机械减速器齿轮传动的优化设计
机械齿轮传动系统的动力学分析与优化

机械齿轮传动系统的动力学分析与优化齿轮传动是一种常见的动力传递机构,具有传递力矩大、传动效率高等优点,在工业生产中得到广泛应用。
但是,由于齿轮传动系统存在着一些固有的问题,如齿轮啮合时的振动和噪音、齿面磨损等,因此对其进行动力学分析和优化是非常重要的。
1. 动力学分析1.1 齿轮啮合的动力学模型齿轮啮合过程中,齿轮之间存在着瞬时的压力、速度和加速度变化。
可以通过建立齿轮啮合的动力学模型来分析其动态特性。
常用的方法包括等效单齿转动法和有限元法。
通过分析齿轮齿面接触应力和应力分布,可以预测系统的振动和噪音水平,为后续的优化提供依据。
1.2 动力学参数的测量和计算为了进行动力学分析,需要测量和计算一些关键参数,如齿轮的啮合刚度、传递误差、滚子轴承的刚度等。
其中,传递误差是影响齿轮传动系统性能的重要因素之一,其大小与齿轮加工质量、啮合配合、齿轮轴向和径向跳动等因素有关。
通过合理的测量方法和计算模型,可以准确地获取这些参数,并对系统进行分析。
2. 动力学优化2.1 齿轮传动系统的振动和噪音控制由于齿轮啮合时的动态特性,齿轮传动系统常常会产生振动和噪音。
为了减小振动和噪音的水平,可以从多个方面进行优化,如合理设计齿形、减小啮合间隙、提高齿轮加工精度等。
此外,也可以采用减振装置,如弹性联轴器、减震器等,来降低系统的振动能量传递。
2.2 传动效率的提高传动效率是衡量齿轮传动系统性能的重要指标之一。
为了提高传动效率,可以从减小传动误差、改善齿轮表面质量、减小传动间隙等方面入手。
此外,合理选择润滑方式和润滑油,也可以有效地降低系统的摩擦和磨损,提高传动效率。
2.3 齿轮传动系统的寿命预测齿轮传动系统的寿命是评估其使用寿命和可靠性的重要指标。
通过综合考虑齿轮的强度、疲劳寿命和磨损等影响因素,可以建立寿命预测模型,对系统进行寿命预测和优化设计。
此外,还可以通过监测齿轮的工作状态和健康状况,进行实时的故障诊断和维护。
3. 总结齿轮传动系统的动力学分析和优化是提高其性能和可靠性的重要手段。
减速器优化设计论文

1 前言 (2)1.1复合形法减速器优化设计的意义 (2)1.1.1 机械优化设计与减速器设计现状 (2)1.1.2优化设计的步骤 (3)1.1.3减速器优化设计的分析 (5)1.1.4减速器的研究意义与发展前景 (6)1.2国内外发展状况 (7)1.2.1、国内减速器技术发展简况 (7)1.2.2、国内减速器技术发展简况 (8)1.3论文的主要内容 (9)2 齿轮啮合参数优化设计的数学模型的建立 (9)2.1设计变量的确定 (9)2.2目标函数的确定 (10)2.3约束条件的建立 (11)3优化设计方法-复合形法调优 (12)3.1复合形法介绍 (12)3.2复合形法计算步骤 (13)3.3单级圆柱齿轮减速器复合形法FORTRAN优化目标函数和约束函数子程序 (14)3.4优化结果 (16)4 减速器的常规设计 (16)4.1减速器的结构与性能介绍 (16)4.2.带传动零件的设计计算 (17)4.3齿轮的设计计算及结构说明 (18)4.4.联轴器的选择 (21)4.5.轴的设计及校核 (21)4.5.1.从动轴结构设计 (21)4.5.2.主动轴的设计 (22)4.5.3.危险截面的强度校核 (23)4.6.键的选择及校核 (25)4.7.轴承的选择及校核 (25)4.8.减速器润滑方式、密封形式 (25)4.8.1.密封 (26)4.8.2.润滑 (26)5优化结果分析 (26)6减速器3D简略设计过程(UG) (26)6.1.减速器机盖设计 (26)6.2减速器机座设计 (28)6.3轴的设计 (28)6.3.1传动轴的设计 (28)6.3.2齿轮轴的设计 (29)6.4齿轮的设计 (30)6.5轴承的设计(以大轴承为例) (32)6.5减速器的装配(其它零部件说明省略) (33)7 总结 (34)8 参考文献 (35)9 致谢 (36)1 前言1.1 复合形法减速器优化设计的意义1.1.1 机械优化设计与减速器设计现状机械优化设计是在电子计算机广泛应用的基础上发展起来的一门先进技术。
齿轮减速器传动比的最佳分配与优化设计
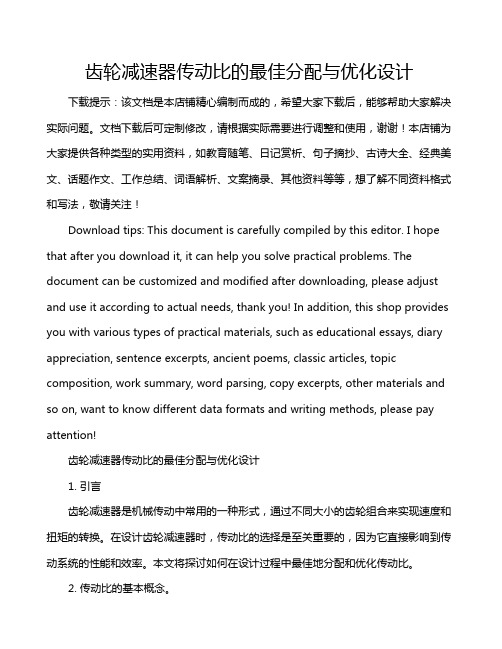
齿轮减速器传动比的最佳分配与优化设计下载提示:该文档是本店铺精心编制而成的,希望大家下载后,能够帮助大家解决实际问题。
文档下载后可定制修改,请根据实际需要进行调整和使用,谢谢!本店铺为大家提供各种类型的实用资料,如教育随笔、日记赏析、句子摘抄、古诗大全、经典美文、话题作文、工作总结、词语解析、文案摘录、其他资料等等,想了解不同资料格式和写法,敬请关注!Download tips: This document is carefully compiled by this editor. I hope that after you download it, it can help you solve practical problems. The document can be customized and modified after downloading, please adjust and use it according to actual needs, thank you! In addition, this shop provides you with various types of practical materials, such as educational essays, diary appreciation, sentence excerpts, ancient poems, classic articles, topic composition, work summary, word parsing, copy excerpts, other materials and so on, want to know different data formats and writing methods, please pay attention!齿轮减速器传动比的最佳分配与优化设计1. 引言齿轮减速器是机械传动中常用的一种形式,通过不同大小的齿轮组合来实现速度和扭矩的转换。
基于matlab的单级圆柱齿轮减速器优化设计
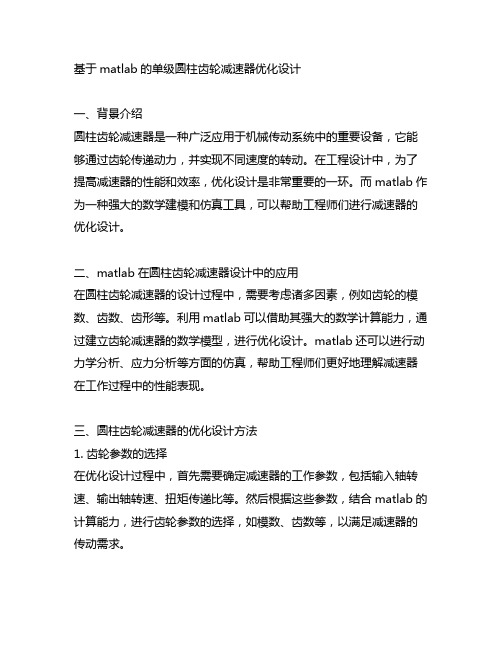
基于matlab的单级圆柱齿轮减速器优化设计一、背景介绍圆柱齿轮减速器是一种广泛应用于机械传动系统中的重要设备,它能够通过齿轮传递动力,并实现不同速度的转动。
在工程设计中,为了提高减速器的性能和效率,优化设计是非常重要的一环。
而matlab作为一种强大的数学建模和仿真工具,可以帮助工程师们进行减速器的优化设计。
二、matlab在圆柱齿轮减速器设计中的应用在圆柱齿轮减速器的设计过程中,需要考虑诸多因素,例如齿轮的模数、齿数、齿形等。
利用matlab可以借助其强大的数学计算能力,通过建立齿轮减速器的数学模型,进行优化设计。
matlab还可以进行动力学分析、应力分析等方面的仿真,帮助工程师们更好地理解减速器在工作过程中的性能表现。
三、圆柱齿轮减速器的优化设计方法1. 齿轮参数的选择在优化设计过程中,首先需要确定减速器的工作参数,包括输入轴转速、输出轴转速、扭矩传递比等。
然后根据这些参数,结合matlab的计算能力,进行齿轮参数的选择,如模数、齿数等,以满足减速器的传动需求。
2. 齿形的优化齿轮的齿形对于减速器的传动性能具有重要影响,通过matlab可以进行齿形的优化设计,以确保齿轮的传动效率和传动平稳性。
3. 传动效率的分析传动效率是评价减速器性能的重要指标之一,利用matlab可以进行减速器传动效率的分析,找出影响传动效率的因素,并进行优化设计,提高减速器的传动效率。
4. 结构强度的分析除了传动效率外,减速器的结构强度也是需要考虑的重要因素。
matlab可以进行减速器的结构强度分析,找出可能存在的弱点并进行设计改进,以保证减速器的结构强度和稳定性。
四、实例分析通过一个实例来展示基于matlab的单级圆柱齿轮减速器的优化设计过程。
首先我们需要确定减速器的工作参数,比如输入轴转速为1000rpm,输出轴转速为100rpm,扭矩传递比为10。
然后利用matlab进行齿轮参数的选择,计算得到需要的模数和齿数。
基于MatLab的齿轮减速器的可靠性优化设计

4、根据可靠性模型,对减速器进行优化设计,寻求最佳设计方案。
4、如果仿真结果不满足设计要求,需要对优化方案进行调整,并重新进行仿 真分析,直至达到预期效果。
参考内容二
内容摘要
随着现代工业的不断发展,齿轮减速器作为一种广泛应用于机械系统中的传 动装置,其性能和设计质量对于整个系统的运行至关重要。而MATLAB作为一种强 大的数学计算和工程设计工具,为齿轮减速器的优化设计提供了有效的手段。
4、根据可靠性模型,对减速器进行优化设计,寻求最佳设计方案。
4、根据可靠性模型,对减速器 进行优化设计,寻求最佳设计方 案。
4、根据可靠性模型,对减速器进行优化设计,寻求最佳设计方案。
1、在MATLAB中导入优化后的减速器设计方案,并利用Simulink模块构建优 化后的减速器模型。
4、根据可靠性模型,对减速器进行优化设计,寻求最佳设计方案。
利用MATLAB的数值计算功能,可以对齿轮减速器的性能进行详细分析。例如, 可以通过模拟齿轮的啮合过程,计算齿轮的应力、接触强度等;通过分析减速器 的传动效率,评估其传动性能。这些分析结果可以为优化设计提供重要的参考依 据。
3、优化设计
3、优化设计
基于MATLAB的优化设计工具箱,可以对齿轮减速器的参数进行优化。通过定 义优化目标函数,如最小化齿轮应力、最大化传动效率等,可以求解出满足要求 的最佳参数组合。这种方法可以在保证性能的同时,降低材料消耗和制造成本。
基于MatLab的齿轮减速器 的可靠性优化设计
01 引言
目录
02 内容概述
03 MatLab基础知识
齿轮减速器的设计原理

齿轮减速器的设计原理齿轮减速器是一种常见的机械传动装置,它通过齿轮的啮合来实现输入轴和输出轴的速度减速。
其设计原理主要涉及齿轮的选择、啮合计算、齿轮副的设计和齿轮轴的设计等。
首先,齿轮的选择是齿轮减速器设计的第一步。
齿轮的选择要根据减速比、输出转矩和输入转速等要求进行考虑。
一般来说,应首先确定减速比,然后根据输入转矩和转速来选择合适的大齿轮和小齿轮。
在齿轮的啮合计算中,需要考虑的主要参数有模数、齿数、压力角、法向齿厚等。
模数和齿数的选择要满足传动比的要求,同时也要考虑齿轮的强度和齿面接触疲劳寿命。
压力角的选择要保证齿轮的副啮合性能,一般常用的压力角有20和14.5。
法向齿厚的计算要根据齿轮的模数和齿数,以及齿轮的强度要求来决定。
齿轮副的设计要保证齿轮的啮合性能和传动效率。
首先,要确定齿轮副的中心距和轴间距,中心距的选择要考虑齿轮的尺寸和间隙以及齿面接触强度等要求。
轴间距的选择要考虑到轴承的选取和齿轮轴的强度要求。
其次,要进行啮合线的绘制和齿轮副的啮合角计算,以保证齿轮的正常啮合。
最后,要进行齿轮副的传动效率计算,以评估齿轮传动的效果。
齿轮轴的设计也是齿轮减速器设计中的重要一环。
齿轮轴的设计要满足齿轮的传动力矩和齿轮的转速要求。
一般来说,齿轮轴的强度计算要以齿轮轴上的最大力矩为基础,考虑到轴的材料和截面形状,计算轴的抗弯强度和抗扭强度。
同时还要考虑齿轮轴的刚度和轴承的选取,以保证齿轮的正常工作。
总之,齿轮减速器的设计原理涉及齿轮的选择、啮合计算、齿轮副的设计和齿轮轴的设计等多个方面。
通过科学合理地设计齿轮减速器,可以实现输入轴和输出轴的速度减小,并且保证传动的可靠性和高效性。
rv减速器中摆线轮齿形优化修形与参数化设计

摆线轮齿形优化修形与参数化设计随着机械制造技术的不断进步和现代工业的快速发展,各种各样的机械设备在日常生活和生产中得到了广泛的应用。
而作为机械传动系统中关键的一环,减速器在提高传动效率、减小体积和减轻重量方面发挥着至关重要的作用。
而减速器中的摆线轮齿形优化修形与参数化设计,则是保证减速器正常运转和提高性能的关键之一。
1. 摆线轮齿形优化修形的意义摆线轮作为减速器中的主要传动元件,其齿形的优化修形对于减小摩擦、提高传动效率和延长零件使用寿命至关重要。
以往传统的摆线轮齿形设计往往存在着一些缺陷,比如齿根强度不足、传动效率低、噪声大等问题。
而通过对摆线轮齿形进行优化修形,可以有效地解决这些问题,提高减速器的整体性能。
2. 摆线轮齿形优化修形的方法与技术在摆线轮齿形的优化修形过程中,可以采用一系列现代化的方法与技术。
利用计算机仿真技术对摆线轮齿形进行力学分析,找出齿形设计中存在的问题并进行改进。
还可以借助CAD/CAM软件进行参数化设计,快速、精准地生成优化后的摆线轮齿形。
这些方法与技术的应用,可以大大提高摆线轮齿形优化修形的效率和精度。
3. 摆线轮齿形优化修形的关键技术与要点在进行摆线轮齿形优化修形时,需要重点关注一些关键技术与要点。
首先是确定优化修形的目标,例如提高传动效率、减小噪声等,并进行相应的设计方案选择。
其次是进行齿形参数化设计,确定摆线轮齿形的各项参数,并结合计算机仿真技术进行力学分析,找出存在的问题并进行优化。
最后是进行实际加工验证,验证优化后的摆线轮齿形设计是否可以满足要求,并在实际生产中取得良好的效果。
4. 摆线轮齿形优化修形的应用与展望摆线轮齿形优化修形是一个重要的工程技术领域,其应用范围非常广泛。
除了在减速器中的应用外,还可以应用于其他机械传动系统中,如齿轮箱、电机等,以提高传动效率和性能。
未来随着工业制造技术的不断发展,摆线轮齿形优化修形还有很大的发展空间,可以结合新型材料、加工工艺等,进一步提高传动系统的整体性能。
基于可靠性的齿轮减速器优化设计

./ 引言
基于可靠性的齿轮减速器优化设计是在保证齿 轮减速器工作可靠性的基础上对齿轮减速器进行优 化设计, 考虑到约束条件的多样性和齿轮传动设计 中许多的不确定因素, 在以体积、 质量最小为目标的 齿轮减速器优化设计数学模型中, 将可靠性指标直 接引入约束条件中, 克服了常规齿轮减速器优化设 计将静态性能和边界约束作为约束条件, 没有考虑 影响齿轮强度的可靠性指标的缺陷。从而使建立的 可靠性优化设计数学模型更为科学合理, 齿轮啮合 参数和约束条件更加符合客观实际。
第 !" 卷 第 #$ 期 ) !$$+ 年 #$ 月
水利电力机械 ,-./0 12*3/0%-*14 5 /6/1.071 82,/0 9-1:7*/04
%&’( !") *&( #$ 2;<( !$$+
)
基 于 可 靠 性 的 齿 轮 减 速 器 优 化 设 计
.=> &?<@AB’ C>D@EF &G E>BH H>CI;>HD JBD>C &F C>?>FCBJ@’@<K 郭谆钦 LM2 N=IFOP@F
,( ’ ) ([ &3 ] - # 分别代表 #, !, %, 1 斜齿轮; # 4 % 为弹性影响系数, 查机械手册; ’ % 为传动比的绝 对值; 5 % 为齿轮宽度, 取两轮中较小值; [!5 ] / 为接 触疲劳许用应力。 (%) 斜齿轮的重合度一般应大于 ! , 即: ,( % ’) ( ( 6 % ) 5 % 9:*! % - ! ’$ 。 ! "% # 0 ,-.!$ 7
!
/% * ( ’% ) #) 0 ’ $。 5 % $! 0 ’%
高速精密齿轮传动装置的动态特性及优化设计分析

高速精密齿轮传动装置的动态特性及优化设计分析摘要高速精密齿轮传动装置应用广泛,但其动态特性对其性能和寿命起着至关重要的作用。
本文旨在探讨高速精密齿轮传动装置的动态特性及其优化设计分析,提供可靠的理论依据和建议。
引言齿轮传动作为一种古老而重要的机械传动形式,广泛应用于各个领域。
高速精密齿轮传动装置具有高传动精度、高效率和高承载能力等优点,被广泛应用于航空航天、汽车制造、机床等高精度领域。
然而,由于高速精密齿轮传动装置的特殊性,其动态特性与传统齿轮传动装置存在很大差异,因此需要进行深入研究和优化设计。
一、高速精密齿轮传动装置的动态特性分析1. 齿轮系统的振动特性高速精密齿轮传动装置在运行过程中会产生振动,这对其运行稳定性和寿命造成影响。
通过分析齿轮系统的振动特性,可以深入了解振动产生的原因,进而采取相应的措施进行优化设计。
常用的分析方法包括模态分析、有限元分析等。
2. 齿轮系统的动力特性高速精密齿轮传动装置在运转过程中受到多种动力因素的影响,包括齿轮重力、惯性力、接触力等。
这些力的作用对齿轮系统的传动性能和动态特性产生影响。
通过分析动力特性,可以了解齿轮系统受力情况,为优化设计提供依据。
3. 齿轮系统的噪声特性高速精密齿轮传动装置的噪声水平直接关系到其在实际运行中的可接受性。
噪声问题不仅影响操作者的工作环境,还可能对装置自身产生负面影响。
通过噪声特性分析,可以确定噪声产生的原因,采取合适的措施进行降噪处理。
二、高速精密齿轮传动装置的优化设计分析1. 优化齿轮的几何参数齿轮的几何参数对精密齿轮传动装置的性能起着决定性的作用。
通过优化齿轮的几何参数,可以提高齿轮传动的精度和承载能力。
常用的优化方法包括参数优化、拓扑优化等。
2. 优化齿轮的材料选择材料的选择对精密齿轮传动装置的使用寿命和可靠性至关重要。
通过优化材料选择,可以提高齿轮的强度和耐磨性能,减少疲劳寿命的损失。
适当的材料选择还可以降低成本和减少装置的重量。
齿轮传动的可靠性优化设计
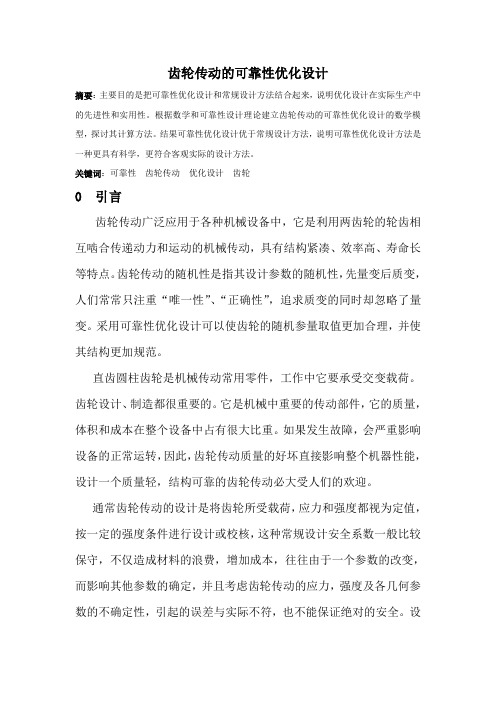
齿轮传动的可靠性优化设计摘要:主要目的是把可靠性优化设计和常规设计方法结合起来,说明优化设计在实际生产中的先进性和实用性。
根据数学和可靠性设计理论建立齿轮传动的可靠性优化设计的数学模型,探讨其计算方法。
结果可靠性优化设计优于常规设计方法,说明可靠性优化设计方法是一种更具有科学,更符合客观实际的设计方法。
关键词:可靠性齿轮传动优化设计齿轮0 引言齿轮传动广泛应用于各种机械设备中,它是利用两齿轮的轮齿相互啮合传递动力和运动的机械传动,具有结构紧凑、效率高、寿命长等特点。
齿轮传动的随机性是指其设计参数的随机性,先量变后质变,人们常常只注重“唯一性”、“正确性”,追求质变的同时却忽略了量变。
采用可靠性优化设计可以使齿轮的随机参量取值更加合理,并使其结构更加规范。
直齿圆柱齿轮是机械传动常用零件,工作中它要承受交变载荷。
齿轮设计、制造都很重要的。
它是机械中重要的传动部件,它的质量,体积和成本在整个设备中占有很大比重。
如果发生故障,会严重影响设备的正常运转,因此,齿轮传动质量的好坏直接影响整个机器性能,设计一个质量轻,结构可靠的齿轮传动必大受人们的欢迎。
通常齿轮传动的设计是将齿轮所受载荷,应力和强度都视为定值,按一定的强度条件进行设计或校核,这种常规设计安全系数一般比较保守,不仅造成材料的浪费,增加成本,往往由于一个参数的改变,而影响其他参数的确定,并且考虑齿轮传动的应力,强度及各几何参数的不确定性,引起的误差与实际不符,也不能保证绝对的安全。
设计的齿轮传动质量差,可靠性低,承载能力小。
因此,为了使齿轮传动设计既贴近实际工况,又有最优方案,提出将优化设计和可靠性设计理论有机结合起来的设计方法,该方法无论对缩小尺寸,减轻质量,提高承载能力和保证设计可靠性均有现实意义。
可靠性设计方法认为作用在齿轮上的载荷和材料性能等都不是定值,而是随机变量,具有明显的离散性质,在数学上必须用分布函数来描述,由于齿轮的载荷和材料性能等都是随机变量,所以必须用概率统计的方法求解。
优化设计-减速器工程实例
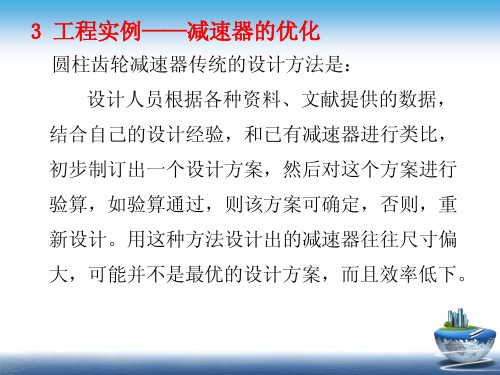
[ x1 , x 2 , x 3 , x 4 , x 5 , ]
T
3.3 建立目标函数
将距离用设计变量表示,确定目标函数为
各变量的上下限:
1 i f x [x1x 3 (2 x 5 ) x 2 x 4 (1 2 )] 2 x5
2 m1 5
16 Z3 22
3.5 m2 6 5 i1 8
g6 ( x ) x 3 22 0 g8 ( x ) x 4 22 0 g10 ( x ) x 5 8 0
3.5 非线性约束
3.5.1 高速级大齿轮和低速级轴不发生干涉的条件
a 2 h a 2 E 28 5 33
1 1 m2 Z3 (1 i 2 ) m1 ( Z2 2) 33 2 2
2 KT2 YFa YSa Y F [ F ] 3 2 d m 2 Z3
[ F ] 303 .57 MPa
式中: K K A K V K K 1 1.05 1.2 1.43 1.802
T2 52 .525 i1 0.98 Nm
YFa 2.93
式中:
1 A [m1Z1 (2 i1 ) m2 Z3 (1 2i2 )] 2
m1、m3:高速级与低速级齿轮 模数;
i1、i 2:高速级与低速级齿轮 传动比;
Z1、Z3:高速级与低速级小齿 轮齿数。 其中独立参数为: m1、m2、Z1、Z3、i1
优化设计变量取 : X [m1 , m 2 , Z1 , Z3 , i1 ]T
二级直齿圆柱齿轮减速器的结构简图
a1
a2
3.1 已知设计参数
高速轴输入功率P1=5.5kW, 高速轴转速n1 =1000r/min, 总传动比i=31.5, 齿轮的齿宽系数ψd=1; 大齿轮45号钢,调质处理,硬度为240HBS, 小齿轮40Cr,调质处理,硬度为280HBS。 7级精度,设计寿命不少于10年。
二级齿轮减速器的优化设计

二级齿轮减速器的优化设计在机械传动领域,二级齿轮减速器是一种常见的传动装置,广泛应用于各种工业领域。
然而,随着科技的不断进步和实际应用需求的提高,对于二级齿轮减速器的优化设计也变得越来越重要。
本文将就二级齿轮减速器的优化设计进行探讨。
我们来了解一下二级齿轮减速器的基本结构。
它主要由输入轴、一级齿轮传动、中间轴、二级齿轮传动和输出轴等部分组成。
其中,一级齿轮传动和二级齿轮传动分别起到了初步减速和进一步减速的作用,以满足整体传动系统的需求。
针对二级齿轮减速器的优化设计,我们主要以下几个方面:传动比是衡量减速器性能的一个重要指标,它决定了减速器的减速能力。
在优化设计过程中,我们需要根据实际应用需求,选择合适的传动比,以实现最佳的减速效果。
同时,还需要考虑传动比的稳定性和可靠性,以保证减速器在长时间运行中保持稳定。
效率是衡量减速器能耗的另一个重要指标。
在优化设计过程中,我们需要减速器的效率,通过采用高性能的材料、优化齿轮形状、降低摩擦等措施,以减少能量损失,提高效率。
结构优化主要是指对减速器的整体结构和零部件进行优化设计,以提高其稳定性和可靠性。
例如,我们可以对齿轮的结构进行优化,以提高其承载能力和使用寿命;也可以对轴承进行优化设计,以减小运转过程中的摩擦和磨损。
维护优化主要是指简化维护流程、提高维护效率等方面。
通过优化设计,我们可以使减速器的维护变得更加简便,同时也可以降低维护成本,提高设备的整体可靠性。
二级齿轮减速器的优化设计是提高整个传动系统性能和稳定性的关键环节。
我们应当从传动比、效率、结构和维护等多个方面进行优化设计,以提升减速器的综合性能,并降低能耗和维护成本。
只有不断追求卓越和进步,才能满足日益严格的工业需求,为我国的机械制造业发展贡献力量。
本文旨在探讨二级斜齿轮减速器的优化设计,旨在提高其性能、效率和寿命。
我们将简要介绍二级斜齿轮减速器的基本概念及其在各个领域中的应用,然后提出优化方案,最后对优化方案进行效果评估和总结。
减速器的设计-毕业论文

减速器的设计-毕业论文引言:减速器是机械传动系统的核心组成部分,广泛应用于各种工业自动化设备、机器人、汽车、船舶等领域。
减速器的设计是实现机械传动系统稳定、高效、可靠运行的关键。
本篇论文将探讨减速器的设计,包括减速器的基本原理、设计流程、优化方法和应用实例。
主体:1. 减速器的基本原理减速器通过齿轮传动实现输出轴的低速高扭矩旋转。
齿轮传动的减速比由齿轮的齿数比决定。
减速器由输入轴、输出轴和中间的齿轮传动系统组成。
输入轴与电机相连,输出轴与负载相连。
减速器的设计需要根据负载的要求和电机的特性来确定齿轮的齿数比和减速比。
2. 减速器的设计流程减速器的设计流程包括以下步骤:(1)确定负载要求:首先需要确定负载的转矩、转速和工作环境等要求。
(2)选择减速比:根据负载要求和电机特性,选择合适的减速比。
(3)选择齿轮类型:选择合适的齿轮类型,例如圆柱齿轮、蜗杆齿轮、行星齿轮等。
(4)计算齿轮参数:计算齿轮参数,包括齿轮模数、齿数、压力角、齿宽等。
(5)确定减速器结构:根据计算结果确定减速器的结构,包括轴承、密封、润滑等。
(6)进行模拟分析:通过模拟分析验证设计的可行性和优化方案。
(7)制造和测试:制造减速器并进行测试,验证设计的性能和可靠性。
3. 减速器的优化方法减速器的优化方法包括以下几个方面:(1)优化齿轮传动:通过优化齿轮的齿形、齿轮间隙、表面质量等参数,提高齿轮传动的效率和寿命。
(2)优化轴承:选择合适的轴承类型和材料,提高轴承的承载能力和寿命。
(3)优化润滑系统:选择合适的润滑方式和润滑油,减少磨损和摩擦,提高减速器的寿命和效率。
(4)优化结构设计:通过优化减速器的结构设计,减少噪音和振动,提高减速器的稳定性和可靠性。
结论:减速器的设计是机械传动系统中的核心问题,需要综合考虑多种因素。
减速器的设计流程包括负载要求、减速比选择、齿轮参数计算、减速器结构确定、模拟分析、制造和测试等步骤。
减速器的优化方法包括优化齿轮传动、轴承、润滑系统和结构设计等方面。
基于惩罚函数法的二级圆柱齿轮减速器的优化设计

惩罚函数法二级圆柱齿轮减速器的优化设计摘要:减速器是各类机械设备中广泛使用的传动装置。
其主要特点为传递功率大、制造简单、维修方便和使用寿命长等优点。
传统的减速器设计一般通过反复的试凑、校核确定设计方案,虽然也能获得满足给定条件的设计方案,实践证明,按照传统设计方法作出的设计方案,大部分都有改进的余地,不是最佳方案。
本文将对二级圆柱齿轮减速器进行优化设计。
考虑到以中心距最小为目标,在此采用了惩罚函数法。
通过设计变量的选取、目标函数和约束条件的确定,建立了圆柱齿轮减速器设计的数学模型。
编写了优化设计程序,通过在计算机上运行和计算,得出优化设计各参数的大小。
从理论上对圆柱齿轮减速器的结构进行了分析并作了常规设计,并对其它的一些附件进行了相应的设计,设计完毕,对其齿面、齿根弯曲强度进行校核,结果满足要求。
结果表明,采用优化设计方法后,在满足强度要求的前提下,减速器的尺寸大大降低了,减少了用材及成本,提高了设计效率和质量。
关键词:圆柱齿轮减速器优化设计惩罚函数法中心距常规设计指导老师签名:Penalty function Optimal Design for Two-Grade Helical Cylindrical Gear RedactorAbstract:Reducer is a transmission device which is widely found in mechanicalequipment. The main characteristics of it is large power transmission、manufacture simple、easy maintenance and long life. Traditionally, in order to get satisfied design data of reducer, you must cut and try again and again. Although this design can satisfy conditions given. Proved by the practice, according to the traditional design method to the design, most of them have room for improvement, it is not optimal.In this article we will two-grade helical cylindrical gear redactor conduct optimal design . Taking account the minimum distance of center into the goal, penalty function used in this method . In this paper, by the way of selecting design variable , setting up goal function and restriction condition , the mathematical model of cylindrical gear reducer is established . The preparation of the optimal design program , run by thecomputer and calculating the optimal design parameters . The structure of the gear reducer is analyzed and made conventional design in theory, and some otheraccessories for the corresponding design , which proved reasonable for the the checking of Tooth surface and tooth root bending strength after the designation completed . The results show that the optimal design methods , strength requirements are met under the premise of the size reducer greatly reduced, reducing the timber and the cost , improve the design efficiency and quality.Key words:Helical Cylindrical Gear Redactor optimal design penalty functionCenter distance Conventional DesignSignature of supervisor:目录1 序言1.1 选题的依据及意义 (1)1.2 研究概况及发展趋势 (1)1.3 减速器的主要类型 (2)1.4 减速器结构 (4)1.5 圆柱齿轮传动的特点 (5)1.6机械零件优化设计概述 (5)2 二级圆柱齿轮减速器优化设计数学模型的创建2.1 优化设计介绍 (6)2.1.1 优化设计的意义与发展 (6)2.1.2 优化设计方法的选择 (8)2.1.3 优化设计中主要术语概述 (9)2.1.3.1 优化方法 (9)2.1.3.2 设计变量 (9)2.1.3.3 约束条件 (10)2.1.3.4 目标函数 (11)2.1.3.5 数学模型 (11)2.2 优化设计的步骤 (12)2.2.1 建立数学模型 (12)2.2.2 选择最优化算法 (13)2.2.3 程序设计 (14)2.2.4 计算机自动刷选最优设计方案 (14)2.3 优化设计与常规设计的比较 (14)2.4 原始数据及设计要求 (15)2.5 减速器轮传动类型的选择 (15)2.6 建立优化设计的数学模型 (16)3 采用惩罚函数法进行调优3.1 惩罚函数法的简介 (18)3.1.1 内点惩罚函数法 (19)3.1.2 内点法的计算步骤 (20)3.1.3 外点惩罚函数法 (20)3.1.4 混合惩罚函数法 (21)3.2 二级圆柱齿轮减速器优化程序 (21)4 二级圆柱齿轮减速器的设计及计算4.1 传动方案的选择 (22)4.2 电动机的选择 (23)4.2.1 型号的选择 (23)4.2.2 功率的选择 (24)4.2.3 转速的选择 (24)4.3 电动机型号的最终确定 (25)4.4 传动装置运动的计算和动力参数的确定 (26)4.4.1 各轴转速的计算 (26)4.4.2 各轴输入功率的确定 (26)4.4.3 各轴输入转矩T(N•m) (26)4.5 传动件的设计计算 (27)4.5.1 带传动的形式和参数确定 (27)4.5.2 齿轮类型选择及参数确定 (28)4.6 轴的设计计算 (36)4.7 轴的校核计算 (38)4.8 滚动轴承型号的选择 (38)4.9 联接键的选择及其校核 (39)4.10 减速器机体结构尺寸计算表及附件的选择 (40)4.11 润滑方式的选择 (41)4.11.1 传动件的润滑 (41)4.11.2 滚动轴承的润滑 (42)总结 (43)参考文献 (44)致谢 (45)附录 A (46)惩罚函数法二级圆柱齿轮减速器的优化设计1序言1.1选题的依据及意义齿轮减速器是原动机和工作机之间的独立的闭式传动装置,用来降低转速和增大转矩,以满足工作需要,在某些场合也用来增速,称为增速器。
单机圆柱齿轮减速器优化设计
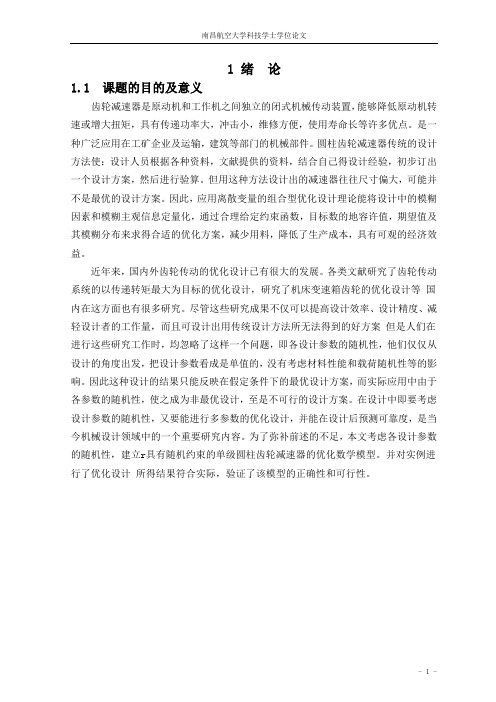
1 绪论1.1 课题的目的及意义齿轮减速器是原动机和工作机之间独立的闭式机械传动装置,能够降低原动机转速或增大扭矩,具有传递功率大,冲击小,维修方便,使用寿命长等许多优点。
是一种广泛应用在工矿企业及运输,建筑等部门的机械部件。
圆柱齿轮减速器传统的设计方法使:设计人员根据各种资料,文献提供的资料,结合自己得设计经验,初步订出一个设计方案,然后进行验算。
但用这种方法设计出的减速器往往尺寸偏大,可能并不是最优的设计方案。
因此,应用离散变量的组合型优化设计理论能将设计中的模糊因素和模糊主观信息定量化,通过合理给定约束函数,目标数的地容许值,期望值及其模糊分布来求得合适的优化方案,减少用料,降低了生产成本,具有可观的经济效益。
近年来,国内外齿轮传动的优化设计已有很大的发展。
各类文献研究了齿轮传动系统的以传递转矩最大为目标的优化设计,研究了机床变速箱齿轮的优化设计等国内在这方面也有很多研究。
尽管这些研究成果不仅可以提高设计效率、设计精度、减轻设计者的工作量,而且可设计出用传统设计方法所无法得到的好方案但是人们在进行这些研究工作时,均忽略了这样一个问题,即各设计参数的随机性,他们仅仅从设计的角度出发,把设计参数看成是单值的,没有考虑材料性能和载荷随机性等的影响。
因此这种设计的结果只能反映在假定条件下的最优设计方案,而实际应用中由于各参数的随机性,使之成为非最优设计,至是不可行的设计方案。
在设计中即要考虑设计参数的随机性,又要能进行多参数的优化设计,并能在设计后预测可靠度,是当今机械设计领域中的一个重要研究内容。
为了弥补前述的不足,本文考虑各设计参数的随机性,建立r具有随机约束的单级圆柱齿轮减速器的优化数学模型。
并对实例进行了优化设计所得结果符合实际,验证了该模型的正确性和可行性。
1.2 国内外研究概况及发展趋势最优化方法在机构设计和零件设计中应用广泛,效果显著。
近十年来,国内外对整台机器或某一机械系统的设计,采用最优化方法代替原来传统的设计方法也越来越多。
RV减速器啮合性能分析与优化设计
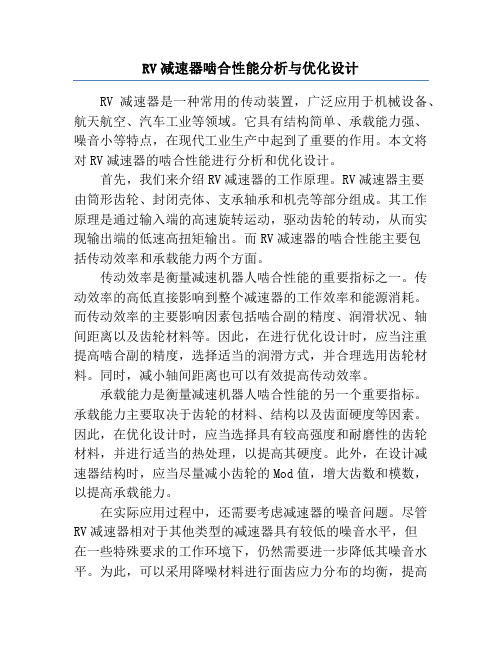
RV减速器啮合性能分析与优化设计RV减速器是一种常用的传动装置,广泛应用于机械设备、航天航空、汽车工业等领域。
它具有结构简单、承载能力强、噪音小等特点,在现代工业生产中起到了重要的作用。
本文将对RV减速器的啮合性能进行分析和优化设计。
首先,我们来介绍RV减速器的工作原理。
RV减速器主要由筒形齿轮、封闭壳体、支承轴承和机壳等部分组成。
其工作原理是通过输入端的高速旋转运动,驱动齿轮的转动,从而实现输出端的低速高扭矩输出。
而RV减速器的啮合性能主要包括传动效率和承载能力两个方面。
传动效率是衡量减速机器人啮合性能的重要指标之一。
传动效率的高低直接影响到整个减速器的工作效率和能源消耗。
而传动效率的主要影响因素包括啮合副的精度、润滑状况、轴间距离以及齿轮材料等。
因此,在进行优化设计时,应当注重提高啮合副的精度,选择适当的润滑方式,并合理选用齿轮材料。
同时,减小轴间距离也可以有效提高传动效率。
承载能力是衡量减速机器人啮合性能的另一个重要指标。
承载能力主要取决于齿轮的材料、结构以及齿面硬度等因素。
因此,在优化设计时,应当选择具有较高强度和耐磨性的齿轮材料,并进行适当的热处理,以提高其硬度。
此外,在设计减速器结构时,应当尽量减小齿轮的Mod值,增大齿数和模数,以提高承载能力。
在实际应用过程中,还需要考虑减速器的噪音问题。
尽管RV减速器相对于其他类型的减速器具有较低的噪音水平,但在一些特殊要求的工作环境下,仍然需要进一步降低其噪音水平。
为此,可以采用降噪材料进行面齿应力分布的均衡,提高减速器的噪音性能。
除了上述的啮合性能分析与优化设计,RV减速器的维护保养也是保证其正常工作的重要环节。
应定期检查润滑油的质量和加油量,及时更换老化的润滑油。
此外,还应注意减速器工作的温度和振动情况,避免过高的温度和剧烈的振动对减速器的影响。
总之,RV减速器的啮合性能是影响其工作效率和可靠性的重要因素。
通过分析和优化设计,可以提高传动效率、承载能力,并降低噪音水平。
齿轮传动系统的多目标优化设计

齿轮传动系统的多目标优化设计
齿轮传动系统是一种常见且重要的动力传动机构,广泛应用于机械设备中。
在
设计齿轮传动系统时,通常会面临多个目标的优化问题,例如提高传动效率、减小噪音和振动、延长使用寿命等。
因此,进行齿轮传动系统的多目标优化设计是非常关键的。
首先,进行齿轮传动系统的多目标优化设计需要考虑到各个目标之间的相互影
响和制约关系。
在设计过程中,需要充分了解各个目标之间的权衡关系,找到最佳的平衡点。
例如,提高传动效率可能会导致噪音和振动的增加,因此需要在这两个目标之间进行权衡。
其次,进行齿轮传动系统的多目标优化设计需要考虑到各个参数之间的相互影响。
齿轮传动系统设计涉及到众多参数,如模数、齿数、啮合角等,这些参数的选择会直接影响到系统的性能。
因此,在优化设计过程中需要充分考虑各个参数之间的协调关系,找到最佳的参数组合方案。
此外,进行齿轮传动系统的多目标优化设计还需要利用先进的优化方法和工具。
现代优化算法如遗传算法、粒子群算法等具有强大的寻优能力,可以帮助工程师高效地找到最佳的设计方案。
同时,借助仿真软件如ANSYS、ADAMS等,可以对
设计方案进行全面的性能评估,验证设计的有效性。
总的来说,齿轮传动系统的多目标优化设计是一个复杂而重要的工程问题,需
要综合考虑各种因素,并借助先进的方法和工具进行设计。
只有在系统性能、成本、可靠性等多个方面进行全面优化,才能设计出高效、稳定、可靠的齿轮传动系统,满足实际工程需求。
希望以上内容能够对您的工作有所帮助。
减速器行星齿轮传动常规设计和优化设计的比较

1 常规设 计 …
结合塔式起 重机 回转 驱动机 构 的设计 , 根据所 用发 电机 、 速器 及 回转 驱动 元件 的不 同 , 械驱 动 的 减 机 回转 机构 可出现多种 驱动形 式 . 过 比较 , 通 确定选 择立式 电动 机一联 轴器一水 平安置 的制 动器一立 式齿 轮 减 速器一 最后 一级大 齿轮 ( 或针轮 ) 传动这 种方案 , 它具 有平 面 布置 紧凑 , 更好 地 利用 了空 间 , 免 了圆 锥 避
维普资讯
第 5卷第 3期 2o o 7年 7月
中
国工程机来自械学报
V_ . 0 5No 3 1 .
C NE EJ U N L O 0 S R T 0 C E Y HI S R A F C N T I 1 N MA H O I C R
eS.
K ywo d :pa eayg a ;r u e ;o t l ei ;cn e t n ld i e rs l t e r e cr p i s g n r d ma d n o v n i a e g o sn
作者 曾经在塔 式起重 机 回转 驱动 机构及其 减速器 的设计 中 , 采用常 规设 计方法设 计减 速器 , 所设计 的
oj t efn t n dcn t i sa detbi igmahmai l o e . an hl,h ei yl crb be i ci sa o s a t, alhn te t a m d l Me w i ted g cc al e c v u o n rn n s s c s e sn e
减速器采用三级 Z K—H型行星齿轮传动 , 后来在学习过程中接触到行星齿轮传动 的优化设计 , 于是在对
两 者 的理 解上 , 了 比较 . 作 本文介 绍 了减 速器行 星齿轮 传动 的常规 设计 , 还介 绍 了行 星齿 轮 传动 的优化设 计, 最后通 过实例进 行 了 比较 , 出 了结论 . 得 对工程 实 际有一定 的指 导意义 .
RV减速器可靠性优化设计方法

性假设的剩余强度可以表示为:
1
r(n)=r(0)-[r(0)-o-mas] —R-晋]
(9)
式中:"0)-初始静强度;o■”*—循环应力峰值;忙疲劳寿命; n—载荷循环次数;T—与载荷和材料相关。 联立式(8)〜式(9),得到齿轮强度的模糊时变可靠度为: (1.1M)同彳也尸)
_(M)_可6)
1
exp
式中:Z]—入齿轮齿数;Z?—行星齿轮齿数;Z”~~齿数;Z。一摆线 轮齿数,为了获得大传动比,RV减速器中的摆线针轮传动 一般取一齿差,即z”_z” = l。
3 RV减速器可靠性分析
实践表明,RV减速器主要承载部件中的行星齿轮、摆线轮 和曲柄轴承易失效皿,因此对这三个子部件的可靠性展开分析。
(1)齿轮的强度模糊可靠性吟呵。在计算两级传动的强度可 靠度时把应力作为随机变量处理,将强度作为模糊变量,根据应
Abstract: The established the tune-varying fuzzy reliability analysis model with main load bearing components and analyzed
the reliability variation rules of relevant parts during service according to the structural characteristics of RV reducer. Results showed that the cycloid wheel is the weakest part which affects the reliability ofthe whole machine. Aimed at optimizing the reli ability ofcycloid wheel and the volume ofthe whole machine, the reliability optimization design method ofRV reducer was pro posed based on the principle of the weakest link. The optimization design and reliability based optimization design were carried outfor the living example. The comparison showed that the latter has a significant improvement on high reliability with reducing ofvolume. Those results verified the correctness ofthe method which provided a new perspectivefor parameter optimization of RV reducer.
- 1、下载文档前请自行甄别文档内容的完整性,平台不提供额外的编辑、内容补充、找答案等附加服务。
- 2、"仅部分预览"的文档,不可在线预览部分如存在完整性等问题,可反馈申请退款(可完整预览的文档不适用该条件!)。
- 3、如文档侵犯您的权益,请联系客服反馈,我们会尽快为您处理(人工客服工作时间:9:00-18:30)。
《装备制造技术》2007年第1期斜齿圆柱齿轮减速器具有传递功率大,冲击小,维修方便,使用寿命长等许多优点,在工业上得到了广泛应用。
因此,对该种减速器进行优化设计,具有可观的经济效益。
单级斜齿圆柱齿轮减速器模糊可靠性优化设计方法:应用模糊可靠性优化设计理论能够将设计中的模糊因素和模糊主观信息定量化,通过合理给定约束函数、目标函数的容许值、期望值及其模糊分布(隶属函数)来求得一合适的优化方案。
例如:某大型机械采用单级圆柱齿轮减速器,减速器传动参数为:z1=33,z2=105,mn=3.5,!=14°59′,b1=b2=100mm;小齿轮材料为38SiMnMo、调质,硬度为220~240HB。
高速轴许用功率P1为80kW,高速轴转速730r/min,单向运转,长期连续工作。
要求以常用定型减速器的有关参数和设计规范为基础,传动比允许误差±5%,在满足各约束的条件下,使减速器具有最紧凑的结构。
1数学模型的建立1.1确定设计变量由原始条件可知,减速器中齿轮传动需确定的参数值为:齿轮法向模数mn,小齿轮齿数z1,分度圆螺旋角",齿宽b(取两轮齿宽相等)。
则设计变量为X=[x1,x2,x3,x4]T=[mn,z1,#,b]T。
1.2建立目标函数根据设计要求,以最小体积为追求的目标,既可减轻重量,又可节约材料,降低成本。
为简化计算,用齿轮分度圆圆柱体积来近似代替齿轮的体积,则目标函数可表示为:minF(X)=b$mn2Z12(u2+1)4cos2%1.3建立模糊约束条件约束条件有性能约束和几何变量约束两部分,对于应力等性能约束,必须考虑其从完全许用到完全不许用的中间过渡过程,对于几何变量约束,必须考虑其边界实际存在的模糊性。
这些约束均为设计空间的模糊子集,建立约束条件如下:1.3.1接触应力约束根据公式有:&H=ZEZHZ’Z(2KT1bd12!・U+1U由齿轮材料可知,小齿轮优于大齿轮,取大齿轮硬度为220HB,查得бHlim2=570MPa,推荐取[бH]=0.96cHlim,则有[бH2]=513MPa,于是有:g1(X)=513-ZEZHZ)Z*2KT1・COS2X3・U+1U!≤0(1)1.3.2弯曲应力约束根据公式有:бF1=2KT1bd1mnYFalYSalY+Y,бF2=бF1YFa2・YSa2YFal・YSal由原始条件取小齿轮HB=260,大齿轮HB=220,查得бFlim1=600MPa,бFlim2=490MPa。
由于齿轮单向运转,取[бF]=0.7бFlim,得[бF1]=420MPa,[бF2]=343MPa。
于是有g2(X)=420-2KT1・COSX3YFal・YSal・Y-・Y.≤0(2)g3(X)=343-2KT1・COSX3YFal・YSal・Y/・Y0≤0(3)1.3.3模数约束对于传递动力的齿轮,模数应大于1.5,由于该机械为大型机械,所需动力较大,故取2≤mn≤3.5。
得g4(x)=2-X1≤0(4)=X1-3.5≤0(5)1.3.4齿数约束对于软齿面闭式传动,齿数宜取多一些(模数相应减少),一般取20≤z1≤40,得设计与计算机械减速器齿轮传动的优化设计吴敏(岳阳职业技术学院湖南岳阳414000)摘要:单级斜齿圆柱齿轮减速器的优化设计,是一个多目标优化问题。
事实上把所有的优化原则作为优化目标,很难同时达到最优,只能在综合考虑各个目标的情况下,应用模糊可靠性优化设计理论将设计过程中大量的模糊数据进行科学的处理、定量的分析和研究,通过综合评价来求得一合适的优化方案。
关键词:斜齿圆柱齿轮;减速器;评价矩阵;优化设计中图分类号:TH12文献标识码:A文章编号:1672-545X(2007)01-0001-02收稿日期:2006-11-06作者简介:吴敏(1964-),男,湖南常德人,湖南岳阳职业技术学院高级讲师,主要研究方向:机电一体化技术、职业教育理论。
""""""#"$%%%%%%$"$X4X21・X22X4X21・X22X4X21・X22g5(5)X1X1设计水平u1制造水平u212345高材质好坏u3使用条件u4重要程度u5维修费用u612345较高一般较低低1.00.90.400高较高一般较低低1.00.90.400好好较好较好一般一般一般一般较差较差差差0.850.90.51.01.01.01.0000.80.70.50.50.40.20.20.3000重要大较重要较大不太重要较少不重要少吴敏.精品课程评价指标体系的研究[J].高等职业教育(天津职业大学学报),2005,14(3):48-51.王迁和,姜培刚.直齿圆柱齿轮传动的模糊可靠性优化设计[J].机械设计与制造,2000,6(3):1-2.徐静,董雁,翁慧艳.斜齿圆柱齿轮减速器模糊可靠性优化设计[J].机械设计与制造工程,2001,30(3):17-19.谢庆生,罗延科,李屹.机械工程模糊优化方法[M].北京:机械工业出(下转第16页)许用范围许用范围G(X)G(X)1XX001λ*λ*图1齿轮应力隶属函数图2几何、变量约束隶属函数输入X(0)T0,C,εK=0以X(K)为初始点,求Φ(X,YK)的最优点X0(K)K=0TK+1=C・TKK=K+1X(K)=X・(K+1)X1・(K)-X・(K+1)<!1i=1,2,……n‖X・(K)-X・(K-1)‖<"输出XK,F(X・(K+1))结束开始NNNYYY图3内点惩罚函数程序框图g6(x)=20-X2≤0(6)g7(x)=X2-40≤0(7)1.3.5螺旋角约束螺旋角一般取8°~25°因此g8(x)=8°-X2≤0(8)g9(x)=X3-25°≤0(9)1.3.6齿宽系数约束设齿轮相对于轴承对称分布,故取ψd为0.8~1.4,得g10(x)=0.8-X4・COSX3・X2≤0(10)g11(x)=X4・COSX3・X2-1.4≤0(11)2隶属函数的确定对各类约束的模糊子集均采用线性隶属函数。
齿轮应力的隶属函数服从图1的形式,其含义为应力不超出一定的模糊范围,其他约束或变量的隶属函数则服从图2的形式,其含义是约束或变量的取值应满足一定的模糊上下限。
3模糊优化模型的求解本设计采用最优化水平截集法,将模糊问题转化为非模糊优化问题,然后再用普通优化方法求解,其基本步骤如下:3.1确定影响λ*取值的因素、因素等级及其隶属度,见表1。
表1影响因素、因素等级及其隶属度影响因素等级隶属度因素3.2确定备择集根据本设计要求及模糊约束的性质,规定对隶属度小于0.5的均不予考虑,给定备择集如下:λ={0.5,0.5,0.7,0.8,0.85,0.9,0.92,0.95,0.97,0.99}3.3确定因素等级权重集及因素权重集为了准确反映各因素及因素等级对评判对象λ的影响,赋予各因素及因素等级以不同的权重W和Wi。
其中因素权重集确定为:W={0.2,0.2,0.15,0.10,0.180.17}3.4进行二级模糊综合评判由模糊矩阵乘法得到评判结果:B={0.188,0.306,0.477,0.696,0.805,0.762,0.577,0.492,0.335,0.228}按加权平均法得最优截集的水平为0.85,从而将模糊优化问题转化为普通优化问题。
3.5优化方法及结果本优化总共有4个变量,11个约束条件,采用内点惩罚函数法对其进行优化设计。
内点处罚函数法框图如图3所示,其中X(0)为初始惩罚因子,C为递减系数,ε为收敛精度。
现以原设计方案的参数为初始点,X(0)=[3.5,33,14°59′,100],经程序运算,得到模糊最优解如下:X=[3.32,28.47,12°35′15″,91.85]T程序框图如下:由于齿数必须为整数,模数必须为标准值,齿宽也应圆整为整数,故需将最优解圆整到符合工程要求的值。
最后得到符合工程要求的值为:X=[3.5,29,12°35′15″,92]T。
将原设计结果与优化设计结果代入目标函数,经计算得:原体积F=11655034.97mm3;优化后的体积F=8280794.89mm3,优化后目标函数减少29%。
参考文献:[1][2][3][4]SolvingMethodtoPlanarCrank-slideMechanismSynthesiswithLINGOSoftwareTANYan-xian1,ZENGXia-wen1,CAISu-ling1,LUOYou-xin2(1.HunanIndustryPolytechnic,Changsha410082,China;(2.ChangdeTeachersUniversity,ChangdeHunan415000,China)Abstract:Afteranalyzingallmethodsforfindingsolutionofcrank-slidemechanismsynthesis,anewmethodswaspresented,whichcanfindallsolutiontomechanismsynthesisandisbasedonLINGO10.0software.ThesolutionfoundbyLINGO10.0isusedasarestrictiontoruntheprogramagaintofoundanothernewsolutiontillallsolutionsarefound.Theproblemofplanarcrank-slidemechanismwassolvedbythismethod,whichprovidesasimplerealizationmethodformechanicsdesign.Keywords:Planarcrank-slidemechanism;LINGOsoftware;Mechanismsynthesis(上接第6页)ResearchingFeatureRecognitionTechnologyofEntityModelKEChang-zhong,ZENGXia(WuhanUniversityofTechnology,MechanicalandElectricalEngineeringInstitute,HuBeiWuhan,430070,China)Abstract:EffectiveintegrationofCADandCAMisdemandedbymanufacturingindustries.SoanintelligentinterfacebetweenCADandCAMisimperative.NowCADdescribesandmemoriespartsbygeometryortopology,butCAPPexpertspartrepresentationintermsofmanufacturingfeatures.Thereforefeaturerecognitionhasbeenanimportantresearcharea.Inthispaper,itisexpatiatedonrepresentativetechniqueoffeaturerecognitionbythetheoryofentitymodelandfeaturerecognition,andanalysesit.Thefeaturerecognitionbasedonbordermatchingisusedinaninstanceandtorealizeextractionofentityfeatureinformation.Keyword:featurerecognition,entitymodeling,extractionoffeatureinformation(上接第8页)[5][6][7][8]版社,2002.董玉革.机械模糊可靠性设计[M].北京:机械工业出版社,2000.黄洪钟.模糊设计[M].北京:机械工业出版社,1999.王彩华,宋连天.模糊论方法学[M].北京:中国建筑工业出版社,1988.李安贵,张志宏,段风英.模糊数学及其应用[M].北京:冶金工业出版社,1994.MechanicalStep-downGearTransmissionOptimizedDesignWUMin(YueyangVocationalandTechnicalCollege,YueyangHunan414000,China)Abstract:Thesinglestageskewedtoothcylindricalgearsreductiongearoptimizeddesign,isamulti-objectiveoptimizationquestion.Infactalloptimizedprincipletooktheoptimizedgoal,verydifficultsimultaneouslytoachievesuperiorly,onlywillbeableintheoverallevaluationeachgoalsituation,theapplicationfuzzyreliabilityoptimizationdesigntheorytodesignintheprocessthemassivefuzzydatatocarryonthescienceprocessing,thequotaanalysisandtheresearch,willobtainanappropriateoptimizationplanthroughthequalitysyntheticevaluation.Keywords:Skewedtoothcylindricalgears;Reductiongear;Appraisalmatrix;Optimizeddesign(上接第2页)FailureAnalysisontheCrackingofThermocoupleSleevePipeHEJia-sheng1,3,CUIHao-xuan1,ZHUXiao-ming2,ZHUGuang-qiang1,WUJian-ping2,LUYuan-ming2(1.SchoolofMechanicalEngineering,WuhanInstituteofTechnology,Wuhan430074,China;2.WuhanSubsidiaryCompany,ChinaPetrochemicalCo.Ltd.Wuhan430082,China;3.WuhanResearchCenterofPressureVesselandPipingSafetyEngineering,Wuhan430074,China)Abstract:Themechanismofcrackinginitiationandgrowthundervariableloadinducesthefailureofthermocouplesleevepipearestudiedthroughanalysisofchemicalcompositionandmacro/micro-metallurgicalstructure.Theanalyticalresultsshowthatthefailurereasonofthethermocouplesleevepipewasweldingundercutthatinducedmicrocosmicdefect.Keyword:Weldingundercut;Fatigue;Austeniticstainlesssteel;Failureanalysis;Crackinginitiation!!!!!!!!!!!!!!!!!!!!!!!!!!!!!!!!!!!!!!!!!!!!!!!!!!!!!!!!!!!!!!!!!!!!!!!!!!!!!!!!!!!!!!!!!!!!!!!!!!!!!!!!!!!!!!!!!!!!!!!!!!!!!!!!!!!!!!!!!!。