液态硅胶模具设计要点
光学液态硅胶模具设计方案解析

善和优化。
年推出的 84 像素矩阵式 ADB 模组,代表着光学液态
2.1
个性化设计和多样化发展。图 1 所示为矩阵式 ADB
据实际经验发现,硅胶件受流动方向和累积公差影
硅胶正式进入汽车照明领域,打开的汽车照明系统的
多针齿模组示意图。
液态硅胶材料的收缩率
目前 LSR 材料的收缩率在 2%~2.5%左右,但是根
热传导率低的材料,如钛合金或者是传导率低的树脂
性和一致性。如图 4 所示,加热丝 A、加热丝 B 与加热
阀针与定模仁接触面必须使用隔热帽,其隔热帽选择
材料。
不同区域所需要的加热丝功率,有效控制模温的稳定
丝 C 属于一根加热丝,但是根据科学热量模拟分析,
加热丝 A-1 和 A-4 的加热功率是加热丝 A-2 和 A-3
针对硅胶阀针,也有着特殊要求,也必须使用含
2.4
1
2.5
模具抽真空气设计
光学硅胶在注塑过程中容易裹挟气泡,所以,模
300MPa 以上的承压的材料,为保证隔热板强度,隔热
具必须增加抽真空工序,配置抽真空泵站,其模具密
0.05~0.1mm,如图 3 所示。
圈槽的边缘需要倒圆角处理,放置模具尖钢割坏密封
板 中 间 需 要 增 加 承 压 块 ,承 压 块 比 耐 磨 板 厚 度 高
silicone mold design stage. The field of automotive lighting has special requirements for silicone
products, such as high-gloss mirror, small warpage deformation and no cape flyedge design
液体硅胶产品设计方案模板
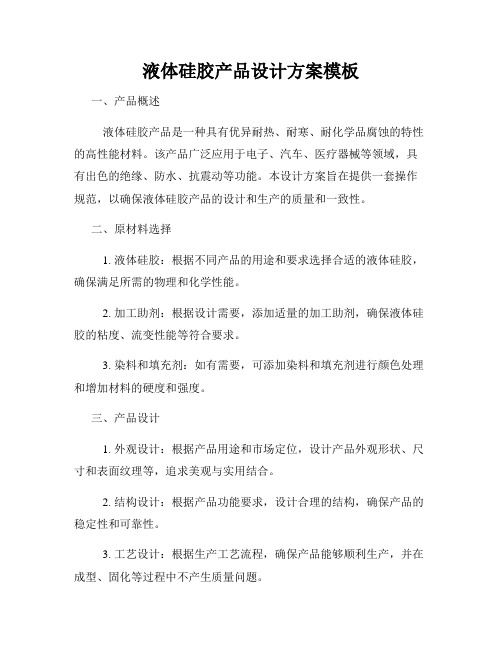
液体硅胶产品设计方案模板一、产品概述液体硅胶产品是一种具有优异耐热、耐寒、耐化学品腐蚀的特性的高性能材料。
该产品广泛应用于电子、汽车、医疗器械等领域,具有出色的绝缘、防水、抗震动等功能。
本设计方案旨在提供一套操作规范,以确保液体硅胶产品的设计和生产的质量和一致性。
二、原材料选择1. 液体硅胶:根据不同产品的用途和要求选择合适的液体硅胶,确保满足所需的物理和化学性能。
2. 加工助剂:根据设计需要,添加适量的加工助剂,确保液体硅胶的粘度、流变性能等符合要求。
3. 染料和填充剂:如有需要,可添加染料和填充剂进行颜色处理和增加材料的硬度和强度。
三、产品设计1. 外观设计:根据产品用途和市场定位,设计产品外观形状、尺寸和表面纹理等,追求美观与实用结合。
2. 结构设计:根据产品功能要求,设计合理的结构,确保产品的稳定性和可靠性。
3. 工艺设计:根据生产工艺流程,确保产品能够顺利生产,并在成型、固化等过程中不产生质量问题。
四、产品制造过程1. 材料配比:按设计要求进行液体硅胶和其他材料的配比,确保各种原材料在适宜的比例下进行混合。
2. 混合:使用搅拌设备对原材料进行充分混合,确保混合均匀,消除气泡等不良现象。
3. 充模:将混合好的液体硅胶倒入模具中,确保模具内部表面涂布均匀。
4. 固化:按设计要求和工艺条件,对液体硅胶进行固化处理,使其在一定时间内达到预期性能。
5. 后处理:将固化后的产品进行去除模具、修整、清洁等后处理工序,确保产品质量。
五、产品质量控制1. 原材料检验:对所采购的液体硅胶和其他原材料进行检测,确保其符合产品质量要求。
2. 生产过程控制:对每个生产环节进行严格的控制和记录,确保产品的一致性和稳定性。
3. 产品检测:对成品产品进行抽样检测,测试其物理性能、化学性能等指标,确保产品质量达标。
4. 不良品处理:对不合格或不良品进行分类、记录和处理,以提高产品质量和生产效率。
六、环境保护1. 废弃物处理:对生产过程中产生的废弃物进行分类、储存和处理,确保环境的卫生和安全。
液态硅胶模具设计要点1.2379

液态硅胶模具设计要点1.2379液态硅胶模具设计要点1.2379液态硅胶模具是一种常用于制作工艺品、玩具、电子产品外壳等产品的模具,它具有耐热、耐磨、精度高等特点,因此在工业生产中得到了广泛的应用。
设计液态硅胶模具时,要考虑到产品的形状、材质、工艺要求等多个方面,以确保最终的模具能够满足生产需要。
在本文中,我将介绍液态硅胶模具设计的要点,并逐步解释每个要点的重要性。
首先,设计液态硅胶模具需要考虑到1.2379材质的选择。
1.2379是一种优质的工具钢,具有较高的硬度、耐磨性和耐热性,非常适合用于制作液态硅胶模具。
这种材质的选择可以确保模具具有足够的耐用性和稳定性,能够承受长时间的使用而不失去精度。
此外,1.2379材质还具有良好的加工性能,可以轻松实现模具的精密加工,从而确保产品的精度和表面质量。
其次,设计液态硅胶模具需要考虑到模具的结构。
模具的结构设计直接影响着产品的成型效果和生产效率。
一般来说,液态硅胶模具的结构应该尽可能简单,以便于脱模和组装。
同时,还需要考虑到产品的具体形状和尺寸,合理确定模具的分型面和开模方式,以确保产品能够完整成型并且易于脱模。
此外,还需要考虑到模具的冷却系统和排气系统的设计,以确保产品的表面质量和减少生产周期。
另外,设计液态硅胶模具还需要考虑到产品的工艺要求。
不同的产品在成型过程中可能需要不同的工艺要求,比如表面光洁度、尺寸精度、壁厚均匀性等。
因此,在设计模具时需要充分了解产品的工艺要求,并根据这些要求合理确定模具的设计参数,比如模腔的尺寸、结构和表面处理方式等。
只有充分考虑产品的工艺要求,才能确保模具能够满足产品的生产需求。
总之,设计液态硅胶模具是一个复杂的工程,需要综合考虑产品的形状、材质、工艺要求等多个方面。
只有在充分了解产品的需求和合理选择材质、设计结构、考虑工艺要求的基础上,才能设计出满足生产需要的液态硅胶模具。
希望本文能够对液态硅胶模具的设计有所帮助。
硅胶模具注意事项
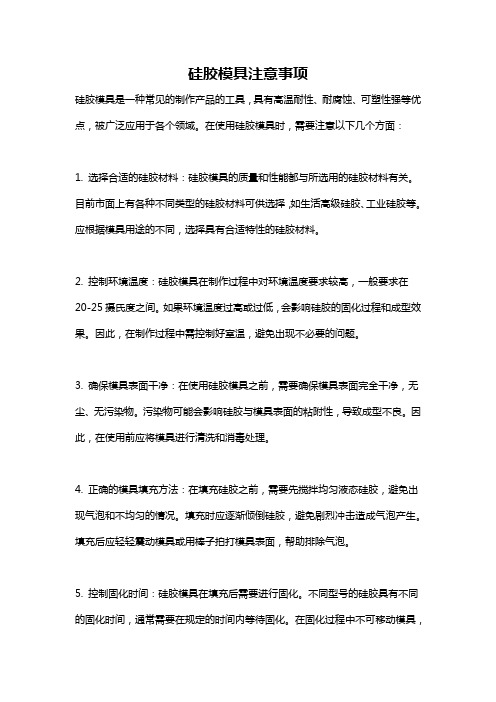
硅胶模具注意事项硅胶模具是一种常见的制作产品的工具,具有高温耐性、耐腐蚀、可塑性强等优点,被广泛应用于各个领域。
在使用硅胶模具时,需要注意以下几个方面:1. 选择合适的硅胶材料:硅胶模具的质量和性能都与所选用的硅胶材料有关。
目前市面上有各种不同类型的硅胶材料可供选择,如生活高级硅胶、工业硅胶等。
应根据模具用途的不同,选择具有合适特性的硅胶材料。
2. 控制环境温度:硅胶模具在制作过程中对环境温度要求较高,一般要求在20-25摄氏度之间。
如果环境温度过高或过低,会影响硅胶的固化过程和成型效果。
因此,在制作过程中需控制好室温,避免出现不必要的问题。
3. 确保模具表面干净:在使用硅胶模具之前,需要确保模具表面完全干净,无尘、无污染物。
污染物可能会影响硅胶与模具表面的粘附性,导致成型不良。
因此,在使用前应将模具进行清洗和消毒处理。
4. 正确的模具填充方法:在填充硅胶之前,需要先搅拌均匀液态硅胶,避免出现气泡和不均匀的情况。
填充时应逐渐倾倒硅胶,避免剧烈冲击造成气泡产生。
填充后应轻轻震动模具或用棒子拍打模具表面,帮助排除气泡。
5. 控制固化时间:硅胶模具在填充后需要进行固化。
不同型号的硅胶具有不同的固化时间,通常需要在规定的时间内等待固化。
在固化过程中不可移动模具,避免对硅胶造成损伤。
6. 模具保养与存储:使用完硅胶模具后,应及时进行模具的清洗和保养。
避免模具长时间暴露在阳光下或恶劣环境中,以免造成模具老化变形。
同时,硅胶模具应存放在干燥通风的地方,避免潮湿和高温环境。
7. 注意使用安全:在使用硅胶模具时应注意自身的安全。
避免硅胶溅入眼睛、口腔等易受伤的部位,避免直接皮肤接触硅胶。
同时,应戴好手套、口罩等防护用具,避免吸入或吞食硅胶。
总之,使用硅胶模具时需要选择合适的材料、控制环境温度、保持模具清洁、注意填充方法和固化时间、正确保养与存储、以及注意使用安全等。
只有正确使用和维护硅胶模具,才能保证其长久使用并获得良好的产品效果。
硅胶模具制作方法

硅胶模具制作方法硅胶模具是一种常用的模具制作材料,它具有良好的柔韧性和耐高温性能,可以用于制作各种复杂形状的模具。
下面将介绍一种简单的硅胶模具制作方法。
首先,准备工作。
我们需要准备好所需的硅胶材料、模具原型、搅拌器、容器等工具。
硅胶材料通常由硅胶液和固化剂组成,按照一定的比例混合使用。
其次,制作模具原型。
模具原型可以是我们需要复制的物体,也可以是我们用其他材料制作的原型。
在制作模具原型时,需要注意保持其表面的光滑和整洁,以便于后续的模具制作工作。
然后,混合硅胶液和固化剂。
根据硅胶材料的配比要求,将硅胶液和固化剂按照一定的比例混合均匀。
在搅拌的过程中,可以轻轻搅拌,避免产生过多的气泡。
接下来,倒入模具原型。
将混合好的硅胶液倒入模具原型的表面,让其完全覆盖模具原型。
在倒入硅胶液的过程中,需要注意避免产生气泡,可以轻轻震动模具原型,让气泡顺利排出。
然后,等待硅胶固化。
根据硅胶材料的固化时间,等待一定的时间让硅胶完全固化。
在固化的过程中,需要将模具放置在平整的表面上,避免发生变形。
最后,取出模具。
当硅胶完全固化后,可以将模具原型从硅胶模具中取出。
此时,我们就得到了一个复制模具,可以用于复制原始物体。
总的来说,硅胶模具制作方法并不复杂,只需要准备好材料和工具,按照一定的步骤进行操作即可。
制作出来的硅胶模具具有良好的柔韧性和耐高温性能,可以满足各种复杂形状的模具制作需求。
希望以上方法对你有所帮助,祝你制作模具顺利!。
液态硅橡胶模具设计的七大要点

液态硅橡胶模具设计的七大要点热固性液态硅橡胶(LSR)注压模具的结构,总的来说跟热塑性胶料所用的模具结构相似,但也有不少显著差别。
例如,LSR胶料一般粘度较低,因而充模时间很短,即使在很低的注射压力下也是如此。
为了避免空气滞留,在模具中设置良好的排气装置是至关重要的。
另外,LSR胶料在模具内不会像热塑性胶料那样收缩,它们往往遇热膨胀,遇冷轻微收缩。
因而,其制品并不总是如所期望的那样留在模具的凸面上,而是滞留在表面积较大的模腔内。
1 收缩率虽然LSR并不会在模内收缩,但它们在脱模和冷却后,常常会收缩2.5%-3%。
至于究竟收缩多少,在一定程度上取决于该胶料的配方。
不过,从模具角度考虑,收缩率可能受到几种因素的影响,其中包括模具的温度、胶料脱模时的温度,以及模腔内的压力和胶料随后的压缩情况。
注射点的位置也值得斟酌,因为胶料流动方向的收缩率通常比与胶料垂直流动方向的收缩率大一些。
制品的外形尺寸对其收缩率也有影响,较厚的制品的收缩率一般要比较薄者小。
如果需进行二次硫化,则可能再额外地收缩 2 分型线确定分型线的位置是设计硅橡胶注压模具的前几个步骤之一。
排气主要是通过位于分型线上的槽沟来实现的,这样的槽沟必经处在注压胶料最后到达的区域内。
这样有助于避免内部产生气泡和降低胶接处的强度损失。
由于LSR粘度较低,分型线必须精确,以免造成溢胶。
即便如此在定型的制品上还常能看见分型线。
脱模受制品的几何尺寸和分型面位置的影响。
将制品设计成稍有倒角,有助于保证制品对所需的另一半模腔有一致的亲合力。
3 排气随着LSR的注入,滞留在模腔内的空气在模具闭合时被压缩,然后随着充模过程而通过通气槽沟被排出。
空气如果不能完全排出,就会滞留在胶料内(这样往往会造成制品部分露出白边)。
通气槽沟一般宽度为lmm-3mm,深度为0.004mm-0.005mm。
在模具内抽真空可创造最佳的排气效果。
这是通过在分型线上设计一个垫圈,并用真空泵迅速将所有的模腔抽成真空来实现的。
液态模具基础知识
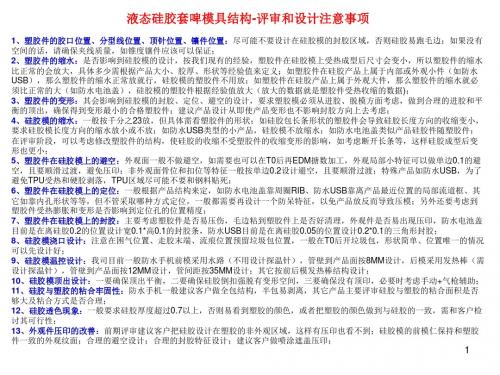
2
液态硅胶设计要点
液态硅胶模与塑胶模的区别
1、成型原理对比: 与塑胶模最大的不同是冷却入水(即入水系统需冷却),模仁加热固化成型(即成型 部分需加热), 刚好与塑胶模成型原理相反; 2、模具结构对比: 流道板和唧嘴走冷水,A板和B板放加热棒(也可以用油温),建议直接模仁设计发热 管,避免 温度损失过快,其它同塑胶模结构一致; 一、唧嘴走冷水,与热嘴原理相反; 二、前后模仁加热,与塑胶模走冷水相反; 三、A板和B板底部加隔热板,防止热传递; 四、进胶口为针点状和翼状,流道板分流道全部密封; 五、顶出多为推块、推板顶出或气枪辅助手动取产品,下不了顶针,因为顶针位易跑批锋,加不了 自拆,但模具温度较高,手动取产品不易;顶出行程注意不能太少,一般高于分型面20MM, 利于清理垃圾。 六、产品有披锋可采用CNC锣自拆或EDM(同固态相同,个人不建议使用); 七、一般不设计镶件结构,镶件处易跑批锋,如果非要镶,可以设计斜度紧配避免或设计顶块加 自拆解决(个人建议); 八、分型面尽可能设计平面,磨床加工,否则CNC加工弧面封胶,易导致批锋,需设计自拆(个人 认为液态硅胶一般不设计自拆); 九、设计完成后检查出模角度,有些虽然考虑到加工没有问题,但模仿顶出后会发现有干涉,所以 倒扣位需加工和出模方式都要考量; 十、排气槽深度不要超过0.005MM.否则会有毛边产生; 十一、了解客户对产品要求,一般选用液态注射对毛边和气纹等都是有很高要求,高光高透和胶料 小于40度瑕疵最易显现; 十二、产品直身可以脱模,即可以不用脱模角度; 3
液态硅胶设计要点
收缩率的定义
1、收缩一般为2.3%左右,与原材料性能及硬度、 成型温度、产品大小有关;一般 硬度越硬,缩水越小;如固态硅胶缩水一般为3.2 %或2.8 %,手机护套放
模具必会的知识点总结

模具必会的知识点总结一、硅胶模具的制作硅胶模具是一种用于制作复杂形状的模具材料,常用于造型、雕塑、工艺品等领域。
硅胶模具的制作需要注意以下几个关键步骤:1.选择合适的硅胶材料硅胶材料有不同的硬度和颜色可供选择,根据模具的使用需求和具体形状来选择合适的硅胶材料。
2.制作原型制作原型是硅胶模具制作的第一步,原型可以是任何形状的物体,通常使用泥土、蜡或者3D打印等材料制作。
3.涂抹分离剂在制作原型的表面涂抹一层分离剂,以便硅胶与原型分离。
4.混合硅胶材料将硅胶材料按照说明书中的比例混合均匀,然后倒入模具框内,以覆盖原型。
5.脱模等待硅胶完全固化后,将模具框拆除,取出原型,即可得到硅胶模具。
二、金属模具的制作金属模具是用于生产工业制品的常见模具类型,其制作过程相对复杂,需要掌握以下几个关键步骤:1.设计模具结构根据所需产品的形状和尺寸,设计模具的结构和尺寸,包括模具的上、下模板、模具芯等部件。
2.选择合适的材料金属模具通常使用工程钢或其他合金材料制作,需要根据产品的使用要求、生产数量和成本等因素选择合适的材料。
3.数控加工利用数控机床等设备将设计好的模具结构加工成实际模具部件,要求尺寸精度高,表面光洁度好。
4.组装模具将加工好的模具部件组装成完整的模具,包括上、下模板的安装,模具芯的安装等。
5.调试模具对组装好的模具进行调试,包括模具的合模性能、开模性能、产品的成型效果等方面的测试和调整。
6.模具表面处理对模具的表面进行处理,包括抛光、镀硬铬等,以提高模具的耐磨性和寿命。
三、模具设计模具设计是模具制作的关键环节,好的模具设计能够提高生产效率、降低生产成本,提高产品质量。
模具设计需要掌握以下几个关键知识点:1.产品结构分析分析所需生产的产品的结构特点,确定产品的形状、尺寸、壁厚等参数。
2.模具结构设计根据产品结构特点,设计合理的模具结构,包括模具的上、下模板、模具芯、冷却系统等。
3.材料选择根据产品的使用要求和生产成本等因素选择合适的材料,包括模具材料和模具零部件材料。
液态硅胶模具制作方法

液态硅胶模具制作方法嘿,你问液态硅胶模具制作方法呀,那咱就来好好聊聊。
首先呢,你得准备好材料和工具哦。
就像要做饭得先把食材和锅碗瓢盆准备好一样。
液态硅胶是主角啦,还有模具的原型,比如说你要做一个手机壳的模具,那手机壳就是原型哦。
然后就是一些工具,像搅拌棒、量杯之类的。
接下来,要把原型处理干净哦。
把它上面的灰尘啊、杂质啊都擦掉,就像给它洗个澡一样,让它干干净净的。
不然这些小脏东西会影响模具的质量哦。
然后在原型表面涂上一层脱模剂,这就像是给它穿上一层滑滑的“衣服”,等会儿硅胶成型后就容易和它分开啦。
然后呢,开始调制液态硅胶啦。
按照一定的比例把硅胶和固化剂倒在量杯里,用搅拌棒慢慢地搅拌均匀。
这个搅拌的过程可要有耐心哦,就像搅拌蛋糕面糊一样,要让它们充分混合。
搅拌的时候要注意不要产生太多气泡哦,不然模具上会有小坑坑的。
如果不小心有了气泡,可以把量杯轻轻敲一敲,让气泡跑出来。
接着,把搅拌好的液态硅胶慢慢地倒在原型上。
要倒得均匀一点,就像给蛋糕抹奶油一样,让硅胶把原型都包裹住。
可以用搅拌棒轻轻地引导硅胶流动,确保每个角落都能被覆盖到。
倒完硅胶后,就把它放在一个安静的地方让它固化。
这个过程就像等蛋糕烤熟一样,需要一点时间。
一般来说,根据硅胶的说明书,等几个小时或者更久一点,硅胶就会变成固体啦。
等硅胶固化后,就可以把模具从原型上取下来啦。
轻轻地把模具剥开,就像剥橘子一样,你会看到一个和原型一模一样的硅胶模具哦。
这时候你会有点小兴奋呢,就像自己完成了一件小艺术品。
比如说你想做一些小饰品的液态硅胶模具。
你准备好一个漂亮的小挂件作为原型,按照上面的步骤一步步来。
涂好脱模剂,调好硅胶,倒在原型上,等它固化。
最后你得到了模具,就可以用这个模具来制作很多一样的小饰品啦。
你可以往模具里倒入各种材料,比如树脂、石膏等,做出各种漂亮的小玩意儿。
是不是很有趣呢 所以呀,液态硅胶模具制作方法其实并不难,只要你细心耐心,就能做出很棒的模具哦。
谈谈硅胶制品模具设计

浅谈硅橡胶产品模具的设计
作者:Chris liu 文锋硅胶May.2012
如今硅胶的应用越来越广泛,从最初主要应用于硅胶按键,防水圈,密封圈等机械,电子产品的配件,现以发展到我们生活的各个方面,比如说我们日常用的餐具,烘焙用具,制冰模等,及日常用的笔记本封皮,手机保护套,平板电脑保护套等各个领域,这些都得益于我们在模具设计上的创新和发展,可以说,一个新型硅胶产品的成功与否,主要是由模具决定的,形成和生产技术相对比较公开和透明。
目前来讲,传统的遥控器,电话机类按键模具开发已经比较成熟,对于一些新型产品的开发和设计,则处理不断地改进之中,本人于2011年初,成功地开发将硅胶材料运用到日常用的笔记本封皮上,开创了硅胶材料新的应用,一时成为高档笔记本的首选,今年初成功地设计并开发出带盖的iPhone 手机保护套,之后又开发出iPad平板电脑保护套,这些都是没有先例的尝试,成功来源对硅胶这种材料本身性能的充分理解及生产工艺与模具设计的完美结合。
硅胶模具设计手册
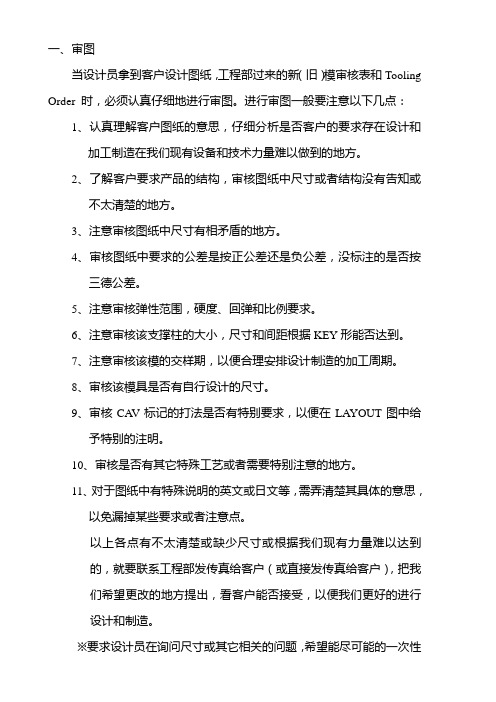
一、审图当设计员拿到客户设计图纸,工程部过来的新(旧)模审核表和Tooling Order 时,必须认真仔细地进行审图。
进行审图一般要注意以下几点:1、认真理解客户图纸的意思,仔细分析是否客户的要求存在设计和加工制造在我们现有设备和技术力量难以做到的地方。
2、了解客户要求产品的结构,审核图纸中尺寸或者结构没有告知或不太清楚的地方。
3、注意审核图纸中尺寸有相矛盾的地方。
4、审核图纸中要求的公差是按正公差还是负公差,没标注的是否按三德公差。
5、注意审核弹性范围,硬度、回弹和比例要求。
6、注意审核该支撑柱的大小,尺寸和间距根据KEY形能否达到。
7、注意审核该模的交样期,以便合理安排设计制造的加工周期。
8、审核该模具是否有自行设计的尺寸。
9、审核CA V标记的打法是否有特别要求,以便在LAYOUT图中给予特别的注明。
10、审核是否有其它特殊工艺或者需要特别注意的地方。
11、对于图纸中有特殊说明的英文或日文等,需弄清楚其具体的意思,以免漏掉某些要求或者注意点。
以上各点有不太清楚或缺少尺寸或根据我们现有力量难以达到的,就要联系工程部发传真给客户(或直接发传真给客户),把我们希望更改的地方提出,看客户能否接受,以便我们更好的进行设计和制造。
※要求设计员在询问尺寸或其它相关的问题,希望能尽可能的一次性问清楚,避免浪费更多的时间。
※另外,随着现代竞争的交样期越来越激烈,在模具行业要求模具的交样期越来越短。
所以对于有些不影响设计或能够先进行设计和制作的模具,则先进行设计与制作等尺寸或结构齐全后进行再重新设计和制造。
例如问弹性壁能否自行设计pim大小的问题,即可先设计,开模(弹性壁暂不做,但要用Ф1.0的刀光R角深度1.0左右,以便EDM碰中用。
放电完后再进行弹性壁的设计及制造,对于交样期较短的模具可以灵活掌握,但要求设计时尺寸应做得稍微保守一些,以便尺寸来了以后可以进接制作或进行更改。
※客户所提供的图纸上,硬度单位一般为shore A,而我们公司橡胶原料的硬度是以Jis为标准的,因此审核图纸或进行弹性壁设计时按以下标准进行硬度的换算。
液体硅胶不同成型方式方法介绍

液体硅胶不同成型方式方法介绍液体硅胶是一种高性能的材料,具有优异的耐热性、耐寒性、耐臭氧、抗紫外线、电绝缘性能等优点。
因此,在工业生产和日常生活中,液体硅胶被广泛地应用于模具制造、电子元件封装、食品加工、医疗器械、家具制造等领域。
液体硅胶成型方式有很多种,下面我们来介绍几种比较常见的成型方式。
一、压模模压成型压模模压成型是液体硅胶制造模具常用的成型方式。
它适用于制作成型精度高、细节复杂的模具,如模具表面呈现的花纹、图案等。
该成型方式要求模具表面光滑,无油污,且需要在涂布模具分离剂之后加工。
具体操作过程如下:1. 选用合适的模具,涂布分离剂。
2. 混合液体硅胶A、B组分。
3. 将混合后的液体硅胶注入模具中,通过压模机施加压力,整个成型过程在常温下完成。
4. 成型完成后,从模具中取出成品,进行下一步的后处理。
二、注塑成型注塑成型是将液体硅胶注入注射成型机中,在高温和高压条件下形成作为成型物的一种成型方式。
该成型方式适用于生产精度高、尺寸规范的硅胶制品,在医疗器械、汽车零配件等领域得到广泛应用。
具体操作过程如下:1. 选用适量的液体硅胶A、B组分,并混合。
2. 料筒预热至适宜的温度,将混合后的液体硅胶注入料筒中。
3. 利用注塑机进行加热和注塑操作,机器将加热后的液体硅胶注入模具中,成形制品。
4. 成品冷却卸模,进行下一步的后处理。
三、流水线工艺流水线工艺是将液体硅胶连续注入成型模具中,通过高温固化、挤出切割等方式,快速、高效地进行生产制品。
该成型方式在食品加工、医疗器械等领域得到广泛应用。
具体操作过程如下:1. 设计制造合适的成型模具。
2. 确定流水线生产过程,制定生产流程的控制方案。
3. 在流水线上设置不同的工位,在工位之间连贯衔接,并对成型过程进行自动化控制和监控。
4. 混合液体硅胶A、B组分,根据生产需要连续注入模具中,进行加热、冷却、切割等操作,在生产线上形成合格的硅胶制品。
液体硅胶不同成型方式各有特点,具体应用需要结合生产需要、技术要求、成本控制等因素进行选择。
液态硅胶模具讲解
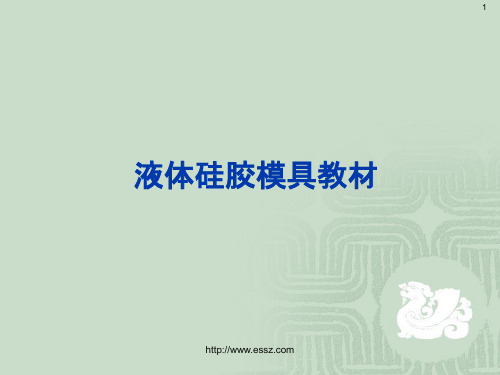
5
1.LIMS 模 具 概 要 No.2
材料是用小罐装或大桶装供给,成型时为全 密封状态,不会混入杂物。
固化是不会产生有害气体,作业环境良好。
6
2.喷嘴的种类
①热流道方式(No.1)
优点
构造简单,价格低廉 模具制作期间短 使用ARBURG设备可
2.喷嘴的种类 ②开放式喷嘴(No.1)
8
喷嘴的分解状态
喷嘴的组装状态
9
2.喷嘴的种类
②开放式喷嘴(No.2)
优点
缺点
构造较为简单,维修 容易
喷嘴本体直径小,可 以制作精细制品
(但进料口平衡的调整 较为困难)
使用直料口会造成进 料口未固化痕迹。
5.模具材质・表面状态&表面处理 ①模具材质 ②模具表面状态 ③模具表面处理
6.隔热板
7.脱模方法
4
1.LIMS 模 具 概 要 No.1
用于LIMS材料注射成形的模具,一般在模腔, 模芯处会用加热杆进行加热。
用LIMS材料生产制品,固化速度为1mm/数 秒。它比压缩成型以及固体成型的成型周期 要短。
短所
构造复杂,价格较 高
需要一定的技术进 行维修
需要成形机的信号 <通常> 开始注射→保压结束
2.喷嘴的种类 ②针阀式喷嘴(No.3)
喷嘴分解状态
13
喷嘴组装状态
14
2.喷嘴的种类 ②针阀式喷嘴(No.4) 始终通过冷却水冷却喷嘴 喷嘴根据成形机信号打开 除喷出工位以外,喷嘴为常闭状态 喷嘴直径 φ0.3~φ2.5
固化时间
・a)模具温度180℃以上: 3-4 SEC/mm ・b)模具温度170℃以上:5-6 SEC/mm
液态硅胶耳塞模具的工艺流程
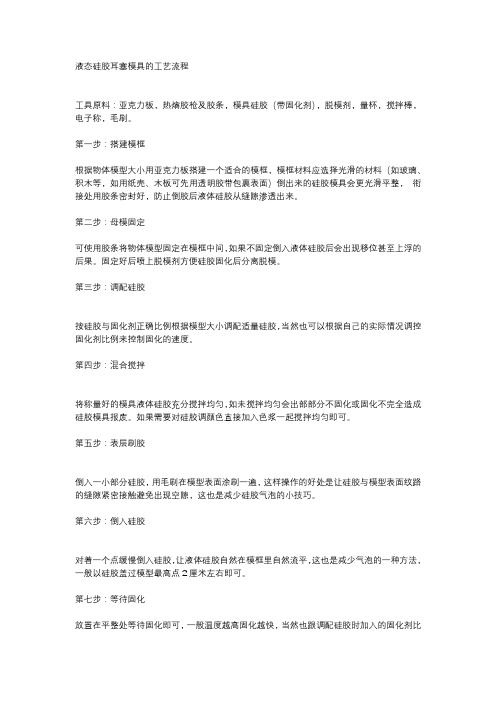
液态硅胶耳塞模具的工艺流程工具原料:亚克力板,热熔胶枪及胶条,模具硅胶(带固化剂),脱模剂,量杯,搅拌棒,电子称,毛刷。
第一步:搭建模框根据物体模型大小用亚克力板搭建一个适合的模框,模框材料应选择光滑的材料(如玻璃、积木等,如用纸壳、木板可先用透明胶带包裹表面)倒出来的硅胶模具会更光滑平整,衔接处用胶条密封好,防止倒胶后液体硅胶从缝隙渗透出来。
第二步:母模固定可使用胶条将物体模型固定在模框中间,如果不固定倒入液体硅胶后会出现移位甚至上浮的后果。
固定好后喷上脱模剂方便硅胶固化后分离脱模。
第三步:调配硅胶按硅胶与固化剂正确比例根据模型大小调配适量硅胶,当然也可以根据自己的实际情况调控固化剂比例来控制固化的速度。
第四步:混合搅拌将称量好的模具液体硅胶充分搅拌均匀,如未搅拌均匀会出部部分不固化或固化不完全造成硅胶模具报废。
如果需要对硅胶调颜色直接加入色浆一起搅拌均匀即可。
第五步:表层刷胶倒入一小部分硅胶,用毛刷在模型表面涂刷一遍,这样操作的好处是让硅胶与模型表面纹路的缝隙紧密接触避免出现空隙,这也是减少硅胶气泡的小技巧。
第六步:倒入硅胶对着一个点缓慢倒入硅胶,让液体硅胶自然在模框里自然流平,这也是减少气泡的一种方法,一般以硅胶盖过模型最高点2厘米左右即可。
第七步:等待固化放置在平整处等待固化即可,一般温度越高固化越快,当然也跟调配硅胶时加入的固化剂比例有关,当温度低于0℃时固化剂会失去活性比较难固化。
第八步:开模取出一般1-2小时即能初步固化,6-8小时左右就可完全固化,固化时间受厚度、温度的影响,等待完全固化后就可以开模取出了。
以上就是关于硅胶模具制作的工艺流程介绍,当然翻模有灌模、分片模、刷模多种方式。
液态硅胶注塑成型工艺

液态硅胶注塑成型工艺
一、前期准备
1.1 确定产品设计图纸及工艺要求。
1.2 选择适合的硅胶材料并进行试验。
1.3 准备注塑机、模具、硅胶预处理设备等。
二、硅胶预处理
2.1 硅胶原料进行混合:将固体硅胶和液态硅胶按照一定比例混合,搅拌均匀。
2.2 去泡:将混合后的硅胶放入真空罐中,去除气泡。
2.3 加热:将真空罐加热至一定温度,使硅胶变得流动性更好。
三、注塑成型
3.1 安装模具:将模具安装在注塑机上,并调整好注射位置和压力。
3.2 加料:将经过预处理的硅胶放入注塑机的料斗中,开启注射器进行加料。
3.3 注射成型:根据产品设计要求,控制好温度、压力等参数,进行注射成型。
同时注意观察模具情况,避免出现漏料或卡模等问题。
四、脱模与修整
4.1 脱模:待产品冷却后,打开注塑机脱模,取出硅胶制品。
4.2 修整:对于有划痕、毛边等问题的产品,进行修整处理。
五、后期处理
5.1 检验:对硅胶制品进行外观检验、尺寸检验等,确保产品符合质量要求。
5.2 包装:将合格的硅胶制品进行包装,标注清晰的产品信息。
5.3 存储:将包装好的硅胶制品存放在干燥、通风、避光的仓库中,避免受潮或受阳光直射。
综上所述,液态硅胶注塑成型工艺需要经过前期准备、硅胶预处理、注塑成型、脱模与修整以及后期处理等多个环节。
在每个环节中都需要严格控制各项参数,并注意观察模具情况和产品质量。
只有这样才能保证生产出符合质量要求的硅胶制品。
人体模型用液体硅橡胶工艺指标

人体模型用液体硅橡胶工艺指标
液体硅橡胶是一种常用于制作人体模型的材料,它具有许多优点,比如柔软、耐用、易于加工等。
以下是液体硅橡胶工艺在制作人体模型时的一些指标:
1. 弹性和柔软度,液体硅橡胶的弹性和柔软度是制作人体模型时需要考虑的重要指标。
它们影响着模型的触感和外观,因此需要根据模型的具体要求来选择合适的硅橡胶。
2. 耐用性,人体模型通常需要经受频繁的移动和变形,因此液体硅橡胶的耐用性是一个重要考量因素。
耐磨、抗拉伸和抗撕裂等性能需要得到充分考虑。
3. 成型工艺,液体硅橡胶的成型工艺包括模具制作、注塑、浇铸等步骤,需要考虑材料的流动性、凝固时间、固化方式等因素,以确保模型的细节和质量。
4. 颜色和质地,液体硅橡胶可以通过添加颜料来调配不同的颜色,同时还可以通过调整配方来改变材料的质地,以满足不同人体模型的需求。
5. 安全环保,液体硅橡胶在制作人体模型时需要符合相关的安全和环保标准,确保模型对人体无害。
总的来说,液体硅橡胶在制作人体模型时需要考虑的指标包括材料的弹性和柔软度、耐用性、成型工艺、颜色和质地以及安全环保等方面。
选用合适的液体硅橡胶,可以制作出质地优良、外观逼真的人体模型。
- 1、下载文档前请自行甄别文档内容的完整性,平台不提供额外的编辑、内容补充、找答案等附加服务。
- 2、"仅部分预览"的文档,不可在线预览部分如存在完整性等问题,可反馈申请退款(可完整预览的文档不适用该条件!)。
- 3、如文档侵犯您的权益,请联系客服反馈,我们会尽快为您处理(人工客服工作时间:9:00-18:30)。
2、在设计模具排气槽有独到经验,保证模具不困气,产品不缺胶。
4,对模具加热部分可用电加热或水,油加热,保证模温均匀,确保产品品质
5、可以设计复杂结构的模具,多层模芯顶出,双物料模具。
7,产品好品率达到95%以上,在国内同行可以说是数一数二的。
由于液态硅橡胶低粘度性,在加工过程中要考虑材料的回流和漏胶,因此对螺杆的止逆环有较高要求,以保证注射入模具的液体硅胶料量准确,不会出现披锋,对模具封胶位有较高要求,典型的排气槽一般宽为1~3 m m, 深为O.O 0 4~ O.OO 5 mm,最好在模具中加装抽真空结构,以保证模腔内的空气及时排出。
如图示为液体硅胶注塑模具,成型产品为医疗产品,该模具特点:
1,产品为PA环(尼龙环)+液态硅胶二次注射成型,硅胶硬度为5度
2、模具采用6组电加热独立控制,保证模温均匀;
3、采用抽真空技术加速模腔内空气的排出,防止困气,缺胶不良;
4,流道系采用冷流道+潜浇品热流道技术
5,分型面用胶圈密封防止抽真空时空气进入模腔
其产品表现为较好的热稳定性、抗寒性、生理惰性,优良的电绝缘性能,燃烧时不会产生有毒的物质等。因此在在医疗产品,婴儿用品,汽车制造,食品行业,电子产品方面潜水用品、厨房用具以及密封件等的生产设计中得到广泛的应用并成为不可替代的材料。
2,液态硅胶的注塑成型特点:
液态硅胶(Liquid Silicone Rubber),分为A 胶与B 胶,利用定量装置控制两者为1:1 之比例,再透过静态混合器(Static Mixer)予以充份混合,泵入注塑机的料筒后再进行注塑成型生产。
150℃),同时硅橡胶具有受压变形的特点。
1)为了避免湍流和喷射,使用小注胶口。
2) 使用针状或翼状注胶口
3) 用T 型导向栓代替柱形导向栓,脱模时气吹方式,加隔热层/板。
4)不要使用含阻聚剂的防锈剂/油,一般可用甲苯、二甲苯等
此外,固化的LSR 容易黏在金属表面上,应用最为普遍的脱模技术包括顶针顶出和空气推顶。
液体硅胶注塑成塑成型概述:
1、液体硅胶
液态硅胶(Liquid Silicone Rubber)是一种无毒、耐热、高复原性的柔性热固性材料,其硫变行为主要表现为低粘度、快速固化、剪切变稀以及较高的热膨胀系数。
LSR是以铂金作为催化剂的双液态快速硫化材料,可以采用注塑的方式、大量、快速硫化、重复性机械生产。
同时塑特威的公司的硅胶成型工艺人员经验丰富,熟悉多种液态硅胶和固体硅胶的成型性能,能合理设定成型工艺参数,并对各种硅胶成型不良缺陷处理有相当丰富的经验。
我们对硅胶成型设备也有相当的了解,对德国雅宝公司的硅胶成型机,德国2KM供料系统有多年使用经验,可以协助客培训操作人员。
科安公司设计模具的特点:
由于LSR 膨胀系数较高,加热时会发生膨胀,冷却时却有微小的收缩,因此部件不能在模具中保持精确的侧边距。所以可以采用冷流道加工,LSR 应保持较低温度和流动性,冷流道采用闭合式系统,在注射循环中,闭合系统在每一个流道中都采用“封胶针”或“针形阀”来控制LSR 材料的准确计量。由于硅橡胶具有显著的受热膨胀特性,收缩率为2~4%(硫化温度为
对工艺参数要求调整合适的流化时间及模温以保证产品能完全固化和不发生变形。一般不用到保压,但要求精确设定料量。
3,液体硅胶模具特点
在模具设计中,一般有以下几种形式:
1) 热流道
比较浪费物料,设计简单,成本低,多用于大制品。
2) 有针阀的冷流道
可实现自动化,周期短。
3) 无针阀的冷流道
科安的模具工程设计人员,在硅胶模具的设计及制造上,有长达8~10年的工作经验,有着多家世界500强公司合作或工作经验,并随时学习接触最新的设计及硅胶产品成型工艺。我们常用的设计软件有CAD、Pro/E、MasterCam、SolidWorks、UG。我们经年累月的为客户设计并制造各种形式的模具,从简单的双层平板模、双层凹凸模、到结构复杂的三层模、四层模、活动模芯模、多层模芯顶出模、转射模(Transfer mold)、注塑模(Injection mold)、热流道液态硅胶注塑模、冷流道液态硅胶注塑模等,我们都有相当丰富的设计及制造经验。
8,设计的模具可适用立式注塑机,卧式液态硅胶射出机,热压流化