(新)高速线材活套控制
高速线材主控台控制操作技术

第一章主控台操作分工与操作技术素质要求主控台是控制全轧线生产的中心操作室,是全厂的中央信息处理站,在高速线材轧机的连轧控制中,主控台对轧制的正常顺利进行起着关键作用。
一、主控台所管辖的区域设备主控台所管辖的区域设备有:(1)加热炉出口处夹送辊、粗轧机组、中轧机组、预精轧机组、精轧机组以及夹送辊、吐丝机。
(2)粗轧机组1#机架前卡断剪、粗轧机组8#机架后的曲柄剪、预精轧机组前的回转飞剪、事故卡断剪、精轧机组前的回转飞剪、事故碎断剪及事故卡断剪。
(3)轧线上所有活套控制器。
(4)出炉辊道、分钢辊道(5)预水冷段,水冷段二、主控台的职能与控制对象主控台的职能与控制对象有:(1)设定、调用、修改轧制程序。
(2)控制上述所有轧制区设备的动作及运行。
(3)监控轧制区的轧制过程,实现轧制工艺参数和程序控制最优化。
(4)控制轧机各机组的轧辊冷却水开与闭。
(5)组织、协调轧制生产工艺,保证生产的正常进行。
(6)担负轧制生产线的日常生产信息传递,进行轧制区物料跟踪方面的操作。
(7)有关生产数据报表的记录与汇总。
(8)监视全生产线的机械、电气、能源介质供应系统的设备运行状况与故障显示。
三、主控台与生产调度室及各操作台(点)的分工和关系1、主控台与生产调度室的关系主控台主要负责生产线上轧制生产的组织与协调,即偏重于轧钢生产人员本身的内部指挥;生产调度室主要负责轧制生产的总体指挥与协调,它的任务有:与水、电、风、气等外部能源介质供应单位的联系,对高速线材厂(车间)各专业(轧钢、电气、机修)的指挥与协调,即偏重于轧钢外部的联系。
2、主控台与各操作台(点)的关系根据高速线材生产工艺流程特点,轧制生产线上配置有6 个操作台:入炉加热出钢操作台(负责原料区原料的入炉与计量、加热炉加热工艺操作和出钢操作);主控台(负责轧制区的轧制生产工艺操作和轧钢生产协调);集卷操作台(负责散卷采集操作);打包操作台(负责将散卷打包操作);称重标牌操作台(负责成品盘卷的称量,标牌打印操作);卸卷操作台(负责卸卷操作)。
高速线材产品外部质量控制

高速线材产品外部质量控制路炜温东张家口宣龙高速线材有限责任公司075100摘要:简述高速线材产品外部质量要求,分析高速线材产品质量要求中精度、耳子、折叠、麻面、划痕、分层、裂纹、结疤等缺陷产生的原因,并根据生产实际提出相应的防止措施。
关键词:高速线材外部质量要求缺陷防止措施1 前言高速线材热轧盘条是热轧型钢截面尺寸最小的一种,由于截面积小、轧制道次多、盘卷供货、控冷工艺复杂,所以给产品的质量控制增加了难度。
宣钢高线厂从2001年第一条生产线投产,发展到今天拥有两条“精品线材”生产线、一条高强度大盘卷棒线材生产线。
在企业发展壮大的同时,积累了丰富的生产技术经验。
以下对线材产品外部质量控制及一些措施进行论述。
2 产品外部质量要求2.1精度:直径偏差和不圆度(见附表)附表:直径偏差和不圆度2.2表面质量钢材的表面是否有不允许存在的冶金缺陷,不得有耳子、折叠、麻面、划痕、分层、裂纹、结疤等缺陷。
3 缺陷产生的原因3.1 产品尺寸精度超差3.1.1允许直径偏差超标:(1)换辊、换槽后试轧时,成品架次压下量不足(辊缝值过大)及成品前架次的辊缝值调整不当都会使直径偏差过大。
(2)钢坯加热温度不均匀,轧件温度过低(主要指头、尾部)也会时允许偏差超差。
3.1.2不圆度超差:(1)换辊、槽后试轧时,成品架辊缝设定不当及成品前来料尺寸不合适,造成成品孔槽轧件未充满。
(2)试轧时,粗、中轧机架速度不匹配,造成机架间拉钢,也会使不圆度超差。
(3)轧制过程中,成品架入口滚动导卫轮烧坏及长时间轧制后轧槽磨损。
(4)成品架次错辊。
3.2 表面质量3.2.1 耳子线材表面平行与长度方向的条状凸起,产生于一侧为单边耳子,双侧尾双边儿子,断面上、下两个半圆错开的叫错边耳子。
3.2.1.1耳子产生的根本原因有以下几点:(1)过充满:前孔来料尺寸过大,到后架轧机充满轧制而形成耳子,调整时应把我好各架轧机的充满度,正确合理的调整辊缝,对于精轧机应该合理调整首架辊缝。
浅谈高速线材厂活套原理及其故障
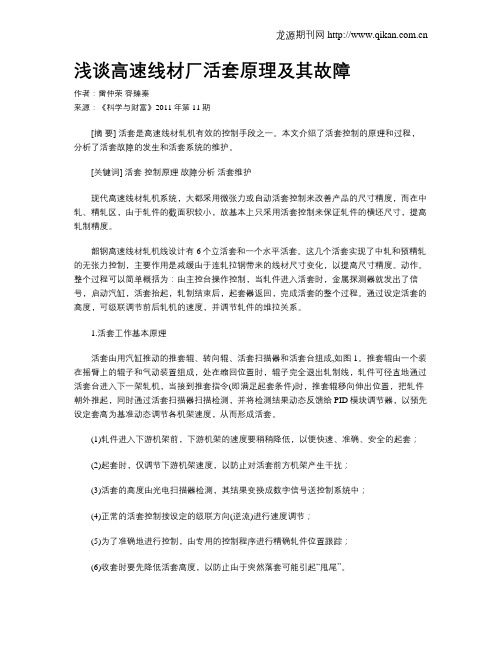
浅谈高速线材厂活套原理及其故障作者:雷仲荣容臻秦来源:《科学与财富》2011年第11期[摘要] 活套是高速线材轧机有效的控制手段之一。
本文介绍了活套控制的原理和过程,分析了活套故障的发生和活套系统的维护。
[关键词] 活套控制原理故障分析活套维护现代高速线材轧机系统,大都采用微张力或自动活套控制来改善产品的尺寸精度,而在中轧、精轧区,由于轧件的截面积较小,故基本上只采用活套控制来保证轧件的横坯尺寸,提高轧制精度。
韶钢高速线材轧机线设计有6个立活套和一个水平活套。
这几个活套实现了中轧和预精轧的无张力控制,主要作用是减缓由于连轧拉钢带来的线材尺寸变化,以提高尺寸精度。
动作。
整个过程可以简单概括为:由主控台操作控制,当轧件进入活套时,金属探测器就发出了信号,启动汽缸,活套抬起,轧制结束后,起套器返回,完成活套的整个过程。
通过设定活套的高度,可级联调节前后轧机的速度,并调节轧件的堆拉关系。
1.活套工作基本原理活套由用汽缸推动的推套辊、转向辊、活套扫描器和活套台组成,如图1。
推套辊由一个装在摇臂上的辊子和气动装置组成,处在缩回位置时,辊子完全退出轧制线,轧件可径直地通过活套台进入下一架轧机,当接到推套指令(即满足起套条件)时,推套辊移向伸出位置,把轧件朝外推起,同时通过活套扫描器扫描检测,并将检测结果动态反馈给PID模块调节器,以预先设定套高为基准动态调节各机架速度,从而形成活套。
(1)轧件进入下游机架前,下游机架的速度要稍稍降低,以便快速、准确、安全的起套;(2)起套时,仅调节下游机架速度,以防止对活套前方机架产生干扰;(3)活套的高度由光电扫描器检测,其结果变换成数字信号送控制系统中;(4)正常的活套控制按设定的级联方向(逆流)进行速度调节;(5)为了准确地进行控制,由专用的控制程序进行精确轧件位置跟踪;(6)收套时要先降低活套高度,以防止由于突然落套可能引起“甩尾”。
扫描器的检测角是固定的,其扫描范围用与活套台的距离来调节。
高速线材生产的质量控制
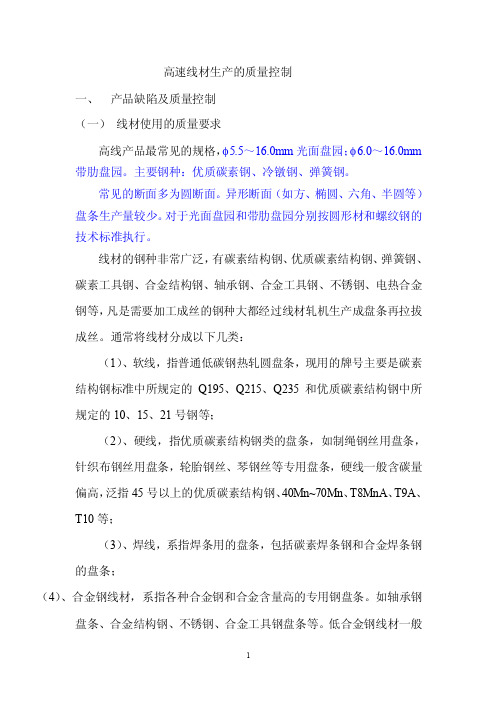
高速线材生产的质量控制一、产品缺陷及质量控制(一)线材使用的质量要求高线产品最常见的规格,φ5.5~16.0mm光面盘园;φ6.0~16.0mm 带肋盘园。
主要钢种:优质碳素钢、冷镦钢、弹簧钢。
常见的断面多为圆断面。
异形断面(如方、椭圆、六角、半圆等)盘条生产量较少。
对于光面盘园和带肋盘园分别按圆形材和螺纹钢的技术标准执行。
线材的钢种非常广泛,有碳素结构钢、优质碳素结构钢、弹簧钢、碳素工具钢、合金结构钢、轴承钢、合金工具钢、不锈钢、电热合金钢等,凡是需要加工成丝的钢种大都经过线材轧机生产成盘条再拉拔成丝。
通常将线材分成以下几类:(1)、软线,指普通低碳钢热轧圆盘条,现用的牌号主要是碳素结构钢标准中所规定的Q195、Q215、Q235和优质碳素结构钢中所规定的10、15、21号钢等;(2)、硬线,指优质碳素结构钢类的盘条,如制绳钢丝用盘条,针织布钢丝用盘条,轮胎钢丝、琴钢丝等专用盘条,硬线一般含碳量偏高,泛指45号以上的优质碳素结构钢、40Mn~70Mn、T8MnA、T9A、T10等;(3)、焊线,系指焊条用的盘条,包括碳素焊条钢和合金焊条钢的盘条;(4)、合金钢线材,系指各种合金钢和合金含量高的专用钢盘条。
如轴承钢盘条、合金结构钢、不锈钢、合金工具钢盘条等。
低合金钢线材一般划归为硬线,如有特殊性能也可划入合金钢类。
线材按用途分为两类,一类是直接使用的,多用作建筑钢筋;一类是深加工后使用的,用来拉丝成为金属制品或冷墩成螺钉、螺母等。
对线材质量要求更多的是必须满足后部工序的使用性能。
一般线材交货技术条件规定的内容有:外形及尺寸精度;表面质量及氧化铁皮;截面质量及金相组织;截面是指垂直于线材中心线的断面;化学成分及力学性能(包括深加工的工艺性能);盘重;保装及标志。
线材的用途不同其质量要求也各有侧重,如冷墩材除对力学性能有严格要求外,最主要的是要求冷墩不开裂,而要想保证不开裂就要严格控制夹杂及表面裂纹、折叠、划伤等会造成开裂的缺陷。
高速线材轧机的活套控制
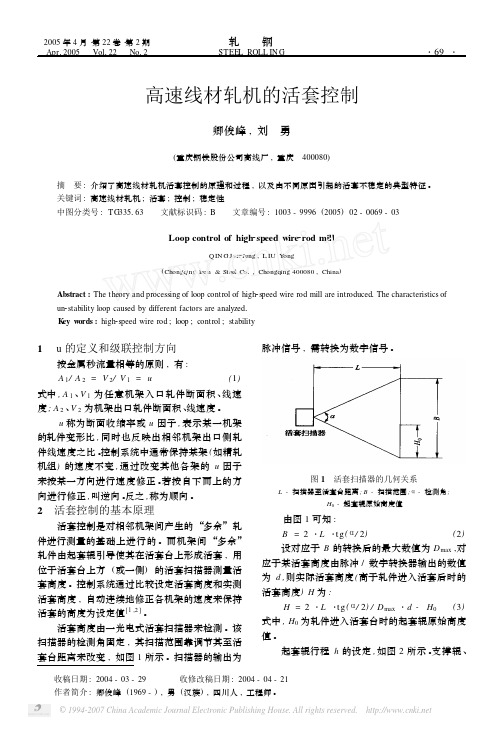
高速线材轧机的活套控制卿俊峰,刘 勇(重庆钢铁股份公司高线厂,重庆 400080)摘 要:介绍了高速线材轧机活套控制的原理和过程,以及由不同原因引起的活套不稳定的典型特征。
关键词:高速线材轧机;活套;控制;稳定性中图分类号:TG 335163 文献标识码:B 文章编号:1003-9996(2005)02-0069-03Loop control of high 2speed wire 2rod millQIN G J un 2feng ,L IU Y ong(Chongqing Iron &Steel Co 1,Chongqing 400080,China )Abstract :The theory and processing of loop control of high 2speed wire rod mill are introduced 1The characteristics of un 2stability loop caused by different factors are analyzed 1K ey w ords :high 2speed wire rod ;loop ;control ;stability收稿日期:2004-03-29 收修改稿日期:2004-04-21作者简介:卿俊峰(1969-),男(汉族),四川人,工程师。
1 u 的定义和级联控制方向按金属秒流量相等的原则,有:A 1/A 2=V 2/V 1=u(1)式中,A 1、V 1为任意机架入口轧件断面积、线速度;A 2、V 2为机架出口轧件断面积、线速度。
u 称为断面收缩率或u 因子,表示某一机架的轧件变形比,同时也反映出相邻机架出口侧轧件线速度之比。
控制系统中通常保持某架(如精轧机组)的速度不变,通过改变其他各架的u 因子来按某一方向进行速度修正。
若按自下而上的方向进行修正,叫逆向。
反之,称为顺向。
高速线材自动检测与控制安装调试工法

高速线材自动检测与控制安装调试工法中冶集团华冶资源公司天津工业设备安装分公司王文凯彭廷生杨千里薛玉龙刘艳丽1 前言近年来,随着科学技术的不断进步,国内各大钢铁公司加大对企业的技术改革,建成了一批当今世界上比较先进的新型轧机生产线,轧机采用全新的工艺布置,综合计算机管理及过程控制、网路通讯、交流变频调速等先进技术,进一步加强过程自动化控制,实现了以生产过程自动控制为主流的生产工艺。
本工法以天津钢铁有限公司全连续式140万吨/年高速线材工程自动检测与控制系统安装调试为例进行编制而成的。
2 工法特点2.1运用系统工程原理,将复杂的工程原理分解成各个层面、各个区段进行安装、调试。
将检测控制元件,进行分类、区域划分,便于设备安装和调试的实施。
2.2运用模拟手段进行系统回路的预调试,缩短了调试的绝对工期。
2.3充分利用先进的调试设备,保证了安装和调试精度。
充分利用设备和系统的自身性能,节约人力、物力。
2.4本工法适用性强,具有较强的操作性。
3 工法适用范围本工法适用于高速线材安装调试工程,同时也可以适用于轧钢棒材生产线安装调试工程。
4 工艺原理高速线材电气自动化系统配置5台SIEMENS公司的S7-400系列PLC,设有3个操作站,加热炉区、轧机区、风冷线各1个,另外还在主电室设有工程师站。
每个站均配有SIEMENS 公司的PIII工控机。
现场的润滑、液压系统以及轧线各区域配有35台ET200M,主传动采用SIEMENS公司的6RA70系列产品,交流辅传动采用SIEMENS公司的6SE70变频器,每套传动装置均配有一块CBP通信模板,用作6RA70和6SE70调速装置与PROFIBUS-DP相连的接口板。
操作站、工程师站、PLC之间的通信采用工业以太网,通信介质采用同轴电缆,PROFIBUS-DP主要完成PLC与6RA70、6SE70、WINCC以及远程ET200M之间的数据信息通信功能,PROFIBUS-DP的通信介质采用工业屏蔽双绞线。
活套在高速线材生产中的应用
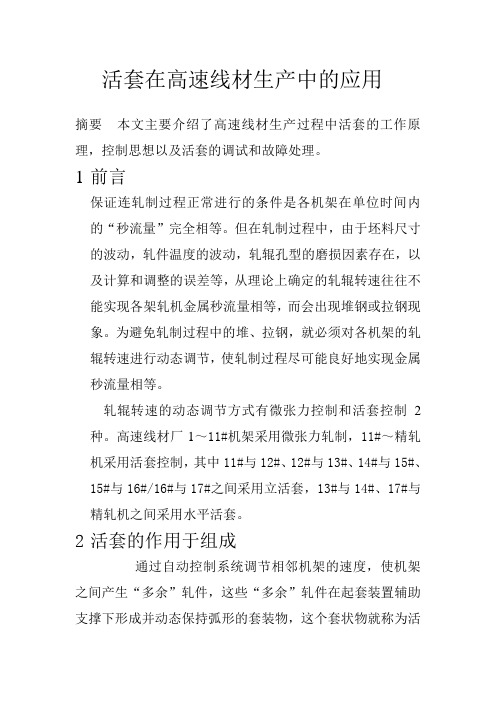
活套在高速线材生产中的应用摘要本文主要介绍了高速线材生产过程中活套的工作原理,控制思想以及活套的调试和故障处理。
1前言保证连轧制过程正常进行的条件是各机架在单位时间内的“秒流量”完全相等。
但在轧制过程中,由于坯料尺寸的波动,轧件温度的波动,轧辊孔型的磨损因素存在,以及计算和调整的误差等,从理论上确定的轧辊转速往往不能实现各架轧机金属秒流量相等,而会出现堆钢或拉钢现象。
为避免轧制过程中的堆、拉钢,就必须对各机架的轧辊转速进行动态调节,使轧制过程尽可能良好地实现金属秒流量相等。
轧辊转速的动态调节方式有微张力控制和活套控制2种。
高速线材厂1~11#机架采用微张力轧制,11#~精轧机采用活套控制,其中11#与12#、12#与13#、14#与15#、15#与16#/16#与17#之间采用立活套,13#与14#、17#与精轧机之间采用水平活套。
2活套的作用于组成通过自动控制系统调节相邻机架的速度,使机架之间产生“多余”轧件,这些“多余”轧件在起套装置辅助支撑下形成并动态保持弧形的套装物,这个套状物就称为活套。
活套可以实现无张力轧制。
所谓无张力轧制,即是在轧制过程中,机架间轧件不存在堆拉关系。
这是通过改变活套存储量来实现的,当相邻两机架间轧件受拉时,套量减小,可起缓冲作用,防止机架间产生张力,免使轧件断面拉缩,影像轧件尺寸的精度,另一方面可以吸收过量的轧件,防止堆钢事故发生。
但活套的套量调节范围是有限的,当相邻机架速度匹配过分不合理或其他原因而引起套量偏差太大。
自动控制系统将来不及或无法调节。
活套按形状可分为水平活套和立活套,水平活套主要用于机架间跨度较大的场合。
活套包括活套台、导槽、四个支撑辊、起套辊及活套扫描仪几部分。
其中支撑辊、起套辊起着轧件的导向和支撑作用。
结构简图1所示3活套控制原理活套控制是通过改变与活套有关的机架速度来实现的。
活套等于活套入口处轧件速度与出口轧件速度之差的积分,当入口速度大于出口速度时,套量就增加,反映在套高逐渐升高,反之套量就逐渐减少,套高降低,相等时套量、套高不变。
高速线材堆钢的原因及控制
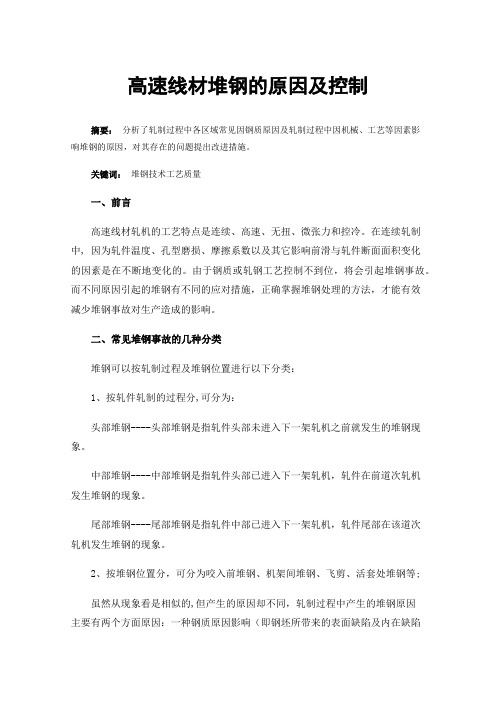
高速线材堆钢的原因及控制摘要:分析了轧制过程中各区域常见因钢质原因及轧制过程中因机械、工艺等因素影响堆钢的原因,对其存在的问题提出改进措施。
关键词:堆钢技术工艺质量一、前言高速线材轧机的工艺特点是连续、高速、无扭、微张力和控冷。
在连续轧制中, 因为轧件温度、孔型磨损、摩擦系数以及其它影响前滑与轧件断面面积变化的因素是在不断地变化的。
由于钢质或轧钢工艺控制不到位,将会引起堆钢事故。
而不同原因引起的堆钢有不同的应对措施,正确掌握堆钢处理的方法,才能有效减少堆钢事故对生产造成的影响。
二、常见堆钢事故的几种分类堆钢可以按轧制过程及堆钢位置进行以下分类:1、按轧件轧制的过程分,可分为:头部堆钢----头部堆钢是指轧件头部未进入下一架轧机之前就发生的堆钢现象。
中部堆钢----中部堆钢是指轧件头部已进入下一架轧机,轧件在前道次轧机发生堆钢的现象。
尾部堆钢----尾部堆钢是指轧件中部已进入下一架轧机,轧件尾部在该道次轧机发生堆钢的现象。
2、按堆钢位置分,可分为咬入前堆钢、机架间堆钢、飞剪、活套处堆钢等;虽然从现象看是相似的,但产生的原因却不同,轧制过程中产生的堆钢原因主要有两个方面原因:一种钢质原因影响(即钢坯所带来的表面缺陷及内在缺陷引起的),另一种为轧制原因影响(包括生产操作、料型、轧机导卫装配等影响),下面从钢质和轧制两个方面原因来进行分析说明。
三、钢质原因造成堆钢及应对措施:总体来说,炼钢钢坯原因主要有:钢坯纯净度、钢坯表面缺陷、钢坯内在缺陷、几何形状缺陷等原因。
1、连铸坯纯净度达不到要求:主要指冶炼过程中脱氧不良,钢中夹杂物的含量超标,造成组织形态和分布不合理。
夹杂物主要有非金属夹杂物,金属夹杂物,夹渣。
其中非金属夹杂和夹渣属脆性物质,轧制时,如果这两种缺陷超标准,极易造成头部开裂(劈头)顶导卫引起堆钢,极大的影响了成品材的质量。
采取措施:⑴、提高冶炼操作技术水平,严格控制钢水过氧化。
降低钢水中【O】含量,是减少钢水夹杂物产生的源头,也是提高铸坯质量的保证。
- 1、下载文档前请自行甄别文档内容的完整性,平台不提供额外的编辑、内容补充、找答案等附加服务。
- 2、"仅部分预览"的文档,不可在线预览部分如存在完整性等问题,可反馈申请退款(可完整预览的文档不适用该条件!)。
- 3、如文档侵犯您的权益,请联系客服反馈,我们会尽快为您处理(人工客服工作时间:9:00-18:30)。
高速线材厂轧钢工艺培训
活套
现代高速线材轧机为保证产品尺寸精度,采用微张力及无张力轧制,以消除轧制过程中各种动态干扰引起的张力波动和由此引起的轧件尺寸波动。
由于精轧机组为集体传动,故精轧采用微张力轧制,其微张力值由固定速比和各架给定孔槽面积保证,速比不会因控制而改变,轧件面积将因来料面积波动而波动。
为了减少张力变化引起的精轧机的轧件尺寸波动,在精轧机前的预精轧、中轧机机组常设若干个活套,以消除连轧各架的动态速度变化的干扰、保证轧件精度。
活套定义及作用
通过自动控制系统调节相邻机架的速度使机架间产生“多余”轧件,该“多余”轧件在起套装置辅助下形成且能动态保持弧形的套状物,这个套状物就称为活套。
活套控制功能适用于轧件断面小轧制速度较快的场合,能消除连轧机架的动态速度变化的干扰、保证轧件精度,活套可以实现无张力轧制。
所谓无张力轧制即是在轧制过程中,机架间轧件不存在拉钢关系,是通过改变活套存储量来实现的。
当相邻两机架间轧件受拉时,套量减小,可起缓冲作用,防止机架间产生张力,免使轧件断面拉缩,影响轧件尺寸的精度;另一方面吸收过量的轧件,防止堆钢而造成机架间的堆钢事故。
但是活套的套量调节范围及套量的存储量是有限的,当相邻机架速度匹配不合理或其它原因而使起套量偏差太大,自动控制系统来不及或无法调节,就会引起堆钢。
活套由活套台、支撑辊、导槽、起套辊及活套扫描器等组成。
支撑辊、起套辊起着对轧件的导向和支持作用。
起套辊、转向导板均由气缸驱动,起套辊气缸由双电磁阀控制。
活套种类:下活套、侧活套、立活套。
在高速线材轧机上,下活套通常用于中轧机组。
下活套的套量控制比较困难,因为下活套的光电扫描器工作环境恶劣,
难以实现自动控制。
侧活套由水平活套台、推套器及进出口导向辊组成。
推套器是由气缸操纵的导辊。
精轧机前的侧活套不能自由脱套产生,而需要有一个轧机的速度变化推套动作,扫描反馈的控制过程。
立活套是现代高速线材轧机的主要配套技术之一,用以使相邻机架间保持适当套量实现无张力轧制。
在整个轧制过程中,从轧件在下一架轧机咬入后的起套,到后尾收套都由计算机控制。
活套控制的基本原理
活套是用来检测和调整相邻机架间速度关系从而实现无张力轧制的一种手段。
活套控制是对相邻机架间金属秒流量差异进行测量的基础上进行的,金属秒流量差异导致机架间堆钢(或拉钢),轧件由起套辊引导使其形成活套。
在线活套扫描仪可实时反馈实测活套高度,控制系统将实测活套高度与设定活套高度进行比较从而产生速度修正信号,调整上游机架速度以维持活套高度(活套量)在给定值上不变,从而实现其前后机架间正确的速度配合。
当上游道次金属秒流量小于下游道次金属秒流量时,套量就渐渐减少,套高降低;金属秒流量相等时则套高不变。
活套控制就是通过改变与活套相关机架速度来实现的。
变速度差控制为套量控制(△v一△H),基本过程是头部起套一中间稳定为设定套量一尾部收套。
活套扫描器测量出套高实际值,并与套量设定值进行比较,然后根据其偏差值作为活套调节器的修正信号,调整上游机架的速度。
当由于外界条件引起活套大小改变而使活套偏离设定套位时,实际套量不等于设定套量,活套调节器便有输出,通过速度调节系改变活套上游机架速度,并逆向级联调节上游所有机架速度,这种调节会因每一条钢而有所不同,直到稳定为止。
活套的控制过程
起套
以14一15机架间立活套为例,其它活套类似。
当14 机架活套扫描
器检测到轧件头部并延时t1秒,自动控制系统送一个起套信号给电磁阀,起套延时t1秒的确定(以14 到l5 机架的距离除以14 机架出口速度得到时间,来考虑气缸动作延时)应保证轧件刚好咬入l5 机架时,起套辊刚好启动。
当起套辊启动后,活套上游的14 机架升速使14 、l5 之间生“多余”轧件以生成活套,起套过程结束后,14 机架恢复设定值。
根据电机的动态特性,当轧件刚咬入l5机架时,电机会产生一个动态速降,但是控制系统预先给l5 机架以2~4%的动态速降补偿,可以保证不会因动态速降而使刚咬入时产生太多“多余”轧件,即起始套高度为0,这一点可以从不投入活套仍能平稳咬入得到确认。
稳定调节
起套完成后,即进入活套稳定控制阶段。
根据活套扫描仪得到不断变化的套量,通过电控脉冲信号不断地传递给电控系统,系统按逆向级联控制的方向调整相邻上游14 机架的速度,这就相当于连续地修正上游相邻14机架的速度来保证活套的高度与设定值一致。
活套调节是为了补偿轧件尺寸或温度变化而引起的套量变化。
操作人员也要密切关注活套的远行情况,当活套高度超过允许最大高度或者存在严重拉钢的情况下,因超出活套自动控制调整范围,自动控制失效,应及时采取手动控制,以保证生产的安全进行。
收套阶段
当轧件尾部到13机架 (咬钢)信号,即进入收套阶段。
仍然采用一个延时t2,自动控制系统送一个落套信号给电磁阀,落套延时t2,t2的确定(以13到l4机架的距离除以13 机架出口速度得到时间t2,来考虑气缸动作延时),应保证轧件刚好出l4机架时,起套辊刚好落下。
为了安全收套并防止突然收套可能引起的甩尾,在收套阶段,要降低14 机架的速度以配合起套高度在轧件出14 机架降到0。
起套辊不能落套过早,如果落套过早会使轧件在活套台处产生堆钢或甩尾,落套也不能太迟,如果太迟,下一轧件到来之前还未完全落套就会造成冲钢。
活套套形分析
在生产过程中,活套可能形成4种套形,如图所示。
(1)第1种套形是由于活套起套高度设定过大,轧件易在下一机架前产生堆钢及甩尾现象,不易控制。
(2)第4种套形是由于活套起套高度设定过小,轧件对起套辊压力较大,易导致套辊磨损快,机械故障多;另一方面轧件未能实现机架问无张力轧制,对红坯料形控制波动大。
(3)第2种套形是活套起套高度设定恰当,活套辊工作正常,轧件能实现机架间无张力轧制,对红坯料形控制较好,但如遇起套辊收套不及时,也易造成甩尾现象。
(4)第3种套形是活套起套高度设定略小,但活套辊能正常工作,轧件也能实现机架间无张力轧制,对红坯料形控制较好,不易造成甩尾现象。
因此,可根据设备和工艺条件选择第2、第3种套形。
活套事故分析
在实际生产中发现有多种原因引起活套不稳定或堆钢。
1)活套起套辊不起套,原因可能有以下几种:
·活套扫描器有故障,不能检测;
·活套扫描器受震动,没对准检测口;
·活套扫描器镜头脏,检测不稳;
·冷却水太大或天冷雾气大,影响扫描器的检测灵敏度;
·电气线路接触不良及其它原因引起断路,起套信号送不到电磁阀;·电磁阀线包烧坏,阀不能动作;
·电磁阀阀芯堵塞,阀不能动作;
·气源未打开或气管破损;
·气缸或起套辊机械卡死。
2) 活套起套辊不落套原因可能为:
·上游机架的上游机架信号错误;
·电磁阀线包烧坏,阀不能动作;
·气缸或起套辊机械突然卡死。
3) 活套区常堆钢现象分析:
活套起套后时序紊乱,不能正常落套,下一钢坯钻人起套辊造成堆钢。
解决办法,加强现场检测元件维护,确保检测信号的准确,注意保持最佳出钢节奏。
水平活套处堆钢。
因水平活套处两相连机架间距很大,起套过早容易飞钢,过晚又易产生张力,所以要注意起落套的设置。
精轧前水平活套处常因换辊后精轧咬钢困难,加之19机架动态速降补偿时间过长而引起堆钢。
解决办法是调整19机架动态速降补偿参数,控制出钢节奏,同时要注意水平活套套台冷却及禁止碎断钢头带人套台。
4) 活套套量不稳。
一般情况下,调试好的活套都是较稳定的。
如果有不稳定现象发生不要轻易通过修改活套高度给定或升降相邻上游机架转速的方法来使活套稳定下来。
活套的稳定性与有关机架速度控制系统动态特性及粗、中轧堆拉关系,活套区工艺调整有关。
正常情况下,对于同一轧件由头部到尾部活套允许有±15mm的高度变化。
可能引起活套不稳定的几个因素:
电气原因
活套扫描器检测信号不稳,镜头脏,冷却水及雾气太大,检测口化铁皮较多,均易导致信号时有时无,影响活套控制。
机械原因
如果支撑辊、起套辊轴承烧毁,转动不灵活造成磨损不均及卡死,会引活套不稳;起套辊或支撑辊偏心引起套量波动,这种波动一般从形成活套后开始就出现波动一直延续到落套。
工艺原因
导卫安装不当或辊缝设置不当也会引起的活套不稳。
轧件温度变化导致套量波动,这种波动一般出现在轧件尾部或中部以后,操作人员应该及时通知加热炉,以保证钢温的正常。
头部起套太高。
一种可能是椭圆孔压下太多,轧件与下道圆孔型进口导轮不匹配,轧件阻力太大;另一可能性是轧件头,尾部与中部尺
偏差太大。