塑料模具设计参考
塑料模具设计参考文献
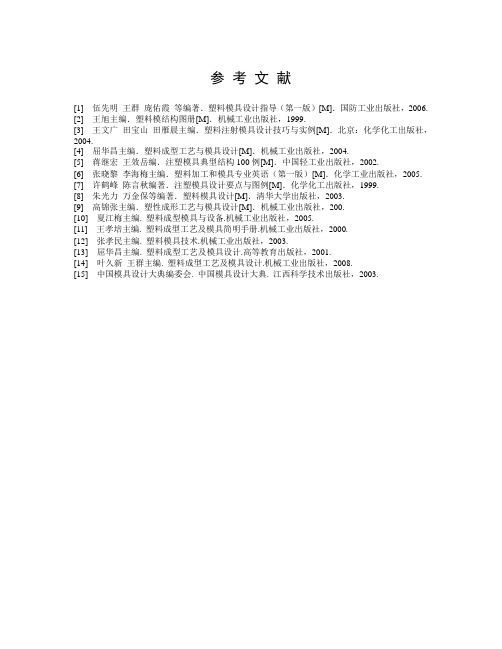
参考文献
[1] 伍先明王群庞佑霞等编著.塑料模具设计指导(第一版)[M].国防工业出版社,2006.
[2] 王旭主编.塑料模结构图册[M].机械工业出版社,1999.
[3] 王文广田宝山田雁晨主编.塑料注射模具设计技巧与实例[M].北京:化学化工出版社,2004.
[4]屈华昌主编.塑料成型工艺与模具设计[M].机械工业出版社,2004.
[5] 蒋继宏王效岳编.注塑模具典型结构100例[M].中国轻工业出版社,2002.
[6] 张晓黎李海梅主编.塑料加工和模具专业英语(第一版)[M].化学工业出版社,2005.
[7] 许鹤峰陈言秋编著.注塑模具设计要点与图例[M].化学化工出版社,1999.
[8] 朱光力万金保等编著.塑料模具设计[M].清华大学出版社,2003.
[9] 高锦张主编.塑性成形工艺与模具设计[M].机械工业出版社,200.
[10] 夏江梅主编. 塑料成型模具与设备.机械工业出版社,2005.
[11] 王孝培主编. 塑料成型工艺及模具简明手册.机械工业出版社,2000.
[12] 张孝民主编. 塑料模具技术.机械工业出版社,2003.
[13] 屈华昌主编. 塑料成型工艺及模具设计.高等教育出版社,2001.
[14] 叶久新王群主编. 塑料成型工艺及模具设计.机械工业出版社,2008.
[15] 中国模具设计大典编委会. 中国模具设计大典. 江西科学技术出版社,2003.。
塑料模具毕业设计题目

塑料模具毕业设计题目1.塑料套管2.小模数双联圆柱直齿轮材料为聚甲醛,大批量生产。
3.卡尺盒(+qq1162401387,获取图纸)4.透明塑料试管5.折页盒6.螺纹盖7.斜三通8.顺水三通9.灭火器壳10.锥齿轮11.螺母12.刷座14.塑料桶盖16.线轮17.导向轮18.台历架19.电视机按钮20.泡沫灭火器喷嘴21.快换接头22.塑料罩23.菜篮24.分油套25.油管接头26.上罩27.矩形罩128.端盖29.圆形盖30.盒子31.矩形罩2 32.矩形罩333.罩盖34.圆端盖35.饮料瓶盖36.座块盖37.连接座38.盒盖39.弯头40.三通管41.外壳42.旋钮43.外壳45.旋钮47.骨架48.罩49.放大镜产品名称:放大镜要求:表面无缺痕材料:透明pp生产批量:大批量50.壳盖名称材料尺寸参数值A B C D E F G H I J塑料壳盖PS 60 80 25 4 3 45 20 74 12 35 技术要求:1. 大批量生产,精度为MT5,壁厚均匀;2. 塑件不允许有裂纹和变形缺陷;3. 脱模斜度30'~1°;4. 未注圆角R=251.塑料扣盖名称材料尺寸参数值A B C DE(Φ)F(Φ)G(Φ)H(Φ)δ(Φ)塑料扣盖PP 75 30 20 5 16 65 10 50 4 技术要求:1. 大批量生产,精度为MT5,壁厚均匀;2. 塑件不允许有裂纹和变形缺陷;3. 脱模斜度30'~1°;4. 未注圆角R=152.塑料仪表盖名称材料尺寸参数值A B C D E F G H塑料仪表盖ABS 70 30 25 35 65 10 5 50 技术要求:1. 大批量生产,精度为MT5,壁厚处处相等;2. 塑件不允许有裂纹和变形缺陷;3. 脱模斜度30'~1°;4. 未注圆角R2~R35. 未注尺寸公差按所有塑料的高精度级查取。
53.多孔塑料罩名称材料尺寸参数值A B C D E F G H I多孔塑料罩PP 60 50 30 4 3 44 8 5 26 技术要求:1. 大批量生产,精度为MT5;2. 塑件不允许有裂纹和变形缺陷;3. 脱模斜度30'~1°;4. 未注圆角R2~R354. 穿线塑料盒盖名称:穿线塑料盒盖技术要求:1. 大批量生产,精度为MT5;2. 塑件不允许有裂纹和变形缺陷;3. 脱模斜度30'~1°;55.对称塑料套管名称:对称塑料套管技术要求:1. 大批量生产,精度为MT5;材料ABS;2. 塑件不允许有裂纹和变形缺陷3. 脱模斜度30'~1°;56. 塑料后盖板名称:塑料后盖板技术要求:1. 大批量生产,精度为MT5;材料ABS;2. 塑件不允许有裂纹和变形缺陷;3. 脱模斜度30'~1°;57.花边塑料盖名称:花边塑料盖技术要求:1. 大批量生产,精度为MT5;材料PP;2. 塑件不允许有裂纹和变形缺陷;3. 脱模斜度30'~1°;58.塑料罩桶名称:塑料罩桶技术要求:1. 大批量生产,精度为MT5;材料ABS;2. 塑件不允许有裂纹和变形缺陷;3. 脱模斜度30'~1°;60.圆形塑料扣盖名称:圆形塑料扣盖技术要求:1. 大批量生产,精度为MT5;材料:ABS;2. 塑件不允许有裂纹和变形缺陷;3. 脱模斜度30'~1°;61.圆形塑料罩壳名称:圆形塑料罩壳技术要求:1. 大批量生产,精度为MT5;材料ABS;2. 塑件不允许有裂纹和变形缺陷;3. 脱模斜度30'~1°;62.阶梯圆筒塑料盖名称:阶梯圆筒塑料盖技术要求:1. 大批量生产,精度为MT5;材料PP;2. 塑件不允许有裂纹和变形缺陷;3. 脱模斜度30'~1°;63. 阶梯圆筒塑料支架名称:阶梯圆筒塑料支架技术要求:1. 大批量生产,精度为MT5;材料ABS2. 塑件不允许有裂纹和变形缺陷;3. 脱模斜度30'~1°;64. 圆形塑料纱筒名称:圆形塑料纱筒技术要求:1. 大批量生产,精度为MT5;材料PP;2. 塑件不允许有裂纹和变形缺陷;3. 脱模斜度30'~1°;65. 圆形塑料桶盖名称:圆形塑料桶盖技术要求:1. 大批量生产,精度为MT5;材料PP;2. 塑件不允许有裂纹和变形缺陷;3. 脱模斜度30'~1°;66. 塑料盒上盖名称:塑料盒上盖技术要求:1. 大批量生产,精度为MT5;材料PE;2. 塑件不允许有裂纹和变形缺陷;3. 脱模斜度30'~1°;67. 塑料方盒上端盖名称:塑料方盒上端盖技术要求:1. 大批量生产,精度为MT5;材料尼龙1010黑色;2. 塑件不允许有裂纹和变形缺陷;3. 脱模斜度30'~1°;68. 圆形塑料包装盒名称:圆形塑料包装盒技术要求:1. 大批量生产,精度为MT5;材料:高密度聚乙烯;2. 塑件不允许有裂纹和变形缺陷;3. 脱模斜度30'~1°;69.弹簧上座名称:弹簧上座技术要求:1. 大批量生产,精度为MT5;材料:ABS;2. 塑件不允许有裂纹和变形缺陷;3. 脱模斜度30'~1°;70.圆形塑料扣盖名称:圆形塑料扣盖技术要求:1. 大批量生产,精度为MT5;材料:ABS;2. 塑件不允许有裂纹和变形缺陷;3. 脱模斜度30'~1°;71.圆形塑料封盖名称:圆形塑料封盖技术要求:1. 大批量生产,精度为MT5;材料:ABS;2. 塑件不允许有裂纹和变形缺陷;3. 脱模斜度30'~1°;72.塑料旋钮名称:塑料旋钮技术要求:1. 大批量生产,精度为MT5;材料:ABS;2. 旋钮表面数字凹进0.4,并涂红色蜡,字型选用3.5#字体;3. 脱模斜度30'~1°;塑件不允许有裂纹和变形缺陷。
塑料模具设计说明书(参考)
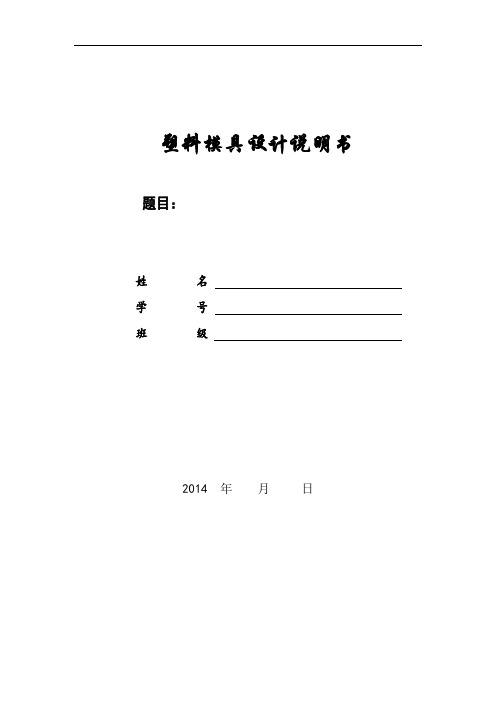
塑料模具设计说明书题目:姓名学号班级2014 年月日目录第一章塑件的工艺分析1.1 任务要求1.2 原料ABS的成型特性和工艺参数1.3 塑件的结构工艺性第二章注射设备的选择2.1 注射成型工艺条件2.2 选择注射机第三章型腔布局与分型面的选择3.1 塑件的布局3.2 分型面的选择第四章浇注系统的设计4.1主流道和定位圈的设计4.2 分流道设计4.3 浇口的设计4.4冷料穴的设计4.5 排气系统的分析第五章主要零部件的设计计算5.1 型芯、型腔结构的确定5.2 成型零件的成型尺寸第六章成型设备的校核6.1、注射成型机注射压力校核6.2、注射量的校核6.3、锁模力的校核相关零件图第一章塑件的工艺分析1.1 任务要求图1 盒盖1.2原料ABS的成型特性和工艺参数ABS是目前产量最大、应用最广的工程塑料。
ABS是不透明非结晶聚合物,无毒、无味,密度为 1.02~1.05 g/cm3。
ABS 具有突出的力学性能,坚固、坚韧、坚硬;具有一定的化学稳定性和良好的介电性能;具有较好尺寸稳定性,易于成型和机械加工,成型塑件表面有较好光泽,经过调色可配成任何颜色,表面可镀铬。
其缺点是耐热性不高,连续工作温度约为70℃,热变形温度约为93℃,但热变形温度比聚苯乙烯、聚氯乙烯、尼龙等都高;耐候性差,在紫外线作用下易变硬发脆。
可采用注射、挤出、压延、吹塑、真空成型、电镀、焊接及表面涂饰等多种成型加工方法。
ABS的成型特性:(1)ABS易吸水,成型加工前应进行干燥处理,表面光泽要求高的塑件应长时间预热干(2)流动性中等,溢边值0.04 mm左右。
(3)壁厚、熔料温度对收缩率影响极小,塑件尺寸精度高。
(4)ABS比热容低,塑化效率高,凝固也快,故成型周期短。
(5)ABS的表观黏度对剪切速率的依赖性很强,因此模具设计中大都采用点浇口形式。
(6)顶出力过大或机械加工时塑件表面会留下白色痕迹,脱模斜度宜取2°以上。
(7)易产生熔接痕,模具设计时应注意尽量减少浇注系统对料流的阻力。
塑料模具毕业设计题目
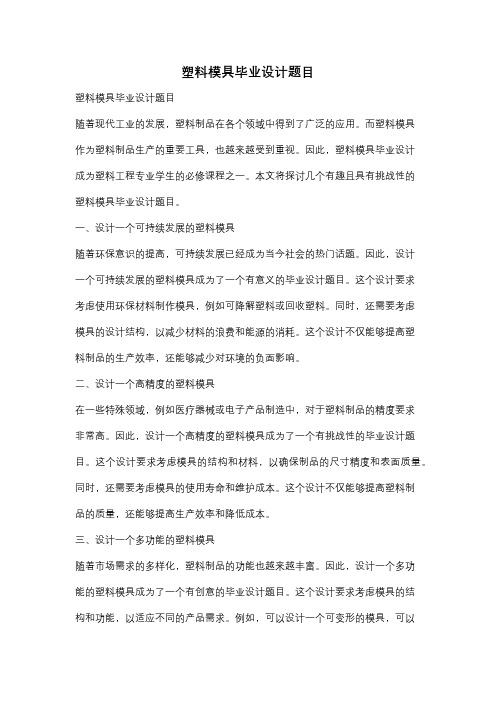
塑料模具毕业设计题目塑料模具毕业设计题目随着现代工业的发展,塑料制品在各个领域中得到了广泛的应用。
而塑料模具作为塑料制品生产的重要工具,也越来越受到重视。
因此,塑料模具毕业设计成为塑料工程专业学生的必修课程之一。
本文将探讨几个有趣且具有挑战性的塑料模具毕业设计题目。
一、设计一个可持续发展的塑料模具随着环保意识的提高,可持续发展已经成为当今社会的热门话题。
因此,设计一个可持续发展的塑料模具成为了一个有意义的毕业设计题目。
这个设计要求考虑使用环保材料制作模具,例如可降解塑料或回收塑料。
同时,还需要考虑模具的设计结构,以减少材料的浪费和能源的消耗。
这个设计不仅能够提高塑料制品的生产效率,还能够减少对环境的负面影响。
二、设计一个高精度的塑料模具在一些特殊领域,例如医疗器械或电子产品制造中,对于塑料制品的精度要求非常高。
因此,设计一个高精度的塑料模具成为了一个有挑战性的毕业设计题目。
这个设计要求考虑模具的结构和材料,以确保制品的尺寸精度和表面质量。
同时,还需要考虑模具的使用寿命和维护成本。
这个设计不仅能够提高塑料制品的质量,还能够提高生产效率和降低成本。
三、设计一个多功能的塑料模具随着市场需求的多样化,塑料制品的功能也越来越丰富。
因此,设计一个多功能的塑料模具成为了一个有创意的毕业设计题目。
这个设计要求考虑模具的结构和功能,以适应不同的产品需求。
例如,可以设计一个可变形的模具,可以生产不同形状和尺寸的塑料制品。
或者设计一个带有自动化功能的模具,可以实现自动上料、成型和脱模等操作。
这个设计不仅能够提高生产效率,还能够满足市场的多样化需求。
四、设计一个智能化的塑料模具随着人工智能技术的发展,智能化的制造方式正在逐渐兴起。
因此,设计一个智能化的塑料模具成为了一个前沿的毕业设计题目。
这个设计要求考虑模具与智能设备的连接和交互,以实现自动化的生产流程。
例如,可以设计一个能够实时监测温度、压力和湿度等参数的模具,以优化生产过程。
塑胶模具设计手册
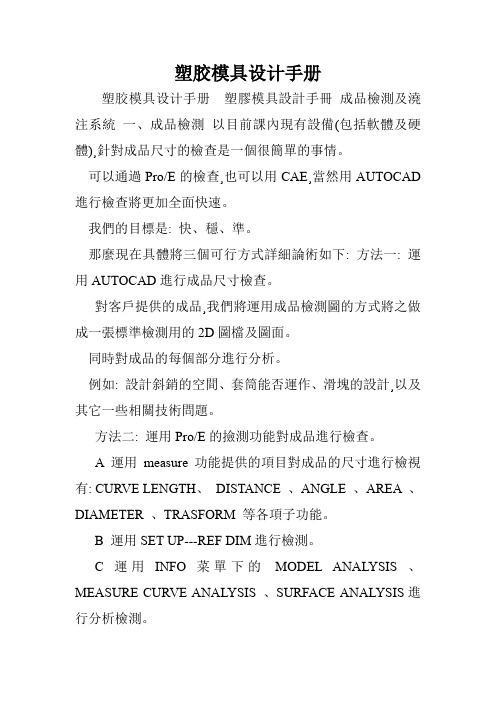
塑胶模具设计手册塑胶模具设计手册塑膠模具設計手冊成品檢測及澆注系統一、成品檢測以目前課內現有設備(包括軟體及硬體)¸針對成品尺寸的檢查是一個很簡單的事情。
可以通過Pro/E的檢查¸也可以用CAE¸當然用AUTOCAD 進行檢查將更加全面快速。
我們的目標是: 快、穩、準。
那麼現在具體將三個可行方式詳細論術如下: 方法一: 運用AUTOCAD進行成品尺寸檢查。
對客戶提供的成品¸我們將運用成品檢測圖的方式將之做成一張標準檢測用的2D圖檔及圖面。
同時對成品的每個部分進行分析。
例如: 設計斜銷的空間、套筒能否運作、滑塊的設計¸以及其它一些相關技術問題。
方法二: 運用Pro/E的撿測功能對成品進行檢查。
A運用measure功能提供的項目對成品的尺寸進行檢視有: CURVE LENGTH、DISTANCE 、ANGLE 、AREA 、DIAMETER 、TRASFORM 等各項子功能。
B 運用SET UP---REF DIM進行檢測。
C 運用INFO菜單下的MODEL ANALYSIS 、MEASURE CURVE ANALYSIS 、SURFACE ANALYSIS進行分析檢測。
方法三:運用CAE功能對成品進行檢測。
二、重量材質部分: 我們知道運用Pro/E的工程計算的功能可以很清楚地計算出成品的體積、重量。
我們運用CAE提供的資料庫將常用塑膠材料的特性進行匯編¸利用方便的塑膠特性選擇注塑成型機的大小。
三、投影面積的大小: 投影面積的大小也可以通過Pro/E 計算¸當然CAE的計算也是可以完成的。
只不過是CAE中投影面積的計算費時太長。
這不是方法上的問題¸而是技巧性的問題。
四、模流分析的結果。
塑膠材料的特性及進膠方式。
一些常見的高份子材料列如下表: 結晶性非結晶性PP 聚丙烯PS(ATACTIC)聚苯乙烯HDPE高密度聚乙烯PV AC 聚酯酸乙烯LDPE低高密度聚乙烯PMMA聚甲基丙烯酸甲酯PA(NYLON) EV A乙烯--醋酸乙烯共聚合物POM聚縮醛A V PTFE EV PEO CHLORINATED PE氯化聚乙烯PETP(PET)聚對苯二甲二乙酯ABS HIPS PPO 賽璐璐(cellulose)纖維素塑膠PC 聚碳酸酯PBT 聚對丁烯二甲二乙酯對一些常見的¸我們公司及客戶們經常使用的塑膠特性做一些簡單的介紹: 一、PC塑料(POLYCARBONATE): PC 兼具有耐熱性、耐沖擊性和透明性。
塑料模具课程设计实例
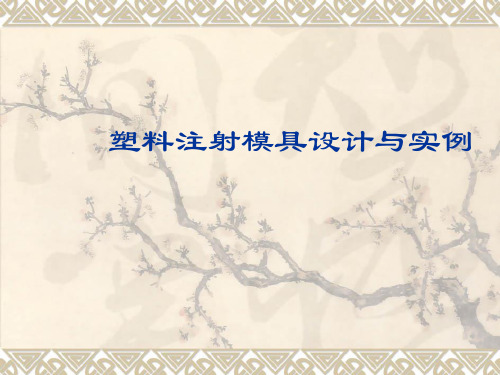
塑料注射模具设计与实例
本章基本内容
(2)模具钢
3Cr2Mo(P20)钢:可预硬化的塑料模具钢,预硬化后
硬度为36~38 HRC,适用于制作塑料注射模具型腔,其 加工性能和表面抛光性较好。 10Ni3CuAIVS(PMS)钢:析出硬化钢。预硬化后时效 硬化,硬度可达40~45 HRC。热变形极小,可做镜面抛 光,特别适合于腐蚀精细花纹。可用于制作尺寸精度高, 生产批量大的塑料注射模具。 6Ni7Ti2Cr钢:马氏体时效钢。在未加工前为固熔体 状态,易于加工。精加工后以480℃~520℃进行时效, 硬度可达50-57 HRC。适用于制造要求尺寸精度高的小 型塑料注射模具,可做镜面抛光。 8CrMnWMoVS(8CrMn)钢:为易切预硬化钢,可做镜面 抛光。其抗拉强度高,常用于大型注射模具。调质后硬 度为33-35 HRC,淬火时可空冷,硬度可达42-60 HRC。 25CrNi3MoAI钢:适用于型腔腐蚀花纹,属于时效硬 化钢。调质后硬度23 25 HRC,可用普通高速钢刀具加 工。时效后硬度38~42 HRC。可以做氮化处理,氮化处 理后表层硬度可达1100 HV。 Crl6Ni4Cu3Nb(PCR)钢:耐腐蚀钢。可以空冷淬火,
塑料注射模具制造特点 塑料注射模具零件常用加工方法和材料 塑料注射模具装配 塑料注射模具设计与制造实例
重点、难点
塑料注射模具制造特点 塑料注射模具零件常用加工方法和材料 塑料注射模具设计
塑料模具设计说明书【范本模板】

湖南工学院课程设计设计课题注塑模具设计设计学院机械工程学院设计班级成型1001班设计者姓名原育民设计时间2013 年 12月目录1. 塑件的工艺分析 (4)1。
1塑件的成型工艺性分析 (4)1。
1.1 塑件材料ABS的使用性能 (5)1.1。
2 塑件材料ABS的加工特性 (5)1.2 塑件的成型工艺参数确定 (6)2 模具的基本结构及模架选择 (6)2。
1 模具的基本结构 (6)2.1.1 确定成型方法 (6)2。
1。
2 型腔布置 (7)2.1.3 确定分型面 (7)2.1。
4 选择浇注系统 (8)2。
1。
5 确定推出方式 (8)2。
1.6 侧向抽芯机构 (9)2.1。
7选择成型设备 (9)2.2 选择模架 (11)2.2.1 模架的结构 (11)2。
2。
2 模架安装尺寸校核 (11)3 模具结构、尺寸的设计计算 (12)3.1 模具结构设计计算 (12)3。
1.1 型腔结构 (12)3.1.2 型芯结构 (12)3。
1.3 斜导柱、滑块结构 (12)3.1。
4 模具的导向结构 (12)3。
2 模具成型尺寸设计计算 (13)3。
2.1 型腔径向尺寸 (13)3。
2。
2 型腔深度尺寸 (13)3.2。
3 型芯径向尺寸 (14)3.2.4 型芯高度尺寸 (14)3。
3 模具加热、冷却系统的计算 (15)3。
3。
1 模具加热 (15)3.3.2 模具冷却 (15)4. 模具主要零件图及加工工艺规程 (16)4。
1 模具定模板零件图及加工工艺规程 (16)4.2 模具侧滑块零件图及加工工艺规程....... 错误!未定义书签。
4.3 模具动模板(型芯固定板)零件图及加工工艺规程 (17)5 模具总装图及模具的装配、试模.......................... 错误!未定义书签。
5。
1 模具的安装试模。
.。
.。
.。
..。
...。
..。
.。
...。
.。
.。
.。
.。
.。
.。
..。
..。
.。
.。
185.2。
塑料模具设计知识试题及答案

塑料模具设计知识试题及答案塑料模具设计知识试题及答案无论在学习或是工作中,我们都不可避免地会接触到试题,借助试题可以对一个人进行全方位的考核。
你知道什么样的试题才是好试题吗?下面是小编收集整理的塑料模具设计知识试题及答案,仅供参考,大家一起来看看吧。
一、判断题(共15题。
将判断结果填进答题卡中,正确的填“√”,错误的填“×”。
每题2分,满分30分。
)1、我国国标规定,细实线的宽度约为粗实线的一半。
2、注塑模胚的材料通常为中碳钢。
3、对于PA和PMMA来说,都可以采用潜伏式浇口。
4、潜伏式浇口和点浇口都是可以自动脱落的进浇方式。
5、在精密模具设计中,与模具开模方向垂直的分型面是可以接受的。
6、模具冷却的目的是快速降低塑料熔体的温度,使之尽快凝固以便顶出。
7、薄壁制品发生缺料时,应该首先进步注射压力。
8、三大高分子材料是塑料、橡胶、化学纤维。
9、为了使嵌件与塑件牢固地连接在一起,嵌件的表面应具有止动的部分,以防嵌件移动。
10、为便于塑料件脱模,应使塑件在开模时尽可能留在定模一侧。
11、为了避免滑块和顶杆发生干涉,滑块必须先于顶杆回位。
12、注塑模具CAD是指技术人员以计算机为工具,对塑料模具进行绘图、分析计算和编写技术文件等设计活动的统称。
13、A3钢属于优质碳素结构钢,45#钢属于普通碳素钢。
14、成型磨削工件外圆弧时,砂轮必须也加工成外圆弧。
15、数控机床按控制方式不同可分为:开环控制系统、闭环控制系统、半闭环控制系统。
二、单项选择题(共20题。
选择正确的答案,并将答案填进答题卡。
每题2分,满分40分。
)1、标注直径为50mm的球面,正确的是。
A、φ50B、Sφ50C、R50D、SR502、一般地,抽芯滑块的动作来自。
A、液压系统B、气压系统C、开模动力D、以上皆是3、为使塑料制品上呈现正凹字样,模具相应位置应该加工字样。
A、正凹B、正凸C、反凹D、反凸4、以下哪种因素对塑料制品的烧焦影响最大?A、注塑压力B、注塑速度C、注塑温度D、模具温度5、通常情况下,使用机械手取生产品,以下哪种说法是不恰当的?A、可以进步生产效率B、可以进步制品质量C、可以缩短注塑周期D、可以缩短冷却时间6、下列塑料材料,不适合使用三板模(小水口)的是。
塑料模具课程设计罩盖模具设计
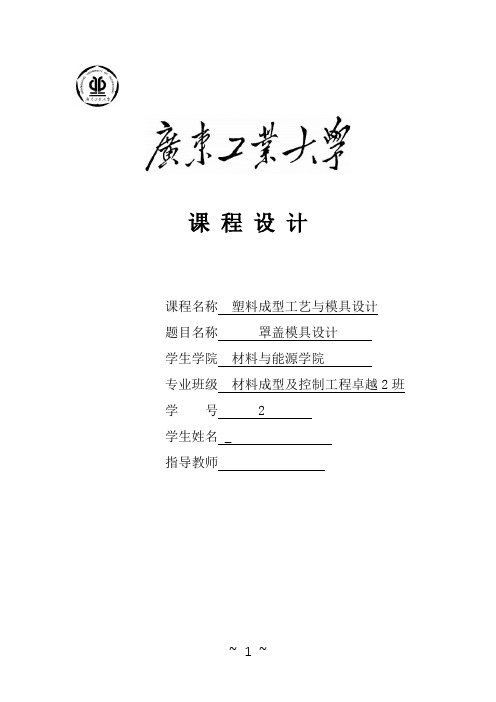
课程设计课程名称塑料成型工艺与模具设计题目名称罩盖模具设计学生学院材料与能源学院专业班级材料成型及控制工程卓越2班学号 2学生姓名 _指导教师目录一、设计课题 (3)二、塑件成型工艺性分析 (3)三、拟定模具的结构形式 (3)四、注射机型号的确定 (7)五、成型零件的结构设计和计算 (8)六、成型零件的结构设计和计算 (9)七、排气槽的设计 (10)八、导向与定位结构的设计 (11)九、总装配图和零件图的绘制 (11)十、结论 (13)十一、参考文献 (13)一、设计课题罩盖,结构如图所示。
大批量生产。
材料ABS。
二、塑件成型工艺性分析2.1、塑件工艺分析(1)外形尺寸该塑件壁厚为3mm,塑件外形尺寸不大,塑料熔体流程不太大,适合与注塑成型。
(2)精度等级公差要求等级较低,能够完成。
(3)脱模斜度ABS属于无定型塑料,成型收缩率较小。
三、拟定模具的结构形式3.1、分型面为位置的确定通过对塑件结构形式的分析,分型面应选在端盖截面积最大且利于开模却取出塑件的底平面上。
如图:圆柱形形芯包紧力的计算:P=EST/R E=塑料弹性模量S=塑件收缩率T=壁厚R=最大径向尺寸经计算后模的包紧力比前模大,故塑件可以留在后模。
3.2、型腔数量和排列方式的确定(1)型腔数量的确定该塑件为大批量生产,可采用一摸多腔的结构形式。
同时考虑到塑件尺寸,模具结构尺寸的大小关系,以及各种成本费用的关系,初步定位一摸两腔的结构形式。
(2)型腔排列形式的确定多腔模式尽量采用平衡式排列布置,且要力求紧凑,并与浇口开设的位置对称。
由于该设计采用的是一摸两腔的布置,故采用直线对称排比。
如下图:(3)模具结构形式的确定从上面的分析可知,本模具设计属于一摸两腔,对称直线排列,采用推管推杆推出的结构形式。
浇注系统设计时,流到采用对称平衡式,浇口采用潜伏式,开模时水口凝料与塑胶自动脱离。
因此定模部分不需要单独开设分型面取出凝料,动模部分需要添加型芯固定板、由上综合分析可知,选用单分型面注射模。
塑料模具毕业设计说明书例子

第三章成型设备的选用3.1 注塑机的选择塑件在分型面上的投影面积:1.754mm2塑件体积: V=1.168mm3塑件密度: =1.0g/cm3所以塑件的质量: m = 1.168×1.0=1.168g根据任务书的要求,该塑件采用侧浇口形式,并且采用一模两腔的形式,加上浇注系统及冷凝料材料体积约为?cm3。
所以初选设备为G54-S200/400其主要技术规格见表3.1。
表3.1 G54-S200/400设备主要技术规格3.2模架的选择通过塑件的分析,以及注塑机的技术规格要求,选用A2型模架,该模架各模板以及相关尺寸见图3.1、表3.2和表3.3。
图3.1 P2型模架示意图表3.2 模架各板厚尺寸表3.3模架孔位置尺寸H1=36㎜;A=56㎜;B=46㎜;H2=46㎜;C=76㎜;H3=36㎜;所以模具的总厚度为:36+56+46+46+76+36=296mm,在注塑机的装模行程之内。
3.3模具参数的校核(1)注射量的校核要求注射量不超过注射机的最大注射量,在注塑生产中,注塑机每一个成型周期向模具腔内注入的塑料熔体体积或质量称为塑件的注射量,其中包括浇注系统内所存留的塑料熔体体积,选择注塑机时,必须保证塑件的注射量小于注塑机的最大注射量的(80~85)%,最小注射量不小于注塑机注射量的20%,根据式kMmax≥M,M=n∑M i+m式中 Mmax-----注塑机最大注射量/ cm3;Mi-----浇注系统凝料的质量或体积/ cm3;m-----单个制件质量或体积/ cm3;n-----型腔数目/个;k-----注射机最大注射量利用系数,一般取0.8。
0.8×320≥2×5.8+4.33≈15.93 cm3。
故:注射机注射量满足要求。
(2)注射压力的校核塑料成型所需要的注射压力是由塑料品种、注射机类型、喷嘴形式、塑件形状以及浇注系统的压力损失等因素决定的。
注射压力的校核是检验注射机的最大注射压力能否满足制品的成型要求。
塑胶模具设计准GB
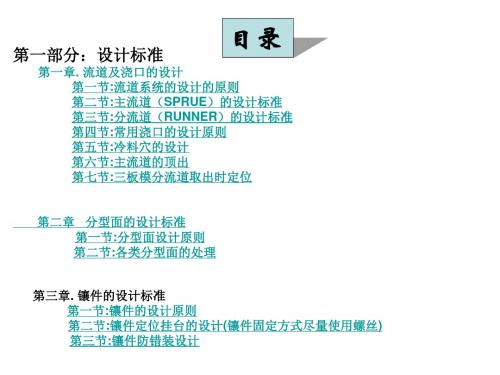
2.对于多品多穴采用非平衡式分流道和进胶口,应依照流动的距离调整水口或流道的 大小,以确保尽可能各腔填充同步。
3.为减少热量及压力损失,流道应尽量短、直,且转角处须加R角保证流动顺畅。流 道表面须用600#以上沙纸省光,如果部品品是镜面,流道须用1000#沙纸省光。
差应提交客户确认;
3、模板间距考虑:分模面的确定要保证母、公模开模行程最短;
4、应尽量避免侧抽芯机构,若无法避免侧抽芯,应使抽芯尽量短,并尽量使滑块全
部出在公模;
5、由于斜滑块合模时锁紧力较小,对于投影面积较大的大型塑件,可将塑件投影面
积大的分模面放在公母模合模的主平面上,而将投影面积较小的分模面作为侧向分模
第一章. 模架的设计
第一节、撑头 第二节、小水口的开模控制机构 第三节、中托司及中托边 第四节、顶针复位开关 第五节、锁模扣 第六节、上 下固定板高度 第七节、定位块 第八节、导柱 导套排气 第九节、模架常用标准件的选择 第十节、模架板吊环螺丝孔的规定
第二章.标准件
第一节:内部自制标准件的选择
第二节:螺丝、顶针等相关标准件数据速查表
目录
三、分流道(RUNNER)的设计标准
1.流道类型
(1).圆形流道 D
(2).U形流道 20°
H=D
D
2.D的系列值:2 2.5 3 3.5 4 4.5 5 6 7 8 (10 12参考使用)
3.D的取值方式:
对于PE、PA等材料,D值可取小值,对于PC、PMMA等材料,D值可取大值。
目录
(2).经验估算
注塑机吨位(TON) ﹤130 ﹤350 350吨以上
塑料模具设计
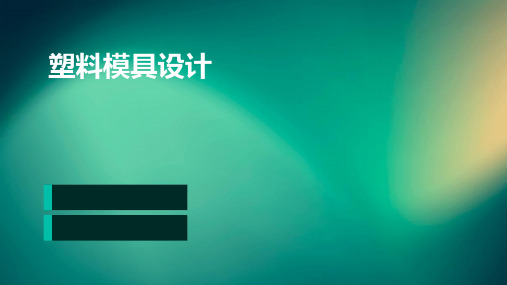
对模具的各个部件进行详细的结构设计, 确定各部件的材料、尺寸、加工精度等。
对模具的强度、刚度、热传导等进行校核 ,确保模具能够满足生产要求,并进行优 化以提高生产效率和产品质量。
塑料模具的分类与特点
按成型工艺分类
注射模具、压缩模具、压注模 具、挤出模具等。
按结构分类
二板式模具、三板式模具、点 浇口模具等。
03 塑料模具设计技术
分型面设计
01
分型面是模具中用于将 模具分成动模和定模的 界面。
02
03
04
分型面的设计应考虑塑料件 的形状、尺寸、精度要求以 及模具的制造和装配工艺。
分型面应尽可能选择在塑 料件的最大轮廓处,以简 化模具结构和方便脱模。
分型面的选择还需考虑模 具的开合和顶出方式,以 确保模具的正常运作。
模具工作原理
成型过程
描述塑料在模具中的流动、成型、 冷却和脱模过程,说明各阶段的 工作原理和相互关系。
动作顺序
说明模具各部分动作的顺序和相互 配合方式,如开模、合模、注射、 保压、冷却、脱模等阶段。
工作循环
描述模具工作循环的过程,包括合 模、注射、保压、冷却、开模、脱 模等步骤,说明各步骤的作用和工 作原理。
调整和优化。
实例二:汽车非常严格,因此模具设计需 要精确控制尺寸和形状。同时,考虑到生产效率,模具应 易于拆卸和组装。
材料选择
钢材是常用的模具材料,因为它具有高强度和耐磨性。对 于大型零部件,可能会选择更加坚固的钢材。
设计流程
与手机壳模具设计类似,但需要考虑更多的因素,如模具 的冷却系统和排气系统等。
浇注系统设计
浇注系统是引导塑料熔体从注 射机流入模具型腔的通道。
浇注系统的设计应确保塑料熔 体的流动平稳,避免出现湍流
塑料模具设计实例

塑料模设计实例塑料注射模具设计与制造实例是通过设计图1.1所示的防护罩的注射模,全面介绍了从塑料成形工艺分析到确定模具的主要结构,最后绘制出模具的塑料注射模具设计全过程。
设计任务:产品名称:防护罩产品材料:ABS(抗冲)产品数量:较大批量生产塑料尺寸:如图1.1所示塑料质量:15克塑料颜色:红色塑料要求:塑料外侧表面光滑,下端外沿不允许有浇口痕迹。
塑料允许最大脱模斜度0.5°图1.1 塑件图一.注射模塑工艺设计1.材料性能分析(1)塑料材料特性ABS塑料(丙乙烯—丁二烯—苯乙烯共聚物)是在聚苯乙烯分子中导入了丙烯腈、丁二烯等异种单体后成为的改性共聚物,也可称为改性聚苯乙烯,具有比聚苯乙烯更好的使用和工艺性能。
ABS是一种常用的具有良好的综合力学性能的工程材料。
ABS 塑料为无定型料,一般不透明。
ABS无毒、无味,成型塑料的表面有较好的光泽。
ABS 具有良好的机械强度,特别是抗冲击强度高。
ABS还具有一定的耐磨性、耐寒性、耐水性、耐油性、化学稳定性和电性能。
ABS的缺点是耐热性不高,并且耐气候性较差,在紫外线作用下易变硬发脆。
(2)塑料材料成形性能使用ABS注射成形塑料制品时,由于其熔体黏度较高,所需的注射成形压力较高,因此塑料对型芯的包紧力较大,故塑料应采用较大的脱模斜度。
另外熔体黏度较高,使ABS制品易产生熔接痕,所以模具设计时应注意减少浇注系统对料流的阻力。
ABS 易吸水,成形加工前应进行干燥处理。
在正常的成形条件下,ABS制品的尺寸稳定性较好。
(3)塑料的成形工艺参数确定查有关手册得到ABS(抗冲)塑料的成形工艺参数:密度 1.01~1.04克/mm3收 缩 率 0.3%~0.8%预热温度 80°c~85°c ,预热时间2~3h料筒温度 后段150°c~170°c ,中段165°C~180°c ,前段180°c~200°c 喷嘴温度 170°c~180°c 模具温度 50°c~80°c 注射压力 60~100MPa注射时间 注射时间20~90s ,保压时间0~5s ,冷却时间20~150s.2.塑件的结构工艺性分析(1)塑件的尺寸精度分析该塑件上未注精度要求的均按照SJ1372中8级精度公差值选取,则其主要尺寸公差标注如下(单位均为mm ):外形尺寸:26.0040+φ、 1.2050+、12.0045+、94.0025+R 内形尺寸:26.008.36+φ 孔 尺 寸:52.0010+φ孔心距尺寸:34.015± (2)塑件表面质量分析该塑件要求外形美观,外表面表面光滑,没有斑点及熔接痕,粗糙度可取Ra0.4μm ,下端外沿不允许有浇口痕迹,允许最大脱模斜度0.5°,而塑件内部没有较高的表面粗糙度要求。
塑料模具设计产品外观要求标准
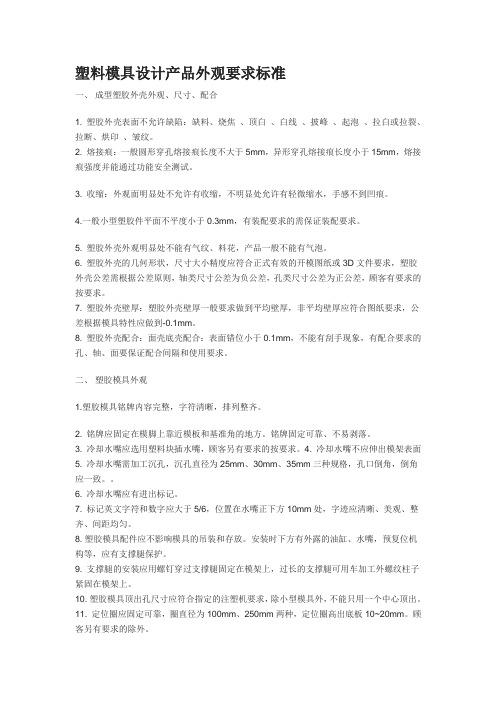
塑料模具设计产品外观要求标准一、成型塑胶外壳外观、尺寸、配合1. 塑胶外壳表面不允许缺陷:缺料、烧焦、顶白、白线、披峰、起泡、拉白或拉裂、拉断、烘印、皱纹。
2. 熔接痕:一般圆形穿孔熔接痕长度不大于5mm,异形穿孔熔接痕长度小于15mm,熔接痕强度并能通过功能安全测试。
3. 收缩:外观面明显处不允许有收缩,不明显处允许有轻微缩水,手感不到凹痕。
4.一般小型塑胶件平面不平度小于0.3mm,有装配要求的需保证装配要求。
5. 塑胶外壳外观明显处不能有气纹、料花,产品一般不能有气泡。
6. 塑胶外壳的几何形状,尺寸大小精度应符合正式有效的开模图纸或3D文件要求,塑胶外壳公差需根据公差原则,轴类尺寸公差为负公差,孔类尺寸公差为正公差,顾客有要求的按要求。
7. 塑胶外壳壁厚:塑胶外壳壁厚一般要求做到平均壁厚,非平均壁厚应符合图纸要求,公差根据模具特性应做到-0.1mm。
8. 塑胶外壳配合:面壳底壳配合:表面错位小于0.1mm,不能有刮手现象,有配合要求的孔、轴、面要保证配合间隔和使用要求。
二、塑胶模具外观1.塑胶模具铭牌内容完整,字符清晰,排列整齐。
2. 铭牌应固定在模脚上靠近模板和基准角的地方。
铭牌固定可靠、不易剥落。
3. 冷却水嘴应选用塑料块插水嘴,顾客另有要求的按要求。
4. 冷却水嘴不应伸出模架表面5. 冷却水嘴需加工沉孔,沉孔直径为25mm、30mm、35mm三种规格,孔口倒角,倒角应一致。
6. 冷却水嘴应有进出标记。
7. 标记英文字符和数字应大于5/6,位置在水嘴正下方10mm处,字迹应清晰、美观、整齐、间距均匀。
8. 塑胶模具配件应不影响模具的吊装和存放。
安装时下方有外露的油缸、水嘴,预复位机构等,应有支撑腿保护。
9. 支撑腿的安装应用螺钉穿过支撑腿固定在模架上,过长的支撑腿可用车加工外螺纹柱子紧固在模架上。
10. 塑胶模具顶出孔尺寸应符合指定的注塑机要求,除小型模具外,不能只用一个中心顶出。
11. 定位圈应固定可靠,圈直径为100mm、250mm两种,定位圈高出底板10~20mm。
塑料模具课程设计说明书
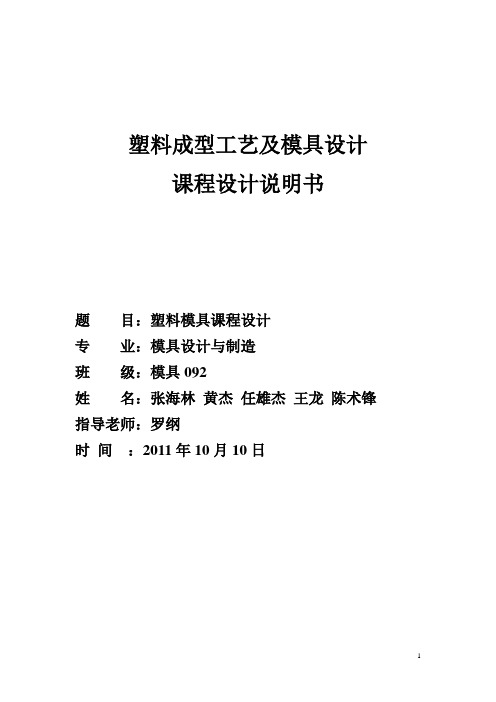
塑料成型工艺及模具设计课程设计说明书题目:塑料模具课程设计专业:模具设计与制造班级:模具092姓名:张海林黄杰任雄杰王龙陈术锋指导老师:罗纲时间:2011年10月10日目录第一部分产品的说明第二部分塑件分析第三部分注射机的型号和规格选择及校核第四部分型腔的数目决定及排布第五部分分型面的选择第六部分浇注系统的设计第七部分型零件的工作尺寸计算第八部分推出机构的设计第九部分模架的选用第十部分冷却系统设计第十一部分抽芯机构设计第十二部分模具的动作过程第十三部分设计小结第十四部分参考资料第 一 部分 产品的说明本塑件结构简单,壁厚均匀,模架结构较简单。
精度要求较高,为五级精度,材料为聚乙烯,成型性能良好,其他并无特殊要求。
1:1第 二 部分 塑件的分析聚乙烯 化学名称:PE材料分析:塑件的材料采用低压法聚合的聚乙烯,聚乙烯无毒,无味,呈乳白色。
聚乙烯有良好的绝缘性、耐化学腐蚀性及耐低温性能,还有很高的耐水性。
用低压法制得的聚乙烯,密度和结晶度较高,刚性大,机械强度高,但透明性较差,适于制备各种工业配件。
这种聚乙烯又称高密度聚乙烯。
但和其他塑料相比,聚乙烯机械强度低,表面硬度差。
成型时在流动方向上和垂直方向上收缩性差异较大,易产生变形、缩孔。
此外,聚乙烯质地柔软且易脱模,塑件有浅的侧凹是可强制脱模。
塑件注射成型工艺参数的确定:根据该塑件的结构特点和得成型性能,查相关手册得到聚丙烯的成型工艺参数:第三部分注射机的型号和规格选择及校核注射模是安装在注射机上的,因此在设计注射模具时应该对注射机有关技术规范进行必要的了解,以便设计出符合要求的模具,同时选定合适的注射机型号。
从模具设计角度考虑,需要了解注射机的主要技术规范。
在设计模具时,最好查阅注射机生产厂家提供的有关“注射机使用说明书”上标明的技术规范,。
因为即使同一规格的注射机,生产厂家不同,其技术规格也略有差异。
1、注射机的选用选用注射机时,通常是以某塑件(或模具)实际需要的注射量和注射压力初选某一公称注射量的注射机型号,然后依次对该机型的公称锁模力、模板行程以及模具安装部分的尺寸一一进行校核。
塑料模具设计(毕业)论文
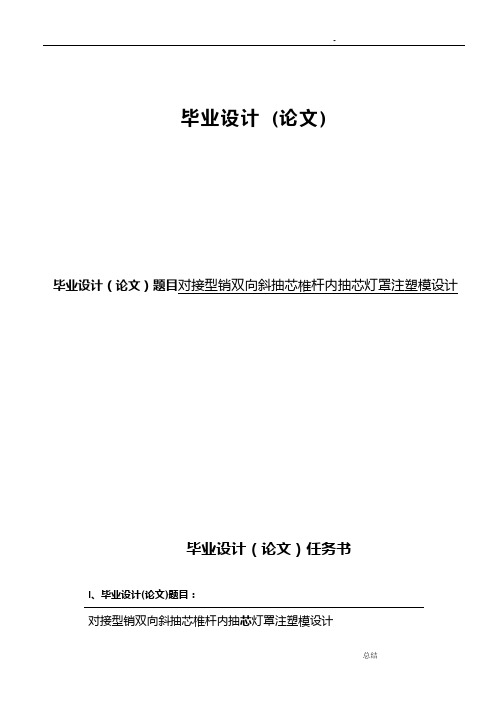
-毕业设计(论文)毕业设计(论文)题目对接型销双向斜抽芯椎杆内抽芯灯罩注塑模设计毕业设计(论文)任务书I、毕业设计(论文)题目:对接型销双向斜抽芯椎杆内抽芯灯罩注塑模设计II、毕业设计(论文)使用的原始资料(数据)及设计技术要求:见《先进注塑模330例设计评注》I I I、毕业设计(论文)工作内容及完成时间:1.绘制产品的三维与二维图,并分析其成型工艺性。
2. 制品的基本参数的计算及注塑机的选用。
3. 模具类型及结构的确定。
4. 模具结构草图的绘制。
5. 模具和成型机械关系的校核。
6.模具零件的设计计算。
7. 绘制模具的装配图(包括三维与二维)。
8. 绘制模具零件图(包括三维与二维)。
9. 编写设计论文。
Ⅳ主要参考资料:1. 模具设计手册2.模具相关书籍3. 机械制图附注:任务书应该附在已完成的毕业设计说明书首页。
零件图:-说明:生产批量:中批量生产料的精度等级:低精度。
摘要注射成型是塑料成型的一种重要方法,它主要适用于热塑性塑料的成型,可以一次成型形状复杂的精密塑件。
本课题就是将塑料圆盖作为设计模型,将注射模具的相关知识作为依据,阐述塑料注射模具的设计过程。
通过对塑料圆盖成型工艺的正确分析,设计了一副一模一腔的塑料模具。
模具中决定塑件几何形状和尺寸的零部件称为成型零件,包括前模板、前模仁、后模板、后模仁、后模镶件、斜导柱、滑块等的设计与加工工艺过程。
成型零部件在工作时直接与塑料接触,在一定的温度下承受熔体的高温和高压,因此必须要有合理的结构、较高的强度和刚度、较好的耐磨性、正确的几何形状、较高的尺寸精度和较低的表面粗糙度。
重要零件的工艺参数的选择与计算,推出机构与浇注系统以及其它结构的设计过程。
设计成型零部件时,应根据塑料的特性、塑件的结构和使用要求,确定型腔的总体布局,选择分型面,确定脱模方式,设计浇注系统、排溢系统等,然后根据加工工艺和装配工艺的要求进行成型零部件的结构设计,计算成型零部件的工作尺寸,对关键的成型零部件进行强度和刚度校核。
CATIA注塑模具教程第8章模具设计举例

第8章模具设计举例产品结构分析及材料选择8.1.1 样件分析在模具设计进程中,一样是先依照制品的结构零件图或样件进行产品的结构分析,以如图8-1所示的过滤器罩为例,该制品三维投影尺寸长宽高为137mm×112mm×45mm,壁厚;外部圆角半径3mm,内部圆角半径,拔模角25°;内有肋板,肋板高28mm厚,拔模角2°。
该制品精度品级一样,尺寸误差±,为降低成型费用,采纳一模多腔,并非对制品进行后序加工。
图8-1 过滤器罩8.1.2 材料选择由于塑料特殊的理化和机械性能,塑料模具设计进程中一个很重要的步骤是选择材料,如此才能够在模具设计进程中确信收缩比等参数,那个地址选择ABS(三种聚合物的共聚物)工程塑料,该材质的性质数据如下:典型应用范围:汽车(仪表板,工具舱门,车轮盖,反光镜盒等),电冰箱,大强度工具(搅拌器,食物加工机,割草机等),机壳体,打字机键盘及喷气式雪撬车等。
注塑模工艺条件:ABS 材料具有吸湿性,要求在加工之前进行干燥处置,建议干燥条件为80~90℃下最少干燥2小时,材料湿度应保证小于%;熔化温度为210~280℃,建议温度245℃,模具温度25~70℃ (模具温度将阻碍制品光洁度,温度较低那么致使光洁度较低);注射压力500~1000bar ;注射速度为中高速度。
化学和物理特性:ABS 是由丙烯腈、丁二烯和苯乙烯三种化学单体合成。
每种单体都具有不同特性,丙烯腈有高强度、热稳固性及化学稳固性;丁二烯具有坚韧性、抗冲击特性;苯乙烯具有易加工、高光洁度及高强度。
从形态上看,ABS 是非结晶性材料。
三种单体的聚合产生了具有两相的三元共聚物,一个是苯乙烯-丙烯腈的持续相,另一个是聚丁二烯橡胶分散相。
ABS 的特性要紧取决于三种单体的比率和两相中的分子结构。
这就能够够在产品设计上具有专门大的灵活性,而且由此产生了市场上百种不同品质的ABS 材料。
- 1、下载文档前请自行甄别文档内容的完整性,平台不提供额外的编辑、内容补充、找答案等附加服务。
- 2、"仅部分预览"的文档,不可在线预览部分如存在完整性等问题,可反馈申请退款(可完整预览的文档不适用该条件!)。
- 3、如文档侵犯您的权益,请联系客服反馈,我们会尽快为您处理(人工客服工作时间:9:00-18:30)。
毕业设计(论文)题目院系专业班级学生姓名指导教师摘要我国加入WTO之后,给国内模具制造业既带来冲击,又带来了机遇,总体来说是机遇大与挑战。
我国的制造业正是迅速崛起的时代,国内制造业前景一片光明。
而在这模具制造业中注塑模的发展更为突出,当然制作一套模具首先它的设计是占很大比例的。
本设计主要介绍了轮子注射模设计与制造方法,先读零件图,塑件工艺性的分析等等。
确定行腔数目,分型面的选择,确定浇注系统,推出机构导向机构,成型零件的结构设计、工作尺寸设计,模具材料的选择,通过Pro/E建模分析模型质量和体积确定最大注射量,选出注塑机的机型并进行一定的校核。
关键词:轮子注射模、塑件工艺性方案、模具的设计PICK TOAfter China's accession to the WTO, to domestic die manufacturing both impact, and brought the opportunity, in general is big and challenge opportunity. China's manufacturing industry is rapidly rising era, the domestic manufacturing for a brighter. And in that mold manufacturing industry in the development of injection mold is more outstanding, of course, making a set of mould first it is designed to take up a large proportion.This design mainly introduces the design and manufacture of wheels injection mould method, read part drawing, the analysis of the technology of plastics, etc. Determine the number of cavity while curing, points the selection of type, sure gating system, roll out institutions steering mechanism, the structure design, molding part work size design, mould material choice, through the Pro/E modeling analysis model quality and volume of maximum injection, to select the model of injection molding machine and certain respectively.Keywords: wheels injection mould, plastic parts technology solutions, the design of the mould目录第一章轮子的工艺性分析一)、塑料的工艺性分析二)、塑件结构工艺性分析三)、塑件尺寸工艺性分析第二章注射机的选择一)行腔数目的的初步确定二)注射机的选择三)最大注射量的校核四)注射压力的校核五)锁模力的校核六)模具与注射机合模部分相关尺寸校核七)开模行程校核八)推出机构校核第三章注射成型方案确定一)分型面的类型。
位置及数量的确定二)浇注系统机构及尺寸设计三)推出机构的选择四)导向机构的选择五)加热/冷却系统的选择及计算第三章注射成型零件设计一)成型零件结构设计二)成型零件工作尺寸设计三)模具材料的选择第四章模具图纸一)模具装配图二)非标件零件图致谢参考文献第一章塑件工艺性分析1.1 塑料工艺性分析该塑件选用的材料是聚甲醛(POM)聚甲醛是以三聚甲醛为原料聚合而成的线型热塑性工程塑料,由于原料(甲醛)来源丰富,综合性能优异,成型方便,因此作为工程塑料发展很快。
POM广泛应用于汽车、机械、仪表、电器、化工和农机等的零部件制造。
POM的化学和物理性质:POM为半透明到不透明的白色粉末或粒料,密度为1.42/g ·cm3左右,着色性好,易燃,高结晶性。
POM具有良好的力学性能,比强度、比刚度十分突出,与金属接近(超过尼龙)抗冲击性能是其他工程材料不能比的。
用于制造各种齿轮、轴承、弹簧、凸轮、螺栓、螺母、泵体及机床导轨等。
POM具有良好的电缘性,几乎不受温度影响,其介电性能在很宽的频率范围内变化不大。
用于制造电动工具外壳、电话机、电视机、计算机及继电器中的零部件。
POM的耐化学性质优良,耐有机溶剂烃、醇、酯、醚和油脂性能良好,不耐强酸、碱及氧化剂。
需加入助剂提高热稳定性。
POM尺寸稳定性好,吸湿性小,可用来制造精密零件。
聚甲醛的成型特性:1)可用注射(95%以上)、技出及吹塑等成型加工方法。
吸湿性小,可不必干燥处理。
2)熔融温度范围窄,热敏性强,易分解,分解时有刺激性和腐蚀性气体产生,熔料不宜在料筒是时间过长塑化时螺杆转速要低,防止过热和长时间受热。
采用直通喷嘴,喷嘴孔径大一些,防止滞料分解。
3)熔融及凝固速度快,有利于缩短成型周期,但结晶速度快,塑件易产生毛斑、折皱、凹陷及熔接痕等。
料问稍低于熔融温度就会结晶,结晶后流动性变差。
4)流动性中等,溢边值约0.04,流动性对温度变化不敏感,对压力十分敏感,可增加压力提高熔体流动性。
5)摩擦系数小,弹性大,对于带有浅侧凹凸的塑件可强行脱模。
6)浇注系统流动阻力应尽量小,浇口截面宜取大些,应避免死角滞料;模具应加热,改善流动性,使塑件内外冷却均匀,防止产生缺陷;成型零件的模具应选耐磨及耐腐蚀的材料,并淬硬及镀铬,应排气。
1.2塑件结构工艺性分析该塑件的表面没有提出特殊要求,通常一般情况下外表面要求光洁,表面粗糙度可以取0.8微米,没有特殊要求的取Ra=3.2微米。
1.3 塑件尺寸的工艺性分析该塑件尺寸较大,整体结构有点复杂。
除了配合尺寸要求精度较高外,其他尺寸精度要求相对较低,但表面粗糙度要求较高,据POM的材料性能,故选一般精度等级:MT6级。
第二章注射机的选择2.1行腔数目的初步确定根据产品(轮子)结构特点,此塑料产品在模具中有两种放置方式:一种是将塑料制品的回转轴线与模具中主流道衬套的轴线垂直;另一种是将此塑料制品的中心线与模具中主流道衬套的轴线平行。
而该塑件的尺寸较大,虽然说是大批量生产但是也得一个一个的来,如果选择一模两腔它所选择的模架会很大,耗材万一在加工过程中遇到损坏,将会很麻烦同时也影响产品的生产。
故该模具在这里采用一模一腔的结构。
型腔的结构采用动、定模对称的结构,易于加工制造。
根据塑件的结构及尺寸精度要求,该塑件在注射时采用一模一。
行腔结构图2.2注射机的选择2.2.1塑件体积的计算跟据零件尺寸通过Pro/E三维建模得出:塑件的体积为V1=168cm3浇注系统的体积为V2=26.6cm3塑件与浇注系统的总体积为V=V1+V2=168+26.6=194.6 cm32.2.2塑件的质量查塑料模具设计教材P123 表4-3某些热塑性塑料的密度及压缩率知聚甲醛的密度为ρ=1.4 g/cm3塑件的体积为V1=168 cm3塑件的质量为m=ρ. V1=235g2.3最大注射量的校核V=Kl·V=1.8·V=1.8X(168+26.6)=350.28cm3根据最大注射量选择注射机,选取注射机的型号为XS-ZY-500,其参数如下:2.4 注射压力校核注射机最大注射压力要大于或等于塑件成型时所需的注射力。
塑件成型所需要的注射压力与注射机的类型、喷嘴的形式、塑料的流动性、浇注系统及行腔的阻力等因素有关。
一般取值在P=40-200Mpa2.5 锁模力的校核F>PA1()F p nA A >+即30X (83.02+0.74)=25.12kN 符合p --注射时型腔内熔体(Mpa ),常取P=20~40Mpa 。
A --塑件在分型面上的投影面积(2cm ) 1A --浇注系统在分型面上的投影面积(2cm ) F --注射机的公称锁模力。
2.6 模具与注射机合模部分相关尺寸校核 2.6.1 模具的外形尺寸安装模具的外形尺寸应小于注射机的拉杆间距,否则模具无法安装。
同时,模具的坐板尺寸不应超过注射机的模板尺寸。
2.6.2喷嘴尺寸 注射机喷嘴前端球面半径r 和孔径d 与模具浇口套始端的球面半径R 及小孔径D 应吻合,以防止高压塑料熔体从缝隙中溢出。
R=r+(1~2)mm 即R=18+(1~2)=19~20 D=d+(0.5~1)mm 即D=5+(0.5~1)=5.5~62.6.7 开模行程的校核开模行程是指模具开合模过程中,注射机移动模板的移动距离。
选注射机时,其最大的开模行程必须大于取塑件或有其他要求时所需分开模具的距离。
对于液压——机械联合作用的锁模机构的注射机,XS-ZY -500其最大开模行程是由连杆机构的冲程或其他机构的冲程所决定,不受模具厚度的影响。
该塑件分型面是双分型面故对于双分型面注射模开模行程的校核:()mm a H H S 10~521+++≥式中 H1——塑件脱模所需的推出距离; H2——塑件高度(不包括浇注系统高) a ——取出浇注系统凝料所需的分模距离(mm ) S1=7+20+10+25=62mm S1<S=500mm,所以条件符合。
2.6.8 推出机构的校核各种型号注射机的推出装置情况各及推出距离等各不相同,设计模具时,必须了解注射机推出杆的直径,推出形式,最大推出距离等,以保证模具的推出机构与注射机的推出机构相适应。
第三章 注射成型方案确定3.1行腔数目的确定模具设计时,必须先确定行腔数目,而型腔数目的确定应考虑技术、经济、质量、设备、批量等多方面的因素。
按注射机的锁模力确定型腔数目N: AP JSaS A P F N -≤式中:Ps——单位投影面积所需的锁模力(Mpa),其值等于注射机最大锁模力与最大成型面积之比,也可以参考表4-5F——注射机的公称压力(N)A a——浇注系统及飞边在分型面上的投影面积(m2);A j——单个塑件在分型面上的投影面积(m2)P S=3500/1000=3.5Mpa3.2分型面的类型、位置及数量的确定分型面的选择设计原则1)分型面应选在塑件外形最大轮廓处;2)分型面的选择应有利于塑件的顺利脱模;3)分型面的选择应保证塑件的精度要求;4)分型面的选择应满足塑件的外观质量要求;5)分型面的选择要便于模具的加工制造;6)分型面的选择应有利于排气;7)分型面的选择还要考虑到型腔在分型面上投影面积的大小。