欧美模具的基本要求
欧美模具的基本要求

欧美模具的基本要求1. 模胚:采用“LKM”模架。
2. 导柱倒装(前模导柱,后模导套)。
3. 面板和A板之间必须有两枚管钉作管位。
4. 顶针板必须要有导柱(即中托司)。
5. 钢材:常用加硬材料:LKM2083、LKM2344、LKM2767.一般加硬至52~54HRC。
6. 定位环:定位环要高出面板4mm,若有隔热板时定位环要高出隔热板4mm。
常用定位环直径:Ø90、Ø100、Ø110、Ø120、Ø125、Ø150、Ø160。
7. 唧嘴圆弧:常用FLAT(即平的)和R15.5 两种。
唧嘴圆弧的开口最小保证:Ø3.5mm。
8. 顶针、司筒采有“DME”“HASCO”标准。
9. 水口:常用潜水和热流道(常用DME、MasterFlow)10. 滑块: 滑块要做定位、限位.(常用波珠螺丝、弹簧定位,杯头螺丝限位)。
11. 压块:压块螺丝常用杯头螺丝和平头螺丝。
12. 斜顶:斜顶要做导滑块和耐磨块,材料采用青铜。
13. 连接块:见图示。
14. 运水塞:采有“HASCO”的1/4”BRS和1/8”BRS两种。
15. 运水内接孔:模具上下要加工, 模具左右不要加工.常用规格:Ø20x20、Ø25x20.。
16. 标识:常有零件名称、零件号、公司名称、型腔标识、材料标识、可回收标识、日期章。
17. 模具表面要求:Sparkerusion(火花纹)、Polished(省模)、Photo etched (蚀纹)。
18. 模胚A、B板之间要有锁模块(两个)。
19. 模具包装采用黄油、透明塑胶袋、消毒木箱。
20 模具标签:模具号、零件号、产品名称、制造日期、模具重量。
浇注系统:1. 所有水口都必须自动切断,自动掉落.浇口一般采用”潜水”或热流道,如采用顶针位进胶,必须如图例2. 唧嘴必须用加硬材如SKD62,硬度必须HRC52左右, 唧嘴圆弧有”平”; “R15.5”等,公差为(+1.0,-0.5),唧嘴圆弧的开口大小最小应保证:3.5mm.(离端面的参考尺寸为3mm)3. 唧嘴如自己制作,请用加硬材料如” ASSAB8407, LKM2767,LKM2083”等,硬度必须HRC52左右,并且内孔一定要抛光,4. 定位环尺寸有“ø90”;”ø110” ; “ø125” ;”ø160” ,离码模板高度一般为: 4.0mm,公差为(+/-0.5) , 详情请见”技术要求”,最大倒角为1 X 1mm5. 浇口离零件胶位的最小距离应保证:1.5mm6. 如用可旋转浇口,分流道形状请用“梯形”7. 胶口设计请注意布局合理,顶出平衡.顶出系统:1. 顶针应采用HASCO标准, 顶针孔应有避空位, 前端配合位长度可设计为15mm.在顶针板内每边至少须避空0.25mm,见图例. 顶针必须能用手轻松可推动.顶针离型芯边缘的距离最小为:1mm2. 特别是”扁顶”需要加避空位.3. 顶针板必须有四根导柱,不需用弹簧. 并且在顶针板上固定一个如”M16”的连接块, 见图,螺纹孔一定要顶针板垂直. 如模具比较大,必须采用球轴承,如HASCO Z系列.4. 顶针顶出时不能有变形或翘起.即整个零件需平衡顶出.5. 顶针痕所形成的阶梯通常必须控制在0.10mm以内.冷却系统:1. 冷却尽量采用大的管径”如能用”ø10”,就必须用” ø10”,不能用” ø8”.2. 冷却管径最小可采用” ø3”3. 所有产品热量集中的地方,如深孔,深槽, 滑块.原则是尽量加多运水.如果太小或窄,则需考虑用”铍青铜”做镶块.4. 冷却管端部沉孔和镙纹孔必须同心,而且不能钻歪.5. 堵水螺栓必须为英制1/8BSP或1/4BSP,外形为锥行。
美制汽车模具设计规范

第八步,模具排气处理。
模具排气分为整圈排气和均匀排气 两种,有一种客人还增加角落排气。
一般比较常用的为整圈排气。
第九步,其他注意事项。
A,模板材料一般采用1020或1050, AB板采用P20,入子一般用P20与 H13两种材料。
B,撑头排布面积一般应超过产品投 影面积一半,撑头壁空一般在5MM 以上。如果撑头排布有困难,需加 厚B板,保证产品底到B板底在100 以上。
PL面若没有处在AB板的正中间,需考 虑在内模料周围做整圈加工以利于排气。
若AB板避空的范围过大, 为防止模具变形,需添加 承压板。一般必须保证在 导柱的位置有承压片。
若插破面积过大,也 应考虑添加耐磨片, 以保证精度和寿命。
斜顶一般常用两种规格,一种小斜顶,采用 圆弧导向件,可调整为任意角度,DME和 PROGRESSIVE有标准件提供.
司筒长度如过长需加接 长版本,不可用非标。
若模具包含斜顶顶出则 模具一般不采用弹弓, 因为要防止斜顶卡死。 所以英制模具的斜顶一 般都采用导套形式,以 保证滑动顺畅。
弹弓计算公式需直接在 剖面图上表达,一般英 制弹弓压缩比率不允许 超过35%,若有超长弹 弓超出范围则应考虑采 用氮气弹弓。 有斜顶和顶块的模具都 必须在回针底部加小弹 弓。 顶块机构设置与斜顶方 式一样,也许导杆导套 与底座,尽可能采用标 准件。
第四步,注塑机信息处理。
隔离柱大小
注塑机信息比较重要,客人一般会指定排号 与资料,其中包括架模方式,(有部分机型 为自动架模)隔离柱大小,注塑孔尺寸,KO 孔规格,码模板尺寸。
注塑孔尺寸 及对应法兰 与灌嘴规格。 一般非客户 指定的话采 用DME标准 件。
KO孔规格, 一般延伸块 采用下图两 种规格,若 模具较大需 有3个公制 试模孔时, 需考虑加椭 圆型KO孔。
欧美模具规范

歐美模具設計規範1. 模胚:採用“LKM”模架。
2. 導柱倒裝(前模導柱,後模導套)。
3. 面板和A板之間必須有兩枚管釘作管位。
4. 頂針板必須要有導柱(即中托司)。
5. 鋼材:常用加硬材料:LKM2083、LKM2344、LKM2767.一般加硬至52~54HRC。
6. 定位環:定位環要高出面板4mm,若有隔熱板時定位環要高出隔熱板4mm。
常用定位環直徑:Ø90、Ø100、Ø110、Ø120、Ø125、Ø150、Ø160。
7. 唧嘴圓弧:常用FLAT(即平的)和R15.5 兩種。
唧嘴圓弧的開口最小保證:Ø3.5mm。
8. 頂針、司筒采有“DME”“HASCO”標準。
9. 水口:常用潛水和熱流道(常用DME、MasterFlow)10. 滑塊: 滑塊要做定位、限位.(常用波珠螺絲、彈簧定位,杯頭螺絲限位)。
11. 壓塊:壓塊螺絲常用杯頭螺絲和平頭螺絲。
12. 斜頂:斜頂要做導滑塊和耐磨塊,材料採用青銅。
13. 連接塊:見圖示。
14. 運水塞:采有“HASCO”的1/4”BRS和1/8”BRS兩種。
15. 運水內接孔:模具上下要加工, 模具左右不要加工.常用規格:Ø20x20、Ø25x20.。
16. 標識:常有零件名稱、零件號、公司名稱、型腔標識、材料標識、可回收標識、日期章。
17. 模具表面要求:Sparkerusion(火花紋)、Polished(省模)、Photo etched (蝕紋)。
18. 模胚A、B板之間要有鎖模組(兩個)。
19. 模具包裝採用黃油、透明塑膠袋、消毒木箱。
20. 模具標簽:模具號、零件號、産品名稱、製造日期、模具重量。
(模架圖例)澆注系統:1. 所有水口都必須自動切斷,自動掉落.澆口一般採用”潛水”或熱流道,如採用頂針位進膠,必須如圖例.2. 唧嘴必須用加硬材如SKD62,硬度必須HRC52左右, 唧嘴圓弧有”平” ; “R15.5”等,公差爲(+1.0,-0.5), 唧嘴圓弧的開口大小最小應保證:3.5mm.(離端面的參考尺寸爲3mm)3. 唧嘴如自己製作,請用加硬材料如” ASSAB8407, LKM2767,LKM2083”等,硬度必須HRC52左右,並且內孔一定要抛光,4. 定位環尺寸有“ø90”;”ø110” ; “ø125”;”ø160” ,離碼模板高度一般爲: 4.0mm,公差爲(+/-0.5) , 詳情請見”技術要求”,最大倒角爲1 X 1mm5. 澆口離零件膠位元的最小距離應保證:1.5mm6. 如用可旋轉澆口,分流道形狀請用“梯形”7. 膠口設計請注意佈局合理,頂出平衡.(澆口圖例)(定位環圖例)(唧嘴圖例)頂出系統:1. 頂針應採用HASCO標準, 頂針孔應有避空位, 前端配合位長度可設計爲15mm.在頂針板內每邊至少須避空0.25mm,見圖例. 頂針必須能用手輕鬆可推動.頂針離型芯邊緣的距離最小爲:1mm2. 特別是”扁頂”需要加避空位.3. 頂針板必須有四根導柱,不需用彈簧. 並且在頂針板上固定一個如”M16”的連接塊, 見圖,螺紋孔一定要頂針板垂直. 如模具比較大,必須採用球軸承,如HASCO Z系列.4. 頂針頂出時不能有變形或翹起.即整個零件需平衡頂出.5. 頂針痕所形成的階梯通常必須控制在0.10mm以內.(頂針避空圖例)(連接塊圖例) 冷卻系統:1. 冷卻儘量採用大的管徑”如能用”ø10”,就必須用”ø10”,不能用”ø8”.2. 冷卻管徑最小可採用”ø3”3. 所有産品熱量集中的地方,如深孔,深槽, 滑塊.原則是儘量加多運水. 如果太小或窄,則需考慮用”鈹青銅”做鑲塊.4. 冷卻管端部沈孔和鏍紋孔必須同心,而且不能鑽歪.5. 堵水螺栓必須爲英制1/8BSP或1/4BSP,外形爲錐行。
模具厂培训-工程通用名词国外产品品质要求

Design Stren gth
UK
BS5950:2000
grade S275 grade S355 grade S460
20500 20500 20500 20500 20500 20500 20500 20500 20500 160000 160000 170000 170000 200000 205000 20500
2)英国(UK)标准模具材料代号 记号 UBT :T型钢(梁用) UCT :T型钢(柱用) CUB、CUC、CSJ :工字钢 其中RHS、SHS、CHS有热轧和冷轧,其余 只有热轧钢
3)欧洲标准(EN)模具材料代号
记号 HX、HL、HE、HD、 HP、DIL、IPE :热轧工字 IPE :斜翼缘工字 U、UPN :平翼缘槽钢 UAP :斜翼缘槽钢 EL :等边角铁 UL :不等边角铁
USA
ASTM
grade A36 grade A529 grade A441 A572 grade 42 A572 grade 50 A572 grade 60 A572 grade 65 grade A242 grade A588
Duplex grade 2205 Stainless
6.图纸识别
300 410 480 400 414 483 414 448 517 552 483 483 550
200 250 350 248 290 345 290 345 414 448 345 345 450
200 250 350 248 345 290 345 290 345 414 345 345 450
410 490 550 430 490 550 430 490 550 500 480 510 490 550 340 494
简述模具制造的基本要求

简述模具制造的基本要求
模具制造的基本要求包括以下几个方面:
1. 设计要求:模具设计需要满足产品的功能要求和外形尺寸要求,确保产品的质量和性能。
设计中需要考虑材料选择、模具结构设计、工艺能力等方面的要求。
2. 制造精度要求:模具制造需要按照设计要求进行加工制造,保证模具的准确性和精度。
制造过程中需要注意尺寸偏差、几何形状误差、表面光洁度等方面的要求。
3. 寿命要求:模具的寿命直接影响到产品的成本和性能。
因此,在制造过程中需要选择合适的材料,进行适当的热处理和表面处理,以提高模具的硬度、抗磨性和耐腐蚀性。
4. 制造周期要求:模具制造的周期时间对产品的开发和生产进度有重要影响。
制造过程中需要合理安排工序和生产工艺流程,确保模具能够按时完成制造。
5. 成本控制要求:模具制造的成本影响着产品的竞争力。
制造过程中需要合理控制材料和加工成本,并在保证质量的前提下优化模具的结构和制造工艺,以降低成本。
总之,模具制造的基本要求是设计合理、精度高、寿命长、制造周期短且成本控制合理。
这样才能满足产品的制造需求,提高生产效率和产品质量。
北美伊莱克斯模具要求

北美伊莱克斯模具要求1.最初的设计图纸需要表达产品外观面要求,模胚尺寸,顶针排位,运水图,产品的分型线,擦穿位,浇口位及尺寸,钢材牌号及硬度(国际牌号),产品问题点等内容2.最后确认的模图需要产品前后模的外观面要求,模具重量,流道尺寸,浇口位及尺寸,国际钢材及硬度,顶出系统及行位,斜顶等抽芯结构,可换镶件位置,冷却系统及产品的最终确认。
3.模具一般要求全自动生产,当产品不能自动下落及生产时,需要特别指出以便客户设计确认4.每套模具需要做完整的MOLDFLOW分析报告,以便确认浇口,注射成型工艺,变形,冷却及产品外观缺陷等方面的改善措施5.模图的BOM表需要表达零件数,名称,材料,热处理硬度,供应商及客户的产品名称及编号6.客户要求用ASSAB(一胜百)的材料做模芯。
其常用对应胶料的钢材及硬度要求见电子文档第23页7.模胚A.B板间的导套需要用自润滑铜导套。
顶针板的中托司也是用铜导套8.每块模板四面都必须有平衡吊孔。
确保吊孔不会穿运水,油路及螺丝孔9.模具的顶针板上下侧需要防尘板设计,锁模片,撬模坑,支撑脚的设计和JUNGWOO要求一致。
当叽嘴沉入模板内50MM以上时,需要将定位圈的内孔设计在85MM以上以便射嘴的伸入。
模具走模时表面涂漆处理。
10.热流道接线插头DME品牌。
热流道板需要带单独冷却水设计。
还要做热流道接线示意图牌子。
插头是用24针点的款式,冷流道只需要开在后模侧,采用锥台式剖面,单边的斜度为7度以上。
还需设计冷料井及排气。
流道的顶出必须符合机械手取件。
11.顶针板需要在水平及垂直的方向上设计KO棍,按照英制排位。
顶针及司筒必须用标准的DME或ROGRESSIVE零件。
当需要非标设计时,必须特别指出及制作备用件。
产品表面为曲面时,顶针司筒需要设计防转。
柱位需要设计司筒顶出。
顶针及司筒的封胶导向长度一般设计为该针直径的2倍。
顶针及司筒的避空孔(扩孔)尺寸只能比对应的顶针加大0.8 MM.当采用推块的设计时,推块的硬度比模芯的硬度相差HRC10左右。
美国模具设计准则

Table of ContentsI. Purpose 目的II. Scope 适用范围III. Die classification 模具类型IV. Metal stamping dies-General Requirements 五金模具一般要求Die design and construction data sheet 模具设计及组装时间表Die design approval 模具设计审核Die design ownership 模具设计所有权Die noise 模具噪音Die design responsibilities 模具设计责任Die performance 模具性能V. Die design criteria 模具设计标准A. Preferred components 优先配件B. Production material 产品材质C. Calculating operating tonnage of die 模具工作吨位D. General die life and construction 模具寿命及构造E. Safety 安全F. Scrap removal 废料移出装置G. Die sets 模具安装H. Die mountingI. Maintenance requirements 维修要求J. Die lubricants 模具润滑K. Die protection 模具保护装置L. Shear clearances 冲裁间隙M. Stock guiding and control 材料导向及定位N. Die material 模具材料O. Parallels 垫脚P. Dowels 合销Q. Punches, buttons, and retainers 冲头,镶件以及固定器R. Springs 弹簧S. Strippers 脱料装置T. Nitrogen systems 氮气系统U. Positive knockouts 正面取出V. Pressure pins 顶料销X. Forming and drawing dies 成型及拉伸模具Y. Cam and slide type diesVI. Stamping and marking 钢印及标记VII. Tryout and approval to ship 试模及船运VIII. Tryout, recertification, and final approval 试模,证明及最终承认IX. Payment terms 付款条约X. Substitutions 备件XI. Changes 设变Any deviation from this Die Building Requirements & Specifications will require a written request from vendor to the Su-dan Corporation Project Engineer.如有任何违背本份模具制造要求及规范,供应商都需向 Su-dan项目工程师提供一份书面要求。
模具制造的基本要求及特点

影响模具精度的主要因素有:
①制品的精度要求 制品的精度要求高,模具工作零件的精度就高。 模具精度的高低不仅对制品精度有直接影响,而对 模具生产周期、生产成本都有很大影响。 ②模具加工手段 模具加工设备的精度、自动化程度是保证模具 精度的基本条件。模具精度主要依赖模具加工设备。 比如慢走丝线切割加工的模具比快走丝线切割 加工的模具精度要高。
模具结构、模具材料、模具标准化程度和加工 手段。材料费在模具生产成本中约占25%~30%, 复杂模具加工费高,材料费在模具生产成本中约占
20%~25%,估算模具成本一般为材料费的3~4倍。 模具特别复杂的,成本为材料费的5倍。
模具材料类别的选择应与模具寿命要求相适应。 模板的厚度应与模具精度及制品批量相适应。应 采取各种措施充分发挥材料的效能。 模具成本很大程度由模具设计人员决定,因此 模具设计人员应有成本意识。 选择加工设备时应与零件精度要求相适应。如慢 走丝线切割加工费是快走丝线切割加工费的8~10 倍;中走丝线切割加工费是快走丝线切割加工费的 2~3倍;对表面粗糙度值小,但精度不是十分高的 模具零件,如塑料模的型芯可采用中走丝线切割加 工。
影响制模周期的主要因素: ①模具标准化程度 大量采用模具标准件和标准模坯可显著缩短制模 周期。(因为标准件可直接在市场采购)
②模具企业专门化程度
生产本企业最擅长的模具类型,做自己最擅长的 加工,搞协作化生产,可缩短制模周期。 (将利润低的普通加工发外加工,自己专门做数控 加工、特种加工和模具装配等技术含量多,附加值 高的工序,这样不仅可缩短制模周期,而且可多做 模具获得更多利润。)
4、模具寿命
模具的寿命是指模具保证产品零件质量的前提下, 所能加工制件的总数量,它包括刃口多次修磨和易损 件更换后的寿命。模具的寿命应与制品产量相适应, 模具寿命对模具制造成本有影响。 模具寿命主要受模具材料和模具结构的制约。 模具材料是根据模具寿命要求或制品生产批量来选择。 普通模具工作零件通常选用合金工具钢Cr12或 Cr12MoV。长寿命模具工作零件通常选用粉末高速 钢或硬质合金。
美国模具五大技术标准介绍【说明解析】
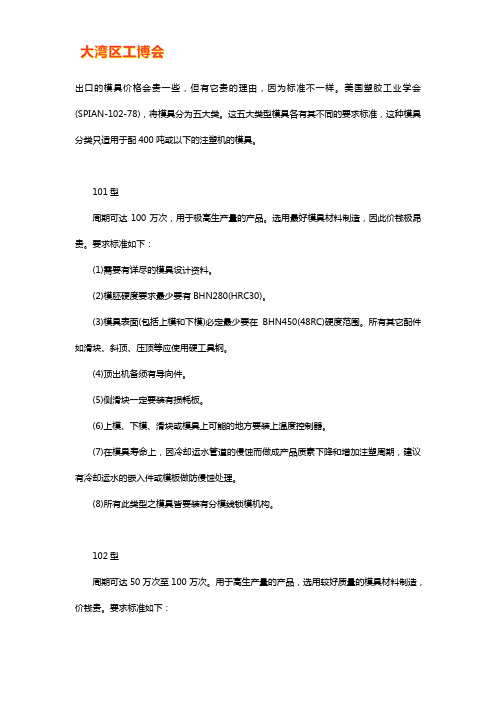
出口的模具价格会贵一些,但有它贵的理由,因为标准不一样。
美国塑胶工业学会(SPIAN-102-78),将模具分为五大类。
这五大类型模具各有其不同的要求标准,这种模具分类只适用于配400吨或以下的注塑机的模具。
101型周期可达100万次,用于极高生产量的产品。
选用最好模具材料制造,因此价钱极昂贵。
要求标准如下:(1)需要有详尽的模具设计资料。
(2)模胚硬度要求最少要有BHN280(HRC30)。
(3)模具表面(包括上模和下模)必定最少要在BHN450(48RC)硬度范围。
所有其它配件如滑块、斜顶、压顶等应使用硬工具钢。
(4)顶出机备须有导向件。
(5)侧滑块一定要装有损耗板。
(6)上模、下模、滑块或模具上可能的地方要装上温度控制器。
(7)在模具寿命上,因冷却运水管道的侵蚀而做成产品质素下降和增加注塑周期,建议有冷却运水的嵌入件或模板做防侵蚀处理。
(8)所有此类型之模具皆要装有分模线锁模机构。
102型周期可达50万次至100万次。
用于高生产量的产品,选用较好质量的模具材料制造,价钱贵。
要求标准如下:(1)需要有详尽的模具设计资料。
(2)模胚硬度要求最少要有BHN280(HRC30)。
(3)上模和下模表面硬度应在BHN540(HRC48)范围。
所有其它功能配件应做热处理。
(4)上模、下模、滑块或模具上可能的地方装上温度控制器。
(5)所有此类型之模具皆要装有分模线锁模机构。
(6)以下项目可能性需要或不需要,取决于最后生产数量的考虑。
建议这些项目同样做一份确认的报价单。
顶出导向件滑块损耗板已做防侵蚀处理的控制器管道电镀上模103型周期可达50万次。
用于中生产量的产品,价钱合理。
要求标准如下:(1)需要有详尽的模具设计资料。
(2)模胚硬度要求最少要有BHN165(HRC17)。
(3)上模和下模必定最少有BHN280(HRC30)硬度或以上。
(4)所有其它配件自由选择。
104型周期可达10万次。
用于低生产量的产品,模具材料耐磨性不高,价钱低于一般合理水平。
模具的基本要求

下一页 返回
第三节模具安全
裸露在外的热模具零件,绝缘保护不好的电接头;模具的安装、 调整、搬运不当,尤其是手工起重模具;压力机的安全装置发 生故障或损坏;在生产中,缺乏适当的交流和指导文件。
目前新生产的压力机,国家规定都必须附设安全保护装置才 能出厂。从事故发生的统计数据表明:在冲压生产中发生的人 身事故比一般机械加工多。压力机用的安全保护装置有安全 网、双手操作机构、摆杆或转板护手装置、光电或安全保护 装置等。在保障冲压加工的安全性方面,除压力机应具有安 全装置外,还必须使所设计的模具具有杜绝人身事故发生的 合理结构和安全措施。
(2)模具材料的加工工艺性能要求 具有良好的热加工工艺性 能,包括锻造、铸造、焊接、热处理等加工性能;具有良好的 冷加工工艺性能,包括切削、研磨、抛光等加工性能;具有良 好的特种加工工艺性能,包括电火花加工、化学与电化学加 工等加工性能。
上一页 下一页 返回
第二节模具寿命与模具材料
3.模具材料的选用原则 模具的种类很多,工作条件千差万别,对模具材料性能的要
上一页 下一页 返回
第三节模具安全
二、提高模具安全的措施 在设计模具时,不仅要考虑到生产效率、制件质量、模具成
模具的基本要求

若模具在使用中出现工作条件很差、安装、操作和保护不当 等原因,会导致模具加速失效。
上一页 下一页 返回
第二节模具寿命与模具材料
2.影响模具寿命的因素及提高寿命的措施 模具因为磨损或其他形式失效终至不可修复而报废之前所成
(3)模具热处理对模具寿命的影响 模具的热处理质量对模具 的性能与使用寿命影响很大。因为热处理的效果直接影响着 模具用钢的硬度、耐磨性、抗咬合性、回火稳定性、耐冲击 以及抗腐蚀性,这些都是与模具寿命直接有关的性质。通过 热处理可以改变模具工作零件的硬度,而硬度对模具寿命的 影响是很大的。硬度提高,韧性一般要降低,而抗压强度、 耐磨性、抗赫合能力则有所提高。
上一页 下一页 返回
第二节模具寿命与模具材料
对冷冲压制件所用的钢板或其他原材料,应在满足使用要求 的前提下,尽量采用成形性能好的材料,以减少冲压变形力, 改善模具工作条件。另外,保证材料表面质量和清洁对任何 冲压工序都是必要的。
对塑料制件而言,不同塑料品种的模塑成型温度和压力是不 同的。模塑过程中产生的腐蚀性气体会腐蚀模具表面。因此, 应在满足使用要求的前提下,尽量选用模塑工艺性能良好的 塑料来成型制件,这样既有利于模塑成型,又有利于提高模 具寿命。
上一页 下一页 返回
第一节模具的精度与表面质量
2.模具表面质量的确定 模具表面质量主要以模具零件的表面粗糙度衡量。对一般没
有标准化的模具工作零件或成形零件,其工作型面的表面粗 糙度要求可参考表3-1确定。不同表面粗糙度等级在模具零件 中的使用范围可参考表3 -2。
上一页 返回
第二节模具寿命与模具材料
谈谈客户对模具加工方面的要求
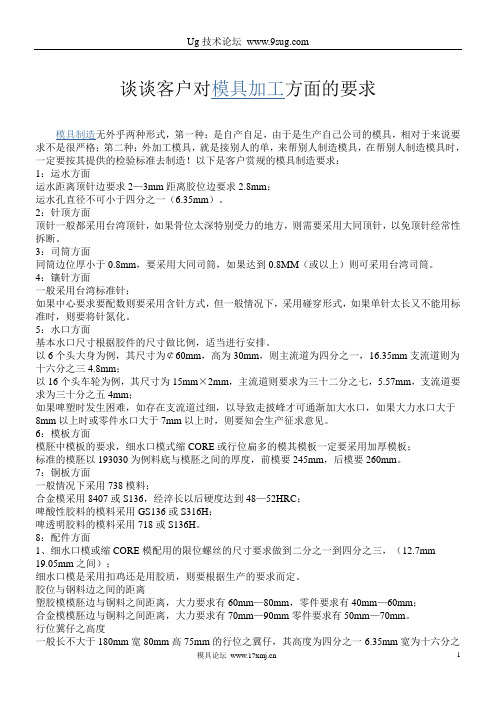
谈谈客户对模具加工方面的要求模具制造无外乎两种形式,第一种:是自产自足,由于是生产自己公司的模具,相对于来说要求不是很严格;第二种:外加工模具,就是接别人的单,来帮别人制造模具,在帮别人制造模具时,一定要按其提供的检验标准去制造!以下是客户赏规的模具制造要求:1:运水方面运水距离顶针边要求2—3mm距离胶位边要求2.8mm;运水孔直径不可小于四分之一(6.35mm)。
2:针顶方面顶针一般都采用台湾顶针,如果骨位太深特别受力的地方,则需要采用大同顶针,以免顶针经常性拆断。
3:司筒方面同筒边位厚小于0.8mm,要采用大同司筒,如果达到0.8MM(或以上)则可采用台湾司筒。
4:镶针方面一般采用台湾标准针;如果中心要求要配数则要采用含针方式,但一般情况下,采用碰穿形式,如果单针太长又不能用标准时,则要将针氮化。
5:水口方面基本水口尺寸根据胶件的尺寸做比例,适当进行安排。
以6个头大身为例,其尺寸为¢60mm,高为30mm,则主流道为四分之一,16.35mm支流道则为十六分之三4.8mm;以16个头车轮为例,其尺寸为15mm×2mm,主流道则要求为三十二分之七,5.57mm,支流道要求为三十分之五4mm;如果啤塑时发生困难,如存在支流道过细,以导致走披峰才可通渐加大水口,如果大力水口大于8mm以上时或零件水口大于7mm以上时,则要知会生产征求意见。
6:模板方面模胚中模板的要求,细水口模式缩CORE或行位扁多的模其模板一定要采用加厚模板;标准的模胚以193030为例料底与模胚之间的厚度,前模要245mm,后模要260mm。
7:铜板方面一般情况下采用738模料;合金模采用8407或S136,经淬长以后硬度达到48—52HRC;啤酸性胶料的模料采用GS136或S316H;啤透明胶料的模料采用718或S136H。
8:配件方面1、细水口模或缩CORE模配用的限位螺丝的尺寸要求做到二分之一到四分之三,(12.7mm19.05mm之间);细水口模是采用扣鸡还是用胶质,则要根据生产的要求而定。
模具的基本要求
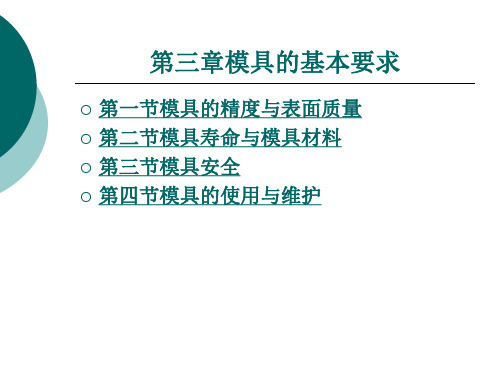
上一页 下一页 返回
第二节模具寿命与模具材料
第三章模具的基本要求
第一节模具的精度与表面质量 第二节模具寿命与模具材料 第三节模具安全 第四节模具的使用与维护
第一节模具的精度与表面质量
一、模具精度与表面质量的概念 1.模具精度 模具精度可分为模具零件本身的精度和发挥模具效能所需的
精度。如凸模、凹模、型芯等零件的尺寸精度、形状精度和 位置精度是属于模具零件本身的精度;各零件装配后,面与面 或面与线之间的平行度、垂直度,定位及导向配合等精度, 都是为了发挥模具效能所需的精度。模具的精度越高,则成 形的制件精度也越高。今后随着模具加工技术手段的提高, 模具精度会有大的提高,模具工作零件或成形零件的互换性 生产将成为现实。
上一页 下一页 返回
第一节模具的精度与表面质量
三、模具精度与表面质量的确定 1.模具精度的确定 模具精度一般由模具零件精度及模架的精度决定。对凸模、
型芯、凹模等模具工作零件或成形零件的型面尺寸精度,一 般可根据成形制件的尺寸精度要求按如下经验方法确定。 冲裁模:凸、凹模按“分别加工法”制造时,普通冲裁取 IT6~IT7,精密冲裁取IT5~IT6;凸、凹模按“实配加工法”制 造时,基准凸模或凹模的制造偏差取冲裁制件公差的1/4。弯 曲模:按IT7~ITS取值。拉深模:按ITS~IT10取值。塑料模:一 般取制件公差的1/4~1/6。压铸模:一般取铸件公差的1/4~1/5。
模具种类繁多,损坏部位也各不相同,但具体的失效形式归 纳起来分为:磨损失效、变形失效、断裂失效、啃伤失效、热 疲劳失效、腐蚀失效等。
国外模具标准
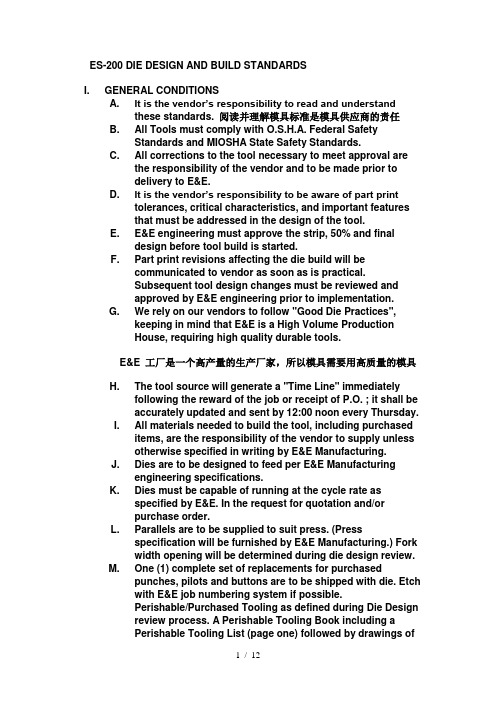
ES-200 DIE DESIGN AND BUILD STANDARDSI. GENERAL CONDITIONSA. It is the vendor’s responsibility to read and understandthese standards. 阅读并理解模具标准是模具供应商的责任B. All Tools must comply with O.S.H.A. Federal SafetyStandards and MIOSHA State Safety Standards.C. All corrections to the tool necessary to meet approval arethe responsibility of the vendor and to be made prior todelivery to E&E.D. It is the vendor’s responsibility to be aware of part printtolerances, critical characteristics, and important featuresthat must be addressed in the design of the tool.E. E&E engineering must approve the strip, 50% and finaldesign before tool build is started.F. Part print revisions affecting the die build will becommunicated to vendor as soon as is practical.Subsequent tool design changes must be reviewed andapproved by E&E engineering prior to implementation.G. We rely on our vendors to follow "Good Die Practices",keeping in mind that E&E is a High Volume ProductionHouse, requiring high quality durable tools.E&E 工厂是一个高产量的生产厂家,所以模具需要用高质量的模具H. The tool source will generate a "Time Line" immediatelyfollowing the reward of the job or receipt of P.O. ; it shall beaccurately updated and sent by 12:00 noon every Thursday.I. All materials needed to build the tool, including purchaseditems, are the responsibility of the vendor to supply unlessotherwise specified in writing by E&E Manufacturing.J. Dies are to be designed to feed per E&E Manufacturing engineering specifications.K. Dies must be capable of running at the cycle rate asspecified by E&E. In the request for quotation and/orpurchase order.L. Parallels are to be supplied to suit press. (Pressspecification will be furnished by E&E Manufacturing.) Forkwidth opening will be determined during die design review.M. One (1) complete set of replacements for purchasedpunches, pilots and buttons are to be shipped with die. Etchwith E&E job numbering system if possible.Perishable/Purchased Tooling as defined during Die Designreview process. A Perishable Tooling Book including aPerishable Tooling List (page one) followed by drawings ofeach perishable component to correlate with the list must be supplied with aforementioned set of replacements uponreceipt of tool at E&E.N. All perishable details, such as cutting and forming sections are to be completely detailed to allow for interchanging.1. Detail prints are to be updated as changes are madeduring assembly and tryout.所有的易损件,比如切边,成形部件要完全说明其材质等详细信息以便互换。
欧美的模具设计标准

欧美的模具设计标准模具设计是现代工业中不可或缺的一环,其作用是将产品的设计图纸转化为实际的产品,为工业生产提供了重要的支持。
在模具设计中,标准化是一个非常重要的概念,因为模具的标准化可以提高生产效率和产品质量,同时也可以降低制造成本。
欧美地区一直是模具设计标准化的先进地区之一,本文将介绍欧美地区的模具设计标准。
1. 模具设计的标准化模具设计的标准化是指在设计、制造和检验过程中,应遵循的规范和标准。
这些规范和标准可以保证模具的精度和质量,同时也可以提高制造效率和降低成本。
欧美地区的模具设计标准化非常严格,其标准涵盖了模具的所有方面,包括材料、尺寸、几何形状、加工工艺等。
2. 欧美地区的模具设计标准欧美地区的模具设计标准包括了许多国际标准和行业标准。
下面介绍一些常见的标准:(1)ISO标准ISO(国际标准化组织)是国际上最大的标准化组织之一,其制定的标准被广泛应用于各个领域,包括模具设计。
ISO制定了许多与模具设计相关的标准,如ISO 2768-1(一般公差)、ISO 286-2(孔和轴的公差)、ISO 8062-3(铸造模具表面粗糙度)、ISO 857-1(模具标准零件)等。
(2)DIN标准DIN(德国工业标准化组织)是德国的标准化组织,其制定的标准被广泛应用于欧洲地区。
DIN制定了许多与模具设计相关的标准,如DIN 16742(模具设计的一般规则)、DIN 8580(制造工艺分类)等。
(3)ASTM标准ASTM(美国材料与试验协会)是美国的标准化组织,其制定的标准被广泛应用于美国地区。
ASTM制定了许多与模具设计相关的标准,如ASTM E18(金属材料的拉伸试验)、ASTM E10(金属材料的硬度试验)等。
(4)JIS标准JIS(日本工业标准)是日本的标准化组织,其制定的标准被广泛应用于日本地区。
JIS制定了许多与模具设计相关的标准,如JIS B 0401(公差及其表示)等。
3. 模具设计标准的应用在模具设计中,标准化的应用非常重要。
模具标准和要求

零件号
零件名
零件尺寸
模 腔 数 量 1+1
模具价格 (含税)
检具 (含 税) 60000
检 具 数 量
潜在模 具 供应商 华威
潜在检 具 供应商 益群
9028197
MOLDING ASM-W/S GARN(LH) A上
928×220×110
445177 120000 67870 80000 409468 400000
– 外观件在开模前均需通过模流分析进行浇口位置、熔接痕、缩痕、翘曲等影响尺 寸和外观质量的因素进行校核和修整,使其对尺寸和外观所造成的影响减至最低 – 对于模流分析中反映出来的问题,一级零部件厂要积极协调模具厂和SGM进行模 具设计和产品原始结构的调整,不能凭侥幸心理,依靠调整注塑工艺过程参数解决 后续的问题,使得问题解决的时间周期过长,并且有些问题永远解决不到位,为以后 的批量生产埋下隐患. – 除华威和延峰伟世通外,模流分析必须通过有资质的申模认可
– SGM认可模具供应商出现问题, SGM直接发布PRR给模具厂 – SGM认可以外模具供应商, SGM发布PRR给一级零部件厂
2.模具供应商评估流程
Step 1 : Tier I presents tool source recommendation including Tier I assessment of the source and completed GM tool source questionnaire Step 2 : GM GPPC conducts tool source assessment (review of questionnaire and onsite evaluation) Document Trail Tool Source Questionnaire Tool Source Assessment
美国JUNGWOO 模具标准

美国JUNGWOO 模具标准。
1.杯头螺丝。
A.所有的杯头螺丝过孔的直径应该比螺丝的直径大1/32”。
B.所有的杯头螺丝的沉头过孔的直径比螺丝杯头大1/32”C.所有的孔都应该有个沉头孔。
2.回针(参考:#21,#2.2)a.回针与“B”板最小的间距为0。
003”b.所有的模具应不少于4根回针,且合模后能很好的接触至“A”板。
c.为了让顶针很好的回位,回针应加弹簧。
d.用弹簧时,每套模具最少应要2个回针上攻牙。
3.导柱。
a.所有的导柱必须有一段合适的配合位。
b.导柱必须比斜导柱先进入。
4.导套。
a.所有的导套必须带托。
b.当导套带托一端在两块板之间没有压住时,需采用平头螺丝压住。
c.所有的导套须加排气。
5.圆顶针和扁顶针。
a.所有的顶针封胶位处需有一段配合位。
b.所有的顶针杯头面须做平防止旋转。
c.在顶针板上,如需要,则多增加一些螺丝。
顶针在前后模的配合位要求。
1.直径在1/2”以下的顶针,配合位要求最小为1/4“最大为1/2“。
2.直径在1/2“以上的顶针,配合位要求最小1/2“最大为1”。
顶针与顶针板的避空。
1.直径1/8“以下的顶针避空共1/64”。
2.超过1/8“的顶针避空为1/32”d.所有的头部深度避空比头部厚度深0.02”e.所有的扁顶针都要有购买清单。
6.销钉。
1.所有固定板加销钉,销钉上做工艺牙。
2.所有的导向块加销钉,以至很好的固定。
3.顶针板不加销钉。
7.中托司。
A 中托司导套采用青铜,在一块板上是轻微的压力配合,另一板上为滑配。
8.垃圾钉。
A 所有的的模具应该要求垃圾钉,厚度在3/16“到4MM。
B.垃圾钉安装方式:直接压入或用螺丝锁。
9.撬模坑:A.所有板在四个角加撬模槽,具有参考每个客户规格或最小深度在“3/16 ,1/4”10.计数器,直身锁。
a。
在B板操作者侧安装计数器。
b.所有模具都必须有直身锁。
11模孔。
a。
所有的板四周都有吊模孔。
深度为直径的1-1/2“b.所有的模具都要有吊模孔在重力中心位置。
- 1、下载文档前请自行甄别文档内容的完整性,平台不提供额外的编辑、内容补充、找答案等附加服务。
- 2、"仅部分预览"的文档,不可在线预览部分如存在完整性等问题,可反馈申请退款(可完整预览的文档不适用该条件!)。
- 3、如文档侵犯您的权益,请联系客服反馈,我们会尽快为您处理(人工客服工作时间:9:00-18:30)。
欧美模具的基本要求
以下为正文内容:
1. 模胚:采用“LKM” 模架。
2. 导柱倒装(前模导柱,后模导套)。
3. 面板和A板之间必须有两枚管钉作管位。
4. 顶针板必须要有导柱(即中托司)。
5. 钢材:常用加硬材料:LKM2083、LKM2344、LKM2767.一般加硬至52~54HRC。
6. 定位环:定位环要高出面板4mm,若有隔热板时定位环要高出隔热板4mm。
常用定位环直径:Ø90、Ø100、Ø110、Ø120、Ø125、Ø150、Ø160。
7. 唧嘴圆弧:常用FLAT(即平的)和R15.5 两种。
唧嘴圆弧的开口最小保证:Ø3.5mm。
8. 顶针、司筒采有“DME”“HASCO”标准。
9. 水口:常用潜水和热流道(常用DME、MasterFlow)
10. 滑块: 滑块要做定位、限位.(常用波珠螺丝、弹簧定位,杯头螺丝限位)。
11. 压块:压块螺丝常用杯头螺丝和平头螺丝。
12. 斜顶:斜顶要做导滑块和耐磨块,材料采用青铜。
13. 连接块:见图示。
14. 运水塞:采有“HASCO”的1/4”BRS和1/8”BRS两种。
15. 运水内接孔:模具上下要加工, 模具左右不要加工.常用规格:Ø20x20、Ø25x20.。
16. 标识:常有零件名称、零件号、公司名称、型腔标识、材料标识、可回收标识、日期章。
17. 模具表面要求:Sparkerusion(火花纹)、Polished(省模)、Photo etched(蚀纹)。
18. 模胚A、B板之间要有锁模块(两个)。
19. 模具包装采用黄油、透明塑胶袋、消毒木箱。
20 模具标签:模具号、零件号、产品名称、制造日期、模具重量。
浇注系统:
1. 所有水口都必须自动切断,自动掉落.浇口一般采用”潜水” 或热流道,如采用顶针位进胶,必须如图例.
2. 唧嘴必须用加硬材如SKD62,硬度必须HRC52左右, 唧嘴圆弧有” 平” ; “ R15.5” 等,公差为(+1.0,-0.5), 唧嘴圆弧的开口大小最小应保证:
3.5mm.(离端面的参考尺寸为3mm)
3. 唧嘴如自己制作,请用加硬材料如” ASSAB8407, LKM2767,LKM2083”等,硬度必须HRC52左右,并且内孔一定要抛光,
4. 定位环尺寸有“ø90”;”ø110” ; “ø125” ;”ø160” ,离码模板高度一般为: 4.0mm,公差为(+/-0.5) , 详情请见”技术要求”,最大倒角为1 X 1mm
5. 浇口离零件胶位的最小距离应保证:1.5mm
6. 如用可旋转浇口,分流道形状请用“梯形”
7. 胶口设计请注意布局合理,顶出平衡.
顶出系统:
1. 顶针应采用HASCO标准, 顶针孔应有避空位, 前端配合位长度可设计为15mm.在顶针板内每边至少须避空0.25mm,见
图例. 顶针必须能用手轻松可推动.顶针离型芯边缘的距离最小为:1mm
2. 特别是”扁顶”需要加避空位.
3. 顶针板必须有四根导柱,不需用弹簧. 并且在顶针板上固定一个如”M16” 的连接块, 见图,螺纹孔一定要顶针板垂直. 如模具比较大,必须采用球轴承,如HASCO Z系列.
4. 顶针顶出时不能有变形或翘起.即整个零件需平衡顶出.
5. 顶针痕所形成的阶梯通常必须控制在0.10mm以内.
冷却系统:
1. 冷却尽量采用大的管径” 如能用”ø10”,就必须用” ø10”,不能用” ø8”.
2. 冷却管径最小可采用” ø3”
3. 所有产品热量集中的地方,如深孔,深槽, 滑块.原则是尽量加多运水.
如果太小或窄,则需考虑用”铍青铜”做镶块.
4. 冷却管端部沉孔和镙纹孔必须同心,而且不能钻歪.
5. 堵水螺栓必须为英制1/8BSP或1/4BSP,外形为锥行。
装配时必须用“乐泰567”胶水,
6. 沉孔之间的距离,沉孔的大小,沉孔的深度,请按“北极光技术要求”沉孔直径和深度公差应控制在(+1,0) 内.
7. 管接头在侧面时,不需沉孔.
8. 隔热板请用4-6个镙钉固定,不要用太多镙钉,以免装卸复杂.
9. 模具上须标明” IN” , “ OUT”, 并定义好编号.
10. 防水圈用HASCO标准
其它
1. 滑块的止位和运动的槽位应为”加硬材料”
2. 日期章背后必须钻一孔, 这样可快速调整日期
3. 不易排气的部位,如薄且深的壁,胫位等 , 如无顶针,则须有排气针.
4. 产品检测报告.(出模前一定给客户)
5. 模具检测报告. (出模前一定给客户)
6. 机器参数. (出模前一定给客户)
7. 最新模具图纸. (出模前一定给客户)
试模要求:
试模必须尽量模仿正常生产状态, 例如加长冷却时间,加长顶出时间等都是不可取的. 一般来说,都需要加上运水和模温机,并根据要求调整前后模具的温度.调试时,一般不允许使用脱模剂.试模时应记录所有不正常现象,如顶出不平衡,粘模, 不饱满,顶出变形,缩水,接合纹,浇口痕迹,顶针痕迹, 色差, 不能自动掉落,水口不能自动剪断.
样板检验要求:
确保样板数量正确样板不能做任何处理,例如:刮掉批锋.样板必须干净,并包装好不被刮伤,变形.标明样板材料,并附带”试模参数”,和”样板检测报告”.格式请见附表样板应在不引起刮伤和变形的状况下间隔包装好,包装箱需用抗变形强度好的纸箱.
包装要求:
包装请用”胶木”, 不要用”原木”, 否则需”植物免疫证”包装之前,防锈油请用HASCO Z262.用塑料膜,先把模具密封,然后用模箱装订好,并用钢带扎好.用大头笔写上零件号,并贴上” 北极光指定的标签(麦头)”,样板如图准备好”装箱单”,包括模具重量,包装体积,数量. 见附表.最后把模具送到”北极光”指定的地方.
最后订上北极光” 标签”公司指定的标签(麦头)式样。