高速线材生产过程自动控制
浅析高速线材生产控制相关要点

浅析高速线材生产控制相关要点841300摘要:高速线材是以电弧炉冶炼的高速钢为原料,通过轧制、拉丝、退火等工序制成的各种线材。
高速线材具有高抗拉强度、高韧性、高塑性及耐高温、耐磨性好、无磁性等优点,在航空航天工业、船舶制造业、轨道交通行业都有广泛应用。
在近几年高速线材的发展趋势下,作为高速线材生产企业来说除了要面临环保的要求以外,还面临着价格竞争的压力,如何能在激烈的市场竞争中占据有力地位呢。
这就需要在许多自身进行进步。
关键词:高速线材;生产控制一、提高人员质量意识,明确质量控制职责质量是企业的生命线,如果质量管理工作不到位,就会出现一系列的企业危机,因此要想生产出优质的高速线材产品,提高人员质量意识是一个非常重要的环节。
首先车间管理人员要了解各工序的生产流程与基本操作技术、相关岗位的职责以及各种特殊工作标准。
明确各个岗位之间产品质量的控制职责。
根据生产、检验计划对每一道工序完成后都要认真做好抽检工作。
生产部门应按照工艺要求做好成品的表面缺陷分析,如轧制过程产生表面缺陷则及时处理。
检验部门应认真做好检验记录检查。
车间与质检部门根据职责分工对所有需要审核的产品进行严格评审,并跟踪审核整改效果。
二、强化设备管理工作设备是企业的核心竞争力,也是企业盈利的主要手段。
设备的安全、稳定、高效运行有利于保证企业正常生产经营运作。
要根据本企业生产经营的特点和现状制定切实可行的方针和措施。
对目前处于淘汰期的老设备要加强维修保养和清理;要对新购置的设备进行技术鉴定,建立完善和稳定先进的档案;要严格落实有关设备日常维修保养制度,确保不发生影响设备正常运转、影响企业正常生产经营秩序行为事故。
设备管理人员要做好设备定期检查工作和维修保养工作。
严格执行设备维护保养规程,保证良好性能;加强对设备电气及机械附件等关键部位的日常检查维修,确保有效运行;要加强对关键部位设备设施运行状态、维修方案等设备运行状况的检查维修力度,确保设备完好率达到98%以上。
高速线材生产的质量控制
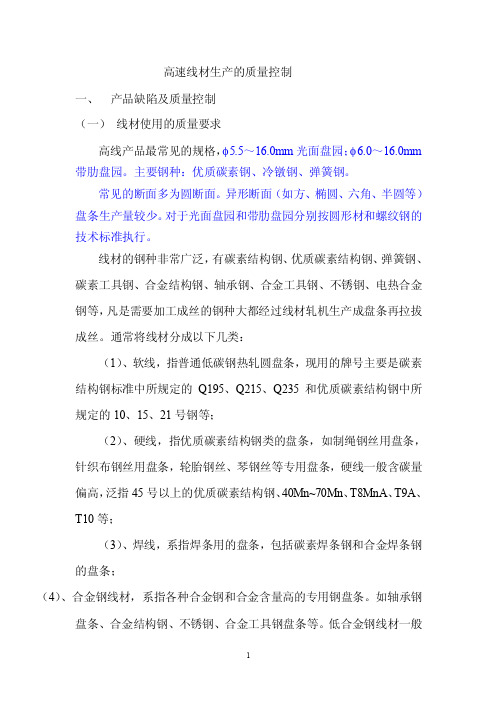
高速线材生产的质量控制一、产品缺陷及质量控制(一)线材使用的质量要求高线产品最常见的规格,φ5.5~16.0mm光面盘园;φ6.0~16.0mm 带肋盘园。
主要钢种:优质碳素钢、冷镦钢、弹簧钢。
常见的断面多为圆断面。
异形断面(如方、椭圆、六角、半圆等)盘条生产量较少。
对于光面盘园和带肋盘园分别按圆形材和螺纹钢的技术标准执行。
线材的钢种非常广泛,有碳素结构钢、优质碳素结构钢、弹簧钢、碳素工具钢、合金结构钢、轴承钢、合金工具钢、不锈钢、电热合金钢等,凡是需要加工成丝的钢种大都经过线材轧机生产成盘条再拉拔成丝。
通常将线材分成以下几类:(1)、软线,指普通低碳钢热轧圆盘条,现用的牌号主要是碳素结构钢标准中所规定的Q195、Q215、Q235和优质碳素结构钢中所规定的10、15、21号钢等;(2)、硬线,指优质碳素结构钢类的盘条,如制绳钢丝用盘条,针织布钢丝用盘条,轮胎钢丝、琴钢丝等专用盘条,硬线一般含碳量偏高,泛指45号以上的优质碳素结构钢、40Mn~70Mn、T8MnA、T9A、T10等;(3)、焊线,系指焊条用的盘条,包括碳素焊条钢和合金焊条钢的盘条;(4)、合金钢线材,系指各种合金钢和合金含量高的专用钢盘条。
如轴承钢盘条、合金结构钢、不锈钢、合金工具钢盘条等。
低合金钢线材一般划归为硬线,如有特殊性能也可划入合金钢类。
线材按用途分为两类,一类是直接使用的,多用作建筑钢筋;一类是深加工后使用的,用来拉丝成为金属制品或冷墩成螺钉、螺母等。
对线材质量要求更多的是必须满足后部工序的使用性能。
一般线材交货技术条件规定的内容有:外形及尺寸精度;表面质量及氧化铁皮;截面质量及金相组织;截面是指垂直于线材中心线的断面;化学成分及力学性能(包括深加工的工艺性能);盘重;保装及标志。
线材的用途不同其质量要求也各有侧重,如冷墩材除对力学性能有严格要求外,最主要的是要求冷墩不开裂,而要想保证不开裂就要严格控制夹杂及表面裂纹、折叠、划伤等会造成开裂的缺陷。
高速线材生产自动化控制的改进与提高

1前言随着PLC的广泛应用,集散型分布式PLC控制的开发和应用,提供了先进有力的控制工具和手段。
应用PLC进行生产过程控制的热潮早在80年代初就已兴起,开始应用之初一般都是仅限于某个局部生产过程,如加热炉的自动燃烧控制等。
后来逐渐发展到大规模引进生产线,在整个工厂、整条生产线全面应用PLC进行全线自动化生产,极大的提高了生产效率和经济效益,大规模集散型PLC控制系统已经在冶金行业广泛使用。
2生产现状和改进措施2.1生产现状我厂早在1987年就引进了美国GE公司的系列六PLC控制系统,用于整个线材生产线的自动化控制,并于1989年热负荷试车成功投入生产,至今已有十几年了。
在这期间,2000年我厂又对整个轧线电气控制系统进行了更新换代改造,PLC 控制系统用GE90-70替代,传动控制系统全部改成数字控制,我们在对该系统运行、维护、检修、改进和完善的过程中,对于提高系统的可靠性、适应性和长期无故障运行的稳定性与提高自动化生产率的关系等方面有了较深的体会和认识,即:一条轧钢自动化生产线效率的高低主要由轧钢工艺水平和自动化水平的高低所决定,而衡量自动化生产水平高低的一个主要指标就是自动化生产作业率,但自动化生产作业率的高低主要取决于构成轧钢自动化生产线的自动化系统的可靠性、适应性和稳定性。
自动化系统的可靠性、适应性和稳定性主要依赖于控制系统内各部分设备器件的可靠性、适应性和稳定性(如控制器、执行器、检测元件……)。
对于轧钢生产线,现场环境较为恶劣,高温、潮湿、粉尘、振动、撞击随时存在。
现场安装的许多检测元件、控制设备经常被损坏,从而造成停机,生产作业率降低,备件消耗增大。
针对这种情况,我们在系统运行、维护、检修的过程中,对其控制系统、控制设备及检测元件都进行了改进与完善,以在控制技术上提高系统的可靠性、适应性和长期无故障运行的稳定性。
2.2改进措施增设以软代硬的智能控制功能。
在广泛应用PLC的今天,采用PLC来取代原来的控制器,就是利用了PLC本身的可靠性、适应性和稳定性,通过在PLC程序实现连锁,取代原接触器及机械连锁。
高速线材生产的质量控制
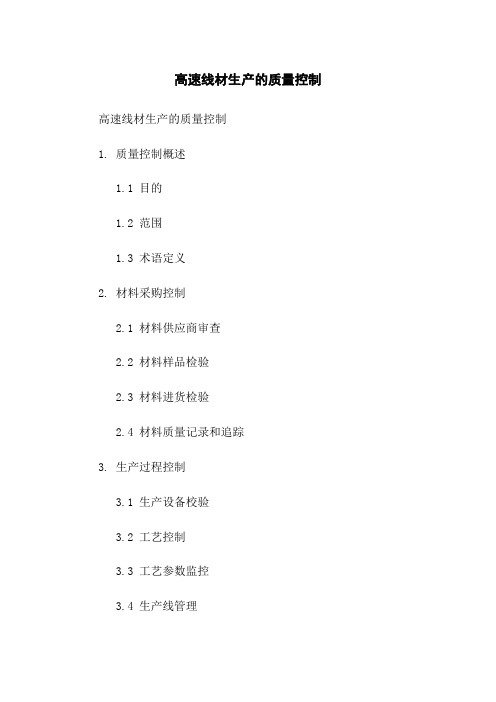
高速线材生产的质量控制高速线材生产的质量控制1. 质量控制概述1.1 目的1.2 范围1.3 术语定义2. 材料采购控制2.1 材料供应商审查2.2 材料样品检验2.3 材料进货检验2.4 材料质量记录和追踪3. 生产过程控制3.1 生产设备校验3.2 工艺控制3.3 工艺参数监控3.4 生产线管理3.5 产品质量抽样检验3.6 不良品处理和追踪4. 检测与检验控制4.1 检测设备校验4.2 产品尺寸检验4.3 产品物理性能检验 4.4 化学成分分析检验 4.5 表面质量检验4.6 异物检查4.7 环境条件监测5. 过程统计与分析5.1 数据采集与记录5.2 过程能力分析5.3 不合格品统计和分析5.4 异常处理和持续改进6. 质量审核与培训6.1 内部质量体系审核6.2 外部质量体系审核6.3 培训计划和实施7. 废品管理7.1 废品分类标识与分析7.2 废品处理与回收措施7.3 废品记录与归档8. 文件与记录管理8.1 文件编制与更新8.2 记录管理要求8.3 文件与记录保管附件:附件1:材料供应商审查表附件2:材料样品检验报告附件3:进货检验记录表附件4:生产设备校验报告附件5:产品质量抽样检验报告附件6:不良品处理记录表附件7:检测设备校验报告附件8:产品尺寸检验记录表附件9:产品物理性能检验报告附件10:化学成分分析检验报告附件11:表面质量检验记录表附件12:异物检查记录表附件13:环境条件监测记录表附件14:过程统计与分析报告附件15:不合格品统计记录表附件16:异常处理记录表附件17:质量体系审核报告附件18:培训计划与记录附件19:废品处理记录表附件20:文件与记录保管清单法律名词及注释:1. 质量控制:指采取一系列预防和控制措施,以确保产品或服务符合规定的质量标准和要求的管理活动。
2. 材料供应商审查:对潜在的材料供应商进行评估和筛选,以确保其能够提供符合要求的材料。
3. 产品质量抽样检验:通过随机抽样的方式,对生产过程中的产品进行检验,以验证产品是否符合质量标准。
高速线材生产的质量控制

高速线材生产的质量控制高速线材生产的质量控制引言高速线材是一种用于传输信号和电力的关键组件,广泛应用于电子、通信、汽车、航空航天等领域。
为了确保高速线材的质量,有效的质量控制措施是必不可少的。
本文将介绍高速线材生产中的一些质量控制方法和措施。
原材料选择和检测原材料选择在高速线材生产的质量控制中,选择合适的原材料是至关重要的。
,应根据产品的设计要求和功能需求,选择合适的导体材料、绝缘材料和包覆材料等。
,还要考虑原材料的性能稳定性、耐热性和机械强度等方面的要求。
只有选择优质的原材料,才能保证高速线材的质量。
原材料检测为了确保所选原材料符合要求,需要进行原材料的质量检测。
常用的检测方法包括外观检查、化学成分分析、物理性能等。
外观检查主要是检查原材料的外观是否存在裂纹、气泡和杂质等问题。
化学成分分析可以通过光谱分析等方法,确定原材料的化学成分是否符合标准要求。
而物理性能则包括导电性能、绝缘性能和机械性能等方面的。
生产工艺控制合理的生产工艺流程确定合理的生产工艺流程是高速线材生产质量控制的关键之一。
在工艺流程设计上,应考虑到产品的特点和生产工艺的可行性,确保每个工艺环节的顺序、持续时间和工艺参数的合理性。
,还需要制定相应的工艺标准,规范每个环节的操作流程。
严格的生产操作规范在高速线材生产的每个环节,都需要有严格的生产操作规范。
这包括原材料的搬运和储存、加工工艺的操作、设备的维护保养等。
通过严格的操作规范,避免因人为因素引起的质量问题。
在线检测和监控高速线材生产过程中,应采用在线检测和监控手段,及时发现和纠正潜在问题,确保产品质量。
常用的在线检测手段包括电性能、绝缘性能、外观检查等。
通过这些检测手段,可以及时发现产品的品质问题,并做出相应调整和改进。
成品检测和检验成品检测高速线材生产完成后,还需要进行成品检测。
成品检测的内容包括外观检查、电性能、绝缘性能和机械性能等。
通过这些检测手段,可以评估产品的质量,并判断是否符合设计要求和标准规范。
第10章-高速线材生产过程自动控制
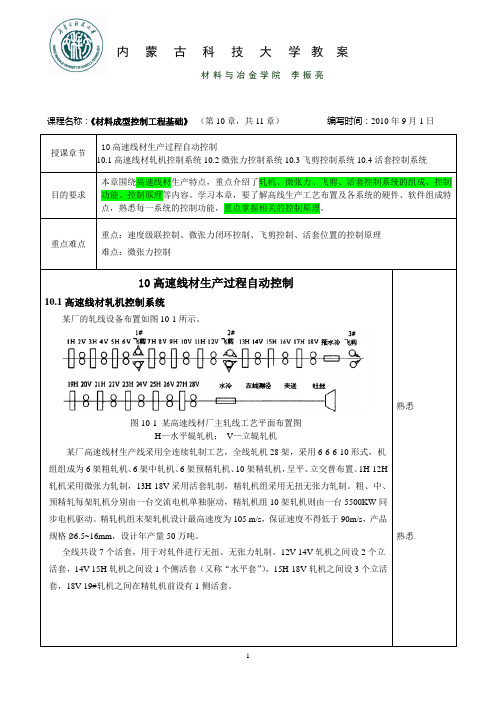
10.3.3.2 飞剪定位速度 V2 算法原理
定位速度 V2 由一速度常数乘以一个可变系数 K3 所得。 V2= K3× V3 式中, V3 为一常数,以此作为定位速度基准值。 飞剪定位时各区域示意图见图 10-8 所示。 (10-22) 熟悉
图 10-8 飞剪定位区域示意图 A-减速区;B-停车区;C-反爬区;D-过反爬区
目的要求
重点难点
10 高速线材生产过程自动控制
10.1 高速线材轧机控制系统
某厂的轧线设备布置如图 10-1 所示。机; V—立辊轧机 某厂高速线材生产线采用全连续轧制工艺,全线轧机 28 架,采用 6-6-6-10 形式,机 组组成为 6 架粗轧机、 6 架中轧机、 6 架预精轧机、 10 架精轧机, 呈平、 立交替布置。 1H-12H 轧机采用微张力轧制,13H-18V 采用活套轧制,精轧机组采用无扭无张力轧制。粗、中、 预精轧每架轧机分别由一台交流电机单独驱动,精轧机组 10 架轧机则由一台 5500KW 同 步电机驱动。精轧机组末架轧机设计最高速度为 105 m/s,保证速度不得低于 90m/s,产品 规格 Ø6.5~16mm,设计年产量 50 万吨。 全线共设 7 个活套,用于对轧件进行无扭、无张力轧制。12V-14V 轧机之间设 2 个立 活套,14V-15H 轧机之间设 1 个侧活套(又称“水平套” ) ,15H-18V 轧机之间设 3 个立活 套,18V-19#轧机之间在精轧机前设有 1 侧活套。 熟悉
了解
图 10-5 起停式飞剪 GE90-30 PLC 控制系统原理图 10.3.2 飞剪动作执行过程
了解
图 10-7 剪切动作执行过程示意图
3
内
10.3.3 飞剪控制原理
蒙
古
高速线材生产的质量控制

高速线材生产的质量控制一、引言本文档旨在介绍高速线材生产的质量控制措施,以确保生产出符合质量标准的高速线材产品。
本文档将详细介绍高速线材生产的各个环节及相应的质量控制措施。
二、原材料采购⑴供应商选择根据产品质量要求,选择符合规范的供应商,建立合作关系。
⑵原材料质量检验对每批次的原材料进行质量检验,包括外观、尺寸、化学成分等方面的检测,确保原材料符合要求。
三、线材生产⑴压延过程控制控制压延机的工作参数,包括温度、压力、速度等,以确保线材的尺寸和表面质量满足要求。
⑵拉拔过程控制控制拉拔机的拉拔比例、速度等参数,以获得所需的线材尺寸和性能。
⑶表面处理对线材进行酸洗、除氧等表面处理工艺,提高线材的质量和表面光洁度。
⑷包装和存储对线材进行适当的包装和存储,防止线材在运输和储存过程中受到损坏。
四、质量检验和测试⑴外观检查对线材的外观进行检查,包括表面光洁度、表面缺陷、尺寸偏差等方面的检验。
⑵物理性能测试对线材进行物理性能测试,包括拉伸强度、延伸率、硬度等方面的测定。
⑶化学成分分析对线材进行化学成分分析,确保符合要求的化学成分范围。
⑷尺寸测量对线材的尺寸进行测量,确保线材尺寸符合要求。
⑸试样保留对每批次的线材留取试样,作为后续质量追溯和纠正措施的依据。
五、质量控制记录记录线材生产过程的各个环节的质量检验和测试结果,保存相关记录表格和报告。
六、质量改进措施针对生产过程中出现的问题和不符合要求的情况,提出相应的质量改进措施,并进行记录和跟踪。
附件:⒈供应商选择标准⒉原材料质量检验记录表⒊线材生产工艺参数记录表⒋外观检查记录表⒌物理性能测试记录表⒍化学成分分析报告⒎尺寸测量报告注释:⒈高速线材●指用于电力传输、汽车制造等领域的高速导电线材。
⒉生产控制●确保生产过程中各个环节和产品质量符合标准要求的管理措施。
⒊质量改进●针对质量问题和不符合要求的情况,采取相应的措施以提高产品质量。
高速无扭轧机产线材(盘条)的自动化技术与智能化控制系统

高速无扭轧机产线材(盘条)的自动化技术与智能化控制系统随着工业技术的发展,无扭轧机产线材(盘条)越来越广泛地应用于钢铁行业。
无扭轧机产线材指的是通过无扭的轧制方法,将钢坯加热至一定温度后,在高速下通过轧机对钢坯进行轧制,最终获得具有不同尺寸和形状的线材或盘条。
而为了提高生产效率和质量,自动化技术和智能化控制系统成为无扭轧机产线材中必不可少的要素。
一、自动化技术在高速无扭轧机产线材中的应用1. 自动化上料系统:高速无扭轧机产线材首先需要将钢坯送入轧机进行加工。
传统的上料方式需要人工操作,效率低且易出现工作安全问题。
而采用自动化上料系统可以实现钢坯的自动化输送,不仅提高了生产效率,还增强了操作的安全性。
2. 自动化控制系统:在高速无扭轧机产线材的运行过程中,涉及到许多参数的控制,如轧机的速度、温度和轧件的尺寸等。
传统的控制方式需要人工调整,存在误差较大的问题。
而采用自动化控制系统可以实时监测并调整这些参数,使得整个产线运行更加稳定和准确。
3. 自动化质检系统:高速无扭轧机产线材在生产过程中需要对轧件的尺寸、表面质量等进行质检。
传统的质检方式需要依靠人工操作,容易出现漏检和误判的情况。
而通过在产线上引入自动化质检系统,可以实现对轧件的自动检测和分类,减少了人工干预的错误可能性,提高了质检效率和准确性。
4. 自动化出料系统:完成轧制后的线材或盘条需要通过自动化出料系统进行分条、缓冷和包装等工序。
传统的出料方式需要人工操作,容易出现错误和安全问题。
引入自动化出料系统可以实现线材或盘条的自动处理和分类,减少了人工干预的错误,提高了出料效率和准确性。
二、智能化控制系统在高速无扭轧机产线材中的应用1. 数据采集与分析:高速无扭轧机产线材中的各个环节都会产生大量的数据,如温度、压力、速度等。
通过智能化控制系统可以实现对这些数据的采集和分析,提供基于数据的决策支持,及时发现并解决潜在的问题,优化生产过程,提高生产效率和质量。
- 1、下载文档前请自行甄别文档内容的完整性,平台不提供额外的编辑、内容补充、找答案等附加服务。
- 2、"仅部分预览"的文档,不可在线预览部分如存在完整性等问题,可反馈申请退款(可完整预览的文档不适用该条件!)。
- 3、如文档侵犯您的权益,请联系客服反馈,我们会尽快为您处理(人工客服工作时间:9:00-18:30)。
图 7-1 某钢铁有限公司工艺流程框图
7.2 高速线材轧机的自动控制系统
为实现对现代化高速线材轧机生产工艺的各种控制功能,需采用计算机系统 进行自动化控制。用于高速线材生产的自动控制系统应具备以下功能: 1) 人-机通讯系统:操作人员通过计算机操作站可以和轧机控制系统进行对话, 能够灵活地进行轧机排列选择、各种参数设定、过程显示和过程监视等; 2) 速度设定:轧机主辅调速电机的速度既可以单独手动设定,也可以通过程序 进行行动设定。通常,每个产品规格对应一个轧制程序,每架被选择轧机的一些 参数(如:传动速比、延伸系数、产品尺寸、轧件平均高度、辊缝值、终轧速度 等)事先编制在程序中,自动设定时,只需重新设定每架轧机更换后的轧辊辊环 直径,由计算机按照秒流量相等原则设定每架轧机速度。设定的速度可以用手动 设定装置进行修正; 3) 微张力控制:在粗轧机组和中轧机组各轧机之间,采用轧件微张力控制保证 连轧关系和轧件断面尺寸。通常,采用主传动电机电枢电流比较法进行微张力控 制轧制,当轧件进入下一架轧机之前,轧机相当于无张力轧制(忽略后张力的影 响),控制系统检测和记忆此时的电枢电流;并在轧件进入下一架轧机之后,再 测量控制轧机传动电机的电枢电流,与无张力时的电机电流值进行比较,其差值 实际上反映了轧件拉力和推力对传动电机的作用。通过调节上游轧机主传动电机 速度,直到电流差值达到允许范围为止。通常,轧件中的张力控制在 5N/mm2 以 下; 4) 自动活套控制:为了保证产品尺寸精度,在中轧机组与预精轧机组之间、预 精轧机组与精轧机组之间以及预精轧机各机架之间设有水平活套或垂直活套,通 过控制活套高度来实现无张力轧制。每个活套处设一个活套高度检测器,用于检 测实际的活套高度,并与活套高度设定值进行比较,当实际活套高度大于设定值 时,上游(或下游)轧机全部降速(或升速);当实际活套高度小于设定值时, 上游各轧机升速(或减速),直到活套高度回到设定范围内为止。为了防止轧件 甩尾产生事故,轧件尾部到达活套之前时,活套前轧机降速,使活套高度降低; 5) 速度级控制:在轧制过程中,当控制系统(如微张力控制、活套控制、手动 机架间控制等)发出某一架轧机调速信号时,为了保证全轧线连轧关系,调速机 架前(或后)轧机也必须按原有的速度比例关系随调整速度的轧机一起升速或降
速。速度级联控制就是根据系统发出的调速信号完成这种速度控制的,其按照级 联流程方向逐架调整轧机速度。轧机速度控制有逆调和顺调之分,以某一轧机主 电机速度为基准,调节上游各架轧机速度,这种控制为逆调;顺调则以某一架轧 机速度为基准,调节下游各架轧机的速度。由于顺调时经常要改变精轧机组、夹 送辊和吐丝机等高速运转的设备速度,这对速度控制不利,而以精轧机为基准的 逆调可使高速设备基本上以比较恒定的速度运行,有利于吐丝速度控制,可形成 均匀一致的线圈。因此,单线轧制时,通常采用逆调,对于双线或多线轧制,通 常以中轧机最后一架轧机的速度为基准,粗、中轧机速度采用逆调,预精轧和精 轧机速度采用顺调; 6) 手动机架间控制:根据生产实际情况,操作人员可进行手动速度修正,消除 万一出现的堆、拉钢事故; 7) 低速运行:在试生产期间或排除故障时,各轧机可以以正常设定轧制速度为 10%的速度运行; 8) 点动爬行:各轧机可以单独手动操作,使轧机以电机基速的 10%的“点动速 度”向前或向后运行,以便于事故处理和设备检修。精轧机组一般只考虑反转点 动; 9) 轧机起/停控制:当轧线生产所需的冷却水系统、压缩空气系统、润滑和液压 系统均已起动,并运转正常时,各架轧机可在主控台起动,即在无负荷状态下加 速到设定速度。各轧机可单独起到和制动,也可成组起动和制动(按粗、中、预 精轧和精轧各组); 10) 粗、中轧机准确停车控制,为了便于轧辊更换操作,要求轧机每次停车后, 轧机的传动万向接手扁头停在垂直位置。为此,在万向拉轴圆周上的给定点装设 一个接近开关,每当轧机停车时,先由正常速度制动至以基速的 10% (或更低) 的 速度运行,然后在接近开关控制下,轧机制动,使轧机的万向接轴扁头停在垂直 位置。这样,更换轧时,由于新轧辊事先在轧辊间装配时已经使轧辊扁头处于垂 直位置,新轧辊放置在换辊小车或机架上后,通过机架移动可使轧辊扁头正好套 入接轴套筒内,从而缩短换辊时间; 11) 轧件跟踪和事故处理。通过布置在轧线上的热金属检测器、活套高度检测器 以及轧机咬钢和抛钢时的电机负荷突变来检测轧件的头、尾位置、轧制中如果按
7.3.2 COROS LS-B 人机接口计算机操作监控系统 COROS 人机接口监控操作系统,主要包括三台计算机。其主要功能如下: 1) 能贮存 250 个轧制程序,200 个冷却程序。主控台操作员可根据所要轧的钢 种和规格。可分别调用不同轧制程序和冷却程序,键入相应可变工艺参数如辊径 等。就可立即投入使用。系统可自动检测操作员设定的数据及所编轧制程序的准 确性; 2) 操作员可根据需要,调用多组不同画面。如初中轧轧制画面、活套画面、小 张力画面、主传动电机电流画面、水箱控制、飞剪画面、轧辊辊径、设定速度修 改画面。三台计算机画面彼此可任意切换并且互为备用; 3) 故障报警信息显示和存贮。方便操作人员及时掌握设备运行动态数据情况和 最新的报警信息; 4) 交直流主付传动柜进线开关、润滑、液压站泵的启动与停止,均可通过画面 自由控制,操作控制方便灵活。
7.3.5 全数字直流传动调速控制装置 西门子公司 6RA24 ATIC S5-155U 可编程序控制器属于多外理器控制器,适用于中等及高 性能的控制任务。它们为所有控制任务提供简单、经济的解决手段。标准化的硬 件、模块化的设计和高性能的编程器有机结合,使得整个系统具备众多良好的性 能。 1) 简单的安装和方便的连接,用户使用非常容易;
2) 可使用不同电压等级的输入输出模板,并且存贮器具备内存模块化和扩展化 功能,系统适应性较强; 3) 智能输出模板完成专业特定复杂任务。减轻中央处理器的负担,同时节约编 程人员大量开发时间; 4) 同一框架最多可用4个中央处理器(CPU)复杂的自动化任务可被分解为可管 理的几个部分。每个处理器独立于其它处理器执行自己的程序,相互间可及时交 换数据,从而有效提高了 PLC 整体处理速度; 5) 编程语言采用 STEP5 语言,包括控制系统流程图(CSF)、梯形图(LAD)语句表 STL)和更高的层次的 GRAPH5 适合不同爱好风格的编程人员随意使用。
7.3 高线轧机自动化控制系统
某高速线材自动化控制系统主要包括:COROS 人机接口计算机监控系统, SIMATIC S5-155U PLC 系统, 全数字交直流传动调速系统。
7.3.1 SIMATIC S5-155U PLC
SIMATIC S5-155U PLC 为德国西门子公司 PLC 系列产品之一。CPU 选用较为 先进的 948,运算速度较快,适合大型钢厂自动化控制所需。
高线也得到了同样的应用。不同区域内现场输入/输出信号分别就近连接到现场 网络各个站点上,网络站点通过接口模块和通讯电缆直接同主控室内主 PLC 控制 器相连,从而构成整个分布式控制系统。
分布式控制系统可分为以下三个部分: 1) SINEC L2-DP 现场总线。每条网络线可最多连接 64 个节点,对不同传输速率 规定最大的电缆允许长度; 2) 总线连接器; 3) 中继器,包括网络放大器、转换器等。
7.3.3 SINEC H1 网络 PLC 之间数据通讯及 PLC 同上位 COROS 计算机之间的数据通讯,则通过 SNEC H1 网络实现。H1 网络属于工业以太网结构,同轴电缆传输方式,传输速率为 10Mbit/S。
7.3.4 ET200 分布式输入输出系统 为节约控制电缆费用,现代控制系统中普遍采用现场网络总线系统,在润忠
正常速度轧件头部在预定时间内没有到达预定地点,表明已出现卡钢事故,则立 即发生事故报警信号。轧线上还没有一些检测事故的热金属检测器和开关。在控 制系统发出事故报警信号后,事故区上游轧线上的事故卡断剪、飞剪和碎断剪等 自动动作,进行事故处理; 12) 飞剪剪切控制。完成各种飞剪的自动切头、切尾和事故剪切控制以及各种参 数的设定(包括剪切速度、速度超前量、切头和切尾长度等)。飞剪既可手动操 作,也可自动控制,在自动过程中,操作人员可根据实际生产情况,随时进行手 动操作。为了防止轧件弯曲,切头时剪刃与轧件接触后的剪切速度的水平分速度 必须秒微稍大于轧件速度;切尾时剪切速度比轧件速度低 0~3% 。为了保证剪切 精度,起/停式控制的飞剪必须有剪刃定位装置, 使剪刃在每次剪切后自动回复 到起动位置; 13) 其它控制。完成步进式加热炉、控制冷却线和盘卷处理线程序控制、辅助设 备控制、润滑和液压系统联锁和顺序控制以及故障记录和报警等。还应适应优化 控制和自诊断功能,以便使控制参数不断被修改,达到最佳化; 14) 生产报告。包括道次报告、班报告、事故延误报告等。
7 高速线材生产过程自动控制
7.1 高速线材生产线简介
以下以沙钢润忠生产线介绍生产工艺流程。 新型摩根轧机采用全线无扭单线连续轧制,高架式布置,设计速度 132m/s, 最 小辊径时保证速度 105m/s, 最大轧制速度 120m/s, 最多轧制 26 道次。坯料尺寸 140mm×140mm×16000mm,成品线材φ5.5~20mm, 螺纹钢盘条φ6~16mm, 最大盘 重达 2.4t,设计年产量 63 万吨,生产钢种有碳结、优质碳结、低合金、弹簧、 焊条和冷镦钢。目前硬线生产占有较大的比例。 连铸坯从连铸机收集台架经辊道和提升装置输送至高架平台,再经装炉辊道 由侧面装入步进式加热炉,完成热装过程。沿线设热坯缓冲台架、冷坯上料台架 (也可冷装)和钢坯称重装置。 钢坯从炉内出炉辊道侧向出料,由拉钢机夹送喂入第一架粗轧机,机前设拉 断剪和高压水除鳞装置。高压水压力 20MPa, 钢坯边轧边除鳞。拉断剪在事故时 卡断钢坯,余段送回炉内保温。 粗、中轧机各 6 架,平立布置,立式轧机采用上传动,1-3 机架为 550 轧机, 4-6 机架为 450 轧机,7-12 机架为 400 轧机, 均匀双支点两辊机, 单独传动。闭 口式钢坯切割牌坊,焊接机架、液压轧辊平衡,液压马达空载压下调整,液压横 移整机座或辊系更换孔型或轧辊。 6 机架后设 1 号起停式曲柄回转飞剪,切头尾和切废,最大剪切断面 3121mm2。 12 机架后设 2 号起停式回转飞剪, 两对刀刃, 切头与切废, 剪切断面 894mm2。 从中轧 10 机架开始到精轧机组 17 机架前均设活套,预精轧机和精轧机组前 为侧活套,其余为立活套,以实现无张力轧制,确保进精轧机的轧件精度。 悬臂式 285mm 预精轧机组共四架, 平立布置, 立式轧机采用下传动, 辊箱与 伞齿轮减速箱合成一体, 提高了主电机标高;带偏心调正的两根轧辊轴装在可单 独装拆的抽屉式小辊箱内, 检修时便于快速更换。预精轧机组前设卡断剪。 轧件出预精轧机组,经 3 号飞剪、侧活套入精轧机组。3 号起停式回转型切 头分段剪, 两组刃, 切头尾和分段, 分段后经碎断剪碎断, 剪切断面 484mm2。精