第7讲 形状和位置精度(三) - 复件
合集下载
形状和位置公差学习

形状和位置公差
1 形位公差的基本概念
经过加工的零件,除了会产生尺寸误差外,也会产生表面形状和位置误差。
形状误差是指加工后实际表面形状对理想表面形状的误差。
如图1-1中的小轴,加工后双点画线表示的表面形状与理想表面形状产生了形状误差。
图1-1
位置误差是指零件的各表面之间、轴线之间或表面与轴线之间的实际相对位置对理想相对位置的误差。
如图1-2中的轴套,其端面对轴线不垂直,产生了位置误差。
形状误差和位置误差都会影响零件的使用性能,因此,对一些零件的重要工作面和轴线,常规定其形状和位置误差的最大允许值,即形状和位置公差(简称形位公差)。
图1-2
2 形位公差特征项目及符号
在技术图样中, 形位公差应采用代号标注。
当无法采用代号标注时,允许在技术要求中用文字说明。
形位公差代号包括形位公差有关项目的符号、形位公差框格、指引线、形位公差数值和其它有关符号及基 准符号。
形位公差的项目和符号,如表1所示。
形状及位置精度

在安装过程中,使用高精度的 测量设备对安装结果进行测量 和校准,以确保达到所需的精 度要求。
对安装人员进行培训,提高他 们的技能和意识,以确保他们 能够正确地执行安装操作。
使用高精度定位系统
使用高精度的GPS系统、激光雷 达、摄像头等定位技术,以提高
位置精度。
在定位系统中进行参数设置和校 准,以确保其精度和可靠性。
使用高精度测量设备
选择高精度测量设备
01
采用高精度的三坐标测量机Байду номын сангаас激光干涉仪等测量设备,对零件
进行精确测量。
定期校准
02
对测量设备进行定期校准,确保其测量精度和可靠性。
掌握测量技术
03
掌握先进的测量技术,如逆向工程、三维扫描等,提高形状精
度测量和评估能力。
04
位置精度的提高方法
提高安装精度
确保安装过程中使用的工具和 夹具的精度,并定期进行校准 和维护。
智能化技术的应用
1 2
机器视觉检测
利用机器视觉技术对产品进行快速、准确的检测, 自动识别形状及位置误差,提高生产效率和精度。
智能传感器
集成智能传感器于制造过程中,实时监测工件状 态和位置,自动调整加工参数,确保加工精度。
3
人工智能优化
通过人工智能技术对加工过程进行优化,预测和 修正形状及位置误差,实现自适应加工。
电子制造领域
总结词
微型化要求
详细描述
随着电子产品不断微型化,电子制造领域对形状及位置精度的要求也越来越高。例如,在制造高精度电路板和微 型电子元件时,需要严格控制零件的位置和尺寸,以确保电子产品的正常运行。
医疗器械领域
总结词
人体相容性要求
机械零件几何精度之形状与位置精度(PPT44张)

因此形位公差带体现了对被测要素的设计要求,也是加工 与检验的依据。
形
形状
形位公差带的形状如图所示
位 大小
大小体现了形位精度要求高低,由设计给定的形位公差数值
公
确定,用以表示形位公差带的宽度或直径
差 带
方向
指组成公差带的几何要素的延伸方向,通常与图 样上公差代号的指引线箭头方向垂直。
的
要Байду номын сангаас
浮动
指形位公差带的位置随实际尺寸的变动而变动。形状
(2)指引线:将框格与被测要素联系起来,指 引线原则上从框格一端的中间位置引出,其箭 头应垂直指向被测要素。
2.被测要素的标注方法
(1)当被测要素为轮廓要素时,指引线的箭头置于该要 素的轮廓线或其延长线上,但应与尺寸线明显错开。如图 (a)、(b)所示。
被测要素为轮廓要素的标注
(2)当被测要素为中心要素时,指引线的箭头应与该要素 的尺寸线对齐,如图 (c)所示
第四节 形状与位置精度
由于加工误差的影响,机械零件的几何要素不仅 有尺寸误差,还会产生形状误差和位置误差。
※形位误差:零件的实际形状、位置对其理想形状、位置 的变动量。
零件的形位误差同样将影响零件、机械的精度以及零 件间配合的性质。形状和位置误差越大,其形状和位置精 度越低;反之,则越高。
形位公差:形位公差是被测实际要素相对于其 理想要素允许的最大变动量,形位公差是用 以限制形位误差。
(3)当同一被测要素有一个以上的公差 特征项目要求并且测量方向相同时,可将 公差框格放在一起,只用同一指引线指向 被测要素,如图(a)所示
(4)当对被测要素任一部分有进一步形位公差 限制时,应将该部分的尺寸标注在形位公差值的 后面,并用斜线分开。如图(b)所示。
形状与位置精度讲解
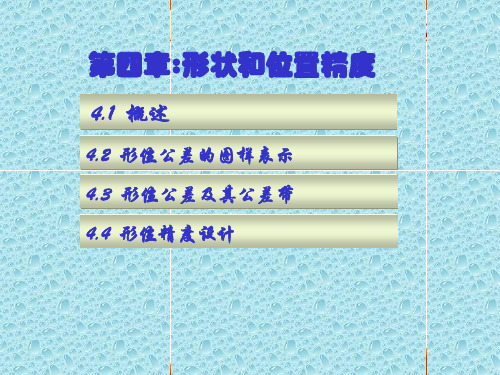
0.03
标注含义: φD中心线对
下表面的平行度公差为 0.03mm
公差带图
4.3 形位公差及其公差带
线对线在任意方向上的平行度
0.06
标注含义:φD1中心线对φD2中
心线的平行度公差0.06mm
公差带图
4.3 形位公差及其公差带
线对线在两垂直方向上的平行度
0.1
标注含义: φD1中心线对φD2中
基准 是用来确定被测要素方位的参考对象。
基准的种类
1. 单一基准
2.公共基准
4.3 形位公差及其公差带
3、基准体系:由两个或三个基准共同确定被测要 素的方位。
4.3 形位公差及其公差带
基准的体现
加工后的零件,实际基准都存在一定的形状误 差,不宜直接使用实际基准要素作为基准,通常 用形状足够精确的表面模拟体现
值 0.01 的 两 平 行 直 线 之间的区域。
4.3 形位公差及其公差带
给定一个方向的直线度
标注含义:棱线在铅垂
方向上的直线度公差为 0.02mm。
公差带是距离为公差
值 t的两平行平面之 间的区域。
4.3 形位公差及其公差带
给定互相垂直两个方向的直线度
0.02 0.01
标注含义:棱线在铅垂
方向上直线度公差为 0.01,在水平方向上直 线度公差为0.02。
4.3 形位公差及其公差带
1、线轮廓度
0.04
0.04
4.3 形位公差及其公差带
2、面轮廓度
4.3 形位公差及其公差带
4.3.3、定向(方向)公差带
定义:关联被测要素对基准要素在规定方向上允许 的变动量。
项目:平行度、垂直度、倾斜度(轮廓度)
形状和位置公差课件
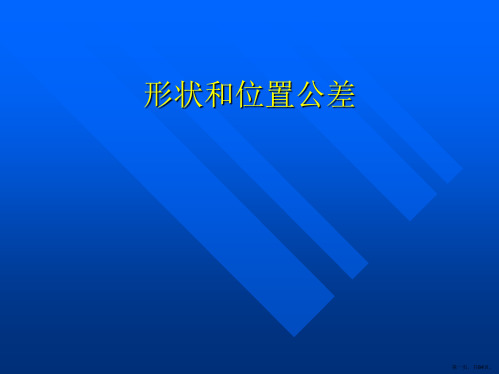
全跳动公差为综合性指标。
第三十三页,共84页。
影响形位公差带的有四个因素:形状、大小、方
向、位置。
公差带的形状:取决公差项目, 有两平行直线组
成的区域;两平行平面组成的区域; 两同心圆柱
面之间的区域等。
公差带的方向: 对于形状公差其放置方向应符合 最小条件; 对于位置公差其放置方向由被测要素 和基准的几何关系确定。
所示。尺寸虽合格却形不成间隙配合,原因是轴 存在着较大的形状误差。
图7-1 轴孔尺寸公差与轴的形状误差
第三页,共84页。
形状误差:轴线不直、平面不平、轴或孔的横截
面不圆等。
位置误差:不平行、不垂直、不同轴等。
由于零件形位误差的存在,将对机器的精度、结
合强度、密封性、工作平稳性、使用寿命等产生
不良影响。因此,对一些重要零件有必要给定形
向上的变动量的指标。
垂直度公差带定义和示例见表7-3。 (三)倾斜度:限制实际被测要素对于基准在给定
角度方向上变动量的指标。
第二十八页,共84页。
被测要素与基准的倾斜角度用理论正确角度表示。
二、定位公差和误差 定位公差:关联实际被测要素对具有确定位置的理 想要素的允许变动量。
理想要素的位置由基准和理论正确尺寸确定。
1. 规定:位置误差的评定应符合最小条件。 规定有两层意思: (1)基准要素理想形状的位置,应符合最小条件。 (2)理想被测要素的位置,应符合最小条件。 2. 平面度的测量 (1)将A平面放在高精度的平板上; (2)以平板为基准测量顶面的平行度。
第四十页,共84页。
平板可认为是具有理想 形状的基准要素,且与
形状和位置公差
第一页,共84页。
第一节形状公差和误差
一、概述
第三十三页,共84页。
影响形位公差带的有四个因素:形状、大小、方
向、位置。
公差带的形状:取决公差项目, 有两平行直线组
成的区域;两平行平面组成的区域; 两同心圆柱
面之间的区域等。
公差带的方向: 对于形状公差其放置方向应符合 最小条件; 对于位置公差其放置方向由被测要素 和基准的几何关系确定。
所示。尺寸虽合格却形不成间隙配合,原因是轴 存在着较大的形状误差。
图7-1 轴孔尺寸公差与轴的形状误差
第三页,共84页。
形状误差:轴线不直、平面不平、轴或孔的横截
面不圆等。
位置误差:不平行、不垂直、不同轴等。
由于零件形位误差的存在,将对机器的精度、结
合强度、密封性、工作平稳性、使用寿命等产生
不良影响。因此,对一些重要零件有必要给定形
向上的变动量的指标。
垂直度公差带定义和示例见表7-3。 (三)倾斜度:限制实际被测要素对于基准在给定
角度方向上变动量的指标。
第二十八页,共84页。
被测要素与基准的倾斜角度用理论正确角度表示。
二、定位公差和误差 定位公差:关联实际被测要素对具有确定位置的理 想要素的允许变动量。
理想要素的位置由基准和理论正确尺寸确定。
1. 规定:位置误差的评定应符合最小条件。 规定有两层意思: (1)基准要素理想形状的位置,应符合最小条件。 (2)理想被测要素的位置,应符合最小条件。 2. 平面度的测量 (1)将A平面放在高精度的平板上; (2)以平板为基准测量顶面的平行度。
第四十页,共84页。
平板可认为是具有理想 形状的基准要素,且与
形状和位置公差
第一页,共84页。
第一节形状公差和误差
一、概述
形状和位置公差实用讲义

面对线(面)垂直度公差
• 被测面必须位于距 离为公差值0.01且 垂直于基准轴线的 两平行平面之间. • 被测面必须位于距 离为公差值0.01且 垂直于基准表面的 两平行平面之间.
线对线(面)倾斜度公差
• 被测轴线必须位于 距离为公差值0.01 且与基准轴线成一 理论正确角度的两 平行平面之间. • 被测轴线必须位于 距离为公差值0.01 且与基准表面成理 论正确角度的两平 行平面之间.
基准要素的标注(3)
• 对于具有对称形状的零件, 可以标注任选基准。此时, 用指示箭头代替基准代号中 的短横线。 • 当以中心线、中心平面或轴 线作为基准时,基准不能直 接放在中心线、中心平面或 轴线上。 • 基准符号的短横线不能直接 与形位公差框格相连。
直线度公差带
• 被测表面的素线必 须位于距离为公差 值0.01的两平行直 线内. • 被测圆柱面的任一 素线必须位于公差 值0.01的两平行平 面之内. • 被测圆柱面的轴线 必须位于直径为公 差值φ0.1的圆柱面 内.
同轴度公差
• 外圆的圆心必须位 于直径为公差值 φ0.01且与基准圆心 同心的圆内. • 大圆柱面的轴线必 须位于直径为公差 值0.01且与公共基 准线A-B同轴的圆柱 面内.
对称度公差
• 被测中心平面必须 位于距离为公差值 0.01且相对于基准 中心平面对称配置 的两平行平面之间. • 当被测要素和基准 要素均为轴线时,则 该两轴线必需相互 垂直.
圆跳动公差
• 径向圆跳动公差表示φd轴在任
一垂直于基准轴线的测量平面上, 其实际轮廓必须位于半径差为公 差值0.02、圆心在基准轴线A上 的两同心圆之间.
• 端面圆跳动公差表示右端面在
任一与基准轴线A同轴的测量圆 柱面上,其实际轮廓必须位于宽度 为公差值0.02、圆心在基准轴线 A上且垂直于基准轴线的两圆柱 面内.
《形状及位置精度》课件

介绍一些关于形状及位置精度前沿研究的相关文献和学术论文。
采用精密测量工具如三坐标测量机,使用几何形状误差评定方法。
什么是位置精度
1 定义位置精度
位置精度是工件某一特定 点与其理想位置之间的偏 差。
2 影响因素
位置精度受制造过程中的 定位、夹持和加工误差的 影响。
3 测量方法
使用定位误差测量工具如 光学测量仪,以及位置精 度评估方法。
形状及位置精度的重要性
形状及位置精度
形状及位置精度在现代社会中起着至关重要的作用。本课件将介绍形状精度、 位置精度的定义、影响因素和测量方法,以及提高精度的技术手段和应用案 例分析。
什么是形状精度
1 定义形状精度
形状精度指工件与其理想形状之间的差异程度。
2 影响因素
形状精度受材料特性、加工工艺以及测量工具的影响。
3 测量方法
3
质量控制
制定严格的质量管理标准,进行全过程的质量监控和追溯分析。
实际案例分析
对于不同的应用领域分析形状及位置精度 需求
针对航空航天、医疗器械等行业的精密零部件生产, 分析其对形状及位置精度的具体要求。
分析实际应用中的形状及位置精度问题
通过典型案例,探讨在实际生产中可能遇到的形状 及位置精度的挑战和解决方法。
在哪些领域应用广泛
汽车制造、航空航天、电子设备等高精度行业对形状及位置精度要求极高。
为什么需要形状及位置精度
精确的形状及位置精度能够保证产品的质量、性能和可靠性。
如何提高形状及位置精度1 Nhomakorabea技术手段
采用现代化的生产工艺,如数控加工和自动化装配,以减少人为误差。
2
工程应用
合理设计夹具和定位结构,使用高精度测量仪器进行在线检测和调整。
采用精密测量工具如三坐标测量机,使用几何形状误差评定方法。
什么是位置精度
1 定义位置精度
位置精度是工件某一特定 点与其理想位置之间的偏 差。
2 影响因素
位置精度受制造过程中的 定位、夹持和加工误差的 影响。
3 测量方法
使用定位误差测量工具如 光学测量仪,以及位置精 度评估方法。
形状及位置精度的重要性
形状及位置精度
形状及位置精度在现代社会中起着至关重要的作用。本课件将介绍形状精度、 位置精度的定义、影响因素和测量方法,以及提高精度的技术手段和应用案 例分析。
什么是形状精度
1 定义形状精度
形状精度指工件与其理想形状之间的差异程度。
2 影响因素
形状精度受材料特性、加工工艺以及测量工具的影响。
3 测量方法
3
质量控制
制定严格的质量管理标准,进行全过程的质量监控和追溯分析。
实际案例分析
对于不同的应用领域分析形状及位置精度 需求
针对航空航天、医疗器械等行业的精密零部件生产, 分析其对形状及位置精度的具体要求。
分析实际应用中的形状及位置精度问题
通过典型案例,探讨在实际生产中可能遇到的形状 及位置精度的挑战和解决方法。
在哪些领域应用广泛
汽车制造、航空航天、电子设备等高精度行业对形状及位置精度要求极高。
为什么需要形状及位置精度
精确的形状及位置精度能够保证产品的质量、性能和可靠性。
如何提高形状及位置精度1 Nhomakorabea技术手段
采用现代化的生产工艺,如数控加工和自动化装配,以减少人为误差。
2
工程应用
合理设计夹具和定位结构,使用高精度测量仪器进行在线检测和调整。
形状和位置公差及检测 (3)PPT课件
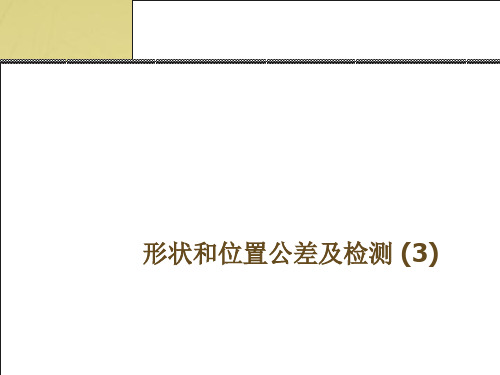
公差带形状是圆形或圆柱时,公差值前加注“ ”,如是球形,加注“S ”:
------在任意方向的直线度 ------线对线在任意方向的平行度 ------线对面在任意方向的垂直度 ------位置度 ------同轴度 基准符号不准用E、I、J、M、O、P、L、R、F:
------E:包容要求 ------I、J、O易与1、0混扰 ------M:最大实体要求 ------P:延伸公差带要求 ------L:最小实体要求 ------R:可逆要求 ------F:自由状态要求
3)基准体系(三基面体系) ——由三个相互垂直的平面所构成的基准体系
90°
B 90°
C 90°
A
图4-4 三基面体系
三、位置公差
2.定向公差与公差带 • 定向公差——是指关联实际要素对基准在方向上允许的变
动全量。 • 定向公差包括平行度、垂直度和倾斜度三项。
三、位置公差 ——平行度
1)“面对面”的平行度
跳动公差 1、圆跳动公差 2、全跳动公差
三、位置公差
1、基准 基准是确定被测要素的方向、位置的参考对象。 1) 单一基准——由一个要素建立的基准称为单一基准。 2) 组合基准(公共基准)——由两个或两个以上的要素所建立 的一个独立基准称为组合基准或公共基准。
0.05
A-B
单一基准
A
B
组合基准
三、位置公差
0.03 A-B
0.1CZ
A
B
多要素同要求的简化标注
多处要素用同一公差带时的标注
一、概 述
(5) 当同一个被测要素有多项形位公差要求,其标注方法又是 一致时,可以将这些框格绘制在一起,并引用一根指引线。
A A
同一要素多项要求的简化标注
------在任意方向的直线度 ------线对线在任意方向的平行度 ------线对面在任意方向的垂直度 ------位置度 ------同轴度 基准符号不准用E、I、J、M、O、P、L、R、F:
------E:包容要求 ------I、J、O易与1、0混扰 ------M:最大实体要求 ------P:延伸公差带要求 ------L:最小实体要求 ------R:可逆要求 ------F:自由状态要求
3)基准体系(三基面体系) ——由三个相互垂直的平面所构成的基准体系
90°
B 90°
C 90°
A
图4-4 三基面体系
三、位置公差
2.定向公差与公差带 • 定向公差——是指关联实际要素对基准在方向上允许的变
动全量。 • 定向公差包括平行度、垂直度和倾斜度三项。
三、位置公差 ——平行度
1)“面对面”的平行度
跳动公差 1、圆跳动公差 2、全跳动公差
三、位置公差
1、基准 基准是确定被测要素的方向、位置的参考对象。 1) 单一基准——由一个要素建立的基准称为单一基准。 2) 组合基准(公共基准)——由两个或两个以上的要素所建立 的一个独立基准称为组合基准或公共基准。
0.05
A-B
单一基准
A
B
组合基准
三、位置公差
0.03 A-B
0.1CZ
A
B
多要素同要求的简化标注
多处要素用同一公差带时的标注
一、概 述
(5) 当同一个被测要素有多项形位公差要求,其标注方法又是 一致时,可以将这些框格绘制在一起,并引用一根指引线。
A A
同一要素多项要求的简化标注
形状及位置精度

差
差
圆跳动 跳 动
号面轮廓度Fra bibliotek全 跳 动 全周符号
§3––2 基本术语
机械零件是由构成其几何特征的若干 点、线、面组成的,这些点、线、面统 称为几何要素(简称要素)。 一.要 素:构成零件几何特征的点、线、 面称为要素
图 4-1 零件几何要素 点要素:圆锥顶点5和球心8; 线要素:素线6和轴线7; 面要素:球面1圆锥面2环状平面3和圆柱面 4。
给定任意方向的 直线度公差带, 它表示实际轴心 线只允许在公差 t4所确定的圆柱 体内变动
3,测量:
(1)小零件用刀口尺测量
零件精度高,用光隙法判断间隙的大小。 零件精度低,用塞尺检查间隙的大小。
2)对低精度中等尺寸的零件,用打表法测量。
将被测零件支承在平板上,调整支架使被测直线的两端基本 等高。然后沿平板移动表架,等距测量被测要素上的各点。 缺点:测量精度与平板精度有关,被测件不易过大。
例:测点 0 1 2 3 4 读数(μm) 0 3 2 -3 2
以测点的序号作为横坐标值,以测得值作为纵坐标值,依此 将各点描绘在坐标纸上,相邻点用直线连接,则构成了被测 要素的误差折线图。按最小条件作两条平行直线将误差折线 包容,两条平行直线的垂直坐标距离为 5 1 ,这就是被测直 3 线的直线度误差。
(4)对于高精度中等、较大尺寸的零件, 用自准直仪或水平仪测量。(注:相对法,有累
积误差)(瑞士的elautocollimator )
例:用水平仪测量一零件的直线度误差,水平仪 的分度值为0.01mm (格) /m,若实际分度值 i=1.8(μm),测量数据如下: 测点 1 2 3 读数(格) 3 0 0
3、测量
(1)对于精度较高的小零件,如光学元件、量 块表面等,其平面度误差一般用平晶法测量。
形状和位置精度

全跳动公差: ★全跳动公差: 是指被测实际要素绕基准轴线作无 轴向移动连续多周回转, 轴向移动连续多周回转,同时指示表作 平行或垂直于基准轴线的直线移动时, 平行或垂直于基准轴线的直线移动时, 在整个表面上所允许的最大跳动量。 在整个表面上所允许的最大跳动量。
§3.4 公差原则
GB/T4249GB/T4249-1996 ——ISO 8015 GB/T16671-1996 形状和位置公差 最大实体要求、 GB/T16671最大实体要求、 最小实体要求和可逆要求 ——ISO 2692:1996
§3.4 公差原则
形位公差要求 公差原则: 公差原则:处理尺寸公差与形位公差之间 关系的规定 独立原则 相关要求 包容要求 最大实体要求 最小实体要求 零形位公差 可逆要求 零件的同一几何要素 尺寸公差要求
一、名词术语
最大实体状态: 最大实体状态:孔或轴具有材料量为最多时的状态 最小实体状态: 最小实体状态:孔或轴具有材料量为最少时的状态
●被测要素的实际尺寸不得超出最小实体尺寸
边界
孔和轴的极限尺寸判断原则(泰勒原则): 对于轴的合格条件: dfe ≤ dM da ≥ dL Dfe≥ DM Da ≤ DL dfe =da +f ≤ dM= dmax da ≥ dL = dmin
对于孔的合格条件: Dfe=Da― f ≥ DM=Dmin Da ≤ DL =Dmax
内接的最大理想轴
外接的最小理想孔
Dfe
孔的体外作用尺寸
轴的体外作用尺寸
Dfe=Da―f
dfe=da + f
Dfe: 实际孔 最大 轴 fe: 在结合面全长上, 在结合面全长上,与 外接的 理想 的尺寸 dfe: 实际轴 最小 孔 fe:
相关主题
- 1、下载文档前请自行甄别文档内容的完整性,平台不提供额外的编辑、内容补充、找答案等附加服务。
- 2、"仅部分预览"的文档,不可在线预览部分如存在完整性等问题,可反馈申请退款(可完整预览的文档不适用该条件!)。
- 3、如文档侵犯您的权益,请联系客服反馈,我们会尽快为您处理(人工客服工作时间:9:00-18:30)。
四、形状与位置精度的检测
2.位置误差的评定原则
最小条件不仅是形状误差的评定原 则,也是位置误差的评定原则。位 置误差分为定向误差、定位误差和 跳动误差三类。
四、形状与位置精度的检测
3.直线度误差的评定
1)坐标变换:直线度的测 量可采用水平仪或三坐标 测量仪,用水平仪所测得 的数据是工件上两测点间 的相对高度差,需将各测 点数据变换到统一坐标上 。通常选用原点的坐标值 为0,将各测点的读数顺序 依次累加即可获得相应各 点的统一坐标。
4)可逆要求的应用
可逆要求用于最大(最小)实体要求时,与最大(最小 )实体要求的应用场合相同。可逆要求不但允许尺寸公 差补偿给形位公差,而且还允许形位公差补偿给尺寸公 差,进一步放宽了零件的合格条件。
三、形位精度设计
3.形位公差项目的选择
1)认真分析零件各重要部位的功能要求,确定是否标注 形位公差以及应该标注哪些项目。所设计的形位公差用常 用设备和方法加工就能保证者,不必在设计图样上标出( 做未注公差处理),通常也不检查;若功能需要,要求零 件上某些要素的形位精度高于未注公差要求时,则必须将 这些形位公差标注在图样上。 2)应从工厂现有的检测条件来考虑形位公差项目的选择 。如用圆跳动代替同轴度,用全跳动代替圆柱度等。
可逆要求仅适用于中心要素,即轴线或中心平面,并且不能 独立使用,也没有自己的边界,必须和最大实体要求或最小 实体要求一起使用。
三、形位精度设计
1.形位精度设计的内容P75-79
正确处理尺寸公差和形位公差之间的关系,合理选用公 差原则和相关要求。
根据零件的要素特点、检测条件以及有关标准件的要求 ,选择形位公差项目。 根据零件的功能和精度要求、制造成本等,确定形位公 差等级。 按标准规定进行图样标注。 对于大批量生产的产品,其尺寸精度和形位精度的设计并 不是一蹴而就的,往往经由实验或实践反复验证后,得到 稳定的设计数据。一般地,跳动较为容易检测;对于轴套 类零件,端七径八较为容易保证。
四、形状与位置精度的检测
3.直线度误差的评定
2)最小区域法评 定:评定给定平 面内直线度误差 的最小区域应符 合两个条件—误 差曲线全部位于 两平行直线之间 ;两平行直线与 误差曲线成“高低-高”或“低-高 -低”相间三点接 触。
四、形状与位置精度的检测
4.平面度误差的评定
最小区域法评定:两平行理想平面与被测实际平面接触状 态为下列三种情况之一,即符合最小条件—被测实际平面 与两平行平面的接触点投影在一个面上呈三角形,“三高 夹一低”或“三低夹一高”(三角形准则);被测实际平 面与两平行理想平面的接触点投影在一个面上成交叉形( 交叉准则);被测实际平面与两平行理想平面的接触点投 影在一个面上呈一直线,“两高夹一低”或“两低夹一高 ”(直线准则)。
D fe D m in t, 且 D m in D a D m ax d
fe
对于轴
d m ax t, 且 d m in d a d m ax
1)当轴的实际尺寸偏离最大实体尺寸 时,允许轴线的直线度误差可以超过 给定的公差值。 2)轴的局部实际尺寸不能超出最小极 限尺寸和最大极限尺寸。
三、形位精度设计
2.公差原则与相关要求的应用
2)包容要求的应用 包容要求用于有配合要求的场合,以保证所需要的最小间 隙或最大过盈,也常用于作为基准使用的孔、轴类零件。
三、形位精度设计
2.公差原则与相关要求的应用
3)最大实体要求的应用 最大实体要求应用于满足可装配性,但无严格配合要求 的场合。采用最大实体要求可最大限度地提高零件制造 的经济性。
2)有配合要求的要素,其形状公差值通常在尺寸公差值 的25~60%选取,适合大部分工艺条件。该百分比若过小 会对工艺装备的精度要求过高,若过大则会给保证尺寸本 身的精度带来困难。
3)对薄壁件或细长轴这类刚性较差的零件以及距离较远 的孔,因其工艺性不好,加工精度受到影响,需选取较大 的公差值。 重要零件可通过理论计算或试验法选取 形位公差值。非重要零件多用类比法。
fe
d M d max ,且 d a d L d min
1)当轴的实际尺寸小于最大 实体尺寸时,才允许轴线有直 线度误差。
3)轴的局部实际尺寸不能小 于最小实体尺寸。
二、形位公差与尺寸公差的关系—相关要求
3.包容要求
7
二、形位公差与尺寸公差的关系—相关要求
4.最大实体要求
最大实体要求(maximum material requireemt,MMR)是一种相关要 求,既可用于被测要素(单一要素或关联要素),也可用于基准中心要 素。 对于孔
3)确定形位公差项目要参照相关专业标准规定,例如与 滚动轴承相配合的孔、轴的形位公差项目,在滚动轴承标 准中已有规定。
三、形位精度设计
4.形位公差值的确定
确定形位公差值的方法有类比法和计算法两种。 1)同一要素的形状公差值应小于其定向定位公差值;跳 动公差具有综合控制的性质,因此回转表面及其素线的形 状公差值和定向、定位公差值均应小于相应的跳动公差值 ;同一要素的圆跳动公差应小于全跳动公差。
实验三:用摆差测定仪测量跳动误差
三、实验内容
实验三:用摆差测定仪测量跳动误差
四、形状与位置精度的检测
三坐标测量仪
轴的体外 作用尺寸
孔的体外作用尺寸(mating size for hole):在接合面全 长上,与实际孔内接的最大 理想轴的尺寸。
孔的体外 作用尺寸
d
fe
D fe
一、基本概念 2、最大实体极限、最小实体极限
最大实体极限(maximum material limit,MML):对应于 孔或轴具有允许的材料量为最多时的极限尺寸。 最小实体极限(minimum material limit,LML):对应于 孔或轴具有允许的材料量为最少时的极限尺寸。
实际要素在最大实体状态下的尺 寸,称为最大实体尺寸( maximum material size,MMS) 。内表面(孔)和外表面(轴) 的最大实体尺寸:
D M D m in , d M d m ax
D L D m ax , d L d m in
二、形位公差与尺寸公差的关系
2.独立原则
三、形位精度设计
4.形位公差值的确定
形位公差的未注出值,GB/T1184-1996规定了三个公差等 级—H、K、L, 在图样中可标注:未注形位公差按GB/T 1184—K ,各形位公差项目的值均有表格供查(P76-77) 表4-2——4-5
各形位公差等级的数值如表4-6——4-9
四、形状与位置精度的检测
一、基本概念
3)最大实体状态与最大实体 尺寸
实际要素在给定长度上处处位于 极限尺寸之内,并具有允许的材 料量为最多时的状态,称为最大 实体状态(maximum material condition,MMC)。
4)最小实体状态与最小实体 尺寸
实际要素在给定长度上处处位于 极限尺寸之内,并具有允许的材 料量为最少时的状态,称为最小 实体状态(least material condition , LMC)。 实际要素在最小实体状态下的尺 寸,称为最小实体尺寸(least material size,LMS)。内表面 (孔)和外表面(轴)的最小实 体尺寸:
独立原则(independence principle,IP)是指设计图样上给 定的形位公差和尺寸公差相互无关,应分别满足要求的一种 公差原则。
Ø0.01
含义:轴的直线度误差不允许大于Ø0.01mm,不受尺 寸公差带限制;实际尺寸可在Ø19.079~Ø20mm范围内 变动,不受轴线直线度公差带影响。
(a)
二、形位公差与尺寸公差的关系—相关要求
4.最大实体要求
若可逆要求用于MMR时其动态公差带图
— Φ 0.1
M R
(c)
(d)
二、形位公差与尺寸公差的关系—相关要求 5.可逆要求
采用最大实体要求和最小实体要求时,只允许尺寸公差补偿 给形位公差。而可逆要求(reciprocity requirement,RR) 是在不影响零件功能的前提下,当被测要素的形位误差值小 于给定的形位公差时,允许其相应的尺寸公差增大的一种相 关要求。
第七讲 形状和位置精度(三)
本讲讨论如下内容: 一、基本概念
二、形位公差与尺寸公差的关系
三、形位精度设计 四、形状与位置精度的检测
一、基本概念 1.轴的体外作用尺寸、孔的体外作用尺寸
轴的体外作用尺寸(mating size for shaft):在接合面 全长上,与实际轴外接的最 小理想孔的尺寸。
三、形位精度设计
2.公差原则与相关要求的应用
1)独立原则的应用 独立原则是进行几何精度设计的一种基本公差原则,应用 最为广泛。无论精度高低均可采用独立原则。
对形位精度要求严格,需独立加以控制而不允许受尺寸影 响的要素。
形位和尺寸精度要求差距较大 形位要求与尺寸要求本身无必然联系的要素。 形位要求与尺寸要求均较低的非配合要素。
四、形状与位置精度的检测
4.平面度误差的评定——测量方法
基准平面
待测平面
4.平面度误差的评定——测量方法
相对基面的z值向最小条件平面变换
z值坐标变换后增量与坐标x和y的值成正比
四、形状与位置精度的检测
4.平面度误差的评定
基面旋转:为使理想平面包容所有的点,需要对 基面进行旋转。P82
三、实验内容
1.形状误差的评定原则
最小条件:被测实际要素相对于理想要素的最大变动量为最小。 对于轮廓要素, 符合最小条件的 理想要素处于实 体之外并与被测 实际要素相接触 ,使被测实际要 素对它的最大变 动量为最小。
四、形状与位置精度Байду номын сангаас检测
1.形状误差的评定原则
最小条件:被测实际要素相对于理想要素的最大变动量为最小。 对于中心要 素,符合最 小条件的理 想要素穿过 实际中心要 素,使实际 要素对它的 最大变动量 为最小。