高速重轨线万能精轧机设备的故障分析和诊断张建伟_084843
高速线材轧机机械故障诊断系统

高速线材轧机机械故障诊断系统【摘要】我国的高速线材轧机是在上个世纪六十年代才从国外引进,随着线材生产技术的不断改进和发展,高速线材轧机所生产的产品无论是在规格还是质量方面,都比最初引进时有了很大的提高,尤其近几年建筑行业的迅猛发展,直接推动了高速线材轧机产品数量的增长和质量的提升,高速线材轧机也跟上时代发展的步伐,更加适应了现代社会对高速线材轧机产品的经济和技术需求。
【关键词】高速线材;轧机;故障诊断导语虽然我国高速线材轧机生产技术在近几年得以良好的发展,但是高速线材轧机在运行过程中往往容易出现故障。
高速线材轧机作为一个大型的机械设备,国内很多企业对它都没有一个完善的故障检测系统,这就大大影响了企业的正常工作。
所以高速线材轧机的故障诊断技术被越来越多的企业重视,企业原有的单一的检测系统已经不能适应整个企业工业化生产的需求[1]。
本文将和现代化信息技术结合,从高速线材轧机的系统结构出发,具体的分析高速线材轧机整体故障的诊断方法,希望对其相关企业具有借鉴作用。
1 高速线材轧机故障诊断系统的结构高速线材轧机机械的故障诊断系统主要由五个部分组成,分别是:测量速度电据处理器。
其中测量速度电板的作用是对每台高速线材轧机流水线输出产品的速度进行检测并记录,这项数据将是整个故障诊断系统的必要辅助工具;供油压力、供油流量以及设备温度检测器可以对高速线材轧机设备中的每一个检测位置的温度、不同位置的供油压力和供油流量在同一时间内统一进行检测,并且检测数据将同步在电子屏幕上显示;综合信号处理器主要是将高速线材轧机设备在工作过程中发出的所有信号进行统一的处理后,发送给综合数据储存中心;数据储存器主要是进行信息数据的初步采集,再对所采集的数据进行系统识别,并将最终的数据信息分类传给数据处理器;数据处理器则是将数据储存器传来的数据进行接收,再应用专业的高速线材轧机故障诊断系统对所有数据进行分析和诊断,并最终给出详细的诊断报告。
高速无扭精轧机组设备故障诊断分析

高速无扭精轧机组设备故障诊断分析高速无扭精轧机组是金属材料的精密加工设备,广泛应用于轧制不锈钢、铜、铝及其合金等材料。
在生产过程中,设备故障的出现会给生产带来严重影响,因此及时准确地诊断故障并采取正确的维修措施对于保障设备正常运转和生产进度至关重要。
本文将对高速无扭精轧机组设备故障诊断分析进行阐述,希望能对相关从业人员有所帮助。
一、故障现象描述1. 外径尺寸偏大或偏小:在生产过程中,外径偏大或偏小是一种常见的故障现象。
当外径偏大时,产品无法满足客户的要求,造成浪费;而当外径偏小时,则会影响产品的装配和使用效果,同样会给企业带来损失。
2. 螺纹拉伸不达标:在生产过程中,如果螺纹的拉伸性能达不到标准要求,那么产品的使用效果和安全性都会受到影响,严重时甚至会导致产品报废。
3. 生产效率低下:生产效率是衡量设备运行状态好坏的重要指标之一,如果生产效率低下,将会直接影响企业的产能和经济效益。
二、故障原因分析1. 设备磨损严重:设备长时间使用后,往往会出现各种磨损现象,比如轧辊表面磨损、导轨磨损等,这些磨损会直接影响设备的精度和稳定性。
2. 设备使用不当:操作人员在使用设备时如果没有按照操作规程进行操作,比如轧辊调整不当、刀具使用不当等,都可能会导致设备故障的发生。
3. 部件松动:高速无扭精轧机组设备中的各种连接部件,比如螺栓、销轴等,如果松动或者脱落,都会影响设备的正常运转。
4. 部件损坏:设备中的各种部件,比如轴承、齿轮等,如果损坏或者磨损严重,都会导致设备故障的发生。
5. 润滑不良:设备运行时需要一定的润滑保养工作,如果润滑不良或者润滑油污染,都会影响设备的正常运转。
三、故障诊断方法1. 视觉检查:通过对设备各个部位进行外观检查,观察是否存在明显的异常情况,比如磨损、松动、脱落等。
2. 测量检查:通过使用测量工具,比如卡尺、游标卡尺等,对设备的各个关键尺寸进行测量,查找是否存在超出标准的情况。
3. 振动检测:利用振动检测仪等工具,对设备运行时的振动情况进行监测,判断设备各部位轴承、齿轮等是否存在异常。
线材精整设备故障原因分析与改进措施

线材精整设备故障原因分析与改进措施【摘要】线材精整设备在使用过程中难免会受到各种因素的影响,导致设备运行发生故障,损坏设备性能。
为此,本文从线材精整设备故障原因入手,对设备在运行使用中存在的各种问题,以及对应的原因进行分析,并在此基础上探讨问题的解决对策,总结出相关结论,供同行参考。
【关键词】线材精整设备;故障;产生原因;改进措施;分析线形精整设备与系统由多个部分组成,如散卷冷却线、集卷收集系统、PF 运输线、打包机等。
这些构成部分在实际运行时难免会发生运行故障,致使企业的生产节奏被打乱,生产效益降低。
为此强调,在线材精整设备运行过程中,一定要控制好设备质量与性能,防止设备在运行过程中发生故障,影响生产。
下面,笔者结合线材精整设备的故障原因,对设备故障的防范以及控制措施作详细分析。
1.线材精整设备运行中存在的问题由前言可知,线材精神整设备主要由四大部分构成,所以该设备如果在实际运行中发生了故障,其故障产生原因极有可能是因为四大部分运行不当引起。
线材精整设备运行使用过程中存在的主要问题有以下几种:1.1散卷冷却线首段辊道问题散卷冷却线在线材精整设备运行中发挥的作用是输送线材成品盘卷,以及冷却盘卷。
该装置的首段安装在吐丝机后方,而经由吐丝机成卷过后的产品正好可以落到散卷冷却装置的首段辊道上,然后在辊道的移动下被输送、运走。
一般来说,散卷冷却线辊道只会设置12段,供420根辊子,在12段辊道中,第一段或首段是最容易发生故障的部位。
由于散卷冷却线辊道采用单侧链集中传动做传动方式,所以在辊道传动过程中,必须频繁启停辊道,这样才能实现钢材的有效传送。
从功能方面看,这种钢材传送方式是可行的,但是分析传送效果,则辊道在频繁启停过程中很容易发生停止跳动、辊道变形或辊道断裂问题,导致散卷冷却线无法正常工作,从而影响到精整设备的运行质量。
1.2 P/F运输线的问题P/F运输线位于集卷站下部,起到的作用是接收盘卷,然后对盘卷进行输送,并在输送过程中对盘卷进行冷却,切割、捆绑和称重。
高速线材精轧机常见故障分析与故障诊断方法研究本科毕业论文

学号:1006060113Xingtai Polytechnic College毕业论文GRADUATE DESIGN论文题目:高速线材精轧机常见故障分析与故障诊断方法研究学生姓名:专业班级:材料成型与控制技术院系:资源与环境工程系指导教师:目录摘要 (2)ABSTRACT (2)引言 (4)1 高速线材轧机的发展 (5)1.1线材轧机的发展与高速线材轧机的诞生 (5)1.2高速线材轧机的发展概况 (5)1.2.1高速线材轧机机型 (5)1.2.2高速线材轧机的发展与成熟 (6)1.2.3高速线材精轧轧机的典型结构 (7)2 高速线材精轧机的故障机理和故障特征 (8)2.1精轧机轴承的故障机理和故障特征 (8)2.1.1滚动轴承常见故障形式 (9)2.1.2滚动轴承的震动信号特征 (10)2.2精轧机齿轮的故障机理和故障特征 (11)2.2.1齿轮常见的故障形式 (11)2.2.2齿轮的震动信号号特征 (12)3 高速线材精轧机故障诊断方法研究 (13)3.1精轧机振动信号的时域波形分析 (14)3.2精轧机振动信号的幅值域分析 (15)结论 (15)致谢 (16)参考文献 (18)摘要精轧机组是线材厂的关键设备,对精轧机组进行在线监测,可以提前预知设备的工作状态以及故障的发展趋势,对保证企业的安全生产有重大意义。
锥齿轮箱是精轧机的重要零部件,因此研究锥齿轮箱的诊断技术对于降低设备维修费用,提高产品质量和市场竞争力具有重要的工程应用价值。
论文针对高速线材精轧机故障开展研究,利用便携式仪器,对关键设备进行点检,按照一定周期采集设备的振动数据进行统计并分析。
以曲线形式反映在系统工作站,成功捕捉到精轧机的各种故障,避免了恶性事故的发生,取得了显著的经济效益。
关键词: 高速线材轧机;齿轮箱;在线监测;故障研究ABSTRACTThe finishing mill is the key part of high speed rolling mill. The working condition andfault trends can be predicted by the on-line monitoring and fault diagnosis system, whichis very important to ensure the safety in production. Bevel gear box is an important component of finishing mill, therefore to study the diagnosis technology of bevel gear box to reduce equipment maintenance costs, improve product quality and market competitiveness has important engineering application value. Paper for high speed wire rod finishing mill failure to carry out the research, the use of portable instruments, the key equipment to check, according to certain cycle vibration dataacquisition equipment for statistics and analysis. Workstation in curve form reflected in the system, successfully capture the finishing mill all kinds of fault, to avoid the malignant accident, has obtained the remarkable economic benefits.Keywords: High-speed wire mills; Gear Box; On-Line Monitoring; Fault diagnosis;引言企业的发展动力来源于员工的较高素质,员工的专业知识与技能的熟练握是企业高效率生产及操作技能水平。
轧机设备典型故障及解决方法分析

轧机设备典型故障及解决方法分析发布时间:2021-07-12T01:14:58.968Z 来源:《中国科技人才》2021年第11期作者:刘化佳[导读] 例如轧机液压系统。
液压装置受损通常是在液压系统深层位置,液压系统体积大,无法及时拆卸,检测条件有限,无法直接观测表面症状判断故障。
山钢股份莱芜分公司检修事业部山东省济南市 271104摘要:轧机是冶金生产企业的关键设备,一旦出现故障,就会导致生产被迫中断,直接造成巨大的经济损失,有时还很可能会产生连锁反应,导致整个设备损坏,更严重地会造成人员安全事故。
故障诊断法是综合信息处理技术和计算机技术等多种技术的方法,广泛使用在轧机设备维护过程中。
使用故障诊断法一方面可以延长轧机使用期限,节省维护费用和时间,一方面可以提高轧机使用效率。
基于此,本文对轧机设备典型故障及故障诊断方法进行了探讨。
关键词:轧机设备;典型故障;故障诊断方法1轧机故障特殊性分析1.1故障点隐蔽例如轧机液压系统。
液压装置受损通常是在液压系统深层位置,液压系统体积大,无法及时拆卸,检测条件有限,无法直接观测表面症状判断故障。
如果在轧机的液压系统中,筏板内有堵塞的情况出现,就会影响到轧机液压系统的运行,阻碍故障点诊断和查找。
1.2故障因果关系烦琐压轧机设备故障症状和原因之间存在重叠关系,某个故障可能由于多方原因导致出现问题,或者可能是由于多种故障诱发产生的问题,阻碍后续故障诊断和排查。
1.3故障影响因素特征轧机设备在运行时会受到多种因素影响,比如电网电压,工作任务温度等,故障发生点和方向也存在着随机性,增加了诊断故障和处理故障的难度。
1.4故障分散性故障失效分布有着分散性特征,同时它也和设计的使用环境、加工材料有关系,轧机内部的元件在使用时可能会出现严重磨损,甚至轧机内部的关键元件使用期限也存在差异,让故障处理效果受到影响。
2轧机设备典型故障2.1轧机传动系统故障(1)张力波动大比较常见。
国产高速线材精轧机辊箱常见故障分析及处理措施之欧阳学创编

*时间:2021.03.03 创作:欧阳学国产高速线材精轧机辊箱常见故障分析及处理措施1前言承抱死等事故。
韶钢高速线材厂二线精轧机组是国产仿摩根五代高速线材轧机, 轧制速度可达 90m /s, 自 2008年 3 月投产以来, 轧机辊箱的故障较多, 延误生产时间造成人力物力消耗, 严重影响和制约了生产, 使得设备维护压力增加, 设备消耗也增加了生产成本。
针对辊箱出现的常见故障, 笔者进入了深入的分析, 并采取了相应的解决方案及预防措施, 故障大大降低, 辊箱平均使用寿命由初期的 2个月提高到平均 7个月, 部分使用寿命达到了 12个月, 取得了良好的效果, 达到国产精轧辊箱维护的先进水平。
生产中精轧机辊箱故障频繁发生给生产带来严重影响, 为此辊箱发生的一些故障进行分析总结, 并进行1. 油膜轴承5. 固定卡板2. 轧辊轴6. 铜螺丝3. 弹性垫片7. 调整丝杆4. 角接触球轴承8. 偏心套[ 1]精轧机组辊箱常见故障如下。
( 1) 轧辊轴窜动超标, 将影响到成品质量, 特别是出成品的机架, 严重则造成堆钢、辊环炸裂及轧辊轴与油膜轴承抱死等故障。
( 2) 进水问题一直严重影响正常生产, 并常使油品严重污染、乳化, 滤芯堵塞, 造成经常调闸、轴承等磨损加剧或烧油膜轴承等恶性循环现象, 经常性故障造成大量人力及备件损耗, 维护成本高。
( 3) 油膜轴承烧毁, 严重的出现轧辊轴与油膜轴3辊箱常见故障分析针对精轧辊箱出现的以上常见故障, 分别进行深入分析, 总结如下。
( 1) 造成辊箱轧辊轴窜动超标的因素弹性垫片的质量直接影响辊箱轧辊轴及轴承的使用, 弹性垫141整改。
辊箱结构如图 1所示。
到位, 轧制过程中受轧制冲击或振动等影响后弹性垫片变形后, 弹性垫片与轴承间出现间隙, 轧辊轴窜动超标, 严重的冲断轴端挡板螺栓或压盖紧固螺栓; 由于装配过程轴承压盖或端概螺栓安装力矩不均匀, 部分螺栓无有效防松措施, 受轧制冲击振动影响, 轴承压盖或端盖紧固螺栓松动或断裂, 轧辊轴窜动超标。
高速线材轧机机械故障诊断系统
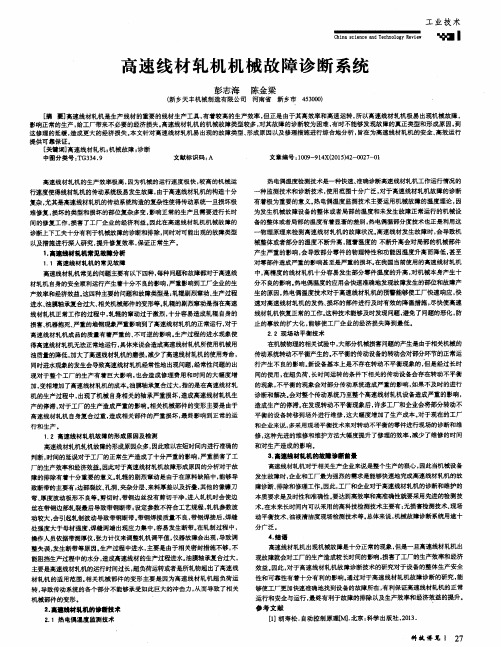
C hi na s ci e n c e a nd T e c h n o l o g y R ev i e w
●I
高 速 陈金梁
( 新 乡天 丰机 械制 造 有 限公 司 河南 省 新 乡市 4 5 3 0 0 0 )
传动系统转动不平衡产生的。 不平衡的传动设备的转动会对部分环节的正常运
行 产生 不 良的影 响。 新设备 基本 上是 不存在 转动 不平衡 现象 的 。 但是 经过 长时
间的使用, 在超负荷、 长时间运转的条件下相关的传动设备会存在转动不平衡
的现象 , 不平衡 的现 象会对 部分 传动 系统 造成严 重 的影响 , 如果 不及 时 的进 行
2 . 2现 场 动平衡 技术
在机械 物理 的相关试 验中 , 大 部分机 械损害 问题 的产 生是 由于 相关机械 的
油质量的降低 , 加大了高速线材轧机的磨损, 减少了高速线材轧机的使用寿命 ,
同时进 水现象 的发生 会导致 高速线材 轧机 经常 性地 出现 问题 , 经常 性 问题 的 出 现对 于 整个 工厂 的生 产有 着 巨大影 响 , 也 会造 成修 理费 用和 时 间的大 幅度 增 加, 变相增 加 了高 速线材 轧机 的成 本 。 油膜轴 承复合过 大 , 指的是在 高速线 材轧
间的修 复工作 , 损害 了工厂企 业 的经济 利益 。 因此在高 速线 材轧机 机械 故 障的
种 监测 技术和 诊 断技术 , 使 用范 围十分 广泛 , 对 于高速 线材 轧机 故障 的诊 断
有着 极为 重要 的意义 。 热电偶 温度 监测技 术主要 运用 机械 故 障的温度 理论 , 因
速 对高 速线材 轧机 的发 热 、 损坏 的部件 进行 及时有 效 的降温措 施 , 尽快 使高 速
精轧机故障分析

由于高线轧机粗、精轧机故障率较高的问题,轧钢厂一般采用在线监测技术加强对这两类设备的管理与维护。
大大提高了故障预测和诊断准确率。
经过实践,在线监测系统对大型厂的设备安全可靠运行起到积极的保障作用,降低了设备故障率,减少了故障停机台时,能使轧钢厂的设备管理水平提升一个新台阶。
1 高线精轧机传动系统简图下图是高线精轧机传动系统简图,该机组10个机架安放于整体刚性底座上,由一台电机集中传动。
主电机经增速机输入轴上的大齿轮带动两根输出轴,通过齿形联轴节与两根传动轴相联,分别驱动左右两侧的机架。
2 常见故障精轧机结构紧凑,各机架的伞齿轮箱零部件等不具备互换性,且价格昂贵,备件量很少,设备一旦发生事故就很可能酿成严重的后果,因此监测设备的运行状况并准确及时进行处理是精轧机设备维护的重要内容。
精轧机的监测主要包括振动、声音、温度、润滑油品、轴承间隙变化等多方面进行跟踪检测,其中振动监测采集方便、分析手段多样、结果准确等特点,是设备状态监测主要手段。
2.1机架振动值不稳定27#精轧机的伞齿轮箱检修后在试车过程中发现了异常现象。
空负荷试车转速在60%时检测27#机③点径向的振动速度为0.8mm/s,当递增到70%时,振动出现明显增大,达到4.5mm/s,继续提升到77%后振动速度达到8.9mm/s。
按照该速度进行生产,轧机带上负荷后,振动值降到4.7mm/s,但在轧制的间隔时间即无负荷时振动又回升到8.9mm/s,该机架其他各点检测也有类似的现象,但幅值略小。
空负荷与负载时检测的27#机运转时的振动频谱异常。
从频谱来看确认该机架存在明显的不平衡故障,且带有一定的不对中。
在轧机负载时基频的幅值降到3.61 mm/s,这说明主动伞齿轮轴的不平衡量是变化的,即轧机的负载改变了主动伞齿轮轴的不平衡程度。
之后对27#机主动伞齿轮轴进行检查,发现主动伞齿轮轴与增速箱之间的联轴器外套法兰面没有完全贴合,有一个位置存在0.2mm的间隙,进行处理重新安装后检测27#机空载为2.0mm/s,负载时为2.8mm/s,设备恢复正常。
高速缝纫机常见故障分析及维修

高速缝纫机常见机械故障分析及维修一、跳针(一)偶然性跳针。
1.原因一:机针尖发毛、机针弯曲、机针槽不光滑或选择不当。
排除方法:更换合适的新机针。
2.原因二:机针安装歪斜,机针与旋梭距离不当。
排除方法:调整机针与旋梭尖的距离,使之在标准范围内。
3.原因三:缝线粗细不匀,捻度不匀,影响线环形成。
排除方法:按标准选择质量好的缝纫线。
4.原因四:针杆高度位置不对。
排除方法:调整针干高度。
5.原因五:旋梭嘴磨损。
排除方法:修磨、抛光。
6.原因六:压脚压力过小,缝线抖动,压不住线,影响成环。
排除方法:加大压脚压力。
7.原因七:压脚槽太宽,机针刺布退出时,面料上升影响线环形成。
这种情况缝薄料时影响最大。
排除方法:根据面料将压脚移左、右,可将宽槽用焊锡填满。
8.原因八:挑线簧太低,面料、针、线匹配不当。
排除方法:适当调高挑线簧。
9.原因九:针板孔太大,缝薄型面料时面料随机下降,延迟线环的形成。
排除方法;更换新针板。
10.原因十:旋梭定位不标准,梭尖与机针左右距离太远。
排除方法:按标准适当调整(二)连续性跳针1.原因一:高速缝纫时,机针和线发热,使缝线软化,难以形成理想的线环。
排除方法:使用化纤线高速缝纫时,可采用在面线的过线处加硅油冷却,或采用压缩空气对机针进行吹风冷却。
2.原因二:上线拉力太大,缝线受到较大的拉伸作用,线环不易形成。
排除方法:调小上线张力,使缝纫线在缝料下面时受到的拉伸尽量小。
3.原因三:缝制厚薄不同的过渡部位,或缝纫不同软硬、松紧的面料所造成的跳针。
排除方法:根据面料薄厚及其性质,及时调整机器各零部件的配合尺寸。
在厚薄过度的地方,放慢速度缝纫。
二、断面(上)线锁式线迹由上线、下线交织而成,因此可分为断面线和断底线两类。
面(上)线所经过的零部件较多,其原因较为复杂。
(一)平缝机一启动上线即断1.原因一:机针装反或针柄未顶到位。
排除方法:检查机针及针柄。
2.原因二:上轮倒转。
排除方法;检查上轮转动方向。
高线精轧机设备故障诊断技术及在生产中的运用

北方钒钛2019年第3期高线精轧机设备故障诊断技术及在生产中的运用张建业周海波徐国峰张雪冬宋艳辉(线材事业部)0引言机械设备的大型化、连续化、高速化和自动化的发展带来了生产效率的提高、成本的降低,以及能源和人力的节约,然而一旦发生故障,就会造成很大的损失。
因此就需要及时、准确、预测出设备的运行状态。
所谓设备诊断技术,就是“在设备运行中或基本不拆卸全部设备的情况下,掌握设备运行状态,判定产生故障的部位和原因,并预测预报未来状态的技术”。
因此,它是防止事故的有效措施,也是设备维修的重要依据。
采用此项技术能够克服“过剩维修”及“维修不足”,从而达到设备寿命周期费用最经济和设备综合效率最高的要求。
1振动诊断技术的应用1.1机械故障诊断的内容包括以下三个方面:1)设备运行状态的监测———根据机械设备在运行时产生的信息判断设备是否运行正常,其目的是为了早期发现设备故障的苗头。
2)设备运行状态的趋势预报———在状态监测的基础上进一步对设备运行状态的发展趋势进行预测,其目的是为了预知设备劣化的速度以便为生产安排和维修计划提前作好准备。
3)故障类型、程度、部位、原因的确定———最重要的是故障类型的确定,它是在状态监测的基础上,当确认机器已处于异常状态时所需要进一步解决的问题,其目的是为最后的诊断决策提供依据。
1.2故障诊断的基本方法:1)简易诊断法传统的直接观察法,如“听、摸、看、闻.”是早已存在的古老方法,并一直沿用到现在,在一些情况下仍然十分有效。
但因其主要依靠人的感觉和经验,故有较大的局限性。
简易诊断法指主要采用便携式的简易诊断仪器,如测振仪、声级计、工业内窥镜、红外点温仪对设备进行人工巡回监测,根据设定的标准或人的经验分析,了解设备是否处于正常状态。
若发现异常,通过对监测数据分析进一步了解其发展的趋势。
因此,简易诊断法主要解决的是状态监测和一般的趋势预报问题。
是机械维护工人和设备管理人员经常使用的方法。
2)精密诊断法精密诊断法指对已产生异常状态的设备采用精密诊断仪器和各种分析手段(包括计算机辅助分析方法、诊断专家系统等)进行综合分析,以期了解故障的类型、程度、部位和产生的原因及故障发展的趋势等问题。
高速无扭精轧机组设备故障诊断分析
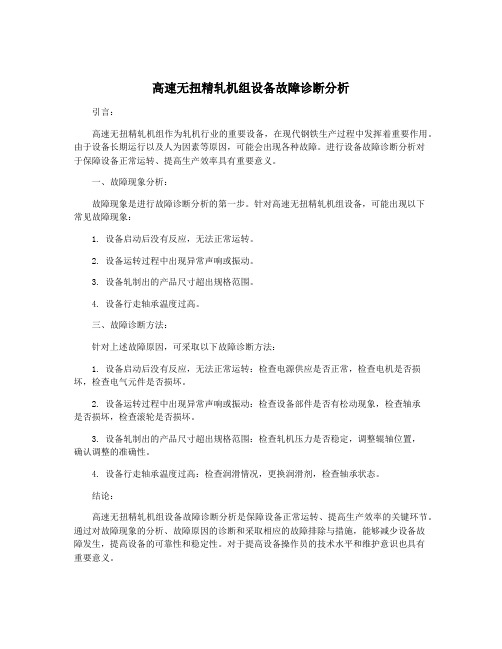
高速无扭精轧机组设备故障诊断分析
引言:
高速无扭精轧机组作为轧机行业的重要设备,在现代钢铁生产过程中发挥着重要作用。
由于设备长期运行以及人为因素等原因,可能会出现各种故障。
进行设备故障诊断分析对
于保障设备正常运转、提高生产效率具有重要意义。
一、故障现象分析:
故障现象是进行故障诊断分析的第一步。
针对高速无扭精轧机组设备,可能出现以下
常见故障现象:
1. 设备启动后没有反应,无法正常运转。
2. 设备运转过程中出现异常声响或振动。
3. 设备轧制出的产品尺寸超出规格范围。
4. 设备行走轴承温度过高。
三、故障诊断方法:
针对上述故障原因,可采取以下故障诊断方法:
1. 设备启动后没有反应,无法正常运转:检查电源供应是否正常,检查电机是否损坏,检查电气元件是否损坏。
2. 设备运转过程中出现异常声响或振动:检查设备部件是否有松动现象,检查轴承
是否损坏,检查滚轮是否损坏。
3. 设备轧制出的产品尺寸超出规格范围:检查轧机压力是否稳定,调整辊轴位置,
确认调整的准确性。
4. 设备行走轴承温度过高:检查润滑情况,更换润滑剂,检查轴承状态。
结论:
高速无扭精轧机组设备故障诊断分析是保障设备正常运转、提高生产效率的关键环节。
通过对故障现象的分析、故障原因的诊断和采取相应的故障排除与措施,能够减少设备故
障发生,提高设备的可靠性和稳定性。
对于提高设备操作员的技术水平和维护意识也具有
重要意义。
高线厂精轧机组常见事故原因及解决方案
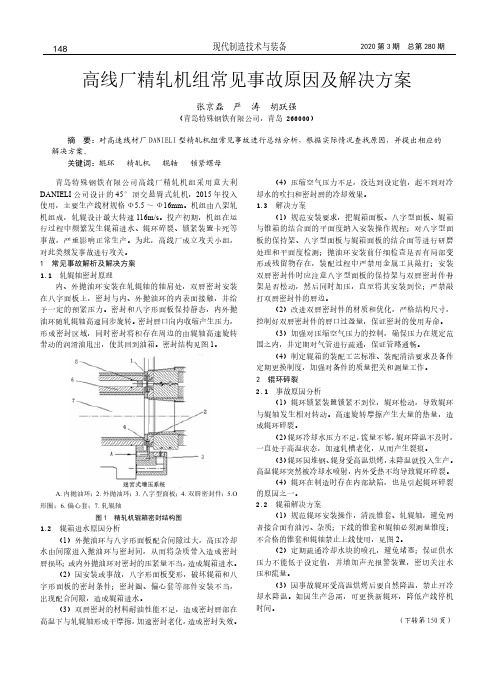
青岛特殊钢铁有限公司高线厂精轧机组采用意大利DANIELI公司设计的45°顶交悬臂式轧机,2015年投入使用,主要生产线材规格Ф5.5~Ф16mm。
机组由八架轧机组成,轧辊设计最大转速116m/s。
投产初期,机组在运行过程中频繁发生辊箱进水、辊环碎裂、锁紧装置卡死等事故,严重影响正常生产。
为此,高线厂成立攻关小组,对此类频发事故进行攻关。
1 常见事故解析及解决方案1.1 轧辊轴密封原理内、外抛油环安装在轧辊轴的轴肩处,双唇密封安装在八字面板上,密封与内、外抛油环的内表面接触,并给予一定的预紧压力。
密封和八字形面板保持静态,内外抛油环随轧辊轴高速同步旋转。
密封唇口向内收缩产生压力,形成密封区域,同时密封将积存在周边的由辊轴高速旋转带动的润滑油甩出,使其回到油箱。
密封结构见图1。
A.内抛油环;2.外抛油环;3.八字型面板;4.双唇密封件;5.O 形圈;6.偏心套;7.轧辊轴图1 精轧机辊箱密封结构图1.2 辊箱进水原因分析(1)外抛油环与八字形面板配合间隙过大,高压冷却水由间隙进入抛油环与密封间,从而将杂质带入造成密封唇损坏;或内外抛油环对密封的压紧量不当,造成辊箱进水。
(2)因安装或事故,八字形面板变形,破坏辊箱和八字形面板的密封条件;密封圈、偏心套等部件安装不当,出现配合间隙,造成辊箱进水。
(3)双唇密封的材料耐油性能不足,造成密封唇部在高温下与轧辊轴形成干摩擦,加速密封老化,造成密封失效。
(4)压缩空气压力不足,没达到设定值,起不到对冷却水的吹扫和密封唇的冷却效果。
1.3 解决方案(1)规范安装要求,把辊箱面板、八字型面板、辊箱与锥箱的结合面的平面度纳入安装操作规程;对八字型面板的保持架、八字型面板与辊箱面板的结合面等进行研磨处理和平面度检测;抛油环安装前仔细检查是否有局部变形或残留物存在,装配过程中严禁用金属工具敲打;安装双唇密封件时应注意八字型面板的保持架与双唇密封件骨架是否松动,然后同时加压,直至将其安装到位;严禁敲打双唇密封件的唇边。
高速无扭精轧机组设备故障诊断分析

上海市黄浦区第十中学2024届九年级物理第一学期期中学业质量监测试题注意事项1.考试结束后,请将本试卷和答题卡一并交回.2.答题前,请务必将自己的姓名、准考证号用0.5毫米黑色墨水的签字笔填写在试卷及答题卡的规定位置.3.请认真核对监考员在答题卡上所粘贴的条形码上的姓名、准考证号与本人是否相符.4.作答选择题,必须用2B铅笔将答题卡上对应选项的方框涂满、涂黑;如需改动,请用橡皮擦干净后,再选涂其他答案.作答非选择题,必须用05毫米黑色墨水的签字笔在答题卡上的指定位置作答,在其他位置作答一律无效.5.如需作图,须用2B铅笔绘、写清楚,线条、符号等须加黑、加粗.一、选择题1.粗细相同的两根镍铬合金电阻线,长度关系是L1>L2,串联接入电路后,流过它们的电流分别为I1、I2;.两端电压分别为U1、U2。
则下列关系正确的是A.I1=I2,U1>U2B.I1=I2,U1<U2C.I1>I2,U1<U2, D.I1<I2,U1>U22.汽车匀速直线上坡的过程中,各物理量随时间变化关系正确的是()A.B.C.D.3.如何外部检测植物含水量的变化呢?科学家用条状石墨烯制成的湿敏电阻R,附着在叶片上,植物含水量变低,R x变小,电表示数变小;植物含水量变高,R x变大,电表示数变大.电源电压恒定,R0为定值电阻,下列电路图中符合要求的是A.B. C.D.4.如图所示,一同学做测量小灯泡的电阻实验时,把电压表与电流表的位置接错了.闭合开关后,电路可能发生的现象是A.电流表和电压表都烧坏B.电流表烧坏,电压表正常C.电压表烧坏,电流表正常D.先烧坏电流表,再烧坏电压表5.如图是汽油机工作的四个冲程,其中表示机械能转化为内能的冲程是A.B.C.D.6.甲、乙、丙三个轻质泡沫小球用绝缘细线悬挂在天花板上,它们之间相互作用时的场景如图所示,已知丙球与用毛皮摩擦过的橡胶棒所带的电荷相同,下列判断正确的是A.甲、乙两球均带正电B.甲、乙两球均带负电C.甲球带正电、乙球一定带负电D.甲球带负电、乙球可能不带电7.下列关于能量转化、转移现象的说法,错误的是A.电池充电,电能转化为化学能B.电动机工作,电能转化为机械能C.用热水袋取暖,能量发生了转移D.暖瓶塞被热气弹开,机械能转化为内能8.把两个灯泡连接到电源两极上,用电压表测得两个灯泡两端的电压相等,则这两个灯泡的连接方式()A.一定并联B.一定串联C.串联、并联都有可能D.无法判断9.在国际单位制中,电压的单位是A.安培B.伏特C.焦耳D.瓦特10.如图所示是重庆一中物理兴趣小组的同学们设计的一种风力测量仪,电源电压恒定不变,是均匀电阻丝,金属丝(电阻忽赌不计)的上端固定在O点,下端系有一块型料片A,当风从左向右吹动塑料片时,金属丝向右摆动并与电阻线保持良好的接触.图中仪表的示数随风力增大而增大的有()A.①②B.③④C.②③D.②④11.用两个相同的加热器,分别对质量相等的甲、乙两种液体加热,其温度随时间变化的图像如图所示,由图像可以看出A.甲的比热容比乙的大B.甲的比热容比乙的小C.甲和乙的比热容相同D.加热时甲、乙初温相同12.甲、乙两个办公室为了互相传呼方便,在两个办公室各装了一个电铃,要使两个办公室的任何一方按开关都能使对方的电铃发声,正确的电路图是(图中的虚线表示房间的墙壁)()A.B.C.D.二、填空题13.小雨通过比较电路中不同位罝的电流表的示数来研究串联电路的电流规律,他所用的电路图如图甲所示,闭合开关后,两电流表指针偏转情况如图乙所示.(1)小雨发现电流表A2的指针偏转角度比A1的小,所以他认为“串联电路电流每流经一个用电器都会减弱一些”. 请你指出造成他错误判断的原因:__________________,(2)电流表A1的示数是______________A.14.如图所示,将一个底部封闭的薄壁金属管固定在支架上,管中装一些酒精,然后用塞子塞紧管口.把一根橡皮条缠在管子上并迅速来回拉动,很快会观察到塞子被酒精蒸汽顶出.在此实验中,是通过_____的方式使金属管壁的温度升高;塞子被酒精蒸汽顶出的过程中,______能转化为机械能.15.如图是灯泡L和电阻R中电流随电压变化的图象.由图象可知若将两元件串联接入电路中使通过L的电流为0.15A,则电源应是_____V ; 若将它们并联接在电压为2V的电源两端,电路中的总电流为_____A.16.如图甲所示,用弹簧测力计竖直向上缓慢提升静止在水平桌面上的钩码.弹簧测力计的示数F与弹簧测力计的零刻度线A点上升高度h A之间的关系如图乙所示.则钩码的重力大小为_______ N;当弹簧测力计的示数是1.5N时,钩码受到的合力大小是_______ N.从开始提升到h A=30cm的过程中,弹簧测力计的拉力对钩码做功为______________ .三、实验题17.(8分)小明为研究醋的导电性能,将两根裸铜线a、b插入醋中,并将裸铜线a、b连入电路,如图所示。
轧机故障案例分析
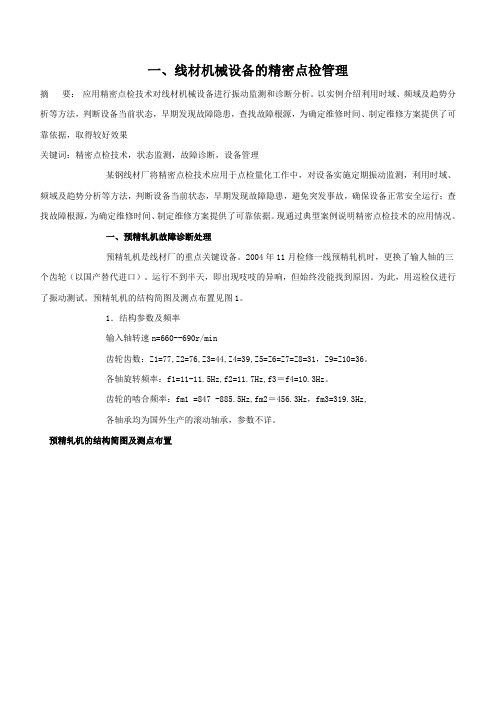
一、线材机械设备的精密点检管理摘要:应用精密点检技术对线材机械设备进行振动监测和诊断分析。
以实例介绍利用时域、频域及趋势分析等方法,判断设备当前状态,早期发现故障隐患,查找故障根源,为确定维修时间、制定维修方案提供了可靠依据,取得较好效果关键词:精密点检技术,状态监测,故障诊断,设备管理某钢线材厂将精密点检技术应用于点检量化工作中,对设备实施定期振动监测,利用时域、频域及趋势分析等方法,判断设备当前状态,早期发现故障隐患,避免突发事故,确保设备正常安全运行;查找故障根源,为确定维修时间、制定维修方案提供了可靠依据。
现通过典型案例说明精密点检技术的应用情况。
一、预精轧机故障诊断处理预精轧机是线材厂的重点关键设备。
2004年11月检修一线预精轧机时,更换了输人轴的三个齿轮(以国产替代进口)。
运行不到半天,即出现吱吱的异响,但始终没能找到原因。
为此,用巡检仪进行了振动测试。
预精轧机的结构简图及测点布置见图1。
1.结构参数及频率输入轴转速n=660--690r/min齿轮齿数:Z1=77,Z2=76,Z3=44,Z4=39,Z5=Z6=Z7=Z8=31,Z9=Z10=36。
各轴旋转频率:f1=11-11.5Hz,f2=11.7Hz,f3=f4=10.3Hz。
齿轮的啮合频率:fm1 =847 -885.5Hz,fm2=456.3Hz,fm3=319.3Hz,各轴承均为国外生产的滚动轴承,参数不详。
预精轧机的结构简图及测点布置图1 预精轧机的结构简图及测点布置2.诊断分析(1)测试结果(见表1)表中Hv, Vv, Av分别是水平、垂直和轴向的速度值,单位为mm/s; Ha, Va, Aa分别是水平、垂直和轴向的加速度值,单位为m/s2 。
(2)诊断分析从表1可看出,15架振动烈度比14架小,水平和轴向加速度幅值比14架大,但加速度最大值在14架。
由于此设备结构较特殊,故不适合采用绝对标准,而又无相对标准可参照。
高速无扭精轧机组设备故障诊断分析

高速无扭精轧机组设备故障诊断分析发布时间:2021-06-17T11:13:37.373Z 来源:《科学与技术》2021年第29卷2月6期作者:端木凡雷[导读] 在长时间的运行过程中,因受到操作不当、设备老化等各种原因的影响,导致设备往往容易出现各种故障问题端木凡雷身份证号码:37292819840105****摘要:在长时间的运行过程中,因受到操作不当、设备老化等各种原因的影响,导致设备往往容易出现各种故障问题。
因此需要对设备故障进行科学诊断,才能有效制定适宜的维修方案,保障设备的安全运行。
在这一背景下,本文将以高速无扭精轧机组设备作为主要研究对象,对其故障诊断进行简要分析研究。
关键词:高速无扭精轧机;齿轮;故障诊断1 高速无扭精轧机组的简要概述为有效说明高速无扭精轧机组设备的故障诊断,本文将以某公司设计研发的高速无扭精轧机组为例。
该机组设备中机架呈“V”字型相互垂直布置,整体刚性底座中装有十架轧机,采用直流变频调速电机负责为其集中传动。
两根齿轮轴输出功率在位于增速箱输入轴中的大齿轮的直接带动下,负责主传动[1]。
而在齿型联轴节的作用下,输出轴有效联接两根传动轴,对兩侧轧机提供驱动作用。
由于高速无扭精轧机组设备结构具有较高的复杂性,并且具有转速高、运动部件众多且彼此相互关联等诸多特性,因此一直以来也是运维人员的关注重点。
但由于在长时间的运行下,高速无扭精轧机组设备中的部分零部件出现松动、脱落或是老化、磨损等问题,而容易导致机组设备出现各种故障问题,因此需要工作人员及时对高速无扭精轧机组设备进行故障诊断,以便可以第一时间有效排除故障问题,恢复高速无扭精轧机组设备的正常、安全运行。
2 高速无扭精轧机组设备的故障诊断(1)立伞齿轮故障在高速无扭精轧机组设备的运行过程中,立伞齿轮故障是其较为常见的一种故障。
其故障表现通常为进行高速无扭精轧机组设备点检时,轧机整体出现较大振动。
此时工作人员通过对振动值进行实时监测,对获得的检测频谱图进行分析,可知在出现振动幅值最高峰值的位置处,一般会与立伞轴轴频相对应。
精轧机减速器的故障分析及诊断

精轧机减速器的故障分析及诊断摘要:精轧机是热轧生产线上的重要组成部分,然而由于设计缺陷和制造质量问题的存在,减速机齿轮点蚀、断齿、断轴故障频繁发生,这给热轧厂的生产经营造成了巨大的损失。
本文从精轧机减速器的结构特点入手,对减速机常见故障原因进行了分析,并针对存在的问题,从技术和管理两方面提出了解决措施。
关键词:精轧机;减速器;故障;分析;诊断1.引语精轧机是热轧生产线上的重要组成部分,然而由于设计缺陷和制造质量问题的存在,减速机齿轮点蚀、断齿、断轴故障频繁发生,这给热轧厂的生产经营造成了巨大的损失。
精轧减速机可靠性低的问题,已成为制约一些连轧厂设备正常运行的最主要因素之一。
2.减速机结构2.1.机体结构主减速机机体全部为焊接结构。
机体工作剖分面只有一个,然而机体分三层。
主要受力部分为机体和中机体,用厚钢板焊接而成。
断面尺寸主要取决于主减速机的承载能力。
机盖布置在中机体之上,不承受工作载荷,用薄钢板焊接而成。
机盖四周有向下伸出的凸板,插入中机体内靠上部的环形油槽,利用槽里的积存润滑油来“水封”以防止机体外杂物进入机体里。
机盖和中机体之间采用两个方向的缺槽来定位。
机盖和中机体之间仅用直径不大的几个螺栓轻微固定即可。
这种结构对减速机的检查、维修十分方便,尤其对内部油管的检修、齿面接触状况的监督尤为方便。
2.2.齿轮的结构齿轮的结构形式很多,如齿轮轴、锻造齿轮、焊接齿轮等。
齿轮的承载能力随着工业技术的发展而提高,多采用合金钢锻造齿轮或焊接齿轮。
主减速机的齿轮、齿轮轴和焊接齿轮的齿圈材料全部选用优质合金钢17Cr2Ni2Mo,经过渗碳淬火磨齿加工。
磨削后的齿面硬度HRC57-62。
主减速机的齿轮都经过修形,即齿端修形和沿齿高修形。
2.3.轴承的选择主减速机全部选用滚动轴承,当轴承既承受轴向力又承受径向力时,如轴承01 和02 一般选用双列圆锥滚子轴承(带油孔油槽)。
当轴承只承受径向力时,如轴承03 和04 一般选用双列圆柱滚子轴承(带油孔油槽)。
热轧精轧机标定异常的原因分析
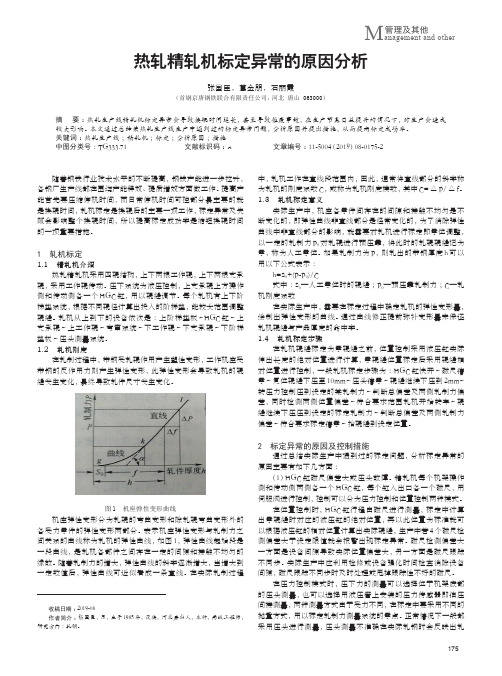
175管理及其他M anagement and other热轧精轧机标定异常的原因分析张国臣,葛金朋,石丽霞(首钢京唐钢铁联合有限责任公司,河北 唐山 063000)摘 要:热轧生产线精轧机标定异常会导致换辊时间延长,甚至导致推废事故,在生产节奏日益提升的情况下,对生产会造成较大影响。
本文通过总结某热轧生产线生产中遇到过的标定异常问题,分析原因并提出措施,从而提高标定成功率。
关键词:热轧生产线;精轧机;标定;分析原因;措施中图分类号:TG333.71 文献标识码:A 文章编号:11-5004(2019)08-0175-2收稿日期:2019-08作者简介:张国臣,男,生于1985年,汉族,河北唐山人,本科,高级工程师,研究方向:轧钢。
随着钢铁行业技术水平的不断提高,钢铁产能进一步拉升,各钢厂生产线都在围绕产能释放、提质增效方面做工作。
提高产能首先要压缩停机时间,而日常停机时间可控部分最主要的就是换辊时间,轧机标定是换辊后的主要一项工作,标定异常及失败会影响整个换辊时间,所以提高标定成功率是缩短换辊时间的一项重要措施。
1 轧机标定1.1 精轧机介绍热轧精轧机采用四辊结构,上下两根工作辊,上下两根支承辊,采用工作辊传动。
压下系统为液压控制,上支承辊上方操作侧和传动侧各一个HGC 缸,用以辊缝调节。
每个轧机有上下阶梯垫系统,根据不同辊径计算出投入的阶梯垫,能较大范围调整辊缝。
轧机从上到下的设备依次是:上阶梯垫板~HGC 缸~上支承辊~上工作辊~弯窜系统~下工作辊~下支承辊~下阶梯垫板~压头测量系统。
1.2 轧机刚度在轧制过程中,带钢受轧辊作用产生塑性变形,工作机座受带钢的反作用力则产生弹性变形,此弹性变形会导致轧机的辊缝发生变化,最终导致轧件尺寸发生变化。
图1 机座弹性变形曲线机座弹性变形分为轧辊的弯曲变形和除轧辊弯曲变形外的各受力零件的弹性变形两部分。
表示机座弹性变形与轧制力之间关系的曲线称为轧机的弹性曲线,如图1,弹性曲线起始段是一段曲线,是轧机各部件之间存在一定的间隙和接触不均匀的缘故。
高速公路计重设备的日常维护与常见故障处理
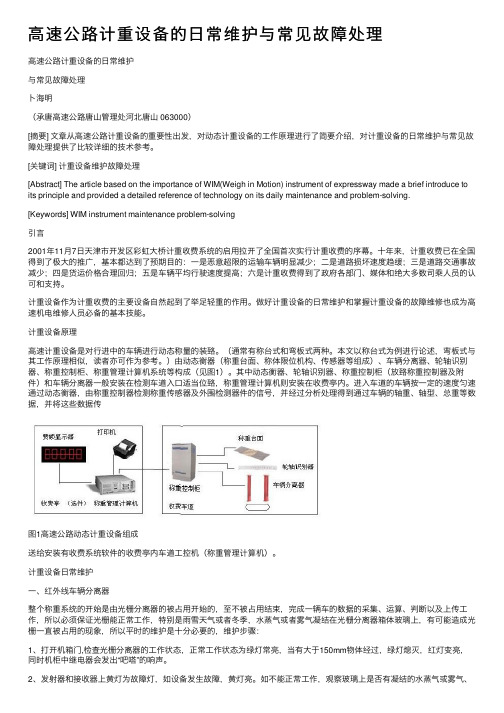
⾼速公路计重设备的⽇常维护与常见故障处理⾼速公路计重设备的⽇常维护与常见故障处理⼘海明(承唐⾼速公路唐⼭管理处河北唐⼭ 063000)[摘要] ⽂章从⾼速公路计重设备的重要性出发,对动态计重设备的⼯作原理进⾏了简要介绍,对计重设备的⽇常维护与常见故障处理提供了⽐较详细的技术参考。
[关键词] 计重设备维护故障处理[Abstract] The article based on the importance of WIM(Weigh in Motion) instrument of expressway made a brief introduce to its principle and provided a detailed reference of technology on its daily maintenance and problem-solving. [Keywords] WIM instrument maintenance problem-solving引⾔2001年11⽉7⽇天津市开发区彩虹⼤桥计重收费系统的启⽤拉开了全国⾸次实⾏计重收费的序幕。
⼗年来,计重收费已在全国得到了极⼤的推⼴,基本都达到了预期⽬的:⼀是恶意超限的运输车辆明显减少;⼆是道路损坏速度趋缓;三是道路交通事故减少;四是货运价格合理回归;五是车辆平均⾏驶速度提⾼;六是计重收费得到了政府各部门、媒体和绝⼤多数司乘⼈员的认可和⽀持。
计重设备作为计重收费的主要设备⾃然起到了举⾜轻重的作⽤。
做好计重设备的⽇常维护和掌握计重设备的故障维修也成为⾼速机电维修⼈员必备的基本技能。
计重设备原理⾼速计重设备是对⾏进中的车辆进⾏动态称量的装臵。
(通常有称台式和弯板式两种。
本⽂以称台式为例进⾏论述,弯板式与其⼯作原理相似,读者亦可作为参考。
)由动态衡器(称重台⾯、称体限位机构、传感器等组成)、车辆分离器、轮轴识别器、称重控制柜、称重管理计算机系统等构成(见图1)。
精轧机说明书

高速线材精轧机组安装使用说明书制造单位:哈尔滨广旺机电设备制造有限公司设备图号: ZJF90d00使用客户:出厂日期:目录第一章、技术说明 (2)第二章、设备安装调整 (4)第三章、设备的使用维护与更换 (7)第四章、常见故障及排除 (13)第五章、附件 (14)精轧机组是高速线材车间的重要设备,为了保证精轧机组正常运转,用户须了解机组的性能、安装、运行与日常维护等基本常识。
本说明书就以上几个方面作了简单的介绍,用户在安装、使用机组前请先阅读本手册。
本说明书供武安文煜高线专用。
第一章技术说明一、设备用途本精轧机组为摩根五代顶交45°无扭重载高速线材精轧机组,图纸由国内设计转化完成。
本机组通过10机架连续微张力轧制,将上游轧机输送的轧件,轧制成φ5.5-φ20mm的成品线材。
二、设备主要性能参数1. 工艺参数:●来料规格:φ17—φ22mm●来料温度:>900℃●成品规格: φ5.5-φ20mm●主要钢种:碳钢、优质碳素钢、低合金钢、合金钢、焊条钢、冷镦钢等●第10架出口速度:≤95m/s(轧制φ6.5规格时)2. 设备参数:●机组组成:∅230轧机(5架)、∅170轧机(5架)、增速箱、大底座、挡水板与防水槽、缓冲箱、保护罩、联轴器、精轧机组配管等。
●机架数量: 10架(1-5架为∅230轧机,6-10架为∅170轧机同种规格的轧辊箱可以互换)●布置方式:顶交45°,10机架集中传动●辊环尺寸:∅230轧机:∅228.3/∅205×72mm∅170轧机:∅170.66/∅153×57.35/70mm ●传动电机: AC同步变频电机,功率: 5500kW●振动值:≤4.5 mm/s●噪音:≤80dB(距轧机1.5米处)●机组总速比(电机速度/装辊转速)见下表:●机组润滑方式:稀油集中润滑油压: 0.35MPa(点压力)总耗量:1200L/min油品: Mobil 525清洁度:10μ供油温度:38°C -42°C●保护罩液压系统:工作压力:15MPa系统流量:20 l/min●装辊工作压力:高压45 MPa -49.5MPa,低压22 MPa -25 MPa●卸辊工作压力:最大70MPa第二章设备安装调整一、安装调整顺序●将机组底座、增速箱、和主电机初步就位。
高速线材打捆机机电系统故障分析及改进措施

高速线材打捆机机电系统故障分析及改进措施摘要:对打捆机机电系统的组成、打捆机主体的工作原理、故障现象及产生原因进行了阐述。
提出了相应的具体改进措施。
经过实践,取得了很好的成效。
关键词;打捆机机电故障应对措施0前言安钢高速线材打捆机是集电气、机械、液压、气动为一体的自动化程度较高的设备。
打捆机从2000年投产使用到现在已十年,由于设备老化和使用维护方面存在问题,设备机电系统故障日益凸显,已严重影响到成品打包质量和生产的顺利进行。
因此,排除打捆机的机电系统故障显得十分迫切和重要。
我们从系统组成入手,对故障现象做了认真分析和总结,提出了有针对性的改进措施。
经过实践,取得了很好的效果。
打捆机故障率明显降低,用户满意度得到提升。
1打捆机的系统组成安钢第一炼轧厂所用打捆机由瑞典进口,型号为PCH_4KNA。
它设计独特新颖,结构复杂、紧凑,控制精确。
如下图:它是卧式打捆机,主要由压实车、升降托台、收线挡板、滚轮、导轨、钩式运输机、储线架、打捆单元、喂线单元、打捆导槽系统、气动设备、电气元件和液压元件等组成。
两个压实车(1#、2#、)在滚轮上移动。
每个压实车有两个液压缸驱动。
打捆机的线导系统位于2#压实小车上,线导相对于压实车的水平运动通过液压马达来完成。
四个打捆单元位于1#压实小车上,与水平面成45度角。
打捆单元用于扭结、切断和夹紧打捆线。
四个喂线单元也安装在压实小车上主要用于喂线和收线。
喂线长度可以度量,收线的停止也由此单元进行控制。
打捆机能够根据程序指令自动压实并捆住线卷。
通过操作面板可以进行手动打捆、自动打捆和远程控制全自动打捆等操作。
2打捆机的程序控制动作打捆机的PLC系统是由一套S7412-2DP和九套ET200S及一套E900组成。
PLC主站采用西门子公司S7-400系列的CPU412-2DP,通过DP网与其它从站进行数据通讯,并进行数据处理。
它的程序控制动作包括:1、弯曲导槽的打开(S1)与闭合(S2)2、喂线3、夹紧与夹紧打开4、打捆单元进入与打捆单元复位(S20)5、摆动缸进入(S22)与摆动缸复位(S21)6、快速收线与低速收线7、收线挡板打开与闭合8、扭结9、剪切10、扭结轮复位(S23)11、一#压盘的前进与后退12、二#压盘的前进(S13)慢速前进(S15)与后退(S14)慢速后退(S16)13、托台的上升与下降14、一步压实15、二步压实16、线导闭合与线导复位3打包机主体工作原理及控制信号的组成3.1升降台在两个液压缸的推动下,可沿垂直方向上下移动。
- 1、下载文档前请自行甄别文档内容的完整性,平台不提供额外的编辑、内容补充、找答案等附加服务。
- 2、"仅部分预览"的文档,不可在线预览部分如存在完整性等问题,可反馈申请退款(可完整预览的文档不适用该条件!)。
- 3、如文档侵犯您的权益,请联系客服反馈,我们会尽快为您处理(人工客服工作时间:9:00-18:30)。
高速重轨线万能精轧机设备的故障分析和诊断
武钢股份设备维修总厂张建伟武汉430081
摘要:通过对万能精轧机设备冲击及异响的故障进行振动测试与分析,找出造成异常的部位及原因,据此与维护人员一起制定合理的处理方案,解决了设备的异响问题。
关键词:万能精轧机异常振动冲击扁头装配间隙衬套磨损
1、设备概况:
武钢高速重轨线串联可逆式万能轧机设备系德国西马克SMS公司制造。
2007年投入生产,设计年产量105万吨。
采用5机架万能轧制法生产钢轨。
万能轧机和轧边机采用CCS 紧凑式结构全液压压下、液压位置控制HPC、自动辊缝控制AGC 和下水平辊动态轴向调整,轧辊和导卫成组快速更换,轧机刚度好,调整精度高。
图1 可逆式万能轧机结构示意图
1、机前延伸辊道
2、机前提升台架
3、机前对中装置
4、UR轧机
5、E轧边机
6、UF轧机
7、机后对中装置8、机后提升台架器9、机后延伸辊道10、轧机主万向连轴×3
11、人字齿轮箱×3 12、连杆×3 13、轧机主电机×3 14、换辊横移台架 15、自动换辊装置
2、机组状况及测试方案:
机组在2009年2月4号经点检发现UF精轧机在空载时齿轮分配箱与轧辊部位存在间断性异响。
要求对设备进行振动诊断测试,找出异常的原因和部位。
UF轧机电机功率4000KW 转速:0-65/190rpm ,最大轧制速度10m/s。
整个测试系统由振动传感器、数据采集器、动态分析仪、预知维修软件和计算机组成。
分别采取绝对振动测试和相对振动测试方法。
如图2、图3所示。
图2 绝对振动测试
图3 相对振动测试
设备的绝对振动测试仪器为ROZI-802数据采集器,分析软件为上海容知公司MRS 2.0。
相对振动测试仪器为日本ONO SOKKI公司VT-510电涡流式位移测试仪和CF-360动态分析仪。
应用预知维修软件提供对测点数据库的管理,巡检路径的设置,由数据采集器将实测数据回放至计算机,对实测数据进行处理、分析、比较,对设备的运行状态做趋势分析和预报并对故障设备进行诊断分析。
传动示意图及传感器测点布置示意图如图3所示,表中H、V、A分别表示水平、垂直、轴向方向。
图 4 精轧机传动示意图及传感器布置图
3、测试数据分析:
3.1测试数据
采用ROZI-701(光电转速计)实时检测输出轴转速。
通过对轧机齿轮分配箱空载时各测点的振动加速度进行测试,当输出轴转速在49-50rpm时,振动最大点在下输出轴轴向位置,幅值为0.23 m/s2,峭度指标达到6.82。
振动幅值见表1。
表1 UF 轧机齿轮分配箱各测点数据
单位2
与历史数据进行比较发现,加速度幅值及变化不大。
但波形异常,存在强烈的冲击信号,峭度指标有大幅上升。
(见图5、图6)
图5 测点2A 2月4号时域波形及指标
图6 测点2A 历史时域波形及指标
同时发现,在输出轴低转速时冲击现象明显,改变输出轴转速冲击周期同步发生变化,当输出轴转速升高(大于120rpm )或低速轧制过程中,冲击信号及异常响声趋于减弱和消失。
3.2 数据分析
UF 轧机下轴测点时域中出现冲击信号的周期为592.2ms (1.69Hz ),与当时输出轴转速49rpm ,0.8166Hz 精确同步,即转动一周冲击出现二次。
为转速的同步信号,可排除齿轮分配箱的齿轮和轴承存在异常。
传动轴在旋转过程中产生周期性的撞击,可能由于主万向节轴间隙过大造成。
对现场设备结构进行分析:上、下主传动节轴采用的是十字轴式万向联轴器,主轴全长约4850mm ,采用扁头套传递扭矩至轧辊。
当传动轴上的部件存在过大径向间隙时,在转动900或1800时传动轴因重力跌落下坠,形成冲击,冲击间隔与转速精确同步,造成异响与振动,经衰减传递到齿轮箱。
当高速运转时,连接轴偏心形成的离心力将克服连接轴所产生的重力,使得故障特征在较低速时明显好转。
在轧制过程中扭矩形成的摩擦力将克服连接轴所产生的重力,使得故障特征较空载时好转。
与现场的测试和观察的情况相吻合。
使用CF -360动态分析仪、VT -510非接触位移传感器测量上下连杆万向节端面的相对
指标名称 指标值 指标名称 指标值 有效值 0.23 峭度指标 6.82 脉冲指标 6.39 波形指标 1.44 裕度指标
8.17
歪度指标
-0.11
指标名称 指标值 指标名称 指标值 有效值 0.09 峭度指标 3.42 脉冲指标 5.44 波形指标 1.28 裕度指标
6.50
歪度指标
0.06
位移变化。
判断得出产生滑动的是下连接轴。
(见图7、图8)
图7 上传动轴位移较平稳 图8 下传动轴位移突变
结合设备情况,下传动轴部件存在过大的间隙而产生滑动,转动一圈撞击二次的部位有: 1)、连接轴螺栓松动。
2)、扁头套定位衬套有磨损或松动。
工作辊扁头尺寸出现偏差。
3)、连杆万向节十字包,其中一组轴承或衬套磨损。
3.3 检查处理及对策:
经查:1)、各连接轴螺栓无松动。
2)、工作辊扁头尺寸差异在标准范围内。
3)、扁头套定位衬套内孔已为椭圆形,设计要求Φ220.5H7,查得孔的公差是0.046mm 。
实测最大直径达227.41mm 。
远超出设计要求,衬套出现了过度磨损,有干摩擦痕迹。
对衬套磨损原因进行分析认为:该部位润滑情况不良。
主要是冷却水的冲刷、轧件高温烘烤,油脂耐热性差,造成流失造成。
建议每班换辊时检查润滑情况并及时加注润滑脂,定期检查衬套磨损情况。
换辊时,保证对位良好,避免造成衬套损伤。
图9 衬套的磨损图 图10 衬套的结构图
4、结束语
对磨损的扁头衬套进行更换处理及采取预防措施后运行至今状况良好。
对精轧机的监测实例说明,利用预知维修系统对故障设备进行测试、分析和诊断,找出引起故障的原因和部
位,并提出解决方法,制定有针对性的预防措施和维护标准,可缩短检修时间降低维修成本
衬套磨损
衬套
和费用,可以保证设备长期、稳定、安全、优质运行。