺纹标准中:
(1)螺纹公差等级 由于普通螺纹中径(D2、 d2)是决定配合性质的主要尺寸,按照 GB197-81《普通螺纹 公差与配合(直径 1~355㎜)》规定,普通螺纹公差规定有内、 外螺纹中径公差(TD2、Td2)、内螺纹小径 公差(TD1)和外螺纹大径公差(Td)。内、 外螺纹中径公差和顶径公差等级如表所示。
●对于内螺纹规定了代号为G、H的两种基
本偏差;
●对于外螺纹规定了代号为e、f、g、h四种
基本偏差,如图所示。
3.螺纹公差等级及尺寸偏差计算(6)
内螺纹公差带
3.螺纹公差等级及尺寸偏差计算(7)
外螺纹公差带
4.螺纹标记含义(1)
(1)外螺纹标记 外螺纹标记如图所示。 M 20—5g S 6g— 旋合长度代号一、螺纹Βιβλιοθήκη 础知识1.常见螺纹类型(1)
(1)按照用途分类 螺纹按用途不同可 分为联接螺纹和传动螺纹。
1.常见螺纹类型(2)
(2)按照牙型分类 按牙型不同分为三角形、 圆形、矩形、梯形、锯齿形螺纹。 (3)按照螺旋线旋向分类 按螺旋线方向不 同分为右旋螺纹和左旋螺纹。 (4)按照螺旋线数分类 按螺旋线数多少分 为单线螺纹和多线螺纹。 (5)按照母体形状分类 按母体形状不同分 为圆柱螺纹和圆锥螺纹。
4.螺纹标记含义(4)
(3)关于螺纹标记的几点说明: 3)对于左旋螺纹,应在旋合长度之后标注 “LH”代号,右旋螺纹不需要标注; 4)对于螺纹旋合长度,分为三组,即短旋合长 度(S)、中等旋合长度(N)和长旋合长度 (L),一般采用中等旋合长度。
二、螺纹加工工艺设计
1.螺纹加工走刀路线设计(1)
2.螺纹加工切削用量的选用(6)
(2)进给速度 螺纹加工时数控车床主轴转 速和工作台纵向进给量存在严格数量关系, 即主轴旋转 1 转,工作台移动一个待加工工 件螺纹导程距离。因此在加工程序中只要给 出主轴转速和螺纹导程,数控系统会自动运 算并控制工作台纵向移动速度。
2.螺纹加工切削用量的选用(7)
2.普通螺纹尺寸计算( 3 ) (5)牙型高度 h 牙型 1
高度表达式为:
5 h1 H 0.5143P 8
(6)外螺纹小径d1 螺纹小径表达式为:
外
d1 d 1.0825P
(7)内螺纹小径D1 内 螺纹小径的基本尺寸与 外 螺 纹 小 径 相 同 (D1=d1)。
3.螺纹公差等级及尺寸偏差计算(1)
3.螺纹公差等级及尺寸偏差计算(2)
螺纹公差等级
螺纹直径 中径 D2 公差等级
内螺纹
小径(顶径) D1 中径 大径(顶径) d2 d
4、5、6、7、8
外螺纹
3、4、5、6、7、8、 9
4、6、8
3.螺纹公差等级及尺寸偏差计算(3) 各公差等级中3级最高,9级最低,6级为 基本级。内螺纹小径公差值和外螺纹大径 公差值可以依据螺纹螺距和公差等级的不 同查表获得;内、外螺纹中径公差值可以 依据螺纹公称直径大小和精度等级的不同 查表获取(相关手册或国家标准包含有螺 纹公差表)。
顶径公差带代号
中径公差带代号 公称直径 普通螺纹代号
4.螺纹标记含义(2)
(2)内螺纹标记 内螺纹标记如图所示。 M20×1.5—6H—S— LH
螺纹旋向
螺纹短旋合长度
中径和顶径公差带代号
螺距(指细牙)
公称直径
普通螺纹代号
4.螺纹标记含义(3)
(3)关于螺纹标记的几点说明: 1)对于粗牙螺纹螺距,可以省略标注其螺距项, 而细牙螺纹则必须标注; 2)对于多线螺纹,采用“公称直径×Ph导程P螺距” 方式标注,或者在后面增加括号用英文进行说明, 如两线为“two starts”,三线为“three starts”;
1.螺纹加工走刀路线设计(4)
2.螺纹加工切削用量的选用(5)
(1)主轴转速 螺纹加工时主轴转速可用下 面经验公式进行计算: 1200 n K P P—工件螺距 K—保险系数,一般取80 如果数控系统能够支持高速螺纹加工,则可 采用高档螺纹加工刀具,主轴转速按照线速 度200m/min选取;而经济性数控车床如果 采用高主轴转速加工螺纹则会出现乱牙现象。
(3)背吃刀量 如果螺纹牙型较深、螺距较 大,则可采用分次进给方式进行加工。每次 进给的背吃刀量用螺纹深度减去精加工背吃 刀量所得的差按递减规律分配 。常用螺纹加 工切削次数与背吃刀量数值如表所示。
螺距 牙深 1次 2次
0.649 0.7 0.4
1.0 螺纹加工切削用量的选用( 1.5 2.0 2.5 3.0 3.5 2. 84.0 ) 0.974 0.8 0.6 1.299 0.9 0.6 1.624 1.0 0.7 1.949 1.2 0.7 2.273 1.5 0.7 2.598 1.5 0.8
2.普通螺纹尺寸计算(1)
(1)螺纹的公称直径 就是大径的基本尺寸(D 或d)。 (2)原始三角形高度 H 原始三角形高度H 表达式为:
3 H P 0.866P 2
2.普通螺纹尺寸计算(2)
( 3 )中径( d2 、 D2 ) 中径表达式为
d 2 D2 d 0.6495 P
(4)削平高度 外螺纹 牙顶和内螺纹牙底均在 H/8处削平;外螺纹牙底 和内螺纹牙顶均在H/4处 削平。