T202有机硫加氢催化剂硫化方案
T202C(二甲基二硫)硫化方案

T202C有机硫加氢催化剂硫化方案T202C有机硫加氢催化剂硫化就是利用焦炉气中高浓度H2S或低浓度焦炉气加二甲基二硫,将催化剂的金属组分由氧化态转化成相应的硫化态的过程。
硫化的关键是要避免金属氧化态在与H2S反应转化成硫化态之前被热氢还原。
所以,催化剂硫化时,必须控制好温度与循环气中H2S含量,在H2S未穿透催化剂床层前,床层最高点温度不应超过230℃。
一、利用低硫煤气加二甲基二硫硫化方案1、硫化条件:气源:焦炉气硫化空速:一般控制在300~400h-1,2、升温硫化流程及曲线(1)流程:焦炉气——压缩机——升温炉——2台预加氢反应器并联——一级加氢反应器——放空(2)升温硫化及放硫曲线:见表1二、硫化说明及注意事项1、系统用氮气(氮气纯度>99.9%)置换合格后(主要指氧含量小于0.5%),点燃升温炉,根据升温曲线调节燃气量,一般控制升温炉出口温度不大于床层温度50℃,床层到200℃并拉平后,引入低硫煤气(经湿脱),并配入二甲基二硫,控制床层最高温度≤400℃。
用煤气升温也可以,只是对催化剂有一定影响。
2、铁钼反应器床层到200℃,开始有硫化反应,为了加速硫化,系统压力可逐渐提到1.0Mpa,另外开始滴加二甲基二硫。
(每吨催化剂约需二甲基二硫65Kg),3、硫化时注意提温不提氢,提氢不提温原则。
4、硫化初期,二甲基二硫配入后分析入口H2S≤10g/Nm3,硫化主期,逐步增加二甲基二硫加入量,使入口H2S达到10-20g/Nm3。
5、370℃时开始有放硫反应,为了加速放硫,在370℃恒温后,压力逐步降到0.1-0.2Mpa并停止加二甲基二硫。
6、硫化及放硫期间,每小时分析一次铁钼反应器进出口H2S和H2含量,当进出口H2S和H2含量基本相等时硫化结束,当出口H2S≤300mg/Nm3时,放硫结束。
7、硫化结束后将压力提到0.8Mpa、关闭进出口阀,使铁钼反应器保温、保压。
8、床层在120度以前主要是脱催化剂吸附水的过程,故应每半小时开导淋一次放水。
T202A型加氢催化剂在焦化干气脱硫装置上的应用
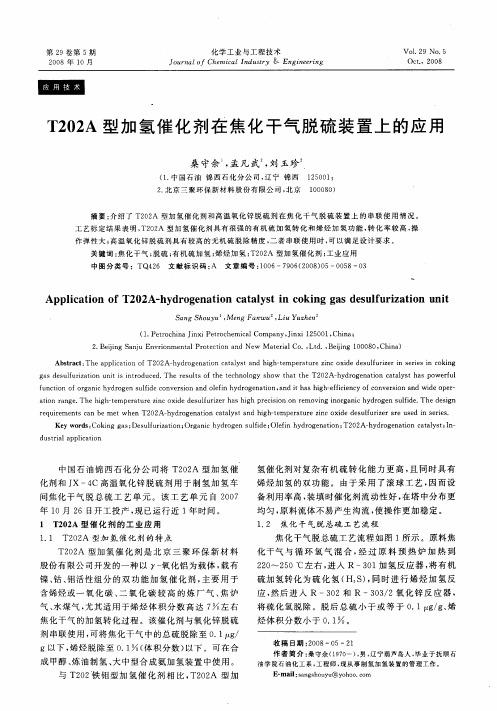
20 年 1 08 0月
化 学工 业 与工 程 技 术 J u n l f C e c lI d s y & E g n e ig o r a h mi n u t o a r n i er n
V o129 N O 5 . .
0 c. 00 t。2 8
T 0 A 型加 氢 催化 剂在 焦化 干气 脱 硫 装 置上 的应 用 22
桑 守余 孟 凡 武 刘 玉珍 , ,
(. 国石 油 锦 西石 化 分 公 司 , 宁 锦 西 15 0 ; 1中 辽 201
2 北 京 三 聚环 保 新 材 料 股 份 有 限 公 司 , 京 1 0 8 ) . 北 0 0 0
Ab t a t Th p l a i n o 0 A— y r g n t n c t l s n ih t mp r t r i co ie d s l r e n s re n c k n sr c : e a p i t fT2 2 h d o e a i a ay ta d h g —e e a u ezn x d e u f i r i e is i o ig c o o u z g sd s l rz t n u i i i to u e . e r s l ft e t c n l g h w h tt e T2 2 h d o e a i n c t l s a o ru a e u f ia i n t s n r d c d Th e u t o h e h o o y s o t a h 0 A— y r g n t a a y th s p we f l u o s o f n t n o r a i h d o e u f e c n e so n lf y r g n t n a d i h sh g — fiin yo o v r in a d wie o e — u c i fo g n c y r g n s li o v r i n a d o e i h d o e a i , n t a i h efce c fc n e so n d p r o d n o a in r n e Th i h tm p r t r ic o i ed s l r e a i h p e ii n o e vn n r a i h d o e ufd . ed sg t a g . eh g - e e a u e zn x d e u f i rh sh g r cso n r mo i g i o g nc y r g n s lie Th e i n o u z r q ie n sc n b twh n T2 2 h d o e a in c t l s n i h t mp r t r i co i e d s l rz ra e u e n s re . e u r me t a eme e 0 A— y r g n to a ay ta d h g — e e a u e zn xd e u f ie r s d i e is u Ke r s Co i g g s De u f rz to Or a i y r g n s l d ; ei y r g n t n T2 2 h d o e a i n c t l s ;n y wo d : k n a ; s lu i in; g n c h d o e u f e Olfn h d o e a i ; 0 A— y r g n t a a y t I — a i o o
T202A脱硫剂硫化方案

T202A脱硫剂硫化方案本次公司因生产需要,将原脱氧槽脱氧剂更换为****公司T202A 镍钼脱硫剂,共6.5方。
T202A型加氢催化剂在未硫化前其活性金属组分:钴、钼、镍为氧化态。
为了最大的发挥其活性,使用前必须进行预硫化。
1、硫化原理及工艺条件1.1加氢催化剂的主要活性组分有 Co-Mo、Ni-Mo 和 Fe-Mo 等类型,在氢气存在条件下,可与H2S发生如下硫化反应:MoO3+H2+2H2S=MoS2+3H2O9Fe2O3+16H2S+11H2=2Fe9S8+27H2O9CoO+8H2S+H2=Co9S8+9H2O3NiO+H2+2H2S=Ni3S2+3H2O1.2 硫化剂及氢解反应常见的硫化剂有二硫化碳(CS2)、二甲基硫醚(DMS)、二甲基二硫(DMDS),均可以在 H2 气氛中发生氢解反应生成 H2S:CS2+4H2=2H2S+CH4CH3SCH3+2H2=H2S+2CH4CH3SSCH3+3H2=2H2S+2CH41.3 硫化剂用量简算法CS2用量:催化剂体积数(m3)×堆比重(T/m3)×65(Kg/T)=CS2用量(Kg)CS2一般为铁桶包装,规格:250Kg/桶,请自行核算所需购买数量。
DMDS 用量:催化剂体积数(m3)×堆比重(T/m3)×80(Kg/T)=DMDS 用量(Kg)DMDS 一般为铁桶包装,规格:250Kg/桶,请自行核算所需购1.4 硫化条件气源:原料气(其中 H2含量≥20%),硫化氢 3-10g/Nm3。
硫化的关键是要避免金属氧化物在与 H2S 反应转化成硫化态之前被热氢还原。
所以,催化剂硫化时,必须控制好温度与循环气中 H2S 含量,在 H2S 未穿透催化剂床层前,床层最高点温度不应超过 230℃ 2、升温硫化流程2.1 硫化工艺说明:2.1.1本次硫化升温阶段用1#氮压机氮气进行升温,升温热源用再生气预热器的中变气提供,速率控制用再生气预热器进口新配的DN125冷氮气阀控制。
加氢装置催化剂预硫化方案
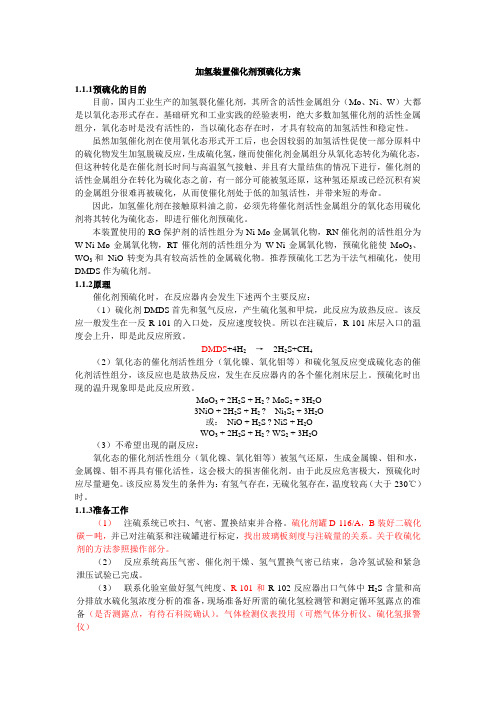
预硫化和进油之间,催化剂是相当有活性的,如遇到紧急情况,催化剂床层的温度更加难以控制,很有可能引起床层飞温。因此应严格地遵守预硫化步骤中有关温度的限制并且密切监视反应器床层温度,这样才不会发生飞温。
预硫化期间,催化剂被还原会造成催化剂损坏。还原是催化剂上的金属氧化物反应生成纯的金属,而不是反应产生金属硫化物的一种反应。在较高的温度下,循环氢中硫化氢含量又少,还原反应就发生的快。因此,在预硫化期间,准确的控制硫化温度和硫化氢浓度是至关重要的。
(3)185℃前,DMDS的注入速度不宜过快,以免累积在反应器床层中发生集中分解放热;
(4)200℃以前,应严格控制升温速率不大于给定值;
(5)循环氢中H2S含量未被检出或浓度小于0.3%时,反应器内床层温度不得超过230℃。
(6)硫化期间,正常下不用冷氢,但冷氢阀必须处于随时可用状态。硫化过程中应严密观察反应器各床层温度的变化。若单个催化剂床层温升达到10℃,立即投用冷氢控制床层温度,并停止升温;若单个催化剂床层温升达到20℃以上,且呈快速上升趋势,则停炉熄火,并立即启动紧急放空系统(7bar/min)。
(1)预硫化期间新氢中断
预硫化期间,DMDS反应生成硫化氢所需的新氢量以及补充反应器回路中分解损失的氢气量以及泄漏氢气量是很少的,因此不需要补充很多的新氢。预硫化期间如果新氢中断,必须降低硫化温度,尽可能的放慢压力损失的速度。当氢气恢复之后,装置立即快速地重新开始预硫化。事故处理过程如下:
1新氢中断,降低反应温度,适当的情况下,可用冷氢把所有的床层温度降低50℃或降到150℃,如果床层温度本身低于150℃,把温度降到140℃,如果预计在3~4小时内能恢复,保持床层平均温度在这一温度。
(7)硫化期间如发生故障而中止了硫化,重新开始时必须恢复到中止前的状态进行。
加氢催化剂预硫化方案

1. 引言加氢催化剂是广泛应用于石化工业领域的关键催化剂之一。
为了提高加氢催化剂的活性和稳定性,预硫化技术被广泛应用。
本文将从预硫化的原理、影响因素以及常见的预硫化方案等方面进行探讨。
2. 预硫化的原理预硫化是指在加氢催化剂使用之前,使用硫化物溶液进行处理,使其表面形成一层硫化物膜。
这一膜可以防止催化剂表面被氧化物或其他不活性物质占据,从而提高催化剂的活性和稳定性。
预硫化的原理可以归结为两个方面:•活性金属硫化物的形成:活性金属如镍、钼等能够与硫化物反应形成硫化物,这种硫化物能够促进加氢反应的进行,提高催化剂的反应活性。
•表面硫化膜的形成:硫化物膜可以阻隔外界氧气和不活性物质的侵蚀,减少催化剂的表面被氧化的机会,提高催化剂的稳定性。
3. 预硫化的影响因素预硫化的效果受到多种因素的影响,下面列举了一些主要的影响因素:3.1 硫化剂的选择预硫化过程中使用的硫化剂对催化剂的性能起着至关重要的作用。
常用的硫化剂包括硫化氢(H2S)、二硫化碳(CS2)等。
不同的硫化剂在反应中会产生不同的硫化物,并对催化剂表面的化学状态产生影响。
3.2 预硫化温度和时间预硫化温度和时间是影响预硫化效果的关键因素。
一般来说,高温和长时间的预硫化会使硫化剂更充分地与催化剂发生反应,生成更完善的硫化物膜。
然而,过高的温度可能会导致催化剂的部分活性成分被分解或损失,因此需要根据具体情况选择合适的预硫化温度和时间。
3.3 氛围条件预硫化过程中的气氛条件也会对催化剂的预硫化效果产生影响。
一般情况下,加氢环境中的氢气浓度越高,硫化剂与催化剂的反应速度越快,硫化物膜形成的效果也越好。
4. 常见的预硫化方案4.1 H2S气体预硫化H2S气体预硫化是一种常用的预硫化方式。
预硫化过程中,将催化剂放入加热炉中,通入含有H2S气体的加硫气体。
通过控制炉内温度和气氛浓度,使硫化剂与催化剂表面反应生成硫化物。
4.2 溶液浸泡预硫化溶液浸泡预硫化是另一种常见的预硫化方式。
T202型铁钼有机硫加氢转化催化剂的硫化工艺

T202型铁钼有机硫加氢转化催化剂的硫化工艺T202型铁钼有机硫加氢转化催化剂的硫化工艺童庆慧,潘利新(黑龙江黑化集团有限公司,黑龙江齐齐哈尔161041)摘要:介绍了T202 型铁钼有机硫加氢转化催化剂硫化工艺的应用情况,阐述了以CS2为硫化剂时的操作要点,指出在系统外硫化工艺可以提高经济效益,工艺管线改造后使干法脱硫槽可以根据生产实际情况倒换,无需停车。
关键词:焦炉气;硫化反应;硫化剂中图分类号:TQ 113 文献标识码:A 文章编号:1004-0935(2013)07-0877-03黑龙江黑化集团有限公司硝铵厂合成氨系统是以焦化厂副产焦炉气为原料生产合成氨,设计生产能力为55 kt/a, 经过技术改造,生产能力达到65kt/a。
焦炉气中硫的存在除了会毒害催化剂外,还会腐蚀设备和管道,因此原料气的净化脱硫是很重要的一步。
有机硫的脱除多采用加氢转化脱除方法。
加氢转化催化剂的作用在于使烃类原料中所含的有机硫化合物产生氢解反应,转化成易于脱除的无机硫(主要是硫化氢),以便进一步除去。
焦炉气中有机硫组份较复杂,多用铁钼催化剂。
国内常用的铁钼加氢转化多为T202 型,系用γ-Al2O3 担载2.9%~4.3% Fe2O3 和7.5%~10.5% MoO3。
1·催化剂的装填及升温硫化1.1 催化剂的装填在加氢转化反应器中,T202 型有机硫加氢催化剂一般分三段填装。
按照触媒装填要求,每一层下面覆二层白钢网,网上压大小瓷球各一层,然后装触媒,触媒上再压大小瓷球各一层。
最下面一层装触媒106 桶计4.24 t。
中层装触媒130 桶计5.2 t。
上层连中心管装触媒161 桶计6.44 t。
共计397 桶,总计15.88 t。
下层装完瓷球后距人孔100 mm,中层距人孔150 mm,上层距中心管上端100 mm。
1.2 催化剂的升温硫化T202 型催化剂在未硫化前其金属组分铁和钼为氧化态,对一氧化碳含量高的原料气甲烷化副反应较大,同时,对有机硫化物虽有一定活性,但活性不稳定,而且活性较硫化态的低,因此,T202 型催化剂在使用前必须进行硫化处理。
加氢催化剂硫化方案

制氢装置催化剂硫化方案硫化前准备:1、催化剂已按填装方案填装完毕2、压缩机已试机完成,达到开机条件,所有仪表已联校完成3、制氢系统已用氮气置换合格(O2<0.5%)、气密完成4、准备好硫化剂(DMDS)并注入至硫化剂罐,硫化剂线已试压、吹扫干净(用蒸汽、风彻底吹扫干净)5、准备好硫化用工具:硫化氢检测管、计量水器具、画好升温曲线、记录纸、对讲机消防器具等6、干气、氮气、循环水等已准备就绪LYT-701/LYT-702加氢催化剂硫化1、硫化机理LYT—701/702加氢催化剂活性组份氧化钴、氧化镍、三氧化钼在使用前需将其转化为硫化物才具有活性,这一过程为硫化,其机理为:DMDS(或CS2)+4H2=2H2S+CH4MoO3+2H2S+H2=MoS2+3H2OCoO+H2S=CoS+H2ONi0+ H2S=NiS+H2O硫化时,用干N2-H2(H2≥10%,O2<0.5%)作为硫化原料气,配以适量的CS2或者DMDS,经加热达到一定温度后进入催化剂床层,通常采用循环硫化或一次放空硫化方法。
2、硫化过程1、反应系统气密合格,建立氢气-氮气循环后,进行催化剂硫化。
硫化条件:氢压,MPa ≦0.5MPa循环介质,% N2-H2混合气氢气含量,%(v/v) 30-50空速,h-1 200-500第一个恒温硫化阶段床层温度和时间 230℃恒温6小时第二个恒温硫化阶段床层温度和时间 300℃恒温4-6小时第三个恒温硫化阶段床层温度和时间 350℃恒温4小时硫化剂二甲基二硫或二硫化碳理论需硫量,m %(对催化剂) 约8.0吸硫量计算公式为:⎥⎦⎤⎢⎣⎡⨯+⨯⨯+⨯⨯=C B A c s M C M B M A w w 06.329/806.32306.32s w :理论吸硫量c w :催化剂装量A:MoO 3的百分含量;A M :MoO 3的分子量,143.94B :CoO 的百分含量B M :CoO 的分子量,74.93C:NiO 的百分含量C M :NiO 的分子量,74.70理论生成水重量为:DMDS (或CS 2)注入量计算式:(催化剂量)×8%×94(DMDS 分子量或CS 2)/64(硫分子量)=硫注入量 硫注入量×1.1(10%的余量)=实际硫注入量0.452 吨 气体含硫量计算式:X (气体循环量Nm3)/22.4×0.5%(硫含量)×94(DMDS 分子量或CS2)/64(硫分子量)=X’ Kg 二甲基二硫性质:分子式:CH3SSCH3 分子量:94.20 CAS :624-92-0 淡黄色透明液体。
方案十三(催化剂硫化方案)
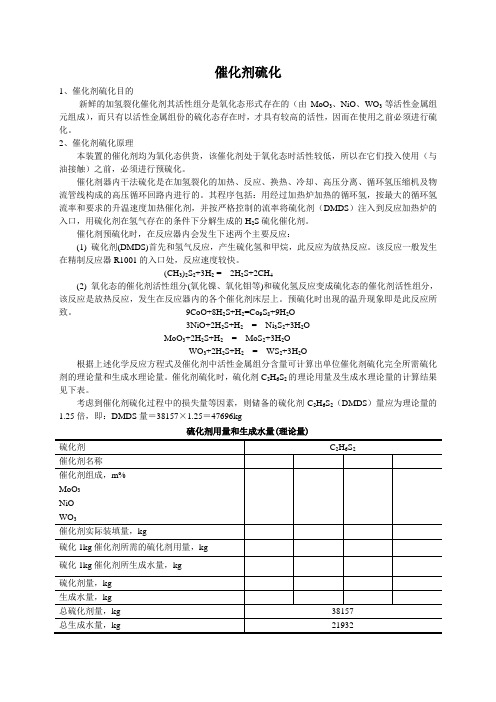
催化剂硫化1、催化剂硫化目的新鲜的加氢裂化催化剂其活性组分是氧化态形式存在的(由MoO3、NiO、WO3等活性金属组元组成),而只有以活性金属组份的硫化态存在时,才具有较高的活性,因而在使用之前必须进行硫化。
2、催化剂硫化原理本装置的催化剂均为氧化态供货,该催化剂处于氧化态时活性较低,所以在它们投入使用(与油接触)之前,必须进行预硫化。
催化剂器内干法硫化是在加氢裂化的加热、反应、换热、冷却、高压分离、循环氢压缩机及物流管线构成的高压循环回路内进行的。
其程序包括:用经过加热炉加热的循环氢,按最大的循环氢流率和要求的升温速度加热催化剂,并按严格控制的流率将硫化剂(DMDS)注入到反应加热炉的入口,用硫化剂在氢气存在的条件下分解生成的H2S硫化催化剂。
催化剂预硫化时,在反应器内会发生下述两个主要反应:(1) 硫化剂(DMDS)首先和氢气反应,产生硫化氢和甲烷,此反应为放热反应。
该反应一般发生在精制反应器R1001的入口处,反应速度较快。
(CH3)2S2+3H2 = 2H2S+2CH4(2) 氧化态的催化剂活性组分(氧化镍、氧化钼等)和硫化氢反应变成硫化态的催化剂活性组分,该反应是放热反应,发生在反应器内的各个催化剂床层上。
预硫化时出现的温升现象即是此反应所致。
9CoO+8H2S+H2=Co9S8+9H2O3NiO+2H2S+H2 = Ni3S2+3H2OMoO3+2H2S+H2= MoS2+3H2OWO3+2H2S+H2= WS2+3H2O根据上述化学反应方程式及催化剂中活性金属组分含量可计算出单位催化剂硫化完全所需硫化剂的理论量和生成水理论量。
催化剂硫化时,硫化剂C2H6S2的理论用量及生成水理论量的计算结果见下表。
考虑到催化剂硫化过程中的损失量等因素,则储备的硫化剂C2H6S2(DMDS)量应为理论量的1.25倍,即:DMDS量=38157×1.25=47696kg硫化剂用量和生成水量(理论量)硫化过程中还可能有不希望发生的副反应:氧化态的催化剂活性组分(氧化镍、氧化钼、氧化钨)被氢气还原,生成金属单质和水,这会极大损害催化剂的活性。
加氢单元催化剂硫化

一段反应器硫化1.硫化作业前的确认(2台反应器硫化管线的盲板均处于开通状态)(1)确认氢气已经建立正确的循环。
R-102已经用阀门隔离。
循环氢气流程;C-101→B-102→D-102→E107→B-101→R-101→E-107→E-106→E-104→E-101→E-108→D-103→E-114→T-103→D-104→C-101(2)确认D-103的工作压力为2430 KPa,此点压力控制已投自动。
氢气浓度>90%,氢气浓度2小时分析一次。
(3)循环氢流量不低于1000Nm3/h。
E-107壳程旁通关闭,以最大负荷对循环氢升温。
(4)通过调节FV-9111。
来维持系统压力。
(5)打至手动维持稳定的补充量,如氢气浓度降低则加大放散和新氢气的补充。
(6)确认硫化剂槽的液位正常。
硫化剂已用BTX稀释到50%浓度。
(7)点燃B-101给反应器升温,系统以25℃/h的速度进行升温,一段加氢反应器的进口温度TISA-9120A为150℃。
恒温,观察D-103液位待液位升高速度低于4L/h,催化剂干燥结束,继续升温至180°C。
冷却器E-108的冷却水要保证蒸汽能足够冷却。
(8)维持反应器温度在180°C,对达到180°C的部分热紧固,并维持此温度。
然后把反应器温度升高到205℃准备硫化。
2.硫化(1)打开一段加氢反应器硫化剂注入管道阀门,按照泵的操作步骤启动硫化剂注入泵PU-103,调节冲程逐步至50L/H。
(2)在取样口SC-113处每小时取样检查一次循环氢气中硫化氢的含量,当检测出硫化氢且高分罐有水出现后,以25℃/h的速度将第一段加氢反应器R-101的进口温度TI-9136提升至230℃,恒温4小时。
在预硫化过程中,温度最高不能超过245℃。
(3)调节硫化剂注入泵的冲程至100L/H。
(4)当SC-113处硫化氢的含量大于3000ppm时,以25℃/h的速度将反应器进口温度提升至315℃。
催化剂升温硫化方案
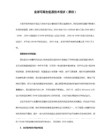
催化剂升温硫化方案一、催化剂的升温1、条件确认(1)现场各检修项目完毕,气密性试验合格,(2)按操作规程进行升温流程确认。
(3)确认开工加热炉柴油,液化压力正常。
2、升温(1)按操作规程进行配氮升温,注意严格控制升温速率≤50℃/h。
(2)当床层(一段)各点温度均达到200℃-220℃时恒温,进行下一步硫化程序。
首次开车升温时,为防止水蒸汽在催化剂上冷凝,应使用惰性气体N2把催化剂加热到工艺气露点以上温度。
采用≤50℃/h升温速度加热催化剂,根据最大可获得流量来设定压力,从而确保气体在催化剂上能很好的分布。
(3)当催化剂床层温度达到200℃-220℃时,进行下一步的硫化程度。
硫化气的切换基本上在常压或较高压力下进行,这取决于气流的方便,(注意:切换工艺气硫化前,一定要开导淋,彻底排放冷凝水)。
二、催化剂的硫化(一)采用工艺气硫化(1)确认工艺气中的硫化氢含量,最好工艺气中的硫化氢含量≥0.2%(VOL)。
(2)当催化剂床层温度达到200℃-220℃时,把湿工艺气加到氮气中(比例:湿工艺气:氮气=1:3)同氮气一起进入开工炉进行加热,控制反应器入口温度在200℃-220℃。
根据催化剂床层温度逐渐增加工艺气量,并且相应减少氮气量,直到氮气完全撤出。
(3)当硫化催化剂床层温度稳定时,再将工艺气流量增加,并控制入口温度200℃-220℃继续硫化。
(4)当有硫穿透催化剂床层时,逐步提高硫化压力和入口温度继续进行硫化,当压力为1.5MPa、入口温度230℃-250℃-时,此时变换炉出口有硫穿透,并且硫含量不再变化,可以认为硫化结束。
(5)硫化结束后,调整入口温度至正常使用要求的温度,同时增大工艺气量,提高系统压力至正常使用要求的压力。
采用补硫硫化1.加硫的位置:一般为第一变换炉前换热器的前面加硫。
2.CS2罐及加硫氮气管线,阀门配好待用。
3.取样点:变换炉入口和出口取样。
4.硫化期间4114-PVC-3保持全开。
加氢催化剂硫化阶段的操作原则

加氢催化剂硫化阶段的操作原则
1.硫化期间,严格执行操作规程中的不得、严禁、必须等字样的内
容;严格执行开工方案及工艺指标;
2.硫化前必须确认高压系统氧含量≤0.1%(体积);
3.硫化期间,高分压力必须≤12.5MPa,为10.5~12.5 MPa;
4.硫化期间,高分气H2纯度≥75%(V),为75~97%(V);
5.硫化期间,高压系统静压降速度≤0.1 MPa / h.
6.硫化期间,只能通过调行程调节注硫量,严禁使用高压注硫泵的
出口阀调节注硫量;
7.硫化启动后注硫量的调整幅度,任何时刻不能单次大幅度,而只
能多次、小幅调整;
8.硫化期间,任一催化剂床层总温升必须控制在≤25℃;
9.硫化期间,R15301第一冷氢阀阀前后压差大于0.4 MPa;R15311
第一冷氢阀前后压差大于0.4 MPa;
10.、硫化期间,“F15301出口温度─R15301第一床层顶温差≤5℃”;
F15311出口温度─R15311第一床层顶温差≤5℃。
12.硫化启动时条件:反应器入口温度175~190℃,反应器入口H2S
含量为3000ppm(V),预期温升≤25℃。
硫化开始后按照硫化方案执行。
加氢催化剂硫化方案
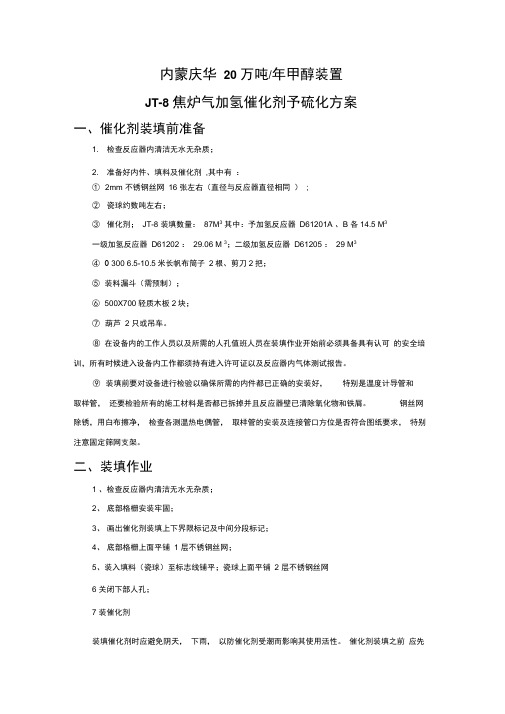
内蒙庆华20 万吨/年甲醇装置JT-8 焦炉气加氢催化剂予硫化方案一、催化剂装填前准备1. 检查反应器内清洁无水无杂质;2. 准备好内件、填料及催化剂,其中有:①2mm 不锈钢丝网16 张左右(直径与反应器直径相同);②瓷球约数吨左右;③催化剂;JT-8 装填数量:87M3其中:予加氢反应器D61201A 、B 各14.5 M3一级加氢反应器D61202 :29.06 M 3;二级加氢反应器D61205 :29 M3④0 300 6.5-10.5米长帆布筒子2根、剪刀2把;⑤装料漏斗(需预制);⑥500X700轻质木板2块;⑦葫芦 2 只或吊车。
⑧在设备内的工作人员以及所需的人孔值班人员在装填作业开始前必须具备具有认可的安全培训,所有时候进入设备内工作都须持有进入许可证以及反应器内气体测试报告。
⑨装填前要对设备进行检验以确保所需的内件都已正确的安装好,特别是温度计导管和取样管,还要检验所有的施工材料是否都已拆掉并且反应器壁已清除氧化物和铁屑。
钢丝网除锈,用白布擦净,检查各测温热电偶管,取样管的安装及连接管口方位是否符合图纸要求,特别注意固定筛网支架。
二、装填作业1 、检查反应器内清洁无水无杂质;2、底部格栅安装牢固;3、画出催化剂装填上下界限标记及中间分段标记;4、底部格栅上面平铺1 层不锈钢丝网;5、装入填料(瓷球)至标志线铺平;瓷球上面平铺2 层不锈钢丝网6 关闭下部人孔;7 装催化剂装填催化剂时应避免阴天,下雨,以防催化剂受潮而影响其使用活性。
催化剂装填之前应先筛去粉尘。
催化剂装填时,从上人孔放入加料帆布筒10.0 米左右和漏斗连接;催化剂装填时视装填设备及人员情况,可进行一台或多台反应器的装填作业。
①漏斗内倒入催化剂0.5-1.0 吨;可根据具体情况确定。
并用吊车吊至反应器人孔上方,漏斗与帆布筒相连,放入催化剂。
②视吊装催化剂的量,取出漏斗和帆布筒由软梯进入反应器,用木板刮平催化剂;③刮平后,根据具体装填高度,帆布筒剪掉约 1 米,继续装催化剂,装量根据第一次实际装填情况可调节。
T202型催化剂在焦炉气二级加氢脱硫工艺中的应用

T202型催化剂在焦炉气二级加氢脱硫工艺中的应用裴学国;亓栋;丁卉;王鲲;刘其智;刘金辉;郭玉峰【摘要】T202 type Fe-Mo hydrogenation conversion catalyst has been used in second stage of hydrogenation conversion fine desulphurization process taking coking-oven gas as the raw material for producing methanol;author has introduced the reaction mechanism,technical index of this catalyst and the process flow for second stage of hydrogenation conversion fine desulphurization using Fe-Mo catalyst;through total sulfur analysis data comparison for conversion rate,by-reaction,hot point temperature and fresh synthetic gas,has summarized the technical reformation effect,result indicates that the first stage and second hydrogenation processes can satisfy the deep purification requirement for coking-oven gas containing various organic sulfide content.%在以焦炉气为原料生产甲醇的二级加氢转化精脱硫工艺中使用了T202型铁钼加氢转化催化剂;介绍了该催化剂的反应机理、技术指标和铁钼催化剂二级加氢转化精脱硫的工艺流程;通过转化率、副反应、热点温度以及合成新鲜气的总硫分析数据对比,总结了技改效果。
神华二级铁钼T202硫化方案1(北京三聚)
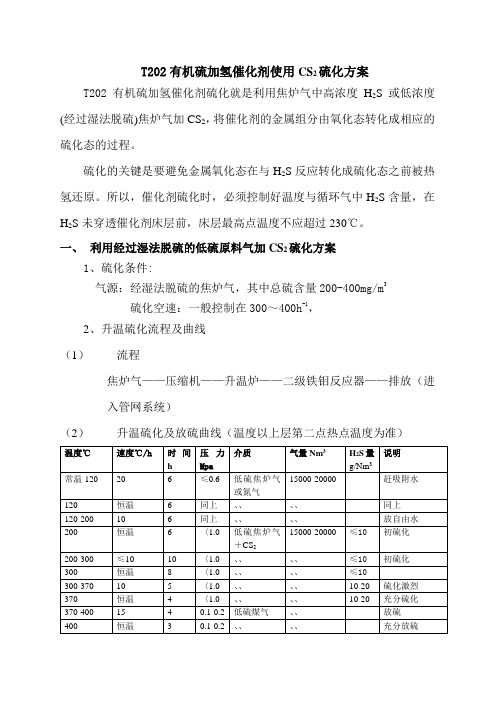
T202有机硫加氢催化剂使用CS2硫化方案T202有机硫加氢催化剂硫化就是利用焦炉气中高浓度H2S或低浓度(经过湿法脱硫)焦炉气加CS2,将催化剂的金属组分由氧化态转化成相应的硫化态的过程。
硫化的关键是要避免金属氧化态在与H2S反应转化成硫化态之前被热氢还原。
所以,催化剂硫化时,必须控制好温度与循环气中H2S含量,在H2S未穿透催化剂床层前,床层最高点温度不应超过230℃。
一、利用经过湿法脱硫的低硫原料气加CS2硫化方案1、硫化条件:气源:经湿法脱硫的焦炉气,其中总硫含量200-400mg/m3硫化空速:一般控制在300~400h-1,2、升温硫化流程及曲线(1)流程焦炉气——压缩机——升温炉——二级铁钼反应器——排放(进入管网系统)(2)升温硫化及放硫曲线(温度以上层第二点热点温度为准)硫化时间约60小时说明:二级铁钼装填T202的重量约40吨。
硫化氢理论加入量:40×65 kg(每吨催化剂需要65kg CS2)×0.842(CS2含S)×1.06(折合H2S)=2320kg实际硫化氢加入量:硫化气体一次通过吸收率按50%,需硫化氢2320kg×2=4640kg需要购买CS2约5.2吨实际吸硫量也可以通过每小时分析的进出口硫化氢含量差、气量,计算每小时的吸硫化氢量,再累加得出实际吸硫量,做硫化度参考。
二、硫化说明及注意事项1、系统用氮气(氮气纯度>99.9%)置换合格后(主要指氧含量小于0.5%),引入低硫煤气(经湿脱)进入升温炉,建立升温流程,点燃升温炉,根据升温曲线调节燃气量,一般控制升温炉出口温度不大于床层温度50℃,床层到200℃并拉平后改入高硫煤气(低硫原料气加CS2),控制床层最高温度≤420℃。
2、铁钼反应器床层到200℃,开始有硫化反应,为了加速硫化,系统压力可逐渐提到1.0Mpa,另外开始滴加CS2。
(每吨催化剂硫化约需CS2 65Kg),3、硫化时注意提温不提氢,提氢不提温原则。
- 1、下载文档前请自行甄别文档内容的完整性,平台不提供额外的编辑、内容补充、找答案等附加服务。
- 2、"仅部分预览"的文档,不可在线预览部分如存在完整性等问题,可反馈申请退款(可完整预览的文档不适用该条件!)。
- 3、如文档侵犯您的权益,请联系客服反馈,我们会尽快为您处理(人工客服工作时间:9:00-18:30)。
T202有机硫加氢催化剂硫化方案
T202有机硫加氢催化剂硫化就是利用焦炉气中高浓度H2S将催化剂的金属组分由氧化态转化成相应的硫化态。
硫化的关键是要避免金属氧化态在与H2S反应转化成硫化态之前被热氢还原。
所以,催化剂硫化时,必须控制好温度与循环气中H2S含量,在H2S未穿透催化剂床层前,床层最高点温度不应超过230℃。
利用未经脱硫的高硫原料气硫化。
1、硫化条件:
气源:未经脱硫的焦炉气,其中含硫5-7g/m3
硫化空速:一般控制在250-400h-1
最高温度≤400℃
压力:0.1-1.0MPa,放硫时降低到0.1-0.2MPa
(1)系统用氮气置换合格后,引入低硫焦炉气(或循环氮气)进入升温炉,建立升温流程,点燃升温炉,根据升温曲线调节燃烧气量,一般控制升温炉出口温度不大于床层温度50℃,将催化剂升温至220℃恒温,待催化剂床层温度拉平后,改高硫原料气对催化剂进行等温硫化,床层最高温度≤450℃。
(2)硫化时将系统压力以每小时0.3-0.5MPa的速率提至硫化曲线要求的操作压力。
(3)在120℃前主要是赶吸附水平稳升温,防止操作过急。
(4)120℃恒温主要是驱赶吸附水,拉平床层温度。
(5)220℃开始有硫化反应应加强分析,每1小时分析一次进出口H2S含量。
(6)300℃时密切注意床层温度付反应开始,应控制入口温度按硫化曲线进行。
(7)300℃-370℃吸硫激烈,应保证充足时间,使硫化彻底具体参照分析数据定,当开始放硫时(出口H2S浓度大于入口H2S浓度)应加快升温。
(8)硫化时提高压力应缓慢进行,最高提至1.0MPa。
放硫时应把温度提到400℃保持0.1-0.2MPa即可,此时应该保证足够时间,当分析进出口硫浓度基本一致,可认为硫化结束。
(9)催化剂硫化结束后要用低硫原料气对催化剂吹扫,这时可将催化剂床层温度保持在400℃,压力逐渐降低,保持在0.1-0.2MPa即可,这一阶段要保证有足够时间,分析出口H2S≤300mg/m3可停止吹扫,将系统压力逐渐提至0.5MPa,设备保温保压。
(10)硫化期间应严格监测氮气纯度,保证氮气纯度>99.9%,原料气中严格控制氧含量≤
0.2%(V)。
(11)升温介质中不允许含有NH3,以防造成钼流失。
(12)硫化时严禁催化剂超温,若出现温升过快应立即停、切气,查明原因后方可再硫化。
(13)硫化时注意提温不提氢,提氢不提温。
4、高温氧化锌升温
二次铁钼槽硫化结束后,利用焦炉气对氧化锌升温:
低硫焦炉气→焦炉气压缩机→油过滤器→升温炉→二次铁钼→2#氧化锌→1#氧化锌→FK
JX-4C高温氧化锌升温方案
1.升温时,当新1#氧化锌、2#氧化锌升至120℃均应安排4-6小时恒温,这时,要及时排放导淋内的冷凝水。
以上均以每槽触媒热点为控制点来调节升温速率,以缩短时间,分别使升温气直接进入1#氧化锌、2#氧化锌,分别将各槽升至指标上限。
待两槽均升至指标上限,逐槽切出。
2.1防止蒸汽进入氧化锌槽。
2.2按时排冷凝水。
2.3不可使用硫化气进行升温。
精脱硫系统升温还原硫化工作结束后系统充氮气保压1.5MPa对系统保温保压防止空气进入系统。
七、转化炉、预热炉、废热锅炉烘炉:
精脱硫系统开始配H2还原后,为缩短开车时间,转化炉、预热炉及废热锅炉可利用氮气对其进行烘炉工作。
1.分析预热炉炉膛:CO+H2<0.5%,燃烧气中O2<0.5%,按预热炉点火操作程序,点燃预热炉火嘴。
2.按以下流程通氮气对上述设备烘炉。
|→精脱硫用
氮气→氧压机→氧气管线→氮气管线→焦炉气预热器→预热炉→转化炉→废热锅炉→焦炉气预热器→初预热器→锅炉给水预热器→脱盐水预热器→第一水冷器→第二水冷器→分离器→放空
3.为确保烘炉质量,在转化炉第一阶段升温时,转化夹套冷却水可不用,待第二阶段升温时,视情况再加。
4.在烘炉过程中,预热炉对流段温度>250℃后可通少量蒸汽保护炉管(现场排放)。
5.转化烘炉氮气量随着炉温的逐渐升高要适当调整,尽可能缩小各测温点间的温差。
转化炉、预热炉、废热锅炉烘炉方案
1.烘炉目的:
各设备在筑炉过程,耐火浇注料中配有7-10%左右的水搅拌而成。
故烘炉的目的主要是除去耐火材料的吸附水和部分结晶水,以免在操作过程中,浇注料中的水份急剧蒸发,使浇注料产生裂纹,剥落甚至炸裂现象,造成设备内壁与高温气体直接接触,设备壳体超温,危及
设备正常运行,故烘炉是确保浇注质量及设备安全的重要环节。
2.烘炉说明:
2.1本次烘炉涉及的设备有:
转化:预热炉(B60601)、转化炉(D60601)、废热锅炉(C60601)
共三台设备,在触媒装填之前需要认真烘炉。
2.2传热介质:通过焦炉气压缩机压缩空气进行,热源由预热炉和升温炉提供。
2.3预热炉利用自身燃烧火嘴进行加热炉膛烘炉,燃料气来自转化工段燃料气混合器,燃烧废气由预热炉顶烟囱高点排空。
转化炉、废热锅炉利用压缩机来压缩空气依次经过升温炉和预热炉的炉内盘管预热后作为热源,进行串联烘炉,气体在焦炉气初预热器出口解法兰放空。
(预热炉辐射段通入压缩空气传热,对流段可通压缩空气或者电厂低压蒸汽均可)
2.4烘炉温度达到指标温度后,以<20℃/h的速率把各设备炉温降到常温,然后拆开人孔,进入内部检查。
3.烘炉应具备的条件:
3.1精脱硫、转化工段所有设备、管道、阀门、仪表都安装完毕,设备及管道的吹除、气密试验都合格、DCS、仪表、电气等都调校合格。
3.2水、电气、仪表空气、低压蒸汽、燃料煤气都具备使用条件。
3.3所有操作人员都熟悉现场工艺流程和设备结构性能、并熟知操作控制手段和烘炉方案。
3.4烘炉用的工具、红外线测温仪、消防器材、防护用品都已准备好。
3.5烘炉的记录表、交接班记录薄、烘炉曲线已准备好。
3.6循环水、脱盐水、低压蒸汽、燃烧煤气能保证正常供给。
3.7焦炉气压缩机试车合格,保证有足够的气量。
4.烘炉准备工作:
4.1绘制各设备烘炉曲线,准备好相关记录用具及相关点火器具。
4.2准备红外线测温仪一台。
4.3燃料气引至升温炉和预热炉入口并置换燃料气管道合格。
4.4拆开焦炉气初预热器壳程的出口作为转化炉和废锅升温介质的排出口。
4.5利用电厂低压蒸汽投运除氧站,保证有合格的除氧水送出同锅炉给水泵送入废锅汽包;转化炉夹套和废锅夹套启动循环水冷却系统。
5、烘炉步骤:
5.1烘炉流程:将预热炉、转化炉、废热锅炉利用串联方式,同时烘炉。
5.2时间安排:在转化工段所有设备管道阀门仪表等安装完毕,气密实验和吹扫工作合格后,转化催化剂装填之前进行。
5.3热源:利用焦炉煤气作为燃料,同升温炉和预热炉其同提供热源。
5.4传热介质:启动一台焦炉气压缩机关出压缩空气,作为炉管内的传热介质。
5.5严格按照预热炉烘炉曲线、转化炉烘炉曲线、废热锅炉曲线进行烘炉,不得任意修改。
5.6烘炉结束后,打开人孔进入炉内检查耐火材料有无脱落和裂缝,换热炉管和内件是否正常,发现问题及时通知设备或衬里制造厂进行处理。
注意:在烘废热锅炉时,要通过汽包及时向废热锅炉内加入锅炉水,并维持正常液位。
以调整汽包压力,使废锅出口温度达到350℃。
6、预热炉烘炉
6.1预热炉烘炉步骤:
6.1.1预热炉技术特性指标按设计要求。
预热炉炉内从上到下共有五个测温点,三个测压点。
6.1.2预热炉烘炉温度指标表:参照预热炉烘炉曲线。
6.2预热炉本体烘炉具体步骤:
6.2.1打开焦炉气压缩机来焦炉气至升温炉盘管入口阀门和出口阀门,同时关闭精脱硫工段氧化锌脱硫槽出口阀门;打开升温炉出口至转化工段的中压蒸汽管道上阀门直至预热炉对流段入口前。
6.2.2启动焦炉气压缩机,焦炉气压缩机压缩空气,由PG-61217-250-4C1,经P-61214-200-4C1管线进入升温炉盘管入口,压缩空气量控制应根据变化及时调整,向升温炉盘管送压缩空气,气体经升温炉初步预热后由出口一路进入焦炉气预热器再进入预热炉辐射段,另一路经蒸汽管网进入预热炉的对流段(根据情况也可通入电厂低压蒸汽),辐射段和对流段的空气再经预热炉加热后进入转化炉和废热锅炉,对转化炉和废热锅炉进行烘炉。
传热压缩空气在焦炉气初预热器壳程出口排空。