车间质量控制流程图
注塑车间质量控制流程图

上海金秋塑料制品有限公司注塑车间质量控制流程1、目的为了确保对注塑产品质量有影响的各工序按规范作业,以保证这些检验处于受控状态。
保证产品的制造过程满足入库要求。
2、范围适用于注塑车间产品生产过程中的质量控制。
3、职责3.1.巡检员负责按订单要求或相应的工艺文件进行注塑过程的产品质量控制. 3.2抽检负责对当班的注塑产品入库前全面检查3.3检验中如有疑问及争执,须由上级协调处理。
4.1 首检、记录和标识:4.1.1注塑生产过程中,操作工必须做好自检记录,检验产品的外观,巡检员做好开机前产品的首件签字封样,并填写《首件检验报告》,生产过程中要按巡检员要求进行产品抽检工作,每次检验项目要完整,并同时对打包产品、作业台产品和机台随机产品三个环节进行验证,发现问题,及时纠正和协调处理。
4.1.2抽检员有权要求操作工对自检不合格的产品进行返工,并对返工产品进行记录、标识和复查,直至达到产品质量要求,否则不允许入库,对不合格的产品在交接班时要确保信息完全传达给下班次人员,以防不良品继续产生;4.1.3检验主管每天要将巡检报表收回并检查巡检记录的情况,对记录有不实或存在疑问则找相关质检员了解确认,如属工作粗心、失误、责任心不足则要求进行通报批评并,对多次未按检验工作指导执行人员将考虑换岗或其它处分;4.1.4各注塑工段完成品合格后,操作工应在产品外包上作好表示,才能转入下一道工序,注塑的成品、半成品、合格和不合格品等,应按规定的区域整齐放置,并按标识和可追溯性管理原则进行标识,检验员有权对过程进行控制和协调,对标识不规范有权要求员工整改或停机整顿。
4.2 过程再确认:4.2.1 换料和换模后产品的检验和确认巡检过程中机台有换料、换模时,质检要按首件检验标准,逐项确认产品的外观、工程尺寸、性能强度和组件装配度等各项品质参数,调查和了解所用物料的批次是否发生变化,便于记录和预防不良的发生;4.2.2 修模后产品的检验和确认当模具发生异常维修结束上机试样时,质检要按首件检验标准,逐项确认产品的外观、工程尺寸、性能强度和组件装配度等各项品质参数,并对照前期样品,确认无误后方可投入批量生产,若模具属重大维修事项则由工艺组依照以上项目检查合格后方可批量生产,必要的时候还需进行长时间的验证跟踪;4.2.3 新人作业后产品的检验和确认当机台发生换人,新人作业等,领班、巡检必须加强巡检次数,明确告之产品的注意事项并确保员工全部理解,过程中反复检查新手作业熟练程度,发生异常要及时纠正,必要时候换熟练员工作业,保证品质的稳定性;4.2.4 停机后产品的检验和确认生产过程中,由于特殊原因等造成机台异常作业而重新开机生产,此时,机台的工作处于不稳定状态,巡检员要按首件检验标准,逐项确认产品的外观、工程尺寸、性能强度和组件装配度等各项品质参数,并对照前期样品,确定产品合格后方可批量生产,并持续跟进直到机台运行、产品质量趋于稳定为止;4.2.5 过程调机后产品的检验和确认生产过程中,产品发生变异,车间领班或车间主管重新调机,当改变机台成型参数而原问题得到克服后,巡检员要重新确认其他检验项目的品质是否出现变异,各种性能是否达到要求,如通过提高温度来克服产品外观不良是否会影响塑胶的物性而使产品变脆等,避免发生新的不良问题造成批量品质事故发生;4.2.6 交班过程产品的检验和确认车间在交班过程中,由于人员发生变动、新换材料未确认已到换班时间、上班次巡检员忘了彻底交接或其他原因等给机台生产埋下质量隐患,对可能造成批量质量事故的风险,接班巡检员除严格执行检验外,必须确认上班次的巡检表、自检表,了解材料使用情况等,及时熟悉上班次的品质情况,采取措施,确保对影响过程能力的变化及时做出反应。
车间质量控制流程图

车间质量控制流程图车间质量控制流程图1、介绍车间质量控制流程图是一个指导车间质量管理流程的图表。
该流程图涵盖了车间质量控制的各个方面,包括设立质量目标、制定质量标准、执行质量检查、纠正和预防措施等内容。
2、质量目标设立流程2.1 确定质量目标的必要性和重要性- 定义车间质量目标的背景和重要性- 制定质量目标达成的时间要求2.2 制定质量目标- 设定车间整体质量目标- 设定各个部门和员工的质量目标- 确定质量目标的具体指标和可衡量性2.3 审查和确认质量目标- 进行质量目标审查和讨论- 确认质量目标的可行性和适应性3、质量标准制定流程3.1 定义质量标准的需求- 确定车间质量标准的必要性和重要性- 确定适用的质量标准和规范3.2 制定质量标准- 确定各个工序和环节的质量标准- 编制相关的质量流程文件和标准操作程序3.3 审查和确认质量标准- 进行质量标准的审查和讨论- 确认质量标准的可行性和适应性4、质量检查流程4.1 制定质量检查计划- 确定质量检查的频次和范围- 制定质量检查的具体内容和方法4.2 执行质量检查- 按照质量检查计划进行检查- 记录质量检查结果并进行分析4.3 整理和报告质量检查结果- 整理质量检查数据和结果- 撰写质量检查报告并上报相关部门5、纠正和预防措施流程5.1 发现质量问题- 通过质量检查、投诉或其他渠道发现质量问题5.2 进行问题分析- 对质量问题进行深入分析和原因追溯- 确定问题的具体原因和责任主体5.3 制定纠正措施- 确定解决质量问题的具体措施- 制定纠正措施的时间要求和责任人5.4 实施纠正措施- 进行纠正措施的实施和监控- 记录纠正措施的执行情况5.5 预防措施的制定- 根据质量问题的分析结果制定相应的预防措施- 确定预防措施的具体内容和实施要求5.6 实施预防措施- 进行预防措施的实施和监控- 记录预防措施的执行情况本文档涉及附件:附件1:质量目标确认记录附件2:质量标准制定表附件3:质量检查计划表附件4:问题分析报告附件5:纠正措施执行记录附件6:预防措施执行记录本文所涉及的法律名词及注释:1、质量目标:制定和实施质量相关目标,以提供企业产品和服务的可靠性、一致性和满意度。
质量部PQC工作流程图

PQC 工作流程图-冲压工作项质量记录/标准参加开班会做生产开班准备接受操作工报检(首件)1.听取班长通报上一班次出现的异常问题;2.对当班生产零件可能会出现的异常作出提示,强调当班需注意的事项;3.接收外部、内部不良信息,转化为内部控制重点项按生产工序准备上批次末件/样件/检具/表单/计量器具等按生产工序准备《检验工艺卡》,可以实现检具测量的工序工作内容(正常)首件检验判定原则:大零件口头报检,小零件送检按《冲压/焊接工艺卡》或《工序检查记录表》的专检要求进行首件检查,可以实现在检具上测量的需按照《检验工艺卡》的要求上检具检查;按照冲压工艺卡核对CY10的零件材料坯料材料牌号/料厚/规格进行确认首件的检验的样本数量按工艺要求:3件/班;检查零件的稳定性与符合性首件封样/三员职责在首件上用蓝色记号笔注明外观检查的要点(检验员技能会让此工作存在问题,要给检验员标准或培训,如何快速提高技能?)在零件上做标记时指导操作工生产的操作要领及模具定位方式,识别零件外观缺陷(口述)首件封样签字(注明合格),交给操作者放入首件台上线上零件的巡检要求操作工人提供生产的工序件,检验员对本工序的几何尺寸全方位的检查可以实现在检具上测量的需按照《检验工艺卡》的要求上检具检查零件的几何尺寸的符合性对工序件外观全方位的检查,对每个部位仔细检查(如毛刺,压痕等)产品质量过程控制三员职责/三检卡记录问题申报三员职责履行:查看操作工的自检方法是否正确,指导操作工识别及自检的检查要点查看操作工三检卡执行情况;是否按要求在实施三检制;按计划对操作工实施三检制执行情况的检查按照《冲压/焊接工艺卡》上专检的内容将专检项测量值记录在《产品质量三检卡》上;同时检查操作工是否按要求记录完整发现工艺文件不符合时通知工艺员确认;如不符合,填写《技术文件问题申报单》,交质检班长处理核对设备参数设定及工装使用是否与工艺一致停止生产,分析原因,清点、标识、隔离、追溯;按《不合格品处理工作流程》处理不合格品处理工人发现工人自己生产出来的,则开具《不合格品处置单》责任人签字;如本序发现上序不良品,需对发现者与生产者开《质量奖惩通知单》(奖/惩)NG生产过程标识卡签字确认每道工序的单个包装单元生产完成后,操作工将《生产过程标识卡》交检验员签字检验员核对《生产过程标识卡》与实物是否一致,包装形态是否满足质量要求,零件质量状态是否合格(外观)末件检验判定按《冲压工艺卡》要求进行末件检查,可以实现在检具上测量的需按照《检验工艺卡》的要求上检具检查;并且与首件进行比对末件的检验的样本数量按工艺要求:3件/班;检查零件的稳定性与符合性确认末件状态,判定现有状态是否需要改善模具工序末件留存将上批次的末件交操作工,换取本批次的末件(工序的最后1件,如存在跨2个班次的工序,则由下一班次留存)将上批次的末件交操作工,换取本批次的末件(工序的最后1件,保存本批次末件,贴样件标签收班工作交接班/交接班记录:在交接班上如实记录当班生产零件的异常及下班次生产过程中需注意的问题,必要时提供缺陷零件;提示下一班质检员留存本批次未生产完的工序的末件检查各自使用的计量器具的精度,简单的保养;归还当班使用的检具,并在下班前归还至检具存放区清点本班次留存的末件,并在下班前归还至末件存放区检查检具部件是否损坏或丢失,提报维修按照下一班次的《制造命令》准备需要的检具,便于下一班次的开班工作在线巡检发现零件不合格,停止生产,通知质检班长及车间班长工作内容(非正常)核对CY10的零件材料坯料材料牌号/料厚/规格(焊接则是对标准件型号,规格,半成品进行核对)要求班组长调整设备气垫压力及模具闭合高度,重新报检(焊接则是在工艺参数范围内调整参数/修整电极)调整后零件状态依旧与工艺或样件有较大差异,通知车间联系模修工/专业工艺员或设备室处理(走车间异常处理)调整的零件清点、标识、隔离与正常生产的零件隔离,按《不合格品处理工作流程》处理,检验员100%确认异常处理部门调整完毕后车间重新报检,PQC 执行首件判定流程NG对不合格零件进行100%清点、标识、隔离、追溯质检班长判定缺陷可接受,放行生产,如不可接受按《不合格品处理工作流程》处理NG在线巡检发现操作工三检制执行不到位纠正操作工三检制执行不到位的行为,同时指导工人如何对零件进行正确的检查及三检卡的填写记录《三检制未执行情况统计表》,要求责任人签字末件发现零件不合格,通知质检班长及车间班长;对不合格零件进行100%清点、标识、隔离、追溯末件检验判定不可接受,需按《不合格品处理工作流程》处理,质检班长联系专业QE ,提报《不合格品评审单》由技质经理组织评审末件确认有缺陷但可以接受,模具需整改,提报《工装模(夹)具维修报验单》通知模修工,一起确认并交接事宜(留样件)如模修工需要留存修模用末件,凭工装组开具的《零件借用表》,开具《不合格品处置单》向车间班长索要本批次最后生产的倒数第2件,标注缺陷部位作为修模样件如质量品质推进中的零件整改,工艺员要求留样用于调试用,直接开具《不合格品处置单》向车间班长索要需要的工序件,交工艺员所有留样调试零件在下个生产周期时如果可以接收时,直接开具《不合格品处置单》,数量为负数,通知车间统计员接收零件零件质量有缺陷,但因为发交原因需要让步接收按《不合格品处理工作流程》通知质检班长联系专业QE ,提报《不合格品评审单》由技质经理组织评审执行评审决议,确认质量,接收让步接收指令,放行生产,按正常的检验流程实施零件质量有缺陷,但因为发交原因需要让步接收按《不合格品处理工作流程》通知质检班长联系专业QE ,提报《不合格品评审单》由技质经理组织评审执行评审决议,确认质量,接收让步接收指令,放行生产,按正常的检验流程实施制造命令交接班记录《产品质量三检卡》《风险零件工序质量检查基准书》风险零件醒目标识制造命令《工序检查记录表》《焊接工艺卡》《冲压工艺卡》《检验工艺卡》《焊接参数卡》《风险零件工序质量检查基准书》《冲压件基础信息一览表》《工序检查记录表》《冲压工艺卡》《焊接参数卡》《风险零件工序质量检查基准书》《工序检查记录表》《焊接工艺卡》《冲压工艺卡》《检验工艺卡》《风险零件工序质量检查基准书》《产品质量三检卡》《三检制执行情况检查计划》《三检制未执行情况统计表》《参数及实验记录表》《技术文件问题申报单》《不合格品处置单》《质量奖惩通知单》《生产过程标识卡》《工序检查记录表》《焊接工艺卡》《冲压工艺卡》《检验工艺卡》《风险零件工序质量检查基准书》《零件借用表》《不合格品处置单》制造命令交接班记录冲压线需核对设备气垫压力值与首件时记录的差异对比,防止变化;固定凸点焊,需检查设备修磨打点数的设置与工艺要求是否一致NGNG发放《产品质量三检卡》到每个工位,如是风险零件需发放《风险零件质量三检卡》使用钢卷尺对材料长宽尺寸及对角线测量,测量结果与材料标签和冲压工艺卡核对使用千分尺对材料厚度测量,测量结果核对材料标签和冲压工艺卡是否一《产品质量三检卡》上专检项内注明,并将测量结果填写在三检卡上。
质量控制(QA)工作流程图
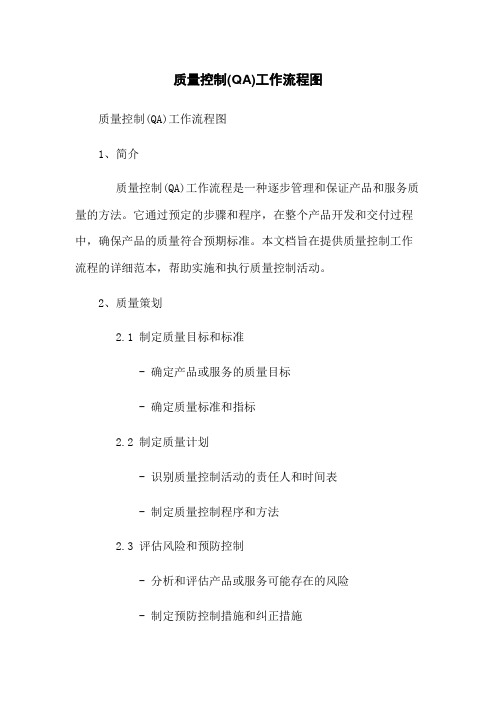
质量控制(QA)工作流程图质量控制(QA)工作流程图1、简介质量控制(QA)工作流程是一种逐步管理和保证产品和服务质量的方法。
它通过预定的步骤和程序,在整个产品开发和交付过程中,确保产品的质量符合预期标准。
本文档旨在提供质量控制工作流程的详细范本,帮助实施和执行质量控制活动。
2、质量策划2.1 制定质量目标和标准- 确定产品或服务的质量目标- 确定质量标准和指标2.2 制定质量计划- 识别质量控制活动的责任人和时间表- 制定质量控制程序和方法2.3 评估风险和预防控制- 分析和评估产品或服务可能存在的风险- 制定预防控制措施和纠正措施3、质量保证3.1 开展质量审核- 进行内部审核,检查质量管理系统的有效性 - 进行外部审核,评估产品或服务的符合性 3.2 实施质量控制计划- 按照质量计划执行各项质量控制活动- 收集和分析质量数据,进行质量改进3.3 管理供应商质量- 评估供应商能力和质量体系- 监督和评估供应商提供的产品或服务质量4、缺陷管理4.1 收集和分析缺陷数据- 建立缺陷管理系统,记录缺陷数据- 分析缺陷数据,找出缺陷的根本原因4.2 实施纠正措施和预防措施- 针对缺陷的根本原因制定纠正措施- 预防类似缺陷再次发生的预防措施4.3 进行缺陷关闭和验证- 确认纠正措施的有效性- 关闭缺陷,并进行验证测试5、文件和记录管理5.1 管理质量相关文件- 确保文件的正确性和及时性- 管理文件的版本控制和变更记录5.2 管理质量相关记录- 确保记录的完整性和准确性- 建立记录的存档和保密措施6、培训和沟通6.1 提供质量培训- 为相关人员提供质量管理和控制的培训- 确保相关人员了解和掌握质量策划和控制方法 6.2 进行质量沟通- 与相关部门和人员进行质量信息的沟通和交流 - 提供质量报告和质量进展更新7、持续改进7.1 分析质量数据- 进行质量数据的统计和分析- 发现潜在问题和改进机会7.2 实施改进措施- 制定改进计划和行动方案- 实施改进措施并进行效果评估7.3 反馈和复审- 根据改进措施的效果进行反馈和复审- 调整和优化质量控制流程附件:2、质量控制记录表3、缺陷管理流程图4、质量培训材料法律名词及注释:1、质量目标和标准:产品或服务的质量要求和期望水平。
质量控制流程图

3 139
1
323 221
3
1
2
2
7 4 10
6 2 26 2
3 1 2 2
2 24
52 61
13
25
1
3
23
1 10 22 1
133
155
124
68
69
269
3
75
98
60
3
2 2
4
57 10 2
2
6
8
持续改善,消除浪费
实施QCPC – 案例
统计并展示FPY数据,每个车间,具体到每个产品每条拉
Process Yield Wk1 Wk2 First Pass Yield 90.6% 0.0%
数据
持续改善,消除浪费
实施QCPC – 分析
定义
测量
分析
改进
控制
使用QCPC核查表上的折返数据,制作已观察到的“折返率”的巴累托图形
计算
折返 率
=
折返数 进入流程的件数
持续改善,消除浪费
实施QCPC – 分析
计算工序层面的折返率
流程 OP 10
折返数 35
OP 20
101
OP 30
77
OP 40
20000 18000 16000 14000 12000 10000
8000 6000 4000 2000
0
120%
17264
13987
8100%0% 69%
72%
76%
80%
83%
86%
89%
91%
93%
95%
96% 97% 98% 99%
质量控制流程图

质量控制流程图
质量控制流程图是一个纵向展示不同质量控制步骤和相应活动之间关系的图表。
以下是一个基本的质量控制流程图的示例:
质量控制流程图由以下几个步骤组成:
1. 定义质量控制目标:在开始质量控制流程之前,需要明确质量控制的目标和标准。
这包括制定产品或服务的质量要求,并确保团队明确这些要求。
2. 制定质量控制计划:根据质量目标和标准,制定一个详细的质量控制计划。
这包括定义质量控制活动的类型、频率和责任人,并确定质量控制资源的需求。
3. 实施质量控制活动:执行质量控制活动,以确保产品或服务符合质量标准。
这些活动可以包括检查、测试、评估和审核。
4. 收集质量数据:收集质量控制活动的结果和数据。
这包括检查结果、测试数据和客户反馈等。
5. 分析质量数据:对收集的质量数据进行分析,以确定产品或服务的质量水平。
这可以通过统计分析、趋势分析和根因分析等方法完成。
6. 制定改进措施:基于质量数据分析的结果,制定改进措施以提高产品或服务的质量。
这可以包括修复缺陷、改进流程和培训员工等活动。
7. 实施改进措施:执行制定的改进措施,并监控其效果。
这可能需要一段时间,以确保改进措施能够持续改善产品或服务的质量。
8. 持续改进:定期评估和更新质量控制流程,以确保其有效性和适应性。
这可以包括改进质量控制计划、培训员工和采用新的质量控制技术等。
以上是一个基本的质量控制流程图示例,具体流程可能因不同的行业和组织而有所不同。
质量控制流程图用于帮助组织清晰地展示质量控制流程,同时也可作为改进和培训的依据。
质量控制流程图
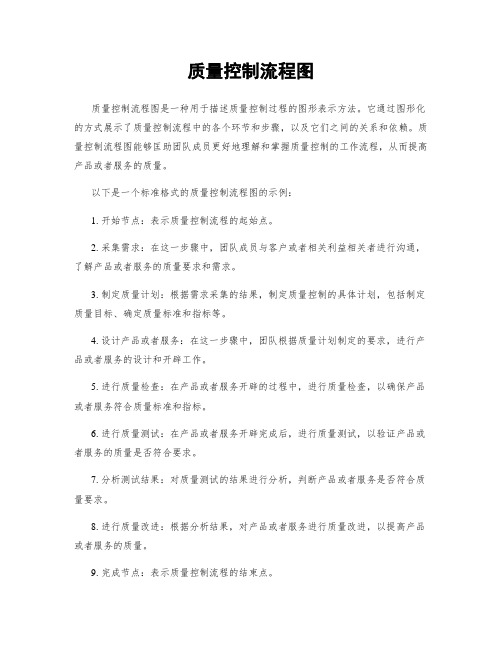
质量控制流程图
质量控制流程图是一种用于描述质量控制过程的图形表示方法。
它通过图形化的方式展示了质量控制流程中的各个环节和步骤,以及它们之间的关系和依赖。
质量控制流程图能够匡助团队成员更好地理解和掌握质量控制的工作流程,从而提高产品或者服务的质量。
以下是一个标准格式的质量控制流程图的示例:
1. 开始节点:表示质量控制流程的起始点。
2. 采集需求:在这一步骤中,团队成员与客户或者相关利益相关者进行沟通,了解产品或者服务的质量要求和需求。
3. 制定质量计划:根据需求采集的结果,制定质量控制的具体计划,包括制定质量目标、确定质量标准和指标等。
4. 设计产品或者服务:在这一步骤中,团队根据质量计划制定的要求,进行产品或者服务的设计和开辟工作。
5. 进行质量检查:在产品或者服务开辟的过程中,进行质量检查,以确保产品或者服务符合质量标准和指标。
6. 进行质量测试:在产品或者服务开辟完成后,进行质量测试,以验证产品或者服务的质量是否符合要求。
7. 分析测试结果:对质量测试的结果进行分析,判断产品或者服务是否符合质量要求。
8. 进行质量改进:根据分析结果,对产品或者服务进行质量改进,以提高产品或者服务的质量。
9. 完成节点:表示质量控制流程的结束点。
以上是一个简单的质量控制流程图示例,实际的质量控制流程可能会更加复杂,具体的步骤和环节可以根据实际情况进行调整和扩展。
质量控制流程图可以匡助团队成员更好地理解和掌握质量控制的工作流程,从而提高产品或者服务的质量。
质量控制流程图

质量控制流程图质量控制是一种系统化的方法,用于确保产品或服务的质量符合预期标准。
质量控制流程图是一种图形化的表达方式,用于展示质量控制过程中各个环节的关系和流程。
下面是一个详细的质量控制流程图的示例,以便更好地理解质量控制的过程。
1. 定义质量标准和目标在质量控制的开始阶段,制定质量标准和目标非常重要。
这些标准和目标应该明确,并且与产品或服务的需求相一致。
2. 设计质量控制计划根据质量标准和目标,制定质量控制计划。
该计划应该包括质量控制的方法、工具和技术,以及质量控制的时间表和责任人。
3. 采集质量数据为了评估产品或服务的质量,需要采集相关的质量数据。
这些数据可以通过各种方式获得,例如实地检查、测试、问卷调查等。
4. 进行质量分析采集到的质量数据需要进行分析,以便了解产品或服务的质量状况。
质量分析可以使用统计方法、图表和其他分析工具来进行。
5. 识别质量问题在质量分析的基础上,识别出产品或服务中存在的质量问题。
这些问题可能包括缺陷、性能不达标、客户投诉等。
6. 制定改进措施一旦质量问题被识别出来,需要制定相应的改进措施。
这些措施应该能够解决质量问题,并且符合质量标准和目标。
7. 实施质量改进将制定的改进措施付诸实施。
这可能包括调整生产过程、培训员工、更新设备等。
8. 监控改进效果改进措施实施后,需要对改进效果进行监控。
这可以通过再次采集质量数据并进行分析来实现。
9. 持续改进质量控制是一个持续的过程,需要不断地进行改进。
根据监控结果,对质量控制流程进行调整和改进,以达到更高的质量水平。
通过质量控制流程图,可以清晰地展示质量控制的各个环节和流程。
这有助于团队成员理解质量控制的要求和步骤,并确保质量控制工作的顺利进行。
同时,质量控制流程图也为管理者提供了一个工具,用于监控和改进质量控制的效果。
请注意,以上是一个示例质量控制流程图,实际的质量控制流程可能因组织和行业的不同而有所差异。
因此,在实际应用中,需要根据具体情况进行调整和修改。
质量控制流程图

质量控制流程图一、引言质量控制流程图是指在产品或者服务的生产过程中,为了确保产品或者服务的质量符合标准要求,所制定的一系列控制措施和流程。
本文将详细介绍质量控制流程图的标准格式及其内容要求。
二、质量控制流程图的标准格式质量控制流程图通常采用流程图的形式进行展示,其标准格式如下:1. 流程图标题:在流程图的顶部中央位置,标明流程图的标题,以清晰地表达流程图的主题。
2. 流程图符号:质量控制流程图中使用的符号应符合国际通用的标准符号,以确保流程图的可读性和易理解性。
常用的符号包括开始/结束符号、流程步骤符号、判断符号、连接线符号等。
3. 流程步骤:在流程图中,每一个流程步骤应以清晰简洁的文字描述和对应的符号表示。
每一个步骤应按照流程的先后顺序进行罗列,以展示整个质量控制流程的逻辑关系。
4. 判断条件:在流程图中,如果存在需要进行判断的条件,应使用判断符号表示,并在符号内部清晰地描述判断条件。
判断条件的结果应包括两个分支,即“是”和“否”,分别对应不同的流程走向。
5. 连接线:流程图中的连接线应准确地连接各个流程步骤,以表达流程之间的逻辑关系。
连接线应使用箭头标识流程的走向,并确保箭头指向正确的流程步骤。
6. 说明文本框:在流程图的适当位置,可以添加说明文本框,用于对流程图中的某些步骤或者符号进行解释和补充说明。
说明文本框的内容应简明扼要,以增加流程图的可读性和易理解性。
三、质量控制流程图的内容要求质量控制流程图的内容要求主要包括以下几个方面:1. 流程步骤:质量控制流程图应准确地展示质量控制的各个步骤,包括质量计划、质量检测、质量分析、质量改进等。
每一个步骤应以清晰简洁的文字描述和对应的符号表示,以确保流程的准确性和易理解性。
2. 质量指标:在流程图中,应明确标明每一个质量控制步骤所涉及的质量指标。
质量指标应具体、可衡量,并符合相关的标准要求。
质量指标的设定应基于产品或者服务的特性和客户需求。
3. 质量控制方法:质量控制流程图应清晰地展示每一个质量控制步骤所采用的质量控制方法。
工厂品质检验控制流程图

首检 尺寸
抽检尺寸
图示 尺寸
首检 尺寸
抽检尺寸
图示 角度
首检 角度
抽检角度
图示 首检 尺寸 尺寸
首检尺寸
图示 尺寸
首检 尺寸
首检尺寸
结果
美兴新型建筑材料(惠州)有限公司
Million Hope-Tech.Building Supplies(HuiZhou)Limited
冲/钻/铣孔加工检验日报表
工程名称:
(6)成品QC对装配 成品进行全检
成品
(4)装配QC员 对配件进行抽检
送地盘
来料控制
一、IQC对型材来料质量控制(标准GB5237.1~5/2008)
1、外观控制: 无变形、刮花、 起泡等;颜色 吻合,无色 差;包装符合 保护要求。
2、尺寸控制:据 模图测量各几 何尺寸,控制 组装性较强位 的公差,膜厚 符合国标及工 程指引要求。
±1.0mm
检测器具或方法
12
用钢尺测量,在受测件外
框两相对端面,距端部
100mm处测量 用钢尺测量,在受测件外
框两相对端面,距端部
100mm处测量 用钢卷尺、∮20圆柱或工
程检测器(专用量具),
测框内角。
用游标深度尺在玉高、宽
度中点处测量
同一水平面高低偏差
≤0.3mm
用游标卡尺或游标深度尺 测量相邻构件取最大值
工厂质量 检 验 控制流 程
(1)I QC对型材来 料进行检验
型材来料
(2)I QC对配件来料 进行检验
(3)制程QC对生产工 序型材进行抽检
合格型材
不合格物料处理
配件来料 合格配件
复合、切割、开角 冲、钻、铣孔(槽) 锣 榫
质量控制流程图

质量控制流程图
质量控制流程图是一种用于描述产品或者服务质量控制过程的图形化工具。
它通过可视化的方式展示质量控制的各个环节和步骤,匡助人们更好地理解和管理质量控制流程。
下面是一个标准格式的质量控制流程图的示例:
1. 开始
- 启动质量控制流程
2. 确定质量标准
- 分析产品或者服务的质量要求
- 制定质量标准和指标
- 确定质量目标
3. 设计质量控制计划
- 制定质量控制计划
- 确定质量控制的方法和技术
- 制定质量控制的时间表和资源需求
4. 实施质量控制
- 进行质量检查和测试
- 采集并分析质量数据
- 评估产品或者服务的质量
- 确定是否符合质量标准
5. 识别问题和改进
- 发现质量问题和缺陷
- 分析问题的根本原因
- 制定改进措施和行动计划
- 实施改进措施并监控效果
6. 完成质量控制
- 完成质量控制流程
- 汇总和分析整个质量控制过程的数据
- 评估质量控制的效果和成果
7. 结束
- 结束质量控制流程
以上是一个简化的质量控制流程图,实际情况中可能会根据具体的产品或者服务的特点进行调整和补充。
质量控制流程图的目的是匡助组织和团队清晰地了解质量控制的步骤和要求,确保产品或者服务的质量符合预期,并持续改进质量水平。
施工过程质量控制流程图

施工过程质量控制流程图一、引言施工过程质量控制是确保工程质量达到预期目标的关键环节。
本文将详细介绍施工过程质量控制的流程图,以便项目团队能够清晰地了解和执行质量控制工作。
二、1. 规划阶段在规划阶段,项目团队需要制定质量控制计划,明确质量目标和要求,并确定质量控制的方法和措施。
流程图如下:(流程图)2. 准备阶段在准备阶段,项目团队需要进行资源准备和培训,确保施工过程质量控制所需的人员、设备和材料的准备工作。
流程图如下:(流程图)3. 施工阶段在施工阶段,项目团队需要按照质量控制计划执行施工工作,并进行实时监控和记录。
流程图如下:(流程图)3.1 质量控制检查在施工过程中,项目团队需要进行质量控制检查,包括对施工材料、施工方法和施工现场进行检查,以确保符合质量要求。
流程图如下:(流程图)3.2 质量控制记录项目团队需要及时记录质量控制检查结果,并进行整理和归档,以备后续的质量评估和验收。
流程图如下:(流程图)4. 总结阶段在施工结束后,项目团队需要进行质量总结和评估,以及对施工过程中发现的问题进行整改和改进。
流程图如下:(流程图)5. 验收阶段在项目验收阶段,项目团队需要按照质量控制计划进行验收工作,并提交相关的质量验收报告。
流程图如下:(流程图)三、结论施工过程质量控制是确保工程质量的重要环节,通过制定质量控制计划、进行质量控制检查和记录、总结和改进等步骤,可以有效提升工程质量。
项目团队应按照流程图的要求,严格执行施工过程质量控制,以确保工程质量达到预期目标。
质量控制流程图

质量控制流程图质量控制流程图是一种用于描述和管理质量控制过程的图形化工具。
它可以帮助组织确保产品或服务的质量符合预期标准,并提供一种可视化的方式来追踪和监控质量控制活动的执行情况。
下面是一个示例的质量控制流程图,用于说明质量控制的各个环节和流程。
1. 质量控制流程图的起点是产品或服务的设计阶段。
在这个阶段,团队会进行详细的产品或服务规划,并制定质量目标和标准。
这些目标和标准将成为后续质量控制活动的依据。
2. 接下来是原材料采购阶段。
在这个阶段,团队会与供应商合作,采购符合质量标准的原材料。
这包括确保原材料的质量认证和合规性,并与供应商建立有效的质量管理体系。
3. 生产或服务过程是质量控制的核心环节。
在这个阶段,团队会执行一系列的质量控制活动,以确保产品或服务的质量符合预期标准。
这些活动包括但不限于以下几个方面:a. 检查和测试:对产品或服务进行全面的检查和测试,以确保其符合质量标准。
这包括使用各种工具和设备进行测量、检验和验证。
b. 过程控制:监控和控制生产或服务过程中的关键参数和指标,以确保其稳定性和一致性。
这可以通过使用统计过程控制(SPC)等工具来实现。
c. 培训和教育:为员工提供必要的培训和教育,以确保他们理解和遵守质量标准和流程。
这可以包括质量教育、技能培训和操作规程的编制。
d. 纠正和预防措施:及时采取纠正措施来解决质量问题,并制定预防措施来防止类似问题的再次发生。
这可以通过使用质量管理工具如8D报告和根本原因分析(RCA)来实现。
4. 完成产品或服务后,团队会进行最终的质量检查和确认。
这包括对产品或服务进行全面的审查和验证,以确保其符合质量标准和客户需求。
5. 最后,质量控制流程图还包括质量记录和报告的环节。
团队会记录和归档所有与质量控制相关的数据和信息,并生成质量报告,以便后续的分析和改进。
质量控制流程图是一个动态的工具,在实际应用中可以根据具体情况进行调整和优化。
通过不断地追踪和监控质量控制活动的执行情况,团队可以及时发现和解决质量问题,并持续改进产品或服务的质量水平。
质量控制流程图

3.1.1 现场质量控制流程图施工准备项工程施工计划施工方案工程质量控制指标检验频率及方法材料、机械、劳动力、现场管理人员准备分项开工报告批准分项开工批复单每道工序施工施工测量放线报告检验试验报告设计施工复核不批准分析原因,及时修复改正或返工材料检查工艺流程检查测量检测试验检测质检工程师检查自检结果工序交接报告不合格抽样检查资料检查试验抽测测量检测工序检验记录检查交工报告不合格合格交工证书现场质量控制流程图3.1.2 质量管理组织机构流程图指挥长生产副指挥长 质量安全 总工程师材 料 厂 科程 工 安全质量试 验 室指挥部质管 工程师质量安全 委员会办指挥部质管 工程师工 程 队 队 程 工 程 队工 质量管理组织机构流程图3.1.3 质量检验总流程图原材料取样不合标准试验格试验结果评定、是否合格试验报告实施控制检验成品抽样检验试验结果评定、是否合格合格不合格作业结论分析原因结束提出处理意见质量检验总流程图3.1.4 工程材料、构配件和设备质量控制流程图承包单位填写《工程材料/构配件/设备报验单》方法:承包单位另选不合格监理工程师审核合格1.审核证明资料2.到厂家考察3.进场材料检验4.进行验证复试承包单位使用工程材料、构配件和设备质量控制流程图3.1.5 技术质量主要工作流程图图纸会审参加设计交底编制施工组织设计工程师审批工程物料确认进场验收技术复核分部工程验收技术交底工程定位交接甲方、监理确认工程师确认隐蔽验收质量验收资料审核甲方、乙方、设计联合验收交付使用送交资料和竣工图回访维修技术质量主要工作流程图3.1.6 创优管理体系流程图单位工程质量检验由总工程师主持、各项目队技术主管、队长及各部门负责人参加单项工程质量检验由总工程师主持、各项目队技术主管、队长及各部门负责人参加各项管理点,由技术室负责施工全过程控制点由工程部负责质量控制及QC 小组活动由领工作业班长主持创全优目标管理由安全质量监察室负责监、检、测制度,分别由监理、副指挥长、技术主管主持,有关人员参加自检、互检、交接检,由作业班长负责目标成本管理:由指挥长主安全生产制度及安全规程手册质量保证持,工程物资、机电、定额、财务部门管理安全预防措施由工程部门制定,随生产计划下达检查制度执行情况由安检工程师负责安全生产保证成本控制保证工料机消耗台账:由调度、材料、机电提供,财务汇总经营活动分析由指挥长主持,财务提供资料,有关人施工人员保证施工保证创优总负责人员参加材料保证择优定点供应保证按标准验收保证优质管理保证施工设备保证施工平面布置图及文明施工要点由工程部门提供具体保证实施条款及督促落实由副指挥长负责文明施工保证技术资料保证可靠性系统性工期保证及时性程序施工,场地整洁,防止污染环境各种原始录、凭证资料、台账,按规定由各部门提供流水施工网络,分项工程施工工序流程科学性、可操作性、实施性施组关键线路、施工总进度控制图3.1.7 工程质量事故处理流程图承包单位严重质量事故一般质量事故按建设部关于《工程建设重大监理部参加业主参加质量事故报告和调查程序》执行总监下达的工程暂停指令承包单位填报工程质量事故报告单设计和承包单位制定事故处理方案监理工程师签发工地指示并督促实施承包人按方案组织实施,监理工程师进行质量检验复查轴线及标高监理工程师复查结果地基处理施工承包单位处理过程抽检监理工程师填报地基处理质量验收签证承包单位监理工程师核验检查结果监理工程师签认基础工程施工监理工程师过程检查填报基础工程质量验收签证承包单位监理工程师核验检查结果合格监理工程师签认不合格承包单位返工有问题不合格承包单位返工口头通知、备忘录、发监理通知不合格承包单位返工承包单位施工口头通知、发备忘录、发监理通知确定回填方案 测量仪器准备熟悉图纸和技术资料准备工作熟悉操作规程和质量标准清理现场、作好排水 清除基底杂物和草皮 回填机械准备分部分项工程书面交底技术交底操作人员参加灰土拌合均匀中间抽查施工自检分层测量填土标高办理回填土隐蔽验收签证 清理现场、文明施工执行验收标准 分层检验填土质量 清除大土块和生石灰块 回填分层,控制厚度质量验收回填土夯实,干密度试验记录 自检记录 质量验收记录 隐蔽验收记录 施工记录资料管理室内:不少于 10%自然 间,但不少于 2 间, 间每 不少于 2 处。
质量控制(QA)工作流程图

质量控制(QA)工作流程图标题:质量控制(QA)工作流程图引言概述:质量控制(QA)工作流程图是一个重要的工具,用于确保产品或服务的质量符合预期标准。
它提供了一个系统性的方法,以确保每个阶段都经过充分的测试和评估,以便在产品或服务交付给客户之前解决任何潜在的问题。
本文将详细介绍质量控制(QA)工作流程图的六个主要方面。
正文内容:1. 测试计划1.1 制定测试目标:明确测试的目的和预期结果。
1.2 确定测试范围:定义需要测试的功能和系统组件。
1.3 制定测试计划:规划测试活动的时间表和资源分配。
2. 测试设计2.1 确定测试用例:根据需求和功能规范,设计测试用例以覆盖各种场景。
2.2 准备测试数据:创建适当的测试数据集,以确保测试覆盖全面。
2.3 编写测试脚本:使用适当的测试工具编写测试脚本,以自动执行测试用例。
3. 测试执行3.1 执行测试用例:按照测试计划执行测试用例,记录测试结果。
3.2 缺陷跟踪和管理:在测试过程中,及时记录和跟踪发现的缺陷,并与开发团队合作解决问题。
3.3 进行回归测试:在修复缺陷后,执行回归测试以确保修复不会引入新的问题。
4. 测试评估4.1 分析测试结果:对测试结果进行仔细分析,识别和分类问题。
4.2 评估测试覆盖率:评估测试用例的覆盖率,确保所有功能和系统组件都得到适当的测试。
4.3 提供测试报告:撰写详细的测试报告,包括测试结果、发现的问题和建议的解决方案。
5. 质量改进5.1 问题解决和修复:与开发团队合作解决发现的问题,并进行必要的修复。
5.2 测试流程改进:根据测试结果和经验教训,改进测试流程和方法,以提高测试效率和准确性。
5.3 培训和知识分享:定期组织培训和知识分享会,提高团队成员的测试技能和质量意识。
6. 最终交付6.1 确认产品可交付:在经过充分的测试和评估后,确认产品或服务达到预期质量标准。
6.2 产品发布:将产品或服务交付给客户,并确保客户满意度。
- 1、下载文档前请自行甄别文档内容的完整性,平台不提供额外的编辑、内容补充、找答案等附加服务。
- 2、"仅部分预览"的文档,不可在线预览部分如存在完整性等问题,可反馈申请退款(可完整预览的文档不适用该条件!)。
- 3、如文档侵犯您的权益,请联系客服反馈,我们会尽快为您处理(人工客服工作时间:9:00-18:30)。
车间质量控制流程图
质检检验自检质控抽检/工序互检
质控流程
一、原材料(辅料)到我司,库管应及时通知质检,
检验外观质量和辅料性能实验;合格后方可接货入库;库管负责人如不通知质检,外观质量不合格、辅料性能实验不合格,由库管负责人承担责任;如原片外观质量、铝条外观、铝条与二次胶
的粘接度、分子筛温升实验(必须让客户带备份分子筛);注:质检按照原材料检验标准进行检验;
二、切割工序:质控员按照公司内控标准、客户要求
及操作规范进行检验和监督;1.质控员要及时对
该工序半成品进行检验,有质量异常及时通知该工段负责人找出原因及时改善,如负责人不及时改善可以直接上报、上级领导给予解决;质检发现质量异常没有及时通知该工序负责人或出现
重大质量事故,对质控部领导和当班质控员进行处罚;2.在切割时发现原片有质量异常,该工序
负责人应及时通知质控员到现场确认,质控员要填写质量异常单,做好投诉原材料供应商的第一首资料;如该工序负责人没有及时通知质控员,
出现质量事故由该工序承担;3.切割LOW-E原
片时,该工序负责人要把箱卡保存好,质控员不
定时的进行抽捡。
如果不按规定操作,后果由工
序负责人承担;4.质控员要及时监督操作员是否
按操作规范进行操作。
(切割LOW-E玻璃时:是
否检验切割刀头油量大小、气孔通畅、台面清洁
度、戴口罩、戴手套、落架、贴软木垫);如不
按操作规范进行操作,质控员要及时处理并通知
该工序负责人;5.该工序补片前要通知质控员到
现场确认玻璃次破原因,方可补片;
三、磨边工序:质控员按照公司内控标准、客户要求
及操作规范进行检验和监督;注:该工序负责人
一定要检验上段工序交接的产品质量,如有异常
处理不了,及时通知质控员进行处理。
不知会质
控员,出现质量事故由该工序负责人承担;1.质
控员要第一时间检测离子水,是否在标准内,有
异常及时通知该工序负责人,如不改善出现质量
事故由该工序负责人承担;2.在生产过程中质控
员要抽捡清洗过来的半成品(清洁度、边部质量、尺寸及对角线偏差)。
有异常要及时通知该工序
负责人,要及时改善,如不改善出现质量事故由
该工序负责人承担;3、打孔前一定要核对好图
纸在进行操作,以防做错(质控员要不定时的进
行抽捡);4. 质控员要及时监督操作员是否按操
作规范进行操。
(磨LOW-E玻璃时:是否检验戴
口罩、戴手套、落架、贴软木垫);如不按操作
规范进行操作,质控员要及时处理并通知该工序
负责人;5. 该工序补片前要通知质控员到现场确
认玻璃次破原因,方可补片;
四、钢化工序:质控员按照公司内控标准、客户要求
及操作规范进行检验和监督;注:该工序负责人
一定要检验上段工序交接的产品质量,如有异常
处理不了,及时通知质控员进行处理。
不知会质
控员,出现质量事故由该工序负责人承担;1.该
工序上片操作员一定要检查每一片玻璃表面的
清洁度及边部质量(如清洗不干净的玻璃粉及胶
带印,吹不干的水迹印、边部有小崩边或掉角,
都会给钢化炉辊道造成不良)有以上质量异常操
作员应及时知会本工序负责人或质控员进行处
理。
上片人员不及时知会,造成质量事故由该工
序负责人承担;2.质控员要对该工序产品做性能
试验,(颗粒度、弯曲度、波筋、应力、抗冲击、落求)钢化前五炉一定要做颗粒度、弯曲度及波
筋,实验结果一定要合格并满足客户要求(以数
据判定结果)。
结果不合格要及时知会该工序负
责人进行改善;(注:该工序要自检)3. 质控员
要及时监督操作员是否按操作规范进行操。
(钢
LOW-E玻璃时:是否检验戴口罩、戴手套、落
架、贴软木垫);如不按操作规范进行操作,质
控员要及时处理并通知该工序负责人;4. 该工序
补片前要通知质控员到现场确认玻璃次破原因,
方可补片;
五、中空工序:质控员按照公司内控标准、客户要求
及操作规范进行检验和监督;注:该工序负责人
一定要检验上段工序交接的产品质量,如有异常
处理不了,及时通知质控员进行处理。
不知会质
控员,出现质量事故由该工序负责人承担;一、
中空产品辅材:1.分子筛灌装前,灌装人员一定
要通知质控员作温升实验,合格后在灌装;(灌
装分子筛一定要按操作流程)2.折铝管前,操作
人员一定要检验铝管的外观质量,如有质量异常
请及时知会该工序负责人或质控员;3.丁基胶涂
在铝管上一定要均匀、平滑不能有断交或少胶。
(丁基胶宽度不能<3mm)如质控员抽捡发现批
量不合格由该工序负责人承担;4.该工序上片人
员:①对LOW-E产品须除膜,自检除膜质量,
是否除干净整齐。
(如除膜不良上片人员一定要知会该工序负责人);质控员在过程中,如抽捡到除膜有批量不合格,该工序负责人承担;②对高透LOW-E产品一定要仔细看清楚膜面,在上片;(该工段人员一定要戴好口罩、白手套,其次保障有足够的光源)5.合片室:①在无尘车间必须戴无尘帽、口罩、白手套或手指套。
(如质控员在抽捡过程中发现该操作人员没有戴无尘帽、口罩、白手套或手指套,对该工序负责人进行处罚。
)②合片人员必须自检清洗过来的玻璃,有质量异常,要及时知会该工段负责人或质控员;③上铝管必须四边均匀一致;6.①下片人员要自检产品外观质量(质控员要进行抽捡)如玻璃四边压力是否一致,有无虚接,(特别注意角部)经过板压后,铝管有无漏分子筛。
如有质量异常及时上报上级领导;②二次密封时:质控员要做胶的基本性能实验(蝴蝶实验、拉断实验)如不合格及时上报并投诉供应商;二次密封胶表面必须光滑平整,不准有气泡花胶;③落架前质控员要对成品外观进行抽捡,如:标签进行抽查,该工段人员要自检。
(如有不符要及时上报该工序负责人或上级领导;)7.质控员抽捡落架产品
时,玻璃表面必须干净,码放整齐。
均匀的垫好软木垫;8.该工序补片前要通知质控员到现场确认玻璃次破原因,方可补片;9.质控员、工序负责人、成品库库管三方进行成品入库(注:中空工序,操作员如不按操作流程及操作规范进行操作,出现质量事故由该工序负责人承担;)六、夹层工序:质控员按照公司内控标准、客户要求
及操作规范进行检验和监督;注:该工序负责人一定要检验上段工序交接的产品质量,如有异常处理不了,及时通知质控员进行处理。
不知会质控员,出现质量事故由该工序负责人承担;1.质控员要监督无尘合片车间人员必须戴无尘帽、口罩、穿无尘衣。
(如质控员在抽捡过程中发现该操作人员没有戴无尘帽、口罩、穿无尘衣,对该工序负责人进行处罚。
)2.质控员对棍压后的产品进行抽捡,如有质量异常及时知会该工序负责人或上报上级领导,(下片人员要自检);3.出高压釜时质控员要进行抽捡,(下片人员要自检)抽捡按照内控标准及客户标准。
如有质量异常及时知会该工序负责人或上报上级领导;4对合格产品进行入库:质控员、工序负责人、成品库库管必须在场;5. 该工序补片前要通知质控员到现场
确认玻璃次破原因,方可补片;注:中空工序,操作员如不按操作流程及操作规范进行操作·,出现质量事故由该工序负责人承担;)
七、客户投诉:。