高速线材轧机间活套知识
高速线材活套调整故障原因及解决方法

高速线材活套调整故障原因及解决方法摘要:目前,大部分生产高速线材的企业引入了无张力轧制技术,通过活套控制方式提高生产效率,在利用轧机开展生产作业时,出于使红钢秒流量得到科学调节的考虑,有关人员往往会选择通过活套调整的方式,对轧机速度加以控制,但是,制约活套调整质效的问题较多,如何使常见故障得到有效解决,成为人们关注的焦点。
关键词:活套调整;高速线材;故障解决策略引言活套是一种安装在高速线材轧机组中的叠层和预层压相邻机架之间的装置,用于调节金属流量平衡,确保连续层压过程中钢料间的张力稳定,消除机架之间的张力波动,五代摩根高速线材生产线,为了保持机架间每秒金属流量相等,需要在机架间采用微张力轧制技术,采用无张力轧制技术在预精轧制和中厚板轧制之间保证材料外观质量很重要。
1活套系统介绍1.1系统构成活套装置被视为检测、调节无张力轧机的核心设备,目前,在相关领域得到广泛运用的活套装备,主要由以下构件组成:气动控制设备、起套辊及检测仪。
研究表明,该装置被赋予的价值如下:若机架所对应含钢转矩、电流与设定值持平,通过启动活套装置的方式,经由气缸为活套辊提供推动力,确保红钢位置出现明显更改,弧形随之形成。
随后,由检测仪负责对红钢位置进行检测,将检测所得数据转变成模拟信号输入到PLC,待PLC对所输入信号进行判读后,方可经由调整电机转速的方式,优化弧形表现出的稳定性,真正做到流量平衡,至此,对轧机运行进行自动控制的操作告一段落。
上述环节中,最应当引起重视的构件为起套辊,负责推动起套辊的构件为气缸,轧线红钢的作用是调整起套辊高度,确保其效能得到充分发挥。
经过多次调整的起套辊,所依托动力元件为活套轮,电磁阀的存在使气缸远程控制成为可能,另外,从某个角度来说,升降起套辊的时间,往往会给轧件质量带来直接影响,这点应尤为重视。
1.2活套装置的升降控制起套辊的升降按照PLC逻辑条件进行控制。
在活套装置主控选用的情况下,在其前后轧机均含钢(转矩电流达到要求值)时,PLC输出控制七点电磁阀动作,气缸升起,起套辊动作。
高线生产简介

高速线材生产设备
二、轧机
高线厂15#~28#均为旋臂式轧机,15#~18#轧机布置 形式为平立交替式,传动方式为单独传动。19#~28#布置形 式为顶角45度,传动方式为集体传动。各架次轧机规格如下:
架次 规格 15#~18# φ285 19#~23# φ228 24#~28# φ170
(3)加热质量好。完全消除了粘钢、翻炉的限制,很大程度上消除了 钢坯黑印,坯料下表面也不会造成划伤
(4)能耗低。由于采用蓄热式,废气排放时经过蓄热式,蓄热体将高 温废气的热量留下给换向后的空气和煤气预热,大大降低了能耗损失。
高速线材生产设备
一、加热炉
高速线材生产设备
二、轧机
高线厂1#~14#均为短应线轧机,轧机布置形式为平立 交替式。短应力线轧机和闭口式轧机相比具有投资少,刚度 大、更换方便的特点。各架次轧机规格如下:
(1)尽量实现钢坯热送。
(2)避免强制加热,加热能力不足时可适当待温。
(3)轧制节奏允许时加大步距,减少钢坯在炉内停 留时间。
高速线材生产工艺
二、加热
4、钢坯除鳞 国内线材生产线钢坯高 压水除鳞是近几年才投入使 用的,因为以前国内线材产 品大多为建筑用材,对表面 质量要求不严格,而且线材 粗轧都有几架箱型孔,有较 好的去除氧化铁皮的效果。 随着线材产品的不断升级, 对线材产品表面质量的要求 不断提高,国内新投产的生 产线都配备了高压水除鳞设 备。
高速线材生产工艺
二、加热
1、原料
线材的原料为小方坯,一般为150*150或 160*160的连铸小方坯,单支重量一般在2~2.5吨。 由于一部分冷墩钢和硬线拉丝用线材需要有较高的 致密度,所以有些钢厂也开始采用初轧坯来做高线 的原料。
线材轧制中的活套控制

维普资讯
冶 金 动 力
METALLURGICBLFOw 既
ZOO1年 第 4期 总 第 8 6期
套的设定 值 ,另一 方面放 慢活套 调节时 间 ,减小 对 下游机 架 的波动影 响 。
5 套量 对 精 轧机 和 夹 送 辊 、吐 丝 机之 间 张 力 的影 响
具体做 法时 :实测 吐丝机 的加 、减速 时 的速 度 变 化牢 ,如图 4示 。
图 3中,由于活套调节器输 出模拟量极性不
同 ,输入端二极管的作用,使积分斜率上升 、下降各 有不 同 ,以满 足加 减速 时的要求 。当套量过 大时 ,活 套调 节器 的输 出为 正 ,精 轧机应 加速 ,积分 时问常 数 TJ= ·c=287K ·lop.=2.87 s。
速度 。 在进行收尾控制时,活套 由下游调节改为上游
调节 ,使得精轧机速度在收尾时不受活套控制的影 响 ,以保证 精轧 机和 夹送辊 间 的微 张力 稳定 。其逻 辑控制是 :当轧件的尾部出 10饥 架时 ,11 机架前 的光电管发出 “收尾控制信号”,记忆精轧前的套 量,使精轧机的速度不受活套变化的影响 ,并将下 游调 节改 为上游 调节 。
4 套量 自动控制 系统
活套在轧机系统中的应用.docx

活套在轧机系统中的应用(上海宝冶建设检修分公司沈林波)摘要:活套是连轧设备中一个较为重要的单元,本文结合武钢csp 厂热轧设备讲叙了活套的基本原理以及常见的一些电气故障和分析处理方法。
关键词:活套控制原理故障、尸■、亠一前言活套是安装在精轧机架之间,用于控制两个机架之间的微张力,防止带钢之间有过多的张力,太多的张力将导致钢被拉断。
当通过下个机架的秒流量比较高的时候,这个现象会发生。
当下个机架的秒流量比较小的时候,套量将建立起来。
一个稳定的增长套量将导致叠轧的形成。
如果叠钢形成,带钢将以几倍的厚度进入下个机架,这将导致辊子的损坏或者轴的损坏。
这样活套控制必须有。
活套控制给了所有前主传动控制的速度修正量。
当秒流量不同的时候,两个机架间的带钢长度将改变,这样将导致活套高度和活套实际角度的改变。
通过活套控制角度总保持在预先设定的范围内。
活套高度的任何改变都将立刻导致所有主传动速度的改变。
每个活套高度的控制是通过影响前一个机架的旋转速度。
一个机架的速度的改变被复制并且作为一个偏差量给定到前一个机架。
这样所有相近的主传动速度的修正量在这些机架里适当减少。
同时在这些机架间的带钢张力是保持不变的。
当机架里没有钢的时候,活套也能移动。
此外当带钢在运行并且活套辊被带钢压下的时候,一个特殊的张力必须产生。
这个压力的发生在轧制力控制与张力控制是相同意义的。
为了实现活套控制的目的,必须设计成位置控制和轧制力控制是串接二活套的工作原理1、结构示意图及设备组成(图一)活套基本结构示意图机械设备和液压设备:活套辊是通过液压缸来移动的。
液压缸的下部分在机架的传动侧。
活套臂的旋转点同杆端相连。
活套围绕在前一个机架的出口侧的轧制线下面的轴旋转。
绕轴旋转的运动被机械运行位置限制。
首先停止(尾端位置)是将活套辊设计在最小的轧制线的下面。
当换辊的时候活套辊要跑到最上的位置,因为空间必须用于入口和导板的运动。
这两个位置都有个一个机械辅助销。
浅谈高速线材厂活套原理及其故障
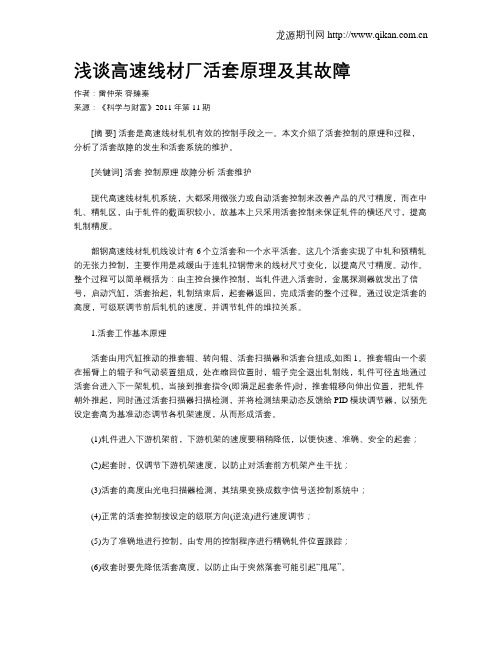
浅谈高速线材厂活套原理及其故障作者:雷仲荣容臻秦来源:《科学与财富》2011年第11期[摘要] 活套是高速线材轧机有效的控制手段之一。
本文介绍了活套控制的原理和过程,分析了活套故障的发生和活套系统的维护。
[关键词] 活套控制原理故障分析活套维护现代高速线材轧机系统,大都采用微张力或自动活套控制来改善产品的尺寸精度,而在中轧、精轧区,由于轧件的截面积较小,故基本上只采用活套控制来保证轧件的横坯尺寸,提高轧制精度。
韶钢高速线材轧机线设计有6个立活套和一个水平活套。
这几个活套实现了中轧和预精轧的无张力控制,主要作用是减缓由于连轧拉钢带来的线材尺寸变化,以提高尺寸精度。
动作。
整个过程可以简单概括为:由主控台操作控制,当轧件进入活套时,金属探测器就发出了信号,启动汽缸,活套抬起,轧制结束后,起套器返回,完成活套的整个过程。
通过设定活套的高度,可级联调节前后轧机的速度,并调节轧件的堆拉关系。
1.活套工作基本原理活套由用汽缸推动的推套辊、转向辊、活套扫描器和活套台组成,如图1。
推套辊由一个装在摇臂上的辊子和气动装置组成,处在缩回位置时,辊子完全退出轧制线,轧件可径直地通过活套台进入下一架轧机,当接到推套指令(即满足起套条件)时,推套辊移向伸出位置,把轧件朝外推起,同时通过活套扫描器扫描检测,并将检测结果动态反馈给PID模块调节器,以预先设定套高为基准动态调节各机架速度,从而形成活套。
(1)轧件进入下游机架前,下游机架的速度要稍稍降低,以便快速、准确、安全的起套;(2)起套时,仅调节下游机架速度,以防止对活套前方机架产生干扰;(3)活套的高度由光电扫描器检测,其结果变换成数字信号送控制系统中;(4)正常的活套控制按设定的级联方向(逆流)进行速度调节;(5)为了准确地进行控制,由专用的控制程序进行精确轧件位置跟踪;(6)收套时要先降低活套高度,以防止由于突然落套可能引起“甩尾”。
扫描器的检测角是固定的,其扫描范围用与活套台的距离来调节。
高速线材活套控制系统的应用

高速线材活套控制系统的应用介绍高速线材活套控制系统的控制原理与控制过程,并对活套系统常见故障进行介绍分析。
标签:高速线材;活套;故障;控制过程前言现代高速线材生产的主要特点是高速、无扭、无张力、连续。
而保证高速、无扭、无张力连续轧制正常进行的条件是各机架的“金属秒流量”相等。
而在实际轧制过程中,由于物料温度、轧辊磨损以及冲击载荷引起的速度波动等因素的存在,从理论上确定的轧辊转速往往不能实现各机架的“金属秒流量”相等,所以在高速线材轧制线中引用微张力控制和活套控制对轧机进行调节。
一般来说微张力控制用于低速轧制区域,活套控制则用于高速轧制区域。
在实际生产中活套直接影响线材的成品质量、产量及成材率等。
因此,活套控制在整个高速线材生产线中地位十分重要,必须合理、有效地控制。
1 活套的定义、组成及作用1.1 活套的定义通过自动控制系统调节相邻机架速度,使机架间产生“多余”物料,物料在起套装置辅助下形成且能动态保持的弧状物,这个弧状物就称为活套。
1.2 活套的组成活套主要有五个部分:分别为活套台、支撑辊、起套辊、气动系统以及活套扫描器,其中支撑辊、起套辊起物料的导向和支撑作用。
气动系统控制起套辊起落,活套扫描器负责测量活套高度。
具体结构如图1所示。
图1 活套结构简图1.3 活套的作用活套是实现高速线材无张力轧制的重要组成部分。
即在轧制过程中,物料不存在堆拉关系。
这是活套通过调节套高实现的,当相邻机架间物料的量减少时,套高会随之减小,活套起缓冲作用,防止物料拉伸,影响物料尺寸;同理,活套还可以吸收机架间过量的物料,防止堆钢。
由此可见活套控制系统的主要作用是吸收因各种原因产生的速度波动,实现无张力轧制,从而提高成品质量。
2 活套的控制基本原理与控制过程2.1 活套的控制原理活套套高控制是通过调节与活套相邻机架速度来实现的。
活套套量等于活套上游机架出口速度V1与下游机架入口速度V2之差的积分,当V1>V2时,套量增加,套高增加,反之套量减少,套高降低,当V1=V2时,套量、套高均不变。
高速线材轧机活套闭环控制系统的研究与应用

高速线材轧机活套闭环控制系统的研究与应用摘要:高速线材预精轧机和精轧机轧制速度较高,仅靠轧机传动装置内置的双闭环调速系统无法保证无张力轧制和不产生堆钢、拉钢的效率,为提升线材产品的金属性能和质量,有效减小现场操作人员的劳动强度,需要做好控制系统的研究,把离散化的思想引入到活套控制环节,实现架轧机间实施无张力轧制。
下面将对高速线材轧机活套闭环控制系统进行研究,从活套闭环控制环节入手进行优化和调整,减少操作人员工作强度,有效避免运行中事故问题的发生。
关键词:高速线材;轧机活套;闭环控制系统前言:活套闭环控制系统是整个轧机控制系统中相当重要的组成部分,控制分为活套形成、活套控制、收尾几部分,执行与工作效率有着直接关系,对活套闭环控制系统进行研究能够有效提高工作开展的效果,减少各类问题的发生。
在实际工作开展中,活套位置通过光电扫描器来测量,轧制过程中轧件头部被活套扫描器检测,活套控制部分开始工作,随后以数字值向控制系统指示出活套位置。
活套闭环控制系统是高速线材轧机控制系统非常重要的组成部分,活套闭环控制系统能够保证预精轧机的之间完成无张力轧制的重要控制,保证产品的性能及质量。
1 高速线材轧机活套闭环控制系统概述现代高速线材轧机,为了保证轧件尺寸精度,除必须设置高精度的主传动自动控制系统来实现轧辊转速的动态调节外,还需在轧线上设置若干活套,以实现无张力轧制。
要形成活套,对轧件截面积有一定的要求,粗轧机组轧件截面积太大,不便于活套的形成;精轧机组系集体传动,不能设置活套。
活套系统中设置有起套辊袭置,其结构为机械曲轴式,由电磁阀控制气缸动作,驱动起套辊升起和落下运动,虽然能够起到支承线材的作用,但不能作上下调节动作[1]。
起套辊升起高度一般设定在距轧制线150~250mm为宜,落套位置应低于轧制线水平位置,扫描器的输出信号反映了线材在轧线上与扫描器的夹角,有效夹角范围最大为±30°,相应的输出电压值为土10V,且所测夹角和电压值成线性关系。
浅析活套控制在高速线材中的应用

浅析活套控制在高速线材中的应用摘要:活套控制是现代轧钢工艺中非常重要的控制手段,活套控制可以提高轧钢的安全性和稳定性,可以有效提高企业的生产质量和效率。
活套控制可以防止拉钢、堆钢问题的出现,有效的控制张力。
本文讨论了高速线材生产中活套控制发挥作用的原理和方式,并就可能出现的故障和问题进行了探讨。
关键词:活套控制;高速线材;故障活套控制被广泛的应用于现代轧钢技术中,以实现连轧的自动控制。
活套控制可以利用活套扫描仪对两台相邻机架间的过剩材料进行扫描,通过过剩材料的弧形曲线轧件高度来测量活套的长度,再对比实测的活套高度和已经设定好的活套高度,自动对各相邻机架的速度进行调整,以便保持活套测定数值和设定数值的一致性。
现代高速线材生产有无扭、高速、连续、无张力等特点,而确保轧制高质量的进行的条件则是保证各机架间“金属秒流量”的相等。
在实际操作中,由于轧辊的磨损程度、材料的温度及冲击载荷引发的速度波动等因素的存在,理论上就无法实现机架间的“金属秒流量”相等。
为了满足这一要求,必须在高速线材轧制生产线中引用活套控制对轧机进行调节,活套控制应用于高速轧制中,可以有效的对生产线上的产品的质量、产量和成材率进行控制。
可以看出活套控制在整个高速线材生产中的重要地位,因此,必须确保活套控制的精度。
一、活套的概念活套指的是自动控制系统调节相邻机架速度,使得机架间产生的能够动态保持的弧状过剩材料。
活套一般由活套台、支撑辊、起套辊、气动系统(电机)和活套扫描仪五个部分组成,这当中起导向和支撑作用的是支撑辊和起套辊,活套扫描仪对活套的高度进行测量,气动系统(电机)则负责控制起套辊的起落,具体如图1所示。
图1 活套结构简图活套在高速线材无张力轧制中发挥着非常重要的作用,活套的存在解决了轧制过程中,材料出现堆拉的问题。
当相邻机架间材料数量减少时,活套通过调节套高让套高也随之减少,起到一个缓冲的作用,以防止材料出现拉伸影响到材料尺寸的精确性。
- 1、下载文档前请自行甄别文档内容的完整性,平台不提供额外的编辑、内容补充、找答案等附加服务。
- 2、"仅部分预览"的文档,不可在线预览部分如存在完整性等问题,可反馈申请退款(可完整预览的文档不适用该条件!)。
- 3、如文档侵犯您的权益,请联系客服反馈,我们会尽快为您处理(人工客服工作时间:9:00-18:30)。
高线轧机间活套基础知识
活套
现代高速线材轧机为保证产品尺寸精度,采用微张力及无张力轧制,以消除轧制过程中各种动态干扰引起的张力波动和由此引起的轧件尺寸波动。
由于精轧机组为集体传动,故精轧采用微张力轧制,其微张力值由固定速比和各架给定孔槽面积保证,速比不会因控制而改变,轧件面积将因来料面积波动而波动。
为了减少张力变化引起的精轧机的轧件尺寸波动,在精轧机前的预精轧、中轧几机组常设若干个活套,以消除连轧各架的动态速度变化的干扰、保证轧件精度。
活套定义及作用
通过自动控制系统调节相邻机架的速度使机架间产生“多余”轧件,该“多余”轧件在起套装置辅助下形成且能动态保持弧形的套状物,这个套状物就称为活套。
活套控制功能适用于轧件断面小轧制速度较快的场合,能消除连轧机架的动态速度变化的干扰、保证轧件精度,活套可以实现无张力轧制。
所谓无张力轧制即是在轧制过程中,机架间轧件不存在拉钢关系,是通过改变活套存储量来实现的。
当相邻两机架间轧件受拉时,套量减小,可起缓冲作用,防止机架间产生张力,免使轧件断面拉缩,影响轧件尺寸的精度;另一方面吸收过量的轧件,防止堆钢而造成机架间的堆钢事故。
但是活套的套量调节范围及套量的存储量是有限的,当相邻机架速度匹配不合理或其它原因而使起套量偏差太大,自动控制系统来不及或无法调节,就会引起堆钢。
活套由活套台、支撑辊、导槽、起套辊及活套扫描器等组成。
支撑辊、起套辊起着对轧件的导向和支持作用。
起套辊、转向导板均由气缸驱动,起套辊气缸由双电磁阀控制。
活套种类:下活套、侧活套、立活套。
在高速线材轧机上,下活套通常用于中轧机组。
下活套的套量控制比较困难,因为下活套的光电扫描器工作环境恶劣,难以实现自动控制。
侧活套由水平活套台、推套器及进出口导向辊组成。
推套器是由气缸操纵的导辊。
精轧机前的侧活套不能自由脱套产生,而需要有一个轧机的速度变化推套动作,扫描反馈的控制过程。
立活套是现代高速线材轧机的主要配套技术之一,用以使相邻机架间保持适当套量实现无张力轧制。
在整个轧制过程中,从轧件在下一架轧机咬入后的起套,到后尾收套都由计算机控制。
活套控制的基本原理
活套是用来检测和调整相邻机架间速度关系从而实现无张力轧制的一种手段。
活套控制是对相邻机架间金属秒流量差异进行测量的基础上进行的,金属秒流量差异导致机架间堆钢(或拉钢),轧件由起套辊引导使其形成活套。
在线活套扫描仪可实时反馈实测活套高度,控制系统将实测活套高度与设定活套高度进行比较从而产生速度修正信号,调整上游机架速度以维持活套高度(活套量)在给定值上不变,从而实现其前后机架间正确的速度配合。
当上游道次金属秒流量小于下游道次金属秒流量时,套量就渐渐减少,套高降低;金属秒流量相等时则套高不变。
活套控制就是通过改变与活套相关机架速度来实现的。
变速度差控制为套量控制(△v一△H),基本过程是头部起套一中间稳定为设定套量一尾部收套。
活套扫描器测量出套高实际值,并与套量设定值进行比较,然后根据其偏差值作为活套调节器的修正信号,调整上游机架的速度。
当由于外界条件引起活套大小改变而使活套偏离设定套位时,实际套量不等于设定套量,活套调节器便有输出,通过速度调节系改变活套上游机架速度,并逆向级联调节上游所有机架速度,这种调节会因每一条钢而有所不同,直到稳定为止。
活套的控制过程
起套
以14一15机架间立活套为例,其它活套类似。
当14 机架活套扫描器检测到轧件头部并延时t1秒,自动控制系统送一个起套信号给电磁阀,起套延时t1秒的确定(以14 到l5 机架的距离除以14 机架出口速度得到时间,来考虑气缸动作延时)应保证轧件刚好咬入l5 机架时,起套辊刚好启动。
当起套辊启动后,活套上游的14 机架升速使14 、l5 之间生“多余”轧件以生成活套,起套过程
结束后,14 机架恢复设定值。
根据电机的动态特性,当轧件刚咬入l5机架时,电机会产生一个动态速降,但是控制系统预先给l5 机架以2~4%的动态速降补偿,可以保证不会因动态速降而使刚咬入时产生太多“多余”轧件,即起始套高度为0,这一点可以从不投入活套仍能平稳咬入得到确认。
稳定调节
起套完成后,即进入活套稳定控制阶段。
根据活套扫描仪得到不断变化的套量,通过电控脉冲信号不断地传递给电控系统,系统按逆向级联控制的方向调整相邻上游14 机架的速度,这就相当于连续地修正上游相邻14机架的速度来保证活套的高度与设定值一致。
活套调节是为了补偿轧件尺寸或温度变化而引起的套量变化。
操作人员也要密切关注活套的远行情况,当活套高度超过允许最大高度或者存在严重拉钢的情况下,因超出活套自动控制调整范围,自动控制失效,应及时采取手动控制,以保证生产的安全进行。
收套阶段
当轧件尾部到13机架 (咬钢)信号,即进入收套阶段。
仍然采用一个延时t2,自动控制系统送一个落套信号给电磁阀,落套延时t2,t2的确定(以13到l4机架的距离除以13 机架出口速度得到时间t2,来考虑气缸动作延时),应保证轧件刚好出l4机架时,起套辊刚好落下。
为了安全收套并防止突然收套可能引起的甩尾,在收套阶段,要降低14 机架的速度以配合起套高度在轧件出14 机架降到0。
起套辊不能落套过早,如果落套过早会使轧件在活套台处产生堆钢或甩尾,落套也不能太迟,如果太迟,下一轧件到来之前还未完全落套就会造成冲钢。
活套套形分析
在生产过程中,活套可能形成4种套形,如图所示。
(1)第1种套形是由于活套起套高度设定过大,轧件易在下一机架前产生堆钢及甩尾现象,不易控制。
(2)第4种套形是由于活套起套高度设定过小,轧件对起套辊压力较大,易导致套辊磨损快,机械故障多;另一方面轧件未能实现机架问无张力轧制,对红坯料形控制波动大。
(3)第2种套形是活套起套高度设定恰当,活套辊工作正常,轧件能实现机架间无张力轧制,对红坯料形控制较好,但如遇起套辊收套不及时,也易造成甩尾现象。
(4)第3种套形是活套起套高度设定略小,但活套辊能正常工作,轧件也能实现机架间无张力轧制,对红坯料形控制较好,不易造成甩尾现象。
因此,可根据设备和工艺条件选择第2、第3种套形。
活套事故分析
在实际生产中发现有多种原因引起活套不稳定或堆钢。
1)活套起套辊不起套,原因可能有以下几种:
①、活套扫描器有故障,不能检测;
②、活套扫描器受震动,没对准检测口;
③、活套扫描器镜头脏,检测不稳;
④、冷却水太大或天冷雾气大,影响扫描器的检测灵敏度;
⑤、电气线路接触不良及其它原因引起断路,起套信号送不到电磁阀;
⑥、电磁阀线包烧坏,阀不能动作;
⑦、电磁阀阀芯堵塞,阀不能动作;
⑧、气源未打开或气管破损;
⑨、气缸或起套辊机械卡死。
2) 活套起套辊不落套原因可能为:
①、上游机架的上游机架信号错误;
②、电磁阀线包烧坏,阀不能动作;
③、气缸或起套辊机械突然卡死。
3) 活套区常堆钢现象分析:
活套起套后时序紊乱,不能正常落套,下一钢坯钻人起套辊造成堆钢。
解决办法,加强现场检测元件维护,确保检测信号的准确,注意保持最佳出钢节奏。
水平活套处堆钢。
因水平活套处两相连机架间距很大,起套过早容易飞钢,过晚又易产生张力,所以要注意起落套的设置。
精轧前水平活套处常因换辊后精轧咬钢困难,加之19机架动态速降补偿时间过长而引起堆钢。
解决办法是调整19机架动态速降补偿参数,控制出钢节奏,同时要注意水平活套套台冷却及禁止碎断钢头带人套台。
4) 活套套量不稳。
一般情况下,调试好的活套都是较稳定的。
如果有不稳定现象发生不要轻易通过修改活套高度给定或升降相邻上游机架转速的方法来使活套稳定下来。
活套的稳定性与有关机架速度控制系统动态特性及粗、中轧堆拉关系,活套区工艺调整有关。
正常情况下,对于同一轧件由头部到尾部活套允许有±15mm的高度变化。
可能引起活套不稳定的几个因素:
电气原因:活套扫描器检测信号不稳,镜头脏,冷却水及雾气太大,检测口化铁皮较多,均易导致信号时有时无,影响活套控制。
机械原因:如果支撑辊、起套辊轴承烧毁,转动不灵活造成磨损不均及卡死,会引活套不稳;起套辊或支撑辊偏心引起套量波动,这种波动一般从形成活套后开始就出现波动一直延续到落套。
工艺原因:导卫安装不当或辊缝设置不当也会引起的活套不稳。
轧件温度变化导致套量波动,这种波动一般出现在轧件尾部或中部以后,操作人员应该及时通知加热炉,以保证钢温的正常。
头部起套太高。
一种可能是椭圆孔压下太多,
轧件与下道圆孔型进口导轮不匹配,轧件阻力太大;另一可能性是轧件头,尾部与中部尺偏差太大。