任务3 炉衬结构
任务2 转炉炉体和支撑装置及其维修 (1)

炉体支撑装置
•
•
2.耳轴(阶梯形圆柱体)
托圈和转炉的全部重力都是通过耳轴经轴承座传递给基 础的。一般用合金钢锻造或铸造加工而成,驱动侧常采 用35CrMo或40Cr,从动侧也可采用45锻钢制造,空心 水冷。
炉体支撑装置
• 3.耳轴与托圈的连接
•
• •
(1) 法兰螺栓连接:工作安全可靠。
(2) 静配合连接:简单,安装和制造较方 (3)耳轴与托圈直接焊接:质量小,结构
• (1)隔热层:石棉板,厚度为10~20mm,贴炉壳,维 修时不拆除(不用石棉板直接永久层贴炉壳) • (2)永久层:保护炉壳,正常生产不损耗,标准型镁 砖,一层砌筑即可。 • (3)填充层:60~100mm,焦油镁砂或焦油白云石 散状捣打而成,减轻对炉壳挤压应便于拆除(可不设,增 加工作层厚度)(用于炉帽和炉身部位) • (4)工作层:决定炉衬寿命,受高温化学侵蚀,机械 冲刷和冲击,温度剧变 • • 炉身:400~800mm 炉底和炉帽:350~600mm
(3)连接装置带有球铰短设施的,其衬套和球 体表面应吻合,并做好润滑工作
炉体支撑装置
• 三.耳轴轴承装置 • 1.耳轴轴承形式和特点
• 工作特点:负荷大,转速低,工作条件恶劣(高温、多尘 、冲击)启动制动频繁,一般转动角度在280°~290°范围 内,轴承零件处于局部工作的情况。
• 2.耳轴轴承支座结构有两种
• 1 . 炉帽 • • 形状为截锥形,上部有炉口和出钢口、护板 作用:减少吹炼时地喷溅损失以及热量地损 等部分。 失,有利于引导炉气排出。
•
• • •
炉口:位于炉帽顶部,属于炉帽部分
炉口作用:加料,插入吹氧管,排出炉气和 水冷炉口 水箱式 埋管式
炉衬

炉衬烘炉与烧结焙烧过程,主要是将石英→石英→磷石英→方石英转变过程。随升温速度变化,第一阶段500℃以下时,主要是排除水分,包括硼酸变为硼酐放出结晶水,石英处于松散状,水蒸汽易透出,但炉衬四周妨碍蒸汽外逸。因此,前期速度可快点。因为400℃左右为保温排气阶段,应保持1h。进入500~650℃期间,硼酸开始变化,低温石英开始转变,周界出现液相。为防止硼酸蒸发转移,应加快升温速度。850~1250℃,石英开始向鳞石英转变,进入初步烧结,应减慢升温速度。1250℃石英激烈转变为鳞石英,超过1470℃逐渐转变为方石英,膨胀开裂倾向很大,应慢速升温。在1500℃~1550℃,保温2~3h。烘炉期间,应注意以下事项。①烘炉结束后,SiO2多晶转变十分缓慢,靠铁水为烧结层,中间为过渡层,近感应器为松散层。即使烘炉烧结完成,那也是表层很薄一层。使用前,应严格控制温度变化,防止温度大起大落,产生裂纹,影响坩埚寿命。靠这种结构能防止透烧开裂,保持炉衬整体性和可靠性。②炉料要低碳少锈,低温缓慢升温,高温满炉烧结。出一炉铁水时,先倒出容量的1/3后重新加满,再倒出容量的1/2重新加满,第3次全部倒完。停炉后用石棉布把炉口封好,减少供水量,延缓冷却速度避免产生裂纹。③新筑好的炉衬必须连续使用7-8炉以上,以便烧结层的形成。此阶段,由于炉衬中仍有水汽,烧结层没有完全形成。为防止对感应圈绝缘的影响,炉衬强度较差,所以送电不超过额定功率85%,以减少金属液在磁场搅拌时冲刷坩埚。
1 坩埚模具的确定
中频炉坩埚是中频炉重要组成部分,要具有耐高温、绝缘、隔热、能量传导作用,要具备抗冲涮,抗压的能力,此外,还必须具有电气特性和不影响磁场的搅拌能力。模具的大小、深度,决定炉壁和炉底厚度。模具过大,炉壁会变薄,其静压强随坩埚容量而增加,坩埚壁承受的冲刷力增加影响炉龄,但可以提高功率因数。模具过小,炉壁变厚,静压强随坩埚容量相应减小,坩埚壁承受的冲刷力减小,有利于延长炉龄,但电阻也随着增加,降低了功率因数,增加了生产成本。因此,选择适宜模具相当重要。
任务2高炉炉体结构

d1——炉喉直径; α——炉腹角;
β——炉身角;
hf hz
d1
β D
α 风口中心线
渣口中心线 d
铁口中心线
图3-1 五段式高炉内型图
h0 h1 h2 h3
h4
h5
Hu
Байду номын сангаас
有效高度:
高炉大钟下降位置的下缘到铁口 中心线间的距离称为高炉有效高度 (Hu),对于无钟炉顶为旋转溜槽最 低位置的下缘到铁口中心线之间的距 离。
其中炉缸、炉腰和炉喉呈圆筒形,炉腹呈 倒锥台形.炉身呈截锥台形。
炉喉
炉身 炉腰 炉腹 炉缸
五段式高炉炉型
高炉炉型:高炉内部借炉墙围成的工作空间几何形 状称为炉型。五段式炉型。
直筒型炉缸能暂存液态渣铁,上部设有风口( 4~40个)
最低部位设有出铁口(1~4个),必要时在中间 部位设1~2渣口。
高炉炉型(五段):炉缸——圆筒形
炉腹——倒锥台形
炉腰——圆筒形
炉身——截台形
炉喉——圆筒形
Hu——有效高度; h0——死铁层厚度; h1——炉缸高度; h2——炉腹高度; h3——炉腰高度; h4——炉身高度; h5——炉喉高度; hf——风口高度; hz——渣口高度; d——炉缸直径;
炉喉
炉喉呈圆柱形。 作用: 承接炉料,稳定料面,保证炉料合理分布。
炉 喉 直 径 与 炉 缸 直 径 比 值 d/D 取 值 在 0.5~0.55之间。
高炉:1.5~2m
7. 死铁层厚度
铁口中心线到炉底砌砖表面之间的 距离称为死铁层厚度。
新设计高炉的死铁层厚度h0=0.2d。
作用:
工业炉炉衬的4种主要结构形式
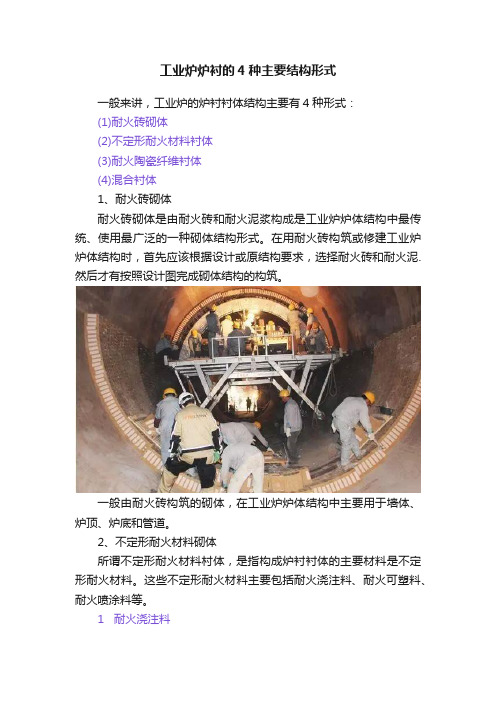
工业炉炉衬的4种主要结构形式一般来讲,工业炉的炉衬衬体结构主要有4种形式:(1)耐火砖砌体(2)不定形耐火材料衬体(3)耐火陶瓷纤维衬体(4)混合衬体1、耐火砖砌体耐火砖砌体是由耐火砖和耐火泥浆构成是工业炉炉体结构中最传统、使用最广泛的一种砌体结构形式。
在用耐火砖构筑或修建工业炉炉体结构时,首先应该根据设计或原结构要求,选择耐火砖和耐火泥.然后才有按照设计图完成砌体结构的构筑。
一般由耐火砖构筑的砌体,在工业炉炉体结构中主要用于墙体、炉顶、炉底和管道。
2、不定形耐火材料砌体所谓不定形耐火材料村体,是指构成炉衬衬体的主要材料是不定形耐火材料。
这些不定形耐火材料主要包括耐火浇注料、耐火可塑料、耐火喷涂料等。
1 耐火浇注料耐火浇注料,在作为炉体结构主要材料时,用于炉体结构的侧墙、炉顶、管道内村和外包扎等工作层.也有用于工作层与炉子钢结构(如:炉壳)之间作为保温层。
2 耐火可塑料从理论上讲,耐火可塑料可以在各种工业炉的主体结构上替代耐火砖的功能。
但实际应用时.还是需要研究完以下问题后再作决定。
1)炉子的种类和形式:是熔炼炉、反应炉还是加热炉;2)炉子结构:炉顶侧墙还是炉底;施工厚度;有无隔热材料;炉墙的高度和荷载情况等.3)炉子的操作情况:炉温及其变化、操作方式是连续还是间歇、被加热物料的状态是固态还是液态或气态、炉内的冲击荷载等;4)经济性和施工条件等。
在实际工业炉炉体结构中,耐火可塑料应用最多的是在炉体的炉顶和炉墙部分。
3 耐火喷涂料由于喷涂施工具有可以在任何角度、任何位置,并形成任何几何形状等优点,因此在工业炉的炉衬设计中,常常采用由喷涂通过喷涂施工形成的衬体。
由于喷涂料的特性与浇注料基本相同,因此在结构形式上也类同于浇注料衬体,在工业炉炉体应用的部位包括炉墙、炉顶、管道内衬壁以及保温层等。
为稳定喷涂料衬体的结构,通常在衬体内也根据具体的结构要求,配设不同形式的金属锚固件或锚固砖等。
3、耐火陶瓷纤维衬体耐火陶瓷纤维作为一种半成品原料,呈松散状,可加工成纤维毯、纤维绳、纤维纸、纤维板、纤维扎块等成品,添加结合剂后可以成为纤维喷涂料或纤维浇注料。
炉衬各部分结构和作用
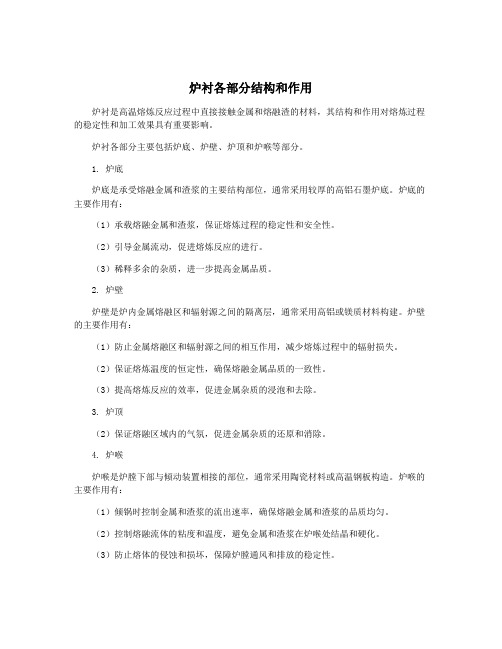
炉衬各部分结构和作用
炉衬是高温熔炼反应过程中直接接触金属和熔融渣的材料,其结构和作用对熔炼过程的稳定性和加工效果具有重要影响。
炉衬各部分主要包括炉底、炉壁、炉顶和炉喉等部分。
1. 炉底
炉底是承受熔融金属和渣浆的主要结构部位,通常采用较厚的高铝石墨炉底。
炉底的主要作用有:
(1)承载熔融金属和渣浆,保证熔炼过程的稳定性和安全性。
(2)引导金属流动,促进熔炼反应的进行。
(3)稀释多余的杂质,进一步提高金属品质。
2. 炉壁
炉壁是炉内金属熔融区和辐射源之间的隔离层,通常采用高铝或镁质材料构建。
炉壁的主要作用有:
(1)防止金属熔融区和辐射源之间的相互作用,减少熔炼过程中的辐射损失。
(2)保证熔炼温度的恒定性,确保熔融金属品质的一致性。
(3)提高熔炼反应的效率,促进金属杂质的浸泡和去除。
3. 炉顶
(2)保证熔融区域内的气氛,促进金属杂质的还原和消除。
4. 炉喉
炉喉是炉膛下部与倾动装置相接的部位,通常采用陶瓷材料或高温钢板构造。
炉喉的主要作用有:
(1)倾锅时控制金属和渣浆的流出速率,确保熔融金属和渣浆的品质均匀。
(2)控制熔融流体的粘度和温度,避免金属和渣浆在炉喉处结晶和硬化。
(3)防止熔体的侵蚀和损坏,保障炉膛通风和排放的稳定性。
综上所述,炉衬各部分的结构和作用密切相关,互相配合协作,确保炉内金属和渣浆的品质稳定和反应效率高效。
3高炉内衬 及 冷却设计

2.2 炉衬的设计高炉炉衬设计的内容是选择各部位炉衬砌体的材质,确定砌体厚度,说明砌筑的方法(包括切缝大小、砌筑方向、膨胀缝及填料等),以及材料计算。
炉衬结构设计和材质选择时应考虑到炉容大小、冶炼条件还应考虑到各部位工作条件、侵蚀机理、各部位冷却设备型式及冷却制度等等。
2.2.1 炉底、炉缸砌体结构炉缸炉底承受高温、高压、渣铁冲刷侵蚀和渗透作用。
工作条件十分恶劣。
炉缸炉底是高炉的重要部位,被侵蚀破坏程度是决定高炉大修的关键。
近30年来大中型高炉广为采用碳砖砌筑。
陶瓷杯炉缸炉底结构:[6]陶瓷杯炉缸炉底结构是提高该处炉衬寿命的一项新技术,它是在炉底碳砖和炉缸碳砖的内缘,砌筑一高铝质杯状刚玉砖砌体层。
利用刚玉砖砌体的高荷重软化温度和较强的抗渣铁侵蚀性能,以及低导热性,使高温等温线高密集的集中在刚玉砖砌体内。
陶瓷杯起保温和使炭砖免受高温渣铁浸蚀的作用。
炭砖的高导热性又可以将陶瓷杯输入热量,很快传导出去,从而达到提高炉衬寿命的作用。
这种结构还有利于提高铁水温度。
本设计采用陶瓷杯炉缸炉底结构。
2.2.2 炉腹、炉腰和炉身下部从炉腹到炉身下部的炉衬要承受煤气流和炉料的磨损,碱金属盒锌蒸气的渗透破坏作用,炉腰以下还要受到高Fe0的初渣的侵蚀,以及由于温度波动所产生的热震破坏作用。
开炉后炉腹部分砌砖很快被侵蚀掉,靠渣皮工作,一般砌一层粘土砖,厚345mm。
炉腰有三种结构形式,即厚墙炉腰、薄墙炉腰和过渡式。
炉身砌砖厚度通常为690-805mm,目前趋于向薄的方向发展,以冷却壁冷却亦可采用衬厚575mm。
炉腹、炉腰和炉身下部较长时间采用粘土砖和高铝砖砌筑。
包钢冶炼含氟矿石,炭砖砌到炉身三分之二处;宝钢一号高炉采用体积密度为2.9t/m3、Al2O3≥88%的高铝砖(刚玉砖);欧美等国以及鞍钢高炉采用碳化硅砖筑炉身中下部,取得良好效果。
本设计采用薄炉壁的设计形式。
2.2.3 炉身上部和炉喉炉身上部和炉喉采用镶砖冷却壁。
教案_3.2高炉炉衬3.2.3 高炉炉衬的设计与砌筑
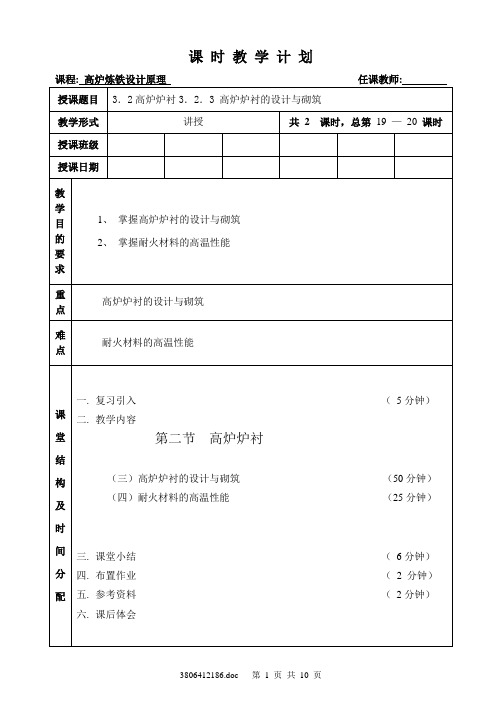
课时教学计划图示图3-7 炉缸砌砖1-砖环;2-炭素填料;3-冷却壁风口、渣口和铁口砖衬以炭砖砌筑时,应设计异型炭砖,见图3-8。
炉缸和炉底均采用光面冷却壁,砌砖与冷却壁之间留有100~150mm缝隙,其中填以炭质填料。
20世纪50年代高炉炉缸烧穿是对我国高炉生产的主要威胁,也是影响高炉寿命的主要限制环节。
当时,炉底、炉缸的砌筑材料是导热性极差的高铝砖和粘土砖,抗不住渣铁的侵蚀和机械冲刷。
50年代末,在我国大高炉开始采用以炭砖为主体的综合炉底,且炉底采用风冷或水冷,炉底、炉缸工作状况大为改观,之后20多年没有发生大高炉炉缸烧穿事故。
进入20世纪80年代以来,情况有了变化,几座强化冶炼水平高(利用系数由六七十年代的1.2~1.5t/m3·d提高到1.8~2.2t/m3·d,甚至更高)的大高炉炉缸(包括被侵蚀后的炉底的围墙部分)纷纷告急,而且出现了大修后一两年内炉缸冷却壁水温差急剧升高,并出现险情,六七十年代那种炉缸炉底一用十几年的现象不复存在了。
对于炉底、炉缸损坏的原因,概括起来有下面几条:热应力导致大块炭砖产生环状断裂;碱腐蚀;液态渣铁冲刷和铁水渗透;机械应力;冷却器漏水;铁水的熔蚀。
常规大尺寸炭砖是以煅烧无烟煤、焦炭为骨料,以沥青焦油为结合剂,经热混合、挤压成形、800~1400℃烧成及机械加工而成。
烧成中结合剂碳化,将炭颗粒粘结并部分挥发逸散,使炭砖形成孔隙。
这些孔隙正是高炉内碱金属入侵的途径。
通常碱金属沿气孔进入炭砖,在750~900℃与碳反应生成层状混合物,使炭砖体积膨胀而裂散。
炉缸常规大炭砖损坏的特征,是在单环环形炭砖内形成环状裂缝。
环状裂缝形成的机理,除碱金属侵蚀外,还与大炭砖导热率较低(10W/m·K)引起的冷热面温度差太大(可达1450℃)有关,它使炭砖在炉缸厚度方向产生不易缓冲的差热膨胀。
工作热面与冷面的体积膨胀差值在同一大炭砖中产生巨大的应力,导致距炭砖热面一定尺寸处形成环状裂缝。
真空电阻炉的炉衬结构
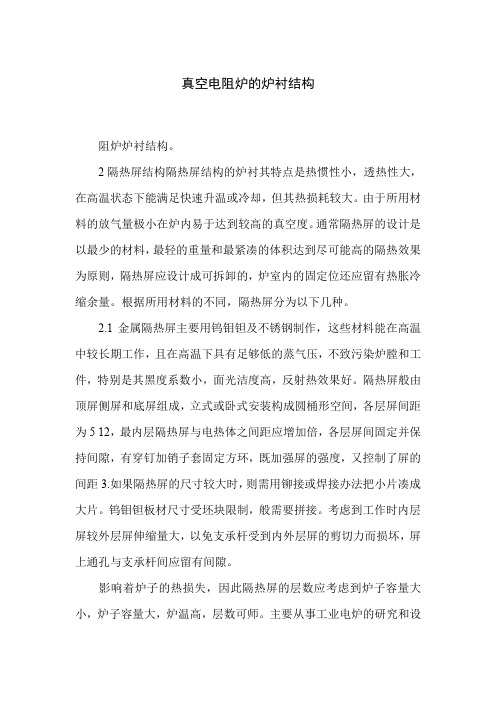
真空电阻炉的炉衬结构阻炉炉衬结构。
2隔热屏结构隔热屏结构的炉衬其特点是热惯性小,透热性大,在高温状态下能满足快速升温或冷却,但其热损耗较大。
由于所用材料的放气量极小在炉内易于达到较高的真空度。
通常隔热屏的设计是以最少的材料,最轻的重量和最紧凑的体积达到尽可能高的隔热效果为原则,隔热屏应设计成可拆卸的,炉室内的固定位还应留有热胀冷缩余量。
根据所用材料的不同,隔热屏分为以下几种。
2.1金属隔热屏主要用钨钼钽及不锈钢制作,这些材料能在高温中较长期工作,且在高温下具有足够低的蒸气压,不致污染炉膛和工件,特别是其黑度系数小,面光洁度高,反射热效果好。
隔热屏般由顶屏侧屏和底屏组成,立式或卧式安装构成圆桶形空间,各层屏间距为5 12,最内层隔热屏与电热体之间距应增加倍,各层屏间固定并保持间隙,有穿钉加销子套固定方环,既加强屏的强度,又控制了屏的间距3.如果隔热屏的尺寸较大时,则需用铆接或焊接办法把小片凑成大片。
钨钼钽板材尺寸受坯块限制,般需要拼接。
考虑到工作时内层屏较外层屏伸缩量大,以免支承杆受到内外层屏的剪切力而损坏,屏上通孔与支承杆间应留有间隙。
影响着炉子的热损失,因此隔热屏的层数应考虑到炉子容量大小,炉子容量大,炉温高,层数可师。
主要从事工业电炉的研究和设计,曾荣获国家新产品奖,机械部科技进步等奖等。
适当增加。
理论计算得知,距热源最近层屏隔热效果为,隔热效果迅速降低,可隔热屏的层数太多意义不大1.推荐炉温在1200以下取46层,炉温在8层,温度在1600即可。
料应当是热面辐射能力大,冷面辐射能力小自身热传导性能低。
显然,现有的任何种金属都不能满足上述要求,因此采用复合材料和面涂层是值得探讨的方法之。
2.2石墨隔热屏石墨隔热屏适用于工件不怕渗碳,不怕还原性气氛,采用石墨作电热体,炉温较高的真空电阻炉,石墨变形。
石墨隔热屏每层都能自立,不需要组装,所以结构简单。
石墨隔热屏比金属隔热屏厚,般为50,屏间距也相应较大,为防止碳挥发对工件污染,在石墨隔热屏内外面喷镀层钨粉或涂氧化氮氧化铌,即可阻止石墨的挥发又增强抗变形能力。
炉衬及厚度

炉衬及厚度(δ)的确定
炉衬组成:炉壳→石棉(100mm)→绝热层→工作层
炉壁衬砖厚度通常按耐火材料热阻计算确定,计算依据的条件是炉壳在操作末期被加热的温度不大于200℃,以免炉壳变形。
一般而言,增加炉衬厚度,炉壳受热及热损失可以减少,这在一定限度内是正确的,但是炉衬厚度δ增加与热损失减少并非线性关系,厚度δ达到一定值以后,再增加炉衬厚度δ,热损减少不显著,反而因为厚度δ增加过大,而增加炉壳直径D壳,耐材消耗增加,散热面积增加,所以比较经济的办法是选择优质材料,使用较薄的炉衬。
中国冶金行业网
按经验值选:炉顶砖厚度(δ)如表6-1。
- 1、下载文档前请自行甄别文档内容的完整性,平台不提供额外的编辑、内容补充、找答案等附加服务。
- 2、"仅部分预览"的文档,不可在线预览部分如存在完整性等问题,可反馈申请退款(可完整预览的文档不适用该条件!)。
- 3、如文档侵犯您的权益,请联系客服反馈,我们会尽快为您处理(人工客服工作时间:9:00-18:30)。
(3)美国UCAR热压小碳砖炉缸——散热型
常规大碳砖与热压小碳砖的主要性能比较见下表
常规大碳砖与热压小碳砖的主要性能比较
体积 项目 密度, g/cm3 常规大 碳砖 热压碳 砖 NMA 1.6 1.62 常温抗压 强度, MPa 17.9 30.5 抗折 强度, MPa 4.1 8.1 透气 率,毫 达西 800 9 600℃ 10.4 18.4 800℃ 10.4 18.8 1000℃ 10.5 19.3 1200℃ 10.9 19.7 导热率, W/m• K
司的陶瓷杯技术 。炉缸结构如图 :
首钢1号高炉炉底、炉缸结构
炉腹、炉腰和炉身下部
(1)炉腹: 一般砌一层高铝砖或粘土砖, 厚度为345mm。
(2)炉腰
炉腰有三种结构形式: 厚壁炉腰、薄壁炉腰和过渡式炉腰。
炉腰结构形式 a-薄壁;b-厚壁;c-过渡式
厚壁炉腰结构: 优点是热损失少,但侵蚀后操作炉 型与设计炉型变化大。
3500℃升华; (2)抗渣性能好;
(3)高导热性; (4)热膨胀系数小,体积稳定性好;
(5)致命弱点是易氧化,对氧化性气
氛抵抗能力差。
4. 不定形耐火材料: 捣打料:用于炉底炭砖与水冷管之间、风 口、铁口、渣口周围及铁沟。 喷涂料:炉壳。
泥浆:把耐火砖粘结成为致密的整体炉衬。
要求泥浆的化学成分与耐火砖的相近。
第二阶段是熔结层形成后的化学侵蚀。 铁水中的碳将砖中二氧化硅还原成 硅,并被铁水所吸收。
影响炉底寿命的因素:
(1)是承受的高压; (2)是高温; (3)是铁水和渣水在出铁时的流动对炉底 的冲刷; (4)砖衬在加热过程中产生温度应力引起 砖层开裂; (5)在高温下渣铁对砖衬的化学侵蚀,特 别是渣液的侵蚀更为严重。
7. 决定炉衬寿命的因素:
(l)炉衬质量,是关键因素。
(2)砌筑质量。
(3)操作因素。 (4)炉型结构尺寸是否合理。
高炉用耐火材料
一. 对耐火材料的要求:
(l)耐火度要高。
耐火度是指耐火材料开始软化的温度。
(2)荷重软化点要高。 荷重软化点是指将直径36mm,高50mm 的试样在0.2Mpa荷载下升温,当温度达到某 一值时,试样高度突然降低,这个温度就是 荷重软化点。
综合炉底的厚度为炉缸直径的0.3倍。
结构见下图:
综合炉底结构示意图 1-冷却壁;2-碳砖;3-碳素填料;4-水冷管; 5-粘土砖;6-保护砖;7-高铝砖;8-耐热混凝土
(3)全碳砖炉底:
全炭砖水冷炉底设计思想用“导热法”, 炭砖抗铁水性和导热性好,与炉底冷却相 配合,向炉底传递更多的热量,将1150它 的铁水凝固等温线上移,在炉底及早形成 一道挡铁墙,铁水渗入减少了;同时炭砖 温度降低了,热应力破坏、碱金屑、锌侵 蚀速度就降低了。
2. 炉缸
1)结构形式: (1)粘土砖或高铝砖炉底——小高炉
(2)碳砖炉缸——大中型高炉
2)炉缸砌筑: (1)粘土砖或高铝砖炉缸的砌筑:
①炉缸各层皆平砌;
②同层相邻砖环的放射缝应错开;
③上下相邻砖层的垂直缝与环缝应错开;
炉缸砌砖
1-砖环;2-炭素填料;3-冷却壁
(2)碳砖炉缸砌筑 ①每层厚400mm; ②每层块数为整数;
陶瓷杯结构及理论等温线分布图
陶瓷杯作用:保温和保护碳砖。 碳砖的高导热性可以将陶瓷杯输入 的热量,很快传导出去 。 陶瓷杯炉底炉缸结构的优越性 :
①提高铁水温度;
②易于复风操作 ;
③防止铁水渗漏。
(5)热压小碳砖——陶瓷杯技术
1994年首钢1号高炉(2536m3)引进
美国UCAR公司的热压碳砖和法国Savie公
满铺碳砖炉底砌筑
a-薄缝;b-厚缝;c-炉壳;d-冷却壁;e-碳砖与冷却壁间填料缝
碳砖砌筑的原则: ①相邻两行碳砖必须错缝,一般在 200mm以上;
②上下两层碳砖砖缝成90º ;
③最上层碳砖砖缝与铁口中心线成90º 。
(3)综合炉底砌筑 ①炉底中心部位的高铝砖砌筑高度必须与 周围环形碳砖高度一致,为400mm; ②高铝砖与环砌碳砖间的连接为厚缝,环 砌碳砖为薄缝连接; ③炉底满铺碳砖侧缝为厚缝连接,端缝为 薄缝连接。 ④环砌碳砖为楔形碳砖。
2. 炉缸:
(1)渣铁的流动、炉内渣铁液面的升降, 大量的煤气流等高温流体对炉衬的冲刷是 主要的破坏因素; (2)化学侵蚀; (3)风口带为最高温度区。
3. 炉腹: (1)高温热应力作用很大;
(2)由于炉腹倾斜故受着料柱压力和
崩料、坐料时冲击力的影响; (3)承受初渣的化学侵蚀。
4. 炉腰 (1)初渣的化学侵蚀; (2)上、下折角处高温煤气流的冲刷 磨损。 (3)高温热应力的影响;
填料 :用来填充炉壳与冷却壁、冷却壁与砌砖
之间的间隙,起密封和补偿收缩作用。
பைடு நூலகம்
优点:
工艺简单、能耗低、整体性好、抗 热震性强、不易剥落,可以减小炉衬厚 度。
高炉各部位炉衬设计与砌筑
1. 炉底 1)结构形式: (1)粘土砖或高铝砖炉底——小高炉 炉底厚度大于炉缸直径的0.6倍 。
(2)综合炉底 综合炉底是在风冷管碳捣层上满铺几 层400mm碳砖,上面环形碳砖砌至风口中 心线,中心部位砌数层400mm高铝砖,环 砌碳砖与中心部位高铝砖相互错台咬合。
薄壁炉腰结构:
热损失大些,但操作炉型与设计炉 型近似。 过渡式炉腰结构:处于两者之间。
(3)炉身下部 炉身下部砌砖厚度为690~805mm,目
前趋于向薄的方向发展,有的炉衬厚度采
用575mm或345mm。
倾斜部分按三层砖错台一次砌筑。
4. 炉身上部和炉喉 : 炉身上部:
一般采用高铝砖或粘土砖砌筑。
1. 粘土砖:
基本特性:
(1)良好的物理机械性能;
(2)抗渣性好;
(3)成本较低。
2. 高铝砖: AL2O3含量大于48%的耐火制品。
基本特性:
(1)比粘土砖有更高的耐火度和荷重软 化点; (2)由于AL2O3为中性,故抗渣性较好;
(3)加工困难,成本较高。
3. 碳质耐火材料: 主要特性:
(1)耐火度高,不熔化也不软化,在
(3)Fe2O3含量要低。 (4)重烧收缩要小。 重烧收缩也称残余收缩,是表示耐火材 料升至高温后产生裂纹可能性大小的一种尺 度。 (5)气孔率要低。 (6)外形质量要好。
二. 高炉常用耐火材料 粘土砖、高铝砖、刚玉砖和 陶瓷质材料: 不定型耐火材料等; 碳质材料 : 碳砖、石墨碳砖、石墨碳化 硅砖、氮结合碳化硅砖等。
高炉炉衬
概念: 按照设计炉型,以耐火材料砌筑的
实体为高炉炉衬。 作用:
(1)在于构成高炉的工作空间; (2)减少高炉的热损失; (3)保护炉壳和其它金属结构免受热应
力和化学侵蚀的作用。
炉衬破损机理
1. 炉底:
炉底破损分两个阶段,初期是铁 水渗入将砖漂浮而形成锅底形深坑;
铁水渗入的条件:
(1)炉底砌砖承受着液体渣铁、 煤气压力、料柱重量的10~12%; (2)砌砖存在砖缝和裂缝。
砌砖与炉壳间隙为100~150mm, 填以水渣——石棉隔热材料。为防止填 料下沉,每隔15~20层砖,砌二层带砖 即砖紧靠炉壳砌筑,带砖与炉壳间隙为 10~15mm。
炉喉: 炉喉钢砖或条状保护板:为铸铁或铸钢件。
炉喉圆周有几十块保护板,板之间留
20~40mm膨胀缝。炉喉高度方向只有一块。
五、炉衬维护 1、灌浆或压入泥料 2、喷补
5. 炉身:
炉身中下部: (1)热应力的影响; (2)受到初渣的化学侵蚀; (3)碱金属和Zn的化学侵蚀。 在炉身上部: (1)下降炉料的磨损; (2)夹带着大量炉尘的高速煤气流的 冲刷。
6. 炉喉: 受到炉料落下时的撞击作用。 1)炉料冲击; 2)高速粉尘煤气流的冲刷; 3)温度频繁变化产生的热应力等。 用金属保护板加以保护,又称炉喉钢砖。
灰份, %
8.0 10.0*
透气率:为常规大碳砖的1%左右; 导热率:比常规大碳砖几乎高一倍
美国UCAR热压小碳砖炉缸结构 1-高铝质耐火砖;2-大碳砖;3-混凝土;4-热压小碳砖
特点: 提高炉衬的导热性能,又称导热炉衬。
缺点:
增大了炉缸的热损失。
(4)法国“陶瓷杯”——隔热保温型 概念: 所谓“陶瓷杯”是指炉底砌砖的下部 为垂直或水平砌筑的碳砖,碳砖上部为1~ 2层刚玉莫莱石砖。炉缸壁是由通过一厚度 灰缝(60mm)分隔的两个独立的圆环组成, 外环为碳砖,内环是刚玉质预制块。炉底 采用水冷、油冷或空气冷却系统
2)炉底砌筑 (1)粘土砖和高铝砖炉底的砌筑:
①均采用立砌,层高345mm;
②砌筑由中心开始,成十字形,结构如图。
③上下两层的十字中心线成22.5º ~45º ;
④上下两层中心点应错开半块砖。
⑤最上层砖缝与铁口中心线成 22.5º ~45º 。
十字形砌砖
砌砖中心线
Kj炉底最后一页
(2)满铺碳砖炉底砌筑 有厚缝和薄缝两种连接形式: 一般是碳砖两端的短缝用薄缝,而 两侧的长缝用厚缝。 满铺碳砖炉底的结构见下图 :
③同层相邻砖环的放射缝应错开;
④上下相邻砖层的垂直缝与环缝应错开; ⑤在碳砖炉缸的内表面设有保护层。过 去砌一层高铝砖,近来用涂料代替高铝 砖,涂料层厚5~8mm。
炉缸厚度: 一般规定铁口水平面处的厚度为 小高炉: 575mm(230+345);
中型高炉:920mm(230+345×2);
大型高炉:1150mm(230×2+345×2) 或更厚些。